turn signal ASTON MARTIN V8 VANTAGE 2010 Workshop Manual
[x] Cancel search | Manufacturer: ASTON MARTIN, Model Year: 2010, Model line: V8 VANTAGE, Model: ASTON MARTIN V8 VANTAGE 2010Pages: 947, PDF Size: 43.21 MB
Page 462 of 947
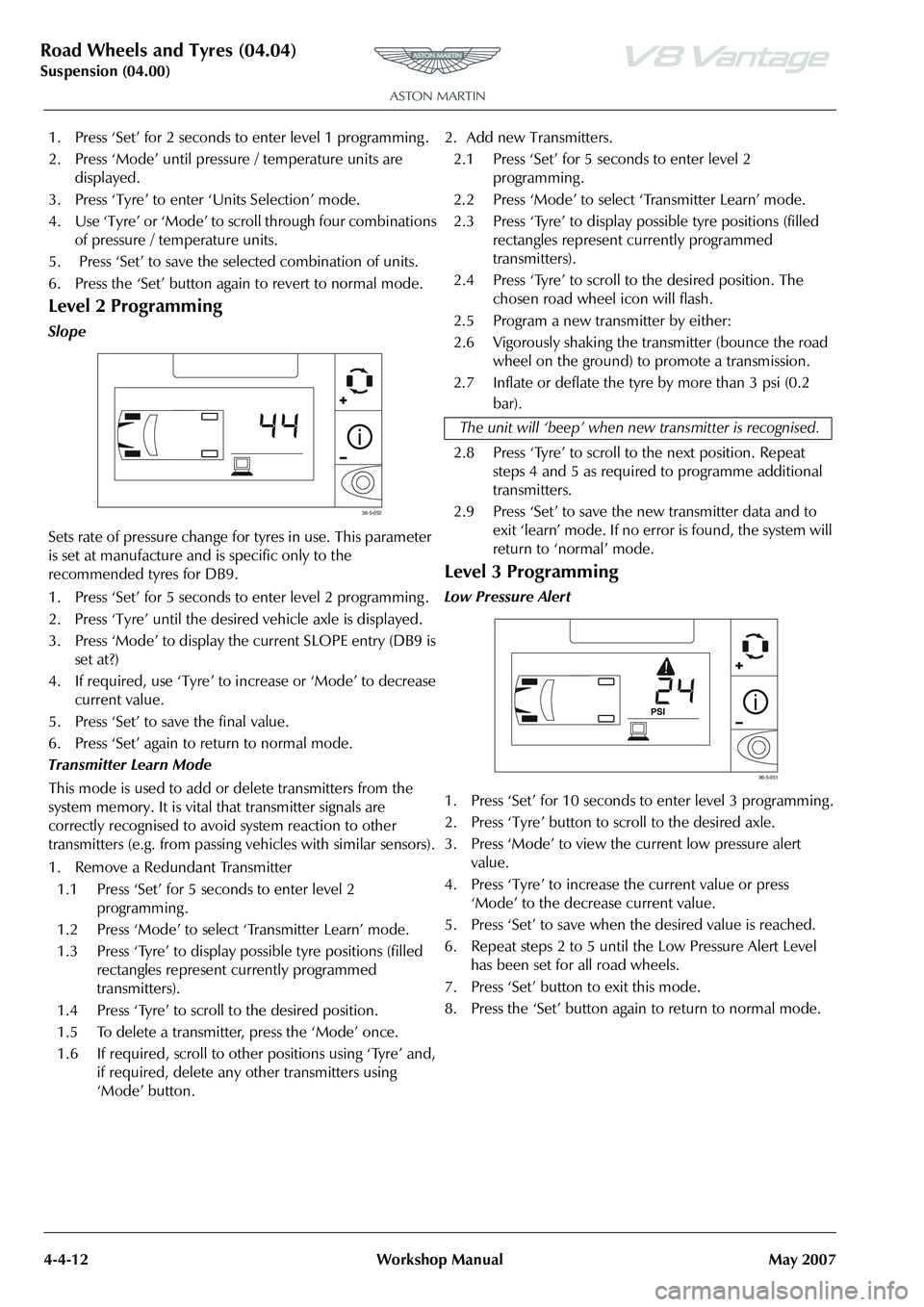
Road Wheels and Tyres (04.04)
