BMW M3 1992 E36 Workshop Manual
Manufacturer: BMW, Model Year: 1992, Model line: M3, Model: BMW M3 1992 E36Pages: 759
Page 261 of 759
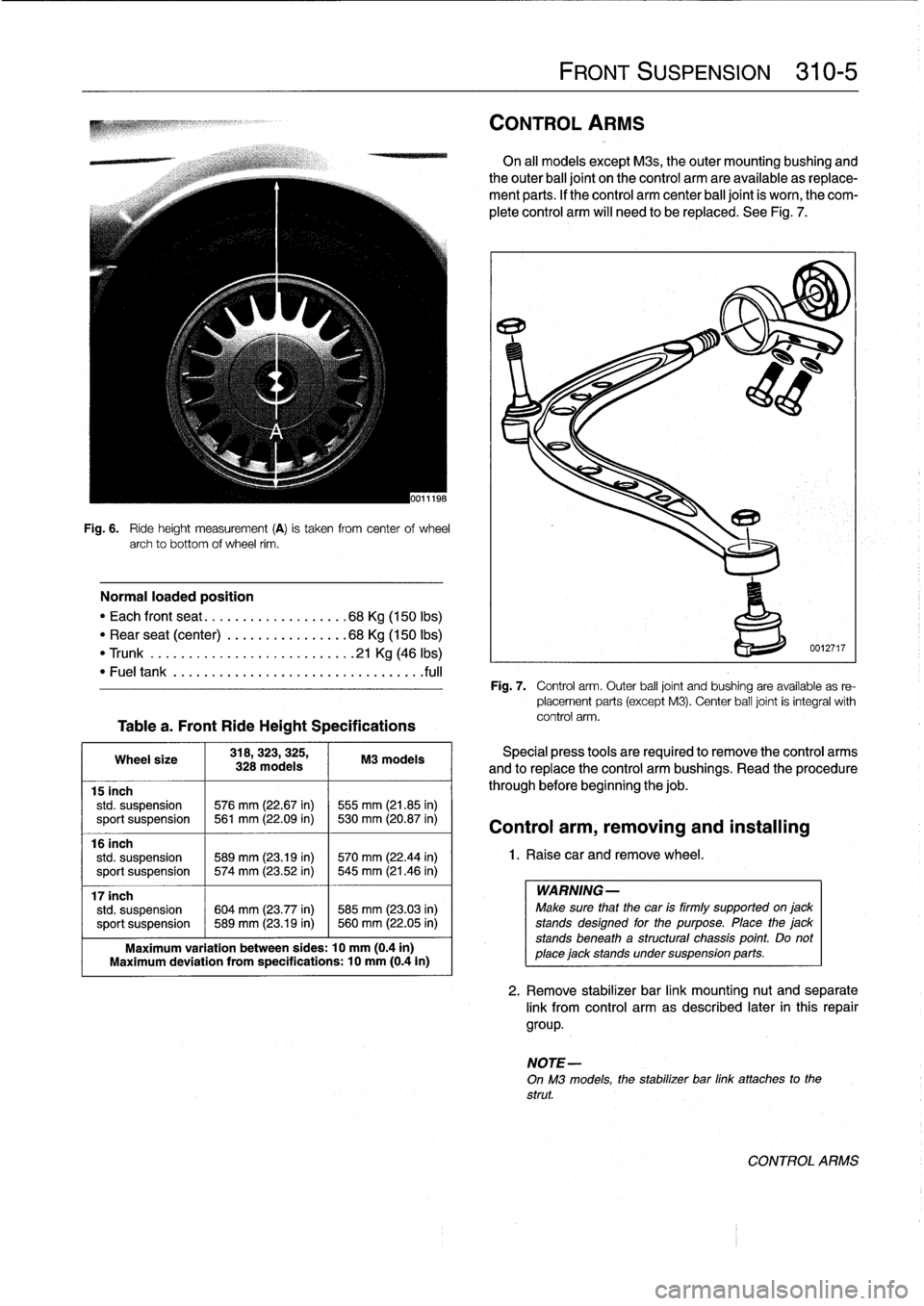
Fig
.
6
.
Ride
height
measurement
(A)
is
taken
from
centerof
wheel
archto
bottom
of
wheel
rim
.
Normal
loaded
position
"
Each
front
seat
...
...
.
..
..........
68Kg
(150
Ibs)
"
Rear
seat
(center)
...
.
.
...........
68Kg
(150
Ibs)
"
Trunk
..........
...
.
.
...........
.21
Kg
(46
lbs)
"
Fuel
tank
...
.
..
....
.
.
....................
.fuf
Tablea
.
Front
RideHeight
Specifications
318,323,325,
Wheel
size
M3
models
328
models
15
inch
std
.
suspension
576
mm
(22.67
in)
1555
mm
(21.85
in)
sport
suspension
~
561
mm
(22.09
in)
530
mm
(20
.87
in)
16
inch
std
.
suspension
589
mm
(23.19
in)
1570
mm
(22
.44
in)
sport
suspensíon
~
574
mm
(23.52
in)
545
mm
(21.46
in)
17
inch
std
.
suspension
604
mm
(23.77
in)
585
mm
(23
.03
in)
sport
suspension
~
589
mm
(23.19
in)
~
560
mm
(22
.05
in)
Maximum
variation
between
sides
:
10
mm
(0.4in)
Maximum
deviation
from
specifications
:
10
mm
(0
.4in)
FRONT
SUSPENSION
310-
5
CONTROL
ARMS
On
al¡
models
except
Mas,
theouter
mounting
bushing
and
theouter
ball
joint
on
the
control
arm
are
available
as
replace-
ment
parts
.
If
the
control
arm
center
ball
joint
is
worn,
the
com-
plete
control
arm
will
need
to
be
replaced
.
See
Fig
.
7
.
Fig
.
7
.
Control
arm
.
Outer
ball
joint
and
bushing
are
available
as
re-
placement
parts
(except
M3)
.
Center
ball
joint
is
integral
with
control
arm
.
Special
press
tools
are
requiredto
remove
the
control
arms
and
to
replace
the
control
arm
bushings
.
Read
the
procedure
through
before
beginning
the
job
.
Control
arm,
removing
and
installing
1
.
Raise
car
and
remove
wheel
.
WARNING-
Make
sure
that
thecar
is
firmly
supportedon
jack
standsdesigned
for
the
purpose
.
Place
the
jack
stands
beneath
a
structural
chassis
point
.
Do
not
place
jack
stands
undersuspension
parts
.
2
.
Remove
stabilizer
bar
link
mounting
nut
and
separate
link
from
control
arm
as
described
later
in
this
repair
group
.
NOTE-
On
M3
models,
the
stabilizer
bar
link
attaches
to
the
strut
.
CONTROL
ARMS
Page 262 of 759
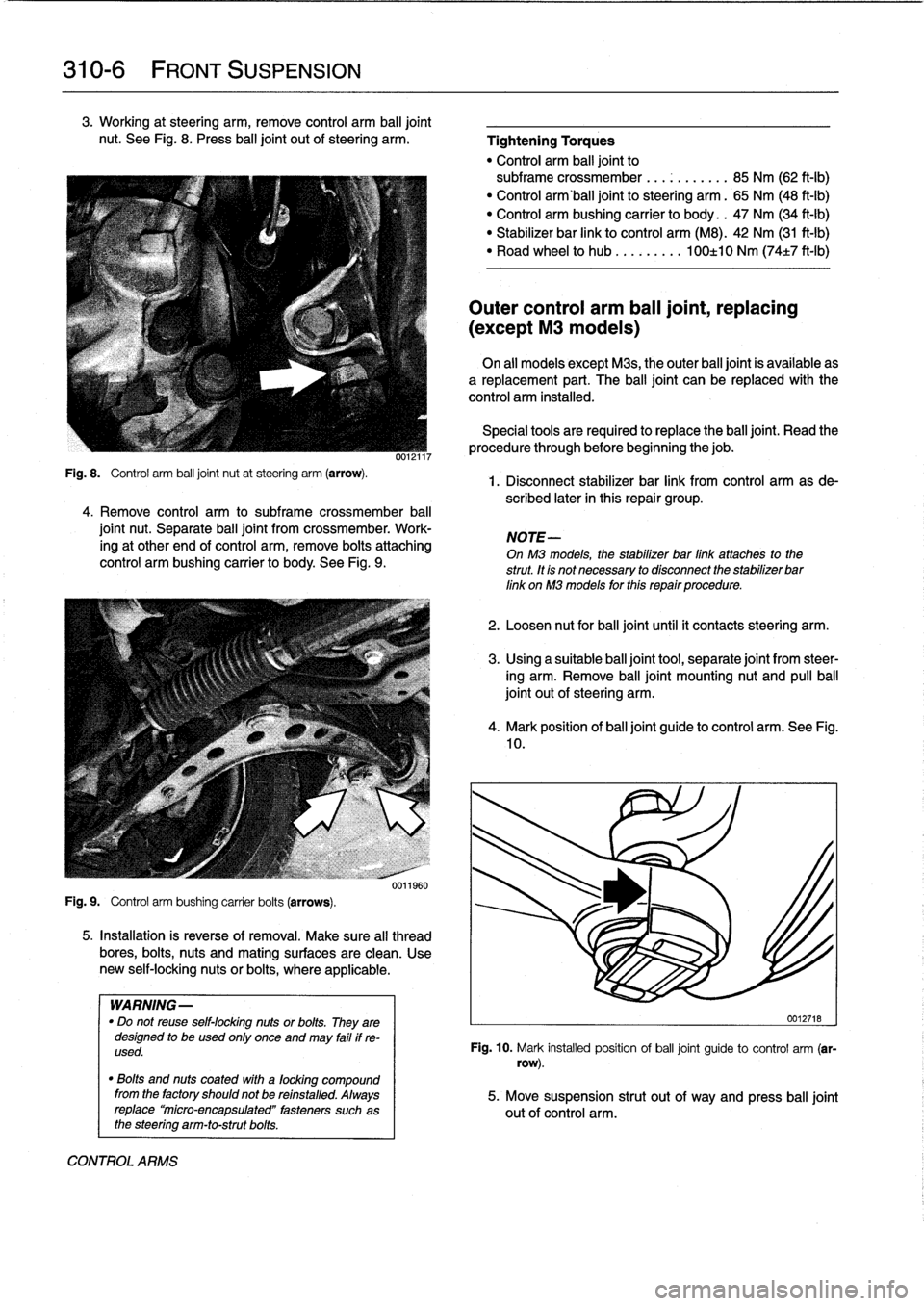
310-
6
FRONT
SUSPENSION
3
.
