check engine BMW 3 SERIES 1983 E30 Workshop Manual
[x] Cancel search | Manufacturer: BMW, Model Year: 1983, Model line: 3 SERIES, Model: BMW 3 SERIES 1983 E30Pages: 228, PDF Size: 7.04 MB
Page 127 of 228
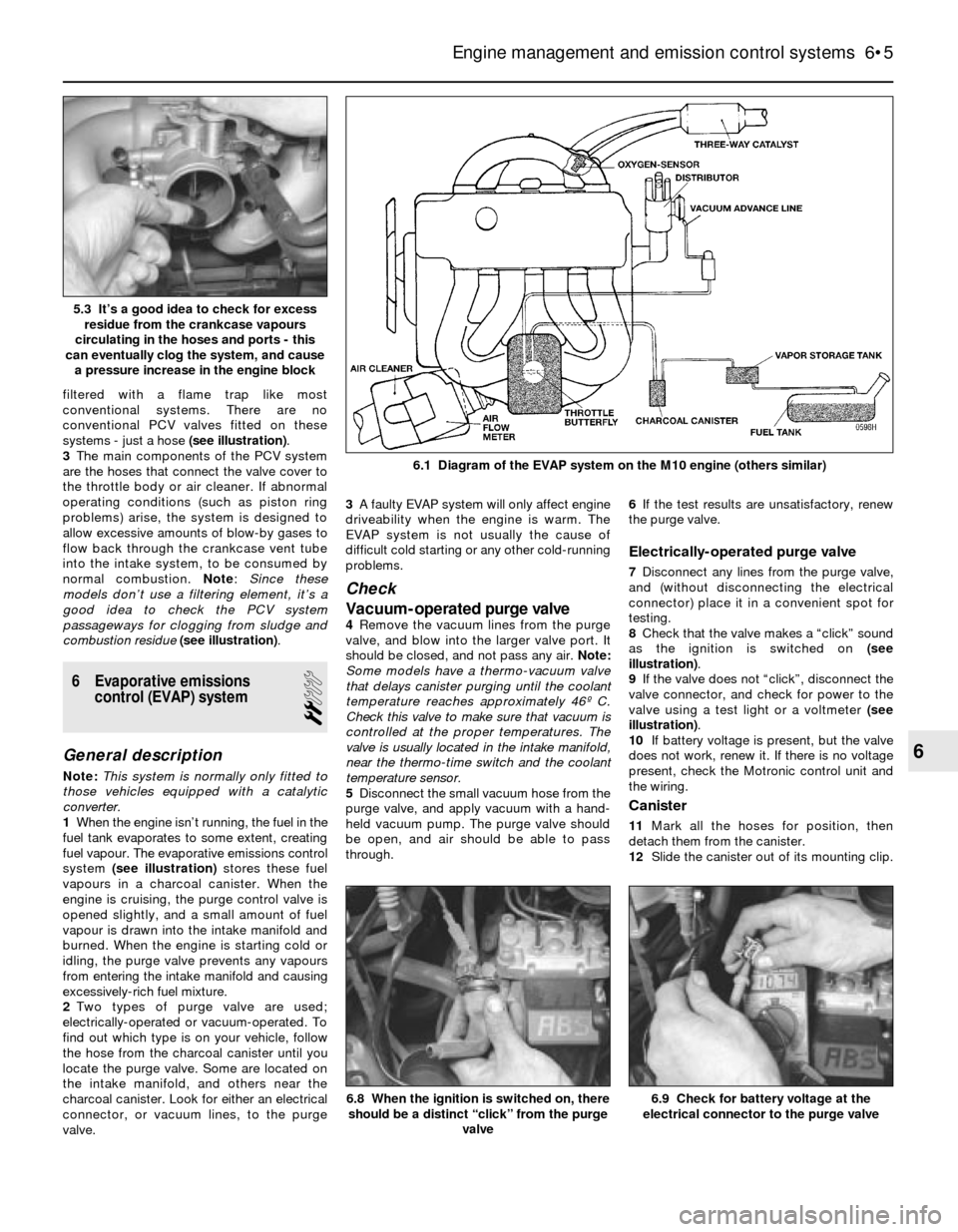
filtered with a flame trap like most
conventional systems. There are no
conventional PCV valves fitted on these
systems - just a hose (see illustration).
3The main components of the PCV system
are the hoses that connect the valve cover to
the throttle body or air cleaner. If abnormal
operating conditions (such as piston ring
problems) arise, the system is designed to
allow excessive amounts of blow-by gases to
flow back through the crankcase vent tube
into the intake system, to be consumed by
normal combustion. Note: Since these
models don’t use a filtering element, it’s a
good idea to check the PCV system
passageways for clogging from sludge and
combustion residue(see illustration).
6 Evaporative emissions
control (EVAP) system
2
General description
Note:This system is normally only fitted to
those vehicles equipped with a catalytic
converter.
1When the engine isn’t running, the fuel in the
fuel tank evaporates to some extent, creating
fuel vapour. The evaporative emissions control
system (see illustration)stores these fuel
vapours in a charcoal canister. When the
engine is cruising, the purge control valve is
opened slightly, and a small amount of fuel
vapour is drawn into the intake manifold and
burned. When the engine is starting cold or
idling, the purge valve prevents any vapours
from entering the intake manifold and causing
excessively-rich fuel mixture.
2Two types of purge valve are used;
electrically-operated or vacuum-operated. To
find out which type is on your vehicle, follow
the hose from the charcoal canister until you
locate the purge valve. Some are located on
the intake manifold, and others near the
charcoal canister. Look for either an electrical
connector, or vacuum lines, to the purge
valve.3A faulty EVAP system will only affect engine
driveability when the engine is warm. The
EVAP system is not usually the cause of
difficult cold starting or any other cold-running
problems.
Check
Vacuum-operated purge valve
4Remove the vacuum lines from the purge
valve, and blow into the larger valve port. It
should be closed, and not pass any air. Note:
Some models have a thermo-vacuum valve
that delays canister purging until the coolant
temperature reaches approximately 46º C.
Check this valve to make sure that vacuum is
controlled at the proper temperatures. The
valve is usually located in the intake manifold,
near the thermo-time switch and the coolant
temperature sensor.
5Disconnect the small vacuum hose from the
purge valve, and apply vacuum with a hand-
held vacuum pump. The purge valve should
be open, and air should be able to pass
through.6If the test results are unsatisfactory, renew
the purge valve.
Electrically-operated purge valve
7Disconnect any lines from the purge valve,
and (without disconnecting the electrical
connector) place it in a convenient spot for
testing.
8Check that the valve makes a “click” sound
as the ignition is switched on (see
illustration).
9If the valve does not “click”, disconnect the
valve connector, and check for power to the
valve using a test light or a voltmeter (see
illustration).
10If battery voltage is present, but the valve
does not work, renew it. If there is no voltage
present, check the Motronic control unit and
the wiring.
Canister
11Mark all the hoses for position, then
detach them from the canister.
12Slide the canister out of its mounting clip.
Engine management and emission control systems 6•5
6.1 Diagram of the EVAP system on the M10 engine (others similar)
6.9 Check for battery voltage at the
electrical connector to the purge valve6.8 When the ignition is switched on, there
should be a distinct “click” from the purge
valve
6
5.3 It’s a good idea to check for excess
residue from the crankcase vapours
circulating in the hoses and ports - this
can eventually clog the system, and cause
a pressure increase in the engine block
Page 128 of 228
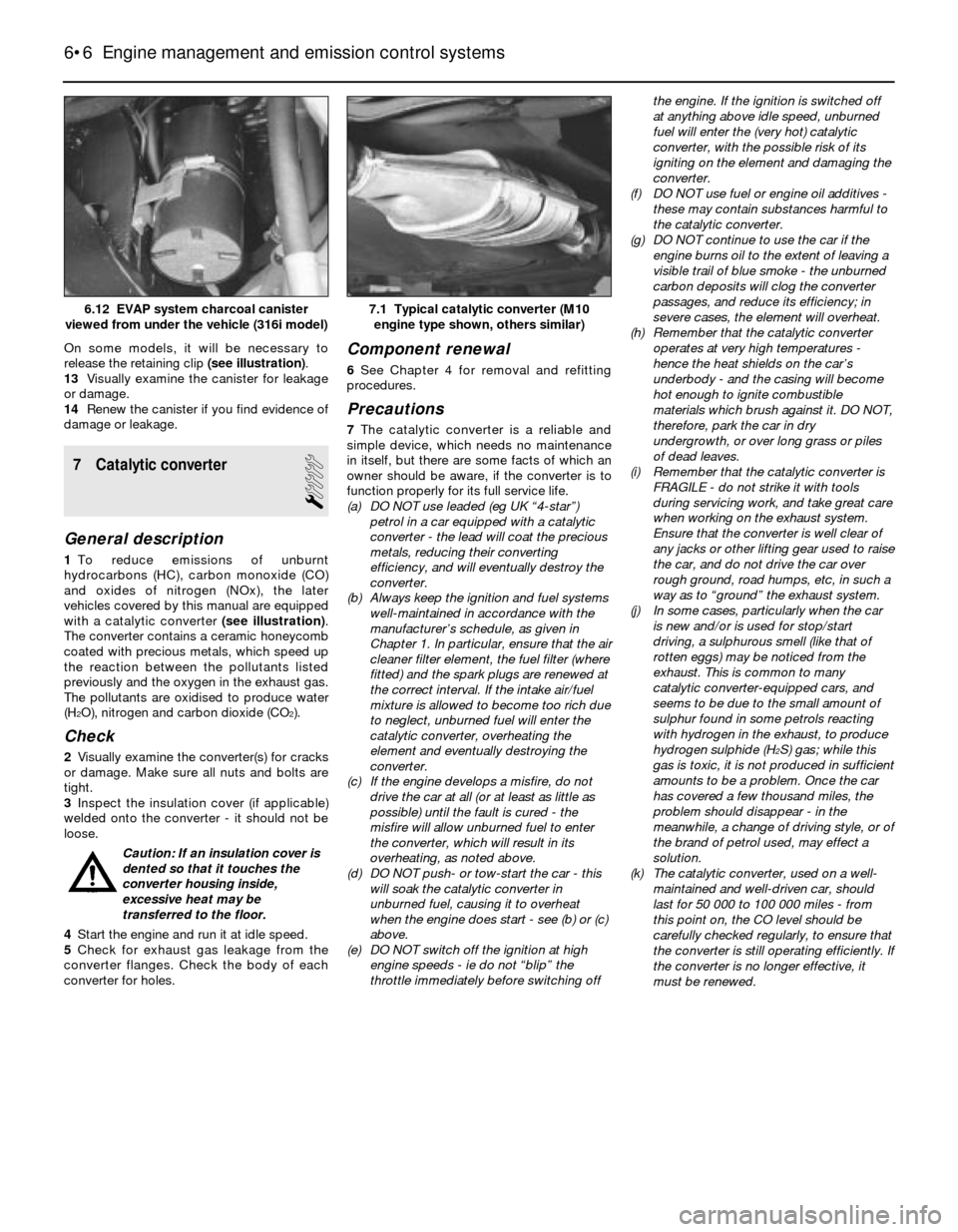
On some models, it will be necessary to
release the retaining clip (see illustration).
