BMW M3 1992 E36 Workshop Manual
Manufacturer: BMW, Model Year: 1992, Model line: M3, Model: BMW M3 1992 E36Pages: 759
Page 141 of 759
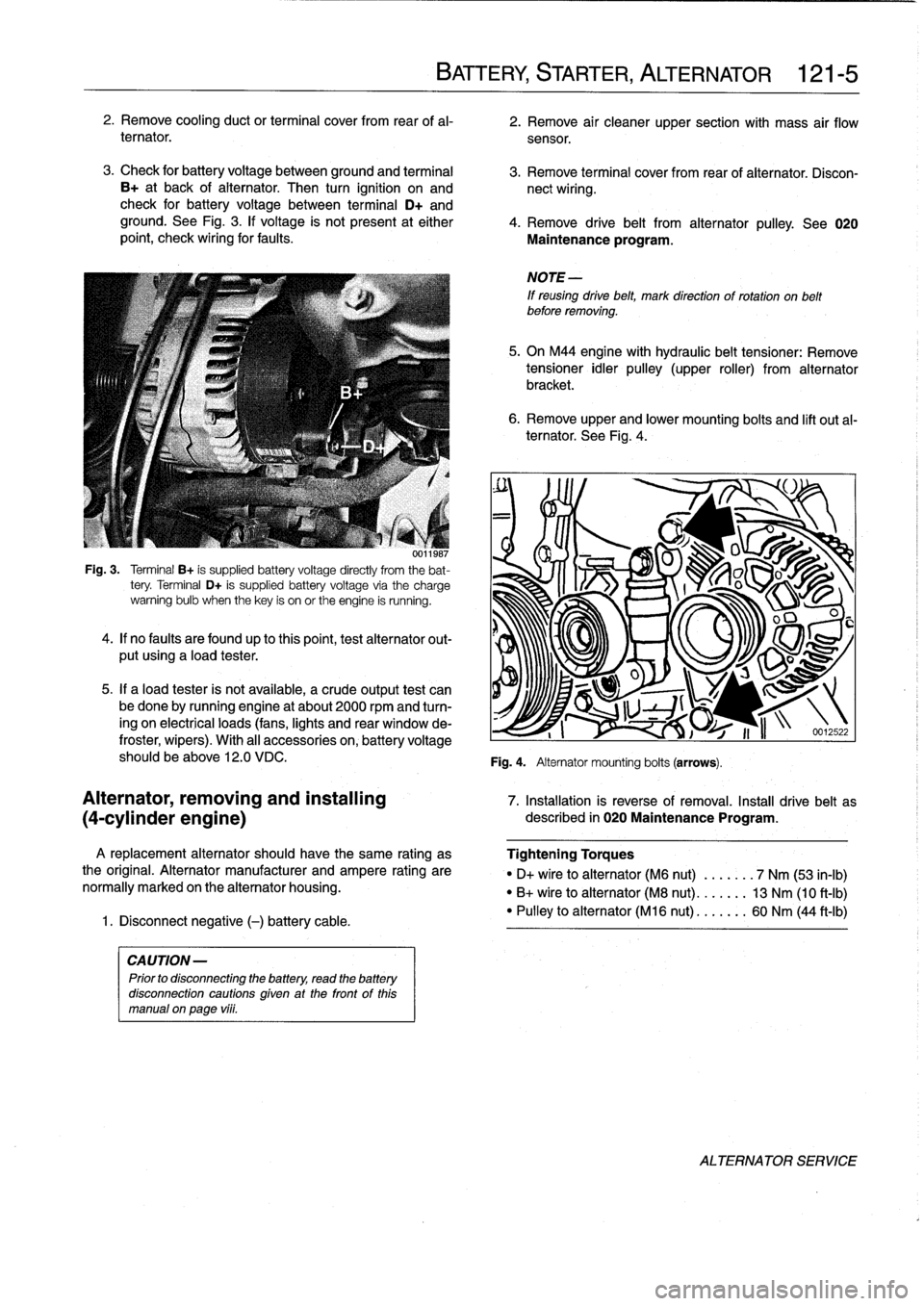
2
.
Remove
cooling
duct
or
terminal
cover
from
rear
of
al-
2
.
Remove
air
cleaner
upper
section
with
mass
air
flow
ternator
.
sensor
.
3
.
Check
for
battery
voltage
between
ground
and
terminal
3
.
Remove
terminal
cover
from
rear
of
alternator
.
Discon
B+
at
back
of
alternator
.
Then
turn
ignition
on
and
nect
wiring
.
check
for
battery
voltage
between
terminal
D+
and
ground
.
See
Fig
.
3
.
lf
voltage
is
not
present
at
either
4
.
Remove
drive
belt
from
alternator
pulley
.
See
020
point,
check
wiring
for
faults
.
Maintenance
program
.
001
¡987
Fig
.
3
.
Terminal
B+
is
supplied
battery
voltage
directly
from
the
bat-
tery
.
Terminal
D+
is
supplied
battery
voltage
via
the
charge
warning
bulb
when
thekey
is
on
or
the
engine
is
running
.
4
.
lf
no
faults
are
foundup
to
thispoint,test
alternator
out-
put
using
a
load
tester
.
5
.
If
a
load
tester
is
not
available,
a
crude
output
test
can
be
done
by
running
engine
at
about
2000
rpmand
turn-
ing
on
electrical
loads
(fans,
lights
and
rear
window
de-
froster,
wipers)
.
With
al¡
accessories
on,
battery
voltage
should
be
above
12
.0
VDC
.
A
replacement
alternator
should
have
the
same
rating
as
the
original
.
Alternator
manufacturer
and
ampere
rating
are
normally
marked
on
the
alternator
housing
.
1
.
Disconnect
negative
(-)
battery
cable
.
CAUTION-
Prior
to
disconnecting
the
battery,
read
the
battery
disconnection
cautions
given
at
the
front
of
this
manual
on
page
vi¡¡
.
BATTERY,
STARTER,
ALTERNATOR
121-
5
6
.
Remove
upper
and
lower
mounting
bolts
and
lift
out
al-
ternator
.
See
Fig
.
4
.
NOTE
-
If
reusing
drive
belt,
mark
direction
of
rotation
on
belt
before
removing
.
5
.
On
M44
engine
with
hydraulic
belt
tensioner
:
Remove
tensioner
idler
pulley
(upper
roller)
from
alternator
bracket
.
Fig
.
4
.
Alternator
mounting
bolts
(arrows)
.
O
u
J
S
v~~
U
I
1
i
n
-12
.22
Alternator,
removing
and
installing
7
.
Installation
is
reverse
of
removal
.
Install
drive
belt
as
(4-cylinder
engine)
described
in
020
Maintenance
Program
.
Tightening
Torques
"
D+
vire
to
alternator
(M6
nut)
.
...
.
.
.
7
Nm
(53
in-lb)
"
B+
wire
to
alternator
(M8
nut)
..
.
.
.
.
.
13
Nm
(10
ft-Ib)
"
Pulley
to
alternator
(M16
nut)
...
..
..
60
Nm
(44
ft-Ib)
ALTERNATOR
SERVICE
Page 142 of 759
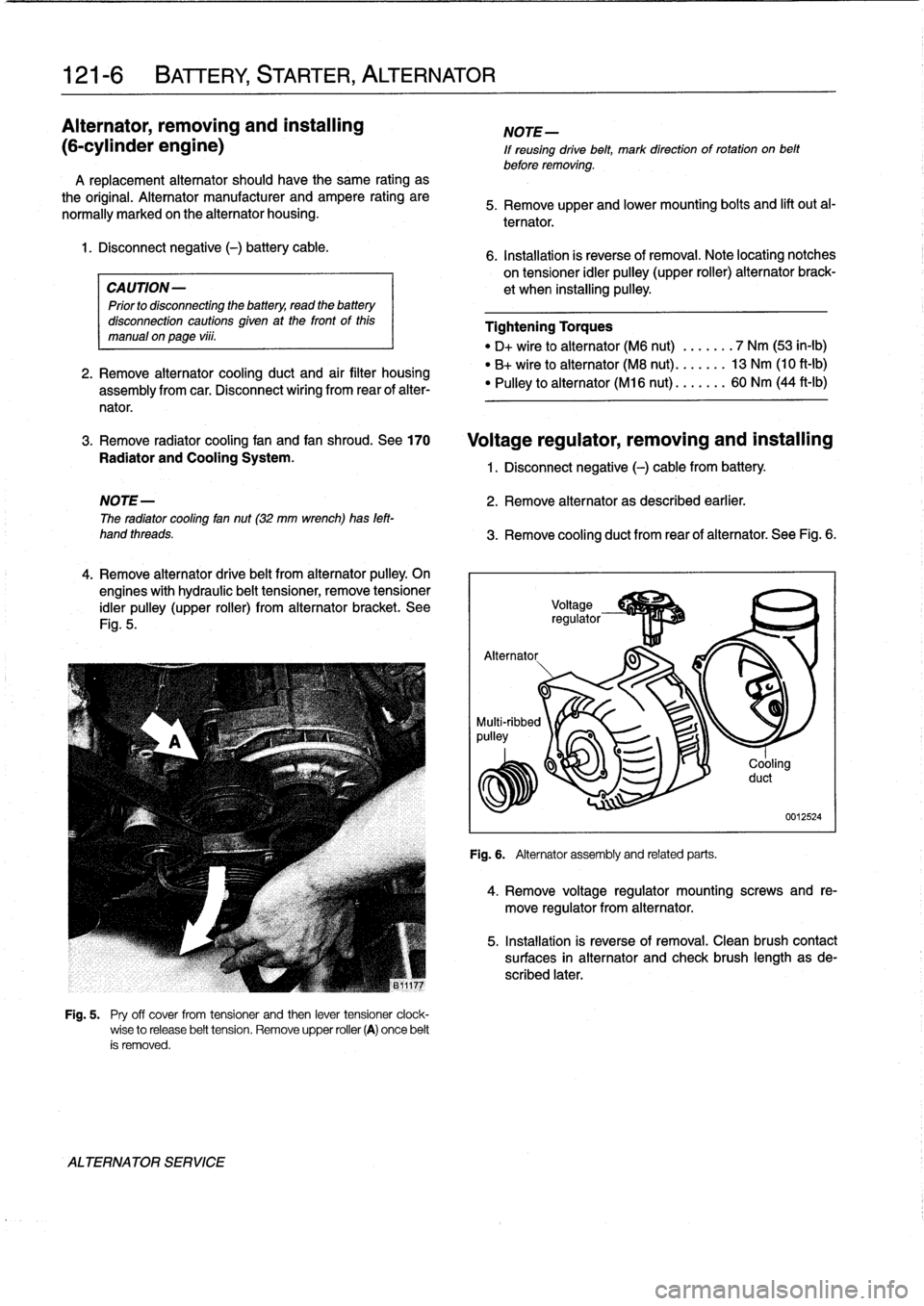
121-
6
BATTERY
STARTER,
ALTERNATOR
Alternator,
removing
and
installing
(6-cylinder
engine)
A
replacement
alternator
should
have
the
same
rating
as
the
original
.
