oil level YAMAHA WR 250F 2009 Owners Manual
[x] Cancel search | Manufacturer: YAMAHA, Model Year: 2009, Model line: WR 250F, Model: YAMAHA WR 250F 2009Pages: 224, PDF Size: 13.93 MB
Page 9 of 224
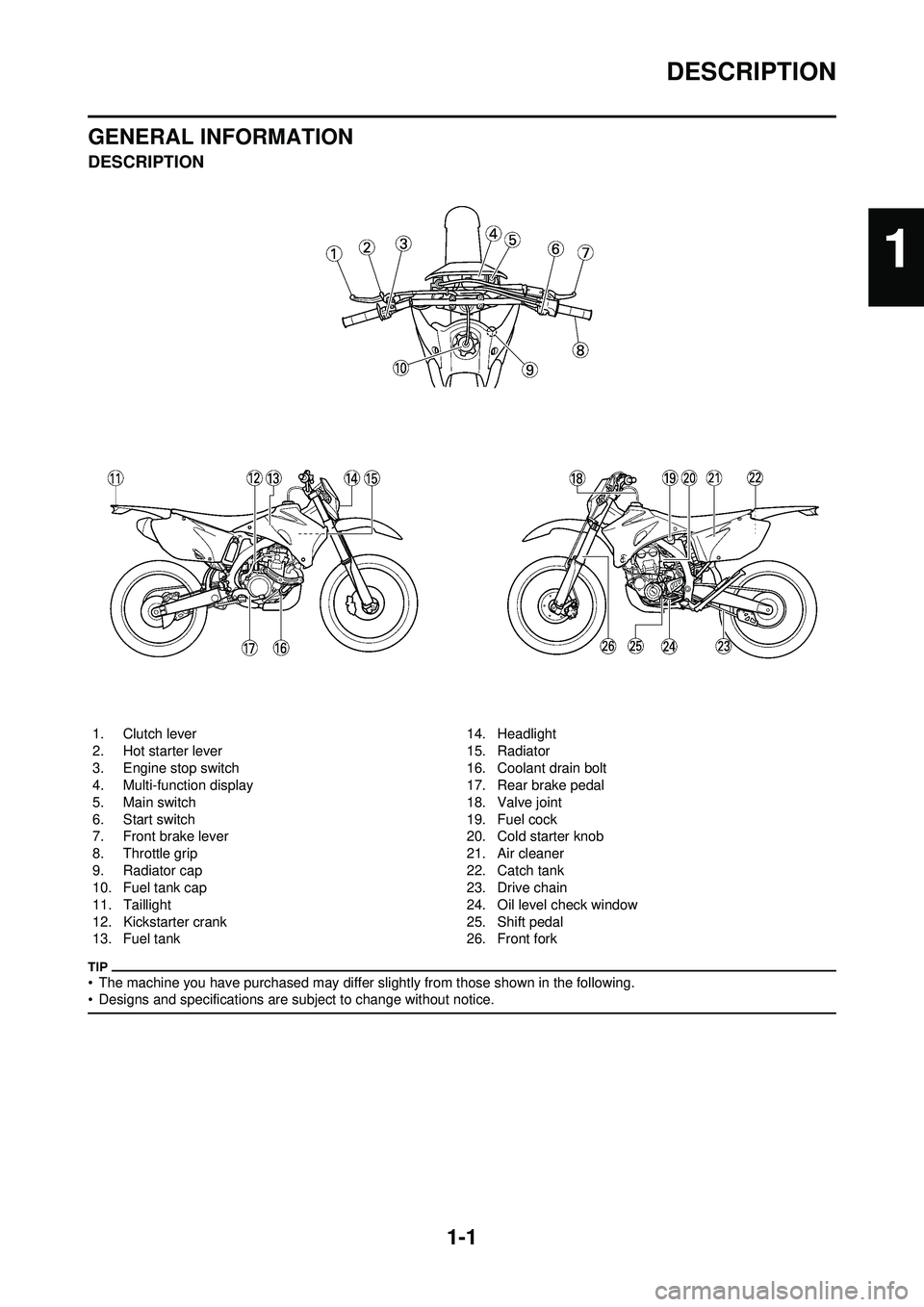
1-1
DESCRIPTION
GENERAL INFORMATION
DESCRIPTION
• The machine you have purchased may differ slightly from those shown in the following.
• Designs and specifications are subject to change without notice.
1. Clutch lever
2. Hot starter lever
3. Engine stop switch
4. Multi-function display
5. Main switch
6. Start switch
7. Front brake lever
8. Throttle grip
9. Radiator cap
10. Fuel tank cap
11. Taillight
12. Kickstarter crank
13. Fuel tank14. Headlight
15. Radiator
16. Coolant drain bolt
17. Rear brake pedal
18. Valve joint
19. Fuel cock
20. Cold starter knob
21. Air cleaner
22. Catch tank
23. Drive chain
24. Oil level check window
25. Shift pedal
26. Front fork
1
Page 22 of 224
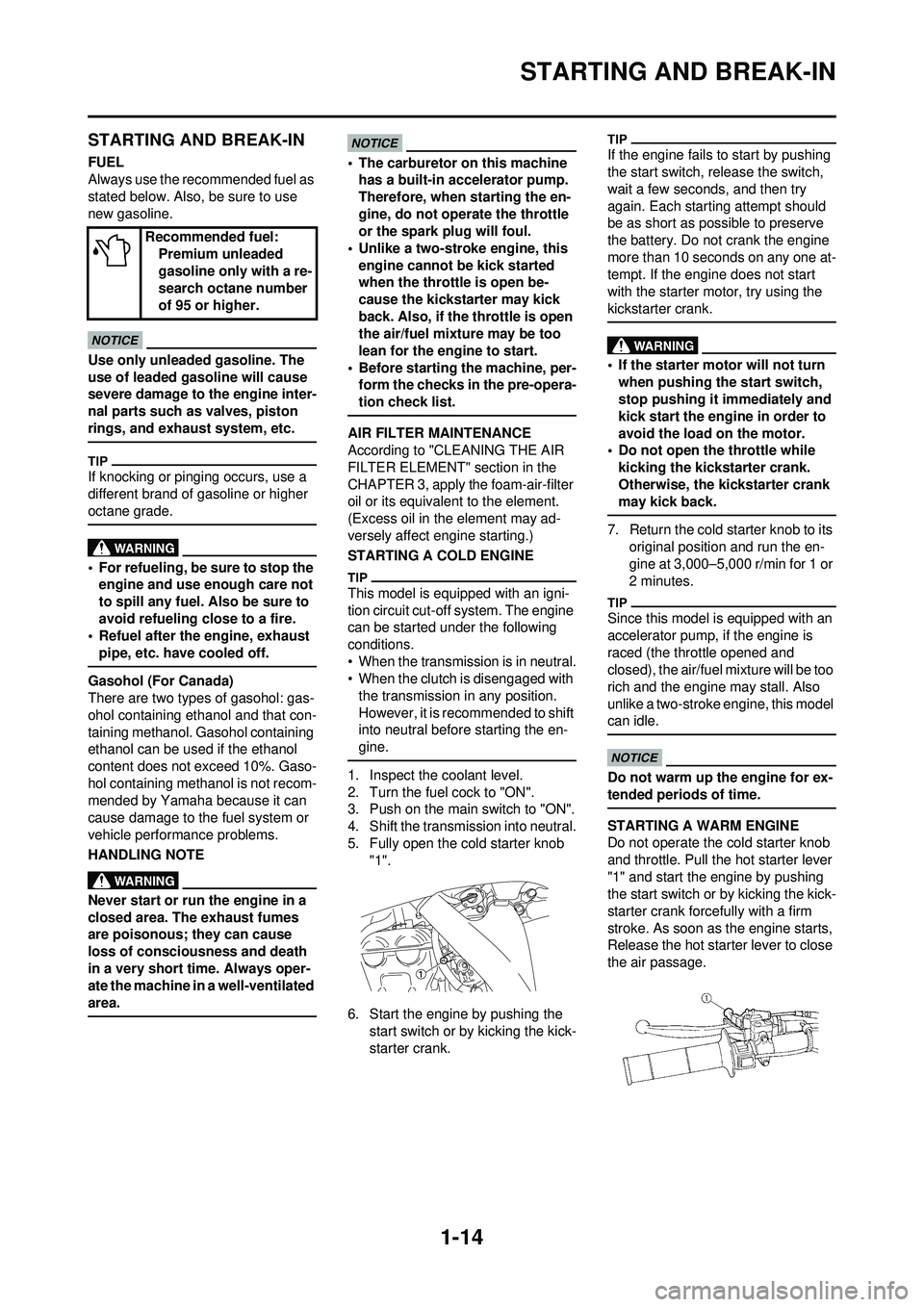
1-14
STARTING AND BREAK-IN
STARTING AND BREAK-IN
FUEL
Always use the recommended fuel as
stated below. Also, be sure to use
new gasoline.