13Visually examine the canister for leakage
or damage.
14Renew the canister if you find evidence of
damage or leakage.
7 Catalytic converter
1
General description
1To reduce emissions of unburnt
hydrocarbons (HC), carbon monoxide (CO)
and oxides of nitrogen (NOx), the later
vehicles covered by this manual are equipped
with a catalytic converter (see illustration).
The converter contains a ceramic honeycomb
coated with precious metals, which speed up
the reaction between the pollutants listed
previously and the oxygen in the exhaust gas.
The pollutants are oxidised to produce water
(H
2O), nitrogen and carbon dioxide (CO2).
Check
2Visually examine the converter(s) for cracks
or damage. Make sure all nuts and bolts are
tight.
3Inspect the insulation cover (if applicable)
welded onto the converter - it should not be
loose.
Caution: If an insulation cover is
dented so that it touches the
converter housing inside,
excessive heat may be
transferred to the floor.
4Start the engine and run it at idle speed.
5Check for exhaust gas leakage from the
converter flanges. Check the body of each
converter for holes.
Component renewal
6See Chapter 4 for removal and refitting
procedures.
Precautions
7The catalytic converter is a reliable and
simple device, which needs no maintenance
in itself, but there are some facts of which an
owner should be aware, if the converter is to
function properly for its full service life.
(a) DO NOT use leaded (eg UK “4-star”)
petrol in a car equipped with a catalytic
converter - the lead will coat the precious
metals, reducing their converting
efficiency, and will eventually destroy the
converter.
(b) Always keep the ignition and fuel systems
well-maintained in accordance with the
manufacturer’s schedule, as given in
Chapter 1. In particular, ensure that the air
cleaner filter element, the fuel filter (where
fitted) and the spark plugs are renewed at
the correct interval. If the intake air/fuel
mixture is allowed to become too rich due
to neglect, unburned fuel will enter the
catalytic converter, overheating the
element and eventually destroying the
converter.
(c) If the engine develops a misfire, do not
drive the car at all (or at least as little as
possible) until the fault is cured - the
misfire will allow unburned fuel to enter
the converter, which will result in its
overheating, as noted above.
(d) DO NOT push- or tow-start the car - this
will soak the catalytic converter in
unburned fuel, causing it to overheat
when the engine does start - see (b) or (c)
above.
(e) DO NOT switch off the ignition at high
engine speeds - ie do not “blip” the
throttle immediately before switching offthe engine. If the ignition is switched off
at anything above idle speed, unburned
fuel will enter the (very hot) catalytic
converter, with the possible risk of its
igniting on the element and damaging the
converter.
(f) DO NOT use fuel or engine oil additives -
these may contain substances harmful to
the catalytic converter.
(g) DO NOT continue to use the car if the
engine burns oil to the extent of leaving a
visible trail of blue smoke - the unburned
carbon deposits will clog the converter
passages, and reduce its efficiency; in
severe cases, the element will overheat.
(h) Remember that the catalytic converter
operates at very high temperatures -
hence the heat shields on the car’s
underbody - and the casing will become
hot enough to ignite combustible
materials which brush against it. DO NOT,
therefore, park the car in dry
undergrowth, or over long grass or piles
of dead leaves.
(i) Remember that the catalytic converter is
FRAGILE - do not strike it with tools
during servicing work, and take great care
when working on the exhaust system.
Ensure that the converter is well clear of
any jacks or other lifting gear used to raise
the car, and do not drive the car over
rough ground, road humps, etc, in such a
way as to “ground” the exhaust system.
(j) In some cases, particularly when the car
is new and/or is used for stop/start
driving, a sulphurous smell (like that of
rotten eggs) may be noticed from the
exhaust. This is common to many
catalytic converter-equipped cars, and
seems to be due to the small amount of
sulphur found in some petrols reacting
with hydrogen in the exhaust, to produce
hydrogen sulphide (H
2S) gas; while this
gas is toxic, it is not produced in sufficient
amounts to be a problem. Once the car
has covered a few thousand miles, the
problem should disappear - in the
meanwhile, a change of driving style, or of
the brand of petrol used, may effect a
solution.
(k) The catalytic converter, used on a well-
maintained and well-driven car, should
last for 50 000 to 100 000 miles - from
this point on, the CO level should be
carefully checked regularly, to ensure that
the converter is still operating efficiently. If
the converter is no longer effective, it
must be renewed.
6•6 Engine management and emission control systems
7.1 Typical catalytic converter (M10
engine type shown, others similar)6.12 EVAP system charcoal canister
viewed from under the vehicle (316i model)
Page 130 of 228
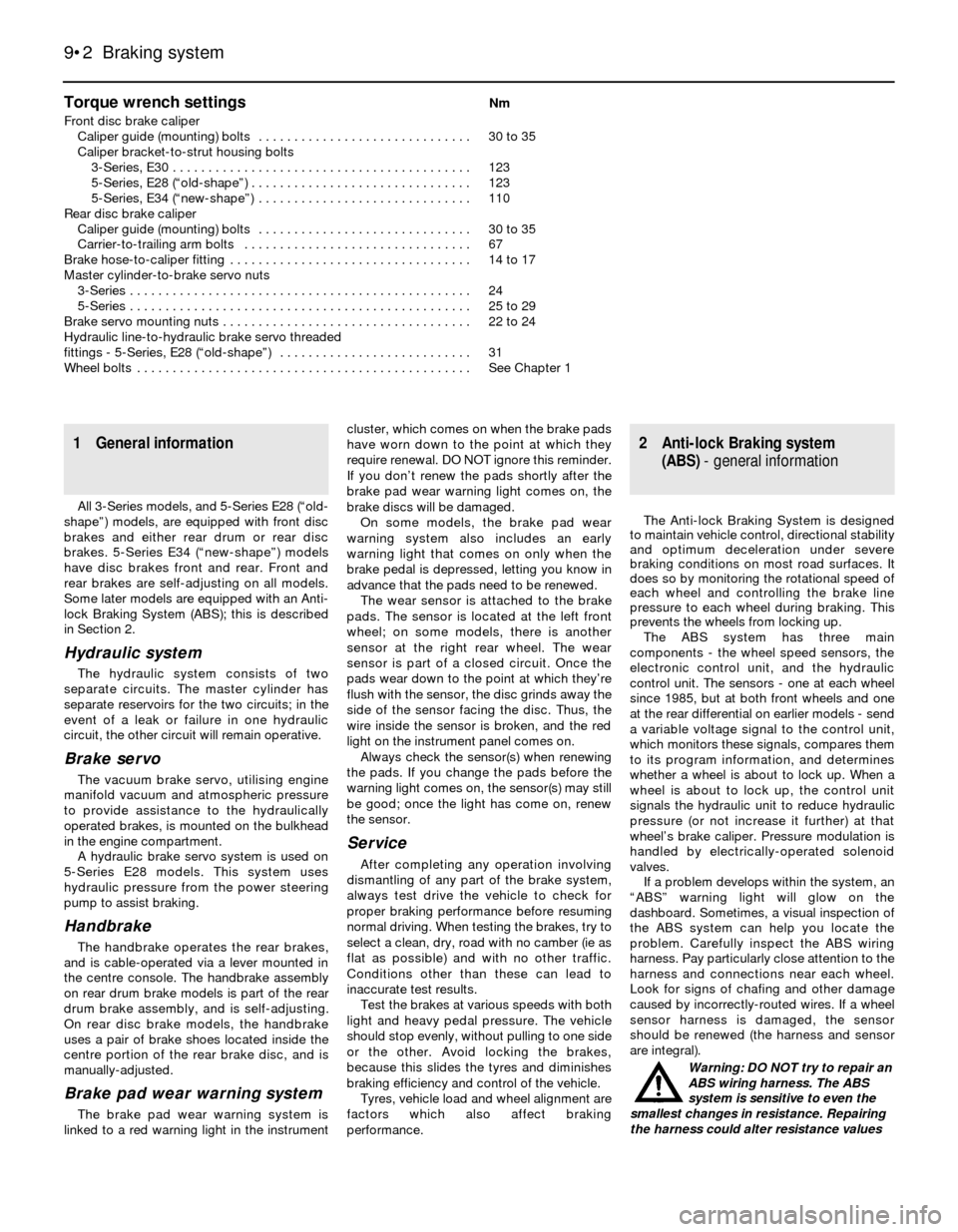
Torque wrench settingsNm
Front disc brake caliper
Caliper guide (mounting) bolts . . . . . . . . . . . . . . . . . . . . . . . . . . . . . . 30 to 35
Caliper bracket-to-strut housing bolts
3-Series, E30 . . . . . . . . . . . . . . . . . . . . . . . . . . . . . . . . . . . . . . . . . . 123
5-Series, E28 (“old-shape”) . . . . . . . . . . . . . . . . . . . . . . . . . . . . . . . 123
5-Series, E34 (“new-shape”) . . . . . . . . . . . . . . . . . . . . . . . . . . . . . . 110
Rear disc brake caliper
Caliper guide (mounting) bolts . . . . . . . . . . . . . . . . . . . . . . . . . . . . . . 30 to 35
Carrier-to-trailing arm bolts . . . . . . . . . . . . . . . . . . . . . . . . . . . . . . . . 67
Brake hose-to-caliper fitting . . . . . . . . . . . . . . . . . . . . . . . . . . . . . . . . . . 14 to 17
Master cylinder-to-brake servo nuts
3-Series . . . . . . . . . . . . . . . . . . . . . . . . . . . . . . . . . . . . . . . . . . . . . . . . 24
5-Series . . . . . . . . . . . . . . . . . . . . . . . . . . . . . . . . . . . . . . . . . . . . . . . . 25 to 29
Brake servo mounting nuts . . . . . . . . . . . . . . . . . . . . . . . . . . . . . . . . . . . 22 to 24
Hydraulic line-to-hydraulic brake servo threaded
fittings - 5-Series, E28 (“old-shape”) . . . . . . . . . . . . . . . . . . . . . . . . . . . 31
Wheel bolts . . . . . . . . . . . . . . . . . . . . . . . . . . . . . . . . . . . . . . . . . . . . . . . See Chapter 1
9•2 Braking system
1 General information
All 3-Series models, and 5-Series E28 (“old-
shape”) models, are equipped with front disc
brakes and either rear drum or rear disc
brakes. 5-Series E34 (“new-shape”) models
have disc brakes front and rear. Front and
rear brakes are self-adjusting on all models.
