ECU ASTON MARTIN V8 VANTAGE 2010 Workshop Manual
[x] Cancel search | Manufacturer: ASTON MARTIN, Model Year: 2010, Model line: V8 VANTAGE, Model: ASTON MARTIN V8 VANTAGE 2010Pages: 947, PDF Size: 43.21 MB
Page 403 of 947
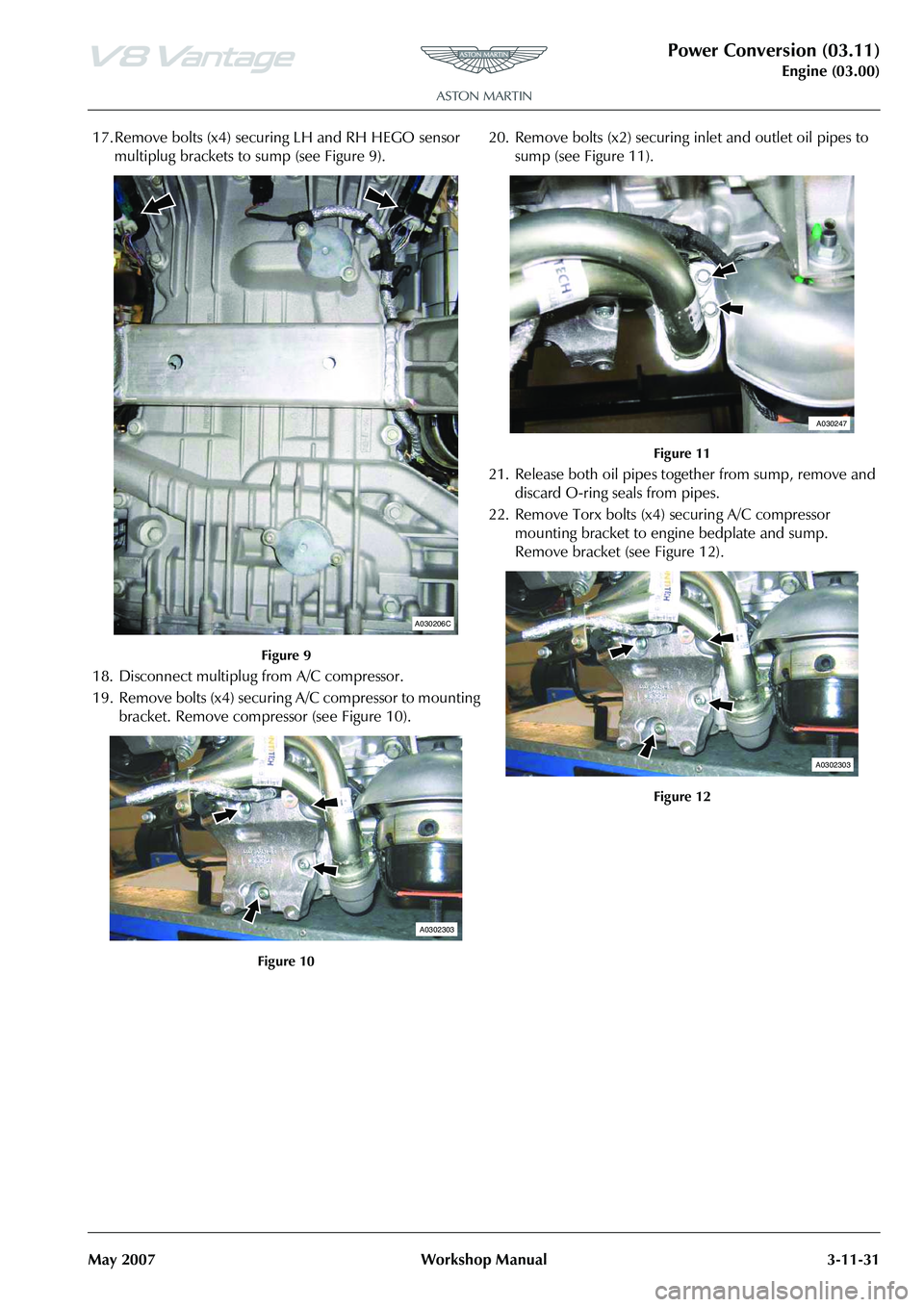
Power Conversion (03.11)
Engine (03.00)
May 2007 Workshop Manual 3-11-31
17. Remove bolts (x4) securing LH and RH HEGO sensor
multiplug brackets to sump (see Figure 9).
Figure 9
18. Disconnect multiplug from A/C compressor.
19. Remove bolts (x4) securing A/C compressor to mounting
bracket. Remove compressor (see Figure 10).
Figure 10
20. Remove bolts (x2) securing inlet and outlet oil pipes to sump (see Figure 11).
Figure 11
21. Release both oil pipes together from sump, remove and discard O-ring seals from pipes.
22. Remove Torx bolts (x4) securing A/C compressor
mounting bracket to engine bedplate and sump.
Remove bracket (see Figure 12).
Figure 12
A030206C
A0302303
A030247
A0302303
Page 404 of 947
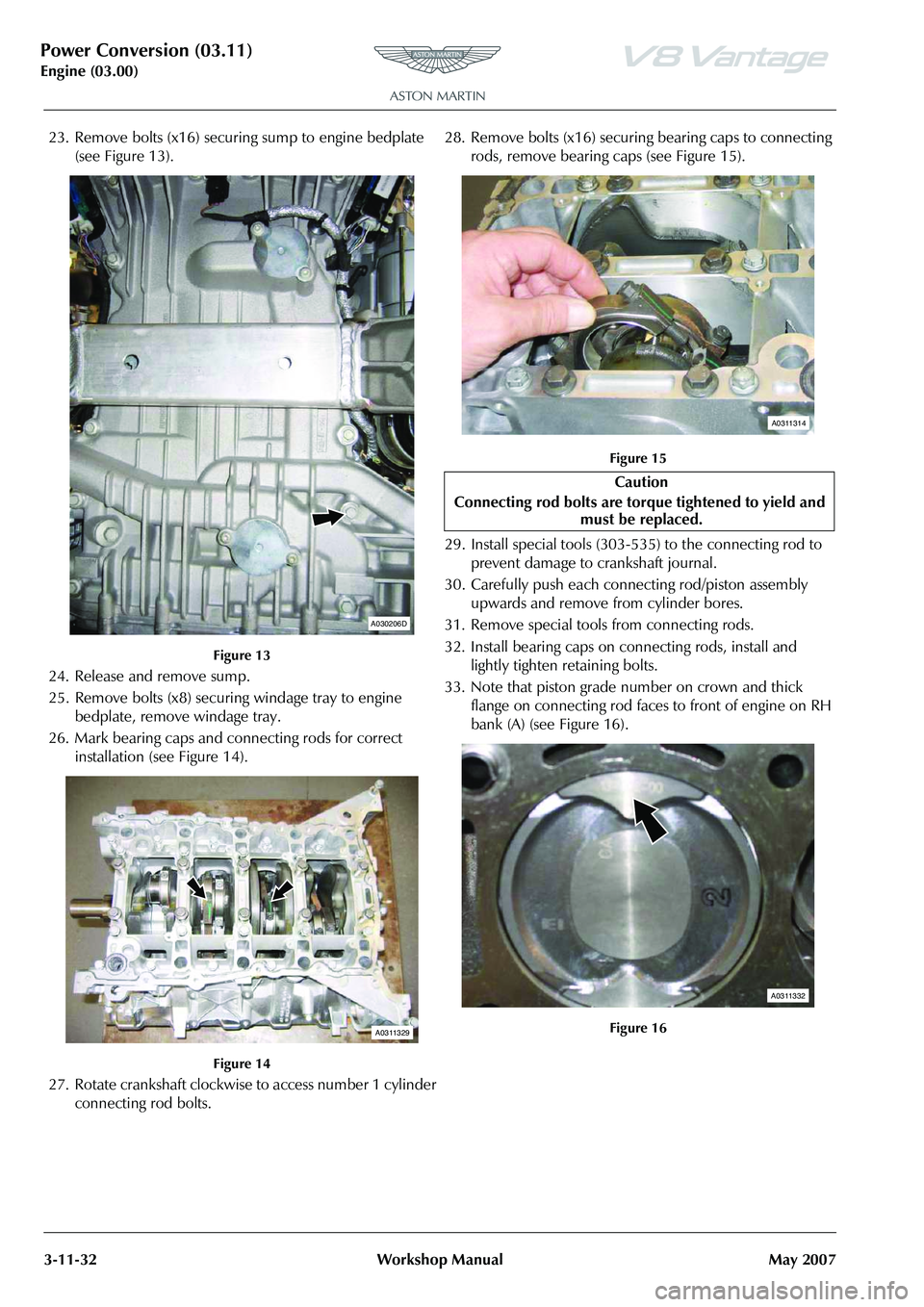
Power Conversion (03.11)
Engine (03.00)3-11-32 Workshop Manual May 2007
23. Remove bolts (x16) securing sump to engine bedplate
(see Figure 13).
