YAMAHA YZ450F 2013 Owners Manual
Manufacturer: YAMAHA, Model Year: 2013, Model line: YZ450F, Model: YAMAHA YZ450F 2013Pages: 228, PDF Size: 11.41 MB
Page 181 of 228
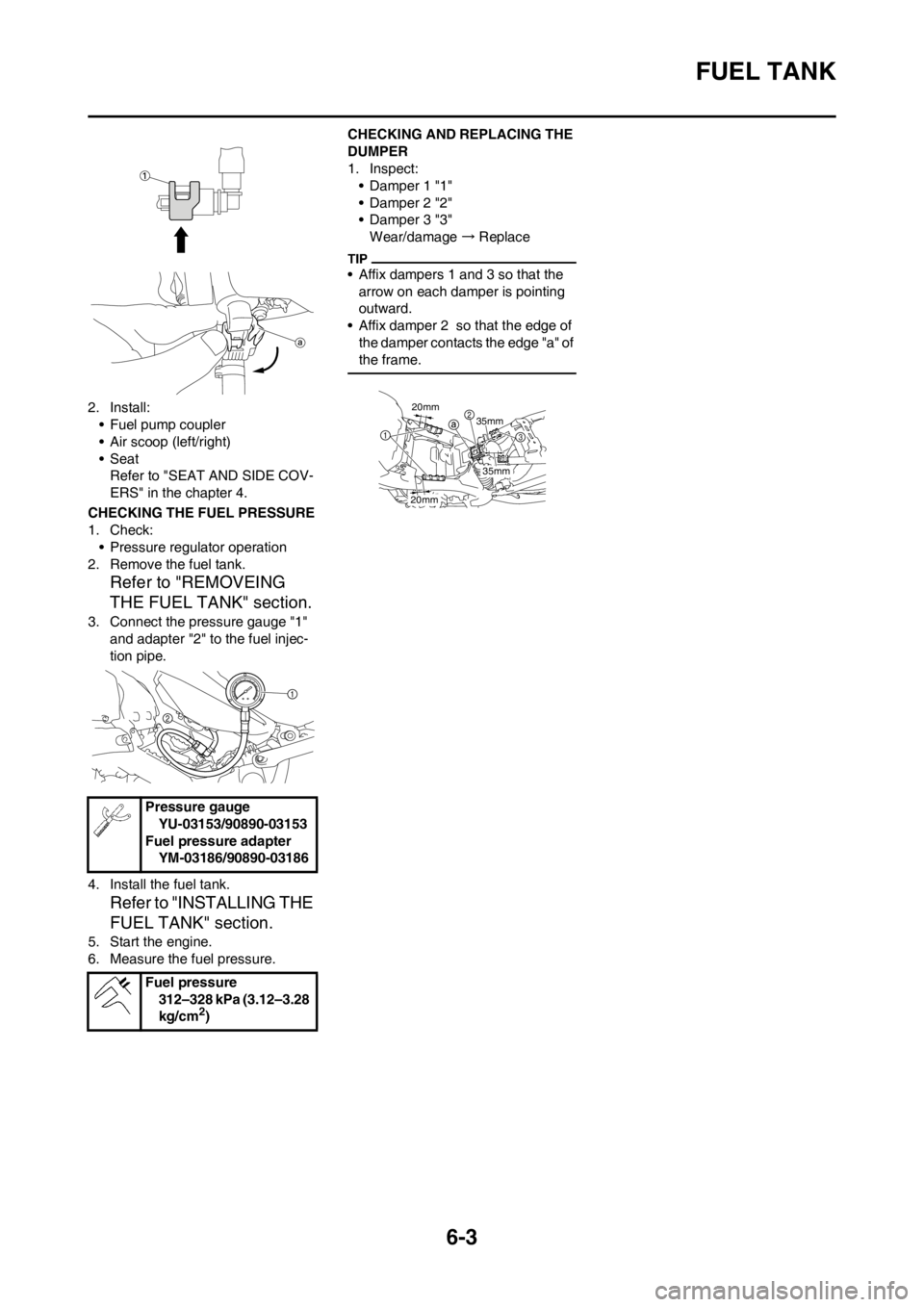
6-3
FUEL TANK
2. Install:
• Fuel pump coupler
• Air scoop (left/right)
• Seat
Refer to "SEAT AND SIDE COV-
ERS" in the chapter 4.
CHECKING THE FUEL PRESSURE
1. Check:
• Pressure regulator operation
2. Remove the fuel tank.
Refer to "REMOVEING
THE FUEL TANK" section.
3. Connect the pressure gauge "1"
and adapter "2" to the fuel injec-
tion pipe.
4. Install the fuel tank.
Refer to "INSTALLING THE
FUEL TANK" section.
5. Start the engine.
6. Measure the fuel pressure.CHECKING AND REPLACING THE
DUMPER
1. Inspect:
• Damper 1 "1"
• Damper 2 "2"
• Damper 3 "3"
Wear/damage → Replace
• Affix dampers 1 and 3 so that the
arrow on each damper is pointing
outward.
• Affix damper 2 so that the edge of
the damper contacts the edge "a" of
the frame.