Some later models are equipped with an Anti-
lock Braking System (ABS); this is described
in Section 2.
Hydraulic system
The hydraulic system consists of two
separate circuits. The master cylinder has
separate reservoirs for the two circuits; in the
event of a leak or failure in one hydraulic
circuit, the other circuit will remain operative.
Brake servo
The vacuum brake servo, utilising engine
manifold vacuum and atmospheric pressure
to provide assistance to the hydraulically
operated brakes, is mounted on the bulkhead
in the engine compartment.
A hydraulic brake servo system is used on
5-Series E28 models. This system uses
hydraulic pressure from the power steering
pump to assist braking.
Handbrake
The handbrake operates the rear brakes,
and is cable-operated via a lever mounted in
the centre console. The handbrake assembly
on rear drum brake models is part of the rear
drum brake assembly, and is self-adjusting.
On rear disc brake models, the handbrake
uses a pair of brake shoes located inside the
centre portion of the rear brake disc, and is
manually-adjusted.
Brake pad wear warning system
The brake pad wear warning system is
linked to a red warning light in the instrumentcluster, which comes on when the brake pads
have worn down to the point at which they
require renewal. DO NOT ignore this reminder.
If you don’t renew the pads shortly after the
brake pad wear warning light comes on, the
brake discs will be damaged.
On some models, the brake pad wear
warning system also includes an early
warning light that comes on only when the
brake pedal is depressed, letting you know in
advance that the pads need to be renewed.
The wear sensor is attached to the brake
pads. The sensor is located at the left front
wheel; on some models, there is another
sensor at the right rear wheel. The wear
sensor is part of a closed circuit. Once the
pads wear down to the point at which they’re
flush with the sensor, the disc grinds away the
side of the sensor facing the disc. Thus, the
wire inside the sensor is broken, and the red
light on the instrument panel comes on.
Always check the sensor(s) when renewing
the pads. If you change the pads before the
warning light comes on, the sensor(s) may still
be good; once the light has come on, renew
the sensor.
Service
After completing any operation involving
dismantling of any part of the brake system,
always test drive the vehicle to check for
proper braking performance before resuming
normal driving. When testing the brakes, try to
select a clean, dry, road with no camber (ie as
flat as possible) and with no other traffic.
Conditions other than these can lead to
inaccurate test results.
Test the brakes at various speeds with both
light and heavy pedal pressure. The vehicle
should stop evenly, without pulling to one side
or the other. Avoid locking the brakes,
because this slides the tyres and diminishes
braking efficiency and control of the vehicle.
Tyres, vehicle load and wheel alignment are
factors which also affect braking
performance.
2 Anti-lock Braking system
(ABS)- general information
The Anti-lock Braking System is designed
to maintain vehicle control, directional stability
and optimum deceleration under severe
braking conditions on most road surfaces. It
does so by monitoring the rotational speed of
each wheel and controlling the brake line
pressure to each wheel during braking. This
prevents the wheels from locking up.
The ABS system has three main
components - the wheel speed sensors, the
electronic control unit, and the hydraulic
control unit. The sensors - one at each wheel
since 1985, but at both front wheels and one
at the rear differential on earlier models - send
a variable voltage signal to the control unit,
which monitors these signals, compares them
to its program information, and determines
whether a wheel is about to lock up. When a
wheel is about to lock up, the control unit
signals the hydraulic unit to reduce hydraulic
pressure (or not increase it further) at that
wheel’s brake caliper. Pressure modulation is
handled by electrically-operated solenoid
valves.
If a problem develops within the system, an
“ABS” warning light will glow on the
dashboard. Sometimes, a visual inspection of
the ABS system can help you locate the
problem. Carefully inspect the ABS wiring
harness. Pay particularly close attention to the
harness and connections near each wheel.
Look for signs of chafing and other damage
caused by incorrectly-routed wires. If a wheel
sensor harness is damaged, the sensor
should be renewed (the harness and sensor
are integral).
Warning: DO NOT try to repair an
ABS wiring harness. The ABS
system is sensitive to even the
smallest changes in resistance. Repairing
the harness could alter resistance values
Page 137 of 228

friction surfaces of the brake shoes or
drums.
12Make sure the adjuster assembly is
properly engaged with its respective notch in
the handbrake lever.
13When refitting the automatic adjustment
mechanism, fit the lever on the shoe first (see
illustration), then hook the lower end of the
spring onto the lever and the upper end into
its hole in the front shoe (see illustration).
14When you’re done, the brake assembly
should look like this (see illustration). Now
proceed to the other brake.
15When you’re done with both brakes, refit
the brake drums.
16If the wheel cylinder was renewed (see
Note 2), bleed the hydraulic system as
described in Section 16.
17Depress the brake pedal repeatedly to
actuate the self-adjusting mechanism. A
clicking sound will be heard from the brake
drums as the adjusters take up the slack.
18Check the handbrake adjustment (Sec-
tion 11).
19Refit the wheels and bolts. Lower the
vehicle to the ground, and tighten the wheel
bolts to the torque listed in the Chapter 1
Specifications. Check the operation of the
brakes carefully before driving the vehicle in
traffic.
7 Master cylinder-
removal and refitting
3
Warning: Brake fluid is
poisonous. It is also an effective
paint stripper. Refer to the
warning at the start of Section 16.
Note: Although master cylinder parts and
overhaul kits are available for most models, we
recommend fitting a new or overhauled
master cylinder complete. It will take you more
time to overhaul the master cylinder than to
renew it, and you can’t even determine
whether the master cylinder is in good enough
condition to overhaul it until you have
dismantled it. You may very well find that itcan’t be overhauled because of its internal
condition.
Removal
1The master cylinder is connected to the
brake vacuum servo, and both are attached to
the bulkhead, located on the left-hand side of
the engine compartment (see illustration).
2Remove as much fluid as you can from the
reservoir with a syringe.
3Place rags under the line fittings, and
prepare caps or plastic bags to cover the
ends of the lines once they are disconnected.
Caution: Brake fluid will damage
paint. Cover all body parts, and
be careful not to spill fluid during
this procedure.
4Loosen the union nuts at the ends of the
brake lines where they enter the master
cylinder. To prevent rounding off the flats on
these nuts, a split ring (“brake”) spanner,
which wraps around the nut, should be used.
5Pull the brake lines away from the master
cylinder slightly, and plug the ends to prevent
dirt contamination and further fluid loss.
6Disconnect any electrical connectors at the
master cylinder, then remove the nutsattaching the master cylinder to the brake
servo. Pull the master cylinder off the studs,
and lift it out of the engine compartment.
Again, be careful not to spill fluid as this is
done. Discard the old O-ring (see illustration)
between the master cylinder and the servo
unit.
Warning: The O-ring should
always be renewed. A faulty O-
ring can cause a vacuum leak,
which can reduce braking performance
and cause an erratic idle.
Bleeding procedure
7Before fitting a new or overhauled master
cylinder, it should be bled on the bench.
Because it will be necessary to apply pressure
to the master cylinder piston and, at the same
time, control flow from the brake line outlets, it
is recommended that the master cylinder be
mounted in a vice. Use a vice with protected
jaws, and don’t clamp the vice too tightly, or
the master cylinder body might crack.
8Insert threaded plugs into the brake line
outlet holes. Tighten them down so that there
will be no air leakage past them, but not so
tight that they cannot be easily loosened.
