BMW M3 1992 E36 Workshop Manual
Manufacturer: BMW, Model Year: 1992, Model line: M3, Model: BMW M3 1992 E36Pages: 759
Page 241 of 759
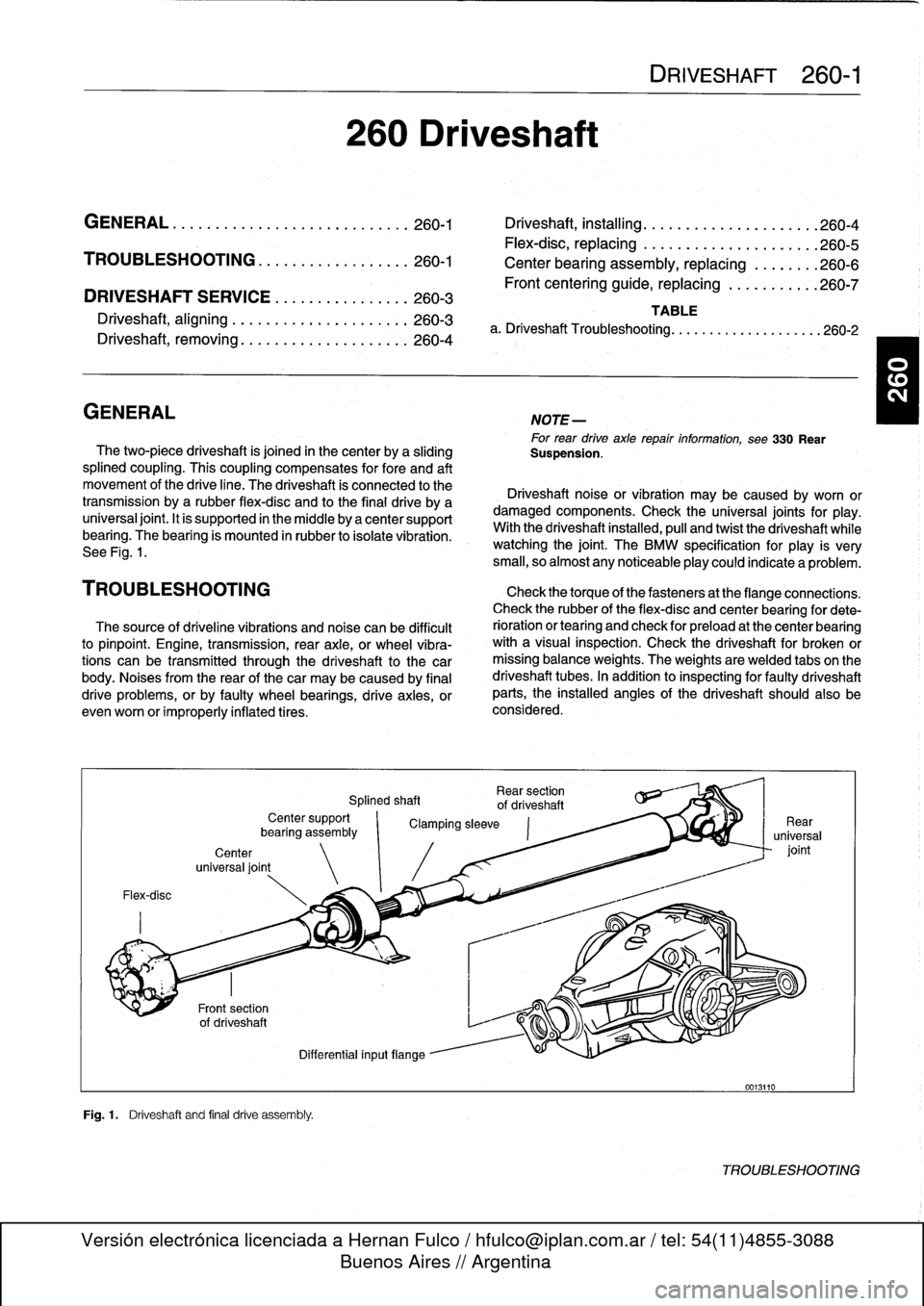
DRIVESHAFT
SERVICE
.
...
.
.
.
...
.
..
.
.
.260-3
Driveshaft,
aligning
...............
.
...
.
.
260-3
Driveshaft,
removing
..............
.
.
.
.
.
.
260-4
260
Driveshaft
DRIVESHAFT
260-1
GENERAL
.
.
.
.
.
.
.
.....
.
.
.
........
.
...
.
260-1
Driveshaft,
installing
.
....
.
..
.
............
260-4
Flex-disc,
replacing
.....
.
.
.
.............
260-5
TROUBLESHOOTING
..
.
.
.
...
.
.........
260-1
Center
bearing
assembly,
replacing
.
......
.260-6
Frontcentering
guide,
replacing
..
.
.......
.
260-7
TABLE
a
.
Driveshaft
Troubleshooting
.
.
...
......
.
....
..
.
.
260-2
GENERAL
NOTE-
For
rear
drive
axlerepair
information,
see330
Rear
The
two-piece
driveshaft
is
joined
in
thecenter
by
a
sliding
Suspension
.
splined
coupling
.
This
coupling
compensates
for
fore
and
aft
movement
of
the
drive
line
.
The
driveshaft
ís
connected
to
the
Driveshaft
noise
or
vibration
may
be
caused
by
worn
or
transmission
bya
rubber
flex-disc
and
to
the
final
drive
by
a
damaged
components
.
Check
the
universal
joints
for
play
.
universal
joint
.
It
is
supported
in
the
micidle
by
a
center
support
With
the
driveshaft
installed,
pull
and
twist
the
driveshaft
while
bearing
.
The
bearing
is
mounted
in
rubber
to
isolate
vibration
.
watching
the
joint
.
The
BMW
specificationfor
play
is
very
See
Fig
.
1
.
small,
so
almost
any
noticeableplay
could
indicate
a
problem
.
TROU
BLESHOOTING
Check
thetorque
of
thefasteners
at
the
flange
connections
.
Check
therubber
of
the
flex-disc
and
center
bearing
for
dete
The
source
of
driveline
vibrations
and
noise
can
be
difficult
rioration
or
tearíng
and
check
for
preload
at
the
center
bearing
to
pinpoint
.
Engine,
transmission,
rear
axle,
or
wheel
vibra-
with
a
visual
inspection
.
Check
the
driveshaft
for
broken
or
tions
can
be
transmitted
through
the
driveshaft
to
the
car
missing
balance
weights
.
The
weights
are
welded
tabs
on
the
body
.
Noises
from
the
rear
of
thecar
may
be
caused
by
final
driveshaft
tubes
.
In
addition
to
inspecting
for
faulty
driveshaft
drive
problems,
orby
faulty
wheel
bearings,
drive
axies,
or
parts,
the
installed
angles
of
the
driveshaft
should
also
be
evenworn
or
improperly
inflatedtires
.
considered
.
Flex-disc
Center
universal
joint
Fig
.1
.
Driveshaft
and
final
drive
assembly
.
