clutch ASTON MARTIN V8 VANTAGE 2010 Service Manual
[x] Cancel search | Manufacturer: ASTON MARTIN, Model Year: 2010, Model line: V8 VANTAGE, Model: ASTON MARTIN V8 VANTAGE 2010Pages: 947, PDF Size: 43.21 MB
Page 650 of 947
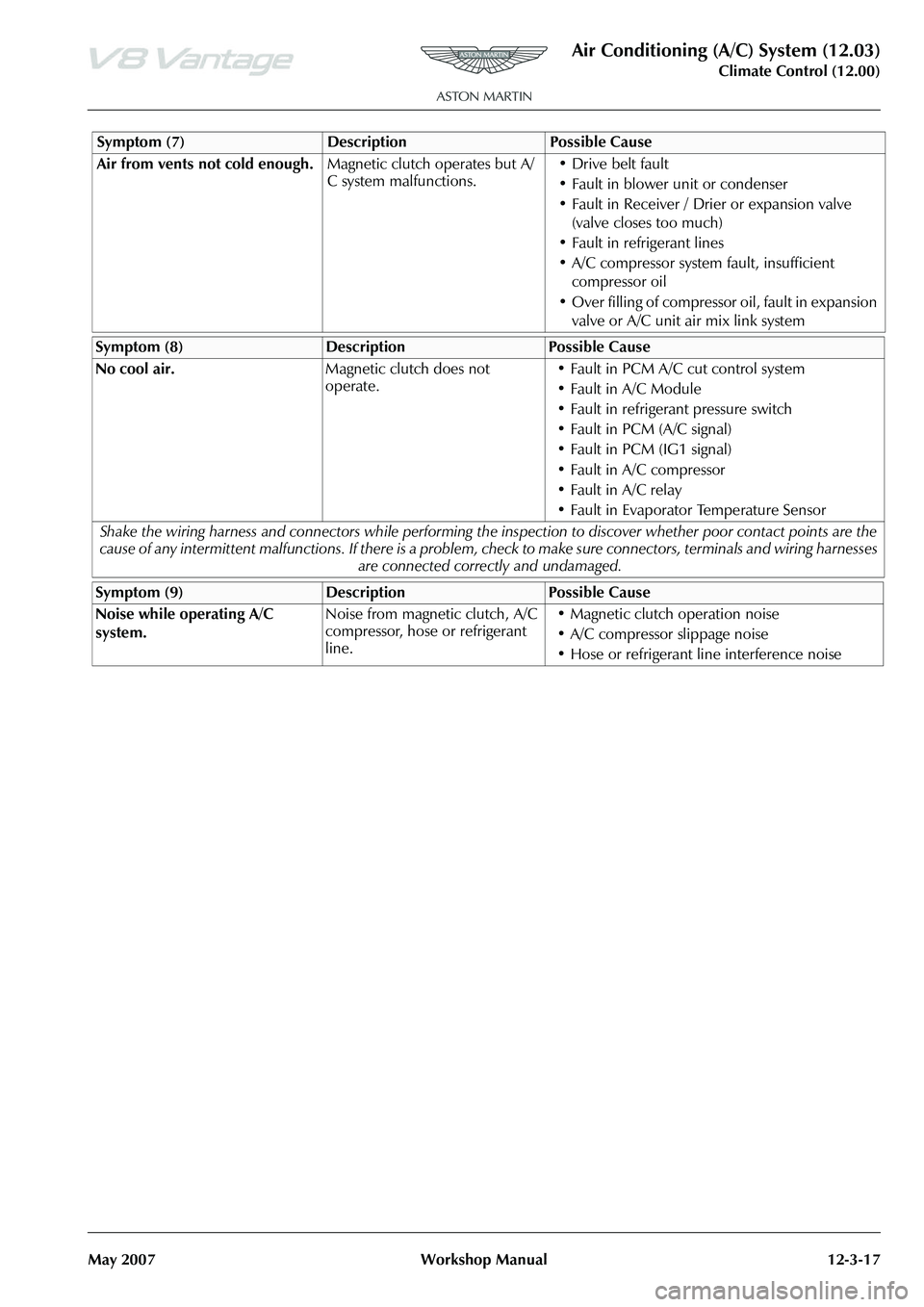
Air Conditioning (A/C) System (12.03)
Climate Control (12.00)
May 2007 Workshop Manual 12-3-17
Symptom (7)DescriptionPossible Cause
Air from vents not cold enough. Magnetic clutch operates but A/
C system malfunctions. • Drive belt fault
• Fault in blower unit or condenser
• Fault in Receiver / Drier or expansion valve
(valve closes too much)
• Fault in refrigerant lines
• A/C compressor system fault, insufficient compressor oil
• Over filling of compressor oil, fault in expansion valve or A/C unit air mix link system
Symptom (8)Possible Cause
No cool air. Magnetic clutch does not
operate. • Fault in PCM A/C cut control system
• Fault in A/C Module
• Fault in refrigerant pressure switch
• Fault in PCM (A/C signal)
• Fault in PCM (IG1 signal)
• Fault in A/C compressor
•Fault in A/C relay
• Fault in Evaporator Temperature Sensor
Shake the wiring harness and connectors wh ile performing the inspection to discover whether poor contact points are the
cause of any intermittent malfunctions. If there is a problem, check to make sure connectors, terminals and wiring harnesses
are connected correctly and undamaged.
