engine YAMAHA YZF-R7 1999 Manual Online
[x] Cancel search | Manufacturer: YAMAHA, Model Year: 1999, Model line: YZF-R7, Model: YAMAHA YZF-R7 1999Pages: 381, PDF Size: 18.88 MB
Page 193 of 381
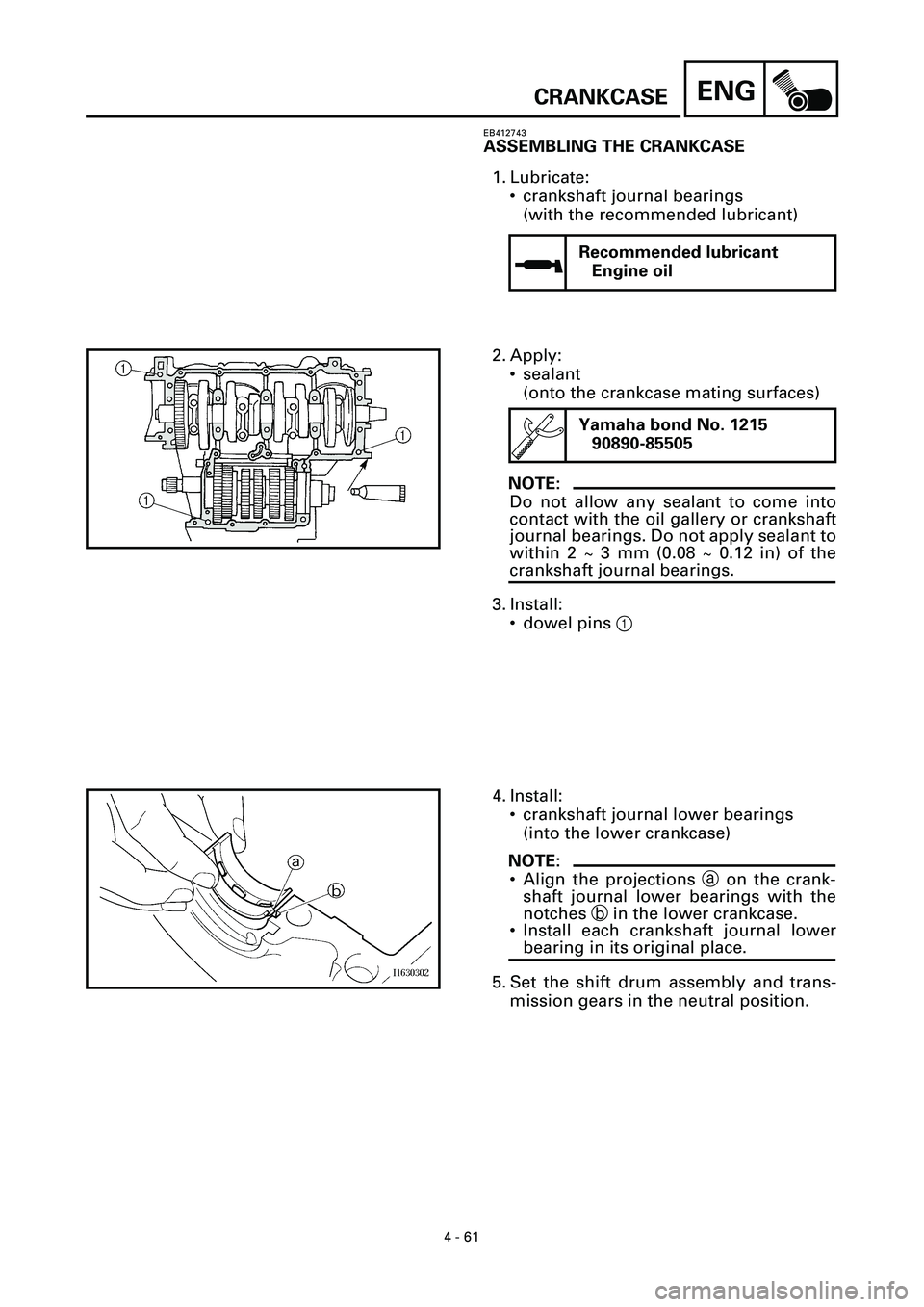
4 - 61
ENG
CRANKCASE
EB412743
ASSEMBLING THE CRANKCASE
1. Lubricate:
• crankshaft journal bearings
(with the recommended lubricant)
Recommended lubricant
Engine oil
2. Apply:
• sealant
(onto the crankcase mating surfaces)
NOTE:
Do not allow any sealant to come into
contact with the oil gallery or crankshaft
journal bearings. Do not apply sealant to
within 2 ~ 3 mm (0.08 ~ 0.12 in) of the
crankshaft journal bearings.
3. Install:
• dowel pins
1
Yamaha bond No. 1215
90890-85505
4. Install:
• crankshaft journal lower bearings
(into the lower crankcase)
NOTE:
• Align the projections
a
on the crank-
shaft journal lower bearings with the
notches
b
in the lower crankcase.
• Install each crankshaft journal lower
bearing in its original place.
5. Set the shift drum assembly and trans-
mission gears in the neutral position.
