transmission oil YAMAHA YZ450F 2015 Owners Manual
[x] Cancel search | Manufacturer: YAMAHA, Model Year: 2015, Model line: YZ450F, Model: YAMAHA YZ450F 2015Pages: 360, PDF Size: 10.82 MB
Page 49 of 360
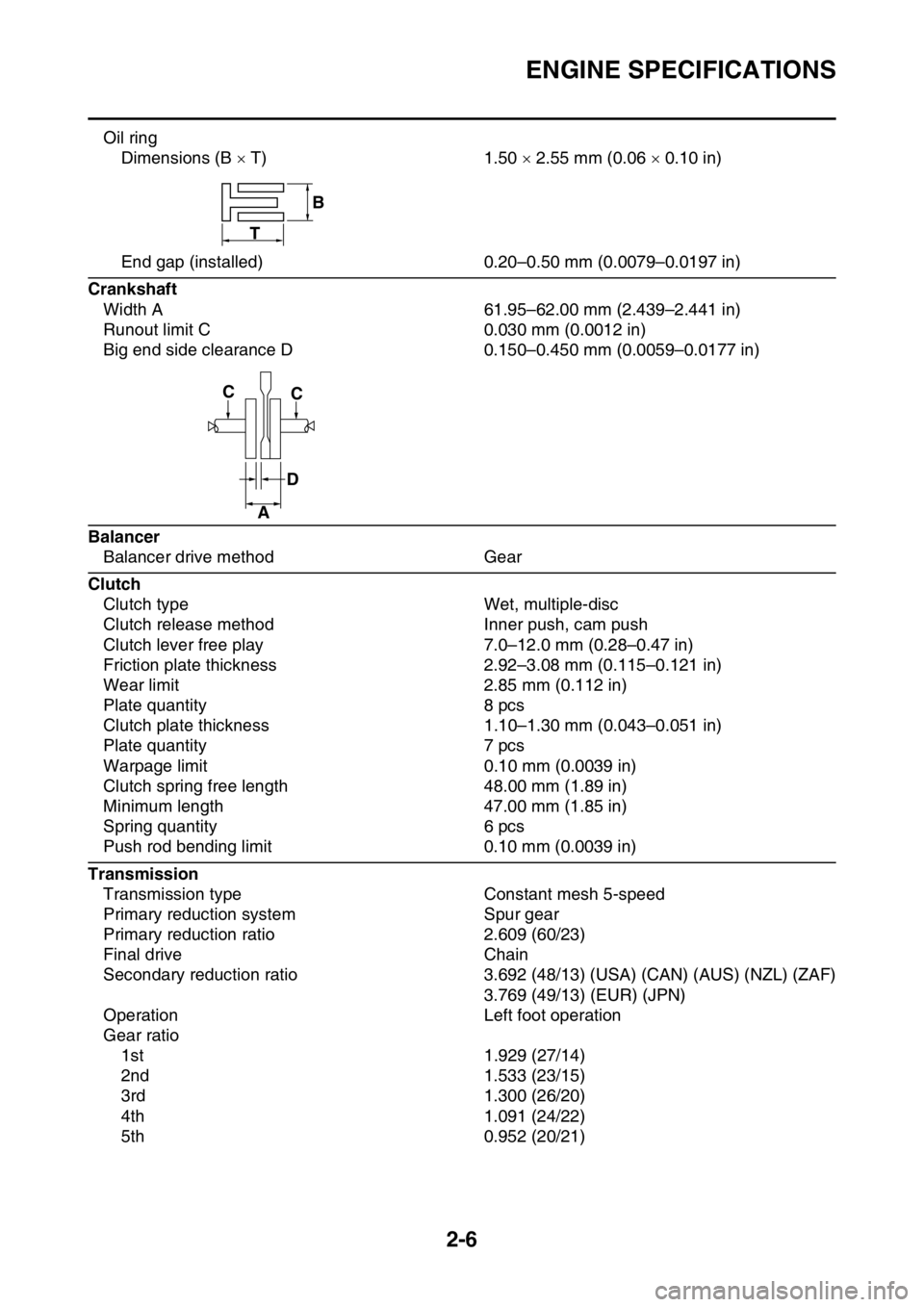
ENGINE SPECIFICATIONS
2-6
Oil ring
Dimensions (B T) 1.50 2.55 mm (0.06 0.10 in)
End gap (installed) 0.20–0.50 mm (0.0079–0.0197 in)
Crankshaft
Width A 61.95–62.00 mm (2.439–2.441 in)
Runout limit C 0.030 mm (0.0012 in)
Big end side clearance D 0.150–0.450 mm (0.0059–0.0177 in)
Balancer
Balancer drive method Gear
Clutch
Clutch type Wet, multiple-disc
Clutch release method Inner push, cam push
Clutch lever free play 7.0–12.0 mm (0.28–0.47 in)
Friction plate thickness 2.92–3.08 mm (0.115–0.121 in)
Wear limit 2.85 mm (0.112 in)
Plate quantity 8 pcs
Clutch plate thickness 1.10–1.30 mm (0.043–0.051 in)
Plate quantity 7 pcs
Warpage limit 0.10 mm (0.0039 in)
Clutch spring free length 48.00 mm (1.89 in)
Minimum length 47.00 mm (1.85 in)
Spring quantity 6 pcs
Push rod bending limit 0.10 mm (0.0039 in)
Transmission
Transmission type Constant mesh 5-speed
Primary reduction system Spur gear
Primary reduction ratio 2.609 (60/23)
Final drive Chain
Secondary reduction ratio 3.692 (48/13) (USA) (CAN) (AUS) (NZL) (ZAF)
3.769 (49/13) (EUR) (JPN)
Operation Left foot operation