Symptom (9)Possible Cause
Noise while operating A/C
system. Noise from magnetic clutch, A/C
compressor, hose or refrigerant
line. • Magnetic clutch operation noise
• A/C compressor slippage noise
• Hose or refrigerant line interference noise
Page 716 of 947
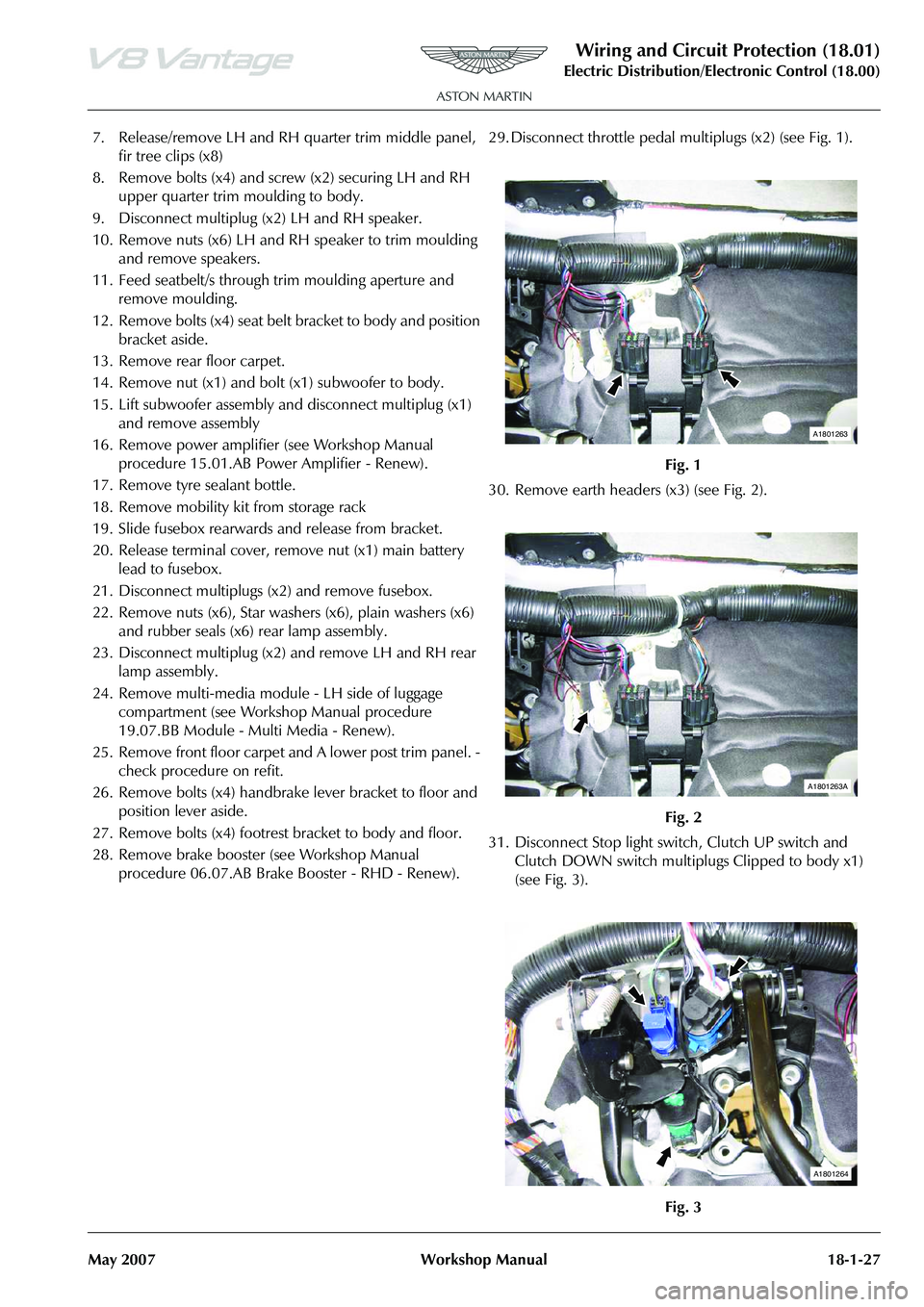
Wiring and Circuit Protection (18.01)
Electric Distribution/Electronic Control (18.00)
May 2007 Workshop Manual 18-1-27
7. Release/remove LH and RH quarter trim middle panel,
fir tree clips (x8)
8. Remove bolts (x4) and screw (x2) securing LH and RH upper quarter trim moulding to body.
9. Disconnect multiplug (x2) LH and RH speaker.
10. Remove nuts (x6) LH and RH speaker to trim moulding and remove speakers.
11. Feed seatbelt/s through trim moulding aperture and remove moulding.
12. Remove bolts (x4) seat belt bracket to body and position bracket aside.
13. Remove rear floor carpet.
14. Remove nut (x1) and bolt (x1) subwoofer to body.
15. Lift subwoofer assembly and disconnect multiplug (x1) and remove assembly
16. Remove power amplifier (see Workshop Manual procedure 15.01.AB Power Amplifier - Renew).
17. Remove tyre sealant bottle.
18. Remove mobility kit from storage rack
19. Slide fusebox rearwards and release from bracket.
20. Release terminal cover, remove nut (x1) main battery lead to fusebox.
21. Disconnect multiplugs (x2) and remove fusebox.
22. Remove nuts (x6), Star wash ers (x6), plain washers (x6)
and rubber seals (x6) rear lamp assembly.
23. Disconnect multiplug (x2) and remove LH and RH rear
lamp assembly.
24. Remove multi-media module - LH side of luggage compartment (see Workshop Manual procedure
19.07.BB Module - Multi Media - Renew).
25. Remove front floor carpet and A lower post trim panel. - check procedure on refit.
26. Remove bolts (x4) handbrake lever bracket to floor and position lever aside.
27. Remove bolts (x4) footrest bracket to body and floor.
28. Remove brake booster (see Workshop Manual procedure 06.07.AB Brake Booster - RHD - Renew). 29.Disconnect throttle pedal multiplugs (x2) (see Fig. 1).