Pressure gauge
YU-03153/90890-03153
Fuel pressure adapter
YM-03186/90890-03186
Fuel pressure
312–328 kPa (3.12–3.28
kg/cm
2)
20mm
20mm
35mm 35mm
Page 182 of 228
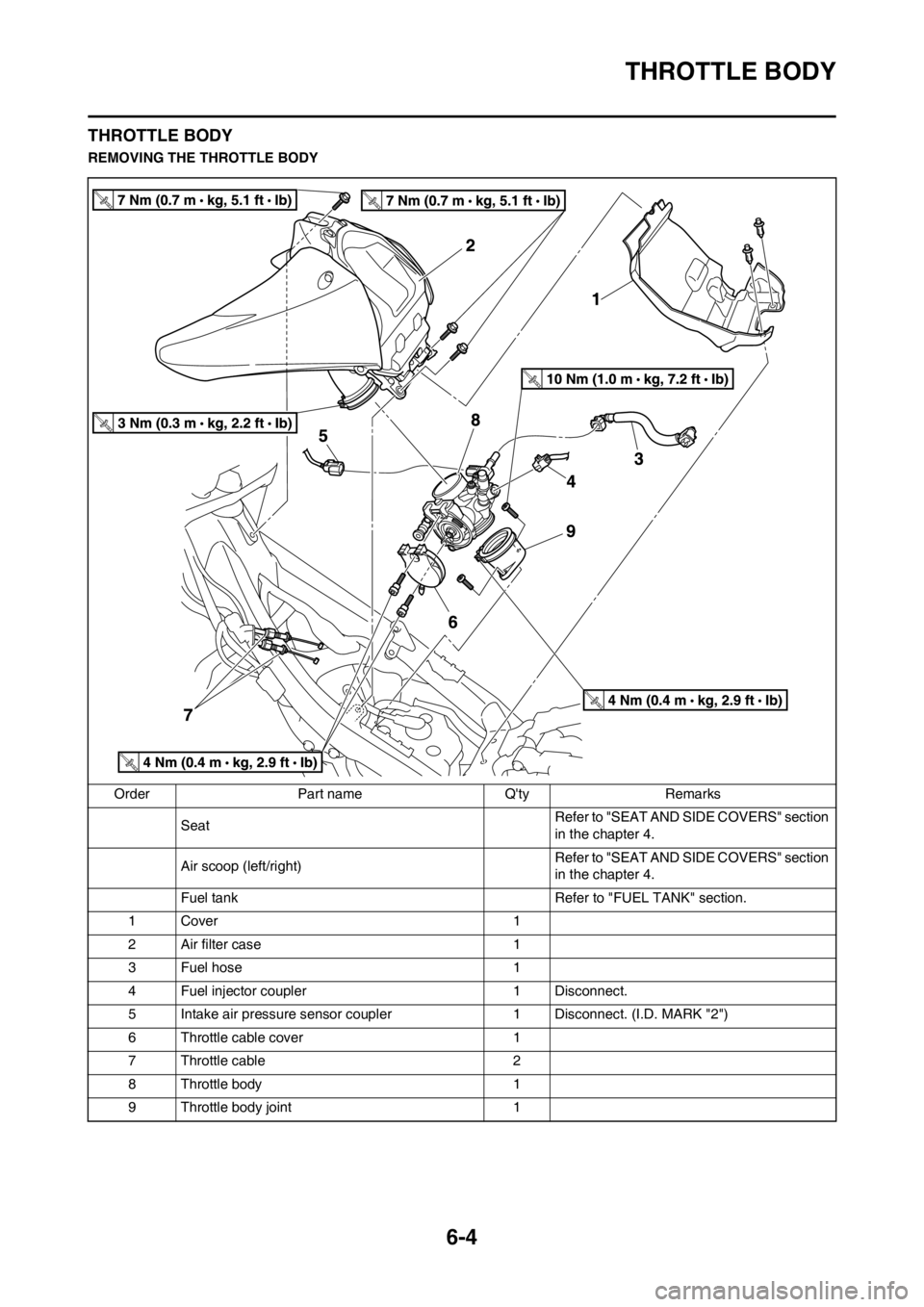
6-4
THROTTLE BODY
THROTTLE BODY
REMOVING THE THROTTLE BODY
Order Part name Q'ty Remarks
SeatRefer to "SEAT AND SIDE COVERS" section
in the chapter 4.
Air scoop (left/right)Refer to "SEAT AND SIDE COVERS" section
in the chapter 4.
Fuel tank Refer to "FUEL TANK" section.
1 Cover 1
2 Air filter case 1
3 Fuel hose 1
4 Fuel injector coupler 1 Disconnect.
5 Intake air pressure sensor coupler 1 Disconnect. (I.D. MARK "2")
6 Throttle cable cover 1
7 Throttle cable 2
8 Throttle body 1
9 Throttle body joint 1
Page 183 of 228
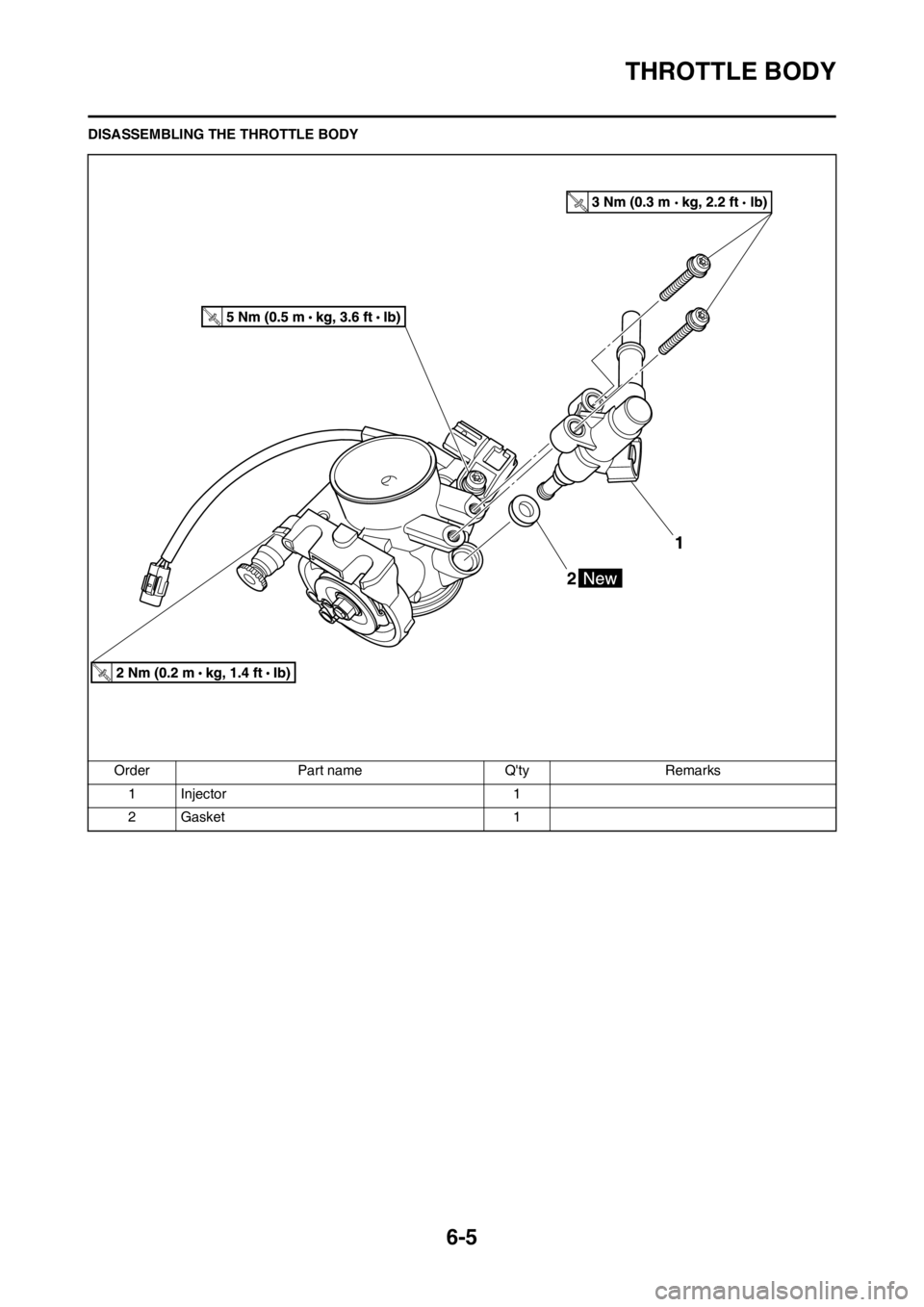
6-5
THROTTLE BODY
DISASSEMBLING THE THROTTLE BODY
Order Part name Q'ty Remarks
1Injector 1
2 Gasket 1
Page 184 of 228
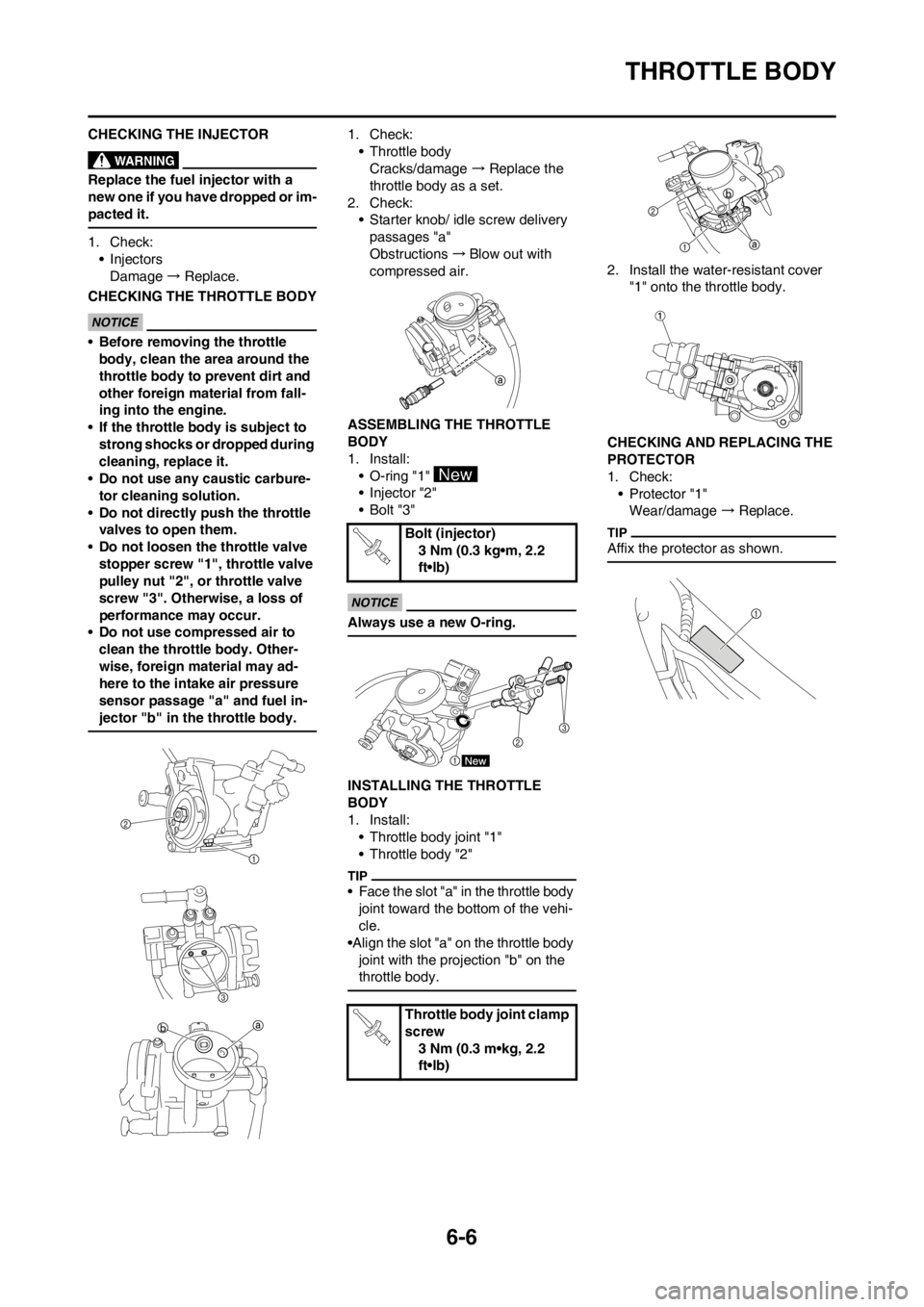
6-6
THROTTLE BODY
CHECKING THE INJECTOR
Replace the fuel injector with a
new one if you have dropped or im-
pacted it.
1. Check:
• Injectors
Damage → Replace.
CHECKING THE THROTTLE BODY
•Before removing the throttle
body, clean the area around the
throttle body to prevent dirt and
other foreign material from fall-
ing into the engine.
•If the throttle body is subject to
strong shocks or dropped during
cleaning, replace it.
•Do not use any caustic carbure-
tor cleaning solution.
•Do not directly push the throttle
valves to open them.
•Do not loosen the throttle valve
stopper screw "1", throttle valve
pulley nut "2", or throttle valve
screw "3". Otherwise, a loss of
performance may occur.
•Do not use compressed air to
clean the throttle body. Other-
wise, foreign material may ad-
here to the intake air pressure
sensor passage "a" and fuel in-
jector "b" in the throttle body.
1. Check:
• Throttle body
Cracks/damage → Replace the
throttle body as a set.
2. Check:
• Starter knob/ idle screw delivery
passages "a"
Obstructions →Blow out with
compressed air.
ASSEMBLING THE THROTTLE
BODY
1. Install:
• O-ring "1"
• Injector "2"
•Bolt "3"
Always use a new O-ring.
