clutch ASTON MARTIN V8 VANTAGE 2010 Workshop Manual
[x] Cancel search | Manufacturer: ASTON MARTIN, Model Year: 2010, Model line: V8 VANTAGE, Model: ASTON MARTIN V8 VANTAGE 2010Pages: 947, PDF Size: 43.21 MB
Page 3 of 947
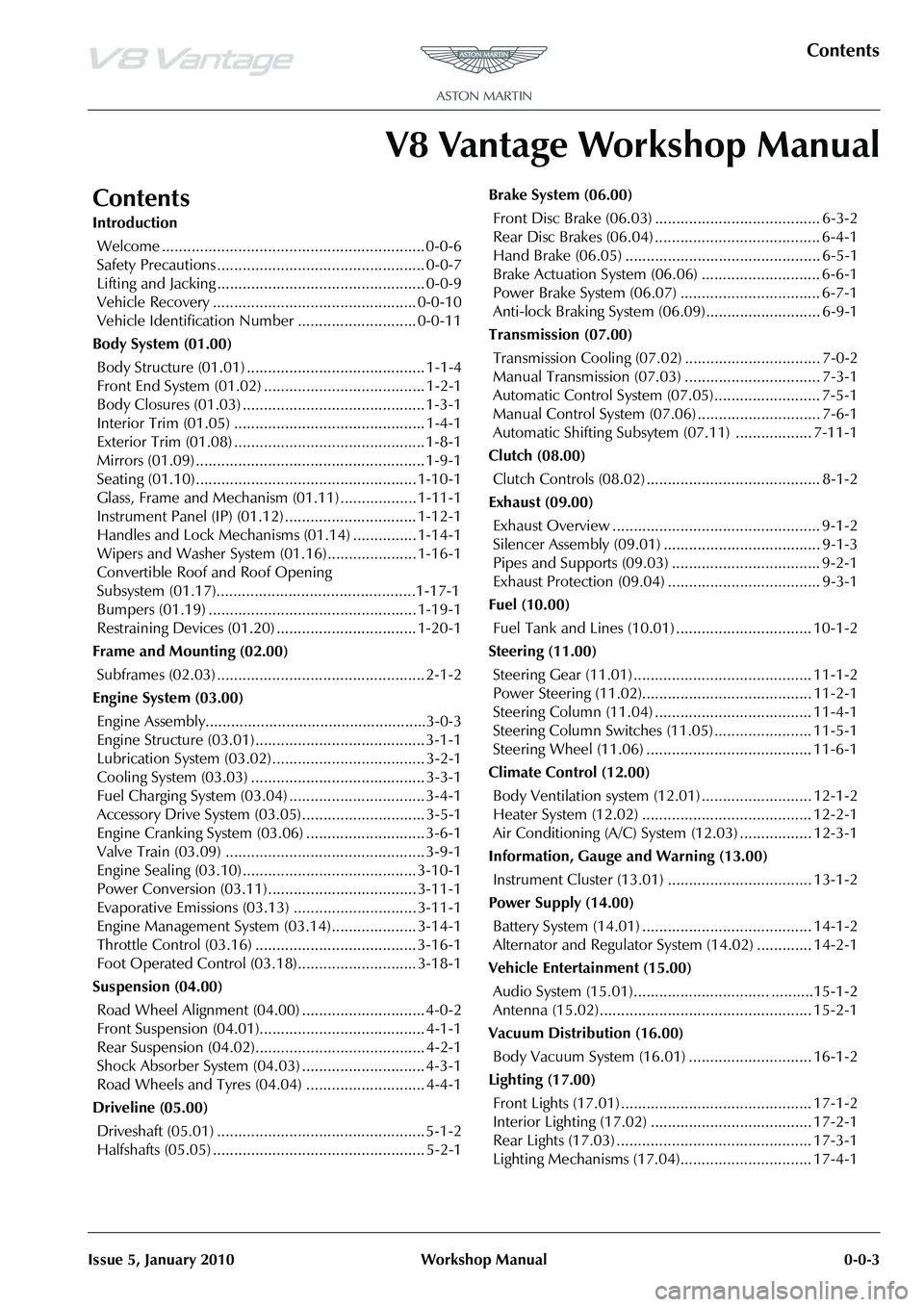
Contents
Issue 5, January 2010 Workshop Manual 0-0-3
V8 Vantage Workshop Manual
Contents
IntroductionWelcome .............................................................. 0-0-6
Safety Precautions ................................................. 0-0-7
Lifting and Jacking ................................................. 0-0-9
Vehicle Recovery ................................................ 0-0-10
Vehicle Identification Number ............................ 0-0-11
Body System (01.00) Body Structure (01.01) .......................................... 1-1-4
Front End System (01.02) ...................................... 1-2-1
Body Closures (01.03) ........................................... 1-3-1
Interior Trim (01.05) ............................................. 1-4-1
Exterior Trim (01.08) ............................................. 1-8-1
Mirrors (01.09) ...................................................... 1-9-1
Seating (01.10).................................................... 1-10-1
Glass, Frame and Mechanism (01.11) .................. 1-11-1
Instrument Panel (IP) (01.12) . .............................. 1-12-1
Handles and Lock Mechanisms (01.14) ............... 1-14-1
Wipers and Washer System (01.16)..................... 1-16-1
Convertible Roof and Roof Opening
Subsystem (01.17)................ ...............................1-17-1
Bumpers (01.19) ................................................. 1-19-1
Restraining Devices (01.20) .... ............................. 1-20-1
Frame and Mounting (02.00) Subframes (02.03) ................................................. 2-1-2
Engine System (03.00) Engine Assembly....................................................3-0-3
Engine Structure (03.01)........................................ 3-1-1
Lubrication System (03.02).................................... 3-2-1
Cooling System (03.03) ......................................... 3-3-1
Fuel Charging System (03.04) ................................ 3-4-1
Accessory Drive System (03.05)............................. 3-5-1
Engine Cranking System (03. 06) ............................ 3-6-1
Valve Train (03.09) ............................................... 3-9-1
Engine Sealing (03.10)......................................... 3-10-1
Power Conversion (03.11)................................... 3-11-1
Evaporative Emissions (03.13) ............................. 3-11-1
Engine Management System (0 3.14).................... 3-14-1
Throttle Control (03.16) ...... ................................ 3-16-1
Foot Operated Control (03.18)............................ 3-18-1
Suspension (04.00) Road Wheel Alignment (04.00) ............................. 4-0-2
Front Suspension (04.01)....................................... 4-1-1
Rear Suspension (04.02)........................................ 4-2-1
Shock Absorber System (04.03) ............................. 4-3-1
Road Wheels and Tyres (04.04) ............................ 4-4-1
Driveline (05.00) Driveshaft (05.01) ................................................. 5-1-2
Halfshafts (05.05) .................................................. 5-2-1 Brake System (06.00)
Front Disc Brake (06.03) ....................................... 6-3-2
Rear Disc Brakes (06.04) ....................................... 6-4-1
Hand Brake (06.05) .............................................. 6-5-1
