YAMAHA YZ450F 2016 Owners Manual
Manufacturer: YAMAHA, Model Year: 2016, Model line: YZ450F, Model: YAMAHA YZ450F 2016Pages: 362, PDF Size: 10.49 MB
Page 231 of 362
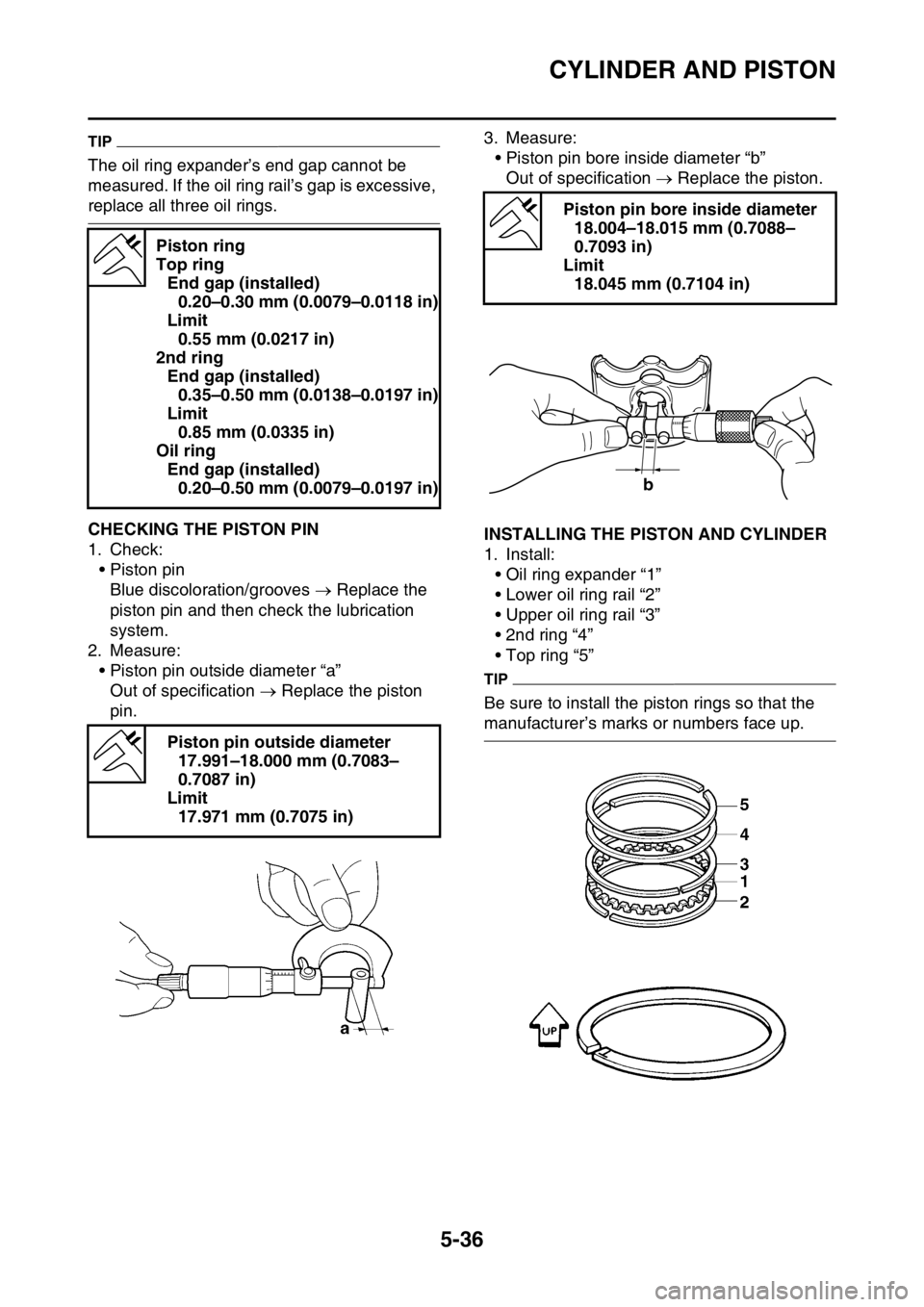
CYLINDER AND PISTON
5-36
TIP
The oil ring expander’s end gap cannot be
measured. If the oil ring rail’s gap is excessive,
replace all three oil rings.
EASB111229CHECKING THE PISTON PIN
1. Check:
• Piston pin
Blue discoloration/grooves Replace the
piston pin and then check the lubrication
system.
2. Measure:
• Piston pin outside diameter “a”
Out of specification Replace the piston
pin.3. Measure:
• Piston pin bore inside diameter “b”
Out of specification Replace the piston.EASB111230INSTALLING THE PISTON AND CYLINDER
1. Install:
• Oil ring expander “1”
• Lower oil ring rail “2”
• Upper oil ring rail “3”
• 2nd ring “4”
• Top ring “5”
TIP
Be sure to install the piston rings so that the
manufacturer’s marks or numbers face up. Piston ring
Top ring
End gap (installed)
0.20–0.30 mm (0.0079–0.0118 in)
Limit
0.55 mm (0.0217 in)
2nd ring
End gap (installed)
0.35–0.50 mm (0.0138–0.0197 in)
Limit
0.85 mm (0.0335 in)
Oil ring
End gap (installed)
0.20–0.50 mm (0.0079–0.0197 in)
Piston pin outside diameter
17.991–18.000 mm (0.7083–
0.7087 in)
Limit
17.971 mm (0.7075 in)
Piston pin bore inside diameter
18.004–18.015 mm (0.7088–
0.7093 in)
Limit
18.045 mm (0.7104 in)
b
Page 232 of 362

CYLINDER AND PISTON
5-37
2. Install:
• Piston “1”
• Piston pin “2”
• Piston pin clips “3”
TIP
• Apply molybdenum disulfide oil to the piston
pin.
