check engine BMW M3 1998 E36 Workshop Manual
[x] Cancel search | Manufacturer: BMW, Model Year: 1998, Model line: M3, Model: BMW M3 1998 E36Pages: 759
Page 174 of 759
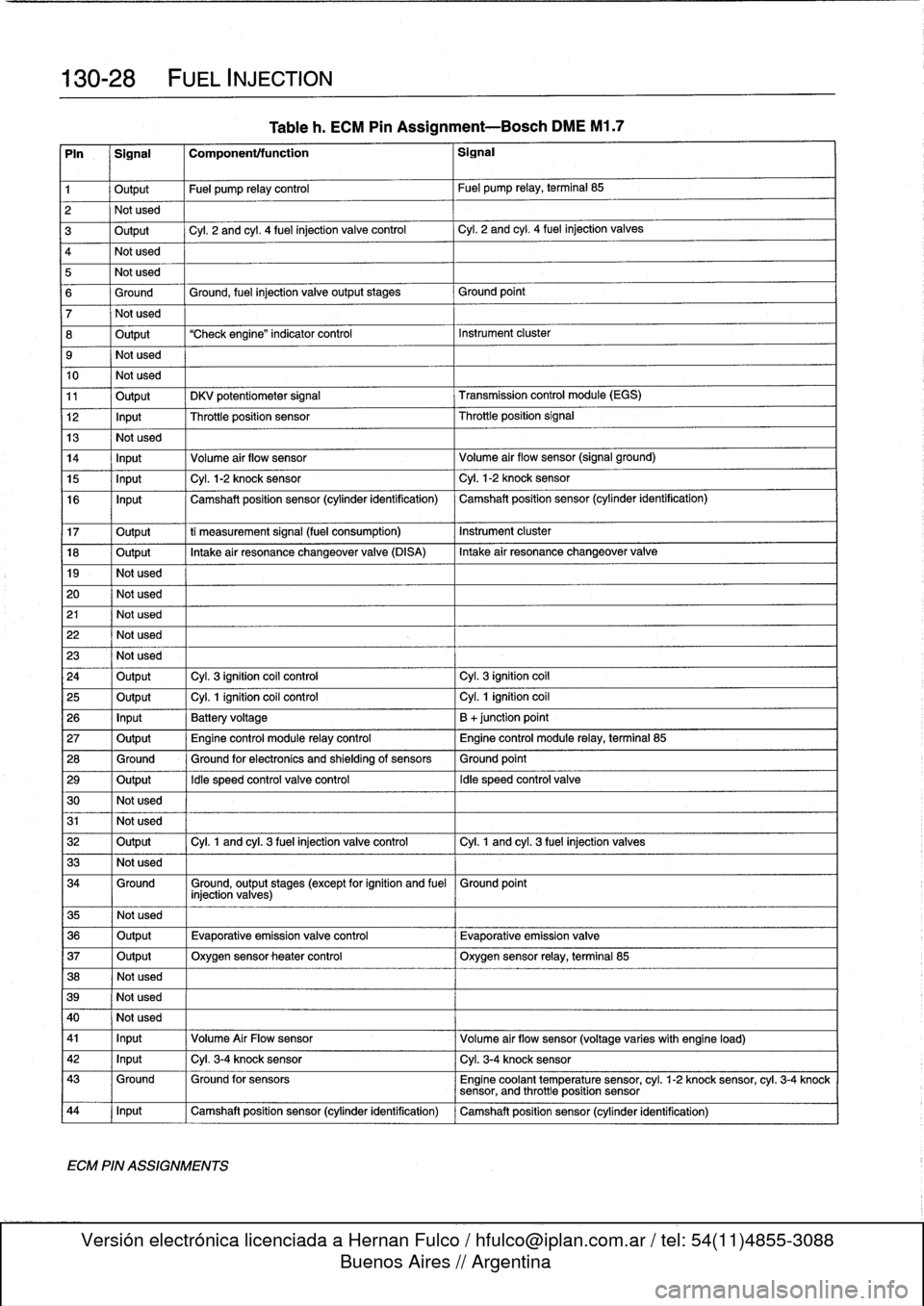
130-
2
8
FUEL
INJECTION
Tableh
.
ECM
Pin
Assignment-Bosch
DME
M1
.7
Pin
Signal
Componenttfunction
Signal
1
Output
Fuel
pump
relay
control
Fuel
pump
relay,
terminal
85
2
Not
used
3
Output
Cyl
.
2
and
cyl
.
4
fuel
injection
valve
control
Cyl
.
2
and
cyl
.
4
fuel
injection
valves
4
Not
used
5
Not
used
6
Ground
Ground,
fuel
injection
valveoutputstages
Ground
point
7
Not
used
8
Output
"Check
engine"
indicator
control
Instrument
cluster
9
Not
used
10
Not
used
11
Output
DKV
potentiometer
signal
Transmission
control
module
(EGS)
12
Input
Throttleposition
sensor
Throttleposition
Signal
13
Not
used
14
Input
Volume
air
flow
sensor
Volume
air
flow
sensor
(signal
ground)
15
Input
Cyl
.
1-2
knock
sensor
Cyl
.
1-2
knock
sensor
16
Input
Camshaft
position
sensor
(cylinder
identification)
Camshaft
position
sensor
(cylinder
identification)
17
Output
ti
measurement
signal
(fuel
consumption)
Instrument
cluster
18
Output
Intakeair
resonance
changeover
valve
(DISA)
Intake
air
resonance
changeover
valve
19
-
Not
used
20
Not
used
21
Not
used
22
Not
used
23
Not
used
24
Output
Cyl
.
3
ignition
coil
control
Cyl
.
3
ignition
coil
25
Output
Cyl
.
1
ignition
coil
control
Cyl
.
1
ignition
coil
26
Input
Battery
voltage
B
+junction
point
27
Output
Engine
control
module
relay
control
Engine
control
module
relay,
terminal
85
28
Ground
Ground
for
electronics
and
shielding
of
sensors
Ground
point
29
Output
Idle
speed
control
valve
control
Idle
speed
control
valve
30
Not
used
31
Not
used
32
Output
Cyl
.
1
and
cyl
.
3
fuel
injection
valve
control
Cyl
.
1
and
cyl
.
3
fuel
injection
valves
33
Not
used
34
Ground
Ground,
output
stages
(except
for
ignition
and
fuel
Ground
point
injection
valves)
35
Not
used
36
Output
Evaporative
emissionvalve
control
Evaporative
emission
valve
37
Output
Oxygen
sensor
heater
control
Oxygen
sensor
relay,
terminal
85
38
Not
used
39
Not
used
40
I
Not
used
41
I
Input
,
Volume
Air
Flow
sensor
Volume
air
flow
sensor
(voltage
varies
with
engine
load)
42
1
Input
1
Cyl
.