30. Remove earth headers (x3) (see Fig. 2).
31. Disconnect Stop light switch, Clutch UP switch and
Clutch DOWN switch multip lugs Clipped to body x1)
(see Fig. 3). Fig. 1
Fig. 2
Fig. 3
$
$ $
$
Page 723 of 947
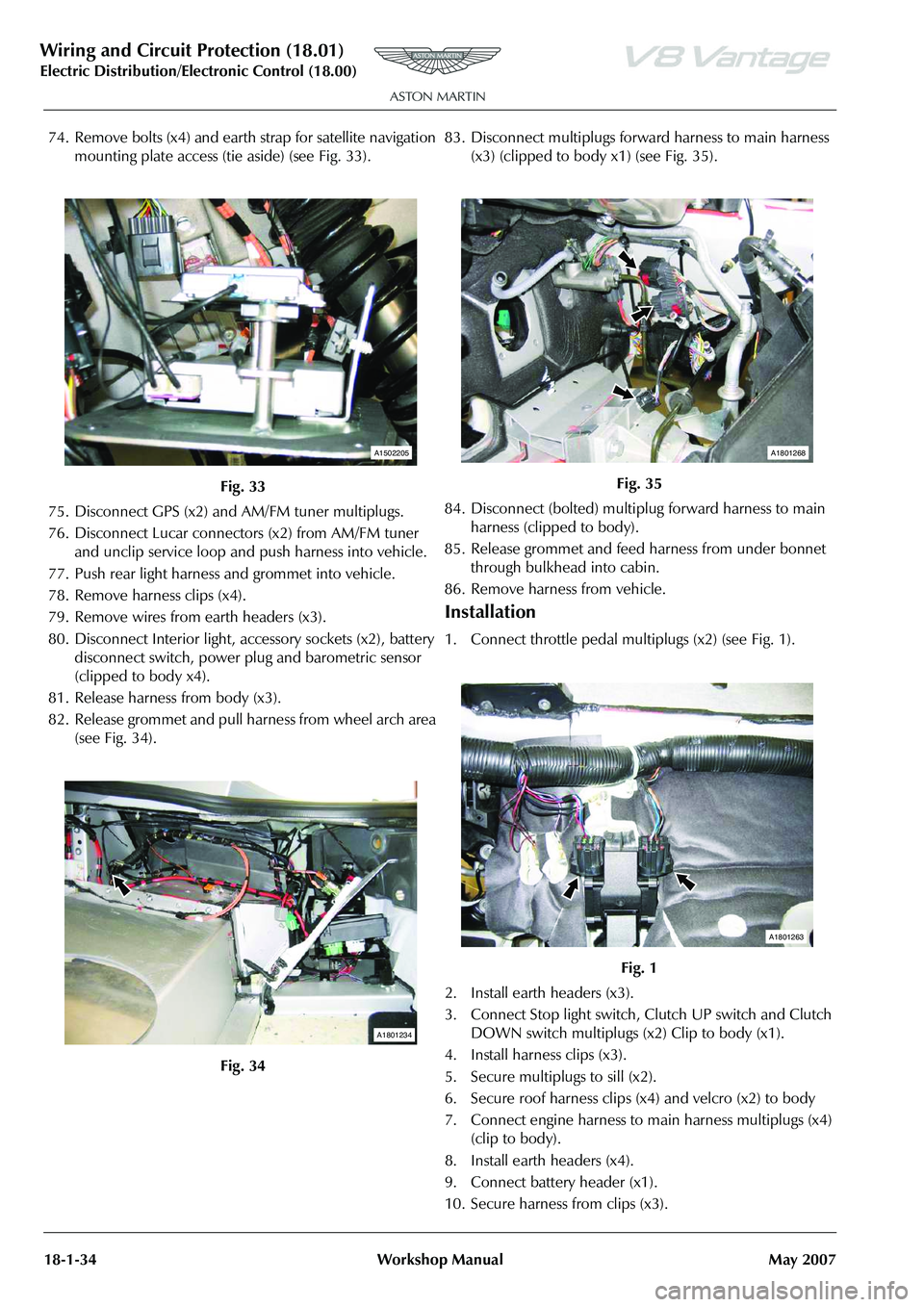
Wiring and Circuit Protection (18.01)
Electric Distribution/E lectronic Control (18.00)
18-1-34 Workshop Manual May 2007
74. Remove bolts (x4) and earth strap for satellite navigation
mounting plate access (tie aside) (see Fig. 33).
75. Disconnect GPS (x2) and AM/FM tuner multiplugs.
76. Disconnect Lucar connectors (x2) from AM/FM tuner and unclip service loop and push harness into vehicle.
77. Push rear light harness and grommet into vehicle.
78. Remove harness clips (x4).
79. Remove wires from earth headers (x3).
80. Disconnect Interior light, accessory sockets (x2), battery disconnect switch, power pl ug and barometric sensor
(clipped to body x4).
81. Release harness from body (x3).
82. Release grommet and pull harness from wheel arch area (see Fig. 34). 83. Disconnect multiplugs forward harness to main harness
(x3) (clipped to body x1) (see Fig. 35).
84. Disconnect (bolted) multiplug forward harness to main harness (clipped to body).
85. Release grommet and feed harness from under bonnet through bulkhead into cabin.
86. Remove harness from vehicle.
Installation
1. Connect throttle pedal mult iplugs (x2) (see Fig. 1).
2. Install earth headers (x3).
3. Connect Stop light switch, Clutch UP switch and Clutch DOWN switch multiplugs (x2) Clip to body (x1).
4. Install harness clips (x3).
5. Secure multiplugs to sill (x2).
6. Secure roof harness clips (x4) and velcro (x2) to body
7. Connect engine harness to main harness multiplugs (x4) (clip to body).
8. Install earth headers (x4).
9. Connect battery header (x1).
10. Secure harness from clips (x3).
Fig. 33
Fig. 34
$
$
Fig. 35
Fig. 1
$
$
Page 727 of 947
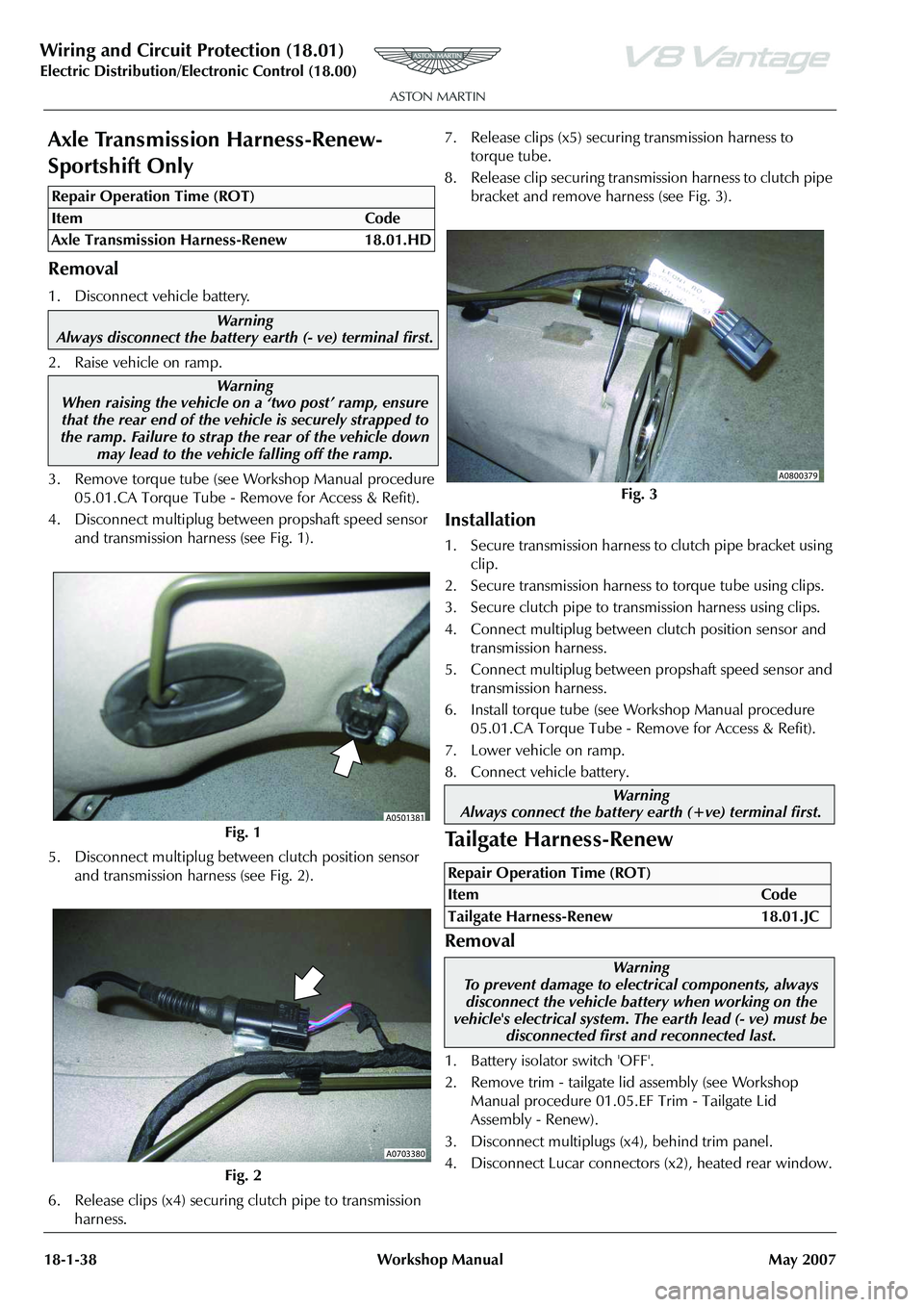
Wiring and Circuit Protection (18.01)
Electric Distribution/E lectronic Control (18.00)