Suspension (04.00)4-4-12 Workshop Manual May 2007
1. Press ‘Set’ for 2 seconds to enter level 1 programming .
2. Press ‘Mode’ until pressure / temperature units are displayed.
3. Press ‘Tyre’ to enter ‘Units Selection’ mode.
4. Use ‘Tyre’ or ‘Mode’ to scroll through four combinations of pressure / temperature units.
5. Press ‘Set’ to save the selected combination of units.
6. Press the ‘Set’ button again to revert to normal mode.
Level 2 Programming
Slope
Sets rate of pressure change for tyres in use. This parameter
is set at manufacture and is specific only to the
recommended tyres for DB9.
1. Press ‘Set’ for 5 seconds to enter level 2 programming .
2. Press ‘Tyre’ until the desired vehicle axle is displayed.
3. Press ‘Mode’ to display the current SLOPE entry (DB9 is set at?)
4. If required, use ‘Tyre’ to increase or ‘Mode’ to decrease current value.
5. Press ‘Set’ to save the final value.
6. Press ‘Set’ again to return to normal mode.
Transmitter Learn Mode
This mode is used to add or delete transmitters from the
system memory. It is vital that transmitter signals are
correctly recognised to avoid system reaction to other
transmitters (e.g. from passing vehicles with similar sensors).
1. Remove a Redundant Transmitter 1.1 Press ‘Set’ for 5 seconds to enter level 2 programming .
1.2 Press ‘Mode’ to select ‘Transmitter Learn’ mode.
1.3 Press ‘Tyre’ to display possible tyre positions (filled rectangles represent currently programmed
transmitters).
1.4 Press ‘Tyre’ to scroll to the desired position.
1.5 To delete a transmitter, press the ‘Mode’ once.
1.6 If required, scroll to other positions using ‘Tyre’ and, if required, delete any other transmitters using
‘Mode’ button. 2. Add new Transmitters.
2.1 Press ‘Set’ for 5 seconds to enter level 2 programming .
2.2 Press ‘Mode’ to select ‘Transmitter Learn’ mode.
2.3 Press ‘Tyre’ to display possible tyre positions (filled rectangles represent currently programmed
transmitters).
2.4 Press ‘Tyre’ to scroll to the desired position. The chosen road wheel icon will flash.
2.5 Program a new transmitter by either:
2.6 Vigorously shaking the transmitter (bounce the road wheel on the ground) to promote a transmission.
2.7 Inflate or deflate the tyre by more than 3 psi (0.2 bar).
2.8 Press ‘Tyre’ to scroll to the next position. Repeat steps 4 and 5 as required to programme additional
transmitters.
2.9 Press ‘Set’ to save the new transmitter data and to exit ‘learn’ mode. If no error is found, the system will
return to ‘normal’ mode.
Level 3 Programming
Low Pressure Alert
1. Press ‘Set’ for 10 seconds to enter level 3 programming .
2. Press ‘Tyre’ button to scroll to the desired axle.
3. Press ‘Mode’ to view the current low pressure alert value.
4. Press ‘Tyre’ to increase the current value or press ‘Mode’ to the decrease current value.
5. Press ‘Set’ to save when the desired value is reached.
6. Repeat steps 2 to 5 until the Low Pressure Alert Level has been set for all road wheels.
7. Press ‘Set’ button to exit this mode.
8. Press the ‘Set’ button again to return to normal mode.
36-5-052
The unit will ‘beep’ when ne w transmitter is recognised.
