fuse box BMW 3 SERIES 1983 E30 Workshop Manual
[x] Cancel search | Manufacturer: BMW, Model Year: 1983, Model line: 3 SERIES, Model: BMW 3 SERIES 1983 E30Pages: 228, PDF Size: 7.04 MB
Page 15 of 228
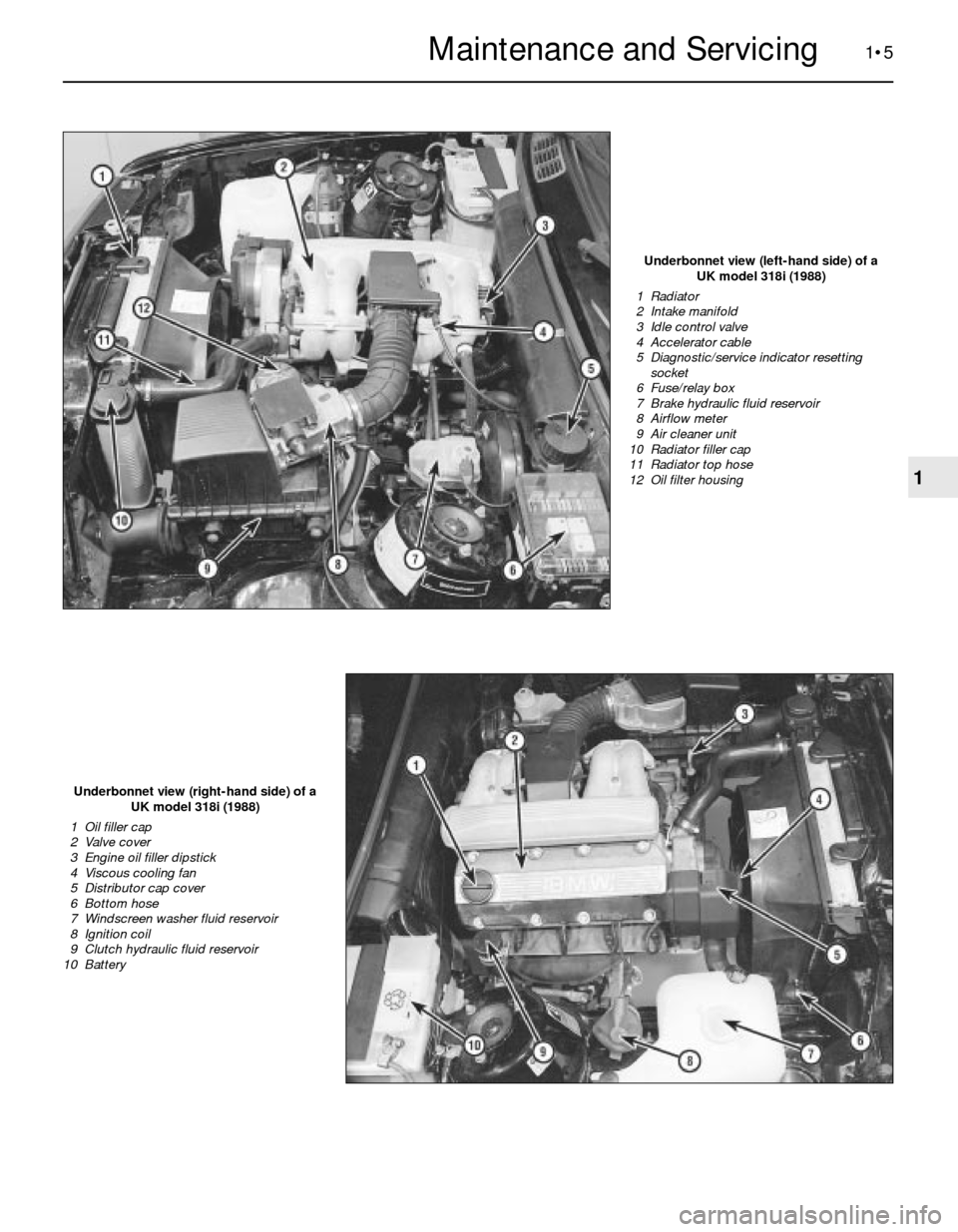
1•5
Underbonnet view (left-hand side) of a
UK model 318i (1988)
1 Radiator
2 Intake manifold
3 Idle control valve
4 Accelerator cable
5 Diagnostic/service indicator resetting
socket
6 Fuse/relay box
7 Brake hydraulic fluid reservoir
8 Airflow meter
9 Air cleaner unit
10 Radiator filler cap
11 Radiator top hose
12 Oil filter housing
Underbonnet view (right-hand side) of a
UK model 318i (1988)
1 Oil filler cap
2 Valve cover
3 Engine oil filler dipstick
4 Viscous cooling fan
5 Distributor cap cover
6 Bottom hose
7 Windscreen washer fluid reservoir
8 Ignition coil
9 Clutch hydraulic fluid reservoir
10 Battery
1
Maintenance and Servicing
Page 75 of 228
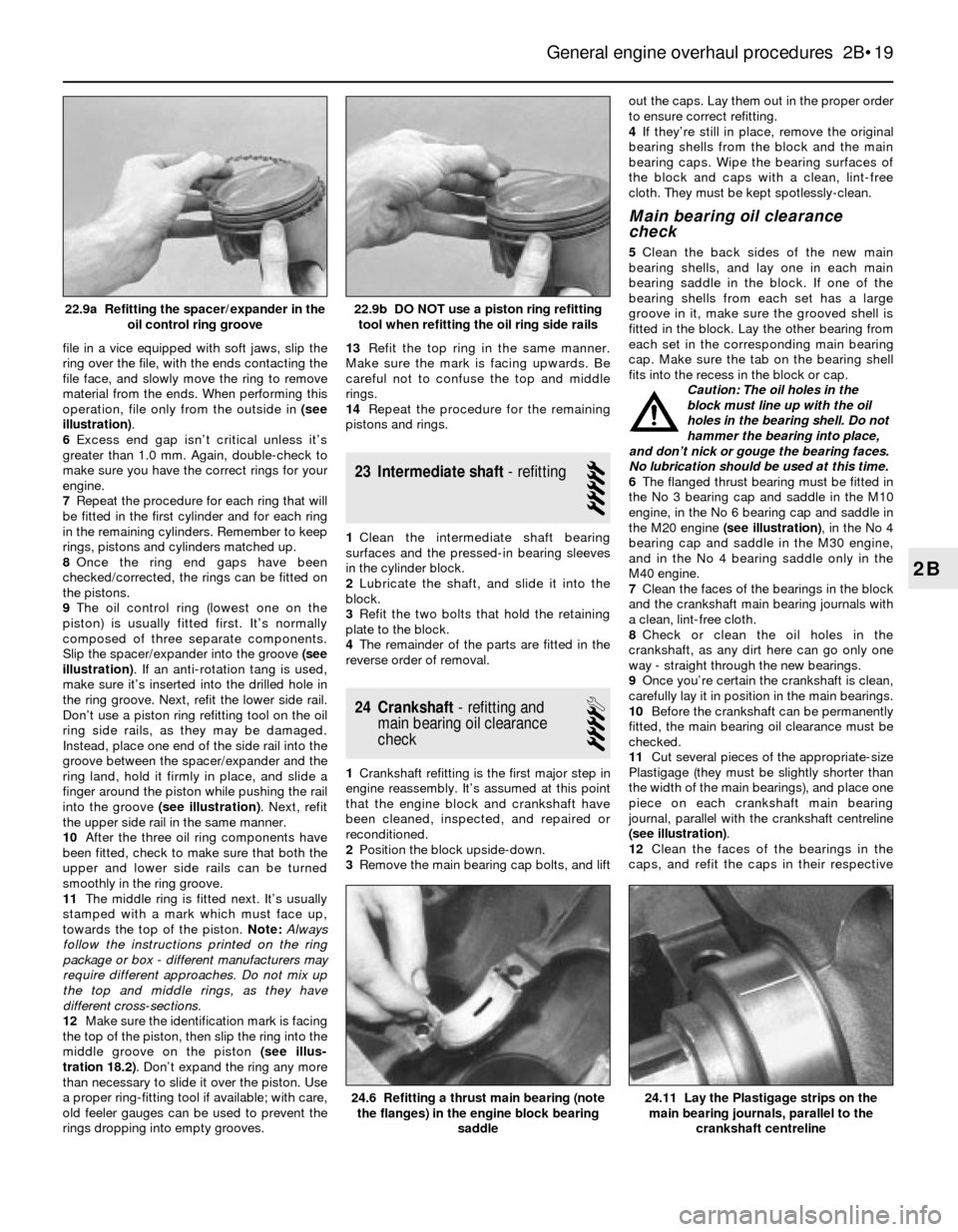
file in a vice equipped with soft jaws, slip the
ring over the file, with the ends contacting the
file face, and slowly move the ring to remove
material from the ends. When performing this
operation, file only from the outside in(see
illustration).
6Excess end gap isn’t critical unless it’s
greater than 1.0 mm. Again, double-check to
make sure you have the correct rings for your
engine.
7Repeat the procedure for each ring that will
be fitted in the first cylinder and for each ring
in the remaining cylinders. Remember to keep
rings, pistons and cylinders matched up.
8Once the ring end gaps have been
checked/corrected, the rings can be fitted on
the pistons.
9The oil control ring (lowest one on the
piston) is usually fitted first. It’s normally
composed of three separate components.
Slip the spacer/expander into the groove(see
illustration). If an anti-rotation tang is used,
make sure it’s inserted into the drilled hole in
the ring groove. Next, refit the lower side rail.
Don’t use a piston ring refitting tool on the oil
ring side rails, as they may be damaged.
Instead, place one end of the side rail into the
groove between the spacer/expander and the
ring land, hold it firmly in place, and slide a
finger around the piston while pushing the rail
into the groove(see illustration). Next, refit
the upper side rail in the same manner.
10After the three oil ring components have
been fitted, check to make sure that both the
upper and lower side rails can be turned
smoothly in the ring groove.
11The middle ring is fitted next. It’s usually
stamped with a mark which must face up,
towards the top of the piston. Note:Always
follow the instructions printed on the ring
package or box - different manufacturers may
require different approaches. Do not mix up
the top and middle rings, as they have
different cross-sections.
