check engine YAMAHA YZ450F 2006 Owner's Manual
[x] Cancel search | Manufacturer: YAMAHA, Model Year: 2006, Model line: YZ450F, Model: YAMAHA YZ450F 2006Pages: 650, PDF Size: 20.71 MB
Page 238 of 650
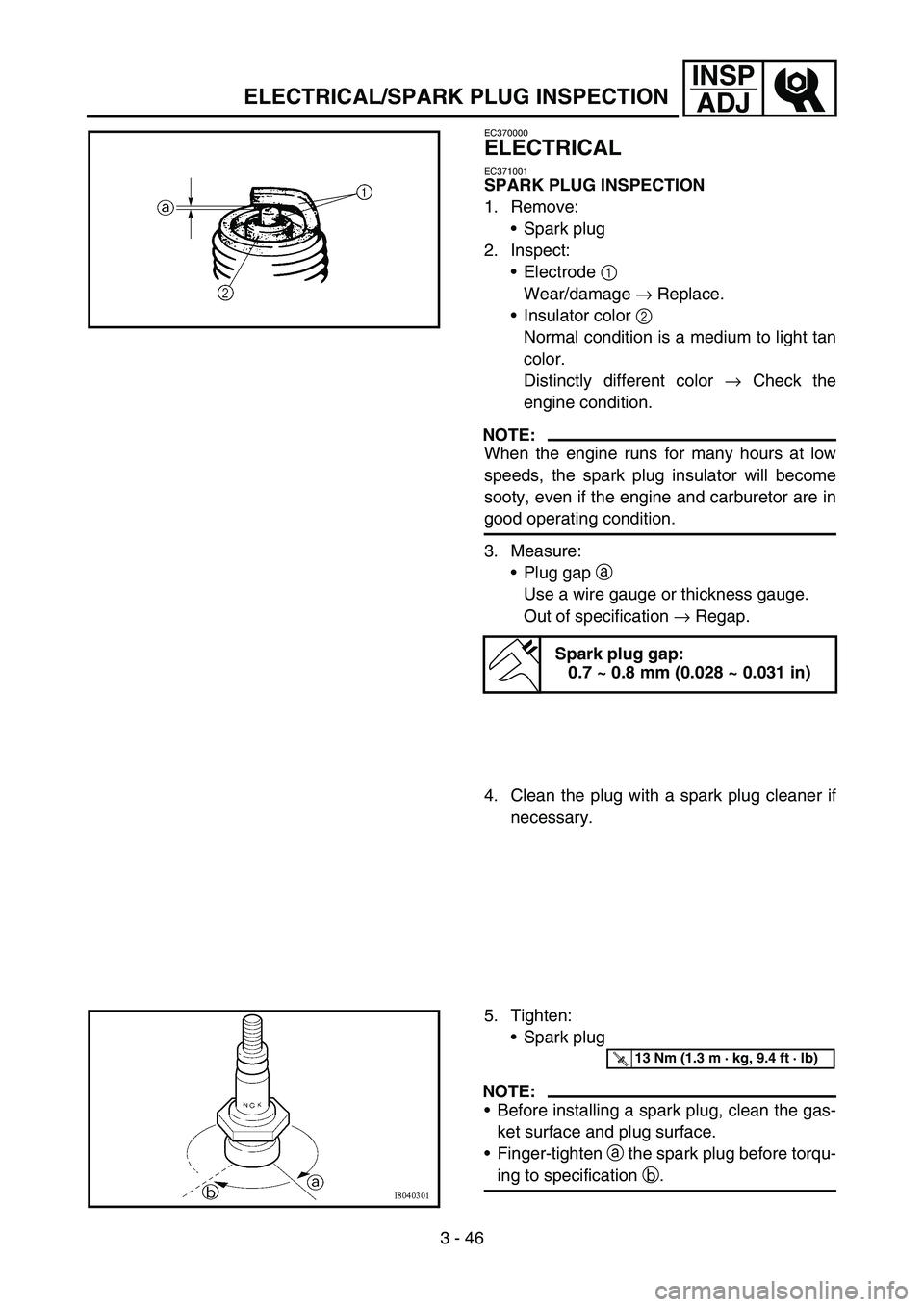
3 - 46
INSP
ADJ
ELECTRICAL/SPARK PLUG INSPECTION
EC370000
ELECTRICAL
EC371001
SPARK PLUG INSPECTION
1. Remove:
Spark plug
2. Inspect:
Electrode 1
Wear/damage → Replace.
Insulator color 2
Normal condition is a medium to light tan
color.
Distinctly different color → Check the
engine condition.
NOTE:
When the engine runs for many hours at low
speeds, the spark plug insulator will become
sooty, even if the engine and carburetor are in
good operating condition.
3. Measure:
Plug gap a
Use a wire gauge or thickness gauge.
Out of specification → Regap.
Spark plug gap:
0.7 ~ 0.8 mm (0.028 ~ 0.031 in)
4. Clean the plug with a spark plug cleaner if
necessary.
5. Tighten:
Spark plug
NOTE:
Before installing a spark plug, clean the gas-
ket surface and plug surface.
Finger-tighten a the spark plug before torqu-
ing to specification b.
