ECU ASTON MARTIN V8 VANTAGE 2010 Workshop Manual
[x] Cancel search | Manufacturer: ASTON MARTIN, Model Year: 2010, Model line: V8 VANTAGE, Model: ASTON MARTIN V8 VANTAGE 2010Pages: 947, PDF Size: 43.21 MB
Page 301 of 947
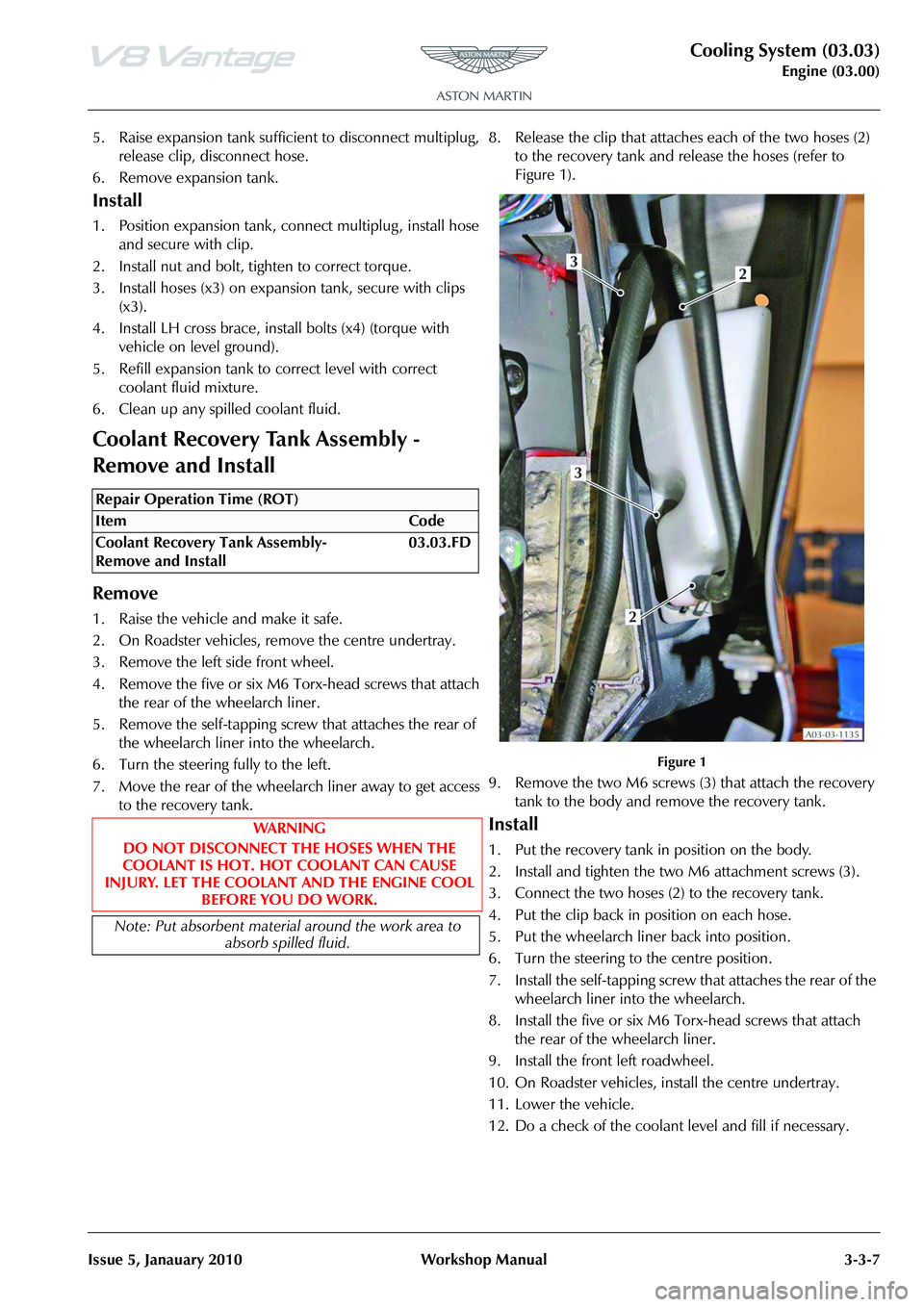
Cooling System (03.03)
Engine (03.00)
Issue 5, Janauary 2010 Workshop Manual 3-3-7
5. Raise expansion tank sufficient to disconnect multiplug, release clip, disconnect hose.
6. Remove expansion tank.
Install
1. Position expansion tank, connect multiplug , install hose and secure with clip.
2. Install nut and bolt, tighten to correct torque.
3. Install hoses (x3) on expansion tank, secure with clips (x3).
4. Install LH cross brace, inst all bolts (x4) (torque with
vehicle on level ground).
5. Refill expansion tank to correct level with correct
coolant fluid mixture.
6. Clean up any spilled coolant fluid.
Coolant Recovery Tank Assembly -
Remove and Install
Remove
1. Raise the vehicle and make it safe.
2. On Roadster vehicles, re move the centre undertray.
3. Remove the left side front wheel.
4. Remove the five or six M6 Torx-head screws that attach the rear of the wheelarch liner.
5. Remove the self-tapping screw that attaches the rear of the wheelarch liner into the wheelarch.
6. Turn the steering fully to the left.
7. Move the rear of the wheela rch liner away to get access
to the recovery tank. 8. Release the clip that attaches each of the two hoses (2)
to the recovery tank and release the hoses (refer to
Figure 1).