Brake Actuation System (06.06 ) ............................ 6-6-1
Power Brake System (06.07) ................................. 6-7-1
Anti-lock Braking System (06.09)........................... 6-9-1
Transmission (07.00) Transmission Cooling (07.02) ................................ 7-0-2
Manual Transmission (07.03) ................................ 7-3-1
Automatic Control System (07.05)......................... 7-5-1
Manual Control System (07.06) ............................. 7-6-1
Automatic Shifting Subsytem (07.11) .................. 7-11-1
Clutch (08.00) Clutch Controls (08.02) ......................................... 8-1-2
Exhaust (09.00) Exhaust Overview ................................................. 9-1-2
Silencer Assembly (09.01) ..................................... 9-1-3
Pipes and Supports (09.03) ................................... 9-2-1
Exhaust Protection (09.04) .................................... 9-3-1
Fuel (10.00) Fuel Tank and Lines (10.01) ................................ 10-1-2
Steering (11.00) Steering Gear (11.01) .......................................... 11-1-2
Power Steering (11.02)........................................ 11-2-1
Steering Column (11.04) ..................................... 11-4-1
Steering Column Switches (1 1.05) ....................... 11-5-1
Steering Wheel (11.06) ....................................... 11-6-1
Climate Control (12.00) Body Ventilation system (12.01) .......................... 12-1-2
Heater System (12.02) ........................................ 12-2-1
Air Conditioning (A/C) System (12.03) ................. 12-3-1
Information, Gauge and Warning (13.00) Instrument Cluster (13.01) .................................. 13-1-2
Power Supply (14.00) Battery System (14.01) ........................................ 14-1-2
Alternator and Regulator System (14.02) ............. 14-2-1
Vehicle Entertainment (15.00) Audio System (15.01)................................ ..........15-1-2
Antenna (15.02).................................................. 15-2-1
Vacuum Distribution (16.00) Body Vacuum System (16.01) ............................. 16-1-2
Lighting (17.00) Front Lights (17.01) ............................................. 17-1-2
Interior Lighting (17.02) ...................................... 17-2-1
Rear Lights (17.03) .............................................. 17-3-1
Lighting Mechanisms (17.04). .............................. 17-4-1
Page 239 of 947
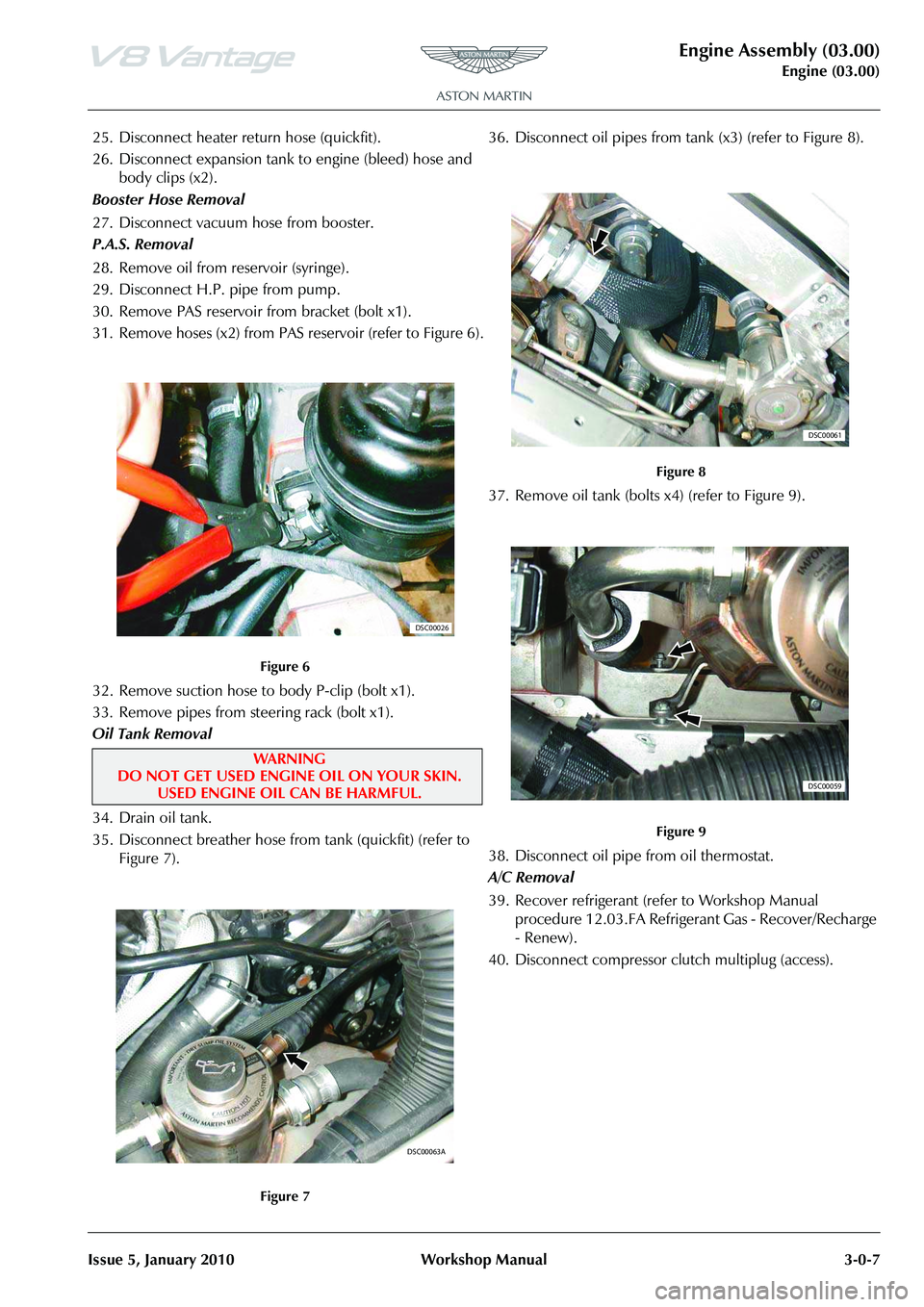
Engine Assembly (03.00)
Engine (03.00)
Issue 5, January 2010 Workshop Manual 3-0-7
25. Disconnect heater re turn hose (quickfit).
26. Disconnect expansion tank to engine (bleed) hose and body clips (x2).
Booster Hose Removal
27. Disconnect vacuum hose from booster.
P.A.S. Removal
28. Remove oil from reservoir (syringe).
29. Disconnect H.P. pipe from pump.
30. Remove PAS reservoir from bracket (bolt x1).
31. Remove hoses (x2) from PAS re servoir (refer to Figure 6).
32. Remove suction hose to body P-clip (bolt x1).
33. Remove pipes from steering rack (bolt x1).
Oil Tank Removal
34. Drain oil tank.
35. Disconnect breather hose from tank (quickfit) (refer to Figure 7). 36. Disconnect oil pipes from tank
(x3) (refer to Figure 8).
37. Remove oil tank (bolts x4) (refer to Figure 9).
38. Disconnect oil pipe from oil thermostat.
A/C Removal
39. Recover refrigerant (refer to Workshop Manual procedure 12.03.FA Refriger ant Gas - Recover/Recharge
- Renew).
40. Disconnect compressor clutch multiplug (access).
Figure 6
WA R N I N G
DO NOT GET USED ENGINE OIL ON YOUR SKIN. USED ENGINE OIL CAN BE HARMFUL.
Figure 7
$ 3 #
$ 3 # !
