weight ASTON MARTIN V8 VANTAGE 2010 Owner's Manual
[x] Cancel search | Manufacturer: ASTON MARTIN, Model Year: 2010, Model line: V8 VANTAGE, Model: ASTON MARTIN V8 VANTAGE 2010Pages: 947, PDF Size: 43.21 MB
Page 642 of 947
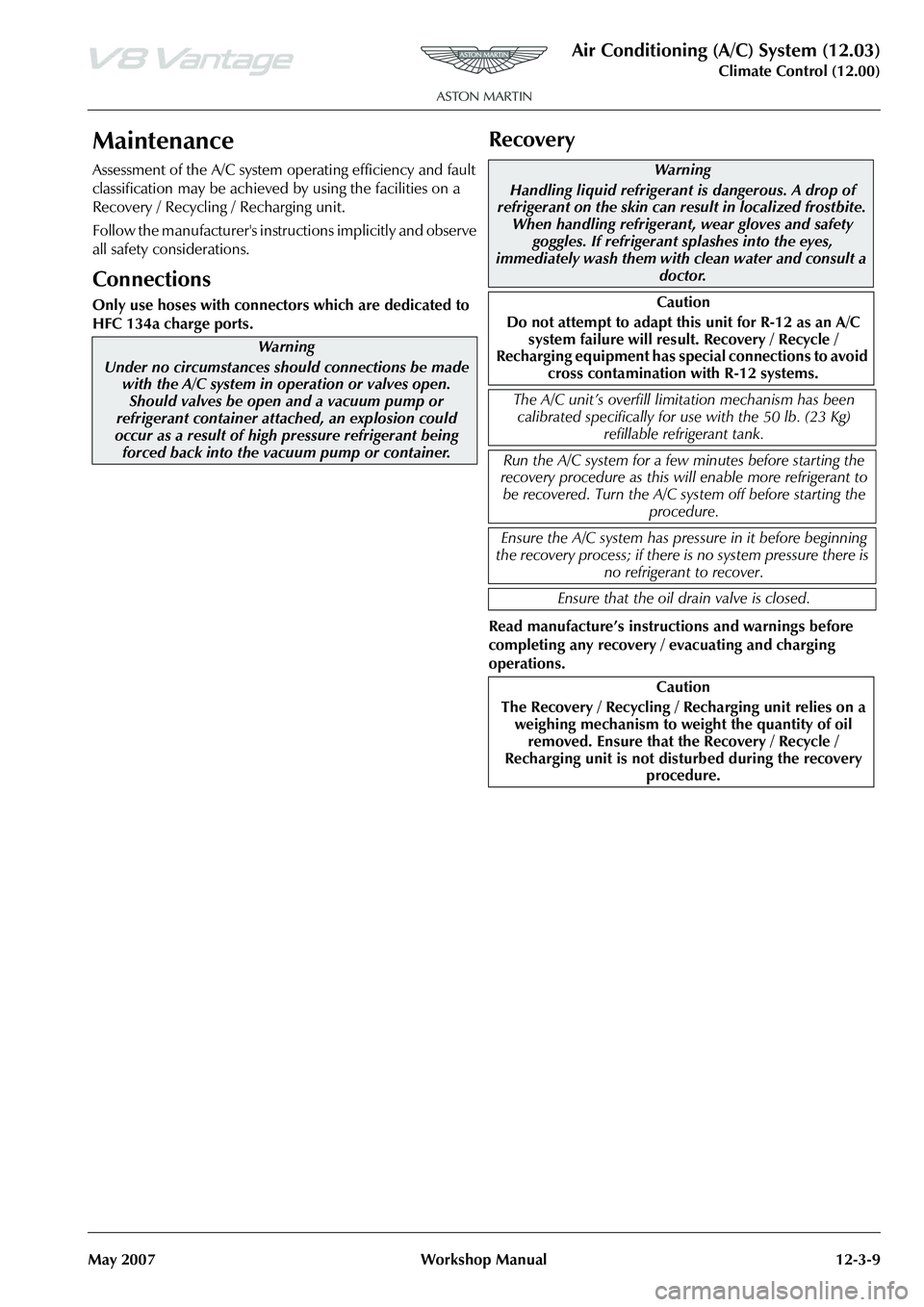
Air Conditioning (A/C) System (12.03)
Climate Control (12.00)
May 2007 Workshop Manual 12-3-9
Maintenance
Assessment of the A/C system operating efficiency and fault
classification may be achieved by using the facilities on a
Recovery / Recycling / Recharging unit.
Follow the manufacturer's instructions implicitly and observe
all safety considerations.
Connections
Only use hoses with connectors which are dedicated to
HFC 134a charge ports.
Recovery
Read manufacture’s instructions and warnings before
completing any recovery / evacuating and charging
operations.
Warning
Under no circumstances should connections be made with the A/C system in operation or valves open. Should valves be open and a vacuum pump or
refrigerant container attached, an explosion could
occur as a result of high pressure refrigerant being forced back into the vacuum pump or container.