Page 194 of 381
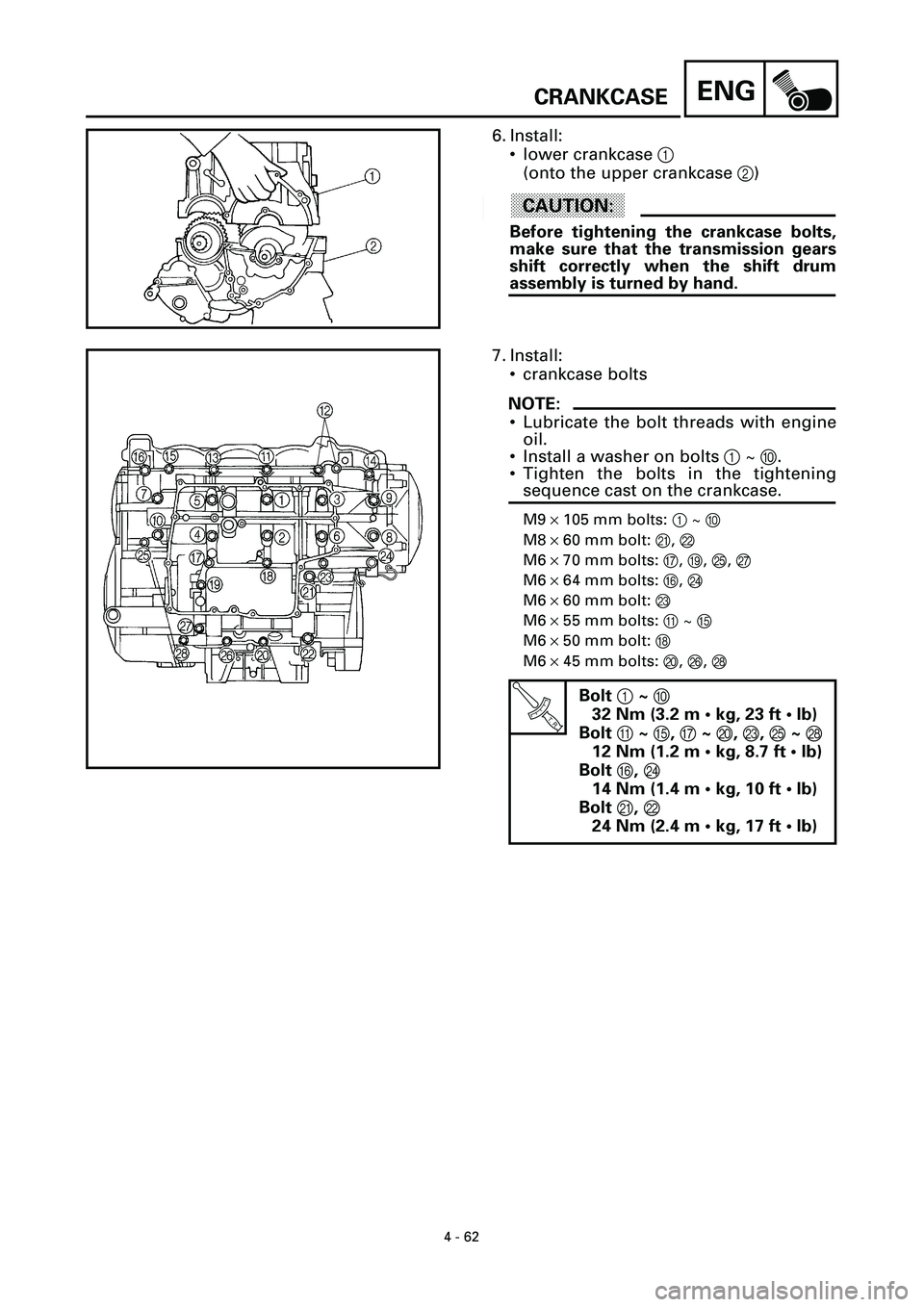
4 - 62
ENG
CRANKCASE
6. Install:
• lower crankcase
1
(onto the upper crankcase
2
)
ACHTUNG:CAUTION:
Before tightening the crankcase bolts,
make sure that the transmission gears
shift correctly when the shift drum
assembly is turned by hand.
7. Install:
• crankcase bolts
NOTE:
• Lubricate the bolt threads with engine
oil.
• Install a washer on bolts
1
~
@
.
• Tighten the bolts in the tightening
sequence cast on the crankcase.
M9
´
105 mm bolts:
1
~
@
M8
´
60 mm bolt:
K
,
L
M6
´
70 mm bolts:
G
,
I
,
O
,
Q
M6
´
64 mm bolts:
F
,
N
M6
´
60 mm bolt:
M
M6
´
55 mm bolts:
A
~
E
M6
´
50 mm bolt:
H
M6
´
45 mm bolts:
J
,
P
,
R
T R..
Bolt
1
~
@
32 Nm (3.2 m • kg, 23 ft • lb)
Bolt
A
~
E
,
G
~
J
,
M
,
O
~
R
12 Nm (1.2 m • kg, 8.7 ft • lb)
Bolt
F
,
N
14 Nm (1.4 m • kg, 10 ft • lb)
Bolt K, L
24 Nm (2.4 m • kg, 17 ft • lb)
Page 200 of 381
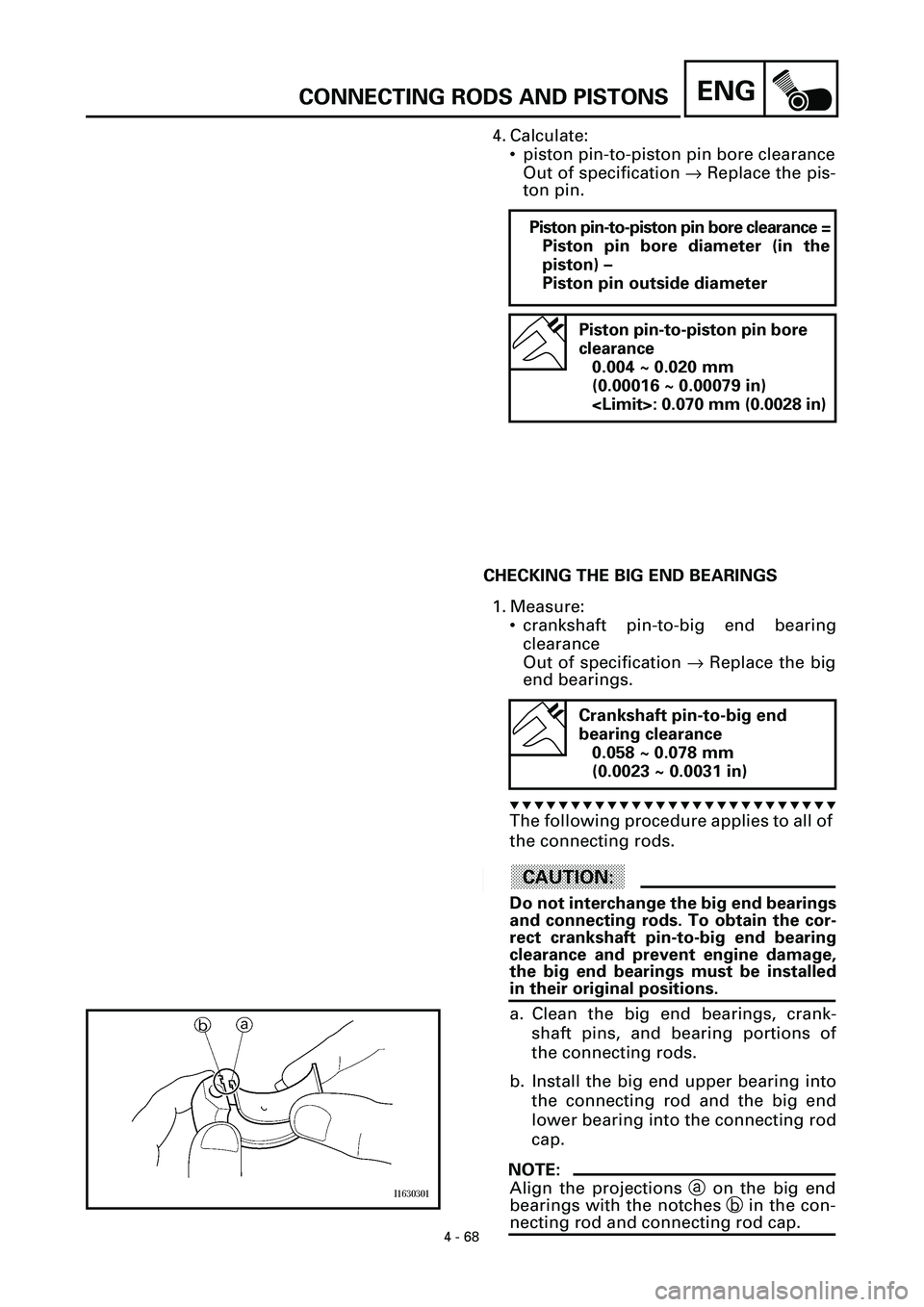
4 - 68
ENGCONNECTING RODS AND PISTONS
4. Calculate:
• piston pin-to-piston pin bore clearance
Out of specification ® Replace the pis-
ton pin.
