transmission ASTON MARTIN V8 VANTAGE 2010 Workshop Manual
[x] Cancel search | Manufacturer: ASTON MARTIN, Model Year: 2010, Model line: V8 VANTAGE, Model: ASTON MARTIN V8 VANTAGE 2010Pages: 947, PDF Size: 43.21 MB
Page 3 of 947
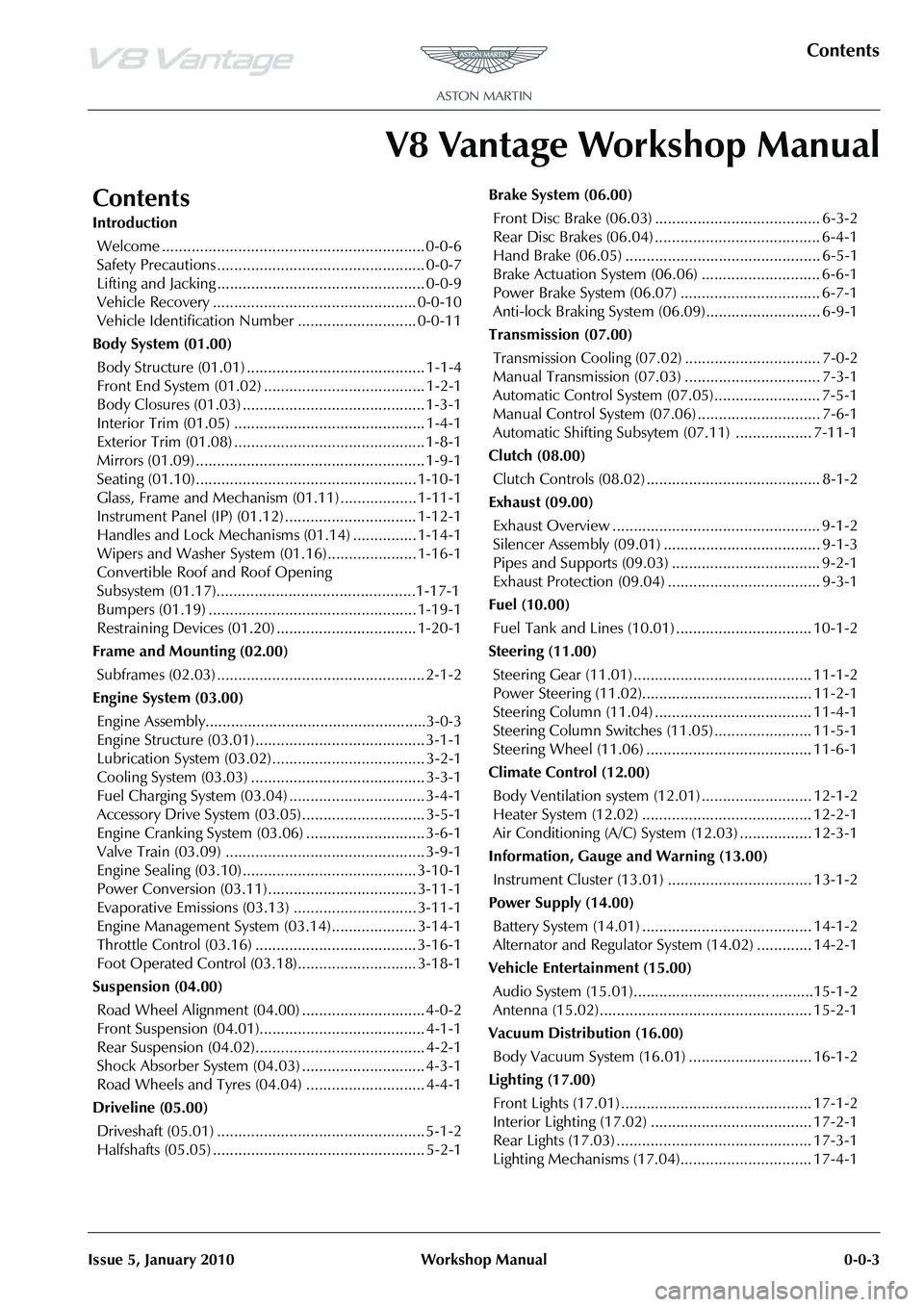
Contents
Issue 5, January 2010 Workshop Manual 0-0-3
V8 Vantage Workshop Manual
Contents
IntroductionWelcome .............................................................. 0-0-6
Safety Precautions ................................................. 0-0-7
Lifting and Jacking ................................................. 0-0-9
Vehicle Recovery ................................................ 0-0-10
Vehicle Identification Number ............................ 0-0-11
Body System (01.00) Body Structure (01.01) .......................................... 1-1-4
Front End System (01.02) ...................................... 1-2-1
Body Closures (01.03) ........................................... 1-3-1
Interior Trim (01.05) ............................................. 1-4-1
Exterior Trim (01.08) ............................................. 1-8-1
Mirrors (01.09) ...................................................... 1-9-1
Seating (01.10).................................................... 1-10-1
Glass, Frame and Mechanism (01.11) .................. 1-11-1
Instrument Panel (IP) (01.12) . .............................. 1-12-1
Handles and Lock Mechanisms (01.14) ............... 1-14-1
Wipers and Washer System (01.16)..................... 1-16-1
Convertible Roof and Roof Opening
Subsystem (01.17)................ ...............................1-17-1
Bumpers (01.19) ................................................. 1-19-1
Restraining Devices (01.20) .... ............................. 1-20-1
Frame and Mounting (02.00) Subframes (02.03) ................................................. 2-1-2
Engine System (03.00) Engine Assembly....................................................3-0-3
Engine Structure (03.01)........................................ 3-1-1
Lubrication System (03.02).................................... 3-2-1
Cooling System (03.03) ......................................... 3-3-1
Fuel Charging System (03.04) ................................ 3-4-1
Accessory Drive System (03.05)............................. 3-5-1
Engine Cranking System (03. 06) ............................ 3-6-1
Valve Train (03.09) ............................................... 3-9-1
Engine Sealing (03.10)......................................... 3-10-1
Power Conversion (03.11)................................... 3-11-1
Evaporative Emissions (03.13) ............................. 3-11-1
Engine Management System (0 3.14).................... 3-14-1
Throttle Control (03.16) ...... ................................ 3-16-1
Foot Operated Control (03.18)............................ 3-18-1
Suspension (04.00) Road Wheel Alignment (04.00) ............................. 4-0-2
Front Suspension (04.01)....................................... 4-1-1
Rear Suspension (04.02)........................................ 4-2-1
Shock Absorber System (04.03) ............................. 4-3-1
Road Wheels and Tyres (04.04) ............................ 4-4-1
Driveline (05.00) Driveshaft (05.01) ................................................. 5-1-2
Halfshafts (05.05) .................................................. 5-2-1 Brake System (06.00)
Front Disc Brake (06.03) ....................................... 6-3-2
Rear Disc Brakes (06.04) ....................................... 6-4-1
Hand Brake (06.05) .............................................. 6-5-1
Brake Actuation System (06.06 ) ............................ 6-6-1
Power Brake System (06.07) ................................. 6-7-1
Anti-lock Braking System (06.09)........................... 6-9-1
Transmission (07.00) Transmission Cooling (07.02) ................................ 7-0-2
Manual Transmission (07.03) ................................ 7-3-1
Automatic Control System (07.05)......................... 7-5-1
Manual Control System (07.06) ............................. 7-6-1
Automatic Shifting Subsytem (07.11) .................. 7-11-1
Clutch (08.00) Clutch Controls (08.02) ......................................... 8-1-2
Exhaust (09.00) Exhaust Overview ................................................. 9-1-2
Silencer Assembly (09.01) ..................................... 9-1-3
Pipes and Supports (09.03) ................................... 9-2-1
Exhaust Protection (09.04) .................................... 9-3-1
Fuel (10.00) Fuel Tank and Lines (10.01) ................................ 10-1-2
Steering (11.00) Steering Gear (11.01) .......................................... 11-1-2
