Reverse BMW 3 SERIES 1984 E30 User Guide
[x] Cancel search | Manufacturer: BMW, Model Year: 1984, Model line: 3 SERIES, Model: BMW 3 SERIES 1984 E30Pages: 228, PDF Size: 7.04 MB
Page 50 of 228
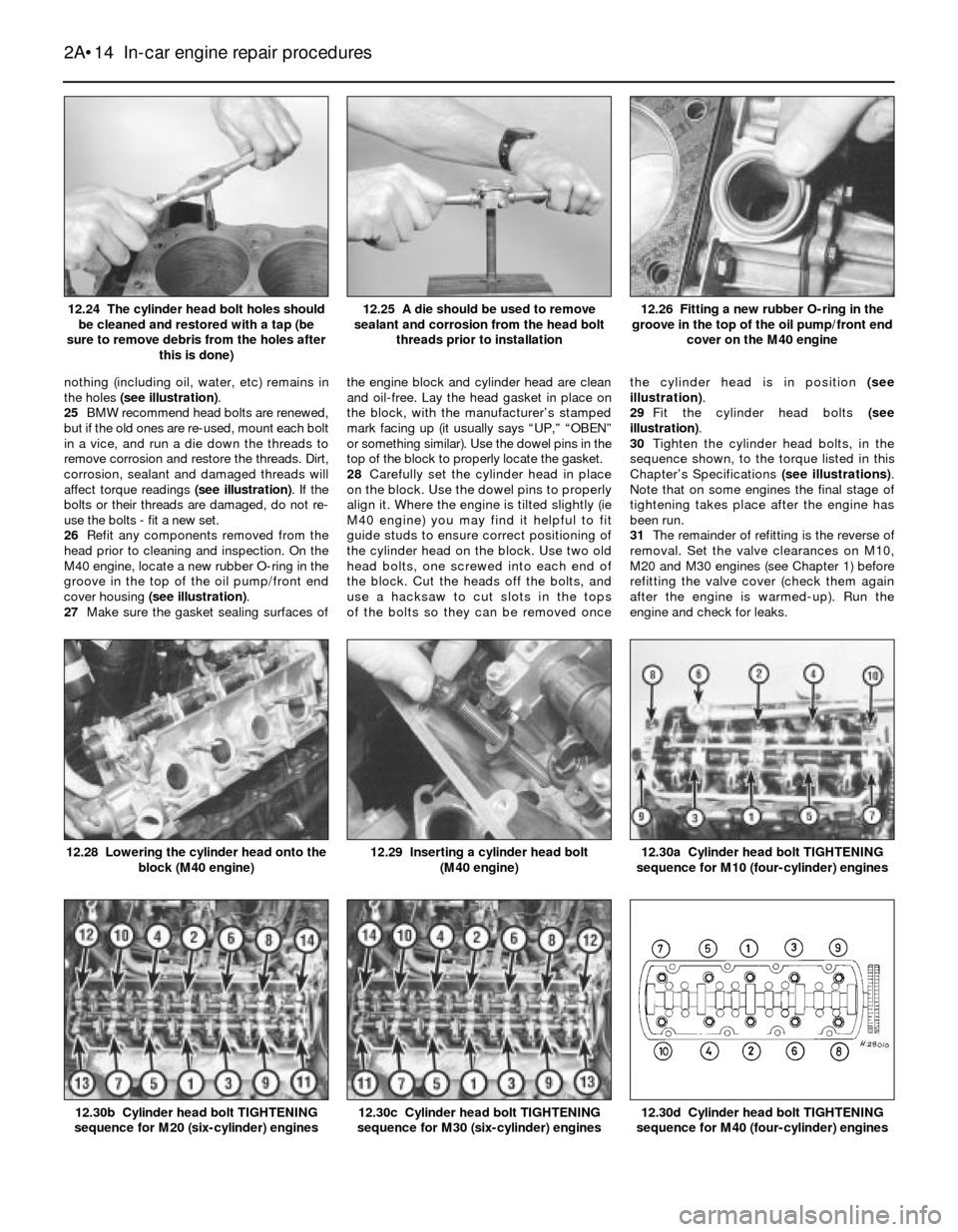
nothing (including oil, water, etc) remains in
the holes (see illustration).
25BMW recommend head bolts are renewed,
but if the old ones are re-used, mount each bolt
in a vice, and run a die down the threads to
remove corrosion and restore the threads. Dirt,
corrosion, sealant and damaged threads will
affect torque readings (see illustration). If the
bolts or their threads are damaged, do not re-
use the bolts - fit a new set.
26Refit any components removed from the
head prior to cleaning and inspection. On the
M40 engine, locate a new rubber O-ring in the
groove in the top of the oil pump/front end
cover housing (see illustration).
27Make sure the gasket sealing surfaces ofthe engine block and cylinder head are clean
and oil-free. Lay the head gasket in place on
the block, with the manufacturer’s stamped
mark facing up (it usually says “UP,” “OBEN”
or something similar). Use the dowel pins in the
top of the block to properly locate the gasket.
28Carefully set the cylinder head in place
on the block. Use the dowel pins to properly
align it. Where the engine is tilted slightly (ie
M40 engine) you may find it helpful to fit
guide studs to ensure correct positioning of
the cylinder head on the block. Use two old
head bolts, one screwed into each end of
the block. Cut the heads off the bolts, and
use a hacksaw to cut slots in the tops
of the bolts so they can be removed oncethe cylinder head is in position (see
illustration).
29Fit the cylinder head bolts (see
illustration).
30Tighten the cylinder head bolts, in the
sequence shown, to the torque listed in this
Chapter’s Specifications (see illustrations).
Note that on some engines the final stage of
tightening takes place after the engine has
been run.
31The remainder of refitting is the reverse of
removal. Set the valve clearances on M10,
M20 and M30 engines (see Chapter 1) before
refitting the valve cover (check them again
after the engine is warmed-up). Run the
engine and check for leaks.
2A•14 In-car engine repair procedures
12.30d Cylinder head bolt TIGHTENING
sequence for M40 (four-cylinder) engines12.30c Cylinder head bolt TIGHTENING
sequence for M30 (six-cylinder) engines12.30b Cylinder head bolt TIGHTENING
sequence for M20 (six-cylinder) engines
12.30a Cylinder head bolt TIGHTENING
sequence for M10 (four-cylinder) engines12.29 Inserting a cylinder head bolt
(M40 engine)12.28 Lowering the cylinder head onto the
block (M40 engine)
12.26 Fitting a new rubber O-ring in the
groove in the top of the oil pump/front end
cover on the M40 engine12.25 A die should be used to remove
sealant and corrosion from the head bolt
threads prior to installation12.24 The cylinder head bolt holes should
be cleaned and restored with a tap (be
sure to remove debris from the holes after
this is done)
Page 52 of 228
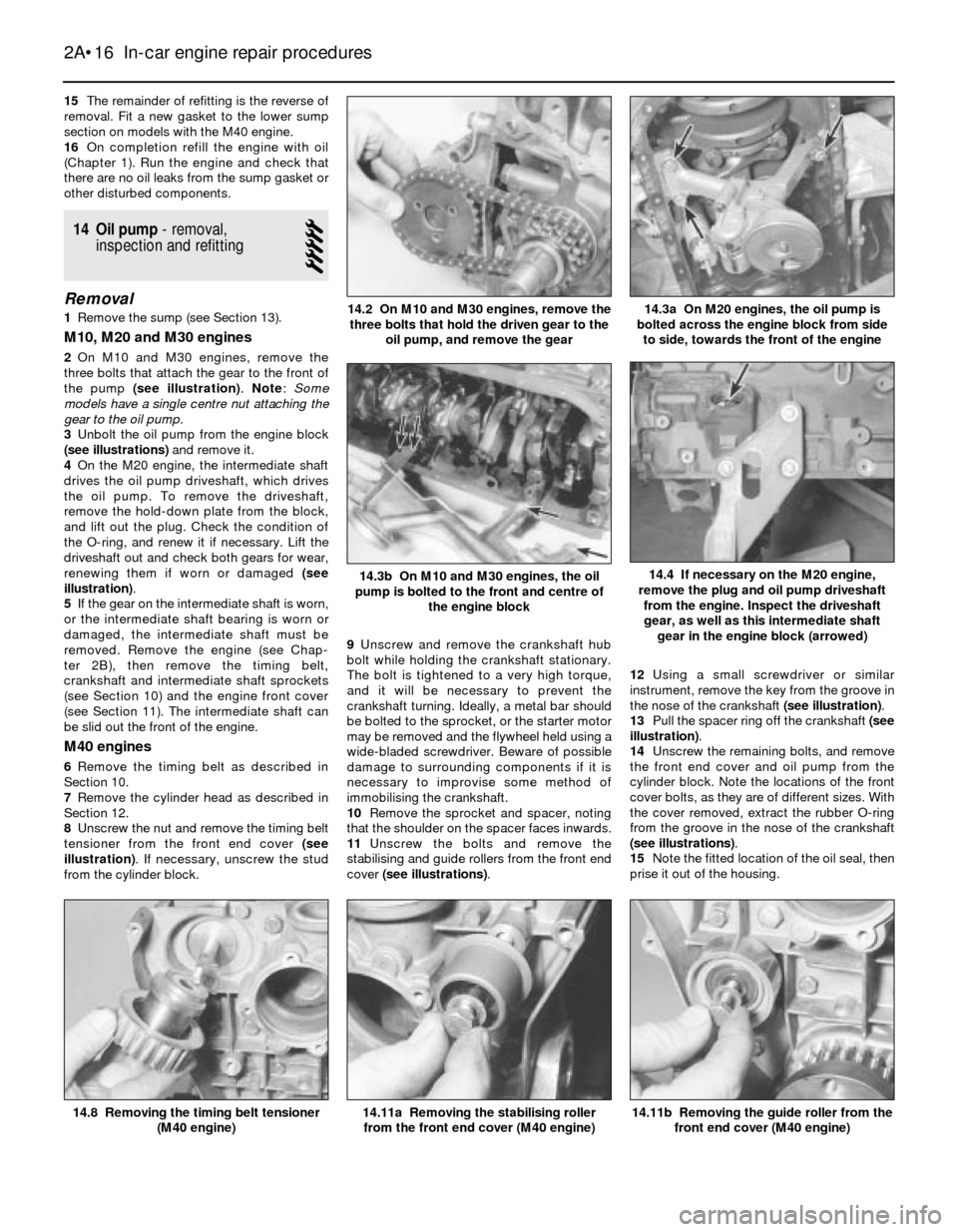
15The remainder of refitting is the reverse of
removal. Fit a new gasket to the lower sump
section on models with the M40 engine.