Piston pin-to-piston pin bore clearance =
Piston pin bore diameter (in the
piston) –
Piston pin outside diameter
Piston pin-to-piston pin bore
clearance
0.004 ~ 0.020 mm
(0.00016 ~ 0.00079 in)
CHECKING THE BIG END BEARINGS
1. Measure:
• crankshaft pin-to-big end bearing
clearance
Out of specification ® Replace the big
end bearings.
t t t t t t t t t t t t t t t t t t t t t t t t t t t
The following procedure applies to all of
the connecting rods.
ACHTUNG:CAUTION:
Do not interchange the big end bearings
and connecting rods. To obtain the cor-
rect crankshaft pin-to-big end bearing
clearance and prevent engine damage,
the big end bearings must be installed
in their original positions.
a. Clean the big end bearings, crank-
shaft pins, and bearing portions of
the connecting rods.
b. Install the big end upper bearing into
the connecting rod and the big end
lower bearing into the connecting rod
cap.
NOTE:
Align the projections a on the big end
bearings with the notches b in the con-
necting rod and connecting rod cap.
Crankshaft pin-to-big end
bearing clearance
0.058 ~ 0.078 mm
(0.0023 ~ 0.0031 in)
Page 203 of 381
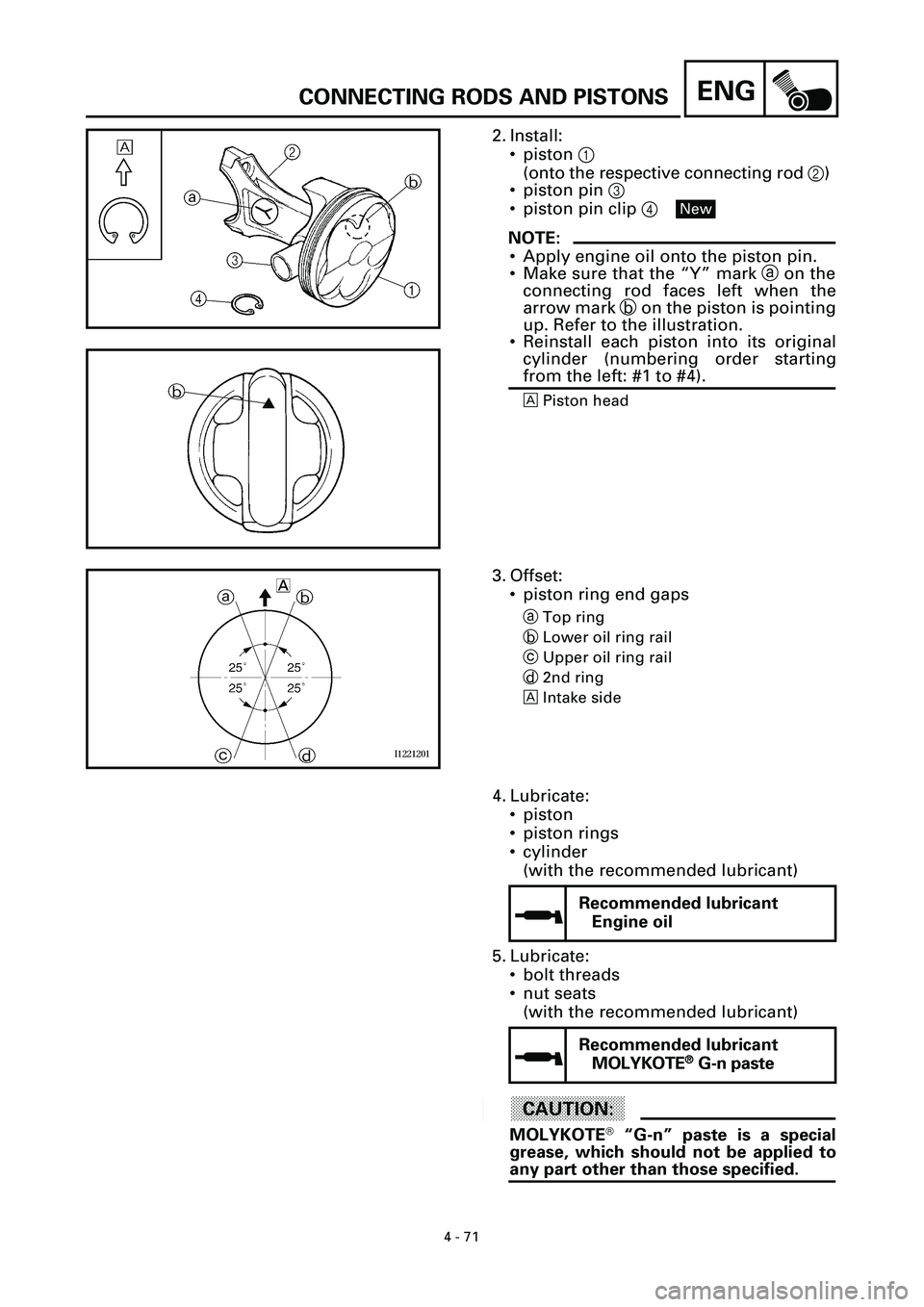
4 - 71
ENGCONNECTING RODS AND PISTONS
2. Install:
• piston 1
(onto the respective connecting rod 2)
• piston pin 3
• piston pin clip 4
NOTE:
• Apply engine oil onto the piston pin.
