BMW M3 1992 E36 Workshop Manual
Manufacturer: BMW, Model Year: 1992, Model line: M3, Model: BMW M3 1992 E36Pages: 759
Page 211 of 759
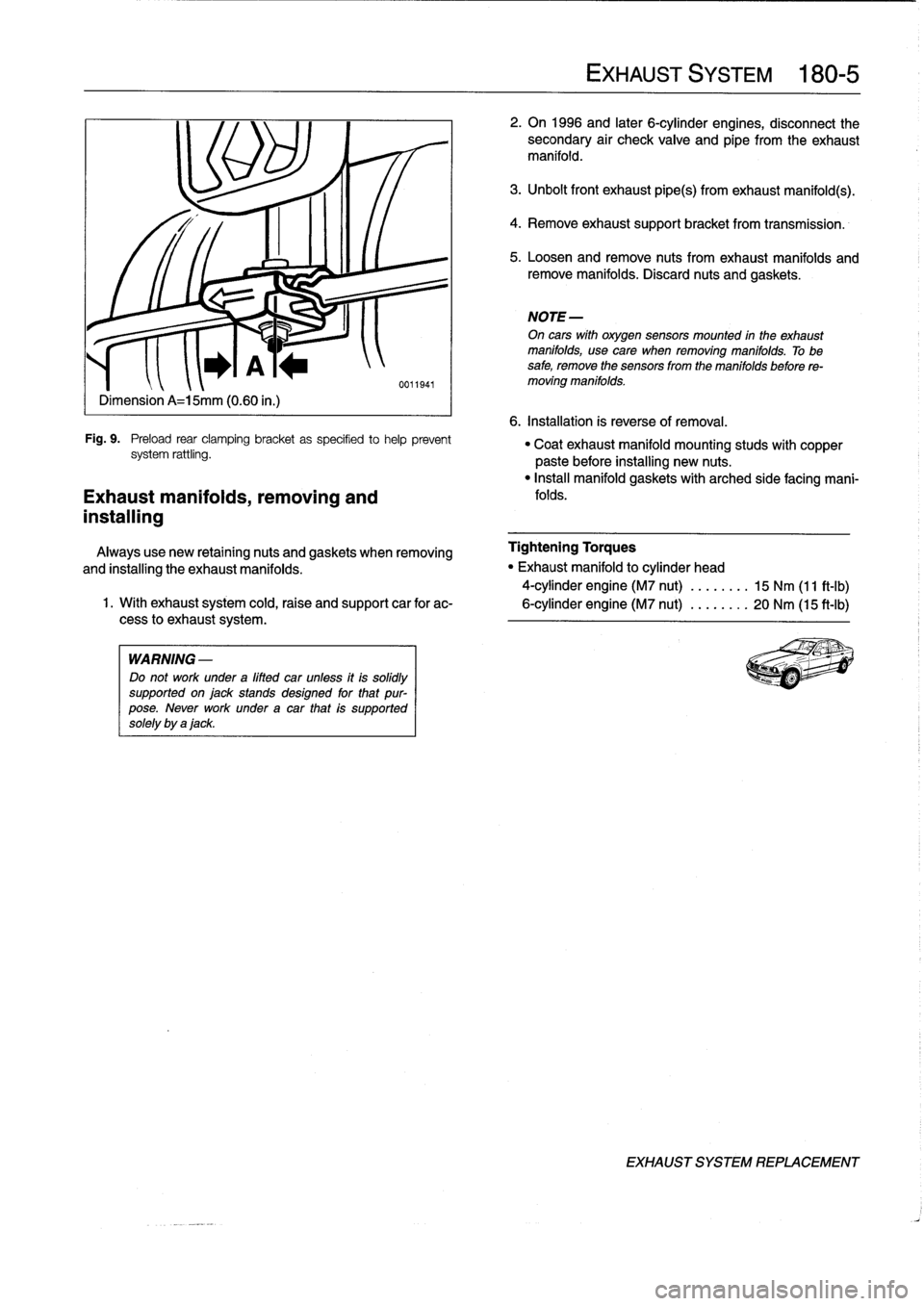
Dimension
A=15mm
(0
.60
in
.)
Fig
.
9
.
Preload
rear
clamping
bracket
as
specifíed
tohelp
prevent
system
rattling
.
Exhaust
manifolds,
removing
and
installing
WARNING
-
Do
not
work
under
a
lifted
car
unfess
itis
solidly
supportedonjackstands
designed
for
that
pur-
pose
.
Never
work
underacar
that
is
supported
solely
by
ajack
.
EXHAUST
SYSTEM
180-
5
2
.
On
1996
and
later
6-cylinder
engines,
disconnect
the
secondary
air
check
valve
and
eipe
from
the
exhaust
manifold
.
3
.
Unbolt
front
exhaust
pipe(s)
from
exhaust
manifold(s)
.
4
.
Remove
exhaustsupport
bracket
from
transmission
.
5
.
Loosen
andremove
nuts
fromexhaust
manifolds
and
remove
manifolds
.
Discard
nuts
and
gaskets
.
NOTE-
On
cars
wíth
oxygen
sensors
mounted
in
the
exhaust
manifolds,
usecare
when
removing
manifolds
.
Tobe
safe,
remove
the
sensors
from
the
manifolds
before
re-
moving
manifolds
.
6
.
Installation
is
reverse
of
removal
.
"
Coatexhaust
manifold
mounting
studs
with
copper
paste
before
installing
new
nuts
.
"
Insta¡¡
manifold
gaskets
with
arched
side
facing
mani-
folds
.
Always
use
new
retaining
nuts
and
gaskets
when
removing
Tightening
Torques
and
installing
the
exhaust
manifolds
.
"
Exhaust
manifold
to
cylinder
head
4-cylinder
engine
(M7
nut)
........
15
Nm
(11
ft-Ib)
1
.
With
exhaust
system
cold,raise
and
support
car
for
ac-
6-cylinder
engine
(M7
nut)
........
20
Nm
(15
ft-Ib)
cess
lo
exhaust
system
.