16On completion refill the engine with oil
(Chapter 1). Run the engine and check that
there are no oil leaks from the sump gasket or
other disturbed components.
14 Oil pump- removal,
inspection and refitting
5
Removal
1Remove the sump (see Section 13).
M10, M20 and M30 engines
2On M10 and M30 engines, remove the
three bolts that attach the gear to the front of
the pump (see illustration). Note: Some
models have a single centre nut attaching the
gear to the oil pump.
3Unbolt the oil pump from the engine block
(see illustrations)and remove it.
4On the M20 engine, the intermediate shaft
drives the oil pump driveshaft, which drives
the oil pump. To remove the driveshaft,
remove the hold-down plate from the block,
and lift out the plug. Check the condition of
the O-ring, and renew it if necessary. Lift the
driveshaft out and check both gears for wear,
renewing them if worn or damaged (see
illustration).
5If the gear on the intermediate shaft is worn,
or the intermediate shaft bearing is worn or
damaged, the intermediate shaft must be
removed. Remove the engine (see Chap-
ter 2B), then remove the timing belt,
crankshaft and intermediate shaft sprockets
(see Section 10) and the engine front cover
(see Section 11). The intermediate shaft can
be slid out the front of the engine.
M40 engines
6Remove the timing belt as described in
Section 10.
7Remove the cylinder head as described in
Section 12.
8Unscrew the nut and remove the timing belt
tensioner from the front end cover (see
illustration). If necessary, unscrew the stud
from the cylinder block.9Unscrew and remove the crankshaft hub
bolt while holding the crankshaft stationary.
The bolt is tightened to a very high torque,
and it will be necessary to prevent the
crankshaft turning. Ideally, a metal bar should
be bolted to the sprocket, or the starter motor
may be removed and the flywheel held using a
wide-bladed screwdriver. Beware of possible
damage to surrounding components if it is
necessary to improvise some method of
immobilising the crankshaft.
10Remove the sprocket and spacer, noting
that the shoulder on the spacer faces inwards.
11Unscrew the bolts and remove the
stabilising and guide rollers from the front end
cover (see illustrations).12Using a small screwdriver or similar
instrument, remove the key from the groove in
the nose of the crankshaft (see illustration).
13Pull the spacer ring off the crankshaft (see
illustration).
14Unscrew the remaining bolts, and remove
the front end cover and oil pump from the
cylinder block. Note the locations of the front
cover bolts, as they are of different sizes. With
the cover removed, extract the rubber O-ring
from the groove in the nose of the crankshaft
(see illustrations).
15Note the fitted location of the oil seal, then
prise it out of the housing.
2A•16 In-car engine repair procedures
14.11b Removing the guide roller from the
front end cover (M40 engine)14.11a Removing the stabilising roller
from the front end cover (M40 engine)14.8 Removing the timing belt tensioner
(M40 engine)
14.3b On M10 and M30 engines, the oil
pump is bolted to the front and centre of
the engine block14.4 If necessary on the M20 engine,
remove the plug and oil pump driveshaft
from the engine. Inspect the driveshaft
gear, as well as this intermediate shaft
gear in the engine block (arrowed)
14.3a On M20 engines, the oil pump is
bolted across the engine block from side
to side, towards the front of the engine14.2 On M10 and M30 engines, remove the
three bolts that hold the driven gear to the
oil pump, and remove the gear
Page 54 of 228
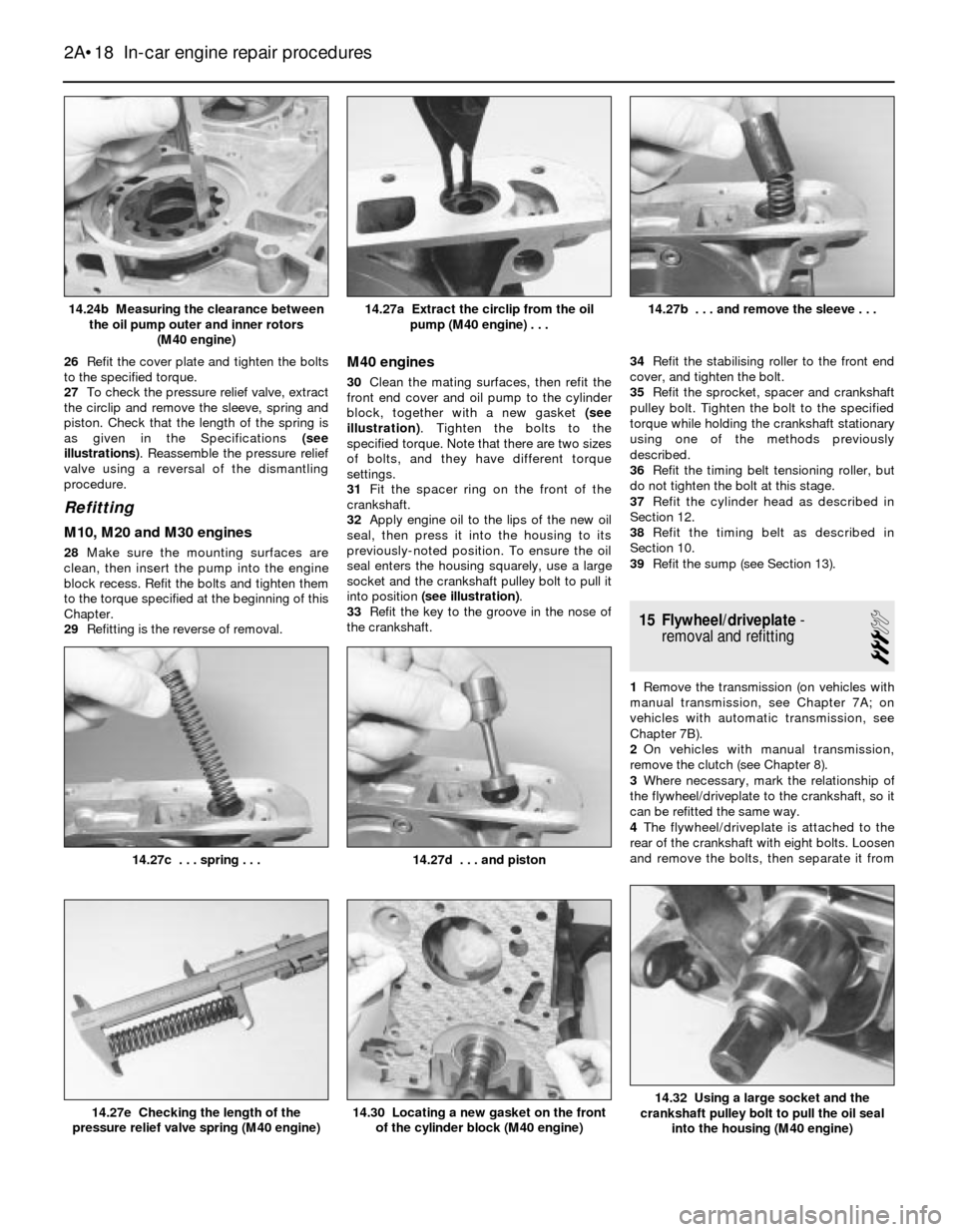
26Refit the cover plate and tighten the bolts
to the specified torque.
27To check the pressure relief valve, extract
the circlip and remove the sleeve, spring and
piston. Check that the length of the spring is
as given in the Specifications (see
illustrations). Reassemble the pressure relief
valve using a reversal of the dismantling
procedure.
Refitting
M10, M20 and M30 engines
28Make sure the mounting surfaces are
clean, then insert the pump into the engine
block recess. Refit the bolts and tighten them
to the torque specified at the beginning of this
Chapter.
29Refitting is the reverse of removal.
M40 engines
30Clean the mating surfaces, then refit the
front end cover and oil pump to the cylinder
block, together with a new gasket (see
illustration). Tighten the bolts to the
specified torque. Note that there are two sizes
of bolts, and they have different torque
settings.
31Fit the spacer ring on the front of the
crankshaft.
32Apply engine oil to the lips of the new oil
seal, then press it into the housing to its
previously-noted position. To ensure the oil
seal enters the housing squarely, use a large
socket and the crankshaft pulley bolt to pull it
into position (see illustration).
33Refit the key to the groove in the nose of
the crankshaft.34Refit the stabilising roller to the front end
cover, and tighten the bolt.
35Refit the sprocket, spacer and crankshaft
pulley bolt. Tighten the bolt to the specified
torque while holding the crankshaft stationary
using one of the methods previously
described.
36Refit the timing belt tensioning roller, but
do not tighten the bolt at this stage.
37Refit the cylinder head as described in
Section 12.
38Refit the timing belt as described in
Section 10.
39Refit the sump (see Section 13).
15 Flywheel/driveplate-
removal and refitting
3
1Remove the transmission (on vehicles with
manual transmission, see Chapter 7A; on
vehicles with automatic transmission, see
Chapter 7B).
2On vehicles with manual transmission,
remove the clutch (see Chapter 8).
3Where necessary, mark the relationship of
the flywheel/driveplate to the crankshaft, so it
can be refitted the same way.