Alternator
manufacturer
and
ampere
rating
are
normally
marked
on
the
alternator
housing
.
1
.
Disconnect
negative
(-)
battery
cable
.
CAUTION-
Prior
to
disconnectiog
the
battery,
read
the
battery
disconnection
cautions
given
at
the
front
of
this
manual
onpage
viii
.
2
.
Remove
alternator
cooling
duct
and
air
filter
housing
assembly
from
car
.
Disconnect
wiring
from
rear
of
alter-
nator
.
3
.
Remove
radiator
cooling
fan
and
fan
shroud
.
See
170
Radiator
and
Cooling
System
.
4
.
Remove
alternator
drive
belt
from
alternator
pulley
.
On
engines
with
hydraulic
belt
tensioner,
remove
tensioner
idler
pulley
(upper
roller)
from
alternator
bracket
.
See
Fig
.
5
.
ALTERNATOR
SERVICE
Fig
.
5
.
Pry
off
cover
from
tensioner
and
then
lever
tensioner
clock-
wise
to
release
belt
tension
.
Remove
upper
roller
(A)
once
belt
ís
removed
.
NOTE-
If
reusing
drive
belt,
mark
direction
of
rotation
on
belt
before
removing
.
5
.
Remove
upper
and
lower
mounting
bolts
and
lift
out
al-
ternator
.
6
.
Installation
is
reverse
of
removal
.
Note
locating
notches
on
tensioner
idler
pulley
(upper
roller)
alternator
brack-
et
when
installing
pulley
.
Tightening
Torques
"
D+
wire
to
alternator
(M6
nut)
.......
7
Nm
(53
in-lb)
"
B+
wireto
alternator
(M8
nut)
.......
13
Nm
(10
ft-Ib)
"
Pulley
to
alternator
(M16
nut)
.......
60
Nm
(44
ft-Ib)
Voltage
regulator,
removing
and
installing
1
.
Disconnect
negative
(-)
cable
from
battery
.
NOTE-
2
.
Remove
alternator
as
described
earlier
.
The
radiator
cooling
fan
nut
(32
mm
wrench)has
left-
hand
threads
.
3
.
Remove
cooling
duct
from
rear
of
alternator
.
See
Fig
.
6
.
Alternator
.
.g-
p~
J
-..
.
Fig
.
6
.
Alternator
assemblyand
related
parts
.
Cooling
duct
0012524
4
.
Remove
voltage
regulator
mounting
screws
and
re-
move
regulator
from
alternator
.
5
.
Installation
is
reverse
of
removal
.
Clean
brush
contact
surfaces
in
alternator
and
check
brush
length
asde-
scribed
later
.
Page 143 of 759
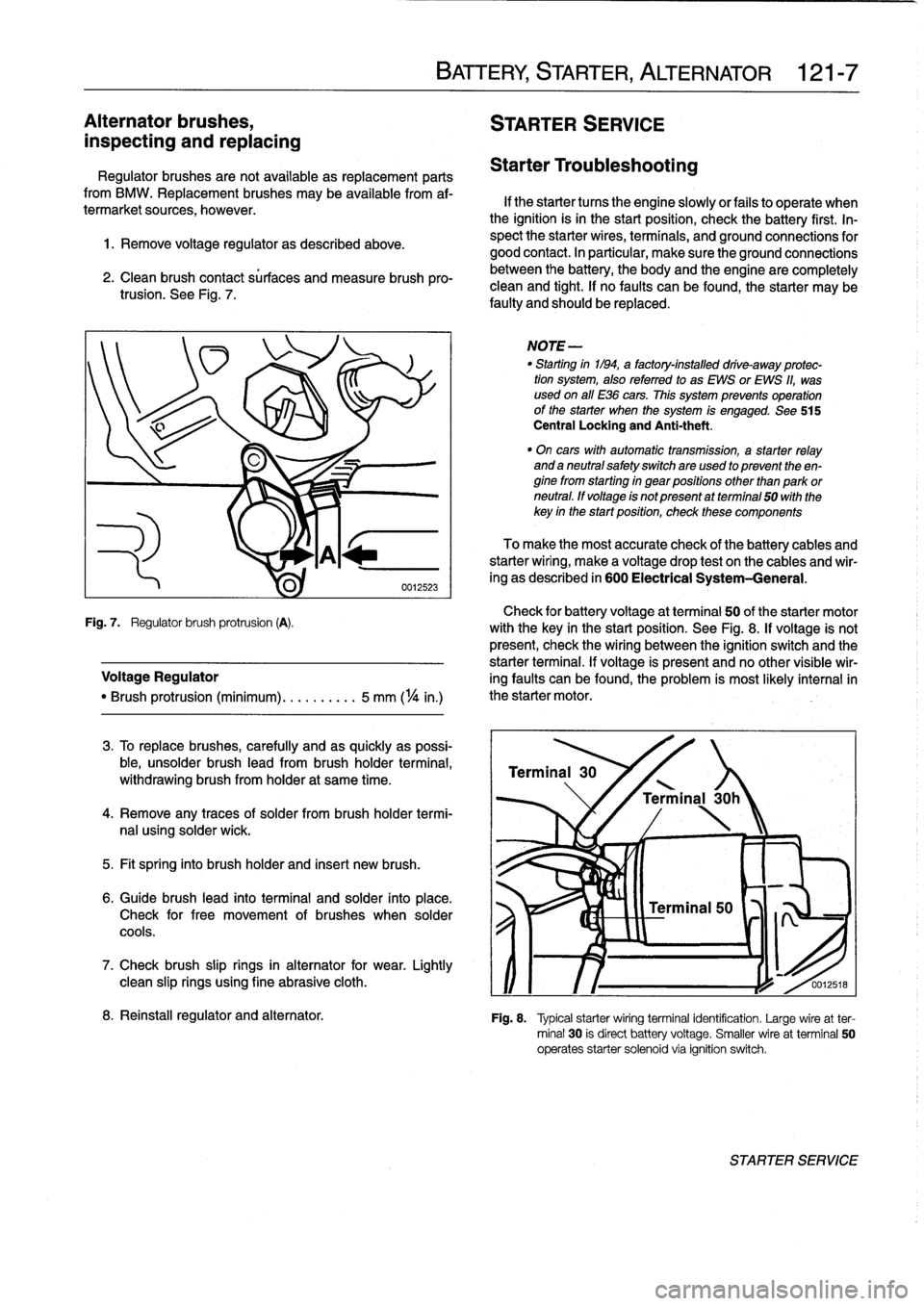
Alternator
brushes,
STARTER
SERVICE
inspecting
and
replacing
Regulator
brushesarenot
available
as
replacement
parts
from
BMW
.
Replacement
brushes
may
be
available
from
af-
termarket
sources,
however
.
1
.
Remove
voltage
regulator
as
described
above
.
2
.
Clean
brush
contact
sürfaces
and
measure
brush
pro-trusion
.
See
Fig
.
7
.
Check
for
battery
voltage
at
terminal
50
of
the
starter
motor
Fig
.
7
.
Regulator
brush
protrusion
(A)
.
with
the
key
in
the
start
position
.
See
Fig
.
8
.
If
voltage
is
not
present,
check
the
wiring
between
the
ignition
switch
and
the
starter
terminal
.
If
voltage
is
present
and
no
other
visible
wir
Voltage
Regulator
ing
faults
can
be
found,
the
problem
is
most
likely
interna¡in
"
Brush
protrusion
(minimum)
.......
.
..
5
mm
(
1
/4
in
.)
the
starter
motor
.
3
.
To
replace
brushes,
carefully
and
as
quickly
as
possi-
ble,
unsolder
brush
lead
from
brush
holder
termina¡,
withdrawing
brush
from
holder
at
same
time
.