INSTALLING THE THROTTLE
BODY
1. Install:
• Throttle body joint "1"
• Throttle body "2"
• Face the slot "a" in the throttle body
joint toward the bottom of the vehi-
cle.
•Align the slot "a" on the throttle body
joint with the projection "b" on the
throttle body.
2. Install the water-resistant cover
"1" onto the throttle body.
CHECKING AND REPLACING THE
PROTECTOR
1. Check:
• Protector "1"
Wear/damage → Replace.
Affix the protector as shown.Bolt (injector)
3 Nm (0.3 kg•m, 2.2
ft•lb)
Throttle body joint clamp
screw
3 Nm (0.3 m•kg, 2.2
ft•lb)
Page 185 of 228
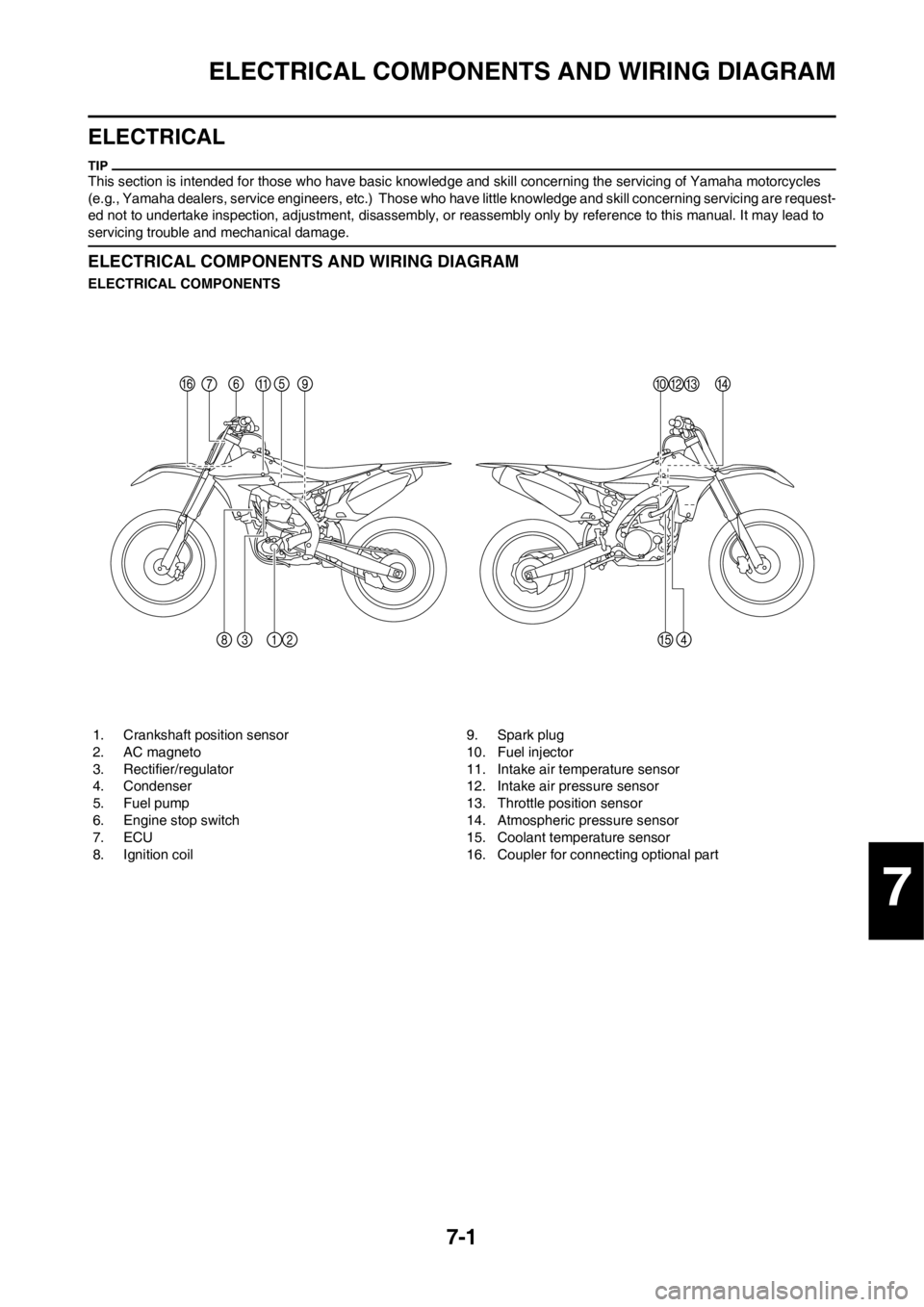
7-1
ELECTRICAL COMPONENTS AND WIRING DIAGRAM
ELECTRICAL
This section is intended for those who have basic knowledge and skill concerning the servicing of Yamaha motorcycles
(e.g., Yamaha dealers, service engineers, etc.) Those who have little knowledge and skill concerning servicing are request-
ed not to undertake inspection, adjustment, disassembly, or reassembly only by reference to this manual. It may lead to
servicing trouble and mechanical damage.