Figure 8
Figure 9
$ 3 #
$ 3 #
Page 242 of 947
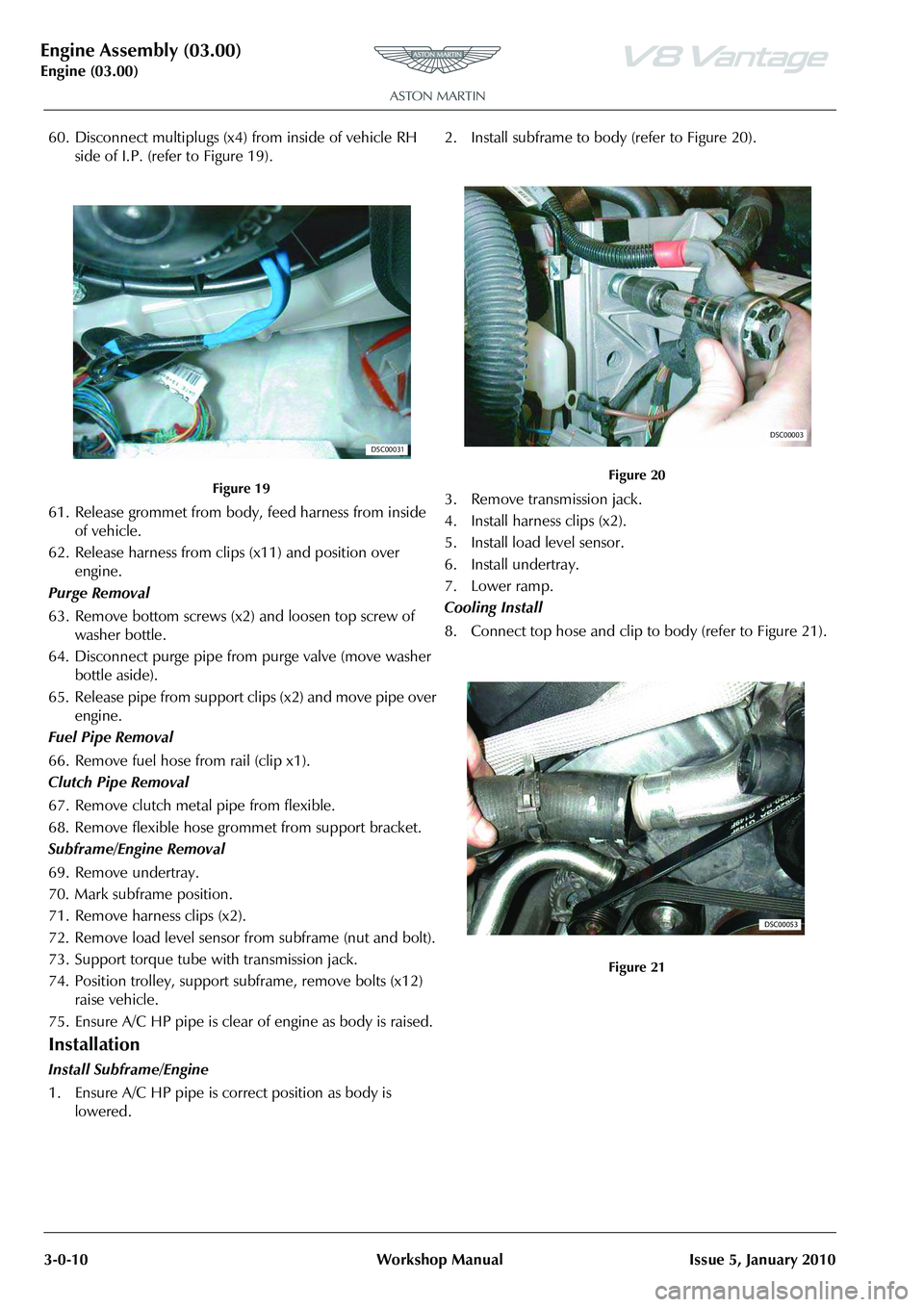
Engine Assembly (03.00)
Engine (03.00)3-0-10 Workshop Manual Issue 5, January 2010
60. Disconnect multiplugs (x4) from inside of vehicle RH side of I.P. (refer to Figure 19).
61. Release grommet from body, feed harness from inside of vehicle.
62. Release harness from clips (x11) and position over engine.
Purge Removal
63. Remove bottom screws (x2) and loosen top screw of washer bottle.
64. Disconnect purge pipe from purge valve (move washer
bottle aside).
65. Release pipe from support clips (x2) and move pipe over engine.
Fuel Pipe Removal
66. Remove fuel hose from rail (clip x1).
Clutch Pipe Removal
67. Remove clutch metal pipe from flexible.
68. Remove flexible hose grommet from support bracket.
Subframe/Engine Removal
69. Remove undertray.
70. Mark subframe position.
71. Remove harness clips (x2).
72. Remove load level sensor from subframe (nut and bolt).
73. Support torque tube with transmission jack.
74. Position trolley, support subframe, remove bolts (x12)
raise vehicle.
75. Ensure A/C HP pipe is clear of engine as body is raised.
Installation
Install Subframe/Engine
1. Ensure A/C HP pipe is co rrect position as body is
lowered. 2. Install subframe to body (refer to Figure 20).