12Make sure the identification mark is facing
the top of the piston, then slip the ring into the
middle groove on the piston (see illus-
tration 18.2). Don’t expand the ring any more
than necessary to slide it over the piston. Use
a proper ring-fitting tool if available; with care,
old feeler gauges can be used to prevent the
rings dropping into empty grooves.13Refit the top ring in the same manner.
Make sure the mark is facing upwards. Be
careful not to confuse the top and middle
rings.
14Repeat the procedure for the remaining
pistons and rings.
23 Intermediate shaft- refitting
5
1Clean the intermediate shaft bearing
surfaces and the pressed-in bearing sleeves
in the cylinder block.
2Lubricate the shaft, and slide it into the
block.
3Refit the two bolts that hold the retaining
plate to the block.
4The remainder of the parts are fitted in the
reverse order of removal.
24 Crankshaft- refitting and
main bearing oil clearance
check
4
1Crankshaft refitting is the first major step in
engine reassembly. It’s assumed at this point
that the engine block and crankshaft have
been cleaned, inspected, and repaired or
reconditioned.
2Position the block upside-down.
3Remove the main bearing cap bolts, and liftout the caps. Lay them out in the proper order
to ensure correct refitting.
4If they’re still in place, remove the original
bearing shells from the block and the main
bearing caps. Wipe the bearing surfaces of
the block and caps with a clean, lint-free
cloth. They must be kept spotlessly-clean.
Main bearing oil clearance
check
5Clean the back sides of the new main
bearing shells, and lay one in each main
bearing saddle in the block. If one of the
bearing shells from each set has a large
groove in it, make sure the grooved shell is
fitted in the block. Lay the other bearing from
each set in the corresponding main bearing
cap. Make sure the tab on the bearing shell
fits into the recess in the block or cap.
Caution: The oil holes in the
block must line up with the oil
holes in the bearing shell. Do not
hammer the bearing into place,
and don’t nick or gouge the bearing faces.
No lubrication should be used at this time.
6The flanged thrust bearing must be fitted in
the No 3 bearing cap and saddle in the M10
engine, in the No 6 bearing cap and saddle in
the M20 engine (see illustration), in the No 4
bearing cap and saddle in the M30 engine,
and in the No 4 bearing saddle only in the
M40 engine.
7Clean the faces of the bearings in the block
and the crankshaft main bearing journals with
a clean, lint-free cloth.
8Check or clean the oil holes in the
crankshaft, as any dirt here can go only one
way - straight through the new bearings.
9Once you’re certain the crankshaft is clean,
carefully lay it in position in the main bearings.
10Before the crankshaft can be permanently
fitted, the main bearing oil clearance must be
checked.
11Cut several pieces of the appropriate-size
Plastigage (they must be slightly shorter than
the width of the main bearings), and place one
piece on each crankshaft main bearing
journal, parallel with the crankshaft centreline
(see illustration).
12Clean the faces of the bearings in the
caps, and refit the caps in their respective
General engine overhaul procedures 2B•19
22.9b DO NOT use a piston ring refitting
tool when refitting the oil ring side rails22.9a Refitting the spacer/expander in the
oil control ring groove
24.11 Lay the Plastigage strips on the
main bearing journals, parallel to the
crankshaft centreline24.6 Refitting a thrust main bearing (note
the flanges) in the engine block bearing
saddle
2B
Page 91 of 228
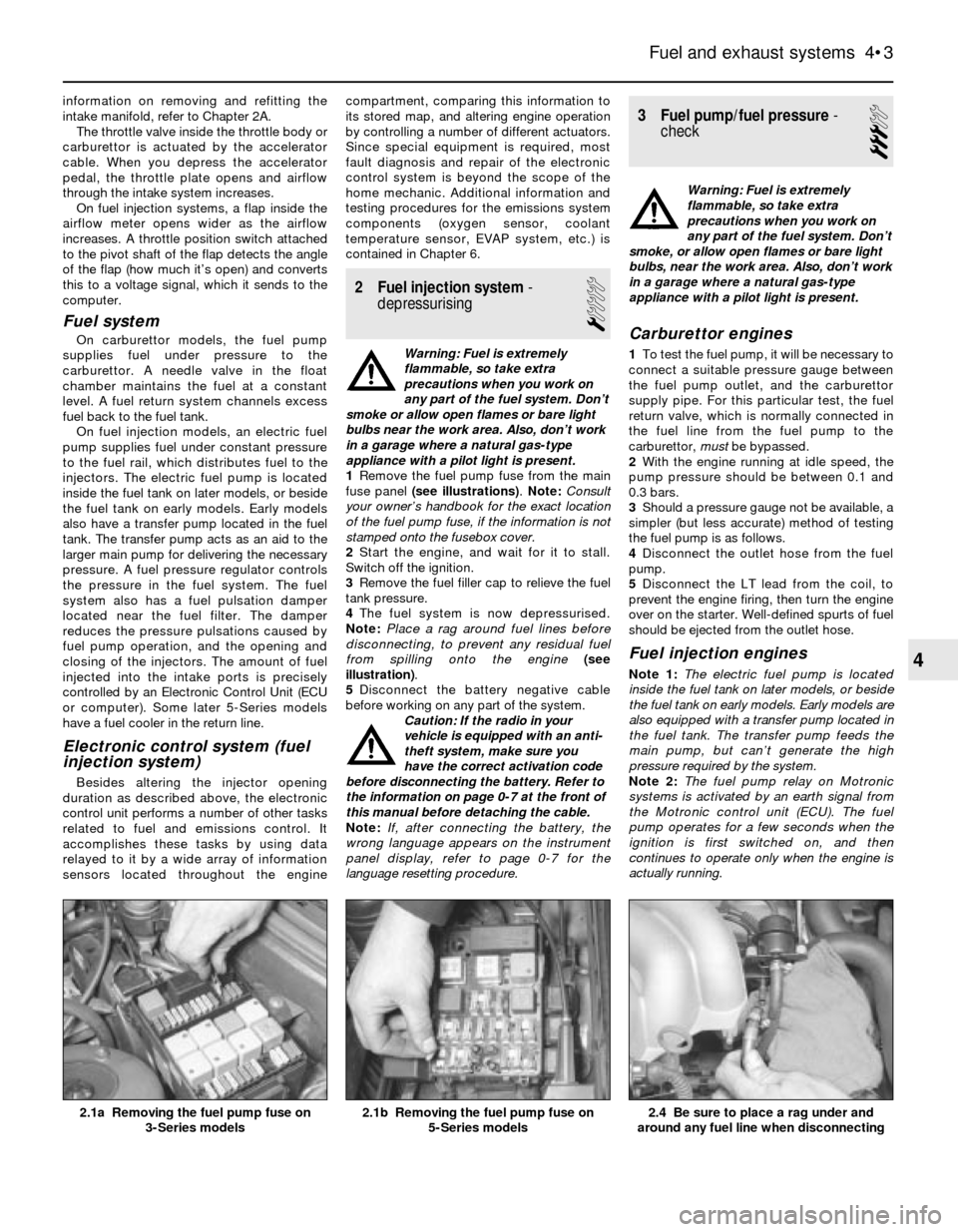
information on removing and refitting the
intake manifold, refer to Chapter 2A.