Use only unleaded gasoline. The
use of leaded gasoline will cause
severe damage to the engine inter-
nal parts such as valves, piston
rings, and exhaust system, etc.
If knocking or pinging occurs, use a
different brand of gasoline or higher
octane grade.
• For refueling, be sure to stop the engine and use enough care not
to spill any fuel. Also be sure to
avoid refueling close to a fire.
• Refuel after the engine, exhaust
pipe, etc. have cooled off.
Gasohol (For Canada)
There are two types of gasohol: gas-
ohol containing ethanol and that con-
taining methanol. Gasohol containing
ethanol can be used if the ethanol
content does not exceed 10%. Gaso-
hol containing methanol is not recom-
mended by Yamaha because it can
cause damage to the fuel system or
vehicle performance problems.
HANDLING NOTE
Never start or run the engine in a
closed area. The exhaust fumes
are poisonous; they can cause
loss of consciousness and death
in a very short time. Always oper-
ate the machine in a well-ventilated
area.
• The carburetor on this machine has a built-in accelerator pump.
Therefore, when starting the en-
gine, do not operate the throttle
or the spark plug will foul.
• Unlike a two-stroke engine, this engine cannot be kick started
when the throttle is open be-
cause the kickstarter may kick
back. Also, if the throttle is open
the air/fuel mixture may be too
lean for the engine to start.
• Before starting the machine, per- form the checks in the pre-opera-
tion check list.
AIR FILTER MAINTENANCE
According to "CLEANING THE AIR
FILTER ELEMENT" section in the
CHAPTER 3, apply the foam-air-filter
oil or its equivalent to the element.
(Excess oil in the element may ad-
versely affect engine starting.)
STARTING A COLD ENGINE
This model is equipped with an igni-
tion circuit cut-off system. The engine
can be started under the following
conditions.
• When the transmission is in neutral.
• When the clutch is disengaged with
the transmission in any position.
However, it is recommended to shift
into neutral before starting the en-
gine.
1. Inspect the coolant level.
2. Turn the fuel cock to "ON".
3. Push on the main switch to "ON".
4. Shift the transmission into neutral.
5. Fully open the cold starter knob "1".
6. Start the engine by pushing the start switch or by kicking the kick-
starter crank.
If the engine fails to start by pushing
the start switch, release the switch,
wait a few seconds, and then try
again. Each starting attempt should
be as short as possible to preserve
the battery. Do not crank the engine
more than 10 seconds on any one at-
tempt. If the engine does not start
with the starter motor, try using the
kickstarter crank.
• If the starter motor will not turn
when pushing the start switch,
stop pushing it immediately and
kick start the engine in order to
avoid the load on the motor.
• Do not open the throttle while
kicking the kickstarter crank.
Otherwise, the kickstarter crank
may kick back.
7. Return the cold starter knob to its original position and run the en-
gine at 3,000–5,000 r/min for 1 or
2 minutes.
Since this model is equipped with an
accelerator pump, if the engine is
raced (the throttle opened and
closed), the air/fuel mixture will be too
rich and the engine may stall. Also