Figure 1
9. Remove the two M6 screws (3) that attach the recovery tank to the body and remove the recovery tank.
Install
1. Put the recovery tank in position on the body.
2. Install and tighten the two M6 attachment screws (3).
3. Connect the two hoses (2) to the recovery tank.
4. Put the clip back in position on each hose.
5. Put the wheelarch liner back into position.
6. Turn the steering to the centre position.
7. Install the self-tapping screw that attaches the rear of the wheelarch liner into the wheelarch.
8. Install the five or six M6 Torx-head screws that attach the rear of the wheelarch liner.
9. Install the front left roadwheel.
10. On Roadster vehicles, install the centre undertray.
11. Lower the vehicle.
12. Do a check of the coolant level and fill if necessary.
Repair Operation Time (ROT)
Page 302 of 947
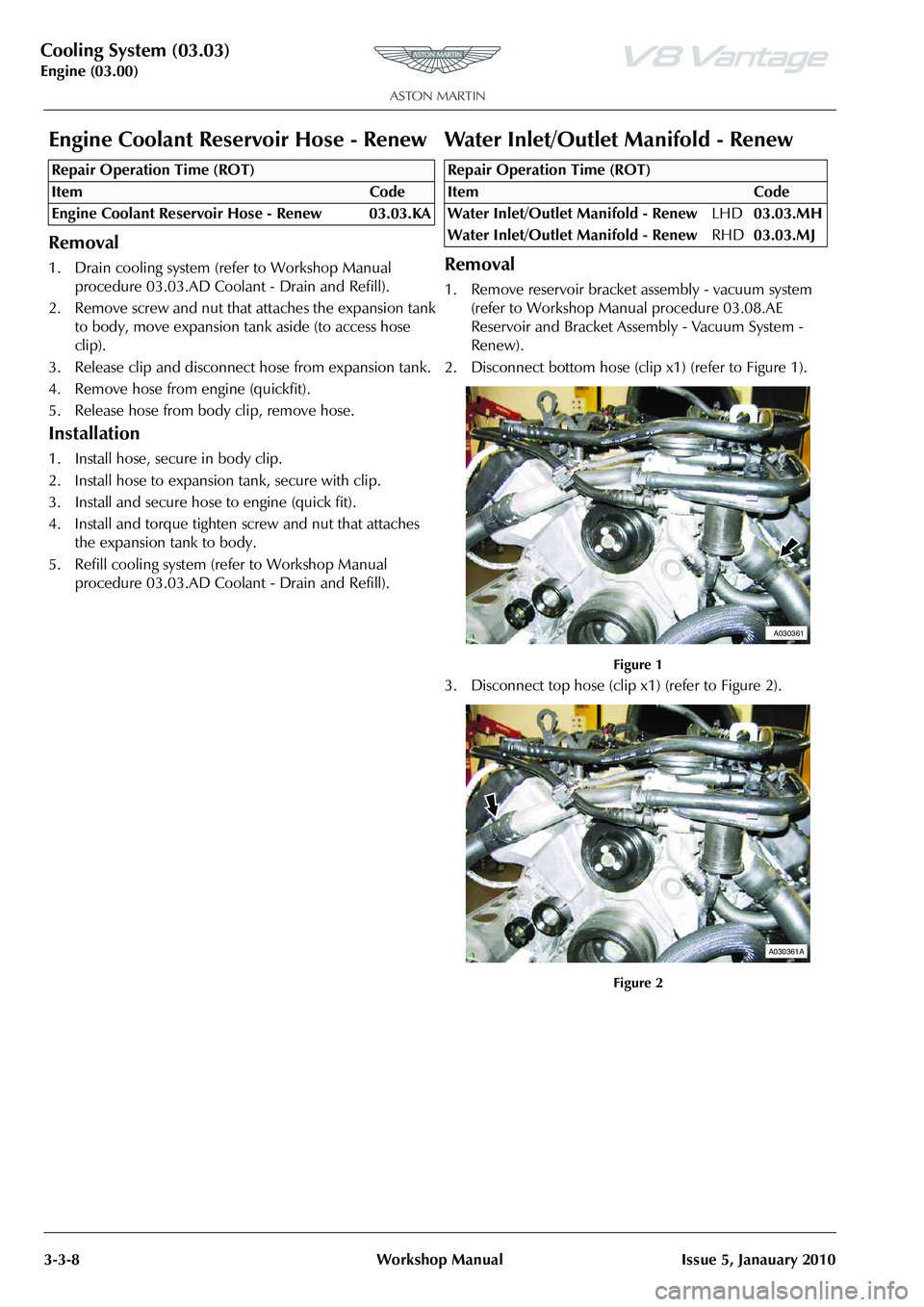
Cooling System (03.03)
Engine (03.00)3-3-8 Workshop Manual Issue 5, Janauary 2010
Engine Coolant Reservoir Hose - Renew
Removal
1. Drain cooling system (refer to Workshop Manual procedure 03.03.AD Coolant - Drain and Refill).
2. Remove screw and nut that attaches the expansion tank to body, move expansion tank aside (to access hose
clip).
3. Release clip and disconnect hose from expansion tank.
4. Remove hose from engine (quickfit).
5. Release hose from body clip, remove hose.
Installation
1. Install hose, secure in body clip.
2. Install hose to expansion tank, secure with clip.
3. Install and secure hose to engine (quick fit).
4. Install and torque tighten screw and nut that attaches the expansion tank to body.
5. Refill cooling system (refer to Workshop Manual procedure 03.03.AD Coolant - Drain and Refill).
Water Inlet/Outlet Manifold - Renew
Removal
1. Remove reservoir bracket assembly - vacuum system (refer to Workshop Manual procedure 03.08.AE
Reservoir and Bracket Assembly - Vacuum System -
Renew).
2. Disconnect bottom hose (cli p x1) (refer to Figure 1).
Figure 1
3. Disconnect top hose (clip x1) (refer to Figure 2).
Figure 2
Repair Operation Time (ROT)Repair Operation Time (ROT)
ItemCode
Water Inlet/Outlet Manifold - Renew LHD03.03.MH
Water Inlet/Outlet Manifold - Renew RHD03.03.MJ
A030361
A030361A
Page 324 of 947
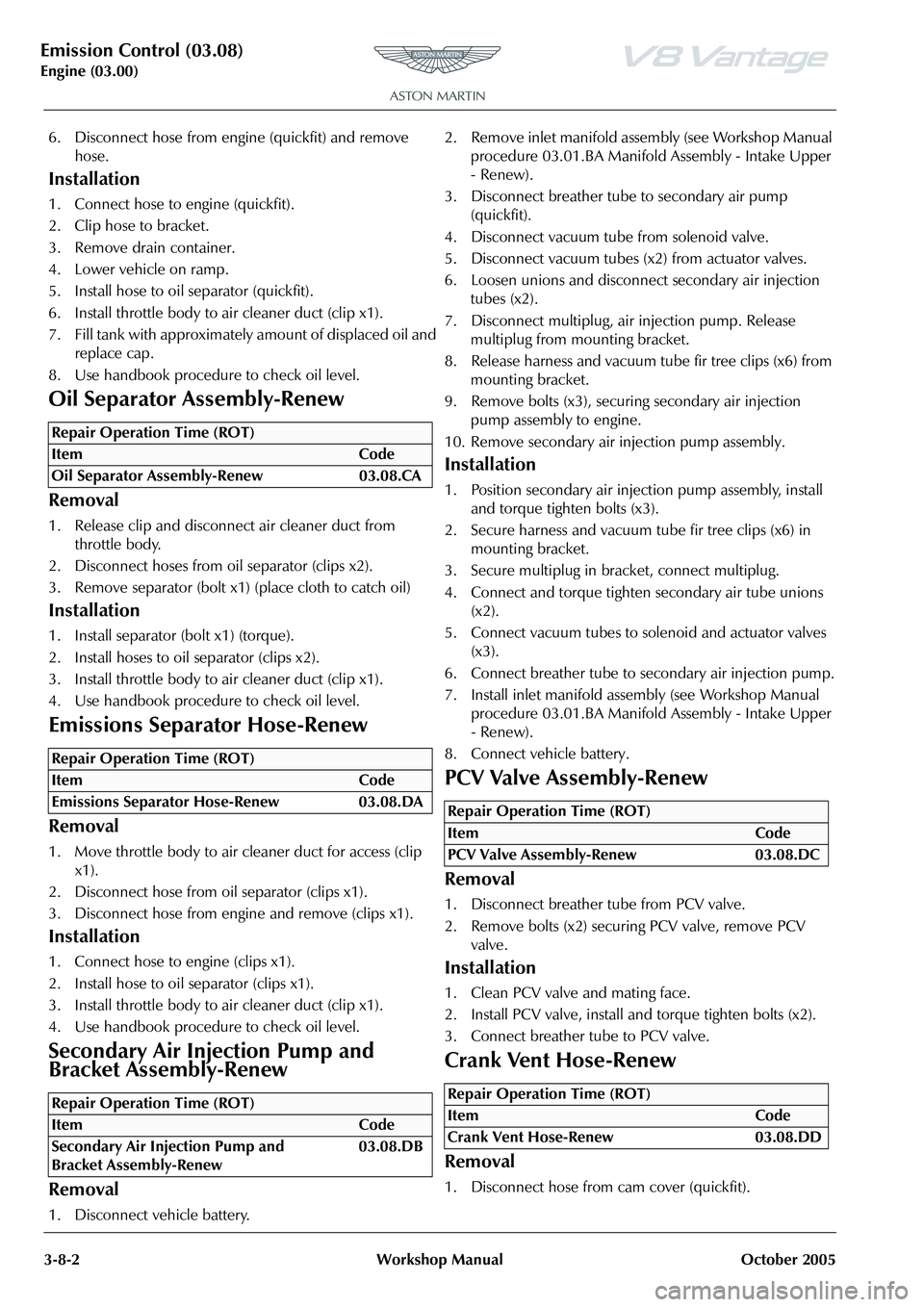
Emission Control (03.08)
Engine (03.00)3-8-2 Workshop Manual October 2005
6. Disconnect hose from engine (quickfit) and remove
hose.
