width BMW 3 SERIES 1983 E30 Workshop Manual
[x] Cancel search | Manufacturer: BMW, Model Year: 1983, Model line: 3 SERIES, Model: BMW 3 SERIES 1983 E30Pages: 228, PDF Size: 7.04 MB
Page 25 of 228
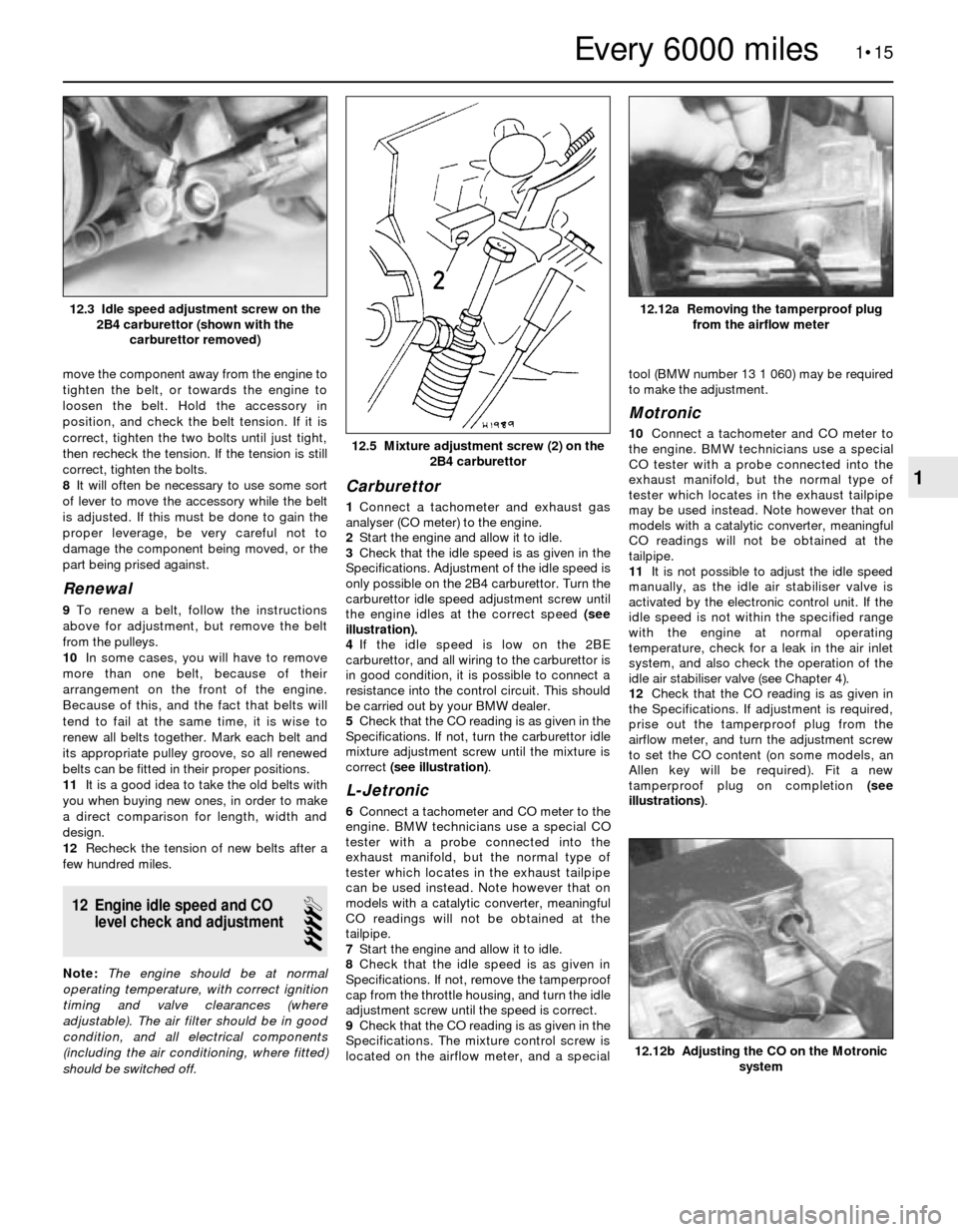
move the component away from the engine to
tighten the belt, or towards the engine to
loosen the belt. Hold the accessory in
position, and check the belt tension. If it is
correct, tighten the two bolts until just tight,
then recheck the tension. If the tension is still
correct, tighten the bolts.
8It will often be necessary to use some sort
of lever to move the accessory while the belt
is adjusted. If this must be done to gain the
proper leverage, be very careful not to
damage the component being moved, or the
part being prised against.
Renewal
9To renew a belt, follow the instructions
above for adjustment, but remove the belt
from the pulleys.
10In some cases, you will have to remove
more than one belt, because of their
arrangement on the front of the engine.
Because of this, and the fact that belts will
tend to fail at the same time, it is wise to
renew all belts together. Mark each belt and
its appropriate pulley groove, so all renewed
belts can be fitted in their proper positions.
11It is a good idea to take the old belts with
you when buying new ones, in order to make
a direct comparison for length, width and
design.
12Recheck the tension of new belts after a
few hundred miles.
12 Engine idle speed and CO
level check and adjustment
4
Note:The engine should be at normal
operating temperature, with correct ignition
timing and valve clearances (where
adjustable). The air filter should be in good
condition, and all electrical components
(including the air conditioning, where fitted)
should be switched off.
Carburettor
1Connect a tachometer and exhaust gas
analyser (CO meter) to the engine.
2Start the engine and allow it to idle.
3Check that the idle speed is as given in the
Specifications. Adjustment of the idle speed is
only possible on the 2B4 carburettor. Turn the
carburettor idle speed adjustment screw until
the engine idles at the correct speed (see
illustration).
4If the idle speed is low on the 2BE
carburettor, and all wiring to the carburettor is
in good condition, it is possible to connect a
resistance into the control circuit. This should
be carried out by your BMW dealer.
5Check that the CO reading is as given in the
Specifications. If not, turn the carburettor idle
mixture adjustment screw until the mixture is
correct (see illustration).
L-Jetronic
6Connect a tachometer and CO meter to the
engine. BMW technicians use a special CO
tester with a probe connected into the
exhaust manifold, but the normal type of
tester which locates in the exhaust tailpipe
can be used instead. Note however that on
models with a catalytic converter, meaningful
CO readings will not be obtained at the
tailpipe.
7Start the engine and allow it to idle.
8Check that the idle speed is as given in
Specifications. If not, remove the tamperproof
cap from the throttle housing, and turn the idle
adjustment screw until the speed is correct.
9Check that the CO reading is as given in the
Specifications. The mixture control screw is
located on the airflow meter, and a specialtool (BMW number 13 1 060) may be required
to make the adjustment.
Motronic
10Connect a tachometer and CO meter to
the engine. BMW technicians use a special
CO tester with a probe connected into the
exhaust manifold, but the normal type of
tester which locates in the exhaust tailpipe
may be used instead. Note however that on
models with a catalytic converter, meaningful
CO readings will not be obtained at the
tailpipe.
11It is not possible to adjust the idle speed
manually, as the idle air stabiliser valve is
activated by the electronic control unit. If the
idle speed is not within the specified range
with the engine at normal operating
temperature, check for a leak in the air inlet
system, and also check the operation of the
idle air stabiliser valve (see Chapter 4).
12Check that the CO reading is as given in
the Specifications. If adjustment is required,
prise out the tamperproof plug from the
airflow meter, and turn the adjustment screw
to set the CO content (on some models, an
Allen key will be required). Fit a new
tamperproof plug on completion (see
illustrations).