9Fill the reservoir with brake fluid of the
recommended type (see “Lubricants, fluids
and capacities” in Chapter 1).
10Remove one plug, and push the piston
assembly into the master cylinder bore to
Braking system 9•9
6.14 When you get everything back
together, this is how it
should look! 6.13b . . . then hook the lower end of the
spring onto the lever as shown; stretch the
spring, and hook the upper end into its
hole in the handbrake shoe6.13a Refit the automatic adjuster lever
first - make sure it’s properly engaged with
the notch in the front end of the
adjuster mechanism . . .
7.6 Always renew the O-ring (1) - groove
arrowed - between the master cylinder and
the brake servo
7.1 To remove the master cylinder, unplug
the electrical connector (top arrow),
disconnect the brake fluid hydraulic line
fittings (lower right arrow, other fitting not
visible in this photo) and remove the two
master cylinder mounting nuts (lower left
arrow, other nut not visible in this photo) -
5-Series master cylinder shown, 3-Series
similar
9
Page 138 of 228

expel the air from the master cylinder. A large
Phillips screwdriver can be used to push on
the piston assembly.
11To prevent air from being drawn back into
the master cylinder, the plug must be refitted
and tightened down before releasing the
pressure on the piston assembly.
12Repeat the procedure until brake fluid free
of air bubbles is expelled from the brake line
outlet hole. Repeat the procedure with the
other outlet hole and plug. Be sure to keep the
master cylinder reservoir filled with brake
fluid, to prevent the introduction of air into the
system.
13High pressure is not involved in the bench
bleeding procedure, so the plugs described
above need not be refitted each time the
piston is released, if wished. Instead, before
releasing the piston, simply put your finger
tightly over the hole to keep air from being
drawn back into the master cylinder. Wait
several seconds for brake fluid to be drawn
from the reservoir into the piston bore, then
depress the piston again, removing your
finger as brake fluid is expelled. Be sure to put
your finger back over the hole each time
before releasing the piston, and when the
bleeding procedure is complete for that outlet,
refit the plug and tighten it up before going on
to the other port.
Refitting
14Refit the master cylinder (together with a
new O-ring) over the studs on the brake servo,
and tighten the mounting nuts only finger-tight
at this time.
15Thread the brake line fittings into the
master cylinder. Since the master cylinder is
still a bit loose, it can be moved slightly in
order for the fittings to thread in easily. Do not
strip the threads as the fittings are tightened.
16Tighten the brake fittings securely, and
the mounting nuts to the torque listed in this
Chapter’s Specifications.
17Fill the master cylinder reservoir with fluid,
then bleed the master cylinder (only if the
cylinder has not already been bled) and the
brake system as described in Section 16.
18To bleed the cylinder on the vehicle, have
an assistant pump the brake pedal severaltimes and then hold the pedal to the floor.
Loosen the fitting nut to allow air and fluid to
escape, then tighten the nut. Repeat this
procedure on both fittings until the fluid is
clear of air bubbles. Test the operation of the
brake system carefully before returning the
vehicle to normal service.
8 Brake vacuum servo-
check, removal and refitting
3
Operating check
1Depress the brake pedal several times with
the engine off, until there is no change in the
pedal travel.
2Depress and hold the pedal, then start the
engine. If the pedal goes down slightly,
operation is normal.
Airtightness check
3Start the engine, and turn it off after one or
two minutes. Depress the brake pedal several
times slowly. If the pedal goes down further
the first time but gradually rises after the
second or third depression, the servo is
airtight.
4Depress the brake pedal while the engine is
running, then stop the engine with the pedal
depressed. If there is no change in the pedal
travel after holding the pedal for 30 seconds,
the servo is airtight.
Removal and refitting
5Dismantling the vacuum servo requires
special tools, and cannot be performed by the
home mechanic. If a problem develops, it is
recommended that a new unit be fitted.
6Remove the master cylinder as described in
Section 7.
7Disconnect the vacuum hose from the
brake servo.
8Working in the passenger compartment,
remove the glovebox and lower left-hand trim
panels.
9Remove the clip and clevis pin to
disconnect the pushrod from the cross-shaft
lever (right-hand-drive models) or brake pedal(left-hand-drive models) (see illustration). On
left-hand-drive models, also disconnect the
brake pedal return spring.
10Remove the four mounting nuts (see
illustration)and withdraw the servo unit from
the engine compartment.
11Inspect the small foam filter (see
illustration)inside the rubber boot on the
pushrod. If the filter is clogged, it may affect
the servo’s performance. To clean the filter,
wash it in a mild soapy solution. If it’s still
dirty, renew it.
12Refitting is the reverse of the removal
procedure. Tighten the brake servo mounting
nuts to the torque listed in this Chapter’s
Specifications. Before you slide the boot into
place over the servo pushrod air filter, make
sure the notches in the filter offset the notches
in the damper by 180 degrees.
13On 3-Series models, adjust the basic
setting of the pushrod’s threaded clevis until
the dimension is correct (see illustration).
When the basic setting is correct, tighten the
locknut, then adjust the brake pedal travel and
9•10 Braking system
8.13 On 3-Series models, adjust
dimension A (the distance between the
middle of the brake lever and the
bulkhead/”firewall”) by loosening the
locknut (1) at the pushrod clevis (2) and
turning the threaded part of the pushrod
until dimension A matches the dimension
listed in this Chapter’s Specifications.
When the basic setting is correct, tighten
the locknut, then adjust the brake pedal
height and the stop-light switch
8.11 An exploded view of a typical servo
pushrod assembly
1 Boot 2 Holder 3 Damper 4 Air filter8.10 Remove the four mounting nuts
(arrows) and withdraw the servo unit from
the engine compartment
(left-hand-drive model shown)
8.9 Disconnect the brake pedal return
spring, then remove the clip and clevis pin
(arrows) to disconnect the pushrod from
the brake pedal (left-hand-drive models)
Page 142 of 228
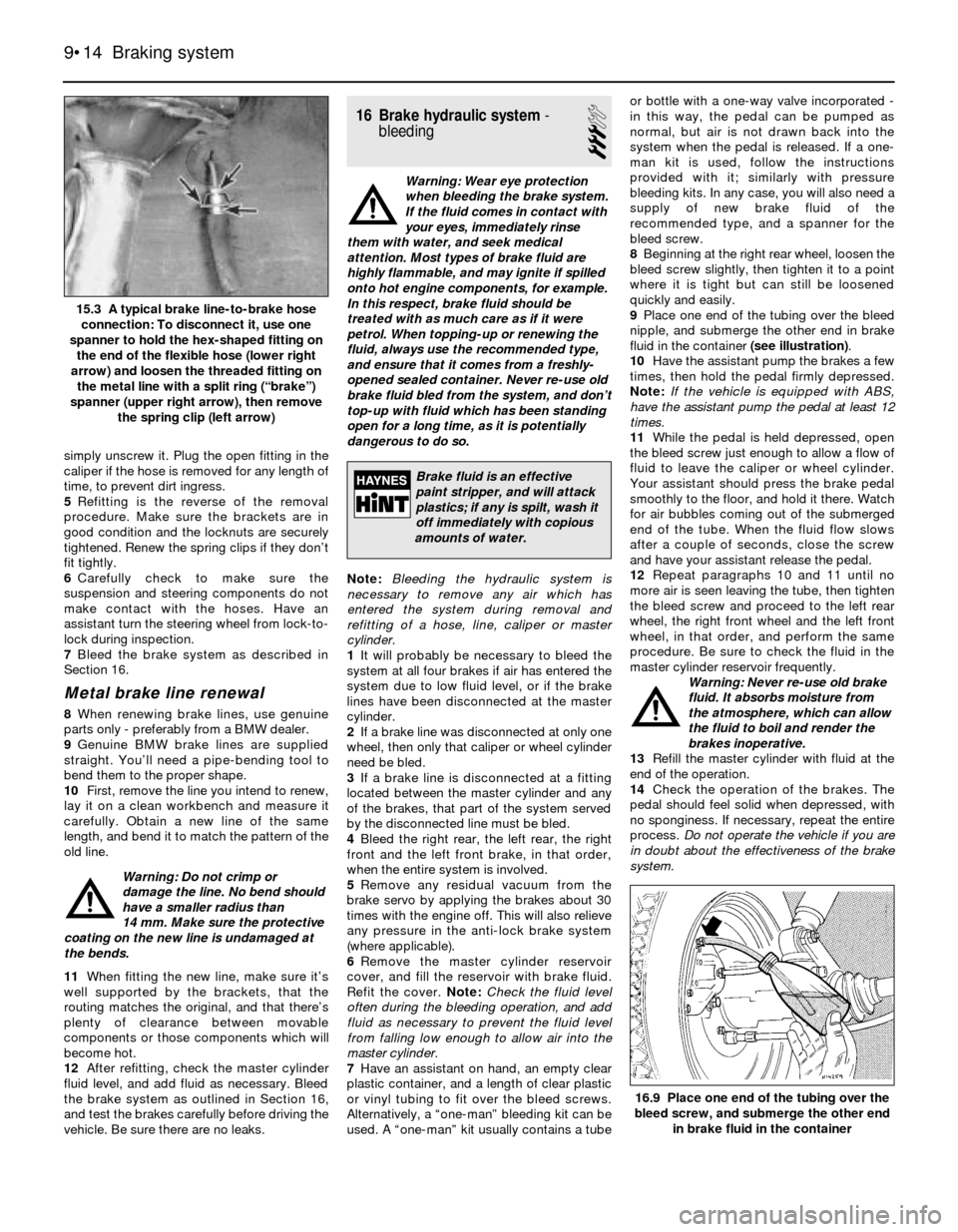
simply unscrew it. Plug the open fitting in the
caliper if the hose is removed for any length of
time, to prevent dirt ingress.