Figure 13
24. Release and remove sump.
25. Remove bolts (x8) securing windage tray to engine bedplate, remove windage tray.
26. Mark bearing caps and connecting rods for correct installation (see Figure 14).
Figure 14
27. Rotate crankshaft clockwise to access number 1 cylinder
connecting rod bolts. 28. Remove bolts (x16) securing bearing caps to connecting
rods, remove bearing caps (see Figure 15).
Figure 15
29. Install special tools (303-535) to the connecting rod to prevent damage to crankshaft journal.
30. Carefully push each connecting rod/piston assembly upwards and remove from cylinder bores.
31. Remove special tools from connecting rods.
32. Install bearing caps on connecting rods, install and lightly tighten retaining bolts.
33. Note that piston grade number on crown and thick flange on connecting rod faces to front of engine on RH
bank (A) (see Figure 16).
Figure 16
A030206D
A0311329
Caution
Connecting rod bolts are tor qu
e tightened to yield and
mu st be replaced.
A0311314
A0311332
Page 405 of 947
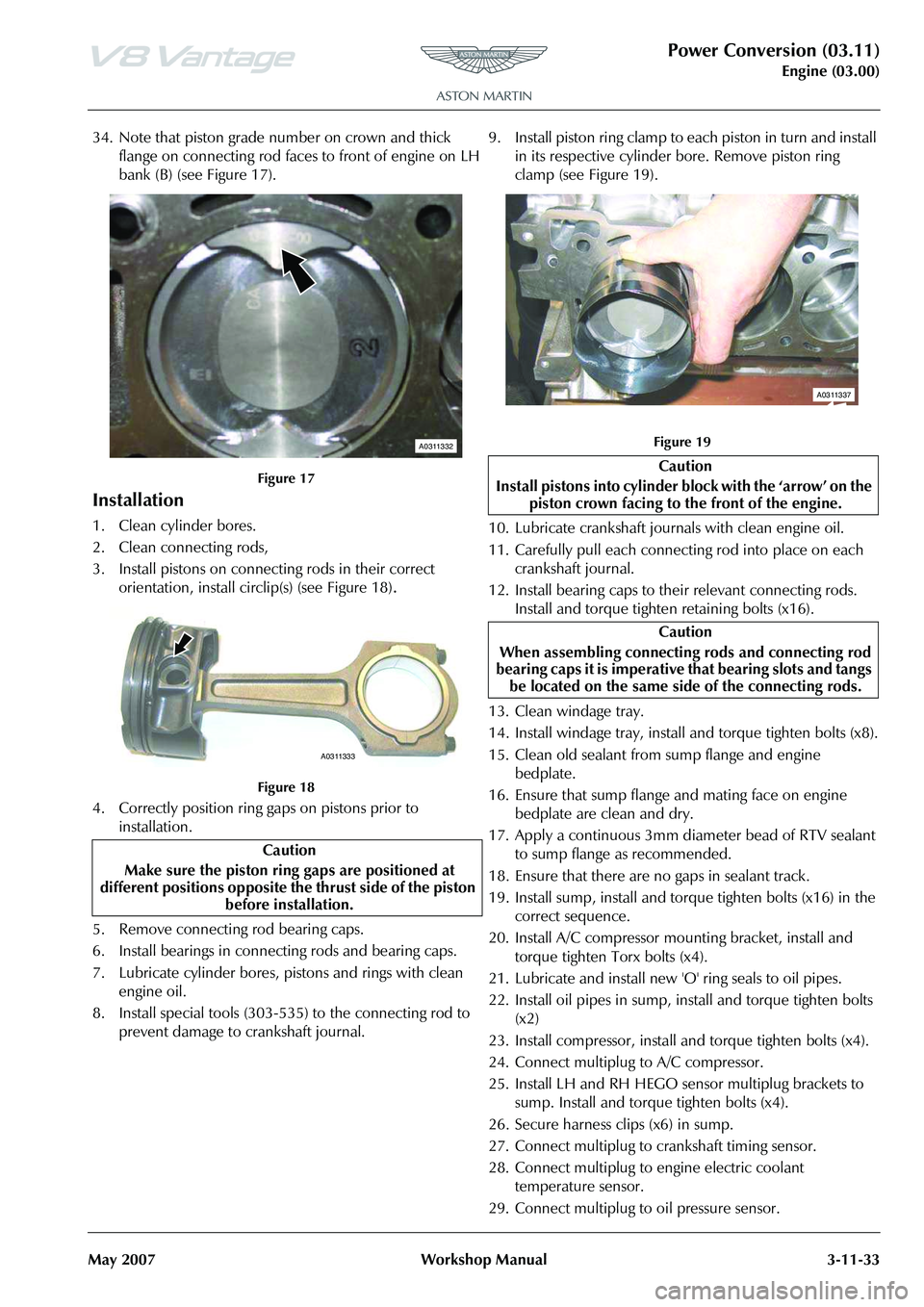
Power Conversion (03.11)
Engine (03.00)
May 2007 Workshop Manual 3-11-33
34. Note that piston grade number on crown and thick
flange on connecting rod faces to front of engine on LH
bank (B) (see Figure 17).
Figure 17
Installation
1. Clean cylinder bores.
2. Clean connecting rods,
3. Install pistons on connecting rods in their correct orientation, install circlip(s) (see Figure 18)
.
Figure 18
4. Correctly position ring gaps on pistons prior to installation.
5. Remove connecting rod bearing caps.
6. Install bearings in connecting rods and bearing caps.
7. Lubricate cylinder bores, pistons and rings with clean
engine oil.
8. Install special tools (303-535) to the connecting rod to prevent damage to crankshaft journal. 9. Install piston ring clamp to each piston in turn and install
in its respective cylinder bore. Remove piston ring
clamp (see Figure 19).
Figure 19
10. Lubricate crankshaft journals with clean engine oil.
11. Carefully pull each connecting rod into place on each crankshaft journal.
12. Install bearing caps to their relevant connecting rods. Install and torque tighten retaining bolts (x16).
13. Clean windage tray.
14. Install windage tray, install and torque tighten bolts (x8).
15. Clean old sealant from sump flange and engine bedplate.
16. Ensure that sump flange and mating face on engine bedplate are clean and dry.
17. Apply a continuous 3mm diameter bead of RTV sealant to sump flange as recommended.
18. Ensure that there are no gaps in sealant track.
19. Install sump, install and torque tighten bolts (x16) in the correct sequence.
20. Install A/C compressor mounting bracket, install and torque tighten Torx bolts (x4).
21. Lubricate and install new 'O' ring seals to oil pipes.
22. Install oil pipes in sump, install and torque tighten bolts (x2)
23. Install compressor, install and torque tighten bolts (x4).
24. Connect multiplug to A/C compressor.
25. Install LH and RH HEGO se nsor multiplug brackets to
sump. Install and torque tighten bolts (x4).