1•15
12.12a Removing the tamperproof plug
from the airflow meter
12.5 Mixture adjustment screw (2) on the
2B4 carburettor
12.3 Idle speed adjustment screw on the
2B4 carburettor (shown with the
carburettor removed)
12.12b Adjusting the CO on the Motronic
system
1
Every 6000 miles
Page 57 of 228
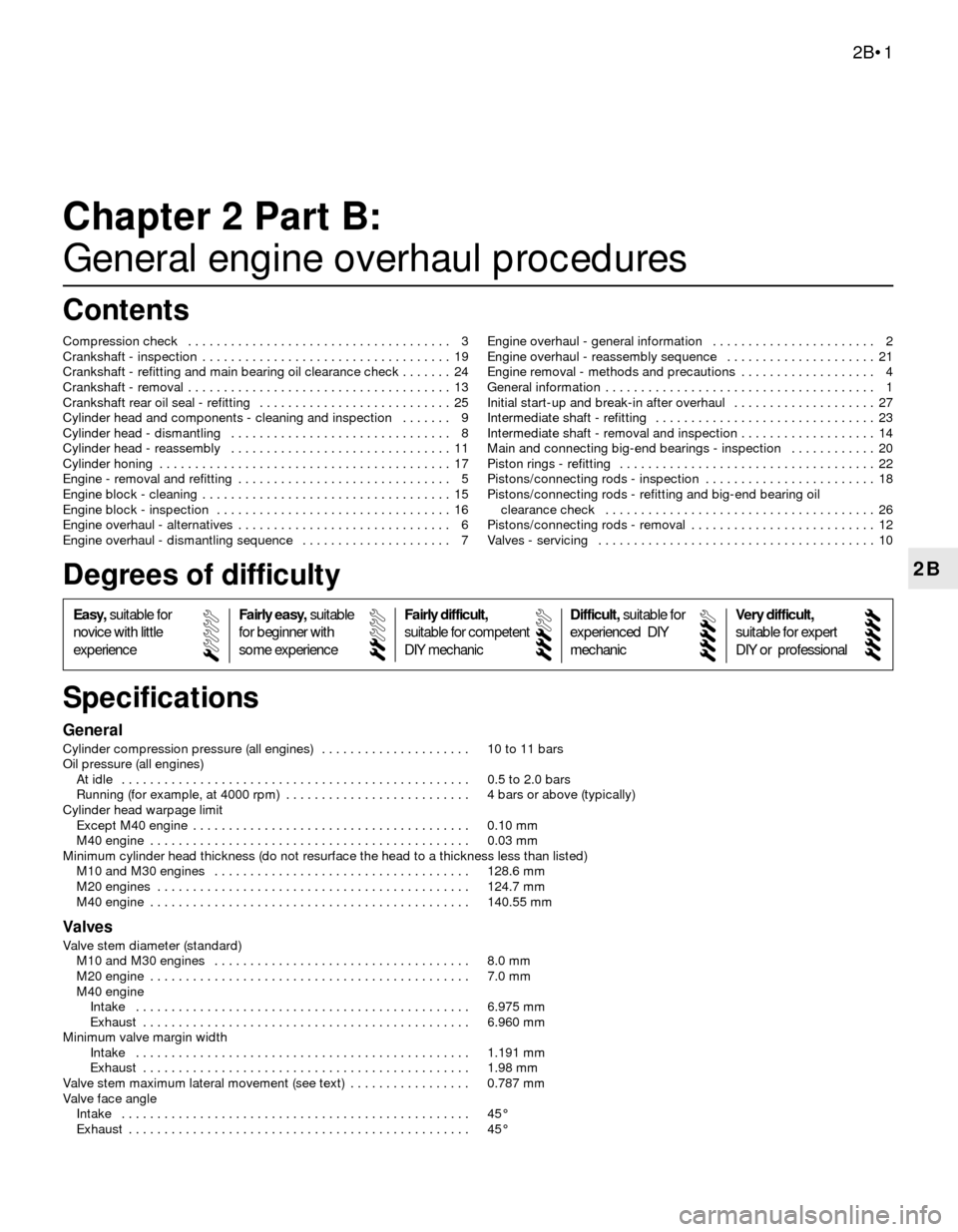
2B
General
Cylinder compression pressure (all engines) . . . . . . . . . . . . . . . . . . . . . 10 to 11 bars
Oil pressure (all engines)
At idle . . . . . . . . . . . . . . . . . . . . . . . . . . . . . . . . . . . . . . . . . . . . . . . . . 0.5 to 2.0 bars
Running (for example, at 4000 rpm) . . . . . . . . . . . . . . . . . . . . . . . . . . 4 bars or above (typically)
Cylinder head warpage limit
Except M40 engine . . . . . . . . . . . . . . . . . . . . . . . . . . . . . . . . . . . . . . . 0.10 mm
M40 engine . . . . . . . . . . . . . . . . . . . . . . . . . . . . . . . . . . . . . . . . . . . . . 0.03 mm
Minimum cylinder head thickness (do not resurface the head to a thickness less than listed)
M10 and M30 engines . . . . . . . . . . . . . . . . . . . . . . . . . . . . . . . . . . . . 128.6 mm
M20 engines . . . . . . . . . . . . . . . . . . . . . . . . . . . . . . . . . . . . . . . . . . . . 124.7 mm
M40 engine . . . . . . . . . . . . . . . . . . . . . . . . . . . . . . . . . . . . . . . . . . . . . 140.55 mm
Valves
Valve stem diameter (standard)
M10 and M30 engines . . . . . . . . . . . . . . . . . . . . . . . . . . . . . . . . . . . . 8.0 mm
M20 engine . . . . . . . . . . . . . . . . . . . . . . . . . . . . . . . . . . . . . . . . . . . . . 7.0 mm
M40 engine
Intake . . . . . . . . . . . . . . . . . . . . . . . . . . . . . . . . . . . . . . . . . . . . . . . 6.975 mm
Exhaust . . . . . . . . . . . . . . . . . . . . . . . . . . . . . . . . . . . . . . . . . . . . . . 6.960 mm
Minimum valve margin width
Intake . . . . . . . . . . . . . . . . . . . . . . . . . . . . . . . . . . . . . . . . . . . . . . . 1.191 mm
Exhaust . . . . . . . . . . . . . . . . . . . . . . . . . . . . . . . . . . . . . . . . . . . . . . 1.98 mm
Valve stem maximum lateral movement (see text) . . . . . . . . . . . . . . . . . 0.787 mm
Valve face angle
Intake . . . . . . . . . . . . . . . . . . . . . . . . . . . . . . . . . . . . . . . . . . . . . . . . . 45°
Exhaust . . . . . . . . . . . . . . . . . . . . . . . . . . . . . . . . . . . . . . . . . . . . . . . . 45°
Chapter 2 Part B:
General engine overhaul procedures
Compression check . . . . . . . . . . . . . . . . . . . . . . . . . . . . . . . . . . . . . 3
Crankshaft - inspection . . . . . . . . . . . . . . . . . . . . . . . . . . . . . . . . . . . 19
Crankshaft - refitting and main bearing oil clearance check . . . . . . . 24
Crankshaft - removal . . . . . . . . . . . . . . . . . . . . . . . . . . . . . . . . . . . . . 13
Crankshaft rear oil seal - refitting . . . . . . . . . . . . . . . . . . . . . . . . . . . 25
Cylinder head and components - cleaning and inspection . . . . . . . 9
Cylinder head - dismantling . . . . . . . . . . . . . . . . . . . . . . . . . . . . . . . 8
Cylinder head - reassembly . . . . . . . . . . . . . . . . . . . . . . . . . . . . . . . 11
Cylinder honing . . . . . . . . . . . . . . . . . . . . . . . . . . . . . . . . . . . . . . . . . 17
Engine - removal and refitting . . . . . . . . . . . . . . . . . . . . . . . . . . . . . . 5
Engine block - cleaning . . . . . . . . . . . . . . . . . . . . . . . . . . . . . . . . . . . 15
Engine block - inspection . . . . . . . . . . . . . . . . . . . . . . . . . . . . . . . . . 16
Engine overhaul - alternatives . . . . . . . . . . . . . . . . . . . . . . . . . . . . . . 6
Engine overhaul - dismantling sequence . . . . . . . . . . . . . . . . . . . . . 7Engine overhaul - general information . . . . . . . . . . . . . . . . . . . . . . . 2
Engine overhaul - reassembly sequence . . . . . . . . . . . . . . . . . . . . . 21
Engine removal - methods and precautions . . . . . . . . . . . . . . . . . . . 4
General information . . . . . . . . . . . . . . . . . . . . . . . . . . . . . . . . . . . . . . 1
Initial start-up and break-in after overhaul . . . . . . . . . . . . . . . . . . . . 27
Intermediate shaft - refitting . . . . . . . . . . . . . . . . . . . . . . . . . . . . . . . 23
Intermediate shaft - removal and inspection . . . . . . . . . . . . . . . . . . . 14
Main and connecting big-end bearings - inspection . . . . . . . . . . . . 20
Piston rings - refitting . . . . . . . . . . . . . . . . . . . . . . . . . . . . . . . . . . . . 22
Pistons/connecting rods - inspection . . . . . . . . . . . . . . . . . . . . . . . . 18
Pistons/connecting rods - refitting and big-end bearing oil
clearance check . . . . . . . . . . . . . . . . . . . . . . . . . . . . . . . . . . . . . . 26
Pistons/connecting rods - removal . . . . . . . . . . . . . . . . . . . . . . . . . . 12
Valves - servicing . . . . . . . . . . . . . . . . . . . . . . . . . . . . . . . . . . . . . . . 10
2B•1
Easy,suitable for
novice with little
experienceFairly easy,suitable
for beginner with
some experienceFairly difficult,
suitable for competent
DIY mechanic
Difficult,suitable for
experienced DIY
mechanicVery difficult,
suitable for expert
DIY or professional
Degrees of difficulty
Specifications Contents
Page 66 of 228
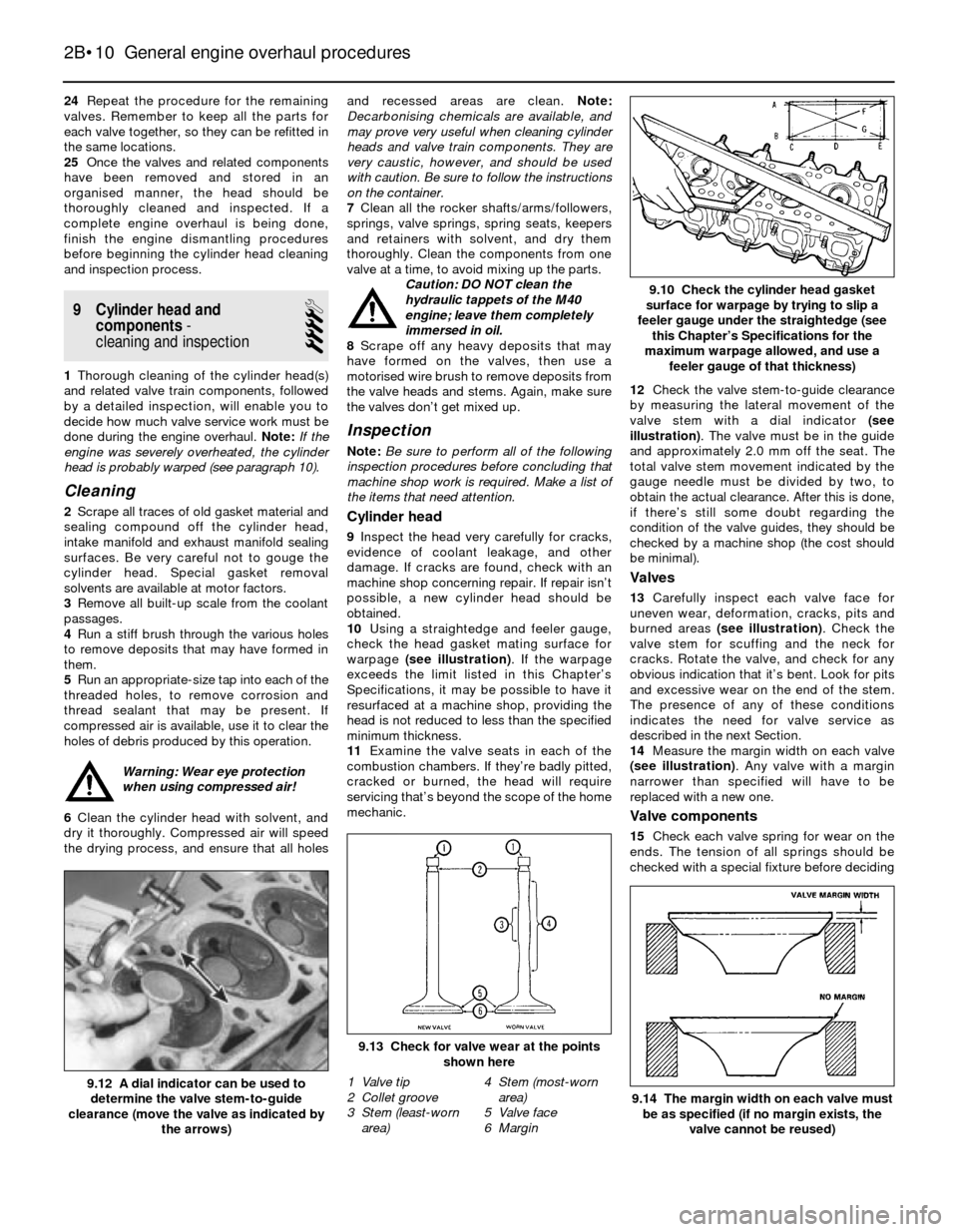
24Repeat the procedure for the remaining
valves. Remember to keep all the parts for
each valve together, so they can be refitted in
the same locations.