• Make sure that the “Y” mark a on the
connecting rod faces left when the
arrow mark b on the piston is pointing
up. Refer to the illustration.
• Reinstall each piston into its original
cylinder (numbering order starting
from the left: #1 to #4).
Piston head
New
3. Offset:
• piston ring end gaps
aTop ring
bLower oil ring rail
cUpper oil ring rail
d2nd ring
Intake side
4. Lubricate:
• piston
• piston rings
• cylinder
(with the recommended lubricant)
5. Lubricate:
• bolt threads
• nut seats
(with the recommended lubricant)
ACHTUNG:CAUTION:
MOLYKOTEâ “G-n” paste is a special
grease, which should not be applied to
any part other than those specified.
Recommended lubricant
Engine oil
Recommended lubricant
MOLYKOTE® G-n paste
Page 204 of 381
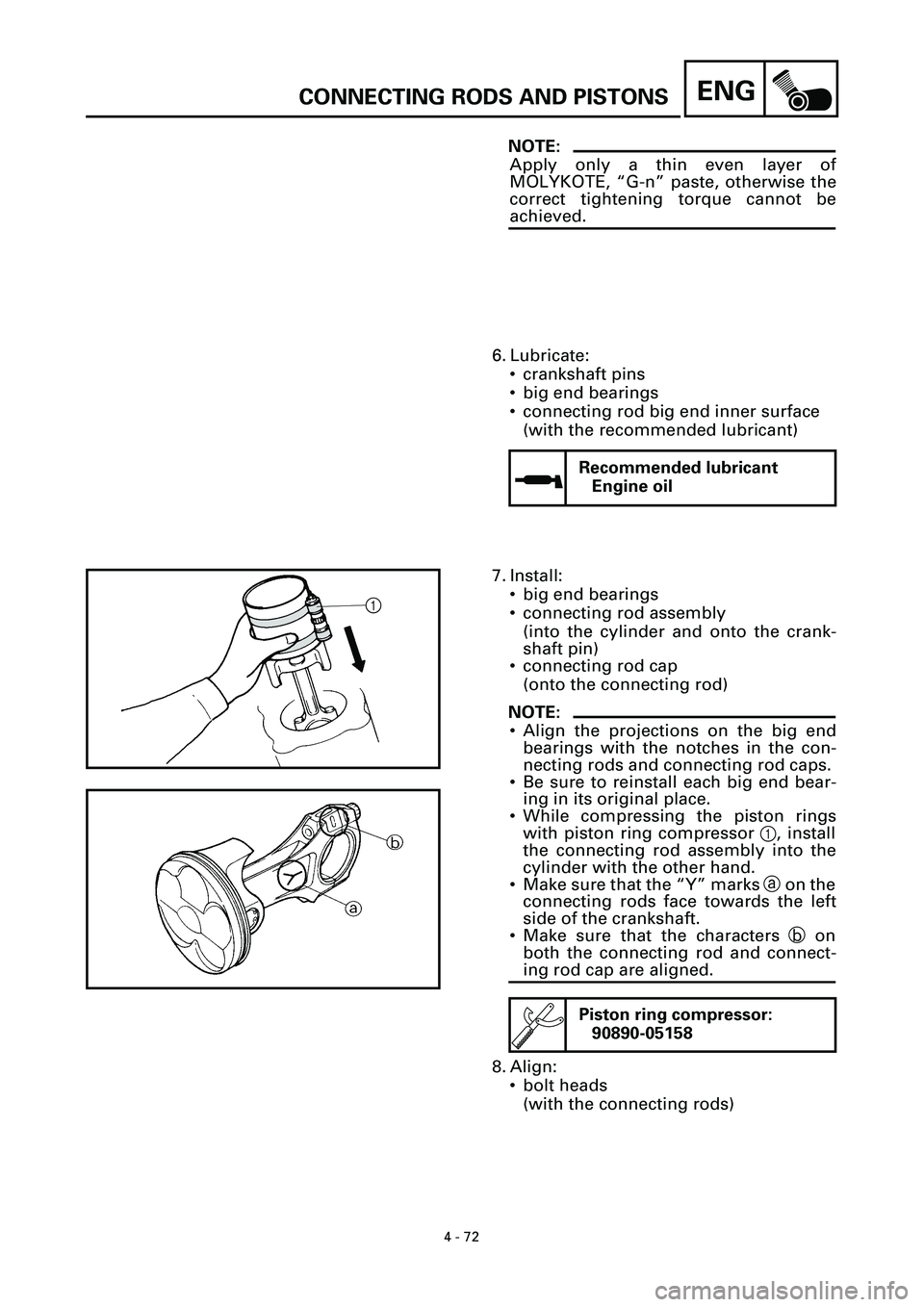
4 - 72
ENGCONNECTING RODS AND PISTONS
NOTE:
Apply only a thin even layer of
MOLYKOTE‚ “G-n” paste, otherwise the
correct tightening torque cannot be
achieved.
6. Lubricate:
• crankshaft pins
• big end bearings
• connecting rod big end inner surface
(with the recommended lubricant)
Recommended lubricant
Engine oil
7. Install:
• big end bearings
• connecting rod assembly
(into the cylinder and onto the crank-
shaft pin)
• connecting rod cap
(onto the connecting rod)
NOTE:
• Align the projections on the big end
bearings with the notches in the con-
necting rods and connecting rod caps.
• Be sure to reinstall each big end bear-
ing in its original place.
• While compressing the piston rings
with piston ring compressor 1, install
the connecting rod assembly into the
cylinder with the other hand.
• Make sure that the “Y” marks a on the
connecting rods face towards the left
side of the crankshaft.
• Make sure that the characters b on
both the connecting rod and connect-
ing rod cap are aligned.