3. Remove transmission jack.
4. Install harness clips (x2).
5. Install load level sensor.
6. Install undertray.
7. Lower ramp.
Cooling Install
8. Connect top hose and clip to body (refer to Figure 21).
Figure 19
$ 3 #
Figure 20
Figure 21
$ 3 #
$ 3 #
Page 244 of 947
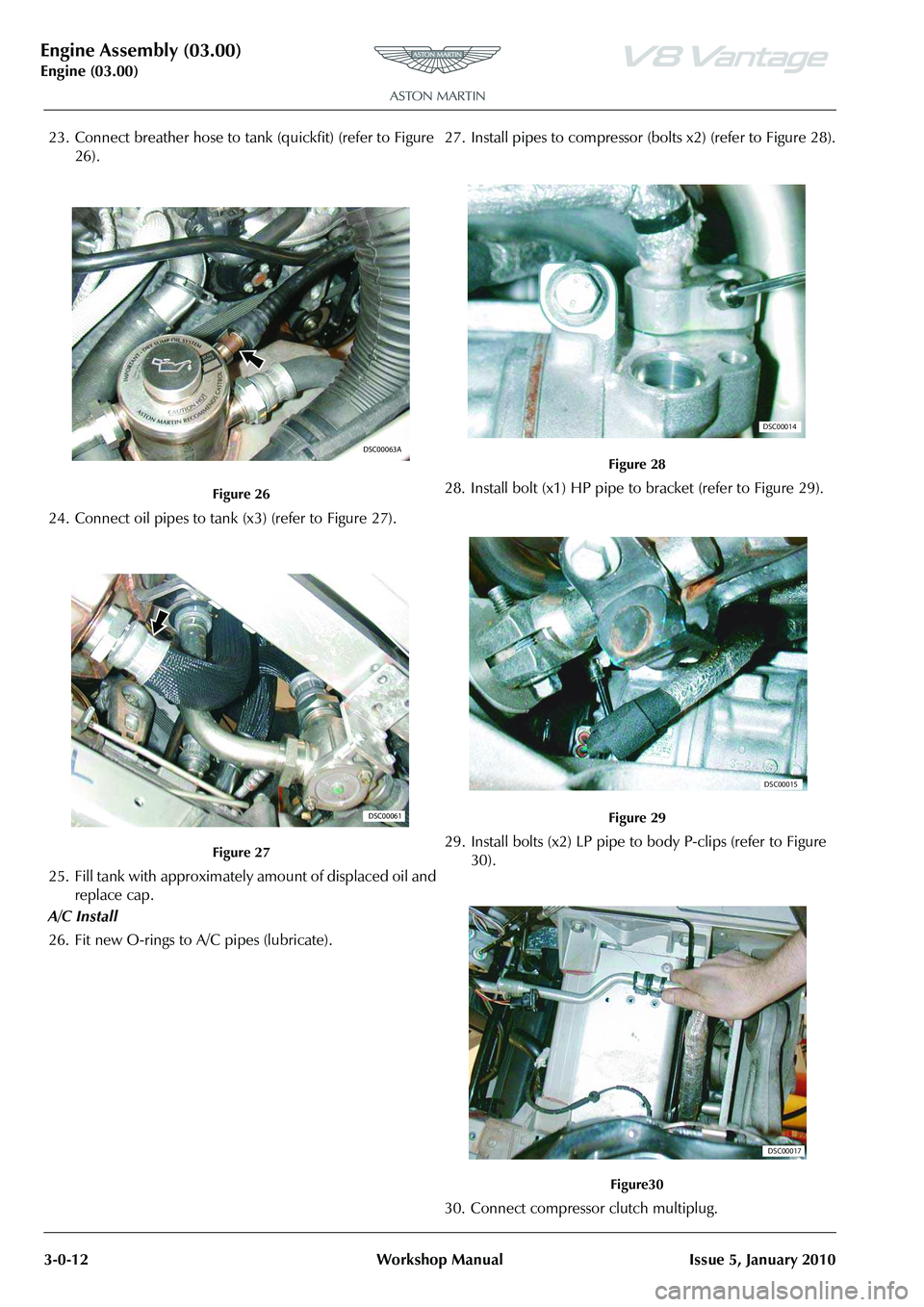
Engine Assembly (03.00)
Engine (03.00)3-0-12 Workshop Manual Issue 5, January 2010
23. Connect breather hose to tank (quickfit) (refer to Figure
26).
24. Connect oil pipes to tank (x3) (refer to Figure 27).
25. Fill tank with approximatel y amount of displaced oil and
replace cap.
A/C Install
26. Fit new O-rings to A/C pipes (lubricate). 27. Install pipes to compressor (b
olts x2) (refer to Figure 28).
28. Install bolt (x1) HP pipe to bracket (refer to Figure 29).
29. Install bolts (x2) LP pipe to body P-clips (refer to Figure 30).
30. Connect compressor clutch multiplug.
Figure 26
Figure 27
$ 3 # !
$ 3 #
Figure 28
Figure 29
Figure30
$ 3 #
$ 3 #
$ 3 #
Page 247 of 947
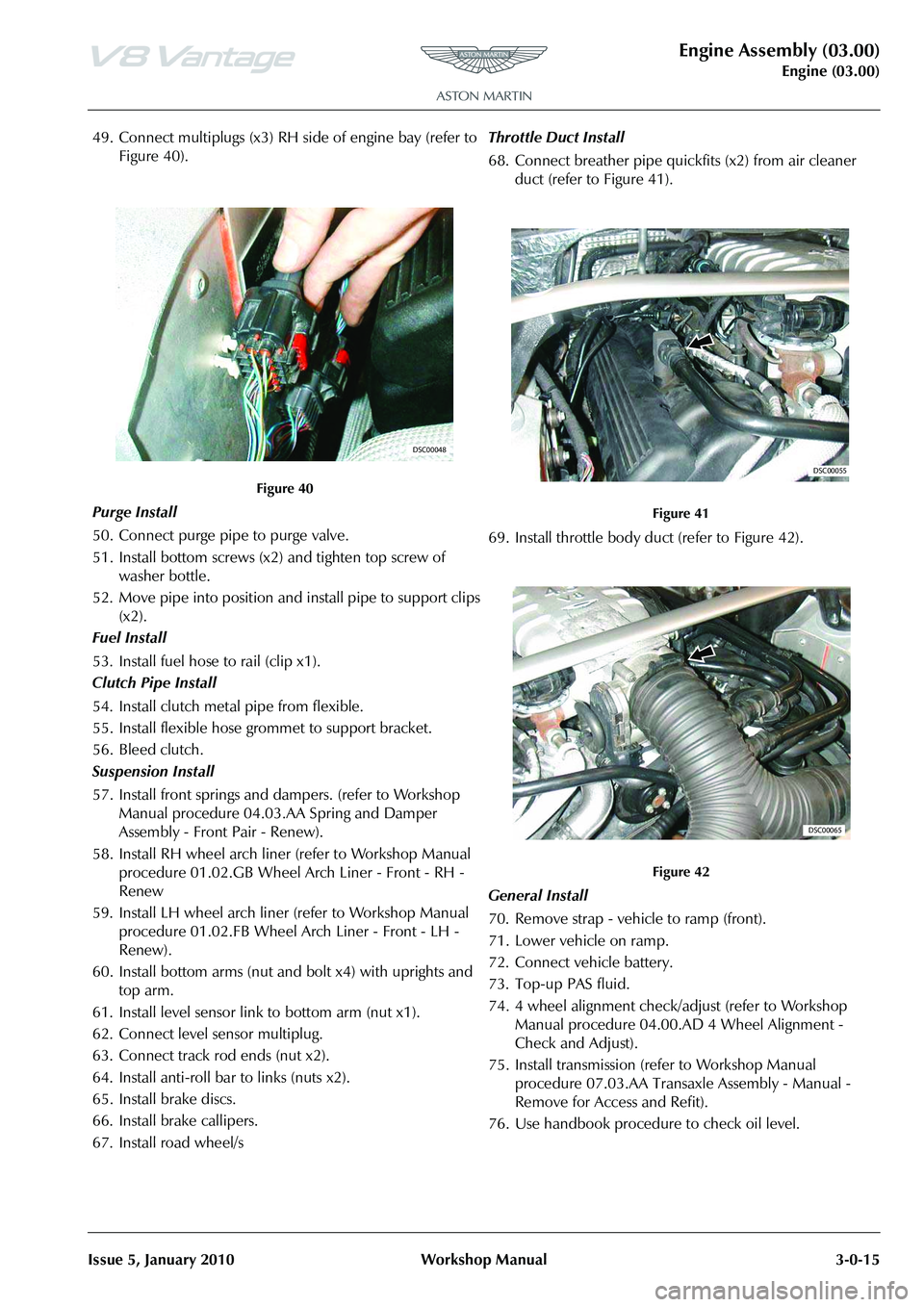
Engine Assembly (03.00)
Engine (03.00)
Issue 5, January 2010 Workshop Manual 3-0-15
49. Connect multiplugs (x3) RH side of engine bay (refer to Figure 40).
Purge Install
50. Connect purge pipe to purge valve.
51. Install bottom screws (x2) and tighten top screw of washer bottle.
52. Move pipe into position and install pipe to support clips (x2).
Fuel Install
53. Install fuel hose to rail (clip x1).
Clutch Pipe Install
54. Install clutch metal pipe from flexible.
55. Install flexible hose grommet to support bracket.
56. Bleed clutch.
Suspension Install
57. Install front springs and dampers. (refer to Workshop Manual procedure 04.03.AA Spring and Damper
Assembly - Front Pair - Renew).
