ESP BMW 3 SERIES 1984 E30 Workshop Manual
[x] Cancel search | Manufacturer: BMW, Model Year: 1984, Model line: 3 SERIES, Model: BMW 3 SERIES 1984 E30Pages: 228, PDF Size: 7.04 MB
Page 6 of 228
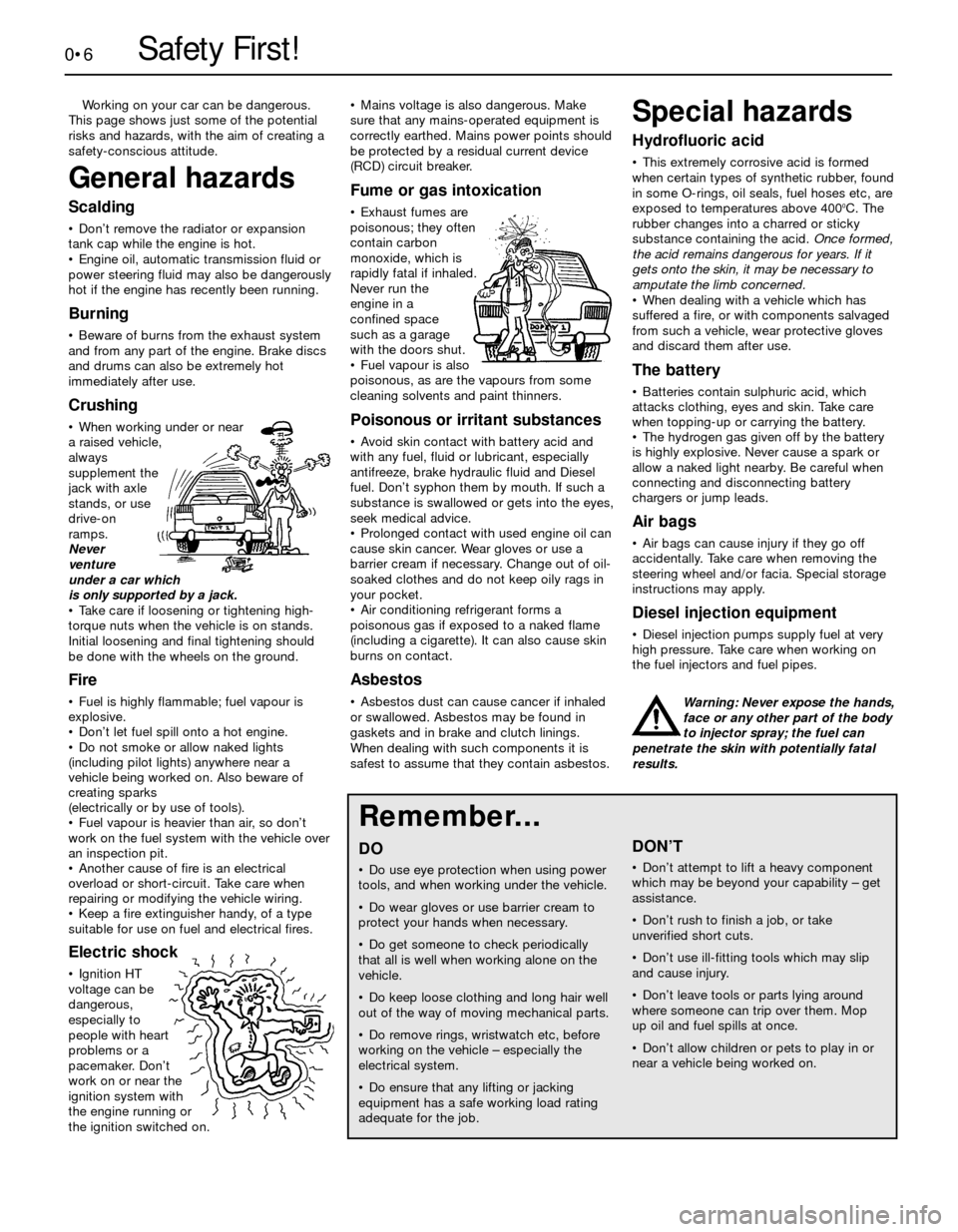
0•6Safety First!
Working on your car can be dangerous.
This page shows just some of the potential
risks and hazards, with the aim of creating a
safety-conscious attitude.
General hazards
Scalding
• Don’t remove the radiator or expansion
tank cap while the engine is hot.
• Engine oil, automatic transmission fluid or
power steering fluid may also be dangerously
hot if the engine has recently been running.
Burning
• Beware of burns from the exhaust system
and from any part of the engine. Brake discs
and drums can also be extremely hot
immediately after use.
Crushing
• When working under or near
a raised vehicle,
always
supplement the
jack with axle
stands, or use
drive-on
ramps.
Never
venture
under a car which
is only supported by a jack.
• Take care if loosening or tightening high-
torque nuts when the vehicle is on stands.
Initial loosening and final tightening should
be done with the wheels on the ground.
Fire
• Fuel is highly flammable; fuel vapour is
explosive.
• Don’t let fuel spill onto a hot engine.
• Do not smoke or allow naked lights
(including pilot lights) anywhere near a
vehicle being worked on. Also beware of
creating sparks
(electrically or by use of tools).
• Fuel vapour is heavier than air, so don’t
work on the fuel system with the vehicle over
an inspection pit.
• Another cause of fire is an electrical
overload or short-circuit. Take care when
repairing or modifying the vehicle wiring.
• Keep a fire extinguisher handy, of a type
suitable for use on fuel and electrical fires.
Electric shock
• Ignition HT
voltage can be
dangerous,
especially to
people with heart
problems or a
pacemaker. Don’t
work on or near the
ignition system with
the engine running or
the ignition switched on.• Mains voltage is also dangerous. Make
sure that any mains-operated equipment is
correctly earthed. Mains power points should
be protected by a residual current device
(RCD) circuit breaker.
Fume or gas intoxication
• Exhaust fumes are
poisonous; they often
contain carbon
monoxide, which is
rapidly fatal if inhaled.
Never run the
engine in a
confined space
such as a garage
with the doors shut.
• Fuel vapour is also
poisonous, as are the vapours from some
cleaning solvents and paint thinners.
Poisonous or irritant substances
• Avoid skin contact with battery acid and
with any fuel, fluid or lubricant, especially
antifreeze, brake hydraulic fluid and Diesel
fuel. Don’t syphon them by mouth. If such a
substance is swallowed or gets into the eyes,
seek medical advice.
• Prolonged contact with used engine oil can
cause skin cancer. Wear gloves or use a
barrier cream if necessary. Change out of oil-
soaked clothes and do not keep oily rags in
your pocket.
• Air conditioning refrigerant forms a
poisonous gas if exposed to a naked flame
(including a cigarette). It can also cause skin
burns on contact.
Asbestos
• Asbestos dust can cause cancer if inhaled
or swallowed. Asbestos may be found in
gaskets and in brake and clutch linings.
When dealing with such components it is
safest to assume that they contain asbestos.
Special hazards
Hydrofluoric acid
• This extremely corrosive acid is formed
when certain types of synthetic rubber, found
in some O-rings, oil seals, fuel hoses etc, are
exposed to temperatures above 400
0C. The
rubber changes into a charred or sticky
substance containing the acid. Once formed,
the acid remains dangerous for years. If it
gets onto the skin, it may be necessary to
amputate the limb concerned.
• When dealing with a vehicle which has
suffered a fire, or with components salvaged
from such a vehicle, wear protective gloves
and discard them after use.
The battery
• Batteries contain sulphuric acid, which
attacks clothing, eyes and skin. Take care
when topping-up or carrying the battery.
• The hydrogen gas given off by the battery
is highly explosive. Never cause a spark or
allow a naked light nearby. Be careful when
connecting and disconnecting battery
chargers or jump leads.
Air bags
• Air bags can cause injury if they go off
accidentally. Take care when removing the
steering wheel and/or facia. Special storage
instructions may apply.
Diesel injection equipment
• Diesel injection pumps supply fuel at very
high pressure. Take care when working on
the fuel injectors and fuel pipes.
Warning: Never expose the hands,
face or any other part of the body
to injector spray; the fuel can
penetrate the skin with potentially fatal
results.
Remember...
DO
• Do use eye protection when using power
tools, and when working under the vehicle.
• Do wear gloves or use barrier cream to
protect your hands when necessary.
• Do get someone to check periodically
that all is well when working alone on the
vehicle.
• Do keep loose clothing and long hair well
out of the way of moving mechanical parts.
• Do remove rings, wristwatch etc, before
working on the vehicle – especially the
electrical system.
• Do ensure that any lifting or jacking
equipment has a safe working load rating
adequate for the job.
A few tips
DON’T
• Don’t attempt to lift a heavy component
which may be beyond your capability – get
assistance.
• Don’t rush to finish a job, or take
unverified short cuts.
• Don’t use ill-fitting tools which may slip
and cause injury.
• Don’t leave tools or parts lying around
where someone can trip over them. Mop
up oil and fuel spills at once.
• Don’t allow children or pets to play in or
near a vehicle being worked on.