T R..13 Nm (1.3 m · kg, 9.4 ft · lb)
Page 240 of 650
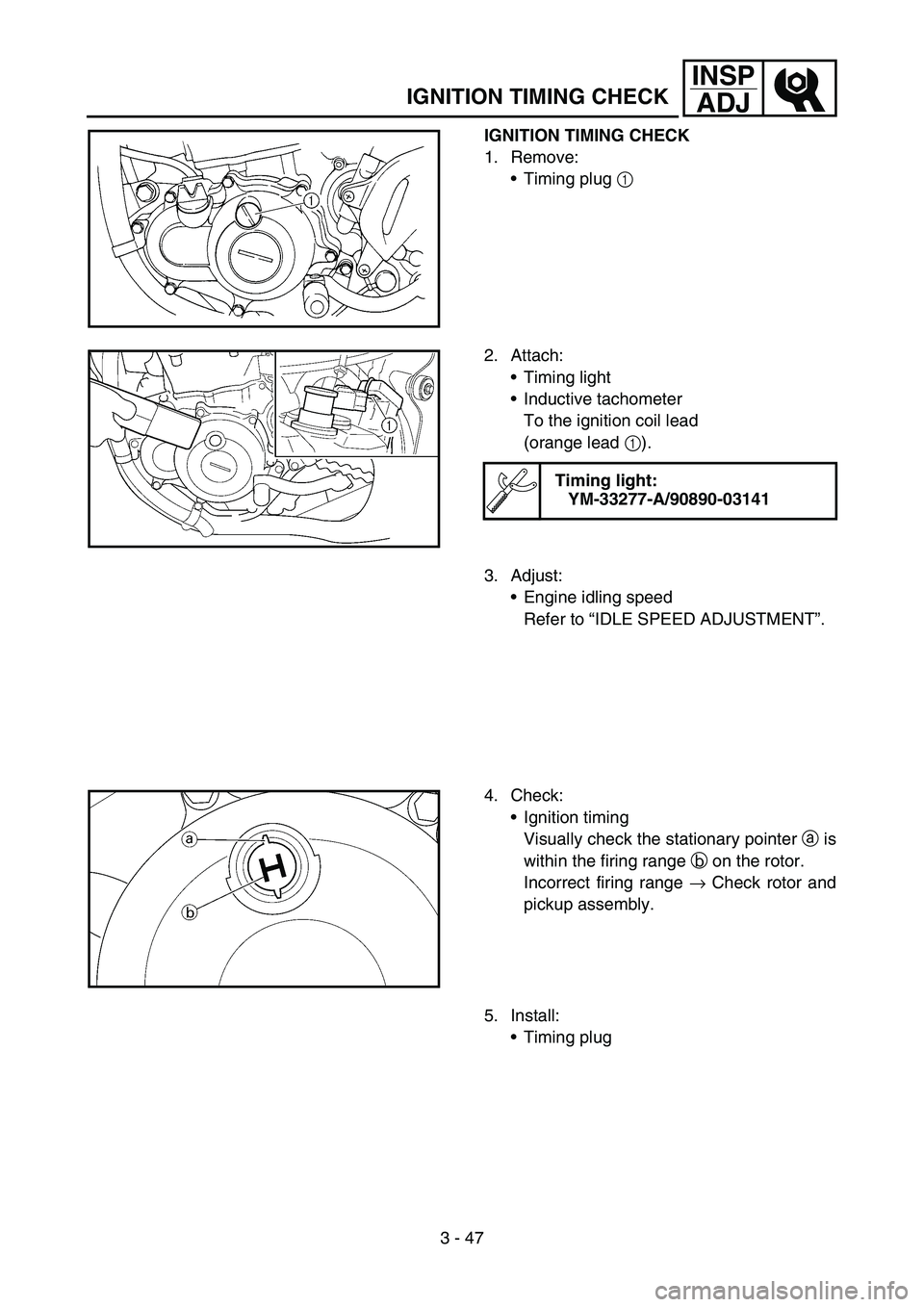
3 - 47
INSP
ADJ
IGNITION TIMING CHECK
IGNITION TIMING CHECK
1. Remove:
Timing plug 1
2. Attach:
Timing light
Inductive tachometer
To the ignition coil lead
(orange lead 1).
Timing light:
YM-33277-A/90890-03141
3. Adjust:
Engine idling speed
Refer to “IDLE SPEED ADJUSTMENT”.
4. Check:
Ignition timing
Visually check the stationary pointer a is
within the firing range b on the rotor.
Incorrect firing range → Check rotor and
pickup assembly.
5. Install:
Timing plug
Page 294 of 650
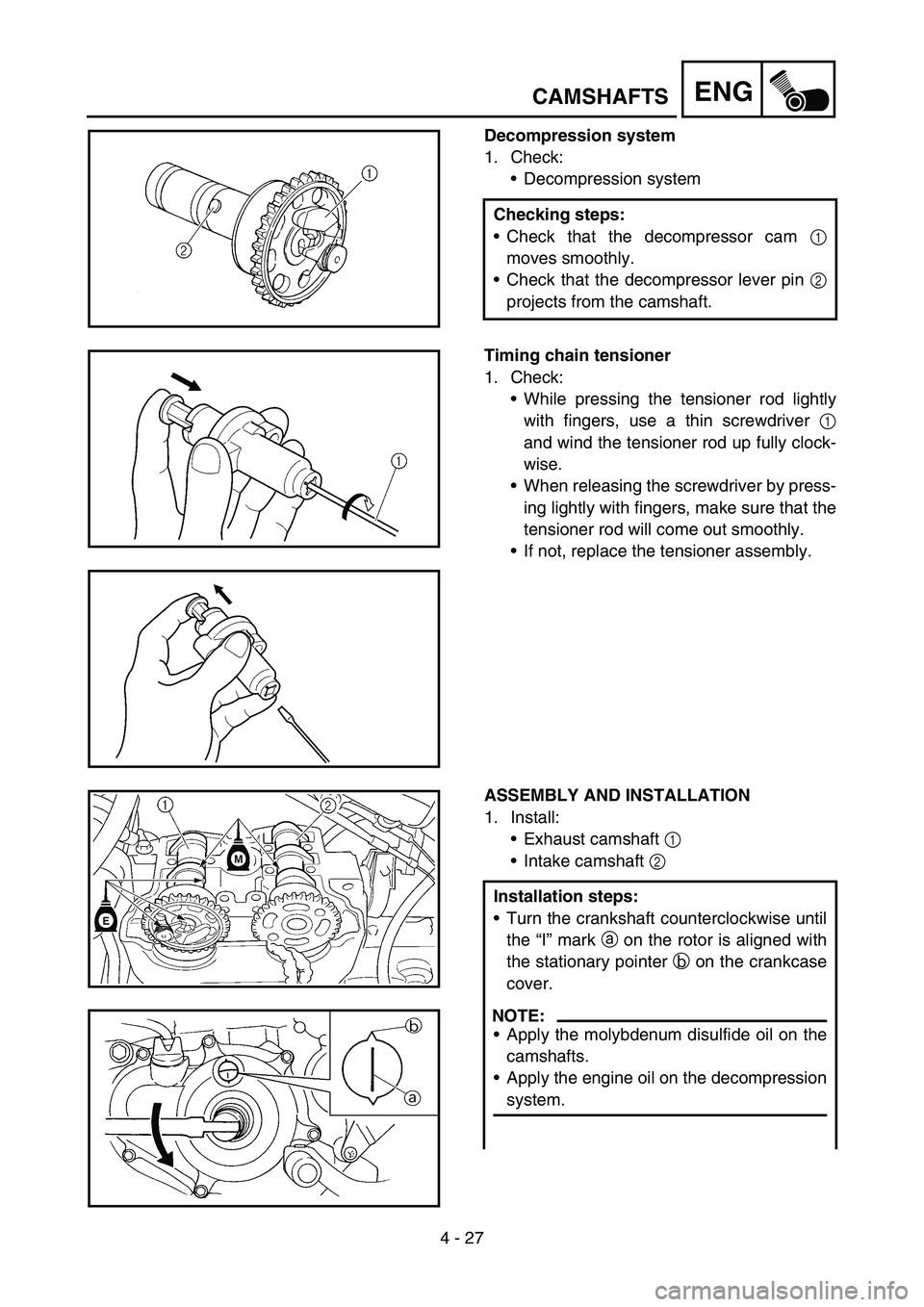
4 - 27
ENGCAMSHAFTS
Decompression system
1. Check:
Decompression system
Checking steps:
Check that the decompressor cam 1
moves smoothly.