Warning
Handling liquid refrigerant is dangerous. A drop of
refrigerant on the skin can result in localized frostbite. When handling refrigerant, wear gloves and safety
goggles. If refrigerant sp lashes into the eyes,
immediately wash them with clean water and consult a doctor.
Caution
Do not attempt to adapt this unit for R-12 as an A/C
system failure will result. Recovery / Recycle /
Recharging equipment has sp ecial connections to avoid
cross contamination wi th R-12 systems.
The A/C unit’s overfill li mitation mechanism has been
calibrated specifically for use with the 50 lb. (23 Kg)
refillable refrigerant tank.
Run the A/C system for a few minutes before starting the
recovery procedure as this wil l enable more refrigerant to
be recovered. Turn the A/C system off before starting the
procedure.
Ensure the A/C system has pre ssure in it before beginning
the recovery process; if there is no system pressure there is
no refrigerant to recover.
Ensure that the oil drain valve is closed.
Caution
The Recovery / Recycling / Re charging unit relies on a
weighing mechanism to weight the quantity of oil
removed. Ensure that the Recovery / Recycle /
Recharging unit is not disturbed during the recovery procedure.
Page 645 of 947
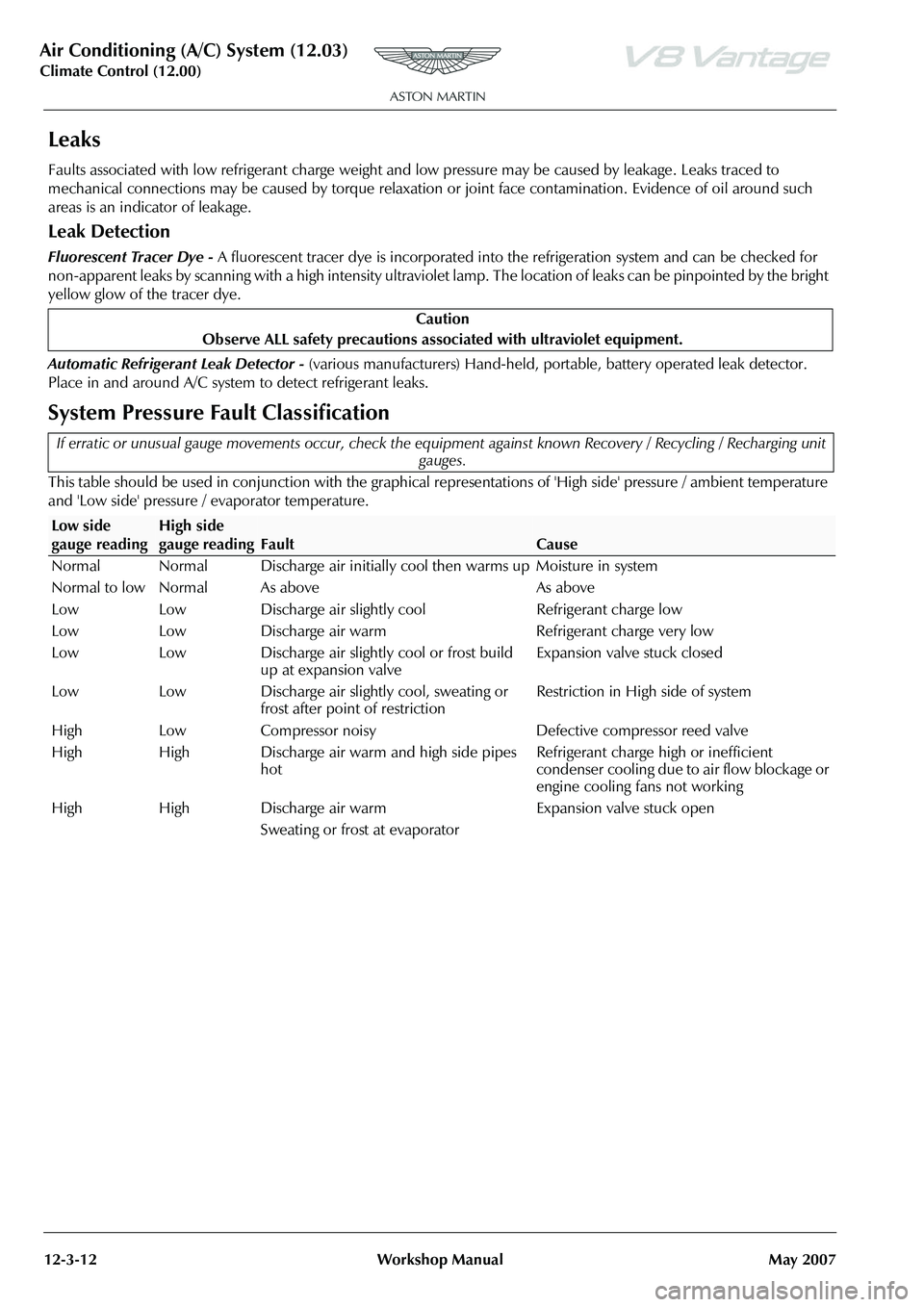
Air Conditioning (A/C) System (12.03)
Climate Control (12.00)
12-3-12 Workshop Manual May 2007
Leaks
Faults associated with low refrigerant charge weight and low pressure may be caused by leakage. Leaks traced to
mechanical connections may be caused by torque relaxation or joint face contamination. Evidence of oil around such
areas is an indicator of leakage.