26. Secure harness clips (x6) in sump.
27. Connect multiplug to crankshaft timing sensor.
28. Connect multiplug to engine electric coolant temperature sensor.
29. Connect multiplug to oil pressure sensor.
Caution
Make sure the piston ring gaps are positioned at
different positions opposite the thrust side of the piston
before installation.
A0311332
A0311333
Caution
Install pistons into cylinder block with the
Page 406 of 947
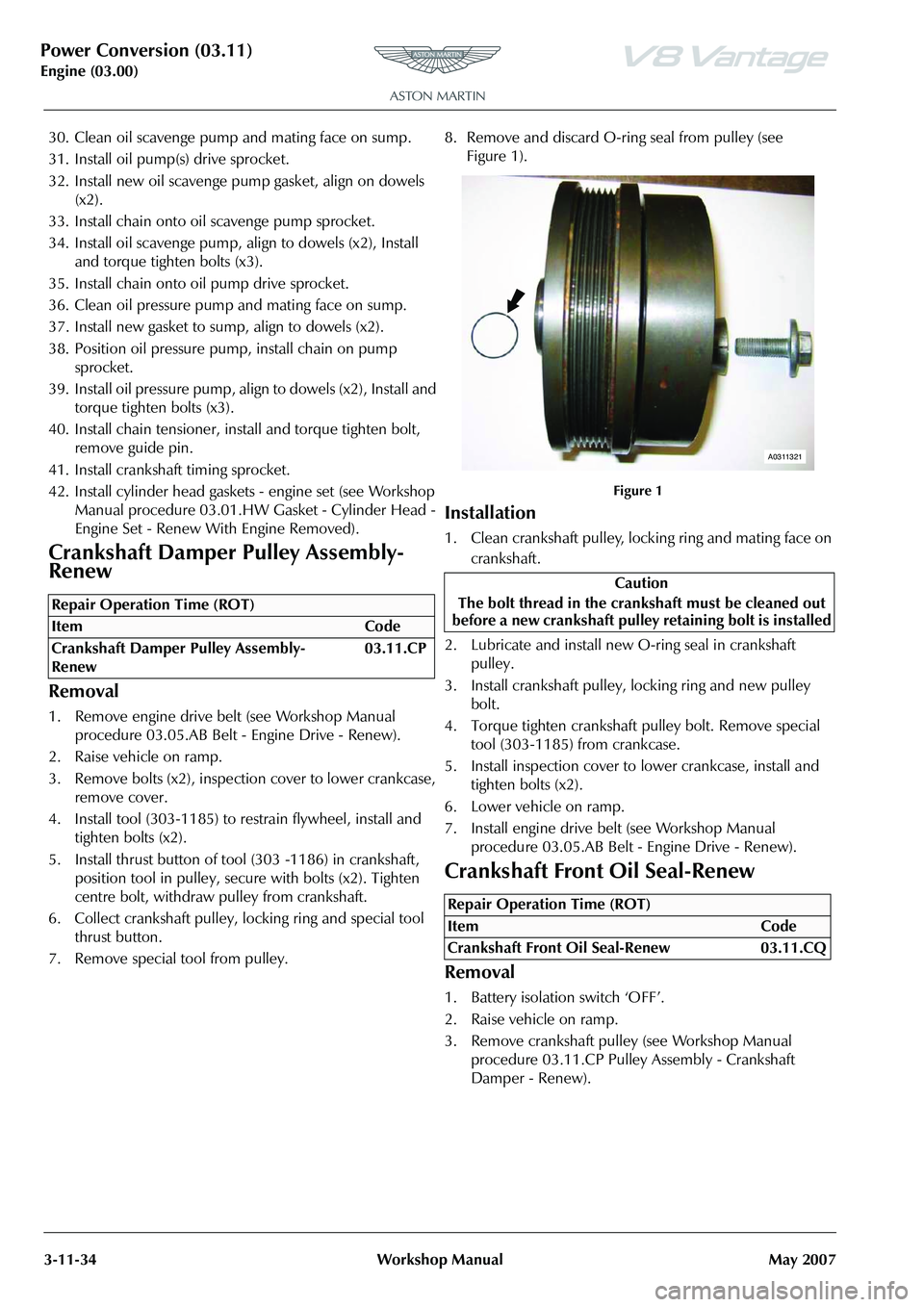
Power Conversion (03.11)
Engine (03.00)3-11-34 Workshop Manual May 2007
30. Clean oil scavenge pump and mating face on sump.
31. Install oil pump(s) drive sprocket.
32. Install new oil scavenge pump gasket, align on dowels
(x2).
33. Install chain onto oil scavenge pump sprocket.
34. Install oil scavenge pump, align to dowels (x2), Install and torque tighten bolts (x3).
35. Install chain onto oil pump drive sprocket.
36. Clean oil pressure pump and mating face on sump.
37. Install new gasket to sump, align to dowels (x2).
38. Position oil pressure pump, install chain on pump sprocket.
39. Install oil pressure pump, alig n to dowels (x2), Install and
torque tighten bolts (x3).
40. Install chain tensioner, install and torque tighten bolt, remove guide pin.
41. Install crankshaft timing sprocket.
42. Install cylinder head gaskets - engine set (see Workshop Manual procedure 03.01.HW Gasket - Cylinder Head -
Engine Set - Renew With Engine Removed).
Crankshaft Damper Pulley Assembly-
Renew
Removal
1. Remove engine drive belt (see Workshop Manual procedure 03.05.AB Belt - Engine Drive - Renew).
2. Raise vehicle on ramp.
3. Remove bolts (x2), inspection cover to lower crankcase, remove cover.
4. Install tool (303-1185) to restrain flywheel, install and tighten bolts (x2).
5. Install thrust button of tool (303 -1186) in crankshaft,
position tool in pulley, secure with bolts (x2). Tighten
centre bolt, withdraw pu lley from crankshaft.
6. Collect crankshaft pulley, locking ring and special tool thrust button.
7. Remove special tool from pulley. 8. Remove and discard O-ring seal from pulley (see
Figure 1).
Figure 1
Installation
1. Clean crankshaft pulley, locking ring and mating face on
crankshaft.
2. Lubricate and install new O-ring seal in crankshaft pulley.
3. Install crankshaft pulley, locking ring and new pulley bolt.
4. Torque tighten crankshaft pulley bolt. Remove special tool (303-1185) from crankcase.
5. Install inspection cover to lower crankcase, install and tighten bolts (x2).
6. Lower vehicle on ramp.
7. Install engine drive belt (see Workshop Manual procedure 03.05.AB Belt - Engine Drive - Renew).
Crankshaft Front Oil Seal-Renew
Removal
1. Battery isolation switch ‘OFF’.
2. Raise vehicle on ramp.
3. Remove crankshaft pulley (see Workshop Manual procedure 03.11.CP Pulley Assembly - Crankshaft
Damper - Renew).