Page 10 of 228
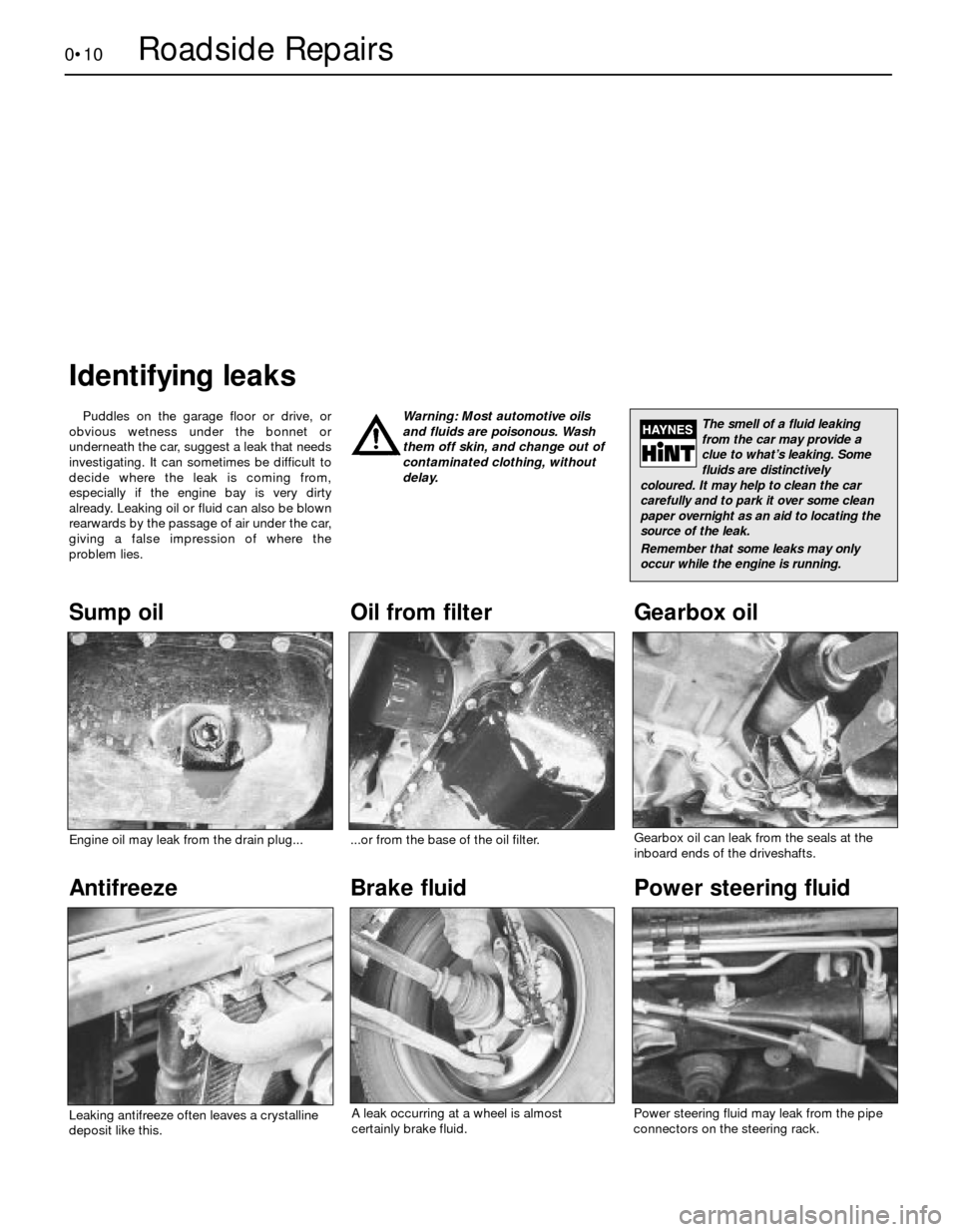
0•10Roadside Repairs
Puddles on the garage floor or drive, or
obvious wetness under the bonnet or
underneath the car, suggest a leak that needs
investigating. It can sometimes be difficult to
decide where the leak is coming from,
especially if the engine bay is very dirty
already. Leaking oil or fluid can also be blown
rearwards by the passage of air under the car,
giving a false impression of where the
problem lies.Warning: Most automotive oils
and fluids are poisonous. Wash
them off skin, and change out of
contaminated clothing, without
delay.
Identifying leaks
The smell of a fluid leaking
from the car may provide a
clue to what’s leaking. Some
fluids are distinctively
coloured. It may help to clean the car
carefully and to park it over some clean
paper overnight as an aid to locating the
source of the leak.
Remember that some leaks may only
occur while the engine is running.
Sump oil Gearbox oil
Brake fluid Power steering fluidOil from filter
Antifreeze
Engine oil may leak from the drain plug......or from the base of the oil filter.
Leaking antifreeze often leaves a crystalline
deposit like this.Gearbox oil can leak from the seals at the
inboard ends of the driveshafts.
A leak occurring at a wheel is almost
certainly brake fluid.Power steering fluid may leak from the pipe
connectors on the steering rack.
Page 23 of 228
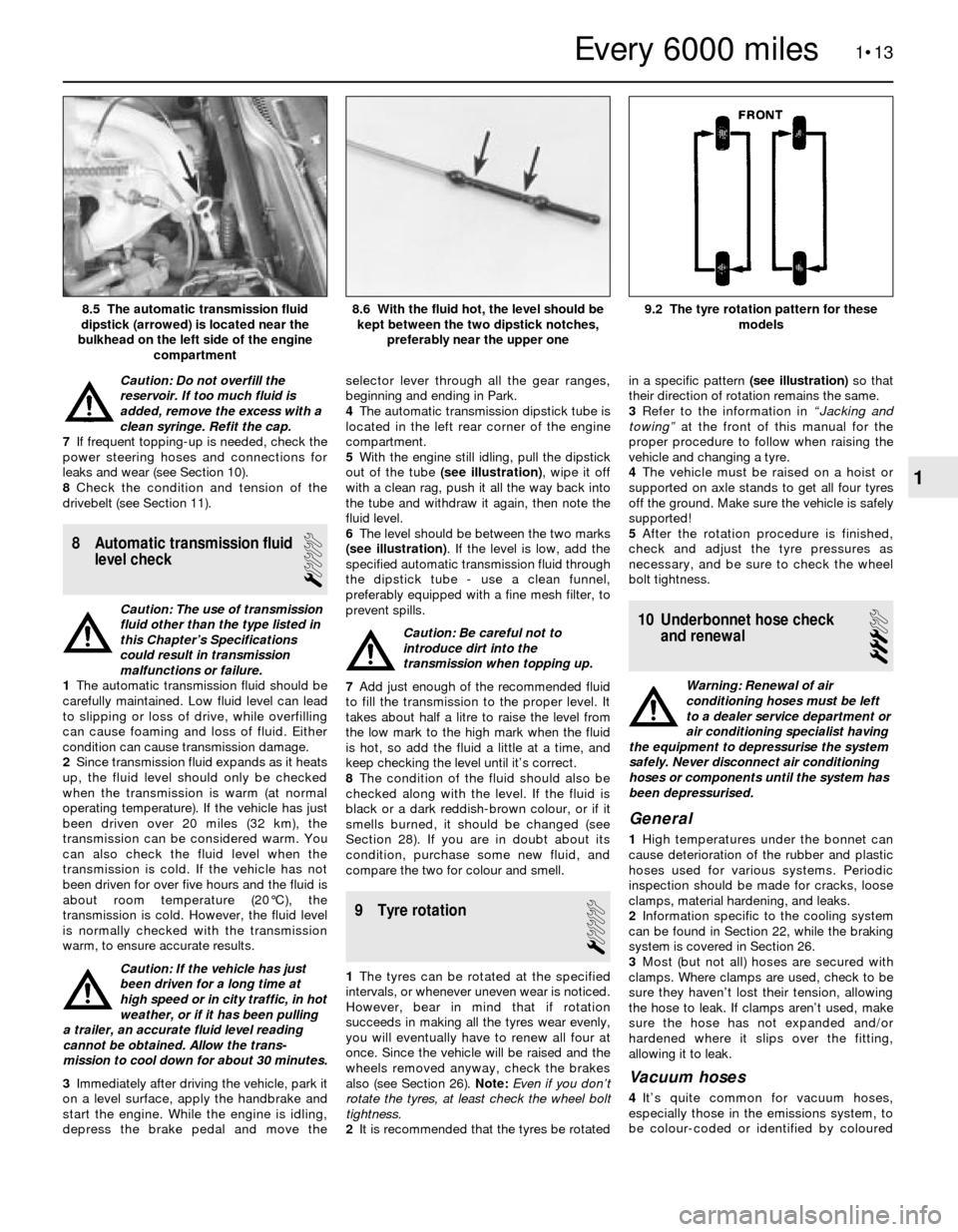
Caution: Do not overfill the
reservoir. If too much fluid is
added, remove the excess with a
clean syringe. Refit the cap.
7If frequent topping-up is needed, check the
power steering hoses and connections for
leaks and wear (see Section 10).
8Check the condition and tension of the
drivebelt (see Section 11).
8 Automatic transmission fluid
level check
1
Caution: The use of transmission
fluid other than the type listed in
this Chapter’s Specifications
could result in transmission
malfunctions or failure.
1The automatic transmission fluid should be
carefully maintained. Low fluid level can lead
to slipping or loss of drive, while overfilling
can cause foaming and loss of fluid. Either
condition can cause transmission damage.
2Since transmission fluid expands as it heats
up, the fluid level should only be checked
when the transmission is warm (at normal
operating temperature). If the vehicle has just
been driven over 20 miles (32 km), the
transmission can be considered warm. You
can also check the fluid level when the
transmission is cold. If the vehicle has not
been driven for over five hours and the fluid is
about room temperature (20°C), the
transmission is cold. However, the fluid level
is normally checked with the transmission
warm, to ensure accurate results.
Caution: If the vehicle has just
been driven for a long time at
high speed or in city traffic, in hot
weather, or if it has been pulling
a trailer, an accurate fluid level reading
cannot be obtained. Allow the trans-
mission to cool down for about 30 minutes.
3Immediately after driving the vehicle, park it
on a level surface, apply the handbrake and
start the engine. While the engine is idling,
depress the brake pedal and move theselector lever through all the gear ranges,
beginning and ending in Park.
4The automatic transmission dipstick tube is
located in the left rear corner of the engine
compartment.
5With the engine still idling, pull the dipstick
out of the tube (see illustration), wipe it off
with a clean rag, push it all the way back into
the tube and withdraw it again, then note the
fluid level.
6The level should be between the two marks
(see illustration). If the level is low, add the
specified automatic transmission fluid through
the dipstick tube - use a clean funnel,
preferably equipped with a fine mesh filter, to
prevent spills.
Caution: Be careful not to
introduce dirt into the
transmission when topping up.