Check that the decompressor lever pin 2
projects from the camshaft.
Timing chain tensioner
1. Check:
While pressing the tensioner rod lightly
with fingers, use a thin screwdriver 1
and wind the tensioner rod up fully clock-
wise.
When releasing the screwdriver by press-
ing lightly with fingers, make sure that the
tensioner rod will come out smoothly.
If not, replace the tensioner assembly.
ASSEMBLY AND INSTALLATION
1. Install:
Exhaust camshaft 1
Intake camshaft 2
Installation steps:
Turn the crankshaft counterclockwise until
the “I” mark a on the rotor is aligned with
the stationary pointer b on the crankcase
cover.
NOTE:
Apply the molybdenum disulfide oil on the
camshafts.
Apply the engine oil on the decompression
system.
Page 376 of 650
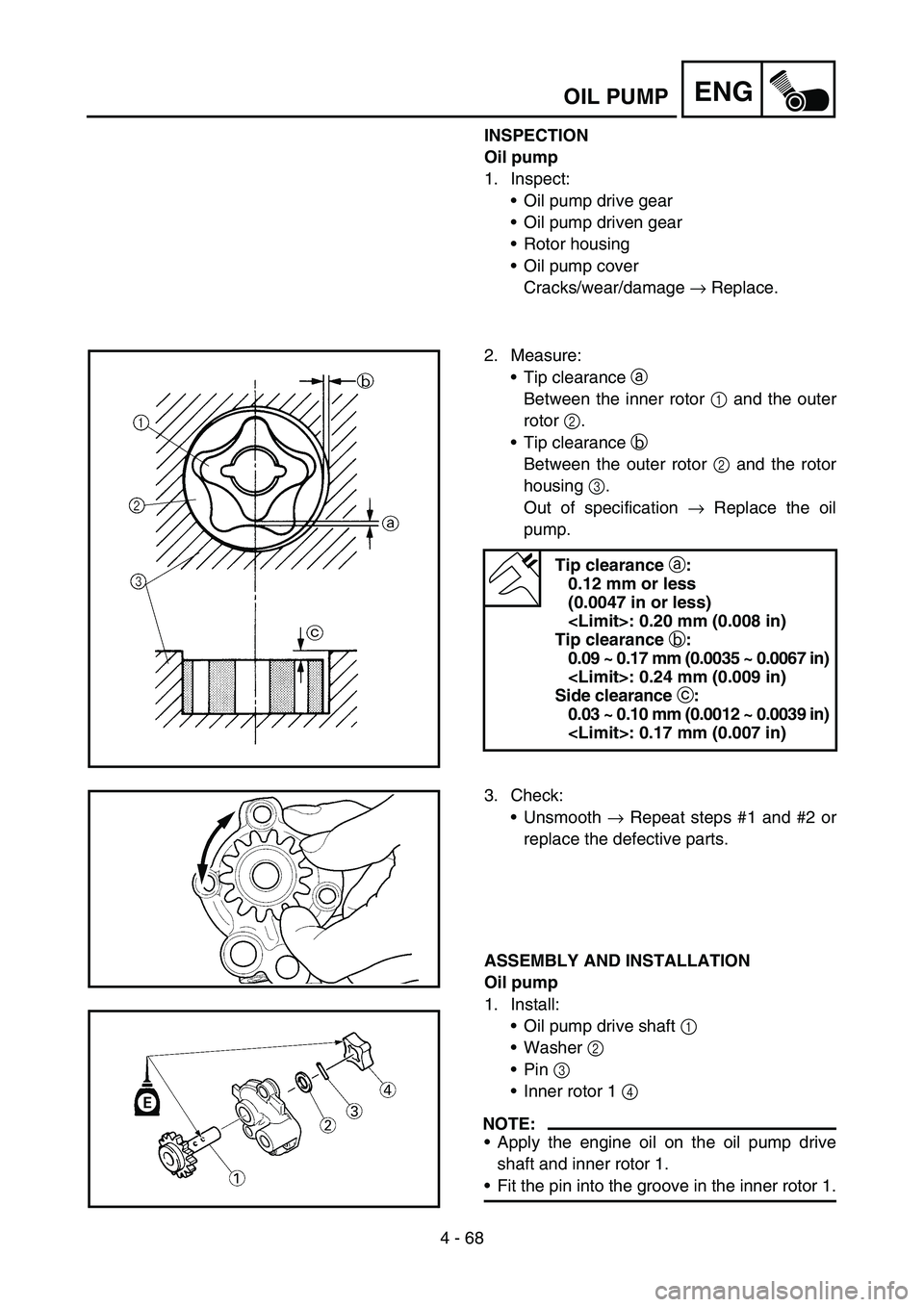
4 - 68
ENGOIL PUMP
INSPECTION
Oil pump
1. Inspect:
Oil pump drive gear
Oil pump driven gear
Rotor housing
Oil pump cover
Cracks/wear/damage → Replace.