Repair Operation Time (ROT)
Caution
The bolt thread in the cran kshaft must be cleaned out
before a new crankshaft pulley retaining bolt is installed
Repair Operation Time (ROT)
ItemCode
Crankshaft Front Oi l Seal-Renew 03.11.CQ
A0311321
Page 408 of 947
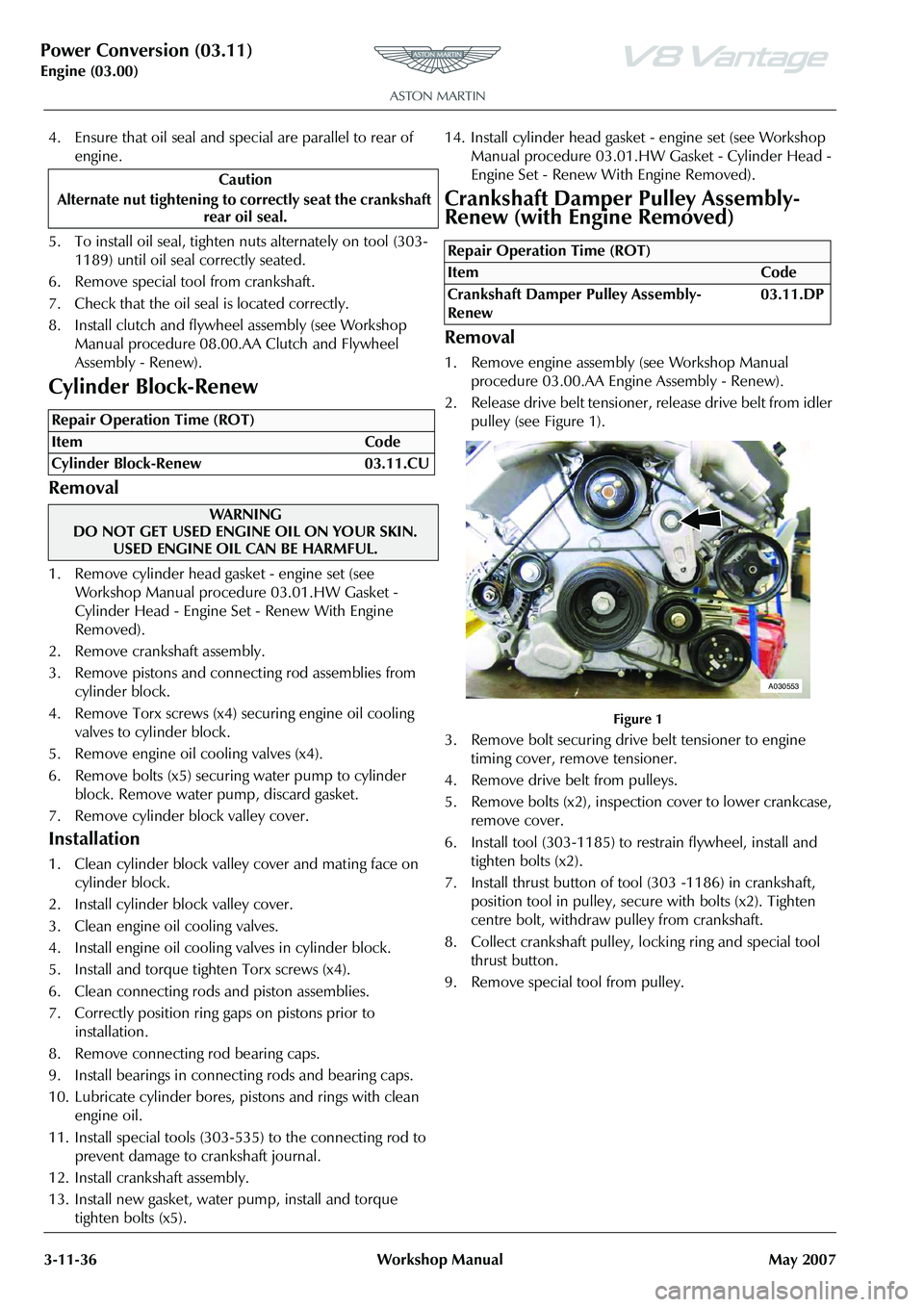
Power Conversion (03.11)
Engine (03.00)3-11-36 Workshop Manual May 2007
4. Ensure that oil seal and special are parallel to rear of
engine.
5. To install oil seal, tighten nuts alternately on tool (303- 1189) until oil seal correctly seated.
6. Remove special tool from crankshaft.
7. Check that the oil seal is located correctly.
8. Install clutch and flywheel assembly (see Workshop Manual procedure 08.00.AA Clutch and Flywheel
Assembly - Renew).
Cylinder Block-Renew
Removal
1. Remove cylinder head gasket - engine set (see Workshop Manual procedure 03.01.HW Gasket -
Cylinder Head - Engine Set - Renew With Engine
Removed).
2. Remove crankshaft assembly.
3. Remove pistons and connecting rod assemblies from cylinder block.
4. Remove Torx screws (x4) securing engine oil cooling
valves to cylinder block.
5. Remove engine oil cooling valves (x4).
6. Remove bolts (x5) securing water pump to cylinder block. Remove water pump, discard gasket.
7. Remove cylinder block valley cover.
Installation
1. Clean cylinder block valley cover and mating face on cylinder block.
2. Install cylinder block valley cover.
3. Clean engine oil cooling valves.
4. Install engine oil cooling valves in cylinder block.
5. Install and torque tighten Torx screws (x4).
6. Clean connecting rods and piston assemblies.
7. Correctly position ring gaps on pistons prior to installation.
8. Remove connecting rod bearing caps.
9. Install bearings in connecting rods and bearing caps.
10. Lubricate cylinder bores, pistons and rings with clean engine oil.
11. Install special tools (303-535) to the connecting rod to prevent damage to crankshaft journal.
12. Install crankshaft assembly.
13. Install new gasket, water pump, install and torque tighten bolts (x5). 14. Install cylinder head gasket - engine set (see Workshop
Manual procedure 03.01.HW Gasket - Cylinder Head -
Engine Set - Renew Wi th Engine Removed).
Crankshaft Damper Pulley Assembly-
Renew (with Engine Removed)
Removal
1. Remove engine assembly (see Workshop Manual
procedure 03.00.AA Engine Assembly - Renew).
2. Release drive belt tensioner, release drive belt from idler pulley (see Figure 1).
Figure 1
3. Remove bolt securing drive belt tensioner to engine timing cover, remove tensioner.
4. Remove drive belt from pulleys.
5. Remove bolts (x2), inspection cover to lower crankcase, remove cover.
6. Install tool (303-1185) to restrain flywheel, install and tighten bolts (x2).
7. Install thrust button of tool (303 -1186) in crankshaft,
position tool in pulley, secure with bolts (x2). Tighten
centre bolt, withdraw pulley from crankshaft.
8. Collect crankshaft pulley, locking ring and special tool thrust button.
9. Remove special tool from pulley.
Caution
Alternate nut tightening to correctly seat the crankshaft rear oil seal.
Repair Operation Time (ROT)
WAR NI NG
DO NOT GET USED ENGINE OIL ON YOUR SKIN.
USED ENGINE OIL CAN BE HARMFUL.
