BMW M3 1992 E36 Workshop Manual
Manufacturer: BMW, Model Year: 1992, Model line: M3, Model: BMW M3 1992 E36Pages: 759
Page 131 of 759
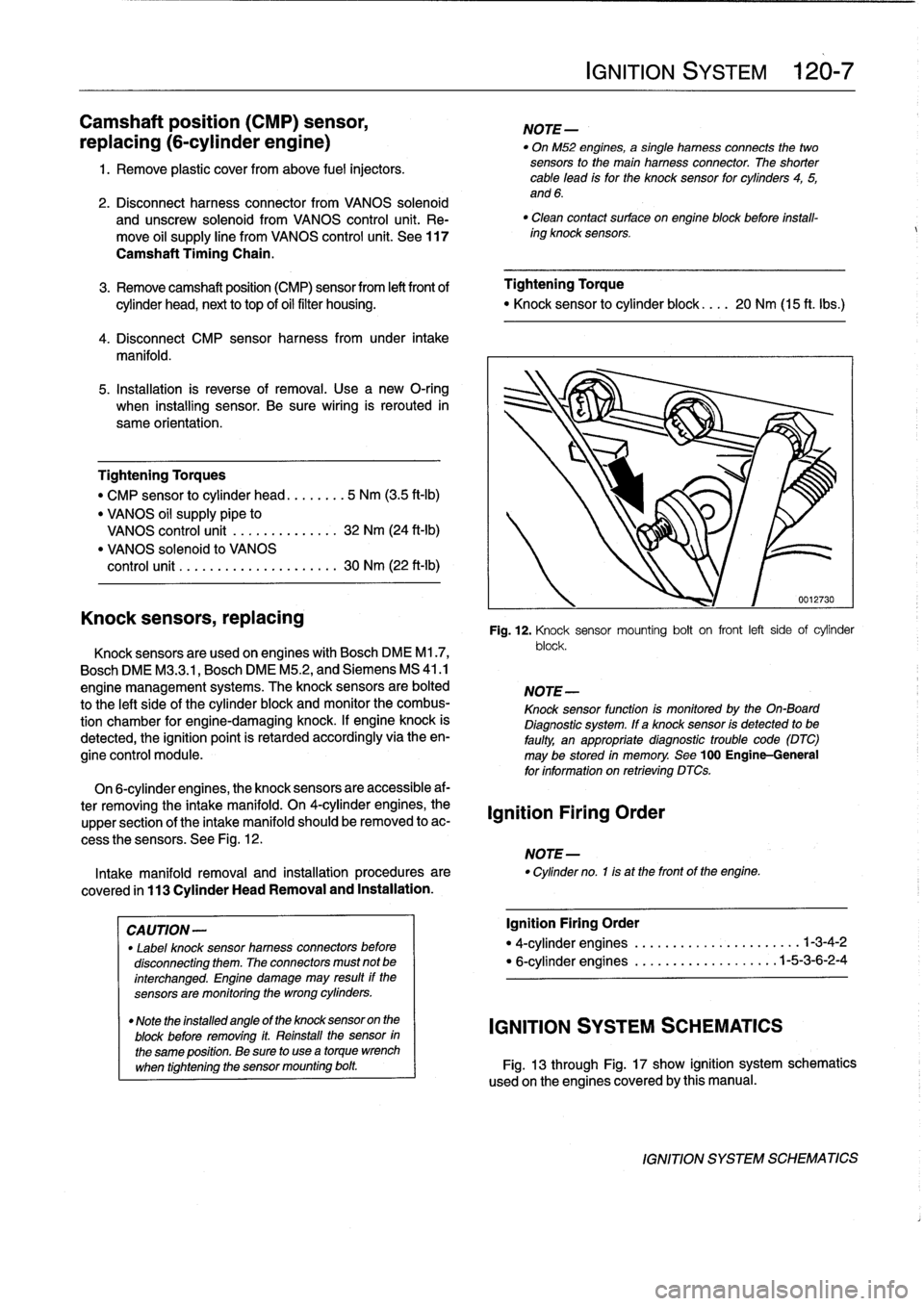
Camshaft
position
(CMP)
sensor,
replacing
(6-cylinder
engine)
1
.
Remove
plastic
cover
from
above
fuel
injectors
.
2
.
Disconnect
harness
connector
from
VANOS
solenoid
and
unscrew
solenoid
from
VANOS
control
unit
.
Re-
"
Clean
contactsurface
on
engine
block
before
fnstall
move
oil
supply
line
from
VANOS
control
unit
.
See
117
ing
knock
sensors
.
Camshaft
Timing
Chain
.
3
.
Remove
camshaft
position
(CMP)
sensor
from
left
frontof
cylinder
head,
next
to
top
of
oil
filter
housing
.
"
Knock
sensor
to
cylinder
block
....
20
Nm
(15
ft
.
lbs
.)
4
.
Disconnect
CMP
sensor
harnessfrom
under
intake
manifold
.
5
.
Installation
is
reverse
of
removal
.
Use
a
new
O-ring
when
installing
sensor
.
Be
sure
wiring
is
rerouted
in
same
orientation
.
Tightening
Torques
"
CMP
sensor
to
cylinder
head
....
.
.
..
5
Nm
(3
.5
ft-Ib)
"
VANOS
oil
supply
pipe
to
VANOS
control
unit
...........
.
..
32
Nm
(24
ft-Ib)
"
VANOS
solenoid
to
VANOS
control
unit
...
.
.................
30
Nm
(22
ft-Ib)
Knock
sensors,
replacing
Knock
sensors
are
usedon
engines
with
Bosch
DME
M1
.7,
Bosch
DME
M3
.3
.1,
Bosch
DME
M5
.2,
and
Siemens
MS
41
.1
engine
management
systems
.
The
knocksensors
are
bolted
to
the
left
sideof
the
cylinder
block
and
monitor
the
combus-
tion
chamber
for
engine-damaging
knock
.
If
engine
knock
is
detected,
the
ignition
point
is
retarded
accordingly
via
the
en-
gine
control
module
.
CA
UTION-
"
Label
knock
sensorharness
connectors
before
disconnecting
them
.
The
connectors
must
not
be
interchanged
.
Engine
damage
may
result
if
the
sensors
are
monitoring
the
wrong
cytinders
.
"
Note
the
installed
angle
of
the
knock
sensoron
the
block
before
removing
it
.
Reinstall
the
sensor
in
the
same
position
.
Be
sure
to
usea
torque
wrench
when
tightening
the
sensormounting
bola
NOTE
-
"
On
M52
engines,
a
single
harness
connects
the
twosensors
to
the
main
harness
connector
.
The
shorter
cable
lead
fs
for
the
knock
sensor
for
cytinders
4,
5,
and
6
.
Tightening
Torque
IGNITION
SYSTEM
120-
7
0012730
Fig
.
12
.
Knock
sensor
mounting
bolt
on
front
left
side
of
cylinder
block
.
NOTE-
Knock
sensor
function
Is
monitoredby
the
On-Board
Diagnostic
system
.
If
a
knock
sensor
is
detected
to
be
faulty,
an
appropriatediagnostic
trouble
code
(DTC)
may
be
stored
in
memory
.
See
100
Engine-General
for
information
on
retrieving
DTCs
.
On
6-cylinder
engines,
the
knock
sensors
are
accessible
af-
ter
removing
the
intake
manifold
.
On
4-cylinder
engines,
the
upper
section
of
the
intake
manifold
should
be
removed
to
ac-
cess
the
sensors
.
See
Fig
.
12
.
NOTE-
Intakemanifold
removal
and
installation
procedures
are
"
Cylinder
no
.
1is
at
the
front
of
the
engine
.
covered
in
113
Cylinder
HeadRemoval
and
Installation
.
Ignition
Firing
Order
Ignition
Firing
Order
"
4-cylinder
engines
.....
..
...
.
..........
.1-3-4-2
"
6-cylinder
engines
...........
..
.
.
..
..
1-5-3-6-2-4
IGNITION
SYSTEM
SCHEMATICS
Fig
.
13
through
Fig
.
17
show
ignition
system
schematics
usedon
the
enginescoveredby
this
manual
.
