coolant ASTON MARTIN V8 VANTAGE 2010 Owner's Manual
[x] Cancel search | Manufacturer: ASTON MARTIN, Model Year: 2010, Model line: V8 VANTAGE, Model: ASTON MARTIN V8 VANTAGE 2010Pages: 947, PDF Size: 43.21 MB
Page 280 of 947
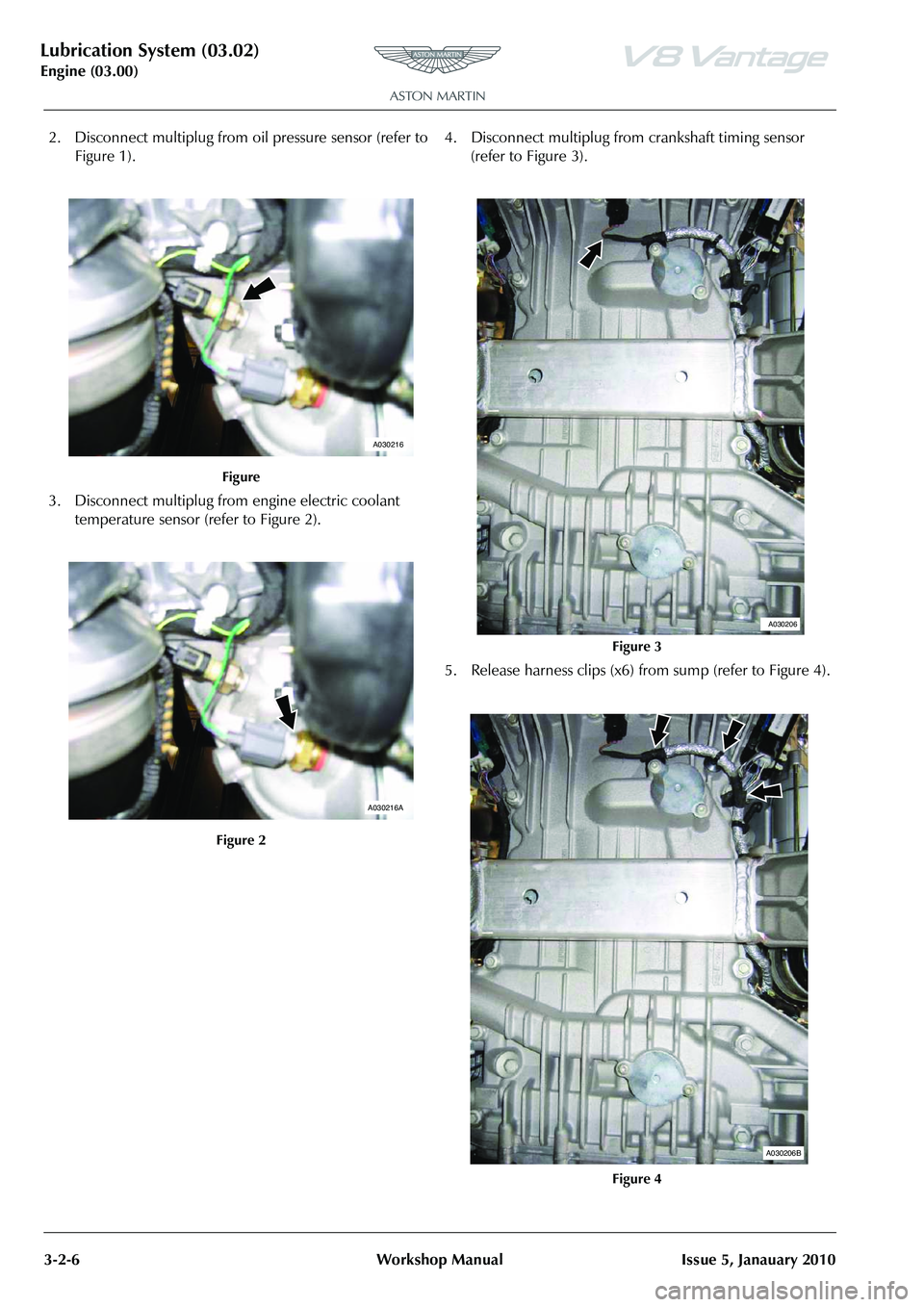
Lubrication System (03.02)
Engine (03.00)3-2-6 Workshop Manual Issue 5, Janauary 2010
2. Disconnect multiplug from oi l pressure sensor (refer to
Figure 1).
3. Disconnect multiplug from engine electric coolant
temperature sensor (refer to Figure 2). 4. Disconnect multiplug from
crankshaft timing sensor
(refer to Figure 3).
5. Release harness clips (x6) from sump (refer to Figure 4).
Figure
Figure 2
A030216
A030216A
Figure 3
Figure 4
A030206
A030206B
Page 282 of 947
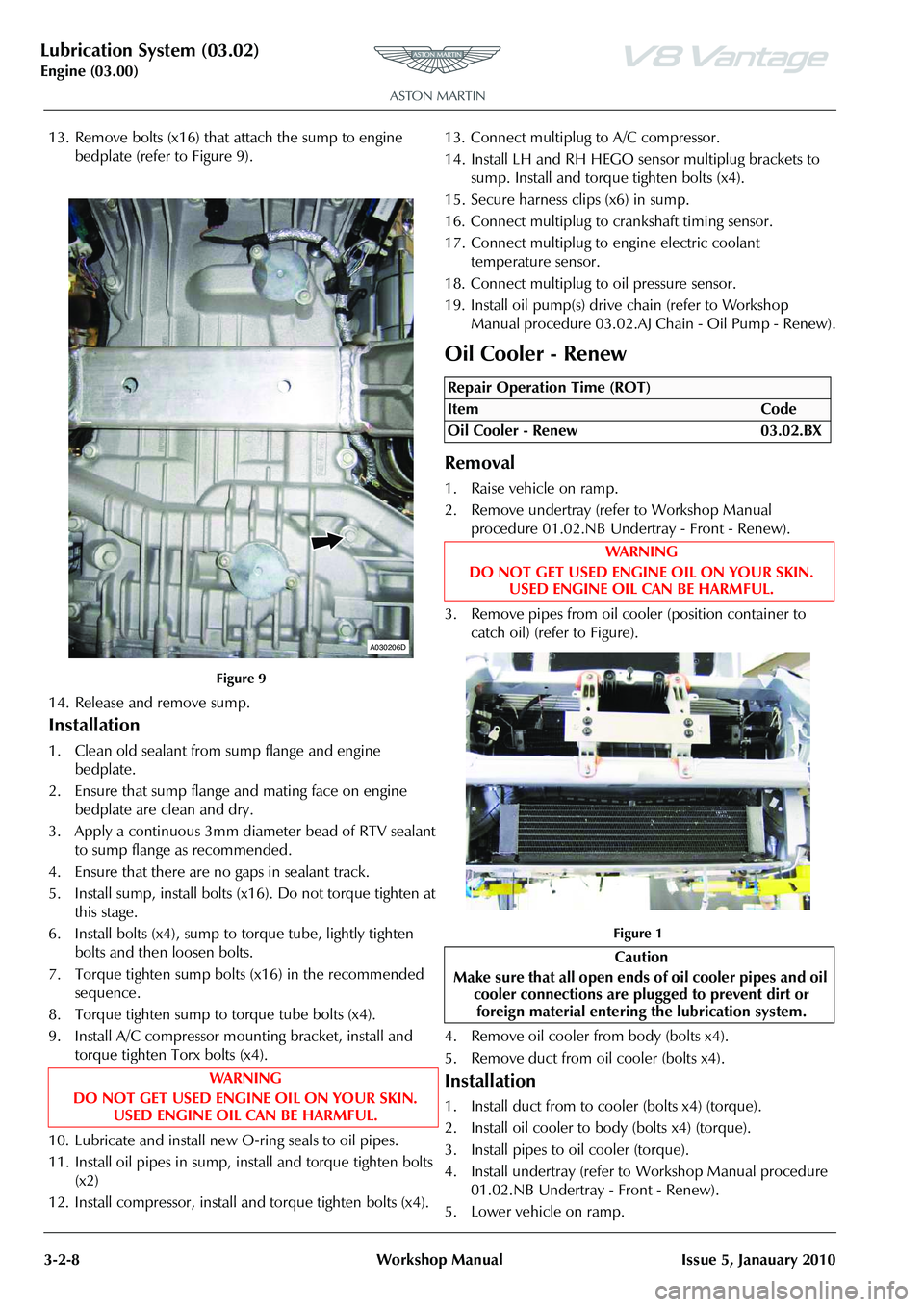
Lubrication System (03.02)