Leak Detection
Fluorescent Tracer Dye - A fluorescent tracer dye is incorporated into th e refrigeration system and can be checked for
non-apparent leaks by scanning with a high intensity ultraviolet lamp. The location of leaks can be pinpointed by the bright
yellow glow of the tracer dye.
Automatic Refrigerant Leak Detector - (various manufacturers) Hand-held, portable, battery operated leak detector.
Place in and around A/C system to detect refrigerant leaks.
System Pressure Fault Classification
This table should be used in conjunction with the graphical representations of 'High side' pressure / ambient temperature
and 'Low side' pressure / evaporator temperature. Caution
Observe ALL safety precautions associ ated with ultraviolet equipment.
If erratic or unusual gauge movements occur, check the equipment against known Recovery / Recycling / Recharging unit
gauges.
Low side
gauge readingHigh side
gauge reading
Fault
Cause
Normal Normal Discharge air initially c ool then warms up Moisture in system
Normal to low Normal As above As above
Low Low Discharge air slightly cool Refrigerant charge low
Low Low Discharge air warm Refrigerant charge very low
Low Low Discharge air slightly cool or frost build up at expansion valve Expansion valve stuck closed
Low Low Discharge air slightly cool, sweating or frost after point of restriction Restriction in High side of system
High Low Compressor noisy Defective compressor reed valve
High High Discharge air warm and high side pipes hot Refrigerant charge high or inefficient
condenser cooling due to air flow blockage or
engine cooling fans not working
High High Discharge air warm
Sweating or frost at evaporator Expansion valve stuck open
Page 682 of 947
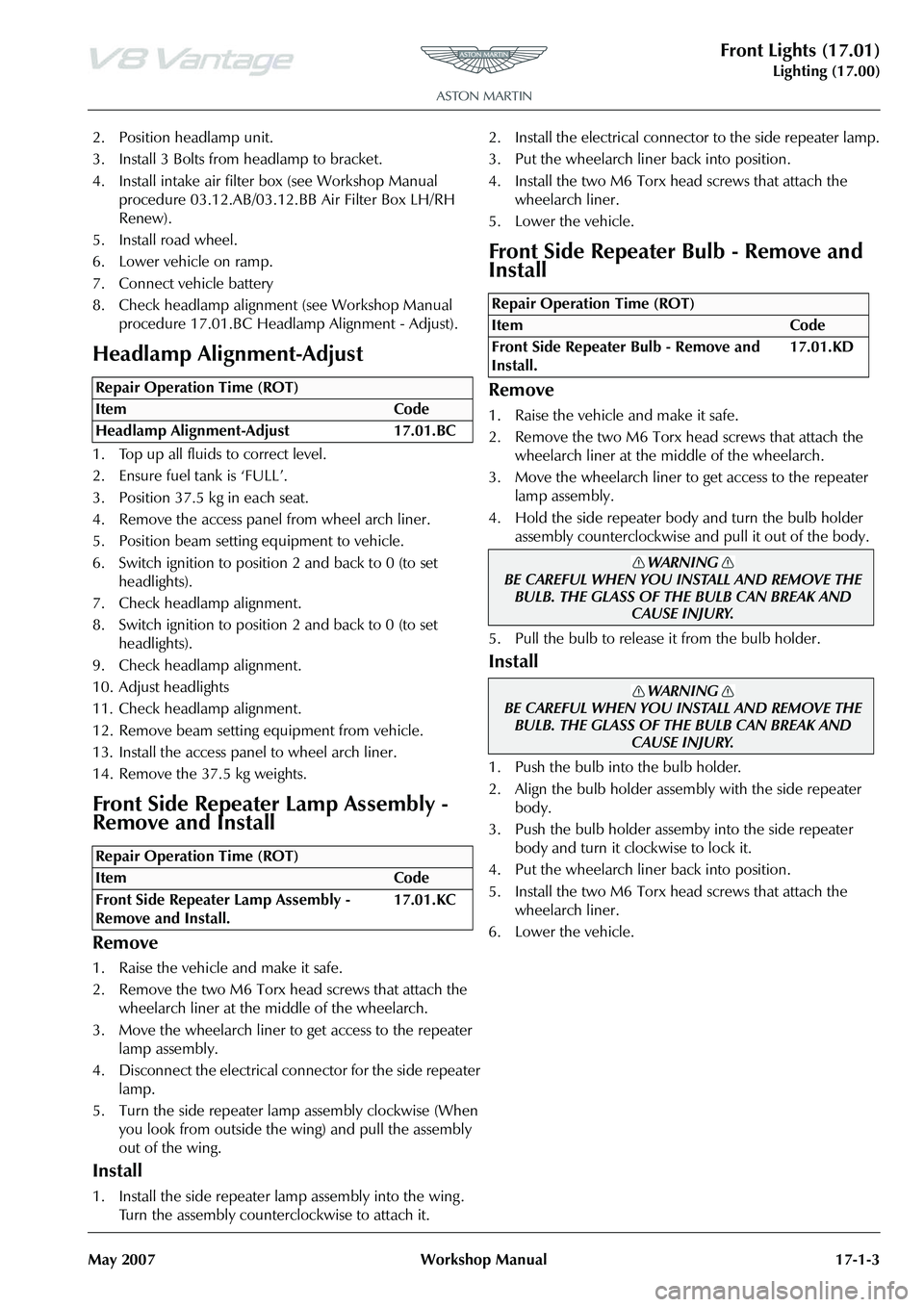
Front Lights (17.01)
Lighting (17.00)