unlike a two-stroke engine, this model
can idle.
Do not warm up the engine for ex-
tended periods of time.
STARTING A WARM ENGINE
Do not operate the cold starter knob
and throttle. Pull the hot starter lever
"1" and start the engine by pushing
the start switch or by kicking the kick-
starter crank forcefully with a firm
stroke. As soon as the engine starts,
Release the hot starter lever to close
the air passage.
Recommended fuel:
Premium unleaded
gasoline only with a re-
search octane number
of 95 or higher.
Page 34 of 224
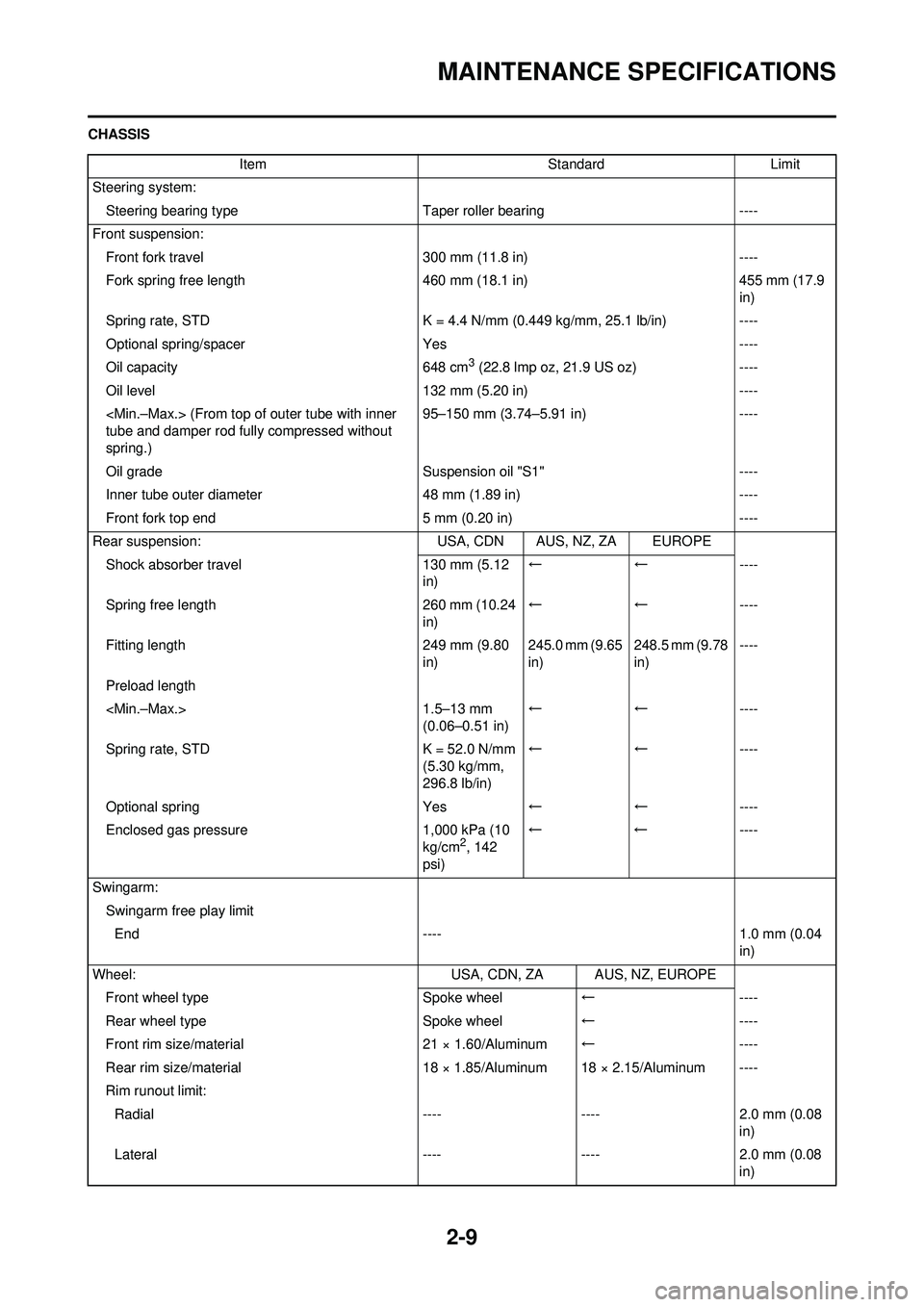
2-9
MAINTENANCE SPECIFICATIONS
CHASSISItem Standard Limit
Steering system: Steering bearing type Taper roller bearing----
Front suspension: Front fork travel 300 mm (11.8 in)----
Fork spring free length 460 mm (18.1 in)455 mm (17.9
in)
Spring rate, STD K = 4.4 N/mm (0.449 kg/mm, 25.1 lb/in)----
Optional spring/spacer Yes----
Oil capacity 648 cm
3 (22.8 lmp oz, 21.9 US oz)----
Oil level 132 mm (5.20 in)----
tube and damper rod fully compressed without
spring.) 95–150 mm (3.74–5.91 in)
----
Oil grade Suspension oil "S1"----
Inner tube outer diameter 48 mm (1.89 in)----
Front fork top end 5 mm (0.20 in)----
Rear suspension: USA, CDN AUS, NZ, ZA EUROPE
Shock absorber travel 130 mm (5.12
in) ←←
----
Spring free length 260 mm (10.24
in) ←←
----
Fitting length 249 mm (9.80
in) 245.0 mm (9.65
in) 248.5 mm (9.78
in)----
Preload length
(0.06–0.51 in) ←←
----
Spring rate, STD K = 52.0 N/mm
(5.30 kg/mm,
296.8 lb/in) ←←
----
Optional spring Yes←← ----
Enclosed gas pressure 1,000 kPa (10
kg/cm
2, 142
psi) ←←
----
Swingarm: Swingarm free play limitEnd ---- 1.0 mm (0.04
in)
Wheel: USA, CDN, ZA AUS, NZ, EUROPE
Front wheel type Spoke wheel←----
Rear wheel type Spoke wheel←----
Front rim size/material 21 × 1.60/Aluminum←----
Rear rim size/material 18 × 1.85/Aluminum 18 × 2.15/Aluminum ----
Rim runout limit: Radial --------2.0 mm (0.08
in)
Lateral --------2.0 mm (0.08
in)
Page 56 of 224
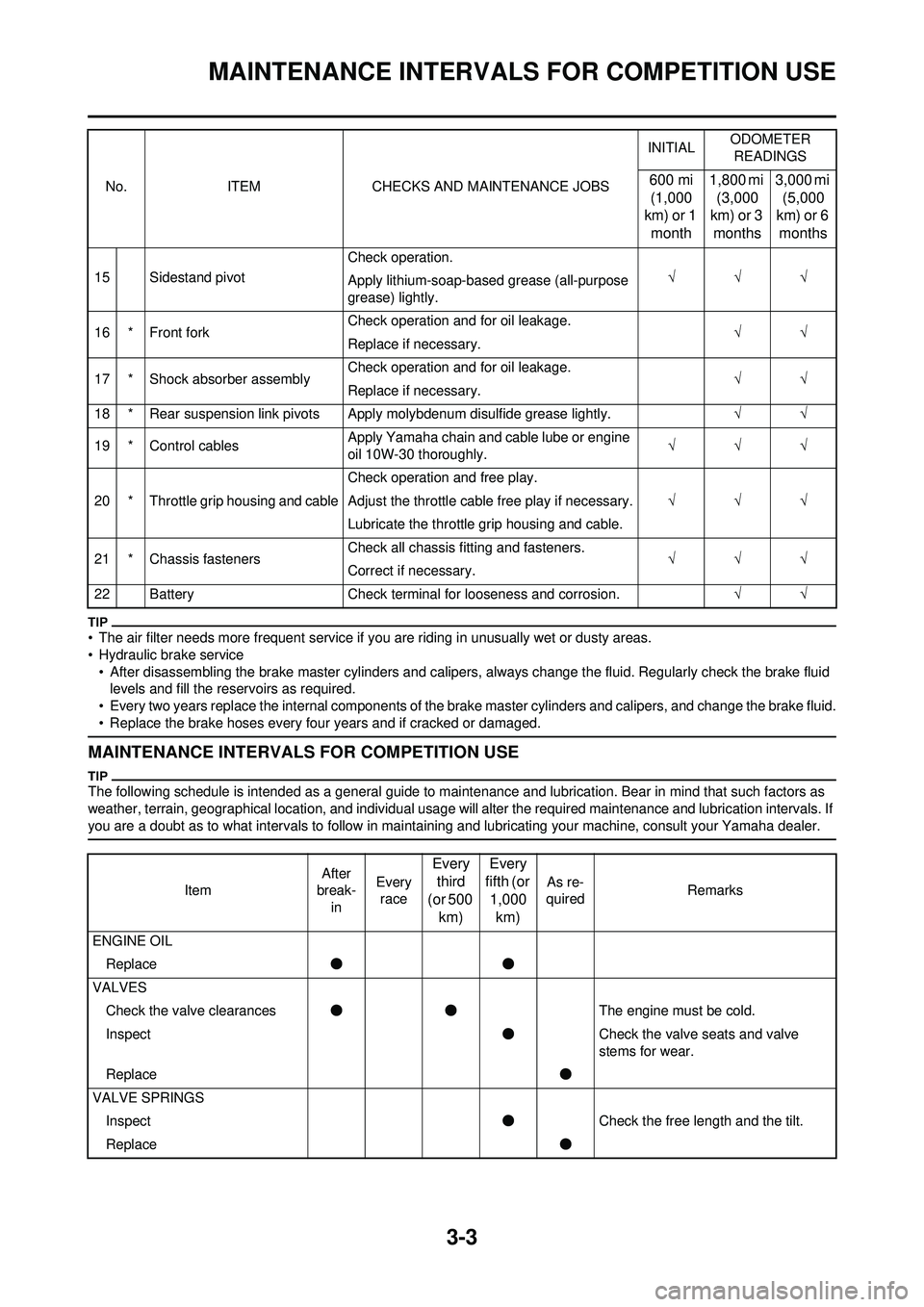
3-3
MAINTENANCE INTERVALS FOR COMPETITION USE
• The air filter needs more frequent service if you are riding in unusually wet or dusty areas.
• Hydraulic brake service• After disassembling the brake master cylinders and calipers, always change the fluid. Regularly check the brake fluid levels and fill the reservoirs as required.
• Every two years replace the internal components of the brake master cylinders and calipers, and change the brake fluid.
• Replace the brake hoses every four years and if cracked or damaged.
MAINTENANCE INTERVALS FOR COMPETITION USE
The following schedule is intended as a general guide to maintenance and lubrication. Bear in mind that such factors as
weather, terrain, geographical location, and individual usage will alter the required maintenance and lubrication intervals. If
you are a doubt as to what intervals to follow in maintaining and lubricating your machine, consult your Yamaha dealer.
15 Sidestand pivot Check operation.
√√√
Apply lithium-soap-based grease (all-purpose
grease) lightly.
16 * Front fork Check operation and for oil leakage.
√√
Replace if necessary.
17 * Shock absorber assembly Check operation and for oil leakage.
√√
Replace if necessary.