3-4
knock
sensor
1
Cyl
.
3-4
knock
sensor
43
Ground
Ground
for
sensors
Engine
coolant
temperature
sensor,
cyl
.
1-2
knock
sensor,
cyl
.
3-4
knock
sensor,
and
throttle
position
sensor
44
1
Input
1
Camshaft
position
sensor
(cylinder
identification)
1
Camshaft
position
sensor
(cylinder
identification)
ECM
PIN
ASSIGNMENTS
Page 176 of 759
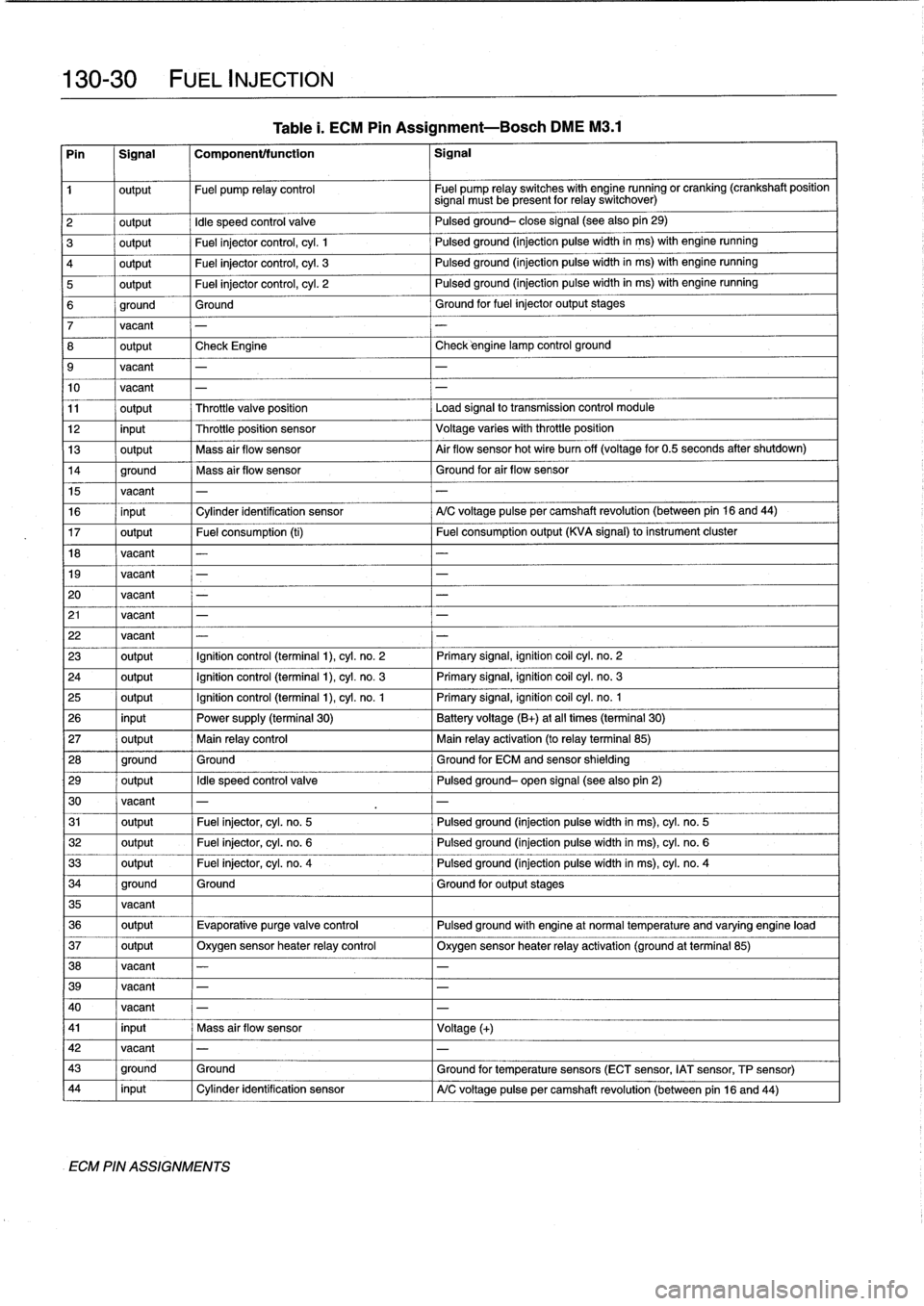
130-
3
0
FUEL
INJECTION
Pin
Signal
Component/function
Signal
ECM
PIN
ASSIGNMENTS
Table
1.
ECM
Pin
Assignment-Bosch
DME
M3
.1
1
output
Fuel
pump
relay
control
Fuel
pump
relay
switches
with
engine
runningor
cranking
(crankshaft
position
Signal
mustbe
present
for
relay
switchover)
2
1
output
1
Idle
speed
control
valve
1
Pulsad
ground-
close
signal
(seealsopin29)
3
output
Fuel
injectorcontrol,
cyl
.
1
Pulsedground
(injection
pulsewidth
in
ms)
with
engine
running
4
output
Fuel
injectorcontrol,
cyl
.
3
Pulsedground
(injection
pulsewidth
in
ms)
with
engine
running
5
output
Fuel
injector
control,
cyl
.
2
Pulsedground
(injection
pulse
width
in
ms)
with
enginerunning
6
ground
Ground
Ground
for
fuel
injector
output
stages
7
vacant
-
-
8
output
Check
Engine
Check
éngine
lamp
control
ground
9
vacant
-
-
10
vacant
-
-
11
output
Throttle
valve
position
Load
signal
to
transmission
control
module
12
input
Throttle
position
sensor
Voltage
varies
with
throttle
position
13
output
Mass
air
flow
sensor
Air
flow
sensor
hotwire
burn
off
(voltage
for
0
.5
seconds
after
shutdown)
14
ground
Mass
air
flow
sensor
Ground
for
air
flow
sensor
15
vacant
-
-
16
input
Cylinder
identification
sensor
A/C
voltage
pulse
per
camshaft
revolution
(between
pin
16
and
44)
17
output
Fuel
consumption
(ti)
Fuel
consumption
output
(KVA
Signal)
to
instrument
cluster
18
vacant
-
-
19
vacant
-
-
20
vacant
-
-
21vacant
-
-
22
vacant
-
-
23
output
Ignition
control
(terminal
1),
cyl
.
no
.
2
Primary
Signal,
ignition
coil
cyl
.
no
.