ELECTRICAL COMPONENTS AND WIRING DIAGRAM
ELECTRICAL COMPONENTS
1. Crankshaft position sensor
2. AC magneto
3. Rectifier/regulator
4. Condenser
5. Fuel pump
6. Engine stop switch
7. ECU
8. Ignition coil9. Spark plug
10. Fuel injector
11. Intake air temperature sensor
12. Intake air pressure sensor
13. Throttle position sensor
14. Atmospheric pressure sensor
15. Coolant temperature sensor
16. Coupler for connecting optional part
7
Page 186 of 228
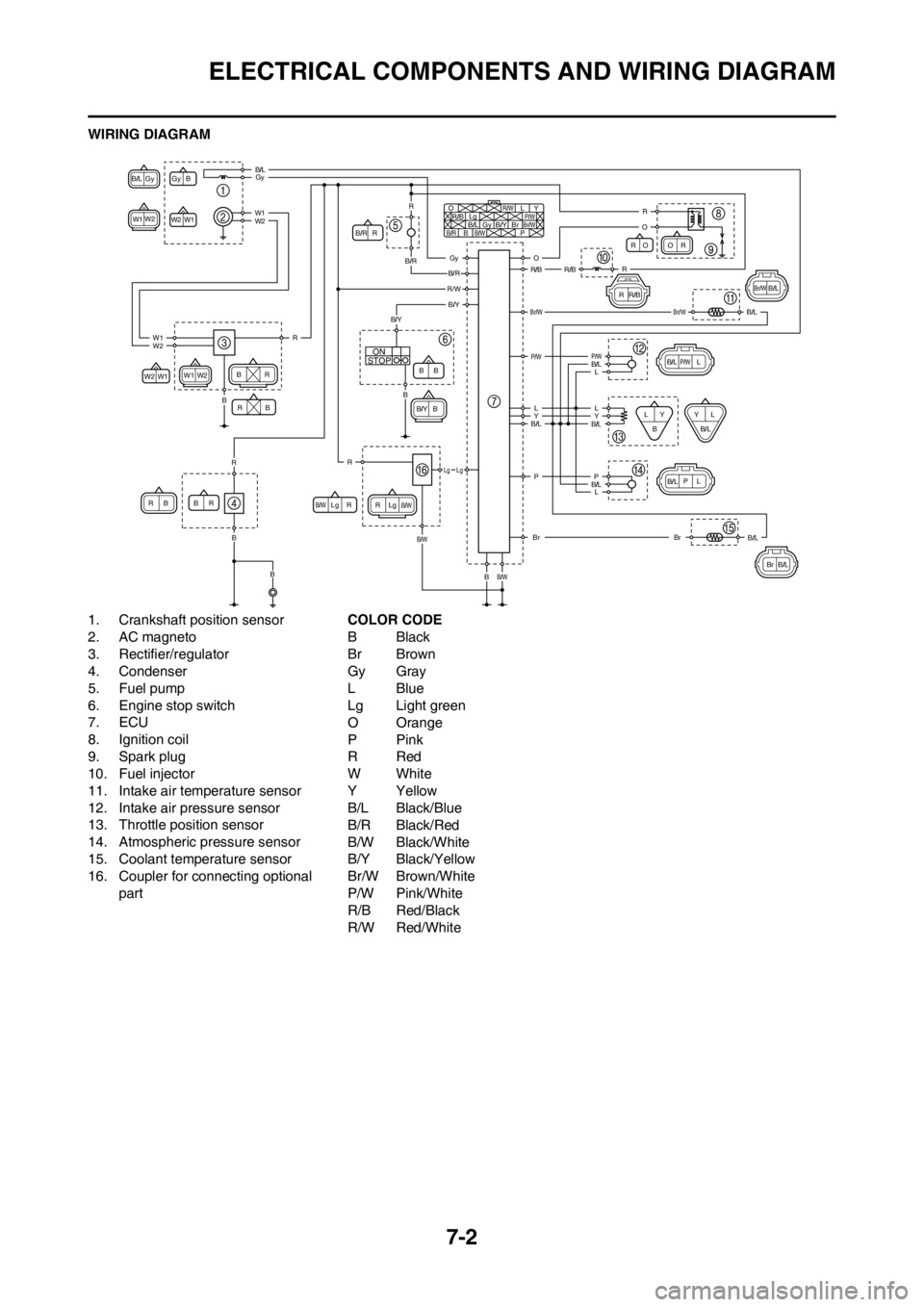
7-2
ELECTRICAL COMPONENTS AND WIRING DIAGRAM
WIRING DIAGRAM
1. Crankshaft position sensor
2. AC magneto
3. Rectifier/regulator
4. Condenser
5. Fuel pump
6. Engine stop switch
7. ECU
8. Ignition coil
9. Spark plug
10. Fuel injector
11. Intake air temperature sensor
12. Intake air pressure sensor
13. Throttle position sensor
14. Atmospheric pressure sensor
15. Coolant temperature sensor
16. Coupler for connecting optional part COLOR CODE
BBlack
Br Brown
Gy Gray
LBlue
Lg Light green
O Orange
PPink
RRed
WWhite
YYellow
B/L Black/Blue
B/R Black/Red
B/W Black/White
B/Y Black/Yellow
Br/W Brown/White
P/W Pink/White
R/B Red/Black
R/W Red/White
STOPON
Gy
Gy
B
B/L
W1
W2
W2 O
R/B
R RR
R
R
R R
Lg
Lg Lg L
P/W
P
YB/RB
B B
BB BB
BB/W
B/W B/W Br/WGyB/L
W1 W1
W2 W2 B/Y
B/Y Br
B/R
R/W
OO
R/B RR
R
L
P/W
PYL
L
LY
Br/WB/L
B/L B/L
B
B/L
B/L