Working
at
steering
arm,
remove
control
arm
balljoint
nut
.
See
Fig
.
8
.
Press
ball
joint
out
ofsteering
arm
.
Fig
.
8
.
Control
arm
ball
joint
nut
at
steering
arm
(arrow)
.
4
.
Remove
control
arm
to
subframe
crossmember
ball
joint
nut
.
Separate
ball
joint
from
crossmember
.
Work-
ing
at
other
end
of
control
arm,
remove
bolts
attaching
control
arm
bushing
carrier
to
body
.
See
Fig
.
9
.
Fig
.
9
.
Control
arm
bushing
carrier
bolts
(arrows)
.
0012117
0011960
5
.
Installation
is
reverse
of
removal
.
Make
sure
al¡
thread
bores,
bolts,
nuts
and
mating
surfaces
are
clean
.
Use
new
self-locking
nutsor
bolts,
where
applicable
.
WARNING-
"
Do
not
reuse
self-locking
nuts
or
bolts
.
They
are
designed
to
be
used
only
once
and
may
failif
re-
used
.
"
Bolts
and
nuts
coated
with
a
focking
compound
from
the
factory
shouldnot
be
refnstalled
.
Always
replace`micro-encapsulated"
fasteners
such
as
the
steering
arm-to-strutbolts
.
CONTROL
ARMS
Tightening
Torques
"
Control
arm
balljoint
to
subframe
crossmember
.
..
...
...
.
.
85
Nm
(62
ft-Ib)
"
Control
arm'ball
joint
to
steering
arm
.
65
Nm
(48
ft-Ib)
"
Control
arm
bushing
carrier
to
body
.
.
47
Nm
(34
ft-Ib)
"
Stabilizer
bar
link
to
control
arm
(M8)
.
42
Nm
(31
ft-Ib)
"
Road
wheel
to
hub
.
...
...
.
.
100±10
Nm
(74±7
ft-Ib)
Outer
control
arm
ball
joint,
replacing
(except
M3
models)
On
all
models
except
Mas,
the
outer
balljoint
is
available
as
a
replacement
part
.
The
ball
joint
can
be
replaced
with
the
control
arm
installed
.
Special
tools
are
requiredto
replace
the
balljoínt
.
Read
the
procedure
through
before
beginning
thejob
.
1
.
Disconnect
stabilizer
bar
link
from
control
arm
asde-
scribed
later
in
this
repair
group
.
NOTE-
On
M3
models,
the
stabilizer
bar
link
attaches
to
the
strut
.
tt
fs
not
necessary
to
disconnect
the
stabilizer
bar
link
on
M3
models
for
thfs
repair
procedure
.
2
.
Loosen
nut
for
balljointuntil
it
contacts
steering
arm
.
3
.
Using
a
suitable
ball
joint
tool,
separate
joint
from
steer-
íng
arm
.
Remove
ball
joint
mounting
nut
and
pullball
joint
out
of
steering
arm
.
4
.
Mark
position
of
balljoint
guide
to
control
arm
.
See
Fig
.
10
.
0012718
Fig
.
10
.
Mark
installed
position
of
ball
joint
guide
to
control
arm
(sr-
row)
.
5
.
Move
suspension
strut
out
of
way
and
press
ball
joint
out
of
control
arm
.
Page 263 of 759
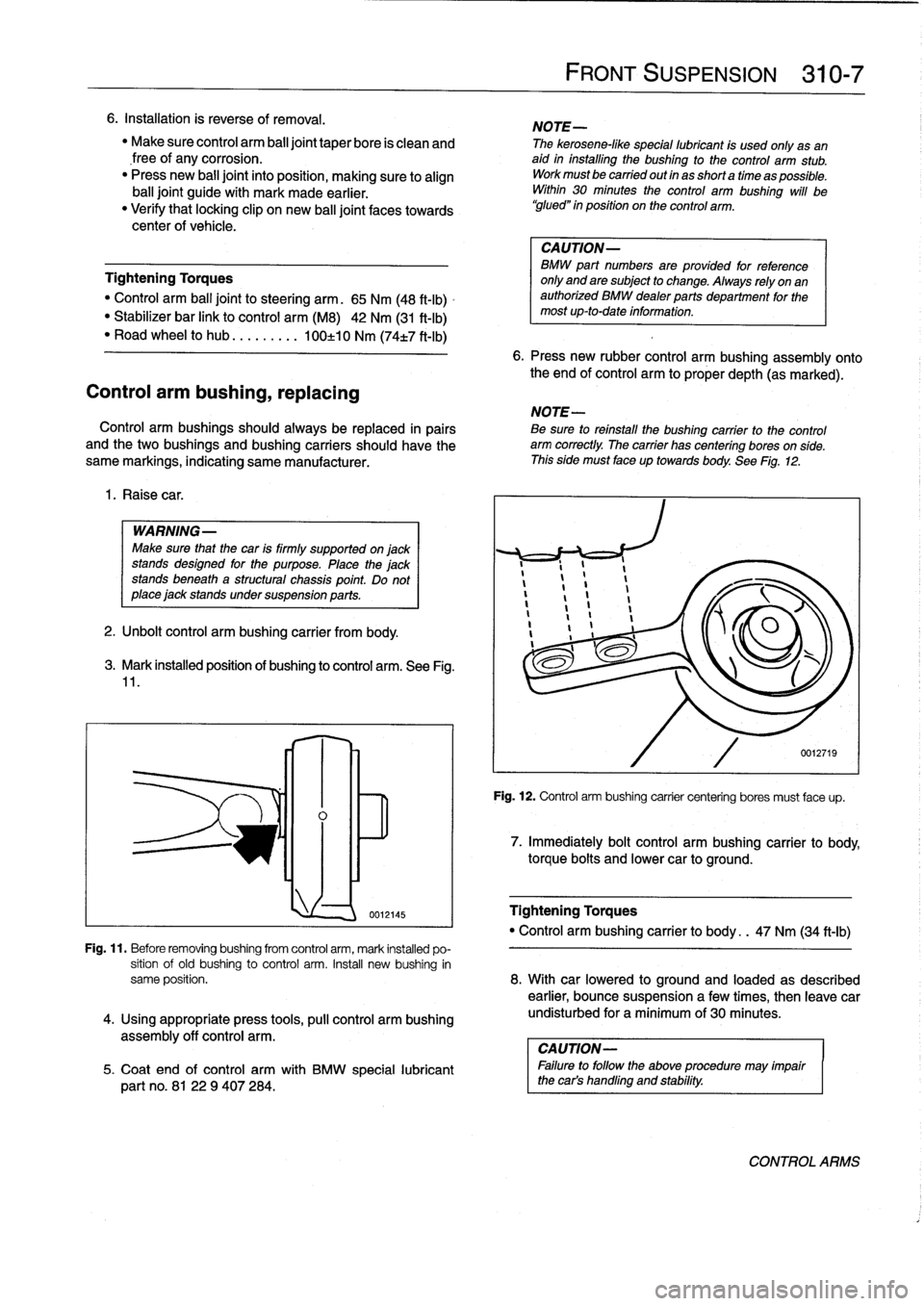
6
.
Installation
is
reverse
of
removal
.
"
Make
sure
control
arm
ball
joint
taper
bore
is
clean
and
free
of
any
corrosion
.
"
Press
new
balljoint
into
position,
making
sure
to
align
balljoint
guide
with
mark
made
earlier
.
"
Verify
that
locking
clip
on
new
ball
joint
faces
towards
center
of
vehicle
.
Tightening
Torques
"
Control
arm
ball
jointto
steering
arm
.
65
Nm
(48
ft-Ib)
"
Stabilizer
bar
link
to
control
arm
(M8)
42
Nm
(31
ft-Ib)
"
Road
wheel
to
hub
.