The throttle valve inside the throttle body or
carburettor is actuated by the accelerator
cable. When you depress the accelerator
pedal, the throttle plate opens and airflow
through the intake system increases.
On fuel injection systems, a flap inside the
airflow meter opens wider as the airflow
increases. A throttle position switch attached
to the pivot shaft of the flap detects the angle
of the flap (how much it’s open) and converts
this to a voltage signal, which it sends to the
computer.
Fuel system
On carburettor models, the fuel pump
supplies fuel under pressure to the
carburettor. A needle valve in the float
chamber maintains the fuel at a constant
level. A fuel return system channels excess
fuel back to the fuel tank.
On fuel injection models, an electric fuel
pump supplies fuel under constant pressure
to the fuel rail, which distributes fuel to the
injectors. The electric fuel pump is located
inside the fuel tank on later models, or beside
the fuel tank on early models. Early models
also have a transfer pump located in the fuel
tank. The transfer pump acts as an aid to the
larger main pump for delivering the necessary
pressure. A fuel pressure regulator controls
the pressure in the fuel system. The fuel
system also has a fuel pulsation damper
located near the fuel filter. The damper
reduces the pressure pulsations caused by
fuel pump operation, and the opening and
closing of the injectors. The amount of fuel
injected into the intake ports is precisely
controlled by an Electronic Control Unit (ECU
or computer). Some later 5-Series models
have a fuel cooler in the return line.
Electronic control system (fuel
injection system)
Besides altering the injector opening
duration as described above, the electronic
control unit performs a number of other tasks
related to fuel and emissions control. It
accomplishes these tasks by using data
relayed to it by a wide array of information
sensors located throughout the enginecompartment, comparing this information to
its stored map, and altering engine operation
by controlling a number of different actuators.
Since special equipment is required, most
fault diagnosis and repair of the electronic
control system is beyond the scope of the
home mechanic. Additional information and
testing procedures for the emissions system
components (oxygen sensor, coolant
temperature sensor, EVAP system, etc.) is
contained in Chapter 6.
2 Fuel injection system-
depressurising
1
Warning: Fuel is extremely
flammable, so take extra
precautions when you work on
any part of the fuel system. Don’t
smoke or allow open flames or bare light
bulbs near the work area. Also, don’t work
in a garage where a natural gas-type
appliance with a pilot light is present.
1Remove the fuel pump fuse from the main
fuse panel (see illustrations). Note:Consult
your owner’s handbook for the exact location
of the fuel pump fuse, if the information is not
stamped onto the fusebox cover.
2Start the engine, and wait for it to stall.
Switch off the ignition.
3Remove the fuel filler cap to relieve the fuel
tank pressure.
4The fuel system is now depressurised.
Note:Place a rag around fuel lines before
disconnecting, to prevent any residual fuel
from spilling onto the engine(see
illustration).
5Disconnect the battery negative cable
before working on any part of the system.
Caution: If the radio in your
vehicle is equipped with an anti-
theft system, make sure you
have the correct activation code
before disconnecting the battery. Refer to
the information on page 0-7 at the front of
this manual before detaching the cable.
Note: If, after connecting the battery, the
wrong language appears on the instrument
panel display, refer to page 0-7 for the
language resetting procedure.