Power Steering (11.02)........................................ 11-2-1
Steering Column (11.04) ..................................... 11-4-1
Steering Column Switches (1 1.05) ....................... 11-5-1
Steering Wheel (11.06) ....................................... 11-6-1
Climate Control (12.00) Body Ventilation system (12.01) .......................... 12-1-2
Heater System (12.02) ........................................ 12-2-1
Air Conditioning (A/C) System (12.03) ................. 12-3-1
Information, Gauge and Warning (13.00) Instrument Cluster (13.01) .................................. 13-1-2
Power Supply (14.00) Battery System (14.01) ........................................ 14-1-2
Alternator and Regulator System (14.02) ............. 14-2-1
Vehicle Entertainment (15.00) Audio System (15.01)................................ ..........15-1-2
Antenna (15.02).................................................. 15-2-1
Vacuum Distribution (16.00) Body Vacuum System (16.01) ............................. 16-1-2
Lighting (17.00) Front Lights (17.01) ............................................. 17-1-2
Interior Lighting (17.02) ...................................... 17-2-1
Rear Lights (17.03) .............................................. 17-3-1
Lighting Mechanisms (17.04). .............................. 17-4-1
Page 6 of 947
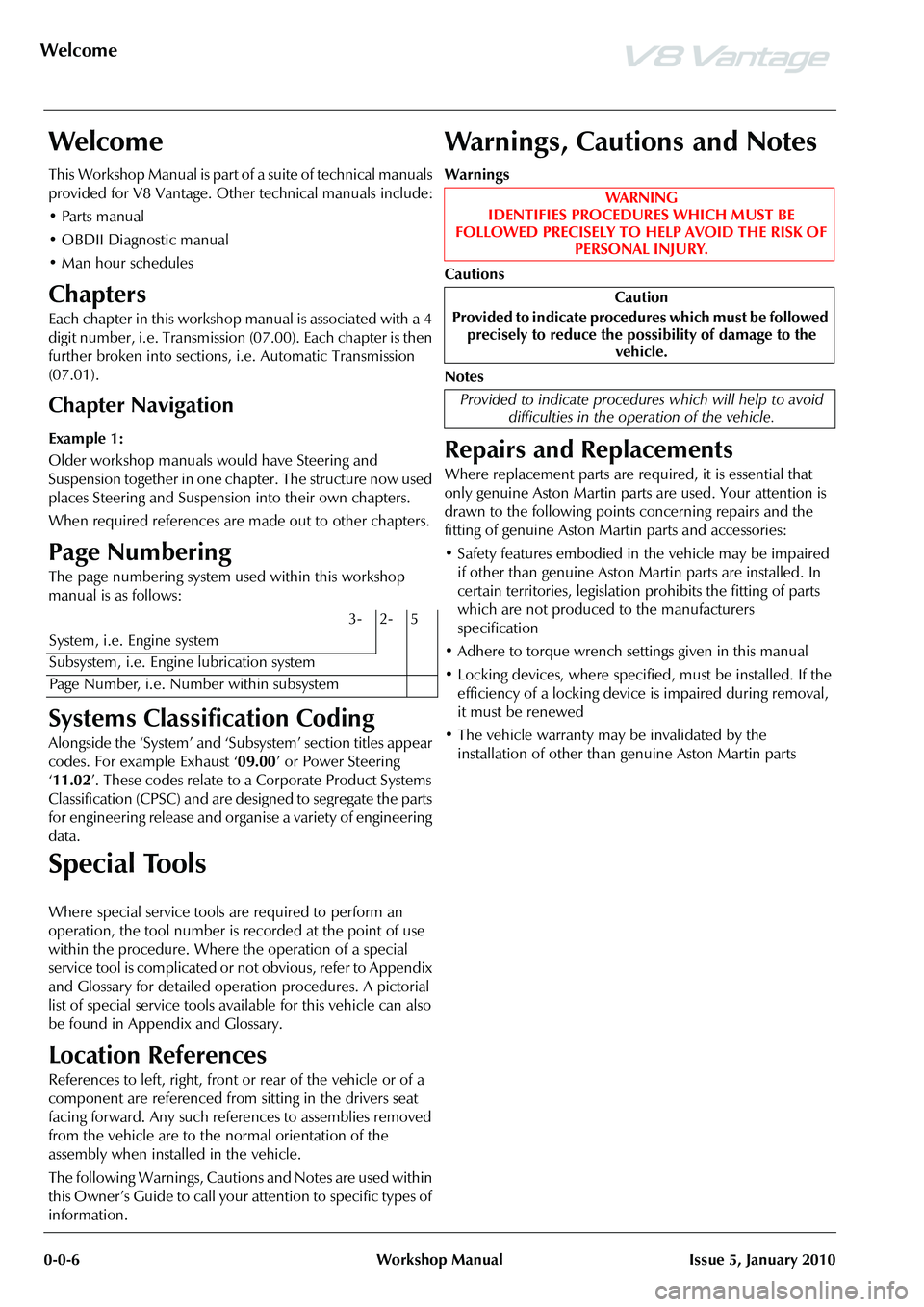
Welcome
0-0-6 Workshop Manual Issue 5, January 2010
Welcome
This Workshop Manual is part of a suite of technical manuals
provided for V8 Vantage. Other technical manuals include:
• Parts manual
• OBDII Diagnostic manual
• Man hour schedules
Chapters
Each chapter in this workshop manual is associated with a 4
digit number, i.e. Transmission (07.00). Each chapter is then
further broken into sections, i.e. Automatic Transmission
(07.01).
Chapter Navigation
Example 1:
Older workshop manuals would have Steering and
Suspension together in one chapter. The structure now used
places Steering and Suspension into their own chapters.
When required references are made out to other chapters.
Page Numbering
The page numbering system used within this workshop
manual is as follows:
Systems Classification Coding
Alongside the ‘System’ and ‘Sub system’ section titles appear
codes. For example Exhaust ‘ 09.00’ or Power Steering
‘ 11.02 ’. These codes relate to a Corporate Product Systems
Classification (CPSC) and are designed to segregate the parts
for engineering release and organise a variety of engineering
data.
Special Tools
Where special service tools are required to perform an
operation, the tool number is recorded at the point of use
within the procedure. Where the operation of a special
service tool is complicated or not obvious, refer to Appendix
and Glossary for detailed operation procedures. A pictorial
list of special service tools available for this vehicle can also
be found in Appendix and Glossary.
Location References
References to left, right, front or rear of the vehicle or of a
component are referenced from sitting in the drivers seat
facing forward. Any such refe rences to assemblies removed
from the vehicle are to the normal orientation of the
assembly when installed in the vehicle.
The following Warnings, Cautions and Notes are used within
this Owner’s Guide to call your attention to specific types of
information.
Warnings, Cautions and Notes
Warnings
Cautions
Notes
Repairs and Replacements
Where replacement parts are required, it is essential that
only genuine Aston Martin parts are used. Your attention is
drawn to the following points concerning repairs and the
fitting of genuine Aston Martin parts and accessories:
• Safety features embodied in the vehicle may be impaired if other than genuine Aston Martin parts are installed. In
certain territories, legislation prohibits the fitting of parts
which are not produced to the manufacturers
specification
• Adhere to torque wrench settings given in this manual
• Locking devices, where specified, must be installed. If the efficiency of a locking device is impaired during removal,
it must be renewed
• The vehicle warranty may be invalidated by the installation of other than genuine Aston Martin parts
3- 2- 5
System, i.e. Engine system
Subsystem, i.e. Engine lubrication system
Page Number, i.e. Number within subsystem
WAR NI NG
IDENTIFIES PROCEDURES WHICH MUST BE
FOLLOWED PRECISELY TO HELP AVOID THE RISK OF PERSONAL INJURY.
Caution
Provided to indicate procedur es which must be followed
precisely to reduce the possibility of damage to the vehicle.
Provided to indicate procedur es which will help to avoid
difficulties in the oper ation of the vehicle.