2
24
output
Ignition
control
(terminal
1),
cyl
.
n
o
.
3
Primary
signal,
ignition
coil
cyl
.
no
.
3
25
output
Ignition
control
(terminal
1),
cyl
.
n
o
.
1
Primary
signal,
ignitioh
coil
cyl
.
no
.
1
26
input
Power
supply
(terminal
30)
Battery
voltage
(B+)
at
al¡
times
(terminal
30)
27
output
Main
relay
control
Main
relay
activation
(to
relay
terminal
85)
28
ground
Ground
Ground
for
ECM
and
sensor
shielding
29
output
Idle
speed
control
valve
Pulsed
ground-
open
signal
(see
also
pin
2)
30
vacant
-
-
31
output
Fuel
injector,cyl
.
no
.
5
Pulsedground
(injection
pulsewidth
in
ms),
cyl
.
no
.
5
32
output
Fuel
injector,cyl
.
no
.
6
Pulsedground
(injection
pulse
width
in
ms),
cyl
.
no
.
6
33
output
Fuel
injector,cyl
.
no
.
4
Pulsedground
(injection
pulsewidth
in
ms),
cyl
.
no
.
4
34
ground
Ground
Ground
for
output
stages
35
vacant
36
output
Evaporative
purgevalve
control
Pulsed
ground
with
engine
at
normal
temperature
and
varying
engine
load
37
output
Oxygen
sensor
heater
relay
control
Oxygen
sensor
heater
relayactivation
(ground
at
terminal
85)
38
vacant
-
-
39
vacant
-
-
40
vacant
-
41
input
Mass
air
flow
sensor
Voltage
(+)
42
vacant
-
-
43
ground
Ground
Ground
for
temperatura
sensors
(ECT
sensor,
IAT
sensor,
TP
sensor)
44
input
Cylinder
identification
sensor
A/C
voltagepulseper
camshaft
revolution
(between
pin
16
and
44)
Page 178 of 759
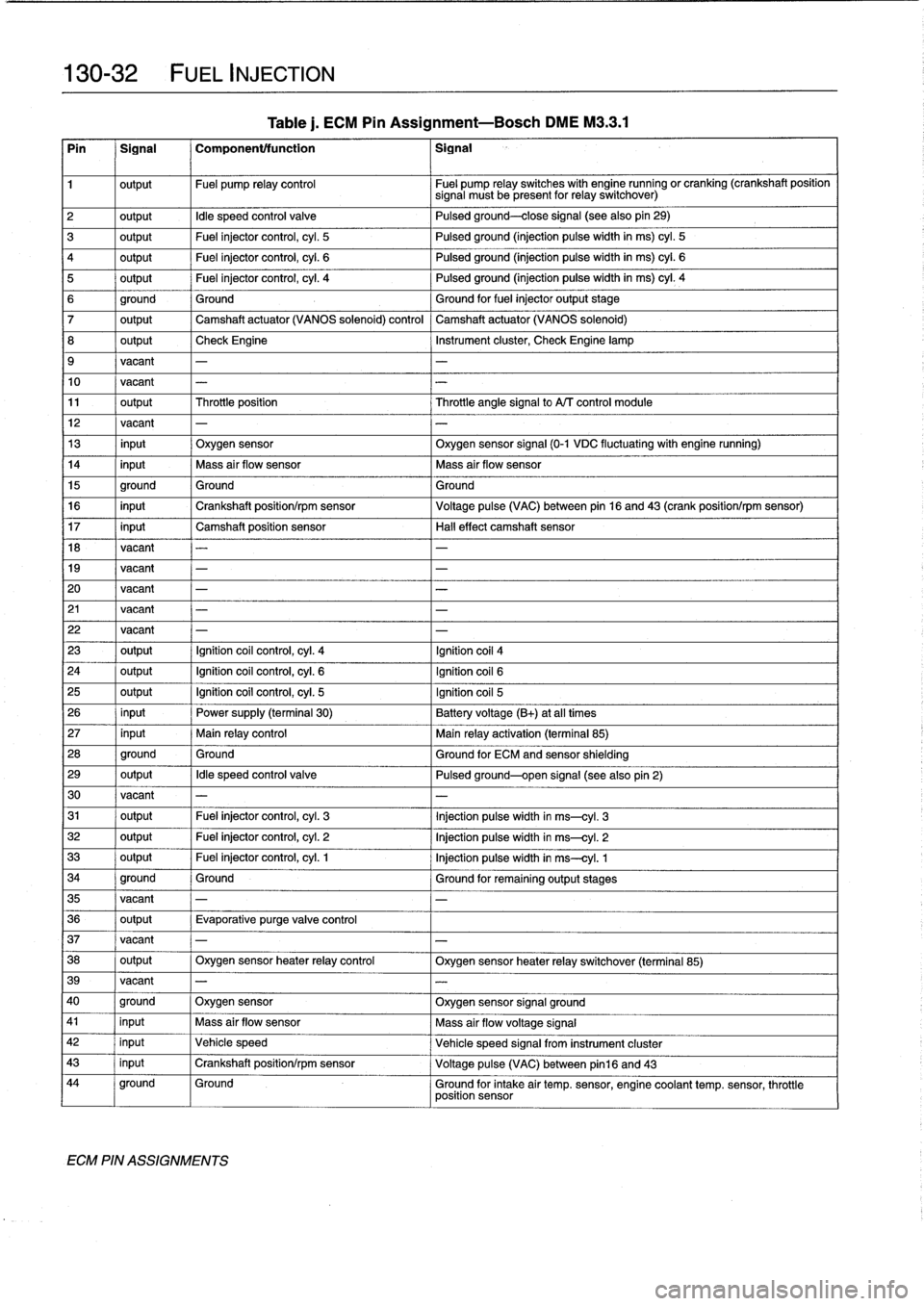
130-
3
2
FUEL
INJECTION
Pin
1
Signal
1
Component/function
1
Signal
1
output
Fuel
pump
relay
control
Fuel
pump
relay
switches
with
engine
running
or
cranking
(crankshaft
position
signal
must
be
present
for
relay
switchover)
2
output
Idle
speed
control
valve
Pulsed
ground-close
signal
(seealso
pin
29)
3
output
Fuel
ínjectorcontrol,
cyl
.
5
Pulsed
ground
(injection
pulsewidth
in
ms)
cyl
.
5
4
output
Fuel
injectorcontrol,
cyl
.
6
Pulsed
ground
(injection
pulsewidth
in
ms)
cyl
.
6
5
output
Fuel
injectorcontrol,
cyl
.
4
Pulsed
ground
(injection
pulsewidth
in
ms)
cyl
.