EXHAUST
SYSTEM
REPLACEMENT
Page 212 of 759
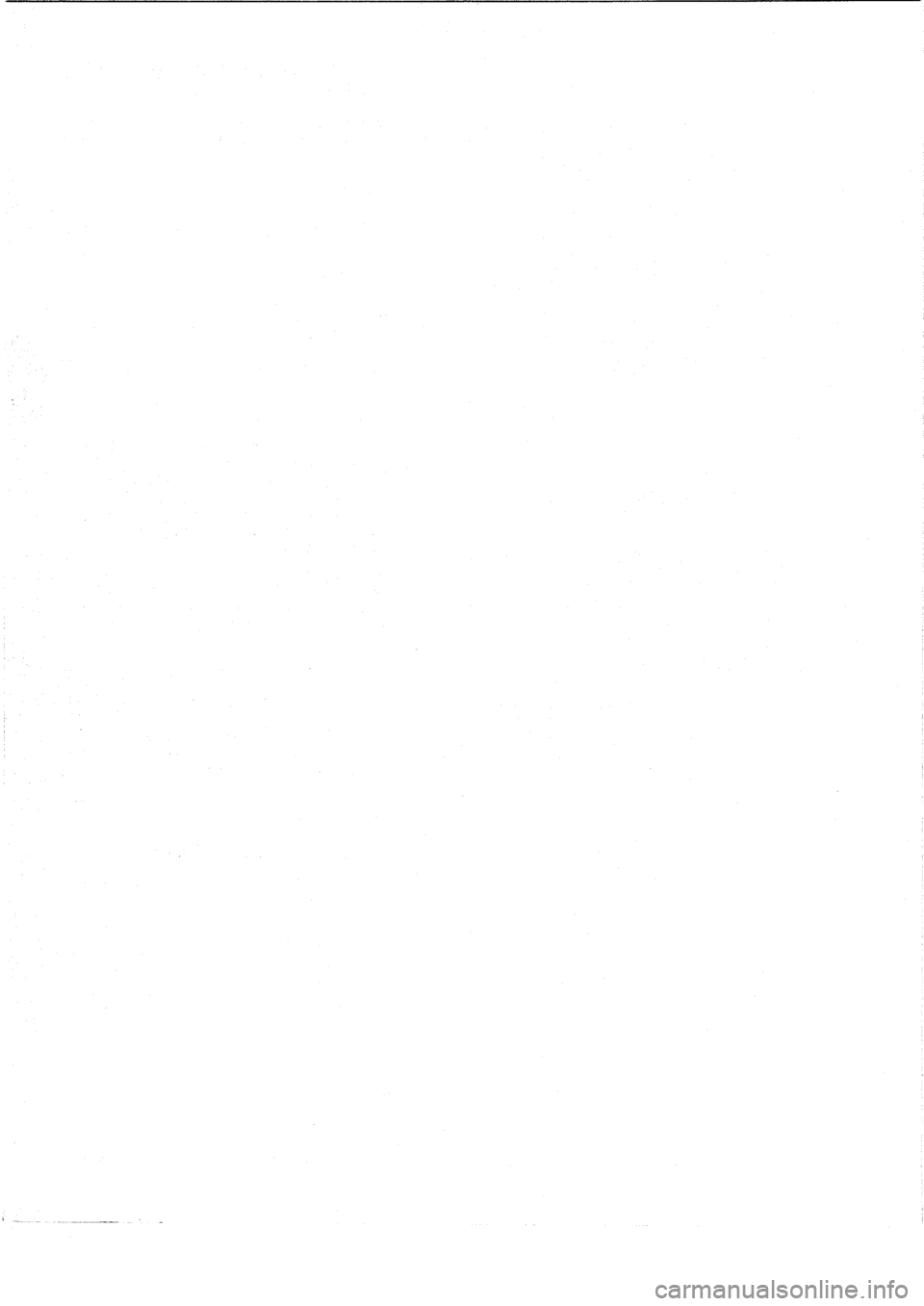
Page 213 of 759
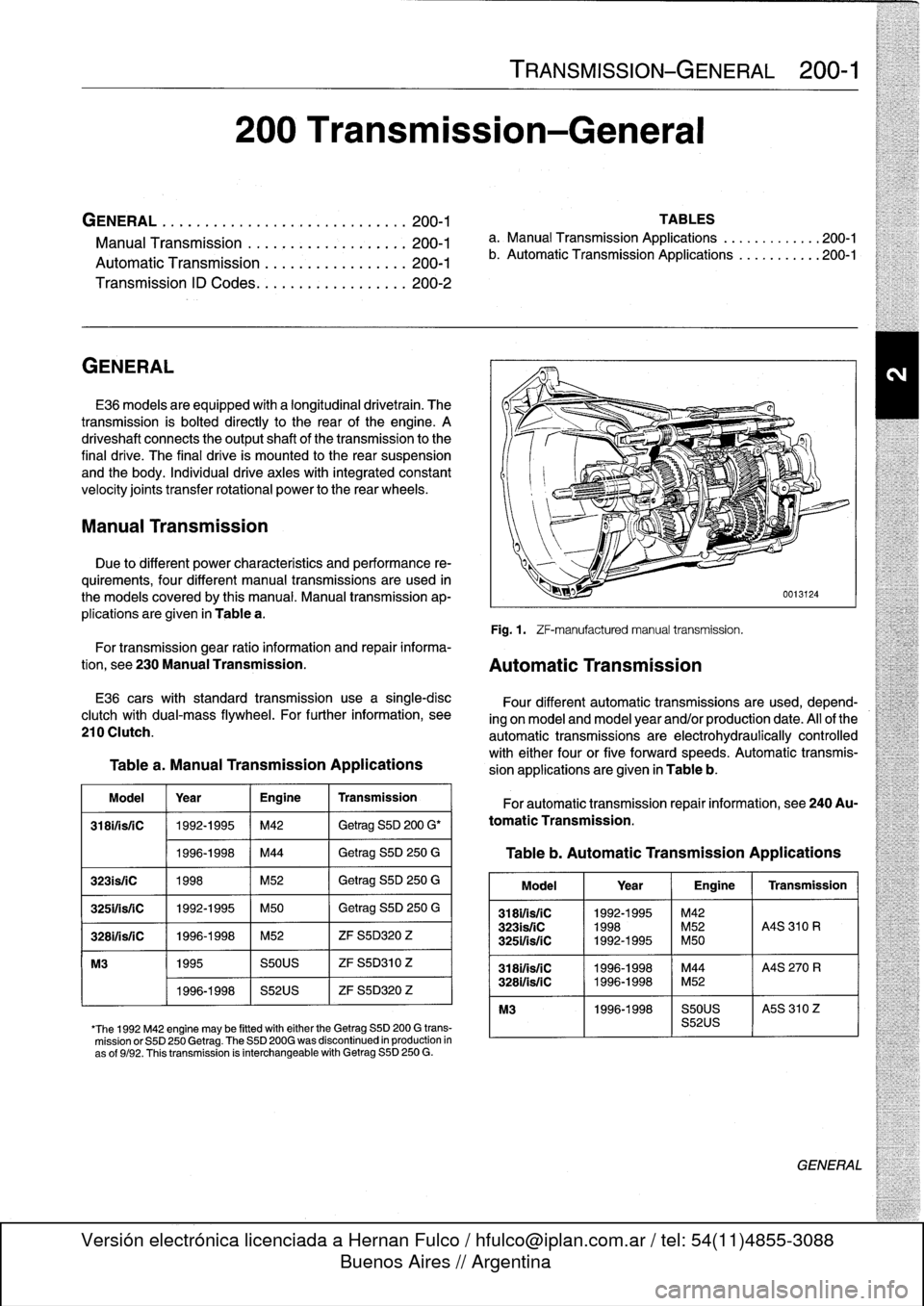
GENERAL
..
.
......
.
.
.
.....
.
...
.
.
.
.
.
.
.
.
200-1
Manual
Transmission
.
.
.....
.
.
.
.'
.
.
.
.
.
.
.
.
200-1
Automatic
Transmission
.........
.
.
.
.
.
.
.
.
200-1
Transmission
ID
Codes
..........
.
.
.
.
.
.
.
.
200-2
GENERAL
E36
models
areequipped
with
a
longitudinal
drivetrain
.
The
transmission
is
bolted
directly
to
the
rear
of
the
engine
.
A
driveshaft
connects
the
output
shaft
of
thetransmission
to
the
final
drive
.
The
final
drive
is
mounted
lo
the
rear
suspension
and
the
body
.
Individual
drive
axles
with
integrated
constant
velocity
joints
transfer
rotational
power
to
the
rear
wheels
.
Manual
Transmission
Due
to
different
power
characteristics
and
performance
re-
quirements,
four
different
manual
transmissions
are
used
in
the
models
coveredby
this
manual
.
Manual
transmission
ap-
plications
are
given
in
Table
a
.
TRANSMISSION-GENERAL
200-1
200
Transmission-General
TABLES
a
.