IGNITION
SYSTEM
SCHEMATICS
Page 132 of 759
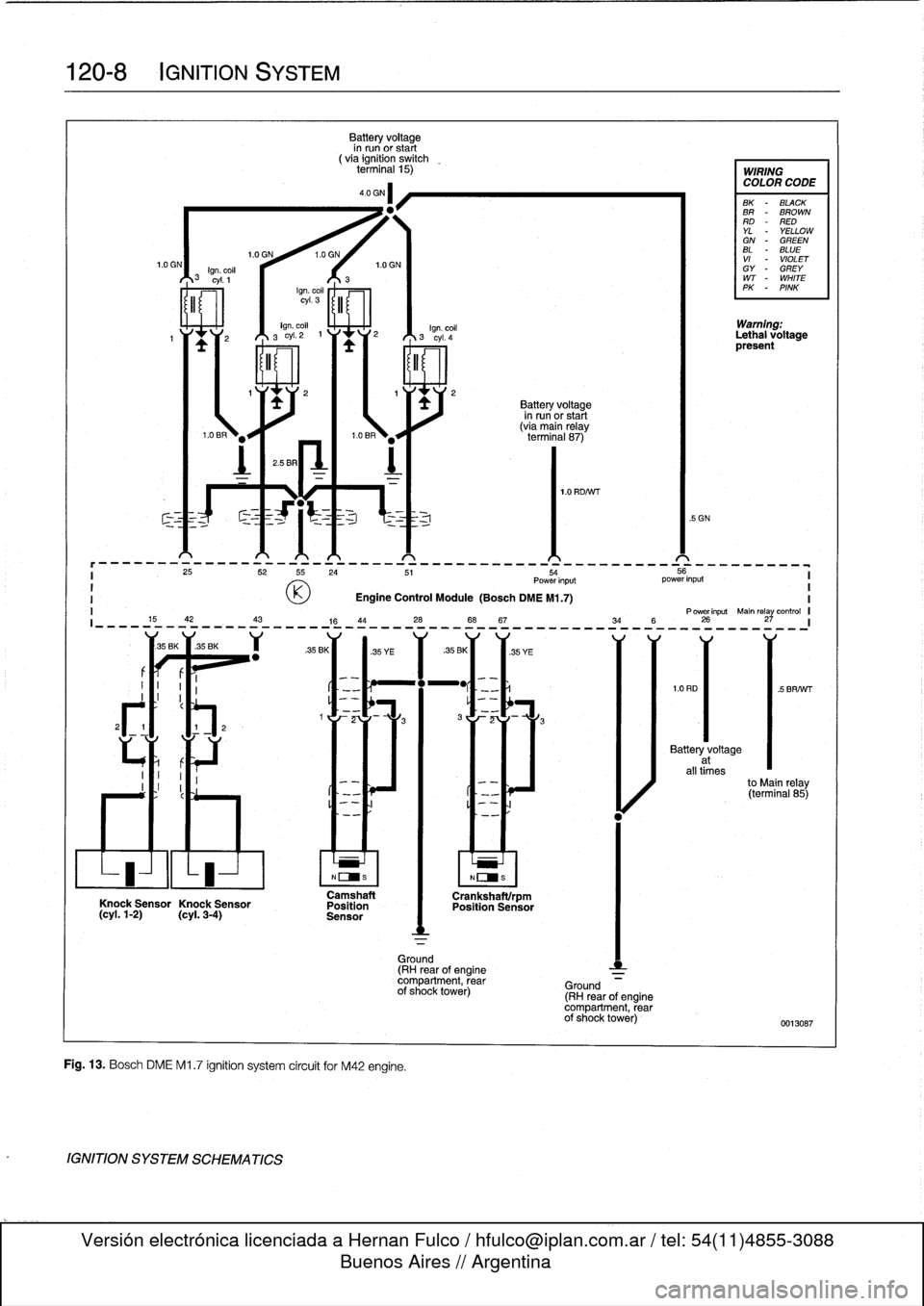
120-8
IGNITION
SYSTEM
1
1
.0
GN
1
.0
Gl
.0
GN
I
Ign
coil
1
.0
GN
.
Tti
%ti
r,
_%ti
_
_
ice_
I
25
52
5524
51
54
56
I
Power
input
power
input
t
U
Engine
Control
Module
(Bosch
DME
Ml
.7)
II
Powerinput
Mainrelaycontrol
I
15
42
43
16442868
67
34
6
26
27
1
-----
__
V
_
--
_
~
8K
.35
BK
.35
13,1
1
.35
YE
1
.35
BK35
VE
.35
3
cyl
.1
1
11
E
S
2
1
.0
BR
2
.5
BR
Ign
.
coil
cyl
.
3
II
Ign
.
coil
Ign
.
coil
3
cyI
.
2
1
Y
_
Y
2
k
3
cyl
.
4
IGNITION
SYSTEM
SCHEMATICS
Battery
voltage
in
run
or
start
(
vía
ignition
switchterminal
15)
WIRING
COLOR
CODE
4
.0
GN
1
.0
BR'V
.
Camshaft
Knock
Sensor
Knock
Sensor
Position
(cyl
.1-2)
(cyl
.3-4)
Sensor
Fig
.
13
.
Bosch
DME
M1
.7
ignition
system
circuit
for
M42
engine
.
Ground
(RH
rearof
engine
compartment,
rear
of
shock
tower)
N[INS
Crankshaftlrpm
Position
Sensor
Battery
voltage
in
run
or
start
(vía
main
relay
terminal
87)
Ground
(RH
rearof
engine
compartment,
rearof
shock
tower)
5GN
BK
-
BLACK
BR
"
BROWN
RD
-
RED
YL-
YELLOW
GN
-
GREEN
BL
-
BLUE
VI
-
VIOLET
GY
-
GREY
WT
-
WHITE
PK
-
PINK
Warning
:
Lethal
voltagepresent
Battery
voltage
at
all
times
to
Main
relay
(terminal
85)
'Y
Y
---------------------
0013087
Page 133 of 759
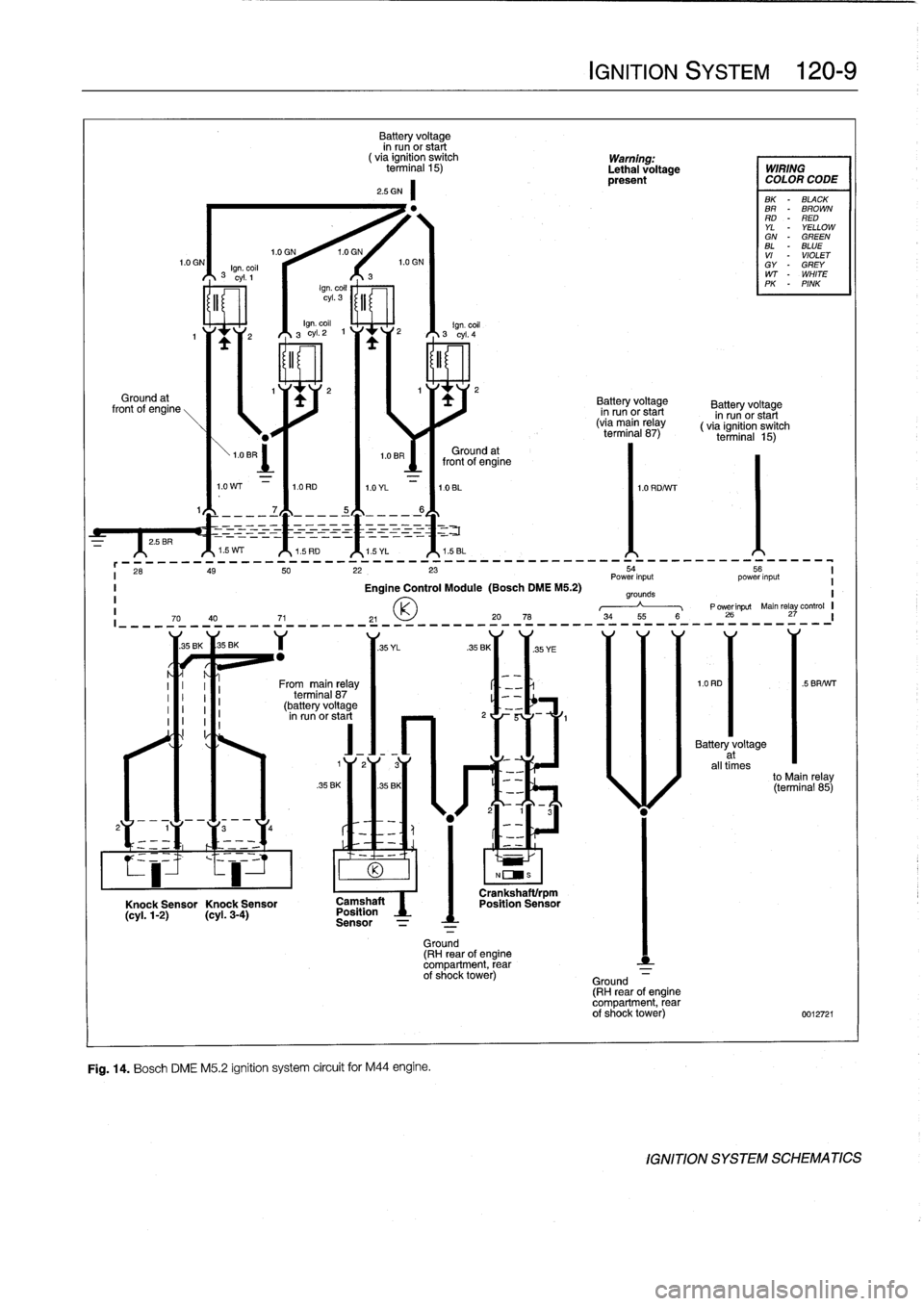
^1
.5WT
^1
.5RD
^1
.5YL
^1
.5BL
r
--__
____-
__-_
___-_
-___-_____--__--
-____-___
____-
i
26
g
5022
23
54
5
I
Power
input
power
input
I
Engine
Control
Module
(Bosch
DME
M5
.2)
I
I
grounds
I
P
owerinput
Main
relay
control
I
70
40
71
21
2078
34
55
626
27
----------------------
-
---------
-
--
-
------------
-
-----------
.,
v
1
1
.1
v
`
1
35BK
35BK
2
(
1Y
¡3
194
Knock
Sensor
Knock
Sensor
(cyl
.1-2)
(cyl
.3-4)
Frommain
relay
terminal
87
(battery
voltage
in
run
or
start
Battery
voltage
in
run
or
start
(
via
ignition
switch
Warnin
terminal
15)
Lethal
óltage
WIRING
present
COLOR
CODE
2
.5
GN
'
1
.0
YL
/
1
.0
BL
/
1
.0
RDNJT
.35
BK
/
/
.35
BK
Camshaft
Position
Sensor
-_
Fig
.
