BMW 3 SERIES 1987 E30 Workshop Manual
Manufacturer: BMW, Model Year: 1987, Model line: 3 SERIES, Model: BMW 3 SERIES 1987 E30Pages: 228, PDF Size: 7.04 MB
Page 151 of 228
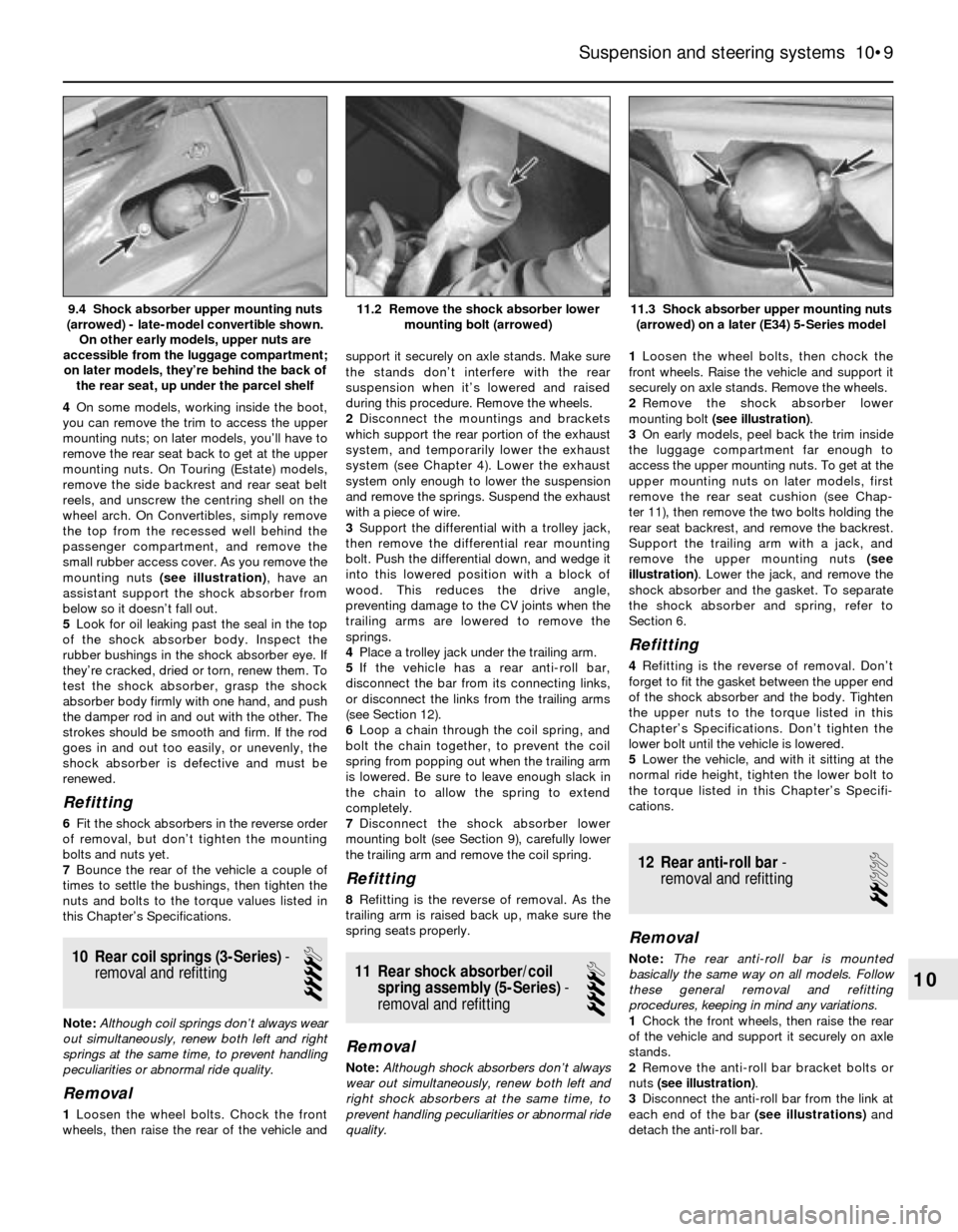
4On some models, working inside the boot,
you can remove the trim to access the upper
mounting nuts; on later models, you’ll have to
remove the rear seat back to get at the upper
mounting nuts. On Touring (Estate) models,
remove the side backrest and rear seat belt
reels, and unscrew the centring shell on the
wheel arch. On Convertibles, simply remove
the top from the recessed well behind the
passenger compartment, and remove the
small rubber access cover. As you remove the
mounting nuts (see illustration), have an
assistant support the shock absorber from
below so it doesn’t fall out.
5Look for oil leaking past the seal in the top
of the shock absorber body. Inspect the
rubber bushings in the shock absorber eye. If
they’re cracked, dried or torn, renew them. To
test the shock absorber, grasp the shock
absorber body firmly with one hand, and push
the damper rod in and out with the other. The
strokes should be smooth and firm. If the rod
goes in and out too easily, or unevenly, the
shock absorber is defective and must be
renewed.
Refitting
6Fit the shock absorbers in the reverse order
of removal, but don’t tighten the mounting
bolts and nuts yet.
7Bounce the rear of the vehicle a couple of
times to settle the bushings, then tighten the
nuts and bolts to the torque values listed in
this Chapter’s Specifications.
10 Rear coil springs (3-Series)-
removal and refitting
4
Note: Although coil springs don’t always wear
out simultaneously, renew both left and right
springs at the same time, to prevent handling
peculiarities or abnormal ride quality.
Removal
1Loosen the wheel bolts. Chock the front
wheels, then raise the rear of the vehicle andsupport it securely on axle stands. Make sure
the stands don’t interfere with the rear
suspension when it’s lowered and raised
during this procedure. Remove the wheels.
2Disconnect the mountings and brackets
which support the rear portion of the exhaust
system, and temporarily lower the exhaust
system (see Chapter 4). Lower the exhaust
system only enough to lower the suspension
and remove the springs. Suspend the exhaust
with a piece of wire.
3Support the differential with a trolley jack,
then remove the differential rear mounting
bolt. Push the differential down, and wedge it
into this lowered position with a block of
wood. This reduces the drive angle,
preventing damage to the CV joints when the
trailing arms are lowered to remove the
springs.
4Place a trolley jack under the trailing arm.
5If the vehicle has a rear anti-roll bar,
disconnect the bar from its connecting links,
or disconnect the links from the trailing arms
(see Section 12).
6Loop a chain through the coil spring, and
bolt the chain together, to prevent the coil
spring from popping out when the trailing arm
is lowered. Be sure to leave enough slack in
the chain to allow the spring to extend
completely.
7Disconnect the shock absorber lower
mounting bolt (see Section 9), carefully lower
the trailing arm and remove the coil spring.
Refitting
8Refitting is the reverse of removal. As the
trailing arm is raised back up, make sure the
spring seats properly.
11 Rear shock absorber/coil
spring assembly (5-Series)-
removal and refitting
4
Removal
Note:Although shock absorbers don’t always
wear out simultaneously, renew both left and
right shock absorbers at the same time, to
prevent handling peculiarities or abnormal ride
quality.1Loosen the wheel bolts, then chock the
front wheels. Raise the vehicle and support it
securely on axle stands. Remove the wheels.
2Remove the shock absorber lower
mounting bolt (see illustration).
3On early models, peel back the trim inside
the luggage compartment far enough to
access the upper mounting nuts. To get at the
upper mounting nuts on later models, first
remove the rear seat cushion (see Chap-
ter 11), then remove the two bolts holding the
rear seat backrest, and remove the backrest.
Support the trailing arm with a jack, and
remove the upper mounting nuts (see
illustration). Lower the jack, and remove the
shock absorber and the gasket. To separate
the shock absorber and spring, refer to
Section 6.
Refitting
4Refitting is the reverse of removal. Don’t
forget to fit the gasket between the upper end
of the shock absorber and the body. Tighten
the upper nuts to the torque listed in this
Chapter’s Specifications. Don’t tighten the
lower bolt until the vehicle is lowered.
5Lower the vehicle, and with it sitting at the
normal ride height, tighten the lower bolt to
the torque listed in this Chapter’s Specifi-
cations.
12 Rear anti-roll bar-
removal and refitting
2
Removal
Note:The rear anti-roll bar is mounted
basically the same way on all models. Follow
these general removal and refitting
procedures, keeping in mind any variations.
1Chock the front wheels, then raise the rear
of the vehicle and support it securely on axle
stands.
2Remove the anti-roll bar bracket bolts or
nuts (see illustration).
3Disconnect the anti-roll bar from the link at
each end of the bar (see illustrations)and
detach the anti-roll bar.
Suspension and steering systems 10•9
11.3 Shock absorber upper mounting nuts
(arrowed) on a later (E34) 5-Series model11.2 Remove the shock absorber lower
mounting bolt (arrowed)9.4 Shock absorber upper mounting nuts
(arrowed) - late-model convertible shown.