25Once the valves and related components
have been removed and stored in an
organised manner, the head should be
thoroughly cleaned and inspected. If a
complete engine overhaul is being done,
finish the engine dismantling procedures
before beginning the cylinder head cleaning
and inspection process.
9 Cylinder head and
components-
cleaning and inspection
4
1Thorough cleaning of the cylinder head(s)
and related valve train components, followed
by a detailed inspection, will enable you to
decide how much valve service work must be
done during the engine overhaul. Note: If the
engine was severely overheated, the cylinder
head is probably warped (see paragraph 10).
Cleaning
2Scrape all traces of old gasket material and
sealing compound off the cylinder head,
intake manifold and exhaust manifold sealing
surfaces. Be very careful not to gouge the
cylinder head. Special gasket removal
solvents are available at motor factors.
3Remove all built-up scale from the coolant
passages.
4Run a stiff brush through the various holes
to remove deposits that may have formed in
them.
5Run an appropriate-size tap into each of the
threaded holes, to remove corrosion and
thread sealant that may be present. If
compressed air is available, use it to clear the
holes of debris produced by this operation.
Warning: Wear eye protection
when using compressed air!
6Clean the cylinder head with solvent, and
dry it thoroughly. Compressed air will speed
the drying process, and ensure that all holesand recessed areas are clean. Note:
Decarbonising chemicals are available, and
may prove very useful when cleaning cylinder
heads and valve train components. They are
very caustic, however, and should be used
with caution. Be sure to follow the instructions
on the container.
7Clean all the rocker shafts/arms/followers,
springs, valve springs, spring seats, keepers
and retainers with solvent, and dry them
thoroughly. Clean the components from one
valve at a time, to avoid mixing up the parts.
Caution: DO NOT clean the
hydraulic tappets of the M40
engine; leave them completely
immersed in oil.
8Scrape off any heavy deposits that may
have formed on the valves, then use a
motorised wire brush to remove deposits from
the valve heads and stems. Again, make sure
the valves don’t get mixed up.
Inspection
Note: Be sure to perform all of the following
inspection procedures before concluding that
machine shop work is required. Make a list of
the items that need attention.
Cylinder head
9Inspect the head very carefully for cracks,
evidence of coolant leakage, and other
damage. If cracks are found, check with an
machine shop concerning repair. If repair isn’t
possible, a new cylinder head should be
obtained.
10Using a straightedge and feeler gauge,
check the head gasket mating surface for
warpage (see illustration). If the warpage
exceeds the limit listed in this Chapter’s
Specifications, it may be possible to have it
resurfaced at a machine shop, providing the
head is not reduced to less than the specified
minimum thickness.
11Examine the valve seats in each of the
combustion chambers. If they’re badly pitted,
cracked or burned, the head will require
servicing that’s beyond the scope of the home
mechanic.12Check the valve stem-to-guide clearance
by measuring the lateral movement of the
valve stem with a dial indicator (see
illustration). The valve must be in the guide
and approximately 2.0 mm off the seat. The
total valve stem movement indicated by the
gauge needle must be divided by two, to
obtain the actual clearance. After this is done,
if there’s still some doubt regarding the
condition of the valve guides, they should be
checked by a machine shop (the cost should
be minimal).
Valves
13Carefully inspect each valve face for
uneven wear, deformation, cracks, pits and
burned areas (see illustration). Check the
valve stem for scuffing and the neck for
cracks. Rotate the valve, and check for any
obvious indication that it’s bent. Look for pits
and excessive wear on the end of the stem.
The presence of any of these conditions
indicates the need for valve service as
described in the next Section.
14Measure the margin width on each valve
(see illustration). Any valve with a margin
narrower than specified will have to be
replaced with a new one.
Valve components
15Check each valve spring for wear on the
ends. The tension of all springs should be
checked with a special fixture before deciding
2B•10 General engine overhaul procedures
9.14 The margin width on each valve must
be as specified (if no margin exists, the
valve cannot be reused)
9.13 Check for valve wear at the points
shown here
9.12 A dial indicator can be used to
determine the valve stem-to-guide
clearance (move the valve as indicated by
the arrows)
9.10 Check the cylinder head gasket
surface for warpage by trying to slip a
feeler gauge under the straightedge (see
this Chapter’s Specifications for the
maximum warpage allowed, and use a
feeler gauge of that thickness)
1 Valve tip
2 Collet groove
3 Stem (least-worn
area)4 Stem (most-worn
area)
5 Valve face
6 Margin
Page 74 of 228
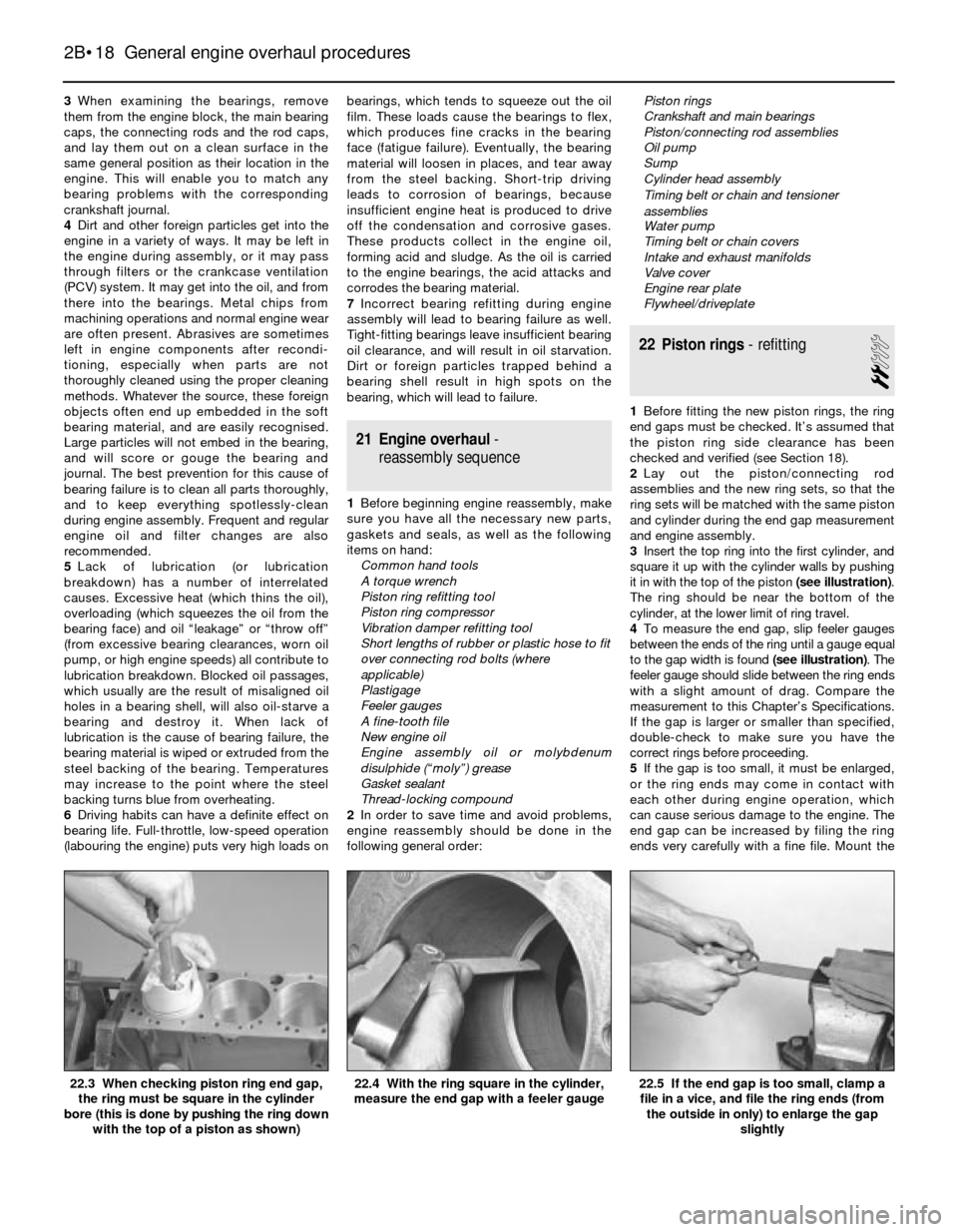
3When examining the bearings, remove
them from the engine block, the main bearing
caps, the connecting rods and the rod caps,
and lay them out on a clean surface in the
same general position as their location in the
engine. This will enable you to match any
bearing problems with the corresponding
crankshaft journal.
4Dirt and other foreign particles get into the
engine in a variety of ways. It may be left in
the engine during assembly, or it may pass
through filters or the crankcase ventilation
(PCV) system. It may get into the oil, and from
there into the bearings. Metal chips from
machining operations and normal engine wear
are often present. Abrasives are sometimes
left in engine components after recondi-
tioning, especially when parts are not
thoroughly cleaned using the proper cleaning
methods. Whatever the source, these foreign
objects often end up embedded in the soft
bearing material, and are easily recognised.
Large particles will not embed in the bearing,
and will score or gouge the bearing and
journal. The best prevention for this cause of
bearing failure is to clean all parts thoroughly,
and to keep everything spotlessly-clean
during engine assembly. Frequent and regular
engine oil and filter changes are also
recommended.
5Lack of lubrication (or lubrication
breakdown) has a number of interrelated
causes. Excessive heat (which thins the oil),
overloading (which squeezes the oil from the
bearing face) and oil “leakage” or “throw off”
(from excessive bearing clearances, worn oil
pump, or high engine speeds) all contribute to
lubrication breakdown. Blocked oil passages,
which usually are the result of misaligned oil
holes in a bearing shell, will also oil-starve a
bearing and destroy it. When lack of
lubrication is the cause of bearing failure, the
bearing material is wiped or extruded from the
steel backing of the bearing. Temperatures
may increase to the point where the steel
backing turns blue from overheating.
