parking ASTON MARTIN V8 VANTAGE 2010 Workshop Manual
[x] Cancel search | Manufacturer: ASTON MARTIN, Model Year: 2010, Model line: V8 VANTAGE, Model: ASTON MARTIN V8 VANTAGE 2010Pages: 947, PDF Size: 43.21 MB
Page 211 of 947
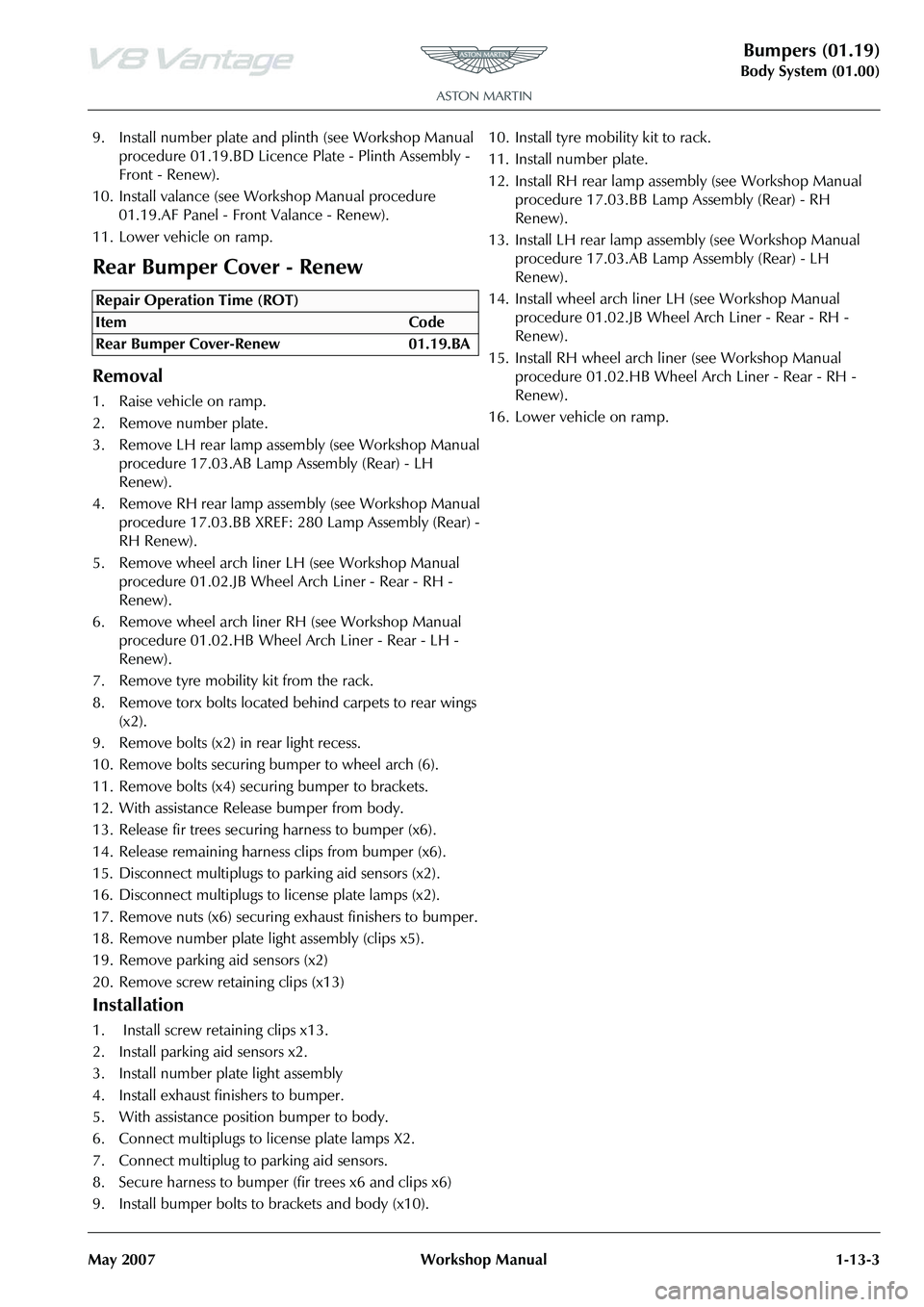
Bumpers (01.19)
Body System (01.00)
May 2007 Workshop Manual 1-13-3
9. Install number plate and plinth (see Workshop Manual procedure 01.19.BD Licence Plate - Plinth Assembly -
Front - Renew).
10. Install valance (see Workshop Manual procedure 01.19.AF Panel - Front Valance - Renew).
11. Lower vehicle on ramp.
Rear Bumper Cover - Renew
Removal
1. Raise vehicle on ramp.
2. Remove number plate.
3. Remove LH rear lamp assembly (see Workshop Manual procedure 17.03.AB Lamp Assembly (Rear) - LH
Renew).
4. Remove RH rear lamp assembly (see Workshop Manual procedure 17.03.BB XREF: 280 Lamp Assembly (Rear) -
RH Renew).
5. Remove wheel arch liner LH (see Workshop Manual procedure 01.02.JB Wheel Arch Liner - Rear - RH -
Renew).
6. Remove wheel arch liner RH (see Workshop Manual procedure 01.02.HB Wheel Arch Liner - Rear - LH -
Renew).
7. Remove tyre mobility kit from the rack.
8. Remove torx bolts located behind carpets to rear wings (x2).
9. Remove bolts (x2) in rear light recess.
10. Remove bolts securing bumper to wheel arch (6).
11. Remove bolts (x4) securing bumper to brackets.
12. With assistance Release bumper from body.
13. Release fir trees securing harness to bumper (x6).
14. Release remaining harness clips from bumper (x6).
15. Disconnect multiplugs to parking aid sensors (x2).
16. Disconnect multiplugs to license plate lamps (x2).
17. Remove nuts (x6) securing exhaust finishers to bumper.
18. Remove number plate light assembly (clips x5).
19. Remove parking aid sensors (x2)
20. Remove screw retaining clips (x13)
Installation
1. Install screw retaining clips x13.
2. Install parking aid sensors x2.
3. Install number pl ate light assembly
4. Install exhaust finishers to bumper.
5. With assistance position bumper to body.
6. Connect multiplugs to license plate lamps X2.
7. Connect multiplug to parking aid sensors.
8. Secure harness to bumper (f ir trees x6 and clips x6)
9. Install bumper bolts to brackets and body (x10). 10. Install tyre mobility kit to rack.
11. Install number plate.
12. Install RH rear lamp asse
mbly (see Workshop Manual
procedure 17.03.BB Lamp Assembly (Rear) - RH
Renew).
13. Install LH rear lamp assembly (see Workshop Manual procedure 17.03.AB Lamp Assembly (Rear) - LH
Renew).
14. Install wheel arch liner LH (see Workshop Manual procedure 01.02.JB Wheel Arch Liner - Rear - RH -
Renew).
15. Install RH wheel arch li ner (see Workshop Manual
procedure 01.02.HB Wheel Arch Liner - Rear - RH -
Renew).