36-5-051
Page 501 of 947
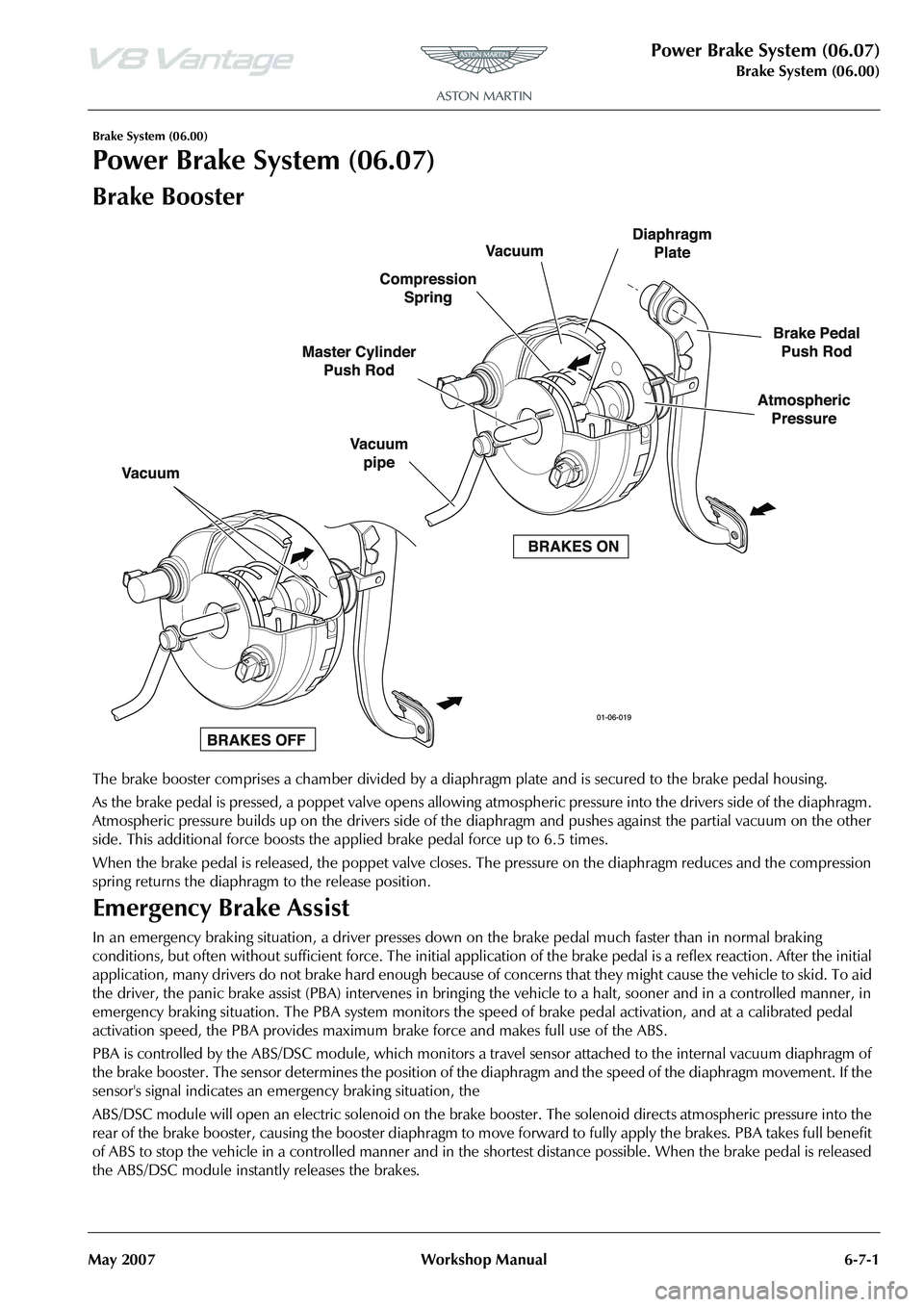
Power Brake System (06.07)
Brake System (06.00)
May 2007 Workshop Manual 6-7-1
Brake System (06.00)
Power Brake System (06.07)
Brake Booster
The brake booster comprises a chamber divided by a diap hragm plate and is secured to the brake pedal housing.
As the brake pedal is pressed, a poppet valve opens allowing at mospheric pressure into the drivers side of the diaphragm.
Atmospheric pressure builds up on the drivers side of the diaphragm and pushes against the partial vacuum on the other
side. This additional force boosts the a pplied brake pedal force up to 6.5 times.
When the brake pedal is released, the poppet valve closes. The pressure on the diaphragm reduces and the compression
spring returns the diaphragm to the release position.