4
.
Remove
any
traces
of
solder
frombrush
holder
termi-
nal
using
solder
wick
.
5
.
Fit
spring
into
brush
holder
and
inserí
new
brush
.
6
.
Guide
brush
lead
into
terminal
and
solder
into
place
.
Check
for
free
movement
of
brushes
when
solder
cools
.
7
.
Check
brush
slip
rings
in
alternator
for
wear
.
Lightly
clean
slip
rings
using
fine
abrasive
cloth
.
BATTERY,
STARTER,
ALTERNATOR
121-
7
Starter
Troubleshooting
If
the
starter
tucos
the
engine
slowlyor
fails
to
operate
when
the
ignition
isin
the
start
position,
check
the
battery
first
.
In-
spect
the
starter
wires,
terminals,
and
ground
connections
for
good
contact
.
In
particular,
make
sure
the
ground
connections
between
the
battery,
the
body
and
the
engine
are
completely
clean
and
tight
.
If
no
faults
can
be
found,
the
starter
may
be
faulty
and
should
be
replaced
.
NOTE
-
"
Starting
in1194,
a
factory-installed
drive-away
protec-
tion
system,
alsoreferred
to
as
EWS
or
EWS
11,
was
used
on
all
E36
cars
.
This
system
prevenís
operation
of
the
starter
when
the
system
is
engaged
.
See
515
Central
Locking
and
Anti-theft
.
"
On
cars
with
automatic
transmission,
a
starter
relay
and
a
neutral
safetyswitchare
used
to
present
theen-
ginefrom
starting
in
gear
positions
other
than
park
or
neutral
.
ff
voltage
is
not
present
atterminal
50
with
the
key
in
the
startposition,
check
these
components
To
make
the
most
accurate
check
of
the
battery
cables
and
starterwiring,
make
a
voltage
drop
test
on
the
cables
and
wir-
ing
as
described
in
600
Electrical
System-General
.
Terminal
30
'
\
/
Terminal
30h
0012518
8
.
Reinstall
regulator
and
alternator
.
Fig
.
8
.
Typical
starterwiring
terminal
identification
.
Large
wireat
ter-
minal
30
is
direct
battery
voltage
.
Smaller
wire
at
terminal
50
operates
starter
solenoid
via
ignition
switch
.
STARTER
SERVICE
Page 144 of 759
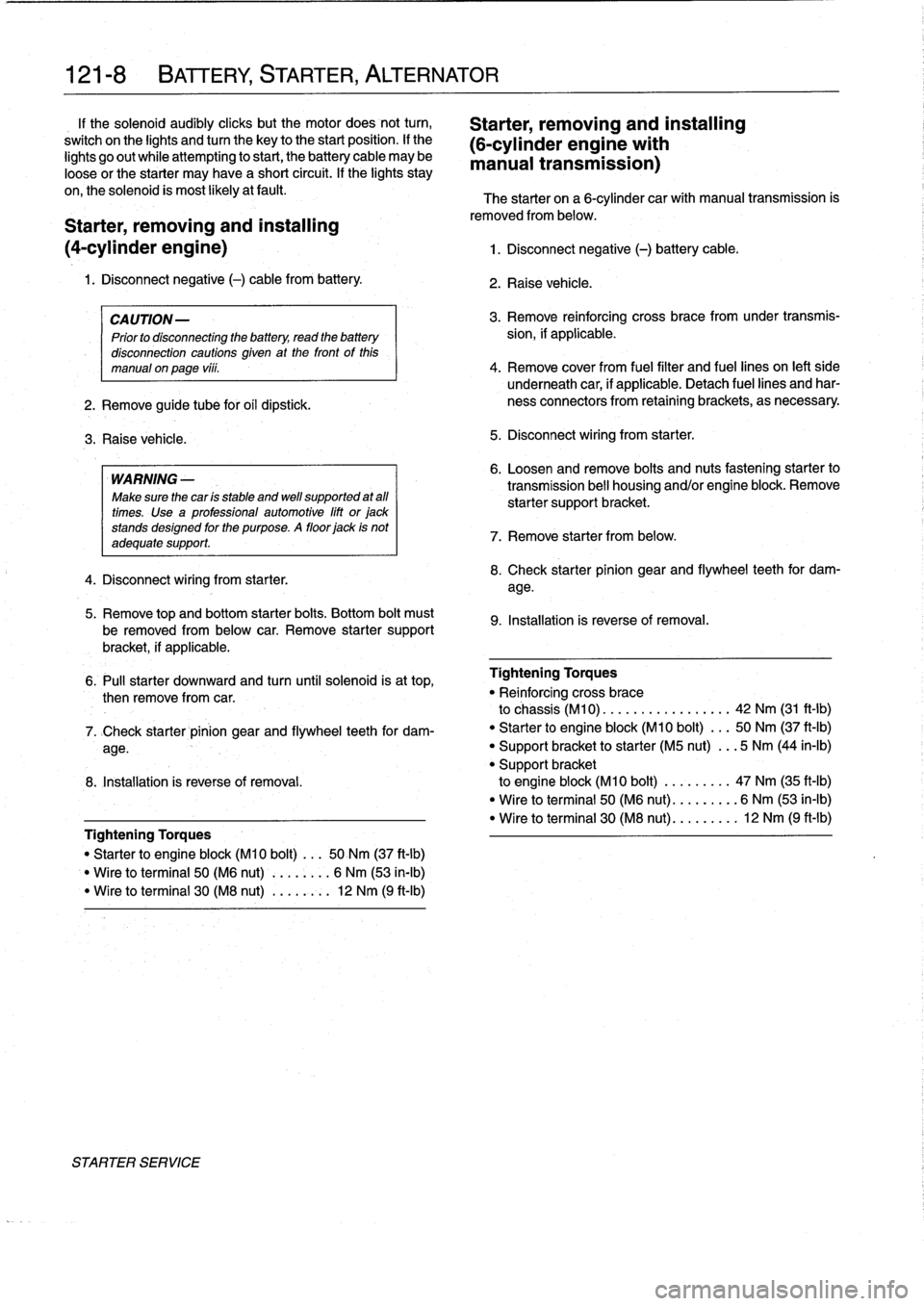
121-
8
BATTERY,
STARTER,
ALTERNATOR
1f
the
solenoid
audibly
cliicks
but
the
motor
does
not
turn,
Starter,
removing
and
installing
switch
on
the
lights
andtum
the
key
to
the
start
position
.
lf
the
(6-cylinder
engine
with
lights
go
out
while
attempting
to
start,
the
battery
cable
may
be
manual
transmission)
loose
or
the
starter
may
have
a
short
circuit
.
If
the
lights
stay
on,the
solenoid
is
most
likely
atfault
.
The
starter
on
a
6-cylinder
car
with
manual
transmission
is
Starter,
removing
and
installing
(4-cylinder
engine)
1
.
Disconnect
negative
(-)
battery
cable
.
1
.
Disconnect
negative
(-)
cable
from
battery
.
CAUTION-
Prior
to
disconnecting
the
battery,
read
the
battery
disconnection
cautions
given
at
the
front
of
this
manual
on
page
viii
.
2
.
Remove
guide
tube
for
oil
dipstick
.
3
.
Raise
vehicle
.
WARNING
-
Make
sure
the
car
ís
stable
and
wefl
supported
at
all
times
.
Use
a
professional
automotive
lift
or
jack
stands
designed
forthe
purpose
.
A
floor
jack
is
not
adequate
support
.
4
.
Disconnect
wiring
from
starter
.
5
.
Remove
top
and
bottom
starter
bolts
.
Bottom
bolt
must
be
removed
from
below
car
.
Remove
starter
support
bracket,
if
applicable
.
removed
from
below
.
2
.
Raise
vehicle
.
3
.
Remove
reinforcing
cross
bracefromunder
transmís-
sion,
if
applicable
.
4
.
Remove
cover
from
fuel
filter
and
fuel
lines
on
left
side
underneath
car,
if
applicable
.
Detach
fuel
lines
and
har-
ness
connectors
from
retainingbrackets,
as
necessary
5
.
Disconnect
wiring
from
starter
.
6
.
Loosen
andremove
bolts
and
nuts
fastening
starter
to
transmission
bell
housing
and/or
engine
block
.
Remove
starter
supportbracket
.
7
.
Remove
starter
from
below
.
8
.
Check
starter
pinion
gear
and
flywheel
teeth
for
dam-
age
.
9
.
Installation
is
reverse
of
removal
.
6
.
Pull
starter
downward
and
turn
until
solenoid
is
at
top,
Tightening
Torques
then
remove
from
car
.
"
Re¡
nforcing
cross
brace
to
chassis
(M10)
..
...............
42
Nm
(31
ft-Ib)
7
.
>Check
starter
pinion
gear
and
flywheel
teeth
for
dam-
"
Starter
to
engine
block
(M10
bolt)
...
50
Nm
(37
ft-Ib)
age
.
"
Support
bracket
to
starter
(M5
nut)
...
5
Nm
(44
in-lb)
"
Support
bracket
8
.
Installation
is
reverse
of
removal
.
to
engine
block
(M10
bolt)
.........
47
Nm
(35
ft-Ib)
"
Wire
to
terminal
50
(M6
nut)
.........
6
Nm
(53
ín-Ib)
"
Wire
to
terminal
30
(M8
nut)
.........