16. Lower vehicle on ramp.
Repair Operation Time (ROT)
Page 453 of 947
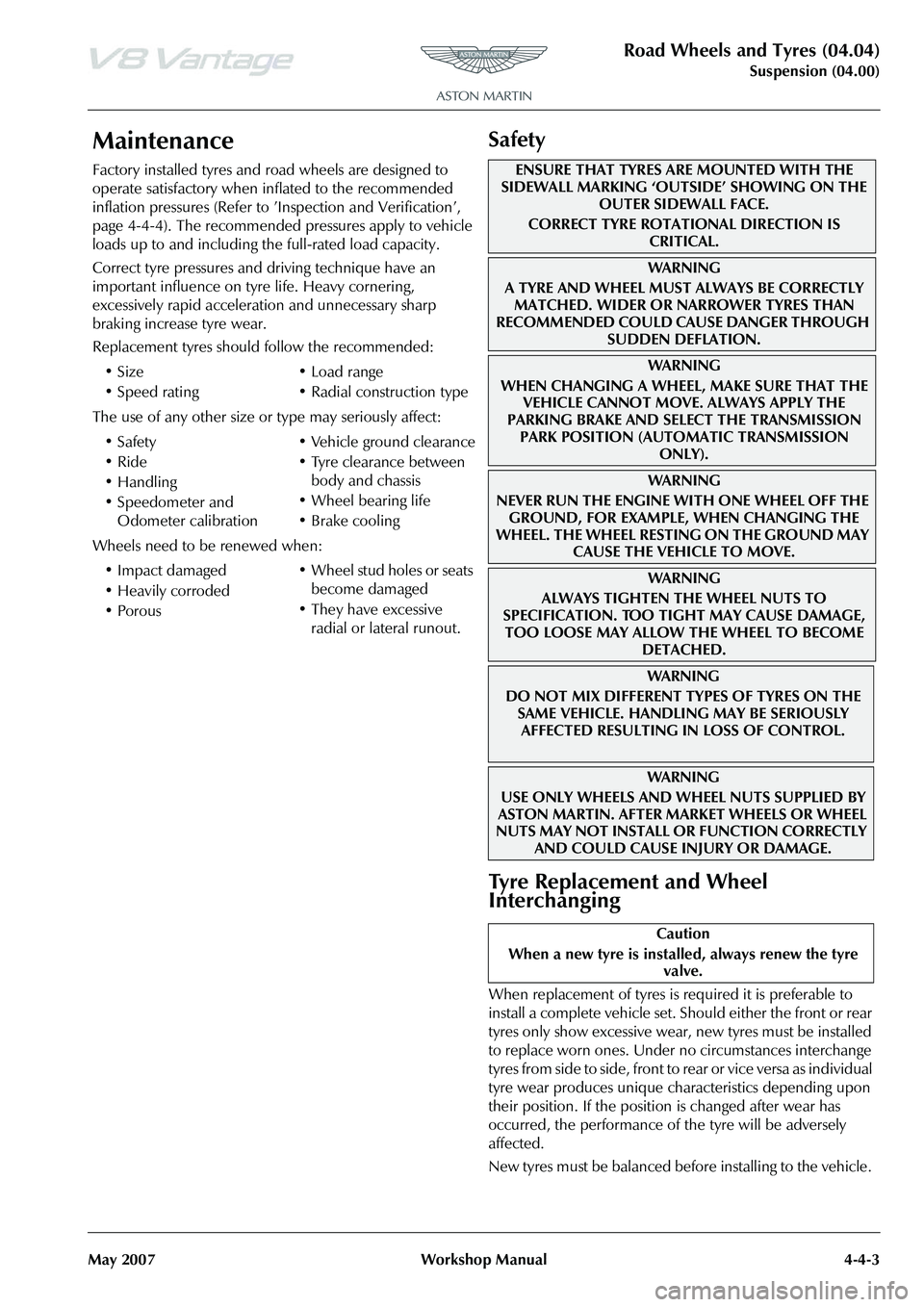
Road Wheels and Tyres (04.04)
Suspension (04.00)
May 2007 Workshop Manual 4-4-3
Maintenance
Factory installed tyres and road wheels are designed to
operate satisfactory when inflated to the recommended
inflation pressures (Refer to ’Inspection and Verification’,
page 4-4-4). The recommended pressures apply to vehicle
loads up to and including the full-rated load capacity.
Correct tyre pressures and driving technique have an
important influence on tyre life. Heavy cornering,
excessively rapid acceleration and unnecessary sharp
braking increase tyre wear.
Replacement tyres should follow the recommended:
The use of any other size or type may seriously affect:
Wheels need to be renewed when:
Safety
Tyre Replacement and Wheel
Interchanging
When replacement of tyres is required it is preferable to
install a complete vehicle set. S hould either the front or rear
tyres only show excessive wear, new tyres must be installed
to replace worn ones. Under no circumstances interchange
tyres from side to side, front to re ar or vice versa as individual
tyre wear produces unique characteristics depending upon
their position. If the position is changed after wear has
occurred, the performance of the tyre will be adversely
affected.
New tyres must be balanced before installing to the vehicle.
•Size
•Speed rating
•Load range
• Radial construction type
•Safety
•Ride
•Handling
• Speedometer and Odometer calibration • Vehicle ground clearance
• Tyre clearance between
body and chassis
• Wheel bearing life
• Brake cooling
• Impact damaged
• Heavily corroded
• Porous • Wheel stud holes or seats
become damaged
• They have excessive radial or lateral runout.
ENSURE THAT TYRES ARE MOUNTED WITH THE
SIDEWALL MARKING ‘OUTSIDE’ SHOWING ON THE
OUTER SIDEWALL FACE.
CORRECT TYRE ROTATIONAL DIRECTION IS CRITICAL.
WA R N I N G
A TYRE AND WHEEL MUST ALWAYS BE CORRECTLY MATCHED. WIDER OR NARROWER TYRES THAN
RECOMMENDED COULD CAUSE DANGER THROUGH
SUDDEN DEFLATION.
WA R N I N G
WHEN CHANGING A WHEEL, MAKE SURE THAT THE VEHICLE CANNOT MOVE. ALWAYS APPLY THE
PARKING BRAKE AND SELE CT THE TRANSMISSION
PARK POSITION (AUTOMATIC TRANSMISSION ONLY).
WA R N I N G
NEVER RUN THE ENGINE WITH ONE WHEEL OFF THE GROUND, FOR EXAMPLE, WHEN CHANGING THE
WHEEL. THE WHEEL RESTING ON THE GROUND MAY CAUSE THE VEHICLE TO MOVE.
WA R N I N G
ALWAYS TIGHTEN THE WHEEL NUTS TO
SPECIFICATION. TOO TIGHT MAY CAUSE DAMAGE,
TOO LOOSE MAY ALLOW TH E WHEEL TO BECOME
DETACHED.
WAR NI NG
DO NOT MIX DIFFERENT TY PES OF TYRES ON THE
SAME VEHICLE. HANDLING MAY BE SERIOUSLY AFFECTED RESULTING IN LOSS OF CONTROL.
WAR NI NG
USE ONLY WHEELS AND WHEEL NUTS SUPPLIED BY
ASTON MARTIN. AFTER MARKET WHEELS OR WHEEL
NUTS MAY NOT INSTALL OR FUNCTION CORRECTLY
AND COULD CAUSE INJURY OR DAMAGE.