Installation
1. Connect hose to engine (quickfit).
2. Clip hose to bracket.
3. Remove drain container.
4. Lower vehicle on ramp.
5. Install hose to oil separator (quickfit).
6. Install throttle body to air cleaner duct (clip x1).
7. Fill tank with approximately amount of displaced oil and replace cap.
8. Use handbook procedure to check oil level.
Oil Separator Assembly-Renew
Removal
1. Release clip and disconnect air cleaner duct from throttle body.
2. Disconnect hoses from oil separator (clips x2).
3. Remove separator (bolt x1) (place cloth to catch oil)
Installation
1. Install separator (bolt x1) (torque).
2. Install hoses to oil separator (clips x2).
3. Install throttle body to air cleaner duct (clip x1).
4. Use handbook procedure to check oil level.
Emissions Separator Hose-Renew
Removal
1. Move throttle body to air cleaner duct for access (clip x1).
2. Disconnect hose from oil separator (clips x1).
3. Disconnect hose from engi ne and remove (clips x1).
Installation
1. Connect hose to engine (clips x1).
2. Install hose to oil separator (clips x1).
3. Install throttle body to air cleaner duct (clip x1).
4. Use handbook procedure to check oil level.
Secondary Air Injection Pump and
Bracket Assembly-Renew
Removal
1. Disconnect vehicle battery. 2. Remove inlet manifold assembly (see Workshop Manual
procedure 03.01.BA Manifold Assembly - Intake Upper
- Renew).
3. Disconnect breather tube to secondary air pump (quickfit).
4. Disconnect vacuum tube from solenoid valve.
5. Disconnect vacuum tubes (x2) from actuator valves.
6. Loosen unions and disconnect secondary air injection tubes (x2).
7. Disconnect multiplug, air injection pump. Release multiplug from mounting bracket.
8. Release harness and vacuum tube fir tree clips (x6) from mounting bracket.
9. Remove bolts (x3), securing secondary air injection pump assembly to engine.
10. Remove secondary air injection pump assembly.
Installation
1. Position secondary air injection pump assembly, install and torque tighten bolts (x3).
2. Secure harness and vacuum tube fir tree clips (x6) in
mounting bracket.
3. Secure multiplug in bracket, connect multiplug.
4. Connect and torque tighten secondary air tube unions (x2).
5. Connect vacuum tubes to solenoid and actuator valves (x3).
6. Connect breather tube to secondary air injection pump.
7. Install inlet manifold assembly (see Workshop Manual procedure 03.01.BA Manifold Assembly - Intake Upper
- Renew).
8. Connect vehicle battery.
PCV Valve Assembly-Renew
Removal
1. Disconnect breather tube from PCV valve.
2. Remove bolts (x2) securing PCV valve, remove PCV valve.
Installation
1. Clean PCV valve and mating face.
2. Install PCV valve, install and torque tighten bolts (x2).
3. Connect breather tube to PCV valve.
Crank Vent Hose-Renew
Removal
1. Disconnect hose from cam cover (quickfit).
Repair Operation Time (ROT)
Repair Operation Time (ROT)
Repair Operation Time (ROT)
Repair Operation Time (ROT)
ItemCode
PCV Valve Assembly-Renew 03.08.DC
Repair Operation Time (ROT)
ItemCode
Crank Vent Hose-Renew 03.08.DD
Page 325 of 947
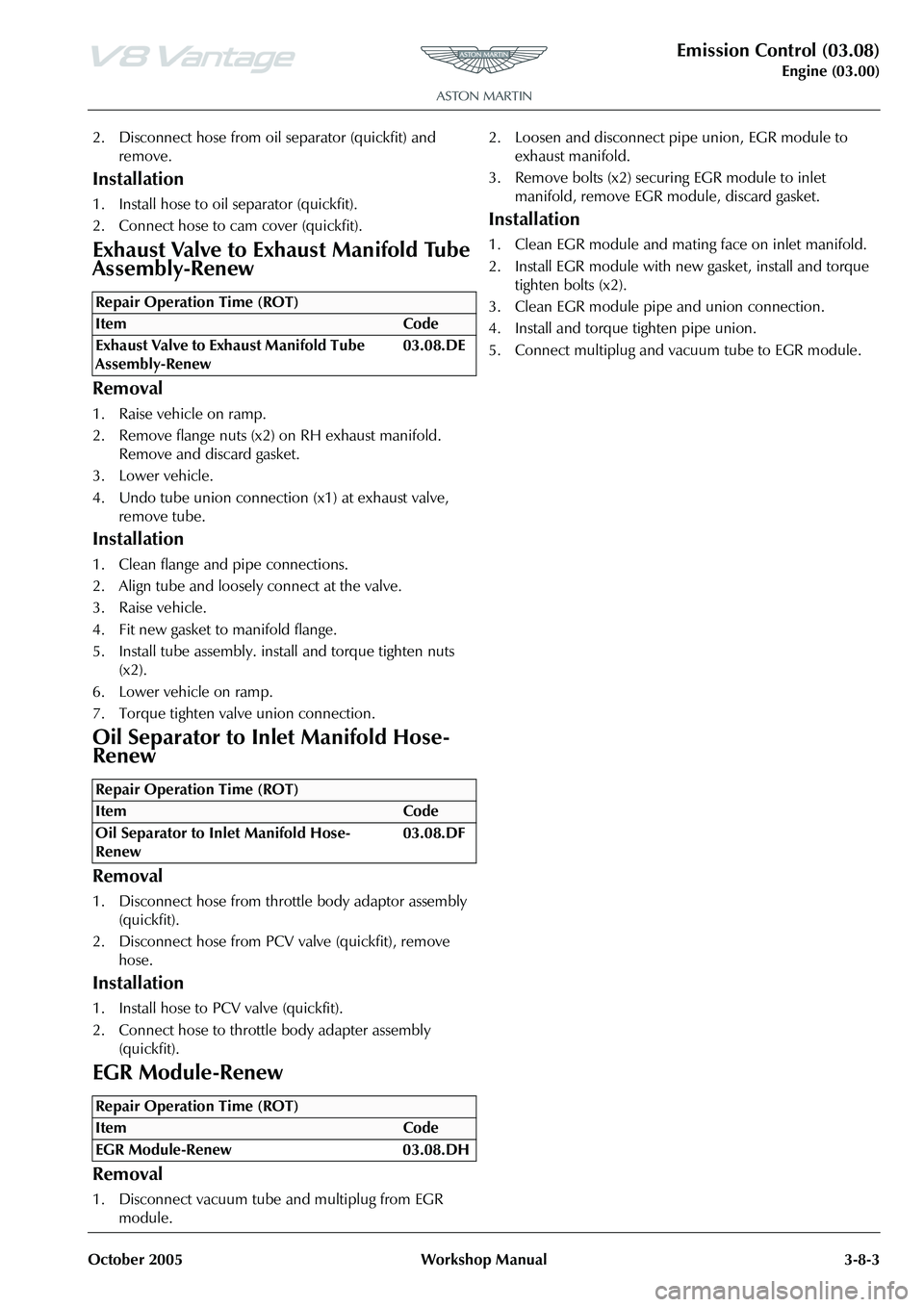
Emission Control (03.08)
Engine (03.00)
October 2005 Workshop Manual 3-8-3
2. Disconnect hose from oil separator (quickfit) and
remove.