Br
W1
Br/W
W2
R
R O
B/L
L
Y
B/L
Br
R
P
Gy
Gy
B/R
B/R
R/WB/Y
B/L
W1
W2
W1 R
R R
B
B/Y
Lg Lg
O
R/B R/B
Br/W
P/W P/W
LL
Y
B/L B/L
B/L
Br
B
B/W
B/W
B
B
B L
B/L P
Page 187 of 228
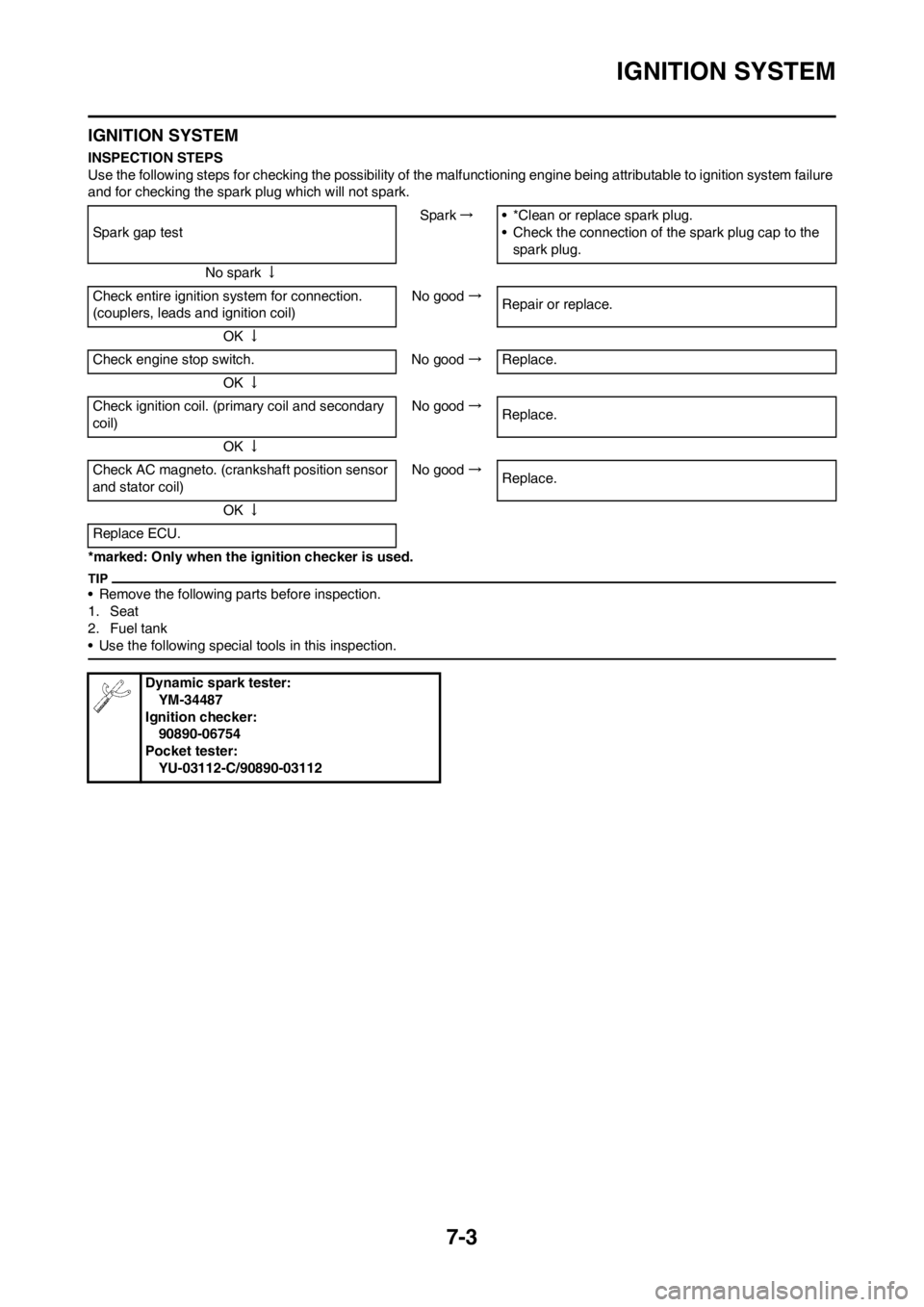
7-3
IGNITION SYSTEM
IGNITION SYSTEM
INSPECTION STEPS
Use the following steps for checking the possibility of the malfunctioning engine being attributable to ignition system failure
and for checking the spark plug which will not spark.
*marked: Only when the ignition checker is used.
• Remove the following parts before inspection.
1. Seat
2. Fuel tank
• Use the following special tools in this inspection.
Spark gap testSpark→• *Clean or replace spark plug.
• Check the connection of the spark plug cap to the
spark plug.
No spark↓
Check entire ignition system for connection.
(couplers, leads and ignition coil)No good→
Repair or replace.
OK↓
Check engine stop switch. No good→Replace.
OK↓
Check ignition coil. (primary coil and secondary
coil)No good→
Replace.
OK↓
Check AC magneto. (crankshaft position sensor
and stator coil)No good→
Replace.
OK↓
Replace ECU.
Dynamic spark tester:
YM-34487
Ignition checker:
90890-06754
Pocket tester:
YU-03112-C/90890-03112
Page 188 of 228
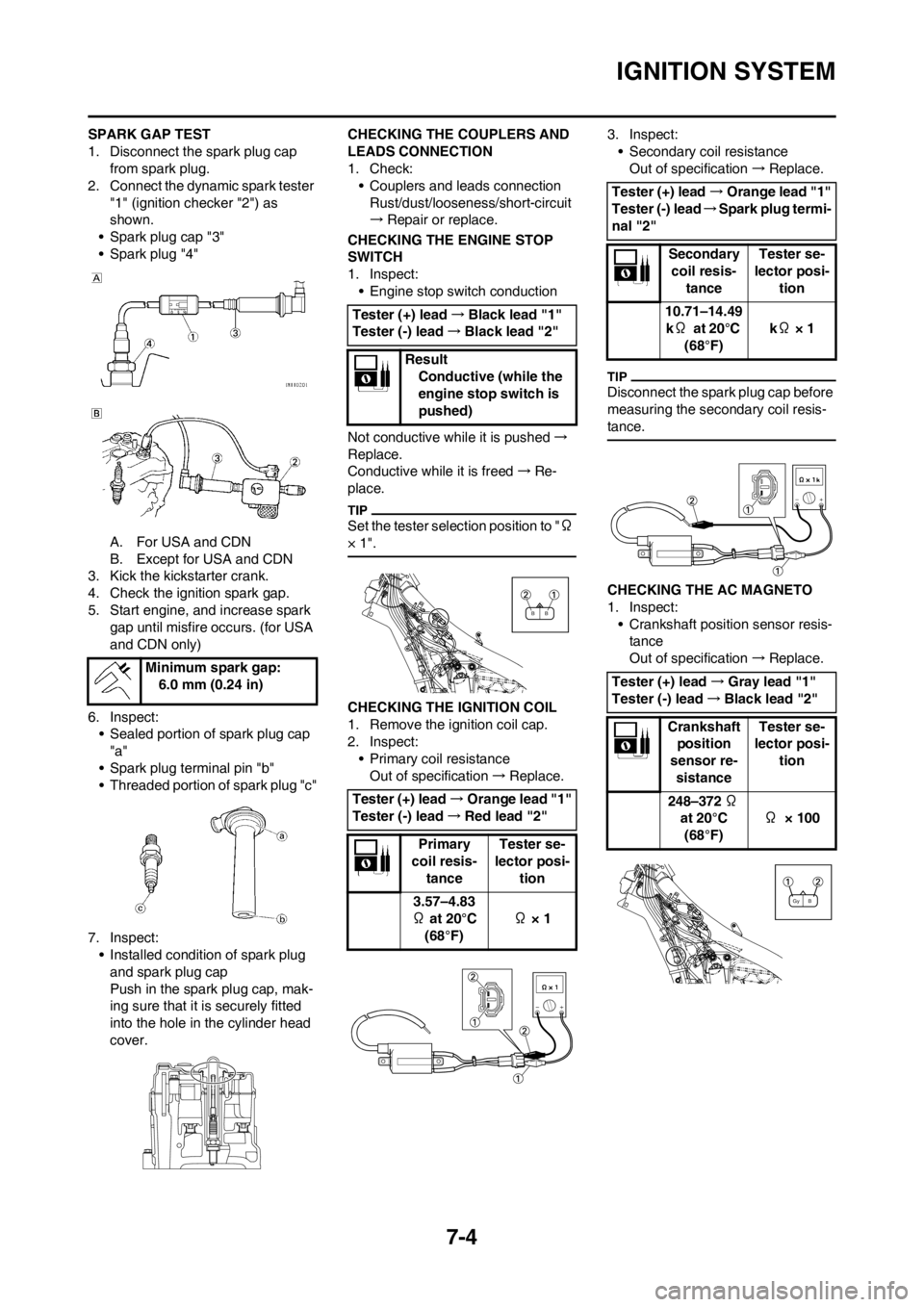
7-4
IGNITION SYSTEM
SPARK GAP TEST
1. Disconnect the spark plug cap
from spark plug.