6Driving habits can have a definite effect on
bearing life. Full-throttle, low-speed operation
(labouring the engine) puts very high loads onbearings, which tends to squeeze out the oil
film. These loads cause the bearings to flex,
which produces fine cracks in the bearing
face (fatigue failure). Eventually, the bearing
material will loosen in places, and tear away
from the steel backing. Short-trip driving
leads to corrosion of bearings, because
insufficient engine heat is produced to drive
off the condensation and corrosive gases.
These products collect in the engine oil,
forming acid and sludge. As the oil is carried
to the engine bearings, the acid attacks and
corrodes the bearing material.
7Incorrect bearing refitting during engine
assembly will lead to bearing failure as well.
Tight-fitting bearings leave insufficient bearing
oil clearance, and will result in oil starvation.
Dirt or foreign particles trapped behind a
bearing shell result in high spots on the
bearing, which will lead to failure.
21 Engine overhaul-
reassembly sequence
1Before beginning engine reassembly, make
sure you have all the necessary new parts,
gaskets and seals, as well as the following
items on hand:
Common hand tools
A torque wrench
Piston ring refitting tool
Piston ring compressor
Vibration damper refitting tool
Short lengths of rubber or plastic hose to fit
over connecting rod bolts (where
applicable)
Plastigage
Feeler gauges
A fine-tooth file
New engine oil
Engine assembly oil or molybdenum
disulphide (“moly”) grease
Gasket sealant
Thread-locking compound
2In order to save time and avoid problems,
engine reassembly should be done in the
following general order:Piston rings
Crankshaft and main bearings
Piston/connecting rod assemblies
Oil pump
Sump
Cylinder head assembly
Timing belt or chain and tensioner
assemblies
Water pump
Timing belt or chain covers
Intake and exhaust manifolds
Valve cover
Engine rear plate
Flywheel/driveplate
22 Piston rings- refitting
2
1Before fitting the new piston rings, the ring
end gaps must be checked. It’s assumed that
the piston ring side clearance has been
checked and verified (see Section 18).
2Lay out the piston/connecting rod
assemblies and the new ring sets, so that the
ring sets will be matched with the same piston
and cylinder during the end gap measurement
and engine assembly.
3Insert the top ring into the first cylinder, and
square it up with the cylinder walls by pushing
it in with the top of the piston (see illustration).
The ring should be near the bottom of the
cylinder, at the lower limit of ring travel.
4To measure the end gap, slip feeler gauges
between the ends of the ring until a gauge equal
to the gap width is found(see illustration). The
feeler gauge should slide between the ring ends
with a slight amount of drag. Compare the
measurement to this Chapter’s Specifications.
If the gap is larger or smaller than specified,
double-check to make sure you have the
correct rings before proceeding.
5If the gap is too small, it must be enlarged,
or the ring ends may come in contact with
each other during engine operation, which
can cause serious damage to the engine. The
end gap can be increased by filing the ring
ends very carefully with a fine file. Mount the
2B•18 General engine overhaul procedures
22.5 If the end gap is too small, clamp a
file in a vice, and file the ring ends (from
the outside in only) to enlarge the gap
slightly22.4 With the ring square in the cylinder,
measure the end gap with a feeler gauge22.3 When checking piston ring end gap,
the ring must be square in the cylinder
bore (this is done by pushing the ring down
with the top of a piston as shown)
Page 75 of 228
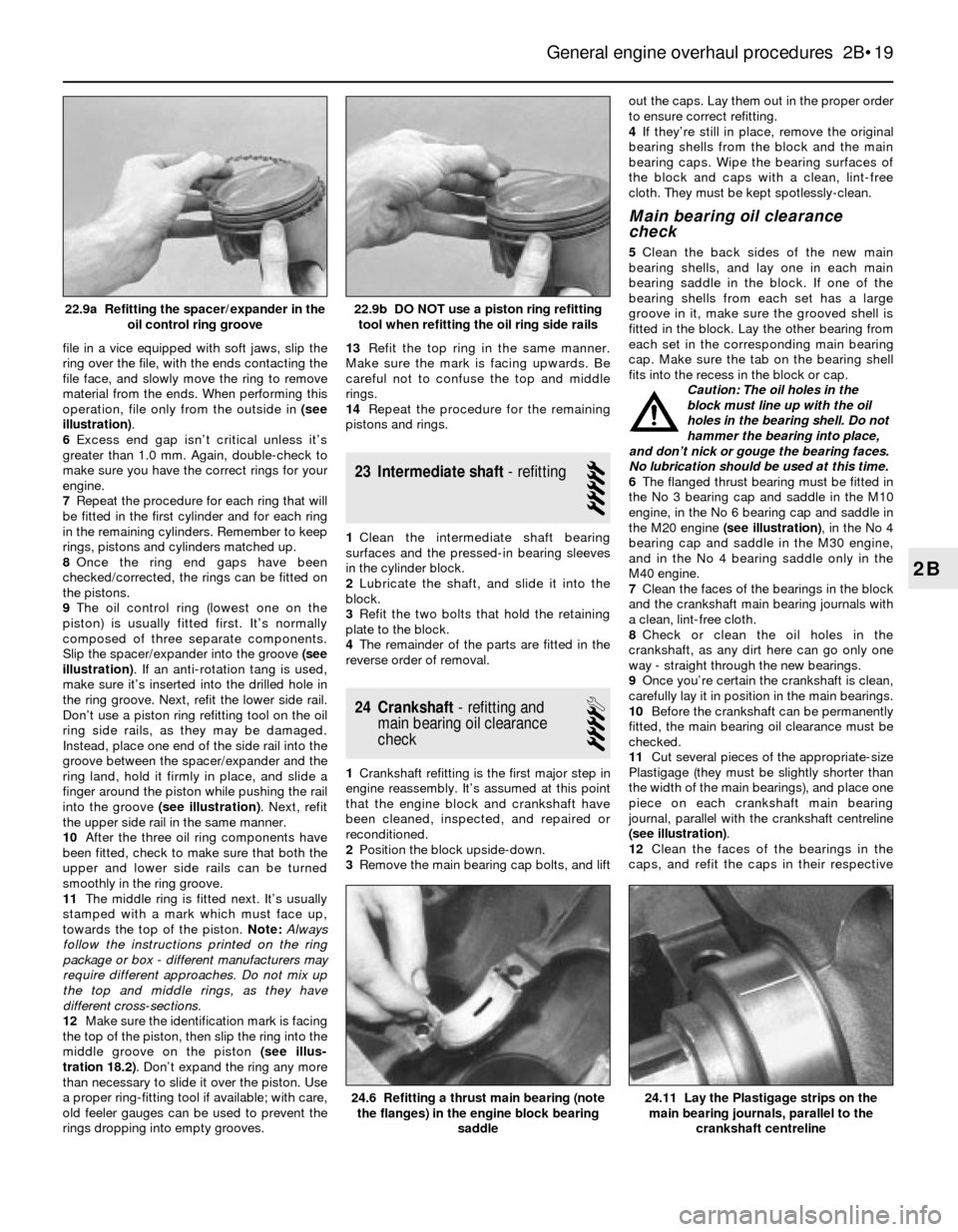
file in a vice equipped with soft jaws, slip the
ring over the file, with the ends contacting the
file face, and slowly move the ring to remove
material from the ends. When performing this
operation, file only from the outside in(see
illustration).
6Excess end gap isn’t critical unless it’s
greater than 1.0 mm. Again, double-check to
make sure you have the correct rings for your
engine.
7Repeat the procedure for each ring that will
be fitted in the first cylinder and for each ring
in the remaining cylinders. Remember to keep
rings, pistons and cylinders matched up.
8Once the ring end gaps have been
checked/corrected, the rings can be fitted on
the pistons.
9The oil control ring (lowest one on the
piston) is usually fitted first. It’s normally
composed of three separate components.
Slip the spacer/expander into the groove(see
illustration). If an anti-rotation tang is used,
make sure it’s inserted into the drilled hole in
the ring groove. Next, refit the lower side rail.
Don’t use a piston ring refitting tool on the oil
ring side rails, as they may be damaged.
Instead, place one end of the side rail into the
groove between the spacer/expander and the
ring land, hold it firmly in place, and slide a
finger around the piston while pushing the rail
into the groove(see illustration). Next, refit
the upper side rail in the same manner.
10After the three oil ring components have
been fitted, check to make sure that both the
upper and lower side rails can be turned
smoothly in the ring groove.
11The middle ring is fitted next. It’s usually
stamped with a mark which must face up,
towards the top of the piston. Note:Always
follow the instructions printed on the ring
package or box - different manufacturers may
require different approaches. Do not mix up
the top and middle rings, as they have
different cross-sections.
12Make sure the identification mark is facing
the top of the piston, then slip the ring into the
middle groove on the piston (see illus-
tration 18.2). Don’t expand the ring any more
than necessary to slide it over the piston. Use
a proper ring-fitting tool if available; with care,
old feeler gauges can be used to prevent the
rings dropping into empty grooves.13Refit the top ring in the same manner.
Make sure the mark is facing upwards. Be
careful not to confuse the top and middle
rings.
14Repeat the procedure for the remaining
pistons and rings.
23 Intermediate shaft- refitting
5
1Clean the intermediate shaft bearing
surfaces and the pressed-in bearing sleeves
in the cylinder block.
2Lubricate the shaft, and slide it into the
block.
3Refit the two bolts that hold the retaining
plate to the block.
4The remainder of the parts are fitted in the
reverse order of removal.
24 Crankshaft- refitting and
main bearing oil clearance
check
4
1Crankshaft refitting is the first major step in
engine reassembly. It’s assumed at this point
that the engine block and crankshaft have
been cleaned, inspected, and repaired or
reconditioned.
2Position the block upside-down.
3Remove the main bearing cap bolts, and liftout the caps. Lay them out in the proper order
to ensure correct refitting.
4If they’re still in place, remove the original
bearing shells from the block and the main
bearing caps. Wipe the bearing surfaces of
the block and caps with a clean, lint-free
cloth. They must be kept spotlessly-clean.