Engine (03.00)3-2-8 Workshop Manual Issue 5, Janauary 2010
13. Remove bolts (x16) that attach the sump to engine bedplate (refer to Figure 9).
14. Release and remove sump.
Installation
1. Clean old sealant from sump flange and engine bedplate.
2. Ensure that sump flange and mating face on engine bedplate are clean and dry.
3. Apply a continuous 3mm diameter bead of RTV sealant to sump flange as recommended.
4. Ensure that there are no gaps in sealant track.
5. Install sump, install bolts (x16). Do not torque tighten at this stage.
6. Install bolts (x4), sump to torque tube, lightly tighten bolts and then loosen bolts.
7. Torque tighten sump bolts (x16) in the recommended sequence.
8. Torque tighten sump to torque tube bolts (x4).
9. Install A/C compressor mounting bracket, install and torque tighten Torx bolts (x4).
10. Lubricate and install new O-ring seals to oil pipes.
11. Install oil pipes in sump, install and torque tighten bolts (x2)
12. Install compressor, install and torque tighten bolts (x4). 13. Connect multiplug to A/C compressor.
14. Install LH and RH HEGO
sensor multiplug brackets to
sump. Install and torque tighten bolts (x4).
15. Secure harness clips (x6) in sump.
16. Connect multiplug to crankshaft timing sensor.
17. Connect multiplug to engine electric coolant temperature sensor.
18. Connect multiplug to oil pressure sensor.
19. Install oil pump(s) drive chain (refer to Workshop
Manual procedure 03.02.AJ Chain - Oil Pump - Renew).
Oil Cooler - Renew
Removal
1. Raise vehicle on ramp.
2. Remove undertray (refer to Workshop Manual procedure 01.02.NB Undertray - Front - Renew).
3. Remove pipes from oil cooler (position container to catch oil) (refer to Figure).
Figure 1
4. Remove oil cooler from body (bolts x4).
5. Remove duct from oil cooler (bolts x4).
Installation
1. Install duct from to cooler (bolts x4) (torque).
2. Install oil cooler to body (bolts x4) (torque).
3. Install pipes to oil cooler (torque).
4. Install undertray (refer to Workshop Manual procedure 01.02.NB Undertray - Front - Renew).
5. Lower vehicle on ramp.
Figure 9
WAR NI NG
DO NOT GET USED ENGINE OIL ON YOUR SKIN. USED ENGINE OIL CAN BE HARMFUL.
A030206D
Repair Operation Time (ROT)
ItemCode
Oil Cooler - Renew 03.02.BX
WAR NI NG
DO NOT GET USED ENGINE OIL ON YOUR SKIN. USED ENGINE OIL CAN BE HARMFUL.
Caution
Make sure that all open ends of oil cooler pipes and oil cooler connections are plugged to prevent dirt or
foreign material entering the lubrication system.
Page 283 of 947
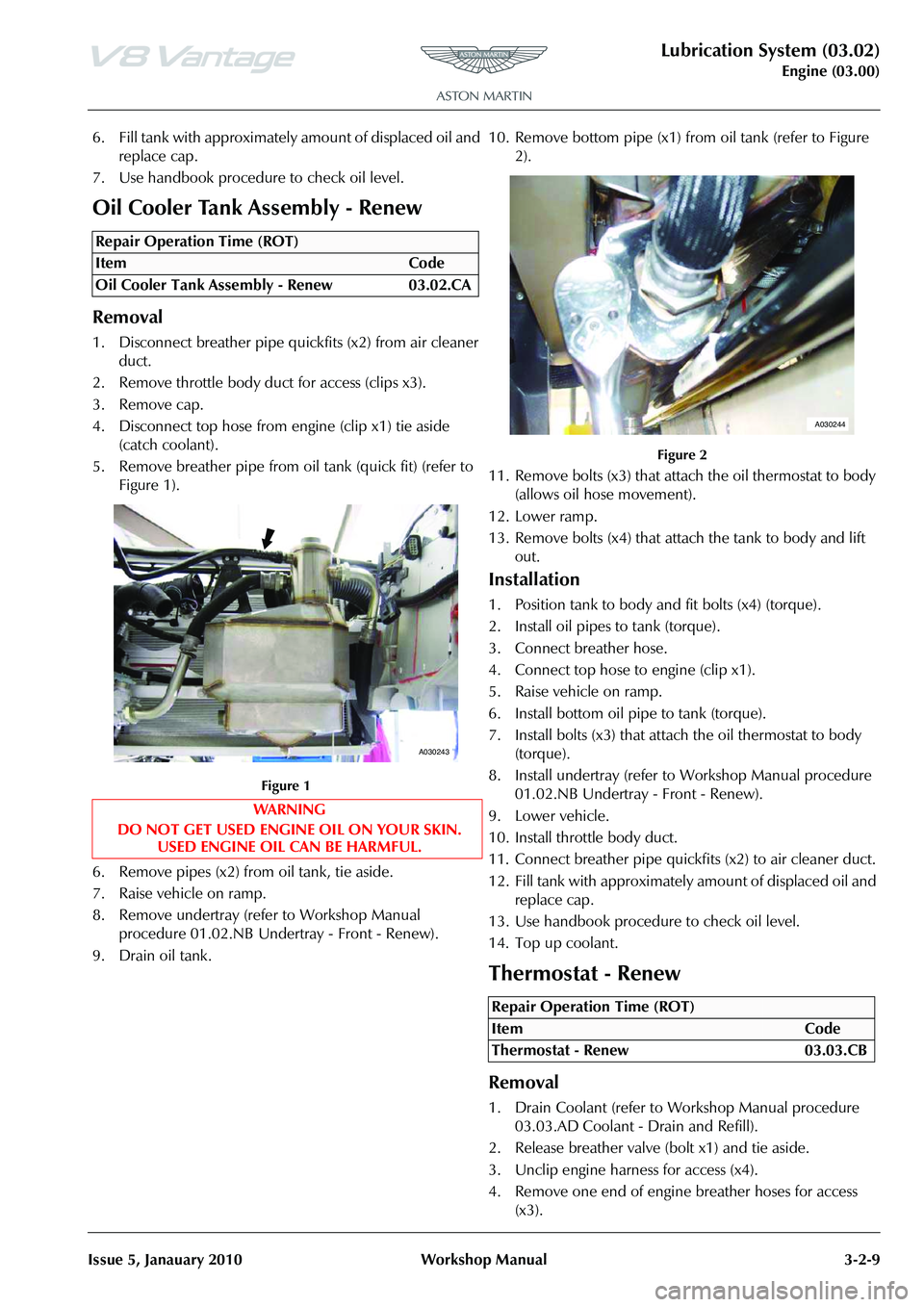
Lubrication System (03.02)
Engine (03.00)