Gear ratio
1st 1.929 (27/14)
2nd 1.533 (23/15)
3rd 1.300 (26/20)
4th 1.091 (24/22)
5th 0.952 (20/21)
B
T
CC
D
A
Page 64 of 360
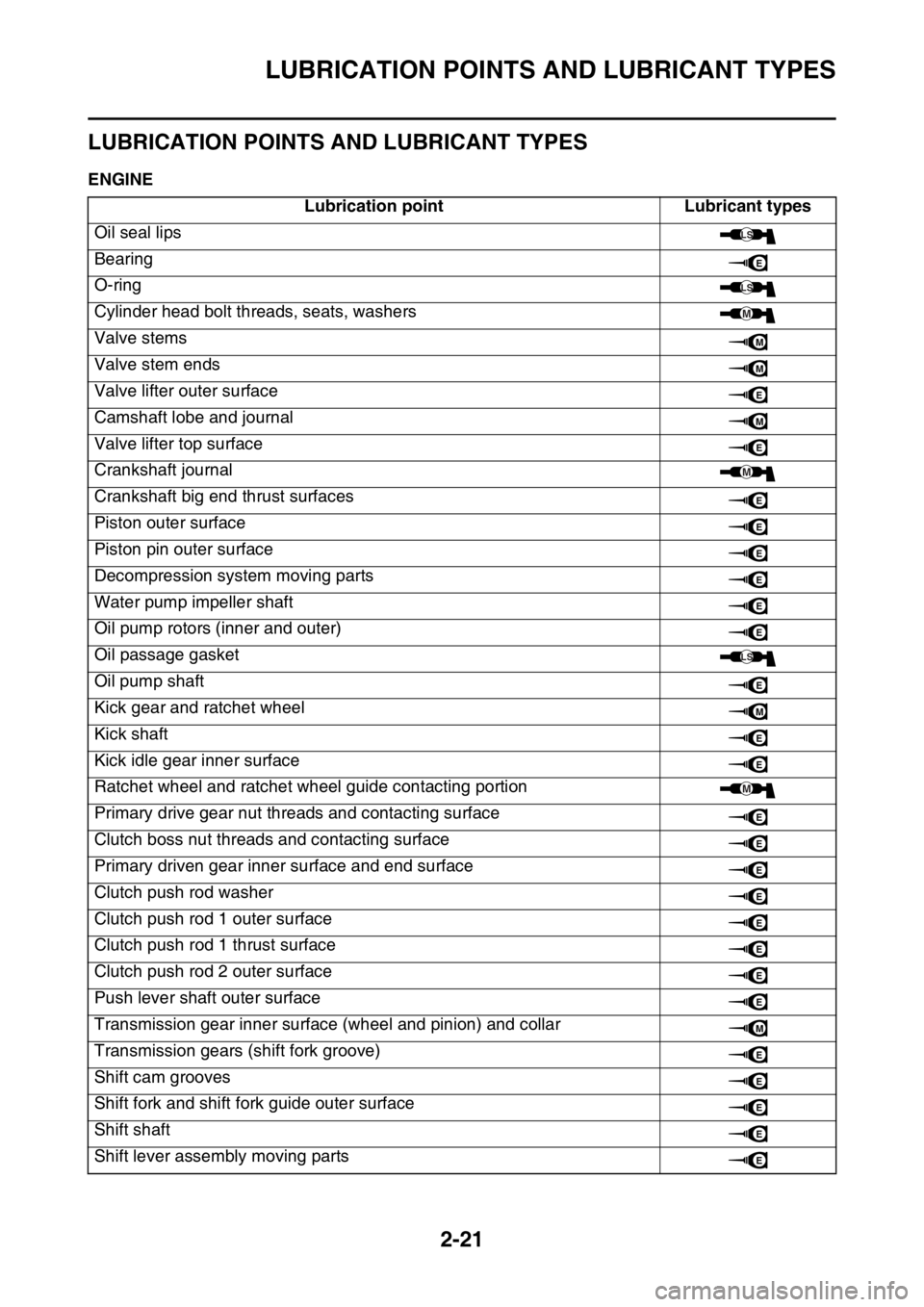
LUBRICATION POINTS AND LUBRICANT TYPES
2-21
EAS1SL5060
LUBRICATION POINTS AND LUBRICANT TYPES
EAS1SL5061ENGINE
Lubrication point Lubricant types
Oil seal lips
Bearing
O-ring
Cylinder head bolt threads, seats, washers
Valve stems
Valve stem ends
Valve lifter outer surface
Camshaft lobe and journal
Valve lifter top surface
Crankshaft journal
Crankshaft big end thrust surfaces
Piston outer surface
Piston pin outer surface
Decompression system moving parts
Water pump impeller shaft
Oil pump rotors (inner and outer)
Oil passage gasket
Oil pump shaft
Kick gear and ratchet wheel
Kick shaft
Kick idle gear inner surface
Ratchet wheel and ratchet wheel guide contacting portion
Primary drive gear nut threads and contacting surface
Clutch boss nut threads and contacting surface
Primary driven gear inner surface and end surface
Clutch push rod washer
Clutch push rod 1 outer surface
Clutch push rod 1 thrust surface
Clutch push rod 2 outer surface
Push lever shaft outer surface
Transmission gear inner surface (wheel and pinion) and collar
Transmission gears (shift fork groove)
Shift cam grooves
Shift fork and shift fork guide outer surface
Shift shaft