5Refitting is the reverse of the removal
procedure. Make sure the brackets are in
good condition and the locknuts are securely
tightened. Renew the spring clips if they don’t
fit tightly.
6Carefully check to make sure the
suspension and steering components do not
make contact with the hoses. Have an
assistant turn the steering wheel from lock-to-
lock during inspection.
7Bleed the brake system as described in
Section 16.
Metal brake line renewal
8When renewing brake lines, use genuine
parts only - preferably from a BMW dealer.
9Genuine BMW brake lines are supplied
straight. You’ll need a pipe-bending tool to
bend them to the proper shape.
10First, remove the line you intend to renew,
lay it on a clean workbench and measure it
carefully. Obtain a new line of the same
length, and bend it to match the pattern of the
old line.
Warning: Do not crimp or
damage the line. No bend should
have a smaller radius than
14 mm. Make sure the protective
coating on the new line is undamaged at
the bends.
11When fitting the new line, make sure it’s
well supported by the brackets, that the
routing matches the original, and that there’s
plenty of clearance between movable
components or those components which will
become hot.
12After refitting, check the master cylinder
fluid level, and add fluid as necessary. Bleed
the brake system as outlined in Section 16,
and test the brakes carefully before driving the
vehicle. Be sure there are no leaks.
16 Brake hydraulic system-
bleeding
3
Warning: Wear eye protection
when bleeding the brake system.
If the fluid comes in contact with
your eyes, immediately rinse
them with water, and seek medical
attention. Most types of brake fluid are
highly flammable, and may ignite if spilled
onto hot engine components, for example.
In this respect, brake fluid should be
treated with as much care as if it were
petrol. When topping-up or renewing the
fluid, always use the recommended type,
and ensure that it comes from a freshly-
opened sealed container. Never re-use old
brake fluid bled from the system, and don’t
top-up with fluid which has been standing
open for a long time, as it is potentially
dangerous to do so.
Note:Bleeding the hydraulic system is
necessary to remove any air which has
entered the system during removal and
refitting of a hose, line, caliper or master
cylinder.
1It will probably be necessary to bleed the
system at all four brakes if air has entered the
system due to low fluid level, or if the brake
lines have been disconnected at the master
cylinder.
2If a brake line was disconnected at only one
wheel, then only that caliper or wheel cylinder
need be bled.
3If a brake line is disconnected at a fitting
located between the master cylinder and any
of the brakes, that part of the system served
by the disconnected line must be bled.
4Bleed the right rear, the left rear, the right
front and the left front brake, in that order,
when the entire system is involved.
5Remove any residual vacuum from the
brake servo by applying the brakes about 30
times with the engine off. This will also relieve
any pressure in the anti-lock brake system
(where applicable).
6Remove the master cylinder reservoir
cover, and fill the reservoir with brake fluid.
Refit the cover. Note:Check the fluid level
often during the bleeding operation, and add
fluid as necessary to prevent the fluid level
from falling low enough to allow air into the
master cylinder.
7Have an assistant on hand, an empty clear
plastic container, and a length of clear plastic
or vinyl tubing to fit over the bleed screws.
Alternatively, a “one-man” bleeding kit can be
used. A “one-man” kit usually contains a tubeor bottle with a one-way valve incorporated -
in this way, the pedal can be pumped as
normal, but air is not drawn back into the
system when the pedal is released. If a one-
man kit is used, follow the instructions
provided with it; similarly with pressure
bleeding kits. In any case, you will also need a
supply of new brake fluid of the
recommended type, and a spanner for the
bleed screw.
8Beginning at the right rear wheel, loosen the
bleed screw slightly, then tighten it to a point
where it is tight but can still be loosened
quickly and easily.
9Place one end of the tubing over the bleed
nipple, and submerge the other end in brake
fluid in the container (see illustration).
10Have the assistant pump the brakes a few
times, then hold the pedal firmly depressed.
Note:If the vehicle is equipped with ABS,
have the assistant pump the pedal at least 12
times.
11While the pedal is held depressed, open
the bleed screw just enough to allow a flow of
fluid to leave the caliper or wheel cylinder.
Your assistant should press the brake pedal
smoothly to the floor, and hold it there. Watch
for air bubbles coming out of the submerged
end of the tube. When the fluid flow slows
after a couple of seconds, close the screw
and have your assistant release the pedal.
12Repeat paragraphs 10 and 11 until no
more air is seen leaving the tube, then tighten
the bleed screw and proceed to the left rear
wheel, the right front wheel and the left front
wheel, in that order, and perform the same
procedure. Be sure to check the fluid in the
master cylinder reservoir frequently.
Warning: Never re-use old brake
fluid. It absorbs moisture from
the atmosphere, which can allow
the fluid to boil and render the
brakes inoperative.
13Refill the master cylinder with fluid at the
end of the operation.
14Check the operation of the brakes. The
pedal should feel solid when depressed, with
no sponginess. If necessary, repeat the entire
process. Do not operate the vehicle if you are
in doubt about the effectiveness of the brake
system.
9•14 Braking system
16.9 Place one end of the tubing over the
bleed screw, and submerge the other end
in brake fluid in the container
15.3 A typical brake line-to-brake hose
connection: To disconnect it, use one
spanner to hold the hex-shaped fitting on
the end of the flexible hose (lower right
arrow) and loosen the threaded fitting on
the metal line with a split ring (“brake”)
spanner (upper right arrow), then remove
the spring clip (left arrow)
Brake fluid is an effective
paint stripper, and will attack
plastics; if any is spilt, wash it
off immediately with copious
amounts of water.
Page 146 of 228
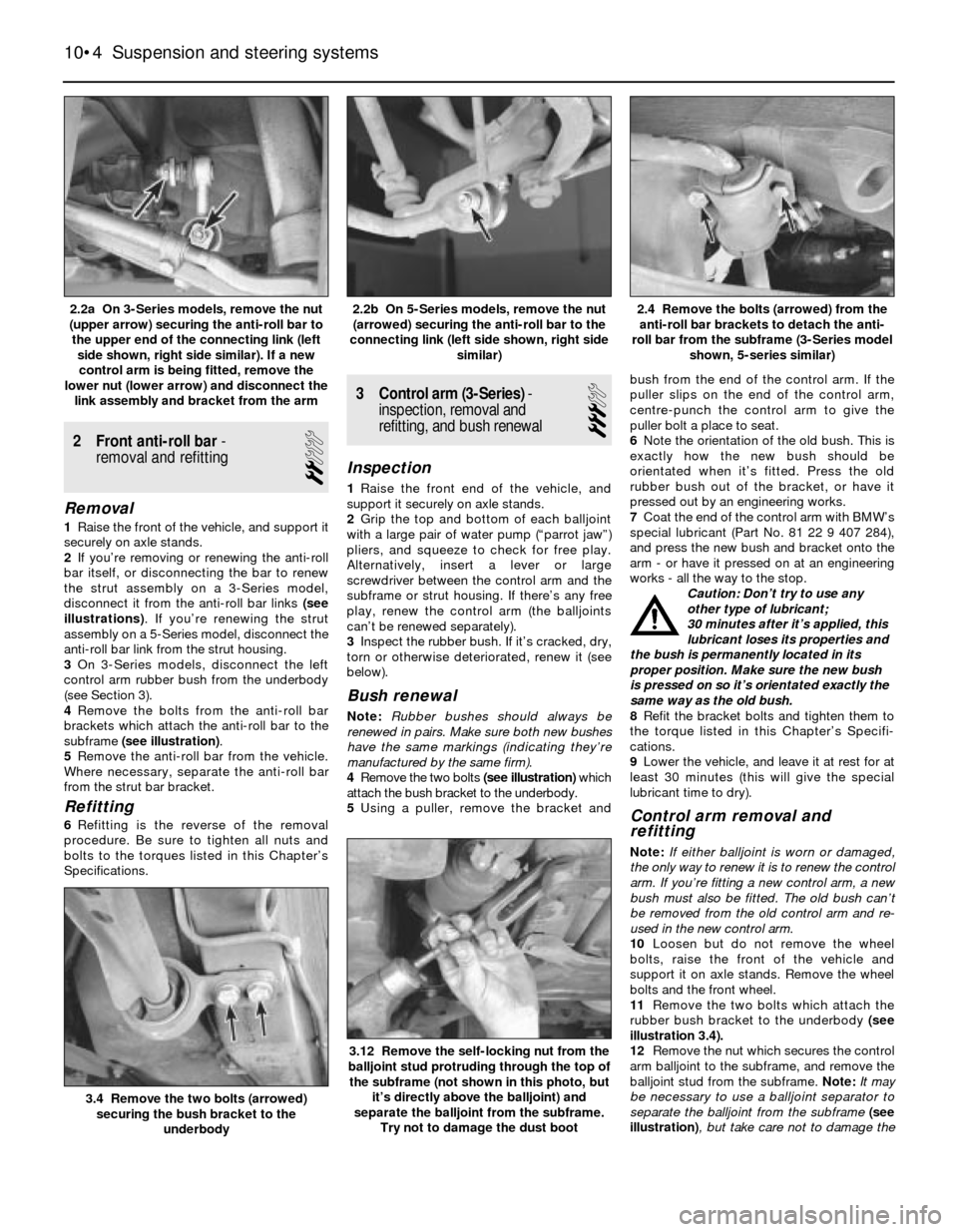
2 Front anti-roll bar-
removal and refitting
2
Removal
1Raise the front of the vehicle, and support it
securely on axle stands.