On other early models, upper nuts are
accessible from the luggage compartment;
on later models, they’re behind the back of
the rear seat, up under the parcel shelf
10
Page 152 of 228
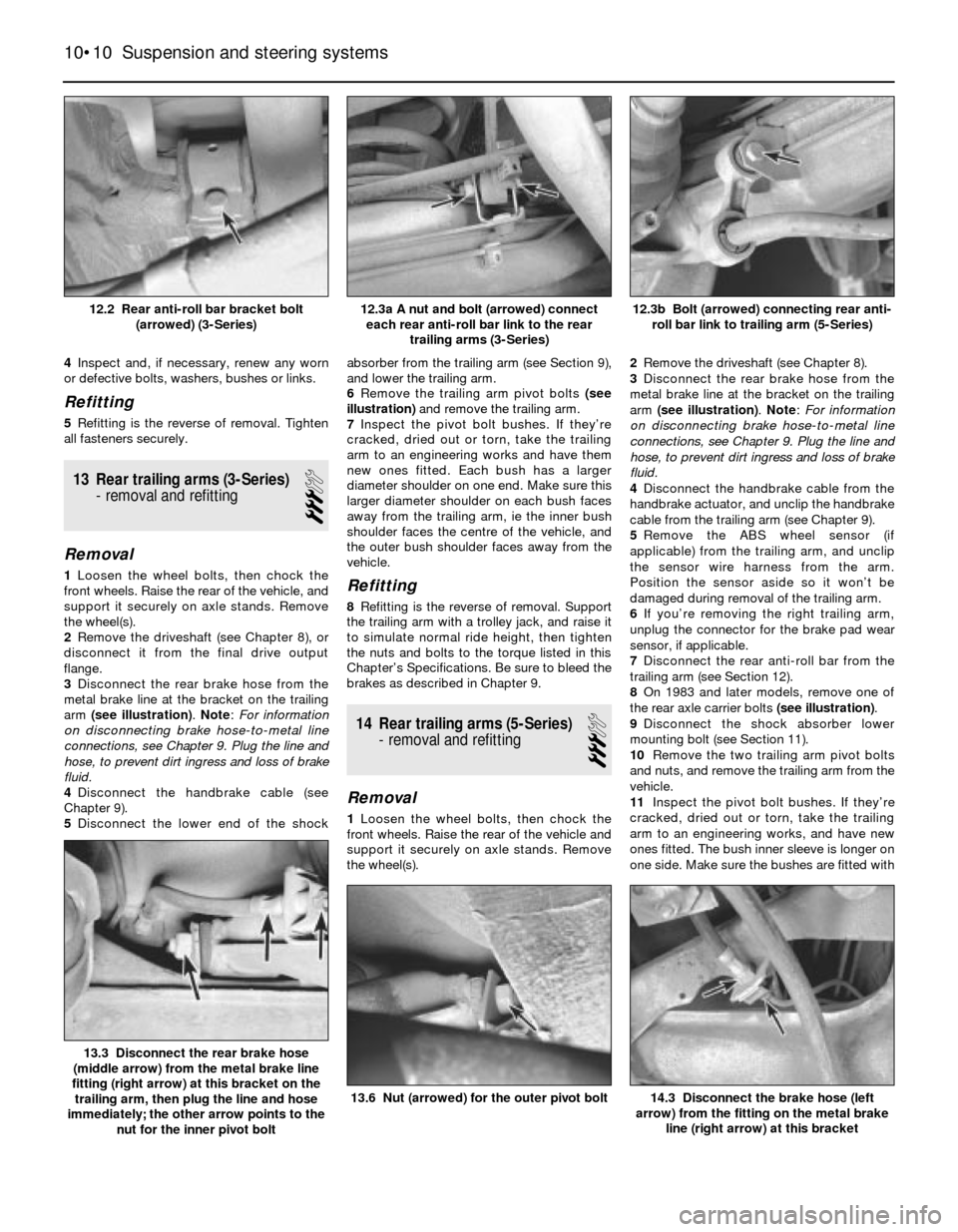
4Inspect and, if necessary, renew any worn
or defective bolts, washers, bushes or links.
Refitting
5Refitting is the reverse of removal. Tighten
all fasteners securely.
13 Rear trailing arms (3-Series)
- removal and refitting
3
Removal
1Loosen the wheel bolts, then chock the
front wheels. Raise the rear of the vehicle, and
support it securely on axle stands. Remove
the wheel(s).
2Remove the driveshaft (see Chapter 8), or
disconnect it from the final drive output
flange.
3Disconnect the rear brake hose from the
metal brake line at the bracket on the trailing
arm (see illustration). Note: For information
on disconnecting brake hose-to-metal line
connections, see Chapter 9. Plug the line and
hose, to prevent dirt ingress and loss of brake
fluid.
4Disconnect the handbrake cable (see
Chapter 9).
5Disconnect the lower end of the shockabsorber from the trailing arm (see Section 9),
and lower the trailing arm.
6Remove the trailing arm pivot bolts (see
illustration)and remove the trailing arm.
7Inspect the pivot bolt bushes. If they’re
cracked, dried out or torn, take the trailing
arm to an engineering works and have them
new ones fitted. Each bush has a larger
diameter shoulder on one end. Make sure this
larger diameter shoulder on each bush faces
away from the trailing arm, ie the inner bush
shoulder faces the centre of the vehicle, and
the outer bush shoulder faces away from the
vehicle.Refitting
8Refitting is the reverse of removal. Support
the trailing arm with a trolley jack, and raise it
to simulate normal ride height, then tighten
the nuts and bolts to the torque listed in this
Chapter’s Specifications. Be sure to bleed the
brakes as described in Chapter 9.
14 Rear trailing arms (5-Series)
- removal and refitting
3
Removal
1Loosen the wheel bolts, then chock the
front wheels. Raise the rear of the vehicle and
support it securely on axle stands. Remove
the wheel(s).2Remove the driveshaft (see Chapter 8).
3Disconnect the rear brake hose from the
metal brake line at the bracket on the trailing
arm (see illustration). Note: For information
on disconnecting brake hose-to-metal line
connections, see Chapter 9. Plug the line and
hose, to prevent dirt ingress and loss of brake
fluid.
4Disconnect the handbrake cable from the
handbrake actuator, and unclip the handbrake
cable from the trailing arm (see Chapter 9).
5Remove the ABS wheel sensor (if
applicable) from the trailing arm, and unclip
the sensor wire harness from the arm.
Position the sensor aside so it won’t be
damaged during removal of the trailing arm.
6If you’re removing the right trailing arm,
unplug the connector for the brake pad wear
sensor, if applicable.
7Disconnect the rear anti-roll bar from the
trailing arm (see Section 12).
8On 1983 and later models, remove one of
the rear axle carrier bolts (see illustration).
9Disconnect the shock absorber lower
mounting bolt (see Section 11).
10Remove the two trailing arm pivot bolts
and nuts, and remove the trailing arm from the
vehicle.
11Inspect the pivot bolt bushes. If they’re
cracked, dried out or torn, take the trailing
arm to an engineering works, and have new
ones fitted. The bush inner sleeve is longer on
one side. Make sure the bushes are fitted with
10•10 Suspension and steering systems
14.3 Disconnect the brake hose (left
arrow) from the fitting on the metal brake
line (right arrow) at this bracket13.6 Nut (arrowed) for the outer pivot bolt
13.3 Disconnect the rear brake hose
(middle arrow) from the metal brake line
fitting (right arrow) at this bracket on the
trailing arm, then plug the line and hose
immediately; the other arrow points to the
nut for the inner pivot bolt
12.3b Bolt (arrowed) connecting rear anti-
roll bar link to trailing arm (5-Series)12.3a A nut and bolt (arrowed) connect
each rear anti-roll bar link to the rear
trailing arms (3-Series)12.2 Rear anti-roll bar bracket bolt
(arrowed) (3-Series)
Page 153 of 228
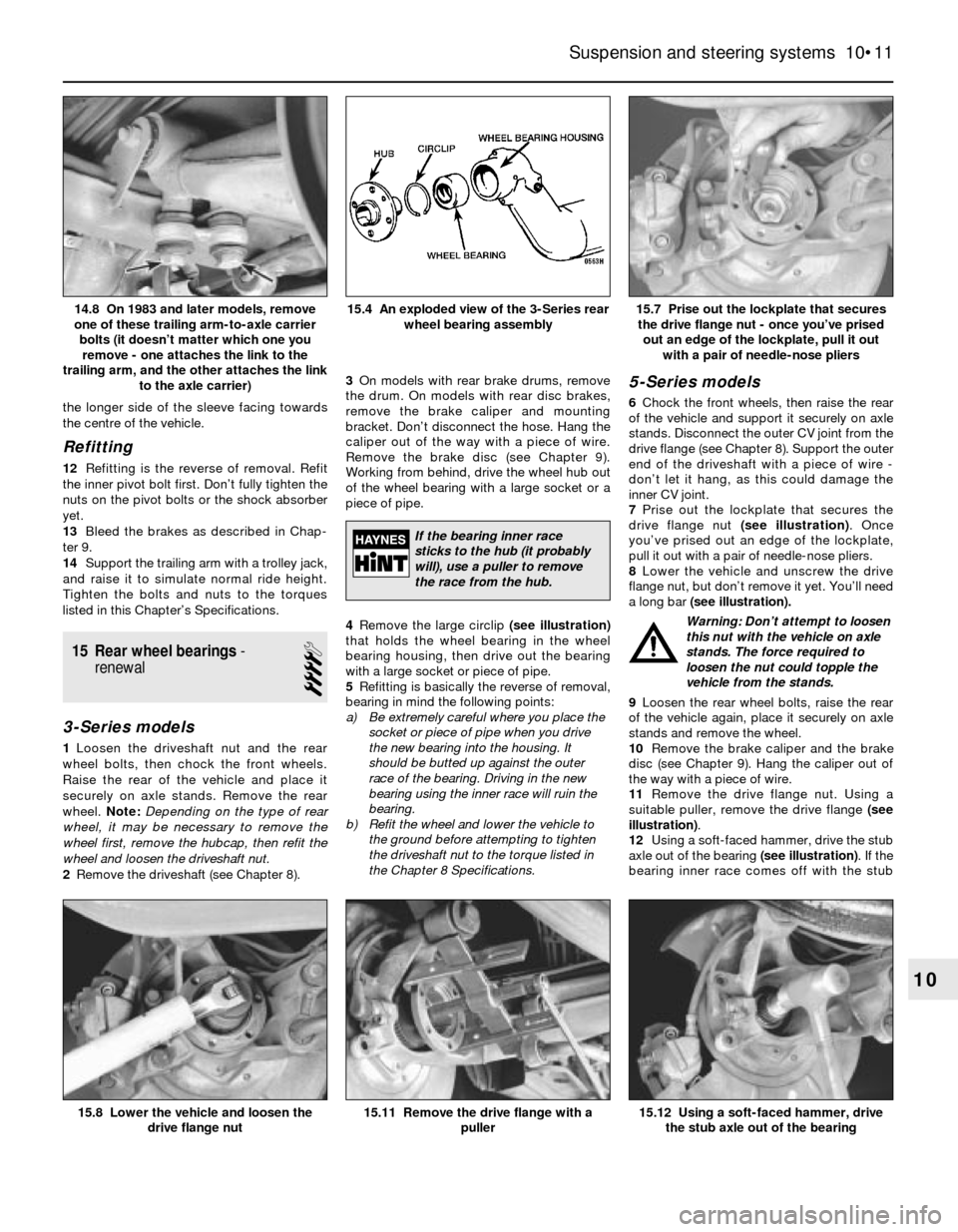
the longer side of the sleeve facing towards
the centre of the vehicle.