Rear
section
Splined
shaft
of
driveshaft
Center
support
`
Clamping
sleeve
bearíng
assembly
Differential
inputflange
0013110
TROUBLESHOOTING
Page 242 of 759
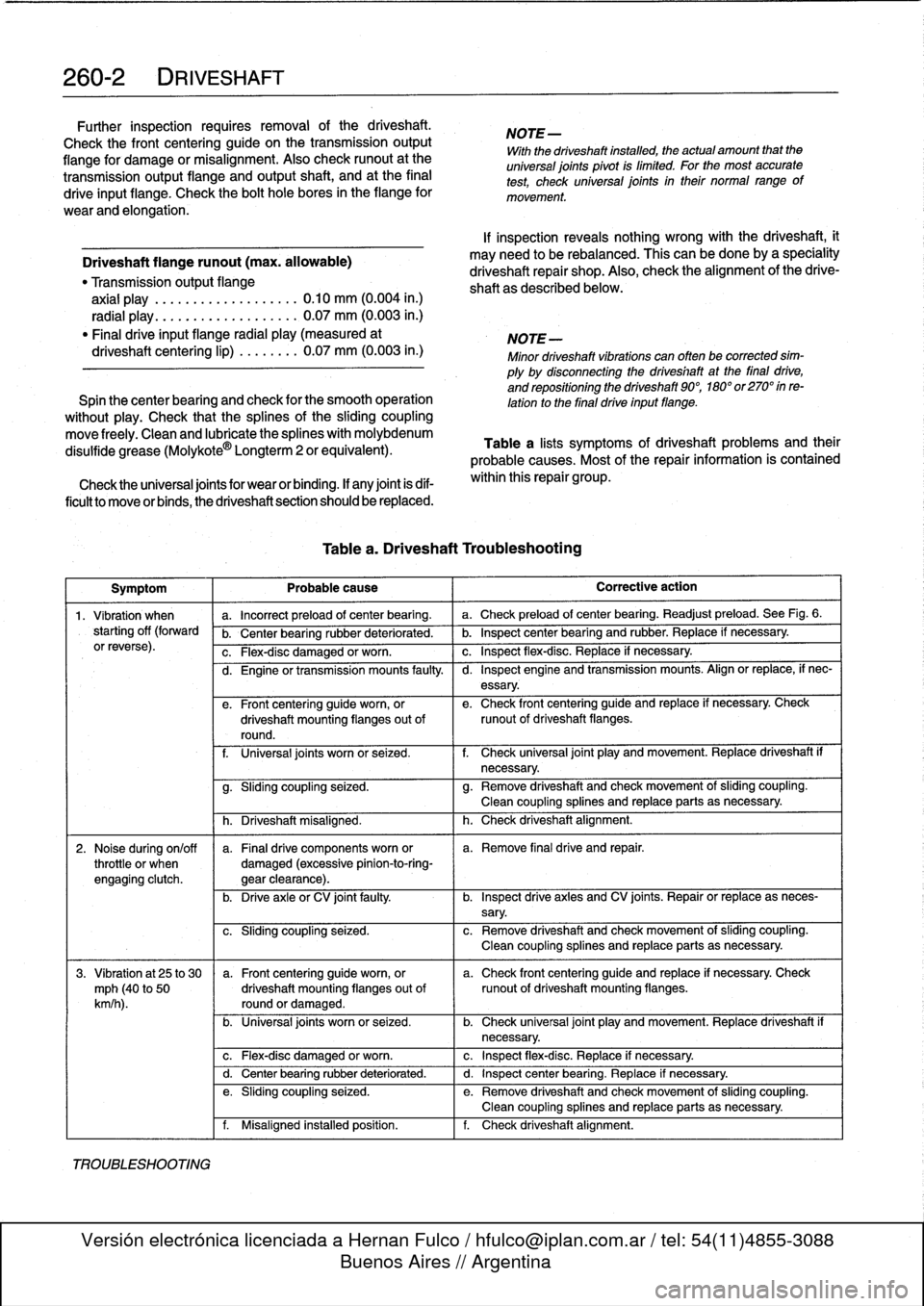
260-2
DRIVESHAFT
Further
inspection
requires
removal
of
the
driveshaft
.
Check
the
front
centering
guide
on
the
transmission
output
flange
for
damage
or
misalignment
.
Also
check
runoutatthe
transmission
outputflange
and
output
shaft,
and
at
the
final
drive
input
flange
.
Check
the
bolt
hole
bores
in
theflange
for
wear
and
elongation
.
Driveshaftflange
runout
(max
.
allowable)
"
Transmission
outputflange
axial
play
...
.
..
...
..
.
.......
0
.10
mm
(0
.004
in
.)
radial
play
.......
...
.
.
.......
0
.07
mm
(0
.003
in
.)
"
Final
driveinput
flange
radial
play
(measured
at
driveshaft
centering
lip)
..
......
0
.07
mm
(0
.003
in
.)
Spinthe
center
bearing
and
check
for
the
smooth
operation
without
play
.
Check
that
thesplines
of
the
sliding
coupling
move
freely
.
Clean
and
lubricate
the
splines
with
molybdenum
disulfide
grease
(Molykote
®
Longterm
2
or
equivalent)
.
Check
the
universal
joints
for
wear
or
binding
.
If
any
joint
isdif-
ficult
to
move
or
binds,
the
driveshaft
section
should
be
replaced
.
Table
a
.
Driveshaft
Troubleshooting
NOTE-
With
the
driveshaft
installed,
theactual
amount
that
the
universal
joints
pivot
is
limited
.
For
the
most
accurate
test,
check
universal
joints
in
their
normal
range
of
movement
.
If
inspection
revealsnothing
wrong
with
the
driveshaft,
it
may
need
to
be
rebalanced
.
This
can
be
done
by
a
speciality
driveshaft
repair
shop
.
Also,
check
the
alignment
ofthe
drive-
shaft
as
described
below
.
NOTE-
Minor
driveshaftvibrations
can
often
be
correctedsim-
ply
by
disconnecting
the
driveshaftat
the
finaldrive,
and
repositíoning
the
driveshaft
90°,
180°
or270°
inre-
lationto
the
final
drive
input
flange
.
Table
a
lists
symptoms
of
driveshaft
problems
and
their
probable
causes
.
Most
of
the
repair
information
is
contained
within
this
repair
group
.
Symptom
Probable
cause
Corrective
action
1
.
Vibration
when
a
.
Incorrect
preload
of
center
bearing
.
a
.
Check
preload
of
center
bearing
.
Readjust
preload
.
See
Fig
.
6
.
starting
off
(forward
b
.
Center
bearing
rubber
deteriorated
.
b
.
Inspect
center
bearing
and
rubber
.
Replace
if
necessary
.
orreverse)
.
c
.
Flex-disc
damaged
or
worn
.
c
.
Inspect
flex-disc
.
Replace
if
necessary
.
TROUBLESHOOTING
d
.
Engine
or
transmission
mounts
faulty
.
I
d
.
Inspect
engine
and
transmission
mounts
.
Align
or
replace,
if
nec-
essary
.
e
.
Front
centering
guide
worn,
or
e
.
Check
front
centering
guide
and
replace
if
necessary
.
Check
driveshaft
mounting
flanges
out
of
runout
of
driveshaft
flanges
.
round
.
f
.
Universal
joints
worn
or
seized
.
f
.
Check
universal
joint
play
and
movement
.
Replace
driveshaft
if
necessary
.
g
.
Sliding
coupling
seized
.
g
.
Remove
driveshaft
and
check
movement
of
sliding
coupling
.
Clean
coupling
splines
and
replace
parts
asnecessary
.
h
.
Driveshaft
misaligned
.
h
.
Check
driveshaft
alignment
.
2
.
Noise
during
on/off
a
.
Finaldrive
components
worn
or
a
.
Remove
final
drive
and
repair
.
throttle
or
when
damaged
(excessive
pinion-to-ring-
engagíng
clutch
.
gear
clearance)
.
b
.
Drive
axleor
CV
joint
faulty
.
b
.
Inspect
drive
axles
and
CV
joints
.
Repair
or
replace
as
neces-
sary
.
c
.
Sliding
coupling
seized
.
c
.
Remove
driveshaft
and
check
movement
of
sliding
coupling
.
Clean
coupling
splines
and
replace
parts
as
necessary
.
3
.
Vibration
at
25
to
30
a
.
Front
centering
guideworn,
or
a
.
Check
front
centering
guide
and
replace
if
necessary
.
Check
mph
(40
to
50
driveshaft
mounting
flanges
out
of
runout
of
driveshaft
mounting
flanges
.
km/h
).
round
or
damaged
.
b
.
Universal
joints
worn
or
seized
.
b
.
Check
universal
joint
play
and
movement
.
Replace
driveshaft
if
necessary
.
c
.
Flex-disc
damaged
or
worn
.
c
.
Inspect
flex-disc
.
Replace
if
necessary
.
d
.
Center
bearing
rubber
deteriorated
.
d
.
Inspect
center
bearing
.
Replace
if
necessary
.
e
.
Sliding
coupling
seized
.
e
.
Remove
driveshaft
and
check
movement
of
sliding
coupling
.
Clean
coupling
splines
and
replace
parts
asnecessary
.
f
.
Misaligned
installed
position
.
f
.
Check
driveshaft
alignment
.