...
...
.
.
100±10
Nm
(74t7
ft-lb)
Control
arm
bushing,
replacing
Control
arm
bushings
should
aiways
be
replaced
in
pairs
and
the
two
bushings
and
bushing
carriers
should
have
the
same
markings,
indicating
same
manufacturer
.
1
.
Raisecar
.
WARNING-
Make
sure
that
the
car
is
firmly
supportedonjackstandsdesigned
for
the
purpose
.
Place
the
jackstands
beneath
a
structural
chassis
point
.
Do
not
place
jack
stands
undersuspension
parts
.
2
.
Unbolt
control
arm
bushing
carrier
from
body
.
3
.
Mark
installed
position
of
bushing
to
control
arm
.
See
Fig
.
11
.
assembly
off
control
arm
.
lnl~
0012145
FRONT
SUSPENSION
310-
7
NOTE-
The
kerosene-like
special
lubricant
is
used
only
asan
aid
in
installing
the
bushing
to
the
control
arm
stub
.
Workmustbe
carried
out
in
as
short
a
time
as
possible
.
Within
30
minutes
the
control
arm
bushing
will
be
`glued"
in
position
on
the
control
arm
.
CAUTION-
BMW
part
numbers
areprovided
for
reference
only
and
are
subject
to
change
.
Always
rely
on
an
authorized
BMW
dealerparts
department
for
the
most
up-to-date
information
.
6
.
Press
new
rubber
control
arm
bushing
assembly
onto
the
end
of
control
arm
to
proper
depth
(as
marked)
.
NOTE-
Be
sure
toreinstall
the
bushing
carrier
to
the
control
arm
correctly
.
The
carrier
has
centering
bores
on
side
.
This
side
must
face
up
towards
body
.
See
Fig
.
12
.
Fig
.
12
.
Control
arm
bushing
carrier
centering
bores
must
face
up
.
7
.
Immediately
bolt
control
arm
bushing
carrier
to
body,
torque
boits
and
lower
car
to
ground
.
Tightening
Torques
"
Control
arm
bushing
carrier
to
body
.
.
47
Nm
(34
ft-ib)
Fig
.
11
.
Before
removingbushing
from
control
arm,
mark
installed
po-
sition
of
old
bushing
to
control
arm
.
Insta¡¡
new
bushing
in
same
position
.
8
.
With
car
lowered
to
ground
and
loaded
as
described
earlier,
bounce
suspensiona
few
times,
then
leave
car
4
.
Using
appropriate
press
tools,
pull
control
arm
bushing
undisturbed
for
a
minimum
of
30
minutes
.
CAUTION-
5
.
Coat
end
of
control
arm
with
BMW
special
lubricant
I
Failure
to
follow
the
above
procedure
may
impair
part
no
.
8122
9
407284
.
the
car's
handling
and
stability
.
CONTROLARMS
Page 264 of 759
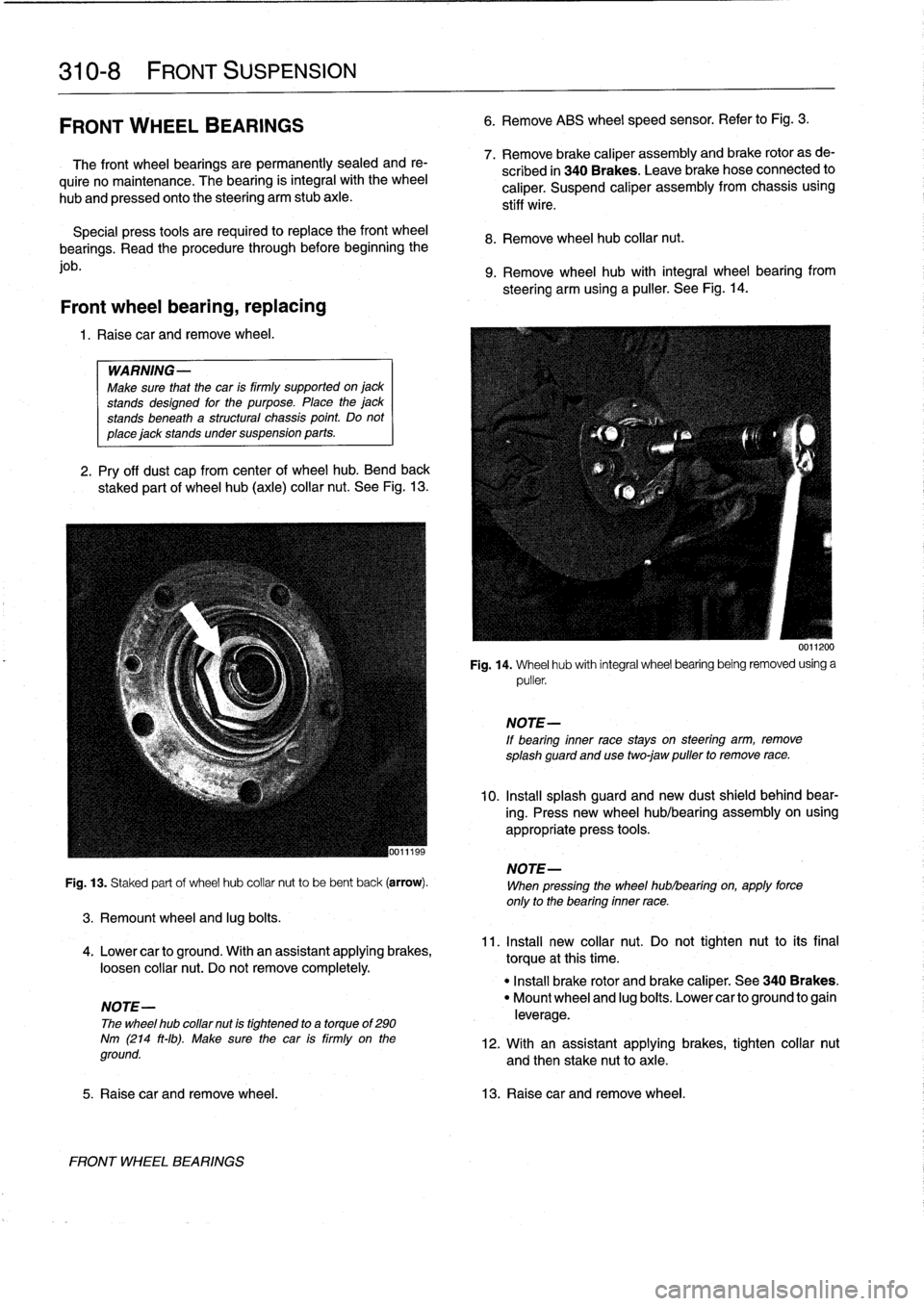
310-
8
FRONT
SUSPENSION
FRONT
WHEEL
BEARINGS
The
front
wheel
bearings
are
permanently
sealed
and
re-
quire
no
maintenance
.
The
bearing
is
integral
with
the
wheel
hub
and
pressed
onto
the
steering
arm
stub
axle
.
Special
press
tools
are
requiredto
replace
the
front
wheel
bearings
.
Read
the
procedure
through
before
beginning
the
job
.
Front
wheel
bearing,
replacing
1
.
Raise
car
and
remove
wheel
.
WARNING-
Make
sure
that
the
car
is
firmly
supportedon
jack
stands
designed
for
the
purpose
.
Place
the
jack
stands
beneatha
structural
chassis
point
.
Do
not
place
jack
stands
under
suspension
parts
.
2
.
Pry
off
dust
cap
from
centerof
wheel
hub
.
Bend
back
staked
part
of
wheel
hub
(axle)
collar
nut
.
See
Fig
.
13
.
Fig
.
13
.
Staked
part
of
wheel
hub
collar
nut
to
be
bent
back
(arrow)
.
3
.
Remount
wheel
and
lug
bolts
.
4
.
Lower
canto
ground
.
With
an
assistant
applying
brakes,
loosen
collar
nut
.
Do
not
remove
completely
.
NOTE-
The
wheel
hub
collar
nut
is
tightened
to
a
torque
of
290
Nm
(214
ft-Ib)
.
Make
sure
the
car
is
firmly
on
the
ground
.
FRONT
WHEEL
BEARINGS
6
.
Remove
ABS
wheel
speed
sensor
.
Refer
to
Fig
.
3
.
7
.
Remove
brake
caliper
assembly
and
brake
rotor
as
de-
scribed
in
340
Brakes
.
Leave
brakehose
connected
to
caliper
.
Suspend
caliper
assembly
from
chassis
using
stiff
wire
.
8
.
Remove
wheel
hub
collar
nut
.
9
.
Remove
wheel
hub
with
integral
wheel
bearing
from
steering
arm
using
a
puller
.
See
Fig
.
14
.
0011200
Fig
.
14
.
Wheel
hub
with
integral
wheel
bearing
being
removed
using
a
puller
.
NOTE-
If
bearing
inner
race
stays
on
steering
arm,
remove
splash
guard
and
usetwo
jaw
puller
to
remove
race
.
10
.
Insta¡¡
splash
guard
and
new
dust
shield
behind
bear-
ing
.