3 Fuel pump/fuel pressure-
check
3
Warning: Fuel is extremely
flammable, so take extra
precautions when you work on
any part of the fuel system. Don’t
smoke, or allow open flames or bare light
bulbs, near the work area. Also, don’t work
in a garage where a natural gas-type
appliance with a pilot light is present.
Carburettor engines
1To test the fuel pump, it will be necessary to
connect a suitable pressure gauge between
the fuel pump outlet, and the carburettor
supply pipe. For this particular test, the fuel
return valve, which is normally connected in
the fuel line from the fuel pump to the
carburettor, mustbe bypassed.
2With the engine running at idle speed, the
pump pressure should be between 0.1 and
0.3 bars.
3Should a pressure gauge not be available, a
simpler (but less accurate) method of testing
the fuel pump is as follows.
4Disconnect the outlet hose from the fuel
pump.
5Disconnect the LT lead from the coil, to
prevent the engine firing, then turn the engine
over on the starter. Well-defined spurts of fuel
should be ejected from the outlet hose.
Fuel injection engines
Note 1:The electric fuel pump is located
inside the fuel tank on later models, or beside
the fuel tank on early models. Early models are
also equipped with a transfer pump located in
the fuel tank. The transfer pump feeds the
main pump, but can’t generate the high
pressure required by the system.
Note 2:The fuel pump relay on Motronic
systems is activated by an earth signal from
the Motronic control unit (ECU). The fuel
pump operates for a few seconds when the
ignition is first switched on, and then
continues to operate only when the engine is
actually running.
Fuel and exhaust systems 4•3
2.4 Be sure to place a rag under and
around any fuel line when disconnecting2.1b Removing the fuel pump fuse on
5-Series models2.1a Removing the fuel pump fuse on
3-Series models
4
Page 170 of 228
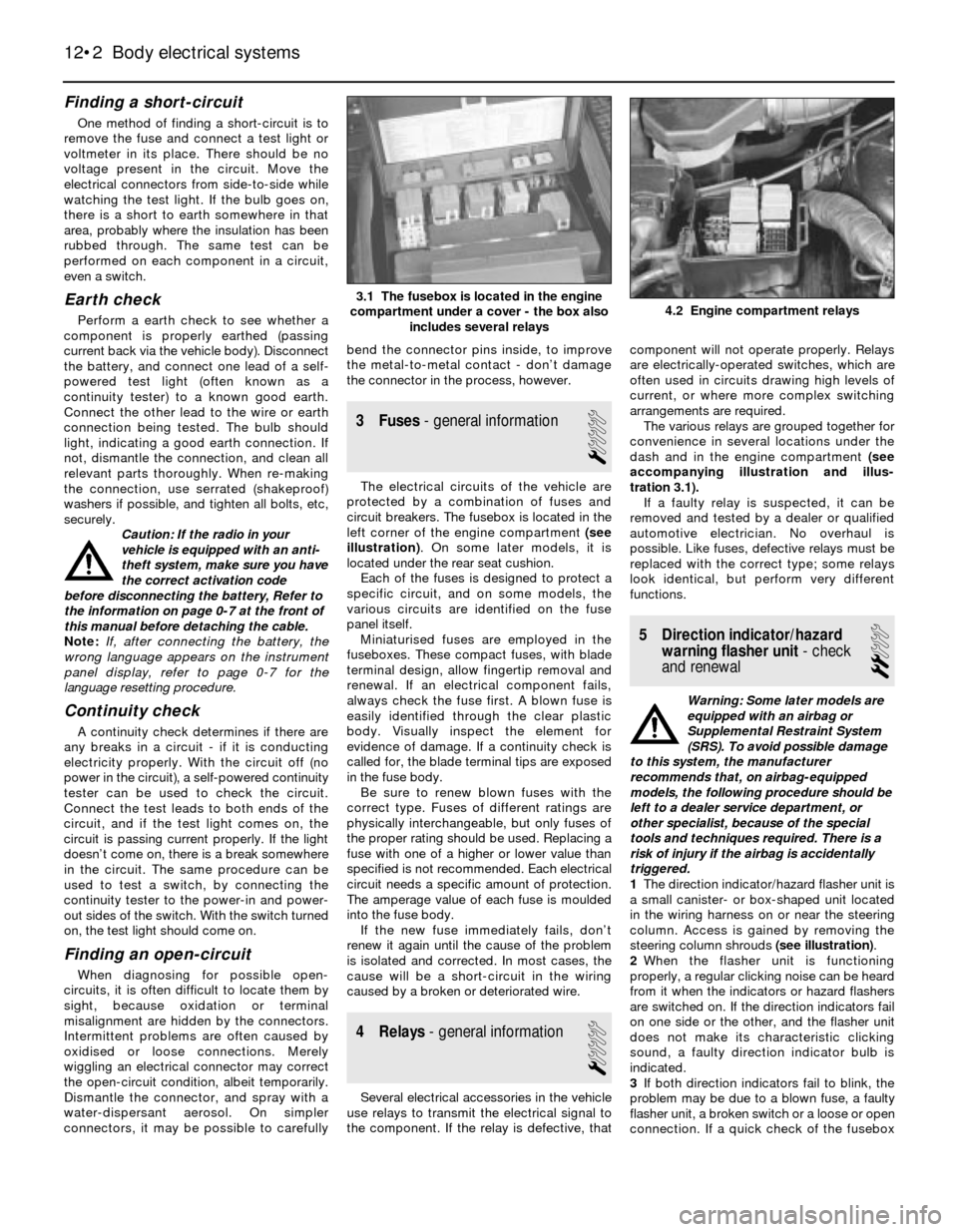
Finding a short-circuit
One method of finding a short-circuit is to
remove the fuse and connect a test light or
voltmeter in its place. There should be no
voltage present in the circuit. Move the
electrical connectors from side-to-side while
watching the test light. If the bulb goes on,
there is a short to earth somewhere in that
area, probably where the insulation has been
rubbed through. The same test can be
performed on each component in a circuit,
even a switch.