Main bearing oil clearance
check
5Clean the back sides of the new main
bearing shells, and lay one in each main
bearing saddle in the block. If one of the
bearing shells from each set has a large
groove in it, make sure the grooved shell is
fitted in the block. Lay the other bearing from
each set in the corresponding main bearing
cap. Make sure the tab on the bearing shell
fits into the recess in the block or cap.
Caution: The oil holes in the
block must line up with the oil
holes in the bearing shell. Do not
hammer the bearing into place,
and don’t nick or gouge the bearing faces.
No lubrication should be used at this time.
6The flanged thrust bearing must be fitted in
the No 3 bearing cap and saddle in the M10
engine, in the No 6 bearing cap and saddle in
the M20 engine (see illustration), in the No 4
bearing cap and saddle in the M30 engine,
and in the No 4 bearing saddle only in the
M40 engine.
7Clean the faces of the bearings in the block
and the crankshaft main bearing journals with
a clean, lint-free cloth.
8Check or clean the oil holes in the
crankshaft, as any dirt here can go only one
way - straight through the new bearings.
9Once you’re certain the crankshaft is clean,
carefully lay it in position in the main bearings.
10Before the crankshaft can be permanently
fitted, the main bearing oil clearance must be
checked.
11Cut several pieces of the appropriate-size
Plastigage (they must be slightly shorter than
the width of the main bearings), and place one
piece on each crankshaft main bearing
journal, parallel with the crankshaft centreline
(see illustration).
12Clean the faces of the bearings in the
caps, and refit the caps in their respective
General engine overhaul procedures 2B•19
22.9b DO NOT use a piston ring refitting
tool when refitting the oil ring side rails22.9a Refitting the spacer/expander in the
oil control ring groove
24.11 Lay the Plastigage strips on the
main bearing journals, parallel to the
crankshaft centreline24.6 Refitting a thrust main bearing (note
the flanges) in the engine block bearing
saddle
2B
Page 76 of 228
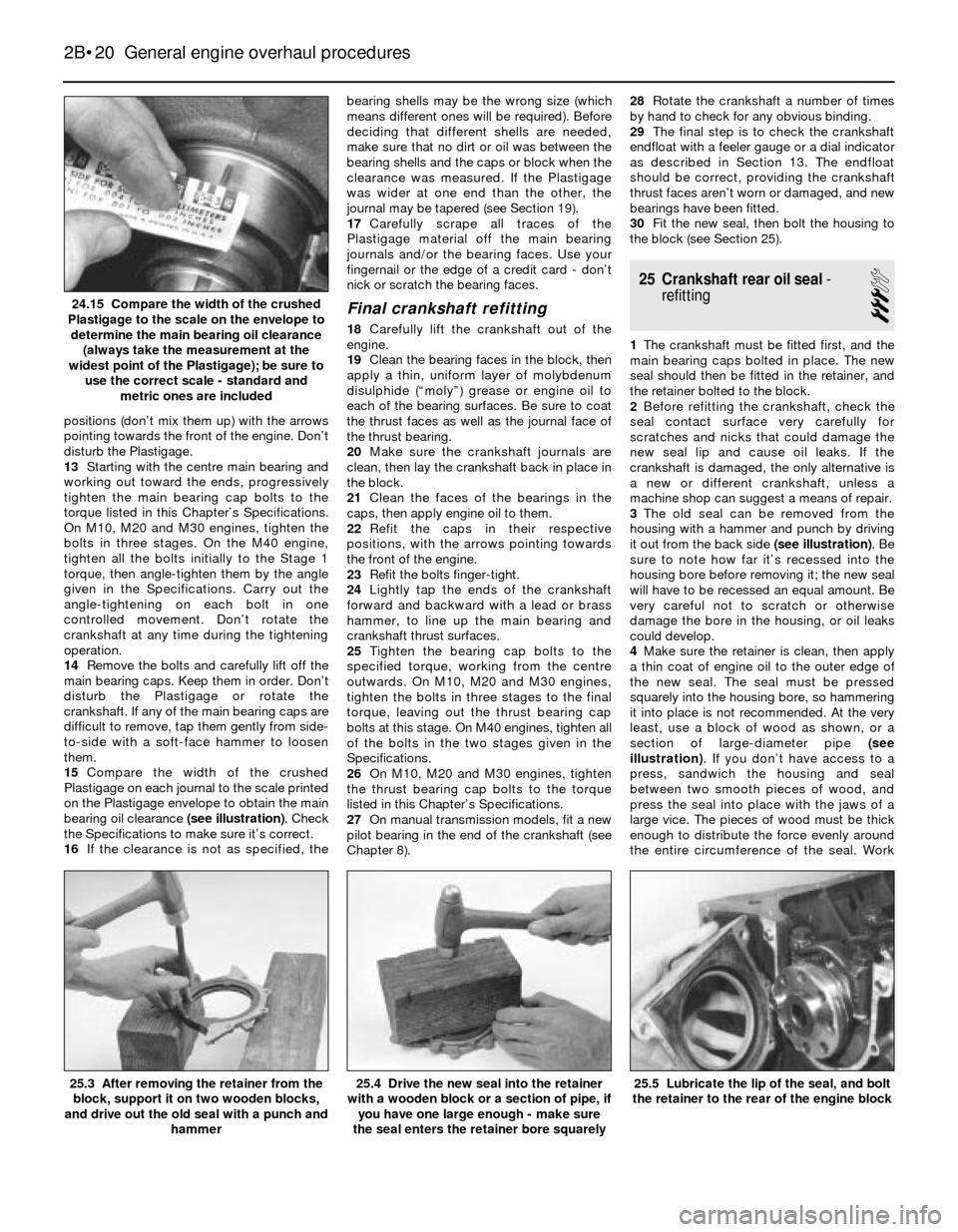
positions (don’t mix them up) with the arrows
pointing towards the front of the engine. Don’t
disturb the Plastigage.
13Starting with the centre main bearing and
working out toward the ends, progressively
tighten the main bearing cap bolts to the
torque listed in this Chapter’s Specifications.
On M10, M20 and M30 engines, tighten the
bolts in three stages. On the M40 engine,
tighten all the bolts initially to the Stage 1
torque, then angle-tighten them by the angle
given in the Specifications. Carry out the
angle-tightening on each bolt in one
controlled movement. Don’t rotate the
crankshaft at any time during the tightening
operation.
14Remove the bolts and carefully lift off the
main bearing caps. Keep them in order. Don’t
disturb the Plastigage or rotate the
crankshaft. If any of the main bearing caps are
difficult to remove, tap them gently from side-
to-side with a soft-face hammer to loosen
them.
15Compare the width of the crushed
Plastigage on each journal to the scale printed
on the Plastigage envelope to obtain the main
bearing oil clearance (see illustration). Check
the Specifications to make sure it’s correct.
16If the clearance is not as specified, thebearing shells may be the wrong size (which
means different ones will be required). Before
deciding that different shells are needed,
make sure that no dirt or oil was between the
bearing shells and the caps or block when the
clearance was measured. If the Plastigage
was wider at one end than the other, the
journal may be tapered (see Section 19).
17Carefully scrape all traces of the
Plastigage material off the main bearing
journals and/or the bearing faces. Use your
fingernail or the edge of a credit card - don’t
nick or scratch the bearing faces.
Final crankshaft refitting
18Carefully lift the crankshaft out of the
engine.
19Clean the bearing faces in the block, then
apply a thin, uniform layer of molybdenum
disulphide (“moly”) grease or engine oil to
each of the bearing surfaces. Be sure to coat
the thrust faces as well as the journal face of
the thrust bearing.
20Make sure the crankshaft journals are
clean, then lay the crankshaft back in place in
the block.
21Clean the faces of the bearings in the
caps, then apply engine oil to them.
22Refit the caps in their respective
positions, with the arrows pointing towards
the front of the engine.
23Refit the bolts finger-tight.
24Lightly tap the ends of the crankshaft
forward and backward with a lead or brass
hammer, to line up the main bearing and
crankshaft thrust surfaces.
25Tighten the bearing cap bolts to the
specified torque, working from the centre
outwards. On M10, M20 and M30 engines,
tighten the bolts in three stages to the final
torque, leaving out the thrust bearing cap
bolts at this stage. On M40 engines, tighten all
of the bolts in the two stages given in the
Specifications.
26On M10, M20 and M30 engines, tighten
the thrust bearing cap bolts to the torque
listed in this Chapter’s Specifications.
27On manual transmission models, fit a new
pilot bearing in the end of the crankshaft (see
Chapter 8).28Rotate the crankshaft a number of times
by hand to check for any obvious binding.
29The final step is to check the crankshaft
endfloat with a feeler gauge or a dial indicator
as described in Section 13. The endfloat
should be correct, providing the crankshaft
thrust faces aren’t worn or damaged, and new
bearings have been fitted.
30Fit the new seal, then bolt the housing to
the block (see Section 25).
25 Crankshaft rear oil seal-
refitting
3
1The crankshaft must be fitted first, and the
main bearing caps bolted in place. The new
seal should then be fitted in the retainer, and
the retainer bolted to the block.
2Before refitting the crankshaft, check the
seal contact surface very carefully for
scratches and nicks that could damage the
new seal lip and cause oil leaks. If the
crankshaft is damaged, the only alternative is
a new or different crankshaft, unless a
machine shop can suggest a means of repair.
3The old seal can be removed from the
housing with a hammer and punch by driving
it out from the back side (see illustration). Be
sure to note how far it’s recessed into the
housing bore before removing it; the new seal
will have to be recessed an equal amount. Be
very careful not to scratch or otherwise
damage the bore in the housing, or oil leaks
could develop.