58. Install RH wheel arch liner (refer to Workshop Manual procedure 01.02.GB Wheel Arch Liner - Front - RH -
Renew
59. Install LH wheel arch liner (refer to Workshop Manual procedure 01.02.FB Wheel Arch Liner - Front - LH -
Renew).
60. Install bottom arms (nut and bolt x4) with uprights and top arm.
61. Install level sens or link to bottom arm (nut x1).
62. Connect level sensor multiplug.
63. Connect track rod ends (nut x2).
64. Install anti-roll bar to links (nuts x2).
65. Install brake discs.
66. Install brake callipers.
67. Install road wheel/s Throttle Duct Install
68. Connect breather pipe quic
kfits (x2) from air cleaner
duct (refer to Figure 41).
69. Install throttle body duct (refer to Figure 42).
General Install
70. Remove strap - vehicle to ramp (front).
71. Lower vehicle on ramp.
72. Connect vehicle battery.
73. Top-up PAS fluid.
74. 4 wheel alignment check/adjust (refer to Workshop Manual procedure 04.00.AD 4 Wheel Alignment -
Check and Adjust).
75. Install transmission (refer to Workshop Manual procedure 07.03.AA Transaxle Assembly - Manual -
Remove for Access and Refit).
76. Use handbook procedure to check oil level.
Figure 40
$ 3 #
Figure 41
Figure 42
$ 3 #
$ 3 #
Page 281 of 947
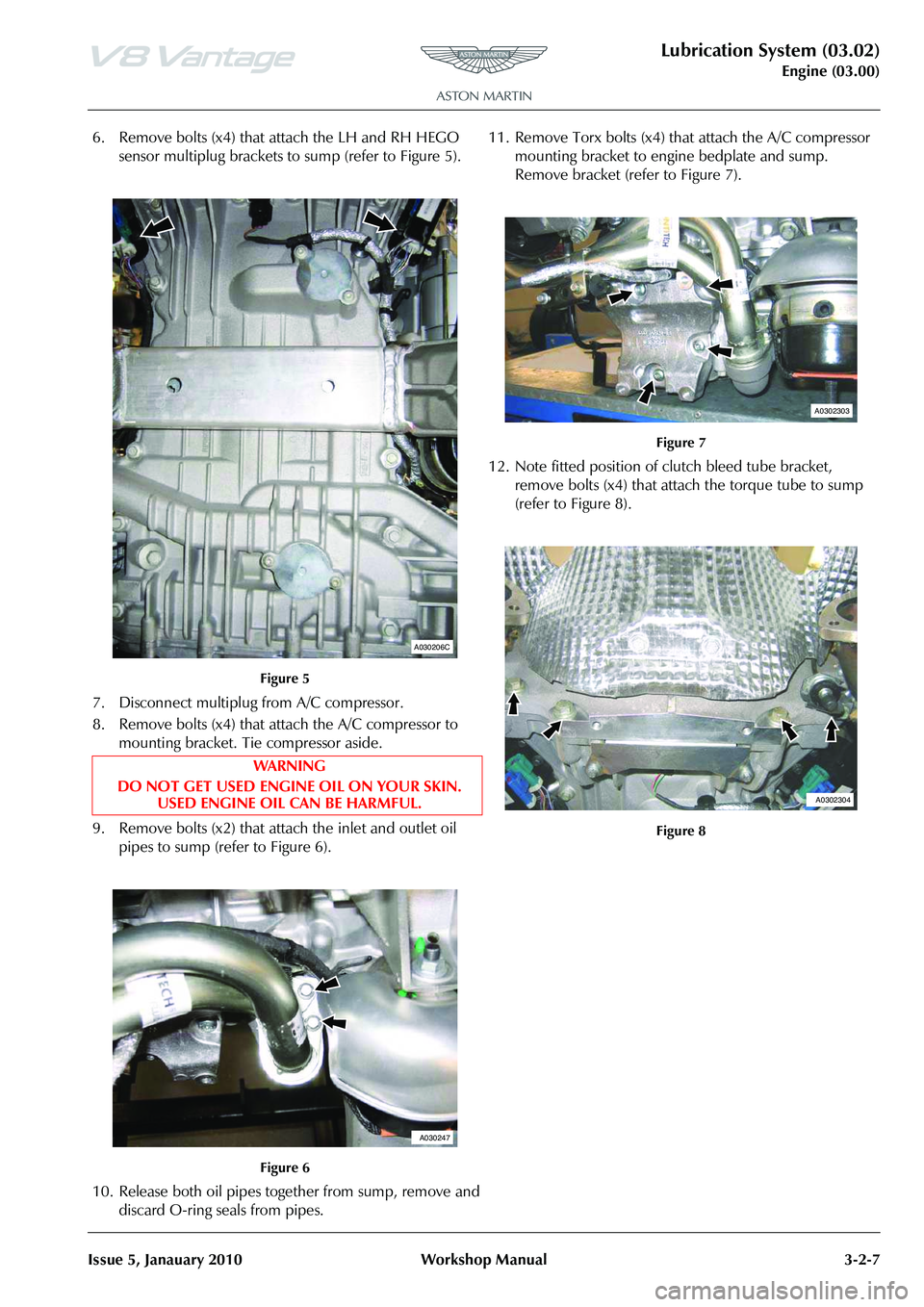
Lubrication System (03.02)
Engine (03.00)
Issue 5, Janauary 2010 Workshop Manual 3-2-7
6. Remove bolts (x4) that attach the LH and RH HEGO sensor multiplug brackets to sump (refer to Figure 5).
7. Disconnect multiplug from A/C compressor.
8. Remove bolts (x4) that attach the A/C compressor to mounting bracket. Tie compressor aside.
9. Remove bolts (x2) that attach the inlet and outlet oil pipes to sump (refer to Figure 6).
10. Release both oil pipes toge ther from sump, remove and
discard O-ring seals from pipes. 11. Remove Torx bolts (x4) that attach the A/C compressor
mounting bracket to engine bedplate and sump.
Remove bracket (refer to Figure 7).
12. Note fitted position of clutch bleed tube bracket, remove bolts (x4) that attach the torque tube to sump
(refer to Figure 8).
Figure 5
WA R N I N G
DO NOT GET USED ENGINE OIL ON YOUR SKIN. USED ENGINE OIL CAN BE HARMFUL.