4
6
ground
Ground
Ground
for
fuel
injector
output
stage
7
output
Camshaft
actuator
(VANOS
solenoid)
control
Camshaft
actuator
(VANOS
solenoid)
8
output
Check
Engine
Instrument
cluster,
Check
Engine
lamp
9
vacant
-
-
10
vacant
-
-
11
output
Throttle
position
Throttle
angle
signal
to
A/T
control
module
12
vacant
-
-
13
input
Oxygen
sensor
Oxygen
sensor
signal
(0-1
VDC
fluctuating
with
engine
running)
14
input
Mass
air
flow
sensor
Mass
air
flow
sensor
15
ground
Ground
Ground
16
input
Crankshaft
position/rpm
sensor
Voltage
pulse
(VAC)
between
pin
16
and
43
(crank
position/rpm
sensor)
17
input
Camshaft
position
sensor
Halleffect
camshaft
sensor
18
vacant
-
-
19
vacant
-
-
20
vacant
-
-
21
vacant
-
-
22
vacant
-
-
23
output
Ignition
coil
control,
cyl
.
4
Ignition
coil
4
24
output
Ignition
coil
control,
cyl
.
6
Ignition
coil
6
25
output
Ignition
coil
control,
cyl
.
5
Ignition
coil
5
26
input
Power
supply
(terminal
30)
Battery
voltage(B+)
at
all
times
27
input
Main
relay
control
Main
relayactivation
(terminal
85)
28
ground
Ground
Ground
for
ECM
and
sensor
shielding
29
output
Idle
speed
control
valve
Pulsed
ground-open
signal
(seealsopin
2)
30
vacant
-
-
31
output
Fuel
injectorcontrol,
cyl
.
3
Injection
pulse
wicith
in
ms-cyl
.
3
32
output
Fuel
injectorcontrol,
cyl
.
2
Injection
pulse
wicith
in
ms-cyl
.
2
33
output
Fuel
injectorcontrol,
cyl
.
1
Injection
pulsewidth
in
ms-cyl
.
1
34
ground
Ground
Ground
for
remaining
output
stages
35
vacant
-
-
36
output
Evaporative
purge
valve
control
37
vacant
-
-
38
output
Oxygen
sensor
heater
relay
control
Oxygen
sensor
heater
relay
switchover
(terminal
85)
39
vacant
-
-
40
ground
Oxygen
sensor
Oxygen
sensor
signal
ground
41
input
Mass
air
flow
sensor
Mass
air
flow
voltage
signal
42
input
Vehicle
speed
Vehicle
speed
signal
from
instrument
cluster
43
input
Crankshaft
position/rpm
sensor
Voltage
pulse
(VAC)
between
pin16
and
43
44
ground
Ground
Ground
for
intake
air
temp
.
sensor,
engine
coolant
temp
.
sensor,
throttle
position
sensor
ECM
PIN
ASSIGNMENTS
Table
j
.
ECM
Pin
Assignment-Bosch
DME
M3
.3
.1
Page 180 of 759
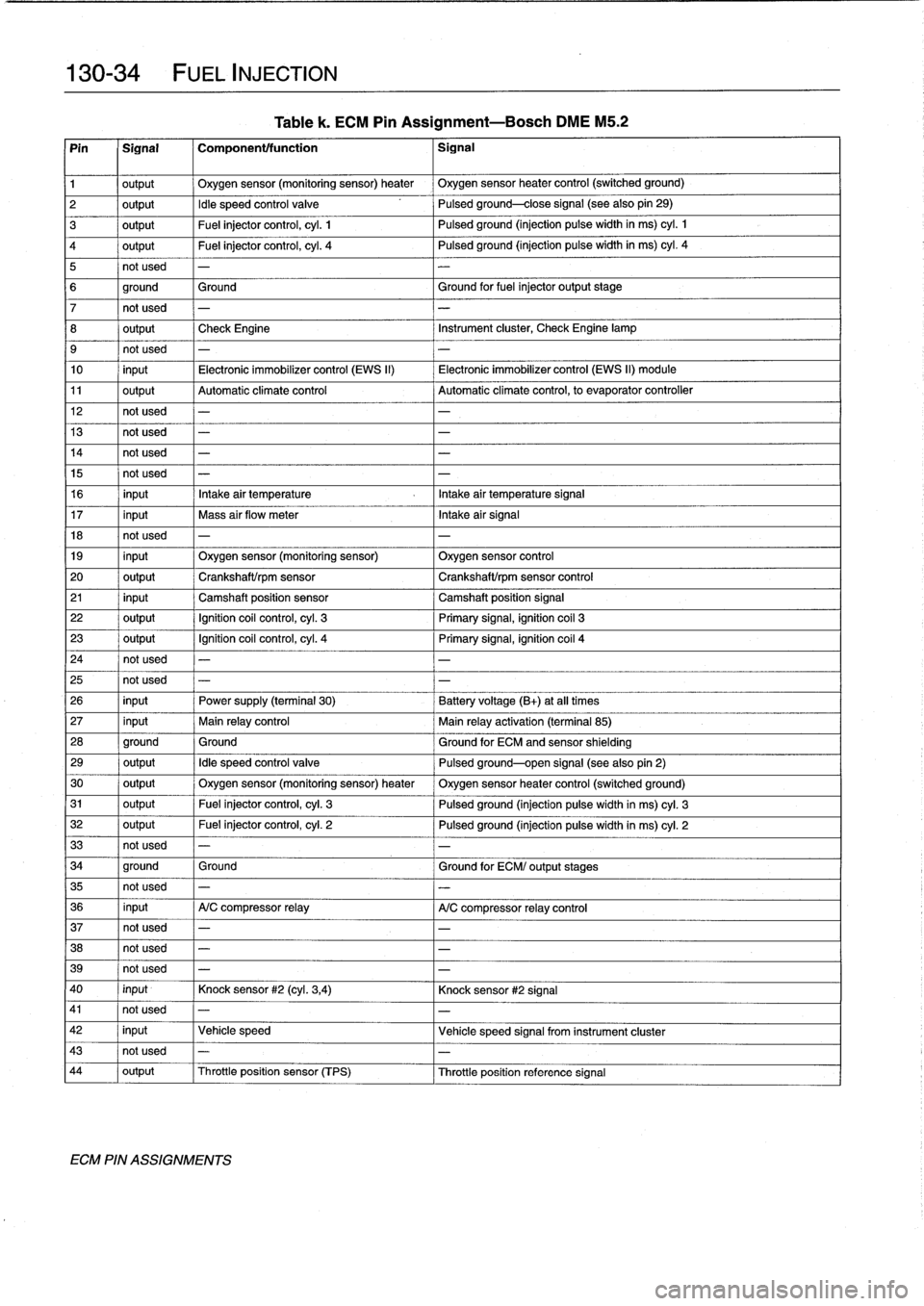
130-
34
FUEL
INJECTION
Pin
i
Signal
1
Component/function
1
Signal
1
output
Oxygen
sensor
(monitoring
sensor)heater
Oxygen
sensor
heater
control
(switched
ground)
2
output
Idle
speed
control
valve
Pulsed
ground-close
signal
(see
also
pin
29)
3
output
Fuel
injector
control,
cyl
.