Installation
1. Install hose to oil separator (quickfit).
2. Connect hose to cam cover (quickfit).
Exhaust Valve to Exhaust Manifold Tube
Assembly-Renew
Removal
1. Raise vehicle on ramp.
2. Remove flange nuts (x2) on RH exhaust manifold. Remove and discard gasket.
3. Lower vehicle.
4. Undo tube union connection (x1) at exhaust valve, remove tube.
Installation
1. Clean flange and pipe connections.
2. Align tube and loosely connect at the valve.
3. Raise vehicle.
4. Fit new gasket to manifold flange.
5. Install tube assembly. install and torque tighten nuts (x2).
6. Lower vehicle on ramp.
7. Torque tighten valve union connection.
Oil Separator to Inlet Manifold Hose-
Renew
Removal
1. Disconnect hose from throttle body adaptor assembly (quickfit).
2. Disconnect hose from PCV valve (quickfit), remove hose.
Installation
1. Install hose to PCV valve (quickfit).
2. Connect hose to throttle body adapter assembly (quickfit).
EGR Module-Renew
Removal
1. Disconnect vacuum tube and multiplug from EGR module. 2. Loosen and disconnect pipe union, EGR module to
exhaust manifold.
3. Remove bolts (x2) securi ng EGR module to inlet
manifold, remove EGR module, discard gasket.
Installation
1. Clean EGR module and mating face on inlet manifold.
2. Install EGR module with new gasket, install and torque tighten bolts (x2).
3. Clean EGR module pipe and union connection.
4. Install and torque tighten pipe union.
5. Connect multiplug and vacuum tube to EGR module.
Repair Operation Time (ROT)
Repair Operation Time (ROT)
Repair Operation Time (ROT)
Page 371 of 947
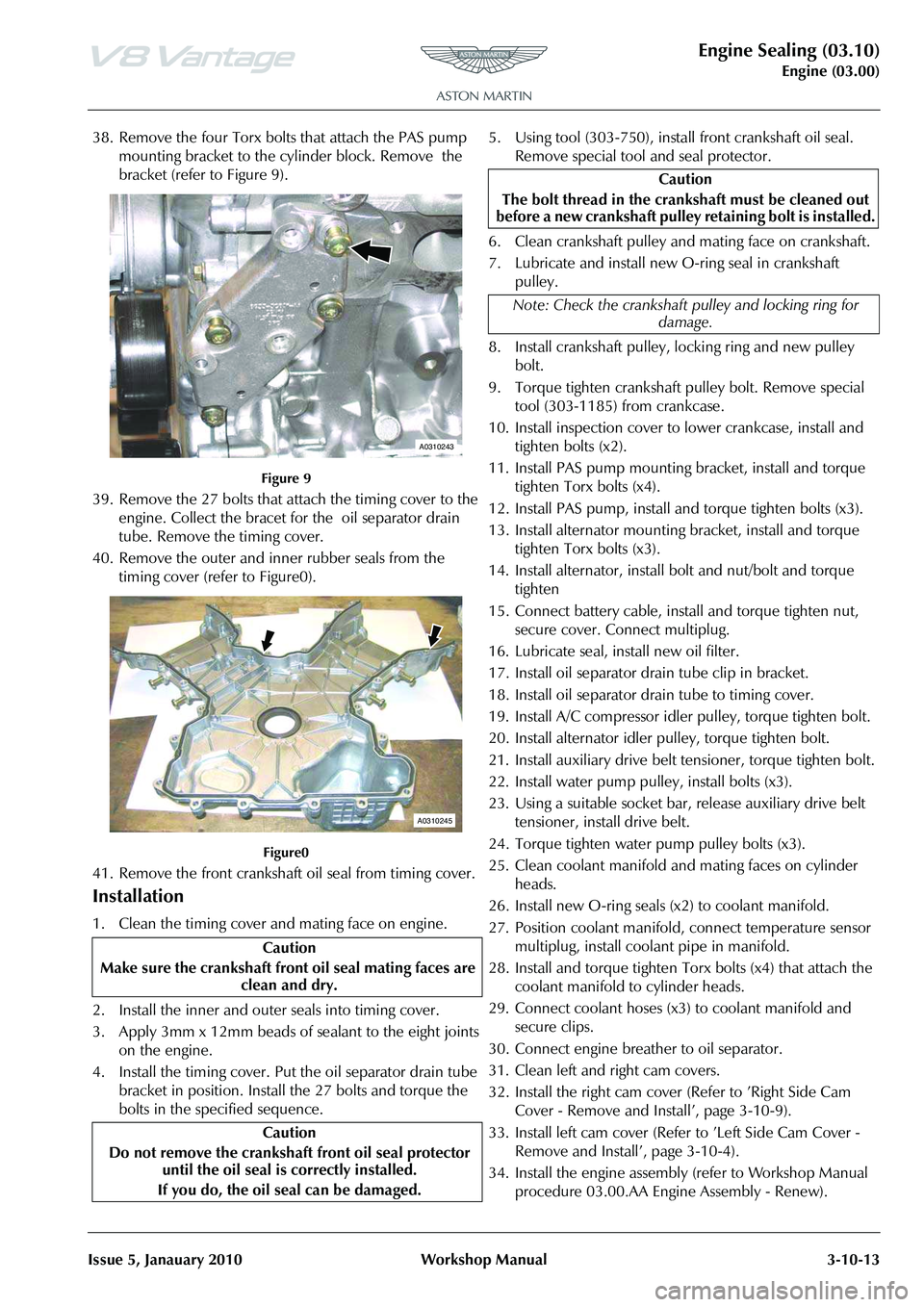
Engine Sealing (03.10)
Engine (03.00)
Issue 5, Janauary 2010 Workshop Manual 3-10-13
38. Remove the four Torx bolts that attach the PAS pump mounting bracket to the cylinder block. Remove the
bracket (refer to Figure 9).
Figure 9
39. Remove the 27 bolts that attach the timing cover to the engine. Collect the bracet for the oil separator drain
tube. Remove the timing cover.
40. Remove the outer and inner rubber seals from the timing cover (refer to Figure0).
Figure0
41. Remove the front crankshaft oil seal from timing cover.
Installation
1. Clean the timing cover and mating face on engine.
2. Install the inner and outer seals into timing cover.
3. Apply 3mm x 12mm beads of sealant to the eight joints
on the engine.
4. Install the timing cover. Put the oil separator drain tube bracket in position. Install the 27 bolts and torque the
bolts in the specified sequence. 5. Using tool (303-750), instal
l front crankshaft oil seal.
Remove special tool and seal protector.
6. Clean crankshaft pulley and mating face on crankshaft.
7. Lubricate and install new O-ring seal in crankshaft pulley.
8. Install crankshaft pulley, locking ring and new pulley bolt.
9. Torque tighten crankshaft pulley bolt. Remove special tool (303-1185) from crankcase.
10. Install inspection cover to lower crankcase, install and tighten bolts (x2).
11. Install PAS pump mounting bracket, install and torque tighten Torx bolts (x4).
12. Install PAS pump, install and torque tighten bolts (x3).
13. Install alternator mounting bracket, install and torque tighten Torx bolts (x3).
14. Install alternator, install bolt and nut/bolt and torque tighten
15. Connect battery cable, install and torque tighten nut, secure cover. Connect multiplug.
16. Lubricate seal, install new oil filter.
17. Install oil separator drai n tube clip in bracket.
18. Install oil separator drain tube to timing cover.
19. Install A/C compressor idler pulley, torque tighten bolt.
20. Install alternator idler pulley, torque tighten bolt.
21. Install auxiliary drive belt te nsioner, torque tighten bolt.
22. Install water pump pulley, install bolts (x3).
23. Using a suitable socket ba r, release auxiliary drive belt
tensioner, install drive belt.