14
.
Bosch
DME
M5
.2
ignition
system
circuit
for
M44
engine
.
Ground
(RH
rear
of
engine
compartment,
rearof
shock
tower)
Crankshaftirpm
Position
Sensor
IGNITION
SYSTEM
120-9
Batteryvoltage
Battery
voltage
in
run
or
start
in
run
or
start
(via
main
relay
(
via
ignition
switch
terminal
87)
terminal
15)
BK
-
BLACX
BR
-
BROWN
RD
-
RED
YL
-
YELLOW
GN
-
GREEN
BL
-
BLUE
VI
-
VIOLET
GY
-
GREY
WT
-
WHITE
PK
-
PINK
Battery
voltage
at
all
times
to
Main
relay
(terminal
85)
Ground
(RH
rear
of
engine
compartment,
rearof
shock
tower)
0012721
lGNITION
SYSTEM
SCHEMATlCS
Page 134 of 759
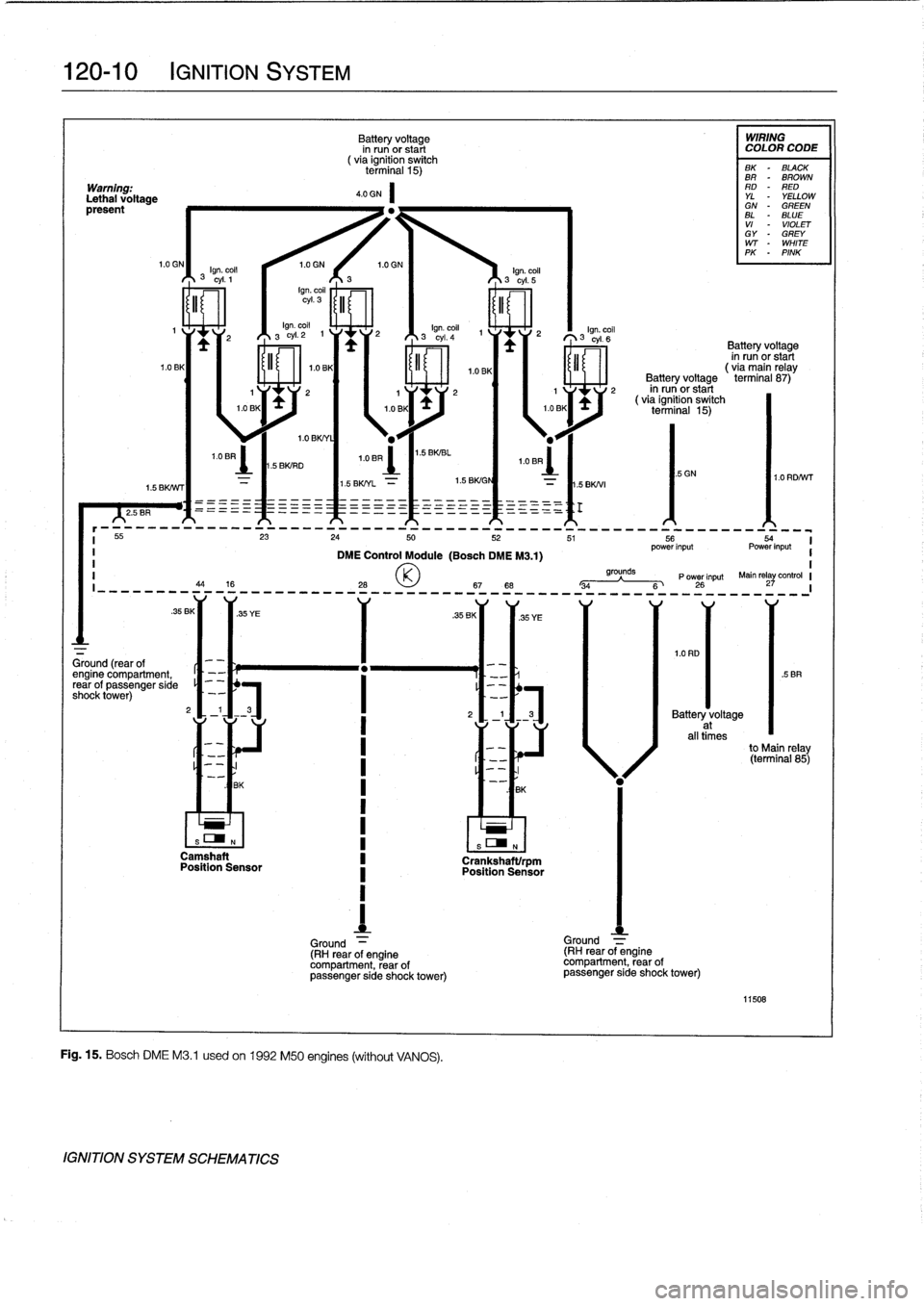
120-10
IGNITION
SYSTEM
Ground
(rear
of
engine
compartment,
rear
of
passenger
side
shock
tower)
.!
BK
Camshaft
Position
Sensor
IGNITION
SYSTEM
SCHEMATICS
Batteryvoltage
in
run
or
start
(
via
ignition
switch
terminal
15)
---------------------------------------------------------
55
S5154
i
power
input
Power
input
1
DME
Control
Module(Bosch
DME
M3
.1)
Ground
-
(RHrear
of
enginecompartment,
rearof
passenger
side
shock
tower)
Fig
.
15
.
Bosch
DME
M3
.1
usedon1992
M50
engines(without
VANOS)
.