Page 11 of 947
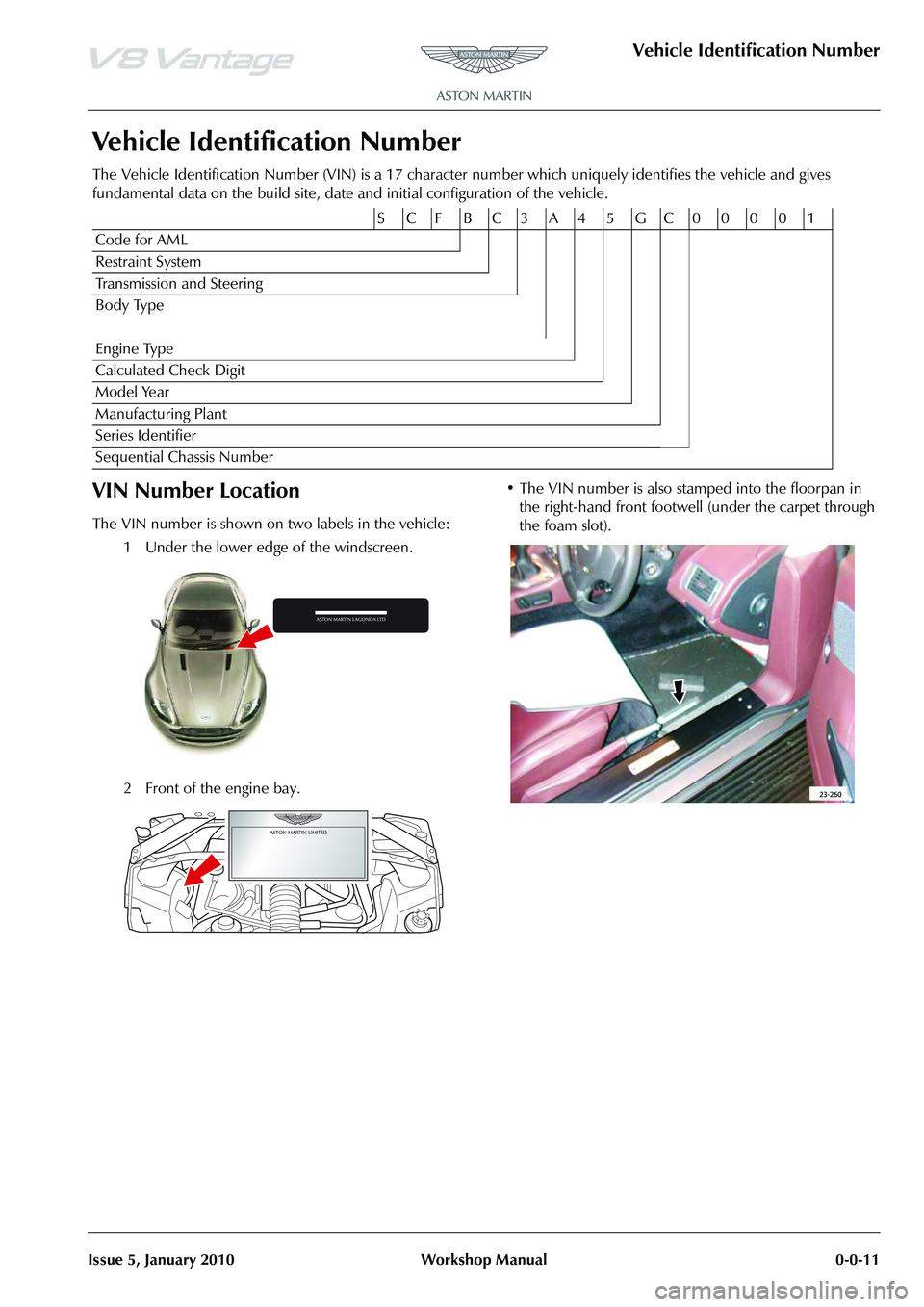
Vehicle Identification Number
Issue 5, January 2010 Workshop Manual 0-0-11
Vehicle Identification Number
The Vehicle Identification Number (VIN) is a 17 character number which uniquely identifies the vehicle and gives
fundamental data on the build site, date and initial configuration of the vehicle.
VIN Number Location
The VIN number is shown on two labels in the vehicle:
1 Under the lower edge of the windscreen.
2 Front of the engine bay. • The VIN number is also stamped into the floorpan in
the right-hand front footwell (under the carpet through
the foam slot).
S CFBC3A45GC00001
Code for AML
Restraint System
Transmission and Steering
Body Type
Engine Type
Calculated Check Digit
Model Year
Manufacturing Plant
Series Identifier
Sequential Chassis Number
Page 223 of 947
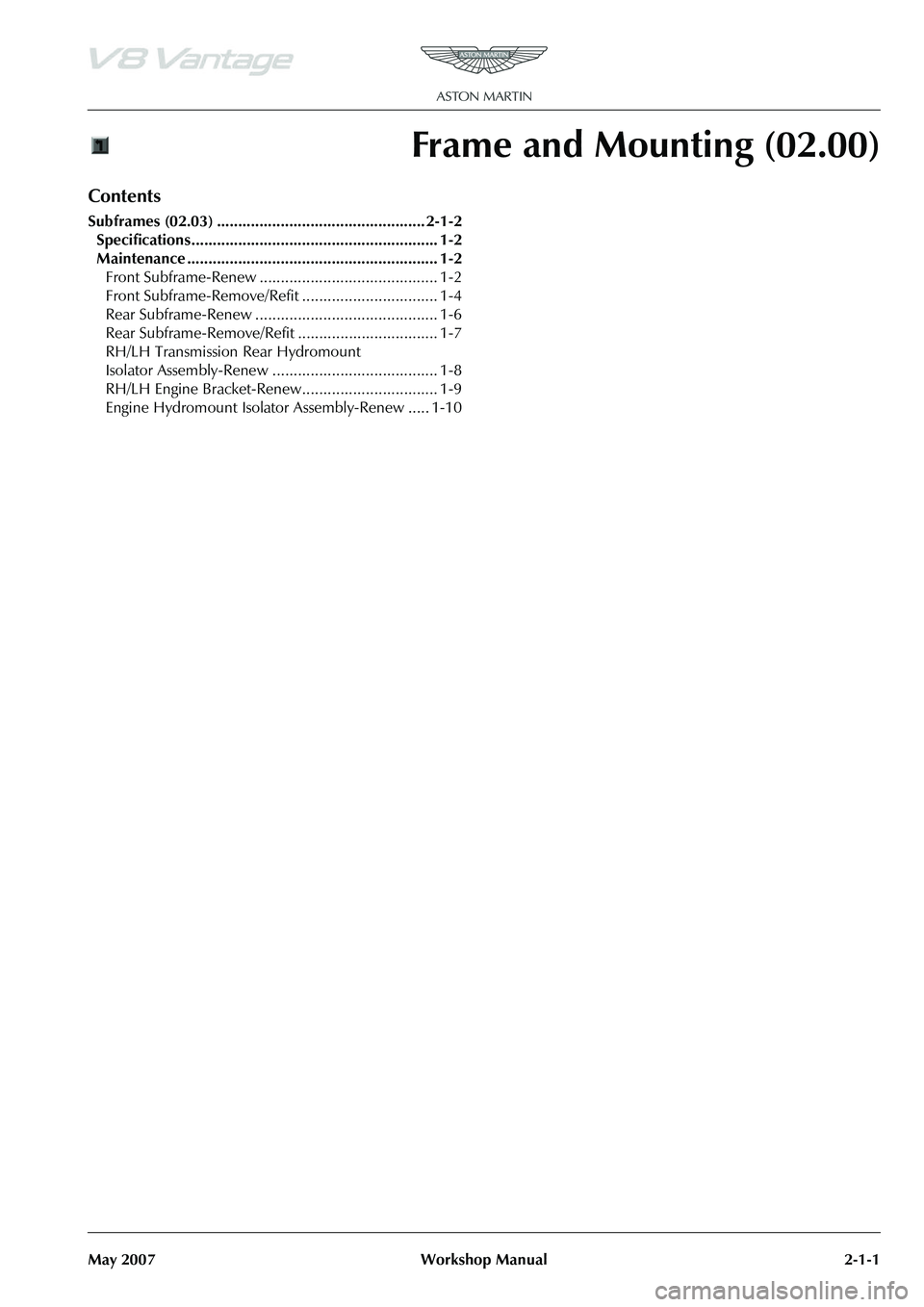
May 2007 Workshop Manual 2-1-1
Frame and Mounting (02.00)
Contents
Subframes (02.03) ................................................. 2-1-2Specifications.......................................................... 1-2
Maintenance ........................................................... 1-2 Front Subframe-Renew .......................................... 1-2
Front Subframe-Remove/Refit ................................ 1-4
Rear Subframe-Renew ........................................... 1-6
Rear Subframe-Remove/Refit ................................. 1-7
RH/LH Transmission Rear Hydromount
Isolator Assembly-Renew ....................................... 1-8
RH/LH Engine Bracket-Renew................................ 1-9
Engine Hydromount Isolator Assembly-Renew ..... 1-10
Page 230 of 947
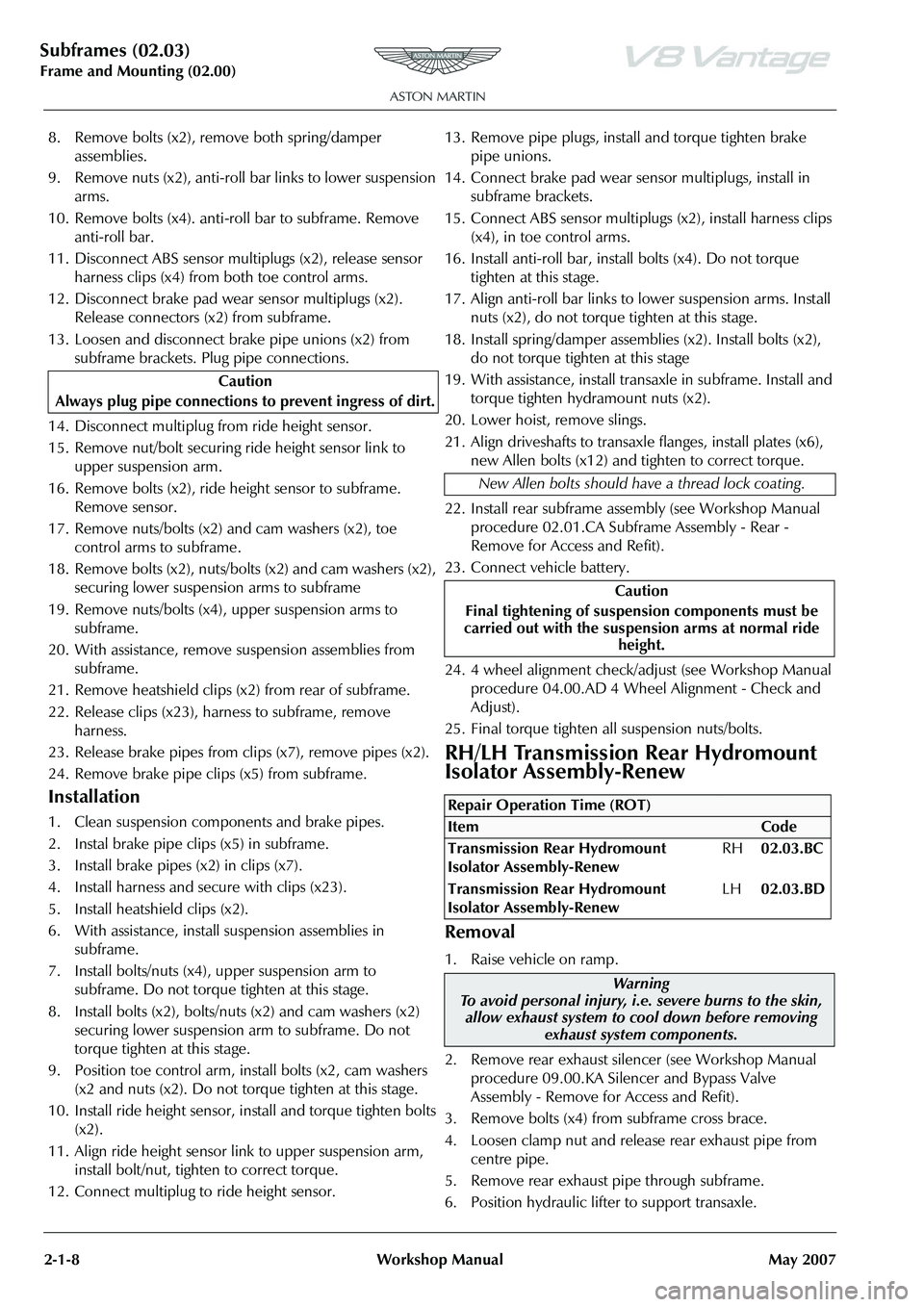
Subframes (02.03)
Frame and Mounting (02.00)
2-1-8 Workshop Manual May 2007
8. Remove bolts (x2), remove both spring/damper assemblies.
9. Remove nuts (x2), anti-roll bar links to lower suspension
arms.
10. Remove bolts (x4). anti-roll bar to subframe. Remove anti-roll bar.
11. Disconnect ABS sensor mult iplugs (x2), release sensor
harness clips (x4) from both toe control arms.
12. Disconnect brake pad wear sensor multiplugs (x2). Release connectors (x2) from subframe.
13. Loosen and disconnect brake pipe unions (x2) from subframe brackets. Pl ug pipe connections.
14. Disconnect multiplug fr om ride height sensor.
15. Remove nut/bolt securing ride height sensor link to
upper suspension arm.