Issue 5, Janauary 2010 Workshop Manual 3-2-9
6. Fill tank with approximately amount of displaced oil and replace cap.
7. Use handbook procedure to check oil level.
Oil Cooler Tank Assembly - Renew
Removal
1. Disconnect breather pipe qu ickfits (x2) from air cleaner
duct.
2. Remove throttle body du ct for access (clips x3).
3. Remove cap.
4. Disconnect top hose from engine (clip x1) tie aside
(catch coolant).
5. Remove breather pipe from oil tank (quick fit) (refer to Figure 1).
Figure 1
6. Remove pipes (x2) fr om oil tank, tie aside.
7. Raise vehicle on ramp.
8. Remove undertray (refer to Workshop Manual procedure 01.02.NB Undertray - Front - Renew).
9. Drain oil tank. 10. Remove bottom pipe (x1) from oil tank (refer to Figure
2).
Figure 2
11. Remove bolts (x3) that attach the oil thermostat to body (allows oil hose movement).
12. Lower ramp.
13. Remove bolts (x4) that attach the tank to body and lift out.
Installation
1. Position tank to body and fit bolts (x4) (torque).
2. Install oil pipes to tank (torque).
3. Connect breather hose.
4. Connect top hose to engine (clip x1).
5. Raise vehicle on ramp.
6. Install bottom oil pipe to tank (torque).
7. Install bolts (x3) that attach the oil thermostat to body (torque).
8. Install undertray (refer to Workshop Manual procedure 01.02.NB Undertray - Front - Renew).
9. Lower vehicle.
10. Install throttle body duct.
11. Connect breather pipe quickf its (x2) to air cleaner duct.
12. Fill tank with approximately amount of displaced oil and replace cap.
13. Use handbook procedure to check oil level.
14. Top up coolant.
Thermostat - Renew
Removal
1. Drain Coolant (refer to Workshop Manual procedure 03.03.AD Coolant - Drain and Refill).
2. Release breather valve (bolt x1) and tie aside.
3. Unclip engine harness for access (x4).
4. Remove one end of engine breather hoses for access (x3).
Repair Operation Time (ROT)
A030243
Repair Operation Time (ROT)
A030244
Page 284 of 947
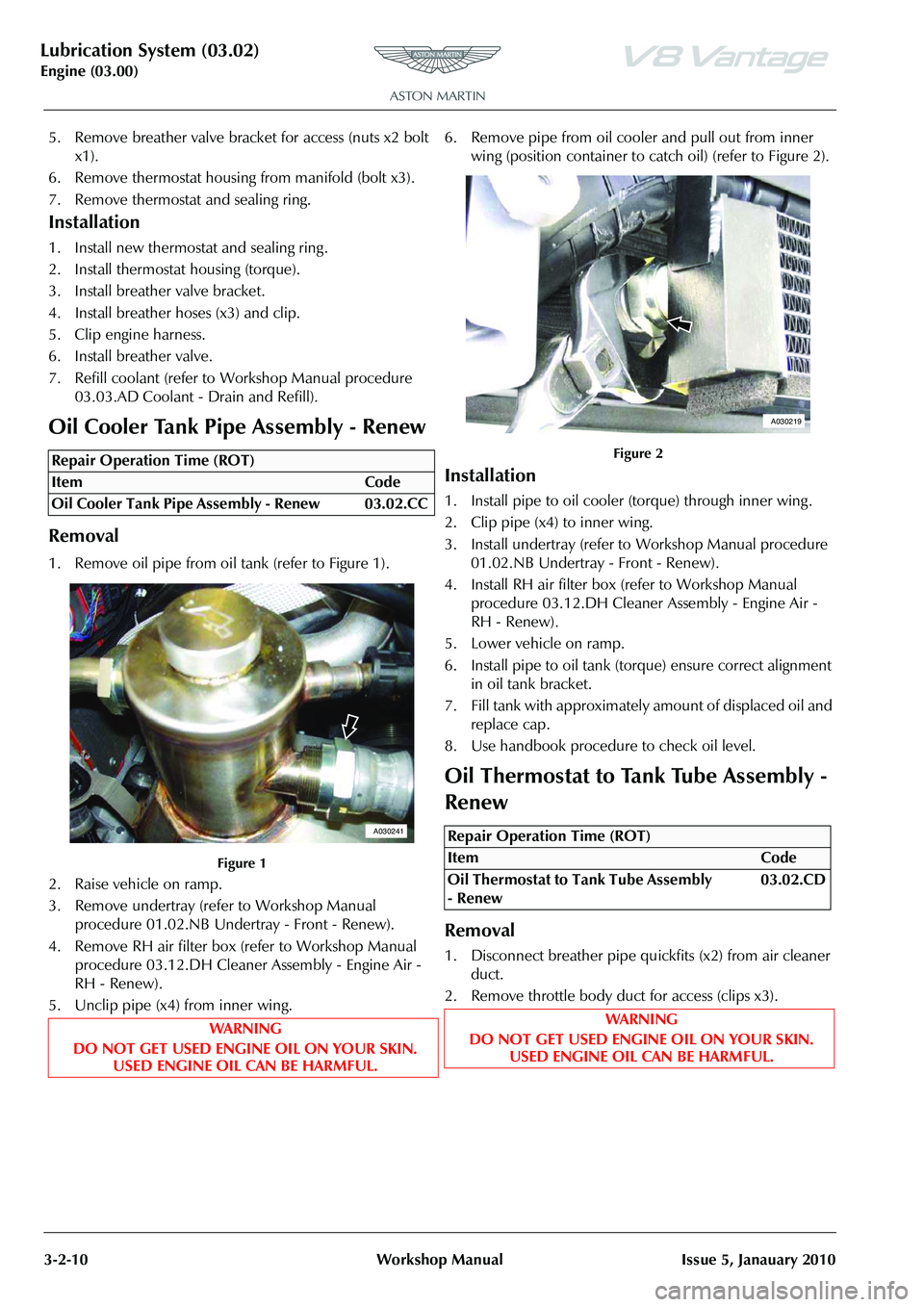
Lubrication System (03.02)
Engine (03.00)3-2-10 Workshop Manual Issue 5, Janauary 2010
5. Remove breather valve bracket for access (nuts x2 bolt x1).
6. Remove thermostat housing from manifold (bolt x3).
7. Remove thermostat and sealing ring.
Installation
1. Install new thermostat and sealing ring .
2. Install thermostat housing (torque).
3. Install breather valve bracket.
4. Install breather hoses (x3) and clip.
5. Clip engine harness.
6. Install breather valve.
7. Refill coolant (refer to Workshop Manual procedure 03.03.AD Coolant - Drain and Refill).
Oil Cooler Tank Pipe Assembly - Renew
Removal
1. Remove oil pipe from oil tank (refer to Figure 1).
Figure 1
2. Raise vehicle on ramp.
3. Remove undertray (refer to Workshop Manual
procedure 01.02.NB Undertray - Front - Renew).