Press
new
wheel
hub/bearing
assembly
on
using
appropriate
press
tools
.
NOTE-
When
pressing
the
wheel
hublbearing
on,
apply
force
only
to
the
bearing
inner
race
.
11
.
Install
new
collar
nut
.
Do
not
tighten
nut
to
its
final
torque
atthis
time
.
"
Install
brake
rotor
and
brake
caliper
.
See
340
Brakes
.
"
Mount
wheel
and
lug
boits
.
Lower
canto
ground
to
gain
leverage
.
12
.
With
an
assistant
applying
brakes,
tighten
collar
nut
and
then
stake
nut
toaxle
.
5
.
Raise
car
and
remove
wheel
.
13
.
Raisecar
and
remove
wheel
.
Page 265 of 759
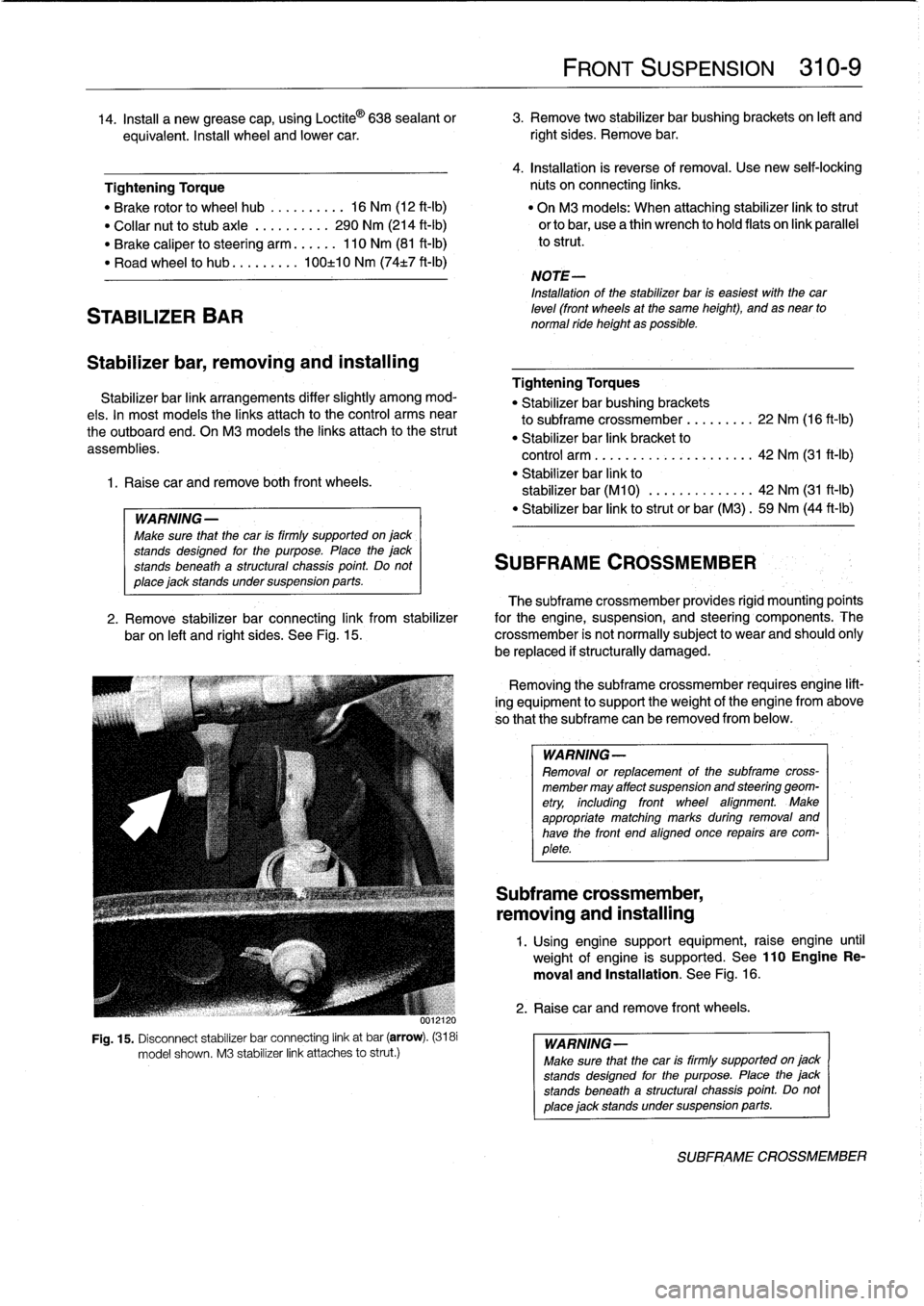
STABILIZER
BAR
Stabilizer
bar,
removing
and
installing
Stabilizer
bar
link
arrangements
differ
slightly
among
mod-
els
.
In
most
models
the
links
attach
lo
the
control
arms
near
the
outboard
end
.
OnM3
models
the
links
attach
lo
the
strut
assemblies
.
1
.
Raise
car
and
remove
both
front
wheels
.
WARNING
-
Make
sure
that
the
car
is
firmly
supported
on
jack
stands
desígned
for
the
purpose
.
Place
the
jack
stands
beneath
a
structural
chassís
point
.
Do
not
place
jack
stands
under
suspension
parts
.
uul
Fig
.
15
.
Disconnect
stabilizer
bar
connecting
link
at
bar
(arrow)
.
(3181
model
shown
.
M3
stabilizer
link
attaches
lo
strut
.)
FRONT
SUSPENSION
310-
9
14
.
Insta¡¡
a
new
grease
cap,
using
Loctite
©
638
sealant
or
3
.
Remove
two
stabilizer
bar
bushing
brackets
on
left
and
equivalent
.
Insta¡¡
wheel
and
lower
car
.
right
sides
.
Remove
bar
.
4
.
Installation
is
reverse
of
removal
.
Use
new
seif-lockíng
Tightening
Torque
núts
on
connecting
links
.
"
Brake
rotor
lo
wheel
hub
..........
16
Nm
(12
ft-Ib)
"
On
M3
models
:
When
attaching
stabilizer
link
lostrut
"
Collar
nut
lo
stubaxle
.
.........
290
Nm
(214
ft-Ib)
orlobar,
usea
thin
wrench
lo
hold
flats
on
link
parallel
"
Brake
caliper
losteering
arm
......
110
Nm
(81
ft-Ib)
lo
strut
.
"
Road
wheel
lo
hub
...
...
.
.
.
100±10
Nm
(74t7
ft-Ib)
NOTE-
Installation
of
the
stabilizer
bar
is
easiest
with
thecar
leve¡
(front
wheels
at
the
same
height),
and
as
near
to
normal
ride
height
as
possible
.
Tightening
Torques
"
Stabilizer
bar
bushing
brackets
lo
subframe
crossmember
...
..
.
..
.
22
Nm
(16
ft-Ib)
"
Stabilizer
bar
link
bracket
lo
control
arm
................
.
.
.
.
.
42
Nm
(31
ft-1b)
"
Stabilizer
bar
link
lo
stabilizer
bar
(M10)
.............
.
42
Nm
(31
ft-Ib)
"
Stabilizer
bar
link
lostrut
or
bar
(M3)
.
59
Nm
(44
ft-Ib)
SUBFRAME
CROSSMEMBER
The
subframe
crossmember
provides
rigid
mounting'poínts
2
.
Remove
stabilizer
bar
connecting
link
from
stabilizer
for
the
engine,
suspension,
and
steering
components
.
The
baron
left
and
right
sides
.
See
Fig
.
15
.
crossmember
is
not
normally
subject
lo
wear
and
should
ohly
be
replaced
if
structurally
damaged
.
Removing
the
subframe
crossmember
requires
engine
lift-
ing
equipment
lo
support
theweight
of
tfhe
engine
from
above
so
that
the
subframe
can
be
removed
from
below
.
WARNING-
Removal
or
replacement
of
the
subframe
cross-
member
may
affect
suspension
and
steering
geom-
etry,
including
front
wheel
afignment
.
Make
appropriate
matching
marks
during
removal
and
have
the
front
end
aligned
once
repairs
are
com-
plete
.
Subframe
crossmember,
removing
and
installing
1
.
Using
enginesupport
equipment,
raise
engine
until
weight
of
engine
is
supported
.
See
110EngineRe-
moval
and
Installation
.
See
Fig
.
16
.
2
.
Raise
car
andremove
front
wheels
.
WARNING-
Make
sure
that
the
car
is
firmly
supportedon
jack
stands
desígned
for
the
purpose
.
Place
the
jack
stands
beneatha
structural
chassís
point
Do
not
place
jack
standsundersuspension
parts
.