Caution
When a new tyre is installe d, always renew the tyre
valve.
Page 483 of 947
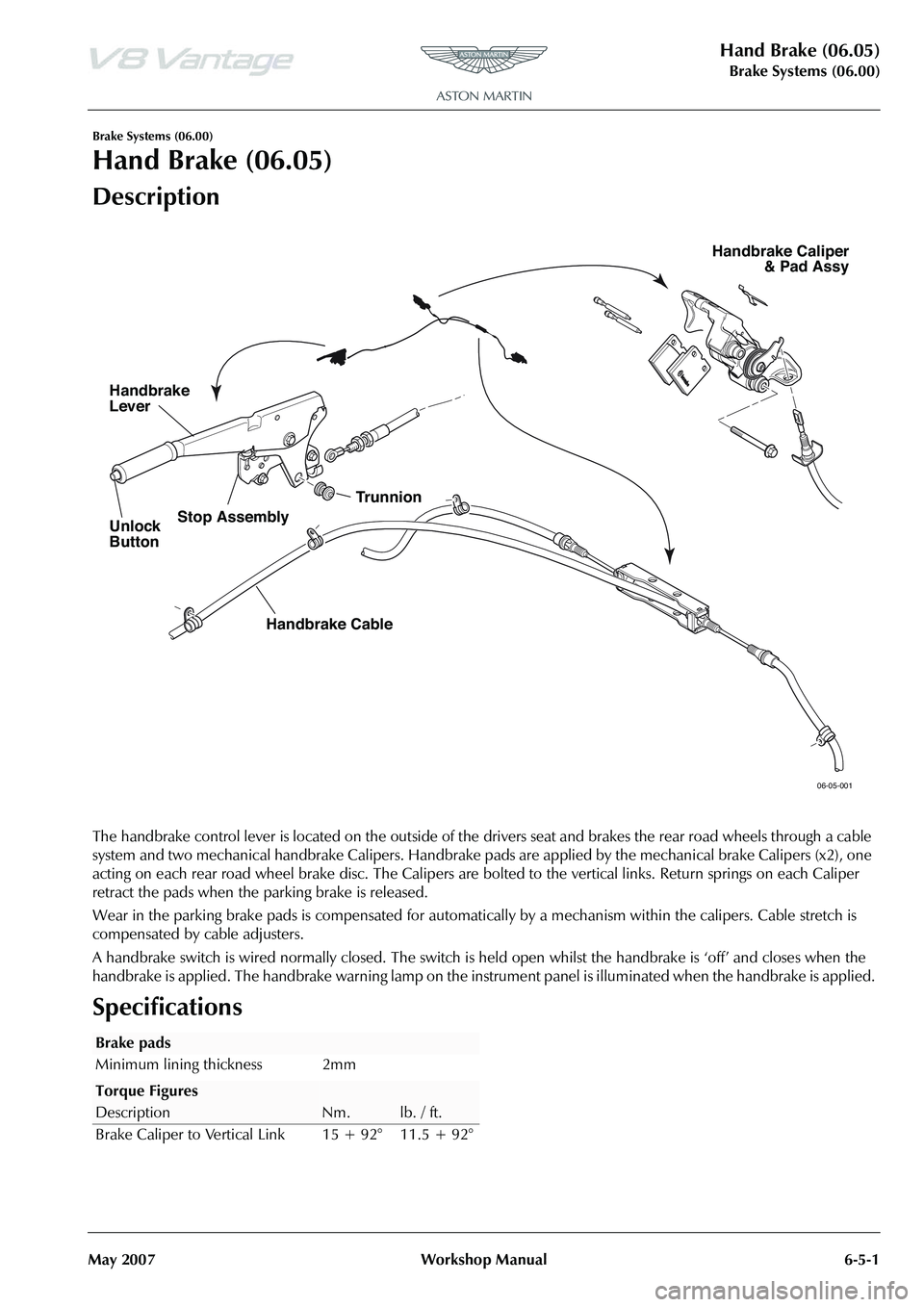
Hand Brake (06.05)
Brake Systems (06.00)
May 2007 Workshop Manual 6-5-1
Brake Systems (06.00)
Hand Brake (06.05)
Description
The handbrake control lever is located on the outside of the drivers seat and brakes the rear road wheels through a cable
system and two mechanical handbrake Calipers. Handbrake pads are applied by the mechanical brake Calipers (x2), one
acting on each rear road wheel brake disc. The Calipers are bo lted to the vertical links. Return springs on each Caliper
retract the pads when the parking brake is released.
Wear in the parking brake pads is compensated for automati cally by a mechanism within the calipers. Cable stretch is
compensated by cable adjusters.
A handbrake switch is wired normally closed. The switch is he ld open whilst the handbrake is ‘off’ and closes when the
handbrake is applied. The handbrake warning lamp on the instrument panel is illuminated when the handbrake is applied.
Specifications
06-05-001
Unlock
Button
Handbrake
Lever
Trunnion
Handbrake Cable
Stop Assembly
Handbrake Caliper
& Pad Assy
Brake pads
Minimum lining thickness 2mm
Torque Figures
DescriptionNm.lb. / ft.