2. Measure:
Tip clearance a
Between the inner rotor 1 and the outer
rotor 2.
Tip clearance b
Between the outer rotor 2 and the rotor
housing 3.
Out of specification → Replace the oil
pump.
Tip clearance
a:
0.12 mm or less
(0.0047 in or less)
Tip clearance
b:
0.09 ~ 0.17 mm (0.0035 ~ 0.0067 in)
Side clearance
c:
0.03 ~ 0.10 mm (0.0012 ~ 0.0039 in)
3. Check:
Unsmooth → Repeat steps #1 and #2 or
replace the defective parts.
ASSEMBLY AND INSTALLATION
Oil pump
1. Install:
Oil pump drive shaft 1
Washer 2
Pin 3
Inner rotor 1 4
NOTE:
Apply the engine oil on the oil pump drive
shaft and inner rotor 1.
Fit the pin into the groove in the inner rotor 1.
Page 418 of 650
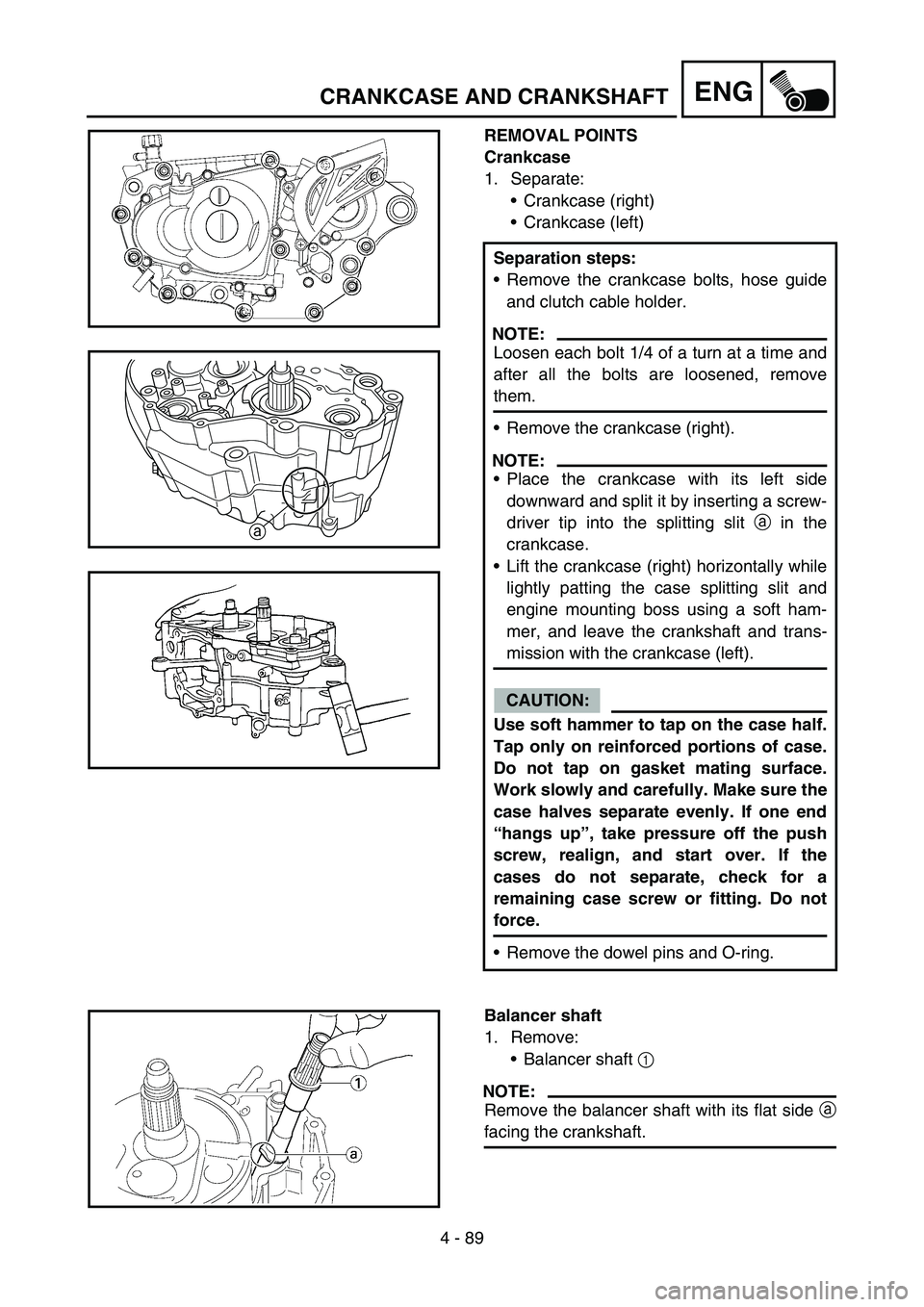
4 - 89
ENGCRANKCASE AND CRANKSHAFT
REMOVAL POINTS
Crankcase
1. Separate:
Crankcase (right)
Crankcase (left)
Separation steps:
Remove the crankcase bolts, hose guide
and clutch cable holder.
NOTE:
Loosen each bolt 1/4 of a turn at a time and
after all the bolts are loosened, remove
them.
Remove the crankcase (right).
NOTE:
Place the crankcase with its left side
downward and split it by inserting a screw-
driver tip into the splitting slit a in the
crankcase.
Lift the crankcase (right) horizontally while
lightly patting the case splitting slit and
engine mounting boss using a soft ham-
mer, and leave the crankshaft and trans-
mission with the crankcase (left).
CAUTION:
Use soft hammer to tap on the case half.
Tap only on reinforced portions of case.
Do not tap on gasket mating surface.
Work slowly and carefully. Make sure the
case halves separate evenly. If one end
“hangs up”, take pressure off the push
screw, realign, and start over. If the
cases do not separate, check for a
remaining case screw or fitting. Do not
force.
Remove the dowel pins and O-ring.
a
Balancer shaft
1. Remove:
Balancer shaft 1
NOTE:
Remove the balancer shaft with its flat side a
facing the crankshaft.