4. Remove RH air filter box (refer to Workshop Manual
procedure 03.12.DH Cleaner Assembly - Engine Air -
RH - Renew).
5. Unclip pipe (x4) from inner wing. 6. Remove pipe from oil cool
er and pull out from inner
wing (position container to catch oil) (refer to Figure 2).
Figure 2
Installation
1. Install pipe to oil cooler (torque) through inner wing .
2. Clip pipe (x4) to inner wing.
3. Install undertray (refer to Workshop Manual procedure 01.02.NB Undertray - Front - Renew).
4. Install RH air filter box (refer to Workshop Manual
procedure 03.12.DH Cleaner Assembly - Engine Air -
RH - Renew).
5. Lower vehicle on ramp.
6. Install pipe to oil tank (torque) ensure correct alignment in oil tank bracket.
7. Fill tank with approximatel y amount of displaced oil and
replace cap.
8. Use handbook procedure to check oil level.
Oil Thermostat to Tank Tube Assembly -
Renew
Removal
1. Disconnect breather pipe qu ickfits (x2) from air cleaner
duct.
2. Remove throttle body duct for access (clips x3).
Repair Operation Time (ROT)
A030241Repair Operation Time (ROT)
ItemCode
Oil Thermostat to Tank Tube Assembly
- Renew 03.02.CD
WAR NI NG
DO NOT GET USED ENGINE OIL ON YOUR SKIN. USED ENGINE OIL CAN BE HARMFUL.
A030219
Page 289 of 947
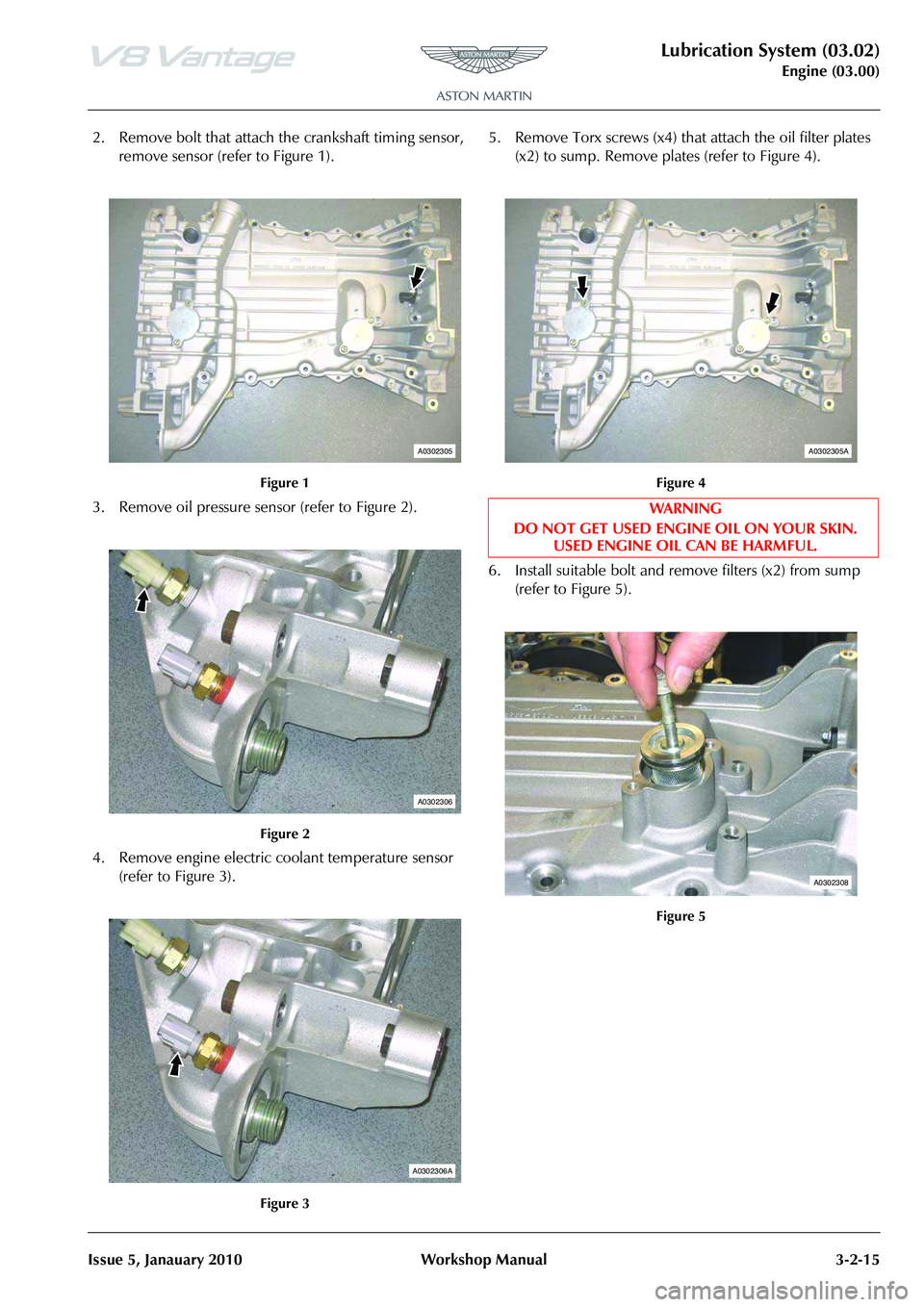
Lubrication System (03.02)
Engine (03.00)
Issue 5, Janauary 2010 Workshop Manual 3-2-15
2. Remove bolt that attach the crankshaft timing sensor, remove sensor (refer to Figure 1).
3. Remove oil pressure sens or (refer to Figure 2).
4. Remove engine electric coolant temperature sensor (refer to Figure 3). 5. Remove Torx screws (x4) that
attach the oil filter plates
(x2) to sump. Remove plates (refer to Figure 4).
6. Install suitable bolt and re move filters (x2) from sump
(refer to Figure 5).
Figure 1
Figure 2
Figure 3
A0302305
A0302306
A0302306A
Figure 4
WA R N I N G
DO NOT GET USED ENGINE OIL ON YOUR SKIN. USED ENGINE OIL CAN BE HARMFUL.