16. Remove bolts (x2), ride height sensor to subframe. Remove sensor.
17. Remove nuts/bolts (x2) and cam washers (x2), toe control arms to subframe.
18. Remove bolts (x2), nuts/bolts (x2) and cam washers (x2),
securing lower suspension arms to subframe
19. Remove nuts/bolts (x4), upper suspension arms to subframe.
20. With assistance, remove suspension assemblies from subframe.
21. Remove heatshield clips (x2) from rear of subframe.
22. Release clips (x23), ha rness to subframe, remove
harness.
23. Release brake pipes from cl ips (x7), remove pipes (x2).
24. Remove brake pipe clips (x5) from subframe.
Installation
1. Clean suspension components and brake pipes.
2. Instal brake pipe clips (x5) in subframe.
3. Install brake pipes (x2) in clips (x7).
4. Install harness and secure with clips (x23).
5. Install heatshield clips (x2).
6. With assistance, install suspension assemblies in subframe.
7. Install bolts/nuts (x4), upper suspension arm to subframe. Do not torque tighten at this stage.
8. Install bolts (x2), bolts/nuts (x2) and cam washers (x2) securing lower suspension arm to subframe. Do not
torque tighten at this stage.
9. Position toe control arm, install bolts (x2, cam washers (x2 and nuts (x2). Do not torque tighten at this stage.
10. Install ride height sensor, in stall and torque tighten bolts
(x2).
11. Align ride height sensor li nk to upper suspension arm,
install bolt/nut, tighten to correct torque.
12. Connect multiplug to ride height sensor. 13. Remove pipe plugs, install and torque tighten brake
pipe unions.
14. Connect brake pad wear sensor multiplugs, install in subframe brackets.
15. Connect ABS sensor multiplugs (x2), install harness clips (x4), in toe control arms.
16. Install anti-roll bar, install bolts (x4). Do not torque tighten at this stage.
17. Align anti-roll bar links to lower suspension arms. Install nuts (x2), do not torque tighten at this stage.
18. Install spring/damper assemblies (x2). Install bolts (x2), do not torque tighten at this stage
19. With assistance, install transaxle in subframe. Install and torque tighten hydramount nuts (x2).
20. Lower hoist, remove slings.
21. Align driveshafts to transaxle flanges, install plates (x6), new Allen bolts (x12) and tighten to correct torque.
22. Install rear subframe asse mbly (see Workshop Manual
procedure 02.01.CA Subframe Assembly - Rear -
Remove for Access and Refit).