.EBK
Crankshaftlrpm
Position
Sensor
5GN
1.0
RD
Ground
(RH
rearof
enginecompartment,
rear
of
passenger
side
shock
tower)
WIRING
COLOR
CODE
BK
-
BLACK
BR
-
BROWN
RD
-
RED
YL
-
YELLOWGN
-
GREEN
BL
-
BLUE
VI-
VIOLET
GY
"
GREY
WT
"
WHITE
PK
-
PINK
Batteryvoltage
in
run
or
start
(
via
main
relay
Battery
voltage
terminal
87)
in
run
or
start
(via
ignition
switch
terminal
15)
11508
1
grounds
Main
rela
control
P
ower
Input
Y
I
-
34
---"--
6
26
27
1
Battery
voltage
at
all
times
to
Main
relay
(terminal
85)
Page 135 of 759
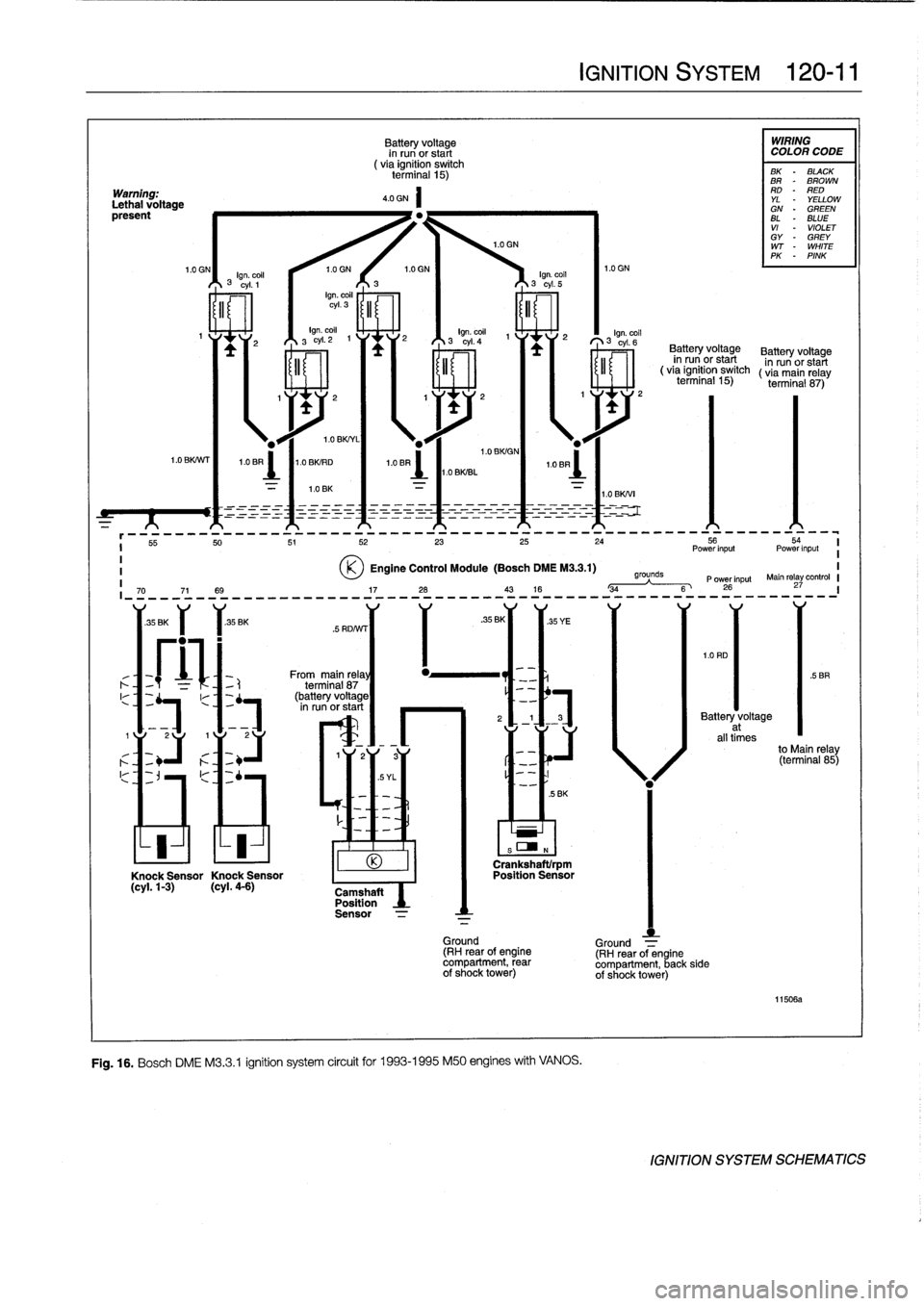
RER
Knock
Sensor
Knock
Sensor
(cyl
.1-3)
(cyl
.4-6)
Batteryvoltage
IMIRING
in
run
or
start
COLORCODE
(
via
ignition
switch
termina¡
15)
BK
BLAOK
BR
BROWN
RD
-
RED
YL
-
YELLOW
GN
"
GREEN
EL
-
BLUF
VI
-
VIOLET
GY
-
GREY
WT
-
WHITE
PK
-
PINK
4
.0
GN
l1/1j\
I'1
/~/1r1
l\r1
1
55
so
si
52
23
25
24
56
54
1
Power
input
Power
input
III
O
Engine
Control
Module
(Bosch
DMEM13
.1)
II
grounds
P
ower
input
Main
relaY
control
I
70
__
_
71
69
17
28
43
16
-34---"-6
26
27
____________________________________________
From
main
relaterminal
87
(battery
voltage
in
run
or
start
.5
YL
Camshaft
Position
Sensor
Ground
(RH
rearof
enginecompartment,
rear
of
shock
tower)
.5
BK
Crankshaft/rpm
Position
Sensor
Fig
.
16
.
Bosch
DME
M33
.1
ignition
system
círcuit
for
1993-1995
M50
engines
with
VANOS
.
IGNITION
SYSTEM
120-11
Ground
=
(RH
rear
of
engine
compartment,
back
sideof
shock
tower)
Batteryvoltage
Battery
voltage
in
run
or
start
in
run
or
start
(
via
ignition
switch
(
via
main
relay
terminal
15)
terminal
87)
1
.0
RD
11506a
.5
BR
Batteryvoltage
at
all
times
to
Main
relay
(terminal
85)
IGNITION
SYSTEM
SCHEMATICS
Page 136 of 759
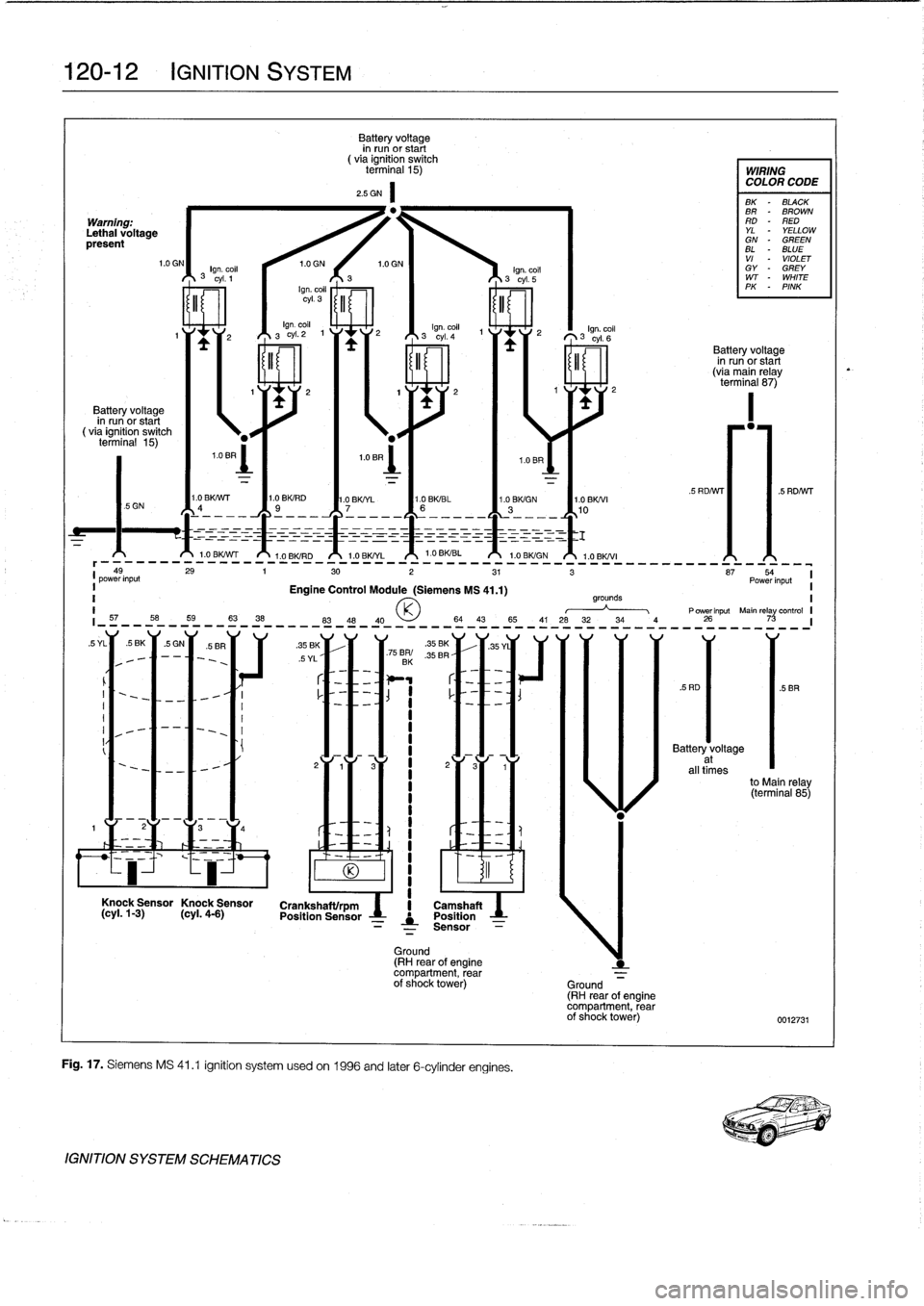
120-12
IGNITION
SYSTEM
Warning
.
Lethal
voltagepresent
Battery
voltage
in
run
or
start
(via
ignitíon
switch
terminal
15)
I
t
IGNITION
SYSTEM
SCHEMATICS
Battery
voltage
in
run
or
start
(
via
ignition
switchterminal
15)
WIRING
COLOR
CODE
Knock
Sensor
Knock
Sensor
Crankshaftlrpm
Camshaft
(cyl
.
1-3)
(cyl
.