Page 243 of 759
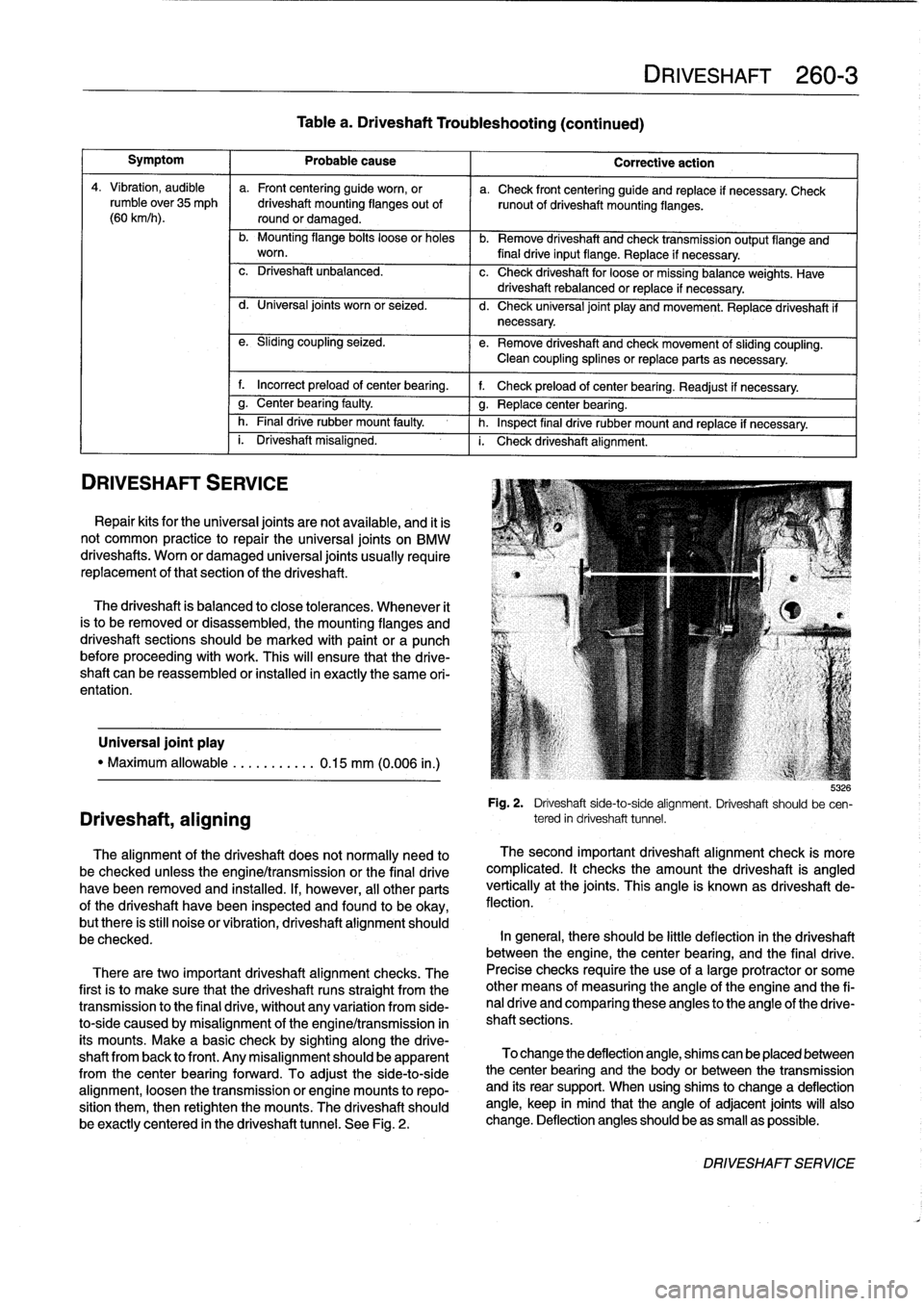
Symptom
1
Probable
cause
4
.
Vibration,
audible
a
.
Front
centering
guide
worn,
or
a
.
Check
front
centering
guide
and
replace
if
necessary
.
Check
rumble
over35
mph
driveshaft
mounting
flanges
out
of
runout
of
driveshaft
mounting
flanges
.
(60
km/h)
.
round
or
damaged
.
b
.
Mounting
flange
bolts
loose
or
holes
b
.
Remove
driveshaft
and
check
transmissionoutput
flange
and
worn
.
final
drive
input
flange
.
Replace
if
necessary
.
c
.
Driveshaft
unbalanced
.
c
.
Check
driveshaft
for
loose
or
missing
balance
weights
.
Have
driveshaft
rebalanced
or
replace
if
necessary
.
DRIVESHAFT
SERVICE
Driveshaft,
aligning
d
.
Universal
joints
worn
or
seized
.
d
.
Check
universal
joint
play
and
movement
.
Replace
driveshaft
if
necessary
.
e
.
Sliding
coupling
seized
.
e
.
Remove
driveshaft
and
check
movement
of
sliding
coupling
.
1
Clean
coupling
splines
or
replace
parts
asnecessary
.
f
.
Incorrect
preload
of
center
bearing
.
f
.
Check
preload
of
center
bearing
.
Readjust
if
necessary
.
g
.
Center
bearing
faulty
.
g
.
Replace
center
bearing
.
h
.
Final
drive
rubber
mount
faulty
h
.
Inspect
final
drive
rubber
mount
and
replace
if
necessary
.i.
Driveshaft
misaligned
.
i.
Check
driveshaft
alignment
.
Repair
kits
for
the
universal
joints
are
not
available,
and
it
is
not
common
practice
to
repair
the
universal
joints
on
BMW
driveshafts
.
Worn
or
damaged
universal
joints
usually
require
replacement
of
that
section
of
the
driveshaft
.
The
driveshaft
is
balanced
to
cose
tolerances
.
Whenever
it
is
to
be
removed
or
disassembied,
the
mounting
flanges
and
driveshaft
sections
should
bemarked
with
paint
or
a
punch
before
proceeding
with
work
.
This
will
ensure
that
the
drive-
shaft
can
be
reassembled
or
installed
in
exactlythe
same
ori-
entation
.
Universal
joint
play
"
Maximum
allowable
...........
0.15
mm
(0.006
in
.)
The
alignment
of
the
driveshaft
does
not
normally
need
to
be
checked
unless
the
engine/transmission
orthe
final
drive
havebeen
removed
and
installed
.
If,
however,
all
other
parts
of
the
driveshaft
havebeen
inspected
and
found
to
be
okay,
butthere
is
still
noise
or
vibration,
driveshaft
alignment
should
be
checked
.
There
aretwo
important
driveshaft
alignment
checks
.
The
first
is
to
make
sure
that
the
driveshaft
runs
straight
from
the
transmission
to
the
final
drive
;
without
any
variation
from
side-
to-side
caused
by
misalignment
ofthe
engine/transmission
in
its
mounts
.
Make
a
basic
check
by
sighting
along
the
drive-
shaft
from
back
lo
front
.
Any
misalignmentshould
be
apparent
from
the
center
bearingforward
.
To
adjustthe
side-to-side
alignment,
loosen
the
transmission
or
engine
mounts
to
repo-
sition
them,
then
retighten
the
mounts
:
The
driveshaft
should
be
exactly
centered
in
the
driveshaft
tunnel
.
See
Fig
.
2
.
Table
a
.
Driveshaft
Troubleshooting
(continued)
DRIVESHAFT
260-3
Corrective
action
b
:izó
Fig
.
2
.
Driveshaft
side-to-side
alignment
.
Driveshaft
should
be
cen-
tered
in
driveshaft
tunnel
.
The
second
important
driveshaft
alignment
check
is
more
complicated
.
It
checks
the
amount
the
driveshaft
is
angled
vertically
at
the
joints
.
This
angle
is
known
as
driveshaft
de-
flection
.
In
general,
there
should
be
little
deflection
in
the
driveshaft
between
the
engine,
thecenter
bearing,
and
the
final
drive
.
Precise
checks
require
theuse
of
a
large
protractor
or
some
other
means
of
measuring
the
angle
of
the
engine
and
the
fi-
nal
drive
and
comparing
these
angles
to
the
angle
of
the
drive-
shaft
sections
.
To
change
the
deflection
angle,
shims
can
be
placed
between
the
center
bearing
and
the
body
or
between
the
transmission
and
íts
rear
support
.
When
using
shims
to
change
a
deflection
angle,
keep
in
mind
that
the
angle
of
adjacent
joints
will
also
change
.
Deflection
anglesshould
beas
small
as
possible
.
DRIVESHAFTSERVICE
Page 244 of 759
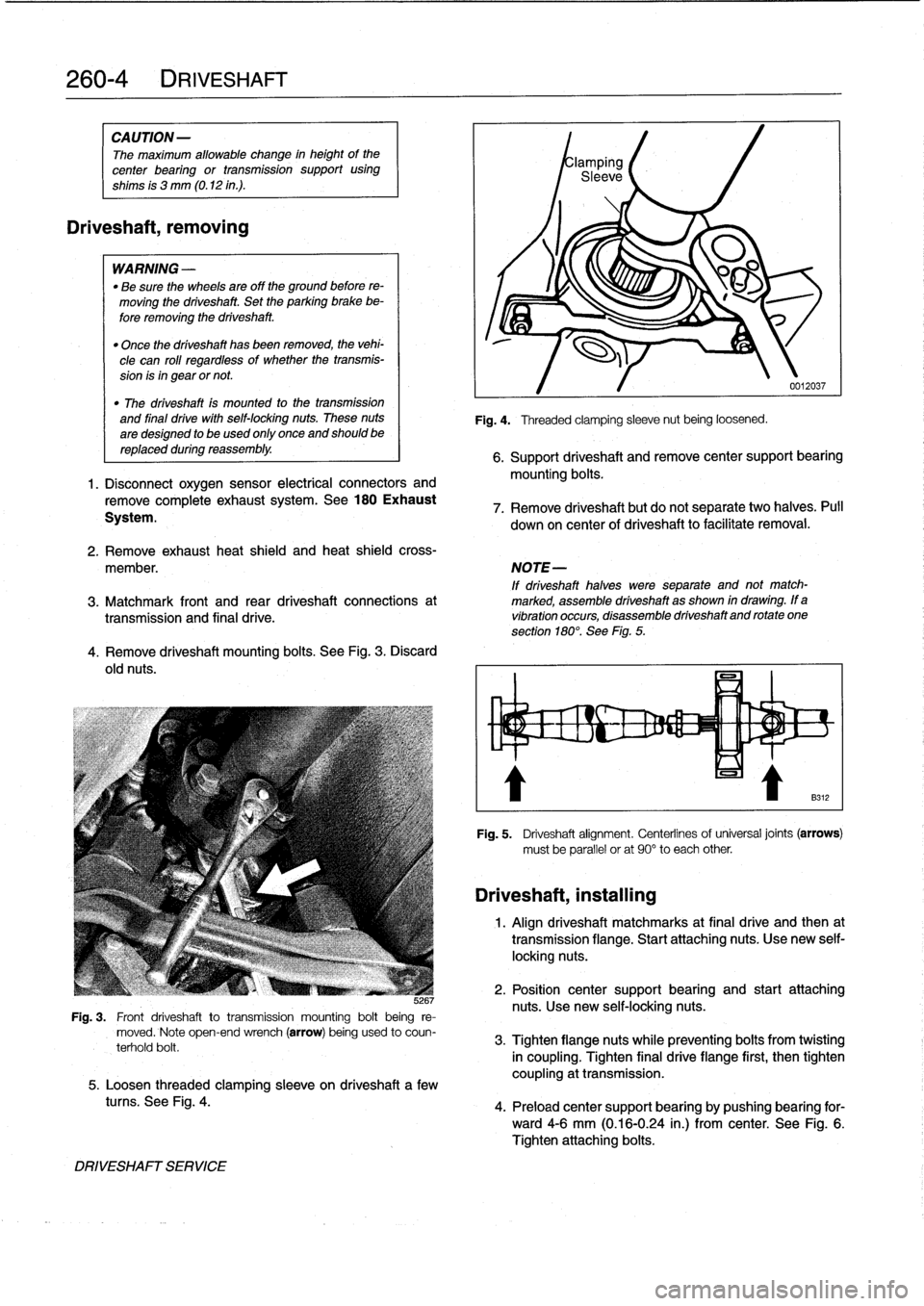
260-
4
DRIVESHAFT
CAUTION
-
The
maximum
allowable
change
in
height
of
the
center
bearing
or
transmission
support
using
shims
is
3
mm
(0
.12
in
.)