2. Connect the dynamic spark tester
"1" (ignition checker "2") as
shown.
• Spark plug cap "3"
• Spark plug "4"
A. For USA and CDN
B. Except for USA and CDN
3. Kick the kickstarter crank.
4. Check the ignition spark gap.
5. Start engine, and increase spark
gap until misfire occurs. (for USA
and CDN only)
6. Inspect:
• Sealed portion of spark plug cap
"a"
• Spark plug terminal pin "b"
• Threaded portion of spark plug "c"
7. Inspect:
• Installed condition of spark plug
and spark plug cap
Push in the spark plug cap, mak-
ing sure that it is securely fitted
into the hole in the cylinder head
cover.CHECKING THE COUPLERS AND
LEADS CONNECTION
1. Check:
• Couplers and leads connection
Rust/dust/looseness/short-circuit
→Repair or replace.
CHECKING THE ENGINE STOP
SWITCH
1. Inspect:
• Engine stop switch conduction
Not conductive while it is pushed→
Replace.
Conductive while it is freed→Re-
place.
Set the tester selection position to "Ω
× 1".
CHECKING THE IGNITION COIL
1. Remove the ignition coil cap.
2. Inspect:
• Primary coil resistance
Out of specification→Replace.3. Inspect:
• Secondary coil resistance
Out of specification→Replace.
Disconnect the spark plug cap before
measuring the secondary coil resis-
tance.
CHECKING THE AC MAGNETO
1. Inspect:
• Crankshaft position sensor resis-
tance
Out of specification→Replace.
Minimum spark gap:
6.0 mm (0.24 in)
Tester (+) lead→Black lead "1"
Tester (-) lead→Black lead "2"
Result
Conductive (while the
engine stop switch is
pushed)
Tester (+) lead→Orange lead "1"
Tester (-) lead→Red lead "2"
Primary
coil resis-
tanceTester se-
lector posi-
tion
3.57–4.83
Ω at 20°C
(68°F) Ω × 1
BB
Tester (+) lead→Orange lead "1"
Tester (-) lead→Spark plug termi-
nal "2"
Secondary
coil resis-
tanceTester se-
lector posi-
tion
10.71–14.49
kΩ at 20°C
(68°F) kΩ × 1
Tester (+) lead→Gray lead "1"
Tester (-) lead→Black lead "2"
Crankshaft
position
sensor re-
sistanceTester se-
lector posi-
tion
248–372 Ω
at 20°C
(68°F)Ω × 100
GyB
Page 189 of 228
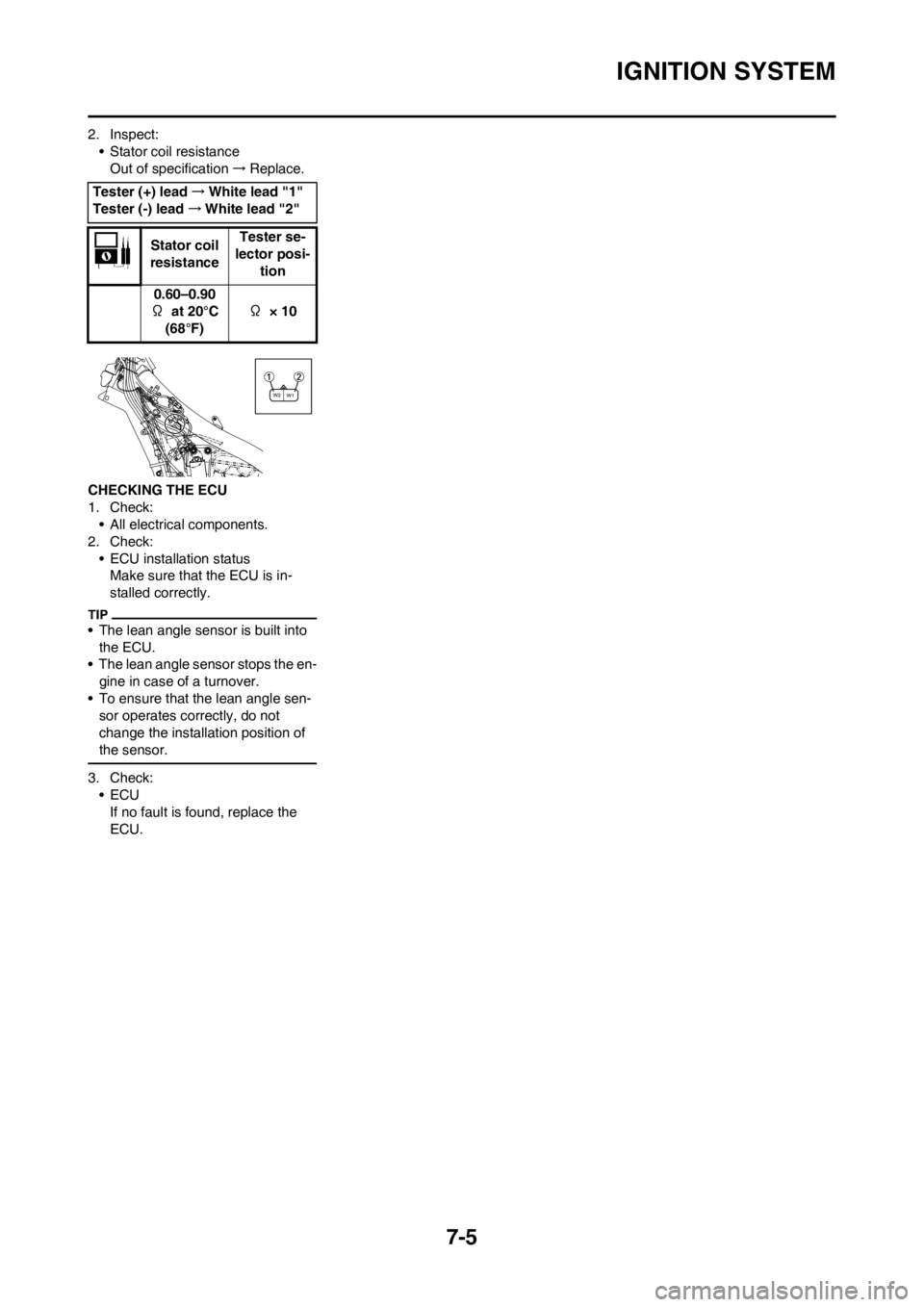
7-5
IGNITION SYSTEM
2. Inspect:
• Stator coil resistance
Out of specification→Replace.