May 2007 Workshop Manual 17-1-3
2. Position headlamp unit.
3. Install 3 Bolts from headlamp to bracket.
4. Install intake air filter box (see Workshop Manual procedure 03.12.AB/03.12.BB Air Filter Box LH/RH
Renew).
5. Install road wheel.
6. Lower vehicle on ramp.
7. Connect vehicle battery
8. Check headlamp alignment (see Workshop Manual procedure 17.01.BC Headlamp Alignment - Adjust).
Headlamp Alignment-Adjust
1. Top up all fluids to correct level.
2. Ensure fuel tank is ‘FULL’.
3. Position 37.5 kg in each seat.
4. Remove the access panel from wheel arch liner.
5. Position beam setting equipment to vehicle.
6. Switch ignition to position 2 and back to 0 (to set headlights).
7. Check headlamp alignment.
8. Switch ignition to position 2 and back to 0 (to set headlights).
9. Check headlamp alignment.
10. Adjust headlights
11. Check headlamp alignment.
12. Remove beam setting equipment from vehicle.
13. Install the access panel to wheel arch liner.
14. Remove the 37.5 kg weights.
Front Side Repeater Lamp Assembly -
Remove and Install
Remove
1. Raise the vehicle and make it safe.
2. Remove the two M6 Torx head screws that attach the wheelarch liner at the middle of the wheelarch.
3. Move the wheelarch liner to get access to the repeater lamp assembly.
4. Disconnect the electrical connector for the side repeater lamp.
5. Turn the side repeater lamp assembly clockwise (When
you look from outside the wing) and pull the assembly
out of the wing.
Install
1. Install the side repeater lamp assembly into the wing . Turn the assembly counterclockwise to attach it. 2. Install the electrical connector to the side repeater lamp.
3. Put the wheelarch liner back into position.
4. Install the two M6 Torx head screws that attach the
wheelarch liner.
5. Lower the vehicle.
Front Side Repeater Bulb - Remove and
Install
Remove
1. Raise the vehicle and make it safe.
2. Remove the two M6 Torx head screws that attach the
wheelarch liner at the middle of the wheelarch.
3. Move the wheelarch liner to get access to the repeater lamp assembly.
4. Hold the side repeater body and turn the bulb holder assembly counterclockwise an d pull it out of the body.
5. Pull the bulb to release it from the bulb holder.
Install
1. Push the bulb into the bulb holder.
2. Align the bulb holder assembly with the side repeater body.
3. Push the bulb holder assemby into the side repeater body and turn it clockwise to lock it.
4. Put the wheelarch liner back into position.
5. Install the two M6 Torx head screws that attach the wheelarch liner.
6. Lower the vehicle.
Repair Operation Time (ROT)
Repair Operation Time (ROT)
Repair Operation Time (ROT)
WARNING
BE CAREFUL WHEN YOU IN STALL AND REMOVE THE
BULB. THE GLASS OF THE BULB CAN BREAK AND CAUSE INJURY.
WARNING
BE CAREFUL WHEN YOU IN STALL AND REMOVE THE
BULB. THE GLASS OF THE BULB CAN BREAK AND
CAUSE INJURY.