• Install the piston with the F mark “a” on it
pointing to its intake (front) side.
• Before installing the piston pin clip, cover the
crankcase opening with a cloth to prevent the
clip from falling into the crankcase.
3. Lubricate:
•Piston
• Piston rings
• Cylinder
4. Offset:
• Piston ring end gap5. Install:
• Cylinder gasket
• Dowel pin
• Cylinder
TIP
• While compressing the piston rings with one
hand, install the cylinder with the other hand.
• Pass the timing chain and timing chain guide
(exhaust side) through the timing chain cavity.
a. Top ring
b. 2nd ring
c. Upper oil ring rail
d. Oil ring expander
e. Lower oil ring rail
New
1
3
2 a
3
ac
eb d
15Ã
15Ã
15Ã
15Ã
15Ã
Cylinder bolt
10 Nm (1.0 m·kgf, 7.2 ft·lbf)
New
T R..
Page 233 of 362
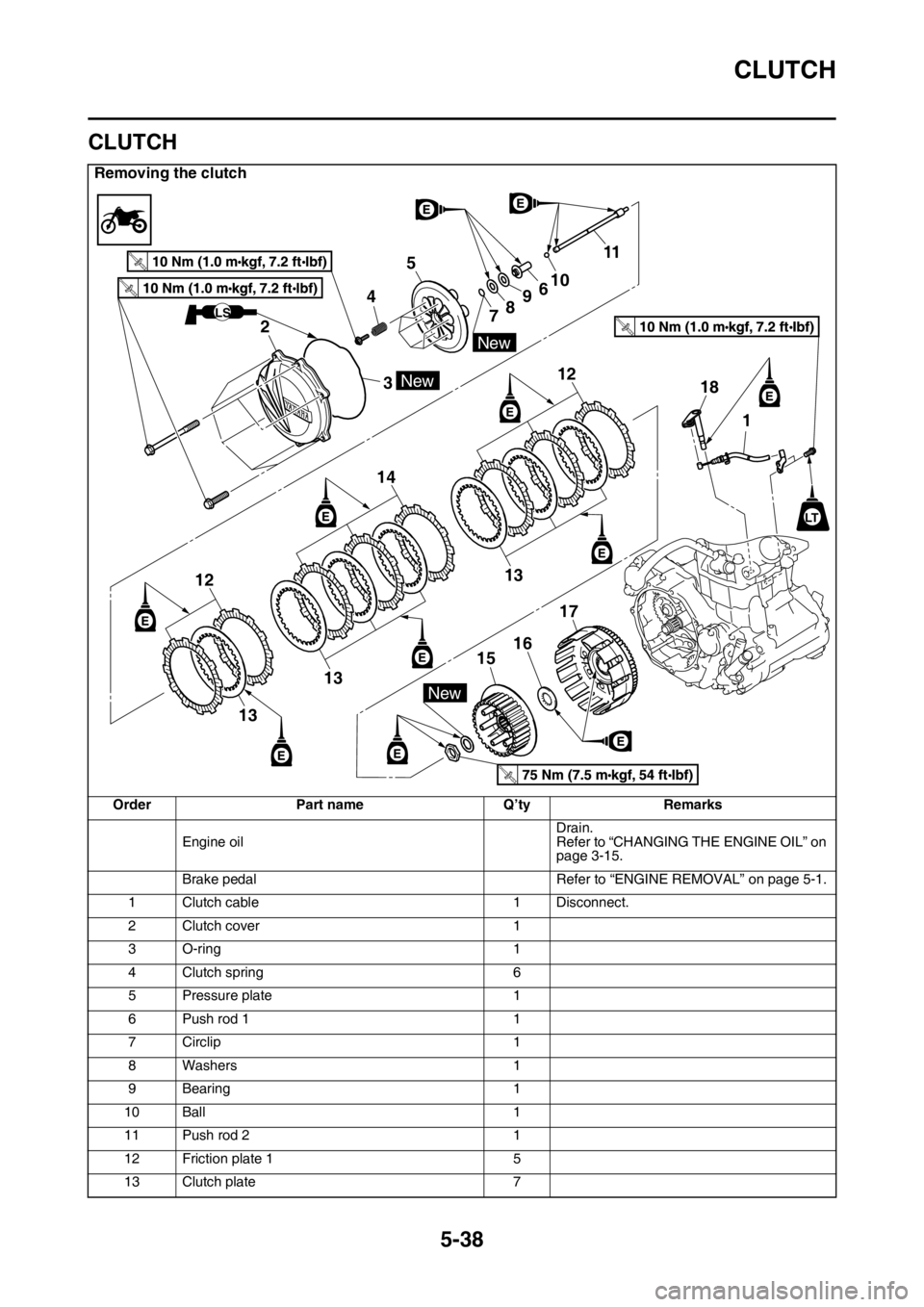
CLUTCH
5-38
EASB111231
CLUTCH
Removing the clutch
Order Part name Q’ty Remarks
Engine oilDrain.
Refer to “CHANGING THE ENGINE OIL” on
page 3-15.
Brake pedal Refer to “ENGINE REMOVAL” on page 5-1.
1 Clutch cable 1 Disconnect.
2 Clutch cover 1
3 O-ring 1
4 Clutch spring 6
5 Pressure plate 1
6 Push rod 1 1
7 Circlip 1
8Washers 1
9 Bearing 1
10 Ball 1
11 Push rod 2 1
12 Friction plate 1 5
13 Clutch plate 7
LS
New
New
New
2
3 45
78961011
13
12
12
18
1
14
13
13
17
16
15
T.R.
T.R.
T.R.
T.R.