Emergency Brake Assist
In an emergency braking situation, a driver presses down on the brake pedal much faster than in normal braking
conditions, but often without sufficient force. The initial appli cation of the brake pedal is a reflex reaction. After the initial
application, many drivers do not brake ha rd enough because of concerns that they might cause the vehicle to skid. To aid
the driver, the panic brake assist (PBA) intervenes in bringing the vehicle to a halt, sooner and in a controlled manner, in
emergency braking situation. The PBA system monitors the speed of brake pedal activation, and at a calibrated pedal
activation speed, the PBA provides maximum brake force and makes full use of the ABS.
PBA is controlled by the ABS/DSC module, which monitors a travel sensor attached to the internal vacuum diaphragm of
the brake booster. The sensor determines the position of th e diaphragm and the speed of the diaphragm movement. If the
sensor's signal indicates an emergency braking situation, the
ABS/DSC module will open an electric solenoid on the brake booster. The solenoid directs atmospheric pressure into the
rear of the brake booster, causing the booster diaphragm to mo ve forward to fully apply the brakes. PBA takes full benefit
of ABS to stop the vehicle in a controlled manner and in the shortest distance possible. When the brake pedal is released
the ABS/DSC module instantly releases the brakes.
Page 507 of 947
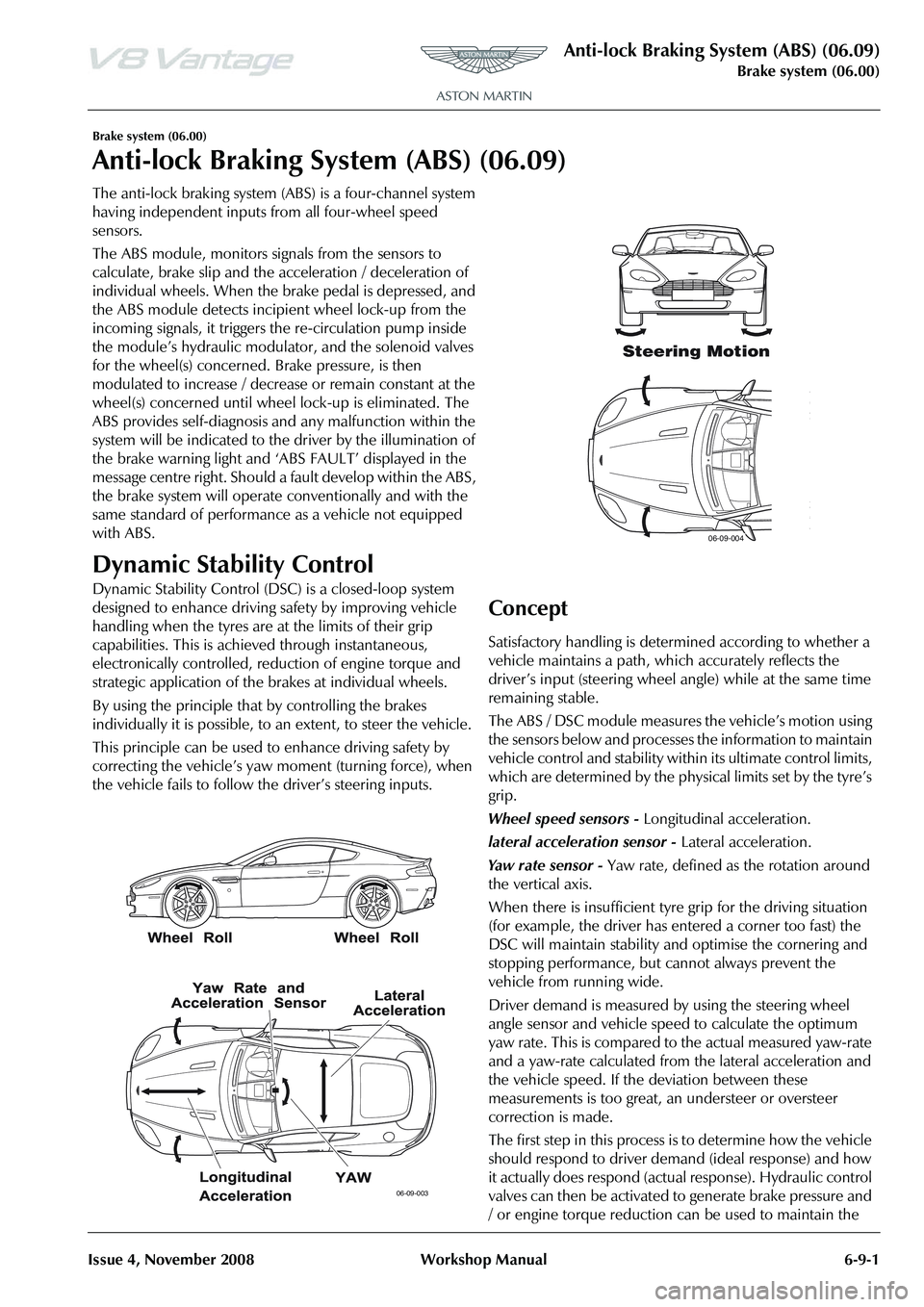
Anti-lock Braking System (ABS) (06.09)
Brake system (06.00)
Issue 4, November 2008 Workshop Manual 6-9-1
Brake system (06.00)
Anti-lock Braking System (ABS) (06.09)
The anti-lock braking system (ABS) is a four-channel system
having independent inputs from all four-wheel speed
sensors.