Page 428 of 650
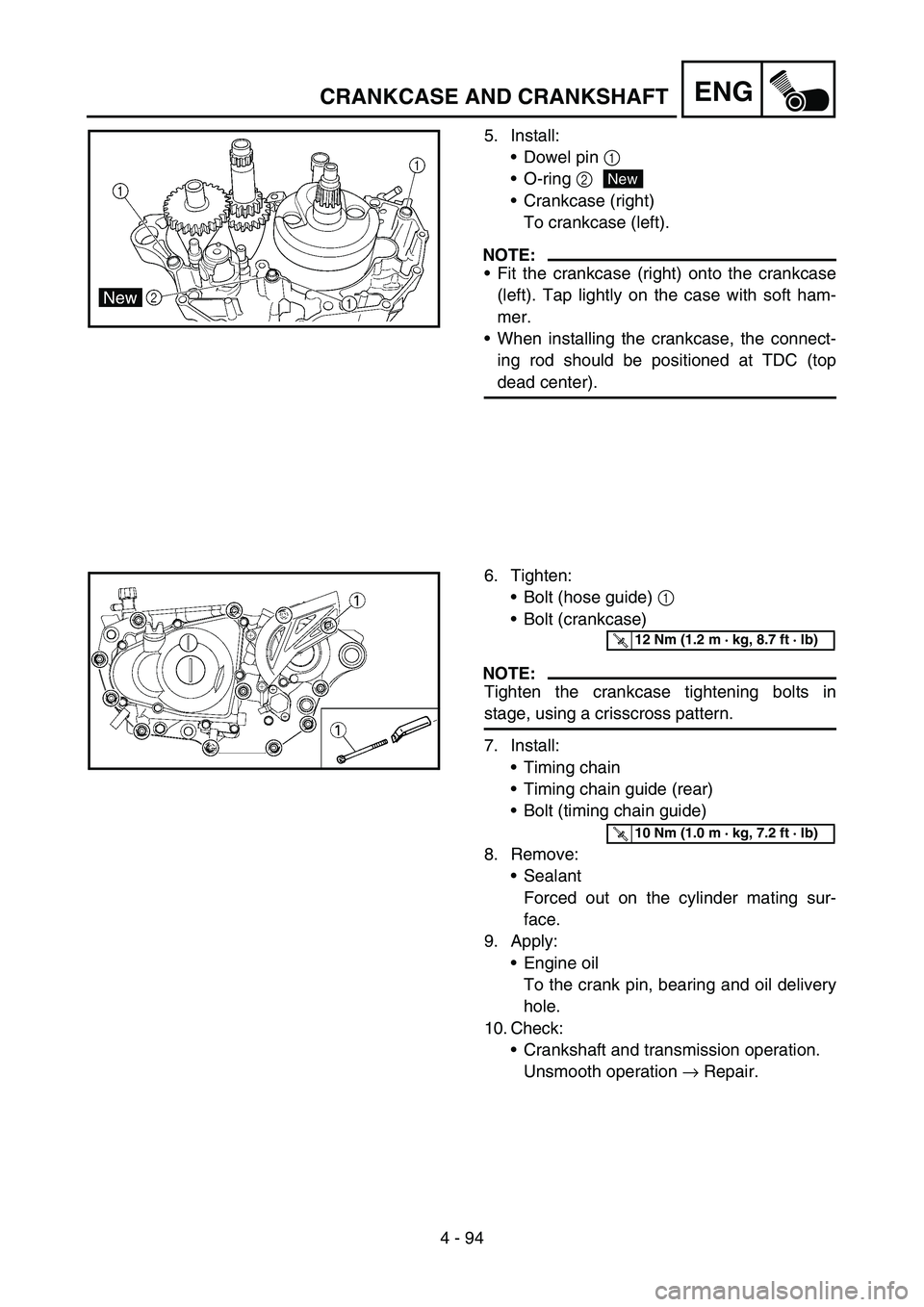
4 - 94
ENGCRANKCASE AND CRANKSHAFT
5. Install:
Dowel pin 1
O-ring 2
Crankcase (right)
To crankcase (left).
NOTE:
Fit the crankcase (right) onto the crankcase
(left). Tap lightly on the case with soft ham-
mer.
When installing the crankcase, the connect-
ing rod should be positioned at TDC (top
dead center).
New
6. Tighten:
Bolt (hose guide) 1
Bolt (crankcase)
NOTE:
Tighten the crankcase tightening bolts in
stage, using a crisscross pattern.
7. Install:
Timing chain
Timing chain guide (rear)
Bolt (timing chain guide)
8. Remove:
Sealant
Forced out on the cylinder mating sur-
face.
9. Apply:
Engine oil
To the crank pin, bearing and oil delivery
hole.
10. Check:
Crankshaft and transmission operation.
Unsmooth operation → Repair.