18-1-38 Workshop Manual May 2007
Axle Transmission Harness-Renew-
Sportshift Only
Removal
1. Disconnect vehicle battery.
2. Raise vehicle on ramp.
3. Remove torque tube (see Workshop Manual procedure
05.01.CA Torque Tube - Re move for Access & Refit).
4. Disconnect multiplug between propshaft speed sensor and transmission harness (see Fig. 1).
5. Disconnect multiplug betwee n clutch position sensor
and transmission harness (see Fig. 2).
6. Release clips (x4) securing clutch pipe to transmission harness. 7. Release clips (x5) securing transmission harness to
torque tube.
8. Release clip securing transmission harness to clutch pipe bracket and remove harness (see Fig. 3).
Installation
1. Secure transmission harness to clutch pipe bracket using clip.
2. Secure transmission harness to torque tube using clips.
3. Secure clutch pipe to tran smission harness using clips.
4. Connect multiplug between clutch position sensor and transmission harness.
5. Connect multiplug between propshaft speed sensor and transmission harness.
6. Install torque tube (see Workshop Manual procedure 05.01.CA Torque Tube - Remove for Access & Refit).
7. Lower vehicle on ramp.
8. Connect vehicle battery.
Tailgate Harness-Renew
Removal
1. Battery isolator switch 'OFF'.
2. Remove trim - tailgate lid assembly (see Workshop Manual procedure 01.05.EF Trim - Tailgate Lid
Assembly - Renew).
3. Disconnect multiplugs (x4), behind trim panel.
4. Disconnect Lucar connectors (x2), heated rear window.
Repair Operation Time (ROT)
Warning
Always disconnect the battery earth (- ve) terminal first.
Warning
When raising the vehicle on a ‘two post’ ramp, ensure
that the rear end of the vehi cle is securely strapped to
the ramp. Failure to strap th e rear of the vehicle down