Figure 6
A030206C
A030247
Figure 7
Figure 8
A0302303
A0302304
Page 373 of 947
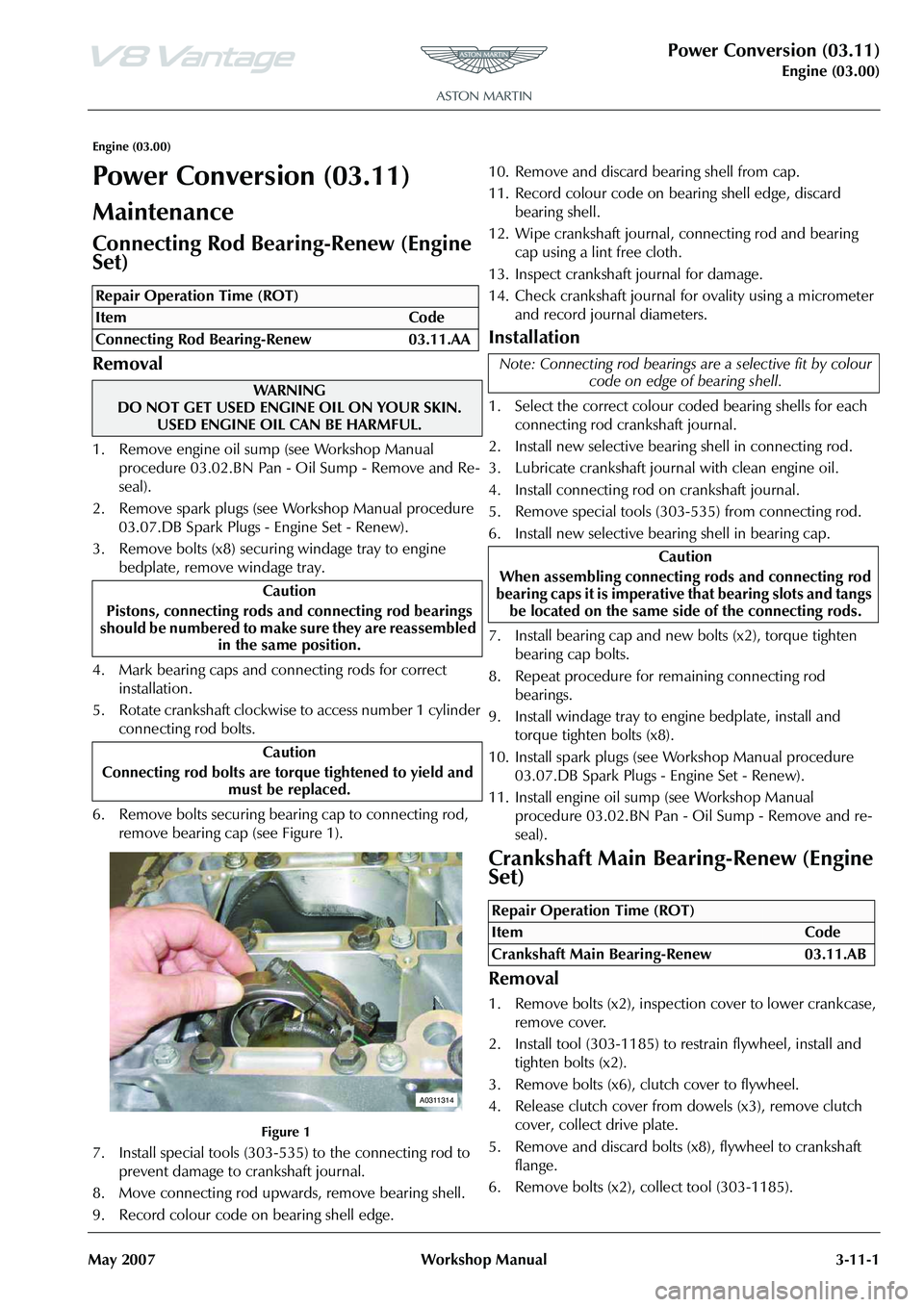
Power Conversion (03.11)
Engine (03.00)
May 2007 Workshop Manual 3-11-1
Engine (03.00)
Power Conversion (03.11)
Maintenance
Connecting Rod Bearing-Renew (Engine
Set)
Removal
1. Remove engine oil sump (see Workshop Manual
procedure 03.02.BN Pan - Oil Sump - Remove and Re-
seal).
2. Remove spark plugs (see Workshop Manual procedure 03.07.DB Spark Plugs - Engine Set - Renew).
3. Remove bolts (x8) securing windage tray to engine bedplate, remove windage tray.
4. Mark bearing caps and connecting rods for correct installation.
5. Rotate crankshaft clockwise to access number 1 cylinder connecting rod bolts.
6. Remove bolts securing bearing cap to connecting rod, remove bearing cap (see Figure 1).
Figure 1
7. Install special tools (303-535) to the connecting rod to prevent damage to crankshaft journal.
8. Move connecting rod upwards, remove bearing shell.
9. Record colour code on bearing shell edge. 10. Remove and discard bearing shell from cap.
11. Record colour code on bearing shell edge, discard
bearing shell.
12. Wipe crankshaft journal, connecting rod and bearing cap using a lint free cloth.
13. Inspect crankshaft journal for damage.
14. Check crankshaft journal for ovality using a micrometer and record journal diameters.
Installation
1. Select the correct colour coded bearing shells for each connecting rod crankshaft journal.
2. Install new selective bearing shell in connecting rod.
3. Lubricate crankshaft journal with clean engine oil.
4. Install connecting rod on crankshaft journal.
5. Remove special tools (303-535) from connecting rod.
6. Install new selective bearing shell in bearing cap.
7. Install bearing cap and new bolts (x2), torque tighten bearing cap bolts.
8. Repeat procedure for remaining connecting rod bearings.
9. Install windage tray to engine bedplate, install and torque tighten bolts (x8).
10. Install spark plugs (see Workshop Manual procedure 03.07.DB Spark Plugs - Engine Set - Renew).
11. Install engine oil sump (see Workshop Manual
procedure 03.02.BN Pan - Oil Sump - Remove and re-
seal).
Crankshaft Main Bearing-Renew (Engine
Set)
Removal
1. Remove bolts (x2), inspection cover to lower crankcase, remove cover.
2. Install tool (303-1185) to restrain flywheel, install and tighten bolts (x2).
3. Remove bolts (x6), clutch cover to flywheel.
4. Release clutch cover from dowels (x3), remove clutch cover, collect drive plate.
5. Remove and discard bolts (x8), flywheel to crankshaft flange.
6. Remove bolts (x2), collect tool (303-1185).
Repair Operation Time (ROT)
WA R N I N G
DO NOT GET USED ENGINE OIL ON YOUR SKIN. USED ENGINE OIL CAN BE HARMFUL.
Caution
Pistons, connecting rods an d connecting rod bearings
should be numbered to make sure they are reassembled
in the same position.
Caution
Connecting rod bolts are tor qu
e tightened to yield and
mu st be replaced.
A0311314
Note: Connecting rod bearings ar e a selective fit by colour
code on edge of bearing shell.
Caution
When assembling connecting rods and connecting rod
bearing caps it is imperative that bearing slots and tangs
be located on the same side of the connecting rods.
Repair Operation Time (ROT)
Page 376 of 947

Power Conversion (03.11)
Engine (03.00)3-11-4 Workshop Manual May 2007
10. Install crankshaft retaining caps (303-534), install and
lightly tighten bolts (x10) (see Figure 8).
Figure 8
11. Install connecting rod bearing caps (x8), install and torque tighten retaining bolts.
12. Remove bolts securing crankshaft retaining caps (303- 534), remove retaining caps (see Figure 9).
Figure 9
13. Apply a 2mm diameter continuous bead of sealant to cylinder block flange ensuring that there are no gaps in
the sealant.
14. Install engine bedplate to cylinder block, install and torque tighten bolts (x34) in the correct sequence.
15. Remove excess sealant from crankshaft rear oil seal
aperture and front face of cylinder block.