T R..12 Nm (1.2 m · kg, 8.7 ft · lb)
T R..10 Nm (1.0 m · kg, 7.2 ft · lb)
Page 438 of 650
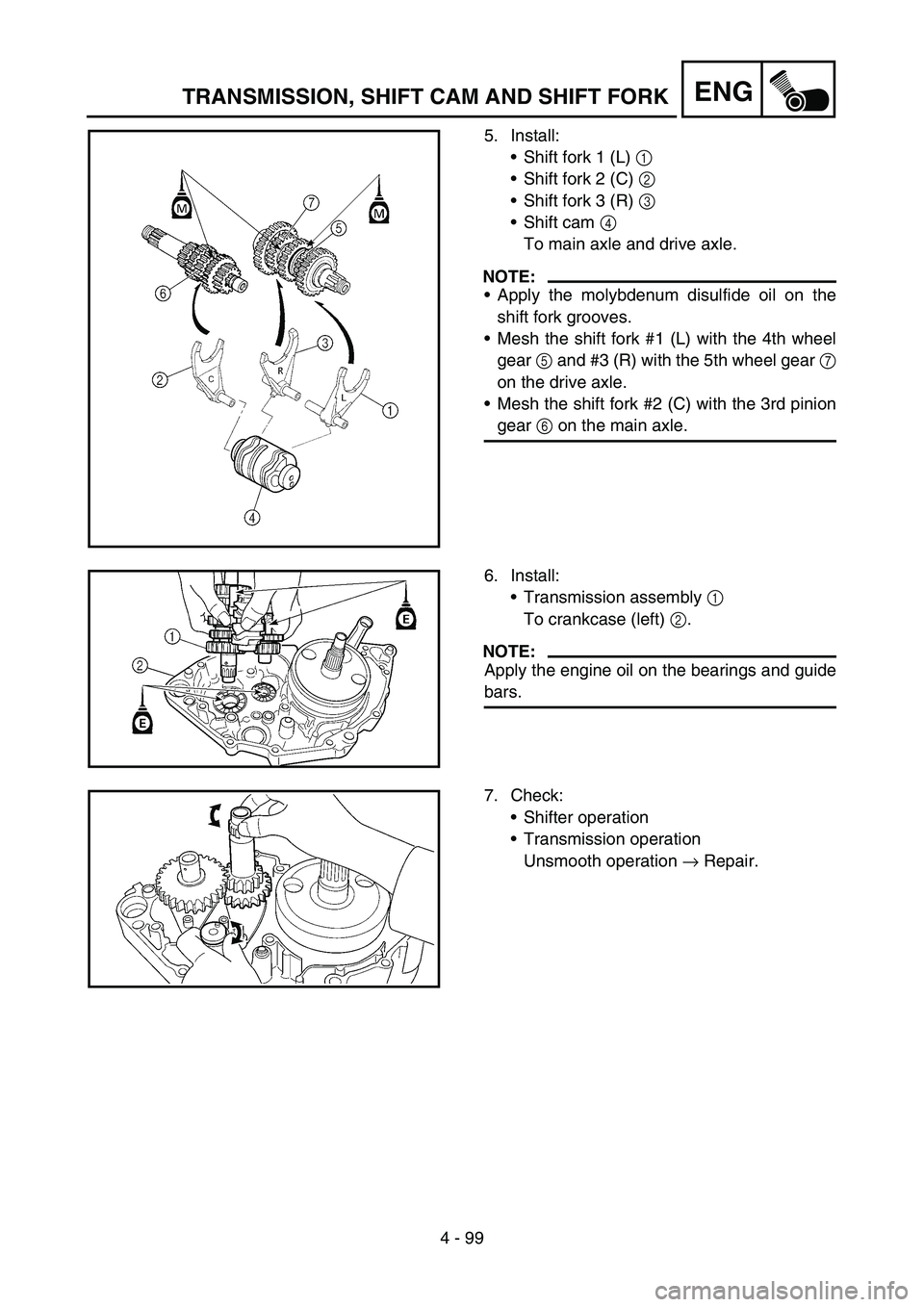
4 - 99
ENGTRANSMISSION, SHIFT CAM AND SHIFT FORK
5. Install:
Shift fork 1 (L) 1
Shift fork 2 (C) 2
Shift fork 3 (R) 3
Shift cam 4
To main axle and drive axle.
NOTE:
Apply the molybdenum disulfide oil on the
shift fork grooves.
Mesh the shift fork #1 (L) with the 4th wheel
gear 5 and #3 (R) with the 5th wheel gear 7
on the drive axle.
Mesh the shift fork #2 (C) with the 3rd pinion
gear 6 on the main axle.
6. Install:
Transmission assembly 1
To crankcase (left) 2.
NOTE:
Apply the engine oil on the bearings and guide
bars.
7. Check:
Shifter operation
Transmission operation
Unsmooth operation → Repair.
Page 581 of 650
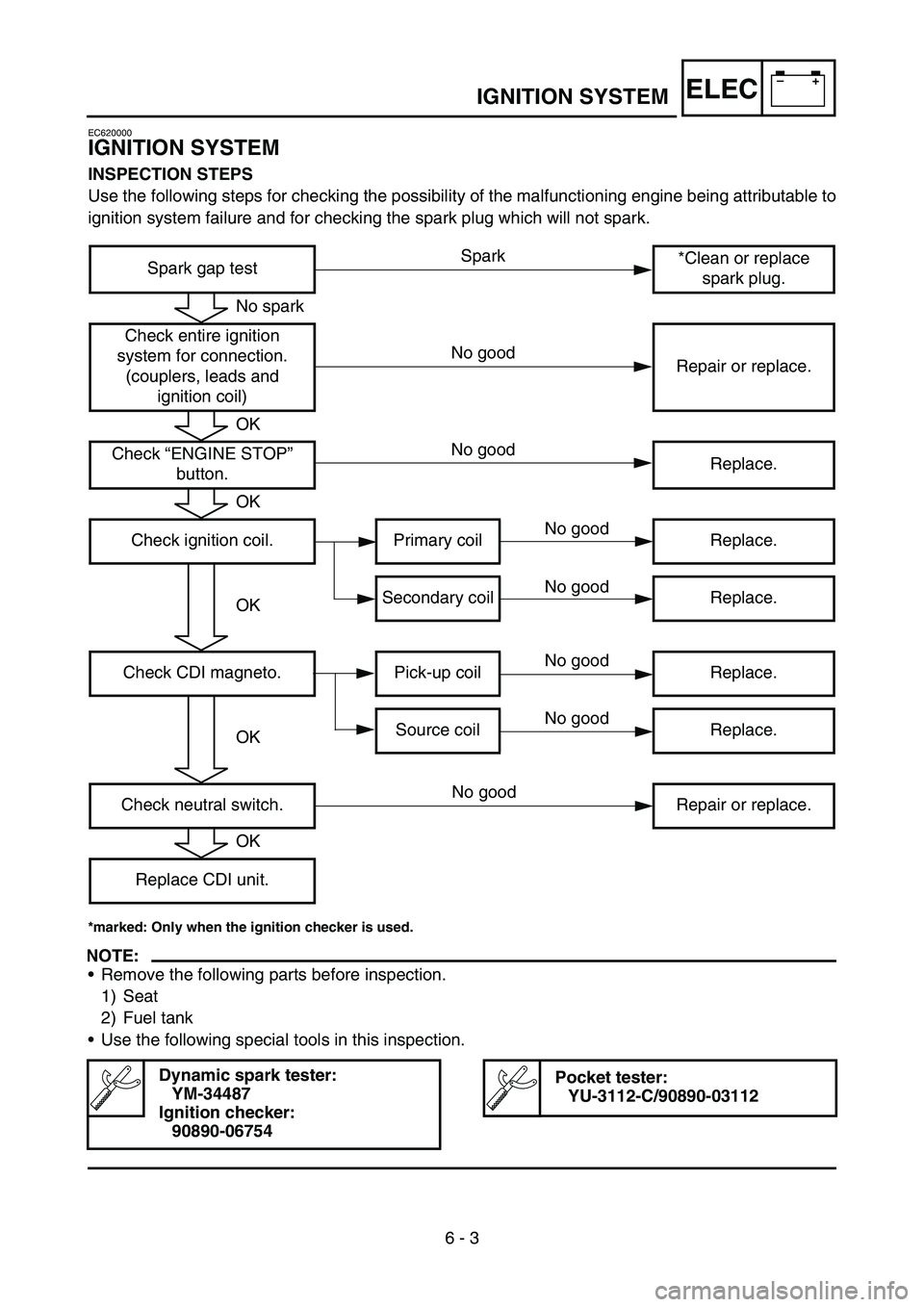
–+ELEC
6 - 3
IGNITION SYSTEM
EC620000
IGNITION SYSTEM
INSPECTION STEPS
Use the following steps for checking the possibility of the malfunctioning engine being attributable to
ignition system failure and for checking the spark plug which will not spark.