4The flywheel/driveplate is attached to the
rear of the crankshaft with eight bolts. Loosen
and remove the bolts, then separate it from
2A•18 In-car engine repair procedures
14.32 Using a large socket and the
crankshaft pulley bolt to pull the oil seal
into the housing (M40 engine)14.30 Locating a new gasket on the front
of the cylinder block (M40 engine)14.27e Checking the length of the
pressure relief valve spring (M40 engine)
14.27d . . . and piston14.27c . . . spring . . .
14.27b . . . and remove the sleeve . . .14.27a Extract the circlip from the oil
pump (M40 engine) . . .14.24b Measuring the clearance between
the oil pump outer and inner rotors
(M40 engine)
Page 55 of 228
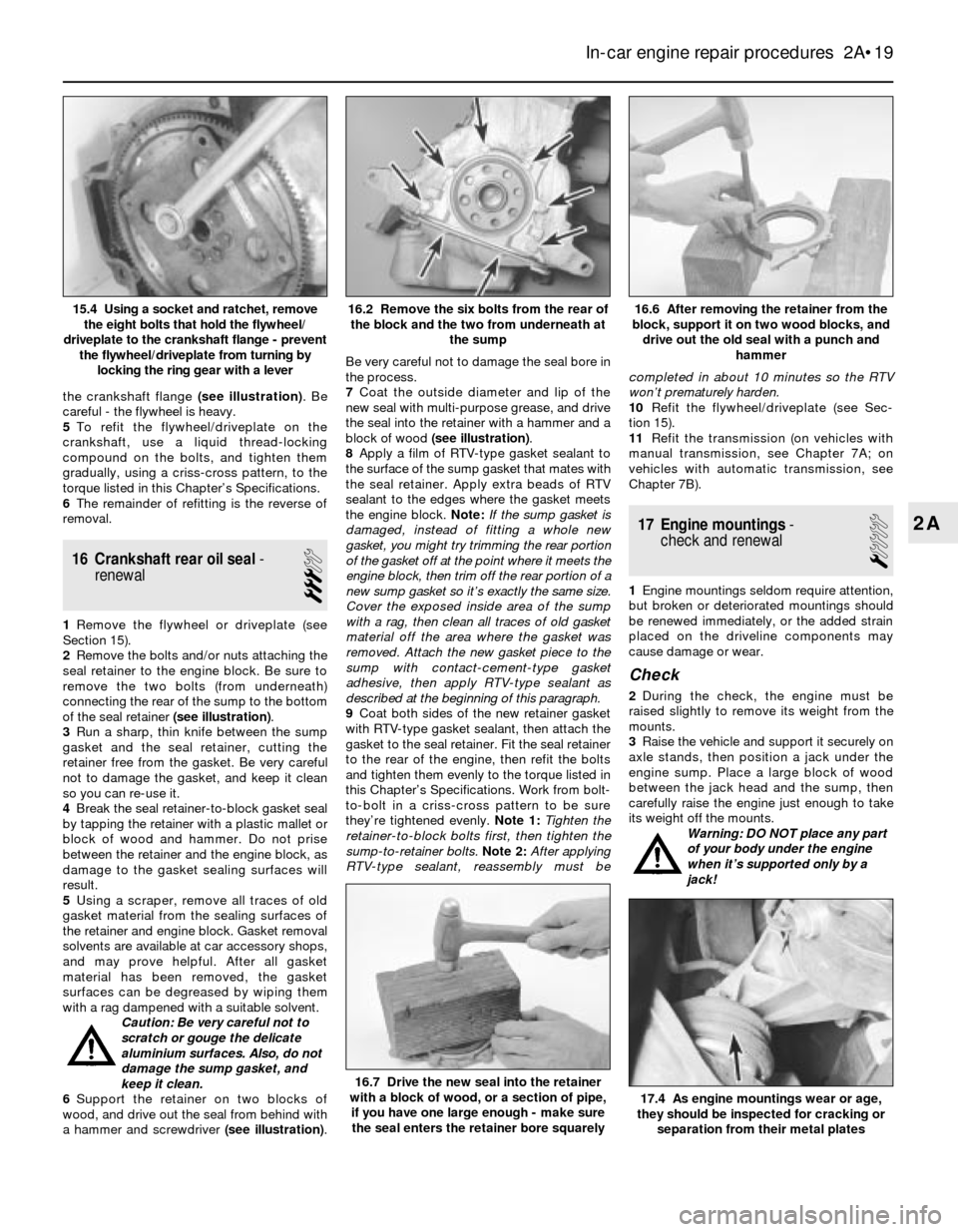
the crankshaft flange (see illustration). Be
careful - the flywheel is heavy.
5To refit the flywheel/driveplate on the
crankshaft, use a liquid thread-locking
compound on the bolts, and tighten them
gradually, using a criss-cross pattern, to the
torque listed in this Chapter’s Specifications.
6The remainder of refitting is the reverse of
removal.
16 Crankshaft rear oil seal-
renewal
3
1Remove the flywheel or driveplate (see
Section 15).
2Remove the bolts and/or nuts attaching the
seal retainer to the engine block. Be sure to
remove the two bolts (from underneath)
connecting the rear of the sump to the bottom
of the seal retainer (see illustration).
3Run a sharp, thin knife between the sump
gasket and the seal retainer, cutting the
retainer free from the gasket. Be very careful
not to damage the gasket, and keep it clean
so you can re-use it.
4Break the seal retainer-to-block gasket seal
by tapping the retainer with a plastic mallet or
block of wood and hammer. Do not prise
between the retainer and the engine block, as
damage to the gasket sealing surfaces will
result.
5Using a scraper, remove all traces of old
gasket material from the sealing surfaces of
the retainer and engine block. Gasket removal
solvents are available at car accessory shops,
and may prove helpful. After all gasket
material has been removed, the gasket
surfaces can be degreased by wiping them
with a rag dampened with a suitable solvent.
Caution: Be very careful not to
scratch or gouge the delicate
aluminium surfaces. Also, do not
damage the sump gasket, and
keep it clean.
6Support the retainer on two blocks of
wood, and drive out the seal from behind with
a hammer and screwdriver (see illustration).Be very careful not to damage the seal bore in
the process.
7Coat the outside diameter and lip of the
new seal with multi-purpose grease, and drive
the seal into the retainer with a hammer and a
block of wood (see illustration).
8Apply a film of RTV-type gasket sealant to
the surface of the sump gasket that mates with
the seal retainer. Apply extra beads of RTV
sealant to the edges where the gasket meets
the engine block. Note:If the sump gasket is
damaged, instead of fitting a whole new
gasket, you might try trimming the rear portion
of the gasket off at the point where it meets the
engine block, then trim off the rear portion of a
new sump gasket so it’s exactly the same size.
Cover the exposed inside area of the sump
with a rag, then clean all traces of old gasket
material off the area where the gasket was
removed. Attach the new gasket piece to the
sump with contact-cement-type gasket
adhesive, then apply RTV-type sealant as
described at the beginning of this paragraph.
9Coat both sides of the new retainer gasket
with RTV-type gasket sealant, then attach the
gasket to the seal retainer. Fit the seal retainer
to the rear of the engine, then refit the bolts
and tighten them evenly to the torque listed in
this Chapter’s Specifications. Work from bolt-
to-bolt in a criss-cross pattern to be sure
they’re tightened evenly.Note 1:Tighten the
retainer-to-block bolts first, then tighten the
sump-to-retainer bolts.Note 2:After applying
RTV-type sealant, reassembly must becompleted in about 10 minutes so the RTV
won’t prematurely harden.
10Refit the flywheel/driveplate (see Sec-
tion 15).
11Refit the transmission (on vehicles with
manual transmission, see Chapter 7A; on
vehicles with automatic transmission, see
Chapter 7B).
17 Engine mountings-
check and renewal
1
1Engine mountings seldom require attention,
but broken or deteriorated mountings should
be renewed immediately, or the added strain
placed on the driveline components may
cause damage or wear.
Check
2During the check, the engine must be
raised slightly to remove its weight from the
mounts.
3Raise the vehicle and support it securely on
axle stands, then position a jack under the
engine sump. Place a large block of wood
between the jack head and the sump, then
carefully raise the engine just enough to take
its weight off the mounts.
Warning: DO NOT place any part
of your body under the engine
when it’s supported only by a
jack!