Shift lever assembly moving parts
LS
E
LS
M
M
M
E
M
E
M
E
E
E
E
E
E
LS
E
M
E
E
M
E
E
E
E
E
E
E
E
M
E
E
E
E
E
Page 90 of 360
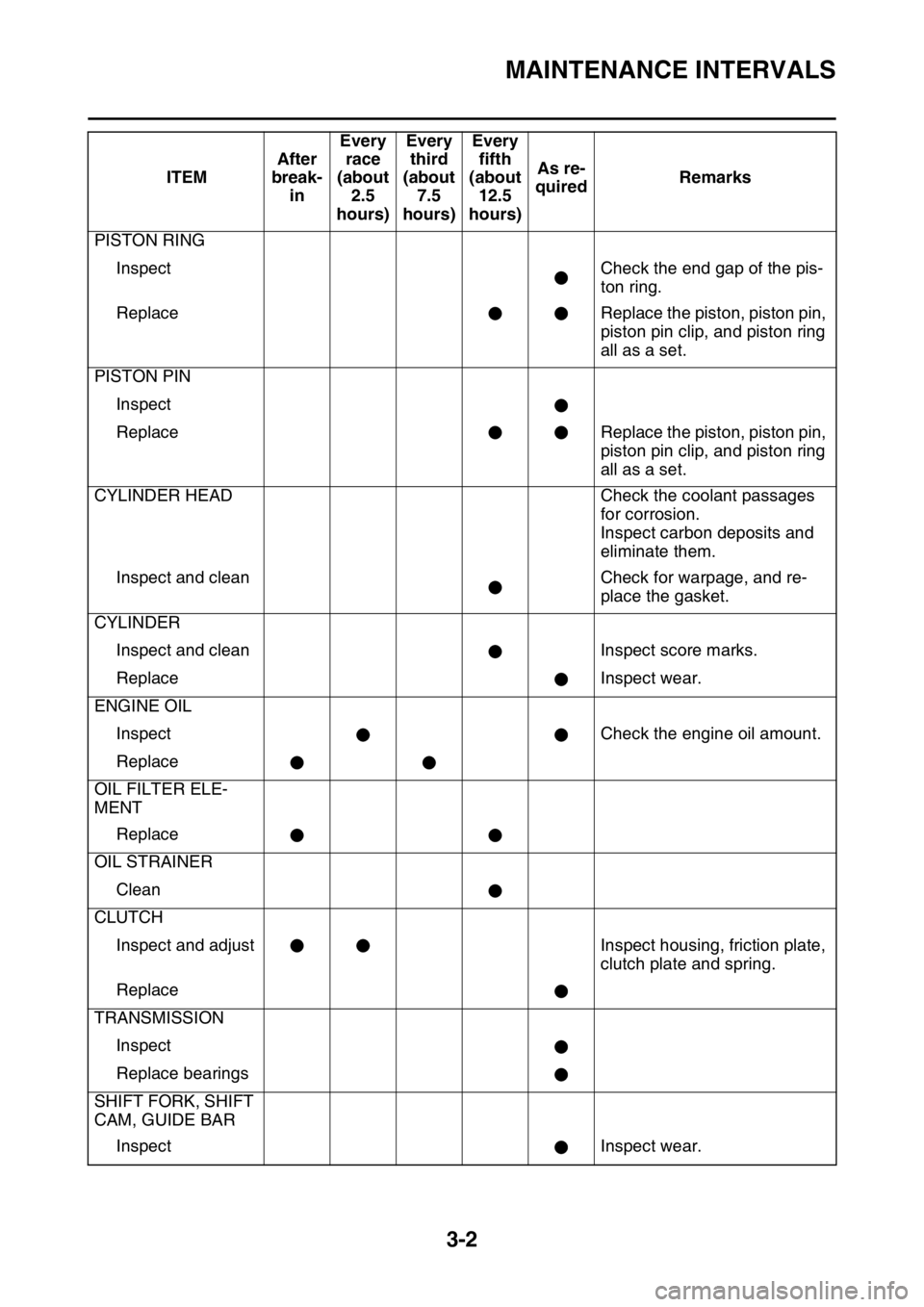
MAINTENANCE INTERVALS
3-2
PISTON RING
Inspect Check the end gap of the pis-
ton ring.
Replace Replace the piston, piston pin,
piston pin clip, and piston ring
all as a set.
PISTON PIN
Inspect
Replace Replace the piston, piston pin,
piston pin clip, and piston ring
all as a set.
CYLINDER HEAD Check the coolant passages
for corrosion.
Inspect carbon deposits and
eliminate them.
Inspect and clean Check for warpage, and re-
place the gasket.
CYLINDER
Inspect and clean Inspect score marks.
Replace Inspect wear.
ENGINE OIL
Inspect Check the engine oil amount.
Replace
OIL FILTER ELE-
MENT
Replace
OIL STRAINER
Clean
CLUTCH
Inspect and adjust Inspect housing, friction plate,
clutch plate and spring.
Replace
TRANSMISSION
Inspect
Replace bearings
SHIFT FORK, SHIFT
CAM, GUIDE BAR
Inspect Inspect wear.ITEMAfter
break-
inEvery
race
(about
2.5
hours)Every
third
(about
7.5
hours)Every
fifth
(about
12.5
hours)As re-
quiredRemarks
Page 115 of 360
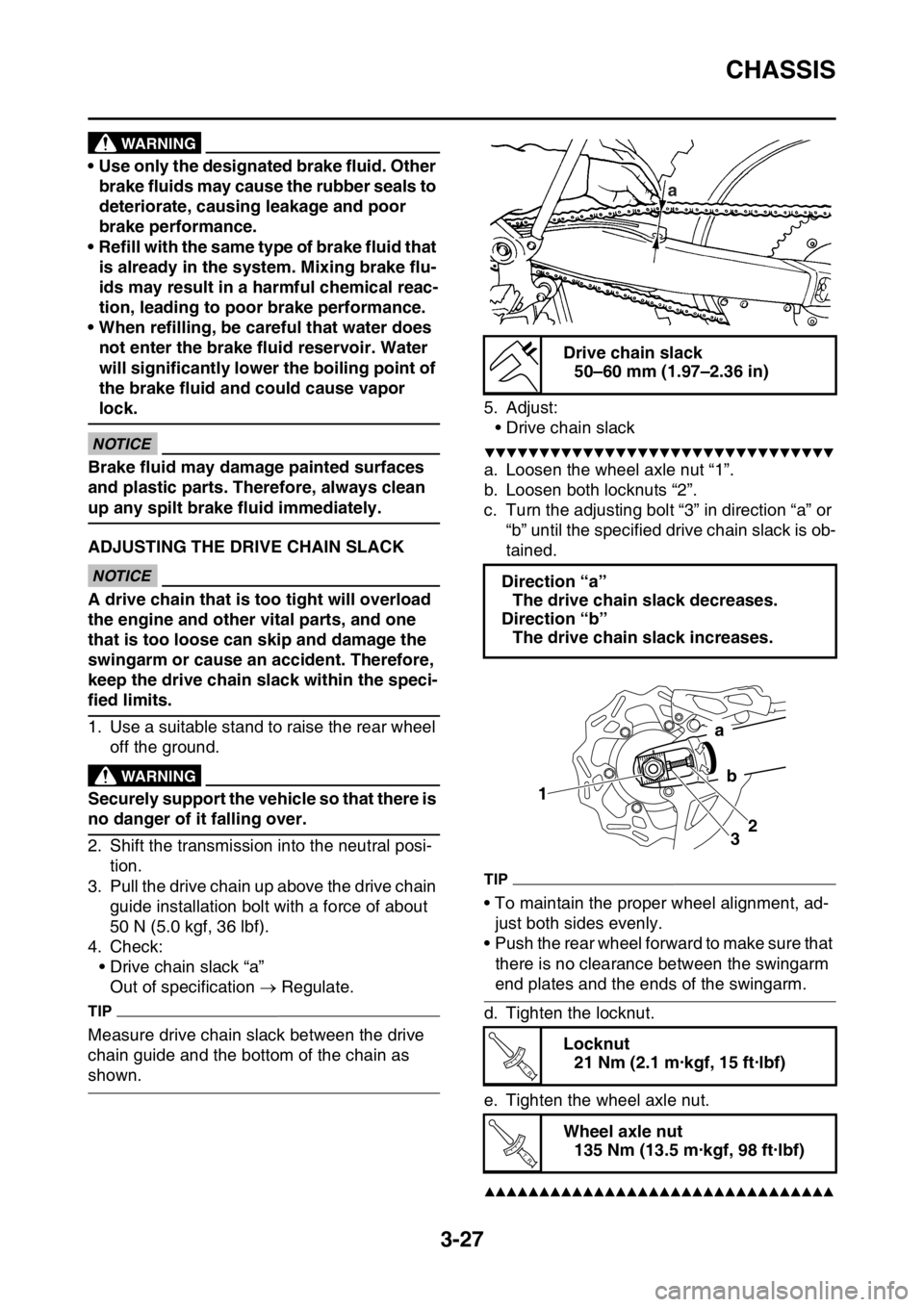
CHASSIS
3-27
WARNING
• Use only the designated brake fluid. Other
brake fluids may cause the rubber seals to
deteriorate, causing leakage and poor
brake performance.