Manual
Transmission
Applications
..
...........
200-1
b
.
Automatic
Transmission
Applications
...........
200-1
Fig
.
1
.
ZF-manufacturedmanual
transmission
.
For
transmission
gear
ratio
information
and
repair
informa-
tion,
see
230
Manual
Transmission
.
Automatic
Transmission
E36
carswith
standard
transmission
use
a
single-disc
clutch
with
dual-mass
flywheel
.
For
further
information,
see
210
Clutch
.
Table
a
.
Manual
Transmission
Applications
Model
Year
Engine
Transmission
318ifisfC
1992-1995
M42
Getrag
S5D
200
G'
1996-1998
M44
Getrag
S5D
250
G
323is/iC
1998
M52
Getrag
S5D
250
G
325ifsriC
1992-1995
M50
Getrag
S5D
250
G
3281/isfC
1996-1998
M52
ZF
S5D320
Z
M3
1995
S50US
ZF
S5D310
Z
1996-1998
S52US
ZF
S5D320
Z
'The
1992
M42
engine
may
be
fitted
witheither
the
Getrag
SSD
200
G
trans-
mission
or
S5D
250
Getrag
.
The
S5D
200G
was
discontinued
in
production
in
as
of
9/92
.
Thistransmission
is
interchangeable
with
Getrag
S5D
250
G
.
Four
different
automatic
transmissions
are
used,
depend-
ing
on
model
and
model
year
and/or
production
date
.
All
of
the
automatic
transmissions
are
electrohydraulically
controlled
with
either
four
or
five
forward
speeds
.
Automatic
transmis-
sion
applications
are
given
in
Table
b
.
For
automatic
transmission
repair
information,
see
240Au-
tomatic
Transmission
.
Table
b
.
Automatic
Transmission
Applications
Model
1
Year
1
Engine
1
Transmission
318i1is/1C
1992-1995
~
M42
323isfiC
1998
M52
A4S
310
R
3251/is/1C
1992-1995
M50
3181/isfC
11996-1998
M44
A4S
270
R
328i/is/1C
1996-1998
M52
M3
1996-1998
S50US
I
A5S
310
Z
S52US
GENERAL
Page 214 of 759
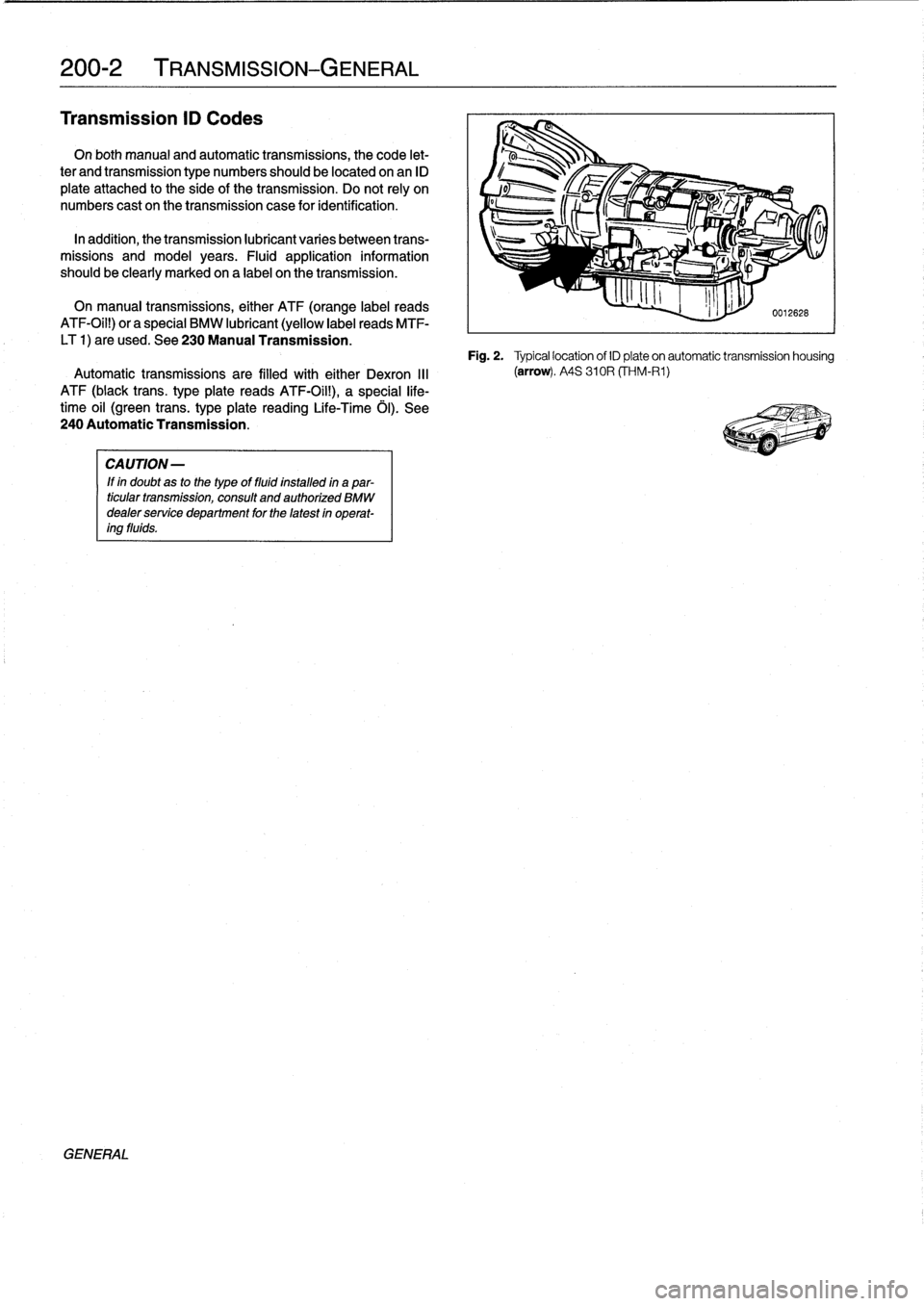
200-2
TRANSMISSION-GENERAL
Transmission
ID
Codes
On
both
manual
and
automatic
transmissions,
the
code
let-
ter
and
transmission
type
numbers
should
be
located
onan
ID
plate
attached
to
the
síde
of
thetransmission
.
Do
not
rely
on
numbers
cast
on
the
transmission
case
for
identification
.
In
addition,
thetransmission
lubricant
varies
between
trans-
missions
and
model
years
.
Fluid
application
information
should
be
clearly
marked
on
a
label
on
thetransmission
.
On
manual
transmissions,
either
ATF
(orange
label
reads
ATF-Oil!)
or
a
special
BMW
lubricant
(yellow
label
reads
MTF-
LT
1)
are
used
.
See
230Manual
Transmission
.
Automatic
transmissions
are
filled
with
either
Dexron
III
ATF
(black
trans
.
type
plate
reads
ATF-Oil!),
a
special
ffe-
time
oil
(green
trans
.
type
plate
reading
Life-Time
ó1)
.
See
240AutomaticTransmission
.
GENERAL
CAUTION-
lf
in
doubtas
to
the
typeof
fluid
installed
in
a
par-
ticular
transmission,
consult
and
authorized
BMW
dealer
service
department
for
the
latest
in
operat-
ing
fluids
.
Fig
.
2
.
Typical
location
of
IDpíate
on
automatic
transmission
housing
(arrow)
.