23. Connect vehicle battery.
24. 4 wheel alignment check/adjust (see Workshop Manual procedure 04.00.AD 4 Wheel Alignment - Check and
Adjust).
25. Final torque tighten all suspension nuts/bolts.
RH/LH Transmission Rear Hydromount
Isolator Assembly-Renew
Removal
1. Raise vehicle on ramp.
2. Remove rear exhaust silenc er (see Workshop Manual
procedure 09.00.KA Silencer and Bypass Valve
Assembly - Remove for Access and Refit).
3. Remove bolts (x4) from subframe cross brace.
4. Loosen clamp nut and release rear exhaust pipe from centre pipe.
5. Remove rear exhaust pipe through subframe.
6. Position hydraulic lift er to support transaxle.
Caution
Always plug pipe connections to prevent ingress of dirt.
New Allen bolts should have a thread lock coating.
Caution
Final tightening of suspension components must be
carried out with the suspensi on arms at normal ride
height.
Repair Operation Time (ROT)
ItemCode
Transmission Rear Hydromount
Isolator Assembly-Renew RH
02.03.BC
Transmission Rear Hydromount
Isolator Assembly-Renew LH
02.03.BD
Warning
To avoid personal injury, i.e. severe burns to the skin, allow exhaust system to cool down before removing
exhaust system components.
Page 237 of 947
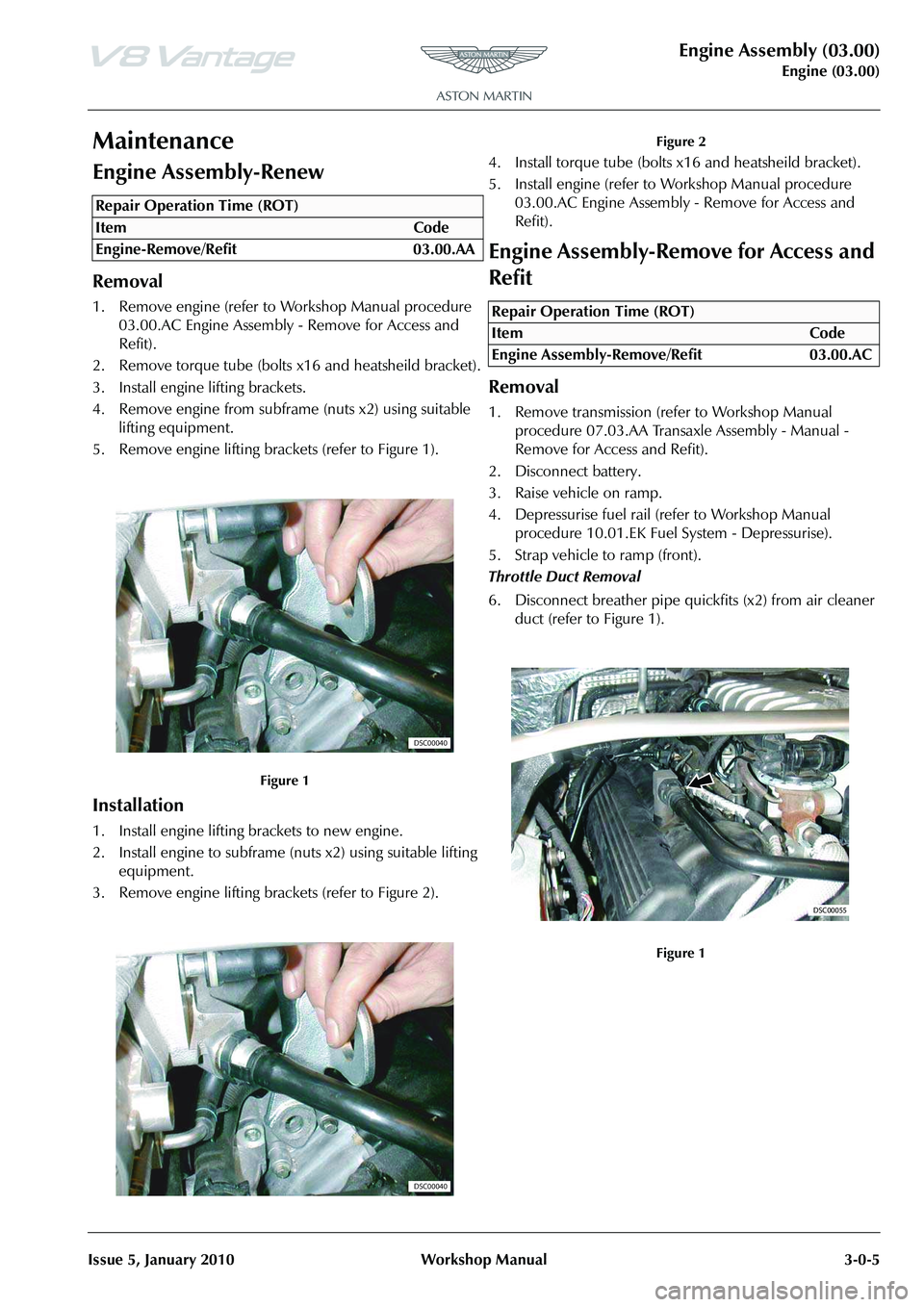
Engine Assembly (03.00)
Engine (03.00)
Issue 5, January 2010 Workshop Manual 3-0-5
Maintenance
Engine Assembly-Renew
Removal
1. Remove engine (refer to Workshop Manual procedure 03.00.AC Engine Assembly - Remove for Access and
Refit).
2. Remove torque tube (bolts x16 and heatsheild bracket).
3. Install engine lifting brackets.
4. Remove engine from subframe (nuts x2) using suitable lifting equipment.
5. Remove engine lifting brack ets (refer to Figure 1).
Installation
1. Install engine lifting brackets to new engine.
2. Install engine to subframe (nuts x2) using suitable lifting
equipment.
3. Remove engine lifting brack ets (refer to Figure 2).4. Install torque tube (bolts x16 and heatsheild bracket).
5. Install engine (refer to Workshop Manual procedure
03.00.AC Engine Assembly - Remove for Access and
Refit).
Engine Assembly-Remove for Access and
Refit
Removal
1. Remove transmission (refer to Workshop Manual procedure 07.03.AA Transaxle Assembly - Manual -
Remove for Access and Refit).
2. Disconnect battery.
3. Raise vehicle on ramp.
4. Depressurise fuel rail (refer to Workshop Manual procedure 10.01.EK Fuel System - Depressurise).
5. Strap vehicle to ramp (front).
Throttle Duct Removal
6. Disconnect breather pipe qu ickfits (x2) from air cleaner
duct (refer to Figure 1).