Refitting
12Refitting is the reverse of removal. Refit
the inner pivot bolt first. Don’t fully tighten the
nuts on the pivot bolts or the shock absorber
yet.
13Bleed the brakes as described in Chap-
ter 9.
14Support the trailing arm with a trolley jack,
and raise it to simulate normal ride height.
Tighten the bolts and nuts to the torques
listed in this Chapter’s Specifications.
15 Rear wheel bearings-
renewal
4
3-Series models
1Loosen the driveshaft nut and the rear
wheel bolts, then chock the front wheels.
Raise the rear of the vehicle and place it
securely on axle stands. Remove the rear
wheel. Note: Depending on the type of rear
wheel, it may be necessary to remove the
wheel first, remove the hubcap, then refit the
wheel and loosen the driveshaft nut.
2Remove the driveshaft (see Chapter 8).3On models with rear brake drums, remove
the drum. On models with rear disc brakes,
remove the brake caliper and mounting
bracket. Don’t disconnect the hose. Hang the
caliper out of the way with a piece of wire.
Remove the brake disc (see Chapter 9).
Working from behind, drive the wheel hub out
of the wheel bearing with a large socket or a
piece of pipe.
4Remove the large circlip (see illustration)
that holds the wheel bearing in the wheel
bearing housing, then drive out the bearing
with a large socket or piece of pipe.
5Refitting is basically the reverse of removal,
bearing in mind the following points:
a) Be extremely careful where you place the
socket or piece of pipe when you drive
the new bearing into the housing. It
should be butted up against the outer
race of the bearing. Driving in the new
bearing using the inner race will ruin the
bearing.
b) Refit the wheel and lower the vehicle to
the ground before attempting to tighten
the driveshaft nut to the torque listed in
the Chapter 8 Specifications.
5-Series models
6Chock the front wheels, then raise the rear
of the vehicle and support it securely on axle
stands. Disconnect the outer CV joint from the
drive flange (see Chapter 8). Support the outer
end of the driveshaft with a piece of wire -
don’t let it hang, as this could damage the
inner CV joint.
7Prise out the lockplate that secures the
drive flange nut (see illustration). Once
you’ve prised out an edge of the lockplate,
pull it out with a pair of needle-nose pliers.
8Lower the vehicle and unscrew the drive
flange nut, but don’t remove it yet. You’ll need
a long bar (see illustration).
Warning: Don’t attempt to loosen
this nut with the vehicle on axle
stands. The force required to
loosen the nut could topple the
vehicle from the stands.
9Loosen the rear wheel bolts, raise the rear
of the vehicle again, place it securely on axle
stands and remove the wheel.
10Remove the brake caliper and the brake
disc (see Chapter 9). Hang the caliper out of
the way with a piece of wire.
11Remove the drive flange nut. Using a
suitable puller, remove the drive flange (see
illustration).
12Using a soft-faced hammer, drive the stub
axle out of the bearing (see illustration). If the
bearing inner race comes off with the stub
Suspension and steering systems 10•11
15.7 Prise out the lockplate that secures
the drive flange nut - once you’ve prised
out an edge of the lockplate, pull it out
with a pair of needle-nose pliers15.4 An exploded view of the 3-Series rear
wheel bearing assembly14.8 On 1983 and later models, remove
one of these trailing arm-to-axle carrier
bolts (it doesn’t matter which one you
remove - one attaches the link to the
trailing arm, and the other attaches the link
to the axle carrier)
15.12 Using a soft-faced hammer, drive
the stub axle out of the bearing15.11 Remove the drive flange with a
puller15.8 Lower the vehicle and loosen the
drive flange nut
10
If the bearing inner race
sticks to the hub (it probably
will), use a puller to remove
the race from the hub.
Page 154 of 228
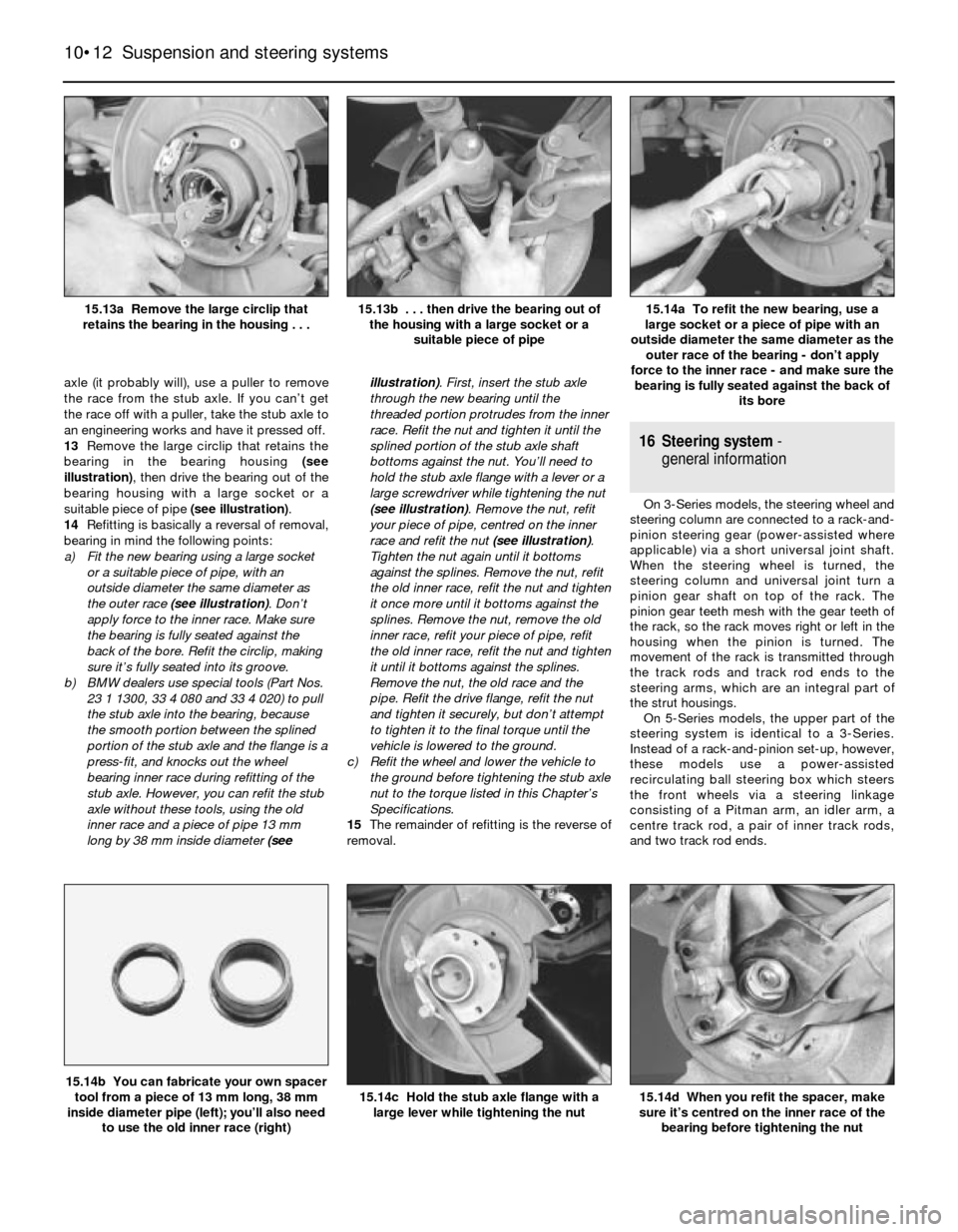
axle (it probably will), use a puller to remove
the race from the stub axle. If you can’t get
the race off with a puller, take the stub axle to
an engineering works and have it pressed off.
13Remove the large circlip that retains the
bearing in the bearing housing (see
illustration), then drive the bearing out of the
bearing housing with a large socket or a
suitable piece of pipe (see illustration).
14Refitting is basically a reversal of removal,
bearing in mind the following points:
a) Fit the new bearing using a large socket
or a suitable piece of pipe, with an
outside diameter the same diameter as
the outer race (see illustration). Don’t
apply force to the inner race. Make sure
the bearing is fully seated against the
back of the bore. Refit the circlip, making
sure it’s fully seated into its groove.
b) BMW dealers use special tools (Part Nos.