In-car engine repair procedures 2A•19
16.6 After removing the retainer from the
block, support it on two wood blocks, and
drive out the old seal with a punch and
hammer16.2 Remove the six bolts from the rear of
the block and the two from underneath at
the sump15.4 Using a socket and ratchet, remove
the eight bolts that hold the flywheel/
driveplate to the crankshaft flange - prevent
the flywheel/driveplate from turning by
locking the ring gear with a lever
17.4 As engine mountings wear or age,
they should be inspected for cracking or
separation from their metal plates
16.7 Drive the new seal into the retainer
with a block of wood, or a section of pipe,
if you have one large enough - make sure
the seal enters the retainer bore squarely
2A
Page 56 of 228
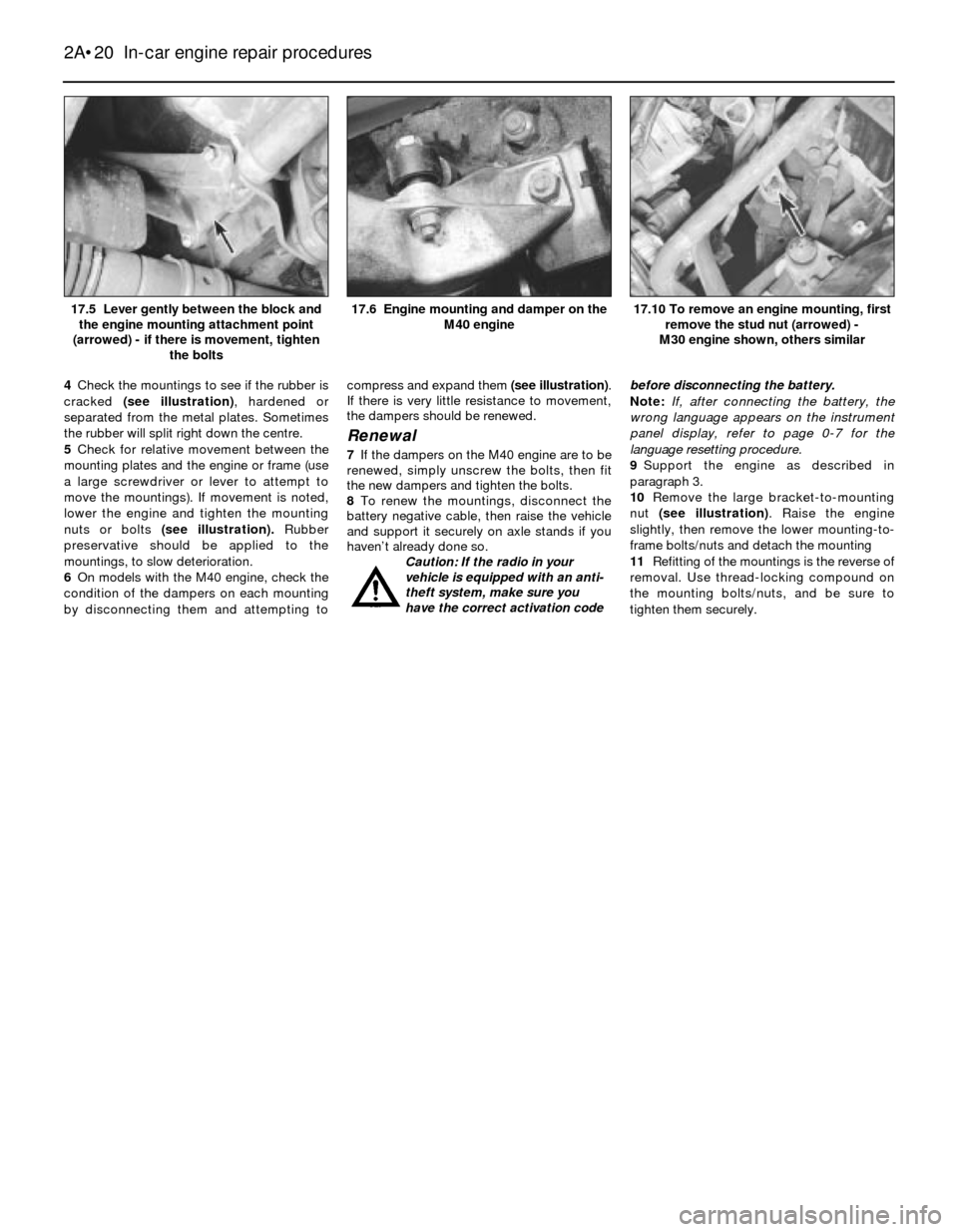
4Check the mountings to see if the rubber is
cracked (see illustration), hardened or
separated from the metal plates. Sometimes
the rubber will split right down the centre.
5Check for relative movement between the
mounting plates and the engine or frame (use
a large screwdriver or lever to attempt to
move the mountings). If movement is noted,
lower the engine and tighten the mounting
nuts or bolts (see illustration). Rubber
preservative should be applied to the
mountings, to slow deterioration.
6On models with the M40 engine, check the
condition of the dampers on each mounting
by disconnecting them and attempting tocompress and expand them (see illustration).
If there is very little resistance to movement,
the dampers should be renewed.
Renewal
7If the dampers on the M40 engine are to be
renewed, simply unscrew the bolts, then fit
the new dampers and tighten the bolts.
8To renew the mountings, disconnect the
battery negative cable, then raise the vehicle
and support it securely on axle stands if you
haven’t already done so.
Caution: If the radio in your
vehicle is equipped with an anti-
theft system, make sure you
have the correct activation codebefore disconnecting the battery.
Note: If, after connecting the battery, the
wrong language appears on the instrument
panel display, refer to page 0-7 for the
language resetting procedure.
9Support the engine as described in
paragraph 3.
10Remove the large bracket-to-mounting
nut (see illustration). Raise the engine
slightly, then remove the lower mounting-to-
frame bolts/nuts and detach the mounting
11Refitting of the mountings is the reverse of
removal. Use thread-locking compound on
the mounting bolts/nuts, and be sure to
tighten them securely.
2A•20 In-car engine repair procedures
17.10 To remove an engine mounting, first
remove the stud nut (arrowed) -
M30 engine shown, others similar17.6 Engine mounting and damper on the
M40 engine17.5 Lever gently between the block and
the engine mounting attachment point
(arrowed) - if there is movement, tighten
the bolts
Page 62 of 228
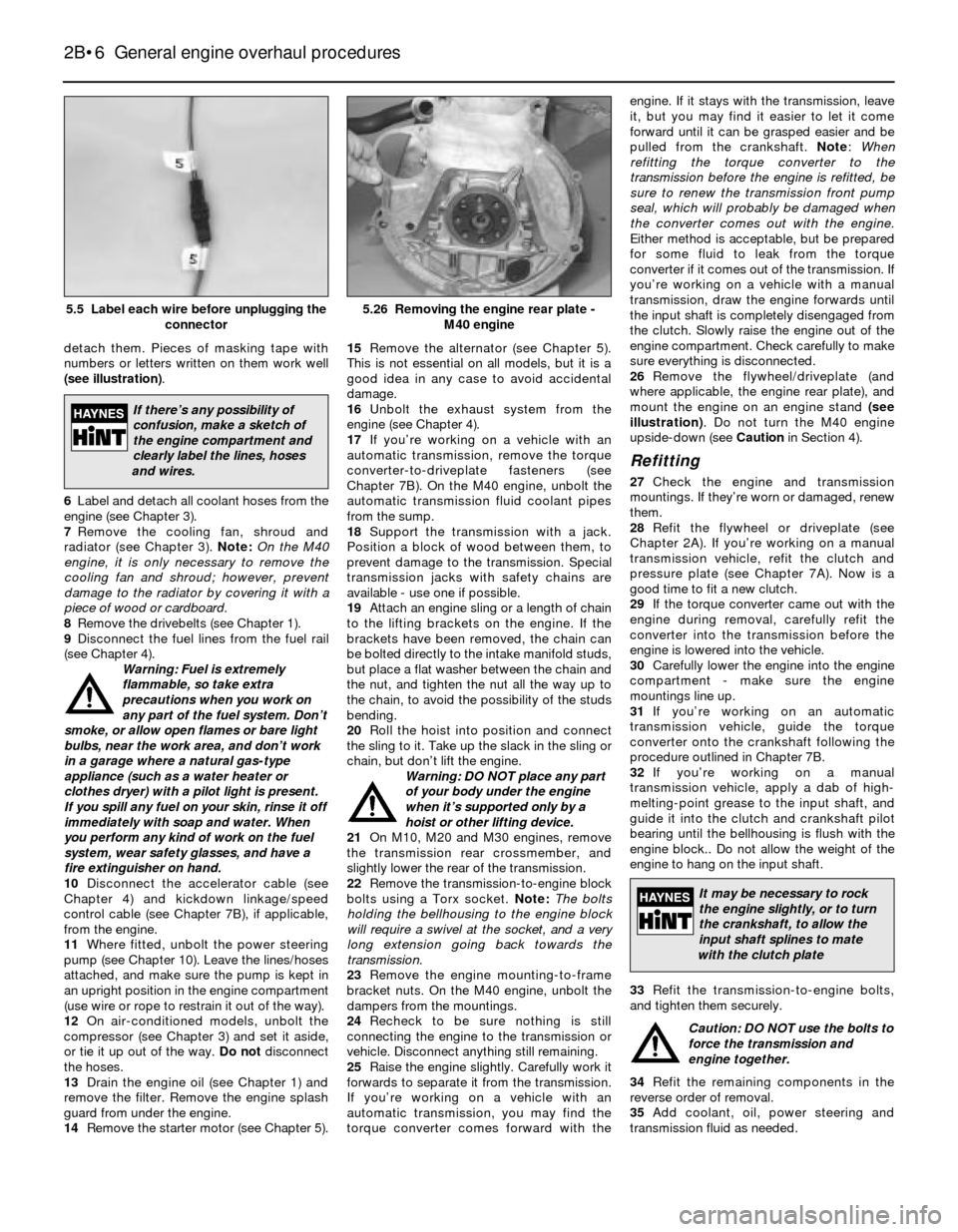
detach them. Pieces of masking tape with
numbers or letters written on them work well
(see illustration).
6Label and detach all coolant hoses from the
engine (see Chapter 3).
7Remove the cooling fan, shroud and
radiator (see Chapter 3). Note:On the M40
engine, it is only necessary to remove the
cooling fan and shroud; however, prevent
damage to the radiator by covering it with a
piece of wood or cardboard.
8Remove the drivebelts (see Chapter 1).
9Disconnect the fuel lines from the fuel rail
(see Chapter 4).
Warning: Fuel is extremely
flammable, so take extra
precautions when you work on
any part of the fuel system. Don’t
smoke, or allow open flames or bare light
bulbs, near the work area, and don’t work
in a garage where a natural gas-type
appliance (such as a water heater or
clothes dryer) with a pilot light is present.
If you spill any fuel on your skin, rinse it off
immediately with soap and water. When
you perform any kind of work on the fuel
system, wear safety glasses, and have a
fire extinguisher on hand.
10Disconnect the accelerator cable (see
Chapter 4) and kickdown linkage/speed
control cable (see Chapter 7B), if applicable,
from the engine.
11Where fitted, unbolt the power steering
pump (see Chapter 10). Leave the lines/hoses
attached, and make sure the pump is kept in
an upright position in the engine compartment
(use wire or rope to restrain it out of the way).