18 * Rear suspension link pivots Apply molybdenum disulfide grease lightly. √√
19 * Control cables Apply Yamaha chain and cable lube or engine
oil 10W-30 thoroughly. √√√
20 * Throttle grip housing and cable Check operation and free play.
√√√
Adjust the throttle cable free play if necessary.
Lubricate the throttle grip housing and cable.
21 * Chassis fasteners Check all chassis fitting and fasteners.
√√√
Correct if necessary.
22 Battery Check terminal for looseness and corrosion. √√
No.
ITEM CHECKS AND MAINTENANCE JOBS INITIAL
ODOMETER
READINGS
600 mi (1,000
km) or 1
month 1,800 mi
(3,000
km) or 3
months 3,000 mi
(5,000
km) or 6
months
Item After
break-
in Every
race
Every
third
(or 500 km) Every
fifth (or 1,000 km)
As re-
quired Remarks
ENGINE OIL Replace ●●
VALVES Check the valve clearances ●● The engine must be cold.
Inspect ●Check the valve seats and valve
stems for wear.
Replace ●
VALVE SPRINGS Inspect ●Check the free length and the tilt.
Replace ●
Page 58 of 224
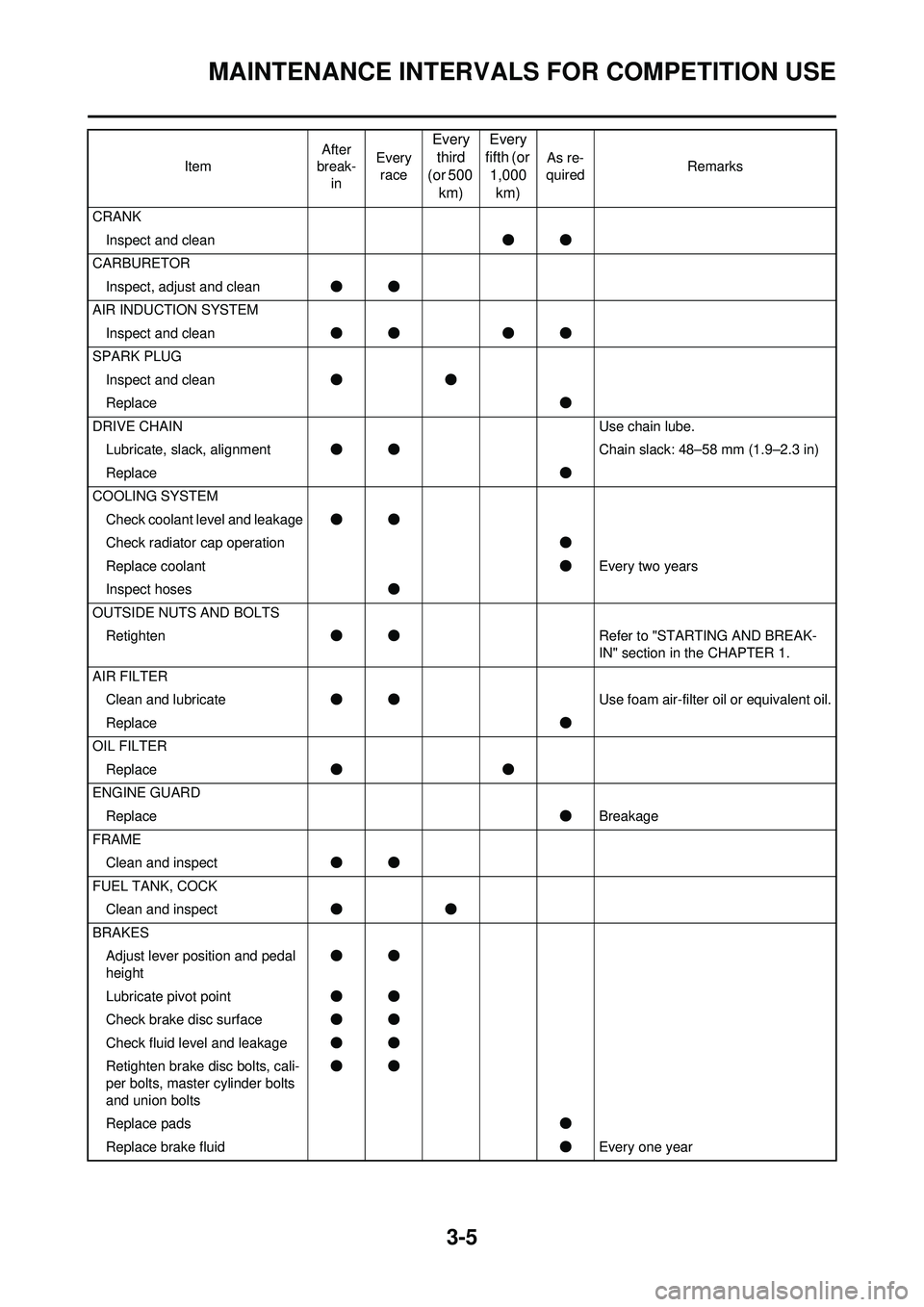
3-5
MAINTENANCE INTERVALS FOR COMPETITION USE
CRANKInspect and clean ●●
CARBURETOR Inspect, adjust and clean ●●
AIR INDUCTION SYSTEM Inspect and clean ●● ●●
SPARK PLUG Inspect and clean ●●
Replace ●
DRIVE CHAIN Use chain lube.
Lubricate, slack, alignment ●● Chain slack: 48–58 mm (1.9–2.3 in)
Replace ●
COOLING SYSTEM Check coolant level and leakage ●●
Check radiator cap operation ●
Replace coolant ●Every two years
Inspect hoses ●
OUTSIDE NUTS AND BOLTS Retighten ●● Refer to "STARTING AND BREAK-
IN" section in the CHAPTER 1.
AIR FILTER Clean and lubricate ●● Use foam air-filter oil or equivalent oil.