1
Pulsed
ground
(injection
pulsewidth
in
ms)
cyl
.
1
4
output
Fuel
injector
control,
cyl
.
4
Pulsed
ground
(injection
pulse
width
in
ms)
cyl
.
4
5
not
used
-
-
6
ground
Ground
Ground
for
fuel
injector
output
stage
7
not
used
-
8
1
output
1
Check
Engine
1
Instrument
cluster,
Check
Engine
lamp
9
not
used
-
-
10
input
Electronic
immobilizer
control
(EWS
II)
Electronic
immobilizer
control
(EWS
II)
module
11
output
Automatic
climate
control
Automatic
climate
control,
to
evaporator
controlier
12
not
used
-
-
13
not
used
-
-
14
not
used
-
-
15
not
used
-
-
16
input
Intake
air
temperature
Intake
air
temperature
Signal
17
input
Mass
air
flow
meter
Intake
air
signal
18
not
used
-
-
19
input
Oxygen
sensor
(monitoring
sensor)
Oxygen
sensor
control
20
output
Crankshaft/rpm
sensor
Crankshaft/rpm
sensor
control
21
input
Camshaft
position
sensor
Camshaft
position
signal
22
output
Ignition
coil
control,
cyl
.
3
Primary
signal,
ignitioncoil
3
23
output
Ignition
coil
control,
cyl
.
4
Primary
signal,
ignitioncoil
4
24
not
used
-
-
25
not
used
-
-
26
input
Power
supply
(terminal
30)
Battery
voltage
(B+)
at
al¡
times
27
input
Main
relay
control
Main
relay
activation
(terminal
85)
28
ground
Ground
Ground
for
ECM
and
sensor
shielding
29
output
Idle
speed
control
valve
Pulsed
ground-open
signal
(seealsopin
2)
30
output
Oxygen
sensor
(monitoring
sensor)
heater
Oxygen
sensor
heater
control
(switched
ground)
31
output
Fuel
injectorcontrol,
cyl
.
3
Pulsed
ground
(injection
pulsewidth
in
ms)
cyl
.
3
32
output
Fuel
injector
control,
cyl
.
2
Pulsed
ground
(injection
pulsewidth
in
ms)
cyl
.
2
33
I
not
used
40
input
Knock
sensor
#2
(cyl
.
3,4)
Knock
sensor
#2
signal
41
not
used
-
-
42
input
Vehicle
speed
Vehicle
speed
signal
from
instrument
cluster
43
not
used
-
-
44
output
Throttleposition
sensor
(TPS)
Throttleposition
reference
signal
ECM
PIN
ASSIGNMENTS
Table
k
.
ECM
Pin
Assignment-Bosch
DME
M5
.2
34
ground
Ground
Ground
for
ECM/
output
stages
35
not
used
-
-
36
input
A/C
compressor
relay
A/C
compressor
relay
control
37
not
used
-
-
38
not
used
-
-
39
not
used
-
-
Page 187 of 759
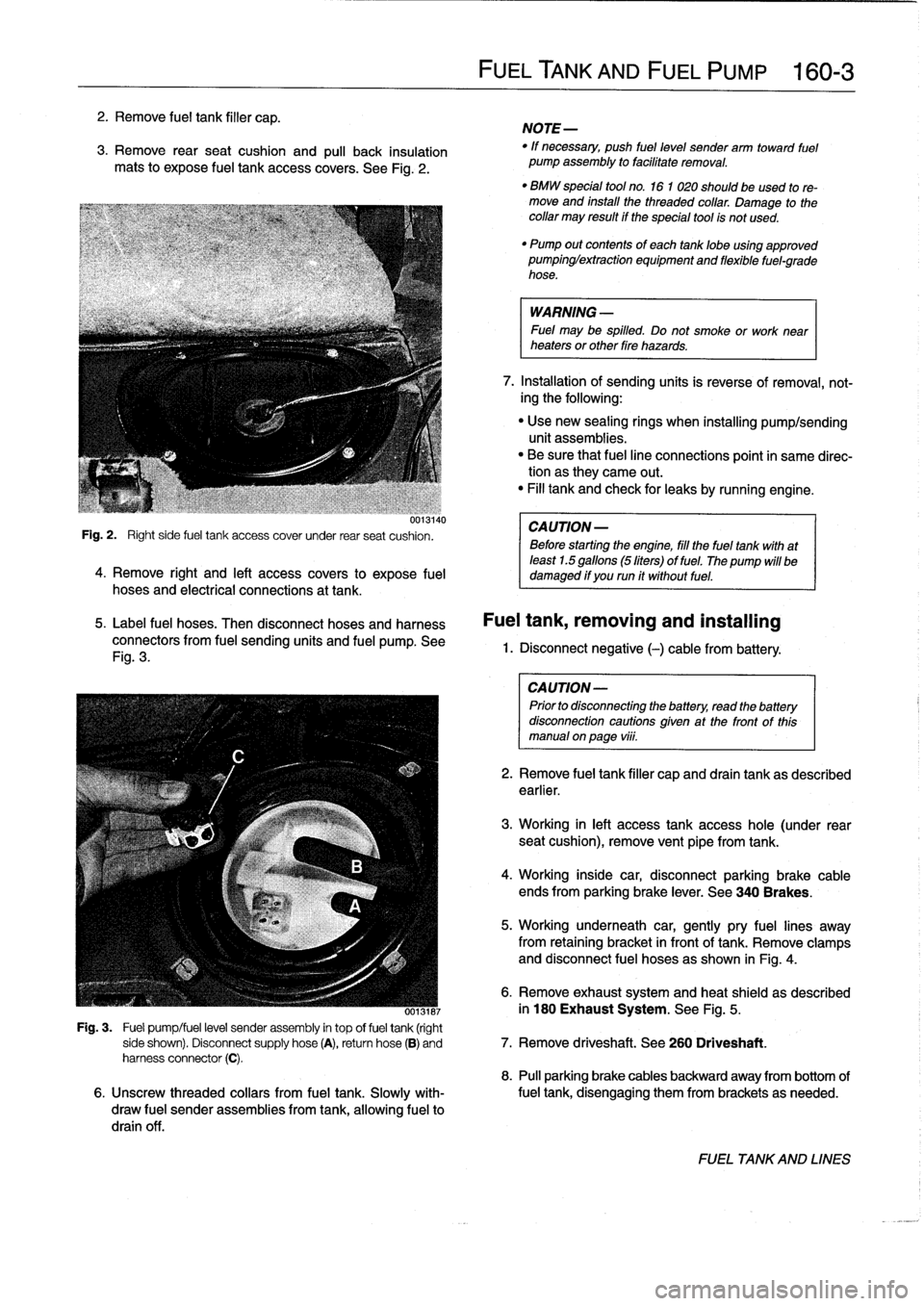
2
.