Figure 5
A0302305A
A0302308
Page 290 of 947
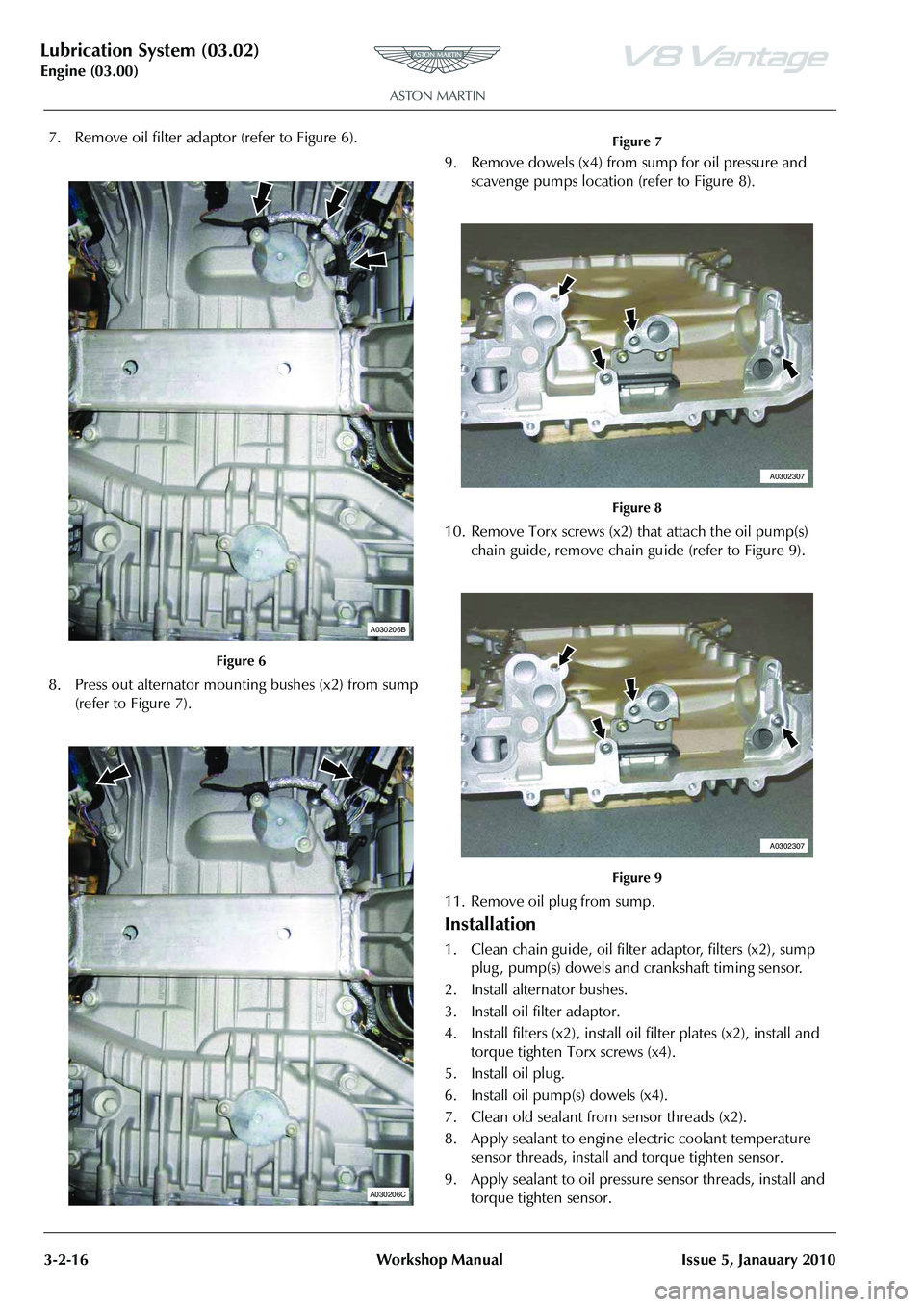
Lubrication System (03.02)
Engine (03.00)3-2-16 Workshop Manual Issue 5, Janauary 2010
7. Remove oil filter adaptor (refer to Figure 6).
8. Press out alternator mounting bushes (x2) from sump (refer to Figure 7). 9. Remove dowels (x4) from
sump for oil pressure and
scavenge pumps location (refer to Figure 8).
10. Remove Torx screws (x2) that attach the oil pump(s)
chain guide, remove chain gu ide (refer to Figure 9).
11. Remove oil plug from sump.
Installation
1. Clean chain guide, oil filter adaptor, filters (x2), sump plug , pump(s) dowels and crankshaft timing sensor.
2. Install alternator bushes.
3. Install oil filter adaptor.
4. Install filters (x2), install oil filter plates (x2), install and
torque tighten Torx screws (x4).