4Make sure the retainer is clean, then apply
a thin coat of engine oil to the outer edge of
the new seal. The seal must be pressed
squarely into the housing bore, so hammering
it into place is not recommended. At the very
least, use a block of wood as shown, or a
section of large-diameter pipe (see
illustration). If you don’t have access to a
press, sandwich the housing and seal
between two smooth pieces of wood, and
press the seal into place with the jaws of a
large vice. The pieces of wood must be thick
enough to distribute the force evenly around
the entire circumference of the seal. Work
2B•20 General engine overhaul procedures
25.5 Lubricate the lip of the seal, and bolt
the retainer to the rear of the engine block25.4 Drive the new seal into the retainer
with a wooden block or a section of pipe, if
you have one large enough - make sure
the seal enters the retainer bore squarely25.3 After removing the retainer from the
block, support it on two wooden blocks,
and drive out the old seal with a punch and
hammer
24.15 Compare the width of the crushed
Plastigage to the scale on the envelope to
determine the main bearing oil clearance
(always take the measurement at the
widest point of the Plastigage); be sure to
use the correct scale - standard and
metric ones are included
Page 77 of 228
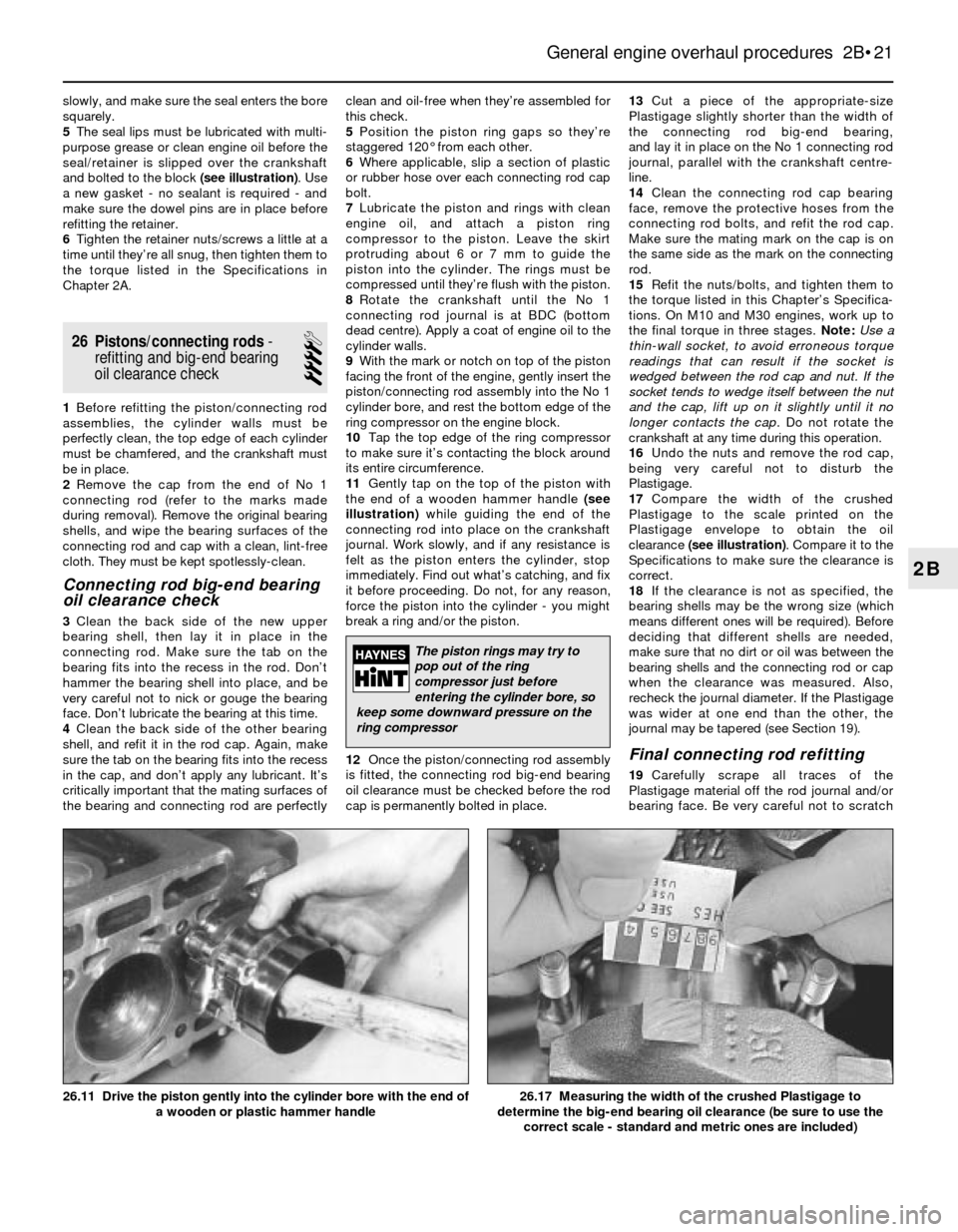
slowly, and make sure the seal enters the bore
squarely.
5The seal lips must be lubricated with multi-
purpose grease or clean engine oil before the
seal/retainer is slipped over the crankshaft
and bolted to the block (see illustration). Use
a new gasket - no sealant is required - and
make sure the dowel pins are in place before
refitting the retainer.
6Tighten the retainer nuts/screws a little at a
time until they’re all snug, then tighten them to
the torque listed in the Specifications in
Chapter 2A.
26 Pistons/connecting rods-
refitting and big-end bearing
oil clearance check
4
1Before refitting the piston/connecting rod
assemblies, the cylinder walls must be
perfectly clean, the top edge of each cylinder
must be chamfered, and the crankshaft must
be in place.
2Remove the cap from the end of No 1
connecting rod (refer to the marks made
during removal). Remove the original bearing
shells, and wipe the bearing surfaces of the
connecting rod and cap with a clean, lint-free
cloth. They must be kept spotlessly-clean.
Connecting rod big-end bearing
oil clearance check
3Clean the back side of the new upper
bearing shell, then lay it in place in the
connecting rod. Make sure the tab on the
bearing fits into the recess in the rod. Don’t
hammer the bearing shell into place, and be
very careful not to nick or gouge the bearing
face. Don’t lubricate the bearing at this time.
4Clean the back side of the other bearing
shell, and refit it in the rod cap. Again, make
sure the tab on the bearing fits into the recess
in the cap, and don’t apply any lubricant. It’s
critically important that the mating surfaces of
the bearing and connecting rod are perfectlyclean and oil-free when they’re assembled for
this check.
5Position the piston ring gaps so they’re
staggered 120° from each other.
6Where applicable, slip a section of plastic
or rubber hose over each connecting rod cap
bolt.
7Lubricate the piston and rings with clean
engine oil, and attach a piston ring
compressor to the piston. Leave the skirt
protruding about 6 or 7 mm to guide the
piston into the cylinder. The rings must be
compressed until they’re flush with the piston.
8Rotate the crankshaft until the No 1
connecting rod journal is at BDC (bottom
dead centre). Apply a coat of engine oil to the
cylinder walls.
9With the mark or notch on top of the piston
facing the front of the engine, gently insert the
piston/connecting rod assembly into the No 1
cylinder bore, and rest the bottom edge of the
ring compressor on the engine block.
10Tap the top edge of the ring compressor
to make sure it’s contacting the block around
its entire circumference.
11Gently tap on the top of the piston with
the end of a wooden hammer handle (see
illustration)while guiding the end of the
connecting rod into place on the crankshaft
journal. Work slowly, and if any resistance is
felt as the piston enters the cylinder, stop
immediately. Find out what’s catching, and fix
it before proceeding. Do not, for any reason,
force the piston into the cylinder - you might
break a ring and/or the piston.
12Once the piston/connecting rod assembly
is fitted, the connecting rod big-end bearing
oil clearance must be checked before the rod
cap is permanently bolted in place.13Cut a piece of the appropriate-size
Plastigage slightly shorter than the width of
the connecting rod big-end bearing,
and lay it in place on the No 1 connecting rod
journal, parallel with the crankshaft centre-
line.
14Clean the connecting rod cap bearing
face, remove the protective hoses from the
connecting rod bolts, and refit the rod cap.
Make sure the mating mark on the cap is on
the same side as the mark on the connecting
rod.
15Refit the nuts/bolts, and tighten them to
the torque listed in this Chapter’s Specifica-
tions. On M10 and M30 engines, work up to
the final torque in three stages. Note:Use a
thin-wall socket, to avoid erroneous torque
readings that can result if the socket is
wedged between the rod cap and nut. If the
socket tends to wedge itself between the nut
and the cap, lift up on it slightly until it no
longer contacts the cap. Do not rotate the
crankshaft at any time during this operation.
16Undo the nuts and remove the rod cap,
being very careful not to disturb the
Plastigage.
17Compare the width of the crushed
Plastigage to the scale printed on the
Plastigage envelope to obtain the oil
clearance (see illustration). Compare it to the
Specifications to make sure the clearance is
correct.
18If the clearance is not as specified, the
bearing shells may be the wrong size (which
means different ones will be required). Before
deciding that different shells are needed,
make sure that no dirt or oil was between the
bearing shells and the connecting rod or cap
when the clearance was measured. Also,
recheck the journal diameter. If the Plastigage
was wider at one end than the other, the
journal may be tapered (see Section 19).