23 1 1300, 33 4 080 and 33 4 020) to pull
the stub axle into the bearing, because
the smooth portion between the splined
portion of the stub axle and the flange is a
press-fit, and knocks out the wheel
bearing inner race during refitting of the
stub axle. However, you can refit the stub
axle without these tools, using the old
inner race and a piece of pipe 13 mm
long by 38 mm inside diameter (seeillustration). First, insert the stub axle
through the new bearing until the
threaded portion protrudes from the inner
race. Refit the nut and tighten it until the
splined portion of the stub axle shaft
bottoms against the nut. You’ll need to
hold the stub axle flange with a lever or a
large screwdriver while tightening the nut
(see illustration). Remove the nut, refit
your piece of pipe, centred on the inner
race and refit the nut (see illustration).
Tighten the nut again until it bottoms
against the splines. Remove the nut, refit
the old inner race, refit the nut and tighten
it once more until it bottoms against the
splines. Remove the nut, remove the old
inner race, refit your piece of pipe, refit
the old inner race, refit the nut and tighten
it until it bottoms against the splines.
Remove the nut, the old race and the
pipe. Refit the drive flange, refit the nut
and tighten it securely, but don’t attempt
to tighten it to the final torque until the
vehicle is lowered to the ground.
c) Refit the wheel and lower the vehicle to
the ground before tightening the stub axle
nut to the torque listed in this Chapter’s
Specifications.
15The remainder of refitting is the reverse of
removal.
16 Steering system-
general information
On 3-Series models, the steering wheel and
steering column are connected to a rack-and-
pinion steering gear (power-assisted where
applicable) via a short universal joint shaft.
When the steering wheel is turned, the
steering column and universal joint turn a
pinion gear shaft on top of the rack. The
pinion gear teeth mesh with the gear teeth of
the rack, so the rack moves right or left in the
housing when the pinion is turned. The
movement of the rack is transmitted through
the track rods and track rod ends to the
steering arms, which are an integral part of
the strut housings.
On 5-Series models, the upper part of the
steering system is identical to a 3-Series.
Instead of a rack-and-pinion set-up, however,
these models use a power-assisted
recirculating ball steering box which steers
the front wheels via a steering linkage
consisting of a Pitman arm, an idler arm, a
centre track rod, a pair of inner track rods,
and two track rod ends.
10•12 Suspension and steering systems
15.14d When you refit the spacer, make
sure it’s centred on the inner race of the
bearing before tightening the nut15.14c Hold the stub axle flange with a
large lever while tightening the nut15.14b You can fabricate your own spacer
tool from a piece of 13 mm long, 38 mm
inside diameter pipe (left); you’ll also need
to use the old inner race (right)
15.14a To refit the new bearing, use a
large socket or a piece of pipe with an
outside diameter the same diameter as the
outer race of the bearing - don’t apply
force to the inner race - and make sure the
bearing is fully seated against the back of
its bore15.13b . . . then drive the bearing out of
the housing with a large socket or a
suitable piece of pipe15.13a Remove the large circlip that
retains the bearing in the housing . . .
Page 155 of 228
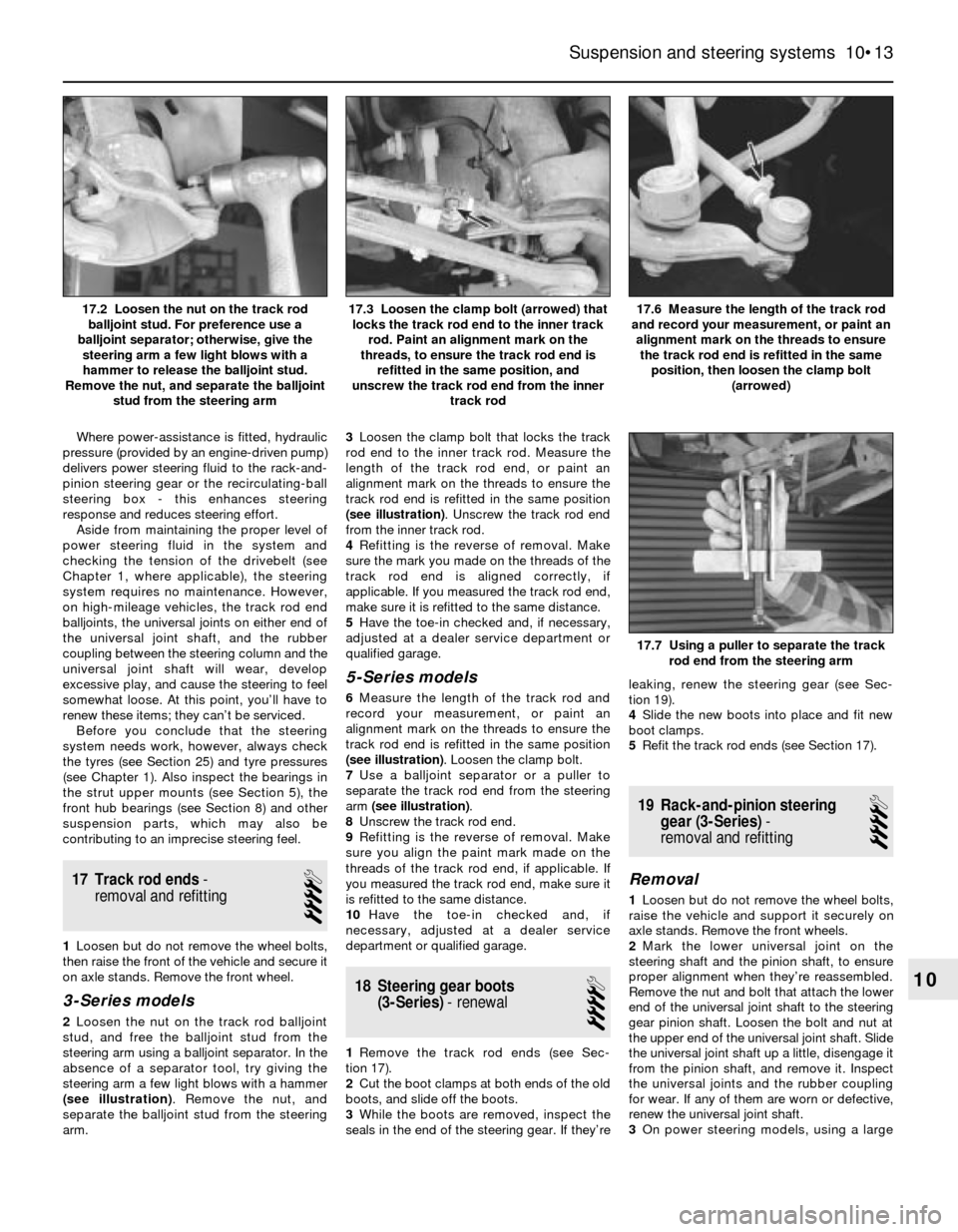
Where power-assistance is fitted, hydraulic
pressure (provided by an engine-driven pump)
delivers power steering fluid to the rack-and-
pinion steering gear or the recirculating-ball
steering box - this enhances steering
response and reduces steering effort.
Aside from maintaining the proper level of
power steering fluid in the system and
checking the tension of the drivebelt (see
Chapter 1, where applicable), the steering
system requires no maintenance. However,
on high-mileage vehicles, the track rod end
balljoints, the universal joints on either end of
the universal joint shaft, and the rubber
coupling between the steering column and the
universal joint shaft will wear, develop
excessive play, and cause the steering to feel
somewhat loose. At this point, you’ll have to
renew these items; they can’t be serviced.
Before you conclude that the steering
system needs work, however, always check
the tyres (see Section 25) and tyre pressures
(see Chapter 1). Also inspect the bearings in
the strut upper mounts (see Section 5), the
front hub bearings (see Section 8) and other
suspension parts, which may also be
contributing to an imprecise steering feel.
17 Track rod ends-
removal and refitting
4
1Loosen but do not remove the wheel bolts,
then raise the front of the vehicle and secure it
on axle stands. Remove the front wheel.
3-Series models
2Loosen the nut on the track rod balljoint
stud, and free the balljoint stud from the
steering arm using a balljoint separator. In the
absence of a separator tool, try giving the
steering arm a few light blows with a hammer
(see illustration). Remove the nut, and
separate the balljoint stud from the steering
arm.3Loosen the clamp bolt that locks the track
rod end to the inner track rod. Measure the
length of the track rod end, or paint an
alignment mark on the threads to ensure the
track rod end is refitted in the same position
(see illustration). Unscrew the track rod end
from the inner track rod.
4Refitting is the reverse of removal. Make
sure the mark you made on the threads of the
track rod end is aligned correctly, if
applicable. If you measured the track rod end,
make sure it is refitted to the same distance.
5Have the toe-in checked and, if necessary,
adjusted at a dealer service department or
qualified garage.
5-Series models
6Measure the length of the track rod and
record your measurement, or paint an
alignment mark on the threads to ensure the
track rod end is refitted in the same position
(see illustration). Loosen the clamp bolt.
7Use a balljoint separator or a puller to
separate the track rod end from the steering
arm (see illustration).
8Unscrew the track rod end.
9Refitting is the reverse of removal. Make
sure you align the paint mark made on the
threads of the track rod end, if applicable. If
you measured the track rod end, make sure it
is refitted to the same distance.
10Have the toe-in checked and, if
necessary, adjusted at a dealer service
department or qualified garage.