• Refill with the same type of brake fluid that
is already in the system. Mixing brake flu-
ids may result in a harmful chemical reac-
tion, leading to poor brake performance.
• When refilling, be careful that water does
not enter the brake fluid reservoir. Water
will significantly lower the boiling point of
the brake fluid and could cause vapor
lock.
ECA13540
NOTICE
Brake fluid may damage painted surfaces
and plastic parts. Therefore, always clean
up any spilt brake fluid immediately.
EAS1SL5099ADJUSTING THE DRIVE CHAIN SLACKECA13550
NOTICE
A drive chain that is too tight will overload
the engine and other vital parts, and one
that is too loose can skip and damage the
swingarm or cause an accident. Therefore,
keep the drive chain slack within the speci-
fied limits.
1. Use a suitable stand to raise the rear wheel
off the ground.
EWA13120
WARNING
Securely support the vehicle so that there is
no danger of it falling over.
2. Shift the transmission into the neutral posi-
tion.
3. Pull the drive chain up above the drive chain
guide installation bolt with a force of about
50 N (5.0 kgf, 36 lbf).
4. Check:
• Drive chain slack “a”
Out of specification Regulate.
TIP
Measure drive chain slack between the drive
chain guide and the bottom of the chain as
shown.5. Adjust:
• Drive chain slack
▼▼▼▼▼▼▼▼▼▼▼▼▼▼▼▼▼▼▼▼▼▼▼▼▼▼▼▼▼▼▼▼
a. Loosen the wheel axle nut “1”.
b. Loosen both locknuts “2”.
c. Turn the adjusting bolt “3” in direction “a” or
“b” until the specified drive chain slack is ob-
tained.
TIP
• To maintain the proper wheel alignment, ad-
just both sides evenly.
• Push the rear wheel forward to make sure that
there is no clearance between the swingarm
end plates and the ends of the swingarm.
d. Tighten the locknut.
e. Tighten the wheel axle nut.
▲▲▲▲▲▲▲▲▲▲▲▲▲▲▲▲▲▲▲▲▲▲▲▲▲▲▲▲▲▲▲▲
Drive chain slack
50–60 mm (1.97–2.36 in)
Direction “a”
The drive chain slack decreases.
Direction “b”
The drive chain slack increases.
Locknut
21 Nm (2.1 m·kgf, 15 ft·lbf)
Wheel axle nut
135 Nm (13.5 m·kgf, 98 ft·lbf)
a
1
32
a
b
T R..
T R..
Page 195 of 360
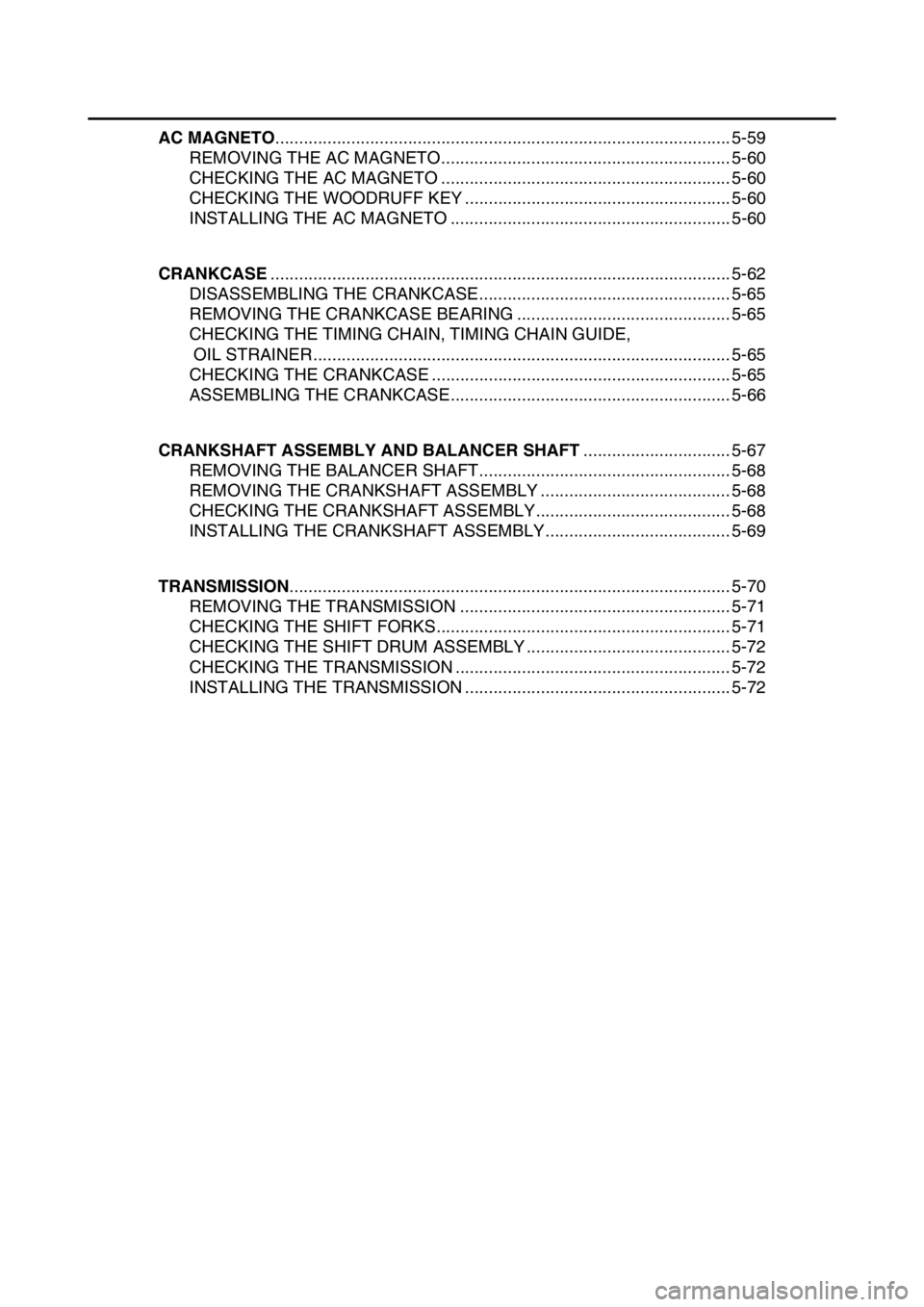
AC MAGNETO................................................................................................ 5-59