12
Nm
(9
ft-lb)
Tightening
Torques
"
Starter
to
engine
block
(M10
bolt)
...
50
Nm
(37
ft-lb)
Wire
to
terminal
50
(M6
nut)
........
6
Nm
(53
in-lb)
"
Wire
toterminal
30
(M8
nut)
...
,
..:.
12
Nm
(9
ft-Ib)
STARTER
SERVICE
Page 145 of 759
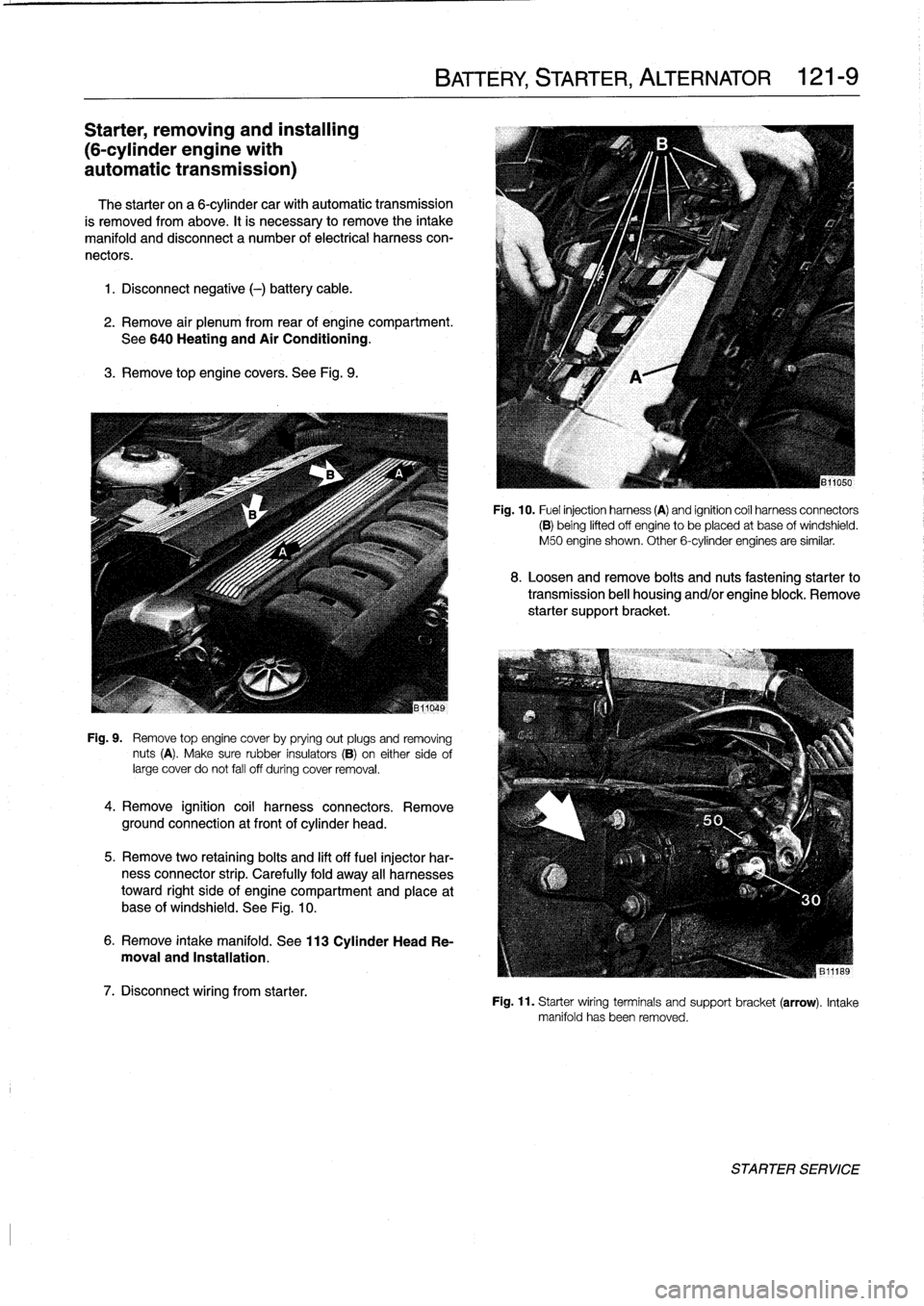
Starter,
removing
and
installing
(6-cylinder
engine
with
automatic
transmission)
The
starter
on
a
6-cylinder
car
with
automatic
transmission
ís
removed
from
above
.
It
is
necessary
to
remove
the
íntake
manifold
and
disconnect
a
number
of
electrical
harness
con-
nectors
.
1
.
Disconnect
negative
(-)
battery
cable
.
2
.
Remove
air
plenum
from
rear
of
engine
compartment
.
See640
Heating
and
Air
Conditioning
.
3
.
Remove
top
enginecovers
.
See
Fig
.
9
.
Fig
.
9
.
Remove
top
engine
cover
by
prying
out
plugs
and
removing
nuts
(A)
.
Make
sure
rubber
insulators
(B)
on
either
sideof
large
cover
do
not
fall
off
during
cover
removal
.
4
.
Remove
ignition
coil
harness
connectors
.
Remove
ground
connection
at
front
of
cylinder
head
.
5
.
Remove
two
retaining
bolts
and
lift
off
fuel
injector
har-
ness
connector
strip
.
Carefully
fold
away
all
harnesses
toward
right
side
of
engine
compartment
and
place
at
base
of
windshield
.
See
Fig
.
10
.
6
.
Remove
intake
manifold
.
See
113
Cylinder
Head
Re-
moval
and
Installation
.
7
.
Disconnect
wiring
from
starter
.
BATTERY,
STARTER,
ALTERNATOR
121-
9
Fig
.
10
.
Fuel
injection
harness
(A)
and
ignition
coíl
harness
connectors
(B)
being
lifted
off
engine
to
be
placed
at
base
ofwindshield
.
M50
engine
shown
.
Other
6-cylinder
engines
are
similar
.
8
.
Loosen
and
remove
bolts
and
nuts
fastening
starter
to
transmission
bell
housing
and/or
engine
block
.
Remove
starter
support
bracket
.
Fig
.
11
.
Starter
wiring
terminals
and
support
bracket(arrow)
.
Intake
manifold
has
been
removed
.
STARTER
SERVICE
Page 146 of 759
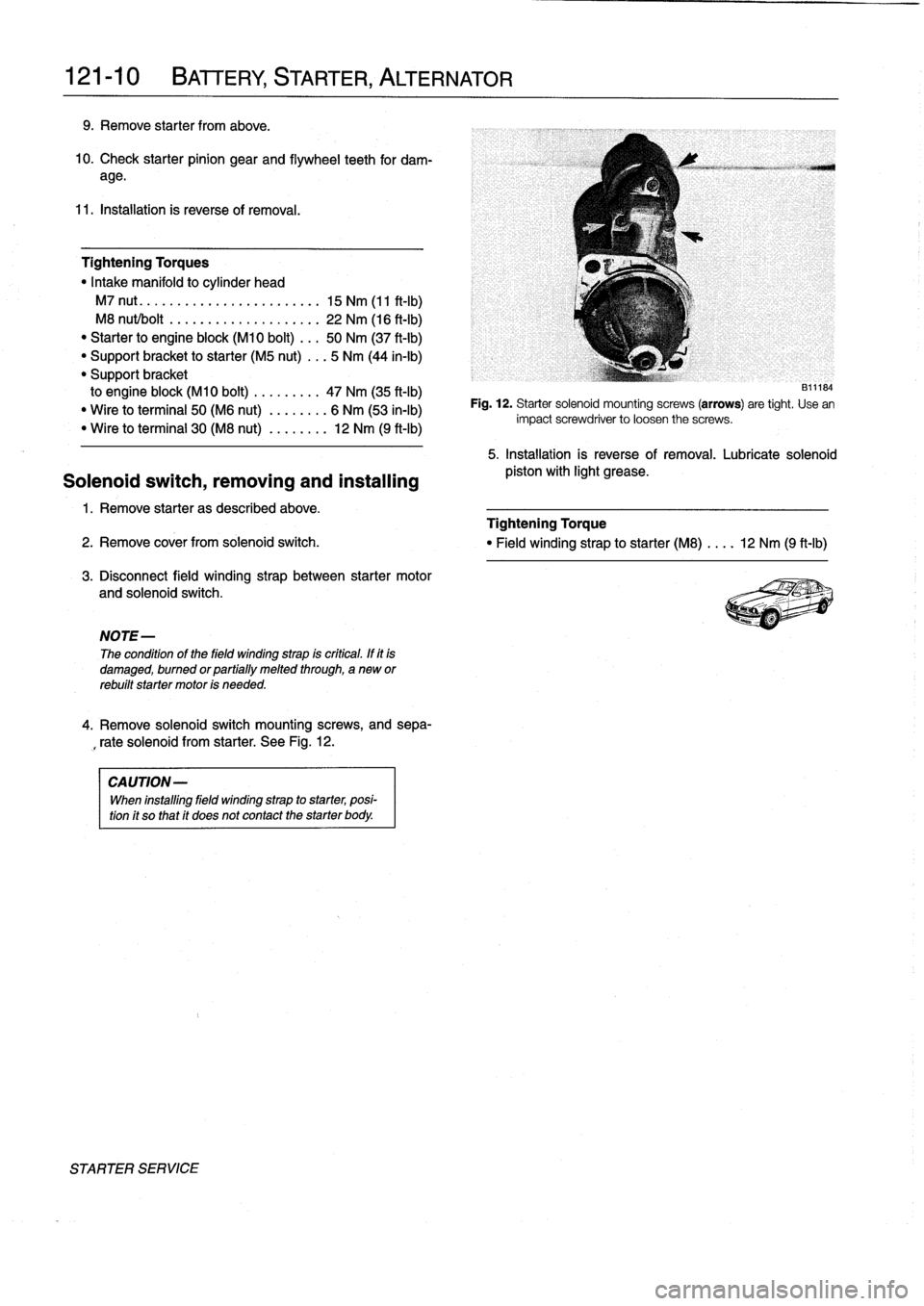
121-1
O
BATTERY,
STARTER,
ALTERNATOR
9
.