.
Driveshaft,
removing
WARNING
-
"
Be
sure
the
wheels
are
off
the
ground
before
re-
moving
the
driveshaft
.
Set
the
parking
brake
be-
fore
removing
the
driveshaft
.
"
Once
the
driveshaft
has
been
removed,
the
vehi-
cle
can
roll
regardless
of
whether
the
transmis-
sion
isin
gear
or
not
.
"
The
driveshaft
fs
mounted
to
thetransmission
and
final
drive
with
self-locking
nuts
.
These
nuts
are
designed
to
be
used
only
once
and
should
be
replaced
during
reassembly
.
1.
Disconnect
oxygen
sensor
electrical
connectors
and
remove
complete
exhaustsystem
.
See
180
Exhaust
System
.
4
.
Remove
driveshaft
mounting
bolts
.
See
Fig
.
3
.
Discard
old
nuts
.
JG
Fig
.
3
.
Front
driveshaft
totransmission
mounting
bolt
being
re-
moved
.
Note
open-end
wrench
(arrow)
being
used
to
coun-
terhold
bolt
.
5
.
Loosen
threaded
clamping
sleeve
on
driveshaft
a
few
tucos
.
See
Fig
.
4
.
DRIVESHAFT
SERVICE
Fig
.
4
.
Threaded
clamping
sleeve
nut
being
loosened
.
0012037
6
.
Support
driveshaft
andremove
center
support
bearing
mounting
bolts
.
7
.
Remove
driveshaft
but
do
not
separate
two
halves
.
Pull
down
on
center
of
driveshaft
to
facilitate
removal
.
2
.
Remove
exhaust
heat
shield
and
heat
shieldcross-
member
.
NOTE-
If
driveshaft
halves
were
separate
and
not
match-
3
.
Matchmark
front
and
rear
driveshaft
connections
at
marked,
assemble
driveshaft
as
shown
in
drawing
.
If
a
transmissíon
and
final
drive
.
vibration
occurs,
disassemble
driveshaftand
rotate
one
section
180°
.
See
Fig
.
5
.
Driveshaft,
installing
Fig
.
5
.
Driveshaft
alignment
.
Centerlinesof
universal
joints
(arrows)
must
be
parallel
or
at
90°
to
each
other
1
.
Align
driveshaft
matchmarks
at
final
drive
and
then
at
transmission
flange
.
Start
attaching
nuts
.
Use
new
self-
locking
nuts
.
2
.
Position
center
support
bearing
and
start
attaching
nuts
.
Use
new
self-locking
nuts
.
3
.
Tighten
flangenuts
while
preventing
bolts
from
twisting
in
coupling
.
Tighten
final
drive
flange
first,
then
tighten
coupling
at
transmission
.
4
.
Preload
center
support
bearing
by
pushing
bearing
for-
ward4-6
mm
(0
.16-0
.24
in
.)
from
center
.
See
Fig
.
6
.
Tighten
attaching
bolts
.
Page 245 of 759
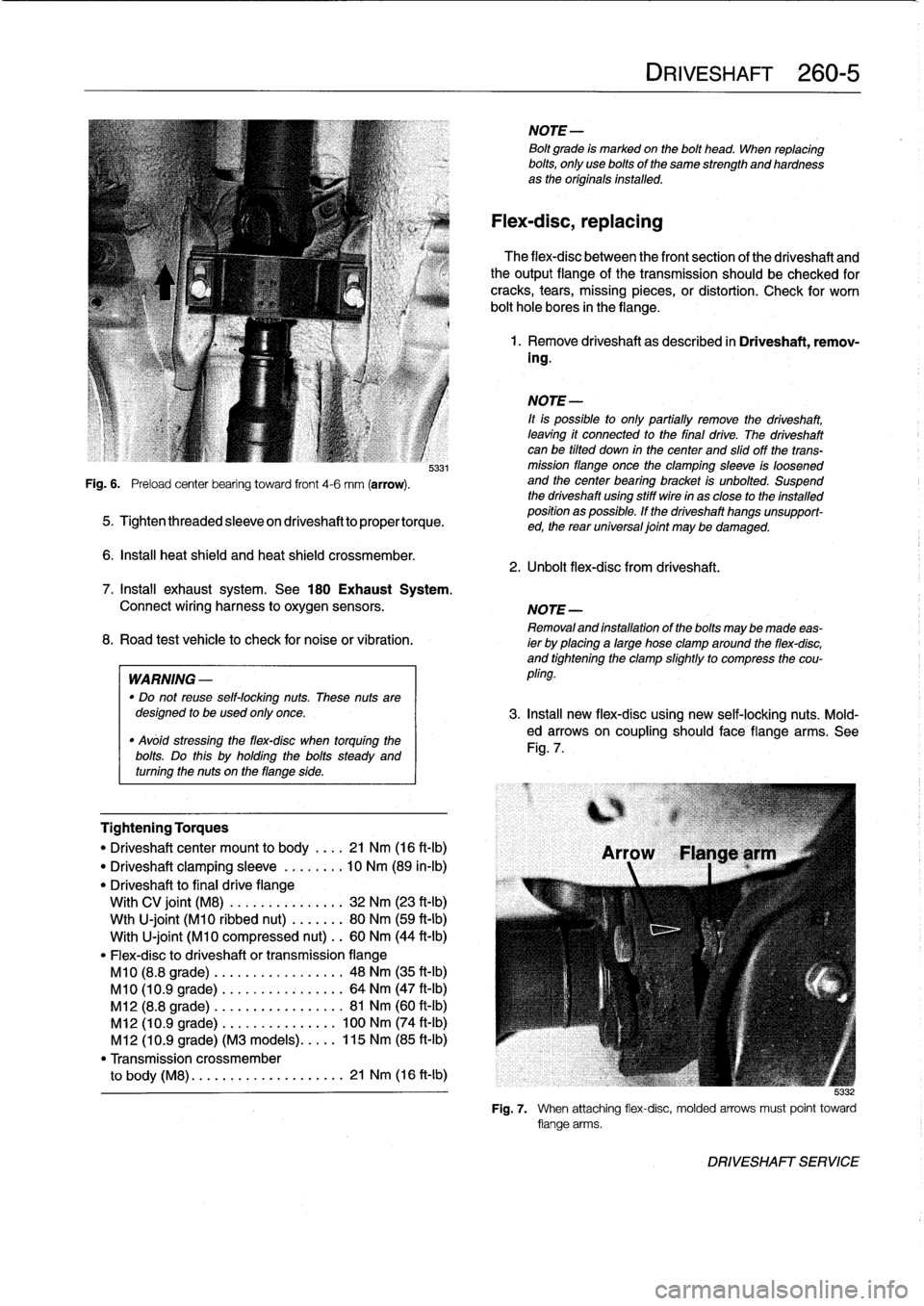
Fig
.
6
.
Preload
center
bearing
toward
front
4-6
mm
(arrow)
.
5331
5
.
Tightenthreadedsleeveondriveshafttopropertorque
.
6
.