Brake Caliper to Vertical Link 15 + 92° 11.5 + 92°
Page 603 of 947
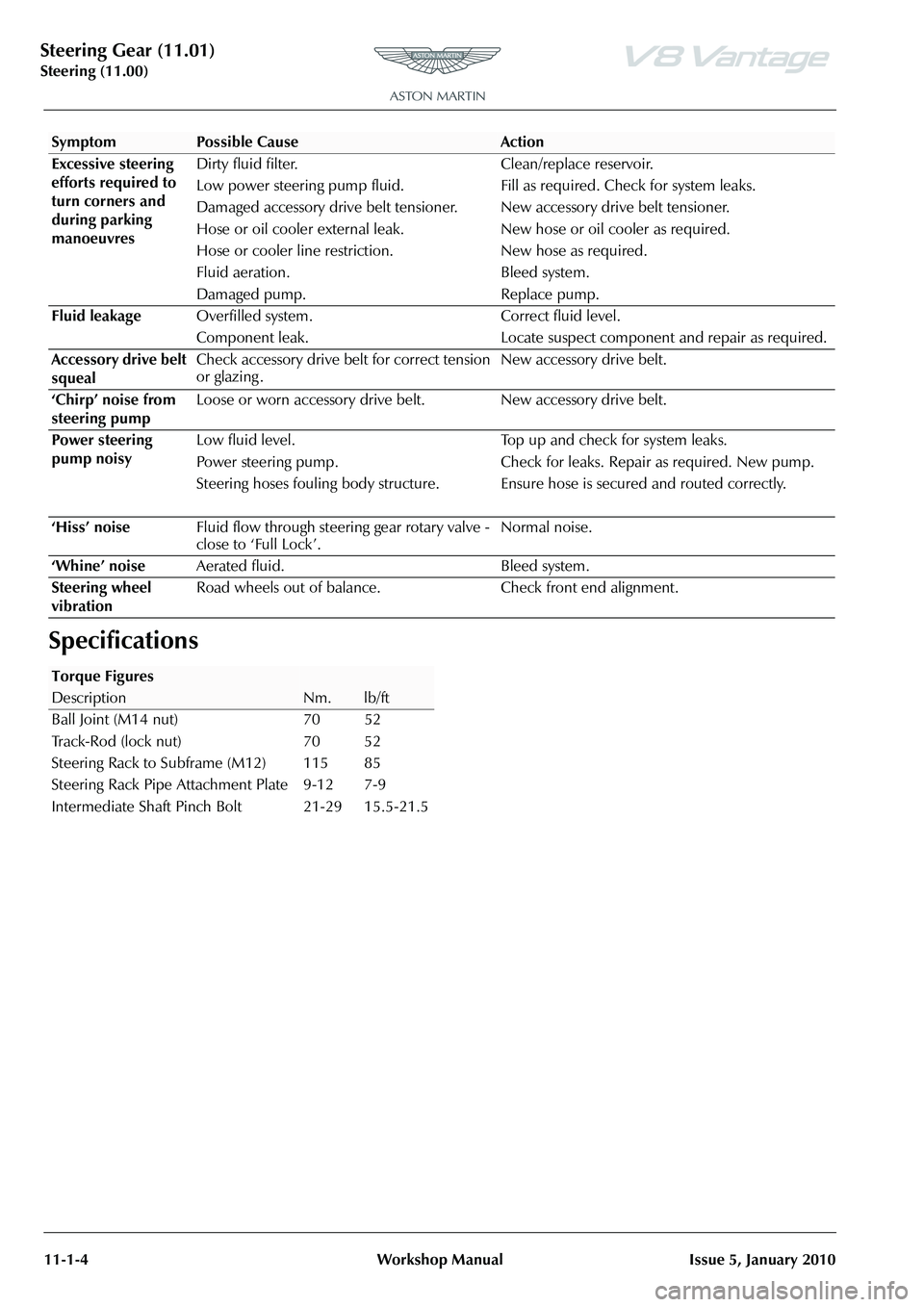
Steering Gear (11.01)
Steering (11.00)11-1-4 Workshop Manual Issue 5, January 2010
Specifications
Excessive steering
efforts required to
turn corners and
during parking
manoeuvres Dirty fluid filter.
Low power steering pump fluid.
Clean/replace reservoir.
Fill as required. Check for system leaks.
Damaged accessory drive belt tensioner. New accessory drive belt tensioner.
Hose or oil cooler external leak. New hose or oil cooler as required.
Hose or cooler line restriction. New hose as required.
Fluid aeration.
Damaged pump. Bleed system.
Replace pump.
Fluid leakage Overfilled system. Correct fluid level.
Component leak. Locate suspect component and repair as required.
Accessory drive belt
squeal Check accessory drive belt for correct tension
or glazing .
New accessory drive belt.
‘Chirp’ noise from
steering pump Loose or worn accessory drive belt. New accessory drive belt.
Power steering
pump noisy Low fluid level. Top up and check for system leaks.
Power steering pump.
Steering hoses fouling body structure. Check for leaks. Repair
as required. New pump.
Ensure hose is secured and routed correctly.
‘Hiss’ noise Fluid flow through steering gear rotary valve -
close to ‘Full Lock’. Normal noise.
‘Whine’ noise Aerated fluid. Bleed system.
Steering wheel
vibration Road wheels out of balance. Check front end alignment.
SymptomPossible CauseAction
Torque Figures
DescriptionNm.lb/ft
Ball Joint (M14 nut) 70 52
Track-Rod (lock nut) 70 52
Steering Rack to Subframe (M12) 115 85
Steering Rack Pipe Attachment Plate 9-12 7-9
Intermediate Shaft Pinch Bolt 21-29 15.5-21.5
Page 604 of 947
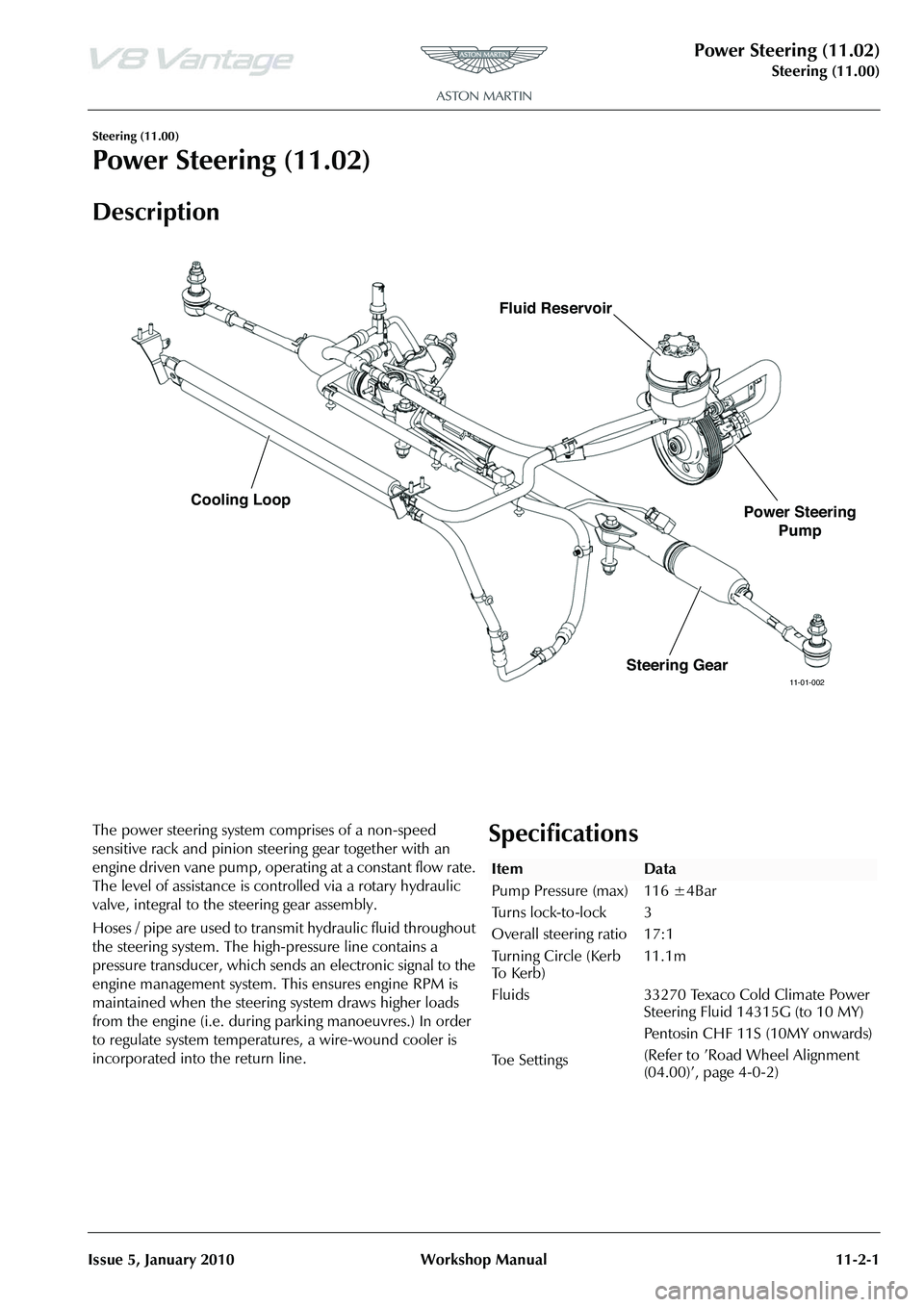
Power Steering (11.02)
Steering (11.00)
Issue 5, January 2010 Workshop Manual 11-2-1
Steering (11.00)
Power Steering (11.02)
Description
The power steering system comprises of a non-speed
sensitive rack and pinion steering gear together with an
engine driven vane pump, operating at a constant flow rate.