12On air-conditioned models, unbolt the
compressor (see Chapter 3) and set it aside,
or tie it up out of the way. Do not disconnect
the hoses.
13Drain the engine oil (see Chapter 1) and
remove the filter. Remove the engine splash
guard from under the engine.
14Remove the starter motor (see Chapter 5).15Remove the alternator (see Chapter 5).
This is not essential on all models, but it is a
good idea in any case to avoid accidental
damage.
16Unbolt the exhaust system from the
engine (see Chapter 4).
17If you’re working on a vehicle with an
automatic transmission, remove the torque
converter-to-driveplate fasteners (see
Chapter 7B). On the M40 engine, unbolt the
automatic transmission fluid coolant pipes
from the sump.
18Support the transmission with a jack.
Position a block of wood between them, to
prevent damage to the transmission. Special
transmission jacks with safety chains are
available - use one if possible.
19Attach an engine sling or a length of chain
to the lifting brackets on the engine. If the
brackets have been removed, the chain can
be bolted directly to the intake manifold studs,
but place a flat washer between the chain and
the nut, and tighten the nut all the way up to
the chain, to avoid the possibility of the studs
bending.
20Roll the hoist into position and connect
the sling to it. Take up the slack in the sling or
chain, but don’t lift the engine.
Warning: DO NOT place any part
of your body under the engine
when it’s supported only by a
hoist or other lifting device.
21On M10, M20 and M30 engines, remove
the transmission rear crossmember, and
slightly lower the rear of the transmission.
22Remove the transmission-to-engine block
bolts using a Torx socket. Note:The bolts
holding the bellhousing to the engine block
will require a swivel at the socket, and a very
long extension going back towards the
transmission.
23Remove the engine mounting-to-frame
bracket nuts. On the M40 engine, unbolt the
dampers from the mountings.
24Recheck to be sure nothing is still
connecting the engine to the transmission or
vehicle. Disconnect anything still remaining.
25Raise the engine slightly. Carefully work it
forwards to separate it from the transmission.
If you’re working on a vehicle with an
automatic transmission, you may find the
torque converter comes forward with theengine. If it stays with the transmission, leave
it, but you may find it easier to let it come
forward until it can be grasped easier and be
pulled from the crankshaft. Note:When
refitting the torque converter to the
transmission before the engine is refitted, be
sure to renew the transmission front pump
seal, which will probably be damaged when
the converter comes out with the engine.
Either method is acceptable, but be prepared
for some fluid to leak from the torque
converter if it comes out of the transmission. If
you’re working on a vehicle with a manual
transmission, draw the engine forwards until
the input shaft is completely disengaged from
the clutch. Slowly raise the engine out of the
engine compartment. Check carefully to make
sure everything is disconnected.
26Remove the flywheel/driveplate (and
where applicable, the engine rear plate), and
mount the engine on an engine stand (see
illustration). Do not turn the M40 engine
upside-down (see Cautionin Section 4).
Refitting
27Check the engine and transmission
mountings. If they’re worn or damaged, renew
them.
28Refit the flywheel or driveplate (see
Chapter 2A). If you’re working on a manual
transmission vehicle, refit the clutch and
pressure plate (see Chapter 7A). Now is a
good time to fit a new clutch.
29If the torque converter came out with the
engine during removal, carefully refit the
converter into the transmission before the
engine is lowered into the vehicle.
30Carefully lower the engine into the engine
compartment - make sure the engine
mountings line up.
31If you’re working on an automatic
transmission vehicle, guide the torque
converter onto the crankshaft following the
procedure outlined in Chapter 7B.
32If you’re working on a manual
transmission vehicle, apply a dab of high-
melting-point grease to the input shaft, and
guide it into the clutch and crankshaft pilot
bearing until the bellhousing is flush with the
engine block.. Do not allow the weight of the
engine to hang on the input shaft.
33Refit the transmission-to-engine bolts,
and tighten them securely.
Caution: DO NOT use the bolts to
force the transmission and
engine together.
34Refit the remaining components in the
reverse order of removal.
35Add coolant, oil, power steering and
transmission fluid as needed.
2B•6 General engine overhaul procedures
5.26 Removing the engine rear plate -
M40 engine5.5 Label each wire before unplugging the
connector
If there’s any possibility of
confusion, make a sketch of
the engine compartment and
clearly label the lines, hoses
and wires.
It may be necessary to rock
the engine slightly, or to turn
the crankshaft, to allow the
input shaft splines to mate
with the clutch plate
Page 75 of 228
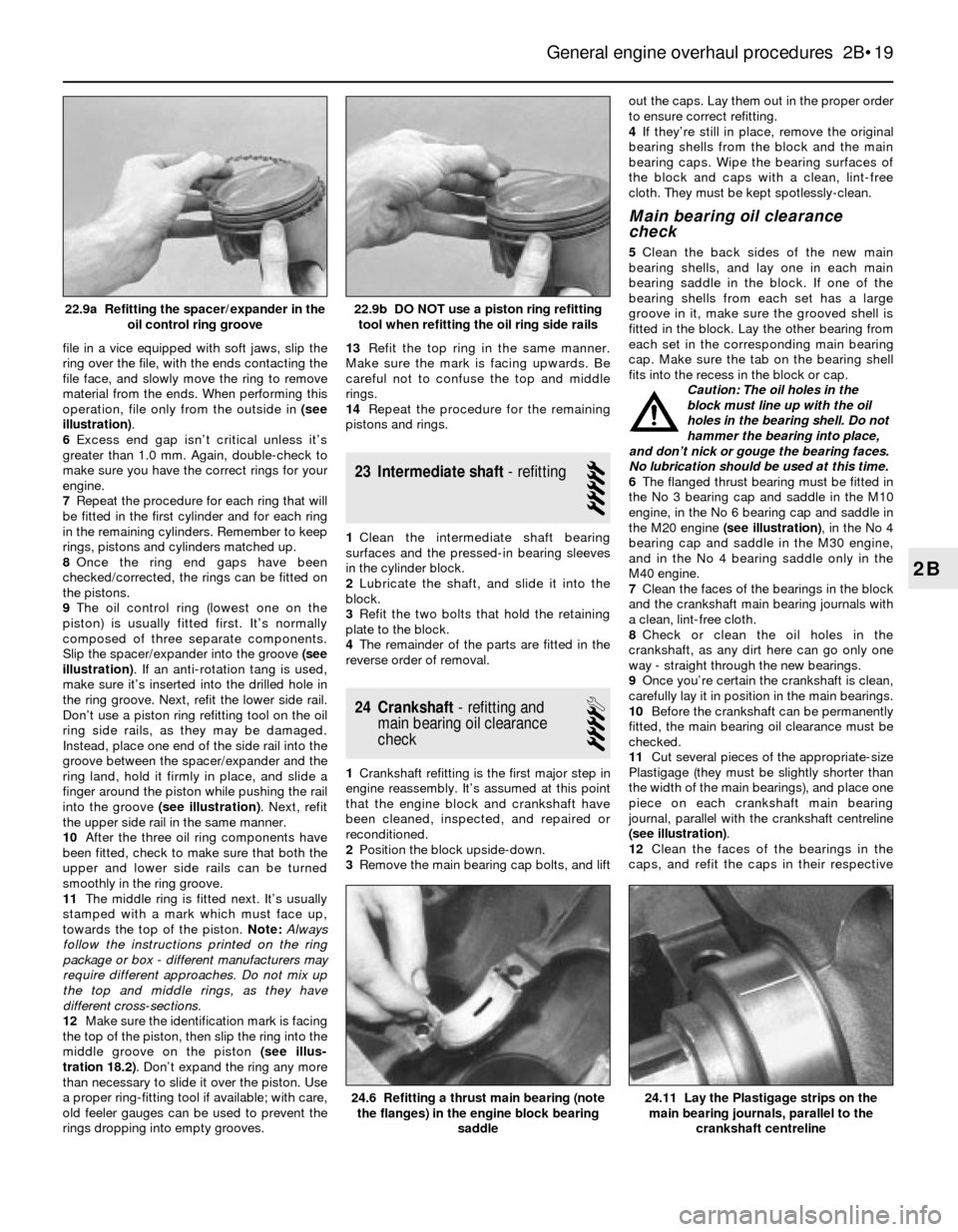
file in a vice equipped with soft jaws, slip the
ring over the file, with the ends contacting the
file face, and slowly move the ring to remove
material from the ends. When performing this
operation, file only from the outside in(see
illustration).
6Excess end gap isn’t critical unless it’s
greater than 1.0 mm. Again, double-check to
make sure you have the correct rings for your
engine.
7Repeat the procedure for each ring that will
be fitted in the first cylinder and for each ring
in the remaining cylinders. Remember to keep
rings, pistons and cylinders matched up.
8Once the ring end gaps have been
checked/corrected, the rings can be fitted on
the pistons.
9The oil control ring (lowest one on the
piston) is usually fitted first. It’s normally
composed of three separate components.
Slip the spacer/expander into the groove(see
illustration). If an anti-rotation tang is used,
make sure it’s inserted into the drilled hole in
the ring groove. Next, refit the lower side rail.
Don’t use a piston ring refitting tool on the oil
ring side rails, as they may be damaged.
Instead, place one end of the side rail into the
groove between the spacer/expander and the
ring land, hold it firmly in place, and slide a
finger around the piston while pushing the rail
into the groove(see illustration). Next, refit
the upper side rail in the same manner.
10After the three oil ring components have
been fitted, check to make sure that both the
upper and lower side rails can be turned
smoothly in the ring groove.
11The middle ring is fitted next. It’s usually
stamped with a mark which must face up,
towards the top of the piston. Note:Always
follow the instructions printed on the ring
package or box - different manufacturers may
require different approaches. Do not mix up
the top and middle rings, as they have
different cross-sections.