Remove
fuel
tank
filler
cap
.
3
.
Remove
rearseat
cushion
and
pull
back
insulation
mats
to
expose
fuel
tank
access
covers
.
See
Fig
.
2
.
uui3140
Fig
.
2
.
Right
side
fuel
tank
access
cover
under
rear
seat
cushion
.
4
.
Remove
right
and
left
access
covers
to
expose
fuel
hoses
and
electrical
connections
at
tank
.
5
.
Label
fuel
hoses
.
Then
disconnect
hoses
and
harness
connectors
from
fuel
sending
units
and
fuel
pump
.
See
Fig
.
3
.
FUELTANK
AND
FUEL
PUMP
160-
3
NOTE-
"
If
necessary,
push
fuel
level
sender
arm
toward
fuel
pump
assembly
to
facilitate
removal
.
"
BMW
special
tool
no
.
16
1
020
should
beused
tore-
move
and
install
the
threaded
collar
.
Damage
to
thecollar
may
result
if
the
special
tool
is
not
used
.
"
Pump
out
contents
of
each
tanklobe
using
approved
pumpinglextraction
equipment
and
flexible
fuel-grade
hose
.
WARNING
-
Fuel
may
be
spilled
.
Do
not
smoke
or
work
near
heaters
or
other
fire
hazards
.
7
.
Installation
of
sending
units
is
reverse
of
removal,
not-
ing
the
following
:
"
Use
new
sealing
rings
when
installing
pump/sending
unit
assemblies
.
"
Be
sure
that
fuel
line
connections
point
in
same
direc-tion
as
they
carne
out
.
"
Fill
tank
and
check
for
leaks
by
running
engine
.
CA
UTION-
Before
starting
the
engine,
fill
the
fuel
tank
with
at
least
1.5
gallons
(5liters)
of
fuel
.
The
pump
will
be
damaged
if
you
run
it
without
fuel
.
Fuel
tank,
removing
and
installing
1.
Disconnect
negative
(-)cablefrom
battery
:
CAUTION-
Prior
to
disconnectiog
the
battery,
read
the
battery
disconnection
cautions
given
at
the
front
of
this
manual
onpage
viii
.
2
.
Remove
fuel
tank
filler
capand
drain
tank
as
described
earlier
.
3
.
Working
in
left
access
tank
access
hole
(under
rear
seat
cushion),
remove
vent
pipe
fromtank
.
4
.
Working
inside
car,
disconnectparking
brake
cable
ends
from
parking
brake
lever
.
See
340
Brakes
.
5
.
Working
underneath
car,
gently
pry
fuel
lines
away
from
retaining
bracket
in
front
of
tank
.
Remove
clamps
and
disconnect
fuel
hoses
as
shown
in
Fig
.
4
.
6
.
Remove
exhaust
system
and
heat
shield
as
described
ooisiai
in
180
Exhaust
System
.
See
Fig
.
5
.
Fig
.
3
.
Fuel
pump/fuel
level
sender
assembly
in
top
offuel
tank
(right
side
shown)
.
Disconnect
supply
hose
(A),
return
hose
(B)
and
7
.
Remove
driveshaft
.
See
260
Driveshaft
.
harness
connector
(C)
.
8
.
Pull
parking
brake
cables
backward
away
from
bottom
of
6
.
Unscrew
threaded
collars
from
fuel
tank
.
Slowly
with-
fuel
tank,
disengaging
them
from
brackets
as
needed
.
draw
fuel
sender
assemblies
from
tank,allowing
fuel
to
drain
off
.
FUEL
TANKAND
LINES
Page 188 of 759
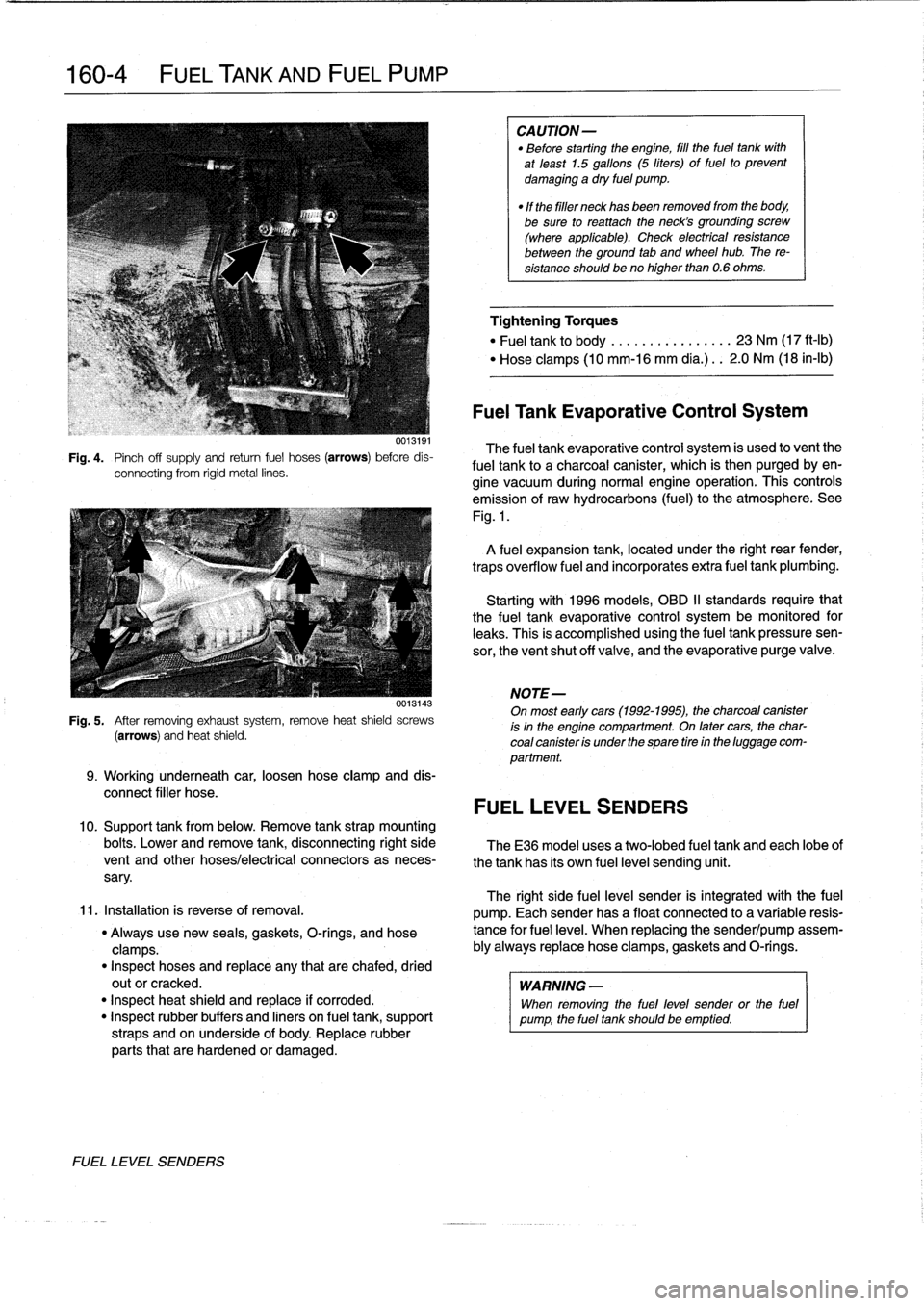
160-
4
FUEL
TANK
AND
FUEL
PUMP
Fig
.