24. Torque tighten water pump pulley bolts (x3).
25. Clean coolant manifold and mating faces on cylinder heads.
26. Install new O-ring seals (x2) to coolant manifold.
27. Position coolant manifold, connect temperature sensor
multiplug, install coolant pipe in manifold.
28. Install and torque tighten Torx bolts (x4) that attach the coolant manifold to cylinder heads.
29. Connect coolant hoses (x3) to coolant manifold and
secure clips.
30. Connect engine breather to oil separator.
31. Clean left and right cam covers.
32. Install the right cam cover (Refer to ’Right Side Cam Cover - Remove and Install’, page 3-10-9).
33. Install left cam cover (Refer to ’Left Side Cam Cover -
Remove and Install’, page 3-10-4).
34. Install the engine assembly (refer to Workshop Manual procedure 03.00.AA Engine Assembly - Renew).
Caution
Make sure the cranks haft front oil seal mating faces are
clean and dry.
Caution
Do not remove the crankshaft front oil seal protector
until the oil seal is correctly installed.
If you do, the oil seal can be damaged.
A0310243
A0310245
Caution
The bolt thread in the cran kshaft must be cleaned out
before a new crankshaft pulley retaining bolt is installed.
Note: Check the crankshaft pulley and locking ring for damage.
Page 373 of 947
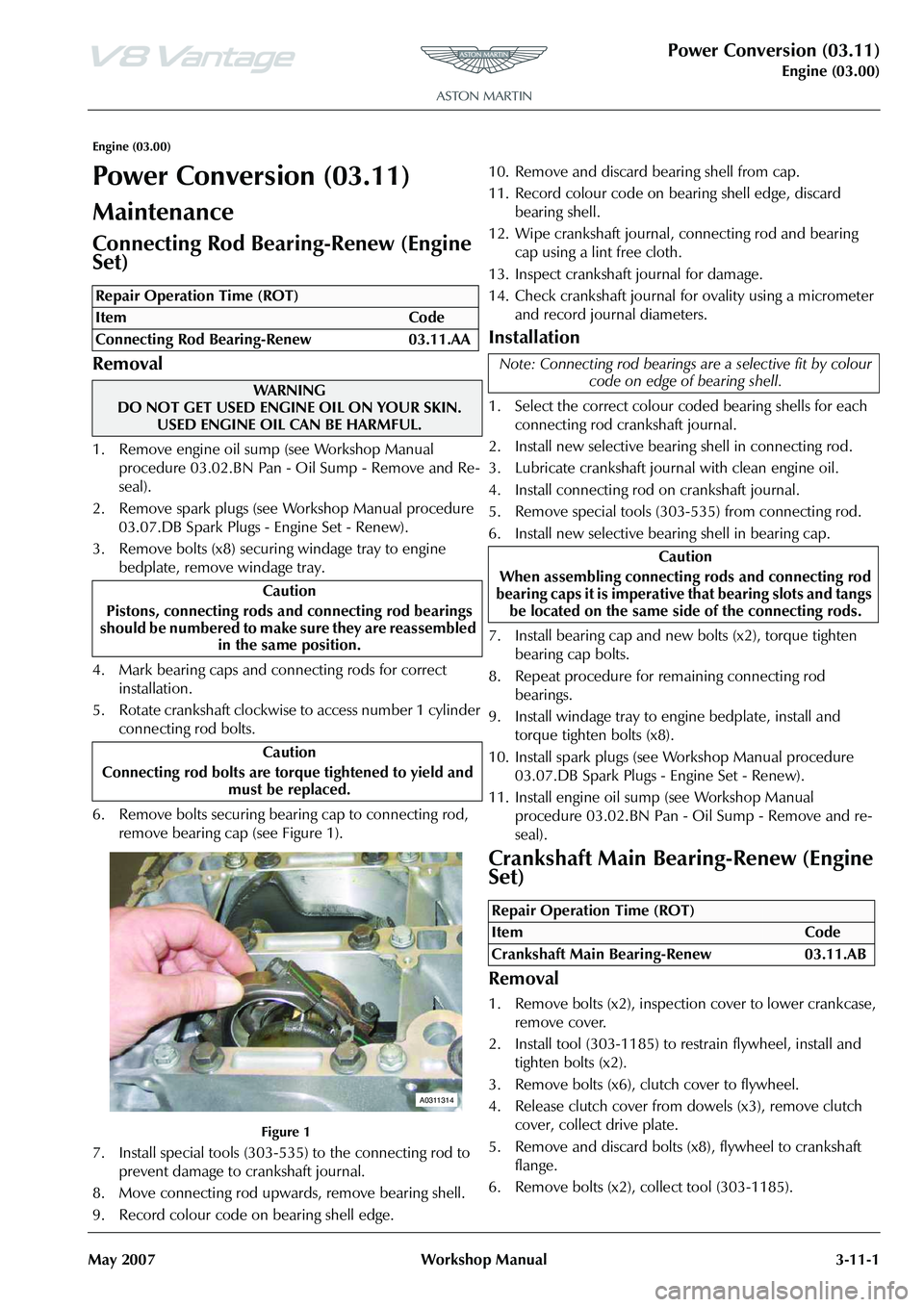
Power Conversion (03.11)
Engine (03.00)
May 2007 Workshop Manual 3-11-1
Engine (03.00)
Power Conversion (03.11)
Maintenance
Connecting Rod Bearing-Renew (Engine
Set)
Removal
1. Remove engine oil sump (see Workshop Manual
procedure 03.02.BN Pan - Oil Sump - Remove and Re-
seal).
2. Remove spark plugs (see Workshop Manual procedure 03.07.DB Spark Plugs - Engine Set - Renew).
3. Remove bolts (x8) securing windage tray to engine bedplate, remove windage tray.
4. Mark bearing caps and connecting rods for correct installation.
5. Rotate crankshaft clockwise to access number 1 cylinder connecting rod bolts.
6. Remove bolts securing bearing cap to connecting rod, remove bearing cap (see Figure 1).
Figure 1
7. Install special tools (303-535) to the connecting rod to prevent damage to crankshaft journal.
8. Move connecting rod upwards, remove bearing shell.
9. Record colour code on bearing shell edge. 10. Remove and discard bearing shell from cap.
11. Record colour code on bearing shell edge, discard
bearing shell.
12. Wipe crankshaft journal, connecting rod and bearing cap using a lint free cloth.
13. Inspect crankshaft journal for damage.
14. Check crankshaft journal for ovality using a micrometer and record journal diameters.
Installation
1. Select the correct colour coded bearing shells for each connecting rod crankshaft journal.
2. Install new selective bearing shell in connecting rod.
3. Lubricate crankshaft journal with clean engine oil.
4. Install connecting rod on crankshaft journal.
5. Remove special tools (303-535) from connecting rod.
6. Install new selective bearing shell in bearing cap.
7. Install bearing cap and new bolts (x2), torque tighten bearing cap bolts.
8. Repeat procedure for remaining connecting rod bearings.
9. Install windage tray to engine bedplate, install and torque tighten bolts (x8).
10. Install spark plugs (see Workshop Manual procedure 03.07.DB Spark Plugs - Engine Set - Renew).
11. Install engine oil sump (see Workshop Manual
procedure 03.02.BN Pan - Oil Sump - Remove and re-
seal).