Insta¡¡
heat
shield
and
heat
shield
crossmember
.
Tightening
Torques
"
Driveshaftcenter
mount
to
body
.
.
..
21
Nm
(16
ft-Ib)
"
Driveshaft
clamping
sleeve
.....
.
.
.
10
Nm
(89
in-lb)
"
Driveshaft
to
final
drive
flange
With
CV
joint
(M8)
............
...
32
Nm
(23
ft-Ib)
Wth
U-joint
(M10
ribbed
nut)
....
...
80
Nm
(59
ft-Ib)
With
U-joint
(M10
compressed
nut)
..
60
Nm
(44
ft-Ib)
"
Flex-disc
to
driveshaft
or
transmissionflange
M10
(8.8
grade)
.........
.
....
..
.
48
Nm
(35
ft-Ib)
M10
(10
.9
grade)
........
.
....
...
64
Nm
(47
ft-Ib)
M12
(8.8
grade)
........
.....
..
.
.
81
Nm
(60
ft-Ib)
M12
(10
.9
grade)
.
.
....
......
...
100
Nm
(74
ft-Ib)
M12
(10
.9
grade)
(M3
models)
..
.
.
.
115
Nm
(85
ft-Ib)
"
Transmission
crossmember
to
body
(M8)
.
....
...........
....
21
Nm
(16
ft-Ib)
NOTE-
Bolt
grade
is
markedon
the
bolt
head
.
When
replacing
bolts,
only
use
bolts
of
the
same
strength
and
hardnessas
the
originalsinstalled
.
Flex-disc,
replacing
The
flex-disc
between
the
front
section
of
the
driveshaft
and
theoutputflange
of
the
transmission
should
be
checked
for
cracks,
tears,
missing
pieces,
or
distortion
.
Check
for
worn
bolt
hole
bores
in
theflange
.
1
.
Remove
driveshaft
as
described
in
Driveshaft,
remov-
ing
.
NOTE-
¡t
is
possible
to
only
partially
remove
the
driveshaft,
leaving
it
connected
to
the
final
drive
.
The
driveshaft
canbe
tilted
down
in
thecenter
and
slidoff
the
trans-
mission
flange
once
the
clamping
sleeve
is
loosened
and
the
center
bearing
bracket
is
unbolted
.
Suspend
the
driveshaft
using
stiff
wire
in
as
close
to
the
installed
position
as
possible
.
If
the
driveshaft
hangs
unsupport-
ed,
the
rear
universal
joint
may
be
damaged
.
2
.
Unbolt
flex-dísc
from
driveshaft
.
DRIVESHAFT
260-
5
7
.
Install
exhaust
system
.
See
180
Exhaust
System
.
Connect
wiring
harness
to
oxygen
sensors
.
NOTE-
Removaland
installation
of
the
boltsmaybe
made
eas-
8
.
Road
test
vehicle
to
check
for
noiseor
vibration
.
ier
by
placing
a
large
hose
clamp
around
the
flex-disc,
and
tightening
the
clamp
slightlyto
compress
the
cou
WARNING
-
pling
.
"
Do
not
reuse
self-locking
nuts
.
These
nuts
aredesigned
to
beused
only
once
.
3
.
Insta¡¡
new
flex-disc
using
new
self-locking
nuts
.
Mold-
"
Avóid
stressing
the
flex-disc
when
torquing
the
ed
arrows
on
coupling
should
face
flange
arms
.
See
bolts
Do
this
holding
the
bolts
Fig
.
7
.
steady
and
.
uy
turning
the
nuts
on
theflange
side
.
5
:132
Fig
.
7
.
When
attaching
flex-disc,
molded
arrows
must
point
toward
flange
arms
.
DRIVESHAFT
SERVICE
Page 246 of 759
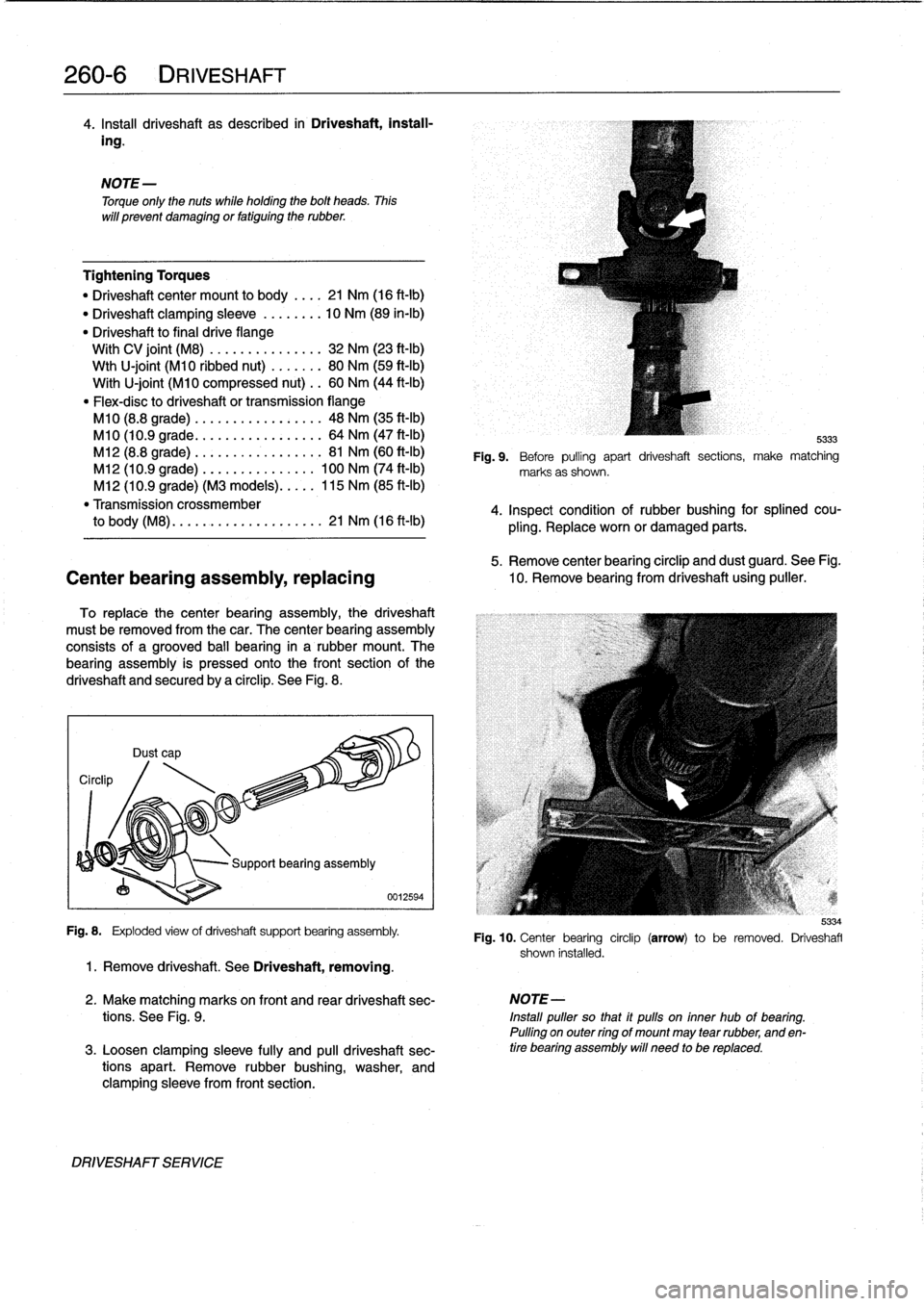
260-
6
DRIVESHAFT
4
.
Insta¡¡
driveshaft
as
described
in
Driveshaft,
install-
ing
.
Tightening
Torques
"
Driveshaft
center
mount
to
body
.
...
21
Nm
(16
ft-Ib)
"
Driveshaft
clamping
sleeve
.....
...
10
Nm
(89
in-lb)
"
Driveshaft
to
final
drive
flange
With
CV
joint
(M8)
............
...
32
Nm
(23
ft-Ib)
Wth
U-joint
(M10
ribbed
nut)
......
.
80
Nm
(59
ft-Ib)
With
U-joint
(M10
compressed
nut)
.
.
60
Nm
(44
ft-Ib)
"
Flex-disc
to
driveshaft
or
transmission
flange
M10
(8
.8
grade)
.
...
.............
48
Nm
(35
ft-Ib)
M10
(10
.9
grade
.
...
.............
64
Nm
(47
ft-Ib)
M12
(8
.8
grade)
..
..
.............
81
Nm
(60
ft-Ib)
M12
(10
.9
grade)
.
..
............
100
Nm
(74
ft-Ib)
M12
(10
.9
grade)
(M3
models)
.....
115
Nm
(85
ft-Ib)
"
Transmission
crossmember
to
body
(M8)
......
...
.
..
........
21
Nm
(16
ft-Ib)
5
.
Remove
center
bearing
circlip
and
dust
guard
.
See
Fig
.
Center
bearing
assembly,
replacing
10
.