Repair Operation Time (ROT)
ItemCode
Crankshaft Damper Pulley Assembly-
Renew 03.11.DP
A030553
Page 417 of 947
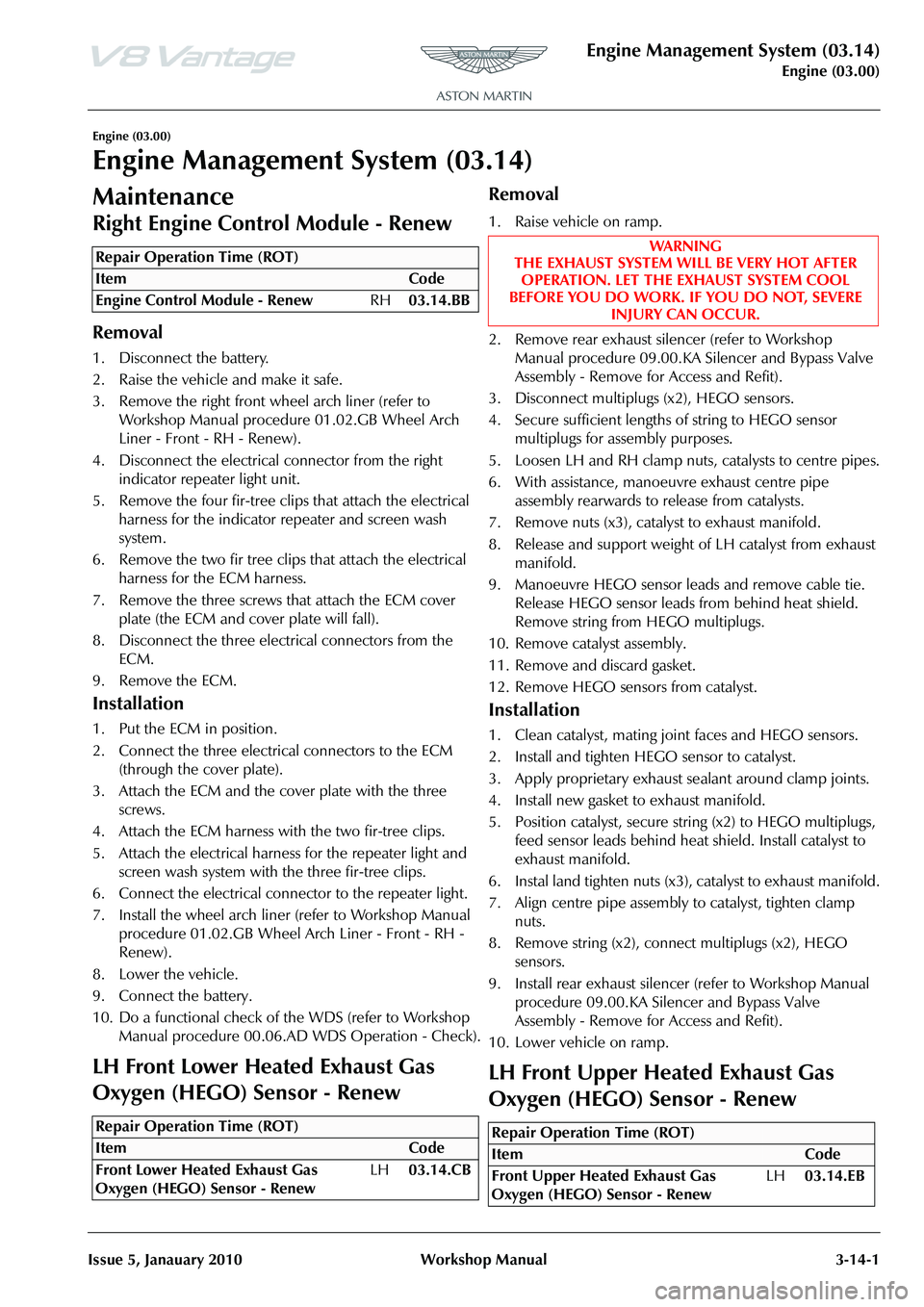
Engine Management System (03.14)
Engine (03.00)
Issue 5, Janauary 2010 Workshop Manual 3-14-1
Engine (03.00)
Engine Management System (03.14)
Maintenance
LH Front Lower Heated Exhaust Gas
Oxygen (HEGO) Sensor - Renew
Removal
1. Raise vehicle on ramp.
2. Remove rear exhaust silencer (refer to Workshop Manual procedure 09.00.KA Silencer and Bypass Valve
Assembly - Remo ve for Access and Refit).
3. Disconnect multiplugs (x2), HEGO sensors.
4. Secure sufficient lengths of string to HEGO sensor multiplugs for assembly purposes.
5. Loosen LH and RH clamp nuts, catalysts to centre pipes.
6. With assistance, manoeuvre exhaust centre pipe assembly rearwards to release from catalysts.
7. Remove nuts (x3), catalyst to exhaust manifold.
8. Release and support weight of LH catalyst from exhaust
manifold.
9. Manoeuvre HEGO sensor leads and remove cable tie. Release HEGO sensor leads from behind heat shield.
Remove string from HEGO multiplugs.
10. Remove catalyst assembly.
11. Remove and discard gasket.
12. Remove HEGO sens ors from catalyst.
Installation
1. Clean catalyst, mating joint faces and HEGO sensors.
2. Install and tighten HEGO sensor to catalyst.
3. Apply proprietary exhaust se alant around clamp joints.
4. Install new gasket to exhaust manifold.
5. Position catalyst, secure string (x2) to HEGO multiplugs, feed sensor leads behind heat shield. Install catalyst to
exhaust manifold.
6. Instal land tighten nuts (x3), catalyst to exhaust manifold.
7. Align centre pipe assembly to catalyst, tighten clamp
nuts.
8. Remove string (x2), conne ct multiplugs (x2), HEGO
sensors.
9. Install rear exhaust silencer (refer to Workshop Manual procedure 09.00.KA Silencer and Bypass Valve
Assembly - Remo ve for Access and Refit).
10. Lower vehicle on ramp.
LH Front Upper Heated Exhaust Gas
Oxygen (HEGO) Sensor - Renew
Repair Operation Time (ROT)
Repair Operation Time (ROT)
WA R N I N G
THE EXHAUST SYSTEM WILL BE VERY HOT AFTER OPERATION. LET THE EXHAUST SYSTEM COOL
BEFORE YOU DO WORK. IF YOU DO NOT, SEVERE
INJURY CAN OCCUR.
Repair Operation Time (ROT)
Page 418 of 947
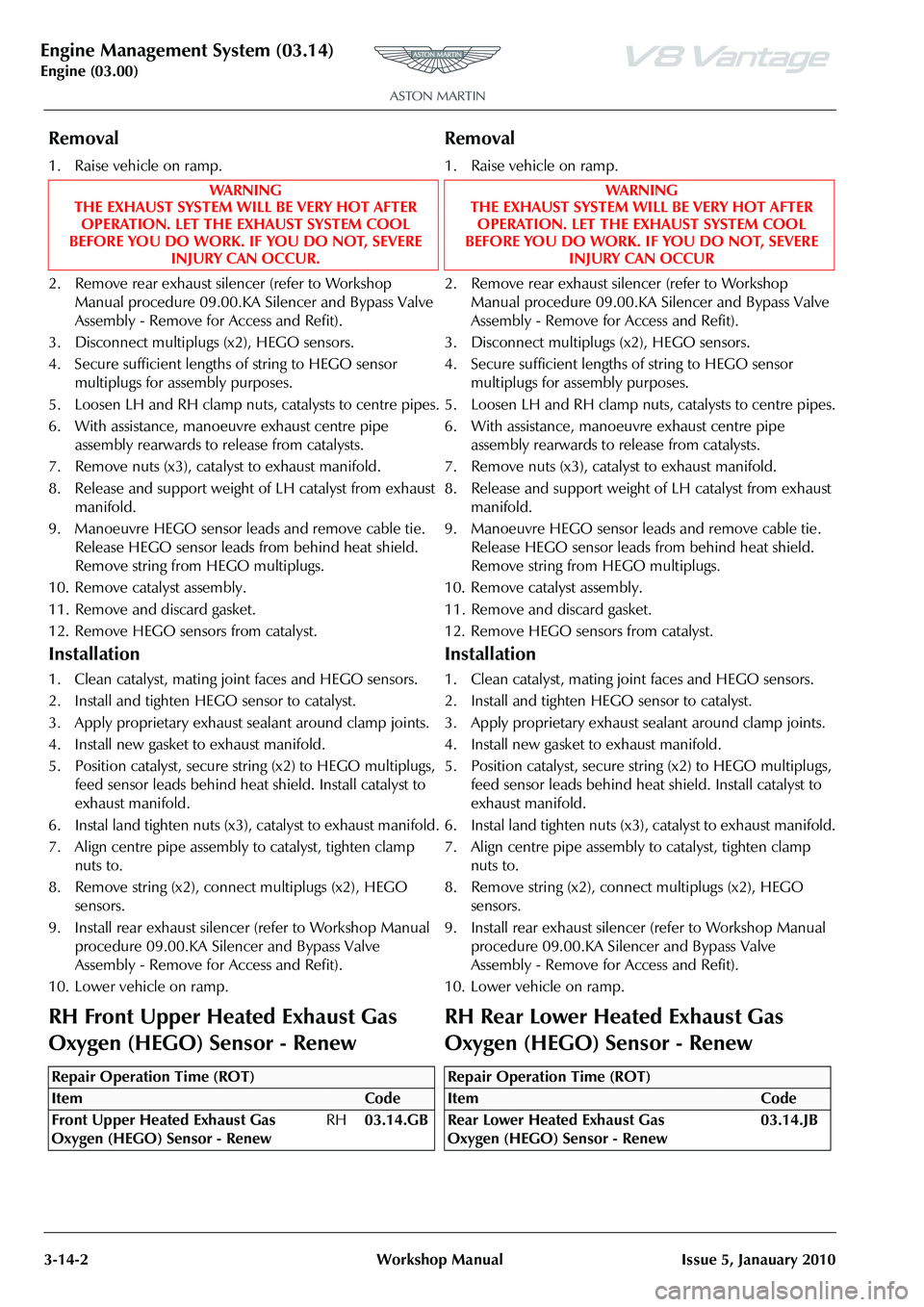
Engine Management System (03.14)
Engine (03.00)3-14-2 Workshop Manual Issue 5, Janauary 2010
Removal
1. Raise vehicle on ramp.
2. Remove rear exhaust silencer (refer to Workshop Manual procedure 09.00.KA Silencer and Bypass Valve
Assembly - Remove for Access and Refit).