Crankshaft Main Bearing-Renew (Engine
Set)
Removal
1. Remove bolts (x2), inspection cover to lower crankcase, remove cover.
2. Install tool (303-1185) to restrain flywheel, install and tighten bolts (x2).
3. Remove bolts (x6), clutch cover to flywheel.
4. Release clutch cover from dowels (x3), remove clutch cover, collect drive plate.
5. Remove and discard bolts (x8), flywheel to crankshaft flange.
6. Remove bolts (x2), collect tool (303-1185).
Repair Operation Time (ROT)
WA R N I N G
DO NOT GET USED ENGINE OIL ON YOUR SKIN. USED ENGINE OIL CAN BE HARMFUL.
Caution
Pistons, connecting rods an d connecting rod bearings
should be numbered to make sure they are reassembled
in the same position.
Caution
Connecting rod bolts are tor qu
e tightened to yield and
mu st be replaced.
A0311314
Note: Connecting rod bearings ar e a selective fit by colour
code on edge of bearing shell.
Caution
When assembling connecting rods and connecting rod
bearing caps it is imperative that bearing slots and tangs
be located on the same side of the connecting rods.
Repair Operation Time (ROT)
Page 374 of 947
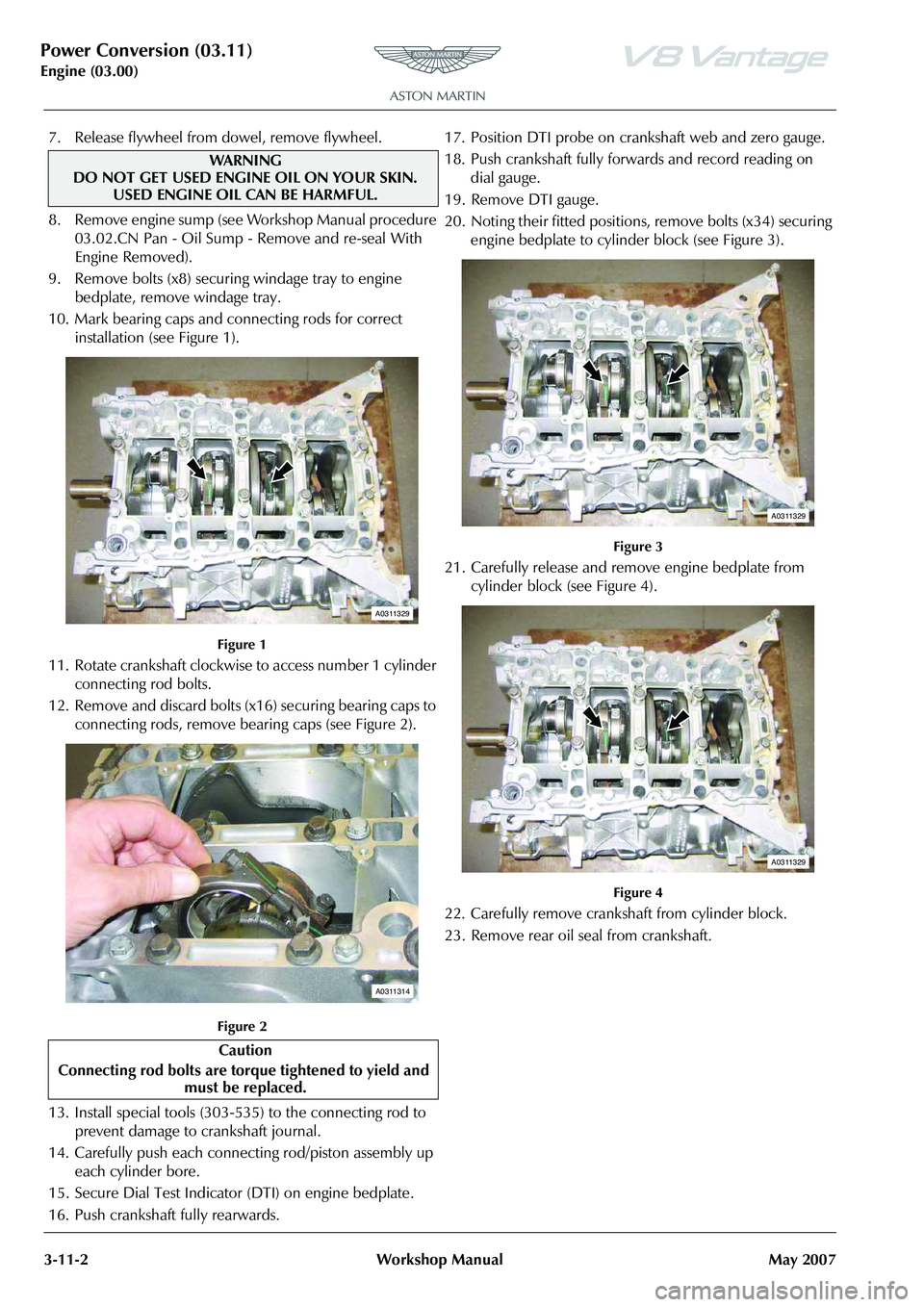
Power Conversion (03.11)
Engine (03.00)3-11-2 Workshop Manual May 2007
7. Release flywheel from dowel, remove flywheel.
8 . R e m o v e e n g i n e s u m p ( s e e Wo r k s h o p M a n u a l p ro c e d u r e
03.02.CN Pan - Oil Sump - Remove and re-seal With
Engine Removed).
9. Remove bolts (x8) securing windage tray to engine bedplate, remove windage tray.
10. Mark bearing caps and connecting rods for correct installation (see Figure 1).
Figure 1
11. Rotate crankshaft clockwise to access number 1 cylinder
connecting rod bolts.
12. Remove and discard bolts (x16) securing bearing caps to connecting rods, remove bearing caps (see Figure 2).
Figure 2
13. Install special tools (303-535) to the connecting rod to prevent damage to crankshaft journal.
14. Carefully push each connecting rod/piston assembly up each cylinder bore.
15. Secure Dial Test Indicator (DTI) on engine bedplate.
16. Push crankshaft fully rearwards. 17. Position DTI probe on cran
kshaft web and zero gauge.
18. Push crankshaft fully forw ards and record reading on
dial gauge.
19. Remove DTI gauge.
20. Noting their fitted positions, remove bolts (x34) securing engine bedplate to cylinder block (see Figure 3).
Figure 3
21. Carefully release and remove engine bedplate from cylinder block (see Figure 4).
Figure 4
22. Carefully remove crankshaft from cylinder block.
23. Remove rear oil seal from crankshaft.
WAR NI NG
DO NOT GET USED ENGINE OIL ON YOUR SKIN.
USED ENGINE OIL CAN BE HARMFUL.
Caution
Connecting rod bolts are tor que tightened to yield and
must be replaced.
A0311329
A0311314
A0311329
A0311329
Page 376 of 947

Power Conversion (03.11)
Engine (03.00)3-11-4 Workshop Manual May 2007
10. Install crankshaft retaining caps (303-534), install and
lightly tighten bolts (x10) (see Figure 8).
Figure 8
11. Install connecting rod bearing caps (x8), install and torque tighten retaining bolts.
12. Remove bolts securing crankshaft retaining caps (303- 534), remove retaining caps (see Figure 9).
Figure 9
13. Apply a 2mm diameter continuous bead of sealant to cylinder block flange ensuring that there are no gaps in
the sealant.