7Add just enough of the recommended fluid
to fill the transmission to the proper level. It
takes about half a litre to raise the level from
the low mark to the high mark when the fluid
is hot, so add the fluid a little at a time, and
keep checking the level until it’s correct.
8The condition of the fluid should also be
checked along with the level. If the fluid is
black or a dark reddish-brown colour, or if it
smells burned, it should be changed (see
Section 28). If you are in doubt about its
condition, purchase some new fluid, and
compare the two for colour and smell.
9 Tyre rotation
1
1The tyres can be rotated at the specified
intervals, or whenever uneven wear is noticed.
However, bear in mind that if rotation
succeeds in making all the tyres wear evenly,
you will eventually have to renew all four at
once. Since the vehicle will be raised and the
wheels removed anyway, check the brakes
also (see Section 26). Note: Even if you don’t
rotate the tyres, at least check the wheel bolt
tightness.
2It is recommended that the tyres be rotatedin a specific pattern (see illustration)so that
their direction of rotation remains the same.
3Refer to the information in “Jacking and
towing”at the front of this manual for the
proper procedure to follow when raising the
vehicle and changing a tyre.
4The vehicle must be raised on a hoist or
supported on axle stands to get all four tyres
off the ground. Make sure the vehicle is safely
supported!
5After the rotation procedure is finished,
check and adjust the tyre pressures as
necessary, and be sure to check the wheel
bolt tightness.
10 Underbonnet hose check
and renewal
3
Warning: Renewal of air
conditioning hoses must be left
to a dealer service department or
air conditioning specialist having
the equipment to depressurise the system
safely. Never disconnect air conditioning
hoses or components until the system has
been depressurised.
General
1High temperatures under the bonnet can
cause deterioration of the rubber and plastic
hoses used for various systems. Periodic
inspection should be made for cracks, loose
clamps, material hardening, and leaks.
2Information specific to the cooling system
can be found in Section 22, while the braking
system is covered in Section 26.
3Most (but not all) hoses are secured with
clamps. Where clamps are used, check to be
sure they haven’t lost their tension, allowing
the hose to leak. If clamps aren’t used, make
sure the hose has not expanded and/or
hardened where it slips over the fitting,
allowing it to leak.
Vacuum hoses
4It’s quite common for vacuum hoses,
especially those in the emissions system, to
be colour-coded or identified by coloured
1•13
9.2 The tyre rotation pattern for these
models8.6 With the fluid hot, the level should be
kept between the two dipstick notches,
preferably near the upper one8.5 The automatic transmission fluid
dipstick (arrowed) is located near the
bulkhead on the left side of the engine
compartment
1
Every 6000 miles
Page 24 of 228
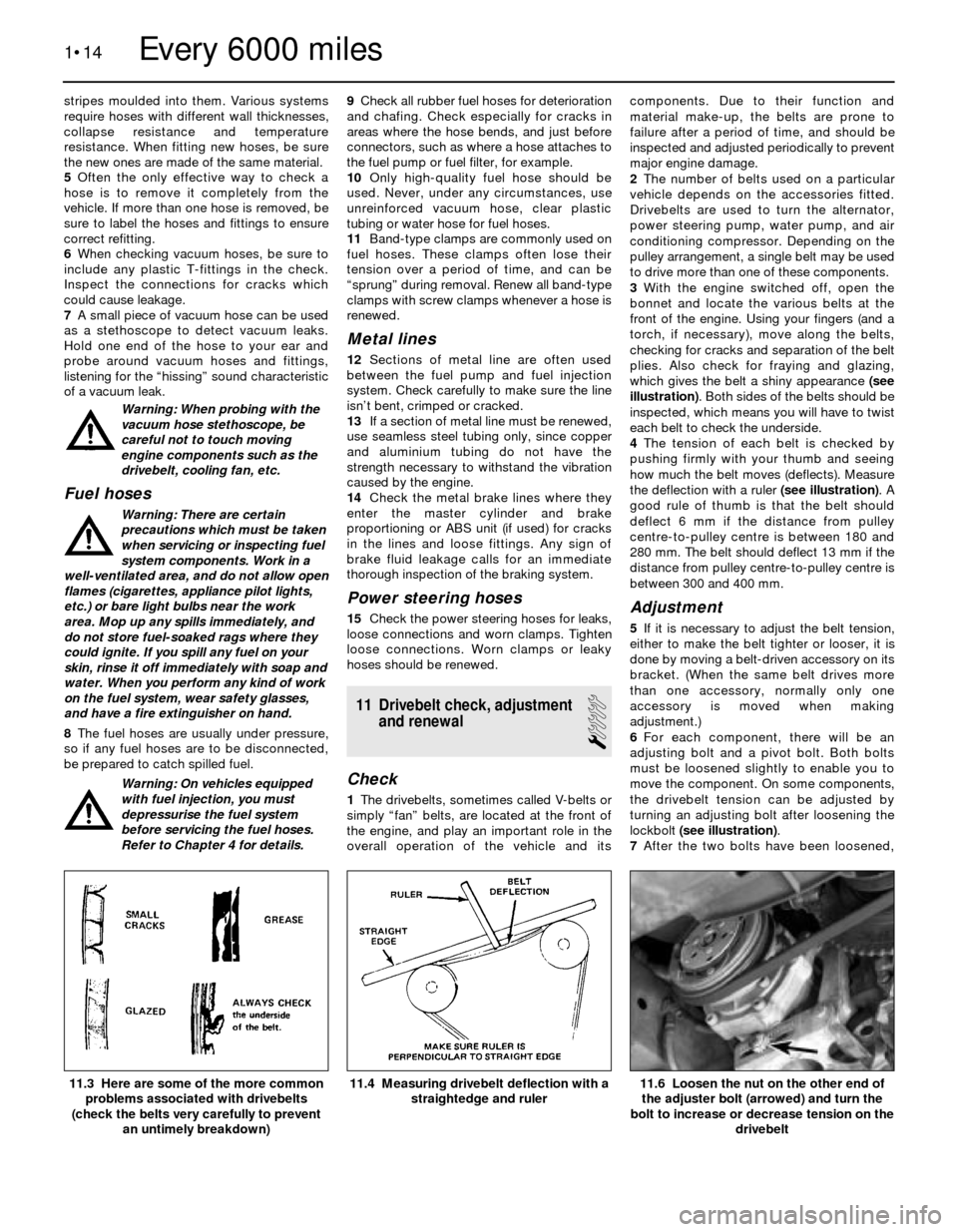
stripes moulded into them. Various systems
require hoses with different wall thicknesses,
collapse resistance and temperature
resistance. When fitting new hoses, be sure
the new ones are made of the same material.
5Often the only effective way to check a
hose is to remove it completely from the
vehicle. If more than one hose is removed, be
sure to label the hoses and fittings to ensure
correct refitting.
6When checking vacuum hoses, be sure to
include any plastic T-fittings in the check.
Inspect the connections for cracks which
could cause leakage.
7A small piece of vacuum hose can be used
as a stethoscope to detect vacuum leaks.
Hold one end of the hose to your ear and
probe around vacuum hoses and fittings,
listening for the “hissing” sound characteristic
of a vacuum leak.
Warning: When probing with the
vacuum hose stethoscope, be
careful not to touch moving
engine components such as the
drivebelt, cooling fan, etc.
Fuel hoses
Warning: There are certain
precautions which must be taken
when servicing or inspecting fuel
system components. Work in a
well-ventilated area, and do not allow open
flames (cigarettes, appliance pilot lights,
etc.) or bare light bulbs near the work
area. Mop up any spills immediately, and
do not store fuel-soaked rags where they
could ignite. If you spill any fuel on your
skin, rinse it off immediately with soap and
water. When you perform any kind of work
on the fuel system, wear safety glasses,
and have a fire extinguisher on hand.
8The fuel hoses are usually under pressure,
so if any fuel hoses are to be disconnected,
be prepared to catch spilled fuel.
Warning: On vehicles equipped
with fuel injection, you must
depressurise the fuel system
before servicing the fuel hoses.
Refer to Chapter 4 for details.9Check all rubber fuel hoses for deterioration
and chafing. Check especially for cracks in
areas where the hose bends, and just before
connectors, such as where a hose attaches to
the fuel pump or fuel filter, for example.
10Only high-quality fuel hose should be
used. Never, under any circumstances, use
unreinforced vacuum hose, clear plastic
tubing or water hose for fuel hoses.
11Band-type clamps are commonly used on
fuel hoses. These clamps often lose their
tension over a period of time, and can be
“sprung” during removal. Renew all band-type
clamps with screw clamps whenever a hose is
renewed.
Metal lines
12Sections of metal line are often used
between the fuel pump and fuel injection
system. Check carefully to make sure the line
isn’t bent, crimped or cracked.
13If a section of metal line must be renewed,
use seamless steel tubing only, since copper
and aluminium tubing do not have the
strength necessary to withstand the vibration
caused by the engine.
14Check the metal brake lines where they
enter the master cylinder and brake
proportioning or ABS unit (if used) for cracks
in the lines and loose fittings. Any sign of
brake fluid leakage calls for an immediate
thorough inspection of the braking system.
Power steering hoses
15Check the power steering hoses for leaks,
loose connections and worn clamps. Tighten
loose connections. Worn clamps or leaky
hoses should be renewed.
11 Drivebelt check, adjustment
and renewal
1
Check
1The drivebelts, sometimes called V-belts or
simply “fan” belts, are located at the front of
the engine, and play an important role in the
overall operation of the vehicle and itscomponents. Due to their function and
material make-up, the belts are prone to
failure after a period of time, and should be
inspected and adjusted periodically to prevent
major engine damage.
2The number of belts used on a particular
vehicle depends on the accessories fitted.
Drivebelts are used to turn the alternator,
power steering pump, water pump, and air
conditioning compressor. Depending on the
pulley arrangement, a single belt may be used
to drive more than one of these components.
3With the engine switched off, open the
bonnet and locate the various belts at the
front of the engine. Using your fingers (and a
torch, if necessary), move along the belts,
checking for cracks and separation of the belt
plies. Also check for fraying and glazing,
which gives the belt a shiny appearance (see
illustration). Both sides of the belts should be
inspected, which means you will have to twist
each belt to check the underside.