Repair Operation Time (ROT)
$ 3 #
$ 3 #
Figure 2
Repair Operation Time (ROT)
$ 3 #
Page 242 of 947
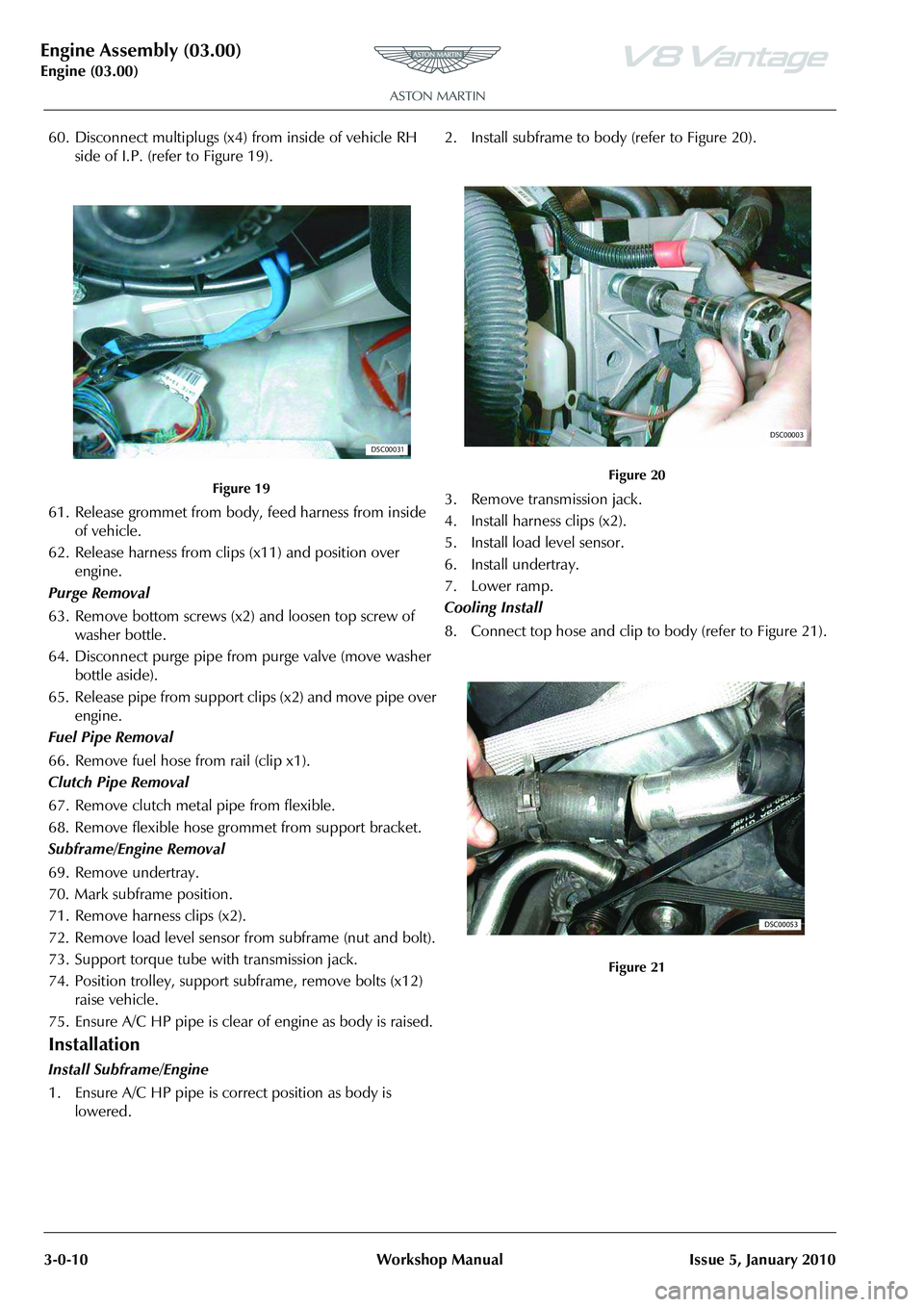
Engine Assembly (03.00)
Engine (03.00)3-0-10 Workshop Manual Issue 5, January 2010
60. Disconnect multiplugs (x4) from inside of vehicle RH side of I.P. (refer to Figure 19).
61. Release grommet from body, feed harness from inside of vehicle.
62. Release harness from clips (x11) and position over engine.
Purge Removal
63. Remove bottom screws (x2) and loosen top screw of washer bottle.
64. Disconnect purge pipe from purge valve (move washer
bottle aside).
65. Release pipe from support clips (x2) and move pipe over engine.
Fuel Pipe Removal
66. Remove fuel hose from rail (clip x1).
Clutch Pipe Removal
67. Remove clutch metal pipe from flexible.
68. Remove flexible hose grommet from support bracket.
Subframe/Engine Removal
69. Remove undertray.
70. Mark subframe position.
71. Remove harness clips (x2).
72. Remove load level sensor from subframe (nut and bolt).
73. Support torque tube with transmission jack.
74. Position trolley, support subframe, remove bolts (x12)
raise vehicle.
75. Ensure A/C HP pipe is clear of engine as body is raised.
Installation
Install Subframe/Engine
1. Ensure A/C HP pipe is co rrect position as body is
lowered. 2. Install subframe to body (refer to Figure 20).
3. Remove transmission jack.
4. Install harness clips (x2).
5. Install load level sensor.
6. Install undertray.
7. Lower ramp.
Cooling Install
8. Connect top hose and clip to body (refer to Figure 21).
Figure 19
$ 3 #
Figure 20
Figure 21
$ 3 #
$ 3 #
Page 247 of 947
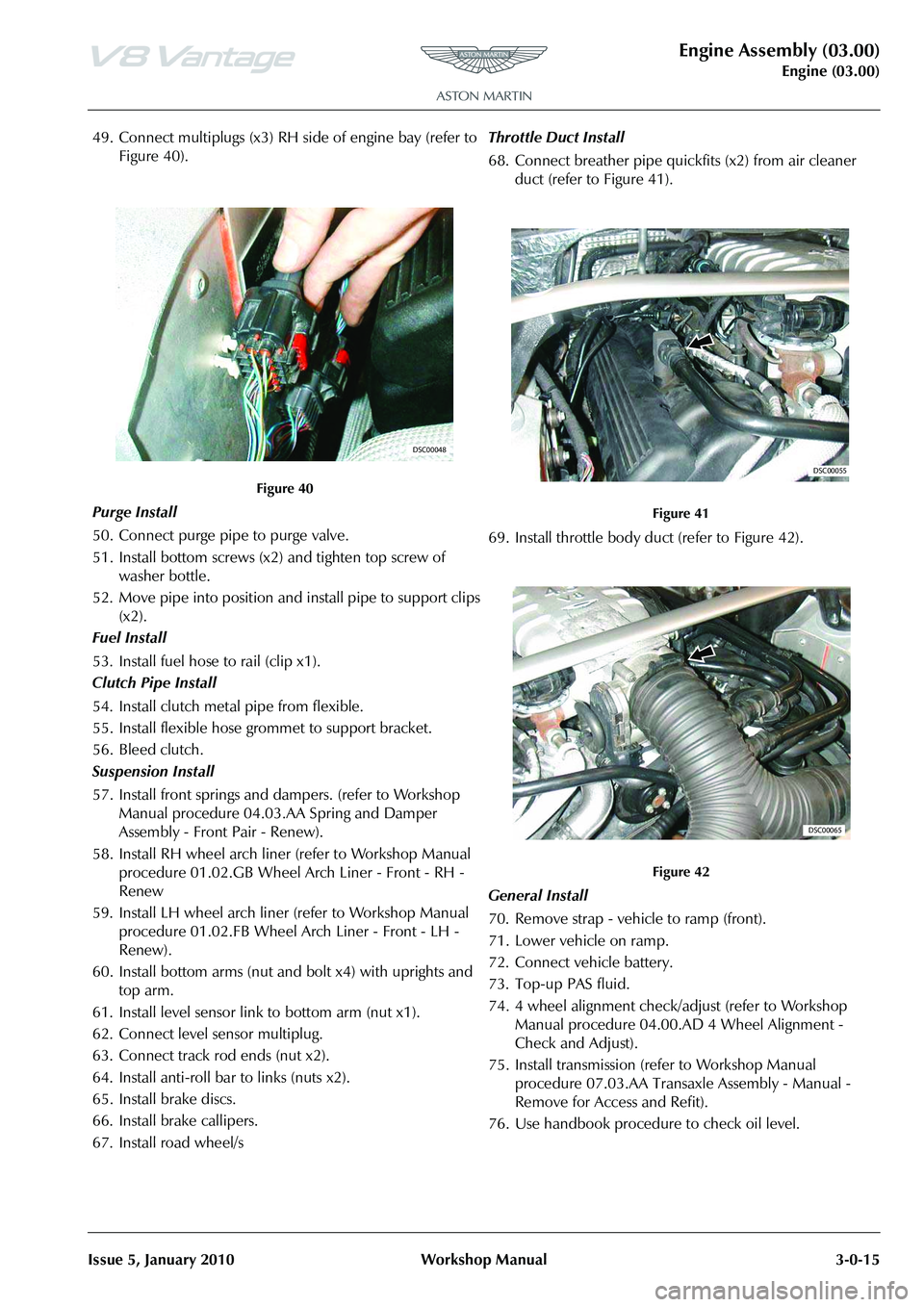
Engine Assembly (03.00)
Engine (03.00)
Issue 5, January 2010 Workshop Manual 3-0-15
49. Connect multiplugs (x3) RH side of engine bay (refer to Figure 40).
Purge Install
50. Connect purge pipe to purge valve.
51. Install bottom screws (x2) and tighten top screw of washer bottle.
52. Move pipe into position and install pipe to support clips (x2).
Fuel Install
53. Install fuel hose to rail (clip x1).
Clutch Pipe Install
54. Install clutch metal pipe from flexible.
55. Install flexible hose grommet to support bracket.
56. Bleed clutch.
Suspension Install
57. Install front springs and dampers. (refer to Workshop Manual procedure 04.03.AA Spring and Damper
Assembly - Front Pair - Renew).