Page 711 of 947
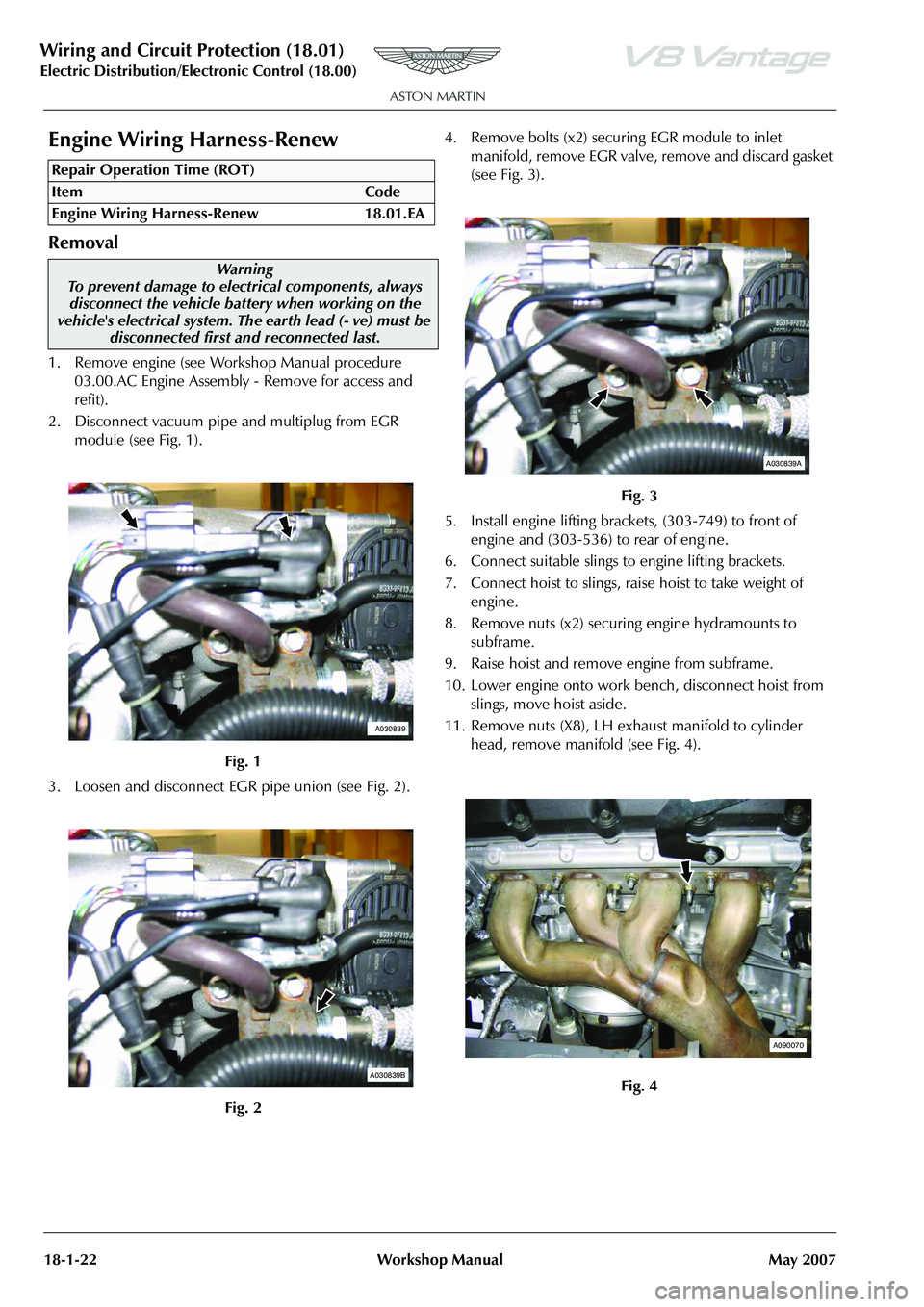
Wiring and Circuit Protection (18.01)
Electric Distribution/E lectronic Control (18.00)
18-1-22 Workshop Manual May 2007
Engine Wiring Harness-Renew
Removal
1. Remove engine (see Workshop Manual procedure
03.00.AC Engine Assembly - Remove for access and
refit).
2. Disconnect vacuum pipe and multiplug from EGR module (see Fig. 1).
3. Loosen and disconnect EGR pipe union (see Fig. 2). 4. Remove bolts (x2) securing EGR module to inlet
manifold, remove EGR valve, remove and discard gasket
(see Fig. 3).
5. Install engine lifting brackets, (303-749) to front of engine and (303-536) to rear of engine.
6. Connect suitable slings to engine lifting brackets.
7. Connect hoist to slings, raise hoist to take weight of engine.
8. Remove nuts (x2) securi ng engine hydramounts to
subframe.
9. Raise hoist and remove engine from subframe.
10. Lower engine onto work be nch, disconnect hoist from
slings, move hoist aside.
11. Remove nuts (X8), LH exhaust manifold to cylinder head, remove manifold (see Fig. 4).
Repair Operation Time (ROT)
Warning
To prevent damage to electrical components, always disconnect the vehicle battery when working on the
vehicle's electrical system. Th e earth lead (- ve) must be
disconnected first and reconnected last.