Remove
starter
from
above
.
10
.
Check
starter
pinion
gear
and
flywheel
teeth
for
dam-
age
.
11
.
Installation
is
reverse
of
removal
.
Tightening
Torques
"
tntakemanifold
to
cylinder
head
M7
nut
...
.
................
...
.
15
Nm
(11
ft-Ib)
M8
nut/bolt
.............
.
.
..
...
22
Nm
(16
ft-Ib)
"
Starter
to
engine
block
(M10
bolt)
...
50
Nm
(37
ft-Ib)
"
Support
bracket
to
starter
(M5
nut)
...
5
Nm
(44
in-lb)
"
Support
bracket
to
engine
block
(M10
bolt)
.
.
..
..
...
47
Nm
(35
ft-Ib)
"
Wire
toterminal
50
(M6
nut)
.
..
.....
6
Nm
(53
in-lb)
"
Wire
toterminal
30
(M8
nut)
...
.....
12
Nm
(9
ft-Ib)
Solenoid
switch,
removing
and
installing
1
.
Remove
starter
as
described
above
.
Tightening
Torque
2
.
Remove
cover
from
solenoid
switch
.
"
Field
winding
strap
to
starter
(M8)
...
.
12
Nm
(9
ft-Ib)
3
.
Disconnect
fieid
winding
strap
between
starter
motor
and
solenoid
switch
.
NOTE-
The
condition
of
the
field
winding
strap
is
critical
.
If
it
is
damaged,
bumed
or
partially
melted
through,
a
new
or
rebuilt
starter
motor
is
needed
.
4
.
Remove
solenoidswitch
mounting
screws,
and
sepa-
,
rate
solenoid
from
starter
.
See
Fig
.
12
.
CAUTION-
When
installing
fieid
winding
strap
to
starter,
posi-
tion
it
so
that
it
does
not
contact
the
starter
body
.
STARTER
SERVICE
131~184
Fig
.
12
.
Starter
solenoid
mounting
screws
(arrows)
are
tight
.
Use
en
impact
screwdriver
to
loosen
the
screws
.
5
.
Installation
is
reverse
of
removal
.
Lubricate
solenoid
pistos
with
light
grease
.
Page 147 of 759
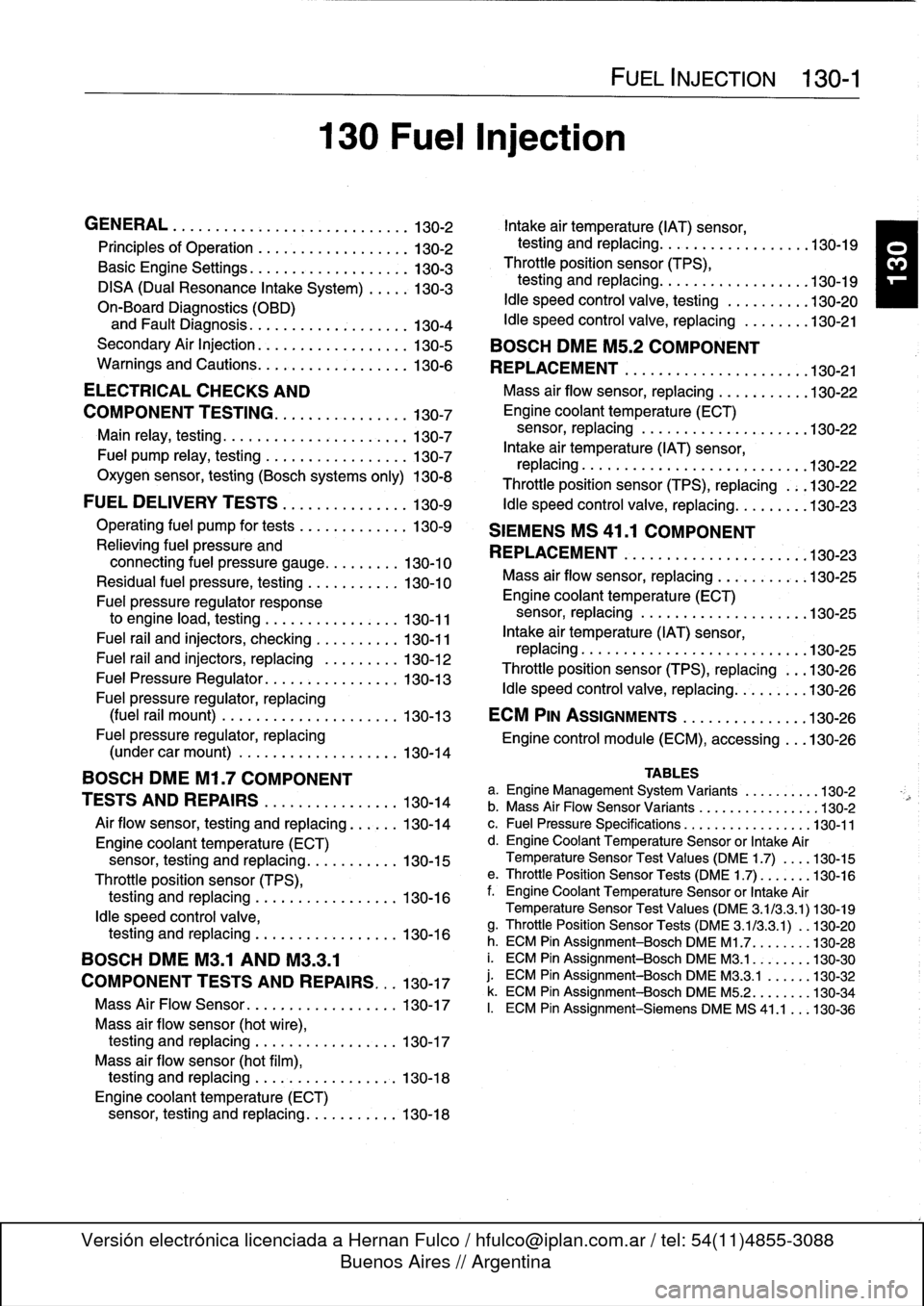
GENERAL
.
.
.
.
.
.
.
.
.
...
.
.
.
.
.
.
.
.........
130-2
Intake
air
temperature
(IAT)
sensor,
Principles
of
Operatinn
.
.
.
.
.
.
.
.
.
.........
130-2
testing
and
replacing
...
.
...
.
.
.
.......
.
130-19
Basic
Engine
Settings
.
.
.
.
.
.
.
.
.
.
.
.
.
.
...
:
.
130-3
Throttle
position
sensor
(TPS),
DISA
(Dual
Resonance
Intake
System)
.
.
.
.
.
130-3
testing
and
replacing
...
.
...
.
.
.
.
.
...
.
.
.130-19
On-Board
Diagnostics
(OBD)
Idle
speed
control
valve,
testing
.
.
.
.
.
.
.
.
.
.
130-20
and
Fault
Diagnosis
.
.
....
.
......
.
.
.
...
130-4
Idle
speed
control
valve,
replacing
.
.
.
.
.
.
..
130-21
SecondaryAir
Injection
.
.
.....
.
.........
.
130-5
BOSCH
DME
M5
.2
COMPONENT
Warnings
and
Cautions
.
.
...
.
.
.
.........
.
130-6
REPLACEMENT
.....
.
......
.
....
.
.
.
..
130-21
ELECTRICAL
CHECKSAND
Mass
air
flow
sensor,
replacing
.
.
....
.
....
130-22
COMPONENT
TESTING
.
.
.
.
.
.
.
.
...
.
.
.
.
.
130-7
Engine
coolant
temperature
(ECT)
Main
sensor,
replacing
..
.
.
.
.
.
.
.
.
.
.
.
.
.
.
.
.
.
.
130-22
rela
y
testing
130
-7
,...
.
.
.
.
.
.
.
.
.
...
.
.
.
.
.
.
.
Intake
air
temperature
(IAT)
sensor,
Fuel
pump
relay,
testing
.
.
.
.
.
.
.
...
.
.
.
.
.
.
.
130-7
rep
lacin
.
.
.
.
.
.
.
.
.
.
.g
.
.
.
.
.
.
.
...
.
.
.
..
.130-22
Oxygen
sensor,
testing
(Boschsystems
only)
130-8
Throttle
poson
sensor
(TPS)
replacing
13022
,
..
.-
FUEL
DELIVERY
TESTS
...
.
....
.
.
.
...
.
130-9
Idle
speed
control
valve,
replacing
...
.
....
.130-23
Operating
fuel
pump
for
tests
.
.
.......
.
...
130-9
SIEMENS
MS
41
.1
COMPONENT
Relieving
fuel
pressure
and
REPLACEMENT
.