16. Clean windage tray.
17. Install windage tray, install and torque tighten bolts (x8). 18. Ensure that oil seal protector is positioned correctly and
install oil seal onto crankshaft flange.
19. Install tool (303-1189) to crankshaft, position nuts on tool against oil seal.
20. Ensure that oil seal and special are parallel to rear of engine.
21. To install oil seal, tighten nuts alternately on tool (303- 1189) until oil seal correctly seated.
22. Remove special tool from crankshaft.
23. Check that the oil se al is located correctly.
24. Clean flywheel and mating face on crankshaft.
25. Install flywheel, align to dowel on crankshaft flange.
26. Install new bolts (x8), install tool (303-1185) to restrain flywheel. Torque tighten bolts (x8) in the correct
sequence.
27. Clean clutch cover and drive plate.
28. Install clutch assembly on flywheel, align to dowels (x3).
29. Install bolts (x6), install clutch alignment tool, evenly torque tighten bolts (x6) in a diagonal sequence.
Remove clutch alignment tool.
30. Remove bolts (x2), collect tool (303-1185).
31. Install inspection cover, install and torque tighten bolts (x2).
32. Install engine sump (see Workshop Manual procedure 03.02.CN Pan - Oil Sump - Remove and Reseal With
Engine Removed).
Crankshaft Assembly-Renew
Removal
1. Remove bolts (x2), inspection cover to lower crankcase, remove cover.
2. Install tool (303-1185) to restrain flywheel, install and tighten bolts (x2).
3. Remove bolts (x6), clutch cover to flywheel.
4. Release clutch cover from dowels (x3), remove clutch cover, collect drive plate.
5. Remove and discard bolts (x8), flywheel to crankshaft flange.
6. Remove bolts (x2), collect tool (303-1185).
7. Release flywheel from dowel, remove flywheel.
8 . R e m o v e e n g i n e s u mp ( s e e Wo r k s h o p M a n u a l p ro c e d u re 03.02.CN Pan - Oil Sump - Remove and Reseal With
Engine Removed).
Caution
Do not lubricate engine bedplate retaining bolts.
Caution
Tighten engine bedplate retaining bolts in the sequence shown.
Caution
Do not rotate crankshaft until all engine bedplate
retaining bolts are tightened to specification.
Caution
Engine bedplate retaining bolts must be tightened
within twenty minutes of applying sealant.
A0311328
A0311328
Caution
Do not use any lubricant on cr ankshaft oil seals or seal
protectors. Make sure all co mponents are clean and dry.
Repair Operation Time (ROT)
ItemCode
Crankshaft Assembly-Renew 03.11.CF
WAR NI NG
DO NOT GET USED ENGINE OIL ON YOUR SKIN.
USED ENGINE OIL CAN BE HARMFUL.
Page 379 of 947
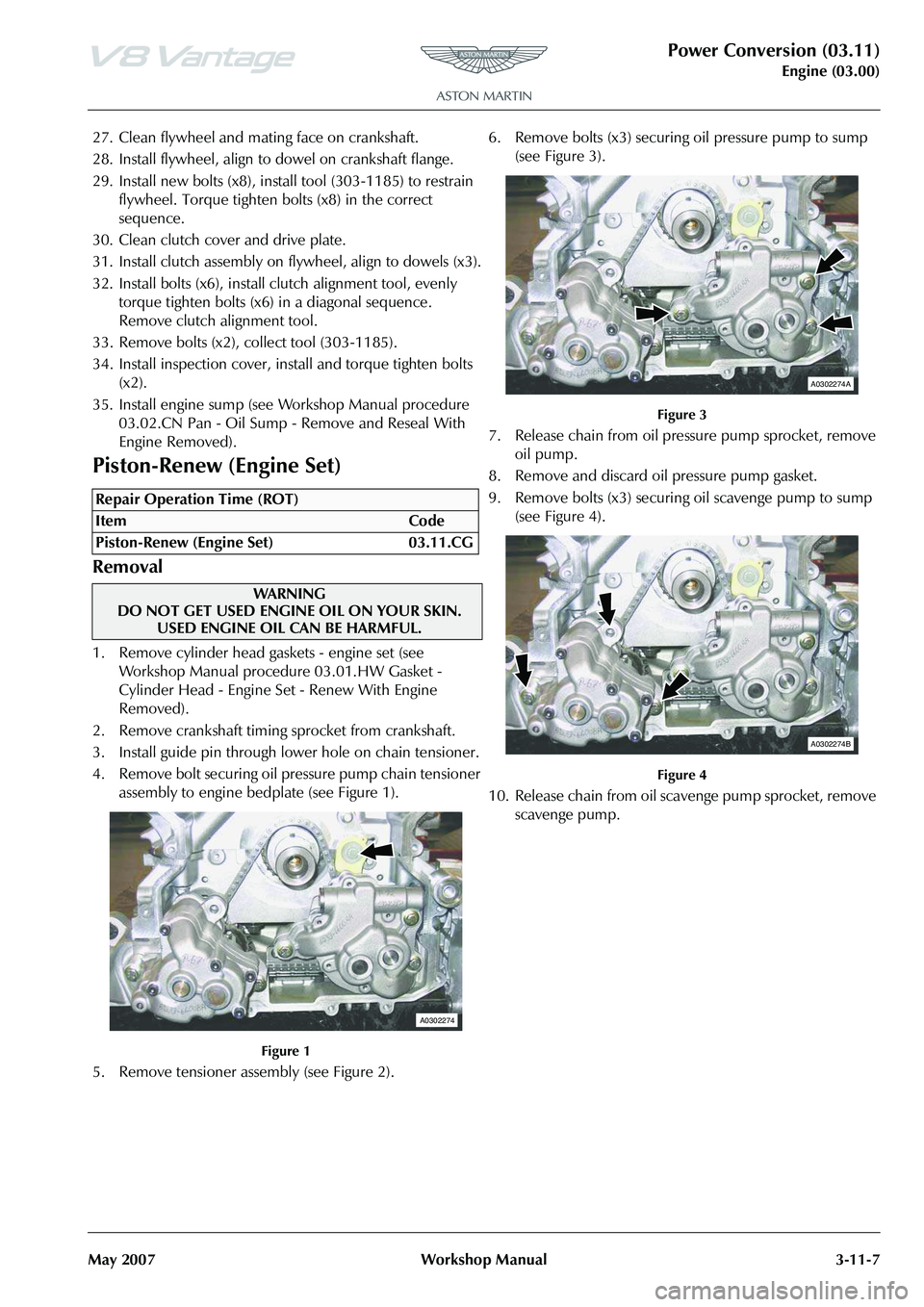
Power Conversion (03.11)
Engine (03.00)
May 2007 Workshop Manual 3-11-7
27. Clean flywheel and mating face on crankshaft.
28. Install flywheel, align to dowel on crankshaft flange.
29. Install new bolts (x8), install tool (303-1185) to restrain
flywheel. Torque tighten bolts (x8) in the correct
sequence.
30. Clean clutch cover and drive plate.
31. Install clutch assembly on fl ywheel, align to dowels (x3).
32. Install bolts (x6), install clutch alignment tool, evenly torque tighten bolts (x6) in a diagonal sequence.
Remove clutch alignment tool.