LT
Page 234 of 362
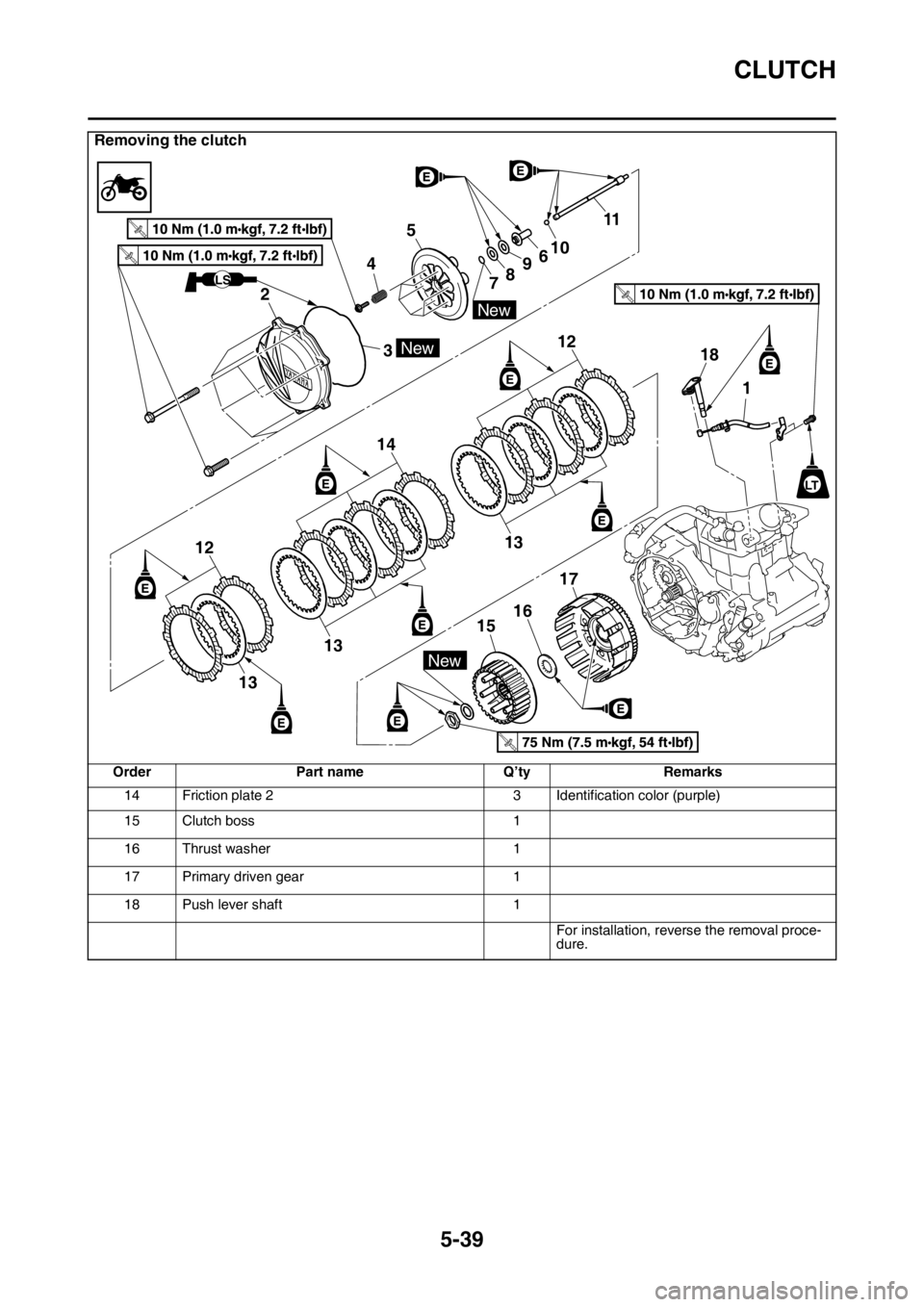
CLUTCH
5-39
14 Friction plate 2 3 Identification color (purple)
15 Clutch boss 1
16 Thrust washer 1
17 Primary driven gear 1
18 Push lever shaft 1
For installation, reverse the removal proce-
dure.
Removing the clutch
Order Part name Q’ty Remarks
LS
New
New
New
2
3 45
78961011
13
12
12
18
1
14
13
13
17
16
15
T.R.
T.R.
T.R.
T.R.