4The tension of each belt is checked by
pushing firmly with your thumb and seeing
how much the belt moves (deflects). Measure
the deflection with a ruler (see illustration). A
good rule of thumb is that the belt should
deflect 6 mm if the distance from pulley
centre-to-pulley centre is between 180 and
280 mm. The belt should deflect 13 mm if the
distance from pulley centre-to-pulley centre is
between 300 and 400 mm.
Adjustment
5If it is necessary to adjust the belt tension,
either to make the belt tighter or looser, it is
done by moving a belt-driven accessory on its
bracket. (When the same belt drives more
than one accessory, normally only one
accessory is moved when making
adjustment.)
6For each component, there will be an
adjusting bolt and a pivot bolt. Both bolts
must be loosened slightly to enable you to
move the component. On some components,
the drivebelt tension can be adjusted by
turning an adjusting bolt after loosening the
lockbolt (see illustration).
7After the two bolts have been loosened,
1•14
11.6 Loosen the nut on the other end of
the adjuster bolt (arrowed) and turn the
bolt to increase or decrease tension on the
drivebelt11.4 Measuring drivebelt deflection with a
straightedge and ruler11.3 Here are some of the more common
problems associated with drivebelts
(check the belts very carefully to prevent
an untimely breakdown)
Every 6000 miles
Page 31 of 228
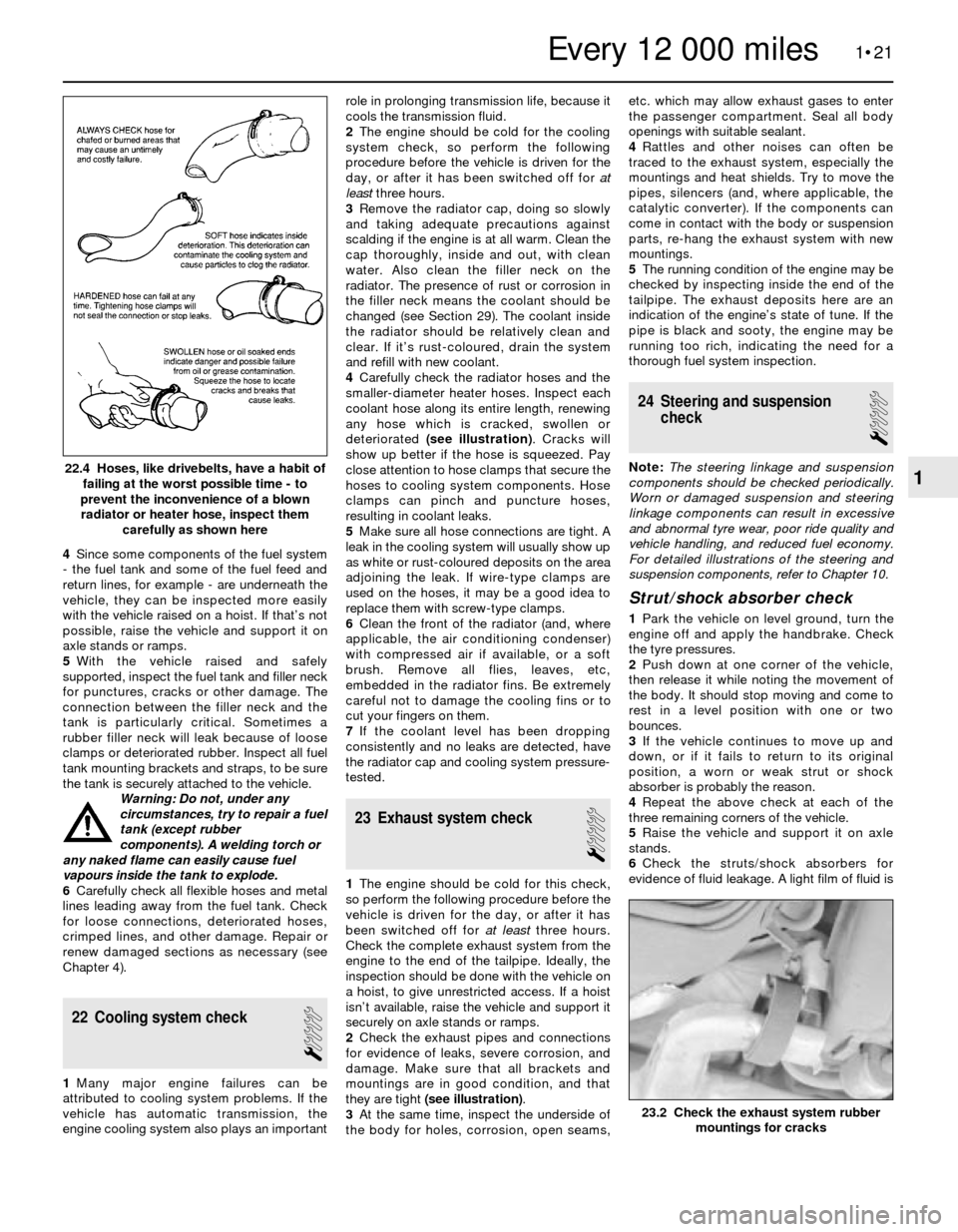
4Since some components of the fuel system
- the fuel tank and some of the fuel feed and
return lines, for example - are underneath the
vehicle, they can be inspected more easily
with the vehicle raised on a hoist. If that’s not
possible, raise the vehicle and support it on
axle stands or ramps.
5With the vehicle raised and safely
supported, inspect the fuel tank and filler neck
for punctures, cracks or other damage. The
connection between the filler neck and the
tank is particularly critical. Sometimes a
rubber filler neck will leak because of loose
clamps or deteriorated rubber. Inspect all fuel
tank mounting brackets and straps, to be sure
the tank is securely attached to the vehicle.
Warning: Do not, under any
circumstances, try to repair a fuel
tank (except rubber
components). A welding torch or
any naked flame can easily cause fuel
vapours inside the tank to explode.
6Carefully check all flexible hoses and metal
lines leading away from the fuel tank. Check
for loose connections, deteriorated hoses,
crimped lines, and other damage. Repair or
renew damaged sections as necessary (see
Chapter 4).
22 Cooling system check
1
1Many major engine failures can be
attributed to cooling system problems. If the
vehicle has automatic transmission, the
engine cooling system also plays an importantrole in prolonging transmission life, because it
cools the transmission fluid.
2The engine should be cold for the cooling
system check, so perform the following
procedure before the vehicle is driven for the
day, or after it has been switched off for at
leastthree hours.
3Remove the radiator cap, doing so slowly
and taking adequate precautions against
scalding if the engine is at all warm. Clean the
cap thoroughly, inside and out, with clean
water. Also clean the filler neck on the
radiator. The presence of rust or corrosion in
the filler neck means the coolant should be
changed (see Section 29). The coolant inside
the radiator should be relatively clean and
clear. If it’s rust-coloured, drain the system
and refill with new coolant.
4Carefully check the radiator hoses and the
smaller-diameter heater hoses. Inspect each
coolant hose along its entire length, renewing
any hose which is cracked, swollen or
deteriorated (see illustration). Cracks will
show up better if the hose is squeezed. Pay
close attention to hose clamps that secure the
hoses to cooling system components. Hose
clamps can pinch and puncture hoses,
resulting in coolant leaks.
5Make sure all hose connections are tight. A
leak in the cooling system will usually show up
as white or rust-coloured deposits on the area
adjoining the leak. If wire-type clamps are
used on the hoses, it may be a good idea to
replace them with screw-type clamps.
6Clean the front of the radiator (and, where
applicable, the air conditioning condenser)
with compressed air if available, or a soft
brush. Remove all flies, leaves, etc,
embedded in the radiator fins. Be extremely
careful not to damage the cooling fins or to
cut your fingers on them.
7If the coolant level has been dropping
consistently and no leaks are detected, have
the radiator cap and cooling system pressure-
tested.
23 Exhaust system check
1
1The engine should be cold for this check,
so perform the following procedure before the
vehicle is driven for the day, or after it has
been switched off for at leastthree hours.
Check the complete exhaust system from the
engine to the end of the tailpipe. Ideally, the
inspection should be done with the vehicle on
a hoist, to give unrestricted access. If a hoist
isn’t available, raise the vehicle and support it
securely on axle stands or ramps.
2Check the exhaust pipes and connections
for evidence of leaks, severe corrosion, and
damage. Make sure that all brackets and
mountings are in good condition, and that
they are tight (see illustration).
3At the same time, inspect the underside of
the body for holes, corrosion, open seams,etc. which may allow exhaust gases to enter
the passenger compartment. Seal all body
openings with suitable sealant.
4Rattles and other noises can often be
traced to the exhaust system, especially the
mountings and heat shields. Try to move the
pipes, silencers (and, where applicable, the
catalytic converter). If the components can
come in contact with the body or suspension
parts, re-hang the exhaust system with new
mountings.
5The running condition of the engine may be
checked by inspecting inside the end of the
tailpipe. The exhaust deposits here are an
indication of the engine’s state of tune. If the
pipe is black and sooty, the engine may be
running too rich, indicating the need for a
thorough fuel system inspection.
24 Steering and suspension
check
1
Note: The steering linkage and suspension
components should be checked periodically.
Worn or damaged suspension and steering
linkage components can result in excessive
and abnormal tyre wear, poor ride quality and
vehicle handling, and reduced fuel economy.
For detailed illustrations of the steering and
suspension components, refer to Chapter 10.
Strut/shock absorber check
1Park the vehicle on level ground, turn the
engine off and apply the handbrake. Check
the tyre pressures.
2Push down at one corner of the vehicle,
then release it while noting the movement of
the body. It should stop moving and come to
rest in a level position with one or two
bounces.
3If the vehicle continues to move up and
down, or if it fails to return to its original
position, a worn or weak strut or shock
absorber is probably the reason.
4Repeat the above check at each of the
three remaining corners of the vehicle.
5Raise the vehicle and support it on axle
stands.