Earth check
Perform a earth check to see whether a
component is properly earthed (passing
current back via the vehicle body). Disconnect
the battery, and connect one lead of a self-
powered test light (often known as a
continuity tester) to a known good earth.
Connect the other lead to the wire or earth
connection being tested. The bulb should
light, indicating a good earth connection. If
not, dismantle the connection, and clean all
relevant parts thoroughly. When re-making
the connection, use serrated (shakeproof)
washers if possible, and tighten all bolts, etc,
securely.
Caution: If the radio in your
vehicle is equipped with an anti-
theft system, make sure you have
the correct activation code
before disconnecting the battery, Refer to
the information on page 0-7 at the front of
this manual before detaching the cable.
Note: If, after connecting the battery, the
wrong language appears on the instrument
panel display, refer to page 0-7 for the
language resetting procedure.
Continuity check
A continuity check determines if there are
any breaks in a circuit - if it is conducting
electricity properly. With the circuit off (no
power in the circuit), a self-powered continuity
tester can be used to check the circuit.
Connect the test leads to both ends of the
circuit, and if the test light comes on, the
circuit is passing current properly. If the light
doesn’t come on, there is a break somewhere
in the circuit. The same procedure can be
used to test a switch, by connecting the
continuity tester to the power-in and power-
out sides of the switch. With the switch turned
on, the test light should come on.
Finding an open-circuit
When diagnosing for possible open-
circuits, it is often difficult to locate them by
sight, because oxidation or terminal
misalignment are hidden by the connectors.
Intermittent problems are often caused by
oxidised or loose connections. Merely
wiggling an electrical connector may correct
the open-circuit condition, albeit temporarily.
Dismantle the connector, and spray with a
water-dispersant aerosol. On simpler
connectors, it may be possible to carefullybend the connector pins inside, to improve
the metal-to-metal contact - don’t damage
the connector in the process, however.
3 Fuses- general information
1
The electrical circuits of the vehicle are
protected by a combination of fuses and
circuit breakers. The fusebox is located in the
left corner of the engine compartment (see
illustration). On some later models, it is
located under the rear seat cushion.
Each of the fuses is designed to protect a
specific circuit, and on some models, the
various circuits are identified on the fuse
panel itself.
Miniaturised fuses are employed in the
fuseboxes. These compact fuses, with blade
terminal design, allow fingertip removal and
renewal. If an electrical component fails,
always check the fuse first. A blown fuse is
easily identified through the clear plastic
body. Visually inspect the element for
evidence of damage. If a continuity check is
called for, the blade terminal tips are exposed
in the fuse body.
Be sure to renew blown fuses with the
correct type. Fuses of different ratings are
physically interchangeable, but only fuses of
the proper rating should be used. Replacing a
fuse with one of a higher or lower value than
specified is not recommended. Each electrical
circuit needs a specific amount of protection.
The amperage value of each fuse is moulded
into the fuse body.
If the new fuse immediately fails, don’t
renew it again until the cause of the problem
is isolated and corrected. In most cases, the
cause will be a short-circuit in the wiring
caused by a broken or deteriorated wire.
4 Relays- general information
1
Several electrical accessories in the vehicle
use relays to transmit the electrical signal to
the component. If the relay is defective, thatcomponent will not operate properly. Relays
are electrically-operated switches, which are
often used in circuits drawing high levels of
current, or where more complex switching
arrangements are required.
The various relays are grouped together for
convenience in several locations under the
dash and in the engine compartment (see
accompanying illustration and illus-
tration 3.1).
If a faulty relay is suspected, it can be
removed and tested by a dealer or qualified
automotive electrician. No overhaul is
possible. Like fuses, defective relays must be
replaced with the correct type; some relays
look identical, but perform very different
functions.
5 Direction indicator/hazard
warning flasher unit- check
and renewal
2
Warning: Some later models are
equipped with an airbag or
Supplemental Restraint System
(SRS). To avoid possible damage
to this system, the manufacturer
recommends that, on airbag-equipped
models, the following procedure should be
left to a dealer service department, or
other specialist, because of the special
tools and techniques required. There is a
risk of injury if the airbag is accidentally
triggered.
1The direction indicator/hazard flasher unit is
a small canister- or box-shaped unit located
in the wiring harness on or near the steering
column. Access is gained by removing the
steering column shrouds (see illustration).