SUBFRAME
CROSSMEMBER
Page 266 of 759
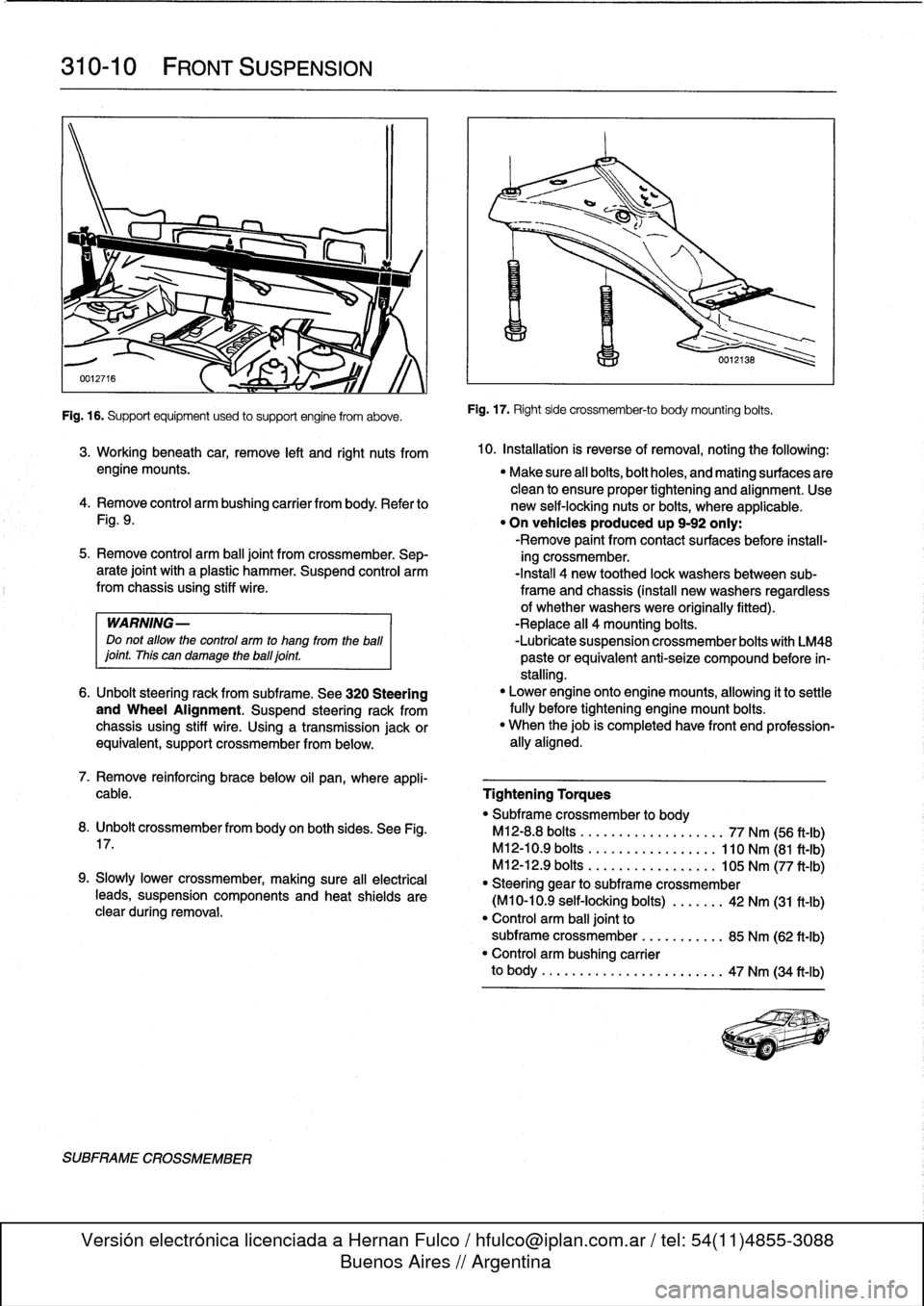
310-
1
0
FRONT
SUSPENSION
Fig
.
16
.
Supportequipment
used
to
support
engine
from
aboye
.
SUBFRAME
CROSSMEMBER
Fig
.
17
.
Right
side
crossmember-to
body
mounting
bolts
.
3
.
Working
beneath
car,
remove
left
and
right
nuts
from
10
.
Installation
is
reverse
ofremoval,
noting
the
followíng
:
engine
mounts
.
"
Make
sure
all
bolts,bolt
holes,
and
mating
surfaces
are
clean
to
ensure
proper
tightening
and
alignment
.
Use
4
.
Remove
control
arm
bushing
carrier
from
body
.
Refer
to
new
self-locking
nuts
or
bolts,
where
applicable
.
Fig
.
9
.
"
On
vehicles
produced
up
9-92
only
:
-Remove
paint
from
contact
surfaces
before
ínstall-
5
.
Remove
control
arm
ball
joint
from
crossmember
.
Sep-
ing
crossmember
.
arate
joint
with
a
plastic
hammer
.
Suspend
control
arm
-Install
4
new
toothed
lock
washersbetween
sub-from
chassis
using
stiff
wire
.
frame
and
chassis
(install
new
washers
regardless
of
whether
washers
were
originally
fitted)
.
WARNING-
-Replace
all
4
mounting
bolts
.
Do
not
allow
the
control
arm
to
hang
from
the
ball
-Lubrícate
suspension
crossmember
bolts
with
LM48
¡oint
.
This
can
damage
theball¡oint
.
paste
orequivalent
anti-seize
compound
before
ín-
stalling
.
6
.
Unbolt
steering
rack
from
subframe
.
See
320
Steering
"
Lower
engine
onto
enginemounts,
allowing
it
to
settle
and
Wheel
Alignment
.
Suspend
steering
rack
from
fully
before
tightening
engine
mount
bolts
.
chassis
using
stiff
wire
.
Using
a
transmission
jackor
"
When
thejob
is
completed
have
front
end
profession-
equivalent,
support
crossmember
from
below
.
ally
aligned
.
7
.
Remove
reinforcing
brace
below
oil
pan,
where
appli-
cable
.
Tightening
Torques
"
Subframe
crossmember
to
body
8
.
Unbolt
crossmemberfrom
body
on
both
sides
.
See
Fig
.
M12-8
.8
bolts
..................
.
77
Nm
(56
ft-Ib)
17
.
M12-10
.9
bolts
.................
110
Nm
(81
ft-Ib)
M12-12
.9
bolts
............
.
...
.
105
Nm
(77
ft-Ib)
9
.
Slowly
Lower
crossmember,
making
sure
all
electrical
"
Steering
gear
to
subframe
crossmember
teads,
suspension
components
and
heat
shields
are
(M10-10
.9
self-locking
bolts)
..
.
.
.
.
.
42
Nm
(31
ft-Ib)
clear
during
removal
.
"
Control
arm
balljoint
to
subframe
crossmember
...
.......
.
85
Nm
(62
ft-Ib)
"
Control
arm
bushing
carrier
to
body
..........
...
.
.....
.
..
..
47
Nm
(34
ft-Ib)
Page 267 of 759
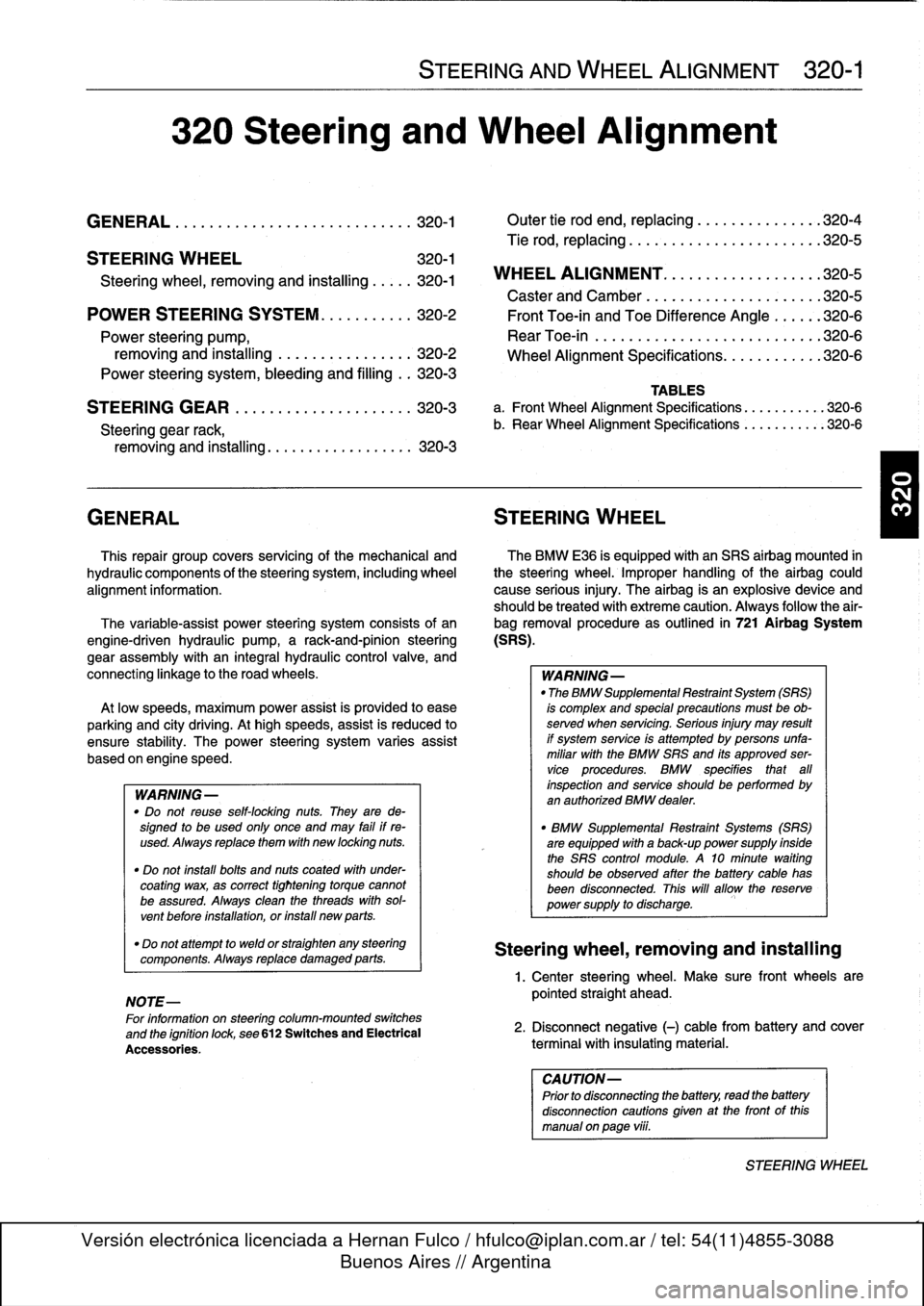
320
Steering
and
Wheel
Alignment
GENERAL
...