8. Align:
• bolt heads
(with the connecting rods)
Piston ring compressor:
90890-05158
1
Page 207 of 381
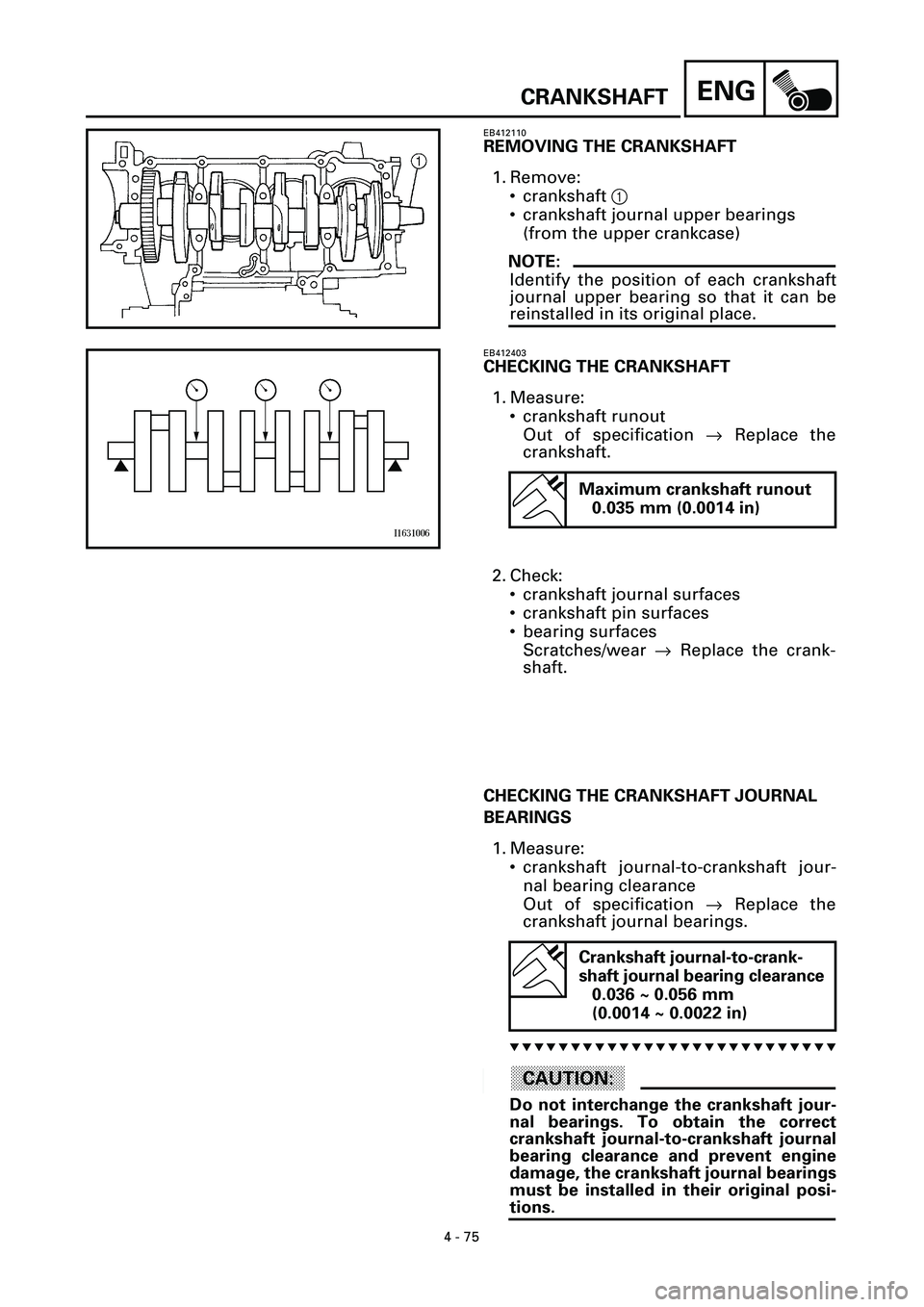
4 - 75
ENGCRANKSHAFT
EB412110
REMOVING THE CRANKSHAFT
1. Remove:
• crankshaft 1
• crankshaft journal upper bearings
(from the upper crankcase)
NOTE:
Identify the position of each crankshaft
journal upper bearing so that it can be
reinstalled in its original place.
EB412403
CHECKING THE CRANKSHAFT
1. Measure:
• crankshaft runout
Out of specification ® Replace the
crankshaft.
Maximum crankshaft runout
0.035 mm (0.0014 in)
2. Check:
• crankshaft journal surfaces
• crankshaft pin surfaces
• bearing surfaces
Scratches/wear ® Replace the crank-
shaft.
CHECKING THE CRANKSHAFT JOURNAL
BEARINGS
1. Measure:
• crankshaft journal-to-crankshaft jour-
nal bearing clearance
Out of specification ® Replace the
crankshaft journal bearings.
t t t t t t t t t t t t t t t t t t t t t t t t t t t
ACHTUNG:CAUTION:
Do not interchange the crankshaft jour-
nal bearings. To obtain the correct
crankshaft journal-to-crankshaft journal
bearing clearance and prevent engine
damage, the crankshaft journal bearings
must be installed in their original posi-
tions.