4-6)
Position
Sensor
Position
-
-
Sensor
-
Fig
.
17
.
Siemens
MS
41
.1
ignition
systemusedon1996
and
later
6-cylinder
engines
.
1.0
BR
PQ
1
.08~1
.0BKIRD
/1
.0BK/YL
'10BK/BL
'1
.03KIGN
10BKNI
4
1D
BK
-
BLACK
BR
-
BROWN
RD
-
RED
YL
-
YELLOW
GN
-
GREEN
BL
-
BLUE
VI-
VIOLET
GY
-
GREY
WT
-
WHITE
PK
-
PINK
Batteryvoltage
in
run
or
start
(via
main
relay
terminal
87)
!1
rl
1.0
B~
^
1.0
BK/RD
^
1.0
BKIYL
^
1
.0
BK/BL
n
1.0
BK/GN
n
1
.0
BKIVI
%~
r
-------
--------------_____________----_______-_-____
49
29
1
30
2
31
3
8754
1
power
input
Power
input
I
1
Engine
Control
Module
(Siemens
MS
41
.1)
1
1
grounds
1
n
1
Powerinput
Mainrelaycontrol
1
1-
57
___
58
_
59
_
__
63
_
38
83
48
40
64
43
65
41
28
32
34
4
26
73
1
-
-----------
-
_-----
-
------
_
------
-
------
-
---
-
.5Y1-
.5BKY.5GNY.5BRY
Y
.35BKY
1
Y
Y
.35BKY/Y35YY
75
.18R/
.5YL-1
1'
.
Batteryvoltage
at
all
times
to
Main
relay
(terminal
85)
Ground
v
(RH
rear
of
engine
Z
compartment,
rear
=
of
shock
tower)
Ground
(RH
rear
of
enginecompartment,
rearof
shock
tower)
0012731
Page 137 of 759
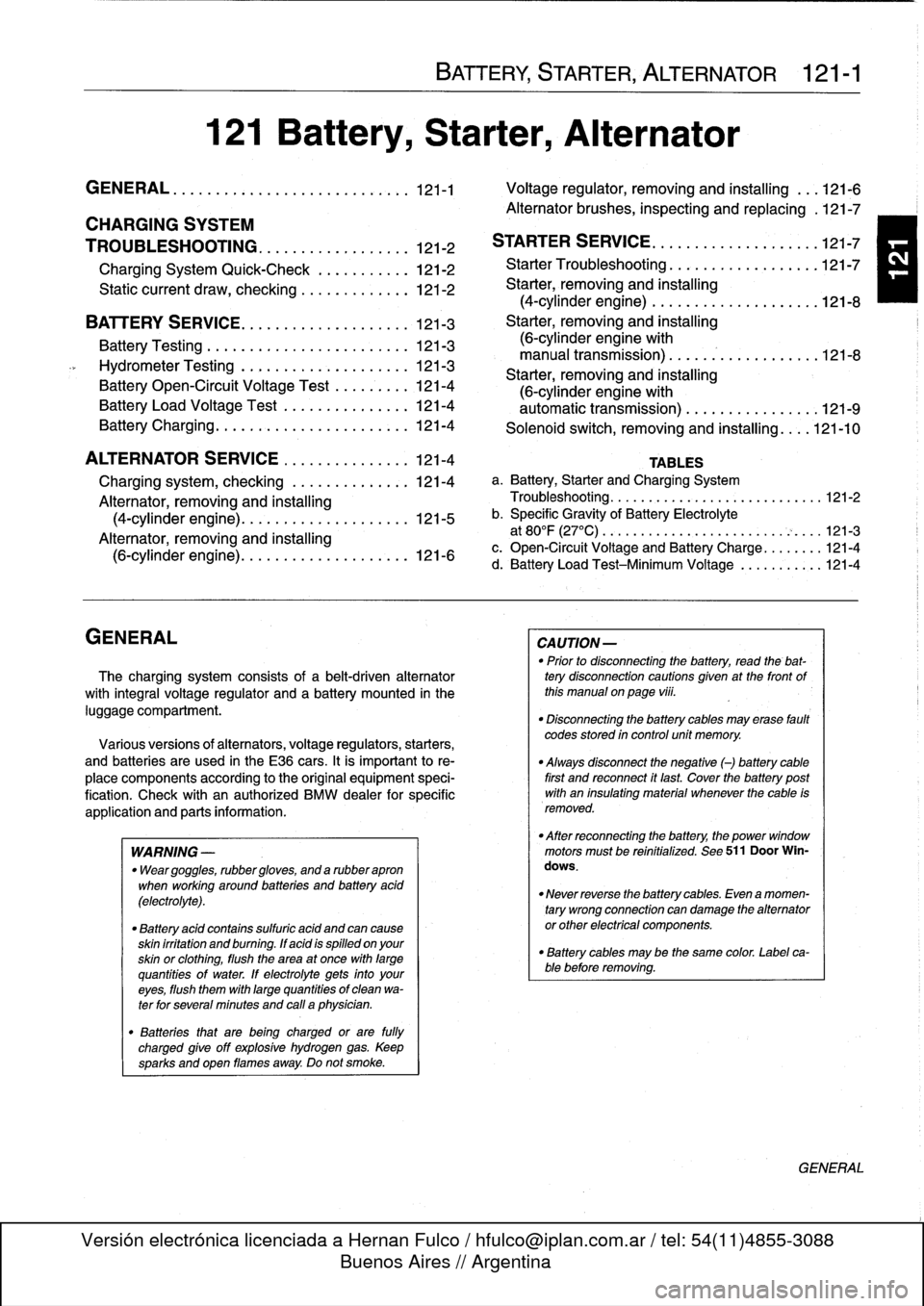
CHARGING
SYSTEM
TROUBLESHOOTING
.............
.
.
.
.
.121-2
Charging
System
Quick-Check
...
.
..
.
...
.
121-2
Static
current
draw,
checking
........
.
...
.
121-2
BATTERY
SERVICE
....................
121-3
Battery
Testing
.
.
.
.
.
.........
.
........
.
121-3
Hydrometer
Testing
.
...
.
.
.
...
.
.........
121-3
Battery
Open-Circuit
Voltage
Test
....
.
....
121-4
Battery
Load
Voltage
Test
.
.
.
.
.
.
.........
121-4
Battery
Charging
.
.
.
.
...
.
.
.
.
.
.
.
.........
121-4
ALTERNATOR
SERVICE
.
.
.
.
.
.
.....
.
...
121-4
Chargingsystem,checking
.
.
.
.
.
.........
121-4
Alternator,
removingand
installing
(4-cylinder
engine)
....
.
.
.
.
.
.
.
.........
121-5
Alternator,
removingand
installing
(6-cylinder
engine)
..
.
.
.
.
.
.
.
.
.
.........
121-6
GENERAL
The
charging
system
consists
of
a
belt-driven
alternator
with
integral
voltage
regulator
and
a
battery
mounted
in
the
luggage
compartment
.
Various
versions
of
alternators,
voltage
regulators,
starters,
and
batteries
are
used
in
the
E36
cars
.
It
is
important
to
re-
place
components
according
tothe
original
equipment
speci-
fication
.
Check
with
an
authorized
BMW
dealer
for
specific
application
and
parts
information
.
WARNING
-
"
Weargoggles,
rubbergloves,
and
a
rubberapron
when
working
around
batteries
and
battery
acid
(electrolyte)
.
"
Battery
acid
contains
sulfuric
acid
and
can
cause
skin
irritation
and
burning
.
ff
acid
is
spilled
onyour
skin
or
clothing,
flush
the
area
at
once
with
large
quantities
of
water
.
lf
electrolyte
gets
into
your
eyes,flush
them
with
largequantities
of
clean
wa-
terfor
several
minutes
and
call
a
physician
.
"
Batteries
that
are
being
charged
or
are
fully
charged
give
off
explosive
hydrogen
gas
.
Keep
sparks
and
open
flames
away
.
Do
not
smoke
.
BATTERY,
STARTER,
ALTERNATOR
121-1
121
Battery,
Starter,
Alternator
GENERAL
..
.
...
.
........
.
...
.
.
.
.
.
.
.
.
.
121-1
Voltage
regulator,
removing
and
ínstalling
.
.
.
121-6
Alternator
brushes,
inspecting
and
replacing
.121-7
STARTER
SERVICE
....
.
.
.
.
.
..........
.121-7
Starter
Troubleshootíng
121-7
15
..
.
.
.
.
.
........
.
.
.
Starter,
removing
and
installing
(4-cylinder
engine)
....
.
.
.
............
.
121-8
Starter,
removing
and
installing
(6-cylinder
engine
with
manual
transmission)
..
.
...........
.
...
121-8
Starter,
removing
and
installing
(6-cylinder
engine
with
automatic
transmission)
................