LT
Page 235 of 362
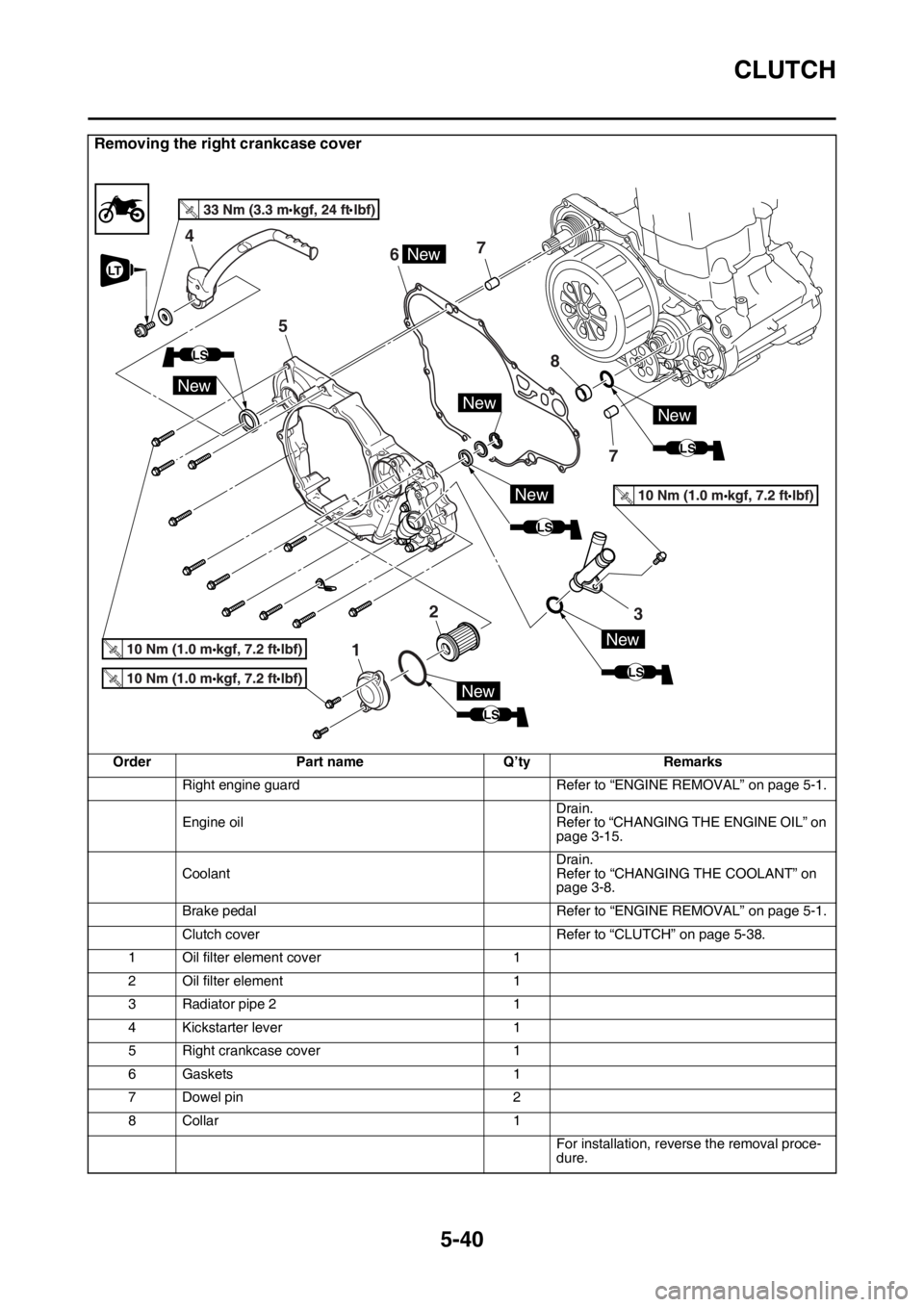
CLUTCH
5-40
Removing the right crankcase cover
Order Part name Q’ty Remarks
Right engine guard Refer to “ENGINE REMOVAL” on page 5-1.
Engine oilDrain.
Refer to “CHANGING THE ENGINE OIL” on
page 3-15.
CoolantDrain.
Refer to “CHANGING THE COOLANT” on
page 3-8.
Brake pedal Refer to “ENGINE REMOVAL” on page 5-1.
Clutch cover Refer to “CLUTCH” on page 5-38.
1 Oil filter element cover 1
2 Oil filter element 1
3 Radiator pipe 2 1
4 Kickstarter lever 1
5 Right crankcase cover 1
6 Gaskets 1
7 Dowel pin 2
8Collar 1
For installation, reverse the removal proce-
dure.
T.R.
LS
New
New
67
2
5
4
1
7 8
New
3
LS
New
New
LS
LS
NewNew
LT
LS
Page 236 of 362
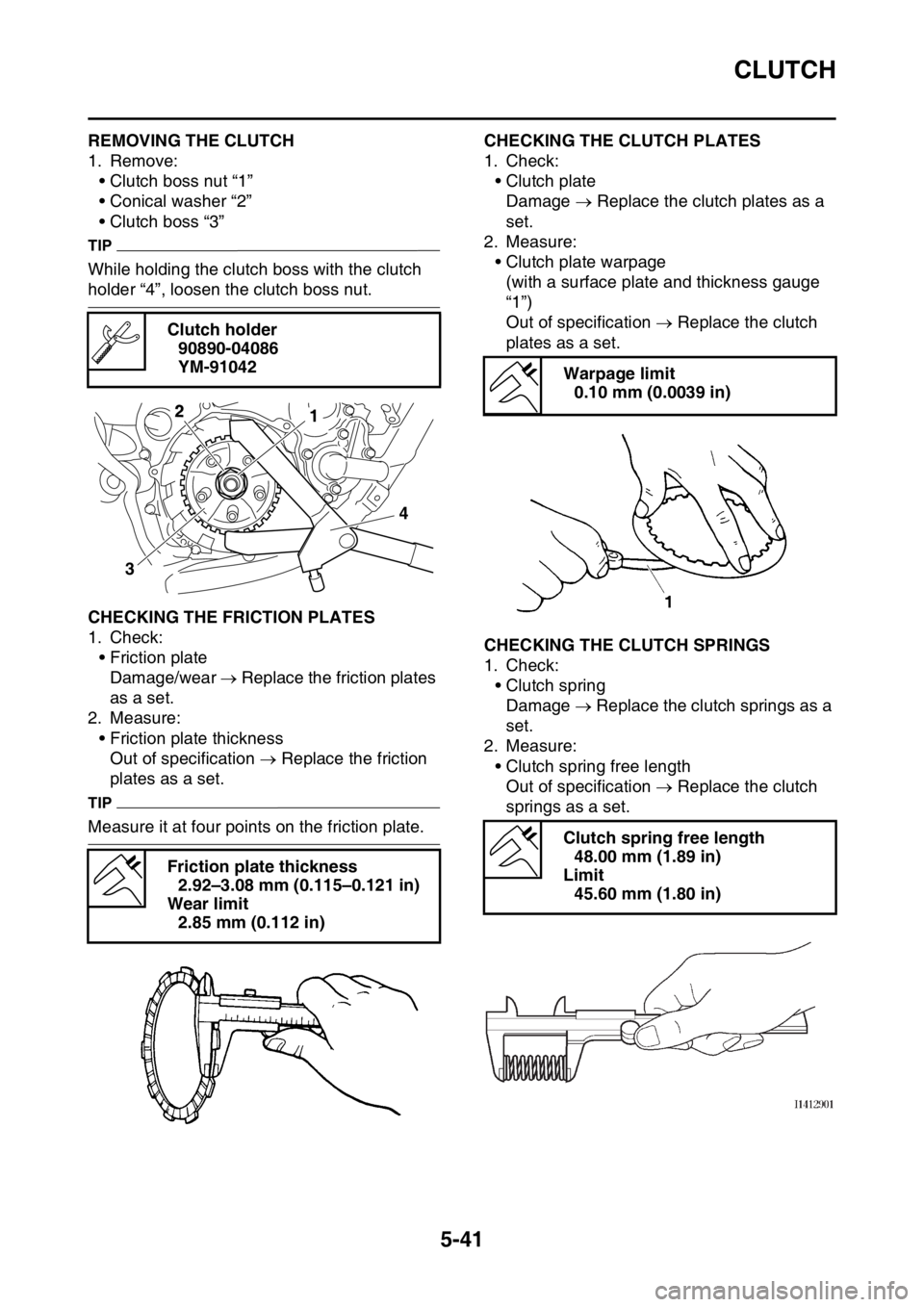
CLUTCH
5-41
EASB111232REMOVING THE CLUTCH
1. Remove:
• Clutch boss nut “1”
• Conical washer “2”
• Clutch boss “3”
TIP
While holding the clutch boss with the clutch
holder “4”, loosen the clutch boss nut.