Crankshaft journal-to-crank-
shaft journal bearing clearance
0.036 ~ 0.056 mm
(0.0014 ~ 0.0022 in)
Page 208 of 381
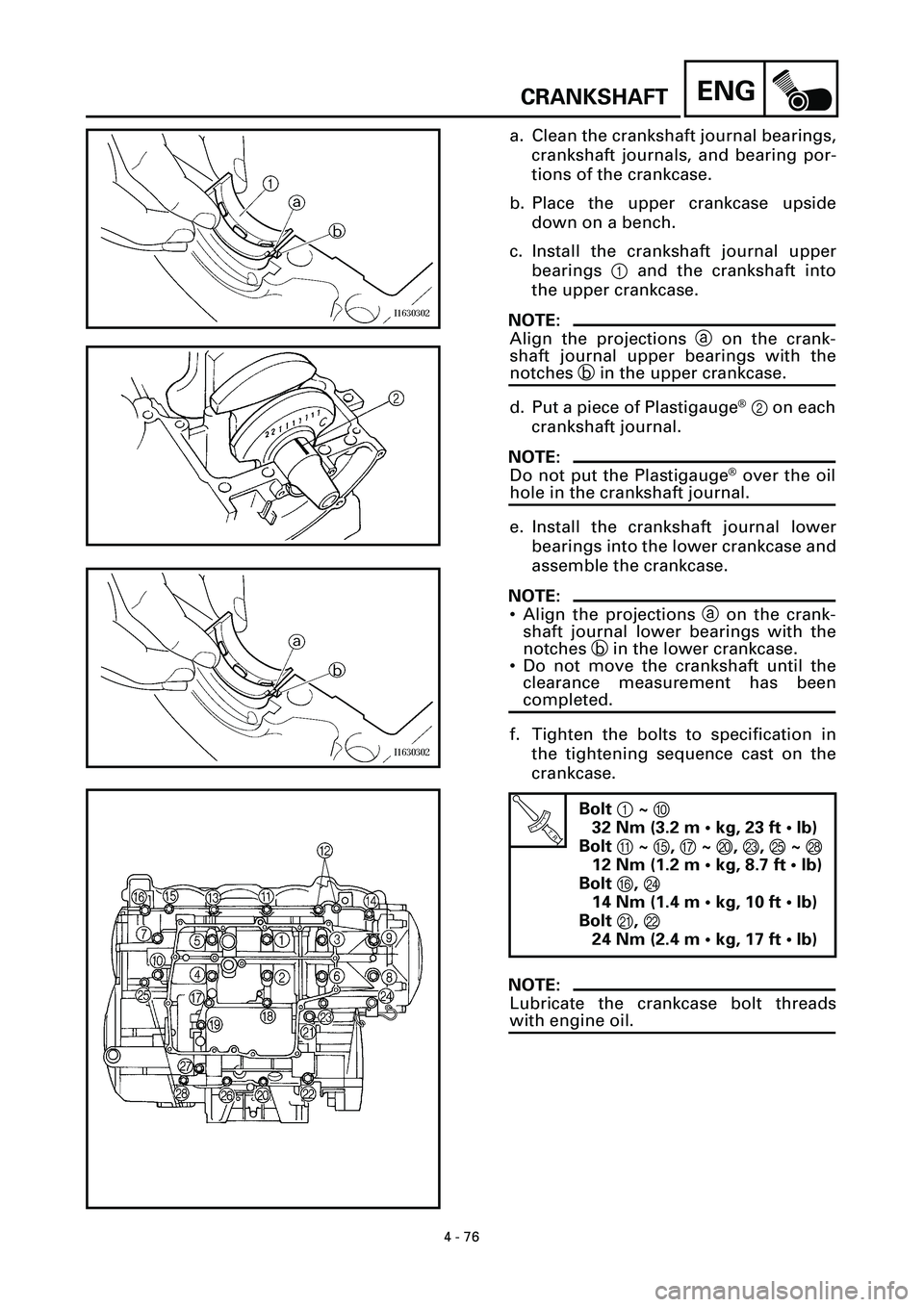
4 - 76
ENGCRANKSHAFT
a. Clean the crankshaft journal bearings,
crankshaft journals, and bearing por-
tions of the crankcase.
b. Place the upper crankcase upside
down on a bench.
c. Install the crankshaft journal upper
bearings 1 and the crankshaft into
the upper crankcase.
NOTE:
Align the projections a on the crank-
shaft journal upper bearings with the
notches b in the upper crankcase.
d. Put a piece of Plastigauge
Ò 2 on each
crankshaft journal.
NOTE:
Do not put the PlastigaugeÒ over the oil
hole in the crankshaft journal.
e. Install the crankshaft journal lower
bearings into the lower crankcase and
assemble the crankcase.
NOTE:
• Align the projections a on the crank-
shaft journal lower bearings with the
notches b in the lower crankcase.
• Do not move the crankshaft until the
clearance measurement has been
completed.
f. Tighten the bolts to specification in
the tightening sequence cast on the
crankcase.
NOTE:
Lubricate the crankcase bolt threads
with engine oil.
T R..
Bolt 1 ~ @
32 Nm (3.2 m • kg, 23 ft • lb)
Bolt A ~ E, G ~ J, M, O ~ R
12 Nm (1.2 m • kg, 8.7 ft • lb)
Bolt F, N
14 Nm (1.4 m • kg, 10 ft • lb)
Bolt K, L
24 Nm (2.4 m • kg, 17 ft • lb)
Page 219 of 381
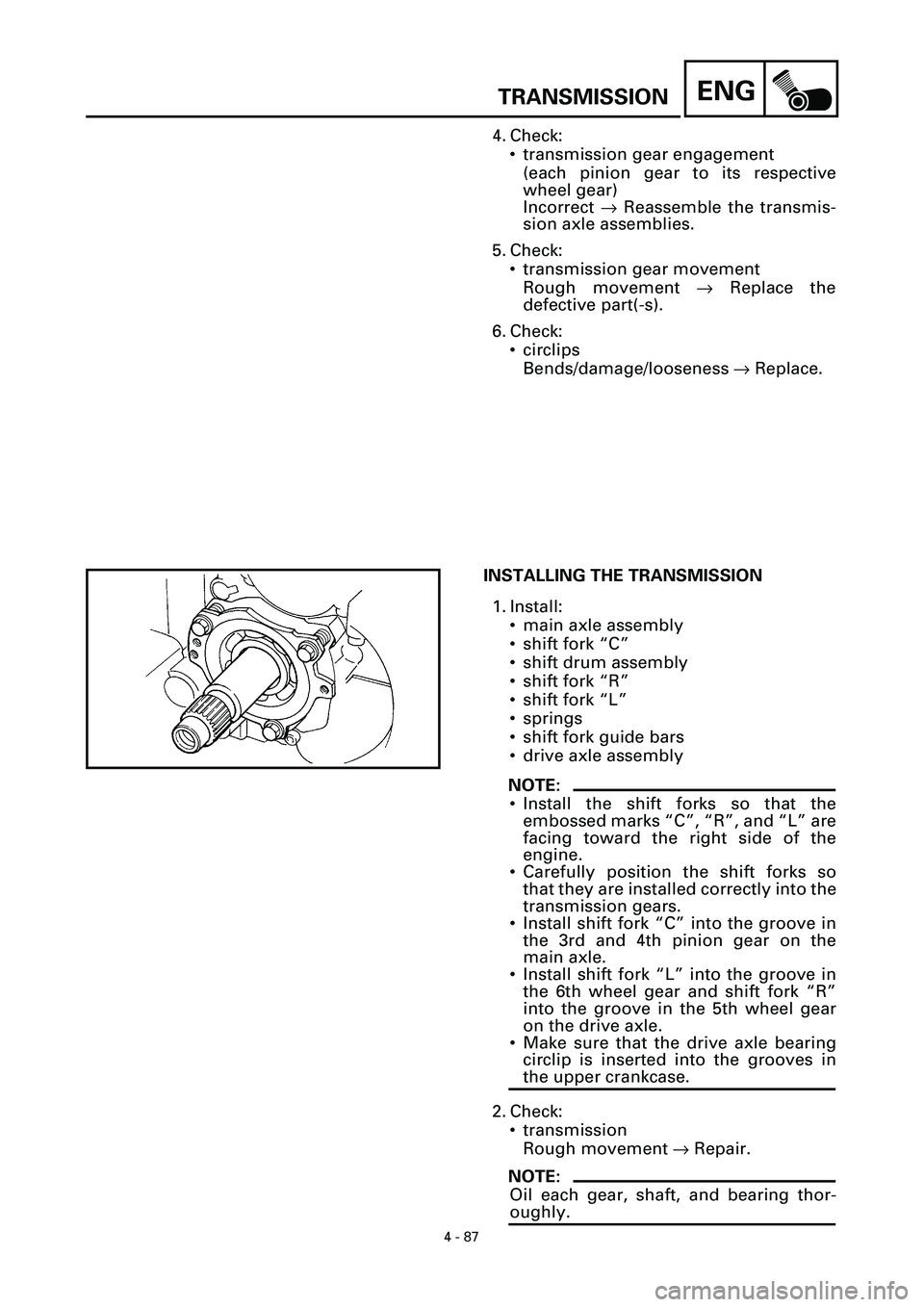