33. Remove bolts (x2), collect tool (303-1185).
34. Install inspection cover, install and torque tighten bolts (x2).
35. Install engine sump (see Workshop Manual procedure 03.02.CN Pan - Oil Sump - Remove and Reseal With
Engine Removed).
Piston-Renew (Engine Set)
Removal
1. Remove cylinder head gaskets - engine set (see Workshop Manual procedure 03.01.HW Gasket -
Cylinder Head - Engine Set - Renew With Engine
Removed).
2. Remove crankshaft timing sprocket from crankshaft.
3. Install guide pin through lower hole on chain tensioner.
4. Remove bolt securing oil pr essure pump chain tensioner
assembly to engine bedplate (see Figure 1).
Figure 1
5. Remove tensioner assembly (see Figure 2). 6. Remove bolts (x3) securing oil pressure pump to sump
(see Figure 3).
Figure 3
7. Release chain from oil pressure pump sprocket, remove oil pump.
8. Remove and discard oil pressure pump gasket.
9. Remove bolts (x3) securing oil scavenge pump to sump
(see Figure 4).
Figure 4
10. Release chain from oil scavenge pump sprocket, remove scavenge pump.
Repair Operation Time (ROT)
WA R N I N G
DO NOT GET USED ENGINE OIL ON YOUR SKIN.
USED ENGINE OIL CAN BE HARMFUL.
A0302274
A0302274A
A0302274B
Page 407 of 947
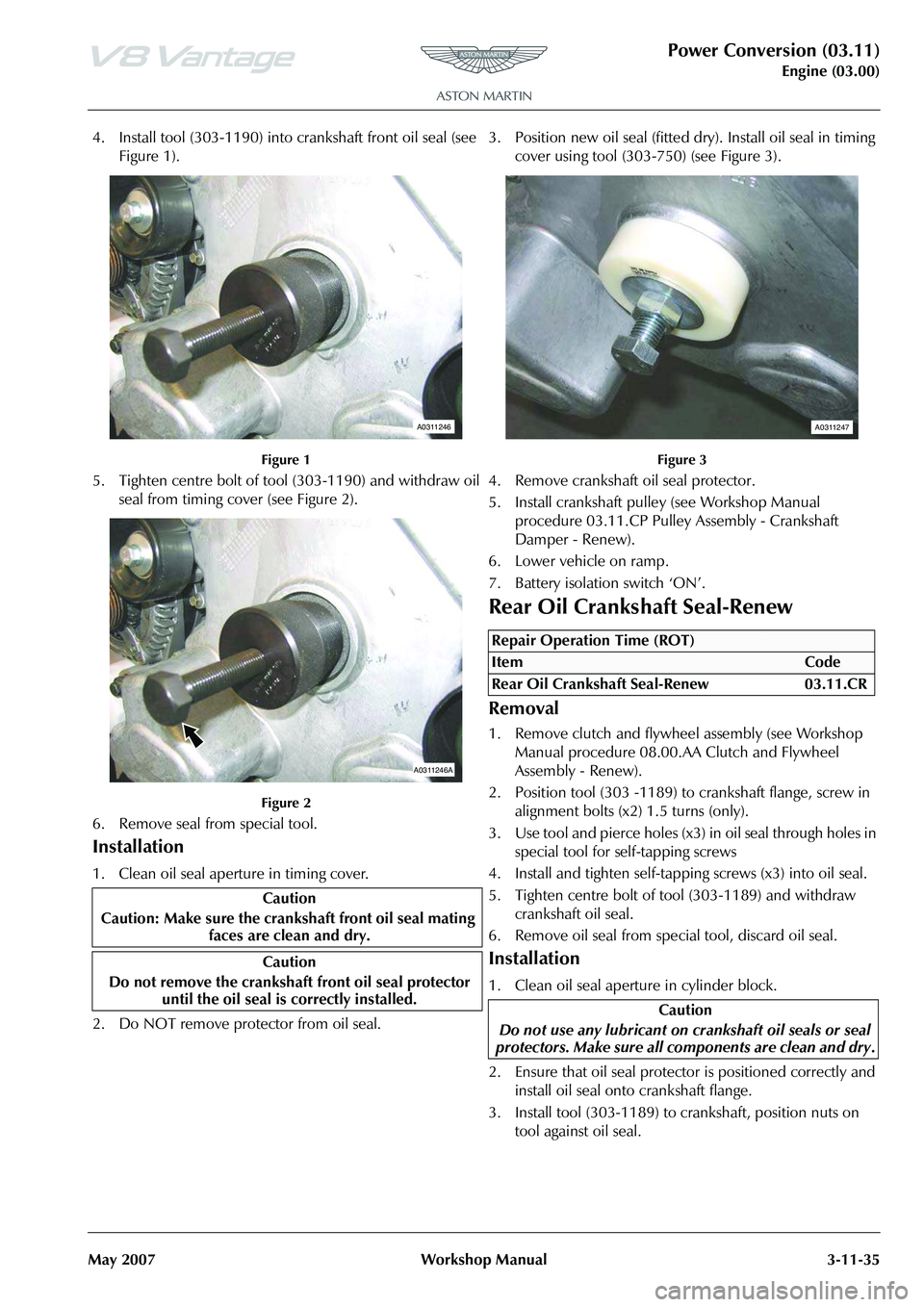
Power Conversion (03.11)
Engine (03.00)
May 2007 Workshop Manual 3-11-35
4. Install tool (303-1190) into crankshaft front oil seal (see
Figure 1).
Figure 1
5. Tighten centre bolt of tool (303-1190) and withdraw oil seal from timing cover (see Figure 2).
Figure 2
6. Remove seal from special tool.
Installation
1. Clean oil seal aperture in timing cover.
2. Do NOT remove protector from oil seal. 3. Position new oil seal (fitted dry). Install oil seal in timing
cover using tool (303-750) (see Figure 3).
Figure 3
4. Remove crankshaft oil seal protector.
5. Install crankshaft pulley (see Workshop Manual procedure 03.11.CP Pulley Assembly - Crankshaft
Damper - Renew).
6. Lower vehicle on ramp.
7. Battery isolation switch ‘ON’.
Rear Oil Crankshaft Seal-Renew
Removal
1. Remove clutch and flywheel assembly (see Workshop Manual procedure 08.00.AA Clutch and Flywheel
Assembly - Renew).
2. Position tool (303 -1189) to crankshaft flange, screw in alignment bolts (x2) 1.5 turns (only).
3. Use tool and pierce holes (x3) in oil seal through holes in special tool for self-tapping screws
4. Install and tighten self-tapping screws (x3) into oil seal.
5. Tighten centre bolt of tool (303-1189) and withdraw crankshaft oil seal.
6. Remove oil seal from spec ial tool, discard oil seal.
Installation
1. Clean oil seal aperture in cylinder block.
2. Ensure that oil seal protecto r is positioned correctly and
install oil seal onto crankshaft flange.
3. Install tool (303-1189) to crankshaft, position nuts on
tool against oil seal.
Caution
Caution: Make sure the cranks haft front oil seal mating
faces are clean and dry.
Caution
Do not remove the crankshaft front oil seal protector
until the oil seal is correctly installed.
A0311246
A0311246A
Repair Operation Time (ROT)
A0311247