Replace ●
OIL FILTER Replace ●●
ENGINE GUARD Replace ●Breakage
FRAME Clean and inspect ●●
FUEL TANK, COCK Clean and inspect ●●
BRAKES Adjust lever position and pedal
height ●●
Lubricate pivot point ●●
Check brake disc surface ●●
Check fluid level and leakage ●●
Retighten brake disc bolts, cali-
per bolts, master cylinder bolts
and union bolts ●●
Replace pads ●
Replace brake fluid ●Every one year
Item
After
break-
in Every
race
Every third
(or 500 km) Every
fifth (or 1,000 km)
As re-
quired Remarks
Page 60 of 224
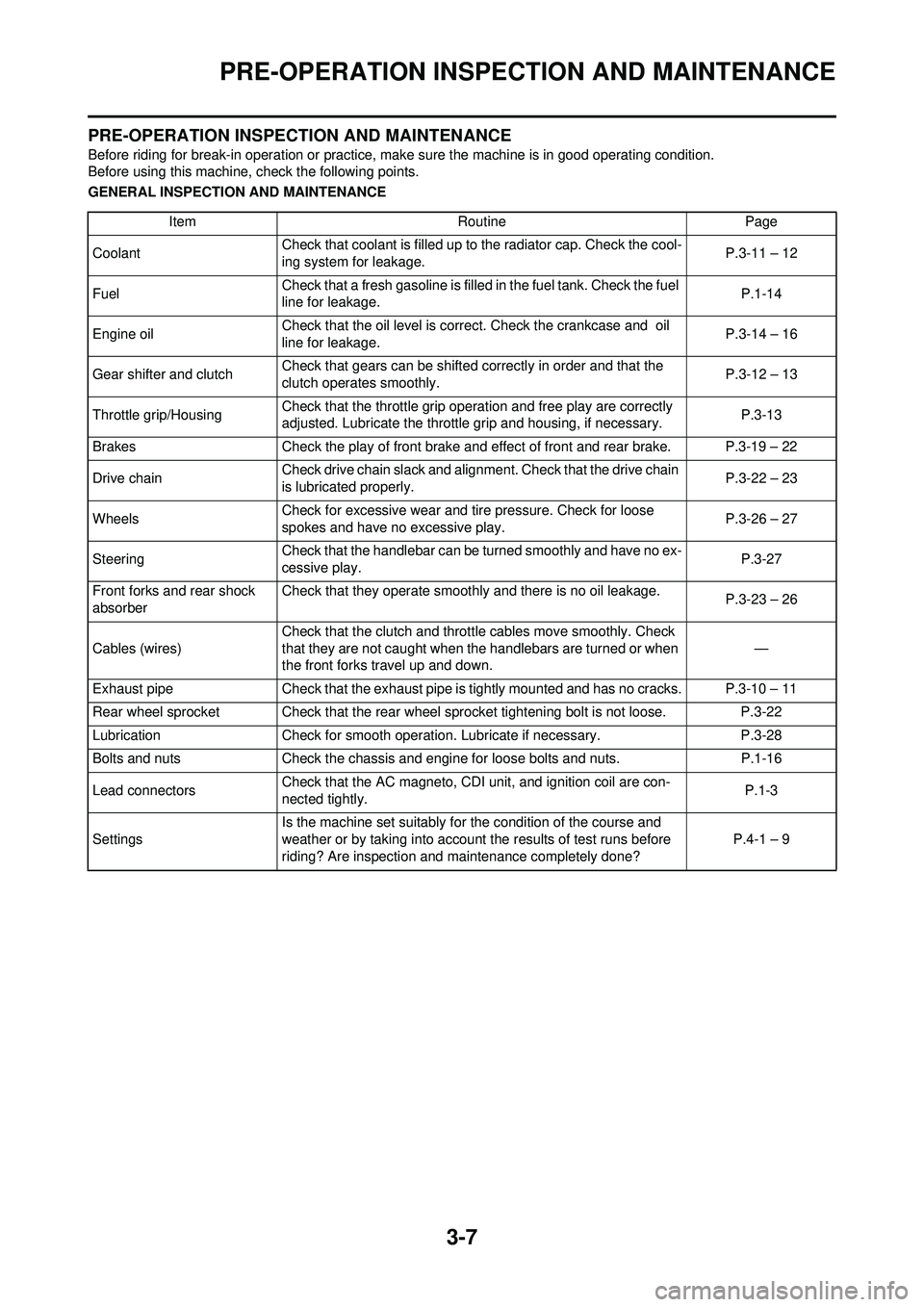
3-7
PRE-OPERATION INSPECTION AND MAINTENANCE
PRE-OPERATION INSPECTION AND MAINTENANCE
Before riding for break-in operation or practice, make sure the machine is in good operating condition.
Before using this machine, check the following points.
GENERAL INSPECTION AND MAINTENANCEItem RoutinePage
Coolant Check that coolant is filled up to the radiator cap. Check the cool-
ing system for leakage. P.3-11 – 12
Fuel Check that a fresh gasoline is filled in the fuel tank. Check the fuel
line for leakage.
P.1-14
Engine oil Check that the oil level is correct. Check the crankcase and oil
line for leakage. P.3-14 – 16
Gear shifter and clutch Check that gears can be shifted correctly in order and that the
clutch operates smoothly. P.3-12 – 13
Throttle grip/Housing Check that the throttle grip operation and free play are correctly
adjusted. Lubricate the throttle grip and housing, if necessary.
P.3-13
Brakes Check the play of front brake and effect of front and rear brake. P.3-19 – 22
Drive chain Check drive chain slack and alignment. Check that the drive chain
is lubricated properly. P.3-22 – 23
Wheels Check for excessive wear and tire pressure. Check for loose
spokes and have no excessive play. P.3-26 – 27
Steering Check that the handlebar can be turned smoothly and have no ex-
cessive play.
P.3-27
Front forks and rear shock
absorber Check that they operate smoothly and there is no oil leakage.
P.3-23 – 26
Cables (wires) Check that the clutch and throttle cables move smoothly. Check
that they are not caught when the handlebars are turned or when
the front forks travel up and down.
—
Exhaust pipe Check that the exhaust pipe is tightly mounted and has no cracks. P.3-10 – 11
Rear wheel sprocket Check that the rear wheel sprocket tightening bolt is not loose. P.3-22
Lubrication Check for smooth operation. Lubricate if necessary. P.3-28
Bolts and nuts Check the chassis and engine for loose bolts and nuts. P.1-16
Lead connectors Check that the AC magneto, CDI unit, and ignition coil are con-
nected tightly. P.1-3
Settings Is the machine set suitably for the condition of the course and
weather or by taking into account the results of test runs before
riding? Are inspection and maintenance completely done? P.4-1 – 9
Page 65 of 224
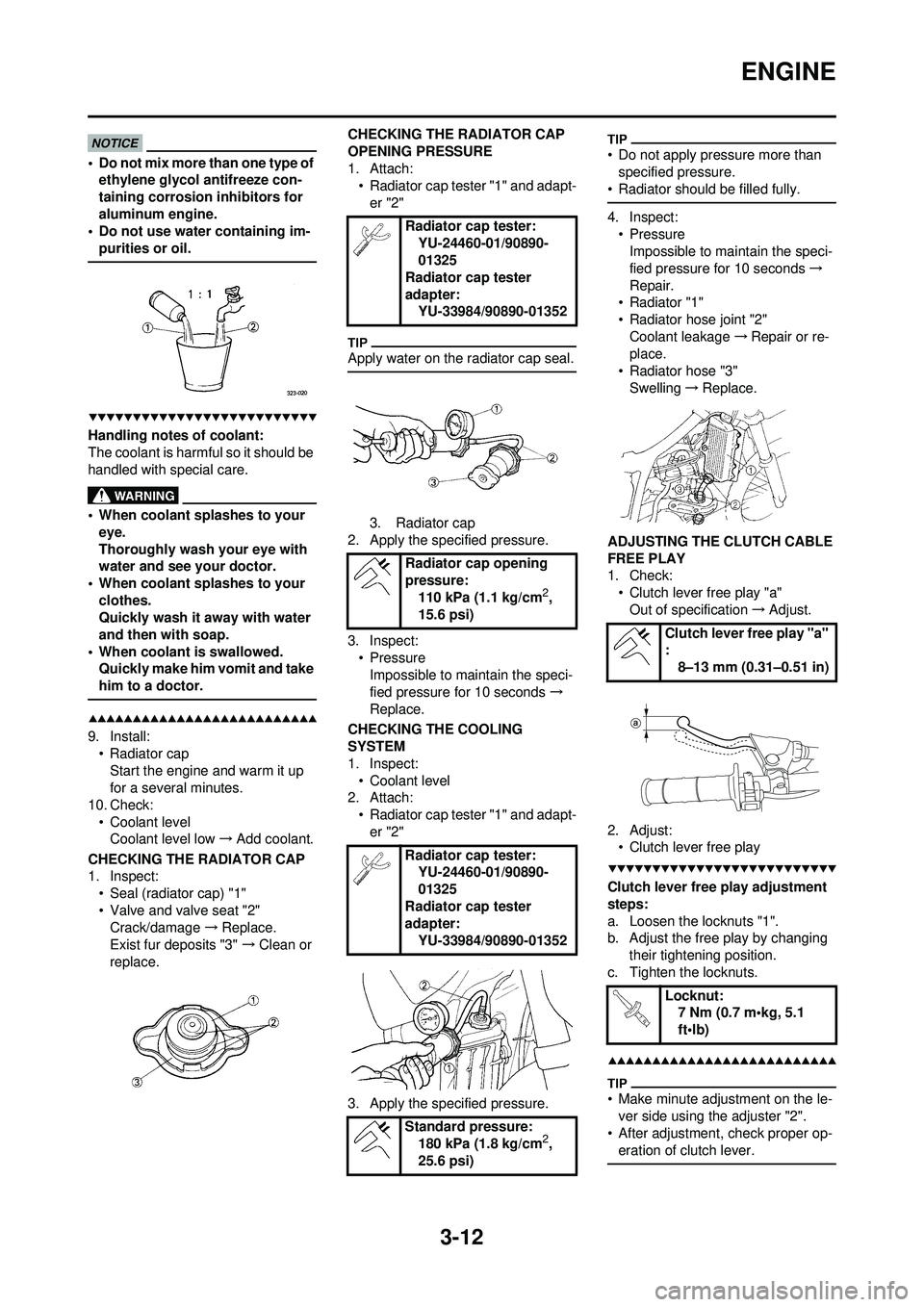
3-12
ENGINE
• Do not mix more than one type of ethylene glycol antifreeze con-
taining corrosion inhibitors for
aluminum engine.