14. Install engine bedplate to cylinder block, install and torque tighten bolts (x34) in the correct sequence.
15. Remove excess sealant from crankshaft rear oil seal
aperture and front face of cylinder block.
16. Clean windage tray.
17. Install windage tray, install and torque tighten bolts (x8). 18. Ensure that oil seal protector is positioned correctly and
install oil seal onto crankshaft flange.
19. Install tool (303-1189) to crankshaft, position nuts on tool against oil seal.
20. Ensure that oil seal and special are parallel to rear of engine.
21. To install oil seal, tighten nuts alternately on tool (303- 1189) until oil seal correctly seated.
22. Remove special tool from crankshaft.
23. Check that the oil se al is located correctly.
24. Clean flywheel and mating face on crankshaft.
25. Install flywheel, align to dowel on crankshaft flange.
26. Install new bolts (x8), install tool (303-1185) to restrain flywheel. Torque tighten bolts (x8) in the correct
sequence.
27. Clean clutch cover and drive plate.
28. Install clutch assembly on flywheel, align to dowels (x3).
29. Install bolts (x6), install clutch alignment tool, evenly torque tighten bolts (x6) in a diagonal sequence.
Remove clutch alignment tool.
30. Remove bolts (x2), collect tool (303-1185).
31. Install inspection cover, install and torque tighten bolts (x2).
32. Install engine sump (see Workshop Manual procedure 03.02.CN Pan - Oil Sump - Remove and Reseal With
Engine Removed).
Crankshaft Assembly-Renew
Removal
1. Remove bolts (x2), inspection cover to lower crankcase, remove cover.
2. Install tool (303-1185) to restrain flywheel, install and tighten bolts (x2).
3. Remove bolts (x6), clutch cover to flywheel.
4. Release clutch cover from dowels (x3), remove clutch cover, collect drive plate.
5. Remove and discard bolts (x8), flywheel to crankshaft flange.
6. Remove bolts (x2), collect tool (303-1185).
7. Release flywheel from dowel, remove flywheel.
8 . R e m o v e e n g i n e s u mp ( s e e Wo r k s h o p M a n u a l p ro c e d u re 03.02.CN Pan - Oil Sump - Remove and Reseal With
Engine Removed).
Caution
Do not lubricate engine bedplate retaining bolts.
Caution
Tighten engine bedplate retaining bolts in the sequence shown.
Caution
Do not rotate crankshaft until all engine bedplate
retaining bolts are tightened to specification.
Caution
Engine bedplate retaining bolts must be tightened
within twenty minutes of applying sealant.
A0311328
A0311328
Caution
Do not use any lubricant on cr ankshaft oil seals or seal
protectors. Make sure all co mponents are clean and dry.
Repair Operation Time (ROT)
ItemCode
Crankshaft Assembly-Renew 03.11.CF
WAR NI NG
DO NOT GET USED ENGINE OIL ON YOUR SKIN.
USED ENGINE OIL CAN BE HARMFUL.
Page 377 of 947
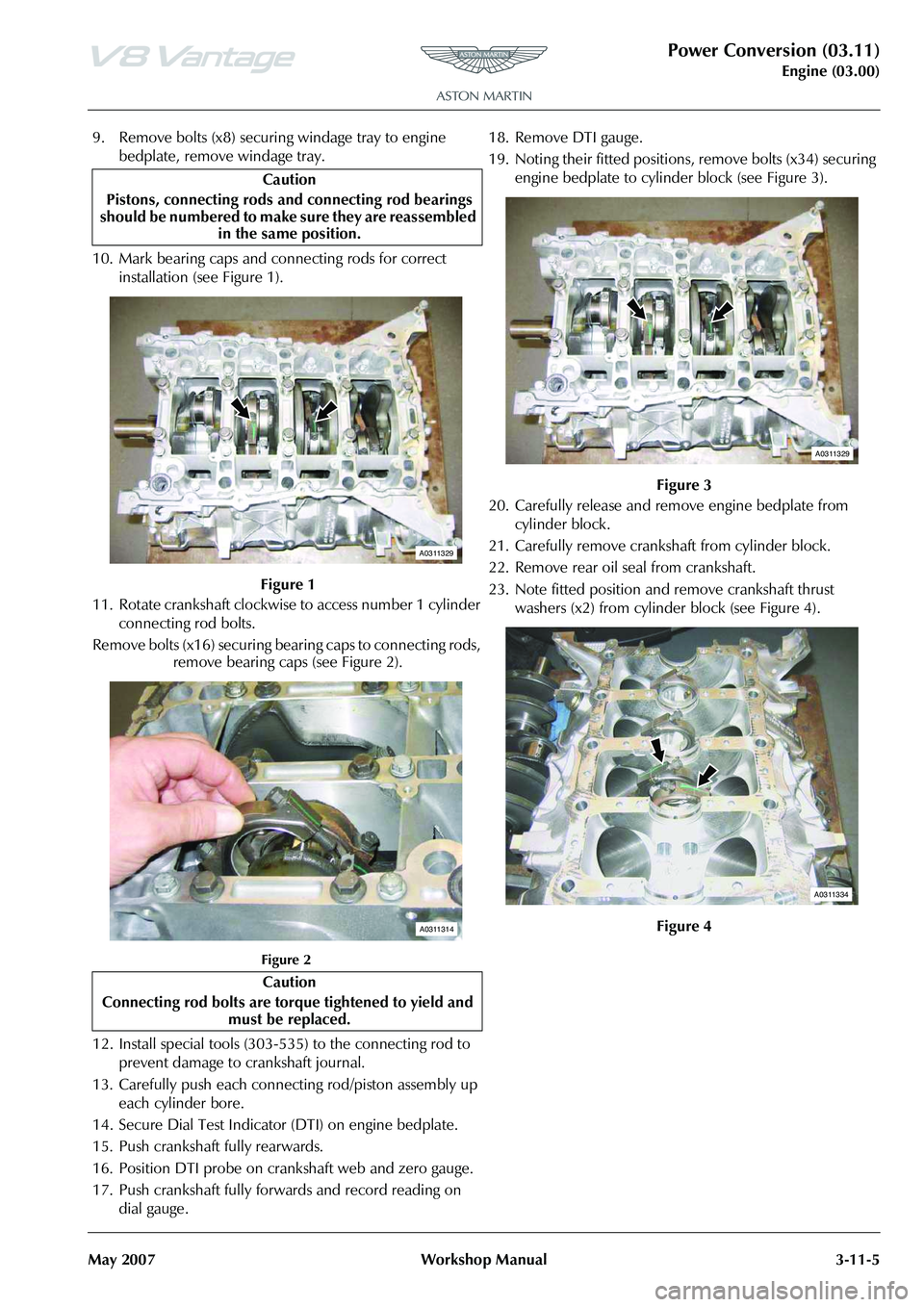
Power Conversion (03.11)
Engine (03.00)
May 2007 Workshop Manual 3-11-5
9. Remove bolts (x8) securing windage tray to engine
bedplate, remove windage tray.
10. Mark bearing caps and connecting rods for correct installation (see Figure 1).
Figure 1
11. Rotate crankshaft clockwis e to access number 1 cylinder
connecting rod bolts.
Remove bolts (x16) securing bearing caps to connecting rods, remove bearing caps (see Figure 2).
Figure 2
12. Install special tools (303-535) to the connecting rod to
prevent damage to crankshaft journal.
13. Carefully push each connecting rod/piston assembly up each cylinder bore.
14. Secure Dial Test Indicator (DTI) on engine bedplate.
15. Push crankshaft fully rearwards.
16. Position DTI probe on crankshaft web and zero gauge.
17. Push crankshaft fully forw ards and record reading on
dial gauge. 18. Remove DTI gauge.