REMOVING THE AC MAGNETO............................................................. 5-60
CHECKING THE AC MAGNETO ............................................................. 5-60
CHECKING THE WOODRUFF KEY ........................................................ 5-60
INSTALLING THE AC MAGNETO ........................................................... 5-60
CRANKCASE................................................................................................. 5-62
DISASSEMBLING THE CRANKCASE..................................................... 5-65
REMOVING THE CRANKCASE BEARING ............................................. 5-65
CHECKING THE TIMING CHAIN, TIMING CHAIN GUIDE,
OIL STRAINER ........................................................................................ 5-65
CHECKING THE CRANKCASE ............................................................... 5-65
ASSEMBLING THE CRANKCASE........................................................... 5-66
CRANKSHAFT ASSEMBLY AND BALANCER SHAFT............................... 5-67
REMOVING THE BALANCER SHAFT..................................................... 5-68
REMOVING THE CRANKSHAFT ASSEMBLY ........................................ 5-68
CHECKING THE CRANKSHAFT ASSEMBLY......................................... 5-68
INSTALLING THE CRANKSHAFT ASSEMBLY....................................... 5-69
TRANSMISSION............................................................................................. 5-70
REMOVING THE TRANSMISSION ......................................................... 5-71
CHECKING THE SHIFT FORKS.............................................................. 5-71
CHECKING THE SHIFT DRUM ASSEMBLY ........................................... 5-72
CHECKING THE TRANSMISSION .......................................................... 5-72
INSTALLING THE TRANSMISSION ........................................................ 5-72
Page 259 of 360
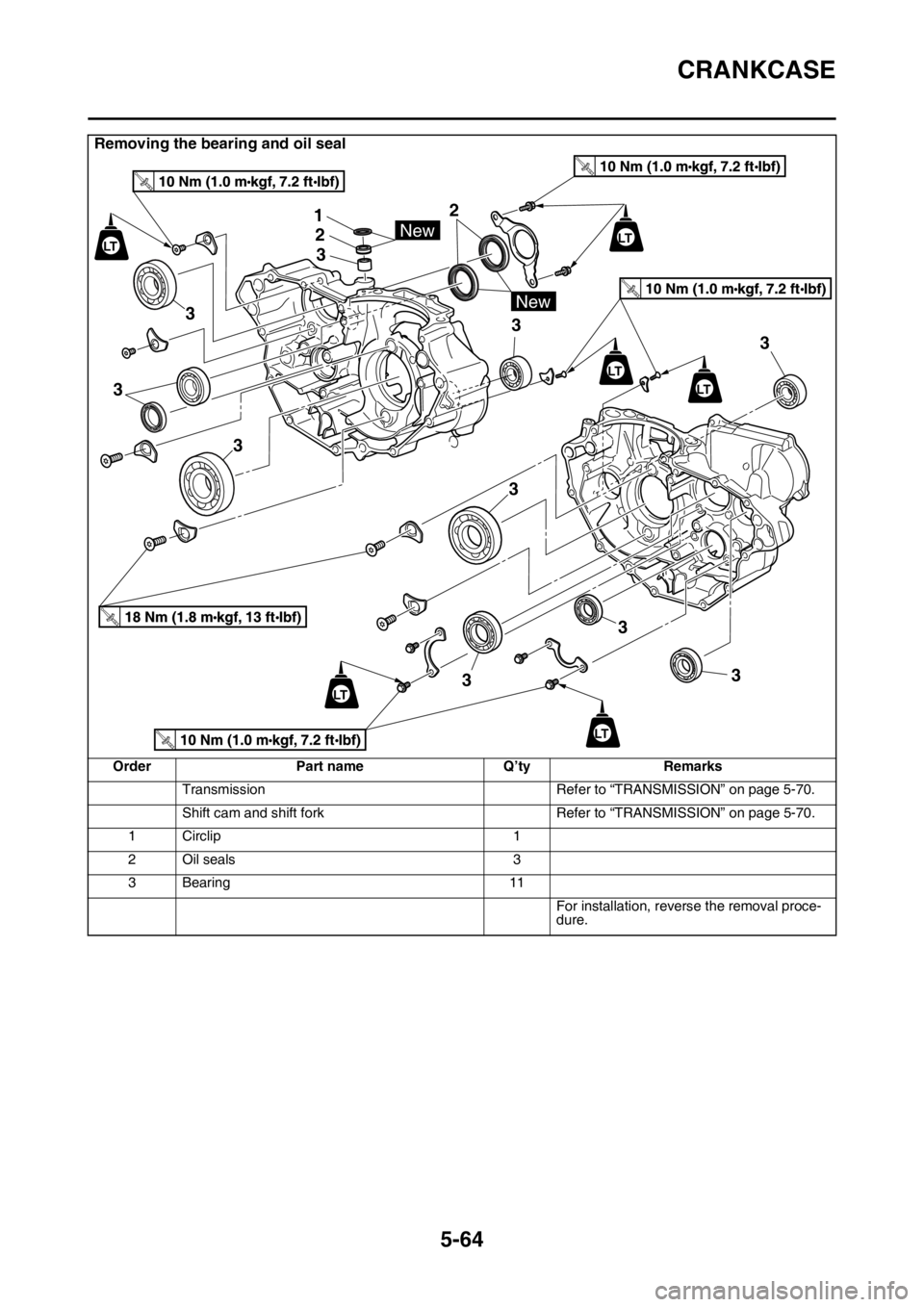
CRANKCASE
5-64
Removing the bearing and oil seal
Order Part name Q’ty Remarks
Transmission Refer to “TRANSMISSION” on page 5-70.