3. Disconnect multiplugs (x2), HEGO sensors.
4. Secure sufficient lengths of string to HEGO sensor multiplugs for assembly purposes.
5. Loosen LH and RH clamp nuts, catalysts to centre pipes.
6. With assistance, manoeuvre exhaust centre pipe assembly rearwards to release from catalysts.
7. Remove nuts (x3), catalyst to exhaust manifold.
8. Release and support weight of LH catalyst from exhaust manifold.
9. Manoeuvre HEGO sensor leads and remove cable tie. Release HEGO sensor leads from behind heat shield.
Remove string from HEGO multiplugs.
10. Remove catalyst assembly.
11. Remove and discard gasket.
12. Remove HEGO sensors from catalyst.
Installation
1. Clean catalyst, mating joint faces and HEGO sensors.
2. Install and tighten HEGO sensor to catalyst.
3. Apply proprietary exhaust sealant around clamp joints.
4. Install new gasket to exhaust manifold.
5. Position catalyst, secure string (x2) to HEGO multiplugs, feed sensor leads behind heat shield. Install catalyst to
exhaust manifold.
6. Instal land tighten nuts (x3), catalyst to exhaust manifold.
7. Align centre pipe assembly to catalyst, tighten clamp nuts to.
8. Remove string (x2), connect multiplugs (x2), HEGO sensors.
9. Install rear exhaust silencer (refer to Workshop Manual
procedure 09.00.KA Silencer and Bypass Valve
Assembly - Remove for Access and Refit).
10. Lower vehicle on ramp.
RH Front Upper Heated Exhaust Gas
Oxygen (HEGO) Sensor - Renew
Removal
1. Raise vehicle on ramp.
2. Remove rear exhaust silencer (refer to Workshop Manual procedure 09.00.KA Silencer and Bypass Valve
Assembly - Remove for Access and Refit).
3. Disconnect multiplugs (x2), HEGO sensors.
4. Secure sufficient lengths of string to HEGO sensor
multiplugs for assembly purposes.
5. Loosen LH and RH clamp nuts, catalysts to centre pipes.
6. With assistance, manoeuvre exhaust centre pipe assembly rearwards to release from catalysts.
7. Remove nuts (x3), catalyst to exhaust manifold.
8. Release and support weight of LH catalyst from exhaust
manifold.
9. Manoeuvre HEGO sensor leads and remove cable tie. Release HEGO sensor leads from behind heat shield.
Remove string from HEGO multiplugs.
10. Remove catalyst assembly.
11. Remove and discard gasket.
12. Remove HEGO sensors from catalyst.
Installation
1. Clean catalyst, mating joint faces and HEGO sensors.
2. Install and tighten HEGO sensor to catalyst.
3. Apply proprietary exhaust sealant around clamp joints.
4. Install new gasket to exhaust manifold.
5. Position catalyst, secure string (x2) to HEGO multiplugs, feed sensor leads behind heat shield. Install catalyst to
exhaust manifold.
6. Instal land tighten nuts (x3), catalyst to exhaust manifold.
7. Align centre pipe assembly to catalyst, tighten clamp nuts to.
8. Remove string (x2), connect multiplugs (x2), HEGO sensors.
9. Install rear exhaust silencer (refer to Workshop Manual procedure 09.00.KA Silencer and Bypass Valve
Assembly - Remove for Access and Refit).
10. Lower vehicle on ramp.
RH Rear Lower Heated Exhaust Gas
Oxygen (HEGO) Sensor - Renew
WAR NI NG
THE EXHAUST SYSTEM WILL BE VERY HOT AFTER OPERATION. LET THE EXHAUST SYSTEM COOL
BEFORE YOU DO WORK. IF YOU DO NOT, SEVERE INJURY CAN OCCUR.
Repair Operation Time (ROT)
WAR NI NG
THE EXHAUST SYSTEM WILL BE VERY HOT AFTER OPERATION. LET THE EXHAUST SYSTEM COOL
BEFORE YOU DO WORK. IF YOU DO NOT, SEVERE INJURY CAN OCCUR
Repair Operation Time (ROT)
ItemCode
Rear Lower Heated Exhaust Gas
Oxygen (HEGO) Sensor - Renew 03.14.JB
Page 419 of 947
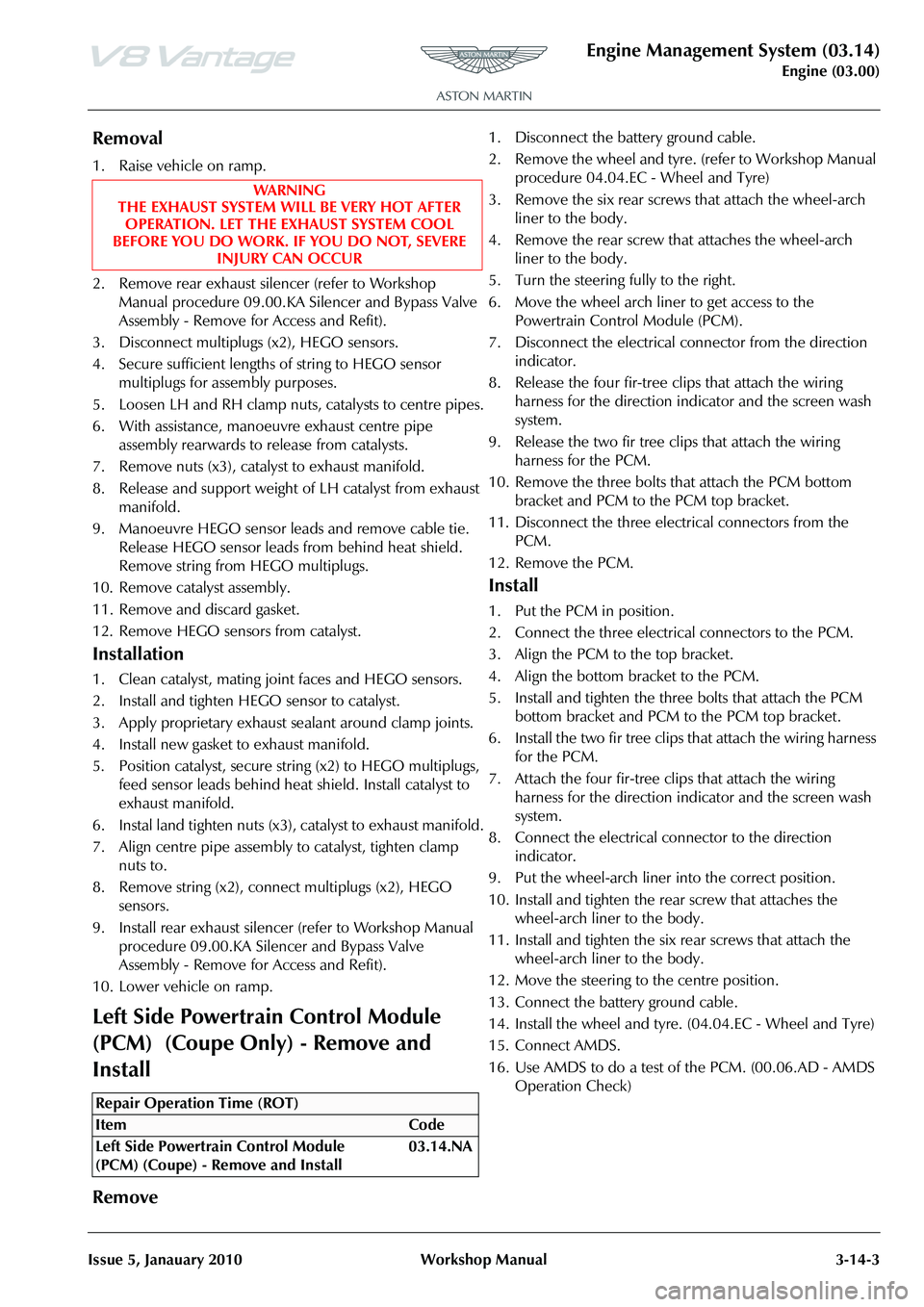
Engine Management System (03.14)
Engine (03.00)
Issue 5, Janauary 2010 Workshop Manual 3-14-3
Removal
1. Raise vehicle on ramp.
2. Remove rear exhaust silencer (refer to Workshop Manual procedure 09.00.KA Silencer and Bypass Valve
Assembly - Remove for Access and Refit).