Final connecting rod refitting
19Carefully scrape all traces of the
Plastigage material off the rod journal and/or
bearing face. Be very careful not to scratch
General engine overhaul procedures 2B•21
26.17 Measuring the width of the crushed Plastigage to
determine the big-end bearing oil clearance (be sure to use the
correct scale - standard and metric ones are included)26.11 Drive the piston gently into the cylinder bore with the end of
a wooden or plastic hammer handle
2B
The piston rings may try to
pop out of the ring
compressor just before
entering the cylinder bore, so
keep some downward pressure on the
ring compressor
Page 124 of 228
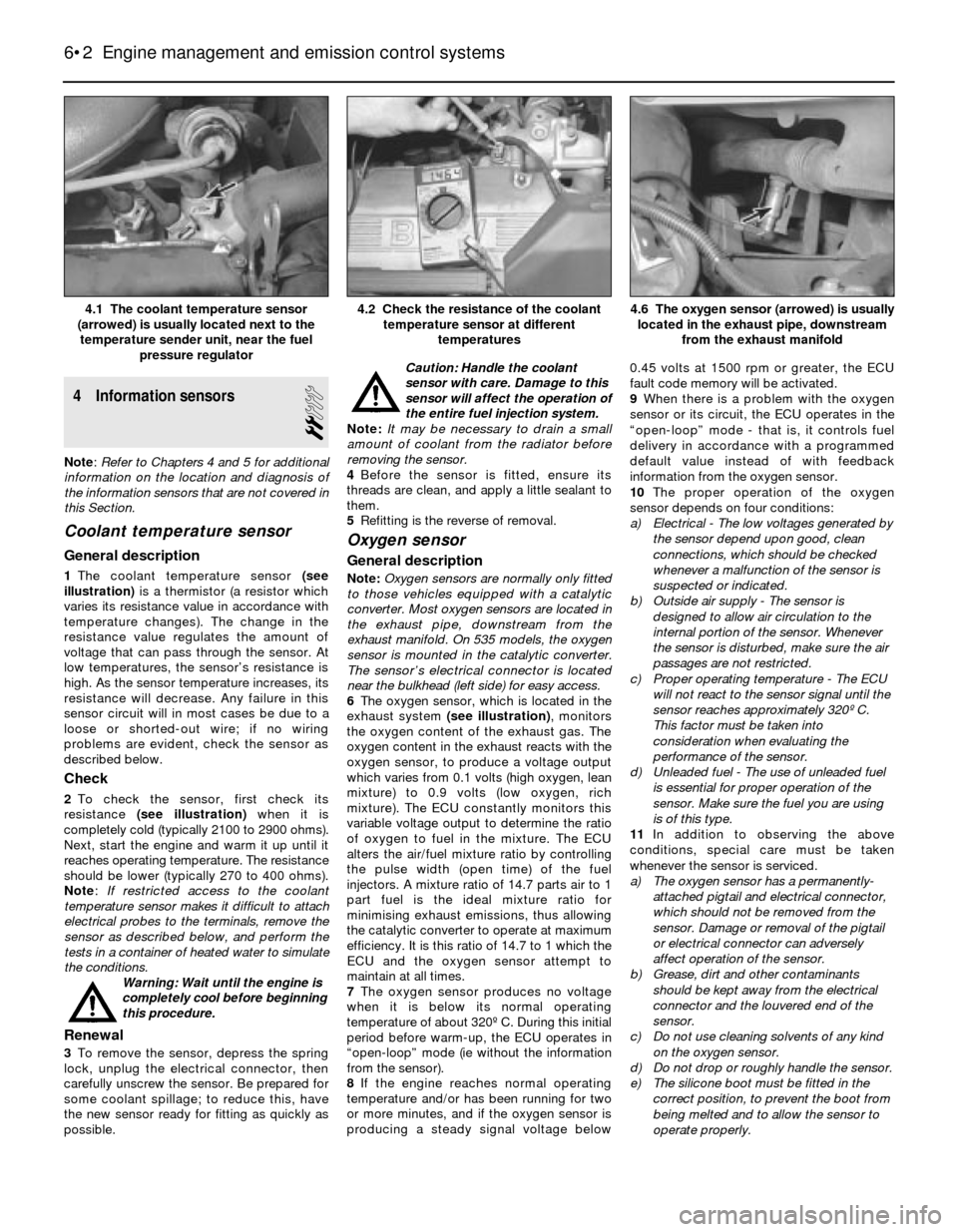
4 Information sensors
2
Note:Refer to Chapters 4 and 5 for additional
information on the location and diagnosis of
the information sensors that are not covered in
this Section.
Coolant temperature sensor
General description
1The coolant temperature sensor (see
illustration)is a thermistor (a resistor which
varies its resistance value in accordance with
temperature changes). The change in the
resistance value regulates the amount of
voltage that can pass through the sensor. At
low temperatures, the sensor’s resistance is
high. As the sensor temperature increases, its
resistance will decrease. Any failure in this
sensor circuit will in most cases be due to a
loose or shorted-out wire; if no wiring
problems are evident, check the sensor as
described below.
Check
2To check the sensor, first check its
resistance (see illustration)when it is
completely cold (typically 2100 to 2900 ohms).
Next, start the engine and warm it up until it
reaches operating temperature. The resistance
should be lower (typically 270 to 400 ohms).
Note: If restricted access to the coolant
temperature sensor makes it difficult to attach
electrical probes to the terminals, remove the
sensor as described below, and perform the
tests in a container of heated water to simulate
the conditions.
Warning: Wait until the engine is
completely cool before beginning
this procedure.
Renewal
3To remove the sensor, depress the spring
lock, unplug the electrical connector, then
carefully unscrew the sensor. Be prepared for
some coolant spillage; to reduce this, have
the new sensor ready for fitting as quickly as
possible.Caution: Handle the coolant
sensor with care. Damage to this
sensor will affect the operation of
the entire fuel injection system.
Note: It may be necessary to drain a small
amount of coolant from the radiator before
removing the sensor.
4Before the sensor is fitted, ensure its
threads are clean, and apply a little sealant to
them.
5Refitting is the reverse of removal.
Oxygen sensor
General description
Note:Oxygen sensors are normally only fitted
to those vehicles equipped with a catalytic
converter. Most oxygen sensors are located in
the exhaust pipe, downstream from the
exhaust manifold. On 535 models, the oxygen
sensor is mounted in the catalytic converter.
The sensor’s electrical connector is located
near the bulkhead (left side) for easy access.
6The oxygen sensor, which is located in the
exhaust system (see illustration), monitors
the oxygen content of the exhaust gas. The
oxygen content in the exhaust reacts with the
oxygen sensor, to produce a voltage output
which varies from 0.1 volts (high oxygen, lean
mixture) to 0.9 volts (low oxygen, rich
mixture). The ECU constantly monitors this
variable voltage output to determine the ratio
of oxygen to fuel in the mixture. The ECU
alters the air/fuel mixture ratio by controlling
the pulse width (open time) of the fuel
injectors. A mixture ratio of 14.7 parts air to 1
part fuel is the ideal mixture ratio for
minimising exhaust emissions, thus allowing
the catalytic converter to operate at maximum
efficiency. It is this ratio of 14.7 to 1 which the
ECU and the oxygen sensor attempt to
maintain at all times.
7The oxygen sensor produces no voltage
when it is below its normal operating
temperature of about 320º C. During this initial
period before warm-up, the ECU operates in
“open-loop” mode (ie without the information
from the sensor).
8If the engine reaches normal operating
temperature and/or has been running for two
or more minutes, and if the oxygen sensor is
producing a steady signal voltage below 0.45 volts at 1500 rpm or greater, the ECU
fault code memory will be activated.
9When there is a problem with the oxygen
sensor or its circuit, the ECU operates in the
“open-loop” mode - that is, it controls fuel
delivery in accordance with a programmed
default value instead of with feedback
information from the oxygen sensor.
10The proper operation of the oxygen
sensor depends on four conditions:
a) Electrical - The low voltages generated by
the sensor depend upon good, clean
connections, which should be checked
whenever a malfunction of the sensor is
suspected or indicated.
b) Outside air supply - The sensor is
designed to allow air circulation to the
internal portion of the sensor. Whenever
the sensor is disturbed, make sure the air
passages are not restricted.
c) Proper operating temperature - The ECU
will not react to the sensor signal until the
sensor reaches approximately 320º C.
This factor must be taken into
consideration when evaluating the
performance of the sensor.
d) Unleaded fuel - The use of unleaded fuel
is essential for proper operation of the
sensor. Make sure the fuel you are using
is of this type.
11In addition to observing the above
conditions, special care must be taken
whenever the sensor is serviced.
a) The oxygen sensor has a permanently-
attached pigtail and electrical connector,
which should not be removed from the
sensor. Damage or removal of the pigtail
or electrical connector can adversely
affect operation of the sensor.
b) Grease, dirt and other contaminants
should be kept away from the electrical
connector and the louvered end of the
sensor.
c) Do not use cleaning solvents of any kind
on the oxygen sensor.
d) Do not drop or roughly handle the sensor.
e) The silicone boot must be fitted in the
correct position, to prevent the boot from
being melted and to allow the sensor to
operate properly.
6•2 Engine management and emission control systems
4.6 The oxygen sensor (arrowed) is usually
located in the exhaust pipe, downstream
from the exhaust manifold4.2 Check the resistance of the coolant
temperature sensor at different
temperatures4.1 The coolant temperature sensor
(arrowed) is usually located next to the
temperature sender unit, near the fuel
pressure regulator
Page 205 of 228
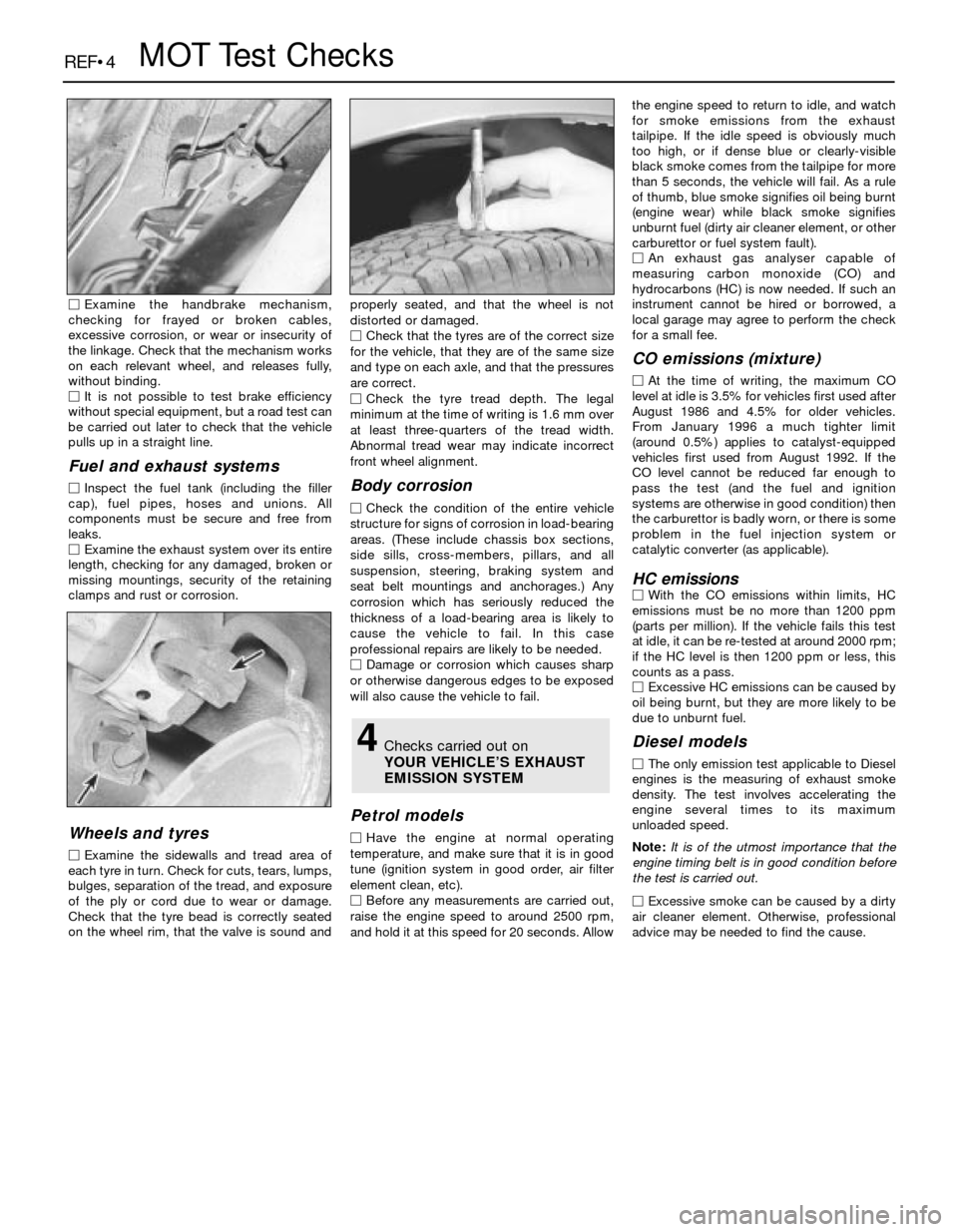
REF•4MOT Test Checks
MExamine the handbrake mechanism,
checking for frayed or broken cables,
excessive corrosion, or wear or insecurity of
the linkage. Check that the mechanism works
on each relevant wheel, and releases fully,
without binding.