121-9
Solenoid
switch,
removingand
installing
....
121-10
TABLES
a
.
Battery,
Starter
and
Charging
System
Troubleshooting
............
.
.
.
.
:...
........
121-2
b
.
Specific
Gravity
of
Battery
Electrolyte
at
80°F
(27°C)
...............
.
.
..
..........
121-3
c
.
Open-Circuit
Voltage
and
Battery
Charge
........
121-4
d
.
Battery
Load
Test-Minimum
Voltage
.
..........
121-4
CAUTION
-
"
Prior
to
disconnectiog
the
battery,
read
the
bat-tery
disconnection
cautions
given
at
the
front
of
this
manual
on
page
viii
.
"
Disconnecting
the
battery
cables
may
erase
fault
codes
stored
in
control
unit
memory
.
"
Always
disconnect
the
negative
()
battery
cable
first
and
reconnect
it
last
.
Cover
the
battery
post
with
an
insulating
material
whenever
the
cable
is
removed
.
"
After
reconnecting
the
battery,
the
power
window
motors
must
be
reinitialized
.
See
511
Door
Win-
dows
.
"
Never
reverse
the
battery
cables
.
Even
a
momen-
tary
wrong
connection
can
damage
the
alternatoror
other
electrical
components
.
"
Battery
cables
may
be
the
same
color
.
Label
ca-blebefore
removing
.
GENERAL
Page 138 of 759
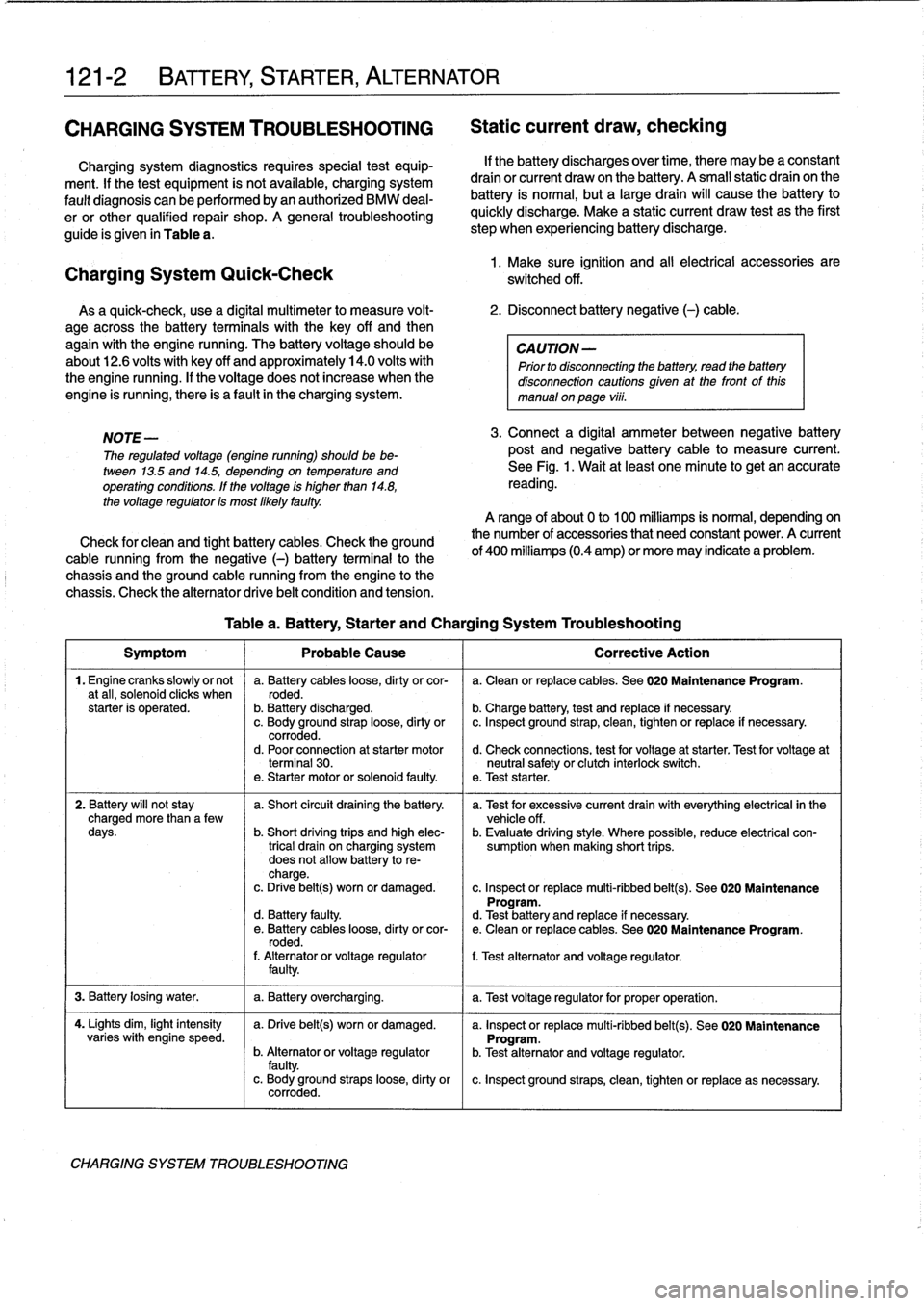
121-2
BATTERY,
STARTER,
ALTERNATOR
CHARGING
SYSTEM
TROUBLESHOOTING
Static
currentdraw,
checking
Charging
system
diagnostics
requires
special
test
equip-
ment
.
If
the
test
equipment
is
not
available,
charging
system
fault
diagnosis
can
be
performedby
an
authorized
BMW
deal-
eror
other
qualified
repair
shop
.
A
general
troubleshooting
guide
is
given
in
Table
a
.
Charging
System
Quick-Check
As
a
quick-check,
use
a
digital
multimeter
lo
measure
volt-
2
.
Disconnect
battery
negative
(-)
cable
.
age
across
the
battery
terminals
with
the
key
off
and
then
again
with
the
engine
running
.
The
battery
voltage
should
be
CAUTION-
about12
.6
volts
with
key
off
and
approximately
14
.0
volts
with
Prior
to
disconnecting
the
battery,
read
the
battery
the
engine
running
.
If
the
voltage
does
not
increase
when
the
disconnection
cautions
given
at
the
front
of
this
engine
is
running,there
is
a
fault
in
the
charging
system
.
manual
onpaga
viii
.
NOTE
-
The
regulated
voltage
(engine
running)
should
be
be-
tween
13
.5
and
14
.5,
depending
on
temperatura
and
operating
conditions
.
If
the
voltage
is
higher
than
14
.8,
the
voltage
regulator
is
most
Mely
faulty
.
Check
for
clean
and
tight
battery
cables
.
Check
the
ground
cable
running
from
the
negative
(-)
battery
terminal
lo
the
chassis
and
the
ground
cable
running
from
the
engine
lo
the
chassis
.
Check
the
alternator
drive
belt
condition
and
tension
.
If
the
battery
discharges
over
time,
there
may
be
a
constant
drain
or
current
draw
on
the
battery
.
A
small
static
drain
on
the
battery
is
normal,
but
a
largedrain
will
cause
the
battery
lo
quickly
discharge
.
Make
a
static
current
draw
test
asthe
first
step
when
experiencing
battery
discharge
.
1
.
Make
sure
ignition
and
al¡
electrical
accessories
are
switched
off
.
3
.
Connect
a
digital
ammeter
between
negative
battery
post
and
negative
battery
cable
lo
measure
current
.
See
Fig
.
1
.
Wait
at
least
one
minuta
lo
get
an
accurate
reading
.
A
range
of
about
0
lo
100
milliamps
is
normal,
dependingon
the
number
of
accessories
that
need
constant
power
.
A
current
of
400
milliamps
(0.4
amp)
or
more
may
indicate
a
problem
.
Table
a
.
Battery,
Starter
and
Charging
System
Troubleshooting
Symptom
1
Probable
Cause
1
Correctiva
Action
1
.
Engine
cranks
slowlyor
not
a
.
Battery
cables
loose,
dirty
orcor-
a
.
Clean
or
replace
cables
.
See020
Maintenance
Program
.
a
tall,
solenoíd
clicks
when
roded
.
starter
is
operated
.
b
.
Battery
discharged
.
b
.
Charge
battery,
test
and
replace
if
necessary
.
c
.
Body
ground
straploose,
dirty
or
c
.
Inspect
ground
strap,
clean,
tighten
or
replace
if
necessary
.
corroded
.
d
.
Poor
connection
at
starter
motor
d
.
Check
connections,
test
for
voltage
at
starter
.
Test
for
voltage
at
terminal
30
.
neutral
safety
or
clutch
interlock
switch
.
e
.
Starter
motor
or
solenoid
faulty
.
e
.
Test
starter
.
2
.