6Check the struts/shock absorbers for
evidence of fluid leakage. A light film of fluid is
1•21
22.4 Hoses, like drivebelts, have a habit of
failing at the worst possible time - to
prevent the inconvenience of a blown
radiator or heater hose, inspect them
carefully as shown here
23.2 Check the exhaust system rubber
mountings for cracks
1
Every 12 000 miles
Page 40 of 228
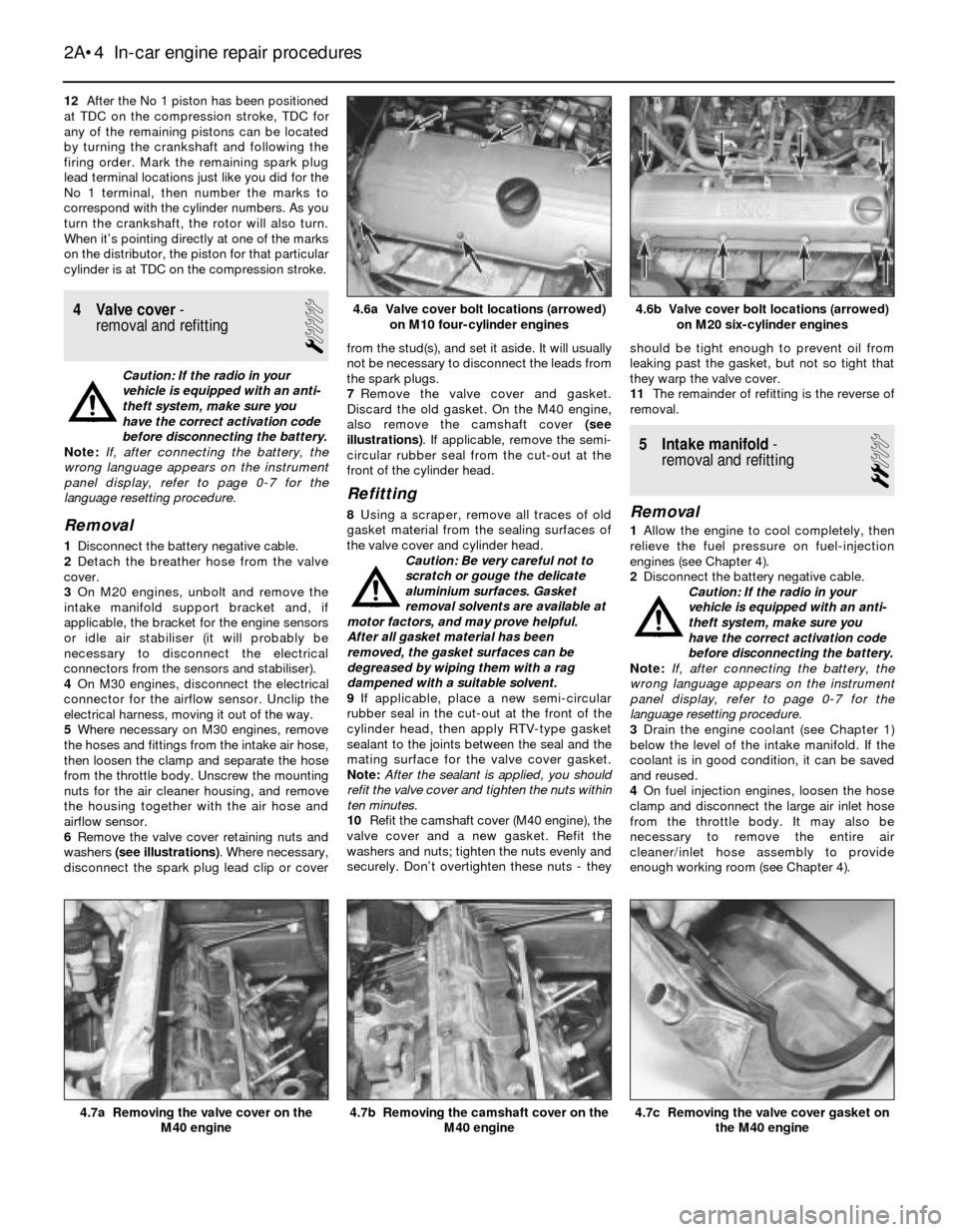
12After the No 1 piston has been positioned
at TDC on the compression stroke, TDC for
any of the remaining pistons can be located
by turning the crankshaft and following the
firing order. Mark the remaining spark plug
lead terminal locations just like you did for the
No 1 terminal, then number the marks to
correspond with the cylinder numbers. As you
turn the crankshaft, the rotor will also turn.
When it’s pointing directly at one of the marks
on the distributor, the piston for that particular
cylinder is at TDC on the compression stroke.
4 Valve cover-
removal and refitting
1
Caution: If the radio in your
vehicle is equipped with an anti-
theft system, make sure you
have the correct activation code
before disconnecting the battery.
Note: If, after connecting the battery, the
wrong language appears on the instrument
panel display, refer to page 0-7 for the
language resetting procedure.
Removal
1Disconnect the battery negative cable.
2Detach the breather hose from the valve
cover.
3On M20 engines, unbolt and remove the
intake manifold support bracket and, if
applicable, the bracket for the engine sensors
or idle air stabiliser (it will probably be
necessary to disconnect the electrical
connectors from the sensors and stabiliser).
4On M30 engines, disconnect the electrical
connector for the airflow sensor. Unclip the
electrical harness, moving it out of the way.
5Where necessary on M30 engines, remove
the hoses and fittings from the intake air hose,
then loosen the clamp and separate the hose
from the throttle body. Unscrew the mounting
nuts for the air cleaner housing, and remove
the housing together with the air hose and
airflow sensor.
6Remove the valve cover retaining nuts and
washers (see illustrations). Where necessary,
disconnect the spark plug lead clip or coverfrom the stud(s), and set it aside. It will usually
not be necessary to disconnect the leads from
the spark plugs.
7Remove the valve cover and gasket.
Discard the old gasket. On the M40 engine,
also remove the camshaft cover (see
illustrations). If applicable, remove the semi-
circular rubber seal from the cut-out at the
front of the cylinder head.
Refitting
8Using a scraper, remove all traces of old
gasket material from the sealing surfaces of
the valve cover and cylinder head.
Caution: Be very careful not to
scratch or gouge the delicate
aluminium surfaces. Gasket
removal solvents are available at
motor factors, and may prove helpful.
After all gasket material has been
removed, the gasket surfaces can be
degreased by wiping them with a rag
dampened with a suitable solvent.
9If applicable, place a new semi-circular
rubber seal in the cut-out at the front of the
cylinder head, then apply RTV-type gasket
sealant to the joints between the seal and the
mating surface for the valve cover gasket.
Note:After the sealant is applied, you should
refit the valve cover and tighten the nuts within
ten minutes.
10Refit the camshaft cover (M40 engine), the
valve cover and a new gasket. Refit the
washers and nuts; tighten the nuts evenly and
securely. Don’t overtighten these nuts - theyshould be tight enough to prevent oil from
leaking past the gasket, but not so tight that
they warp the valve cover.
11The remainder of refitting is the reverse of
removal.
5 Intake manifold-
removal and refitting
2
Removal
1Allow the engine to cool completely, then
relieve the fuel pressure on fuel-injection
engines (see Chapter 4).
2Disconnect the battery negative cable.
Caution: If the radio in your
vehicle is equipped with an anti-
theft system, make sure you
have the correct activation code
before disconnecting the battery.
Note: If, after connecting the battery, the
wrong language appears on the instrument
panel display, refer to page 0-7 for the
language resetting procedure.
3Drain the engine coolant (see Chapter 1)
below the level of the intake manifold. If the
coolant is in good condition, it can be saved
and reused.
4On fuel injection engines, loosen the hose
clamp and disconnect the large air inlet hose
from the throttle body. It may also be
necessary to remove the entire air
cleaner/inlet hose assembly to provide
enough working room (see Chapter 4).
2A•4 In-car engine repair procedures
4.7b Removing the camshaft cover on the
M40 engine4.7a Removing the valve cover on the
M40 engine4.7c Removing the valve cover gasket on
the M40 engine
4.6b Valve cover bolt locations (arrowed)
on M20 six-cylinder engines4.6a Valve cover bolt locations (arrowed)
on M10 four-cylinder engines
Page 51 of 228
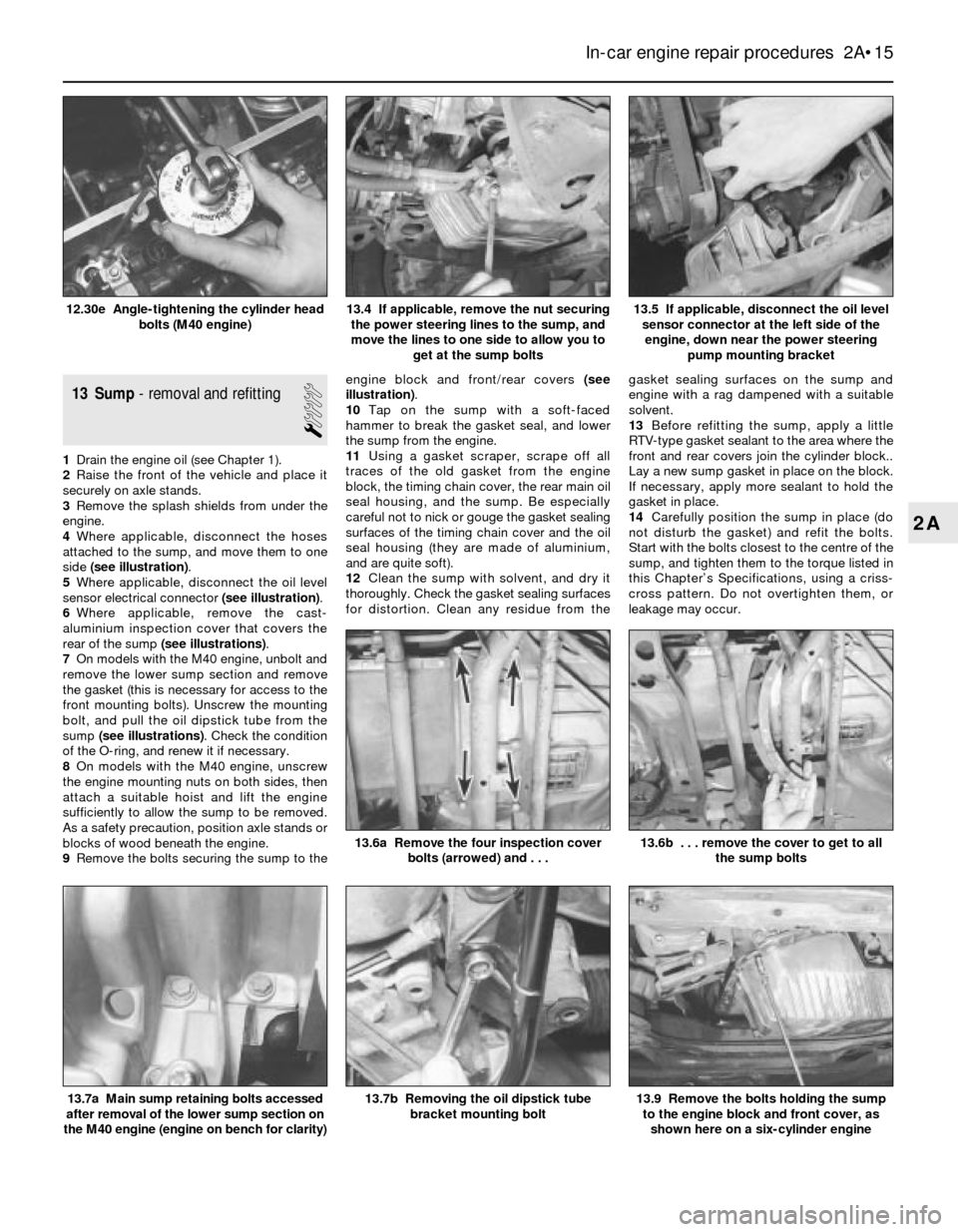
13 Sump- removal and refitting
1
1Drain the engine oil (see Chapter 1).