Remove
bearing
from
driveshaft
using
puller
.
To
replace
thecenter
bearing
assembly,
the
driveshaft
must
be
removed
from
thecar
.
The
center
bearing
assembly
consists
of
a
grooved
ball
bearing
in
a
rubber
mount
.
The
bearing
assembly
is
pressed
onto
the
front
section
of
the
driveshaft
and
securedby
a
circlip
.
See
Fig
.
8
.
Circlip
NOTE
-
Torque
only
the
nuts
while
holding
the
bolt
heads
.
Thís
will
prevent
damaging
or
fatiguing
the
rubber
.
Dust
cap
Fig
.
8
.
Exploded
view
of
driveshaft
support
bearing
assembly
.
1
.
Remove
driveshaft
.
See
Driveshaft,
removing
.
DRIVESHAFT
SERVICE
0012594
5333
Fig
.
9
.
Before
pulling
apart
driveshaft
sections,
make
matching
marks
as
shown
.
4
.
Inspect
condition
of
rubber
bushing
for
splined
cou-
pling
.
Replace
worn
or
damaged
parts
.
2
.
Make
matching
marks
on
front
and
rear
driveshaft
sec-
NOTE-
tions
.
See
Fig
.
9
.
Install
puller
so
that
it
pulls
on
inner
hub
of
bearing
.
Pulling
on
outer
ring
of
mount
may
tear
rubber,
and
en
3
.
Loosen
clamping
sleeve
fully
and
pull
driveshaft
sec-
tire
bearing
assembly
will
need
to
be
replaced
.
tions
apart
.
Remove
rubber
bushing,
washer,
and
clamping
sleeve
from
front
section
.
5334
Fig
.
10
.
Center
bearing
circlip
(arrow)
to
be
removed
.
Driveshafl
shown
installed
.
Page 247 of 759
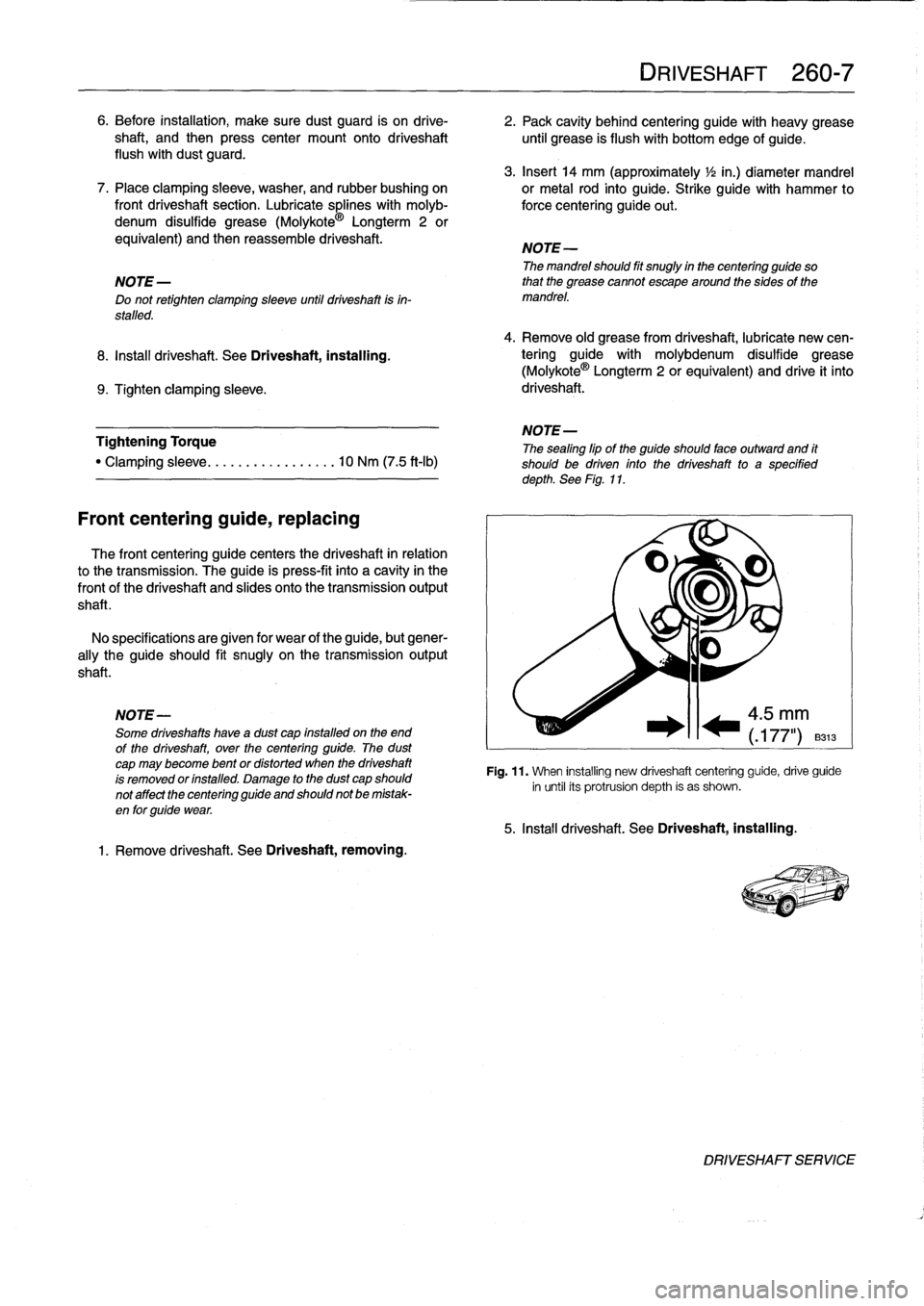
6
.
Before
installation,
make
sure
dust
guard
is
on
drive-
2
.
Pack
cavity
behind
centering
guide
with
heavy
grease
shaft,
and
then
press
center
mount
onto
driveshaft
until
grease
is
flush
with
bottom
edge
of
guide
.
flush
with
dust
guard
.
3
.
Insert
14
mm
(approximately
%z
in
.)
diameter
mandrel
7
.
Place
clamping
sleeve,
washer,
and
rubber
bushing
on
or
metal
rod
finto
guide
.
Strike
guide
with
hammer
to
front
driveshaft
section
.
Lubricate
splines
with
molyb-
force
centering
guide
out
.
denum
disulfide
grease
(Molykote
0
Longterm
2
or
equivalent)
and
then
reassemble
driveshaft
.
NOTE-
The
mandrel
should
fit
snugly
in
thecentering
guideso
NOTE-
that
the
greasecannot
escapearound
the
sides
of
the
Do
not
retighten
clamping
sleeve
until
driveshaft
is
in-
mandrel
.
stalled
.
4
.
Remove
old
greasefrom
driveshaft,
lubricate
new
cen
8
.
Insta¡¡
dríveshaft
.
See
Driveshaft,
installing
.
tering
guide
with
molybdenum
disulfide
grease
(Molykote
®
Longterm2
or
equivalent)
and
drive
it
finto
9
.
Tighten
clamping
sleeve
.
driveshaft
.
NOTE-
Tightening
Torque
The
sealing
lip
of
the
guide
should
face
outward
and
it
"
Clamping
sleeve
.....
...
.
..
......
10
Nm
(7
.5
ft-Ib)
shouldbe
driven
into
the
driveshaft
to
a
specified
depth
.
See
Fig
.
11
.
Front
centering
guide,
replacing
The
front
centering
guide
centers
the
driveshaft
in
relation
to
the
transmission
.
The
guide
is
press-fit
finto
a
cavity
in
the
frontof
the
driveshaft
and
slides
onto
the
transmission
output
shaft
.
No
specifications
are
given
for
wear
of
the
guide,
but
gener-
ally
theguide
should
fit
snugly
on
thetransmissionoutput
shaft
.
NOTE-
Some
driveshafts
have
a
dust
cap
installed
on
the
end
of
the
driveshaft,
over
thecentering
guide
.
The
dust
cap
may
become
bent
or
distorted
when
the
driveshaft
is
removed
or
installed
.
Damage
to
the
dust
capshould
not
affect
the
centering
guide
and
should
not
be
mistak-
en
for
guide
wear
.
1
.
Remove
driveshaft
.
See
Driveshaft,
removing
.
®RIVESHAFT
260-
7
~)I~
4
.5
mm
(
.177")
B313
Fig
.
11
.
When
installing
new
driveshaft
centering
guide,
drive
guide
in
until
its
protrusion
depth
is
as
shown
.
5
.
Install
driveshaft
.
See
Driveshaft,
installing
.