The level of assistance is co ntrolled via a rotary hydraulic
valve, integral to the steering gear assembly.
Hoses / pipe are used to transm it hydraulic fluid throughout
the steering system. The high -pressure line contains a
pressure transducer, which sends an electronic signal to the
engine management system. This ensures engine RPM is
maintained when the steering system draws higher loads
from the engine (i.e. during parking manoeuvres.) In order
to regulate system temperatures, a wire-wound cooler is
incorporated into the return line.Specifications
11-01-002Steering Gear
Cooling Loop
Power Steering
Pump
Fluid Reservoir
ItemData
Pump Pressure (max)
Turns lock-to-lock
Overall steering ratio
Turning Circle (Kerb
To K e r b )
Fluids
Toe Settings 116 ±4Bar
3
17:1
11.1m
33270 Texaco Cold Climate Power
Steering Fluid 14315G (to 10 MY)
Pentosin CHF 11S (10MY onwards)
(Refer to ’Road Wheel Alignment
(04.00)
Page 692 of 947
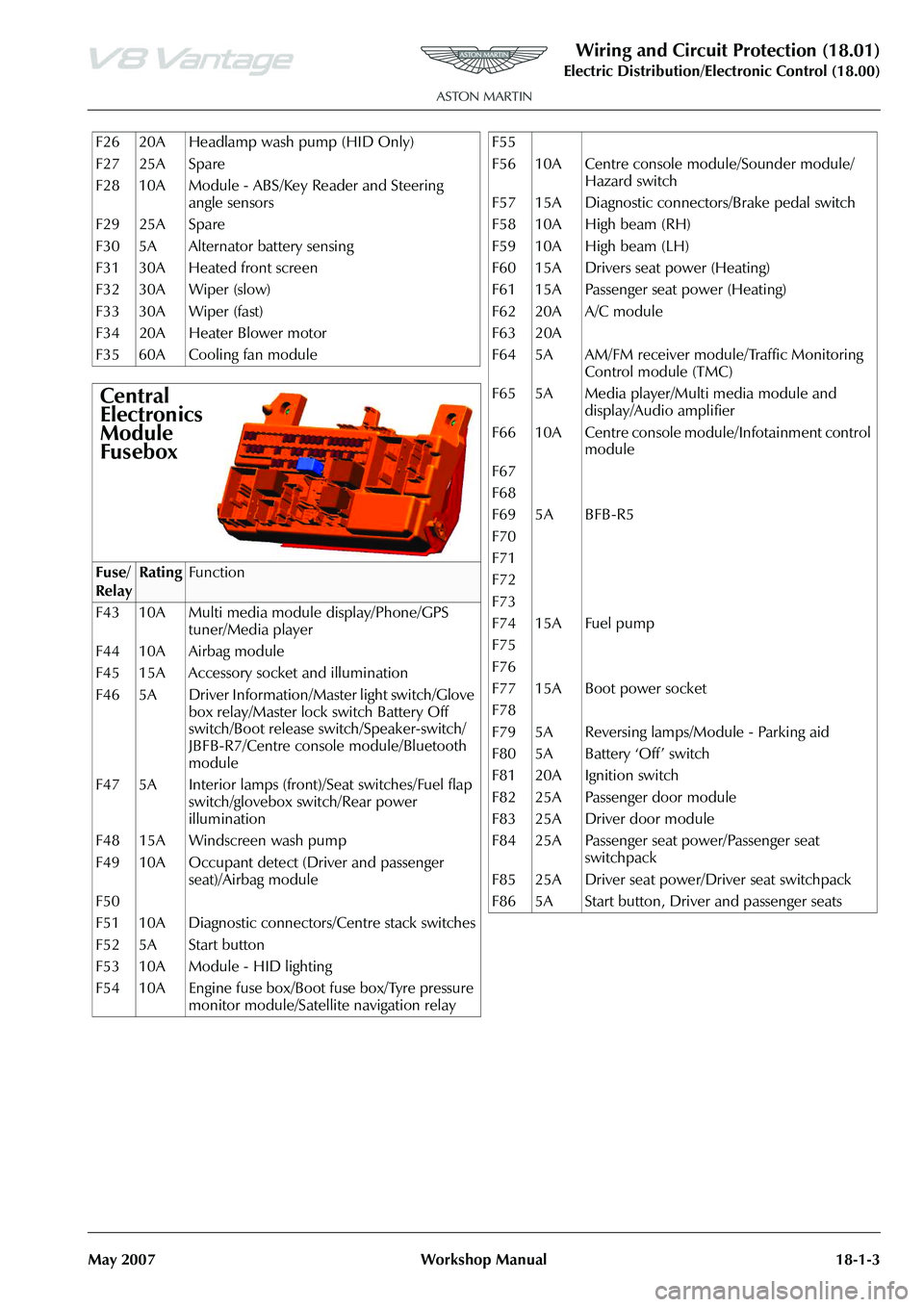
Wiring and Circuit Protection (18.01)
Electric Distribution/Electronic Control (18.00)
May 2007 Workshop Manual 18-1-3
F26 20A Headlamp wash pump (HID Only)
F27 25A Spare
F28 10A Module - ABS/Key Reader and Steering angle sensors
F29 25A Spare
F30 5A Alternator battery sensing
F31 30A Heated front screen
F32 30A Wiper (slow)
F33 30A Wiper (fast)
F34 20A Heater Blower motor
F35 60A Cooling fan module
Central
Electronics
Module
Fusebox
Fuse/
RelayRatingFunction
F43 10A Multi media module display/Phone/GPS tuner/Media player
F44 10A Airbag module
F45 15A Accessory socket and illumination
F46 5A Driver Information/Master light switch/Glove box relay/Master lock switch Battery Off
switch/Boot release switch/Speaker-switch/
JBFB-R7/Centre console module/Bluetooth
module
F47 5A Interior lamps (front)/Seat switches/Fuel flap switch/glovebox switch/Rear power
illumination
F48 15A Windscreen wash pump
F49 10A Occupant detect (Driver and passenger seat)/Airbag module
F50
F51 10A Diagnostic connectors/Centre stack switches
F52 5A Start button
F53 10A Module - HID lighting
F54 10A Engine fuse box/Boot fuse box/Tyre pressure monitor module/Satellite navigation relay
F55
F56 10A Centre console module/Sounder module/
Hazard switch
F57 15A Diagnostic connectors/Brake pedal switch
F58 10A High beam (RH)
F59 10A High beam (LH)
F60 15A Drivers seat power (Heating)
F61 15A Passenger seat power (Heating)
F62 20A A/C module
F63 20A
F64 5A AM/FM receiver module/Traffic Monitoring Control module (TMC)
F65 5A Media player/Multi media module and display/Audio amplifier