Fig. 1
Fig. 2
$
$ %
Fig. 3
Fig. 4
$ $
% $
Page 850 of 947
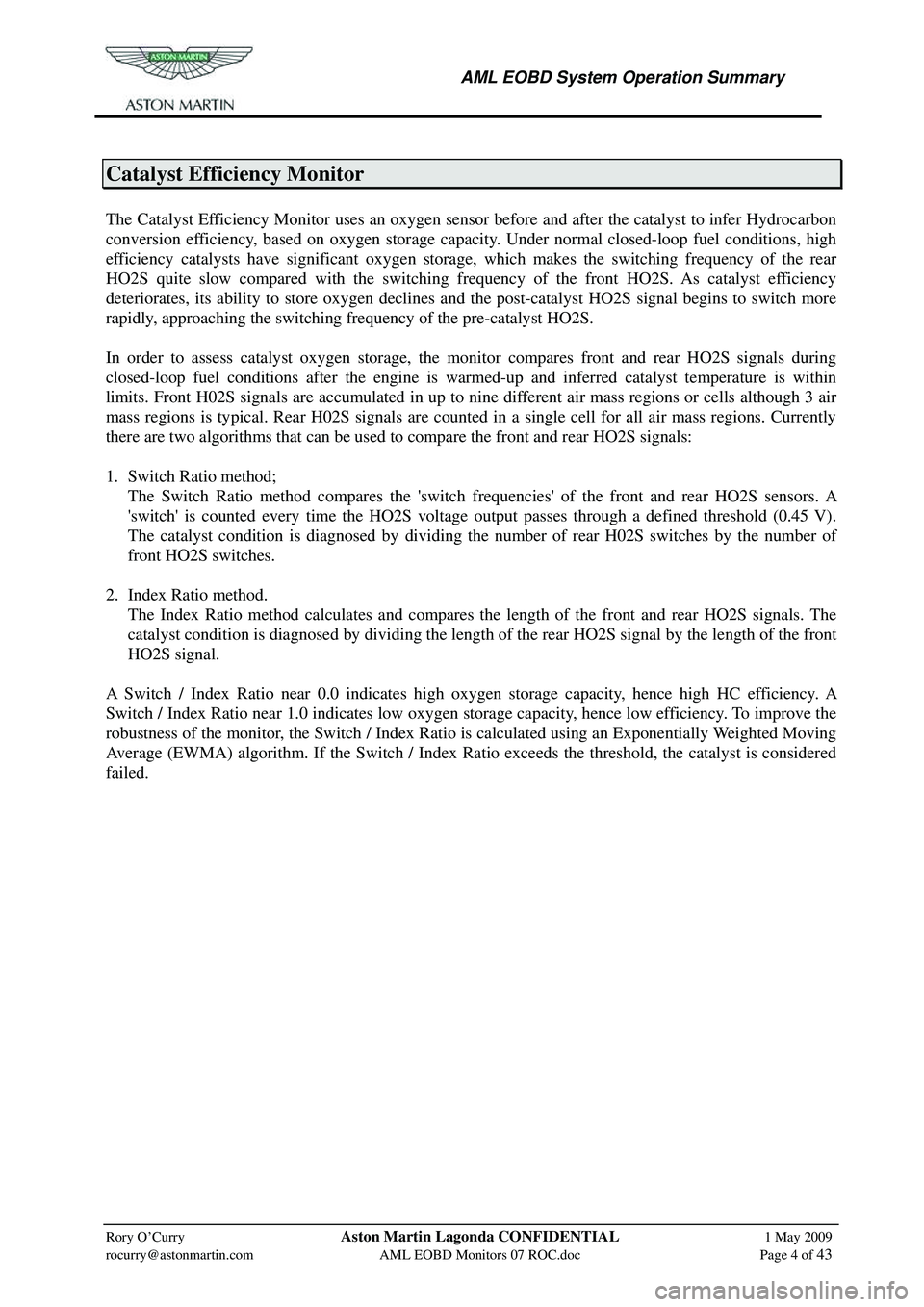
AML EOBD System Operation Summary
Rory O’Curry Aston Martin Lagonda CONFIDENTIAL 1 May 2009
[email protected] AML EOBD Monitors 07 ROC.doc Page 4 of 43
Catalyst Efficiency Monitor
The Catalyst Efficiency Monitor uses an oxygen sensor before and after the catalyst to infer Hydrocarbon
conversion efficiency, based on oxygen storage capac ity. Under normal closed-loop fuel conditions, high
efficiency catalysts have significant oxygen storage, which makes the switching frequency of the rear
HO2S quite slow compared with the switching freque ncy of the front HO2S. As catalyst efficiency
deteriorates, its ability to store oxygen declines and the post-catalyst HO2S signal begins to switch more
rapidly, approaching the switching frequency of the pre-catalyst HO2S.
In order to assess catalyst oxygen storage, the monitor compares front and rear HO2S signals during
closed-loop fuel conditions after the engine is warm ed-up and inferred catalyst temperature is within
limits. Front H02S signals are accumulated in up to ni ne different air mass regions or cells although 3 air
mass regions is typical. Rear H02S signals are counted in a single cell for all air mass regions. Currently
there are two algorithms that can be used to compare the front and rear HO2S signals:
1. Switch Ratio method;
The Switch Ratio method compares the 'switch frequencies' of the front and rear HO2S sensors. A
'switch' is counted every time the HO2S voltage output passes through a defined threshold (0.45 V).