12Make sure the identification mark is facing
the top of the piston, then slip the ring into the
middle groove on the piston (see illus-
tration 18.2). Don’t expand the ring any more
than necessary to slide it over the piston. Use
a proper ring-fitting tool if available; with care,
old feeler gauges can be used to prevent the
rings dropping into empty grooves.13Refit the top ring in the same manner.
Make sure the mark is facing upwards. Be
careful not to confuse the top and middle
rings.
14Repeat the procedure for the remaining
pistons and rings.
23 Intermediate shaft- refitting
5
1Clean the intermediate shaft bearing
surfaces and the pressed-in bearing sleeves
in the cylinder block.
2Lubricate the shaft, and slide it into the
block.
3Refit the two bolts that hold the retaining
plate to the block.
4The remainder of the parts are fitted in the
reverse order of removal.
24 Crankshaft- refitting and
main bearing oil clearance
check
4
1Crankshaft refitting is the first major step in
engine reassembly. It’s assumed at this point
that the engine block and crankshaft have
been cleaned, inspected, and repaired or
reconditioned.
2Position the block upside-down.
3Remove the main bearing cap bolts, and liftout the caps. Lay them out in the proper order
to ensure correct refitting.
4If they’re still in place, remove the original
bearing shells from the block and the main
bearing caps. Wipe the bearing surfaces of
the block and caps with a clean, lint-free
cloth. They must be kept spotlessly-clean.
Main bearing oil clearance
check
5Clean the back sides of the new main
bearing shells, and lay one in each main
bearing saddle in the block. If one of the
bearing shells from each set has a large
groove in it, make sure the grooved shell is
fitted in the block. Lay the other bearing from
each set in the corresponding main bearing
cap. Make sure the tab on the bearing shell
fits into the recess in the block or cap.
Caution: The oil holes in the
block must line up with the oil
holes in the bearing shell. Do not
hammer the bearing into place,
and don’t nick or gouge the bearing faces.
No lubrication should be used at this time.
6The flanged thrust bearing must be fitted in
the No 3 bearing cap and saddle in the M10
engine, in the No 6 bearing cap and saddle in
the M20 engine (see illustration), in the No 4
bearing cap and saddle in the M30 engine,
and in the No 4 bearing saddle only in the
M40 engine.
7Clean the faces of the bearings in the block
and the crankshaft main bearing journals with
a clean, lint-free cloth.
8Check or clean the oil holes in the
crankshaft, as any dirt here can go only one
way - straight through the new bearings.
9Once you’re certain the crankshaft is clean,
carefully lay it in position in the main bearings.
10Before the crankshaft can be permanently
fitted, the main bearing oil clearance must be
checked.
11Cut several pieces of the appropriate-size
Plastigage (they must be slightly shorter than
the width of the main bearings), and place one
piece on each crankshaft main bearing
journal, parallel with the crankshaft centreline
(see illustration).
12Clean the faces of the bearings in the
caps, and refit the caps in their respective
General engine overhaul procedures 2B•19
22.9b DO NOT use a piston ring refitting
tool when refitting the oil ring side rails22.9a Refitting the spacer/expander in the
oil control ring groove
24.11 Lay the Plastigage strips on the
main bearing journals, parallel to the
crankshaft centreline24.6 Refitting a thrust main bearing (note
the flanges) in the engine block bearing
saddle
2B
Page 80 of 228
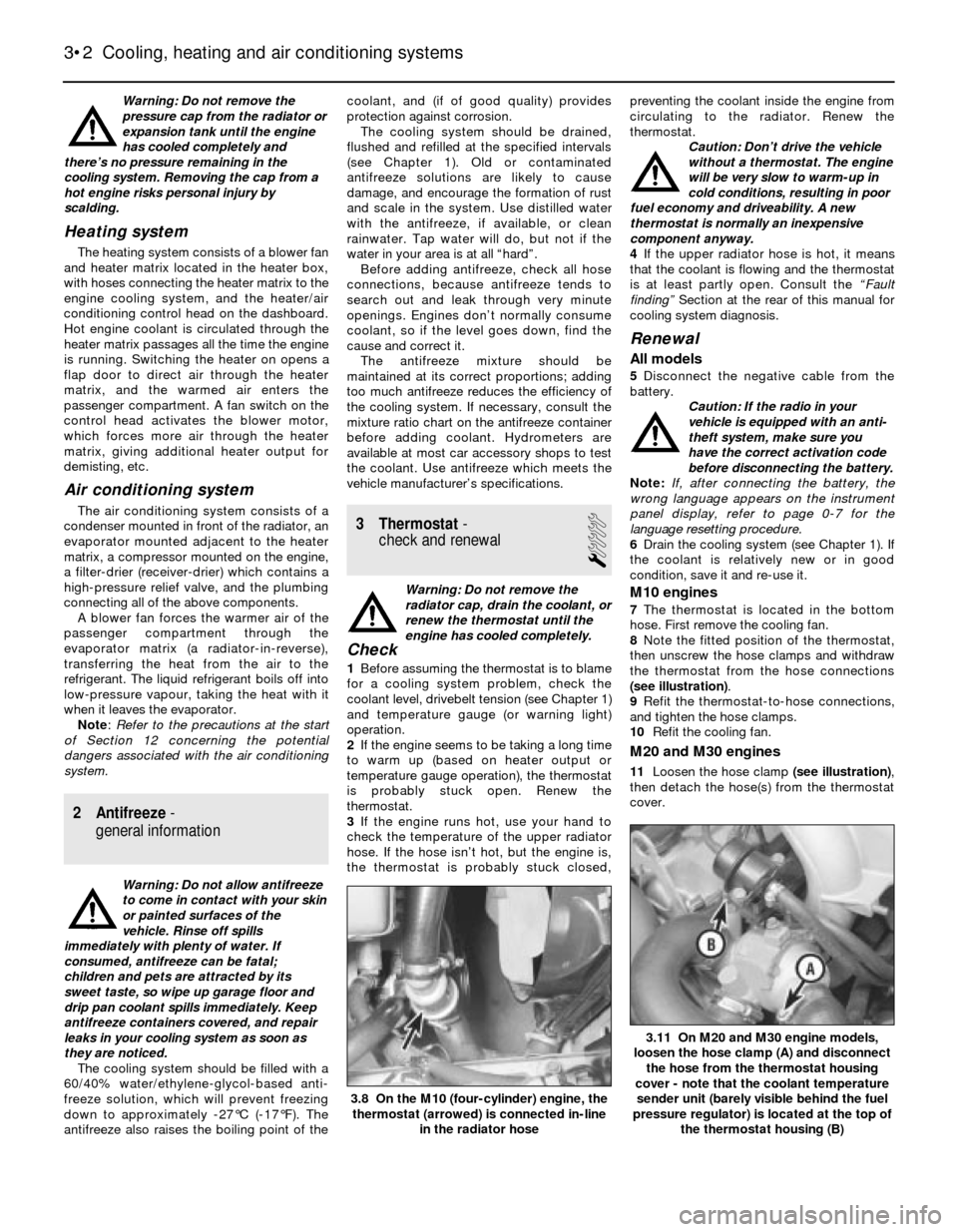
Warning: Do not remove the
pressure cap from the radiator or
expansion tank until the engine
has cooled completely and
there’s no pressure remaining in the
cooling system. Removing the cap from a
hot engine risks personal injury by
scalding.
Heating system
The heating system consists of a blower fan
and heater matrix located in the heater box,
with hoses connecting the heater matrix to the
engine cooling system, and the heater/air
conditioning control head on the dashboard.
Hot engine coolant is circulated through the
heater matrix passages all the time the engine
is running. Switching the heater on opens a
flap door to direct air through the heater
matrix, and the warmed air enters the
passenger compartment. A fan switch on the
control head activates the blower motor,
which forces more air through the heater
matrix, giving additional heater output for
demisting, etc.
Air conditioning system
The air conditioning system consists of a
condenser mounted in front of the radiator, an
evaporator mounted adjacent to the heater
matrix, a compressor mounted on the engine,
a filter-drier (receiver-drier) which contains a
high-pressure relief valve, and the plumbing
connecting all of the above components.
A blower fan forces the warmer air of the
passenger compartment through the
evaporator matrix (a radiator-in-reverse),
transferring the heat from the air to the
refrigerant. The liquid refrigerant boils off into
low-pressure vapour, taking the heat with it
when it leaves the evaporator.
Note: Refer to the precautions at the start
of Section 12 concerning the potential
dangers associated with the air conditioning
system.
2 Antifreeze-
general information
Warning: Do not allow antifreeze
to come in contact with your skin
or painted surfaces of the
vehicle. Rinse off spills
immediately with plenty of water. If
consumed, antifreeze can be fatal;
children and pets are attracted by its
sweet taste, so wipe up garage floor and
drip pan coolant spills immediately. Keep
antifreeze containers covered, and repair
leaks in your cooling system as soon as
they are noticed.
The cooling system should be filled with a
60/40% water/ethylene-glycol-based anti-
freeze solution, which will prevent freezing
down to approximately -27°C (-17°F). The
antifreeze also raises the boiling point of thecoolant, and (if of good quality) provides
protection against corrosion.
The cooling system should be drained,
flushed and refilled at the specified intervals
(see Chapter 1). Old or contaminated
antifreeze solutions are likely to cause
damage, and encourage the formation of rust
and scale in the system. Use distilled water
with the antifreeze, if available, or clean
rainwater. Tap water will do, but not if the
water in your area is at all “hard”.
Before adding antifreeze, check all hose
connections, because antifreeze tends to
search out and leak through very minute
openings. Engines don’t normally consume
coolant, so if the level goes down, find the
cause and correct it.
The antifreeze mixture should be
maintained at its correct proportions; adding
too much antifreeze reduces the efficiency of
the cooling system. If necessary, consult the
mixture ratio chart on the antifreeze container
before adding coolant. Hydrometers are
available at most car accessory shops to test
the coolant. Use antifreeze which meets the
vehicle manufacturer’s specifications.