4
.
Pinch
off
supply
and
retum
fuel
hoses
(arrows)
before
dis-
connecting
from
rigid
metal
lines
.
0013143
Fig
.
5
.
After
removing
exhaustsystem,
remove
heat
shield
screws
(arrows)
and
heat
shield
.
9
.
Working
underneath
car,
loosen
hose
clamp
and
dis-
connect
filler
hose
.
10
.
Support
tank
from
below
.
Remove
tank
strap
mounting
bolts
.
Lower
and
remove
tank,
disconnecting
right
side
TheE36
model
uses
a
two-lobed
fuel
tank
and
each
lobeof
vent
and
other
hoses/electrical
connectors
as
neces-
the
tank
has
its
own
fuel
level
sending
unit
.
sary
.
11
.
Installation
is
reverse
of
removal
.
"
Always
use
new
seals,
gaskets,
O-rings,
and
hose
clamps
.
"
Inspect
hoses
and
replace
any
that
are
chafed,
dried
outor
cracked
.
"
Inspect
heat
shield
and
replace
if
corroded
.
"
Inspect
rubber
buffers
and
liners
on
fuel
tank,
support
straps
and
on
underside
of
body
.
Replace
rubber
parts
that
are
hardened
or
damaged
.
FUEL
LEVEL
SENDERS
CAUTION-
"
Before
starting
the
engine,
fill
the
fuel
tank
with
at
least
1.5
gallons
(5
liters)
of
fuel
to
prevent
damaging
a
dry
fuel
pump
.
"
If
the
filler
neck
has
been
removed
from
the
body,
be
sure
toreattach
theneck's
grounding
screw
(where
applicable)
.
Check
electrical
resistance
between
the
ground
tab
and
wheel
hub
.
The
re-
sistance
shouldbeno
higher
than
0
.6
ohms
.
Tightening
Torques
"
Fuel
tank
to
body
.............
...
23
Nm
(17
ft-Ib)
"
Hose
clamps
(10
mm-16
mm
día
.)
..
2
.0
Nm
(18
in-lb)
Fuel
Tank
Evaporative
Control
System
The
fuel
tank
evaporative
control
system
is
used
to
vent
the
fuel
tank
to
a
charcoal
canister,
which
is
then
purgedby
en-
gine
vacuum
during
normal
engine
operatíon
.
This
controls
emission
of
raw
hydrocarbons
(fuel)
to
the
atmosphere
.
See
Fig
.
1
.
A
fuel
expansion
tank,
located
under
the
right
rear
fender,
traps
overflow
fuel
and
incorporates
extra
fuel
tank
plumbing
.
Startingwith
1996
models,
OBD
II
standards
require
that
the
fuel
tank
evaporative
control
system
be
monitored
for
leaks
.
This
is
accomplished
usingthe
fuel
tankpressuresen-
sor,
the
ventshut
off
valve,
and
the
evaporative
purge
valve
.
NOTE-
On
most
early
cars(1992-1995),
the
charcoal
canister
is
in
the
engine
compartment
.
On
latercars,
the
char-
coal
canister
is
under
the
spare
tire
in
the
luggage
com-
partment
.
FUEL
LEVEL
SENDERS
The
right
side
fuel
leve¡
sender
is
integrated
with
the
fuel
pump
.
Each
senderhas
a
float
connected
to
a
variable
resis-
tance
for
fuel
leve¡
.
When
replacing
the
sender/pump
assem-
bly
always
replace
hose
clamps,gaskets
and
O-rings
.
WARNING
-
When
removing
the
fuel
level
sender
or
the
fuel
pump,
the
fuel
tank
should
be
emptied
.