Shift cam and shift fork Refer to “TRANSMISSION” on page 5-70.
1 Circlip 1
2Oil seals 3
3 Bearing 11
For installation, reverse the removal proce-
dure.
LT
LT
LT
LT
LT
1
22
3
3
33
3
3
3 3
33
New
NewLT
Page 260 of 360

CRANKCASE
5-65
EAS1SL5279DISASSEMBLING THE CRANKCASE
1. Separate:
• Right crankcase
• Left crankcase
▼▼▼▼▼▼▼▼▼▼▼▼▼▼▼▼▼▼▼▼▼▼▼▼▼▼▼▼▼▼▼▼
a. Remove the crankcase bolts.
TIP
Loosen each bolt 1/4 of a turn at a time and af-
ter all the bolts are loosened, remove them.
b. Remove the right crankcase “1”.
TIP
• Place the crankcase with its left side down-
ward and split it by inserting a screwdriver tip
into the splitting slit “a” in the crankcase.
• Lift the right crankcase horizontally while light-
ly patting the crankcase splitting slit and the
engine mounting boss using a soft hammer,
and leave the crankshaft and the transmission
with the left crankcase.
ECA33DD041
NOTICE
Use soft hammer to tap on the case half.
Tap only on reinforced portions of case. Do
not tap on gasket mating surface. Work
slowly and carefully. Make sure the case
halves separate evenly. If the cases do not
separate, check for a remaining case bolt or
fitting. Do not force.c. Remove the dowel pins and O-ring.
▲▲▲▲▲▲▲▲▲▲▲▲▲▲▲▲▲▲▲▲▲▲▲▲▲▲▲▲▲▲▲▲
EAS1SL5280REMOVING THE CRANKCASE BEARING
1. Remove:
• Bearing “1”
TIP
• Remove the bearing from the crankcase by
pressing its inner race.
• Do not use the removed bearing.
EAS1SL5281CHECKING THE TIMING CHAIN, TIMING
CHAIN GUIDE, OIL STRAINER
1. Check:
• Timing chain
Stiffness Replace the camshaft sprocket,
timing chain and crankshaft sprocket as a
set.
2. Check:
• Timing chain guide
Damage/wear Replace
EAS1SL5282CHECKING THE CRANKCASE
1. Wash:
• Crankcase
TIP
• Wash the crankcase in a mild solvent.
• Remove any remaining gasket from the
crankcase mating surface.
1
a
Page 267 of 360
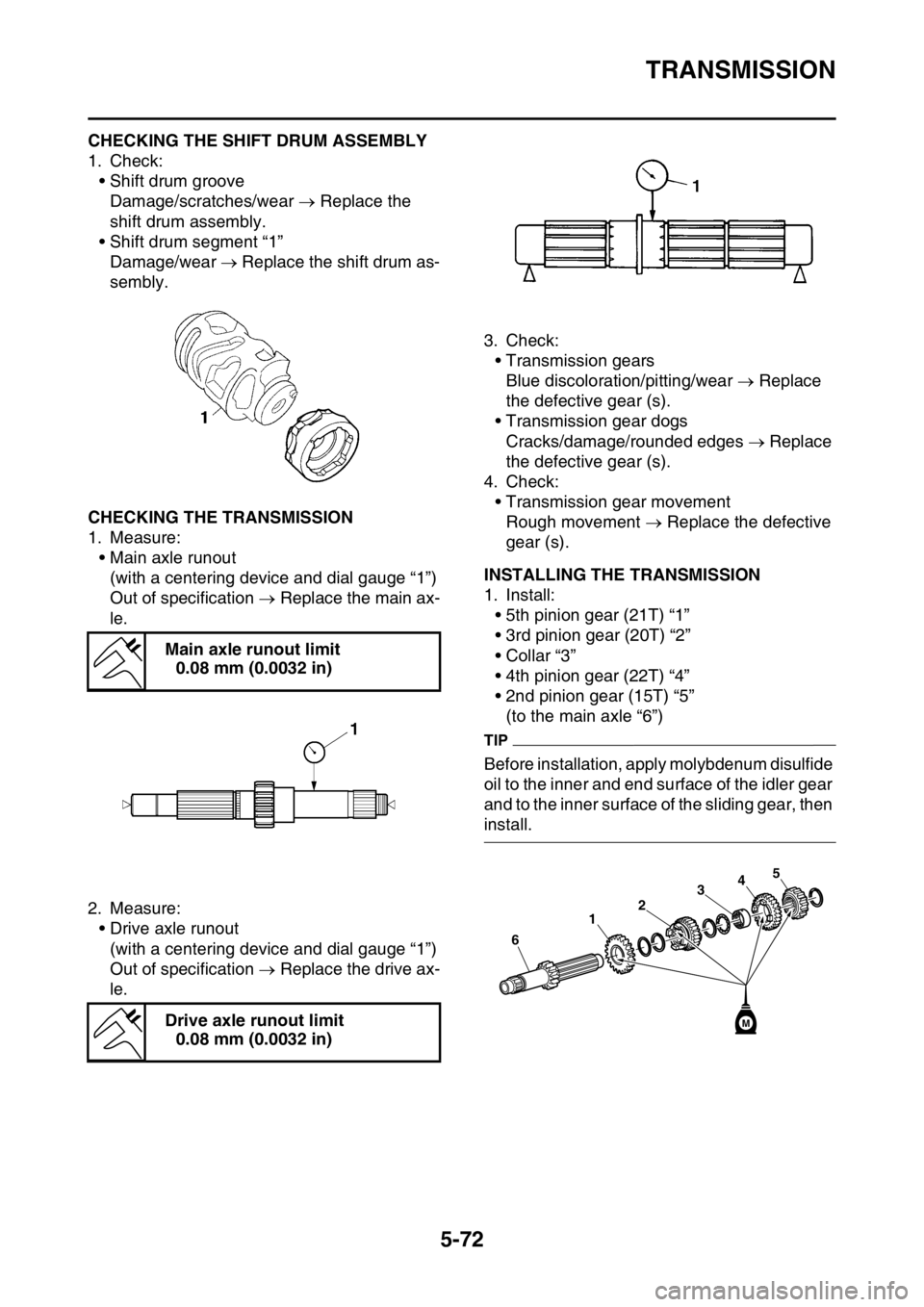
TRANSMISSION
5-72
EAS1SL5292CHECKING THE SHIFT DRUM ASSEMBLY
1. Check:
• Shift drum groove
Damage/scratches/wear Replace the
shift drum assembly.