A4S
310R
(THM-R1)
Page 215 of 759
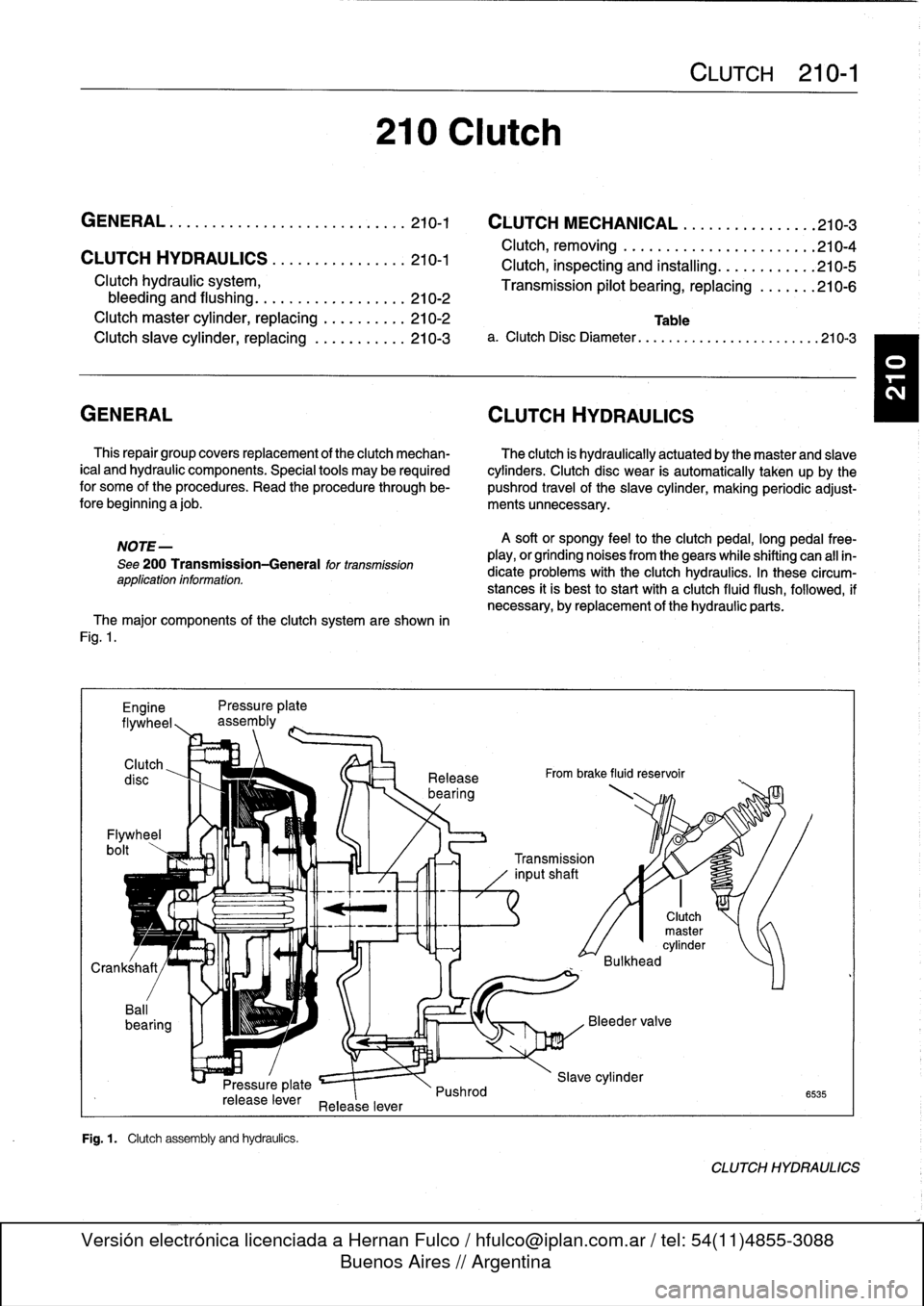
GENERAL
..
.
.
.
.
.
.
.
.
.
.
.
.
.
......
.
......
210-1
CLUTCH
MECHANICAL
.
.
.
.
.
...
.
.....
.
.
210-3
CLUTCH
HYDRAULICS
.
.
.
.............
210-1
Clutch,
removing
.
.
.
.
.
.
.
.
.
.
.
.
.
.
.
.
...
.
.
.
.
210-4
Clutch,inspecting
and
installing
.
.
.
.
.
.
.
.
.
.
.
.210-5Clutch
hydraulic
system,
Transmission
pilot
bearing,replacing
.
.
.
.
...
210-6
bleeding
and
flushing
.
.
.
.
.
.......
.
.....
210-2
Clutch
master
cylinder,
replacing
..
.
.
.
.
.
...
210-2
Table
Clutch
slave
cylinder,
replacing
...
.
.
.
.
.
.
.
.
210-3
a
.
Clutch
Disc
Diameter
.............
..
..
.
......
210-3
GENERAL
CLUTCH
HYDRAULICS
This
repair
group
covers
replacement
of
the
clutch
mechan-
The
Clutch
is
hydraulically
actuated
by
the
master
and
slave
¡cal
and
hydraulic
components
.
Special
tools
may
be
required
cylinders
.
Clutch
disc
wear
is
automatically
taken
upby
the
for
some
of
the
procedures
.
Read
the
procedure
through
be-
pushrod
travelof
the
slave
cylinder,
making
periodic
adjust-fore
beginning
a
job
.
ments
unnecessary
.
NOTE-
See200
Transmission-General
for
transmission
applicatíon
information
.
The
major
components
of
the
clutch
system
are
shown
in
Fig
.
1
.
Engine
Pressure
plate
flywheel,,
assembly
Clutch
Flywheel
bolt
Pressure
plate
release
lever
Release
lever
Fig
.
1
.
Clutch
assembly
and
hydraufcs
.
210
Clutch
Release
bearing
Pushrod
A
soft
or
spongy
feel
to
the
clutchpedal,
long
pedal
free-
play,
or
grinding
noises
from
thegears
while
shifting
can
all
in-
dicate
problems
with
the
Clutch
hydraulics
.
In
these
circum-
stances
it
is
best
to
start
with
a
clutch
fluid
flush,
followed,
if
necessary,
byreplacement
of
the
hydraulic
parts
.