DRIVESHAFT
SERVICE
Page 248 of 759
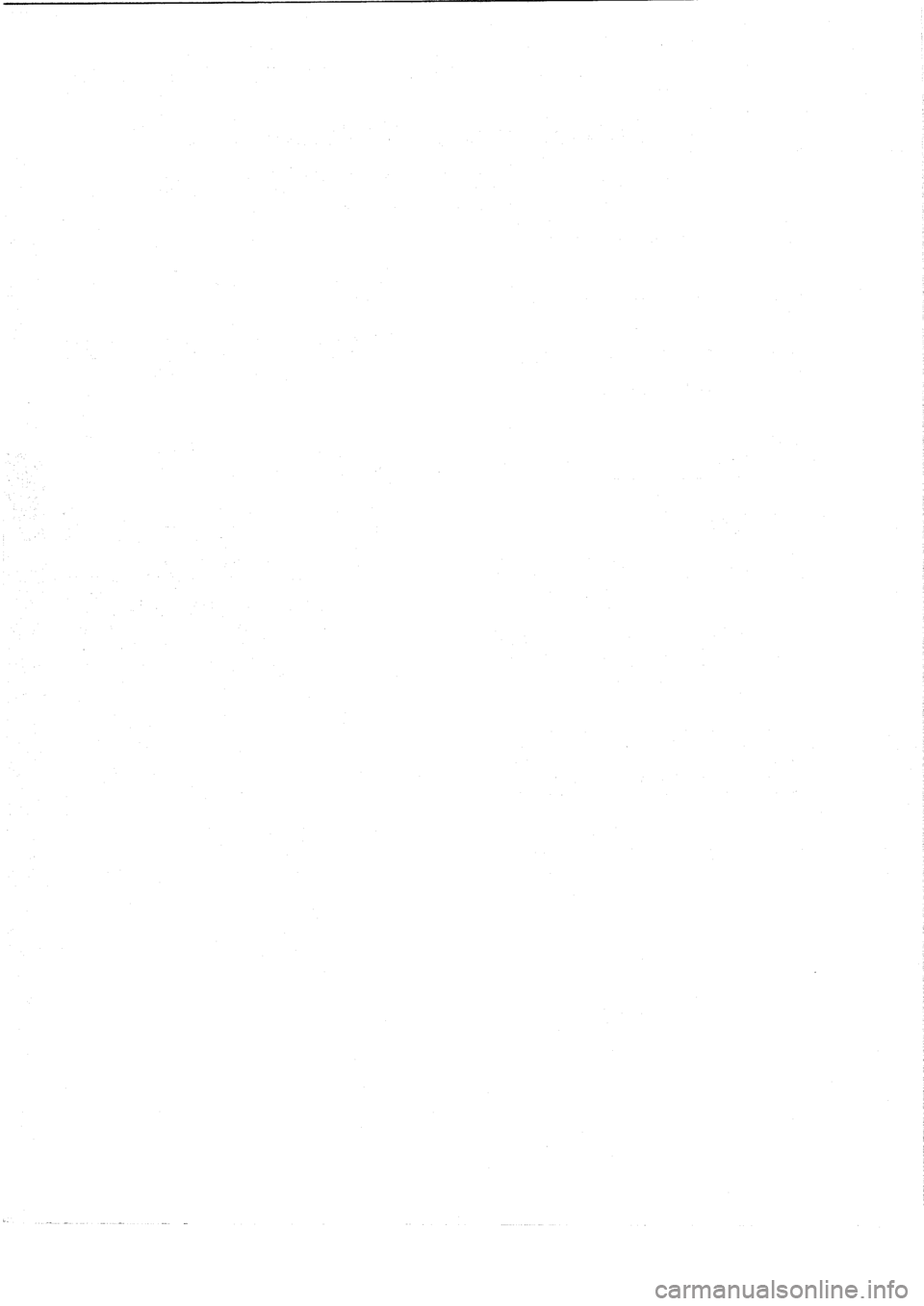
Page 249 of 759
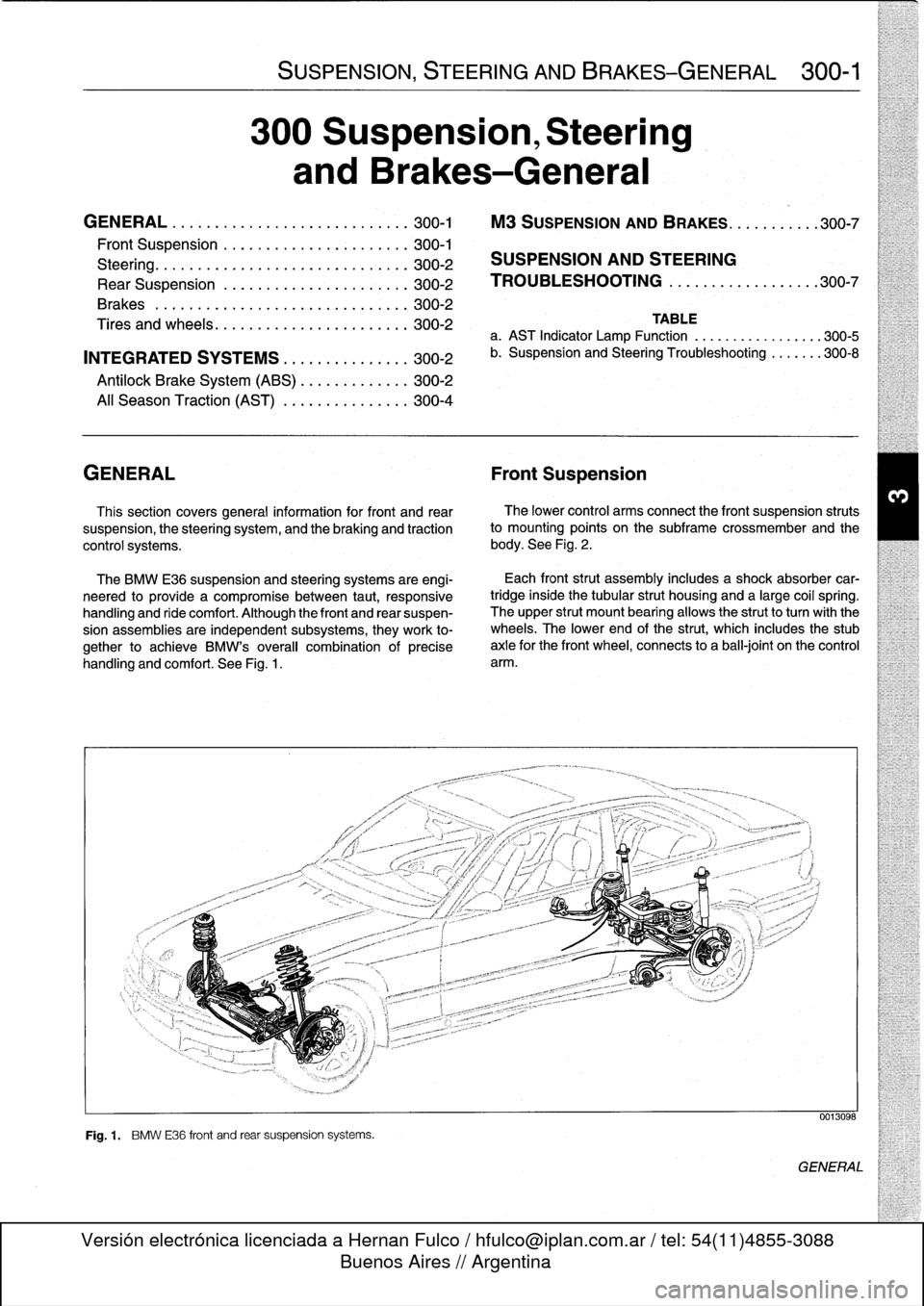
SUSPENSION,
STEERING
ANDBRAKES-GENERAL
300-1
300
Suspension,
Steering
and
Brakes-General
GENERAL
.....
.
....
.
.....
.
.
.
........
.300-1
M3
SUSPENSION
AND
BRAKES
.......
.
...
300-7
Front
Suspension
..........
.
.
.
...
.
.....
300-1
Steering
...
.
.
.
.
.
....
.
.
.
...
.
.
.
...
.
...
.
.
300-2
SUSPENSION
AND
STEERING
Rear
Suspension
....
.
.
.
...
.
.
.
...
.
.....
300-2
TROUBLESHOOTING
..
.
.
.
.............
300-7
Brakes
.
.
.
.
.
.
.
.
....
.
...........
.
.
.
.
.
.
300-2
Tires
and
wheeis
.
................
.
.
.
.
.
.
300-2
TABLE
a
.
AST
Indicator
Lamp
Function
..
..
.
..
.
.........
300-5
INTEGRATED
SYSTEMS
.........
.
.
.
.
.
.
300-2
b
.
Suspension
and
Steering
Troubleshooting
......
.300-8
Antilock
Brake
System
(ABS)
.......
.
.
.
.
.
.
300-2
Al¡
Season
Traction
(AST)
.........
.
.
.
.
.
.
300-4
GENERAL
Front
Suspension
This
section
covers
general
information
for
front
and
rear
The
lower
control
arms
connect
the
front
suspension
struts
suspension,
the
steering
system,
and
the
brakíng
and
traction
to
mounting
points
on
the
subframe
crossmember
and
the
control
systems
.
body
.
See
Fig
.
2
.