EASB111233CHECKING THE FRICTION PLATES
1. Check:
• Friction plate
Damage/wear Replace the friction plates
as a set.
2. Measure:
• Friction plate thickness
Out of specification Replace the friction
plates as a set.
TIP
Measure it at four points on the friction plate.
EASB111234CHECKING THE CLUTCH PLATES
1. Check:
• Clutch plate
Damage Replace the clutch plates as a
set.
2. Measure:
• Clutch plate warpage
(with a surface plate and thickness gauge
“1”)
Out of specification Replace the clutch
plates as a set.
EASB111235CHECKING THE CLUTCH SPRINGS
1. Check:
• Clutch spring
Damage Replace the clutch springs as a
set.
2. Measure:
• Clutch spring free length
Out of specification Replace the clutch
springs as a set. Clutch holder
90890-04086
YM-91042
Friction plate thickness
2.92–3.08 mm (0.115–0.121 in)
Wear limit
2.85 mm (0.112 in)
34
12
Warpage limit
0.10 mm (0.0039 in)
Clutch spring free length
48.00 mm (1.89 in)
Limit
45.60 mm (1.80 in)
Page 237 of 362
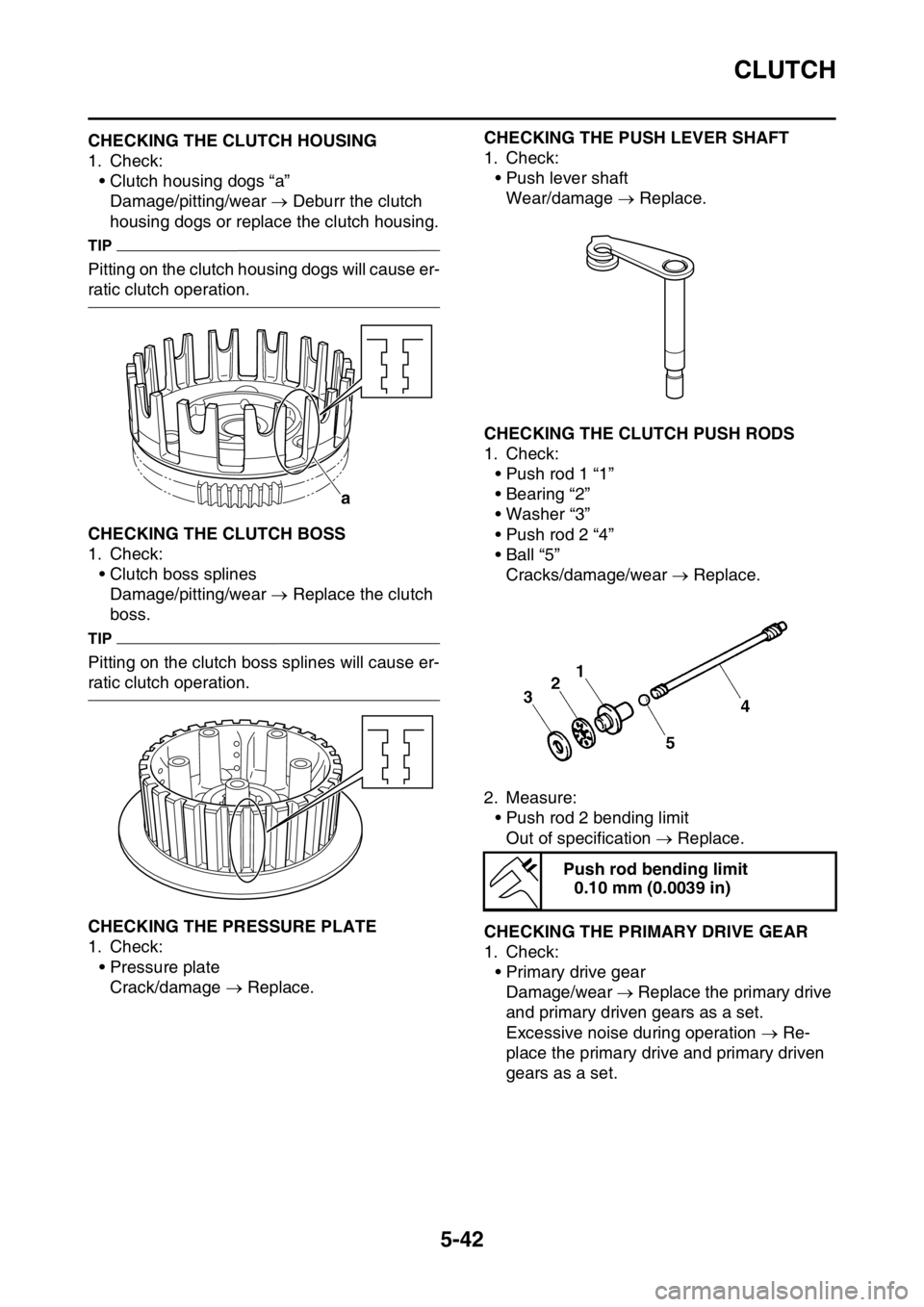
CLUTCH
5-42
EASB111236CHECKING THE CLUTCH HOUSING
1. Check:
• Clutch housing dogs “a”
Damage/pitting/wear Deburr the clutch
housing dogs or replace the clutch housing.