From
brake
fluid
reservoir
CLUTCH
210-1
0
0
Transmission
inputshaft
Clutch
master
cylinder
Bulkhead
Slave
cylinder
6535
CLUTCH
HYDRAULICS
Page 216 of 759
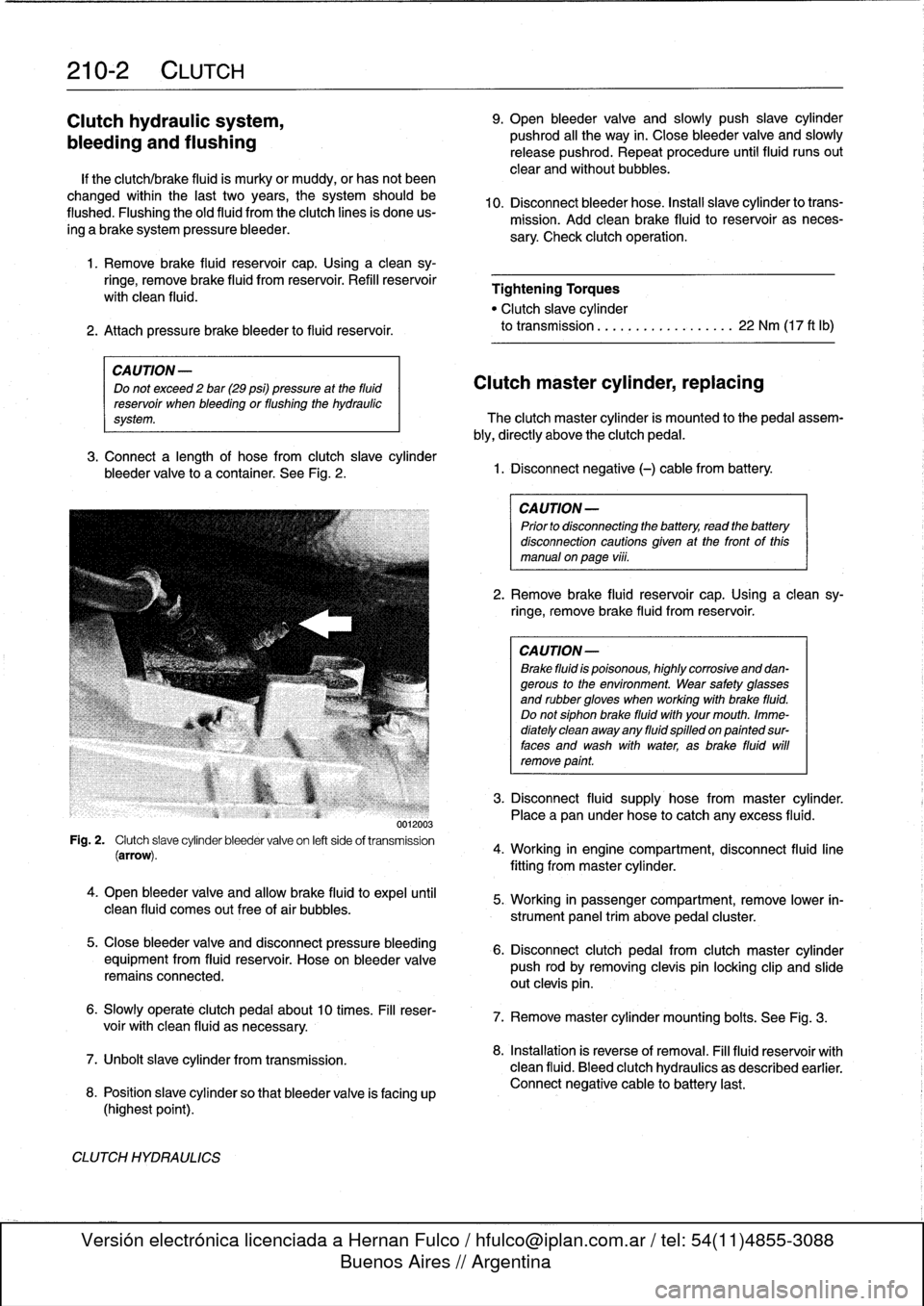
210-2
CLUTCH
Clutch
hydraulic
system,
bleeding
and
flushing
If
the
clutch/brake
fluid
is
murky
or
muddy,
or
has
not
been
changed
within
the
last
two
years,
the
system
should
be
flushed
.
Flushing
the
old
fluid
from
the
clutch
lines
is
done
us-
ing
a
brake
system
pressure
bleeder
.
1
.
Remove
brake
fluíd
reservoir
cap
.
Usinga
clean
sy-
ringe,
remove
brake
fluid
from
reservoir
.
Refill
reservoir
with
clean
fluid
.
2
.
Attach
pressure
brake
bleeder
to
fluid
reservoír
.
CA
UTION-
Do
not
exceed
2
bar
(29
psi)
pressure
at
the
fluid
reservoir
when
bleeding
or
flushing
the
hydraulic
system
.
3
.
Connect
a
length
of
hose
from
clutch
slave
cylinder
bleeder
valve
lo
a
container
.
See
Fig
.
2
.
0012003
Fig
.
2
.
Clutch
slave
cylinder
bleeder
valve
on
left
side
of
transmission
(arrow)
.
4
.
Open
bleeder
valve
and
allow
brake
fluid
to
expel
until
clean
fluid
comes
out
free
of
air
bubbles
.
5
.
Close
bleeder
valve
and
disconnect
pressure
bleeding
equipment
from
fluid
reservoir
.
Hose
on
bleeder
valve
remainsconnected
.
6
.
Slowly
operate
clutch
pedal
about10
times
.
Fill
reser-
voir
with
clean
fluid
asnecessary
.
7
.
Unbolt
slavecylinder
from
transmission
.
8
.
Position
slave
cylinder
so
that
bleeder
valve
is
facing
up
(highest
point)
.
CLUTCH
HYDRAULICS
9
.
Open
bleeder
valve
and
slowly
push
slave
cylinder
pushrod
al¡
the
way
in
.
Close
bleeder
valve
and
slowly
release
pushrod
.
Repeat
procedure
until
fluid
runs
out
clear
and
without
bubbles
.
10
.
Disconnect
bleeder
hose
.
Instan
slavecylinder
lo
trans-
mission
.
Add
cleanbrake
fluid
to
reservoir
as
neces-
sary
.
Check
clutch
operation
.
Tightening
Torques
"
Clutch
slave
cylinder
to
transmission
................
..
22
Nm
(17
ft
lb)
Clutch
master
cylinder,
replacing
The
clutch
master
cylinder
is
mounted
to
the
pedal
assem-
bly,
directly
above
the
clutch
pedal
.
1
.
Disconnect
negative
(-)
cable
from
battery
.
CAUTION-
Prior
to
disconnectiog
the
battery,
read
the
battery
disconnection
cautionsgiven
at
the
front
of
this
manual
on
page
viii
.
2
.
Remove
brake
fluid
reservoir
cap
.
Usinga
clean
sy-
ringe,
remove
brake
fluid
from
reservoir
.
CA
UTION-
Brake
fluid
is
poisonous,
highly
corrosive
and
dan-gerous
to
the
environment
.
Wear
safety
glasses
and
rubbergloves
when
working
with
brake
fluid
.
Do
notsiphonbrake
fluid
with
your
mouth
.
Imme-
diately
clean
away
any
fluid
spilled
on
painted
sur-
faces
and
wash
with
water,
asbrake
fluid
will
remove
point
.
3
.
Disconnect
fluid
supply
hose
from
master
cylinder
.
Placea
pan
under
hose
to
catch
any
excess
fluid
.
4
.
Working
in
engine
compartment,
disconnect
fluid
line
fitting
frommaster
cylinder
.
5
.
Working
in
passenger
compartment,
remove
lower
in-
strument
panel
trim
above
pedal
cluster
.
6
.
Disconnect
clutch
pedal
from
clutch
master
cylinder
push
rod
by
removing
clevis
pin
locking
clip
and
slide
out
clevis
pin
.
7
.
Remove
master
cylinder
mounting
bolts
.
See
Fig
.
3
.
8
.
Installation
is
reverse
of
removal
.
Fill
fluid
reservoir
with
clean
fluid
.
Bleed
clutch
hydraulics
as
described
earlier
.
Connect
negative
cable
to
battery
last
.