may lead to the vehicl e falling off the ramp.
Fig. 1
Fig. 2
!
!
Fig. 3
Warning
Always connect the battery earth (+ve) terminal first.
Repair Operation Time (ROT)
ItemCode
Tailgate Harness-Renew 18.01.JC
Warning
To prevent damage to elec trical components, always
disconnect the vehicle battery when working on the
vehicle's electrical system. The earth lead (- ve) must be disconnected first and reconnected last.
!
Page 744 of 947
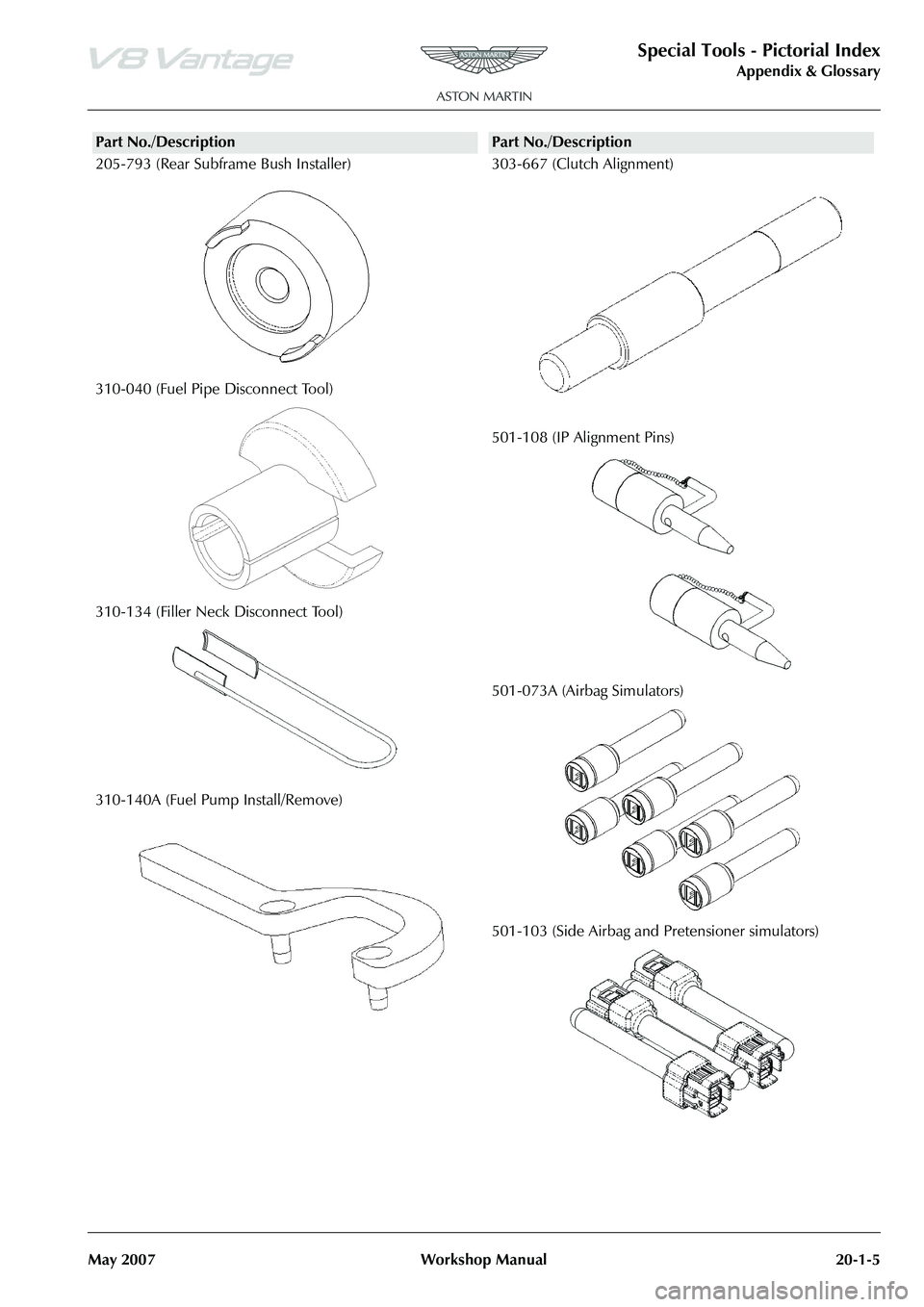
Special Tools - Pictorial Index
Appendix & Glossary
May 2007 Workshop Manual 20-1-5
205-793 (Rear Subframe Bush Installer)
310-040 (Fuel Pipe Disconnect Tool)
310-134 (Filler Neck Disconnect Tool)
310-140A (Fuel Pump Install/Remove)303-667 (Clutch Alignment)
501-108 (IP Alignment Pins)
501-073A (Airbag Simulators)
501-103 (Side Airbag and Pretensioner simulators)
Page 751 of 947
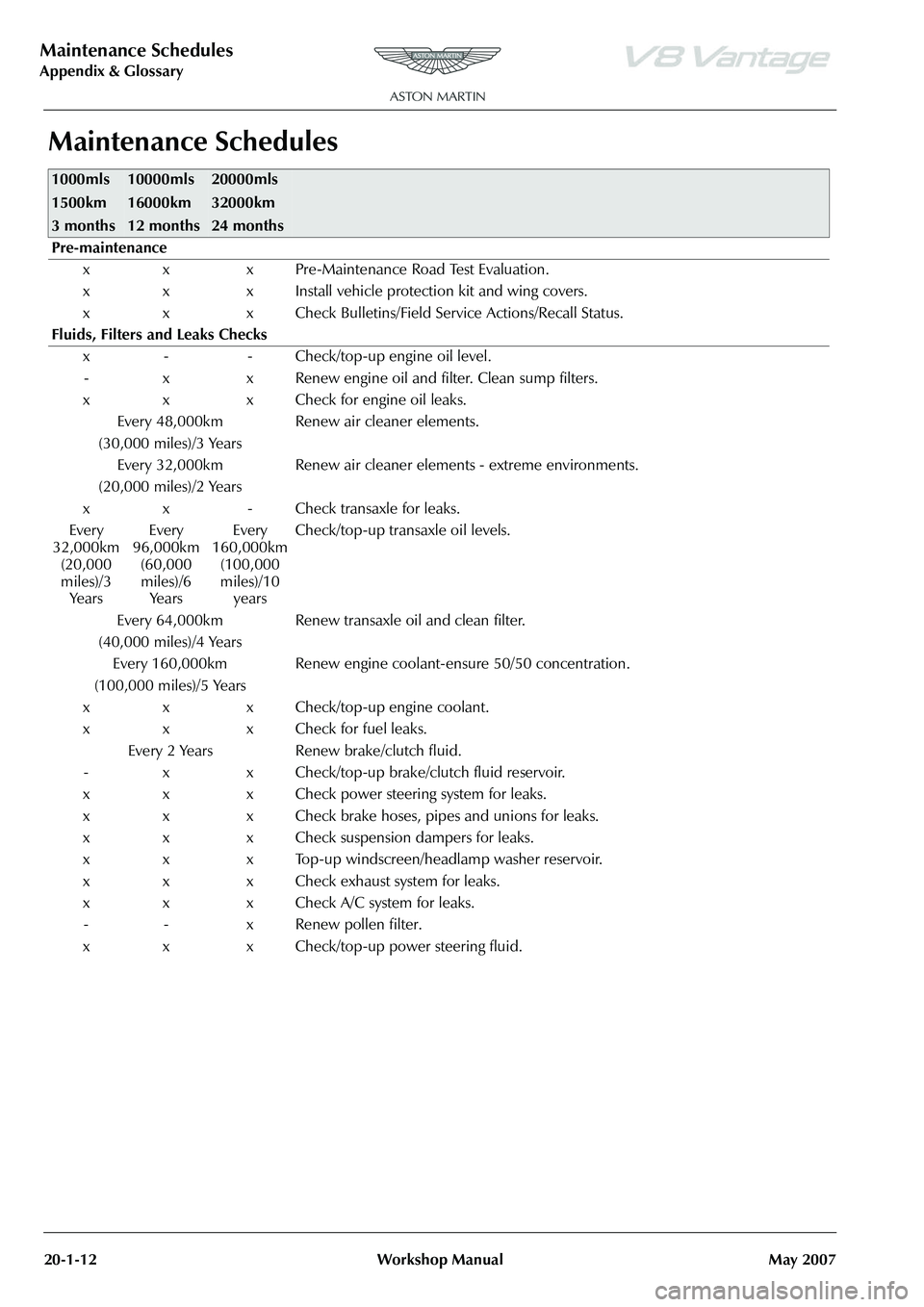
Maintenance Schedules
Appendix & Glossary20-1-12 Workshop Manual May 2007
Maintenance Schedules
1000mls
1500km
3 months10000mls
16000km
12 months20000mls
32000km
24 months
Pre-maintenance
x x x Pre-Maintenance Road Test Evaluation.
x x x Install vehicle protection kit and wing covers.
x x x Check Bulletins/Field Service Actions/Recall Status.
Fluids, Filters and Leaks Checks x - - Check/top-up engine oil level.- x x Renew engine oil and filter. Clean sump filters.
x x x Check for engine oil leaks. Every 48,000km
(30,000 miles)/3 Years Renew air cleaner elements.
Every 32,000km
(20,000 miles)/2 Years Renew air cleaner elements - extreme environments.
x x - Check transaxle for leaks.
Every
32,000km (20,000
miles)/3 Ye a r s Every
96,000km (60,000
miles)/6 Ye a r s Every
160,000km (100,000
miles)/10 years Check/top-up transaxle oil levels.