MIt is not possible to test brake efficiency
without special equipment, but a road test can
be carried out later to check that the vehicle
pulls up in a straight line.
Fuel and exhaust systems
MInspect the fuel tank (including the filler
cap), fuel pipes, hoses and unions. All
components must be secure and free from
leaks.
MExamine the exhaust system over its entire
length, checking for any damaged, broken or
missing mountings, security of the retaining
clamps and rust or corrosion.
Wheels and tyres
MExamine the sidewalls and tread area of
each tyre in turn. Check for cuts, tears, lumps,
bulges, separation of the tread, and exposure
of the ply or cord due to wear or damage.
Check that the tyre bead is correctly seated
on the wheel rim, that the valve is sound andproperly seated, and that the wheel is not
distorted or damaged.
MCheck that the tyres are of the correct size
for the vehicle, that they are of the same size
and type on each axle, and that the pressures
are correct.
MCheck the tyre tread depth. The legal
minimum at the time of writing is 1.6 mm over
at least three-quarters of the tread width.
Abnormal tread wear may indicate incorrect
front wheel alignment.
Body corrosion
MCheck the condition of the entire vehicle
structure for signs of corrosion in load-bearing
areas. (These include chassis box sections,
side sills, cross-members, pillars, and all
suspension, steering, braking system and
seat belt mountings and anchorages.) Any
corrosion which has seriously reduced the
thickness of a load-bearing area is likely to
cause the vehicle to fail. In this case
professional repairs are likely to be needed.
MDamage or corrosion which causes sharp
or otherwise dangerous edges to be exposed
will also cause the vehicle to fail.
Petrol models
MHave the engine at normal operating
temperature, and make sure that it is in good
tune (ignition system in good order, air filter
element clean, etc).
MBefore any measurements are carried out,
raise the engine speed to around 2500 rpm,
and hold it at this speed for 20 seconds. Allowthe engine speed to return to idle, and watch
for smoke emissions from the exhaust
tailpipe. If the idle speed is obviously much
too high, or if dense blue or clearly-visible
black smoke comes from the tailpipe for more
than 5 seconds, the vehicle will fail. As a rule
of thumb, blue smoke signifies oil being burnt
(engine wear) while black smoke signifies
unburnt fuel (dirty air cleaner element, or other
carburettor or fuel system fault).
MAn exhaust gas analyser capable of
measuring carbon monoxide (CO) and
hydrocarbons (HC) is now needed. If such an
instrument cannot be hired or borrowed, a
local garage may agree to perform the check
for a small fee.
CO emissions (mixture)
MAt the time of writing, the maximum CO
level at idle is 3.5% for vehicles first used after
August 1986 and 4.5% for older vehicles.
From January 1996 a much tighter limit
(around 0.5%) applies to catalyst-equipped
vehicles first used from August 1992. If the
CO level cannot be reduced far enough to
pass the test (and the fuel and ignition
systems are otherwise in good condition) then
the carburettor is badly worn, or there is some
problem in the fuel injection system or
catalytic converter (as applicable).
HC emissionsMWith the CO emissions within limits, HC
emissions must be no more than 1200 ppm
(parts per million). If the vehicle fails this test
at idle, it can be re-tested at around 2000 rpm;
if the HC level is then 1200 ppm or less, this
counts as a pass.
MExcessive HC emissions can be caused by
oil being burnt, but they are more likely to be
due to unburnt fuel.
Diesel models
MThe only emission test applicable to Diesel
engines is the measuring of exhaust smoke
density. The test involves accelerating the
engine several times to its maximum
unloaded speed.
Note: It is of the utmost importance that the
engine timing belt is in good condition before
the test is carried out.
M
Excessive smoke can be caused by a dirty
air cleaner element. Otherwise, professional
advice may be needed to find the cause.
4Checks carried out on
YOUR VEHICLE’S EXHAUST
EMISSION SYSTEM
Page 223 of 228

REF•23
REF
Glossary of Technical Terms
JJump startStarting the engine of a vehicle
with a discharged or weak battery by
attaching jump leads from the weak battery to
a charged or helper battery.
LLoad Sensing Proportioning Valve (LSPV)A
brake hydraulic system control valve that
works like a proportioning valve, but also
takes into consideration the amount of weight
carried by the rear axle.
LocknutA nut used to lock an adjustment
nut, or other threaded component, in place.
For example, a locknut is employed to keep
the adjusting nut on the rocker arm in
position.
LockwasherA form of washer designed to
prevent an attaching nut from working loose.
MMacPherson strutA type of front
suspension system devised by Earle
MacPherson at Ford of England. In its original
form, a simple lateral link with the anti-roll bar
creates the lower control arm. A long strut - an
integral coil spring and shock absorber - is
mounted between the body and the steering
knuckle. Many modern so-called MacPherson
strut systems use a conventional lower A-arm
and don’t rely on the anti-roll bar for location.
MultimeterAn electrical test instrument with
the capability to measure voltage, current and
resistance.
NNOxOxides of Nitrogen. A common toxic
pollutant emitted by petrol and diesel engines
at higher temperatures.
OOhmThe unit of electrical resistance. One
volt applied to a resistance of one ohm will
produce a current of one amp.
OhmmeterAn instrument for measuring
electrical resistance.
O-ringA type of sealing ring made of a
special rubber-like material; in use, the O-ring
is compressed into a groove to provide the
sealing action.Overhead cam (ohc) engineAn engine with
the camshaft(s) located on top of the cylinder
head(s).
Overhead valve (ohv) engineAn engine with
the valves located in the cylinder head, but
with the camshaft located in the engine block.
Oxygen sensorA device installed in the
engine exhaust manifold, which senses the
oxygen content in the exhaust and converts
this information into an electric current. Also
called a Lambda sensor.
PPhillips screwA type of screw head having a
cross instead of a slot for a corresponding
type of screwdriver.
PlastigageA thin strip of plastic thread,
available in different sizes, used for measuring
clearances. For example, a strip of Plastigage
is laid across a bearing journal. The parts are
assembled and dismantled; the width of the
crushed strip indicates the clearance between
journal and bearing.
Propeller shaftThe long hollow tube with
universal joints at both ends that carries
power from the transmission to the differential
on front-engined rear wheel drive vehicles.
Proportioning valveA hydraulic control
valve which limits the amount of pressure to
the rear brakes during panic stops to prevent
wheel lock-up.
RRack-and-pinion steeringA steering system
with a pinion gear on the end of the steering
shaft that mates with a rack (think of a geared
wheel opened up and laid flat). When the
steering wheel is turned, the pinion turns,
moving the rack to the left or right. This
movement is transmitted through the track
rods to the steering arms at the wheels.
RadiatorA liquid-to-air heat transfer device
designed to reduce the temperature of the
coolant in an internal combustion engine
cooling system.
RefrigerantAny substance used as a heat
transfer agent in an air-conditioning system.
R-12 has been the principle refrigerant for
many years; recently, however, manufacturers
have begun using R-134a, a non-CFC
substance that is considered less harmful tothe ozone in the upper atmosphere.
Rocker armA lever arm that rocks on a shaft
or pivots on a stud. In an overhead valve
engine, the rocker arm converts the upward
movement of the pushrod into a downward
movement to open a valve.
RotorIn a distributor, the rotating device
inside the cap that connects the centre
electrode and the outer terminals as it turns,
distributing the high voltage from the coil
secondary winding to the proper spark plug.
Also, that part of an alternator which rotates
inside the stator. Also, the rotating assembly
of a turbocharger, including the compressor
wheel, shaft and turbine wheel.
RunoutThe amount of wobble (in-and-out
movement) of a gear or wheel as it’s rotated.
The amount a shaft rotates “out-of-true.” The
out-of-round condition of a rotating part.
SSealantA liquid or paste used to prevent
leakage at a joint. Sometimes used in
conjunction with a gasket.
Sealed beam lampAn older headlight design
which integrates the reflector, lens and
filaments into a hermetically-sealed one-piece
unit. When a filament burns out or the lens
cracks, the entire unit is simply replaced.
Serpentine drivebeltA single, long, wide
accessory drivebelt that’s used on some
newer vehicles to drive all the accessories,
instead of a series of smaller, shorter belts.
Serpentine drivebelts are usually tensioned by
an automatic tensioner.
ShimThin spacer, commonly used to adjust
the clearance or relative positions between
two parts. For example, shims inserted into or
under bucket tappets control valve
clearances. Clearance is adjusted by
changing the thickness of the shim.
Slide hammerA special puller that screws
into or hooks onto a component such as a
shaft or bearing; a heavy sliding handle on the
shaft bottoms against the end of the shaft to
knock the component free.
SprocketA tooth or projection on the
periphery of a wheel, shaped to engage with a
chain or drivebelt. Commonly used to refer to
the sprocket wheel itself.
Starter inhibitor switchOn vehicles with an
O-ring
Serpentine drivebelt
Plastigage