Page 217 of 759
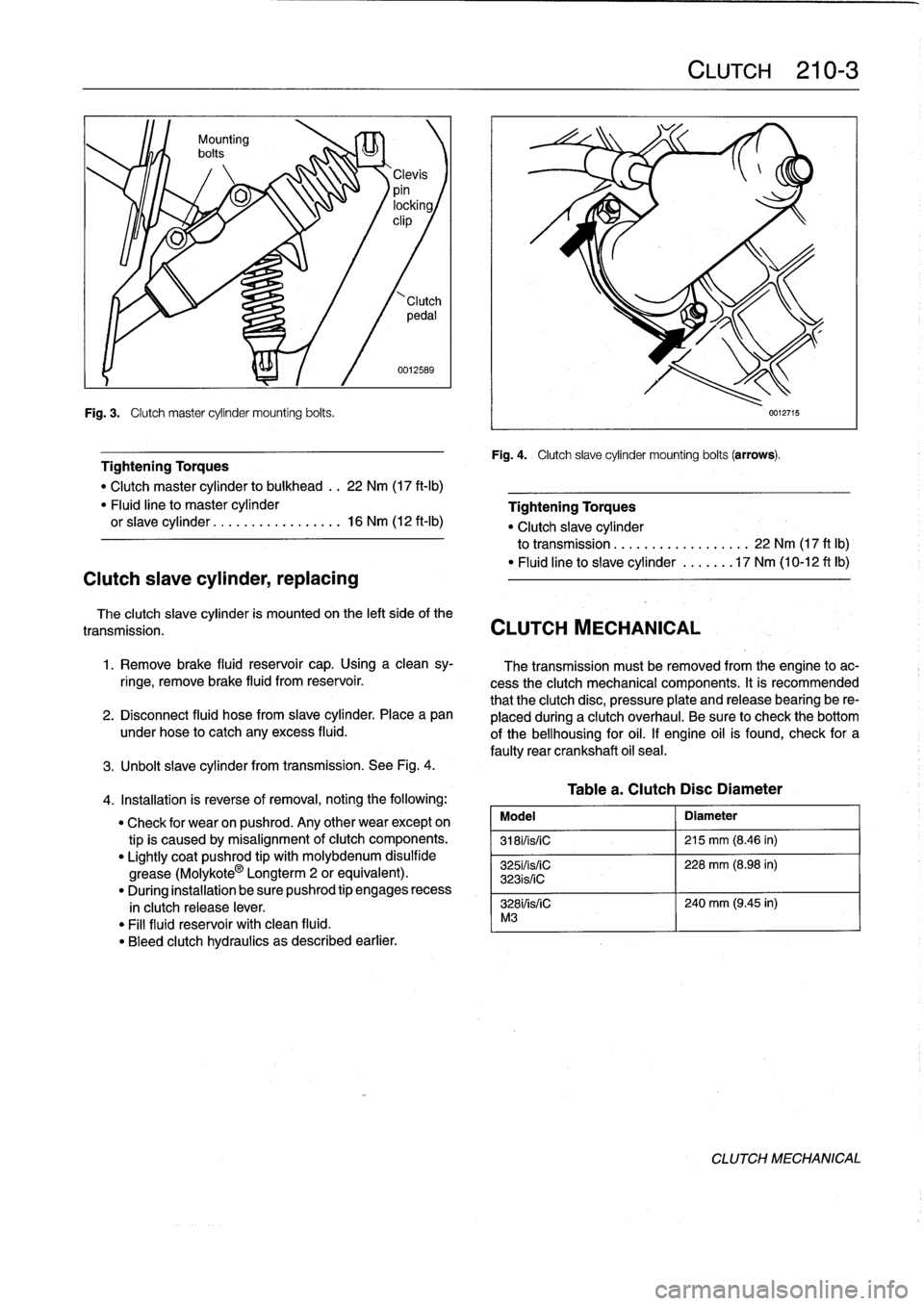
Fig
.
3
.
Clutch
master
cylinder
mounting
bolts
.
Clutch
slave
cylinder,
replacing
0012589
Tightening
Torques
"
Clutch
master
cylinder
to
bulkhead
..
22
Nm
(17
ft-Ib)
"
Fluid
line
to
master
cylinder
orslave
cylinder
.................
16
Nm
(12
ft-1b)
The
clutch
slave
cylinder
is
mounted
on
the
left
side
of
the
transmission
.
CLUTCH
MECHANICAL
1
.
Remove
brake
fluid
reservoir
cap
.
Using
a
clean
sy-
ringe,
remove
brake
fluid
from
reservoir
.
2
.
Disconnect
fluid
hose
from
slave
cylinder
.
Place
a
pan
under
hose
to
catch
any
excess
fluid
.
3
.
Unbolt
slave
cylinder
from
transmission
.
See
Fig
.
4
.
4
.
Installation
is
reverse
of
removal,
noting
the
following
:
"
Check
for
wear
on
pushrod
.
Any
other
wear
except
on
tipis
caused
by
misalignment
of
clutch
components
.
"
Lightly
coat
pushrod
tip
with
molybdenum
disulfide
grease
(Molykote
0
Longterm
2
or
equivalent)
.
"
During
installation
be
sure
pushrod
tip
engages
recess
in
clutch
release
lever
.
"
Fill
fluid
reservoir
with
clean
fluid
.
"
Bleed
clutch
hydraulics
as
described
earlier
.
CLUTCH
210-
3
Fig
.
4
.
Clutch
slave
cylinder
mounting
bolts
(arrows)
.
Tablea
.
ClutchDisc
Diameter
Model
Diameter
3181/is/iC
215
mm
(8
.46
in)
325i/is/iC
228
mm
(8
.98
in)
323is/iC
328i/is/iC
240
mm
(9
.45
in)
M3
0012715
Tightening
Torques
"
Clutch
slave
cylinder
to
transmission
.
.
................
22
Nm
(17
ft
lb)
"
Fluid
line
to
slave
cylinder
......
.17
Nm
(10-12
ft
lb)
The
transmission
must
be
removed
from
the
engine
to
ac-
cess
the
clutch
mechanical
components
.
It
is
recommended
that
the
clutch
disc,
pressure
plate
and
release
bearing
be
re-
placed
duringa
clutch
overhaul
.
Be
sure
to
check
the
bottom
of
the
bellhousing
for
oil
.
If
engine
oil
is
found,
check
for
a
faulty
rear
crankshaft
oil
seal
.