4 - 87
ENGTRANSMISSION
4. Check:
• transmission gear engagement
(each pinion gear to its respective
wheel gear)
Incorrect ® Reassemble the transmis-
sion axle assemblies.
5. Check:
• transmission gear movement
Rough movement ® Replace the
defective part(-s).
6. Check:
• circlips
Bends/damage/looseness ® Replace.
INSTALLING THE TRANSMISSION
1. Install:
• main axle assembly
• shift fork “C”
• shift drum assembly
• shift fork “R”
• shift fork “L”
• springs
• shift fork guide bars
• drive axle assembly
NOTE:
• Install the shift forks so that the
embossed marks “C”, “R”, and “L” are
facing toward the right side of the
engine.
• Carefully position the shift forks so
that they are installed correctly into the
transmission gears.
• Install shift fork “C” into the groove in
the 3rd and 4th pinion gear on the
main axle.
• Install shift fork “L” into the groove in
the 6th wheel gear and shift fork “R”
into the groove in the 5th wheel gear
on the drive axle.
• Make sure that the drive axle bearing
circlip is inserted into the grooves in
the upper crankcase.
2. Check:
• transmission
Rough movement ® Repair.
NOTE:
Oil each gear, shaft, and bearing thor-
oughly.
Page 228 of 381
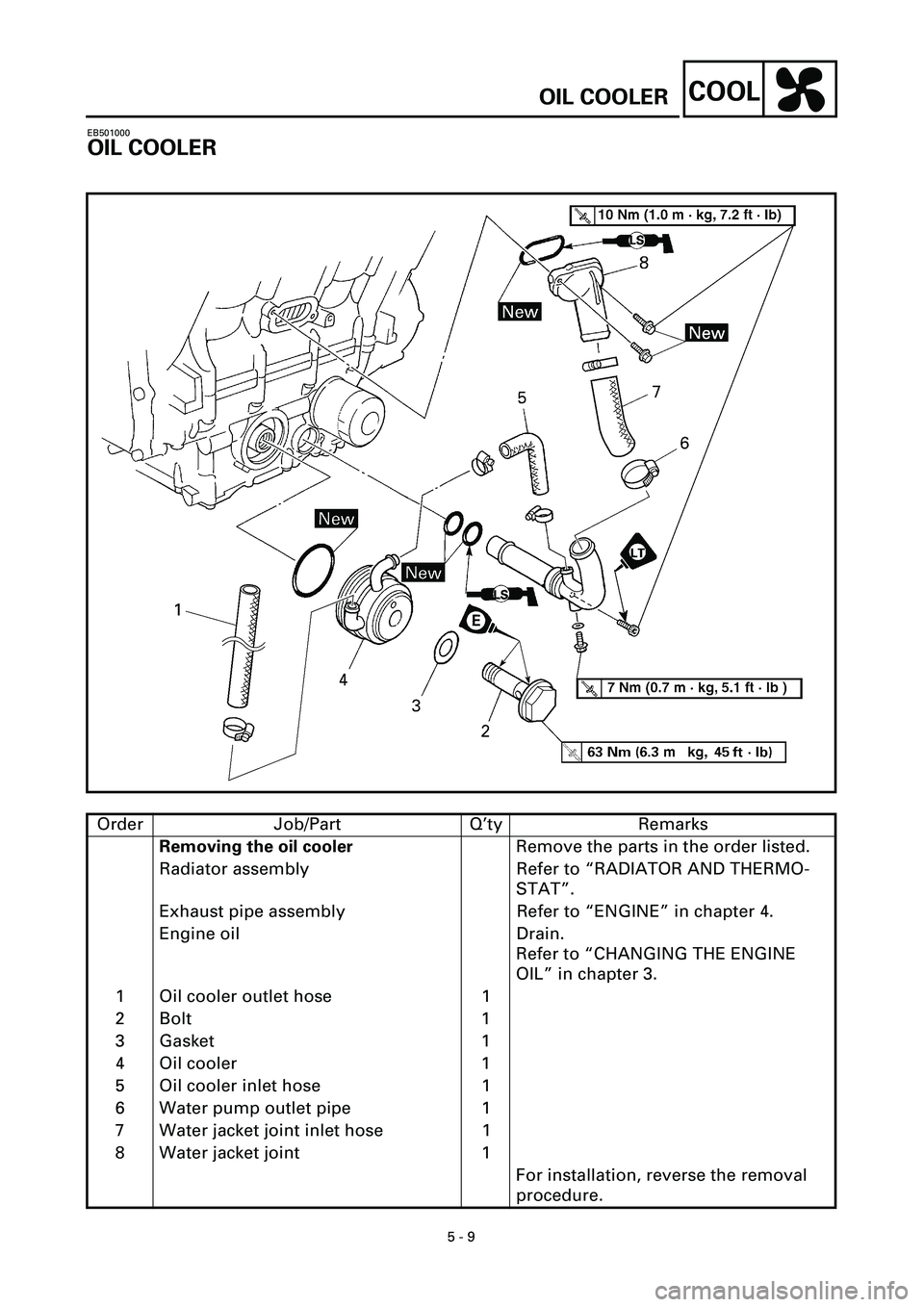
5 - 9
COOL
OIL COOLER
EB501000
OIL COOLER
Order Job/Part Q’ty Remarks
Removing the oil cooler
Remove the parts in the order listed.