Every 64,000km
(40,000 miles)/4 Years Renew transaxle oil and clean filter.
Every 160,000km
(100,000 miles)/5 Years Renew engine coolant-ensure 50/50 concentration.
x x x Check/top-up engine coolant.
x x x Check for fuel leaks. Every 2 Years Renew brake/clutch fluid.
- x x Check/top-up brake/clutch fluid reservoir.
x x x Check power steering system for leaks.
x x x Check brake hoses, pipes and unions for leaks.
x x x Check suspension dampers for leaks.
x x x Top-up windscreen/headlamp washer reservoir.
x x x Check exhaust system for leaks.
x x x Check A/C system for leaks. - - x Renew pollen filter.
x x x Check/top-up power steering fluid.
Page 753 of 947
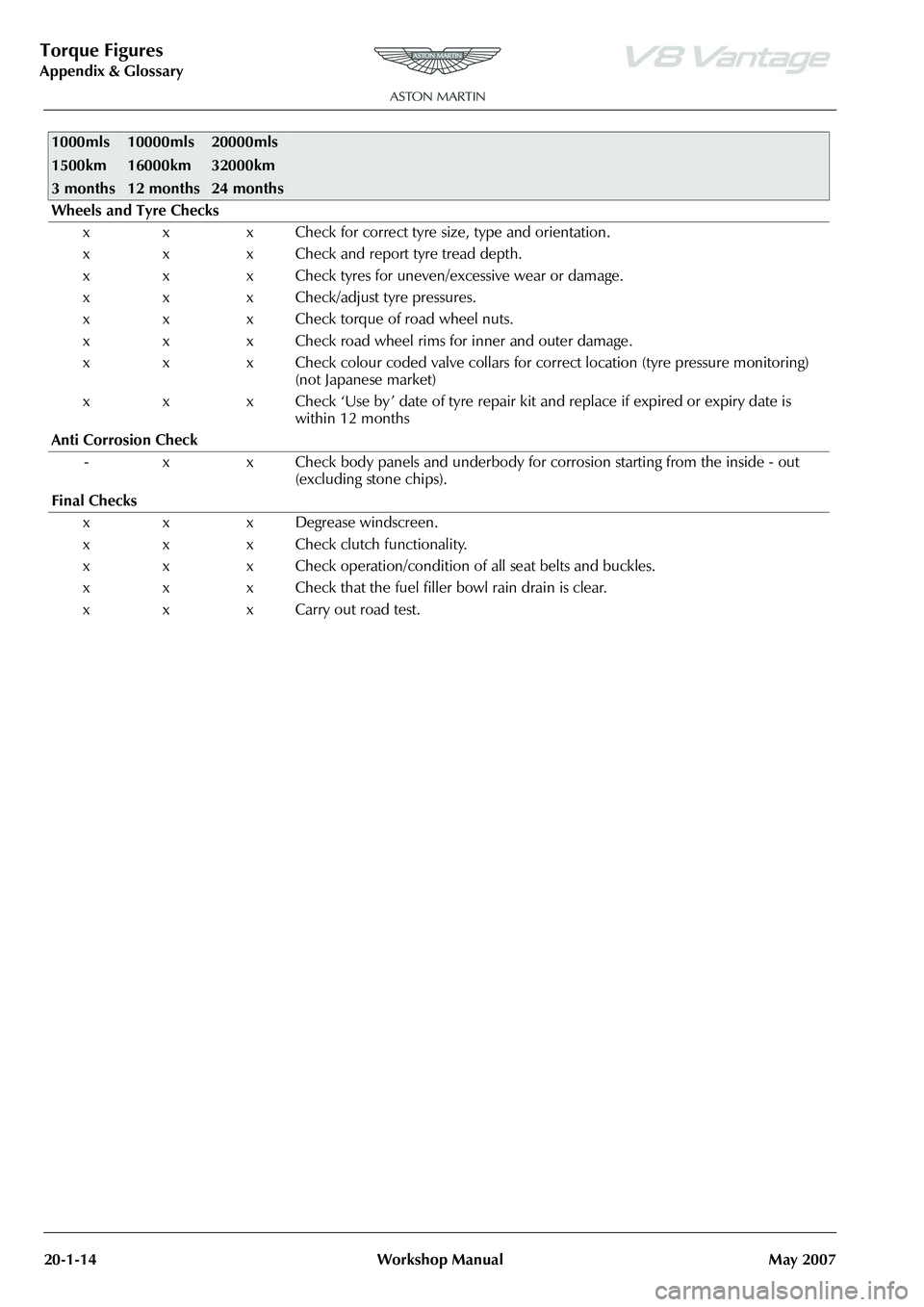
Torque Figures
Appendix & Glossary20-1-14 Workshop Manual May 2007
Wheels and Tyre Checks
x x x Check for correct tyre size, type and orientation.
x x x Check and report tyre tread depth.
x x x Check tyres for uneven/excessive wear or damage.
x x x Check/adjust tyre pressures.
x x x Check torque of road wheel nuts.
x x x Check road wheel rims for inner and outer damage.
x x x Check colour coded valve collars for co rrect location (tyre pressure monitoring)
(not Japanese market)
x x x Check ‘Use by ’ date of tyre repair kit and replace if expired or expiry date is
within 12 months
Anti Corrosion Check - x x Check body panels and underbody for corrosion starting from the inside - out
(excluding stone chips).
Final Checks x x x Degrease windscreen.
x x x Check clutch functionality.
x x x Check operation/condition of all seat belts and buckles.
x x x Check that the fuel filler bowl rain drain is clear.
x x x Carry out road test.