CLUTCH
MECHANICAL
Page 218 of 759
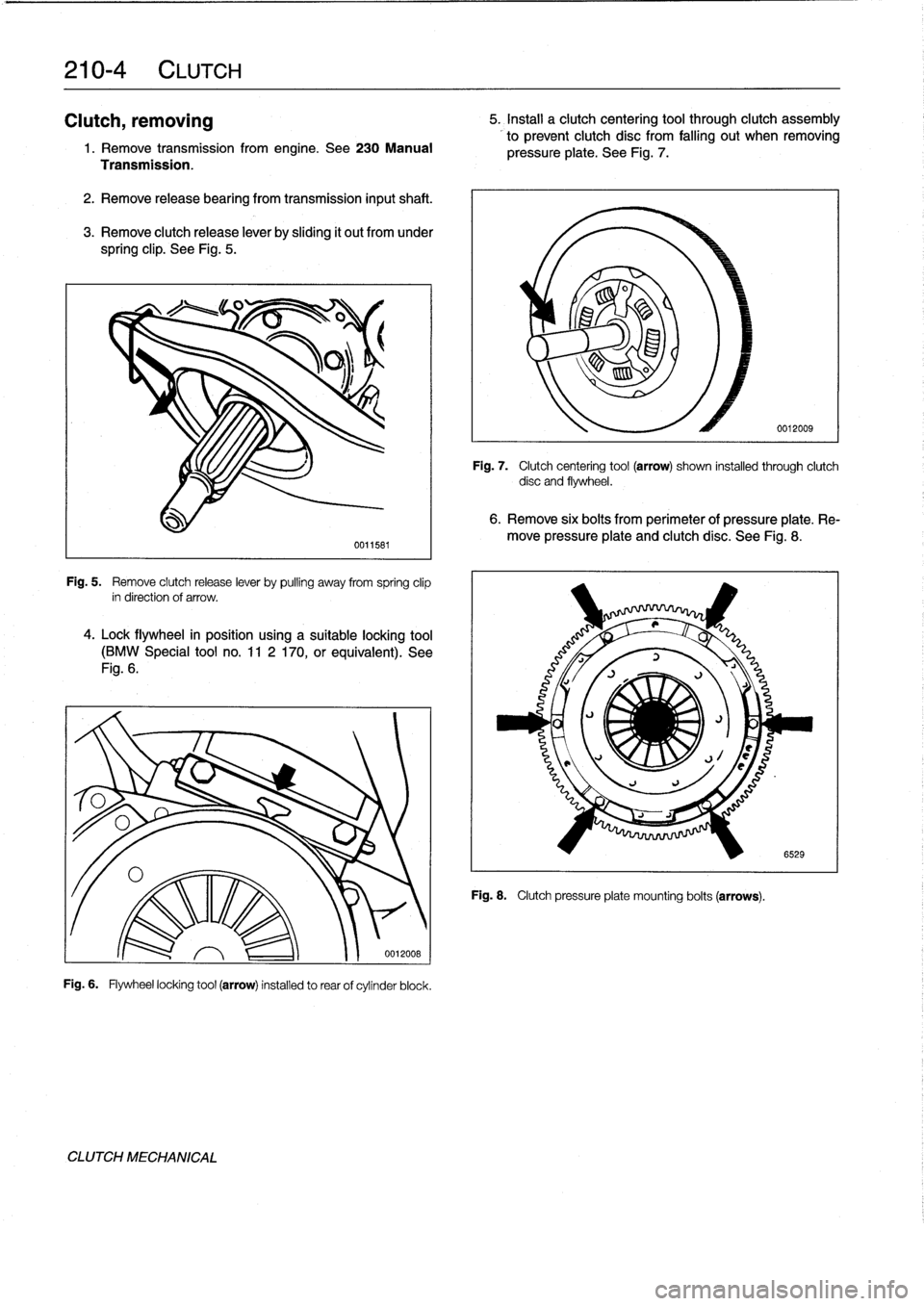
210-
4
CLUTCH
Clutch,
removing
1
.
Remove
transmission
fromengine
.
See230
Manual
Transmission
.
2
.
Remove
release
bearing
from
transmission
inputshaft
.
3
.
Remove
clutch
release
lever
by
sliding
it
out
from
under
spring
clip
.
See
Fig
.
5
.
Fig
.
5
.
Remove
clutch
release
lever
by
pulling
away
from
spring
clip
in
direction
of
arrow
.
4
.
Lock
flywheel
in
posítion
using
a
suitable
locking
tool
(BMW
Special
tool
no
.
11
2
170,or
equivalent)
.
See
Fig
.
6
.
Fig
.
6
.
Flywheel
locking
tool
(arrow)
installed
to
rear
of
cylinder
block
.
CLUTCH
MECHANICAL
0011581
0012008
5
.
Install
a
clutch
centering
tool
through
clutch
assembly
to
prevent
clutch
disc
from
falling
out
when
removing
pressure
plate
.
See
Fig
.
7
.
Fig
.
7
.
Clutch
centering
tool
(arrow)
shown
installed
through
clutch
disc
and
flywheel
.
6
.
Remove
six
bolts
from
perimeter
of
pressure
plate
.
Re-
move
pressure
plate
and
clutch
disc
.
See
Fig
.
8
.
Fig
.
8
.
Clutch
pressure
plate
mounting
bolts
(arrows)
.
0012009
6529
Page 219 of 759
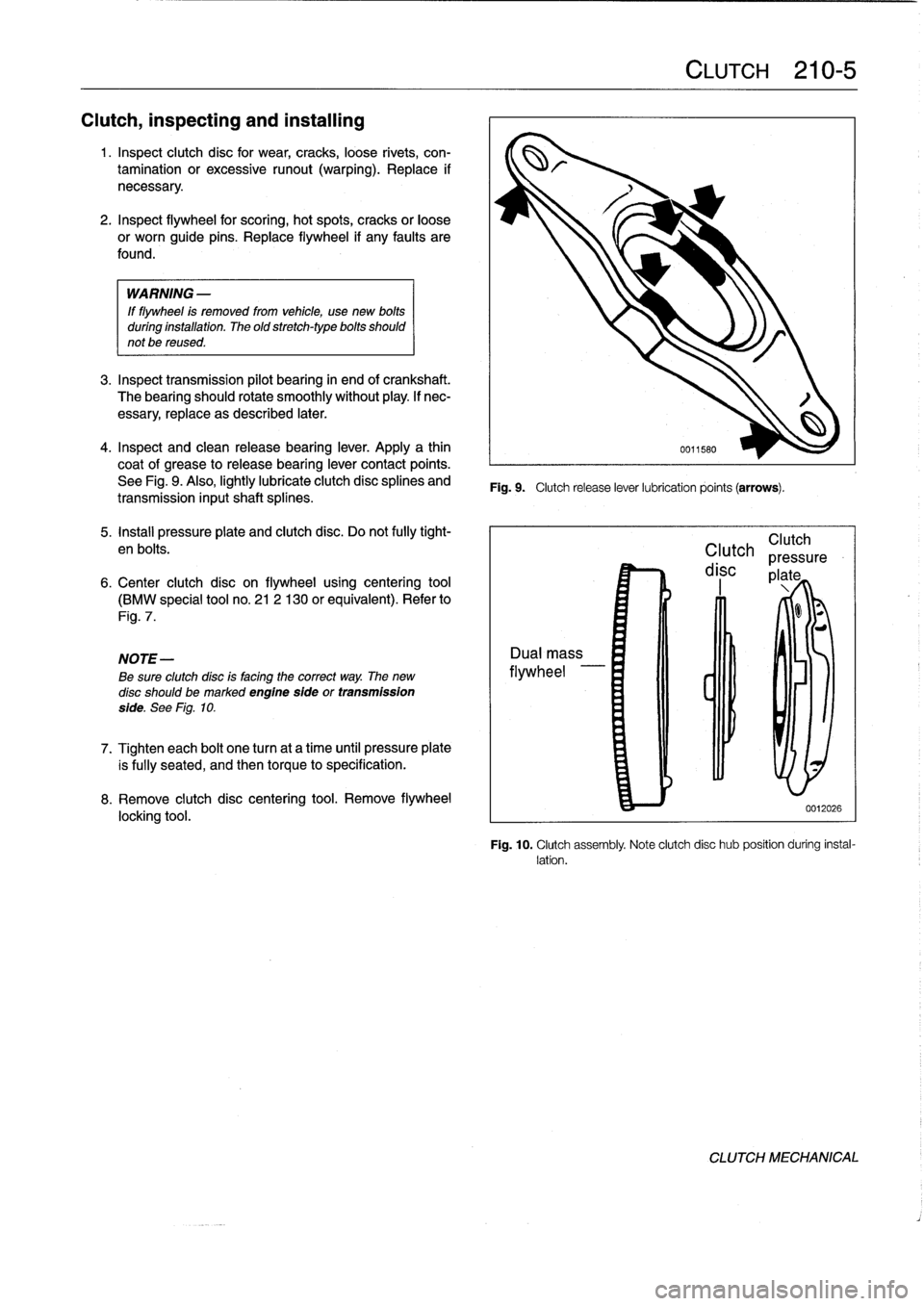
Clutch,
inspecting
and
installing
1
.