CHECKING THE ECU
1. Check:
• All electrical components.
2. Check:
• ECU installation status
Make sure that the ECU is in-
stalled correctly.
• The lean angle sensor is built into
the ECU.
• The lean angle sensor stops the en-
gine in case of a turnover.
• To ensure that the lean angle sen-
sor operates correctly, do not
change the installation position of
the sensor.
3. Check:
•ECU
If no fault is found, replace the
ECU. Tester (+) lead→White lead "1"
Tester (-) lead→White lead "2"
Stator coil
resistanceTester se-
lector posi-
tion
0.60–0.90
Ω at 20°C
(68°F)Ω × 10
W1 W2
Page 190 of 228
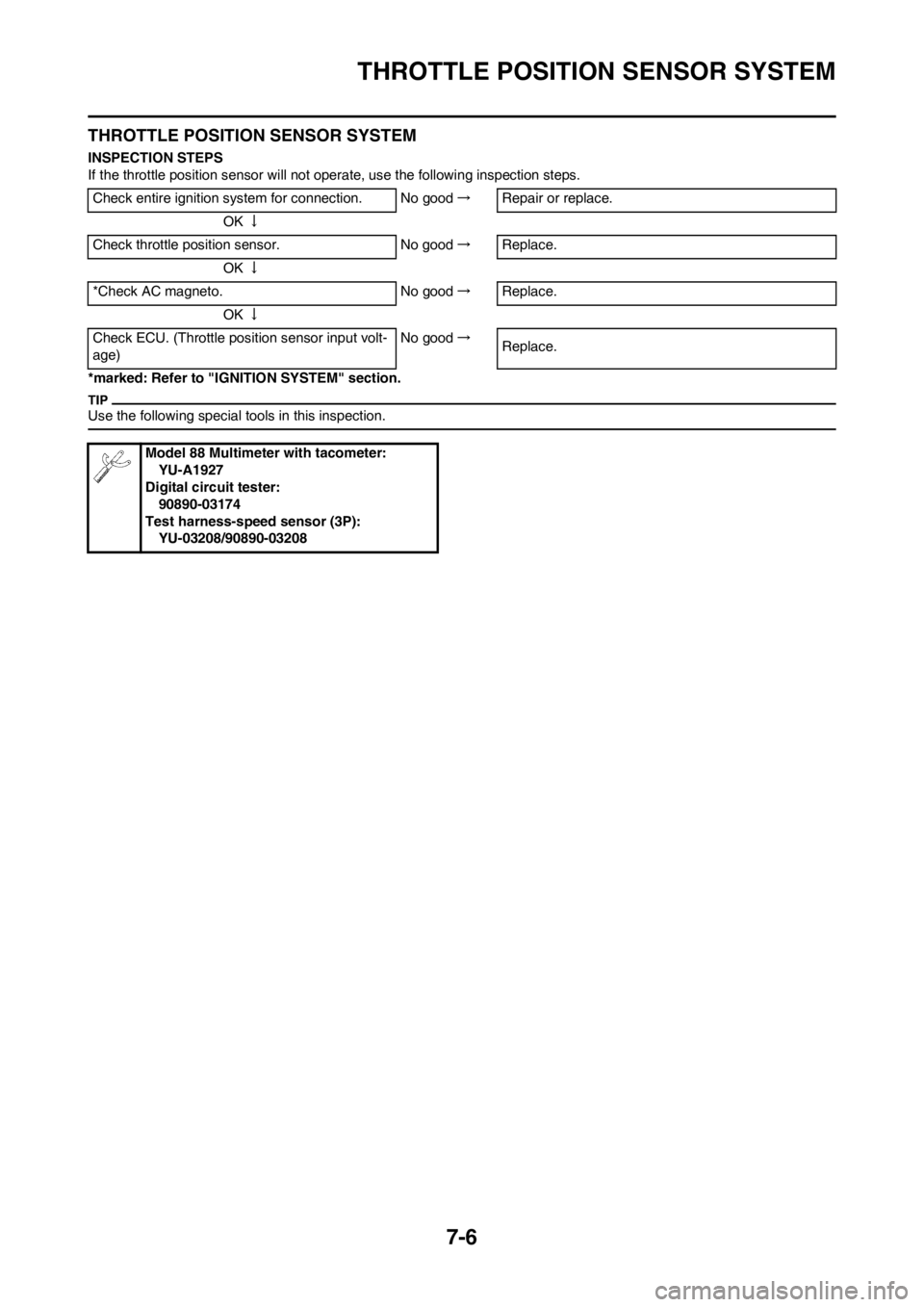
7-6
THROTTLE POSITION SENSOR SYSTEM
THROTTLE POSITION SENSOR SYSTEM
INSPECTION STEPS
If the throttle position sensor will not operate, use the following inspection steps.
*marked: Refer to "IGNITION SYSTEM" section.
Use the following special tools in this inspection.
Check entire ignition system for connection. No good→Repair or replace.
OK↓
Check throttle position sensor. No good→Replace.
OK↓
*Check AC magneto. No good→Replace.
OK↓
Check ECU. (Throttle position sensor input volt-
age)No good→
Replace.
Model 88 Multimeter with tacometer:
YU-A1927
Digital circuit tester:
90890-03174
Test harness-speed sensor (3P):
YU-03208/90890-03208