5. Install oil plug.
6. Install oil pump(s) dowels (x4).
7. Clean old sealant from sensor threads (x2).
8. Apply sealant to engine electric coolant temperature sensor threads, install and torque tighten sensor.
9. Apply sealant to oil pressure sensor threads, install and torque tighten sensor.
Figure 6
A030206B
A030206C
Figure 7
Figure 8
Figure 9
A0302307
A0302307
Page 291 of 947
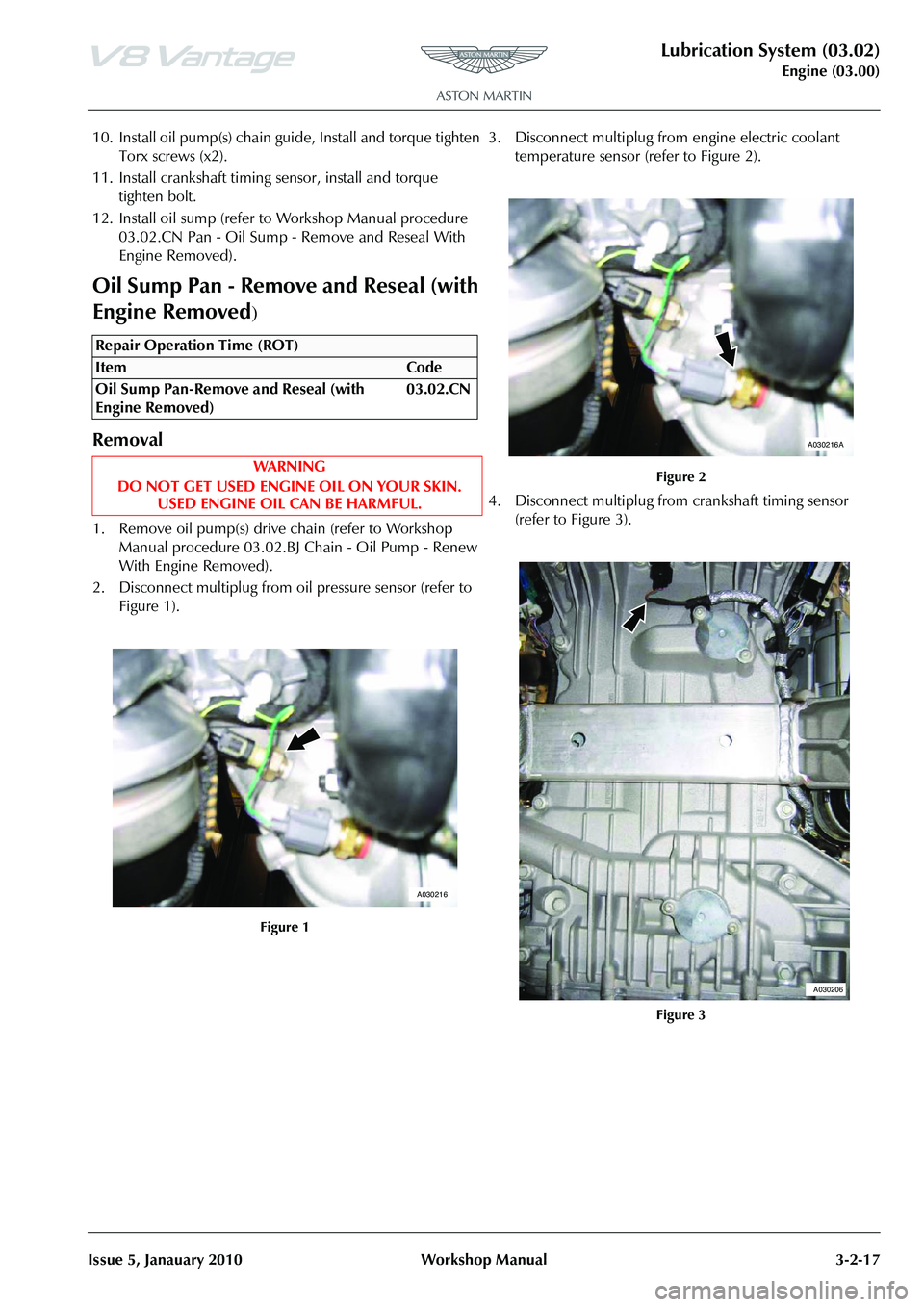
Lubrication System (03.02)
Engine (03.00)
Issue 5, Janauary 2010 Workshop Manual 3-2-17
10. Install oil pump(s) chain guid e, Install and torque tighten
Torx screws (x2).
11. Install crankshaft timing sensor, install and torque
tighten bolt.
12. Install oil sump (refer to Workshop Manual procedure
03.02.CN Pan - Oil Sump - Remove and Reseal With
Engine Removed).
Oil Sump Pan - Remove and Reseal (with
Engine Removed
)
Removal
1. Remove oil pump(s) drive chain (refer to Workshop Manual procedure 03.02.BJ Chain - Oil Pump - Renew
With Engine Removed).
2. Disconnect multiplug from oi l pressure sensor (refer to
Figure 1). 3. Disconnect multiplug from
engine electric coolant
temperature sensor (refer to Figure 2).
4. Disconnect multiplug from crankshaft timing sensor
(refer to Figure 3).
Repair Operation Time (ROT)
A030216
Figure 2
Figure 3
A030216A
A030206
Page 293 of 947
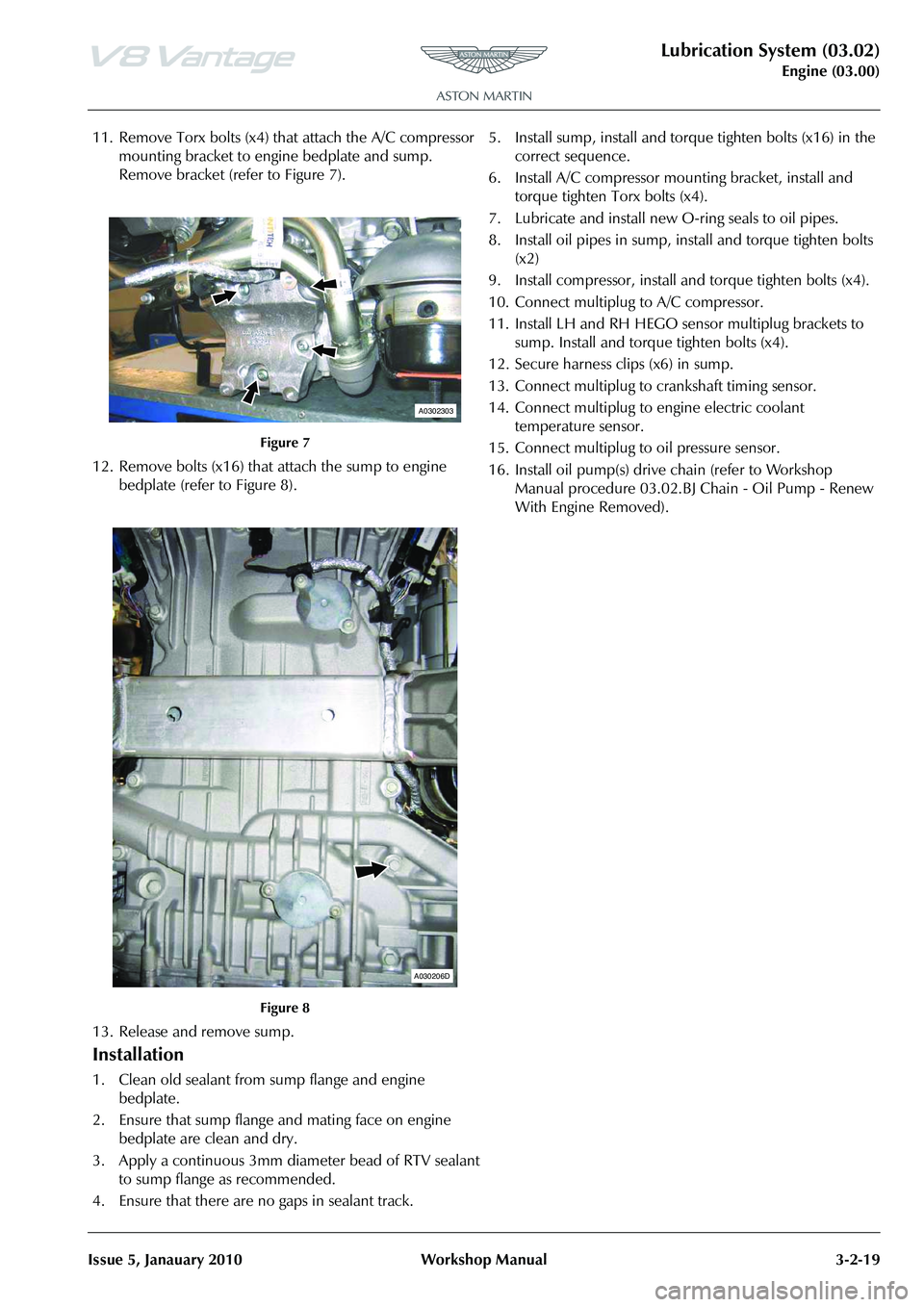
Lubrication System (03.02)
Engine (03.00)
Issue 5, Janauary 2010 Workshop Manual 3-2-19
11. Remove Torx bolts (x4) that attach the A/C compressor mounting bracket to engine bedplate and sump.
Remove bracket (refer to Figure 7).