*marked: Only when the ignition checker is used.
NOTE:
•Remove the following parts before inspection.
1) Seat
2) Fuel tank
•Use the following special tools in this inspection.
Dynamic spark tester:
YM-34487
Ignition checker:
90890-06754Pocket tester:
YU-3112-C/90890-03112
Spark gap test*Clean or replace
spark plug.
Check entire ignition
system for connection.
(couplers, leads and
ignition coil)Repair or replace.
Check “ENGINE STOP”
button.Replace.
Check ignition coil. Primary coil Replace.
Secondary coil Replace.
Check CDI magneto. Pick-up coil Replace.
Source coil Replace.
Check neutral switch. Repair or replace.
Replace CDI unit.
No spark
OK
OK
OK
OK
OK
Spark
No good
No good
No good
No good
No good
No good
No good
Page 584 of 650
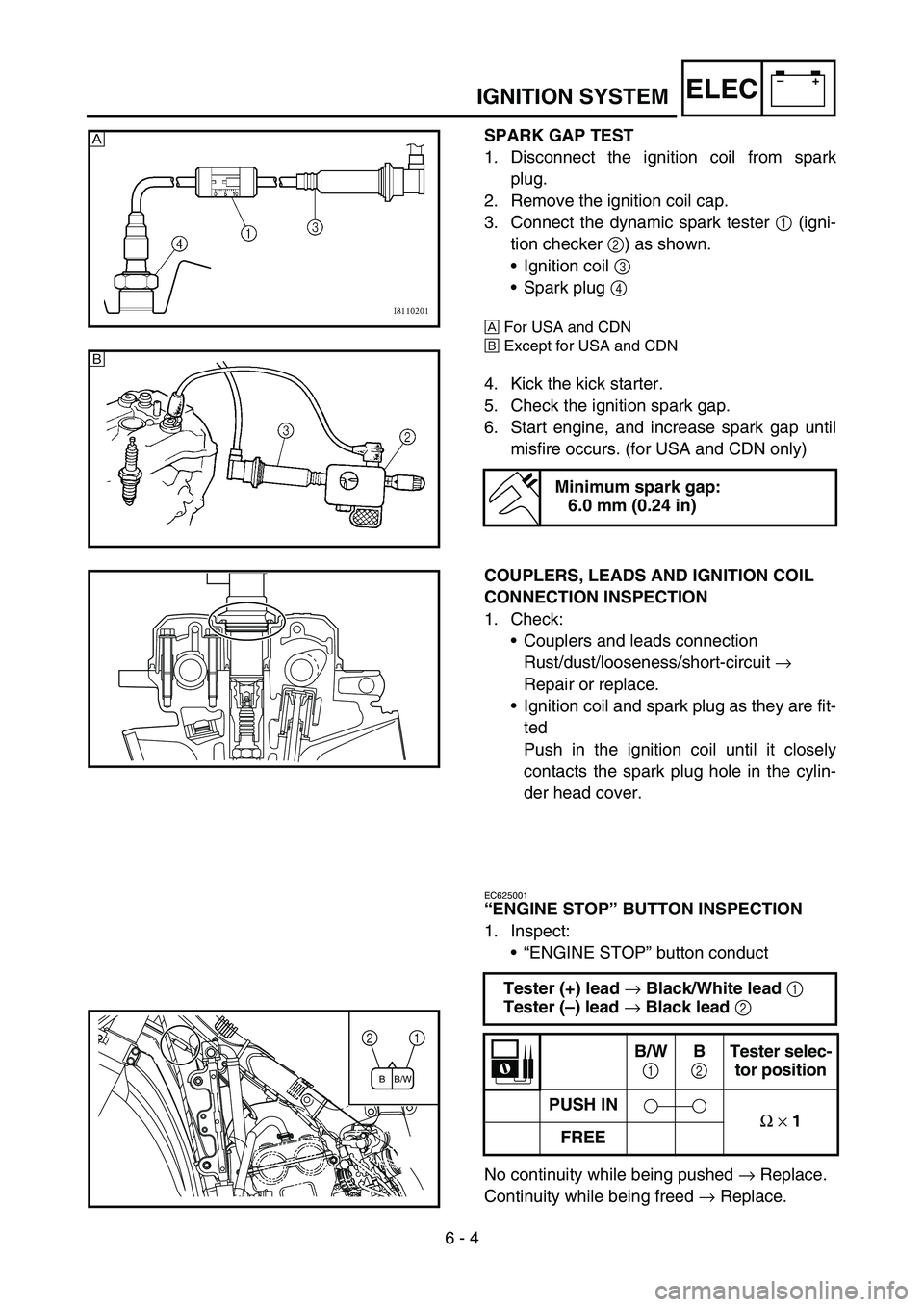
6 - 4
–+ELECIGNITION SYSTEM
SPARK GAP TEST
1. Disconnect the ignition coil from spark
plug.