3 Thermostat-
check and renewal
1
Warning: Do not remove the
radiator cap, drain the coolant, or
renew the thermostat until the
engine has cooled completely.
Check
1Before assuming the thermostat is to blame
for a cooling system problem, check the
coolant level, drivebelt tension (see Chapter 1)
and temperature gauge (or warning light)
operation.
2If the engine seems to be taking a long time
to warm up (based on heater output or
temperature gauge operation), the thermostat
is probably stuck open. Renew the
thermostat.
3If the engine runs hot, use your hand to
check the temperature of the upper radiator
hose. If the hose isn’t hot, but the engine is,
the thermostat is probably stuck closed,preventing the coolant inside the engine from
circulating to the radiator. Renew the
thermostat.
Caution: Don’t drive the vehicle
without a thermostat. The engine
will be very slow to warm-up in
cold conditions, resulting in poor
fuel economy and driveability. A new
thermostat is normally an inexpensive
component anyway.
4If the upper radiator hose is hot, it means
that the coolant is flowing and the thermostat
is at least partly open. Consult the “Fault
finding” Section at the rear of this manual for
cooling system diagnosis.
Renewal
All models
5Disconnect the negative cable from the
battery.
Caution: If the radio in your
vehicle is equipped with an anti-
theft system, make sure you
have the correct activation code
before disconnecting the battery.
Note: If, after connecting the battery, the
wrong language appears on the instrument
panel display, refer to page 0-7 for the
language resetting procedure.
6Drain the cooling system (see Chapter 1). If
the coolant is relatively new or in good
condition, save it and re-use it.
M10 engines
7The thermostat is located in the bottom
hose. First remove the cooling fan.
8Note the fitted position of the thermostat,
then unscrew the hose clamps and withdraw
the thermostat from the hose connections
(see illustration).
9Refit the thermostat-to-hose connections,
and tighten the hose clamps.
10Refit the cooling fan.
M20 and M30 engines
11Loosen the hose clamp (see illustration),
then detach the hose(s) from the thermostat
cover.
3•2 Cooling, heating and air conditioning systems
3.11 On M20 and M30 engine models,
loosen the hose clamp (A) and disconnect
the hose from the thermostat housing
cover - note that the coolant temperature
sender unit (barely visible behind the fuel
pressure regulator) is located at the top of
the thermostat housing (B)
3.8 On the M10 (four-cylinder) engine, the
thermostat (arrowed) is connected in-line
in the radiator hose
Page 82 of 228
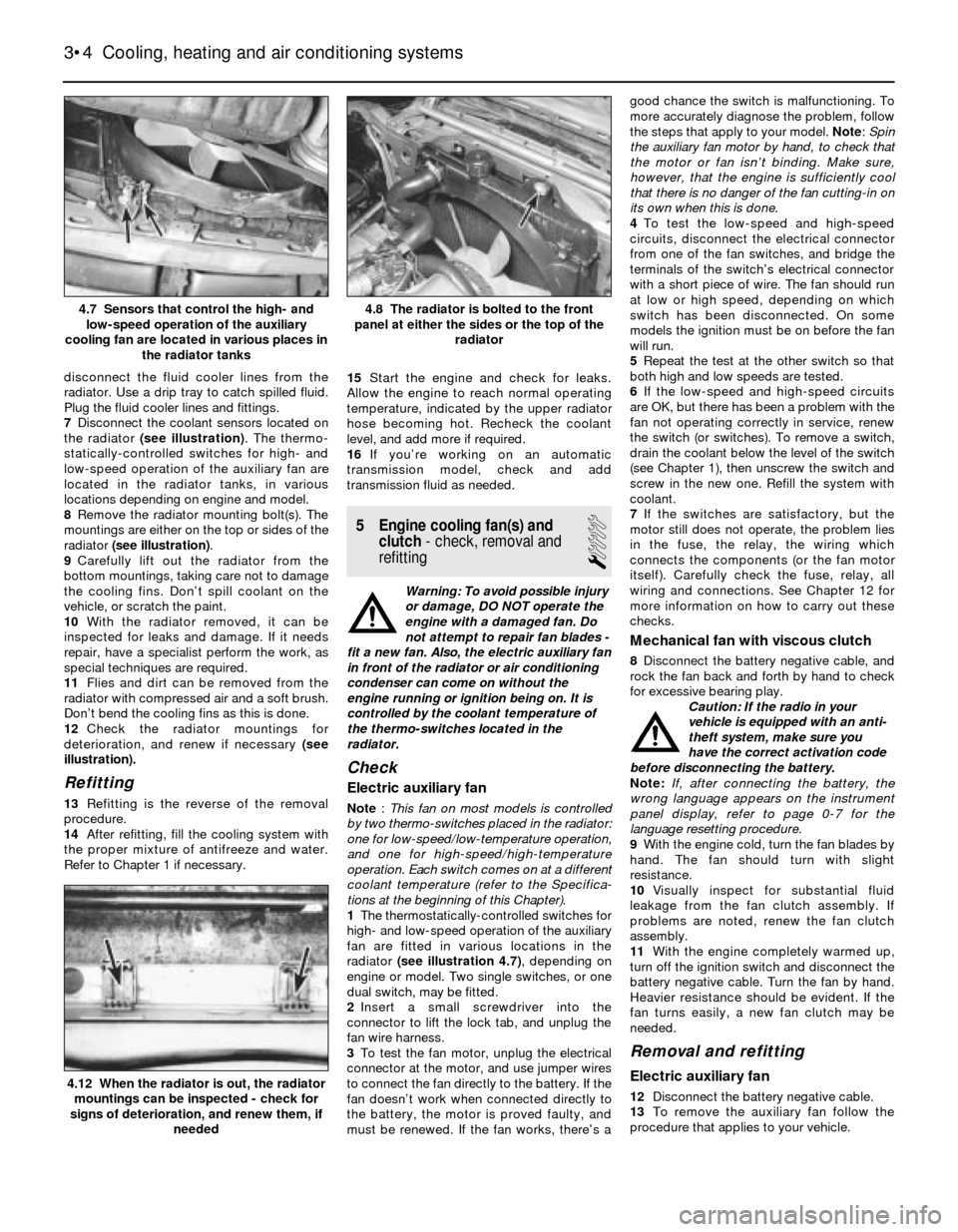
disconnect the fluid cooler lines from the
radiator. Use a drip tray to catch spilled fluid.
Plug the fluid cooler lines and fittings.
7Disconnect the coolant sensors located on
the radiator (see illustration). The thermo-
statically-controlled switches for high- and
low-speed operation of the auxiliary fan are
located in the radiator tanks, in various
locations depending on engine and model.
8Remove the radiator mounting bolt(s). The
mountings are either on the top or sides of the
radiator (see illustration).
9Carefully lift out the radiator from the
bottom mountings, taking care not to damage
the cooling fins. Don’t spill coolant on the
vehicle, or scratch the paint.
10With the radiator removed, it can be
inspected for leaks and damage. If it needs
repair, have a specialist perform the work, as
special techniques are required.
11Flies and dirt can be removed from the
radiator with compressed air and a soft brush.
Don’t bend the cooling fins as this is done.
12Check the radiator mountings for
deterioration, and renew if necessary (see
illustration).
Refitting
13Refitting is the reverse of the removal
procedure.
14After refitting, fill the cooling system with
the proper mixture of antifreeze and water.
Refer to Chapter 1 if necessary.15Start the engine and check for leaks.
Allow the engine to reach normal operating
temperature, indicated by the upper radiator
hose becoming hot. Recheck the coolant
level, and add more if required.
16If you’re working on an automatic
transmission model, check and add
transmission fluid as needed.
5 Engine cooling fan(s) and
clutch- check, removal and
refitting
1
Warning: To avoid possible injury
or damage, DO NOT operate the
engine with a damaged fan. Do
not attempt to repair fan blades -
fit a new fan. Also, the electric auxiliary fan
in front of the radiator or air conditioning
condenser can come on without the
engine running or ignition being on. It is
controlled by the coolant temperature of
the thermo-switches located in the
radiator.
Check
Electric auxiliary fan
Note: This fan on most models is controlled
by two thermo-switches placed in the radiator:
one for low-speed/low-temperature operation,
and one for high-speed/high-temperature
operation. Each switch comes on at a different
coolant temperature (refer to the Specifica-
tions at the beginning of this Chapter).
1The thermostatically-controlled switches for
high- and low-speed operation of the auxiliary
fan are fitted in various locations in the
radiator (see illustration 4.7), depending on
engine or model. Two single switches, or one
dual switch, may be fitted.
2Insert a small screwdriver into the
connector to lift the lock tab, and unplug the
fan wire harness.
3To test the fan motor, unplug the electrical
connector at the motor, and use jumper wires
to connect the fan directly to the battery. If the
fan doesn’t work when connected directly to
the battery, the motor is proved faulty, and
must be renewed. If the fan works, there’s agood chance the switch is malfunctioning. To
more accurately diagnose the problem, follow
the steps that apply to your model. Note: Spin
the auxiliary fan motor by hand, to check that
the motor or fan isn’t binding. Make sure,
however, that the engine is sufficiently cool
that there is no danger of the fan cutting-in on
its own when this is done.
4To test the low-speed and high-speed
circuits, disconnect the electrical connector
from one of the fan switches, and bridge the
terminals of the switch’s electrical connector
with a short piece of wire. The fan should run
at low or high speed, depending on which
switch has been disconnected. On some
models the ignition must be on before the fan
will run.
5Repeat the test at the other switch so that
both high and low speeds are tested.
6If the low-speed and high-speed circuits
are OK, but there has been a problem with the
fan not operating correctly in service, renew
the switch (or switches). To remove a switch,
drain the coolant below the level of the switch
(see Chapter 1), then unscrew the switch and
screw in the new one. Refill the system with
coolant.