2Raise the front of the vehicle and place it
securely on axle stands.
3Remove the splash shields from under the
engine.
4Where applicable, disconnect the hoses
attached to the sump, and move them to one
side (see illustration).
5Where applicable, disconnect the oil level
sensor electrical connector (see illustration).
6Where applicable, remove the cast-
aluminium inspection cover that covers the
rear of the sump (see illustrations).
7On models with the M40 engine, unbolt and
remove the lower sump section and remove
the gasket (this is necessary for access to the
front mounting bolts). Unscrew the mounting
bolt, and pull the oil dipstick tube from the
sump (see illustrations). Check the condition
of the O-ring, and renew it if necessary.
8On models with the M40 engine, unscrew
the engine mounting nuts on both sides, then
attach a suitable hoist and lift the engine
sufficiently to allow the sump to be removed.
As a safety precaution, position axle stands or
blocks of wood beneath the engine.
9Remove the bolts securing the sump to theengine block and front/rear covers (see
illustration).
10Tap on the sump with a soft-faced
hammer to break the gasket seal, and lower
the sump from the engine.
11Using a gasket scraper, scrape off all
traces of the old gasket from the engine
block, the timing chain cover, the rear main oil
seal housing, and the sump. Be especially
careful not to nick or gouge the gasket sealing
surfaces of the timing chain cover and the oil
seal housing (they are made of aluminium,
and are quite soft).
12Clean the sump with solvent, and dry it
thoroughly. Check the gasket sealing surfaces
for distortion. Clean any residue from thegasket sealing surfaces on the sump and
engine with a rag dampened with a suitable
solvent.
13Before refitting the sump, apply a little
RTV-type gasket sealant to the area where the
front and rear covers join the cylinder block..
Lay a new sump gasket in place on the block.
If necessary, apply more sealant to hold the
gasket in place.
14Carefully position the sump in place (do
not disturb the gasket) and refit the bolts.
Start with the bolts closest to the centre of the
sump, and tighten them to the torque listed in
this Chapter’s Specifications, using a criss-
cross pattern. Do not overtighten them, or
leakage may occur.
In-car engine repair procedures 2A•15
13.5 If applicable, disconnect the oil level
sensor connector at the left side of the
engine, down near the power steering
pump mounting bracket13.4 If applicable, remove the nut securing
the power steering lines to the sump, and
move the lines to one side to allow you to
get at the sump bolts12.30e Angle-tightening the cylinder head
bolts (M40 engine)
13.9 Remove the bolts holding the sump
to the engine block and front cover, as
shown here on a six-cylinder engine13.7b Removing the oil dipstick tube
bracket mounting bolt
13.6b . . . remove the cover to get to all
the sump bolts13.6a Remove the four inspection cover
bolts (arrowed) and . . .
13.7a Main sump retaining bolts accessed
after removal of the lower sump section on
the M40 engine (engine on bench for clarity)
2A
Page 53 of 228
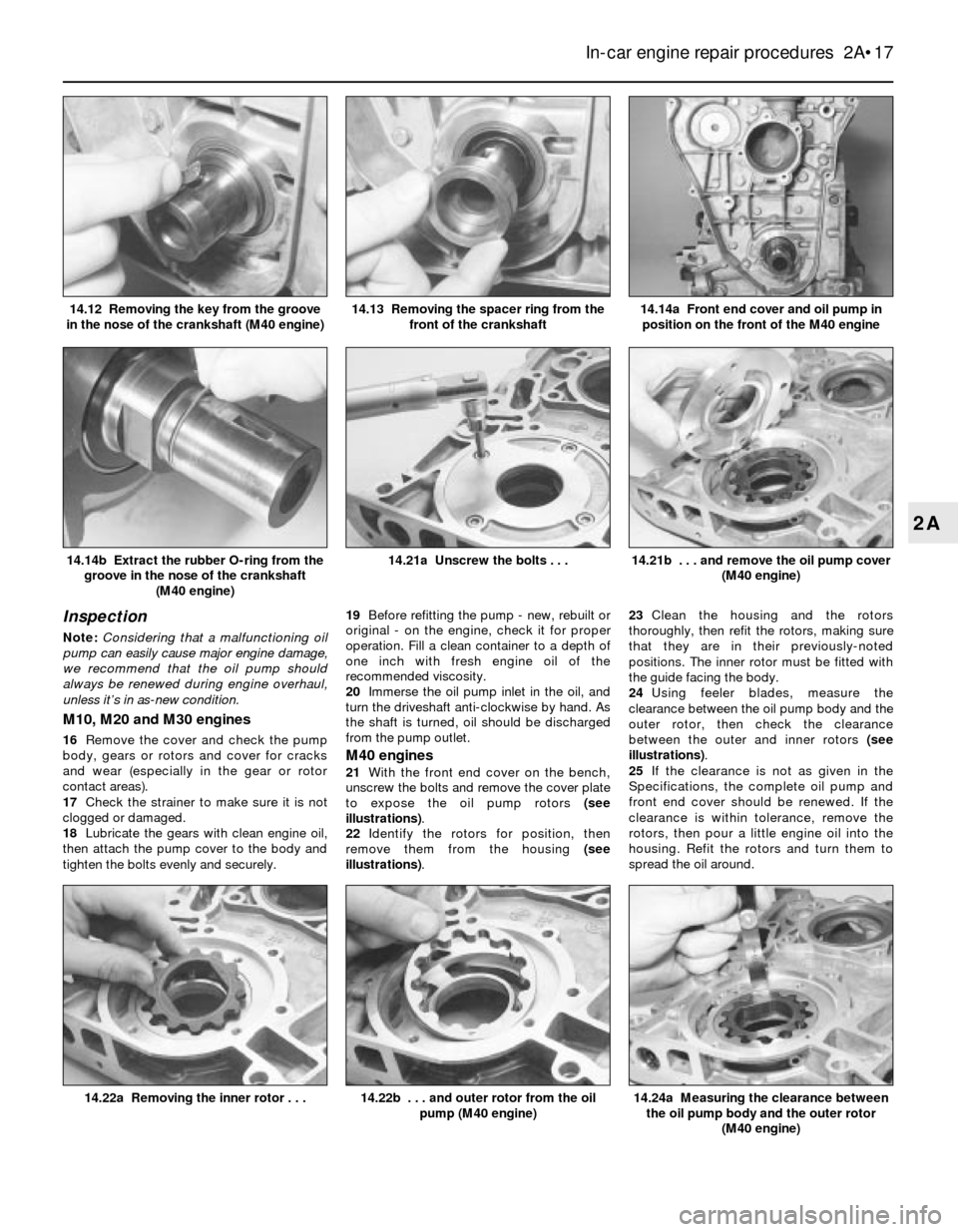
Inspection
Note:Considering that a malfunctioning oil
pump can easily cause major engine damage,
we recommend that the oil pump should
always be renewed during engine overhaul,
unless it’s in as-new condition.
M10, M20 and M30 engines
16Remove the cover and check the pump
body, gears or rotors and cover for cracks
and wear (especially in the gear or rotor
contact areas).
17Check the strainer to make sure it is not
clogged or damaged.
18Lubricate the gears with clean engine oil,
then attach the pump cover to the body and
tighten the bolts evenly and securely.19Before refitting the pump - new, rebuilt or
original - on the engine, check it for proper
operation. Fill a clean container to a depth of
one inch with fresh engine oil of the
recommended viscosity.
20Immerse the oil pump inlet in the oil, and
turn the driveshaft anti-clockwise by hand. As
the shaft is turned, oil should be discharged
from the pump outlet.M40 engines
21With the front end cover on the bench,
unscrew the bolts and remove the cover plate
to expose the oil pump rotors (see
illustrations).
22Identify the rotors for position, then
remove them from the housing (see
illustrations).23Clean the housing and the rotors
thoroughly, then refit the rotors, making sure
that they are in their previously-noted
positions. The inner rotor must be fitted with
the guide facing the body.