F66 10A Centre console module/Infotainment control module
F67
F68
F69 5A BFB-R5
F70
F71
F72
F73
F74 15A Fuel pump
F75
F76
F77 15A Boot power socket
F78
F79 5A Reversing lamps/Module - Parking aid
F80 5A Battery ‘Off’ switch
F81 20A Ignition switch
F82 25A Passenger door module
F83 25A Driver door module
F84 25A Passenger seat power/Passenger seat switchpack
F85 25A Driver seat power/Driver seat switchpack
F86 5A Start button, Driver and passenger seats
Page 693 of 947
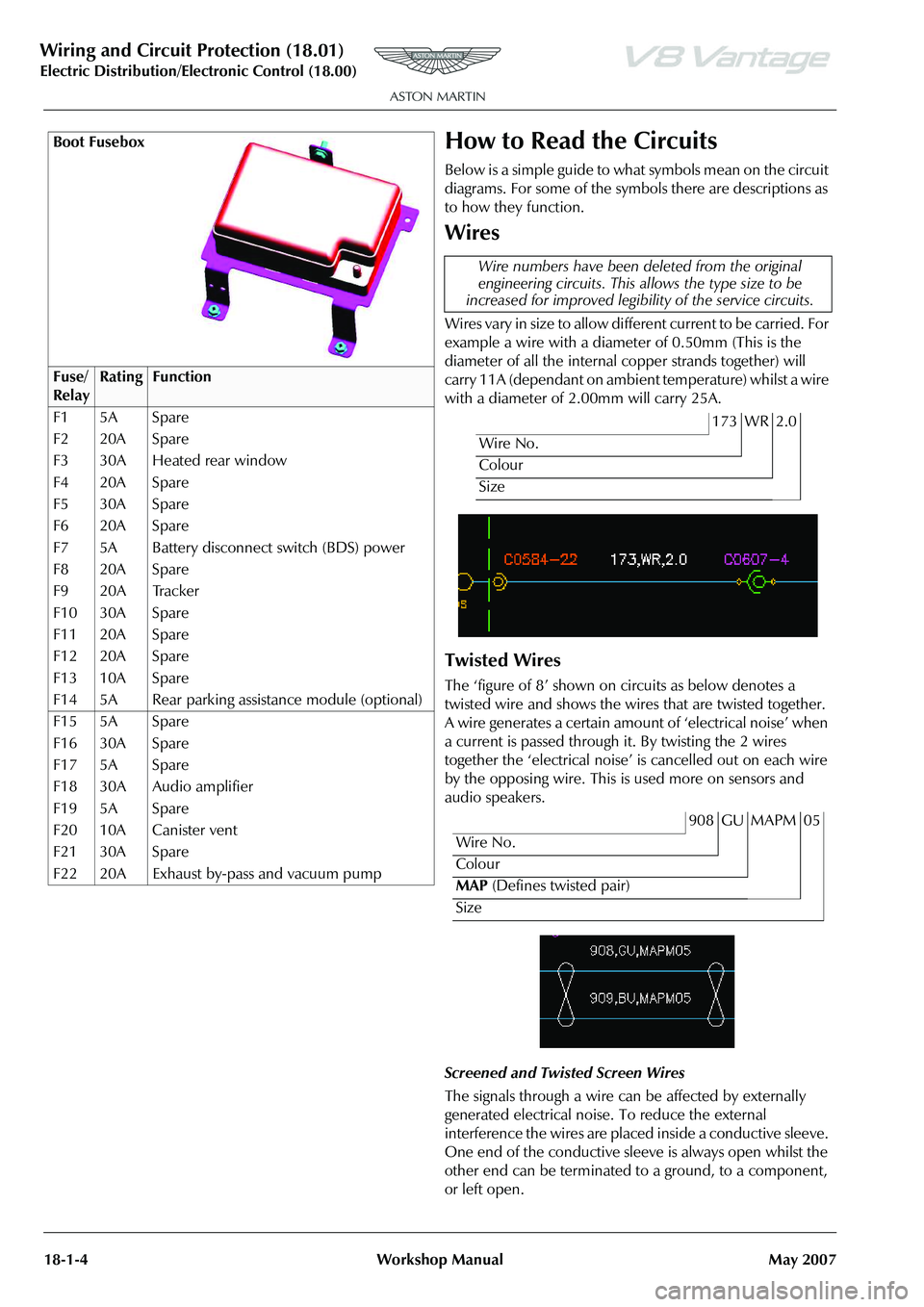
Wiring and Circuit Protection (18.01)
Electric Distribution/E lectronic Control (18.00)
18-1-4 Workshop Manual May 2007
How to Read the Circuits
Below is a simple guide to what symbols mean on the circuit
diagrams. For some of the symbols there are descriptions as
to how they function.
Wires
Wires vary in size to allow diffe rent current to be carried. For
example a wire with a diamet er of 0.50mm (This is the
diameter of all the internal copper strands together) will
carry 11A (dependant on ambient temperature) whilst a wire
with a diameter of 2.00mm will carry 25A.
Twisted Wires
The ‘figure of 8’ shown on circuits as below denotes a
twisted wire and shows the wires that are twisted together.
A wire generates a certain amount of ‘electrical noise’ when
a current is passed through it. By twisting the 2 wires
together the ‘electrical noise’ is cancelled out on each wire
by the opposing wire. This is used more on sensors and
audio speakers.
Screened and Twisted Screen Wires
The signals through a wire can be affected by externally
generated electrical noise. To reduce the external
interference the wires are placed inside a conductive sleeve.
One end of the conductive sleeve is always open whilst the
other end can be terminated to a ground, to a component,
or left open.
Boot Fusebox
Fuse/
RelayRatingFunction
F1 5A Spare
F2 20A Spare
F3 30A Heated rear window
F4 20A Spare
F5 30A Spare
F6 20A Spare
F7 5A Battery disconnect switch (BDS) power
F8 20A Spare
F9 20A Tracker
F10 30A Spare
F11 20A Spare
F12 20A Spare
F13 10A Spare
F14 5A Rear parking assistance module (optional)
F15 5A Spare
F16 30A Spare
F17 5A Spare
F18 30A Audio amplifier
F19 5A Spare
F20 10A Canister vent
F21 30A Spare
F22 20A Exhaust by-pass and vacuum pump
Wire numbers have been deleted from the original
engineering circuits. This al lows the type size to be
increased for improved legibil ity of the service circuits.
173 WR 2.0
Wire No.
Colour
Size
908 GU MAPM 05
Wire No.