19. Noting their fitted positions, remove bolts (x34) securing
engine bedplate to cylinder block (see Figure 3).
Figure 3
20. Carefully release and remove engine bedplate from cylinder block.
21. Carefully remove crankshaft from cylinder block.
22. Remove rear oil seal from crankshaft.
23. Note fitted position and remove crankshaft thrust washers (x2) from cylinder block (see Figure 4).
Figure 4
Caution
Pistons, connecting rods an d connecting rod bearings
should be numbered to make sure they are reassembled
in the same position.
Caution
Connecting rod bolts are tor q
u
e tightened to yield and
mu st be replaced.
A0311329
A0311314
A0311329
A0311334
Page 378 of 947
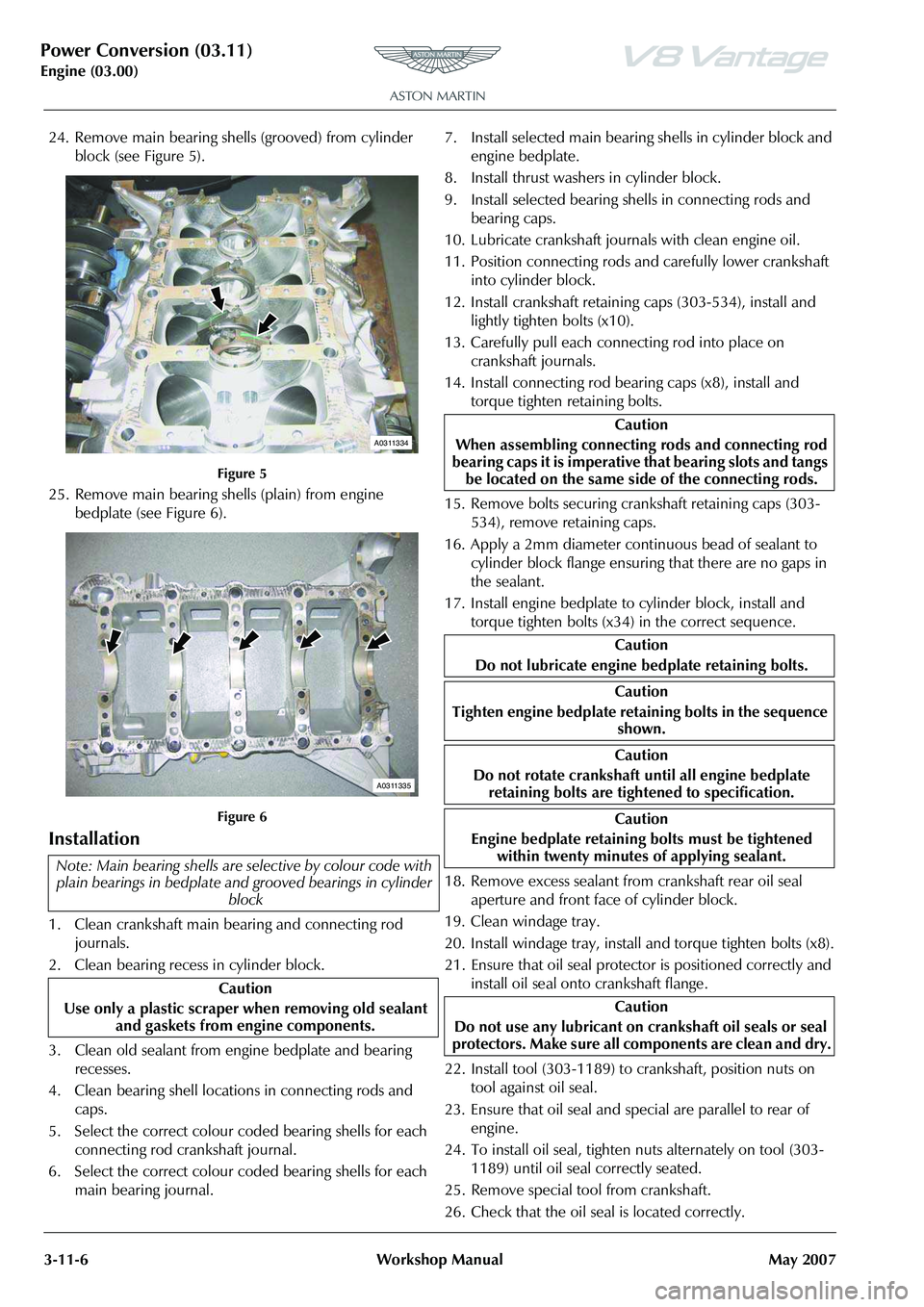
Power Conversion (03.11)
Engine (03.00)3-11-6 Workshop Manual May 2007
24. Remove main bearing shells (grooved) from cylinder
block (see Figure 5).
Figure 5
25. Remove main bearing shells (plain) from engine bedplate (see Figure 6).
Figure 6
Installation
1. Clean crankshaft main bearing and connecting rod journals.
2. Clean bearing recess in cylinder block.
3. Clean old sealant from engine bedplate and bearing recesses.
4. Clean bearing shell locations in connecting rods and caps.
5. Select the correct colour coded bearing shells for each connecting rod crankshaft journal.
6. Select the correct colour coded bearing shells for each main bearing journal. 7. Install selected main bearing
shells in cylinder block and
engine bedplate.
8. Install thrust washers in cylinder block.
9. Install selected bearing shells in connecting rods and bearing caps.
10. Lubricate crankshaft journa ls with clean engine oil.
11. Position connecting rods and carefully lower crankshaft into cylinder block.
12. Install crankshaft retaining caps (303-534), install and lightly tighten bolts (x10).
13. Carefully pull each connecting rod into place on crankshaft journals.
14. Install connecting rod bearing caps (x8), install and torque tighten retaining bolts.
15. Remove bolts securing cran kshaft retaining caps (303-
534), remove retaining caps.
16. Apply a 2mm diameter continuous bead of sealant to cylinder block flange ensuring that there are no gaps in
the sealant.
17. Install engine bedplate to cylinder block, install and torque tighten bolts (x34) in the correct sequence.
18. Remove excess sealant from crankshaft rear oil seal aperture and front face of cylinder block.
19. Clean windage tray.
20. Install windage tray, install and torque tighten bolts (x8).
21. Ensure that oil seal protector is positioned correctly and install oil seal onto crankshaft flange.
22. Install tool (303-1189) to crankshaft, position nuts on tool against oil seal.
23. Ensure that oil seal and special are parallel to rear of engine.
24. To install oil seal, tighten nuts alternately on tool (303- 1189) until oil seal correctly seated.
25. Remove special tool from crankshaft.
26. Check that the oil se al is located correctly.
Note: Main bearing shells are
selective by colour code with
plain bearings in bedplate and grooved bearings in cylinder
block
Caution
Use only a plastic scraper when removing old sealant and gaskets from engine components.
A0311334
A0311335
Caution
When assembling connecting rods and connecting rod
bearing caps it is imperative that bearing slots and tangs
be located on the same side of the connecting rods.
Caution
Do not lubricate engine bedplate retaining bolts.
Caution
Tighten engine bedplate retaining bolts in the sequence shown.
Caution
Do not rotate crankshaft until all engine bedplate
retaining bolts are tightened to specification.
Caution
Engine bedplate retaining bolts must be tightened within twenty minutes of applying sealant.
Caution
Do not use any lubricant on cr ankshaft oil seals or seal
protectors. Make sure all co mponents are clean and dry.