18 Steering gear boots
(3-Series)- renewal
4
1Remove the track rod ends (see Sec-
tion 17).
2Cut the boot clamps at both ends of the old
boots, and slide off the boots.
3While the boots are removed, inspect the
seals in the end of the steering gear. If they’releaking, renew the steering gear (see Sec-
tion 19).
4Slide the new boots into place and fit new
boot clamps.
5Refit the track rod ends (see Section 17).
19 Rack-and-pinion steering
gear (3-Series)-
removal and refitting
4
Removal
1Loosen but do not remove the wheel bolts,
raise the vehicle and support it securely on
axle stands. Remove the front wheels.
2Mark the lower universal joint on the
steering shaft and the pinion shaft, to ensure
proper alignment when they’re reassembled.
Remove the nut and bolt that attach the lower
end of the universal joint shaft to the steering
gear pinion shaft. Loosen the bolt and nut at
the upper end of the universal joint shaft. Slide
the universal joint shaft up a little, disengage it
from the pinion shaft, and remove it. Inspect
the universal joints and the rubber coupling
for wear. If any of them are worn or defective,
renew the universal joint shaft.
3On power steering models, using a large
Suspension and steering systems 10•13
17.6 Measure the length of the track rod
and record your measurement, or paint an
alignment mark on the threads to ensure
the track rod end is refitted in the same
position, then loosen the clamp bolt
(arrowed)17.3 Loosen the clamp bolt (arrowed) that
locks the track rod end to the inner track
rod. Paint an alignment mark on the
threads, to ensure the track rod end is
refitted in the same position, and
unscrew the track rod end from the inner
track rod17.2 Loosen the nut on the track rod
balljoint stud. For preference use a
balljoint separator; otherwise, give the
steering arm a few light blows with a
hammer to release the balljoint stud.
Remove the nut, and separate the balljoint
stud from the steering arm
17.7 Using a puller to separate the track
rod end from the steering arm
10
Page 156 of 228

syringe or hand pump, empty the power
steering fluid reservoir.
4On power steering models, remove the
banjo bolts and disconnect the power
steering pressure and return lines from the
steering gear. Place a container under the
lines to catch spilled fluid. Plug the lines to
prevent excessive fluid loss and
contamination. Discard the sealing washers
(new ones should be used when
reassembling).
5Disconnect the track rod ends from the
steering arms (see Section 17).
6Remove the nuts and bolts from the
steering gear mounting brackets (see
illustration). Discard the old nuts.
7Withdraw the assembly from beneath the
vehicle. Take care not to damage the steering
gear boots.
Refitting
8Refitting is the reverse of removal. Make
sure the marks you made on the lower
universal joint and the pinion shaft are aligned
before you tighten the clamping bolts for the
upper and lower universal joints. Use new
self-locking nuts on the steering rackmounting bolts, and new sealing washers on
the hydraulic line fittings. Tighten the
mounting bolts, the track rod end nuts and the
universal joint shaft clamping bolts to the
torque values listed in this Chapter’s Specifi-
cations.
9Lower the vehicle to the ground.
10On power steering models, fill the
reservoir with the recommended fluid (see
Chapter 1) and bleed the power steering
system (see Section 23).
11It’s a good idea to have the front wheel
alignment checked by a dealer service
department or qualified garage.
20 Steering linkage (5-Series)-
inspection, removal and
refitting
4
Inspection
1Raise the vehicle and place it securely on
axle stands.
2Firmly grasp each front tyre at the top and
bottom, then at the front and rear, and check
for play in the steering linkage by rocking the
tyre back and forth. There should be little or
no play in any of the linkage balljoints. Inspect
the Pitman arm, the idler arm, the centre track
rod, the inner track rods, the track rod ends
and the steering arms for any obvious
damage. Try forcing the linkage parts in
opposite directions from one another. There
should be no play between any of them. If any
of the parts are bent or damaged in any way,
or if any of the balljoints are worn, renew the
parts concerned.
Removal
3Before dismantling the steering linkage,
obtain a suitable balljoint separator. A two-jaw
puller or a wedge-type tool will work (although
the wedge-type tends to tear the balljoint
boots). Sometimes, you can also jar a balljoint
taper pin free from its eye by striking opposite
sides of the eye simultaneously with two large
hammers, but the space available to do this is
limited, and the balljoint stud sometimessticks to the eye because of rust and dirt.
There is also a risk of damaging the
component being struck.
4To remove the outer track rods, disconnect
the track rod ends from the steering arms (see
Section 17). Remove the nut that attaches the
balljoint on the inner end of each outer track
rod to the centre track rod (see illustration).
Using a balljoint separator, disconnect the
outer track rods from the centre track rod. If
you’re renewing the balljoint at either end of
the outer track rods, paint or scribe alignment
marks on the threads to mark their respective
positions as a guide to adjustment during
reassembly (see illustration 17.3).
5To remove the centre track rod, remove the
nuts that attach the centre track rod balljoints
to the Pitman arm and the idler arm, and use a
balljoint separator to disconnect the balljoints
from the two arms.
6To remove the Pitman arm, you’ll have to
remove the steering box first (see Section 21).
Look for match marks between the sector
shaft and arm. If there aren’t any, scribe a
mark across the bottom face of both parts.
Remove the Pitman arm pinch-bolt and nut,
then remove the arm with a puller.
7To unbolt the idler arm, first remove the
small cover bolted to the top of the subframe
crossmember. Put a spanner on the bolt, and
remove the nut recessed into the underside of
the subframe crossmember (see illustration).
Check the idler arm rubber bush for wear. If
it’s damaged or worn, renew it.
8Check each balljoint for excessive play or
stiffness, and for split or deteriorated rubber
dust boots. Renew all worn or damaged
balljoints. The inner and outer track rod ends
on the outer track rods can be renewed
individually; if either balljoint on the centre
track rod is damaged or worn, you must
renew the centre track rod.
Refitting
9Refitting is the reverse of the removal
procedure, but observe the following points:
a) Realign the match marks on the Pitman
arm and the steering box sector shaft
when reassembling them.
b) If you’re fitting new inner or outer track
rod ends on the outer track rods, position
them so that the match marks made
during dismantling are aligned, and make
sure they are equally spaced on each
side.
c) Position the track rod end balljoint studs
on the outer track rods at an angle of 90°
to each other.
d) Make sure the left and right outer track
rods are equal in length when they are
fitted.
e) Tighten all retaining bolts to the torque
values listed in this Chapter’s Specifi-
cations.
f) When reassembly of the linkage is
complete, have the front wheel alignment
checked, and if necessary, adjusted.
10•14 Suspension and steering systems
20.7 To unbolt the idler arm from the
subframe crossmember, remove this nut
(arrowed)
20.4 To remove an outer track rod,
remove this nut (arrowed) from the end of
the centre track rod, and use a balljoint
separator to separate the balljoint stud
from the centre track rod (if you’re
renewing the inner track rod end, mark the
threads with paint before loosening the
clamp bolt and nut)
19.6 Rack-and-pinion steering gear
mounting bolts (arrowed) - 3-Series
models - (self-locking nuts not visible in
this photo)
Page 157 of 228
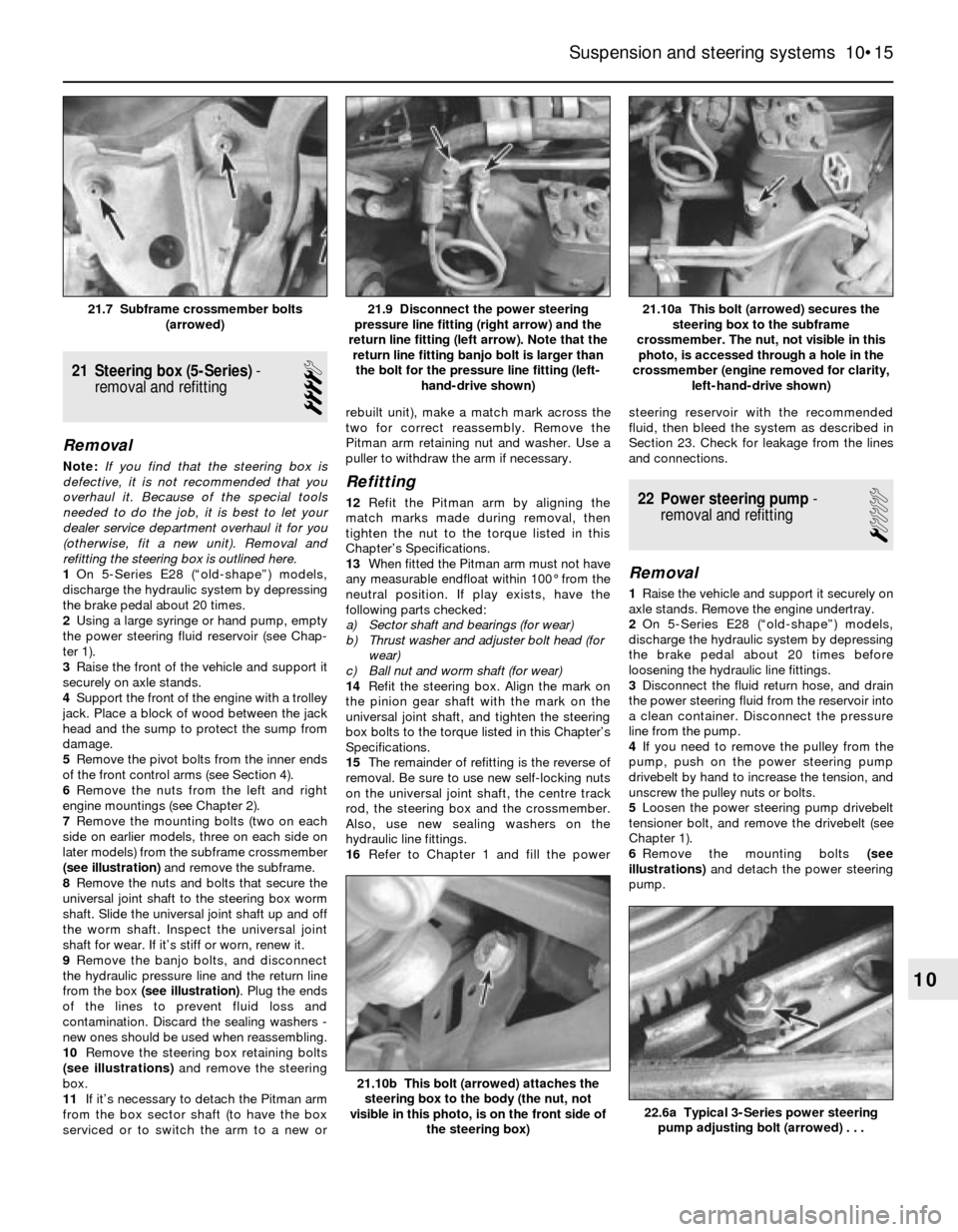
21 Steering box (5-Series)-
removal and refitting
4
Removal
Note:If you find that the steering box is
defective, it is not recommended that you
overhaul it. Because of the special tools
needed to do the job, it is best to let your
dealer service department overhaul it for you
(otherwise, fit a new unit). Removal and
refitting the steering box is outlined here.