7If the switches are satisfactory, but the
motor still does not operate, the problem lies
in the fuse, the relay, the wiring which
connects the components (or the fan motor
itself). Carefully check the fuse, relay, all
wiring and connections. See Chapter 12 for
more information on how to carry out these
checks.
Mechanical fan with viscous clutch
8Disconnect the battery negative cable, and
rock the fan back and forth by hand to check
for excessive bearing play.
Caution: If the radio in your
vehicle is equipped with an anti-
theft system, make sure you
have the correct activation code
before disconnecting the battery.
Note: If, after connecting the battery, the
wrong language appears on the instrument
panel display, refer to page 0-7 for the
language resetting procedure.
9With the engine cold, turn the fan blades by
hand. The fan should turn with slight
resistance.
10Visually inspect for substantial fluid
leakage from the fan clutch assembly. If
problems are noted, renew the fan clutch
assembly.
11With the engine completely warmed up,
turn off the ignition switch and disconnect the
battery negative cable. Turn the fan by hand.
Heavier resistance should be evident. If the
fan turns easily, a new fan clutch may be
needed.
Removal and refitting
Electric auxiliary fan
12Disconnect the battery negative cable.
13To remove the auxiliary fan follow the
procedure that applies to your vehicle.
3•4 Cooling, heating and air conditioning systems
4.12 When the radiator is out, the radiator
mountings can be inspected - check for
signs of deterioration, and renew them, if
needed
4.8 The radiator is bolted to the front
panel at either the sides or the top of the
radiator4.7 Sensors that control the high- and
low-speed operation of the auxiliary
cooling fan are located in various places in
the radiator tanks
Page 83 of 228
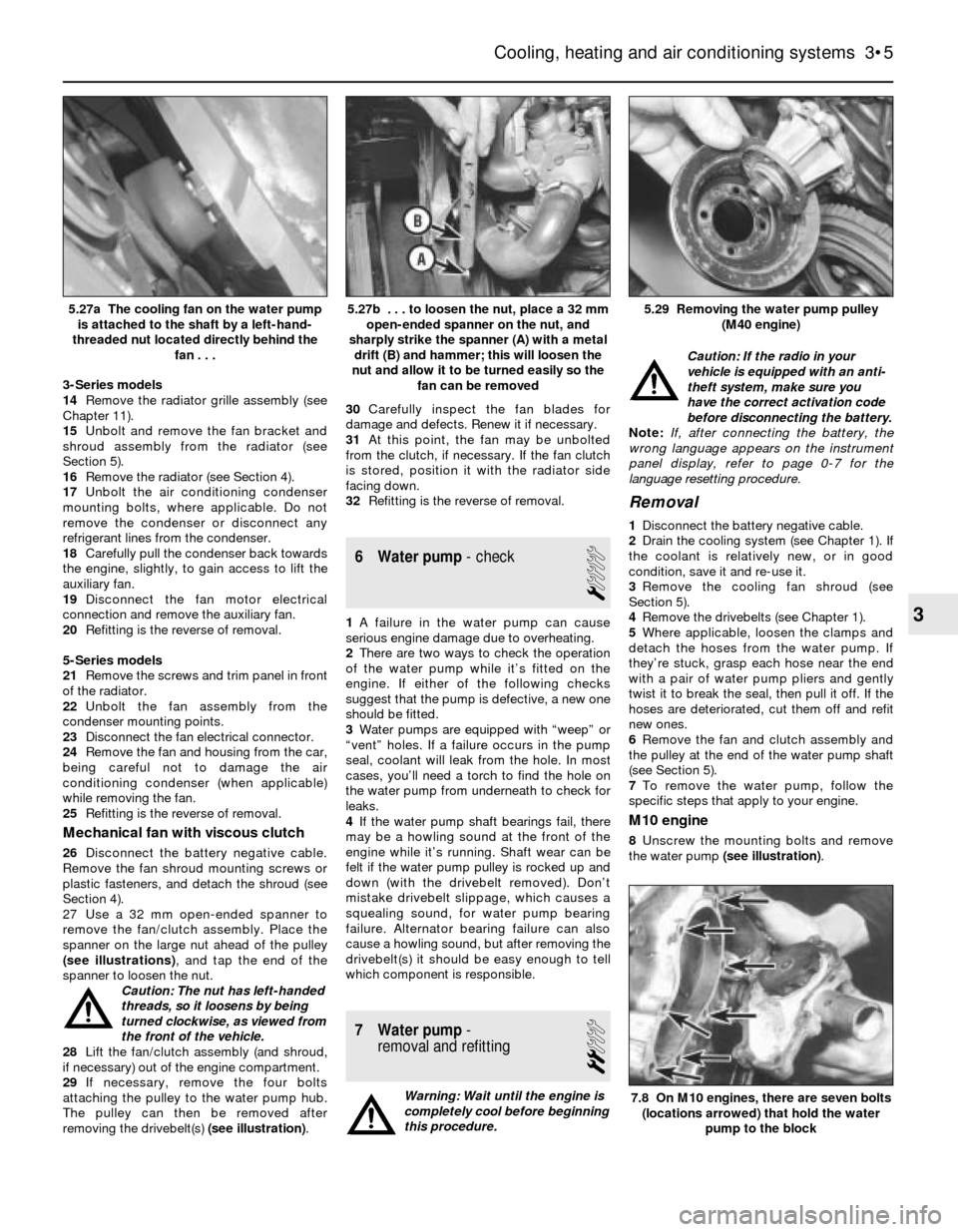
3-Series models
14Remove the radiator grille assembly (see
Chapter 11).
15Unbolt and remove the fan bracket and
shroud assembly from the radiator (see
Section 5).
16Remove the radiator (see Section 4).
17Unbolt the air conditioning condenser
mounting bolts, where applicable. Do not
remove the condenser or disconnect any
refrigerant lines from the condenser.
18Carefully pull the condenser back towards
the engine, slightly, to gain access to lift the
auxiliary fan.
19Disconnect the fan motor electrical
connection and remove the auxiliary fan.
20Refitting is the reverse of removal.
5-Series models
21Remove the screws and trim panel in front
of the radiator.
22Unbolt the fan assembly from the
condenser mounting points.
23Disconnect the fan electrical connector.
24Remove the fan and housing from the car,
being careful not to damage the air
conditioning condenser (when applicable)
while removing the fan.
25Refitting is the reverse of removal.
Mechanical fan with viscous clutch
26Disconnect the battery negative cable.
Remove the fan shroud mounting screws or
plastic fasteners, and detach the shroud (see
Section 4).
27 Use a 32 mm open-ended spanner to
remove the fan/clutch assembly. Place the
spanner on the large nut ahead of the pulley
(see illustrations), and tap the end of the
spanner to loosen the nut.
Caution: The nut has left-handed
threads, so it loosens by being
turned clockwise, as viewed from
the front of the vehicle.
28Lift the fan/clutch assembly (and shroud,
if necessary) out of the engine compartment.
29If necessary, remove the four bolts
attaching the pulley to the water pump hub.
The pulley can then be removed after
removing the drivebelt(s) (see illustration).30Carefully inspect the fan blades for
damage and defects. Renew it if necessary.
31At this point, the fan may be unbolted
from the clutch, if necessary. If the fan clutch
is stored, position it with the radiator side
facing down.
32Refitting is the reverse of removal.
6 Water pump- check
1
1A failure in the water pump can cause
serious engine damage due to overheating.
2There are two ways to check the operation
of the water pump while it’s fitted on the
engine. If either of the following checks
suggest that the pump is defective, a new one
should be fitted.
3Water pumps are equipped with “weep” or
“vent” holes. If a failure occurs in the pump
seal, coolant will leak from the hole. In most
cases, you’ll need a torch to find the hole on
the water pump from underneath to check for
leaks.
4If the water pump shaft bearings fail, there
may be a howling sound at the front of the
engine while it’s running. Shaft wear can be
felt if the water pump pulley is rocked up and
down (with the drivebelt removed). Don’t
mistake drivebelt slippage, which causes a
squealing sound, for water pump bearing
failure. Alternator bearing failure can also
cause a howling sound, but after removing the
drivebelt(s) it should be easy enough to tell
which component is responsible.
7 Water pump-
removal and refitting
2
Warning: Wait until the engine is
completely cool before beginning
this procedure.Caution: If the radio in your
vehicle is equipped with an anti-
theft system, make sure you
have the correct activation code
before disconnecting the battery.
Note: If, after connecting the battery, the
wrong language appears on the instrument
panel display, refer to page 0-7 for the
language resetting procedure.
Removal
1Disconnect the battery negative cable.
2Drain the cooling system (see Chapter 1). If
the coolant is relatively new, or in good
condition, save it and re-use it.
3Remove the cooling fan shroud (see
Section 5).
4Remove the drivebelts (see Chapter 1).
5Where applicable, loosen the clamps and
detach the hoses from the water pump. If
they’re stuck, grasp each hose near the end
with a pair of water pump pliers and gently
twist it to break the seal, then pull it off. If the
hoses are deteriorated, cut them off and refit
new ones.
6Remove the fan and clutch assembly and
the pulley at the end of the water pump shaft
(see Section 5).
7To remove the water pump, follow the
specific steps that apply to your engine.
M10 engine
8Unscrew the mounting bolts and remove
the water pump (see illustration).
Cooling, heating and air conditioning systems 3•5
5.29 Removing the water pump pulley
(M40 engine)5.27b . . . to loosen the nut, place a 32 mm
open-ended spanner on the nut, and
sharply strike the spanner (A) with a metal
drift (B) and hammer; this will loosen the
nut and allow it to be turned easily so the
fan can be removed5.27a The cooling fan on the water pump
is attached to the shaft by a left-hand-
threaded nut located directly behind the
fan . . .
7.8 On M10 engines, there are seven bolts
(locations arrowed) that hold the water
pump to the block
3