...
.
.
.
.
.
.......
.
....
.130-23
connecting
fuel
pressure
gauge
......
.
..
130-10
Residual
fuel
pressure,
testing
.
.....
.
.
.
.
.
130-10
Mass
air
flow
sensor,
replacing
.
.......
.
.
.130-25
Fuel
pressure
regulator
response
Engine
coolant
temperature
(ECT)
to
engine
load,
testing
.
.
.
.
.
.
.
.
.
.
.
.
.
.
.
.
130-11
sensor,
replacing
.....
.
.
.
.
.
.........
.130-25
Fuel
rail
and
injectors,
checking
...
.
.
.
.
.
.
.
130-11
Intake
air
temperature
(IAT)
sensor,
replacing
.
.
.
.
.
.....
.
.
.
.
.
.
.
.......
.
.
.130-25
Fuel
rail
and
injectors,
replacing
..
.
.
.
.
.
.
.
130-12
Throttleposition
sensor
(TPS),
replacing
.
.
.
130-26
Fuel
PressureRegulator
.........
.
.
.
.
.
.
.
130-13
Idle
s
eed
control
valve,
re
lacin
130-26
Fuel
pressure
regulatorreplacing
p
p
g
.'''...
.
'
,
(fuel
rail
mount)
...
.
.
.
.
.
.............
130-13
ECM
PIN
ASSIGNMENTS
.............
.
.
130-26
Fuel
pressure
regulator,
replacing
Engine
control
module
(ECM),
accessing
...
130-26
(undercar
mount)
.
.
.
.
.
.
.
.
.........
.
.
130-14
BOSCH
DME
M1
.7
COMPONENT
TESTS
AND
REPAIRS
.
.
.
.
.
...
.
.
.
.
.
.
.
.
130-14
Air
flow
sensor,
testing
and
replacing
.
.
.
.
.
.
130-14
Engine
coolant
temperature
(ECT)
sensor,
testing
and
replacing
...
.
.
.
.
.
.
.
.
130-15
Throttle
position
sensor
(TPS),
testing
and
replacing
.
..........
.
.....
130-16
Idle
speed
control
valve,
testing
and
replacing
.
.
.
.
.
............
130-16
BOSCH
DME
M3
.1
AND
M33
.1
COMPONENT
TESTS
AND
REPAIRS
.
.
.
130-17
Mass
Air
Flow
Sensor
.
.
.
.
.
.
.
.
.....
.
.
.
.
.130-17
Mass
air
flow
sensor
(hotwire),testing
and
replacing
.
.
.
.
.
.....
.
.
.
.
.
.
.
130-17
Mass
air
flow
sensor
(hot
film),
testíng
and
replacing
.
.
.
.....
.
.
.
.
.
.
.
.
.
130-18
Engine
coolant
temperature
(ECT)
sensor,
testing
and
replacing
..
.
.
.
.
.
...
.
130-18
130
Fuel
i
n
jection
FUEL
INJECTION
130-1
TABLES
a
.
Engine
Management
System
Variants
.........
.130-2
b
.
Mass
Air
Flow
Sensor
Variants
..
.
..
..........
.130-2
c
.
Fuel
Pressure
Specifications
..
.
.
...
..........
130-11
d
.
Engine
Coolant
Temperature
Sensor
or
Intake
Air
Temperature
Sensor
Test
Values
(DME
1
.7)
...
.
130-15
e
.
ThrottlePosition
Sensor
Tests
(DME
1
.7)
......
.130-16
f
.
Engine
Coolant
Temperature
Sensor
or
Intake
Air
Temperature
Sensor
Test
Values
(DME
3
.1/3
.3
.1)130-19
g
.
Throttle
Position
Sensor
Tests
(DME
3
.1/3.3
.1)
.
.130-20
h
.
ECM
Pin
Assignment-Bosch
DME
M1
.7
....
.
..
.130-28
i.
ECM
Pin
Assignment-Bosch
DME
M3
.1
.......
.130-30
j
.
ECM
Pin
Assignment-Bosch
DME
M3
.3
.1
.....
.130-32
k
.
ECM
Pin
Assignment-Bosch
DME
M5
.2
.......
.
130-34
I.
ECM
Pin
Assignment-Siemens
DME
MS
41
.1
..
.
130-36
Page 148 of 759
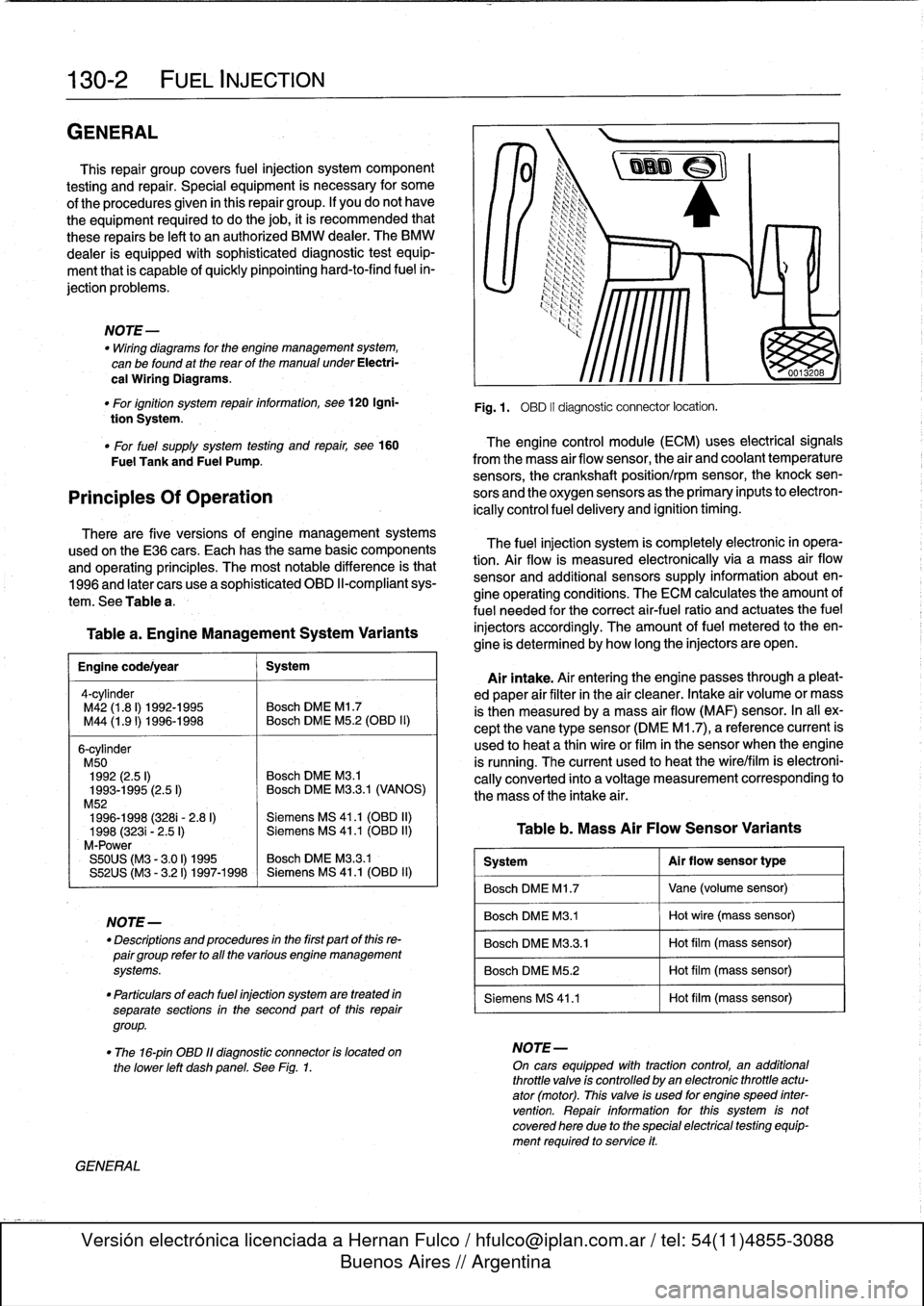
130-2
FUEL
INJECTION
GENERAL
This
repair
group
covers
fuel
injection
system
component
testing
and
repair
.
Special
equipment
is
necessary
for
some
of
the
procedures
given
in
this
repair
group
.
If
you
do
not
have
the
equipment
required
to
do
the
job,
it
is
recommended
that
these
repairs
be
left
to
an
authorized
BMW
dealer
.
The
BMW
dealer
is
equipped
with
sophisticated
diagnostic
test
equip-
ment
that
is
capable
of
quicklypinpointing
hard-to-find
fuel
in-
jection
problems
.
NOTE-
"
Wiring
diagrams
for
the
engine
management
system,
can
be
found
at
the
rear
of
the
manual
under
Electri-
cal
Wiring
Diagrams
.
"
For
ignition
system
repairinformation,
see120
Igni-
tion
System
.
"
For
fuel
supply
system
testing
and
repair,
see160
The
engine
control
module
(ECM)
uses
electrical
signals
Fuel
Tank
and
Fuel
Pump
.
from
the
mass
air
flow
sensor,
the
air
and
coolant
temperature
sensors,
the
crankshaft
position/rpm
sensor,
the
knock
sen
Principies
Of
Operation
sors
and
the
oxygen
sensorsas
the
primary
inputs
to
electron-
ically
control
fuel
delivery
and
ignition
timing
.