Battery
will
not
stay
a
.
Short
circuit
draining
the
battery
.
a
.
Test
for
excessive
current
drainwith
everything
electrical
in
the
charged
more
than
a
few
vehicle
off
.
days
.
b
.
Short
driving
trips
and
high
elec-
b
.
Evaluate
driving
style
.
Where
possible,
reduce
electrical
con
trical
drain
on
charging
system
sumption
when
making
short
trips
.
does
not
allow
battery
to
re-
charge
.
c
.
Drive
belt(s)
worn
or
damaged
.
c
.
Inspect
or
replace
multi-ribbed
belt(s)
.
See
020
Maintenance
Program
.
d
.
Battery
faulty
.
d
.
Test
battery
and
replace
íf
necessary
.
e
.
Battery
cables
loose,
dirty
orcor-
e
.
Clean
or
replace
cables
.
See
020
Maintenance
Program
.
rodad
.
f
.
Alternatoror
voltage
regulator
f
.
Test
alternator
and
voltage
regulator
.
faulty
.
3
.
Battery
losing
water
.
1
a
.
Battery
overcharging
.
1
a
.
Test
voltage
regulator
for
proper
operation
.
4
.
Lights
dim,
light
intensity
a
.
Drive
belt(s)
worn
or
damaged
.
a
.
Inspect
or
replace
multi-ribbed
belt(s)
.
See
020
Maintenance
varies
with
engine
speed
.
Program
.
b
.
Alternatoror
voltage
regulator
b
.
Test
alternator
and
voltage
regulator
.
faulty
.
c
.
Body
ground
straps
loose,
dirty
or
c
.
Inspect
ground
straps,
clean,
tighten
or
replace
as
necessary
.
corroded
.
CHARGING
SYSTEM
TROUBLESHOOTING
Page 139 of 759
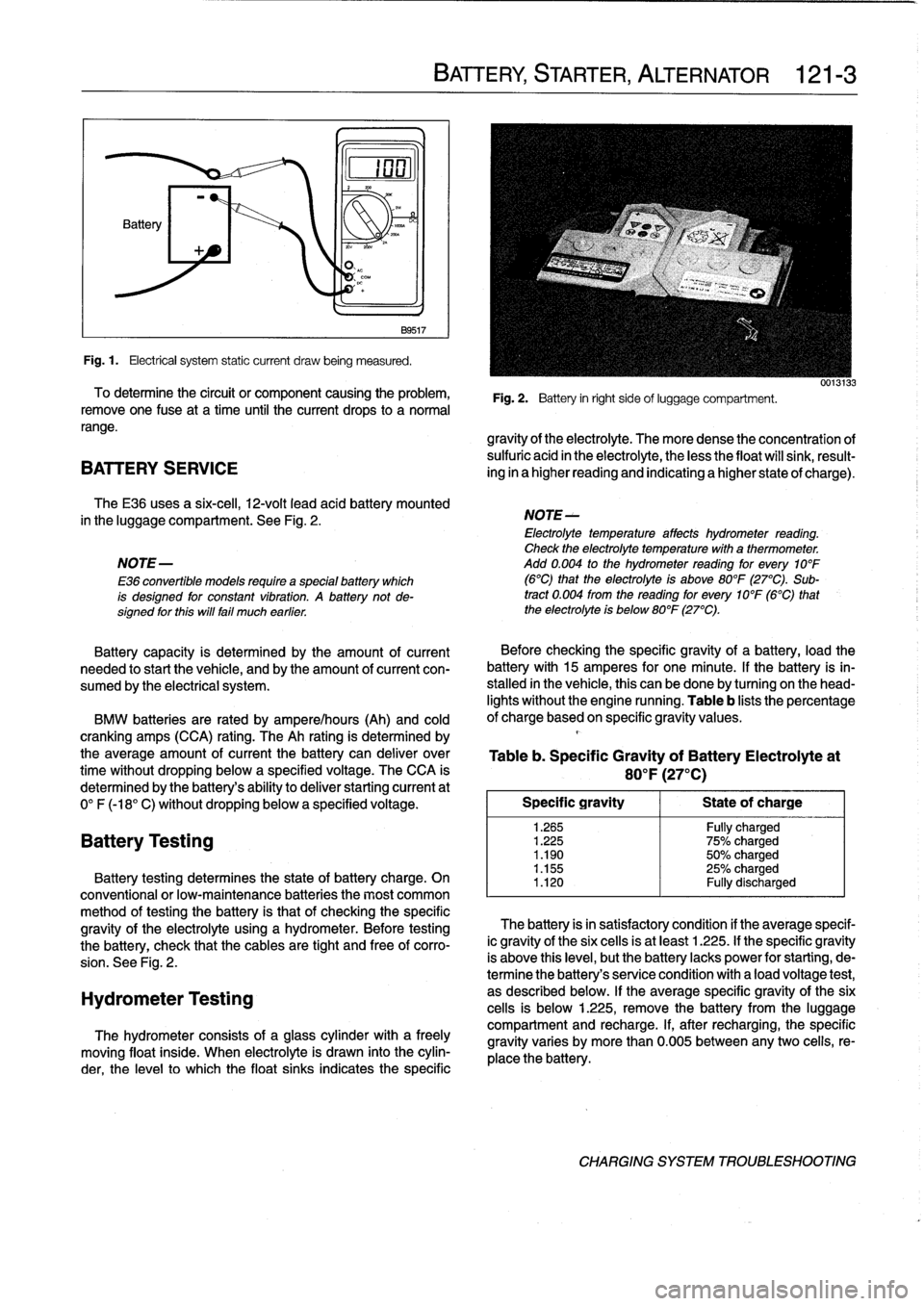
Fig
.1.
Electrical
system
static
current
draw
being
measured
.
To
determine
the
circuit
or
component
causing
the
problem,
remove
one
Puse
at
a
time
until
the
current
drops
to
a
normal
range
.
BATTERY
SERVICE
The
E36
uses
a
six-cell,
12-volt
leadacid
battery
mounted
in
the
luggage
compartment
.
See
Fig
.
2
.
NOTE-
E36
convertible
models
require
a
specialbattery
which
is
designed
for
constant
vibratfon
.
A
battery
not
de-signed
for
this
will
fail
much
earlier
.
Battery
capacity
is
determined
by
the
amount
of
current
needed
tostart
the
vehicle,
and
by
the
amount
of
current
con-
sumed
by
the
electrical
system
.
BMW
batteries
are
rated
by
ampere/hours
(Ah)
and
cold
cranking
amps
(CCA)
rating
.
The
Ah
rating
is
determined
by
the
average
amount
of
current
the
battery
can
deliver
over
time
without
dropping
below
a
specified
voltage
.
The
CCA
is
determined
by
the
battery's
ability
to
deliver
starting
current
at
0°
F
(-18°
C)
without
dropping
below
a
specified
voltage
.
Battery
Testing
noN~A
B9517
Battery
testing
determines
the
state
of
battery
charge
.
On
conventional
or
low-maintenance
batteries
the
most
common
method
of
testing
the
battery
is
that
of
checking
the
specific
gravity
of
the
electrolyte
using
a
hydrometer
.
Before
testing
the
battery,
check
that
the
cables
are
tight
and
free
of
corro-
sion
.
See
Fig
.
2
.
Hydrometer
Testing
The
hydrometer
consists
of
a
glass
cylinder
with
a
freely
moving
float
inside
.
When
electrolyte
is
drawn
into
the
cylin-
der,
the
levelto
which
the
float
sinks
indicates
the
specific
BATTERY,
STARTER,
ALTERNATOR
121-
3
Fig
.
2
.
Battery
in
right
sideof
luggage
compartment
.
gravity
of
the
electrolyte
.
The
more
dense
the
concentration
of
sulfuric
acid
in
the
electrolyte,
the
less
the
float
will
sink,
result-
ing
in
a
higher
reading
and
indicating
a
higher
state
of
charge)
.
NOTE-
Electrolyte
temperature
affects
hydrometer
reading
.
Check
the
electrolyte
temperaturewith
a
thermometer
.
Add
0
.004
to
the
hydrometer
reading
for
every
10°F
(6°C)
that
the
electrolyte
is
above
80°F
(27°C)
.
Sub-
tract
0
.004
from
the
reading
for
every
10°F
(6°C)
that
the
electrolyte
is
below
80°F
(27°C)
.
Before
checking
the
specificgravity
of
a
battery,
load
the
battery
with
15
amperes
for
one
minute
.
lf
the
battery
is
in-
stalled
in
the
vehicle,
this
can
be
done
by
turning
on
the
head-
lights
without
the
engine
running
.
Table
b
lists
the
percentage
of
charge
based
on
specific
gravity
values
.
Table
b
.