TIP
Pitting on the clutch housing dogs will cause er-
ratic clutch operation.
EASB111237CHECKING THE CLUTCH BOSS
1. Check:
• Clutch boss splines
Damage/pitting/wear Replace the clutch
boss.
TIP
Pitting on the clutch boss splines will cause er-
ratic clutch operation.
EASB111238CHECKING THE PRESSURE PLATE
1. Check:
• Pressure plate
Crack/damage Replace.
EASB111239
CHECKING THE PUSH LEVER SHAFT
1. Check:
• Push lever shaft
Wear/damage Replace.
EASB111240CHECKING THE CLUTCH PUSH RODS
1. Check:
• Push rod 1 “1”
• Bearing “2”
• Washer “3”
• Push rod 2 “4”
•Ball “5”
Cracks/damage/wear Replace.
2. Measure:
• Push rod 2 bending limit
Out of specification Replace.
EASB111241CHECKING THE PRIMARY DRIVE GEAR
1. Check:
• Primary drive gear
Damage/wear Replace the primary drive
and primary driven gears as a set.
Excessive noise during operation Re-
place the primary drive and primary driven
gears as a set.
a
Push rod bending limit
0.10 mm (0.0039 in)
Page 238 of 362
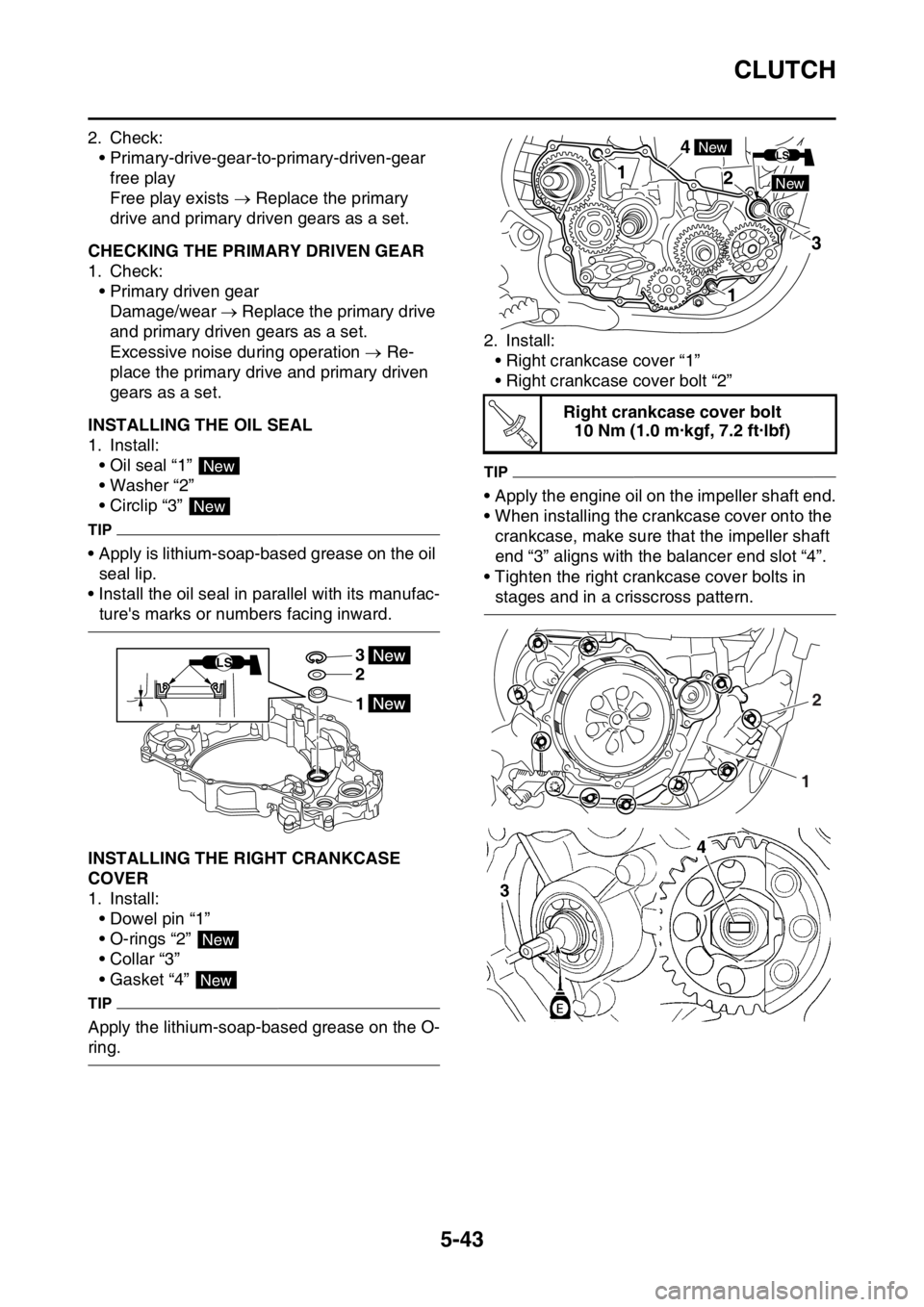
CLUTCH
5-43
2. Check:
• Primary-drive-gear-to-primary-driven-gear
free play
Free play exists Replace the primary
drive and primary driven gears as a set.