.
.
.
...
.
....
.
.
.
.
.
.
.
.
.
...
.
.
320-1
Outer
tie
rod
end,
replacing
.
...
.
.
.
.
.
.
.
...
.
320-4
Tie
rod,
replacing
.
.
.
.
.
.
.
.......
.
.
.
.
.
...
.
320-5
STEERING
WHEEL
320-1
Steering
wheel,
removing
and
installing
.....
320-1
WHEEL
ALIGNMENT
.
.
.
.........
.
.....
.320-5
POWER
STEERING
SYSTEM
.
.
.
.
.
.
.....
320-2
Front
Toe-in
and
Toe
Difference
Angle
.
.
...
.
320-6
Power
steering
pump,
Rear
Toe-in
.
.
.
.
.
.
.
...
.
................
320-6
removing
and
installing
..
.
.
.
.
.
.
.
.
.
.....
320-2
Wheel
Alignment
Specifications
.....
.
......
320-6
Power
steering
system,
bleeding
and
filling
.
.
320-3
STEERING
GEAR
.
.
.
.
...
.
.
.
.
.
.
.
.
.
.....
320-3
Steering
gear
rack,
removing
and
installing
.
...
.
..
.
..
..
..
.
..
.
320-3
GENERAL
STEERING
WHEEL
This
repair
group
covers
servicing
of
the
mechanical
and
The
BMW
E36
is
equipped
with
an
SRS
airbag
mounted
in
hydraulic
components
of
the
steering
system,
including
wheel
the
steering
wheel
.
Improper
handling
of
the
airbag
could
alignment
information
.
cause
serious
injury
.
The
airbag
is
an
explosivedevice
and
should
be
treated
with
extreme
caution
.
Always
follow
the
air-
The
variable-assist
power
steering
system
consistsof
an
bag
removal
procedure
as
outlined
in
721
Airbag
System
engine-driven
hydraulic
pump,
a
rack-and-pinion
steering
(SRS)
.
gear
assembly
with
an
integral
hydraulic
control
valve,
and
connecting
linkage
to
the
road
wheels
.
WARNING-
"
The
BMW
Supplemental
Restraint
System
(SRS)
At
lowspeeds,
maximum
power
assist
is
provided
to
ease
is
complex
and
special
precautions
must
be
ob-
parking
and
city
driving
.
At
high
speeds,
assist
is
reduced
to
served
when
servicing
.
Serious
injury
may
result
ensure
stability
.
The
power
steering
system
varies
assist
if
system
service
is
attempted
by
persons
unfa-
based
on
engine
speed
.
miliar
with
the
BMW
SRS
and
its
approved
ser-
vice
procedures
.
BMW
specifies
that
all
ING-
inspection
and
service
shouldbe
performed
by
WARN
an
authorized
BMW
dealer
.
"
Do
not
reuse
self-locking
nuts
.
They
are
de-signed
to
beused
only
once
and
may
failif
re-
"
BMW
Supplemental
Restraint
Systems
(SRS)
used
.
Always
replace
them
with
new
locking
nuts
.
are
equipped
with
a
back-up
power
supply
inside
the
SRS
control
module
.
A
10minute
waiting
"
Do
not
ínstall
bolts
and
nuts
coated
with
under-
shouldbe
observed
after
the
battery
cable
has
coating
wax,
as
correct
tightening
torque
cannot
been
disconnected
.
This
will
allow
the
reserve
be
assured
.
Always
clean
the
threads
with
sol-
power
supply
to
discharge
.
vent
before
installation,
or
install
new
parts
.
"
Do
not
attempt
to
weldor
straighten
any
steering
components
.
Always
replace
damaged
parts
.
NOTE-
For
information
on
steering
column-mounted
switches
and
the
ignition
lock,
see
612
Switches
and
Electrical
Accessories
.
STEERING
AND
WHEEL
ALIGNMENT
320-1
Caster
and
Camber
.
.
.
.
.
...........
.
....
320-5
TABLES
a
.
Front
Wheel
Alignment
Specifications
.
...
.......
320-6
b
.
Rear
Wheel
Alignment
Specifications
.
...
.......
320-6
Steering
wheel,
removing
and
installing
1
.
Center
steering
wheel
.
Make
sure
front
wheelsare
pointed
straight
ahead
.
2
.
Disconnect
negative
(-)
cable
from
battery
and
cover
terminal
with
insulating
material
.
CAUTION-
Prior
to
disconnectiog
the
battery,
read
the
battery
disconnection
cautions
given
at
the
front
of
this
manual
on
page
viii
.
STEERING
WHEEL
Page 268 of 759
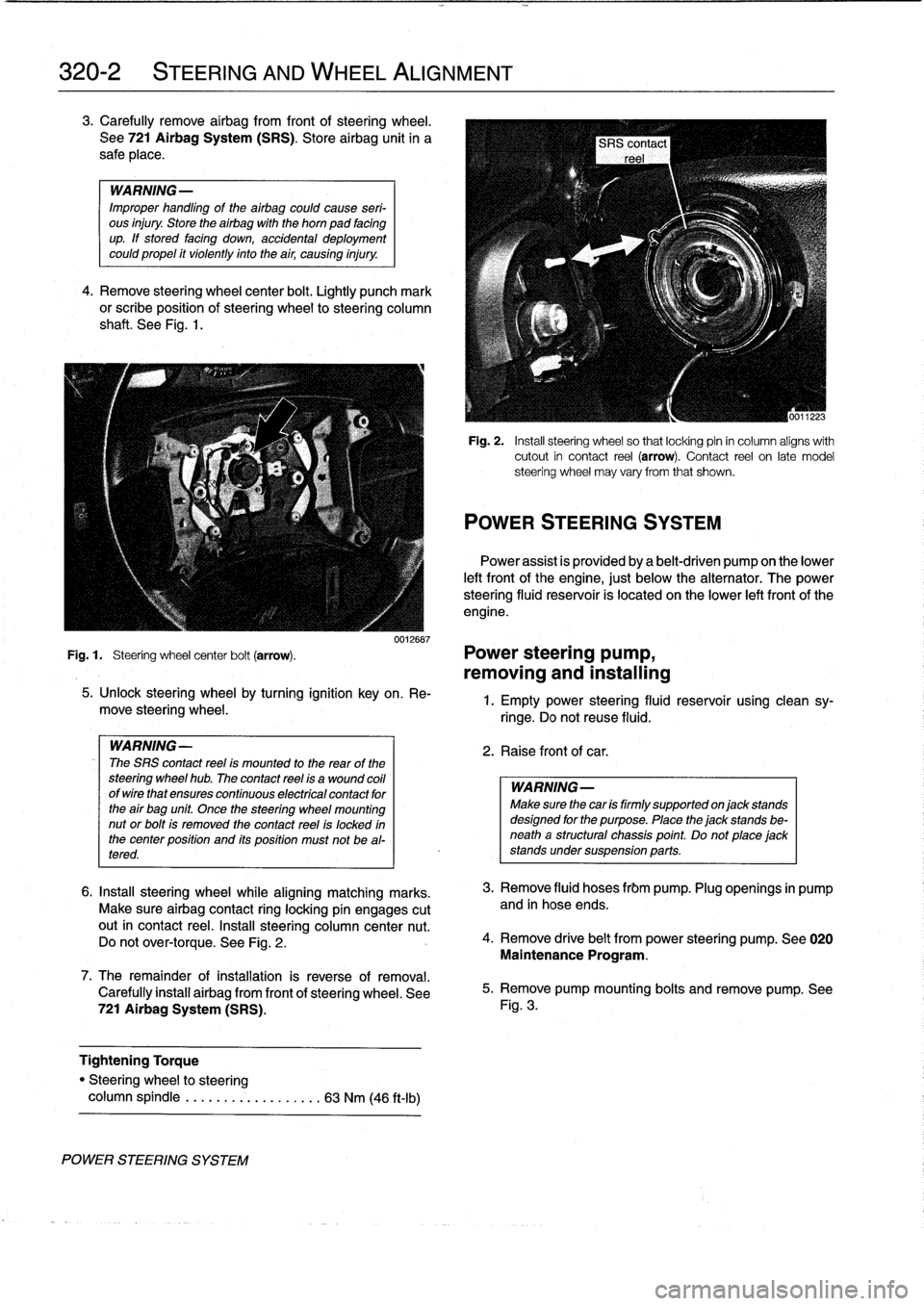
320-2
STEERING
AND
WHEEL
ALIGNMENT
3
.