Specific
Gravity
of
Battery
Electrolyteat
80
°
F
(27°C)
Specific
gravity
1
Stateof
charge
1
.265
Fully
charged
1
.225
75%
charged
1
.190
50%
charged
1
.155
25%
charged
1
.120
Fully
discharged
The
battery
isin
satisfactory
condition
if
theaverage
specif-
ic
gravity
of
the
six
cells
is
at
least
1
.225
.
If
the
specific
gravity
is
above
this
leve¡,
butthe
battery
lacks
power
for
starting,
de-
termine
the
battery's
senrice
condition
with
a
load
voltage
test,
as
described
below
.
If
the
average
specific
gravity
of
the
six
cells
is
below
1
.225,
remove
the
battery
from
the
luggage
compartment
and
recharge
.
If,
after
recharging,
the
specific
gravity
varies
by
more
than
0
.005
between
any
two
celis,
re-
place
the
battery
.
CHARGING
SYSTEM
TROUBLESHOOTING
Page 140 of 759
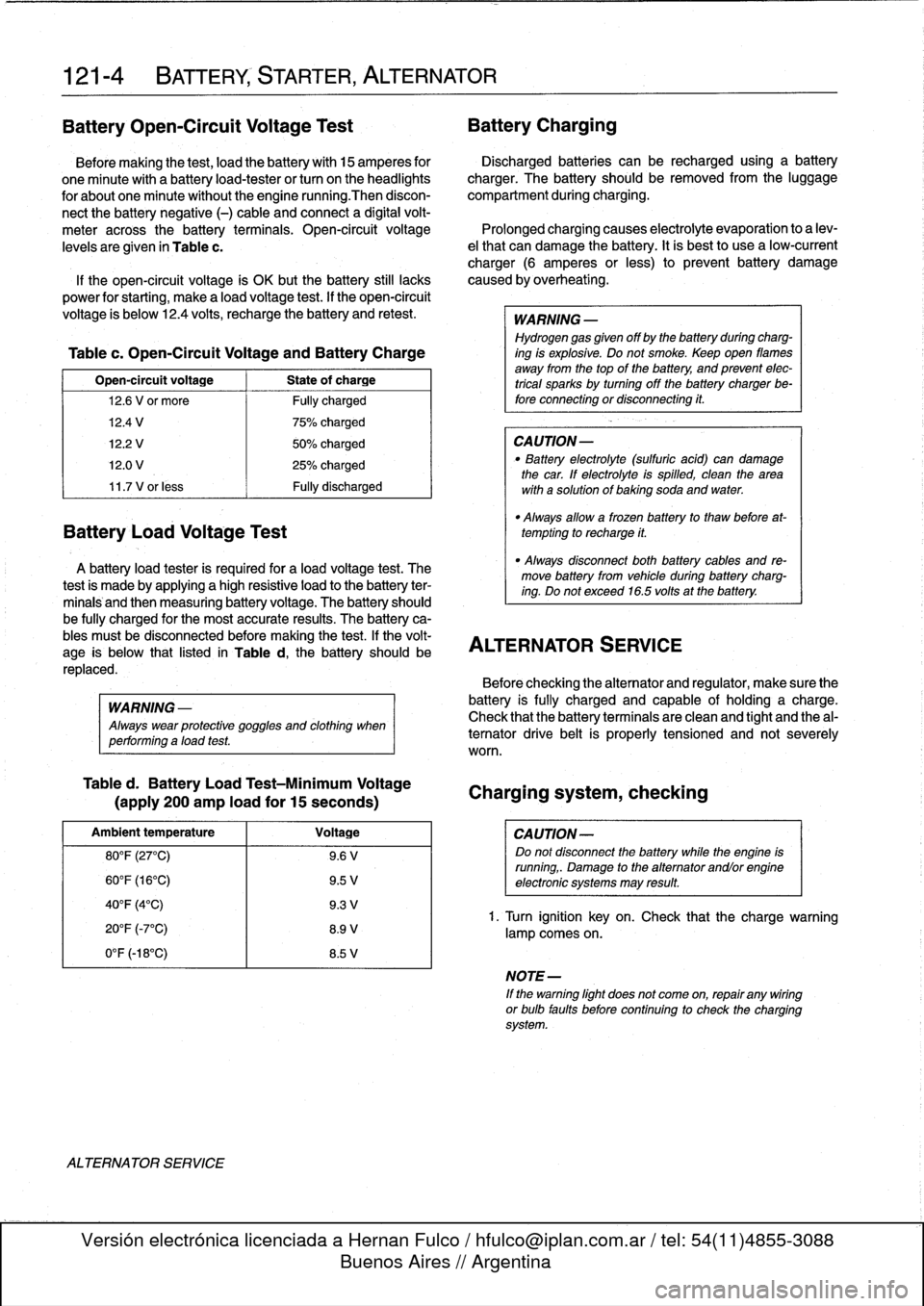
121-
4
BATTERY,
STARTER,
ALTERNATOR
BatteryOpen-Circuit
Voltage
Test
Battery
Charging
Before
making
the
test,
load
the
battery
with
15
amperes
for
Discharged
batteries
can
be
recharged
using
a
battery
one
minute
with
a
batteryload-tester
or
turn
on
the
headlights
charger
.
The
battery
should
be
removed
from
the
luggage
for
about
one
minute
without
the
engine
running
.Then
discon-
compartment
during
charging
.
nect
the
battery
negative
(-)
cable
and
connect
a
digital
volt-
meter
acrossthe
battery
terminals
.
Open-circuit
voltage
Prolonged
charging
causes
electrolyte
evaporation
to
a
lev
levels
are
given
in
Table
c
.
el
that
can
damage
the
battery
.
Itis
bestto
use
a
low-current
charger
(6
amperes
or
less)
to
prevent
battery
damage
If
the
open-circuit
voltage
ís
OK
butthe
battery
still
lacks
caused
by
overheating
.
power
for
starting,
make
a
load
voltage
test
.
If
the
open-circuit
voltage
is
below
12
.4
volts,
recharge
the
battery
and
retest
.
WARNING
-
Hydrogen
gas
given
off
by
the
battery
duringcharg-
Table
c
.
Open-Circuit
Voltage
and
Battery
Charge
ing
is
explosive
.
Do
not
smoke
.
Keep
open
llames
away
from
the
top
of
the
battery,
and
prevent
elec
Open-circuit
voltage
State
of
charge
trical
sparks
by
turning
offthe
battery
charger
be-
12
.6
V
or
more
Fully
charged
fore
connecting
or
disconnecting
it
.
12
.4
V
1
75%
charged
12
.2
V
50%
charged
CAUTION-
12
.0
V
25%
charged
"
Battery
electrolyte
(sulfuric
acid)
can
damage
the
car
.
If
electrolyte
isspilled,
clean
the
area
11
.7
V
or
less
Fully
discharged
with
a
solution
of
baking
soda
and
water
.
Battery
Load
Voltage
Test
A
battery
load
tester
is
required
for
a
load
voltage
test
.
The
-
Always
disconnect
both
battery
cables
and
re-
test
is
made
by
applying
a
high
resistive
load
to
the
battery
ter-
move
battery
from
vehicle
during
battery
charg-
ing
.
Do
not
exceed
16
.5volts
at
the
battery
.
minals
and
then
measuring
battery
voltage
.
The
battery
should
be
fully
charged
for
the
most
accurate
results
.
The
battery
ca-
bles
mustbe
disconnected
before
making
the
test
.
If
the
volt-
ALTERNATOR
$ERVICE
age
is
below
that
listed
in
Table
d,
the
battery
should
be
replaced
.
WARNING
-
Always
wear
protective
goggles
and
clothing
when
performing
aload
test
.
Table
d
.
Battery
Load
Test-Minimum
Voltage
(apply
200
amp
load
for
15
seconds)
Ambient
temperature
Voltage
80°F
(27°C)
9
.6
V
60°F
(16°C)
9
.5
V
40°F
(4°C)
9
.3
V
20°F
(-7°C)
8
.9
V
0°F
(-18°C)
8
.5
V
ALTERNATOR
SERVICE
"
Always
allow
a
frozen
battery
to
thaw
before
at-
tempting
to
recharge
it
.
Before
checking
the
alternator
and
regulator,
make
sure
the
battery
is
fully
charged
and
capable
of
holding
acharge
.
Check
that
the
battery
terminals
are
clean
and
tight
and
the
al-
ternator
drive
belt
is
properly
tensioned
and
not
severely
worn
.
Charging
system,
checking
CAUTION-
Do
not
disconnect
the
battery
while
the
engine
is
running,
.
Damage
to
the
alternator
andlorengine
electronic
systems
may
result
.
1.
Turn
ignition
key
on
.
Check
that
the
chargewarning
lamp
comes
on
.
NOTE-
If
the
warning
light
does
not
come
on,
repair
any
wiring
or
bulb
faults
before
continuing
to
check
the
charging
system
.