3. Disconnect multiplugs (x2), HEGO sensors.
4. Secure sufficient lengths of string to HEGO sensor multiplugs for assembly purposes.
5. Loosen LH and RH clamp nuts, catalysts to centre pipes.
6. With assistance, manoeuvre exhaust centre pipe assembly rearwards to release from catalysts.
7. Remove nuts (x3), catalyst to exhaust manifold.
8. Release and support weight of LH catalyst from exhaust manifold.
9. Manoeuvre HEGO sensor leads and remove cable tie. Release HEGO sensor leads from behind heat shield.
Remove string from HEGO multiplugs.
10. Remove catalyst assembly.
11. Remove and discard gasket.
12. Remove HEGO sensors from catalyst.
Installation
1. Clean catalyst, mating joint faces and HEGO sensors.
2. Install and tighten HEGO sensor to catalyst.
3. Apply proprietary exhaust se alant around clamp joints.
4. Install new gasket to exhaust manifold.
5. Position catalyst, secure string (x2) to HEGO multiplugs, feed sensor leads behind heat shield. Install catalyst to
exhaust manifold.
6. Instal land tighten nuts (x3), catalyst to exhaust manifold.
7. Align centre pipe assembly to catalyst, tighten clamp
nuts to.
8. Remove string (x2), conne ct multiplugs (x2), HEGO
sensors.
9. Install rear exhaust silencer (refer to Workshop Manual procedure 09.00.KA Silencer and Bypass Valve
Assembly - Remove for Access and Refit).
10. Lower vehicle on ramp.
Left Side Powertrain Control Module
(PCM) (Coupe Only) - Remove and
Install
Remove
1. Disconnect the ba ttery ground cable.
2. Remove the wheel and tyre. (refer to Workshop Manual procedure 04.04.EC - Wheel and Tyre)
3. Remove the six rear screws that attach the wheel-arch liner to the body.
4. Remove the rear screw that attaches the wheel-arch liner to the body.
5. Turn the steering fully to the right.
6. Move the wheel arch liner to get access to the Powertrain Control Module (PCM).
7. Disconnect the electrical connector from the direction
indicator.
8. Release the four fi r-tree clips that attach the wiring
harness for the direction indi cator and the screen wash
system.
9. Release the two fir tree clips that attach the wiring harness for the PCM.
10. Remove the three bolts that attach the PCM bottom bracket and PCM to the PCM top bracket.
11. Disconnect the three electrical connectors from the PCM.
12. Remove the PCM.
Install
1. Put the PCM in position.
2. Connect the three electrical connectors to the PCM.
3. Align the PCM to the top bracket.
4. Align the bottom bracket to the PCM.
5. Install and tighten the three bolts that attach the PCM bottom bracket and PCM to the PCM top bracket.
6. Install the two fir tree clips that attach the wiring harness for the PCM.
7. Attach the four fir-tree cl ips that attach the wiring
harness for the direction indi cator and the screen wash
system.
8. Connect the electrical connector to the direction indicator.
9. Put the wheel-arch liner into the correct position.
10. Install and tighten the rear screw that attaches the wheel-arch liner to the body.
11. Install and tighten the six rear screws that attach the wheel-arch liner to the body.
12. Move the steering to the centre position.
13. Connect the battery ground cable.
14. Install the wheel and tyre. (04.04.EC - Wheel and Tyre)
15. Connect AMDS.
16. Use AMDS to do a test of the PCM. (00.06.AD - AMDS Operation Check)
WA R N I N G
THE EXHAUST SYSTEM WILL BE VERY HOT AFTER OPERATION. LET THE EXHAUST SYSTEM COOL
BEFORE YOU DO WORK. IF YOU DO NOT, SEVERE
INJURY CAN OCCUR
Repair Operation Time (ROT)
Page 423 of 947
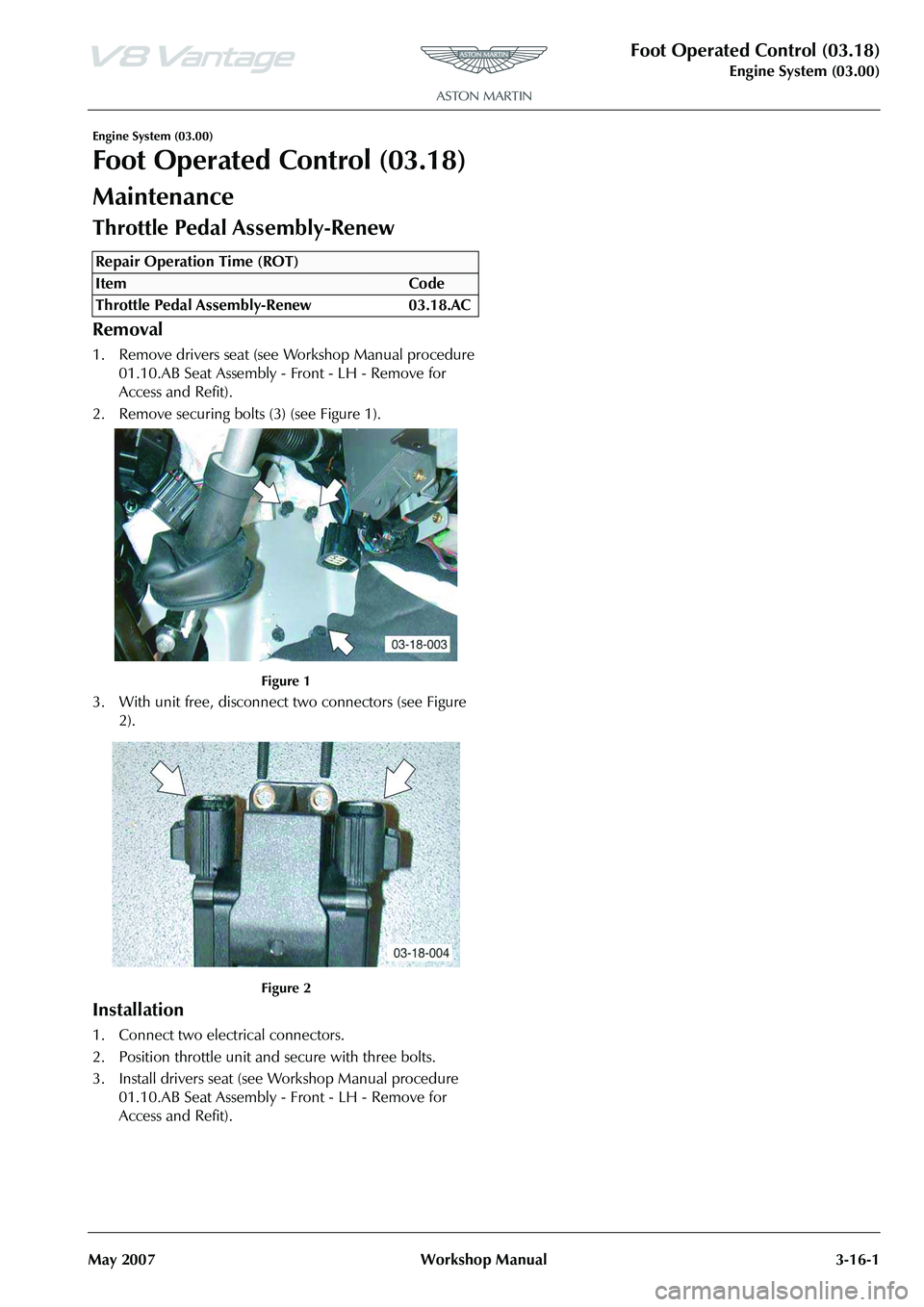
Foot Operated Control (03.18)
Engine System (03.00)
May 2007 Workshop Manual 3-16-1
Engine System (03.00)
Foot Operated Control (03.18)
Maintenance
Throttle Pedal Assembly-Renew
Removal
1. Remove drivers seat (see Workshop Manual procedure
01.10.AB Seat Assembly - Front - LH - Remove for
Access and Refit).