58. Install RH wheel arch liner (refer to Workshop Manual procedure 01.02.GB Wheel Arch Liner - Front - RH -
Renew
59. Install LH wheel arch liner (refer to Workshop Manual procedure 01.02.FB Wheel Arch Liner - Front - LH -
Renew).
60. Install bottom arms (nut and bolt x4) with uprights and top arm.
61. Install level sens or link to bottom arm (nut x1).
62. Connect level sensor multiplug.
63. Connect track rod ends (nut x2).
64. Install anti-roll bar to links (nuts x2).
65. Install brake discs.
66. Install brake callipers.
67. Install road wheel/s Throttle Duct Install
68. Connect breather pipe quic
kfits (x2) from air cleaner
duct (refer to Figure 41).
69. Install throttle body duct (refer to Figure 42).
General Install
70. Remove strap - vehicle to ramp (front).
71. Lower vehicle on ramp.
72. Connect vehicle battery.
73. Top-up PAS fluid.
74. 4 wheel alignment check/adjust (refer to Workshop Manual procedure 04.00.AD 4 Wheel Alignment -
Check and Adjust).
75. Install transmission (refer to Workshop Manual procedure 07.03.AA Transaxle Assembly - Manual -
Remove for Access and Refit).
76. Use handbook procedure to check oil level.
Figure 40
$ 3 #
Figure 41
Figure 42
$ 3 #
$ 3 #
Page 453 of 947
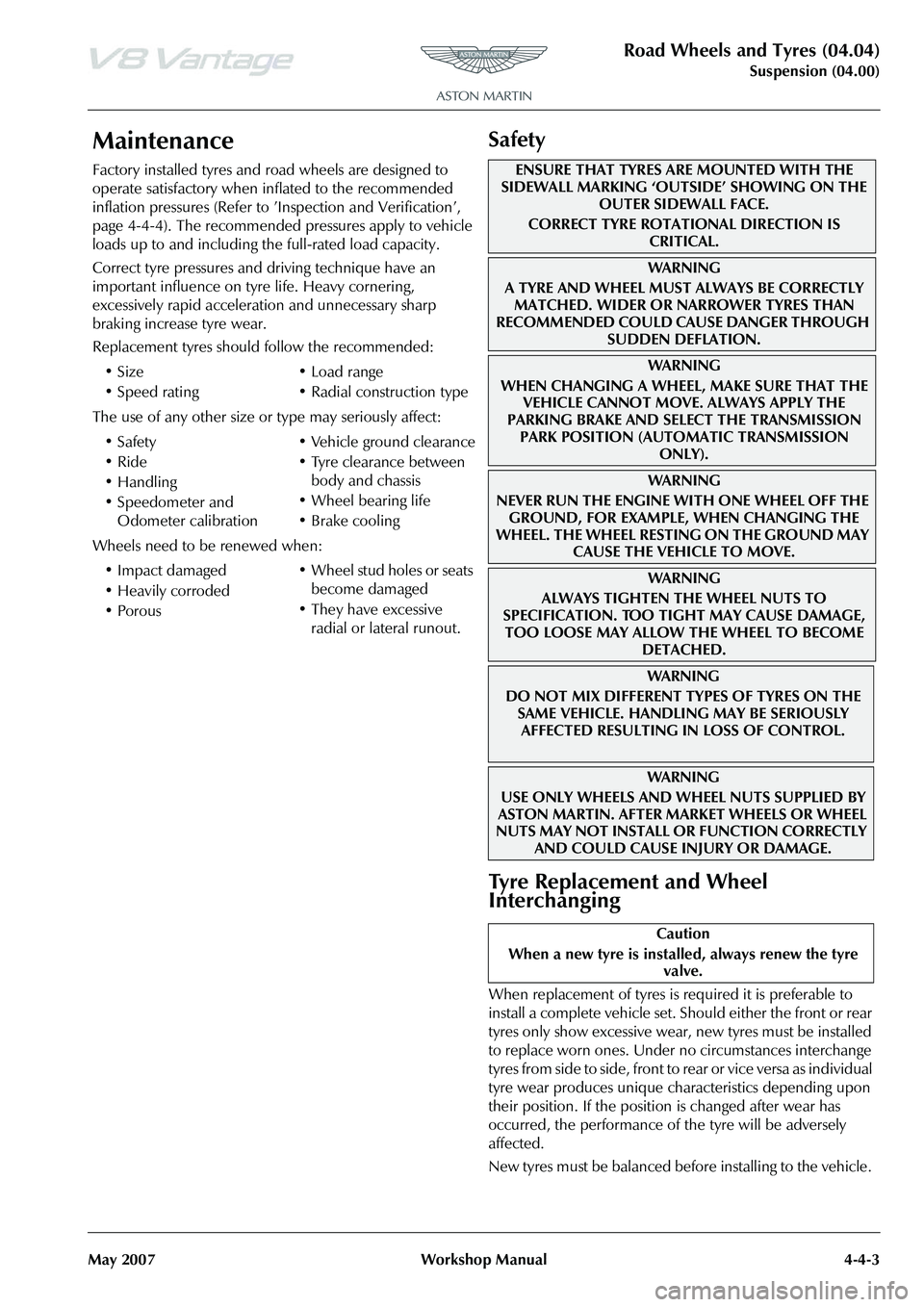
Road Wheels and Tyres (04.04)
Suspension (04.00)
May 2007 Workshop Manual 4-4-3
Maintenance
Factory installed tyres and road wheels are designed to
operate satisfactory when inflated to the recommended
inflation pressures (Refer to ’Inspection and Verification’,
page 4-4-4). The recommended pressures apply to vehicle
loads up to and including the full-rated load capacity.
Correct tyre pressures and driving technique have an
important influence on tyre life. Heavy cornering,
excessively rapid acceleration and unnecessary sharp
braking increase tyre wear.
Replacement tyres should follow the recommended:
The use of any other size or type may seriously affect:
Wheels need to be renewed when:
Safety
Tyre Replacement and Wheel
Interchanging
When replacement of tyres is required it is preferable to
install a complete vehicle set. S hould either the front or rear
tyres only show excessive wear, new tyres must be installed
to replace worn ones. Under no circumstances interchange
tyres from side to side, front to re ar or vice versa as individual
tyre wear produces unique characteristics depending upon
their position. If the position is changed after wear has
occurred, the performance of the tyre will be adversely
affected.
New tyres must be balanced before installing to the vehicle.
•Size
•Speed rating
•Load range
• Radial construction type
•Safety
•Ride
•Handling
• Speedometer and Odometer calibration • Vehicle ground clearance
• Tyre clearance between
body and chassis
• Wheel bearing life
• Brake cooling
• Impact damaged
• Heavily corroded
• Porous • Wheel stud holes or seats
become damaged
• They have excessive radial or lateral runout.
ENSURE THAT TYRES ARE MOUNTED WITH THE
SIDEWALL MARKING ‘OUTSIDE’ SHOWING ON THE
OUTER SIDEWALL FACE.
CORRECT TYRE ROTATIONAL DIRECTION IS CRITICAL.
WA R N I N G
A TYRE AND WHEEL MUST ALWAYS BE CORRECTLY MATCHED. WIDER OR NARROWER TYRES THAN
RECOMMENDED COULD CAUSE DANGER THROUGH
SUDDEN DEFLATION.