Colour
MAP (Defines twisted pair)
Size
Page 718 of 947
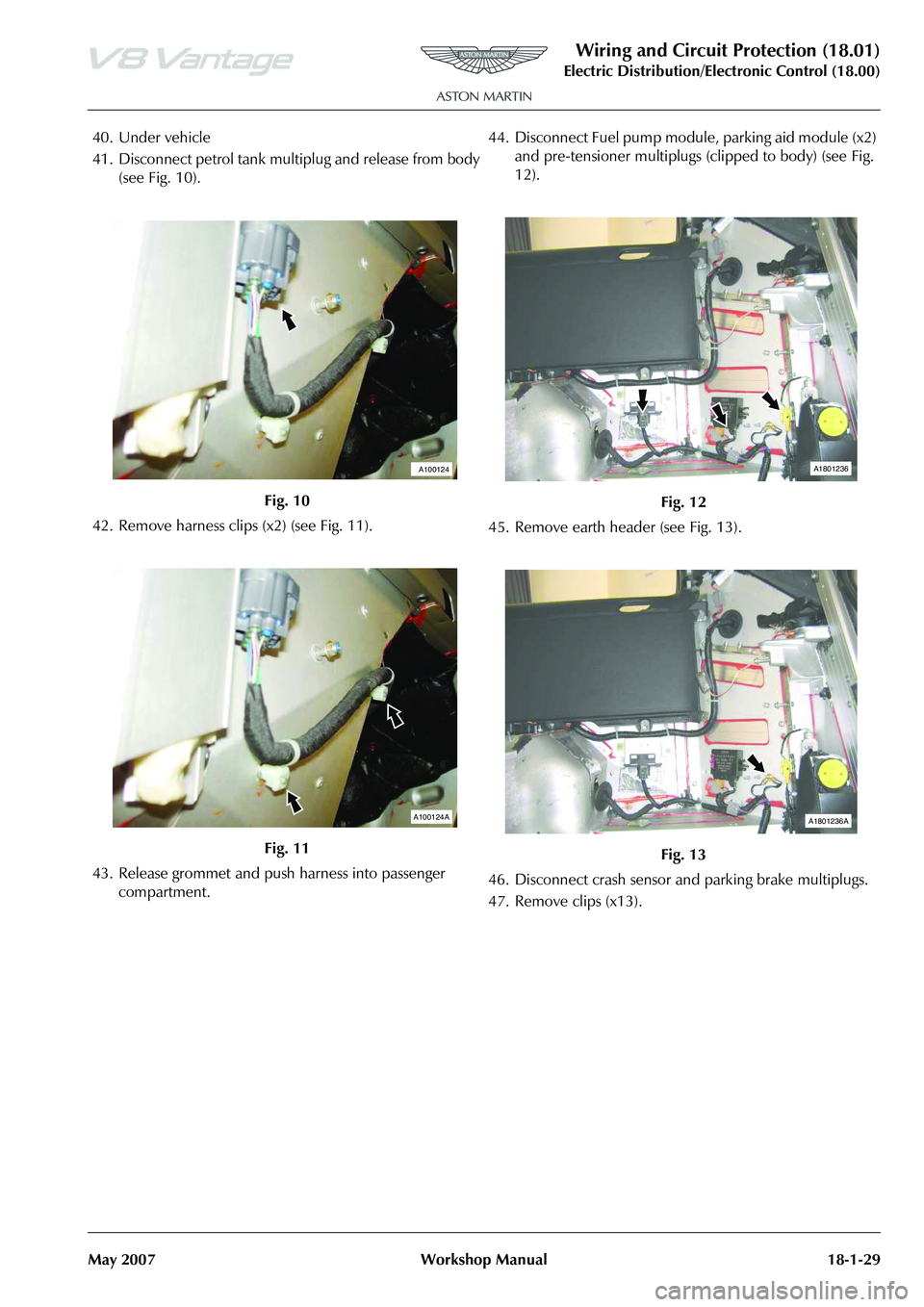
Wiring and Circuit Protection (18.01)
Electric Distribution/Electronic Control (18.00)
May 2007 Workshop Manual 18-1-29
40. Under vehicle
41. Disconnect petrol tank mult iplug and release from body
(see Fig. 10).
42. Remove harness clips (x2) (see Fig. 11).
43. Release grommet and push harness into passenger compartment. 44. Disconnect Fuel pump modu
le, parking aid module (x2)
and pre-tensioner multiplugs (clipped to body) (see Fig.
12).
45. Remove earth header (see Fig. 13).
46. Disconnect crash sensor and parking brake multiplugs.
47. Remove clips (x13).
Fig. 10
Fig. 11
$
$ $
Fig. 12
Fig. 13
$
$ $
Page 724 of 947

Wiring and Circuit Protection (18.01)
Electric Distribution/Electronic Control (18.00)
May 2007 Workshop Manual 18-1-35
11. Connect door harness to main harness multiplug and
secure boot.
12. Connect Crash sensor an d parking brake multiplugs.
13. Connect Fuel pump module, parking aid module (x2) and pre-tensioner multiplugs (clip to body).
14. Install earth header.
15. Install clips (x13).
16. Connect petrol tank multiplug and secure to body
17. Install harness clips (x2).
18. Pull harness from passenger compartment and secure grommet.
19. Connect crash sensor, battery disconnect switch and pre-tensioner multiplugs (clip to body x2).
20. Install battery header.
21. Install earth headers (x2).
22. Secure in-line fuse to body.
23. Secure harness to floor (bolts x4).
24. Install clips (x8).
25. Feed harness into tailgate area and secure grommet (LH).
26. Connect LH tailgate harness multiplug (clip to body).
27. Install LH harness clips (x3).
28. Connect RH tailgate ha rness multiplug (clipped to
body).
29. Feed harness into tailgate area and secure grommet (RH).
30. Install RH harness clips (x4).
31. Install nuts (x7) harness to tunnel.
32. Install earth headers (x2).
33. Connect Airbag module (x2) multiplugs.
34. Install harness clips (x3).
35. Install nuts (x3) harness to tunnel.
36. Install earth headers (x2).
37. Connect Yaw sensor multiplug.
38. Install earth headers (x2).
39. Install nuts (x3) harness to front bulkhead.
40. Install harness clips (x4).
41. Connect fuel filler flap release and interior light
multiplugs.
42. Push rear light harness through body and secure grommet.
43. Install new harness clips (x7).
44. Pull harness from interior, connect Lucar connectors (x2) to AM/FM tuner and clip service loop.
45. Connect GPS (x2) and AM/FM tuner multiplugs.
46. Install bolts (x4) and earth strap for Satellite Navigation mounting plate access.
47. Connect rear bumper harness (x2) and Subframe harness multiplugs (clipped to body x1).
48. Push harness into w/arch area and secure grommet.
49. Install wires to earth headers (x3).
50. Push rear light harness through body and fit grommet. 51. Secure harness to body (x3).
52. Connect Interior light, a
ccessory sockets (x2), battery
disconnect switch, power plug (clipped to body x4).
53. Install new harness clips (x4).
54. Feed harness from cabin th rough bulkhead into under
bonnet area and secure grommet.
55. Connect multiplugs forward harness to main harness (x3) (clip to body).
56. Connect (bolted) multiplug forward harness to main harness (clip to body).
57. Install brake booster (see Workshop Manual procedure 06.07.AB Brake Booster - RHD - Renew
58. Install footrest (bolts x4).
59. Install handbrake lever (bolts x4).
60. Install front floor carpet and a post trim panel.
61. Install multimedia module (see Workshop Manual procedure 19.07.BB Module - Multi Media - Renew).
62. Position LH and RH rear lamp assemblies and connect
multiplugs (x2).