• Do not use water containing im-
purities or oil.
Handling notes of coolant:
The coolant is harmful so it should be
handled with special care.
• When coolant splashes to your eye.
Thoroughly wash your eye with
water and see your doctor.
• When coolant splashes to your clothes.
Quickly wash it away with water
and then with soap.
• When coolant is swallowed. Quickly make him vomit and take
him to a doctor.
9. Install:
• Radiator capStart the engine and warm it up
for a several minutes.
10. Check: • Coolant levelCoolant level low →Add coolant.
CHECKING THE RADIATOR CAP
1. Inspect: • Seal (radiator cap) "1"
• Valve and valve seat "2"Crack/damage →Replace.
Exist fur deposits "3" →Clean or
replace. CHECKING THE RADIATOR CAP
OPENING PRESSURE
1. Attach:
• Radiator cap tester "1" and adapt-
er "2"
Apply water on the radiator cap seal.
3. Radiator cap
2. Apply the specified pressure.
3. Inspect: •PressureImpossible to maintain the speci-
fied pressure for 10 seconds →
Replace.
CHECKING THE COOLING
SYSTEM
1. Inspect: • Coolant level
2. Attach:
• Radiator cap tester "1" and adapt-er "2"
3. Apply the specified pressure.
• Do not apply pressure more than specified pressure.
• Radiator should be filled fully.
4. Inspect: •PressureImpossible to maintain the speci-
fied pressure for 10 seconds →
Repair.
•Radiator "1"
• Radiator hose joint "2"
Coolant leakage →Repair or re-
place.
• Radiator hose "3" Swelling →Replace.
ADJUSTING THE CLUTCH CABLE
FREE PLAY
1. Check: • Clutch lever free play "a"Out of specification →Adjust.
2. Adjust: • Clutch lever free play
Clutch lever free play adjustment
steps:
a. Loosen the locknuts "1".
b. Adjust the free play by changing
their tightening position.
c. Tighten the locknuts.
• Make minute adjustment on the le- ver side using the adjuster "2".
• After adjustment, check proper op-
eration of clutch lever.
Radiator cap tester: YU-24460-01/90890-
01325
Radiator cap tester
adapter: YU-33984/90890-01352
Radiator cap opening
pressure: 110 kPa (1.1 kg/cm
2,
15.6 psi)
Radiator cap tester: YU-24460-01/90890-
01325
Radiator cap tester
adapter: YU-33984/90890-01352
Standard pressure: 180 kPa (1.8 kg/cm
2,
25.6 psi)
Clutch lever free play "a"
: 8–13 mm (0.31–0.51 in)
Locknut: 7 Nm (0.7 m•kg, 5.1
ft•lb)
Page 67 of 224
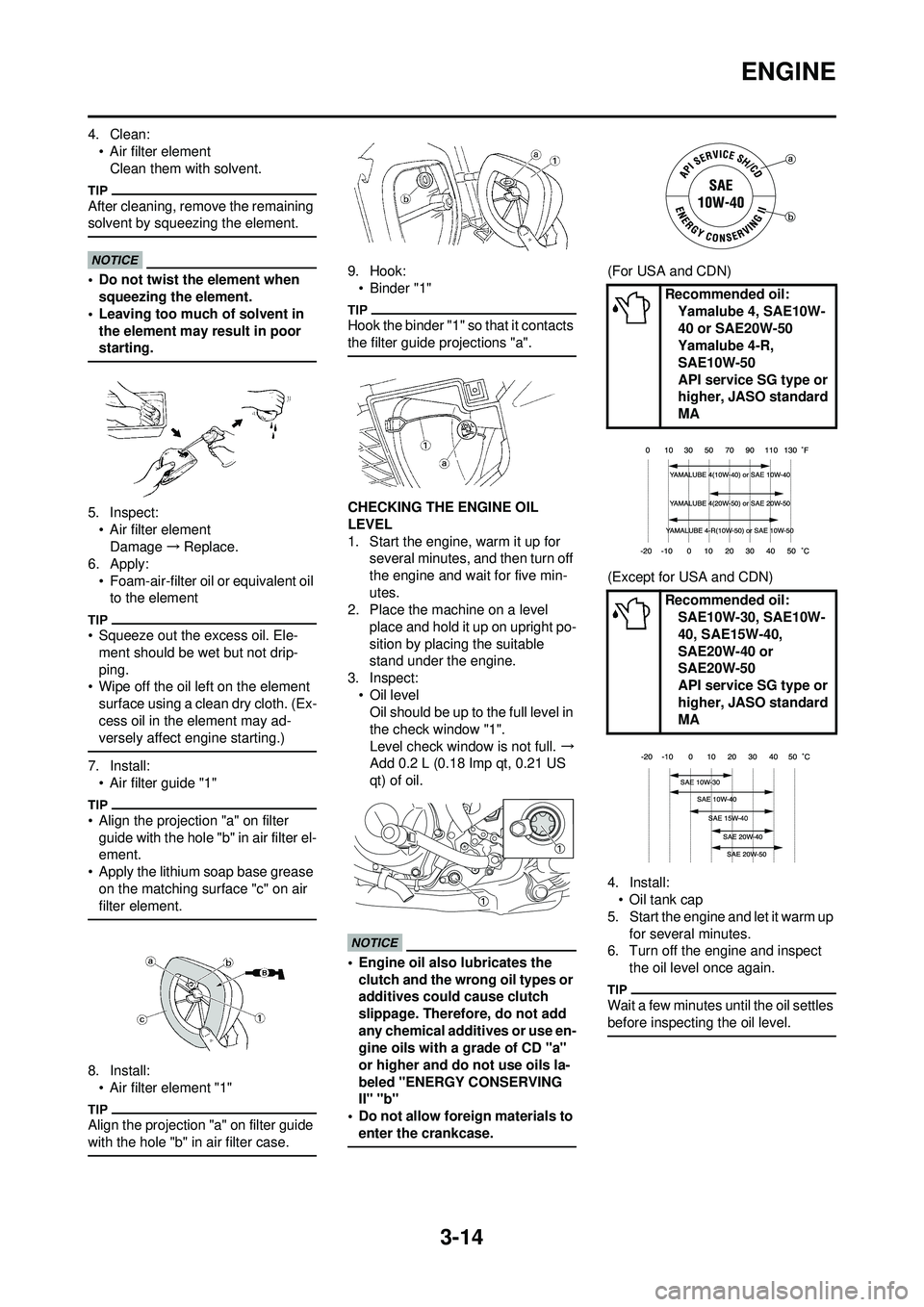
3-14
ENGINE
4. Clean:• Air filter elementClean them with solvent.
After cleaning, remove the remaining
solvent by squeezing the element.
• Do not twist the element when squeezing the element.
• Leaving too much of solvent in the element may result in poor
starting.