2When the flasher unit is functioning
properly, a regular clicking noise can be heard
from it when the indicators or hazard flashers
are switched on. If the direction indicators fail
on one side or the other, and the flasher unit
does not make its characteristic clicking
sound, a faulty direction indicator bulb is
indicated.
3If both direction indicators fail to blink, the
problem may be due to a blown fuse, a faulty
flasher unit, a broken switch or a loose or open
connection. If a quick check of the fusebox
12•2 Body electrical systems
4.2 Engine compartment relays3.1 The fusebox is located in the engine
compartment under a cover - the box also
includes several relays
Page 226 of 228
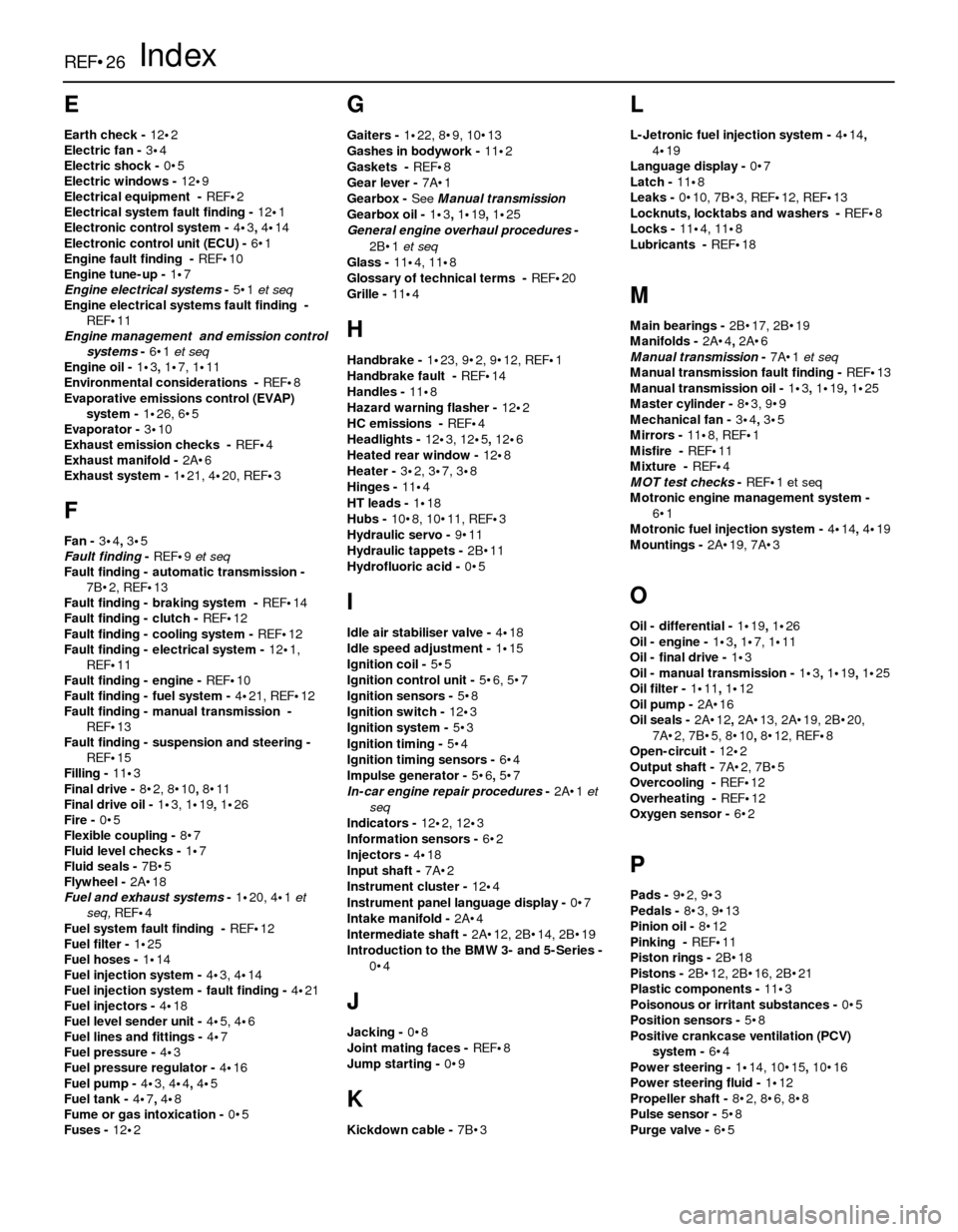
REF•26Index
E
Earth check - 12•2
Electric fan - 3•4
Electric shock - 0•5
Electric windows - 12•9
Electrical equipment - REF•2
Electrical system fault finding - 12•1
Electronic control system - 4•3, 4•14
Electronic control unit (ECU) - 6•1
Engine fault finding - REF•10
Engine tune-up - 1•7
Engine electrical systems- 5•1et seq
Engine electrical systems fault finding -
REF•11
Engine management and emission control
systems- 6•1et seq
Engine oil - 1•3, 1•7, 1•11
Environmental considerations - REF•8
Evaporative emissions control (EVAP)
system - 1•26, 6•5
Evaporator - 3•10
Exhaust emission checks - REF•4
Exhaust manifold - 2A•6
Exhaust system - 1•21, 4•20, REF•3
F
Fan - 3•4, 3•5
Fault finding- REF•9et seq
Fault finding - automatic transmission -
7B•2, REF•13
Fault finding - braking system - REF•14
Fault finding - clutch - REF•12
Fault finding - cooling system - REF•12
Fault finding - electrical system - 12•1,
REF•11
Fault finding - engine - REF•10
Fault finding - fuel system - 4•21, REF•12
Fault finding - manual transmission -
REF•13
Fault finding - suspension and steering -
REF•15
Filling - 11•3
Final drive - 8•2, 8•10, 8•11
Final drive oil - 1•3, 1•19, 1•26
Fire - 0•5
Flexible coupling - 8•7
Fluid level checks - 1•7
Fluid seals - 7B•5
Flywheel - 2A•18
Fuel and exhaust systems- 1•20, 4•1et
seq,REF•4
Fuel system fault finding - REF•12
Fuel filter - 1•25
Fuel hoses - 1•14
Fuel injection system - 4•3, 4•14
Fuel injection system - fault finding - 4•21
Fuel injectors - 4•18
Fuel level sender unit - 4•5, 4•6
Fuel lines and fittings - 4•7
Fuel pressure - 4•3
Fuel pressure regulator - 4•16
Fuel pump - 4•3, 4•4, 4•5
Fuel tank - 4•7, 4•8
Fume or gas intoxication - 0•5
Fuses - 12•2
G
Gaiters - 1•22, 8•9, 10•13
Gashes in bodywork - 11•2
Gaskets - REF•8
Gear lever - 7A•1