2If you’re removing or renewing the anti-roll
bar itself, or disconnecting the bar to renew
the strut assembly on a 3-Series model,
disconnect it from the anti-roll bar links (see
illustrations). If you’re renewing the strut
assembly on a 5-Series model, disconnect the
anti-roll bar link from the strut housing.
3On 3-Series models, disconnect the left
control arm rubber bush from the underbody
(see Section 3).
4Remove the bolts from the anti-roll bar
brackets which attach the anti-roll bar to the
subframe (see illustration).
5Remove the anti-roll bar from the vehicle.
Where necessary, separate the anti-roll bar
from the strut bar bracket.
Refitting
6Refitting is the reverse of the removal
procedure. Be sure to tighten all nuts and
bolts to the torques listed in this Chapter’s
Specifications.
3 Control arm (3-Series)-
inspection, removal and
refitting, and bush renewal
3
Inspection
1Raise the front end of the vehicle, and
support it securely on axle stands.
2Grip the top and bottom of each balljoint
with a large pair of water pump (“parrot jaw”)
pliers, and squeeze to check for free play.
Alternatively, insert a lever or large
screwdriver between the control arm and the
subframe or strut housing. If there’s any free
play, renew the control arm (the balljoints
can’t be renewed separately).
3Inspect the rubber bush. If it’s cracked, dry,
torn or otherwise deteriorated, renew it (see
below).
Bush renewal
Note:Rubber bushes should always be
renewed in pairs. Make sure both new bushes
have the same markings (indicating they’re
manufactured by the same firm).
4Remove the two bolts (see illustration)which
attach the bush bracket to the underbody.
5Using a puller, remove the bracket andbush from the end of the control arm. If the
puller slips on the end of the control arm,
centre-punch the control arm to give the
puller bolt a place to seat.
6Note the orientation of the old bush. This is
exactly how the new bush should be
orientated when it’s fitted. Press the old
rubber bush out of the bracket, or have it
pressed out by an engineering works.
7Coat the end of the control arm with BMW’s
special lubricant (Part No. 81 22 9 407 284),
and press the new bush and bracket onto the
arm - or have it pressed on at an engineering
works - all the way to the stop.
Caution: Don’t try to use any
other type of lubricant;
30 minutes after it’s applied, this
lubricant loses its properties and
the bush is permanently located in its
proper position. Make sure the new bush
is pressed on so it’s orientated exactly the
same way as the old bush.
8Refit the bracket bolts and tighten them to
the torque listed in this Chapter’s Specifi-
cations.
9Lower the vehicle, and leave it at rest for at
least 30 minutes (this will give the special
lubricant time to dry).
Control arm removal and
refitting
Note:If either balljoint is worn or damaged,
the only way to renew it is to renew the control
arm. If you’re fitting a new control arm, a new
bush must also be fitted. The old bush can’t
be removed from the old control arm and re-
used in the new control arm.
10Loosen but do not remove the wheel
bolts, raise the front of the vehicle and
support it on axle stands. Remove the wheel
bolts and the front wheel.
11Remove the two bolts which attach the
rubber bush bracket to the underbody (see
illustration 3.4).
12Remove the nut which secures the control
arm balljoint to the subframe, and remove the
balljoint stud from the subframe. Note:It may
be necessary to use a balljoint separator to
separate the balljoint from the subframe (see
illustration), but take care not to damage the
10•4 Suspension and steering systems
3.12 Remove the self-locking nut from the
balljoint stud protruding through the top of
the subframe (not shown in this photo, but
it’s directly above the balljoint) and
separate the balljoint from the subframe.
Try not to damage the dust boot
3.4 Remove the two bolts (arrowed)
securing the bush bracket to the
underbody
2.4 Remove the bolts (arrowed) from the
anti-roll bar brackets to detach the anti-
roll bar from the subframe (3-Series model
shown, 5-series similar)2.2b On 5-Series models, remove the nut
(arrowed) securing the anti-roll bar to the
connecting link (left side shown, right side
similar)2.2a On 3-Series models, remove the nut
(upper arrow) securing the anti-roll bar to
the upper end of the connecting link (left
side shown, right side similar). If a new
control arm is being fitted, remove the
lower nut (lower arrow) and disconnect the
link assembly and bracket from the arm
Page 148 of 228
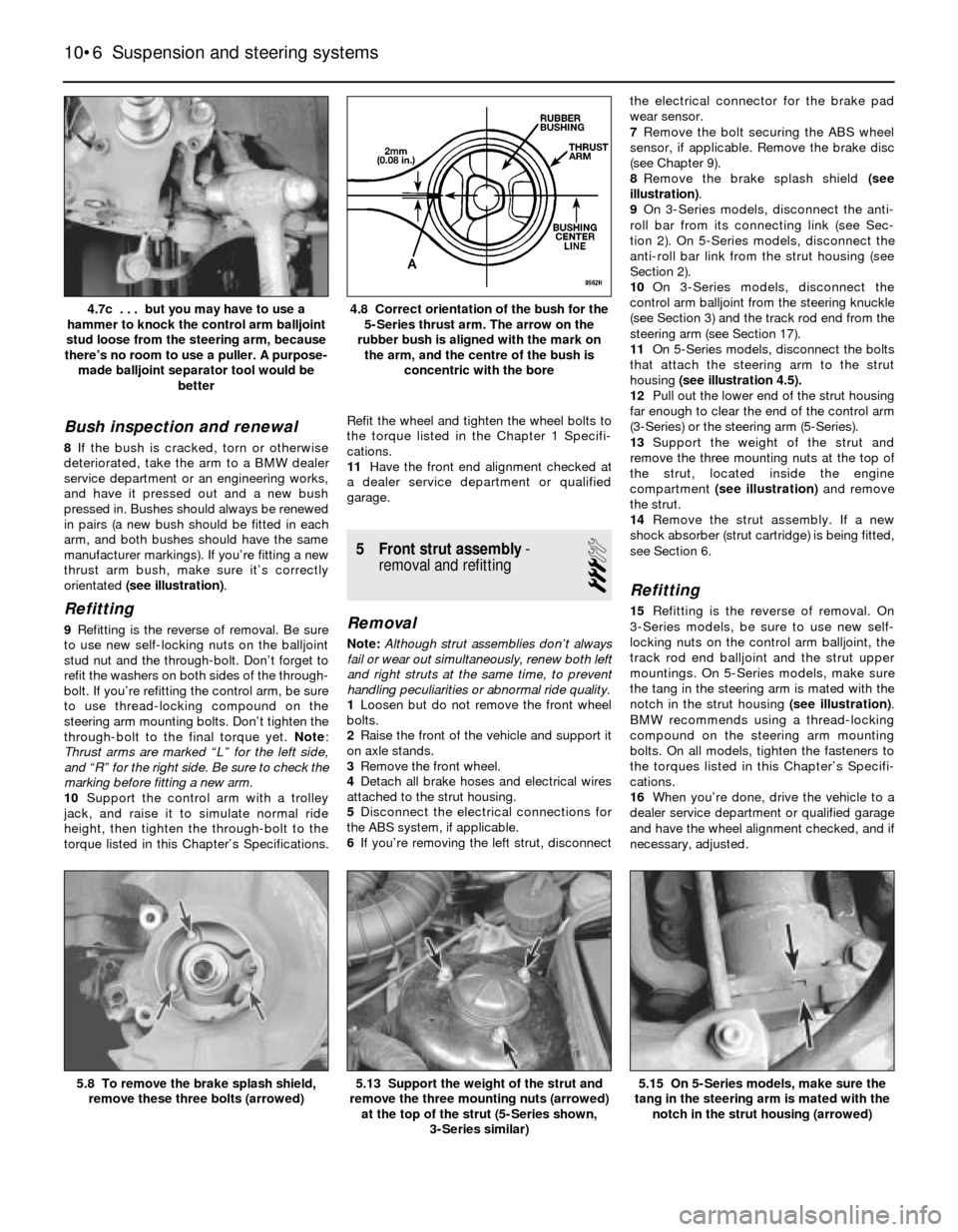
Bush inspection and renewal
8If the bush is cracked, torn or otherwise
deteriorated, take the arm to a BMW dealer
service department or an engineering works,
and have it pressed out and a new bush
pressed in. Bushes should always be renewed
in pairs (a new bush should be fitted in each
arm, and both bushes should have the same
manufacturer markings). If you’re fitting a new
thrust arm bush, make sure it’s correctly
orientated (see illustration).
Refitting
9Refitting is the reverse of removal. Be sure
to use new self-locking nuts on the balljoint
stud nut and the through-bolt. Don’t forget to
refit the washers on both sides of the through-
bolt. If you’re refitting the control arm, be sure
to use thread-locking compound on the
steering arm mounting bolts. Don’t tighten the
through-bolt to the final torque yet. Note:
Thrust arms are marked “L” for the left side,
and “R” for the right side. Be sure to check the
marking before fitting a new arm.
10Support the control arm with a trolley
jack, and raise it to simulate normal ride
height, then tighten the through-bolt to the
torque listed in this Chapter’s Specifications.Refit the wheel and tighten the wheel bolts to
the torque listed in the Chapter 1 Specifi-
cations.
11Have the front end alignment checked at
a dealer service department or qualified
garage.
5 Front strut assembly-
removal and refitting
3
Removal
Note:Although strut assemblies don’t always
fail or wear out simultaneously, renew both left
and right struts at the same time, to prevent
handling peculiarities or abnormal ride quality.
1Loosen but do not remove the front wheel
bolts.
2Raise the front of the vehicle and support it
on axle stands.
3Remove the front wheel.
4Detach all brake hoses and electrical wires
attached to the strut housing.