1000mls
1500km
3 months10000mls
16000km
12 months20000mls
32000km
24 months
Page 877 of 947
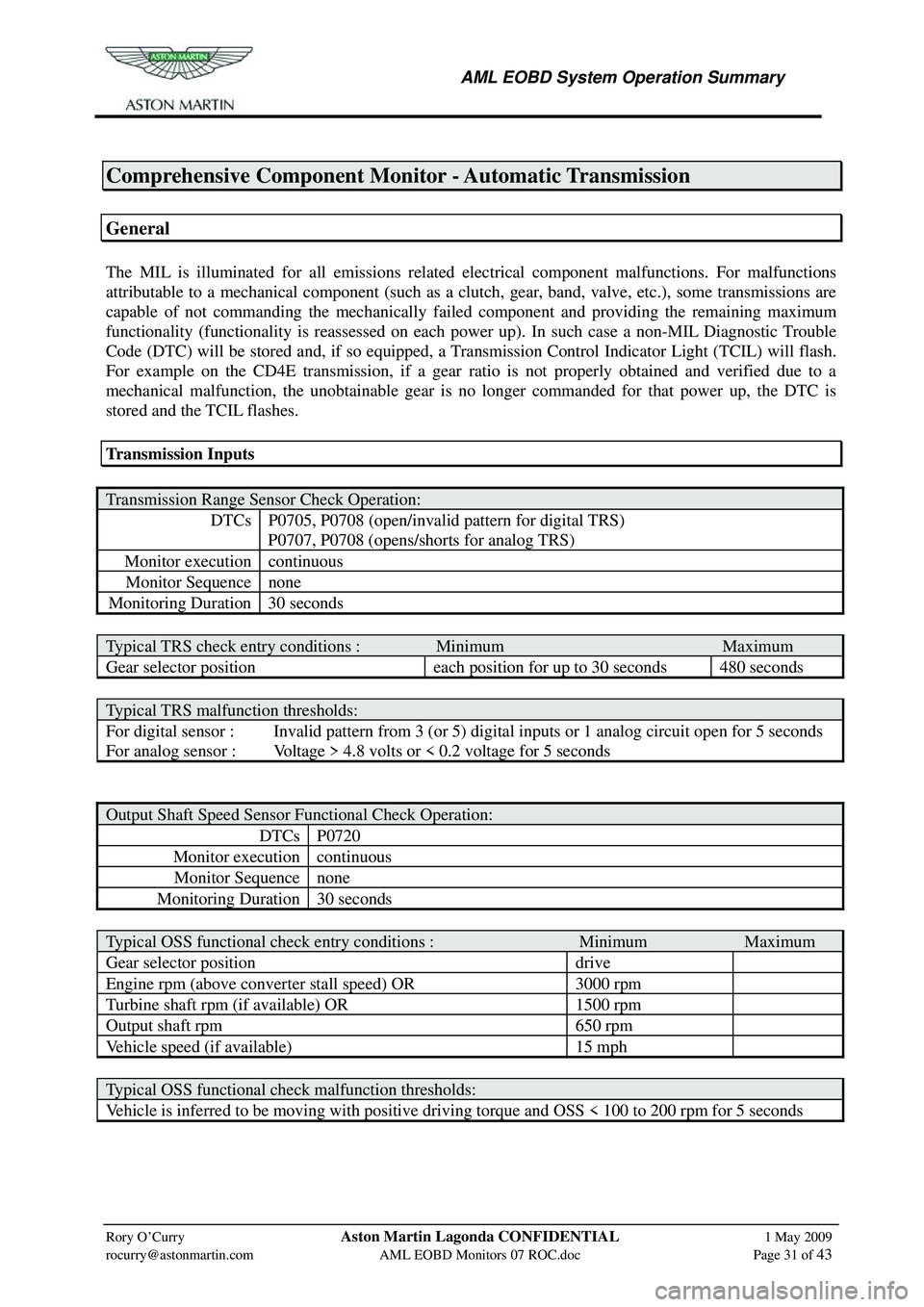
AML EOBD System Operation Summary
Rory O’Curry Aston Martin Lagonda CONFIDENTIAL 1 May 2009
[email protected] AML EOBD Monitors 07 ROC.doc Page 31 of 43
Comprehensive Component Monitor - Automatic Transmission
General
The MIL is illuminated for all emissions related electrical component malfunctions. For malfunctions
attributable to a mechanical component (such as a clutch, gear, band, valve, etc.), some transmissions are
capable of not commanding the mechanically faile d component and providing the remaining maximum
functionality (functionality is reassessed on each power up). In such case a non-MIL Diagnostic Trouble
Code (DTC) will be stored and, if so equipped, a Transmission Control Indicator Light (TCIL) will flash.
For example on the CD4E transmission, if a gear ratio is not properly obtained and verified due to a
mechanical malfunction, the unobtainable gear is no longer commanded for that power up, the DTC is
stored and the TCIL flashes.
Transmission Inputs
Transmission Range Sensor Check Operation:
DTCs P0705, P0708 (open/invalid pattern for digital TRS)
P0707, P0708 (opens/shorts for analog TRS)
Monitor execution continuous
Monitor Sequence none
Monitoring Duration 30 seconds
Typical TRS check entry conditions : Minimum Maximum
Gear selector position each position for up to 30 seconds 480 seconds
Typical TRS malfunction thresholds:
For digital sensor : Invalid pattern from 3 (or 5) digital inputs or 1 analog circuit open for 5 seconds
For analog sensor : Voltage > 4.8 volts or < 0.2 voltage for 5 seconds
Output Shaft Speed Sensor Functional Check Operation:
DTCs P0720
Monitor execution continuous
Monitor Sequence none
Monitoring Duration 30 seconds
Typical OSS functional check entry conditions : Minimum Maximum
Gear selector position drive
Engine rpm (above converter stall speed) OR 3000 rpm
Turbine shaft rpm (if available) OR 1500 rpm
Output shaft rpm 650 rpm
Vehicle speed (if available) 15 mph
Typical OSS functional check malfunction thresholds:
Vehicle is inferred to be moving with positive driving torque and OSS < 100 to 200 rpm for 5 seconds
Page 879 of 947

AML EOBD System Operation Summary
Rory O’Curry Aston Martin Lagonda CONFIDENTIAL 1 May 2009
[email protected] AML EOBD Monitors 07 ROC.doc Page 33 of 43
Transmission Outputs
Shift Solenoid Check Operation:
DTCs SS A - P0750 electrical, P1714 ISIG functional,
SS B - P0755 electrical, P1715 ISIG functional,
SS C - P0760 electrical, P1716 ISIG functional,
SS D - P0765 electrical, P1717 ISIG functional
SS E - P0770 electrical
Monitor execution electrical - continuous, functi onal - during off to on solenoid transitions
Monitor Sequence none
Typical SS malfunction thresholds:
Output driver feedback circuit does not match commanded driver state for 5 seconds.
ISIG functional check: ISIG chip hardware circu it does not detect characteristic current dip and rise
produced by solenoid movement for 10 solenoid events.
Torque Converter Clutch Check Operation:
DTCs P0743 electrical, P1740 ISIG functional
Monitor execution electrical – continuous, functi onal - during off to on solenoid transitions
Monitor Sequence none
Typical TCC malfunction thresholds:
Output driver feedback circuit does not match commanded driver state for 5 seconds
(> 1.0 volt if commanded on, < 2.0 volts if commanded off.)
ISIG functional check: ISIG chip hardware circu it does not detect characteristic current dip and rise
produced by solenoid movement.