2. Remove the ignition coil cap.
3. Connect the dynamic spark tester 1 (igni-
tion checker 2) as shown.
•Ignition coil 3
•Spark plug 4
ÈFor USA and CDN
ÉExcept for USA and CDN
4. Kick the kick starter.
5. Check the ignition spark gap.
6. Start engine, and increase spark gap until
misfire occurs. (for USA and CDN only)
Minimum spark gap:
6.0 mm (0.24 in)
È
É
COUPLERS, LEADS AND IGNITION COIL
CONNECTION INSPECTION
1. Check:
•Couplers and leads connection
Rust/dust/looseness/short-circuit →
Repair or replace.
•Ignition coil and spark plug as they are fit-
ted
Push in the ignition coil until it closely
contacts the spark plug hole in the cylin-
der head cover.
EC625001
“ENGINE STOP” BUTTON INSPECTION
1. Inspect:
•“ENGINE STOP” button conduct
No continuity while being pushed → Replace.
Continuity while being freed → Replace. Tester (+) lead
→ Black/White lead
1
Tester (–) lead
→ Black lead
2
B/W
1 B
2 Tester selec-
tor position
PUSH IN
Ω
× 1
FREE1 2
B/W B
Page 594 of 650
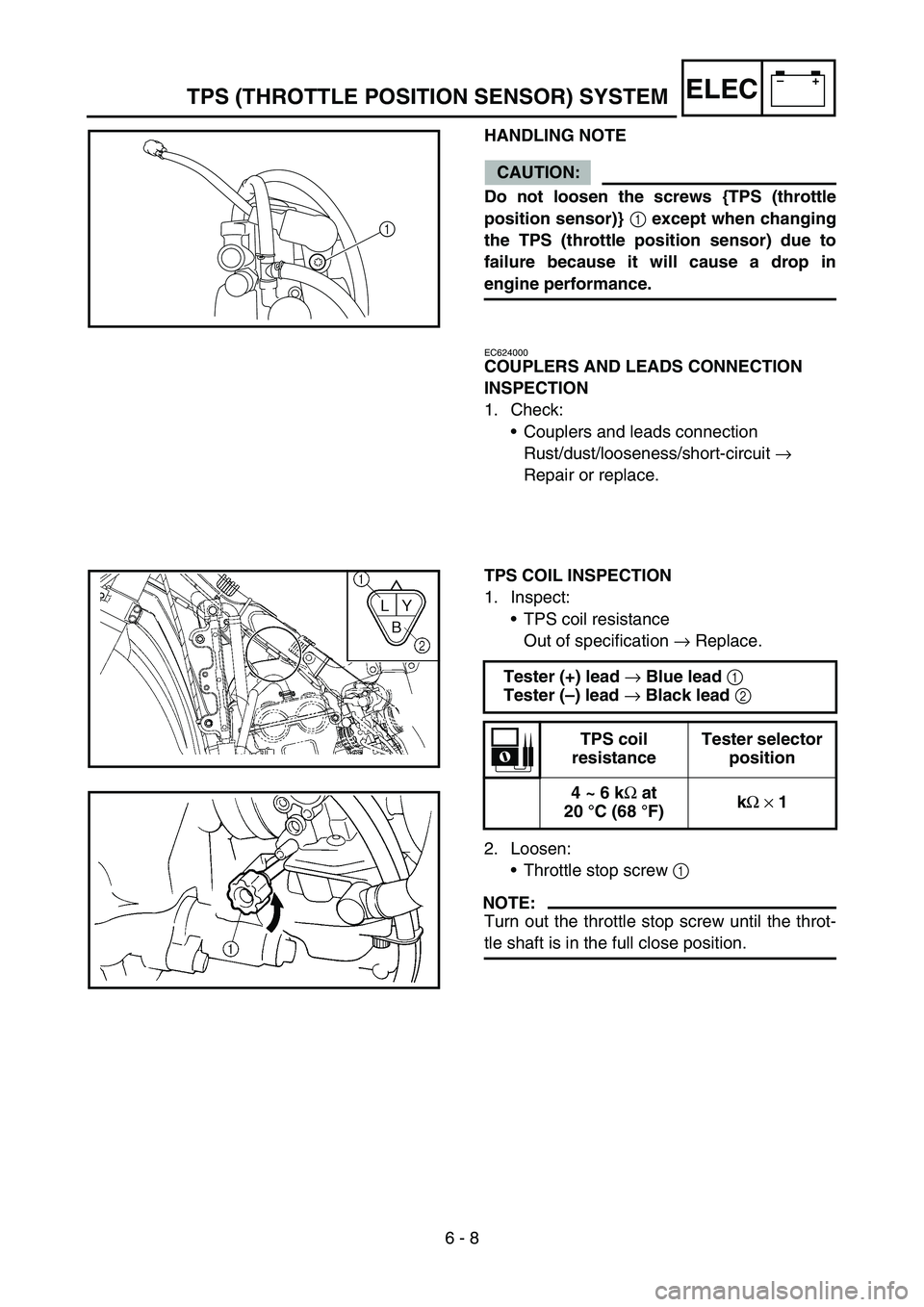
6 - 8
–+ELECTPS (THROTTLE POSITION SENSOR) SYSTEM
HANDLING NOTE
CAUTION:
Do not loosen the screws {TPS (throttle
position sensor)}
1 except when changing
the TPS (throttle position sensor) due to
failure because it will cause a drop in
engine performance.
1
EC624000
COUPLERS AND LEADS CONNECTION
INSPECTION
1. Check:
•Couplers and leads connection
Rust/dust/looseness/short-circuit →
Repair or replace.
TPS COIL INSPECTION
1. Inspect:
•TPS coil resistance
Out of specification → Replace.
2. Loosen:
•Throttle stop screw 1
NOTE:
Turn out the throttle stop screw until the throt-
tle shaft is in the full close position.Tester (+) lead
→ Blue lead
1
Tester (–) lead
→ Black lead
2
TPS coil
resistanceTester selector
position
4 ~ 6 kΩ at
20 °C (68 °F)kΩ × 1