EASB111242CHECKING THE PRIMARY DRIVEN GEAR
1. Check:
• Primary driven gear
Damage/wear Replace the primary drive
and primary driven gears as a set.
Excessive noise during operation Re-
place the primary drive and primary driven
gears as a set.
EASB111243INSTALLING THE OIL SEAL
1. Install:
• Oil seal “1”
• Washer “2”
• Circlip “3”
TIP
• Apply is lithium-soap-based grease on the oil
seal lip.
• Install the oil seal in parallel with its manufac-
ture's marks or numbers facing inward.
EASB111244INSTALLING THE RIGHT CRANKCASE
COVER
1. Install:
• Dowel pin “1”
• O-rings “2”
• Collar “3”
• Gasket “4”
TIP
Apply the lithium-soap-based grease on the O-
ring.2. Install:
• Right crankcase cover “1”
• Right crankcase cover bolt “2”
TIP
• Apply the engine oil on the impeller shaft end.
• When installing the crankcase cover onto the
crankcase, make sure that the impeller shaft
end “3” aligns with the balancer end slot “4”.
• Tighten the right crankcase cover bolts in
stages and in a crisscross pattern.
New
New
3
2
1
LS
New
New
Right crankcase cover bolt
10 Nm (1.0 m·kgf, 7.2 ft·lbf)
1
1 4
2
New
New
3
LS
T R..
12
Page 239 of 362
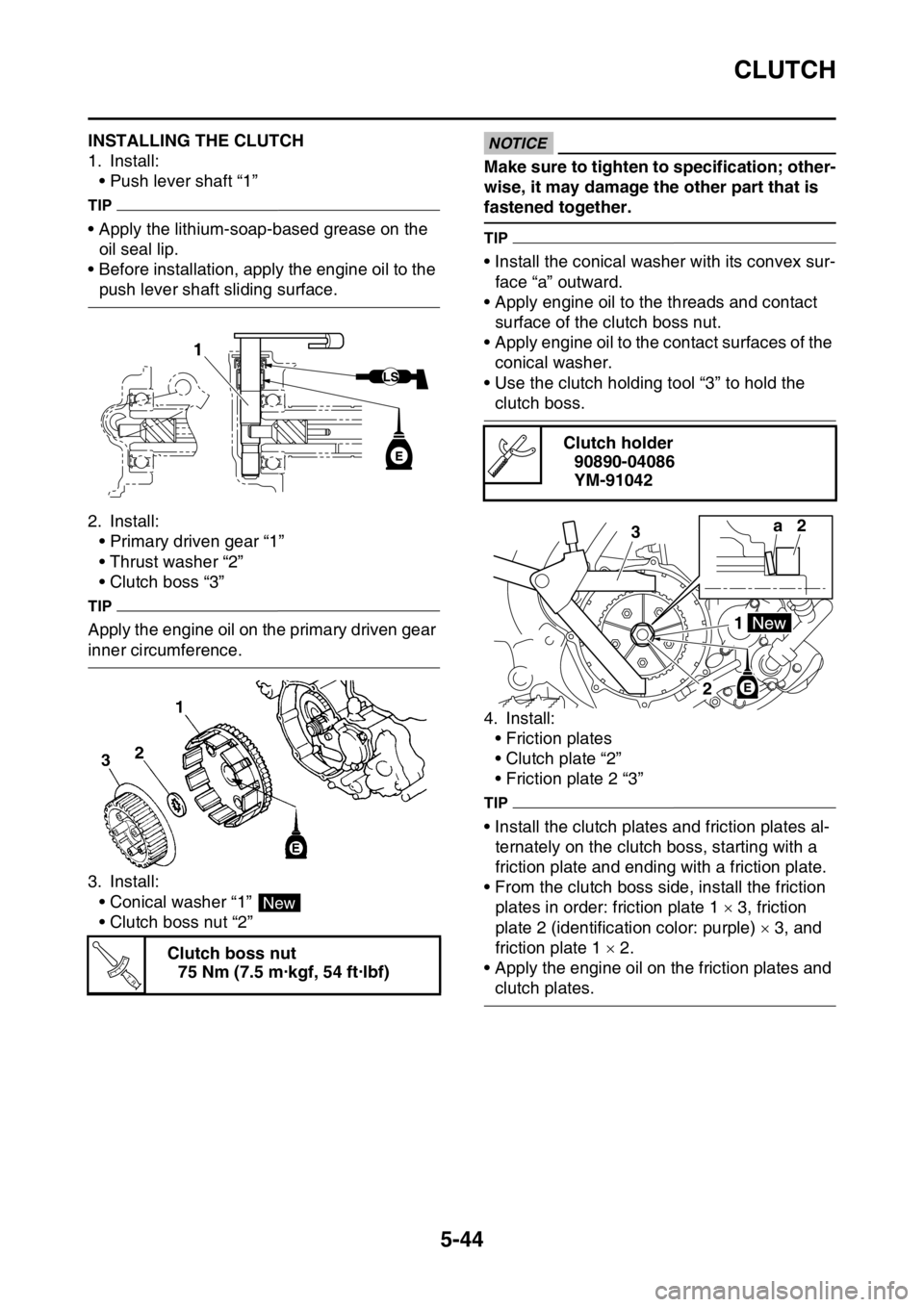
CLUTCH
5-44
EASB111245INSTALLING THE CLUTCH
1. Install:
• Push lever shaft “1”
TIP
• Apply the lithium-soap-based grease on the
oil seal lip.
• Before installation, apply the engine oil to the
push lever shaft sliding surface.
2. Install:
• Primary driven gear “1”
• Thrust washer “2”
• Clutch boss “3”
TIP
Apply the engine oil on the primary driven gear
inner circumference.