Gearbox - SeeManual transmission
Gearbox oil - 1•3, 1•19, 1•25
General engine overhaul procedures-
2B•1et seq
Glass - 11•4, 11•8
Glossary of technical terms - REF•20
Grille - 11•4
H
Handbrake - 1•23, 9•2, 9•12, REF•1
Handbrake fault - REF•14
Handles - 11•8
Hazard warning flasher - 12•2
HC emissions - REF•4
Headlights - 12•3, 12•5, 12•6
Heated rear window - 12•8
Heater - 3•2, 3•7, 3•8
Hinges - 11•4
HT leads - 1•18
Hubs - 10•8, 10•11, REF•3
Hydraulic servo - 9•11
Hydraulic tappets - 2B•11
Hydrofluoric acid - 0•5
I
Idle air stabiliser valve - 4•18
Idle speed adjustment - 1•15
Ignition coil - 5•5
Ignition control unit - 5•6, 5•7
Ignition sensors - 5•8
Ignition switch - 12•3
Ignition system - 5•3
Ignition timing - 5•4
Ignition timing sensors - 6•4
Impulse generator - 5•6, 5•7
In-car engine repair procedures- 2A•1et
seq
Indicators - 12•2, 12•3
Information sensors - 6•2
Injectors - 4•18
Input shaft - 7A•2
Instrument cluster - 12•4
Instrument panel language display - 0•7
Intake manifold - 2A•4
Intermediate shaft - 2A•12, 2B•14, 2B•19
Introduction to the BMW 3- and 5-Series -
0•4
J
Jacking - 0•8
Joint mating faces - REF•8
Jump starting - 0•9
K
Kickdown cable - 7B•3
L
L-Jetronic fuel injection system - 4•14,
4•19
Language display - 0•7
Latch - 11•8
Leaks - 0•10, 7B•3, REF•12, REF•13
Locknuts, locktabs and washers - REF•8
Locks - 11•4, 11•8
Lubricants - REF•18
M
Main bearings - 2B•17, 2B•19
Manifolds - 2A•4, 2A•6
Manual transmission- 7A•1et seq
Manual transmission fault finding - REF•13
Manual transmission oil - 1•3, 1•19, 1•25
Master cylinder - 8•3, 9•9
Mechanical fan - 3•4, 3•5
Mirrors - 11•8, REF•1
Misfire - REF•11
Mixture - REF•4
MOT test checks- REF•1 et seq
Motronic engine management system -
6•1
Motronic fuel injection system - 4•14, 4•19
Mountings - 2A•19, 7A•3
O
Oil - differential - 1•19, 1•26
Oil - engine - 1•3, 1•7, 1•11
Oil - final drive - 1•3
Oil - manual transmission - 1•3, 1•19, 1•25
Oil filter - 1•11, 1•12
Oil pump - 2A•16
Oil seals - 2A•12, 2A•13, 2A•19, 2B•20,
7A•2, 7B•5, 8•10, 8•12, REF•8
Open-circuit - 12•2
Output shaft - 7A•2, 7B•5
Overcooling - REF•12
Overheating - REF•12
Oxygen sensor - 6•2
P
Pads - 9•2, 9•3
Pedals - 8•3, 9•13
Pinion oil - 8•12
Pinking - REF•11
Piston rings - 2B•18
Pistons - 2B•12, 2B•16, 2B•21
Plastic components - 11•3
Poisonous or irritant substances - 0•5
Position sensors - 5•8
Positive crankcase ventilation (PCV)
system - 6•4
Power steering - 1•14, 10•15, 10•16
Power steering fluid - 1•12
Propeller shaft - 8•2, 8•6, 8•8
Pulse sensor - 5•8
Purge valve - 6•5