The
BMW
E36
suspension
and
steering
systems
are
engi-
neered
to
provide
a
compromise
between
taut,
responsive
handling
and
ride
comfort
.
Although
the
front
and
rear
suspen-
sion
assemblies
are
independent
subsystems,
they
work
to-
gether
to
achieve
BMW's
overall
combination
of
precise
handling
and
comfort
.
See
Fig
.
1
.
Fig
.
1
.
BMW
E36
front
and
rear
suspension
systems
.
Each
front
strut
assembly
includes
a
shock
absorber
car-
tridgeinside
the
tubular
strut
housing
and
a
large
coil
spring
.
The
upper
strut
mount
bearing
allows
the
strutto
turnwith
the
wheels
.
The
lower
end
of
the
strut,
which
includes
the
stub
axle
for
the
front
wheel,
connects
to
a
ball-joint
on
the
control
arm
.
0013098
GENERAL
Page 250 of 759
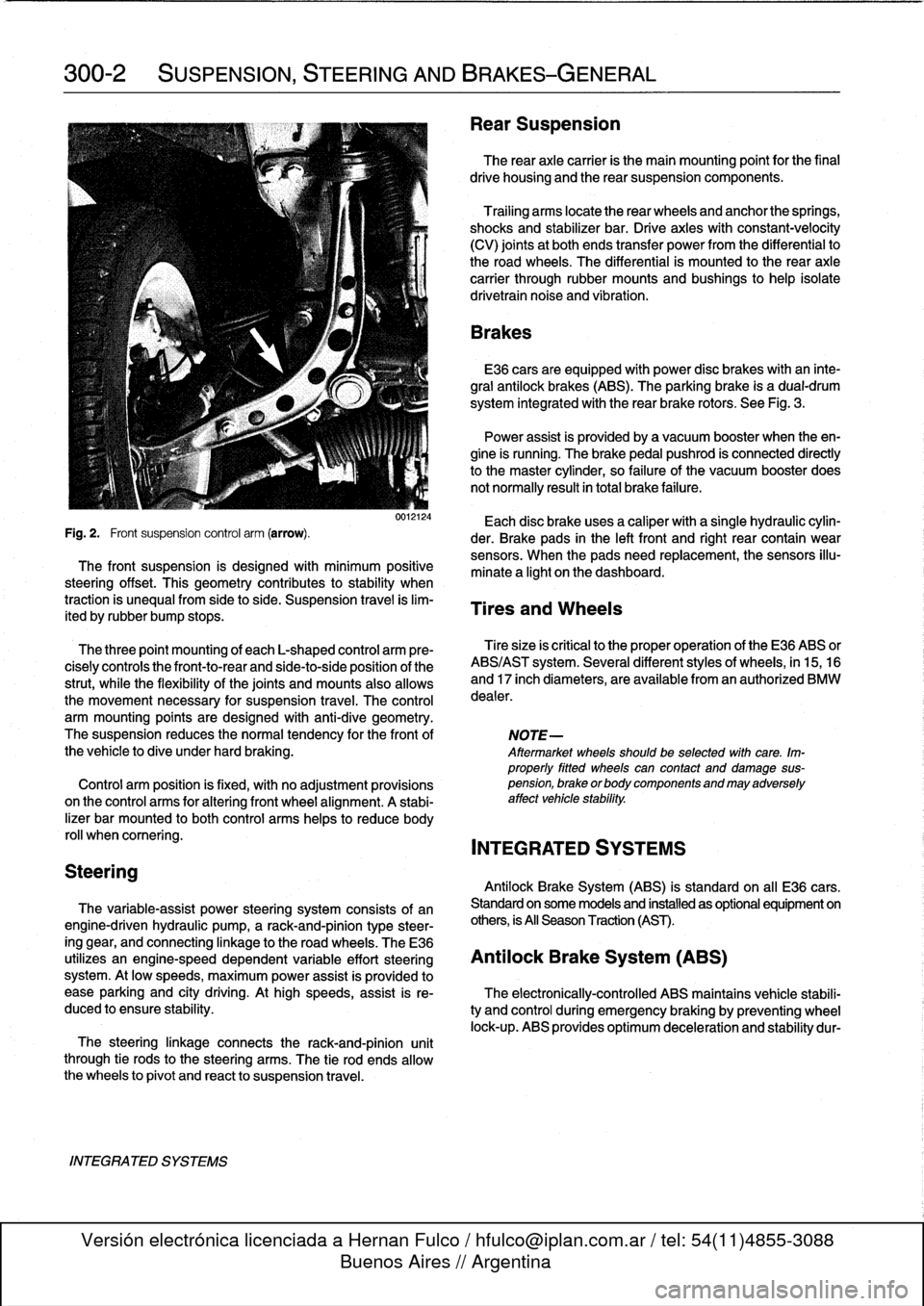
300-2
SUSPENSION,
STEERING
AND
BRAKES-GENERAL
Steering
INTEGRATED
SYSTEMS
The
steering
linkage
connects
the
rack-and-pinion
unit
through
tie
rodsto
the
steering
arms
.
The
tie
rod
ends
allow
the
wheels
to
pivot
and
react
to
suspension
travel
.
Rear
Suspension
The
rear
axle
carrier
is
the
main
mounting
point
for
the
final
drive
housing
and
the
rear
suspension
components
.
Trailing
arms
locatethe
rear
wheels
and
anchorthe
springs,
shocks
and
stabilizer
bar
.
Driveaxies
with
constant-velocity
(CV)
joints
at
both
ends
transfer
power
from
the
differential
to
the
road
wheels
.
The
differential
is
mounted
to
the
rearaxle
carrier
through
rubber
mountsand
bushings
to
hele
isolate
drivetrain
noise
and
vibration
.
Brakes
E36
cars
areequipped
with
power
disc
brakes
with
an
inte-
gral
antilock
brakes
(ABS)
.
The
parking
brake
is
a
dual-drum
system
integrated
with
the
rear
brake
rotors
.
See
Fig
.
3
.
Power
assist
is
provided
by
a
vacuum
booster
when
the
en-
gine
is
running
.
The
brakepedal
pushrod
is
connected
directly
to
the
master
cylinder,
so
failure
of
the
vacuum
booster
does
not
normally
result
in
total
brake
failure
.
0012124
Each
disc
brakeuses
a
caliper
with
a
single
hydraulic
cylin-
Fig
.
2
.
Front
suspension
control
arm
(arrow)
.
der
.
Brake
pads
in
the
left
front
and
right
rear
contain
wear
sensors
.
When
the
padsneed
replacement,the
sensors
illu-
The
front
suspension
is
designed
with
minimum
positive
minate
a
light
on
the
dashboard
.
steering
offset
.
This
geometry
contributes
to
stability
when
traction
is
unequalfrom
side
to
side
.
Suspension
travel
is
lim-
Tires
and
Wheels
ited
by
rubber
bump
stops
.
The
three
point
mounting
of
each
L-shaped
control
arm
ere-
Tiresize
is
critica¡
to
the
proper
operatíon
of
the
E36
ABS
or
cisely
controls
the
front-to-rear
and
side-to-side
position
of
the
ABS/AST
system
.
Severa¡
different
styles
of
wheels,
in
15,16
strut,
while
the
flexibility
of
the
joints
and
mounts
alsoallows
and
17
inch
diameters,
are
available
from
an
authorized
BMW
the
movement
necessary
for
suspension
travel
.
The
control
dealer
.
arm
mounting
points
are
designed
with
anti-dive
geometry
.
The
suspension
reduces
the
normaltendency
for
the
front
of
NOTE-
the
vehicle
to
dive
under
hard
braking
.
Aftermarket
wheelsshould
be
selected
wlth
care
.
Im-
properly
fitted
wheels
can
contact
anddamage
sus
Control
arm
position
is
fixed,
with
no
adjustment
provisions
pension,
brakeorbodycomponentsandmayadversely
on
the
control
arms
for
alter¡ng
front
wheel
al
ignment
.
A
stabi-
affect
vehicle
stability
.
lizer
bar
mounted
to
both
control
arms
heles
to
reduce
body
rol¡
whencomering
.
INTEGRATED
SYSTEMS
Antilock
Brake
System
(ABS)
is
standard
on
all
E36
cars
.
The
variable-assist
power
steering
system
consists
of
an
Standard
on
some
models
and
installed
as
optional
equipment
on
engine-driven
hydraulic
pump,
a
rack-and-pinion
type
steer-
others,
is
All
Season
Traction
(AST)
.
ing
gear,
and
connecting
linkage
to
the
road
wheels
.
TheE36
utilizes
an
engine-speed
dependent
variable
effort
steering
Antilock
Brake
System
(ABS)
system
.
At
low
speeds,
maximum
power
assist
is
provided
to
ease
parking
and
city
driving
.
Athigh
speeds,
assist
is
re-
The
electronically-controlled
ABS
maintains
vehícle
stabili
duced
to
ensure
stability
.
ty
and
control
during
emergency
braking
by
preventing
wheel
lock-up
.
ABS
provides
optimum
deceleration
and
stability
dur-