3. Install:
• Conical washer “1”
• Clutch boss nut “2”
ECA1DX1020
NOTICE
Make sure to tighten to specification; other-
wise, it may damage the other part that is
fastened together.
TIP
• Install the conical washer with its convex sur-
face “a” outward.
• Apply engine oil to the threads and contact
surface of the clutch boss nut.
• Apply engine oil to the contact surfaces of the
conical washer.
• Use the clutch holding tool “3” to hold the
clutch boss.
4. Install:
• Friction plates
• Clutch plate “2”
• Friction plate 2 “3”
TIP
• Install the clutch plates and friction plates al-
ternately on the clutch boss, starting with a
friction plate and ending with a friction plate.
• From the clutch boss side, install the friction
plates in order: friction plate 1 3, friction
plate 2 (identification color: purple) 3, and
friction plate 1 2.
• Apply the engine oil on the friction plates and
clutch plates. Clutch boss nut
75 Nm (7.5 m·kgf, 54 ft·lbf)
1
New
T R..
Clutch holder
90890-04086
YM-91042
a2
3
21
Page 240 of 362
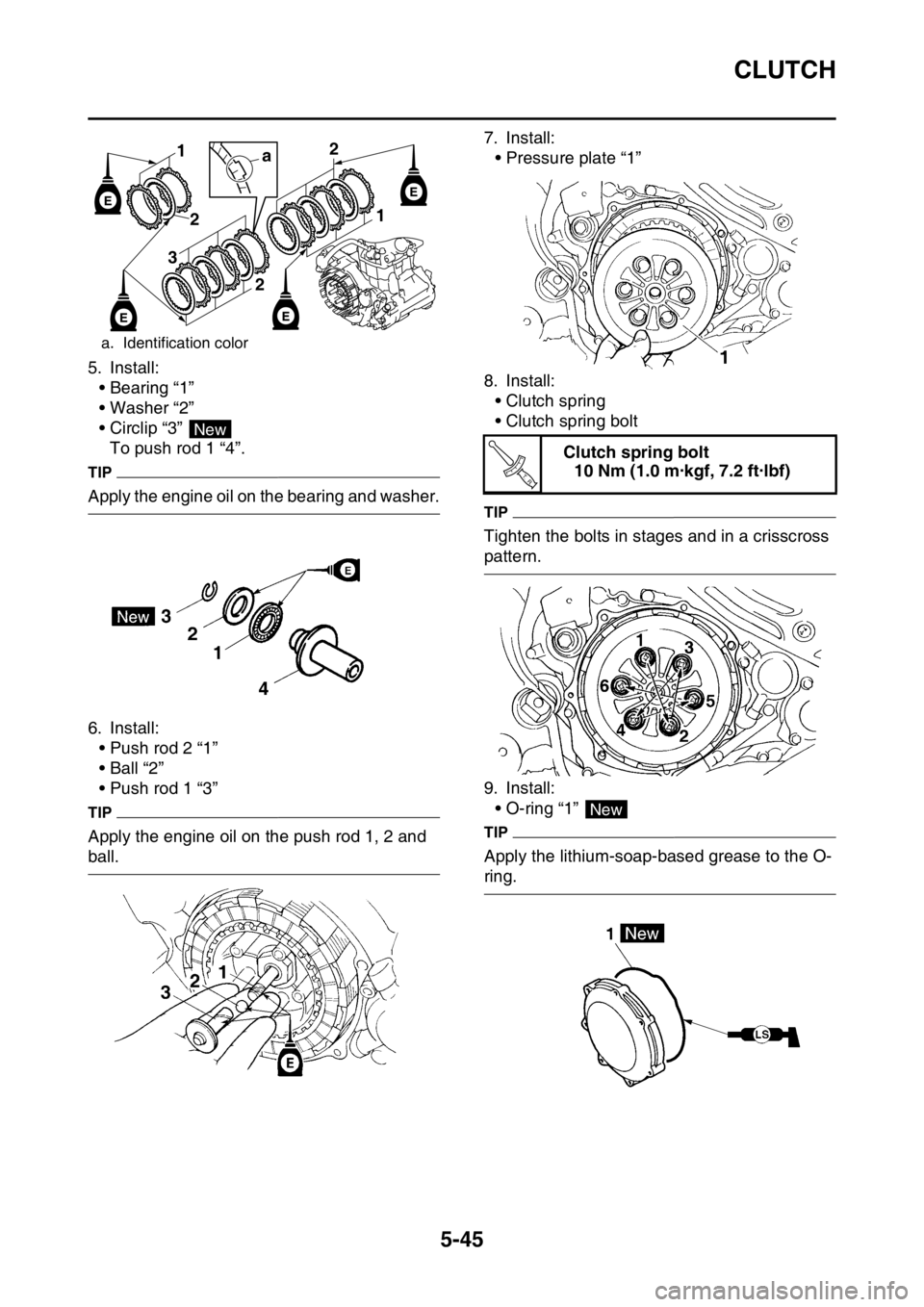
CLUTCH
5-45
5. Install:
• Bearing “1”
• Washer “2”
• Circlip “3”
To push rod 1 “4”.
TIP
Apply the engine oil on the bearing and washer.
6. Install:
• Push rod 2 “1”
•Ball “2”
• Push rod 1 “3”
TIP
Apply the engine oil on the push rod 1, 2 and
ball.7. Install:
• Pressure plate “1”
8. Install:
• Clutch spring
• Clutch spring bolt
TIP
Tighten the bolts in stages and in a crisscross
pattern.
9. Install:
• O-ring “1”
TIP
Apply the lithium-soap-based grease to the O-
ring.
a. Identification color
1
2a
3
2
2
1
New
Clutch spring bolt
10 Nm (1.0 m·kgf, 7.2 ft·lbf)
T R..
New