5. Inspect:• Air filter elementDamage →Replace.
6. Apply: • Foam-air-filter oil or equivalent oil to the element
• Squeeze out the excess oil. Ele-
ment should be wet but not drip-
ping.
• Wipe off the oil left on the element
surface using a clean dry cloth. (Ex-
cess oil in the element may ad-
versely affect engine starting.)
7. Install:• Air filter guide "1"
• Align the projection "a" on filter guide with the hole "b" in air filter el-
ement.
• Apply the lithium soap base grease on the matching surface "c" on air
filter element.
8. Install:• Air filter element "1"
Align the projection "a" on filter guide
with the hole "b" in air filter case.
9. Hook:• Binder "1"
Hook the binder "1" so that it contacts
the filter guide projections "a".
CHECKING THE ENGINE OIL
LEVEL
1. Start the engine, warm it up for several minutes, and then turn off
the engine and wait for five min-
utes.
2. Place the machine on a level
place and hold it up on upright po-
sition by placing the suitable
stand under the engine.
3. Inspect: • Oil levelOil should be up to the full level in
the check window "1".
Level check window is not full. →
Add 0.2 L (0.18 Imp qt, 0.21 US
qt) of oil.
• Engine oil also lubricates the
clutch and the wrong oil types or
additives could cause clutch
slippage. Therefore, do not add
any chemical additives or use en-
gine oils with a grade of CD "a"
or higher and do not use oils la-
beled "ENERGY CONSERVING
II" "b"
• Do not allow foreign materials to enter the crankcase.
(For USA and CDN)
(Except for USA and CDN)
4. Install:• Oil tank cap
5. Start the engine and let it warm up for several minutes.
6. Turn off the engine and inspect
the oil level once again.
Wait a few minutes until the oil settles
before inspecting the oil level.
Recommended oil:Yamalube 4, SAE10W-
40 or SAE20W-50
Yamalube 4-R,
SAE10W-50
API service SG type or
higher, JASO standard
MA
Recommended oil: SAE10W-30, SAE10W-
40, SAE15W-40,
SAE20W-40 or
SAE20W-50
API service SG type or
higher, JASO standard
MA
4
Page 68 of 224
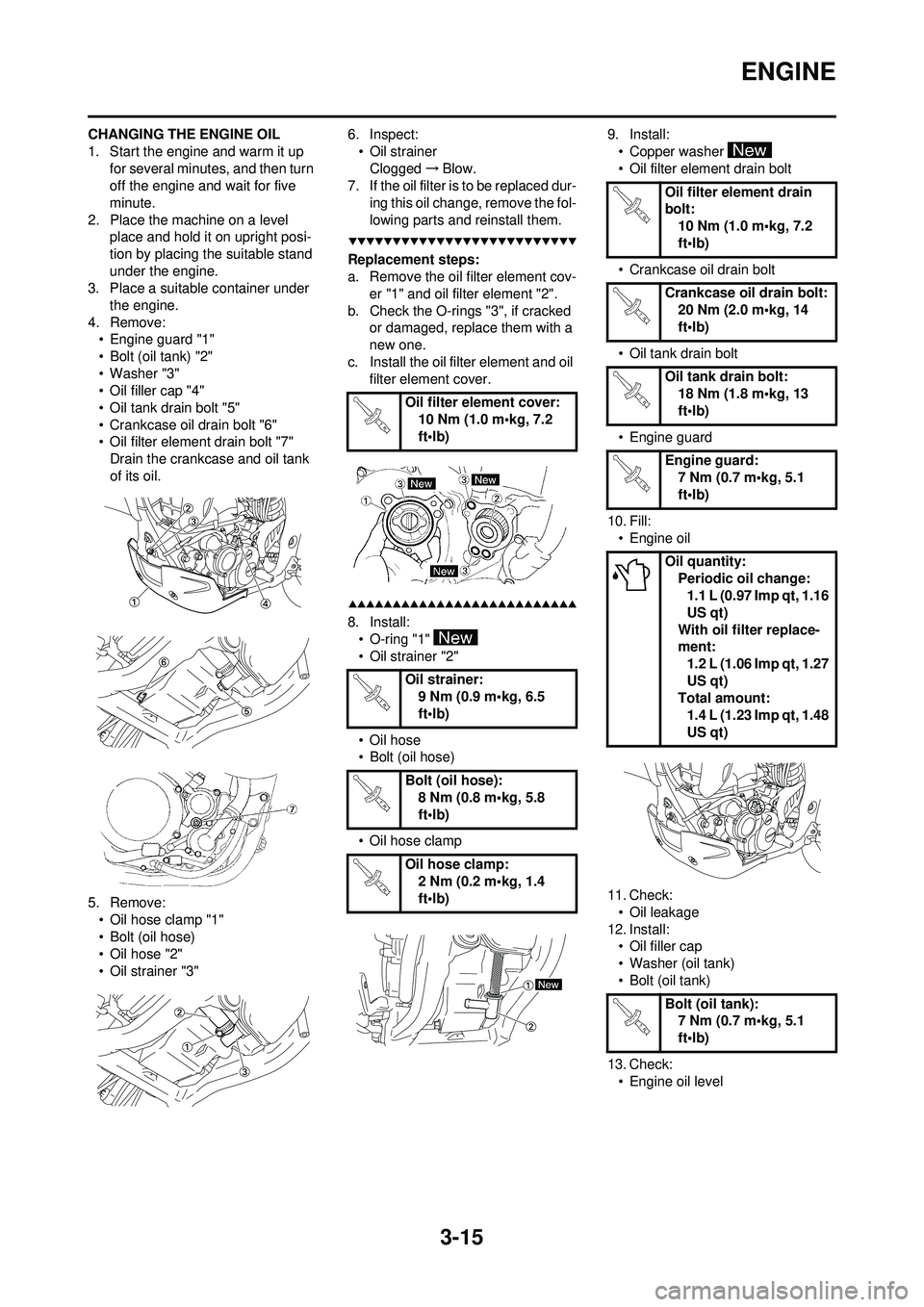
3-15
ENGINE
CHANGING THE ENGINE OIL
1. Start the engine and warm it up for several minutes, and then turn
off the engine and wait for five
minute.
2. Place the machine on a level place and hold it on upright posi-
tion by placing the suitable stand
under the engine.
3. Place a suitable container under
the engine.
4. Remove: • Engine guard "1"
• Bolt (oil tank) "2"
• Washer "3"
• Oil filler cap "4"
• Oil tank drain bolt "5"
• Crankcase oil drain bolt "6"
• Oil filter element drain bolt "7"
Drain the crankcase and oil tank
of its oil.
5. Remove: • Oil hose clamp "1"
• Bolt (oil hose)
•Oil hose "2"
• Oil strainer "3" 6. Inspect:
• Oil strainerClogged →Blow.
7. If the oil filter is to be replaced dur-
ing this oil change, remove the fol-
lowing parts and reinstall them.
Replacement steps:
a. Remove the oil filter element cov-er "1" and oil filter element "2".
b. Check the O-rings "3", if cracked or damaged, replace them with a
new one.
c. Install the oil filter element and oil filter element cover.