63. Install rubber seals (x3), plain washers (x3), and star washers (x3). Install and tighten nuts (x3).
64. Position fusebox, connect main battery feed, install and torque tighten nut, install terminal cover.
65. Connect multiplugs (x2) and install fusebox in mounting bracket.
66. Install mobility kit.
67. Install tyre sealant bottle.
68. Install power amplifier (see Workshop Manual procedure 15.01.AB Power Amplifier - Renew).
69. Fit rear floor carpet - check procedure
70. Connect multiplug (x1) subwoofer.
71. Install subwoofer (nut x1 and bolt x1).
72. Install seat belt bracket (bolts x4).
73. Install speaker to LH and RH trim moulding (nuts x6).
74. Connect multiplug (x2) LH and RH speaker
75. Feed seatbelt/s through quarter trim moulding.
76. Install quarter trim moulding (bolts x2 and screw x1).
77. Install RH and LH quarter trim middle panel, secure
with clips, Install and tighten screw.
78. Install RH rear wheel arch liner (see Workshop Manual procedure 01.02.JB Wheel Arch Liner - Rear - RH -
Renew).
79. Install central electronic module (see Workshop Manual procedure 18.01.LC Module - Central Electronic -
Renew).
80. Install instrument panel (see Workshop Manual procedure 01.12.AB Instrument Panel - Facia Assembly
- Remove for Access and Refit).
81. Install front header panel (see Workshop Manual procedure 01.05.BB Panel Assembly - Header - Renew).
82. Connect vehicle battery.
Page 731 of 947
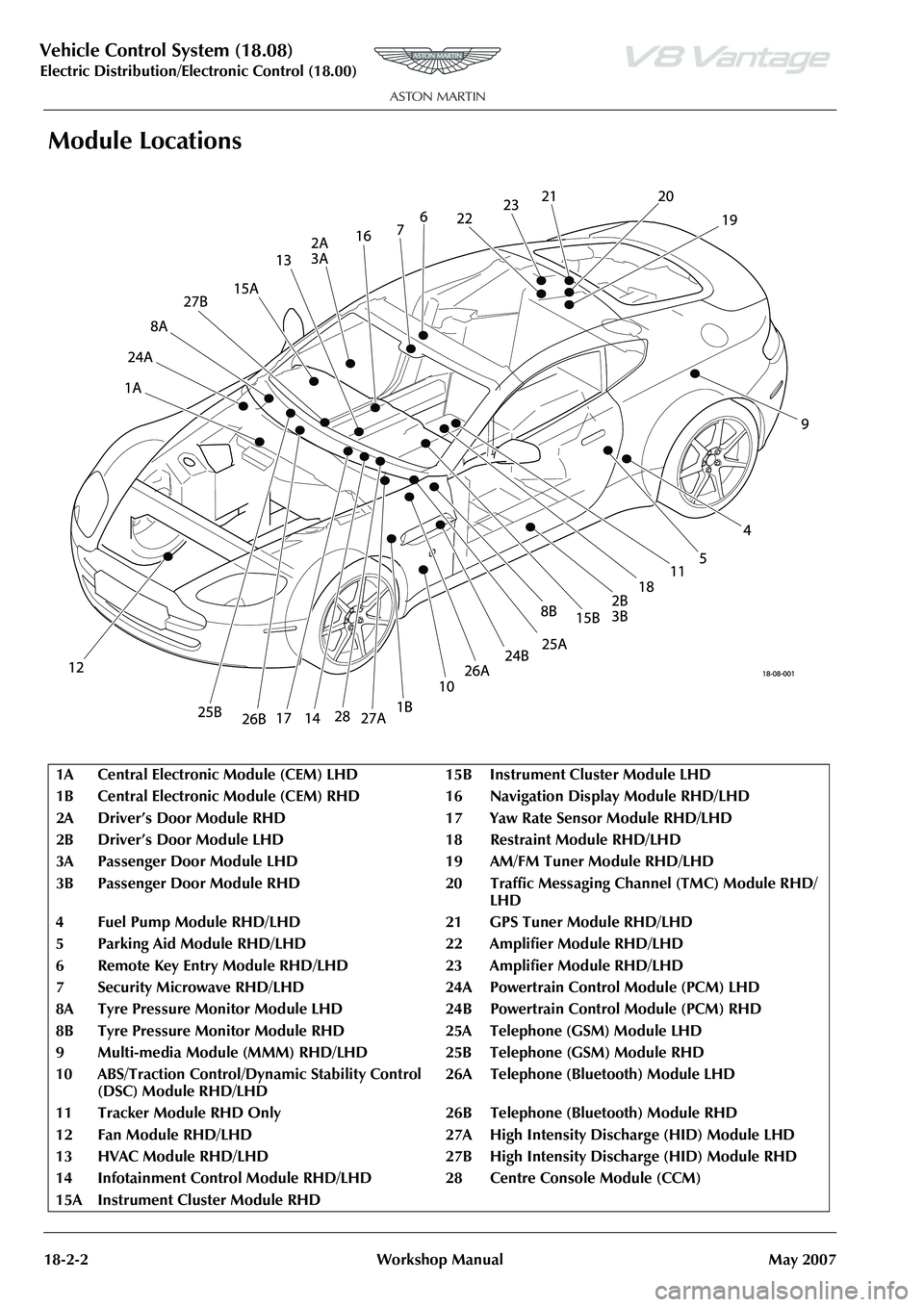
Vehicle Control System (18.08)
Electric Distribution/Electronic Control (18.00)
18-2-2 Workshop Manual May 2007
Module Locations
1A Central Electronic Module (CEM) LH D15BInstrument Cluster Module LHD
1B Central Electronic Module (CEM) RH D 16 Navigation Display Module RHD/LHD
2A Driver’s Door Module RHD 17 Yaw Rate Sensor Module RHD/LHD
2B Driver’s Door Module LHD 1 8Restraint Module RHD/LHD
3A Passenger Door Module LHD 19 AM/FM Tuner Module RHD/LHD
3B Passenger Door Module RHD 20 Traffic Messaging Channel (TMC) Module RHD/
LHD
4 Fuel Pump Module RHD/LHD 21 GPS Tuner Module RHD/LHD
5 Parking Aid Module RHD/LHD 22 Amplifier Module RHD/LHD
6 Remote Key Entry Module RHD/LH D23Amplifier Module RHD/LHD
7 Security Microwave RHD/LHD 24A Powe rtrain Control Module (PCM) LHD
8A Tyre Pressure Monitor Module LHD 24B Powertrain Control Module (PCM) RHD
8B Tyre Pressure Monitor Module RHD 25A Telephone (GSM) Module LHD
9Multi-media Module (MMM) RHD/LHD 25B Teleph one (GSM) Module RHD
10 ABS/Traction Control/Dy namic Stability Control
(DSC) Module RHD/LHD 26A Telephone (Bluetooth) Module LHD
11 Tracker Module RHD Only 26B Tel ephone (Bluetooth) Module RHD
12 Fan Module RHD/LHD 27A High Intensity Discharge (HID) Module LHD
13 HVAC Module RHD/LHD 27B High Intensity Discharge (HID) Module RHD
14 Infotainment Control Module RHD/ LHD 28 Centre Console Module (CCM)
15A Instrument Cluster Module RHD