5Disconnect the electrical connections for
the ABS system, if applicable.
6If you’re removing the left strut, disconnectthe electrical connector for the brake pad
wear sensor.
7Remove the bolt securing the ABS wheel
sensor, if applicable. Remove the brake disc
(see Chapter 9).
8Remove the brake splash shield (see
illustration).
9On 3-Series models, disconnect the anti-
roll bar from its connecting link (see Sec-
tion 2). On 5-Series models, disconnect the
anti-roll bar link from the strut housing (see
Section 2).
10On 3-Series models, disconnect the
control arm balljoint from the steering knuckle
(see Section 3) and the track rod end from the
steering arm (see Section 17).
11On 5-Series models, disconnect the bolts
that attach the steering arm to the strut
housing (see illustration 4.5).
12Pull out the lower end of the strut housing
far enough to clear the end of the control arm
(3-Series) or the steering arm (5-Series).
13Support the weight of the strut and
remove the three mounting nuts at the top of
the strut, located inside the engine
compartment (see illustration)and remove
the strut.
14Remove the strut assembly. If a new
shock absorber (strut cartridge) is being fitted,
see Section 6.
Refitting
15Refitting is the reverse of removal. On
3-Series models, be sure to use new self-
locking nuts on the control arm balljoint, the
track rod end balljoint and the strut upper
mountings. On 5-Series models, make sure
the tang in the steering arm is mated with the
notch in the strut housing (see illustration).
BMW recommends using a thread-locking
compound on the steering arm mounting
bolts. On all models, tighten the fasteners to
the torques listed in this Chapter’s Specifi-
cations.
16When you’re done, drive the vehicle to a
dealer service department or qualified garage
and have the wheel alignment checked, and if
necessary, adjusted.
10•6 Suspension and steering systems
5.15 On 5-Series models, make sure the
tang in the steering arm is mated with the
notch in the strut housing (arrowed)5.13 Support the weight of the strut and
remove the three mounting nuts (arrowed)
at the top of the strut (5-Series shown,
3-Series similar)5.8 To remove the brake splash shield,
remove these three bolts (arrowed)
4.8 Correct orientation of the bush for the
5-Series thrust arm. The arrow on the
rubber bush is aligned with the mark on
the arm, and the centre of the bush is
concentric with the bore4.7c . . . but you may have to use a
hammer to knock the control arm balljoint
stud loose from the steering arm, because
there’s no room to use a puller. A purpose-
made balljoint separator tool would be
better
Page 149 of 228
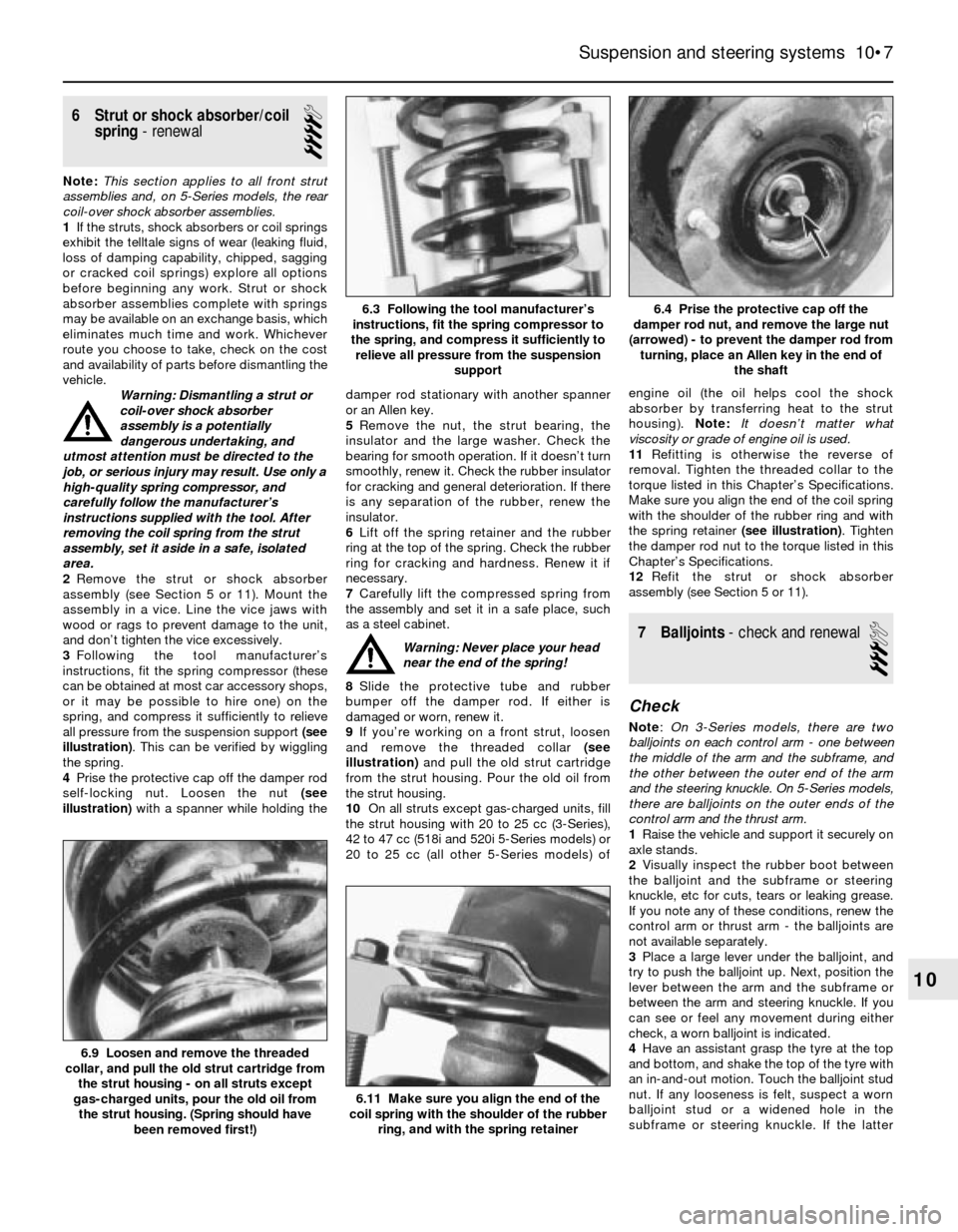
6 Strut or shock absorber/coil
spring- renewal
4
Note:This section applies to all front strut
assemblies and, on 5-Series models, the rear
coil-over shock absorber assemblies.
1If the struts, shock absorbers or coil springs
exhibit the telltale signs of wear (leaking fluid,
loss of damping capability, chipped, sagging
or cracked coil springs) explore all options
before beginning any work. Strut or shock
absorber assemblies complete with springs
may be available on an exchange basis, which
eliminates much time and work. Whichever
route you choose to take, check on the cost
and availability of parts before dismantling the
vehicle.
Warning: Dismantling a strut or
coil-over shock absorber
assembly is a potentially
dangerous undertaking, and
utmost attention must be directed to the
job, or serious injury may result. Use only a
high-quality spring compressor, and
carefully follow the manufacturer’s
instructions supplied with the tool. After
removing the coil spring from the strut
assembly, set it aside in a safe, isolated
area.
2Remove the strut or shock absorber
assembly (see Section 5 or 11). Mount the
assembly in a vice. Line the vice jaws with
wood or rags to prevent damage to the unit,
and don’t tighten the vice excessively.
3Following the tool manufacturer’s
instructions, fit the spring compressor (these
can be obtained at most car accessory shops,
or it may be possible to hire one) on the
spring, and compress it sufficiently to relieve
all pressure from the suspension support (see
illustration). This can be verified by wiggling
the spring.
4Prise the protective cap off the damper rod
self-locking nut. Loosen the nut (see
illustration)with a spanner while holding thedamper rod stationary with another spanner
or an Allen key.
5Remove the nut, the strut bearing, the
insulator and the large washer. Check the
bearing for smooth operation. If it doesn’t turn
smoothly, renew it. Check the rubber insulator
for cracking and general deterioration. If there
is any separation of the rubber, renew the
insulator.
6Lift off the spring retainer and the rubber
ring at the top of the spring. Check the rubber
ring for cracking and hardness. Renew it if
necessary.
7Carefully lift the compressed spring from
the assembly and set it in a safe place, such
as a steel cabinet.
Warning: Never place your head
near the end of the spring!
8Slide the protective tube and rubber
bumper off the damper rod. If either is
damaged or worn, renew it.
9If you’re working on a front strut, loosen
and remove the threaded collar (see
illustration)and pull the old strut cartridge
from the strut housing. Pour the old oil from
the strut housing.
10On all struts except gas-charged units, fill
the strut housing with 20 to 25 cc (3-Series),
42 to 47 cc (518i and 520i 5-Series models) or
20 to 25 cc (all other 5-Series models) ofengine oil (the oil helps cool the shock
absorber by transferring heat to the strut
housing). Note:It doesn’t matter what
viscosity or grade of engine oil is used.
11Refitting is otherwise the reverse of
removal. Tighten the threaded collar to the
torque listed in this Chapter’s Specifications.
Make sure you align the end of the coil spring
with the shoulder of the rubber ring and with
the spring retainer (see illustration). Tighten
the damper rod nut to the torque listed in this
Chapter’s Specifications.
12Refit the strut or shock absorber
assembly (see Section 5 or 11).
7 Balljoints- check and renewal
3
Check
Note:On 3-Series models, there are two
balljoints on each control arm - one between
the middle of the arm and the subframe, and
the other between the outer end of the arm
and the steering knuckle. On 5-Series models,
there are balljoints on the outer ends of the
control arm and the thrust arm.