1On 5-Series E28 (“old-shape”) models,
discharge the hydraulic system by depressing
the brake pedal about 20 times.
2Using a large syringe or hand pump, empty
the power steering fluid reservoir (see Chap-
ter 1).
3Raise the front of the vehicle and support it
securely on axle stands.
4Support the front of the engine with a trolley
jack. Place a block of wood between the jack
head and the sump to protect the sump from
damage.
5Remove the pivot bolts from the inner ends
of the front control arms (see Section 4).
6Remove the nuts from the left and right
engine mountings (see Chapter 2).
7Remove the mounting bolts (two on each
side on earlier models, three on each side on
later models) from the subframe crossmember
(see illustration)and remove the subframe.
8Remove the nuts and bolts that secure the
universal joint shaft to the steering box worm
shaft. Slide the universal joint shaft up and off
the worm shaft. Inspect the universal joint
shaft for wear. If it’s stiff or worn, renew it.
9Remove the banjo bolts, and disconnect
the hydraulic pressure line and the return line
from the box (see illustration). Plug the ends
of the lines to prevent fluid loss and
contamination. Discard the sealing washers -
new ones should be used when reassembling.
10Remove the steering box retaining bolts
(see illustrations)and remove the steering
box.
11If it’s necessary to detach the Pitman arm
from the box sector shaft (to have the box
serviced or to switch the arm to a new orrebuilt unit), make a match mark across the
two for correct reassembly. Remove the
Pitman arm retaining nut and washer. Use a
puller to withdraw the arm if necessary.
Refitting
12Refit the Pitman arm by aligning the
match marks made during removal, then
tighten the nut to the torque listed in this
Chapter’s Specifications.
13When fitted the Pitman arm must not have
any measurable endfloat within 100° from the
neutral position. If play exists, have the
following parts checked:
a) Sector shaft and bearings (for wear)
b) Thrust washer and adjuster bolt head (for
wear)
c) Ball nut and worm shaft (for wear)
14Refit the steering box. Align the mark on
the pinion gear shaft with the mark on the
universal joint shaft, and tighten the steering
box bolts to the torque listed in this Chapter’s
Specifications.
15The remainder of refitting is the reverse of
removal. Be sure to use new self-locking nuts
on the universal joint shaft, the centre track
rod, the steering box and the crossmember.
Also, use new sealing washers on the
hydraulic line fittings.
16Refer to Chapter 1 and fill the powersteering reservoir with the recommended
fluid, then bleed the system as described in
Section 23. Check for leakage from the lines
and connections.22 Power steering pump-
removal and refitting
1
Removal
1Raise the vehicle and support it securely on
axle stands. Remove the engine undertray.
2On 5-Series E28 (“old-shape”) models,
discharge the hydraulic system by depressing
the brake pedal about 20 times before
loosening the hydraulic line fittings.
3Disconnect the fluid return hose, and drain
the power steering fluid from the reservoir into
a clean container. Disconnect the pressure
line from the pump.
4If you need to remove the pulley from the
pump, push on the power steering pump
drivebelt by hand to increase the tension, and
unscrew the pulley nuts or bolts.
5Loosen the power steering pump drivebelt
tensioner bolt, and remove the drivebelt (see
Chapter 1).
6Remove the mounting bolts (see
illustrations)and detach the power steering
pump.
Suspension and steering systems 10•15
21.10a This bolt (arrowed) secures the
steering box to the subframe
crossmember. The nut, not visible in this
photo, is accessed through a hole in the
crossmember (engine removed for clarity,
left-hand-drive shown)21.9 Disconnect the power steering
pressure line fitting (right arrow) and the
return line fitting (left arrow). Note that the
return line fitting banjo bolt is larger than
the bolt for the pressure line fitting (left-
hand-drive shown)21.7 Subframe crossmember bolts
(arrowed)
22.6a Typical 3-Series power steering
pump adjusting bolt (arrowed) . . .
21.10b This bolt (arrowed) attaches the
steering box to the body (the nut, not
visible in this photo, is on the front side of
the steering box)
10
Page 158 of 228
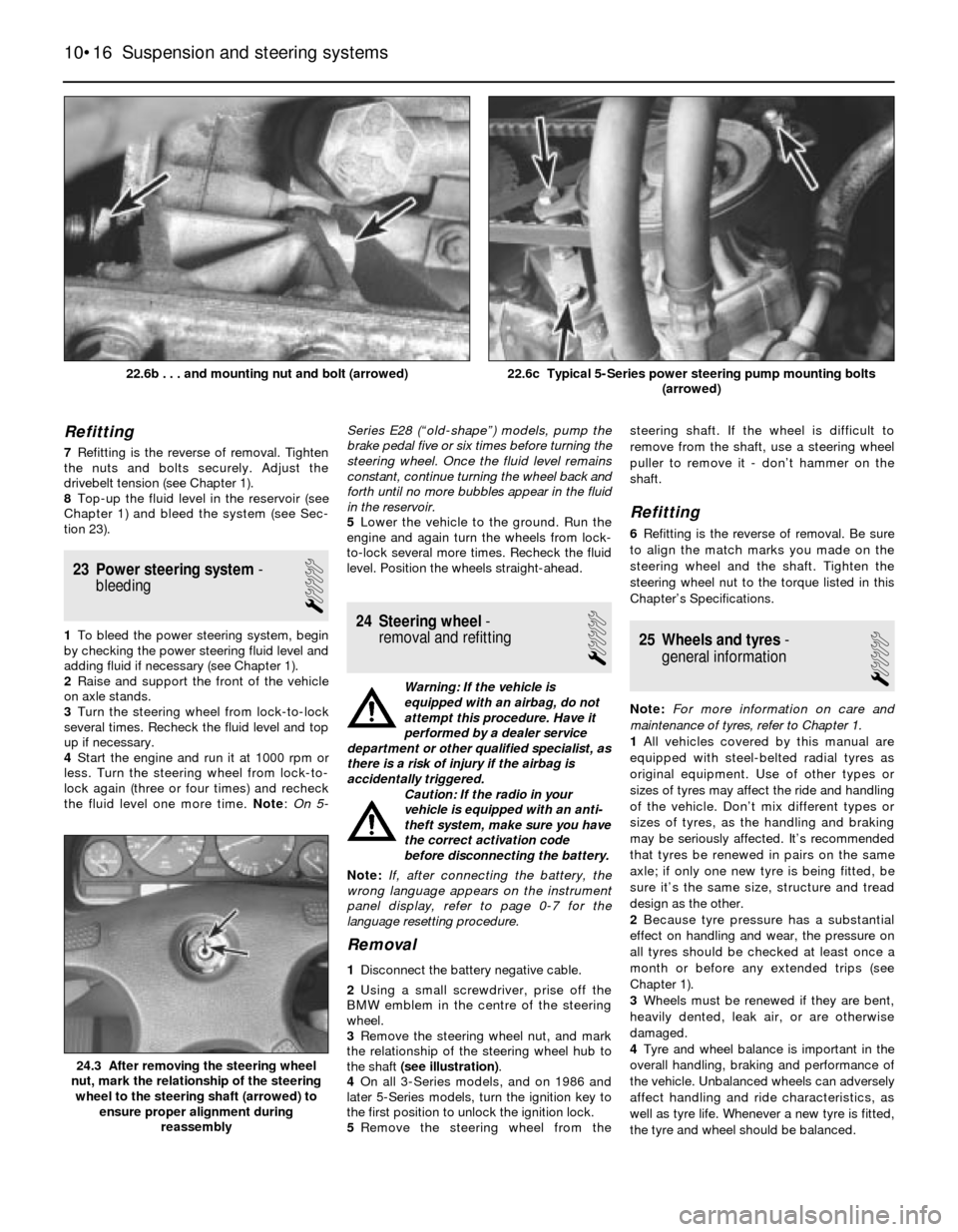
Refitting
7Refitting is the reverse of removal. Tighten
the nuts and bolts securely. Adjust the
drivebelt tension (see Chapter 1).