There
are
five
versions
of
engine
management
systems
usedon
the
E36
cars
.
Each
has
the
same
basic
components
and
operating
principles
.
The
most
notable
difference
is
that
1996
and
later
cars
use
a
sophisticated
OBD
II-compliant
sys-
tem
.
See
Table
a
.
Table
a
.
Engine
Management
System
Variants
Engine
code/year
1
System
4-cy1inder
M42
(1
.8
I)
1992-1995
Bosch
DME
Ml
.7
M44
(1
.91)
1996-1998
~
Bosch
DME
M5
.2
(OBD
II)
6-cylinder
M50
1992
(2.5
I)
Bosch
DME
M3
.1
1993-1995
(2.5
I)
Bosch
DME
M3
.3.1
(VANOS)
M52
1996-1998
(3281-
2
.8
I)
Siemens
MS
41
.1
(OBD
II)
1998
(3231
-
2
.5
I)
Siemens
MS
41
.1
(OBD
II)
M-Power
S50US
(M3
-
3
.01)
1995
Bosch
DME
M3
.3
.1
S52US
(M3
-
3
.21)
1997-1998
Siemens
MS
41
.1
(0131)
11)
NOTE-
-
Descriptions
and
procedures
in
the
first
partof
this
re-
pairgroup
refer
to
all
the
various
engine
management
systems
.
"
Particulars
of
each
fuel
injection
system
are
treated
in
separate
sections
in
the
second
part
of
this
repair
group
.
GENERAL
Fig
.1
.
OBD
II
diagnostic
connector
locatíon
.
The
fuel
injection
system
is
completely
electronic
in
opera-
tion
.
Air
flow
is
measured
electronically
via
a
mass
air
flow
sensor
and
additional
sensors
supply
information
about
en-
gine
operating
conditions
.
The
ECM
calculates
the
amount
of
fuel
needed
for
the
correct
air-fuel
ratio
and
actuates
the
fuel
injectors
accordingly
.
The
amount
offuel
metered
to
theen-
gine
is
determined
by
how
long
the
injectors
are
open
.
Airintake
.
Air
entering
the
engine
passes
through
a
pleat-
ed
paper
air
filter
in
the
air
cleaner
.
Intake
air
volume
or
mass
is
then
measured
bya
mass
air
flow
(MAF)
sensor
.
In
al¡
ex-
cept
the
vane
type
sensor
(DME
M1
.7),
a
reference
current
is
used
to
heat
a
thin
wireor
film
in
the
sensor
when
the
engine
is
running
.
The
current
used
to
heat
the
wire/film
is
electroni-
cally
converted
into
a
voltage
measurement
corresponding
to
the
mass
of
the
intake
air
.
Table
b
.
Mass
Air
Flow
Sensor
Variants
System
Al
r
flow
sensor
type
Bosch
DME
M1
.7
Vane
(volume
sensor)
Bosch
DME
M3
.1
Hot
wire
(mass
sensor)
Bosch
DME
M3
.3
.1
Hot
film
(mass
sensor)
Bosch
DME
M5
.2
Hot
film
(mass
sensor)
Siemens
MS
41
.1
Hot
film
(mass
sensor)
"
The
16-pin
OBD
11
diagnostic
connector
is
located
on
NOTE-
the
lower
left
dashpanel
.
See
Fig
.
1
.
On
cars
equipped
wíth
tractioncontrol,
an
additional
throttle
valve
is
controlled
by
an
electronic
throttle
actu-
ator
(motor)
.
This
valve
is
used
for
engine
speed
inter
vention
.
Repair
information
forthis
system
is
notcovered
here
due
to
the
special
electrical
testing
equip-
ment
required
to
service
it
.
Page 149 of 759
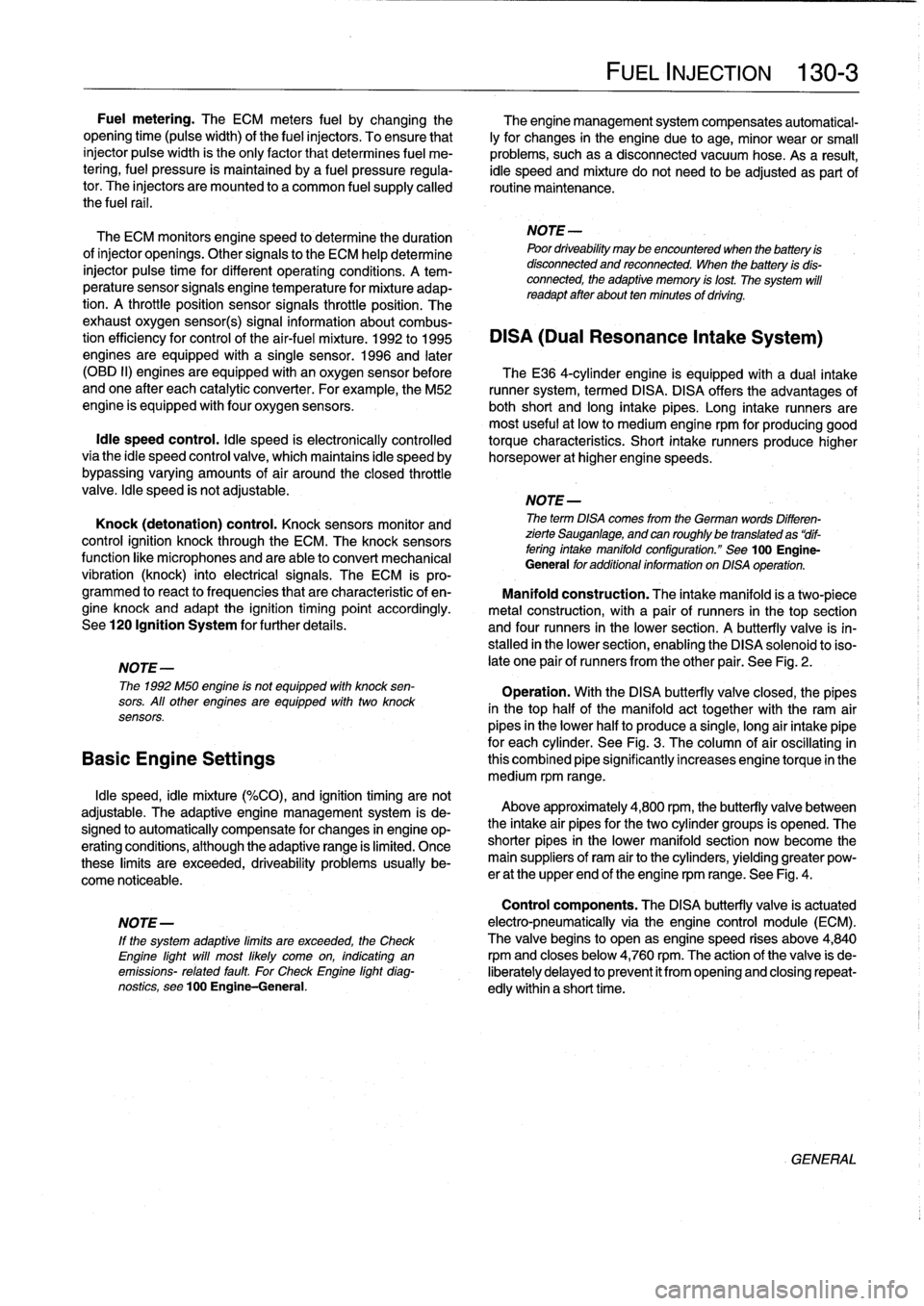
FUEL
INJECTION
130-
3
Fuel
metering
.
The
ECM
meters
fuel
bychanging
the
The
engine
management
system
compensates
automatical-
opening
time
(pulsewidth)
of
the
fuel
injectors
.
To
ensure
that
ly
for
changes
in
the
engine
due
to
age,
minor
wear
or
small
injector
pulsewídth
is
the
only
factor
that
determines
fuel
me-
problems,
such
as
a
disconnected
vacuum
hose
.
Asa
result,
tering,fuel
pressure
is
maintained
bya
fuel
pressure
regula-
idle
speed
and
mixture
do
not
need
lo
be
adjustedas
partof
tor
.
The
injectors
are
mounted
lo
a
common
fuel
supply
called
routine
maintenance
.
the
fuel
rail
.
The
ECM
monitors
engine
speed
to
determine
the
duration
NOTE-
ofinjector
openings
.
Other
signals
to
the
ECM
help
determine
Poordriveabilitymaybe
encountered
when
the
batteryis
injector
pulse
time
for
different
operating
conditions
.
A
tem-
disconnected
and
reconnected
.
when
the
battery
is
dis-
connected,
the
adaptive
memory
is
lost
The
system
will
perature
sensor
signals
engine
temperature
for
mixture
adap-
readaptafterabout
ten
minutes
of
drfving
.
tion
.
A
throttle
position
sensor
signals
throttle
position
.
The
exhaust
oxygen
sensor(s)
signal
information
about
combus-
tion
efficiency
for
control
of
the
air-fuel
mixture
.
1992
to
1995
DISA
(Dual
Resonance
Intake
System)
engines
are
equipped
with
a
single
sensor
.
1996
and
later
(OBD
II)
engines
are
equipped
with
an
oxygen
sensor
before
TheE36
4-cylinder
engine
is
equipped
with
a
dual
intake
andone
after
each
catalytic
converter
.
Forexample,the
M52
runner
system,
termed
DISA
.