• Shift drum segment “1”
Damage/wear Replace the shift drum as-
sembly.
EAS1SL5293CHECKING THE TRANSMISSION
1. Measure:
• Main axle runout
(with a centering device and dial gauge “1”)
Out of specification Replace the main ax-
le.
2. Measure:
• Drive axle runout
(with a centering device and dial gauge “1”)
Out of specification Replace the drive ax-
le.3. Check:
• Transmission gears
Blue discoloration/pitting/wear Replace
the defective gear (s).
• Transmission gear dogs
Cracks/damage/rounded edges Replace
the defective gear (s).
4. Check:
• Transmission gear movement
Rough movement Replace the defective
gear (s).
EAS1SL5294INSTALLING THE TRANSMISSION
1. Install:
• 5th pinion gear (21T) “1”
• 3rd pinion gear (20T) “2”
• Collar “3”
• 4th pinion gear (22T) “4”
• 2nd pinion gear (15T) “5”
(to the main axle “6”)
TIP
Before installation, apply molybdenum disulfide
oil to the inner and end surface of the idler gear
and to the inner surface of the sliding gear, then
install. Main axle runout limit
0.08 mm (0.0032 in)
Drive axle runout limit
0.08 mm (0.0032 in)
34
2
1
6
5
M
Page 268 of 360
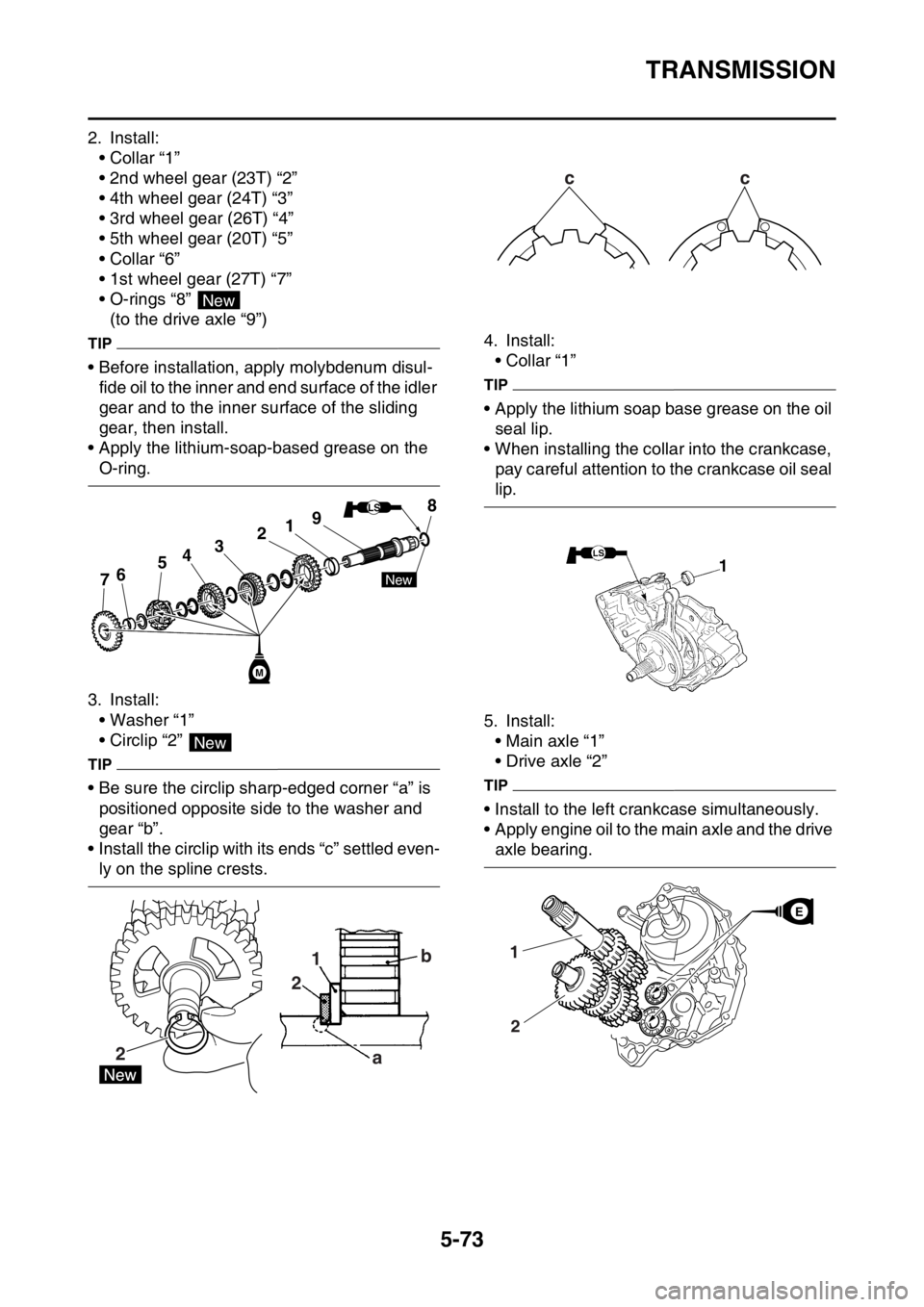
TRANSMISSION
5-73
2. Install:
• Collar “1”
• 2nd wheel gear (23T) “2”
• 4th wheel gear (24T) “3”
• 3rd wheel gear (26T) “4”
• 5th wheel gear (20T) “5”
• Collar “6”
• 1st wheel gear (27T) “7”
• O-rings “8”
(to the drive axle “9”)
TIP
• Before installation, apply molybdenum disul-
fide oil to the inner and end surface of the idler
gear and to the inner surface of the sliding
gear, then install.