Inspect
clutch
disc
for
wear,
cracks,
loose
rivets,
con-
tamination
or
excessive
runout
(warping)
.
Replace
if
necessary
.
2
.
Inspect
flywheel
for
scoring,
hot
spots,
cracks
or
loose
or
worn
guide
pins
.
Replace
flywheel
if
any
faults
are
found
.
WARNING
-
If
flywheel
is
removed
from
vehicle,
use
new
bolts
duríng
installation
.
The
old
stretch-typebolts
should
not
be
reused
.
3
.
Inspecttransmission
pilot
bearing
in
end
of
crankshaft
.
The
bearing
should
rotate
smoothly
without
play
.
If
nec-
essary,
replace
as
described
later
.
4
.
Inspect
and
clean
releasebearing
lever
.
Apply
a
thin
coat
of
grease
to
releasebearíng
lever
contact
points
.
See
Fig
.
9
.
Also,
lightly
lubricate
clutch
disc
splines
and
transmission
inputshaft
splínes
.
5
.
Install
pressure
plate
and
clutch
disc
.
Do
not
fully
tight-
en
bolts
.
6
.
Center
clutch
disc
on
flywheel
using
centering
tool
(BMW
special
tool
no
.
21
2
130
or
equivalent)
.
Refer
to
Fig
.
7
.
NOTE-
Be
sure
clutchdísc
is
facing
the
correct
way
.
The
new
disc
should
bemarked
engine
sfde
or
transmission
side
.
See
Fig
.
10
.
7
.
Tighten
each
bolt
one
turn
at
a
time
until
pressure
plate
is
fully
seated,
and
then
torque
to
specification
.
8
.
Remove
clutch
disc
centering
tool
.
Remove
flywheel
locking
tool
.
Fig
.
9
.
Clutch
release
lever
lubrication
points
(arrows)
.
CLUTCH
210-
5
Clutch
Clutch
pressure
disc
plate
0012026
Fig
.
10
.
Clutch
assembly
Note
clutch
disc
hub
position
during
instal-
lation
.
CLUTCH
MECHANICAL
Page 220 of 759
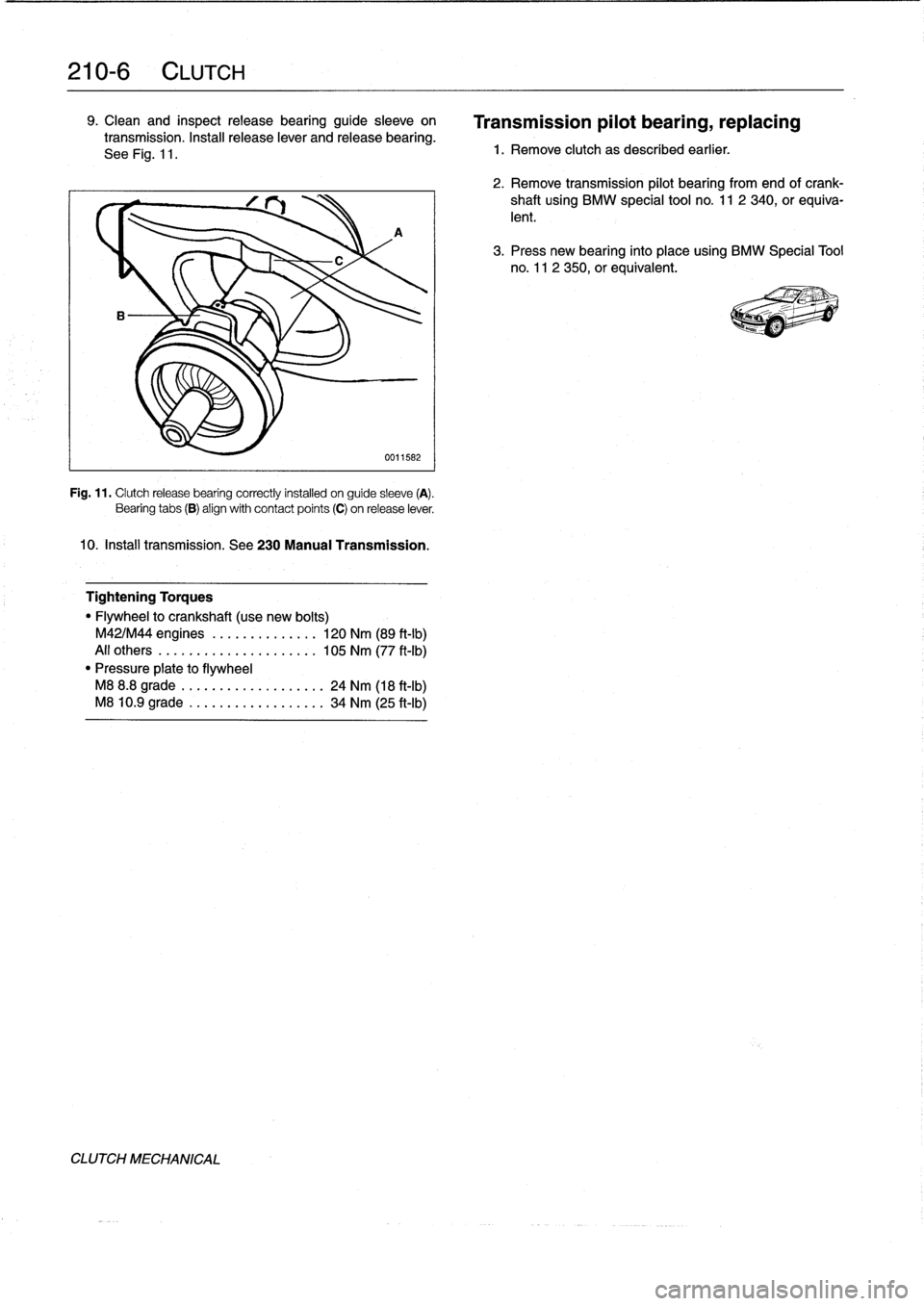
210-
6
CLUTCH
9
.
Clean
and
inspectrelease
bearing
guide
sleeve
on
transmission
.
Install
release
lever
and
release
bearing
.
See
Fig
.
11
.
A
0011582
Fig
.
11
.
Clutchrelease
bearing
correctly
installed
on
guide
sleeve
(A)
.
Bearing
tabs
(B)
align
with
contact
points
(C)
on
release
lever
.
10
.
Insta¡¡
transmission
.
See230
Manual
Transmission
.
Tightening
Torques
"
Flywheel
to
crankshaft
(use
new
bolts)
M42/M44
engines
....
.
..
...
....
120
Nm
(89
ft-Ib)
All
others
..........
..
.
..
......
105
Nm
(77
ft-Ib)
"
Pressure
píate
to
flywheel
M8
8
.8
grade
......
...
.
.
........
24
Nm
(18
ft-Ib)
M8
10
.9
grade
.....
..
..
..
.......
34
Nm
(25
ft-Ib)
CLUTCH
MECHANICAL
Transmission
pilot
bearing,
replacing
1
.
Remove
clutch
as
described
earlier
.
2
.
Remove
transmission
pilot
bearing
from
end
ofcrank-
shaft
using
BMW
special
tool
no
.
11
2
340,
or
equiva-
lent
.
3
.
Press
new
bearing
finto
placeusing
BMW
Specíal
Tool
no
.
11
2
350,or
equivalent
.