The ABS module, monitors signals from the sensors to
calculate, brake slip and the acceleration / deceleration of
individual wheels. When the brake pedal is depressed, and
the ABS module detects incipient wheel lock-up from the
incoming signals, it triggers the re-circulation pump inside
the module’s hydraulic modulator, and the solenoid valves
for the wheel(s) concerned. Brake pressure, is then
modulated to increase / decrease or remain constant at the
wheel(s) concerned until whee l lock-up is eliminated. The
ABS provides self-diagnosis and any malfunction within the
system will be indicated to the dr iver by the illumination of
the brake warning light and ‘ABS FAULT’ displayed in the
message centre right. Should a fault develop within the ABS,
the brake system will operate conventionally and with the
same standard of performanc e as a vehicle not equipped
with ABS.
Dynamic Stability Control
Dynamic Stability Control (DSC ) is a closed-loop system
designed to enhance driving safety by improving vehicle
handling when the tyres are at the limits of their grip
capabilities. This is achieved through instantaneous,
electronically controlled, reduction of engine torque and
strategic application of the brakes at individual wheels.
By using the principle that by controlling the brakes
individually it is possible, to an extent, to steer the vehicle.
This principle can be used to enhance driving safety by
correcting the vehicle’s yaw moment (turning force), when
the vehicle fails to follow th e driver’s steering inputs.
Concept
Satisfactory handling is determined according to whether a
vehicle maintains a path, wh ich accurately reflects the
driver
Page 604 of 947
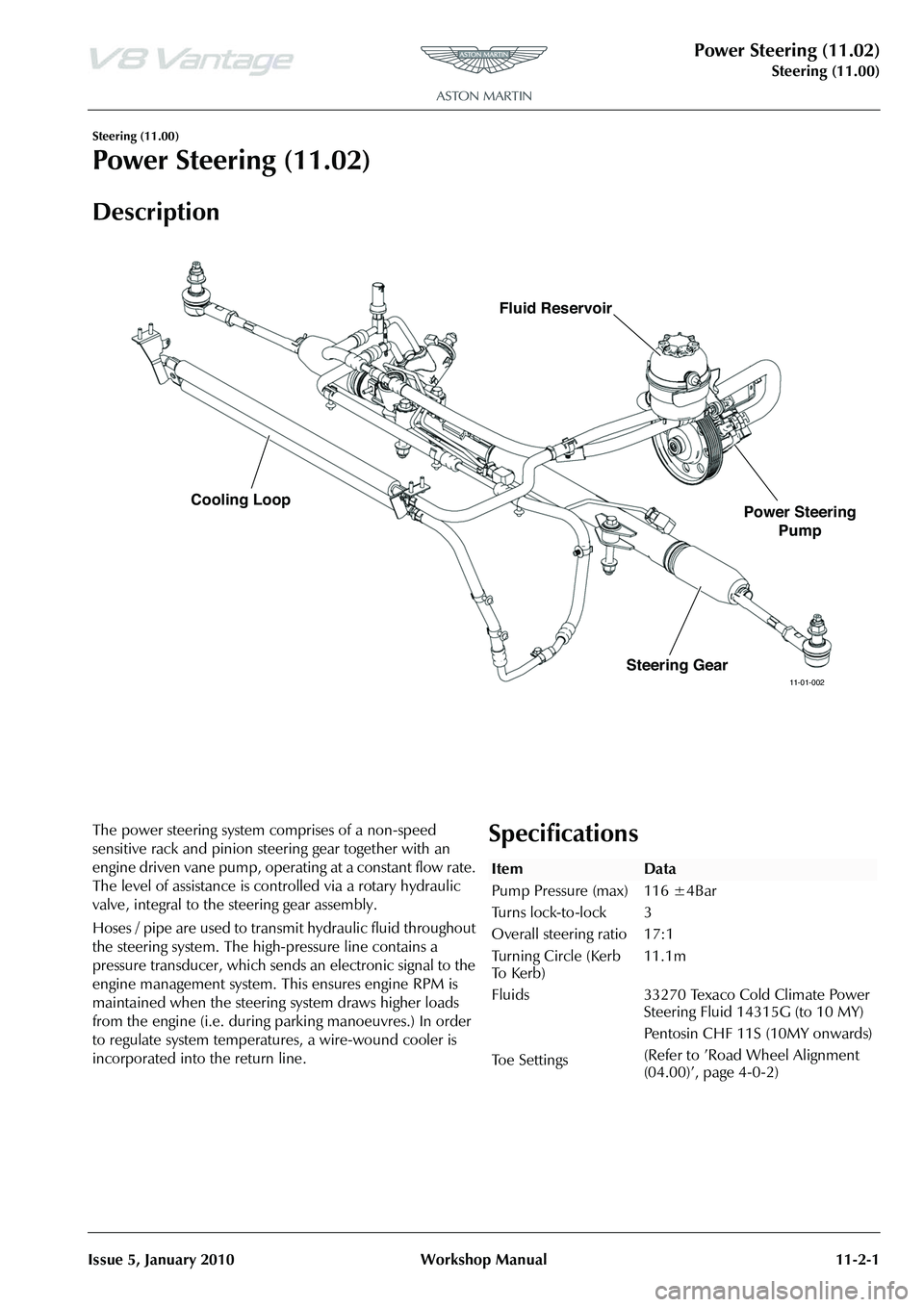
Power Steering (11.02)
Steering (11.00)
Issue 5, January 2010 Workshop Manual 11-2-1
Steering (11.00)
Power Steering (11.02)
Description
The power steering system comprises of a non-speed
sensitive rack and pinion steering gear together with an
engine driven vane pump, operating at a constant flow rate.
The level of assistance is co ntrolled via a rotary hydraulic
valve, integral to the steering gear assembly.
Hoses / pipe are used to transm it hydraulic fluid throughout
the steering system. The high -pressure line contains a
pressure transducer, which sends an electronic signal to the
engine management system. This ensures engine RPM is
maintained when the steering system draws higher loads
from the engine (i.e. during parking manoeuvres.) In order
to regulate system temperatures, a wire-wound cooler is
incorporated into the return line.Specifications
11-01-002Steering Gear
Cooling Loop
Power Steering
Pump
Fluid Reservoir
ItemData
Pump Pressure (max)
Turns lock-to-lock
Overall steering ratio
Turning Circle (Kerb
To K e r b )
Fluids
Toe Settings 116 ±4Bar
3
17:1
11.1m
33270 Texaco Cold Climate Power
Steering Fluid 14315G (to 10 MY)
Pentosin CHF 11S (10MY onwards)