WA R N I N G
WHEN CHANGING A WHEEL, MAKE SURE THAT THE VEHICLE CANNOT MOVE. ALWAYS APPLY THE
PARKING BRAKE AND SELE CT THE TRANSMISSION
PARK POSITION (AUTOMATIC TRANSMISSION ONLY).
WA R N I N G
NEVER RUN THE ENGINE WITH ONE WHEEL OFF THE GROUND, FOR EXAMPLE, WHEN CHANGING THE
WHEEL. THE WHEEL RESTING ON THE GROUND MAY CAUSE THE VEHICLE TO MOVE.
WA R N I N G
ALWAYS TIGHTEN THE WHEEL NUTS TO
SPECIFICATION. TOO TIGHT MAY CAUSE DAMAGE,
TOO LOOSE MAY ALLOW TH E WHEEL TO BECOME
DETACHED.
WAR NI NG
DO NOT MIX DIFFERENT TY PES OF TYRES ON THE
SAME VEHICLE. HANDLING MAY BE SERIOUSLY AFFECTED RESULTING IN LOSS OF CONTROL.
WAR NI NG
USE ONLY WHEELS AND WHEEL NUTS SUPPLIED BY
ASTON MARTIN. AFTER MARKET WHEELS OR WHEEL
NUTS MAY NOT INSTALL OR FUNCTION CORRECTLY
AND COULD CAUSE INJURY OR DAMAGE.
Caution
When a new tyre is installe d, always renew the tyre
valve.
Page 455 of 947
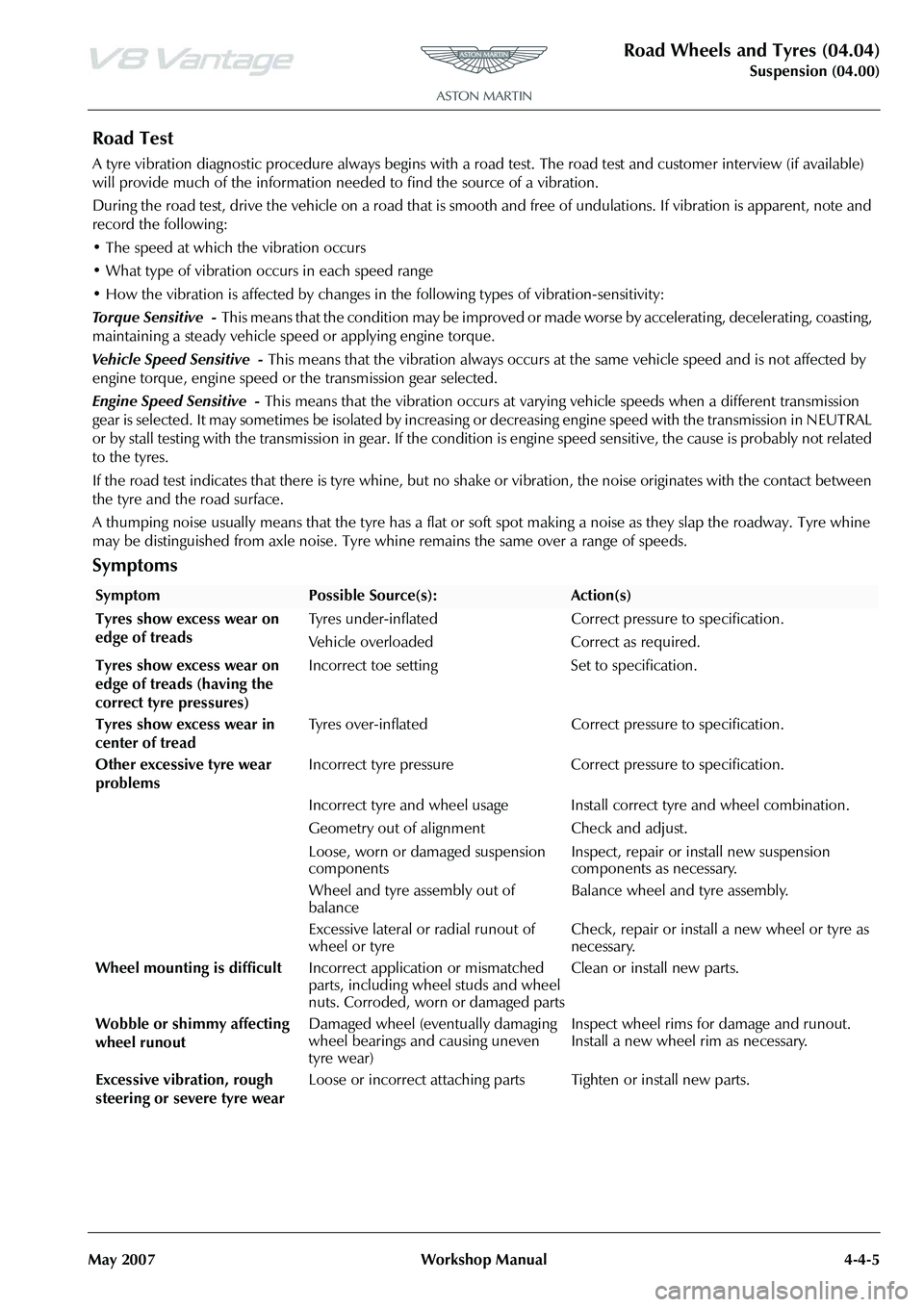
Road Wheels and Tyres (04.04)
Suspension (04.00)
May 2007 Workshop Manual 4-4-5
Road Test
A tyre vibration diagnostic proc edure always begins with a road test. The road test and customer interview (if available)
will provide much of the information neede d to find the source of a vibration.
During the road test, drive the vehicle on a road that is smoot h and free of undulations. If vibration is apparent, note and
record the following:
• The speed at which the vibration occurs
• What type of vibration occurs in each speed range
• How the vibration is affected by changes in the following types of vibration-sensitivity:
Torque Sensitive - This means that the condition may be improved or made worse by accelerating, decelerating, coasting,
maintaining a steady vehicle speed or applying engine torque.
Vehicle Speed Sensitive - This means that the vibration always occurs at the same vehicle speed and is not affected by
engine torque, engine speed or the transmission gear selected.
Engine Speed Sensitive - This means that the vibration occurs at varyin g vehicle speeds when a different transmission
gear is selected. It may sometimes be isolated by increasing or decreasing engine speed with the transmission in NEUTRAL
or by stall testing with the transmission in gear. If the condition is engine speed sensitive, the cause is probably not relate d
to the tyres.
If the road test indicates that there is tyre whine, but no sh ake or vibration, the noise originates with the contact between
the tyre and the road surface.
A thumping noise usually means that the tyre has a flat or soft spot making a noise as they slap the roadway. Tyre whine
may be distinguished from axle noise. Tyre whine remains the same over a range of speeds.
Symptoms
SymptomPossible Source(s):Action(s)
Tyres show excess wear on
edge of treads Tyres under-inflated Correct pressure to specification.
Vehicle overloaded Correct as required.
Tyres show excess wear on
edge of treads (having the
correct tyre pressures) Incorrect toe setting Set to specification.
Tyres show excess wear in
center of tread Tyres over-inflated Correct pressure to specification.
Other excessive tyre wear
problems Incorrect tyre pressure Correct pressure to specification.
Incorrect tyre and wheel usage Install correct tyre and wheel combination.
Geometry out of alignm
ent Check and adjust.
Loose, worn or damaged suspension
components Inspect, repair or install new suspension
components as necessary.
Wheel and tyre assembly out of
balance Balance wheel and tyre assembly.
Excessive lateral or radial runout of
wheel or tyre Check, repair or install a new wheel or tyre as
necessary.
Wheel mounting is difficult Incorrect application or mismatched
parts, including wheel studs and wheel
nuts. Corroded, worn or damaged parts Clean or install new parts.
Wobble or shimmy affecting
wheel runout Damaged wheel (eventually damaging
wheel bearings and causing uneven
tyre wear) Inspect wheel rims for damage and runout.
Install a new wheel rim as necessary.
Excessive vibration, rough
steering or severe tyre wear Loose or incorrect attaching parts Tighten or install new parts.