The catalyst condition is diagnosed by dividing the number of rear H02S switches by the number of
front HO2S switches.
2. Index Ratio method.
The Index Ratio method calculates and compares the length of the front and rear HO2S signals. The
catalyst condition is diagnosed by dividing the length of the rear HO2S signal by the length of the front
HO2S signal.
A Switch / Index Ratio near 0.0 indicates high oxygen storage capacity, hence high HC efficiency. A
Switch / Index Ratio near 1.0 indicates low oxygen storage capacity, hence low efficiency. To improve the
robustness of the monitor, the Switch / Index Ratio is calculated using an Exponentially Weighted Moving
Average (EWMA) algorithm. If the Switch / Index Ratio exceeds the threshold, the catalyst is considered
failed.
Page 871 of 947
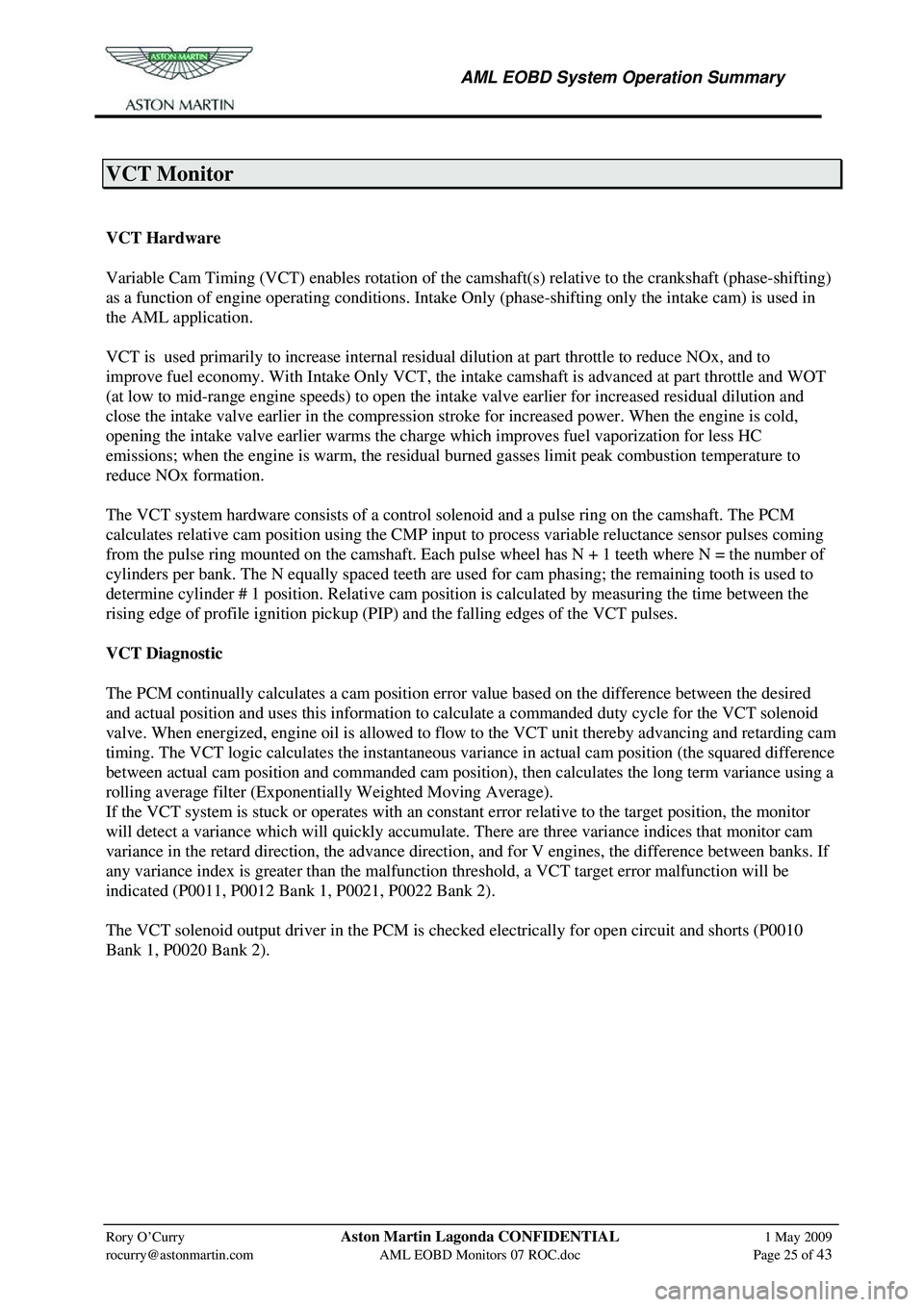
AML EOBD System Operation Summary
Rory O’Curry Aston Martin Lagonda CONFIDENTIAL 1 May 2009
[email protected] AML EOBD Monitors 07 ROC.doc Page 25 of 43
VCT Monitor
Variable Cam Timing System Monitor
VCT Hardware
Variable Cam Timing (VCT) enables rotation of the camshaft(s) relative to the crankshaft (phase-shifting)
as a function of engine operating conditions. Intake Only (phase-shifting only the intake cam) is used in
the AML application.