1Raise the vehicle and support it securely on
axle stands.
2Visually inspect the rubber boot between
the balljoint and the subframe or steering
knuckle, etc for cuts, tears or leaking grease.
If you note any of these conditions, renew the
control arm or thrust arm - the balljoints are
not available separately.
3Place a large lever under the balljoint, and
try to push the balljoint up. Next, position the
lever between the arm and the subframe or
between the arm and steering knuckle. If you
can see or feel any movement during either
check, a worn balljoint is indicated.
4Have an assistant grasp the tyre at the top
and bottom, and shake the top of the tyre with
an in-and-out motion. Touch the balljoint stud
nut. If any looseness is felt, suspect a worn
balljoint stud or a widened hole in the
subframe or steering knuckle. If the latter
Suspension and steering systems 10•7
6.4 Prise the protective cap off the
damper rod nut, and remove the large nut
(arrowed) - to prevent the damper rod from
turning, place an Allen key in the end of
the shaft6.3 Following the tool manufacturer’s
instructions, fit the spring compressor to
the spring, and compress it sufficiently to
relieve all pressure from the suspension
support
6.11 Make sure you align the end of the
coil spring with the shoulder of the rubber
ring, and with the spring retainer
6.9 Loosen and remove the threaded
collar, and pull the old strut cartridge from
the strut housing - on all struts except
gas-charged units, pour the old oil from
the strut housing. (Spring should have
been removed first!)
10
Page 155 of 228
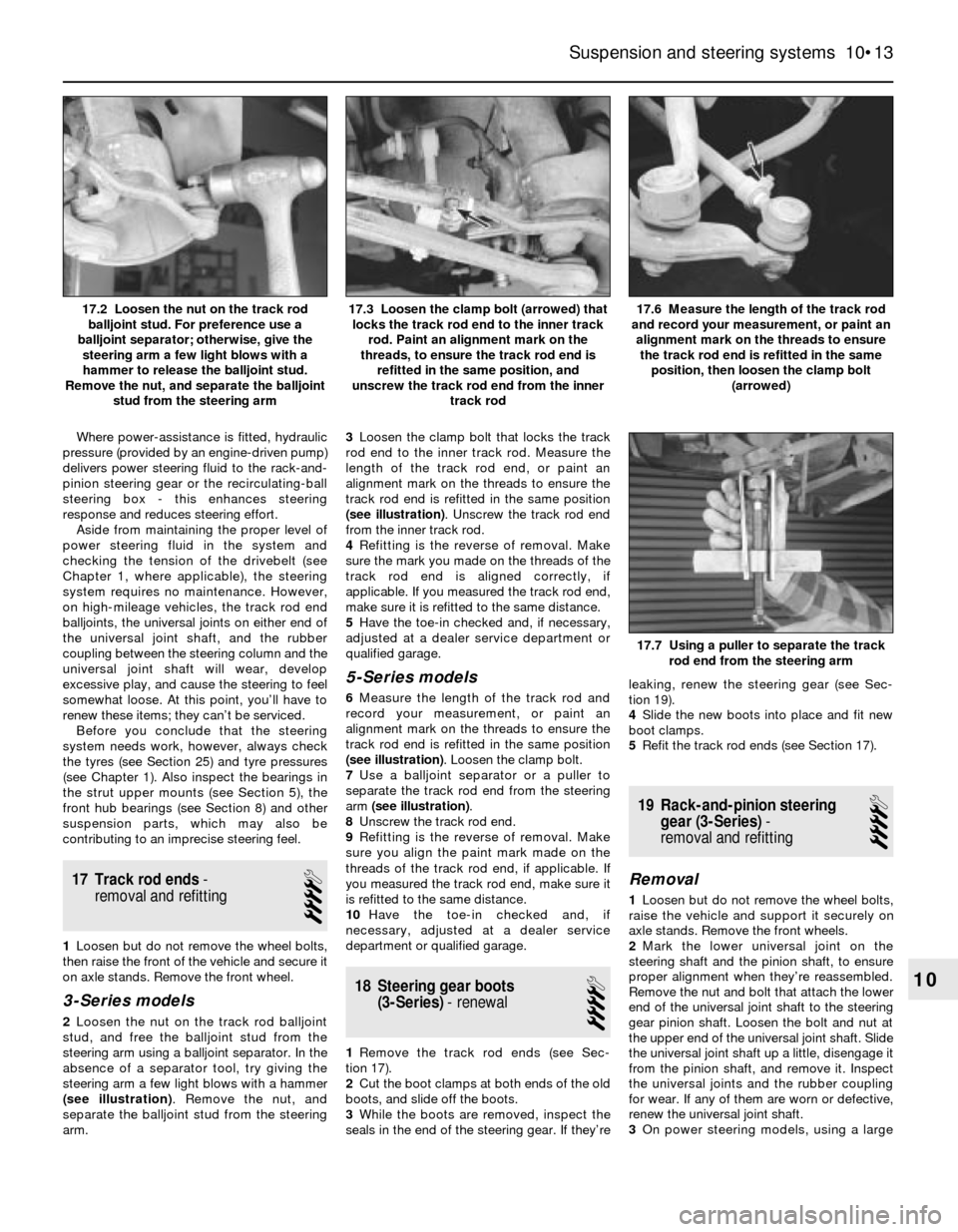
Where power-assistance is fitted, hydraulic
pressure (provided by an engine-driven pump)
delivers power steering fluid to the rack-and-
pinion steering gear or the recirculating-ball
steering box - this enhances steering
response and reduces steering effort.
Aside from maintaining the proper level of
power steering fluid in the system and
checking the tension of the drivebelt (see
Chapter 1, where applicable), the steering
system requires no maintenance. However,
on high-mileage vehicles, the track rod end
balljoints, the universal joints on either end of
the universal joint shaft, and the rubber
coupling between the steering column and the
universal joint shaft will wear, develop
excessive play, and cause the steering to feel
somewhat loose. At this point, you’ll have to
renew these items; they can’t be serviced.
Before you conclude that the steering
system needs work, however, always check
the tyres (see Section 25) and tyre pressures
(see Chapter 1). Also inspect the bearings in
the strut upper mounts (see Section 5), the
front hub bearings (see Section 8) and other
suspension parts, which may also be
contributing to an imprecise steering feel.
17 Track rod ends-
removal and refitting
4
1Loosen but do not remove the wheel bolts,
then raise the front of the vehicle and secure it
on axle stands. Remove the front wheel.
3-Series models
2Loosen the nut on the track rod balljoint
stud, and free the balljoint stud from the
steering arm using a balljoint separator. In the
absence of a separator tool, try giving the
steering arm a few light blows with a hammer
(see illustration). Remove the nut, and
separate the balljoint stud from the steering
arm.3Loosen the clamp bolt that locks the track
rod end to the inner track rod. Measure the
length of the track rod end, or paint an
alignment mark on the threads to ensure the
track rod end is refitted in the same position
(see illustration). Unscrew the track rod end
from the inner track rod.
4Refitting is the reverse of removal. Make
sure the mark you made on the threads of the
track rod end is aligned correctly, if
applicable. If you measured the track rod end,
make sure it is refitted to the same distance.
5Have the toe-in checked and, if necessary,
adjusted at a dealer service department or
qualified garage.
5-Series models
6Measure the length of the track rod and
record your measurement, or paint an
alignment mark on the threads to ensure the
track rod end is refitted in the same position
(see illustration). Loosen the clamp bolt.
7Use a balljoint separator or a puller to
separate the track rod end from the steering
arm (see illustration).
8Unscrew the track rod end.
9Refitting is the reverse of removal. Make
sure you align the paint mark made on the
threads of the track rod end, if applicable. If
you measured the track rod end, make sure it
is refitted to the same distance.
10Have the toe-in checked and, if
necessary, adjusted at a dealer service
department or qualified garage.
18 Steering gear boots
(3-Series)- renewal
4
1Remove the track rod ends (see Sec-
tion 17).
2Cut the boot clamps at both ends of the old
boots, and slide off the boots.
3While the boots are removed, inspect the
seals in the end of the steering gear. If they’releaking, renew the steering gear (see Sec-
tion 19).
4Slide the new boots into place and fit new
boot clamps.
5Refit the track rod ends (see Section 17).
19 Rack-and-pinion steering
gear (3-Series)-
removal and refitting
4
Removal
1Loosen but do not remove the wheel bolts,
raise the vehicle and support it securely on
axle stands. Remove the front wheels.
2Mark the lower universal joint on the
steering shaft and the pinion shaft, to ensure
proper alignment when they’re reassembled.
Remove the nut and bolt that attach the lower
end of the universal joint shaft to the steering
gear pinion shaft. Loosen the bolt and nut at
the upper end of the universal joint shaft. Slide
the universal joint shaft up a little, disengage it
from the pinion shaft, and remove it. Inspect
the universal joints and the rubber coupling
for wear. If any of them are worn or defective,
renew the universal joint shaft.
3On power steering models, using a large
Suspension and steering systems 10•13
17.6 Measure the length of the track rod
and record your measurement, or paint an
alignment mark on the threads to ensure
the track rod end is refitted in the same
position, then loosen the clamp bolt
(arrowed)17.3 Loosen the clamp bolt (arrowed) that
locks the track rod end to the inner track
rod. Paint an alignment mark on the
threads, to ensure the track rod end is
refitted in the same position, and
unscrew the track rod end from the inner
track rod17.2 Loosen the nut on the track rod
balljoint stud. For preference use a
balljoint separator; otherwise, give the
steering arm a few light blows with a
hammer to release the balljoint stud.
Remove the nut, and separate the balljoint
stud from the steering arm
17.7 Using a puller to separate the track
rod end from the steering arm
10