Carefully
remove
airbag
from
front
of
steering
wheel
.
See
721
Airbag
System
(SRS)
.
Store
airbag
unit
in
a
safe
place
.
WARNING-
Improper
handling
of
theaírbag
could
cause
seri-
ous
ínjury
.
Store
theaírbag
with
the
horn
pad
facing
up
.
If
stored
facing
down,
accidental
deployment
could
propel
it
vlolently
into
the
air,
causíng
ínjury
.
4
.
Remove
steering
wheel
center
bolt
.
Lightly
punch
mark
or
scribe
position
of
steering
wheel
to
steering
column
shaft
.
See
Fig
.
1
.
0012687
Fig
.
1
.
Steering
wheel
center
bolt
(arrow)
.
Power
steering
pump,
removing
and
installing
POWER
STEERING
SYSTEM
5
.
Unlock
steering
wheel
by
turning
ignition
key
on
.
Re-
move
steering
wheel
.
WARNING-
The
SRS
contact
reel
ís
mounted
to
the
rear
of
the
steering
wheel
hub
.
The
contact
reel
ís
a
wound
coil
ofwirethat
ensures
continuous
electrícal
contact
for
the
air
bag
unit
Once
the
steering
wheel
mounting
nut
or
bolt
is
removed
the
contact
reel
is
locked
in
the
center
position
and
its
position
must
not
be
al-
tered
.
6
.
Insta¡¡
steering
wheel
while
aligning
matching
marks
.
Make
sure
airbag
contact
ring
locking
pin
engages
cutout
in
contact
reel
.
Insta¡¡
steering
column
center
nut
.
Do
not
over-torque
.
See
Fig
.
2
.
7
.
The
remainder
ofinstallation
is
reverse
of
removal
.
Carefully
install
airbag
from
front
of
steering
wheel
.
See
721
Airbag
System
(SRS)
.
Tightening
Torque
"
Steering
wheel
to
steering
column
spindle
...
..
..
.
..........
63
Nm
(46
ft-Ib)
Fig
.
2
.
Insta¡¡
steering
wheel
so
that
locking
pin
in
column
aligns
with
cutout
in
contact
reel
(arrow)
.
Contact
reel
on
late
model
steering
wheel
may
vary
from
that
shown
.
POWER
STEERING
SYSTEM
Power
assist
is
províded
by
a
belt-driven
pump
on
the
lower
left
front
of
the
engine,
just
below
the
alternator
.
The
power
steering
fluid
resenroir
is
located
on
the
lower
left
front
of
the
engine
.
1
.
Empty
power
steering
fluid
reservoir
usingclean
sy-
ringe
.
Do
not
reuse
fluid
.
2
.
Raise
front
of
car
.
WARNING
Make
sure
thecar
is
firmly
supportedon
jack
stands
designed
for
the
purpose
.
Place
the
jack
stands
be-
neatha
structural
chassis
point
.
Do
not
place
jack
stands
undersuspension
parts
.
3
.
Remove
fluid
hoses
frbm
pump
.
Plug
openings
in
pump
and
in
hose
ends
.
4
.
Remove
drive
belt
from
power
steering
pump
.
See
020
Maintenance
Program
.
5
.
Remove
pump
mounting
bolts
and
remove
pump
.
See
Fig
.
3
.
Page 269 of 759
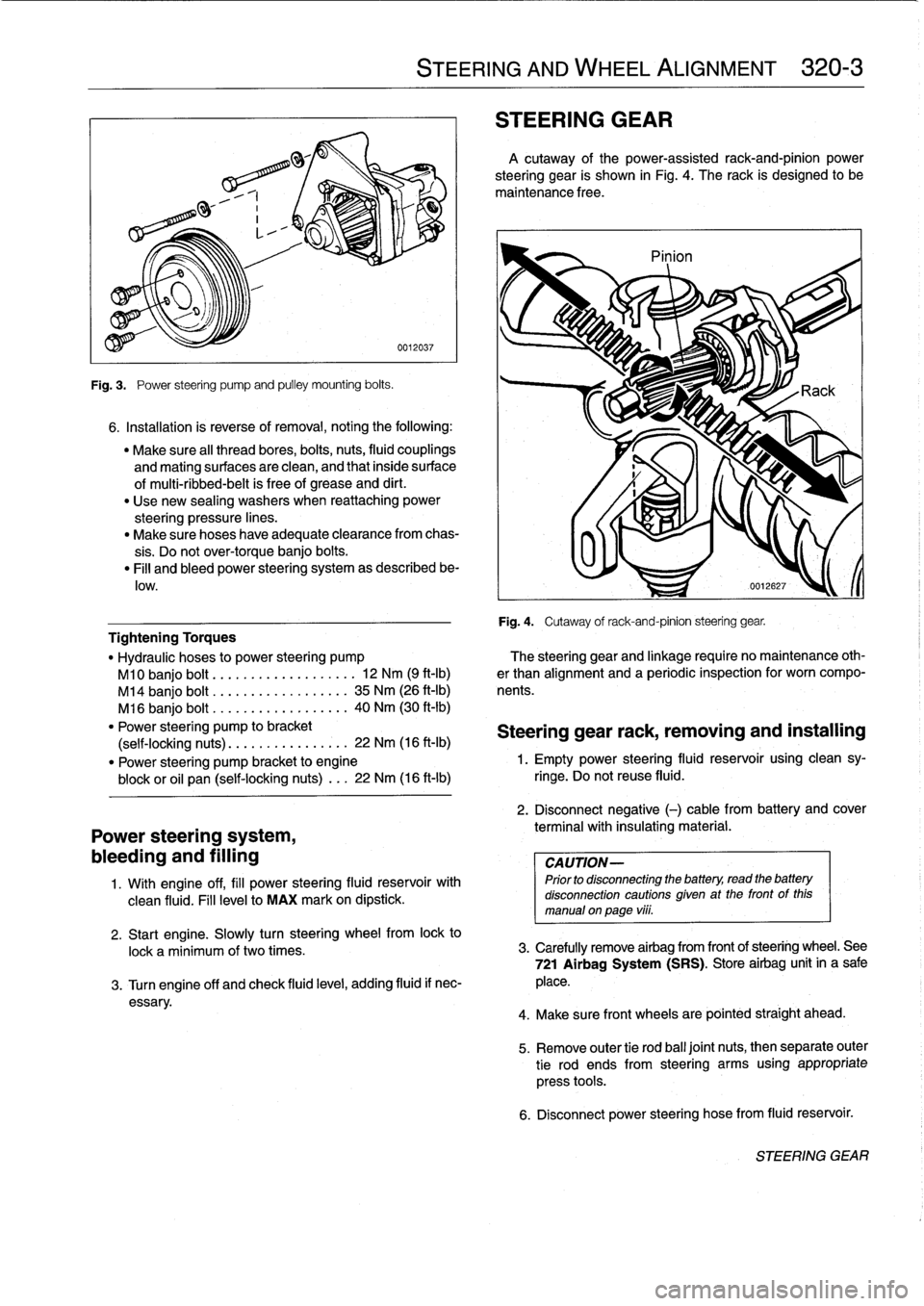
Fig
.
3
.
Power
steering
pump
and
pulley
mounting
bolts
.
6
.
Installation
is
reverse
of
removal,
noting
the
following
:
"
Make
sure
al¡
thread
bores,
bolts,
nuts,
fluid
couplings
and
mating
surfaces
are
clean,
and
that
inside
surface
of
multi-ribbed-belt
is
free
of
grease
and
dirt
.
"
Use
new
sealing
washers
when
reattaching
power
steering
pressure
lines
.
"
Make
sure
hoses
have
adequate
clearance
from
chas-
sis
.
Do
not
over-torque
banjo
bolts
.
"
Fill
and
bleed
power
steering
system
as
described
be-
low
.
Power
steering
system,
bleeding
and
filling
1
.
Wíth
engine
off,
fill
power
steering
fluid
reservoir
with
clean
fluid
.
Fill
levelto
MAX
mark
on
dipstick
.
STEERING
AND
WHEEL
ALIGNMENT
320-
3
STEERING
GEAR
A
cutaway
of
the
power-assisted
rack-and-pinion
power
steering
gear
is
shown
in
Fig
.
4
.
The
rack
is
designed
to
be
maintenance
free
.
Pinion
Fig
.
4
.
Cutaway
of
rack-and-pinion
steering
gear
.
Tightening
Torques
"
Hydraulic
hoses
to
power
steering
pump
?he
steering
gear
and
linkage
require
no
maintenance
oth-
M10
banjo
bolt
.........
..