(Refer to ’Road Wheel Alignment
(04.00)
Page 653 of 947
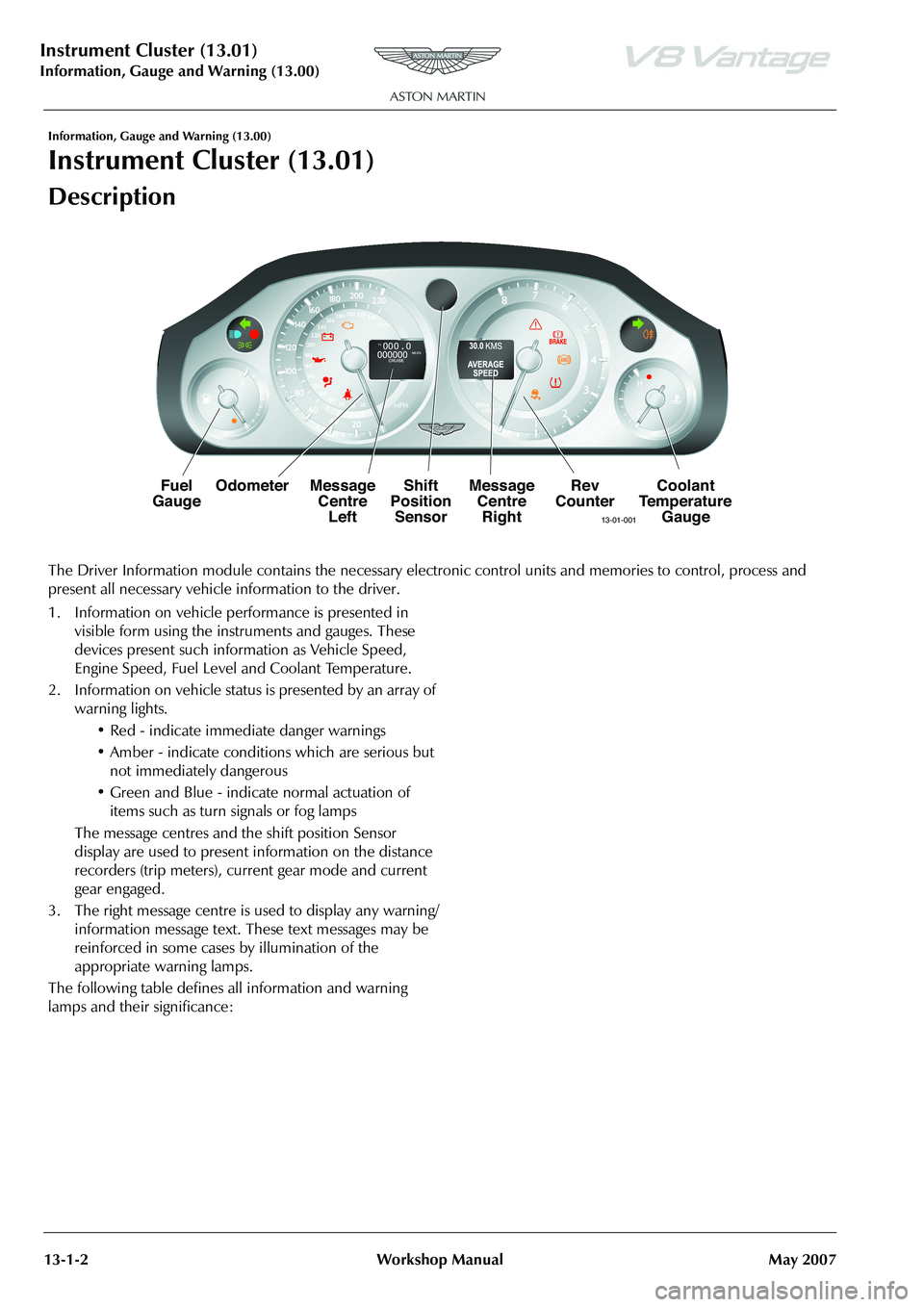
Instrument Cluster (13.01)
Information, Gauge and Warning (13.00)13-1-2 Workshop Manual May 2007
Information, Gauge and Warning (13.00)
Instrument Cluster (13.01)
Description
The Driver Information module contains the necessary electronic control units and memories to control, process and
present all necessary vehicle information to the driver.
1. Information on vehicle performance is presented in visible form using the instruments and gauges. These
devices present such information as Vehicle Speed,
Engine Speed, Fuel Level and Coolant Temperature.
2. Information on vehicle status is presented by an array of warning lights.
• Red - indicate immediate danger warnings
• Amber - indicate conditions which are serious but not immediately dangerous
• Green and Blue - indicate normal actuation of items such as turn signals or fog lamps
The message centres and the shift position Sensor
display are used to present information on the distance
recorders (trip meters), current gear mode and current
gear engaged.
3. The right message centre is used to display any warning/ information message text. These text messages may be
reinforced in some cases by illumination of the
appropriate warning lamps.
The following table defines all information and warning
lamps and their significance:
) X H O
* D X J H 2 G R P H W H U 0 H V V D J H
&