8Top-up the fluid level in the reservoir (see
Chapter 1) and bleed the system (see Sec-
tion 23).
23 Power steering system-
bleeding
1
1To bleed the power steering system, begin
by checking the power steering fluid level and
adding fluid if necessary (see Chapter 1).
2Raise and support the front of the vehicle
on axle stands.
3Turn the steering wheel from lock-to-lock
several times. Recheck the fluid level and top
up if necessary.
4Start the engine and run it at 1000 rpm or
less. Turn the steering wheel from lock-to-
lock again (three or four times) and recheck
the fluid level one more time. Note:On 5-Series E28 (“old-shape”) models, pump the
brake pedal five or six times before turning the
steering wheel. Once the fluid level remains
constant, continue turning the wheel back and
forth until no more bubbles appear in the fluid
in the reservoir.
5Lower the vehicle to the ground. Run the
engine and again turn the wheels from lock-
to-lock several more times. Recheck the fluid
level. Position the wheels straight-ahead.24 Steering wheel-
removal and refitting
1
Warning: If the vehicle is
equipped with an airbag, do not
attempt this procedure. Have it
performed by a dealer service
department or other qualified specialist, as
there is a risk of injury if the airbag is
accidentally triggered.
Caution: If the radio in your
vehicle is equipped with an anti-
theft system, make sure you have
the correct activation code
before disconnecting the battery.
Note: If, after connecting the battery, the
wrong language appears on the instrument
panel display, refer to page 0-7 for the
language resetting procedure.
Removal
1Disconnect the battery negative cable.
2Using a small screwdriver, prise off the
BMW emblem in the centre of the steering
wheel.
3Remove the steering wheel nut, and mark
the relationship of the steering wheel hub to
the shaft (see illustration).
4On all 3-Series models, and on 1986 and
later 5-Series models, turn the ignition key to
the first position to unlock the ignition lock.
5Remove the steering wheel from thesteering shaft. If the wheel is difficult to
remove from the shaft, use a steering wheel
puller to remove it - don’t hammer on the
shaft.
Refitting
6Refitting is the reverse of removal. Be sure
to align the match marks you made on the
steering wheel and the shaft. Tighten the
steering wheel nut to the torque listed in this
Chapter’s Specifications.
25 Wheels and tyres-
general information
1
Note:For more information on care and
maintenance of tyres, refer to Chapter 1.
1All vehicles covered by this manual are
equipped with steel-belted radial tyres as
original equipment. Use of other types or
sizes of tyres may affect the ride and handling
of the vehicle. Don’t mix different types or
sizes of tyres, as the handling and braking
may be seriously affected. It’s recommended
that tyres be renewed in pairs on the same
axle; if only one new tyre is being fitted, be
sure it’s the same size, structure and tread
design as the other.
2Because tyre pressure has a substantial
effect on handling and wear, the pressure on
all tyres should be checked at least once a
month or before any extended trips (see
Chapter 1).
3Wheels must be renewed if they are bent,
heavily dented, leak air, or are otherwise
damaged.
4Tyre and wheel balance is important in the
overall handling, braking and performance of
the vehicle. Unbalanced wheels can adversely
affect handling and ride characteristics, as
well as tyre life. Whenever a new tyre is fitted,
the tyre and wheel should be balanced.
10•16 Suspension and steering systems
24.3 After removing the steering wheel
nut, mark the relationship of the steering
wheel to the steering shaft (arrowed) to
ensure proper alignment during
reassembly
22.6c Typical 5-Series power steering pump mounting bolts
(arrowed)22.6b . . . and mounting nut and bolt (arrowed)
Page 159 of 228
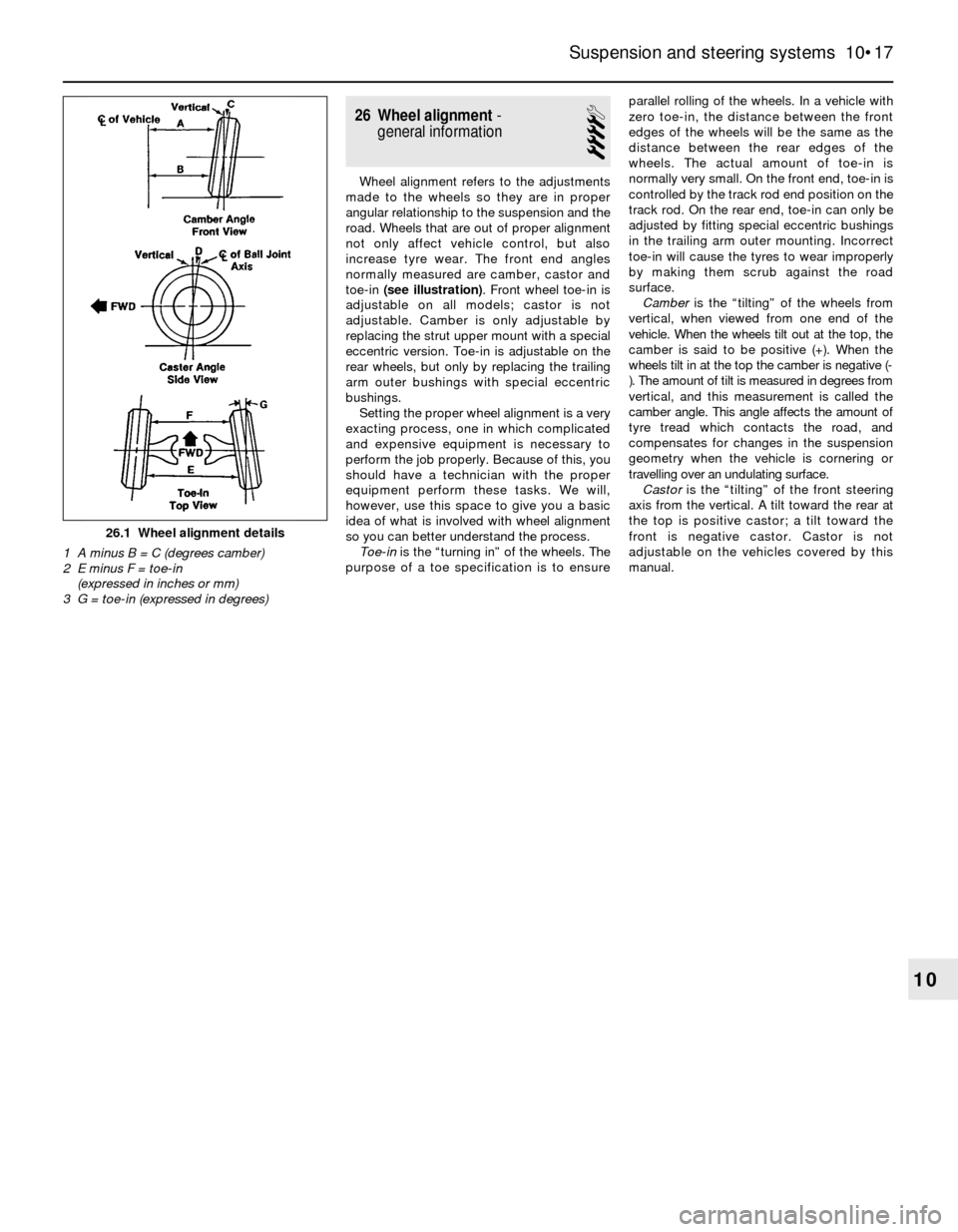
26 Wheel alignment-
general information
4
Wheel alignment refers to the adjustments
made to the wheels so they are in proper
angular relationship to the suspension and the
road. Wheels that are out of proper alignment
not only affect vehicle control, but also
increase tyre wear. The front end angles
normally measured are camber, castor and
toe-in (see illustration). Front wheel toe-in is
adjustable on all models; castor is not
adjustable. Camber is only adjustable by
replacing the strut upper mount with a special
eccentric version. Toe-in is adjustable on the
rear wheels, but only by replacing the trailing
arm outer bushings with special eccentric
bushings.
Setting the proper wheel alignment is a very
exacting process, one in which complicated
and expensive equipment is necessary to
perform the job properly. Because of this, you
should have a technician with the proper
equipment perform these tasks. We will,
however, use this space to give you a basic
idea of what is involved with wheel alignment
so you can better understand the process.
Toe-inis the “turning in” of the wheels. The
purpose of a toe specification is to ensureparallel rolling of the wheels. In a vehicle with
zero toe-in, the distance between the front
edges of the wheels will be the same as the
distance between the rear edges of the
wheels. The actual amount of toe-in is
normally very small. On the front end, toe-in is
controlled by the track rod end position on the
track rod. On the rear end, toe-in can only be
adjusted by fitting special eccentric bushings
in the trailing arm outer mounting. Incorrect
toe-in will cause the tyres to wear improperly
by making them scrub against the road
surface.
Camberis the “tilting” of the wheels from
vertical, when viewed from one end of the
vehicle. When the wheels tilt out at the top, the
camber is said to be positive (+). When the
wheels tilt in at the top the camber is negative (-
). The amount of tilt is measured in degrees from
vertical, and this measurement is called the
camber angle. This angle affects the amount of
tyre tread which contacts the road, and
compensates for changes in the suspension
geometry when the vehicle is cornering or
travelling over an undulating surface.
Castoris the “tilting” of the front steering
axis from the vertical. A tilt toward the rear at
the top is positive castor; a tilt toward the
front is negative castor. Castor is not
adjustable on the vehicles covered by this
manual.