.
...
...
.
12
Nm
(9
ft-Ib)
er
than
alignment
and
a
periodic
inspection
for
worn
compo
M14
banjo
bolt
..............
..
..
35
Nm
(26
ft-Ib)
nents
.
M16
banjo
bolt
..............
...
.
40
Nm
(30
ft-Ib)
"
Power
steering
pump
to
bracket
Steering
gear
rack,
removing
and
installing
(self-locking
nuts)
.............
..
.
22
Nm
(16
ft-Ib)
"
Power
steering
pump
bracket
to
engine
1
.
Empty
power
steering
fluid
reservoir
using
clean
sy-
block
or
oil
pan
(self-locking
nuts)
...
22
Nm
(16
ft-lb)
ringe
.
Do
not
reuse
fluid
.
2
.
Disconnect
negative
(-)
cable
from
battery
and
cover
terminal
with
insulating
material
.
CAUTION-
Prior
to
disconnectiog
the
battery,
read
the
battery
disconnection
cautions
given
at
the
front
of
this
manual
on
page
viii
.
2
.
Start
engine
.
Slowly
turn
steering
wheelfrom
lock
to
lock
a
minimum
of
two
times
.
3
.
Carefully
remove
airbag
from
frontof
steering
wheel
.
See
721
Airbag
System
(SRS)
.
Store
airbag
unit
in
a
sale
3
.
Turn
engine
off
and
check
fluid
leve¡,
adding
fluid
if
nec-
place
.
essary
.
4
.
Make
sure
front
wheelsare
pointed
straight
ahead
.
5
.
Remove
outer
tie
rod
ball
joínt
nuts,
thenseparate
outer
tie
rod
ends
from
steering
arms
using
appropriate
press
tools
.
6
.
Disconnect
power
steering
hose
from
fluid
reservoir
.
STEERING
GEAR
Page 270 of 759
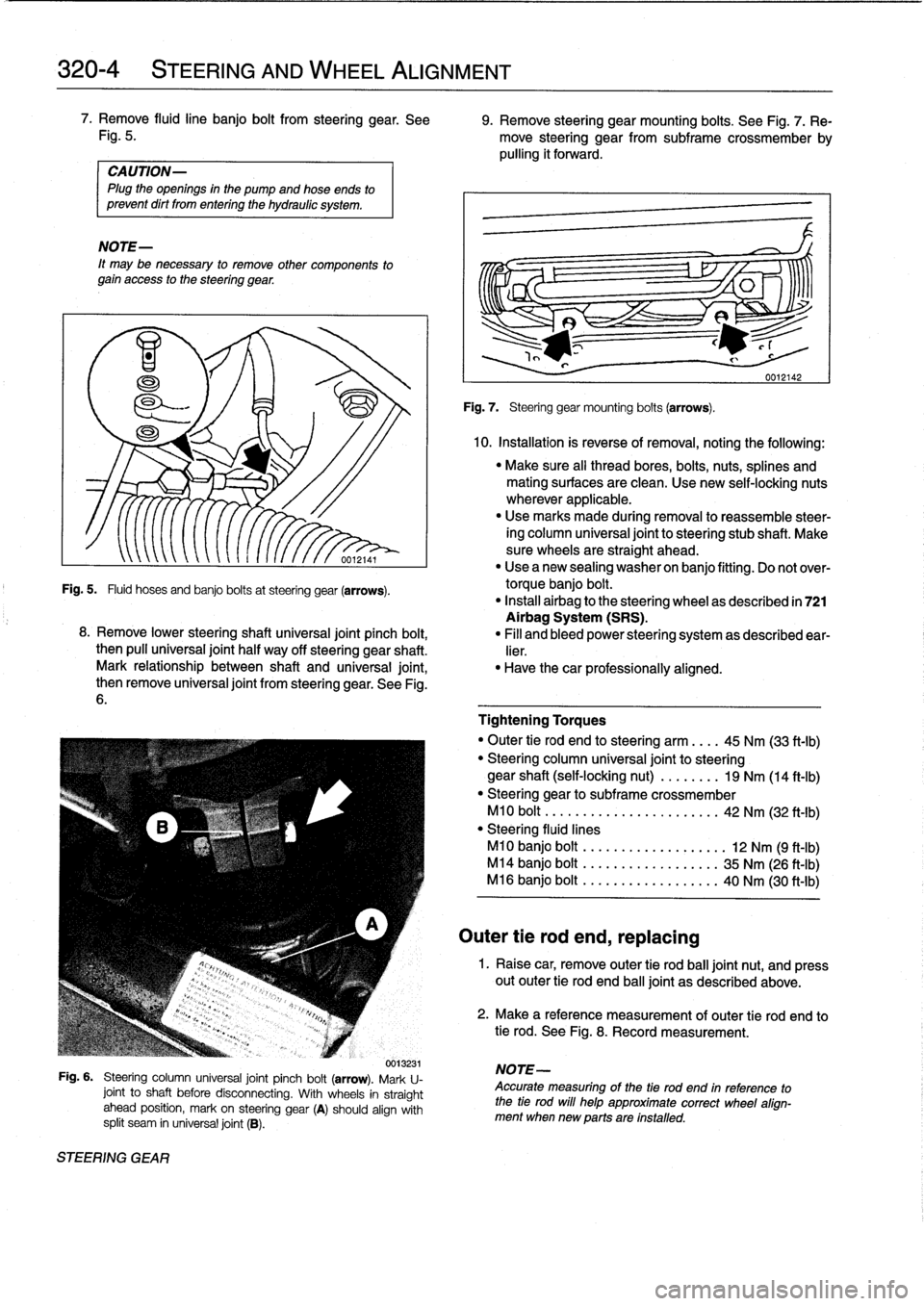
320-
4
STEERING
AND
WHEEL
ALIGNMENT
7
.
Remove
fluidline
banjo
bolt
from
steering
gear
.
See
9
.
Remove
steering
gearmounting
bolts
.
See
Fig
.
7
.
Re
Fig
.
5
.
move
steering
gear
from
subframe
crossmember
by
pulling
it
forward
.
CAUTION-
Plug
the
openings
in
the
pump
and
hoseends
to
prevent
dirt
from
entering
the
hydraulic
system
.
NOTE-
It
may
be
necessary
to
remove
other
components
to
gain
access
to
the
steering
gear
.
"
Make
sure
al¡
thread
bores,
bolts,
nuts,
splines
and
mating
surfaces
are
clean
.
Use
new
self-locking
nuts
wherever
applicable
.
"
Use
marks
made
during
removal
to
reassemble
steer-
ing
column
universal
jointto
steering
stub
shaft
.
Make
sure
wheels
are
straight
ahead
.
"
Use
a
new
sealing
washer
on
banjo
fitting
.
Do
not
over-
Fig
.
5
.
Fluid
hoses
and
banjo
bolts
at
steering
gear
(arrows)
.
torque
banjo
bolt
.
"
Install
airbag
to
the
steering
wheel
as
described
in
721
Airbag
System
(SRS)
.
8
.
Remove
lower
steeringshaft
universal
joint
pinch
bolt,
"
Fill
and
bleed
power
steering
system
as
described
ear-
then
pull
universal
joint
half
way
off
steering
gear
shaft
.
lier
.
Mark
relationship
between
shaft
and
universal
joint,
"
Have
thecar
professionally
aligned
.
then
remove
universal
joint
from
steering
gear
.
See
Fig
.
6
.
0013231
Fig
.
6
.
Steering
column
universal
joint
pinch
bolt
(arrow)
.
Mark
U-
joint
to
shaft
before
disconnecting
.
With
wheels
in
straight
ahead
position,
mark
on
steering
gear
(A)
should
align
with
split
seam
in
universal
joint
(B)
.
STEERING
GEAR
Fig
.
7
.
Steering
gear
mounting
bolts
(arrows)
.
Outer
tie
rod
end,
replacing
10
.
Installation
is
reverse
of
removal,
noting
the
following
:
Tightening
Torques
"
Outer
tie
rod
end
to
steering
arm
.
.
..
45
Nm
(33
ft-Ib)
"
Steering
column
universal
joint
to
steering
gear
shaft
(self-locking
nut)
....
..
..
19
Nm
(14
ft-Ib)
"
Steering
gear
to
subframe
crossmember
M10
bolt
..............
.
...
.....
42
Nm
(32
ft-Ib)
"
Steering
fluíd
lines
M10
banjo
bolt
..
..
..
........
.....
12
Nm
(9
ft-Ib)
M14
banjo
bolt
..
..
..
...
..
...
....
35
Nm
(26
ft-lb)
M16
banjo
bolt
..
.......
..
..
.....
40
Nm
(30
ft-Ib)
1
.
Raise
car,
remove
outer
tie
rod
ball
joint
nut,
and
press
out
outer
tie
rod
end
ball
joint
as
described
above
.
2
.
Make
a
reference
measurement
of
outer
tie
rod
end
to
tie
rod
.
See
Fig
.
8
.
Record
measurement
.
NOTE-
Accurate
measuring
of
the
tie
rod
end
in
reference
to
the
tie
rod
will
help
approximate
correct
wheel
align-
mentwhen
new
parts
are
installed
.