8. Install:
• O-ring "1"
• Oil strainer "2"
• Oil hose
• Bolt (oil hose)
• Oil hose clamp 9. Install:
• Copper washer
• Oil filter element drain bolt
• Crankcase oil drain bolt
• Oil tank drain bolt
• Engine guard
10. Fill: • Engine oil
11. Check: • Oil leakage
12. Install: • Oil filler cap
• Washer (oil tank)
• Bolt (oil tank)
13. Check: • Engine oil level
Oil filter element cover:
10 Nm (1.0 m•kg, 7.2
ft•lb)
Oil strainer: 9 Nm (0.9 m•kg, 6.5
ft•lb)
Bolt (oil hose): 8 Nm (0.8 m•kg, 5.8
ft•lb)
Oil hose clamp: 2 Nm (0.2 m•kg, 1.4
ft•lb)
Oil filter element drain
bolt:10 Nm (1.0 m•kg, 7.2
ft•lb)
Crankcase oil drain bolt: 20 Nm (2.0 m•kg, 14
ft•lb)
Oil tank drain bolt: 18 Nm (1.8 m•kg, 13
ft•lb)
Engine guard: 7 Nm (0.7 m•kg, 5.1
ft•lb)
Oil quantity: Periodic oil change:1.1 L (0.97 Imp qt, 1.16
US qt)
With oil filter replace-
ment: 1.2 L (1.06 Imp qt, 1.27
US qt)
Total amount:
1.4 L (1.23 Imp qt, 1.48
US qt)
Bolt (oil tank): 7 Nm (0.7 m•kg, 5.1
ft•lb)
Page 82 of 224
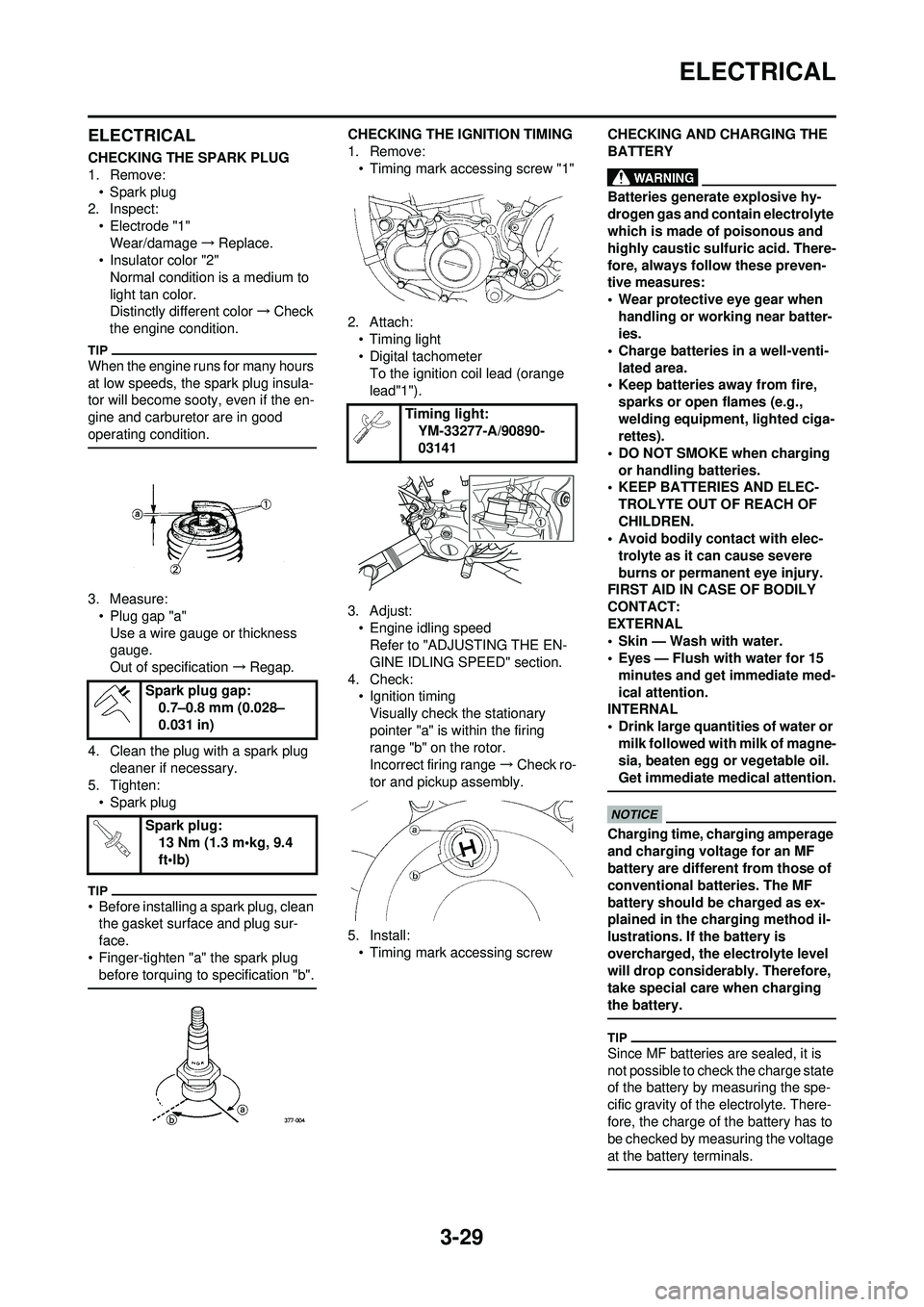
3-29
ELECTRICAL
ELECTRICAL
CHECKING THE SPARK PLUG
1. Remove:• Spark plug
2. Inspect:
• Electrode "1"Wear/damage →Replace.
• Insulator color "2"
Normal condition is a medium to
light tan color.
Distinctly different color →Check
the engine condition.
When the engine runs for many hours
at low speeds, the spark plug insula-
tor will become sooty, even if the en-
gine and carburetor are in good
operating condition.
3. Measure: • Plug gap "a"Use a wire gauge or thickness
gauge.
Out of specification →Regap.
4. Clean the plug with a spark plug cleaner if necessary.
5. Tighten: • Spark plug
• Before installing a spark plug, clean the gasket surface and plug sur-
face.
• Finger-tighten "a" the spark plug before torquing to specification "b".
CHECKING THE IGNITION TIMING
1. Remove:
• Timing mark accessing screw "1"
2. Attach: • Timing light
• Digital tachometerTo the ignition coil lead (orange
lead"1").
3. Adjust: • Engine idling speedRefer to "ADJUSTING THE EN-
GINE IDLING SPEED" section.
4. Check: • Ignition timing
Visually check the stationary
pointer "a" is within the firing
range "b" on the rotor.
Incorrect firing range →Check ro-
tor and pickup assembly.
5. Install: • Timing mark accessing screw CHECKING AND CHARGING THE
BATTERY
Batteries generate explosive hy-
drogen gas and contain electrolyte
which is made of poisonous and
highly caustic sulfuric acid. There-
fore, always follow these preven-
tive measures:
• Wear protective eye gear when
handling or working near batter-
ies.
• Charge batteries in a well-venti- lated area.
• Keep batteries away from fire,
sparks or open flames (e.g.,
welding equipment, lighted ciga-
rettes).
• DO NOT SMOKE when charging or handling batteries.
• KEEP BATTERIES AND ELEC-
TROLYTE OUT OF REACH OF
CHILDREN.
• Avoid bodily contact with elec-
trolyte as it can cause severe
burns or permanent eye injury.
FIRST AID IN CASE OF BODILY
CONTACT:
EXTERNAL
• Skin — Wash with water.
• Eyes — Flush with water for 15
minutes and get immediate med-
ical attention.
INTERNAL
• Drink large quantities of water or
milk followed with milk of magne-
sia, beaten egg or vegetable oil.
Get immediate medical attention.
Charging time, charging amperage
and charging voltage for an MF
battery are different from those of
conventional batteries. The MF
battery should be charged as ex-
plained in the charging method il-
lustrations. If the battery is
overcharged, the electrolyte level
will drop considerably. Therefore,
take special care when charging
the battery.
Since MF batteries are sealed, it is
not possible to check the charge state
of the battery by measuring the spe-
cific gravity of the electrolyte. There-
fore, the charge of the battery has to
be checked by measuring the voltage
at the battery terminals.
Spark plug gap: 0.7–0.8 mm (0.028–
0.031 in)
Spark plug: 13 Nm (1.3 m•kg, 9.4
ft•lb)
Timing light:YM-33277-A/90890-
03141