• Apply the lithium-soap-based grease on the
O-ring.
3. Install:
• Washer “1”
• Circlip “2”
TIP
• Be sure the circlip sharp-edged corner “a” is
positioned opposite side to the washer and
gear “b”.
• Install the circlip with its ends “c” settled even-
ly on the spline crests.4. Install:
• Collar “1”
TIP
• Apply the lithium soap base grease on the oil
seal lip.
• When installing the collar into the crankcase,
pay careful attention to the crankcase oil seal
lip.
5. Install:
• Main axle “1”
• Drive axle “2”
TIP
• Install to the left crankcase simultaneously.
• Apply engine oil to the main axle and the drive
axle bearing.
New
298
3
4
5
6
7
New
M
LS
1
New
21
2
ab
cc
1
2
EE
Page 269 of 360
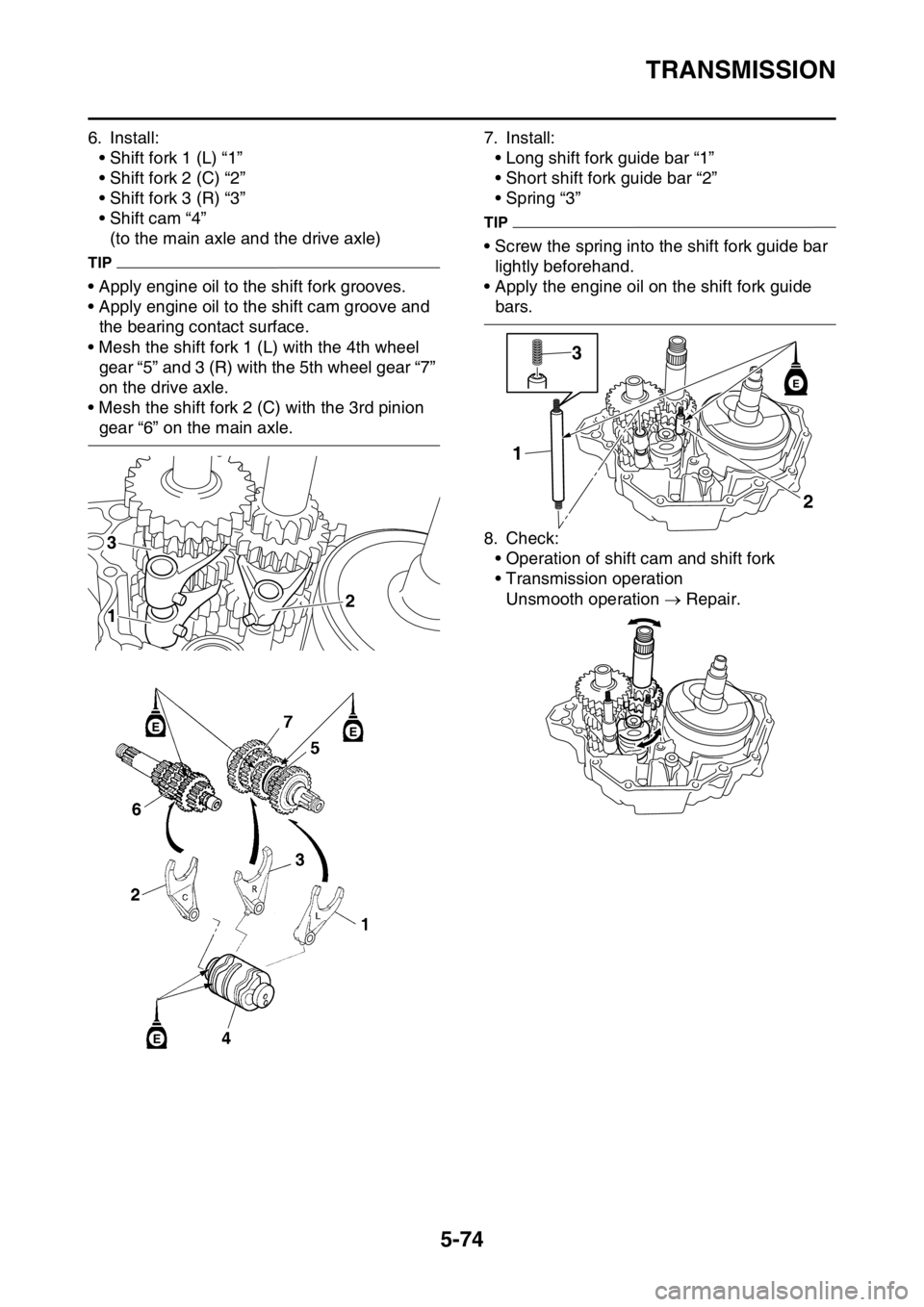
TRANSMISSION
5-74
6. Install:
• Shift fork 1 (L) “1”
• Shift fork 2 (C) “2”
• Shift fork 3 (R) “3”
• Shift cam “4”
(to the main axle and the drive axle)
TIP
• Apply engine oil to the shift fork grooves.
• Apply engine oil to the shift cam groove and
the bearing contact surface.
• Mesh the shift fork 1 (L) with the 4th wheel
gear “5” and 3 (R) with the 5th wheel gear “7”
on the drive axle.
• Mesh the shift fork 2 (C) with the 3rd pinion
gear “6” on the main axle.7. Install:
• Long shift fork guide bar “1”
• Short shift fork guide bar “2”
• Spring “3”
TIP
• Screw the spring into the shift fork guide bar
lightly beforehand.
• Apply the engine oil on the shift fork guide
bars.
8. Check:
• Operation of shift cam and shift fork
• Transmission operation
Unsmooth operation Repair.
3
12
EE
E
2 13
E