Radiator assembly Refer to “RADIATOR AND THERMO-
STAT”.
Exhaust pipe assembly Refer to “ENGINE” in chapter 4.
Engine oil Drain.
Refer to “CHANGING THE ENGINE
OIL” in chapter 3.
1 Oil cooler outlet hose 1
2 Bolt 1
3 Gasket 1
4 Oil cooler 1
5 Oil cooler inlet hose 1
6 Water pump outlet pipe 1
7 Water jacket joint inlet hose 1
8 Water jacket joint 1
For installation, reverse the removal
procedure.
Page 229 of 381
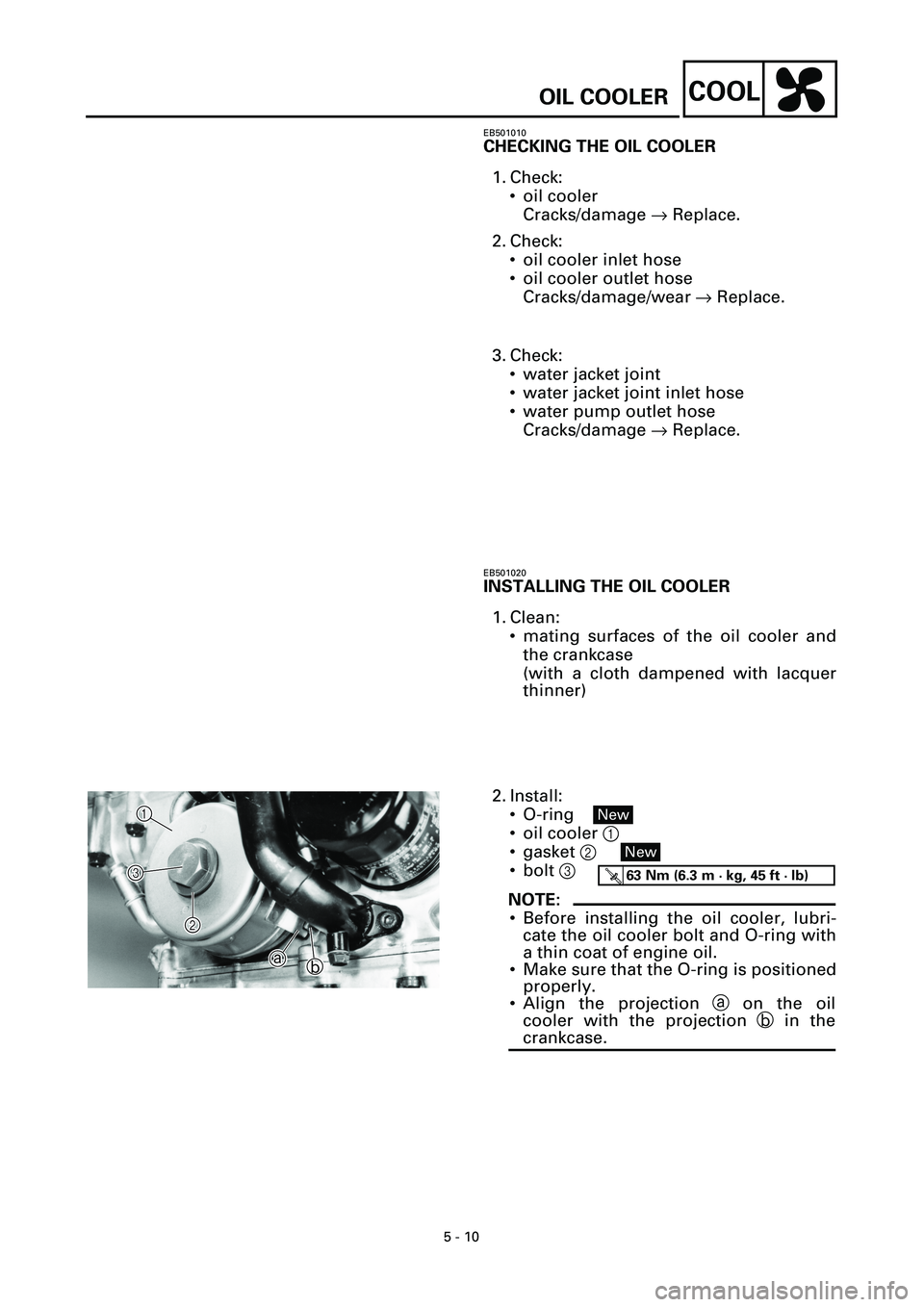
5 - 10
COOL
OIL COOLER
EB501010
CHECKING THE OIL COOLER
1. Check:
• oil cooler
Cracks/damage
®
Replace.
2. Check:
• oil cooler inlet hose
• oil cooler outlet hose
Cracks/damage/wear
®
Replace.
3. Check:
• water jacket joint
• water jacket joint inlet hose
• water pump outlet hose
Cracks/damage
®
Replace.
EB501020
INSTALLING THE OIL COOLER
1. Clean:
• mating surfaces of the oil cooler and
the crankcase
(with a cloth dampened with lacquer
thinner)
2. Install:
• O-ring
• oil cooler
1
• gasket 2
• bolt 3
NOTE:
• Before installing the oil cooler, lubri-
cate the oil cooler bolt and O-ring with
a thin coat of engine oil.
• Make sure that the O-ring is positioned
properly.
• Align the projection a on the oil
cooler with the projection b in the
crankcase.
1
1
3
3
2
2
a ab
b
New
New
T R..63 Nm (6.3 m · kg, 45 ft · lb)