Electronic Pressure Control Check Operation:
DTCs P1747 electrical, P1789, P0797 short to ground (low pressure)
P0745, P0775, P0795 mechanical functional
Monitor execution Continuous
Monitor Sequence None
Monitoring Duration Electrical: 5 seconds,
Mechanical functional: up to 30 seconds
Typical EPC malfunction thresholds:
Current feedback circuit is less than commanded current for 5 seconds
Transmission CCM temporary disablement conditions (other than entry requirements) :
None.
Page 880 of 947
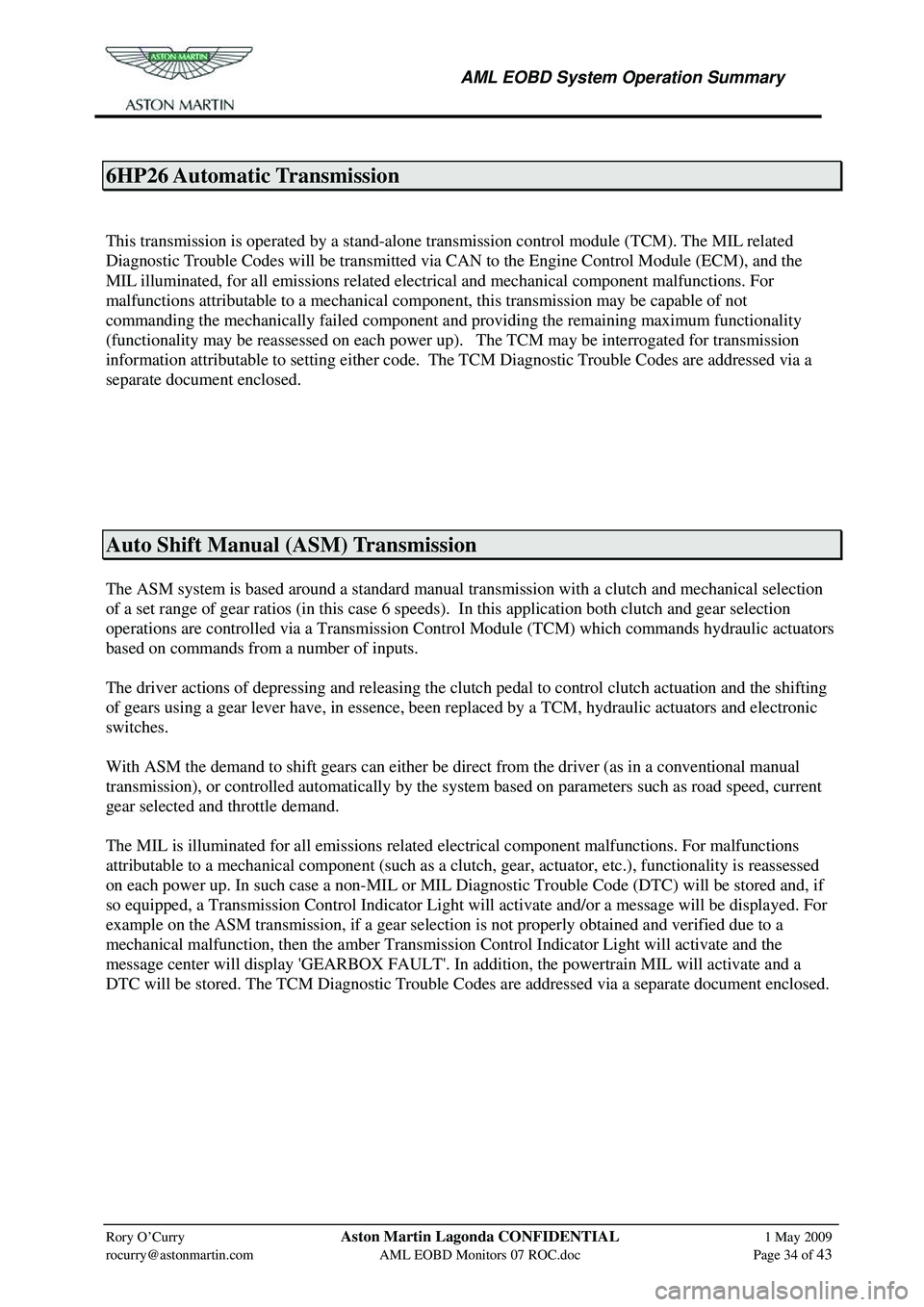
AML EOBD System Operation Summary
Rory O’Curry Aston Martin Lagonda CONFIDENTIAL 1 May 2009
[email protected] AML EOBD Monitors 07 ROC.doc Page 34 of 43
6HP26 Automatic Transmission
This transmission is operated by a stand-alone transmission control module (TCM). The MIL related
Diagnostic Trouble Codes will be transmitted via CAN to the Engine Control Module (ECM), and the
MIL illuminated, for all emissions related electrical and mechanical component malfunctions. For
malfunctions attributable to a mechanical component, this transmission may be capable of not
commanding the mechanically failed component a nd providing the remaining maximum functionality
(functionality may be reassessed on each power up). The TCM may be interrogated for transmission
information attributable to setting either code. The TCM Diagnostic Trouble Codes are addressed via a
separate document enclosed.
Auto Shift Manual (ASM) Transmission
The ASM system is based around a standard manual transmission with a clutch and mechanical selection
of a set range of gear ratios (in this case 6 speeds). In this application both clutch and gear selection
operations are controlled via a Transmission Contro l Module (TCM) which commands hydraulic actuators
based on commands from a number of inputs.
The driver actions of depressing and releasing the clutch pedal to control clutch actuation and the shifting
of gears using a gear lever have, in essence, been re placed by a TCM, hydraulic actuators and electronic
switches.
With ASM the demand to shift gears can either be direct from the driver (as in a conventional manual
transmission), or controlled automatically by the system based on parameters such as road speed, current
gear selected and throttle demand.
The MIL is illuminated for all emissions related electrical component malfunctions. For malfunctions
attributable to a mechanical component (such as a cl utch, gear, actuator, etc.), functionality is reassessed
on each power up. In such case a non-MIL or MIL Diagnos tic Trouble Code (DTC) will be stored and, if
so equipped, a Transmission Control Indicator Light will activate and/or a message will be displayed. For
example on the ASM transmission, if a gear selection is not properly obtained and verified due to a
mechanical malfunction, then the amber Transmission Control Indicator Light will activate and the
message center will display 'GEARBOX FAULT'. In addition, the powertrain MIL will activate and a
DTC will be stored. The TCM Diagnostic Trouble Cod es are addressed via a separate document enclosed.