2. Remove securing bolts (3) (see Figure 1).
Figure 1
3. With unit free, disconnect two connectors (see Figure
2).
Figure 2
Installation
1. Connect two electrical connectors.
2. Position throttle unit and secure with three bolts.
3. Install drivers seat (see Workshop Manual procedure 01.10.AB Seat Assembly - Front - LH - Remove for
Access and Refit).
Repair Operation Time (ROT)
Page 429 of 947
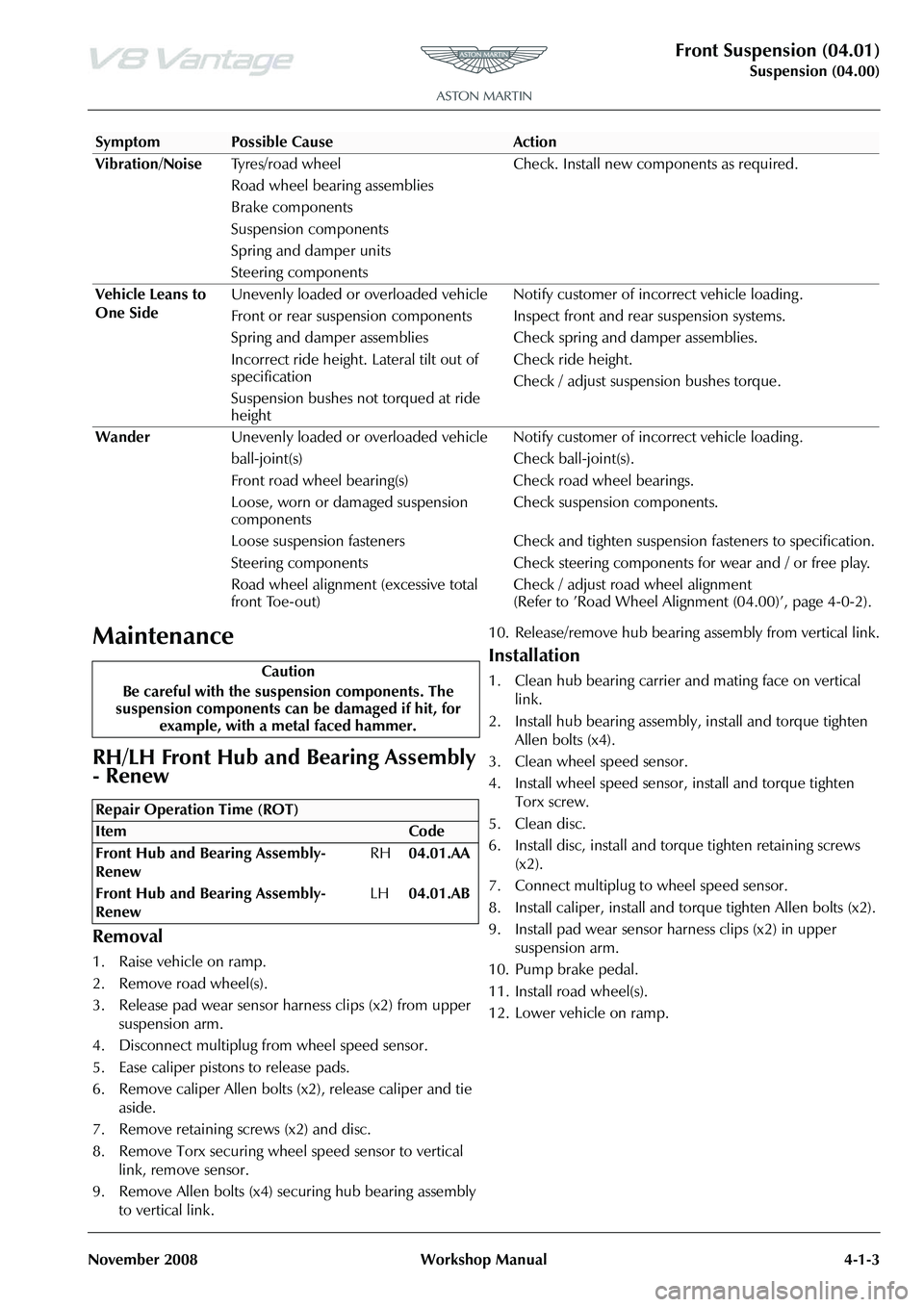
Front Suspension (04.01)
Suspension (04.00)
November 2008 Workshop Manual 4-1-3
Maintenance
RH/LH Front Hub and Bearing Assembly
- Renew
Removal
1. Raise vehicle on ramp.
2. Remove road wheel(s).
3. Release pad wear sensor harness clips (x2) from upper suspension arm.
4. Disconnect multiplug from wheel speed sensor.
5. Ease caliper pistons to release pads.
6. Remove caliper Allen bolts (x2), release caliper and tie
aside.
7. Remove retaining screws (x2) and disc.
8. Remove Torx securing wheel speed sensor to vertical link, remove sensor.
9. Remove Allen bolts (x4) securing hub bearing assembly to vertical link. 10. Release/remove hub bearing assembly from vertical link.
Installation
1. Clean hub bearing carrier and mating face on vertical
link.
2. Install hub bearing assembly, install and torque tighten Allen bolts (x4).
3. Clean wheel speed sensor.
4. Install wheel speed sensor, install and torque tighten Torx screw.
5. Clean disc.
6. Install disc, install and torque tighten retaining screws (x2).
7. Connect multiplug to wheel speed sensor.
8. Install caliper, install and to rque tighten Allen bolts (x2).
9. Install pad wear sensor harness clips (x2) in upper suspension arm.
10. Pump brake pedal.
11. Install road wheel(s).
12. Lower vehicle on ramp.
Vibration/Noise
Tyres/road wheel
Road wheel bearing assemblies
Brake components
Suspension components
Spring and damper units
Steering components Check. Install new components as required.
Vehicle Leans to
One Side Unevenly loaded or overloaded vehicle Notif
y customer of incorrect vehicle loading .
Front or rear suspension components Inspect front and rear suspension systems.
Spring and damper assemblies Check spring and damper assemblies.
Incorrect ride height. Lateral tilt out of
specification
Suspension bushes not torqued at ride
height Check ride height.
Check / adjust suspension bushes torque.
Wander Unevenly loaded or overloaded vehicle Notif y customer of incorrect vehicle loading .
ball-joint(s) Check ball-joint(s).
Front road wheel bearing(s) Check road wheel bearings.
Loose, worn or damaged suspension
components Check suspension components.
Loose suspension fasteners Check and tighten suspension fasteners to specification.
Steering components Check steering components for wear and / or free play.
Road wheel alignment (excessive total
front Toe-out) Check / adjust road wheel alignment
(Refer to ’Road Wheel Alignment (04.00)’, page 4-0-2).
SymptomPossible CauseAction
Caution
Be careful with the suspension components. The
suspension components can be damaged if hit, for example, with a metal faced hammer.
Repair Operation Time (ROT)