12. Remove bolts (x16) that attach the sump to engine bedplate (refer to Figure 8).
13. Release and remove sump.
Installation
1. Clean old sealant from sump flange and engine bedplate.
2. Ensure that sump flange and mating face on engine bedplate are clean and dry.
3. Apply a continuous 3mm diameter bead of RTV sealant to sump flange as recommended.
4. Ensure that there are no gaps in sealant track. 5. Install sump, install and torque tighten bolts (x16) in the
correct sequence.
6. Install A/C compressor mounting bracket, install and torque tighten Torx bolts (x4).
7. Lubricate and install new O-ring seals to oil pipes.
8. Install oil pipes in sump, install and torque tighten bolts (x2)
9. Install compressor, install and torque tighten bolts (x4).
10. Connect multiplug to A/C compressor.
11. Install LH and RH HEGO se nsor multiplug brackets to
sump. Install and torque tighten bolts (x4).
12. Secure harness clips (x6) in sump.
13. Connect multiplug to crankshaft timing sensor.
14. Connect multiplug to engine electric coolant temperature sensor.
15. Connect multiplug to oil pressure sensor.
16. Install oil pump(s) drive chain (refer to Workshop Manual procedure 03.02.BJ Chain - Oil Pump - Renew
With Engine Removed).
Figure 7
Figure 8
A0302303
A030206D
Page 295 of 947
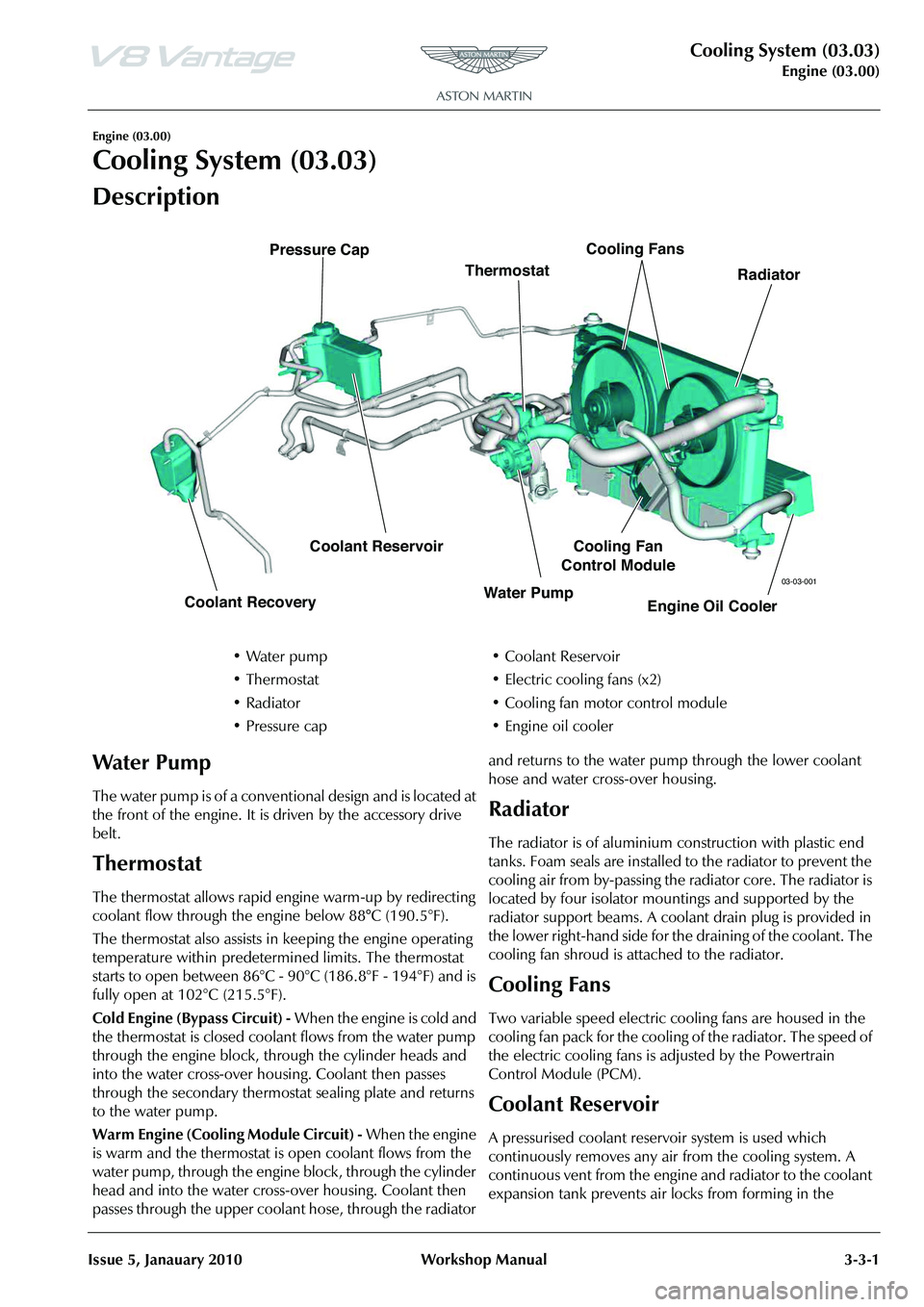
Cooling System (03.03)
Engine (03.00)
Issue 5, Janauary 2010 Workshop Manual 3-3-1
Engine (03.00)
Cooling System (03.03)
Description
The water pump is of a conventional design and is located at
the front of the engine. It is driven by the accessory drive
belt.
Thermostat
The thermostat allows rapid en gine warm-up by redirecting
coolant flow through the engine below 88 °C (190.5°F).
The thermostat also assists in keeping the engine operating
temperature within predetermi ned limits. The thermostat
starts to open between 86°C - 90°C (186.8°F - 194°F) and is
fully open at 102°C (215.5°F).
Cold Engine (Bypass Circuit) - When the engine is cold and
the thermostat is closed coolant flows from the water pump
through the engine block, through the cylinder heads and
into the water cross-over housing. Coolant then passes
through the secondary thermostat sealing plate and returns
to the water pump.
Warm Engine (Cooling Module Circuit) - When the engine
is warm and the thermostat is open coolant flows from the
water pump, through the engine block, through the cylinder
head and into the water cros s-over housing. Coolant then
passes through the upper coolant hose, through the radiator and returns to the water pump through the lower coolant
hose and water cross-over housing.
Radiator
The radiator is of aluminium construction with plastic end
tanks. Foam seals are installed to the radiator to prevent the
cooling air from by-passing the radiator core. The radiator is
located by four isolator mo
untings and supported by the
radiator support beams. A coolant drain plug is provided in
the lower right-hand side for the draining of the coolant. The
cooling fan shroud is attached to the radiator.
Cooling Fans
Two variable speed electric cooling fans are housed in the
cooling fan pack for the cooling of the radiator. The speed of
the electric cooling fans is adjusted by the Powertrain
Control Module (PCM).