VCT is used primarily to increase internal residua l dilution at part throttle to reduce NOx, and to
improve fuel economy. With Intake Only VCT, the in take camshaft is advanced at part throttle and WOT
(at low to mid-range engine speeds) to open the in take valve earlier for increased residual dilution and
close the intake valve earlier in the compression stroke for increased power. When the engine is cold,
opening the intake valve earlier warms the charge which improves fuel vaporization for less HC
emissions; when the engine is warm, the residua l burned gasses limit peak combustion temperature to
reduce NOx formation.
The VCT system hardware consists of a contro l solenoid and a pulse ring on the camshaft. The PCM
calculates relative cam position using the CMP input to process variable reluctance sensor pulses coming
from the pulse ring mounted on the camshaft. Each pul se wheel has N + 1 teeth where N = the number of
cylinders per bank. The N equally spaced teeth are used for cam phasing; the remaining tooth is used to
determine cylinder # 1 position. Relative cam position is calculated by measuring the time between the
rising edge of profile ignition pickup (PIP ) and the falling edges of the VCT pulses.
VCT Diagnostic
The PCM continually calculates a cam position error value based on the difference between the desired
and actual position and uses this information to cal culate a commanded duty cycle for the VCT solenoid
valve. When energized, engine oil is allowed to flow to the VCT unit thereby advancing and retarding cam
timing. The VCT logic calculates the instantaneous va riance in actual cam position (the squared difference
between actual cam position and commanded cam position), then calculates the long term variance using a
rolling average filter (Exponentially Weighted Moving Average).
If the VCT system is stuck or operates with an consta nt error relative to the target position, the monitor
will detect a variance which will quickly accumulate. There are three variance indices that monitor cam
variance in the retard direction, the advance directi on, and for V engines, the difference between banks. If
any variance index is greater than the malfunction threshold, a VCT target error malfunction will be
indicated (P0011, P0012 Bank 1, P0021, P0022 Bank 2).
The VCT solenoid output driver in the PCM is check ed electrically for open circuit and shorts (P0010
Bank 1, P0020 Bank 2).
VCT Monitor Operation:
Page 883 of 947

AML EOBD System Operation Summary
Rory O’Curry Aston Martin Lagonda CONFIDENTIAL 1 May 2009
[email protected] AML EOBD Monitors 07 ROC.doc Page 37 of 43
Glossary of Terms
A/D Analogue to Digital
ASM Auto Shift Manul
BTDC Before Top Dead Centre
CALID CALibration IDentification
CD4E Automatic Transmission for Intermediate size Family saloon.
CID Camshaft Identification.
CKP Crankshaft Position
CMP Camshaft Position
COP Coil on Plug
CPC Camshaft Position Control
CVN Calibration Verification Number
DPFE Delta Pressure Feedback
DTC Diagnostic Trouble Code
ECT Engine Coolant Temperature
EDIS Electronic Distributorless Ignition System
EGR Exhaust Gas Re-circulation.
EOBD European On Bard Diagnostics
EPC Electronic Pressure Control
ETC Electronic Throttle Control
ETM Electronic Throttle Monitor
EVR Electronic Vacuum Regulator
EWMA Exponentially Weighted Moving Average
FMEM Failure Mode and Effects Management
FN Automatic Transmission for Medium size Family Saloon
FWD Front Wheel Drive
HDR High Data Rate
HO2S Heated Oxygen Sensor.
IAC Idle Air Control
IDM Ignition Diagnostic Monitor
IMRC Inlet Manifold Runner Control
IPC Independent Plausibility Checker
KAM Keep Alive Memory
LDR Low Data Rate
LTFT Long Term Fuel Trim
MAF Mass Air Flow
MAP Manifold Absolute Pressure
MIL Malfunction Indicator Lamp
OSS Output Shaft Speed
PCM Powertrain Control Module
PIP Profile Ignition Pickup
RWD Rear Wheel Drive
SAE Society of Automotive Engineers
SAIR Secondary AIR
SCV Swirl Control Valve
STFT Short Term Fuel Trim
TCC Torque Converter Clutch
TCIL Transmission Control Indicator Lamp
TP Throttle Position
TPPC Throttle Plate Position Controller
TRS Transmission Range Sensor
TSS Turbine Shaft Speed
VID Vehicle IDentification
VIN Vehicle Identification No.
VQZ VQuizzer
VMV Vapour Management Valve