24Using feeler blades, measure the
clearance between the oil pump body and the
outer rotor, then check the clearance
between the outer and inner rotors (see
illustrations).
25If the clearance is not as given in the
Specifications, the complete oil pump and
front end cover should be renewed. If the
clearance is within tolerance, remove the
rotors, then pour a little engine oil into the
housing. Refit the rotors and turn them to
spread the oil around.
In-car engine repair procedures 2A•17
14.14a Front end cover and oil pump in
position on the front of the M40 engine14.13 Removing the spacer ring from the
front of the crankshaft14.12 Removing the key from the groove
in the nose of the crankshaft (M40 engine)
14.24a Measuring the clearance between
the oil pump body and the outer rotor
(M40 engine)14.22b . . . and outer rotor from the oil
pump (M40 engine)14.22a Removing the inner rotor . . .
14.21b . . . and remove the oil pump cover
(M40 engine)14.21a Unscrew the bolts . . .14.14b Extract the rubber O-ring from the
groove in the nose of the crankshaft
(M40 engine)
2A
Page 60 of 228
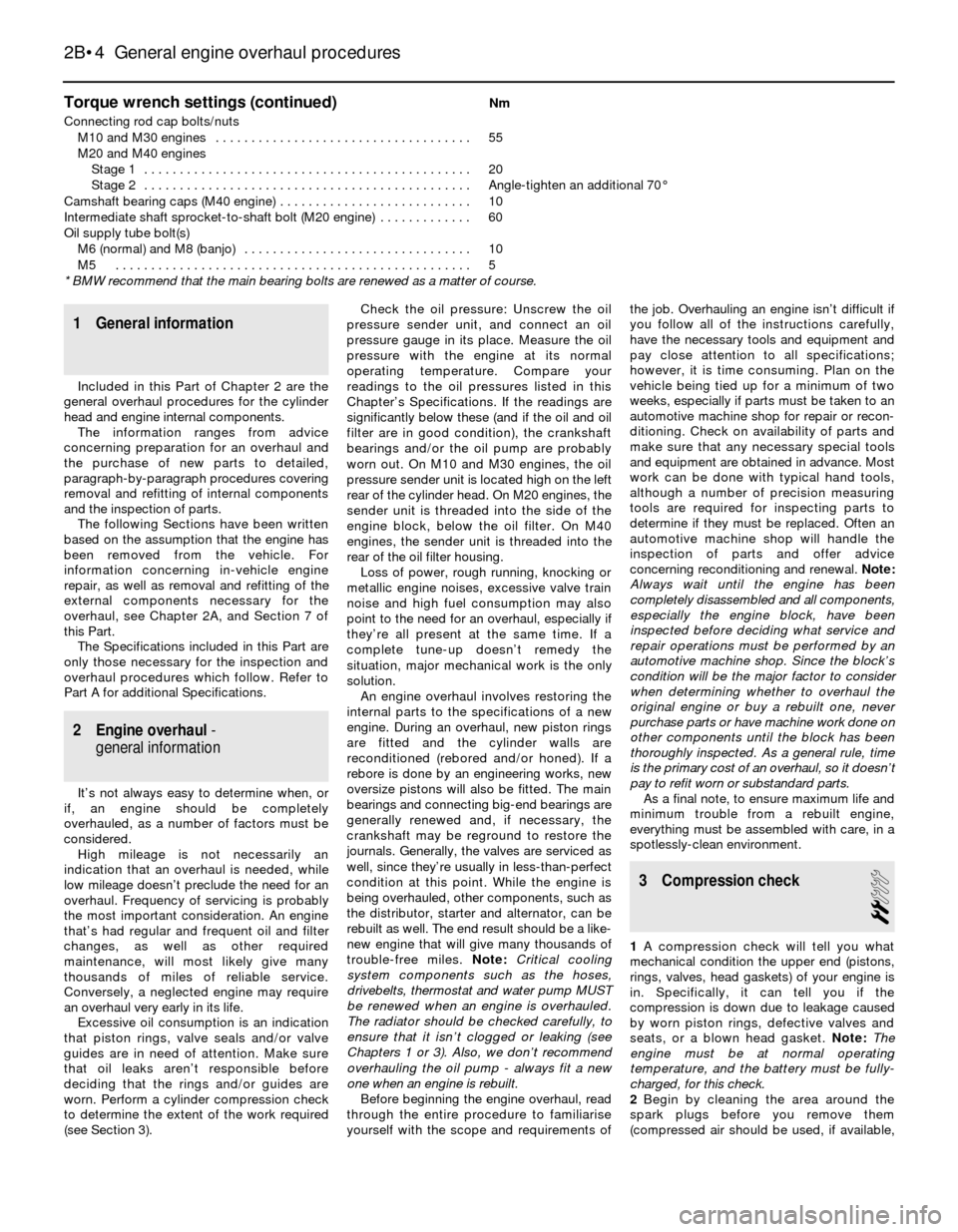
Torque wrench settings (continued)Nm
Connecting rod cap bolts/nuts
M10 and M30 engines . . . . . . . . . . . . . . . . . . . . . . . . . . . . . . . . . . . . 55
M20 and M40 engines
Stage 1 . . . . . . . . . . . . . . . . . . . . . . . . . . . . . . . . . . . . . . . . . . . . . . 20
Stage 2 . . . . . . . . . . . . . . . . . . . . . . . . . . . . . . . . . . . . . . . . . . . . . . Angle-tighten an additional 70°
Camshaft bearing caps (M40 engine) . . . . . . . . . . . . . . . . . . . . . . . . . . . 10
Intermediate shaft sprocket-to-shaft bolt (M20 engine) . . . . . . . . . . . . . 60
Oil supply tube bolt(s)
M6 (normal) and M8 (banjo) . . . . . . . . . . . . . . . . . . . . . . . . . . . . . . . . 10
M5 . . . . . . . . . . . . . . . . . . . . . . . . . . . . . . . . . . . . . . . . . . . . . . . . . . 5
* BMW recommend that the main bearing bolts are renewed as a matter of course.
2B•4 General engine overhaul procedures
1 General information
Included in this Part of Chapter 2 are the
general overhaul procedures for the cylinder
head and engine internal components.
The information ranges from advice
concerning preparation for an overhaul and
the purchase of new parts to detailed,
paragraph-by-paragraph procedures covering
removal and refitting of internal components
and the inspection of parts.
The following Sections have been written
based on the assumption that the engine has
been removed from the vehicle. For
information concerning in-vehicle engine
repair, as well as removal and refitting of the
external components necessary for the
overhaul, see Chapter 2A, and Section 7 of
this Part.
The Specifications included in this Part are
only those necessary for the inspection and
overhaul procedures which follow. Refer to
Part A for additional Specifications.
2 Engine overhaul-
general information
It’s not always easy to determine when, or
if, an engine should be completely
overhauled, as a number of factors must be
considered.
High mileage is not necessarily an
indication that an overhaul is needed, while
low mileage doesn’t preclude the need for an
overhaul. Frequency of servicing is probably
the most important consideration. An engine
that’s had regular and frequent oil and filter
changes, as well as other required
maintenance, will most likely give many
thousands of miles of reliable service.
Conversely, a neglected engine may require
an overhaul very early in its life.
Excessive oil consumption is an indication
that piston rings, valve seals and/or valve
guides are in need of attention. Make sure
that oil leaks aren’t responsible before
deciding that the rings and/or guides are
worn. Perform a cylinder compression check
to determine the extent of the work required
(see Section 3).Check the oil pressure: Unscrew the oil
pressure sender unit, and connect an oil
pressure gauge in its place. Measure the oil
pressure with the engine at its normal
operating temperature. Compare your
readings to the oil pressures listed in this
Chapter’s Specifications. If the readings are
significantly below these (and if the oil and oil
filter are in good condition), the crankshaft
bearings and/or the oil pump are probably
worn out. On M10 and M30 engines, the oil
pressure sender unit is located high on the left
rear of the cylinder head. On M20 engines, the
sender unit is threaded into the side of the
engine block, below the oil filter. On M40
engines, the sender unit is threaded into the
rear of the oil filter housing.
Loss of power, rough running, knocking or
metallic engine noises, excessive valve train
noise and high fuel consumption may also
point to the need for an overhaul, especially if
they’re all present at the same time. If a
complete tune-up doesn’t remedy the
situation, major mechanical work is the only
solution.
An engine overhaul involves restoring the
internal parts to the specifications of a new
engine. During an overhaul, new piston rings
are fitted and the cylinder walls are
reconditioned (rebored and/or honed). If a
rebore is done by an engineering works, new
oversize pistons will also be fitted. The main
bearings and connecting big-end bearings are
generally renewed and, if necessary, the
crankshaft may be reground to restore the
journals. Generally, the valves are serviced as
well, since they’re usually in less-than-perfect
condition at this point. While the engine is
being overhauled, other components, such as
the distributor, starter and alternator, can be
rebuilt as well. The end result should be a like-
new engine that will give many thousands of
trouble-free miles. Note: Critical cooling
system components such as the hoses,
drivebelts, thermostat and water pump MUST
be renewed when an engine is overhauled.
The radiator should be checked carefully, to
ensure that it isn’t clogged or leaking (see
Chapters 1 or 3). Also, we don’t recommend
overhauling the oil pump - always fit a new
one when an engine is rebuilt.
Before beginning the engine overhaul, read
through the entire procedure to familiarise
yourself with the scope and requirements ofthe job. Overhauling an engine isn’t difficult if
you follow all of the instructions carefully,
have the necessary tools and equipment and
pay close attention to all specifications;
however, it is time consuming. Plan on the
vehicle being tied up for a minimum of two
weeks, especially if parts must be taken to an
automotive machine shop for repair or recon-
ditioning. Check on availability of parts and
make sure that any necessary special tools
and equipment are obtained in advance. Most
work can be done with typical hand tools,
although a number of precision measuring
tools are required for inspecting parts to
determine if they must be replaced. Often an
automotive machine shop will handle the
inspection of parts and offer advice
concerning reconditioning and renewal. Note:
Always wait until the engine has been
completely disassembled and all components,
especially the engine block, have been
inspected before deciding what service and
repair operations must be performed by an
automotive machine shop. Since the block’s
condition will be the major factor to consider
when determining whether to overhaul the
original engine or buy a rebuilt one, never
purchase parts or have machine work done on
other components until the block has been
thoroughly inspected. As a general rule, time
is the primary cost of an overhaul, so it doesn’t
pay to refit worn or substandard parts.