Suspension and steering systems 10•17
10
26.1 Wheel alignment details
1 A minus B = C (degrees camber)
2 E minus F = toe-in
(expressed in inches or mm)
3 G = toe-in (expressed in degrees)
Page 160 of 228
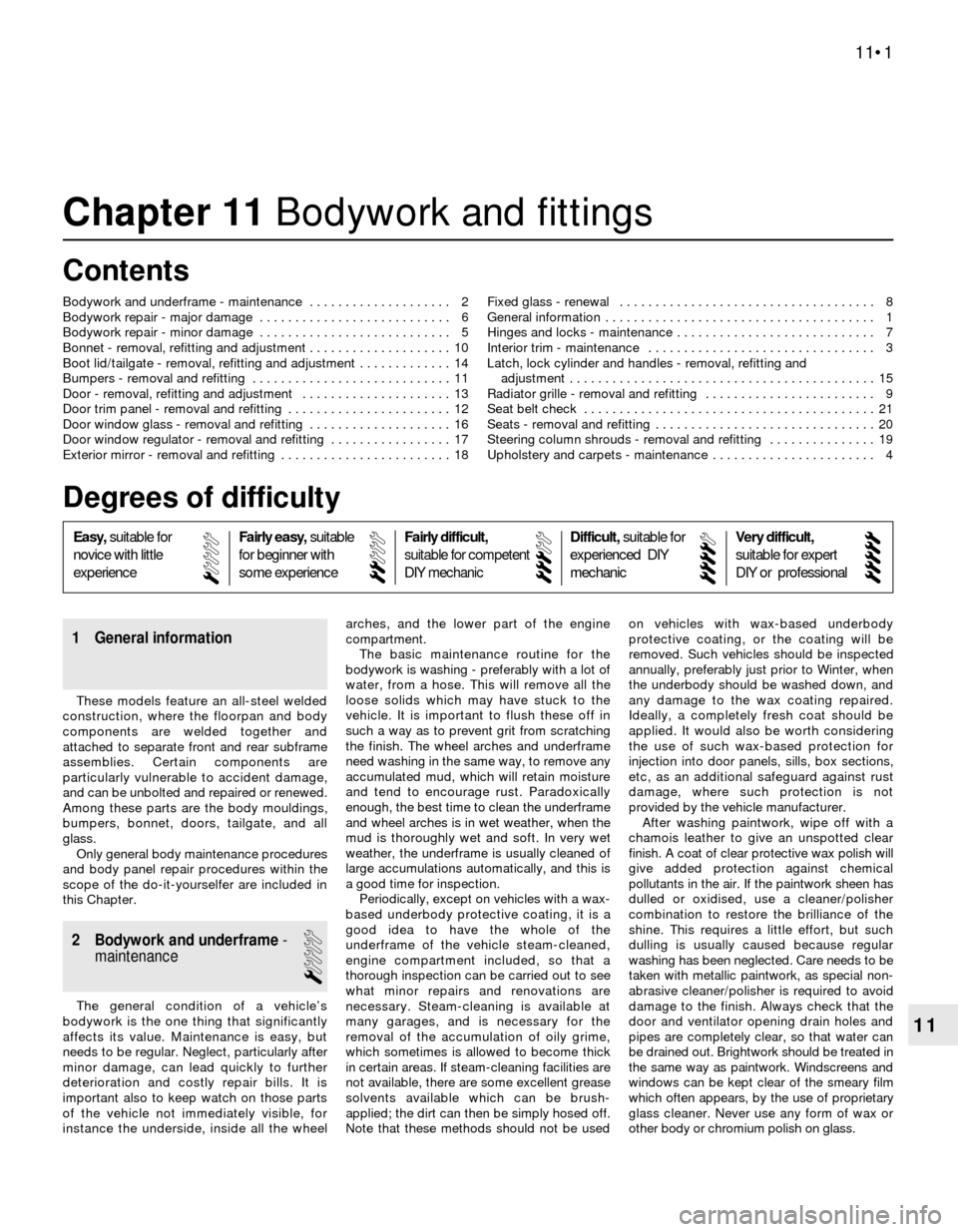
11
1 General information
These models feature an all-steel welded
construction, where the floorpan and body
components are welded together and
attached to separate front and rear subframe
assemblies. Certain components are
particularly vulnerable to accident damage,
and can be unbolted and repaired or renewed.
Among these parts are the body mouldings,
bumpers, bonnet, doors, tailgate, and all
glass.
Only general body maintenance procedures
and body panel repair procedures within the
scope of the do-it-yourselfer are included in
this Chapter.
2 Bodywork and underframe-
maintenance
1
The general condition of a vehicle’s
bodywork is the one thing that significantly
affects its value. Maintenance is easy, but
needs to be regular. Neglect, particularly after
minor damage, can lead quickly to further
deterioration and costly repair bills. It is
important also to keep watch on those parts
of the vehicle not immediately visible, for
instance the underside, inside all the wheelarches, and the lower part of the engine
compartment.
The basic maintenance routine for the
bodywork is washing - preferably with a lot of
water, from a hose. This will remove all the
loose solids which may have stuck to the
vehicle. It is important to flush these off in
such a way as to prevent grit from scratching
the finish. The wheel arches and underframe
need washing in the same way, to remove any
accumulated mud, which will retain moisture
and tend to encourage rust. Paradoxically
enough, the best time to clean the underframe
and wheel arches is in wet weather, when the
mud is thoroughly wet and soft. In very wet
weather, the underframe is usually cleaned of
large accumulations automatically, and this is
a good time for inspection.
Periodically, except on vehicles with a wax-
based underbody protective coating, it is a
good idea to have the whole of the
underframe of the vehicle steam-cleaned,
engine compartment included, so that a
thorough inspection can be carried out to see
what minor repairs and renovations are
necessary. Steam-cleaning is available at
many garages, and is necessary for the
removal of the accumulation of oily grime,
which sometimes is allowed to become thick
in certain areas. If steam-cleaning facilities are
not available, there are some excellent grease
solvents available which can be brush-
applied; the dirt can then be simply hosed off.
Note that these methods should not be usedon vehicles with wax-based underbody
protective coating, or the coating will be
removed. Such vehicles should be inspected
annually, preferably just prior to Winter, when
the underbody should be washed down, and
any damage to the wax coating repaired.
Ideally, a completely fresh coat should be
applied. It would also be worth considering
the use of such wax-based protection for
injection into door panels, sills, box sections,
etc, as an additional safeguard against rust
damage, where such protection is not
provided by the vehicle manufacturer.
After washing paintwork, wipe off with a
chamois leather to give an unspotted clear
finish. A coat of clear protective wax polish will
give added protection against chemical
pollutants in the air. If the paintwork sheen has
dulled or oxidised, use a cleaner/polisher
combination to restore the brilliance of the
shine. This requires a little effort, but such
dulling is usually caused because regular
washing has been neglected. Care needs to be
taken with metallic paintwork, as special non-
abrasive cleaner/polisher is required to avoid
damage to the finish. Always check that the
door and ventilator opening drain holes and
pipes are completely clear, so that water can
be drained out. Brightwork should be treated in
the same way as paintwork. Windscreens and
windows can be kept clear of the smeary film
which often appears, by the use of proprietary
glass cleaner. Never use any form of wax or
other body or chromium polish on glass.
Chapter 11 Bodywork and fittings
Bodywork and underframe - maintenance . . . . . . . . . . . . . . . . . . . . 2
Bodywork repair - major damage . . . . . . . . . . . . . . . . . . . . . . . . . . . 6
Bodywork repair - minor damage . . . . . . . . . . . . . . . . . . . . . . . . . . . 5
Bonnet - removal, refitting and adjustment . . . . . . . . . . . . . . . . . . . . 10
Boot lid/tailgate - removal, refitting and adjustment . . . . . . . . . . . . . 14
Bumpers - removal and refitting . . . . . . . . . . . . . . . . . . . . . . . . . . . . 11
Door - removal, refitting and adjustment . . . . . . . . . . . . . . . . . . . . . 13
Door trim panel - removal and refitting . . . . . . . . . . . . . . . . . . . . . . . 12
Door window glass - removal and refitting . . . . . . . . . . . . . . . . . . . . 16
Door window regulator - removal and refitting . . . . . . . . . . . . . . . . . 17
Exterior mirror - removal and refitting . . . . . . . . . . . . . . . . . . . . . . . . 18Fixed glass - renewal . . . . . . . . . . . . . . . . . . . . . . . . . . . . . . . . . . . . 8
General information . . . . . . . . . . . . . . . . . . . . . . . . . . . . . . . . . . . . . . 1
Hinges and locks - maintenance . . . . . . . . . . . . . . . . . . . . . . . . . . . . 7
Interior trim - maintenance . . . . . . . . . . . . . . . . . . . . . . . . . . . . . . . . 3
Latch, lock cylinder and handles - removal, refitting and
adjustment . . . . . . . . . . . . . . . . . . . . . . . . . . . . . . . . . . . . . . . . . . . 15
Radiator grille - removal and refitting . . . . . . . . . . . . . . . . . . . . . . . . 9
Seat belt check . . . . . . . . . . . . . . . . . . . . . . . . . . . . . . . . . . . . . . . . . 21
Seats - removal and refitting . . . . . . . . . . . . . . . . . . . . . . . . . . . . . . . 20
Steering column shrouds - removal and refitting . . . . . . . . . . . . . . . 19
Upholstery and carpets - maintenance . . . . . . . . . . . . . . . . . . . . . . . 4
11•1
Easy,suitable for
novice with little
experienceFairly easy,suitable
for beginner with
some experienceFairly difficult,
suitable for competent
DIY mechanic
Difficult,suitable for
experienced DIY
mechanicVery difficult,
suitable for expert
DIY or professional
Degrees of difficulty Contents