DISA
offers
the
advantages
of
engine
is
equipped
withfour
oxygen
sensors
.
both
short
and
long
intake
pipes
.
Long
intake
runners
are
most
useful
at
low
to
medium
engine
rpm
for
producing
good
Idle
speed
control
.
ldle
speed
is
electronically
controlled
torque
characteristics
.
Short
intake
runners
produce
hígherviathe
idle
speed
control
valve,
which
maintains
idle
speed
by
horsepower
at
hígher
engine
speeds
.
bypassing
varying
amounts
of
air
around
theclosed
throttle
valve
.
Idle
speed
is
not
adjustable
.
NOTE-
Knock
(detonation)
control
.
Knock
sensors
monitor
and
The
term
DISA
comes
from
the
German
words
Differen-
control
ignition
knock
through
the
ECM
.
The
knock
sensors
zierte
Sauganlage,
and
can
roughlybe
translated
as
"dif-
fering
intake
manifold
configuration
."
See
100
Engine-
function
like
microphones
and
are
able
to
convert
mechanical
General
foradditional
information
on
DISA
operation
.
vibration
(knock)
into
electrical
signals
.
The
ECM
is
pro-
grammed
to
react
to
frequencies
that
are
characteristic
of
en-
Manifold
construction
:
The
intake
manifold
is
a
two-piece
gine
knock
and
adapt
the
ignition
timing
point
accordingly
.
metal
construction,
with
a
pair
of
runners
in
thetop
section
See120
Ignition
System
for
further
details
.
and
four
runners
in
the
lower
section
.
A
butterfly
valve
is
in-
stalled
in
the
lower
section,
enabling
the
DISA
solenoid
toiso-
NOTE-
late
one
pair
of
runners
from
the
other
pair
.
See
Fig
.
2
.
The
1992
M50
engine
is
not
equipped
with
knock
sen-
Operation
.
With
the
DISA
butterfly
valve
closed,
the
pipes
sors
.
All
other
engines
are
equipped
with
two
knock
in
thetop
half
of
the
manifold
act
together
with
the
ram
air
sensors
.
pipes
in
the
lower
halfto
producea
single,
long
air
intake
pipe
for
each
cylinder
.
See
Fig
.
3
.
The
column
of
aír
oscíllating
in
Basic
Engine
Settings
this
combined
pipe
significantly
increases
engine
torque
in
the
medium
rpm
range
.
Idle
speed,
idle
mixture
(%CO),
and
ignition
timing
arenot
adjustable
.
The
adaptive
engine
management
system
is
de-
signed
to
automatically
compensate
for
changes
in
engine
op-
eratingconditions,
although
the
adaptive
range
is
limited
.
Once
these
limits
are
exceeded,
driveability
problems
usually
be-
come
noticeable
.
Above
approximately
4,800
rpm,
the
butterfly
valve
between
the
intake
air
pipes
for
the
two
cylinder
groups
is
opened
.
The
shorter
pipes
in
the
lower
manifold
section
now
become
the
main
suppliers
of
ram
air
to
the
cylinders,yielding
greater
pow-
er
at
the
upper
end
of
the
engine
rpm
range
.
See
Fig
.
4
.
Control
components
.
The
DISA
butterfly
valve
is
actuated
NOTE-
electro-pneumatically
via
the
engine
control
module
(ECM)
.
lf
the
system
adaptive
limits
are
exceeded,
the
Check
The
valve
begins
to
open
as
engine
speed
rises
aboye
4,840
Engine
light
will
most
likely
come
on,
indicating
an
rpmand
closes
below
4,760
rpm
.
The
action
of
the
valve
is
de-
emissions-
related
fault
For
Check
Engine
light
diag-
liberately
delayed
to
prevent
it
from
opening
and
closing
repeat-
nostics,
see100
Engine-General
.
edly
within
a
short
time
.
GENERAL
Page 150 of 759
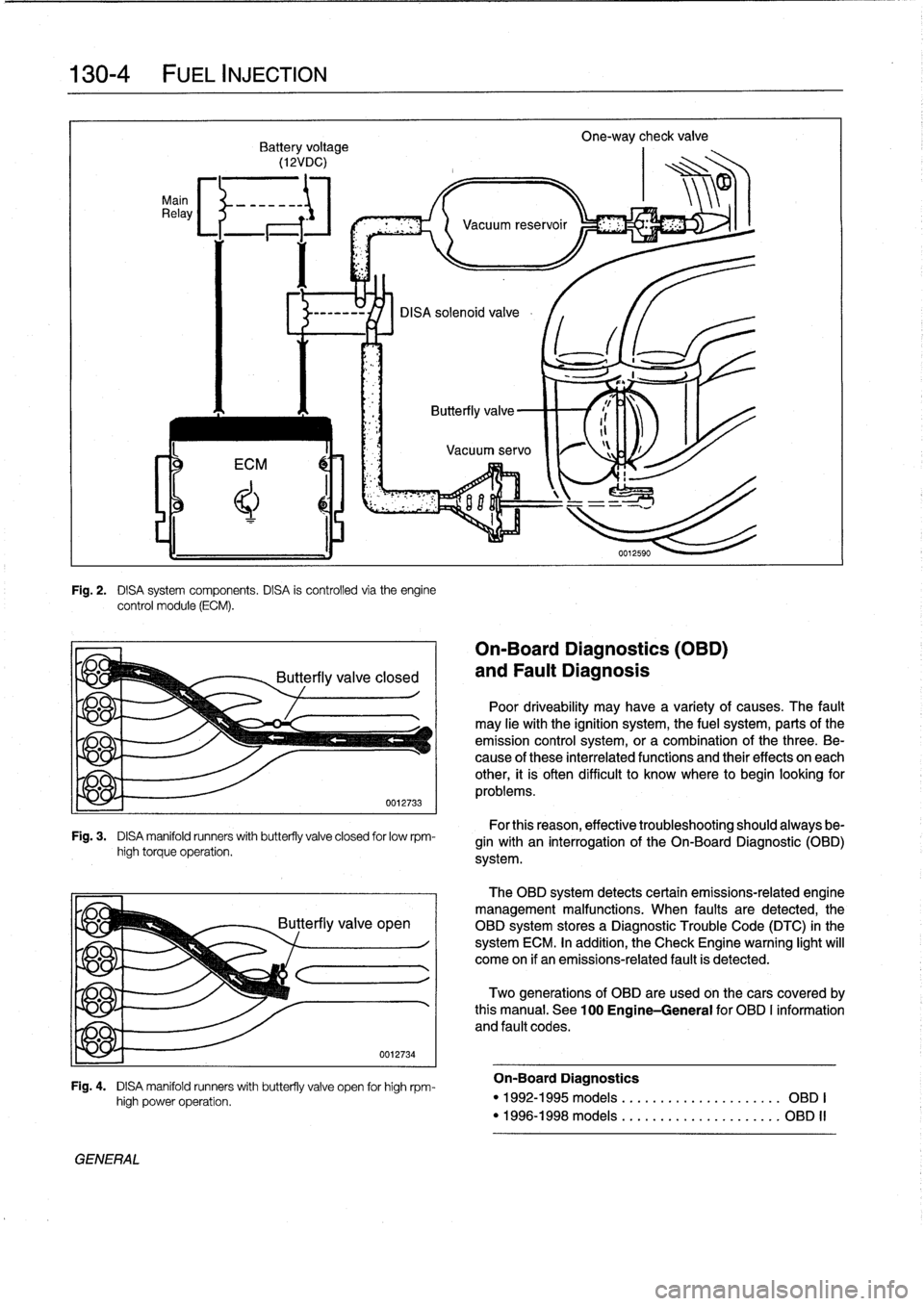
130-
4
FUEL
INJECTION
Main
Relay
Fig
.
2
.
DISA
system
components
.
DISA
is
controlled
via
theengine
control
module
(ECM)
.
Fig
.
3
.
DISA
manifold
runners
with
butterfly
valve
closed
for
lowrpm-
high
torque
operation
.
yje
q
GENERAL
high
power
operation
.
0012734
Fig
.
4
.
DISA
manifold
runners
with
butterfly
valve
open
for
high
rpm-
On-Board
Diagnostics
(OBD)
and
Fault
Diagnosis
Poor
driveability
may
have
a
variety
of
causes
.
The
fault
may
He
withthe
ignition
system,
the
fuel
system,
parts
ofthe
emission
control
system,
ora
combination
of
thethree
.
Be-
cause
of
these
interrelated
functions
and
their
effects
on
each
other,
it
is
often
difficult
to
know
where
to
begin
looking
for
problems
.
For
this
reason,
effective
troubleshooting
should
always
be-
gin
with
an
interrogation
of
the
On-Board
Diagnostic
(01313)
system
.
The
OBD
system
detects
certain
emissions-related
engine
management
malfunctions
.
When
faults
are
detected,the
OBD
system
storesa
Diagnostic
Trouble
Code
(DTC)
in
the
system
ECM
.
In
addition,
the
Check
Engine
warning
light
will
come
on
if
an
emissions-related
fault
is
detected
.
Two
generations
of
OBD
are
used
on
thecars
covered
by
this
manual
.
See
100
Engine-General
for
OBD
I
information
and
fault
codes
.
On-Board
Diagnostics
"
1992-1995models
....
.
...
...
.
...
......
OBD
I
"
1996-1998models
....
.
..
.
.
.
..
...
......
OBD
II