As a final note, to ensure maximum life and
minimum trouble from a rebuilt engine,
everything must be assembled with care, in a
spotlessly-clean environment.
3 Compression check
2
1A compression check will tell you what
mechanical condition the upper end (pistons,
rings, valves, head gaskets) of your engine is
in. Specifically, it can tell you if the
compression is down due to leakage caused
by worn piston rings, defective valves and
seats, or a blown head gasket. Note:The
engine must be at normal operating
temperature, and the battery must be fully-
charged, for this check.
2Begin by cleaning the area around the
spark plugs before you remove them
(compressed air should be used, if available,
Page 67 of 228
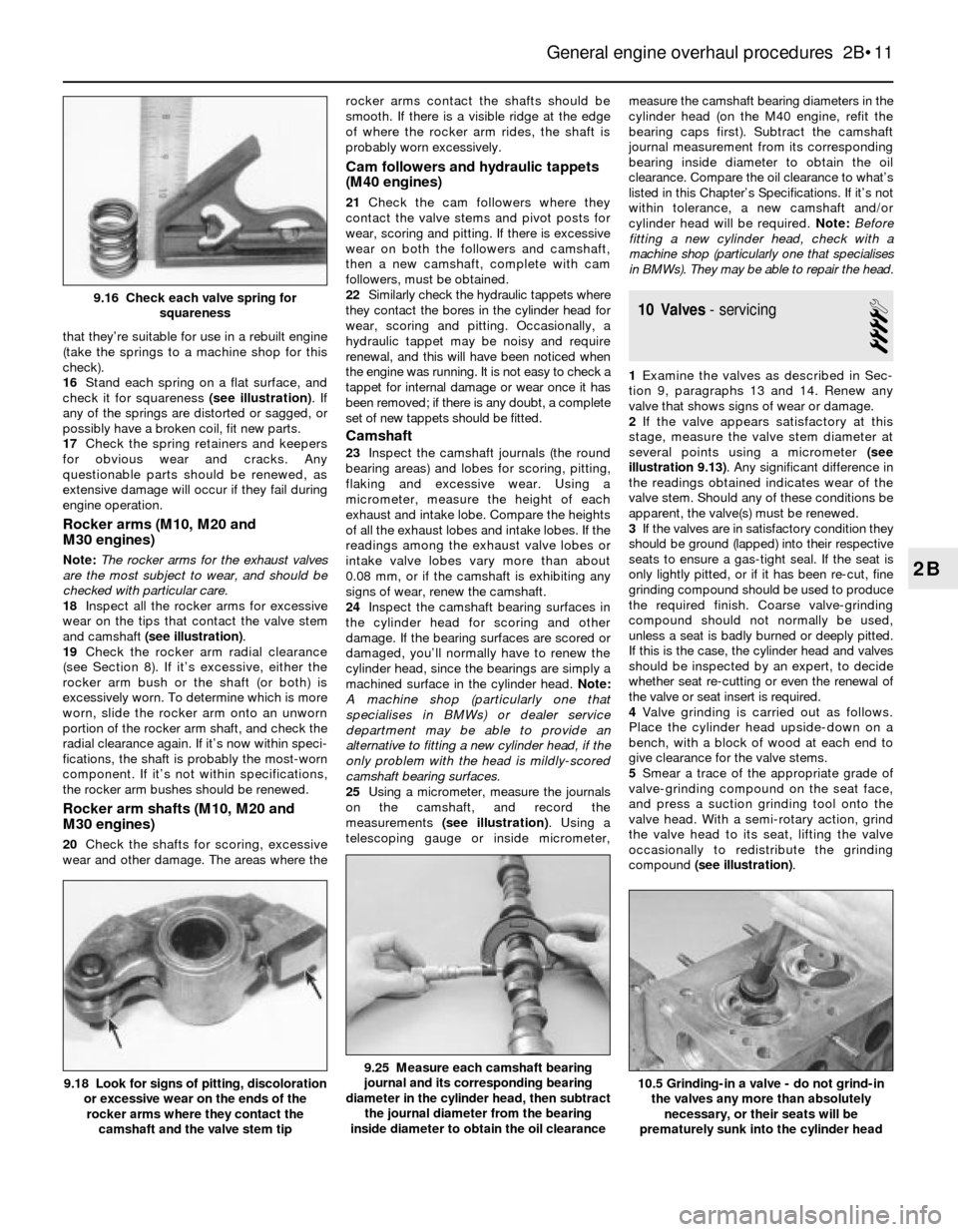
that they’re suitable for use in a rebuilt engine
(take the springs to a machine shop for this
check).
16Stand each spring on a flat surface, and
check it for squareness (see illustration). If
any of the springs are distorted or sagged, or
possibly have a broken coil, fit new parts.
17Check the spring retainers and keepers
for obvious wear and cracks. Any
questionable parts should be renewed, as
extensive damage will occur if they fail during
engine operation.
Rocker arms (M10, M20 and
M30 engines)
Note:The rocker arms for the exhaust valves
are the most subject to wear, and should be
checked with particular care.
18Inspect all the rocker arms for excessive
wear on the tips that contact the valve stem
and camshaft (see illustration).
19Check the rocker arm radial clearance
(see Section 8). If it’s excessive, either the
rocker arm bush or the shaft (or both) is
excessively worn. To determine which is more
worn, slide the rocker arm onto an unworn
portion of the rocker arm shaft, and check the
radial clearance again. If it’s now within speci-
fications, the shaft is probably the most-worn
component. If it’s not within specifications,
the rocker arm bushes should be renewed.
Rocker arm shafts (M10, M20 and
M30 engines)
20Check the shafts for scoring, excessive
wear and other damage. The areas where therocker arms contact the shafts should be
smooth. If there is a visible ridge at the edge
of where the rocker arm rides, the shaft is
probably worn excessively.
Cam followers and hydraulic tappets
(M40 engines)
21Check the cam followers where they
contact the valve stems and pivot posts for
wear, scoring and pitting. If there is excessive
wear on both the followers and camshaft,
then a new camshaft, complete with cam
followers, must be obtained.
22Similarly check the hydraulic tappets where
they contact the bores in the cylinder head for
wear, scoring and pitting. Occasionally, a
hydraulic tappet may be noisy and require
renewal, and this will have been noticed when
the engine was running. It is not easy to check a
tappet for internal damage or wear once it has
been removed; if there is any doubt, a complete
set of new tappets should be fitted.
Camshaft
23Inspect the camshaft journals (the round
bearing areas) and lobes for scoring, pitting,
flaking and excessive wear. Using a
micrometer, measure the height of each
exhaust and intake lobe. Compare the heights
of all the exhaust lobes and intake lobes. If the
readings among the exhaust valve lobes or
intake valve lobes vary more than about
0.08 mm, or if the camshaft is exhibiting any
signs of wear, renew the camshaft.
24Inspect the camshaft bearing surfaces in
the cylinder head for scoring and other
damage. If the bearing surfaces are scored or
damaged, you’ll normally have to renew the
cylinder head, since the bearings are simply a
machined surface in the cylinder head. Note:
A machine shop (particularly one that
specialises in BMWs) or dealer service
department may be able to provide an
alternative to fitting a new cylinder head, if the
only problem with the head is mildly-scored
camshaft bearing surfaces.
25Using a micrometer, measure the journals
on the camshaft, and record the
measurements (see illustration). Using a
telescoping gauge or inside micrometer,measure the camshaft bearing diameters in the
cylinder head (on the M40 engine, refit the
bearing caps first). Subtract the camshaft
journal measurement from its corresponding
bearing inside diameter to obtain the oil
clearance. Compare the oil clearance to what’s
listed in this Chapter’s Specifications. If it’s not
within tolerance, a new camshaft and/or
cylinder head will be required. Note:Before
fitting a new cylinder head, check with a
machine shop (particularly one that specialises
in BMWs). They may be able to repair the head.
10 Valves- servicing
4
1Examine the valves as described in Sec-
tion 9, paragraphs 13 and 14. Renew any
valve that shows signs of wear or damage.
2If the valve appears satisfactory at this
stage, measure the valve stem diameter at
several points using a micrometer (see
illustration 9.13). Any significant difference in
the readings obtained indicates wear of the
valve stem. Should any of these conditions be
apparent, the valve(s) must be renewed.
3If the valves are in satisfactory condition they
should be ground (lapped) into their respective
seats to ensure a gas-tight seal. If the seat is
only lightly pitted, or if it has been re-cut, fine
grinding compound should be used to produce
the required finish. Coarse valve-grinding
compound should not normally be used,
unless a seat is badly burned or deeply pitted.
If this is the case, the cylinder head and valves
should be inspected by an expert, to decide
whether seat re-cutting or even the renewal of
the valve or seat insert is required.
4Valve grinding is carried out as follows.
Place the cylinder head upside-down on a
bench, with a block of wood at each end to
give clearance for the valve stems.
5Smear a trace of the appropriate grade of
valve-grinding compound on the seat face,
and press a suction grinding tool onto the
valve head. With a semi-rotary action, grind
the valve head to its seat, lifting the valve
occasionally to redistribute the grinding
compound (see illustration).
General engine overhaul procedures 2B•11
9.25 Measure each camshaft bearing
journal and its corresponding bearing
diameter in the cylinder head, then subtract
the journal diameter from the bearing
inside diameter to obtain the oil clearance9.18 Look for signs of pitting, discoloration
or excessive wear on the ends of the
rocker arms where they contact the
camshaft and the valve stem tip10.5 Grinding-in a valve - do not grind-in
the valves any more than absolutely
necessary, or their seats will be
prematurely sunk into the cylinder head
2B
9.16 Check each valve spring for
squareness