Coolant Reservoir
A pressurised coolant reservoir system is used which
continuously removes any air from the cooling system. A
continuous vent from the engine and radiator to the coolant
expansion tank prevents air locks from forming in the
•Water pump
• Thermostat
•Radiator
• Pressure cap
• Coolant Reservoir
• Electric cooling fans (x2)
• Cooling fan motor control module
• Engine oil cooler
Radiator
Cooling Fans
Thermostat
Coolant Reservoir Engine Oil Cooler
Cooling Fan
Control Module
Water Pump
Coolant Recovery Pressure Cap
03-03-001
Page 296 of 947
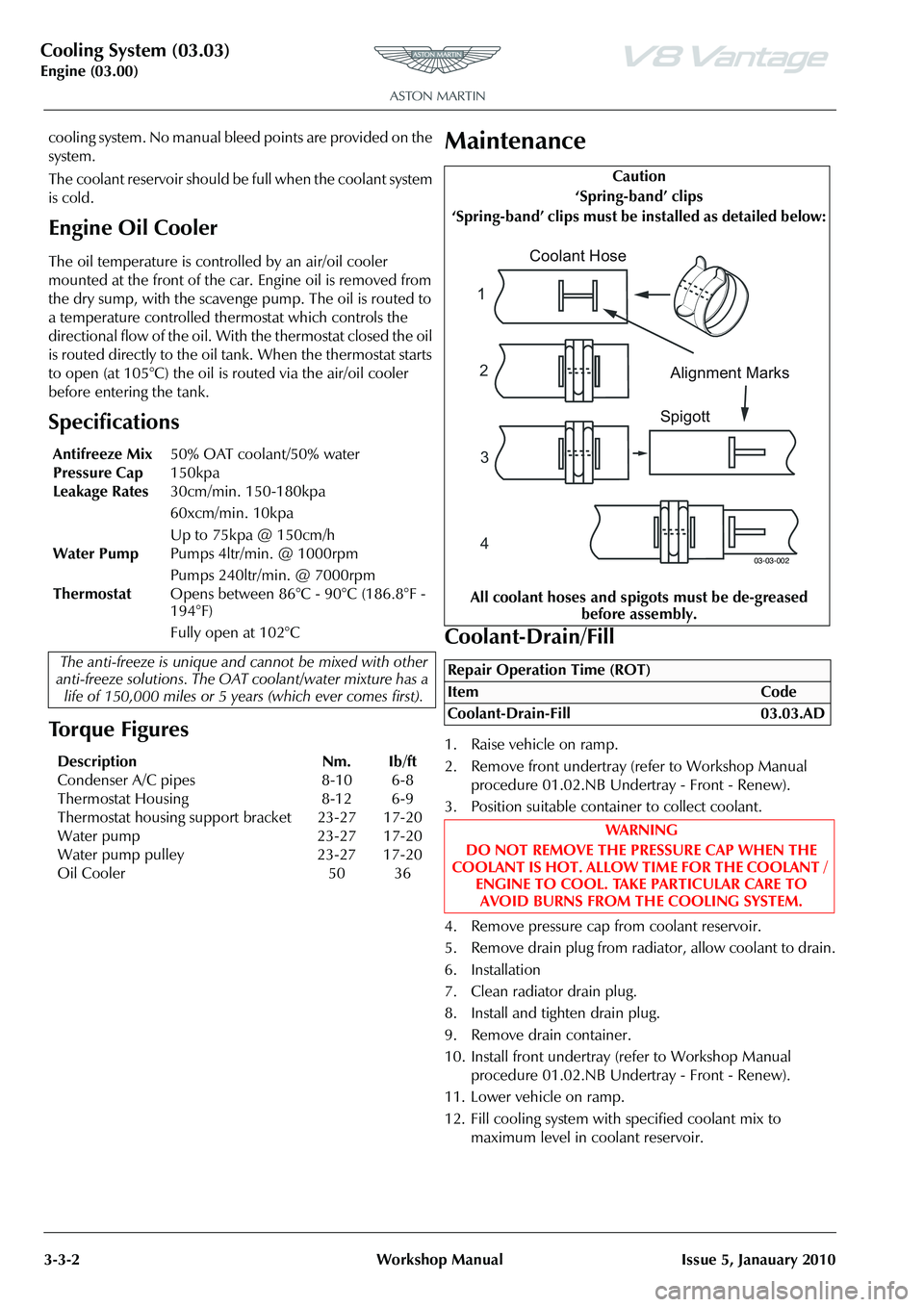
Cooling System (03.03)
Engine (03.00)3-3-2 Workshop Manual Issue 5, Janauary 2010
cooling system. No manual bleed points are provided on the
system.
The coolant reservoir should be full when the coolant system
is cold.
Engine Oil Cooler
The oil temperature is contro lled by an air/oil cooler
mounted at the front of the car. Engine oil is removed from
the dry sump, with the scavenge pump. The oil is routed to
a temperature controlled thermostat which controls the
directional flow of the oil. With the thermostat closed the oil
is routed directly to the oil tank. When the thermostat starts
to open (at 105°C) the oil is routed via the air/oil cooler
before entering the tank.
Specifications
Torque Figures
Maintenance
Coolant-Drain/Fill
1. Raise vehicle on ramp.
2. Remove front undertray (refer to Workshop Manual procedure 01.02.NB Undertray - Front - Renew).
3. Position suitable container to collect coolant.
4. Remove pressure cap from coolant reservoir.
5. Remove drain plug from radiator, allow coolant to drain.
6. Installation
7. Clean radiator drain plug.
8. Install and tighten drain plug.
9. Remove drain container.
10. Install front undertray (refer to Workshop Manual procedure 01.02.NB Undertray - Front - Renew).
11. Lower vehicle on ramp.
12. Fill cooling system with specified coolant mix to maximum level in coolant reservoir.
Antifreeze Mix
50% OAT coolant/50% water
Pressure Cap 150kpa
Leakage Rates 30cm/min. 150-180kpa
60xcm/min. 10kpa
Up to 75kpa @ 150cm/h
Water Pump Pumps 4ltr/min. @ 1000rpm
Pumps 240ltr/min. @ 7000rpm
Thermostat Opens between 86°C - 90°C (186.8°F -
194°F)
Fully open at 102°C
The anti-freeze is un ique and cannot be mixed with other
anti-freeze solutions. The OAT coolant/water mixture has a
life of 150,000 miles or 5 years (which ever comes first).
Description Nm. Ib/ft
Condenser A/C pipes 8-10 6-8
Thermostat Housing 8-12 6-9
Thermostat housing support bracket 23-27 17-20
Water pump 23-27 17-20
Water pump pulley 23-27 17-20
Oil Cooler 50 36
Caution
‘Spring-band’ clips
‘Spring-band’ clips must be installed as detailed below:
All coolant hoses and spigots must be de-greased before assembly.
Repair Operation Time (ROT)
ItemCode
Coolant-Drain-Fill 03.03.AD
WAR NI NG
DO NOT REMOVE THE PRESSURE CAP WHEN THE
COOLANT IS HOT. ALLOW TIME FOR THE COOLANT /
ENGINE TO COOL. TAKE PARTICULAR CARE TO AVOID BURNS FROM THE COOLING SYSTEM.
03-03-002
3
2
4
Coolant Hose SpigottAlignment Marks