Page 189 of 759
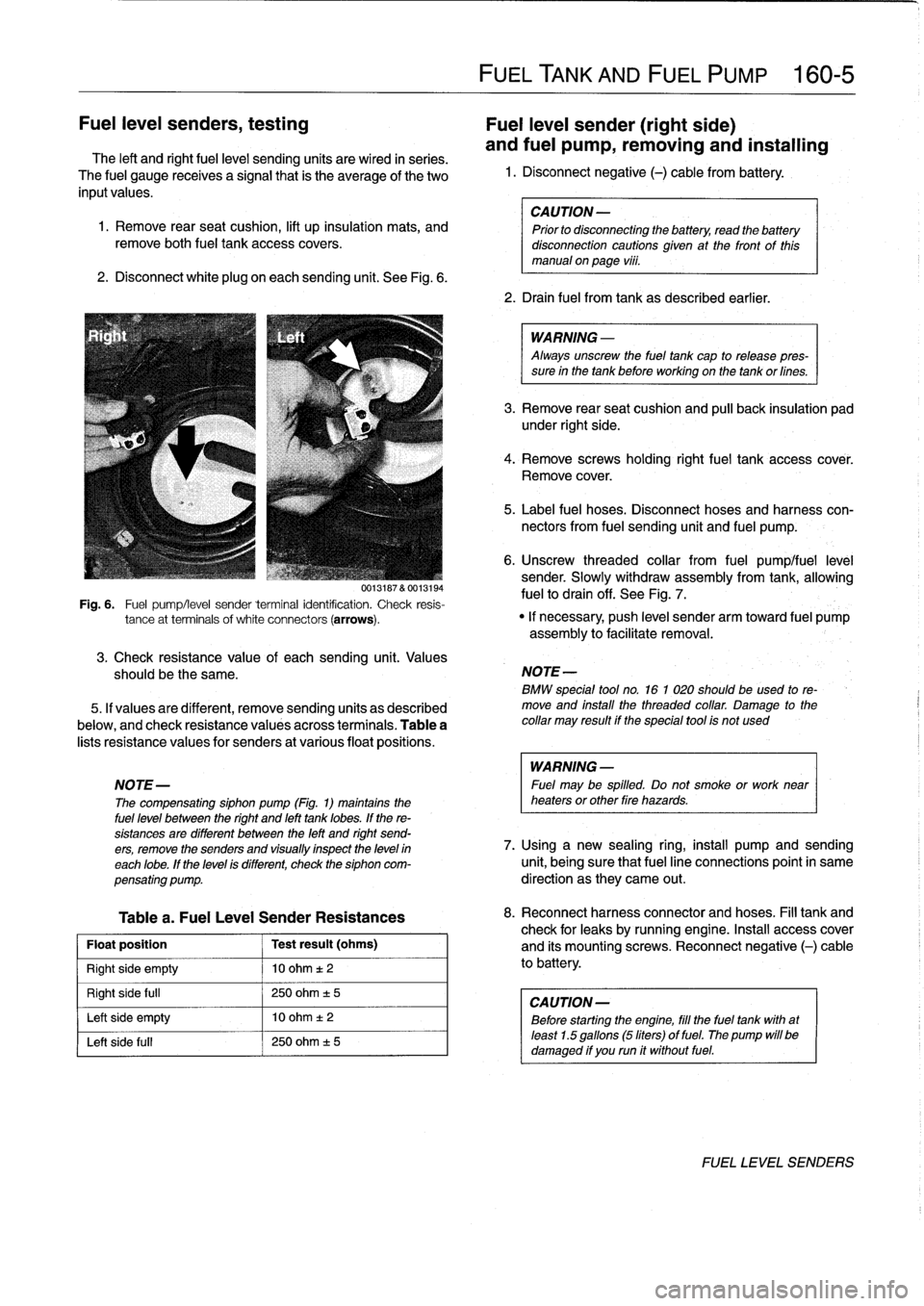
Fuel
leve¡
senders,
testing
Fuel
leve¡
sender
(right
side)
The
left
and
right
fuelleve¡
sending
units
are
wired
in
series
.
and
fuel
pump,
removing
and
installing
The
fuel
gauge
receives
a
signal
that
is
the
average
of
the
two
1
.
Disconnect
negative
(-)
cable
from
battery
.
input
values
.
1
.
Remove
rear
seat
cushion,
lift
up
insulation
mats,
andremove
both
fuel
tank
access
covers
.
2
.
Disconnect
white
plug
on
each
sending
unit
.
See
Fig
.
6
.
3
.
Check
resistance
value
of
eachsending
unit
.
Values
should
be
the
same
.
5
.
If
valuesare
different,
remove
sending
units
as
described
below,
and
check
resistance
valuésacross
terminals
.
Table
a
lists
resistance
values
for
senders
at
various
float
positions
.
Table
a
.
Fuel
Leve¡
Sender
Resistances
Float
position
Test
result
(ohms)
Right
side
empty
10
ohm
t2
Right
side
full
250
ohm
±
5
Left
side
empty
10
ohm
t
2
Left
side
fui¡
250
ohm
±
5
FUEL
TANK
AND
FUEL
PUMP
160-
5
CAUTION
-
Prior
to
disconnecting
the
battery,
read
the
battery
disconnection
cautionsglven
at
the
front
of
this
manual
onpage
viii
.
2
.
Drain
fuel
from
tank
as
described
earlier
.
WARNING
-
Always
unscrew
the
fuel
tank
cap
to
release
pres-
sure
in
the
tank
before
working
on
the
tank
or
fines
.
3
.
Remove
rear
seat
cushion
and
pull
back
insulation
pad
under
right
side
.
4
.
Remove
screws
holding
rightfuel
tank
accesscover
.
Remove
cover
.
5
.
Label
fuel
hoses
.
Disconnect
hoses
and
harness
con-
nectors
from
fuel
sending
unit
and
fuel
pump
.
6
.
Unscrew
threaded
collar
from
fuel
pumplfuel
leve¡
sender
.
Slowly
withdraw
assembly
from
tank,allowing
fuelto
drain
off
.
See
Fig
.
7
.
0013187
&
0013194
Fig
.
6
.
Fuel
pump/leve¡
sender
terminal
identification
.
Check
resis-
tance
at
terminals
of
white
connectors
(arrows)
.
"
If
necessary,
push
leve¡
sender
arm
toward
fuel
pump
assembly
to
facilitate
removal
.
NOTE
-
BMW
special
tool
no
.
16
1
020
should
beused
to
re-
move
and
install
the
threaded
collar
.
Damage
to
the
collar
may
result
if
the
special
tool
is
not
used
WARNING
-
NOTE-
Fuel
may
be
spilled
.
Do
not
smoke
or
work
near
The
compensating
siphon
pump
(Fig
.
1)
maintains
the
heaters
or
other
fire
hazards
.
fuel
leve¡
between
the
right
and
left
tank
lobes
.
If
the
re-
sistances
are
different
between
the
left
and
right
send-
ers,
remove
the
senders
and
visually
inspect
the
leve)
in
7
.
Using
a
new
sealing
ring,
install
pump
and
sending
each
lobe
.
If
the
leve¡
is
different,
check
the
siphon
com-
unit,
being
sure
that
fuel
line
connections
point
in
same
pensating
pump
.
direction
as
they
carne
out
.
8
.
Reconnect
harnessconnector
and
hoses
.
Fill
tank
and
check
for
leaks
by
running
engine
.
Insta¡¡
access
cover
and
its
mountingscrews
.
Reconnect
negative
(-)
cable
to
battery
.
CAUTION
-
Before
starting
the
engine,
fill
the
fuel
tank
with
at
least
1
.5
gallons
(5liters)
of
fuel
.
The
pump
will
be
damaged
if
you
run
it
without
fuel
.
FUEL
LEVEL
SENDERS
Page 190 of 759
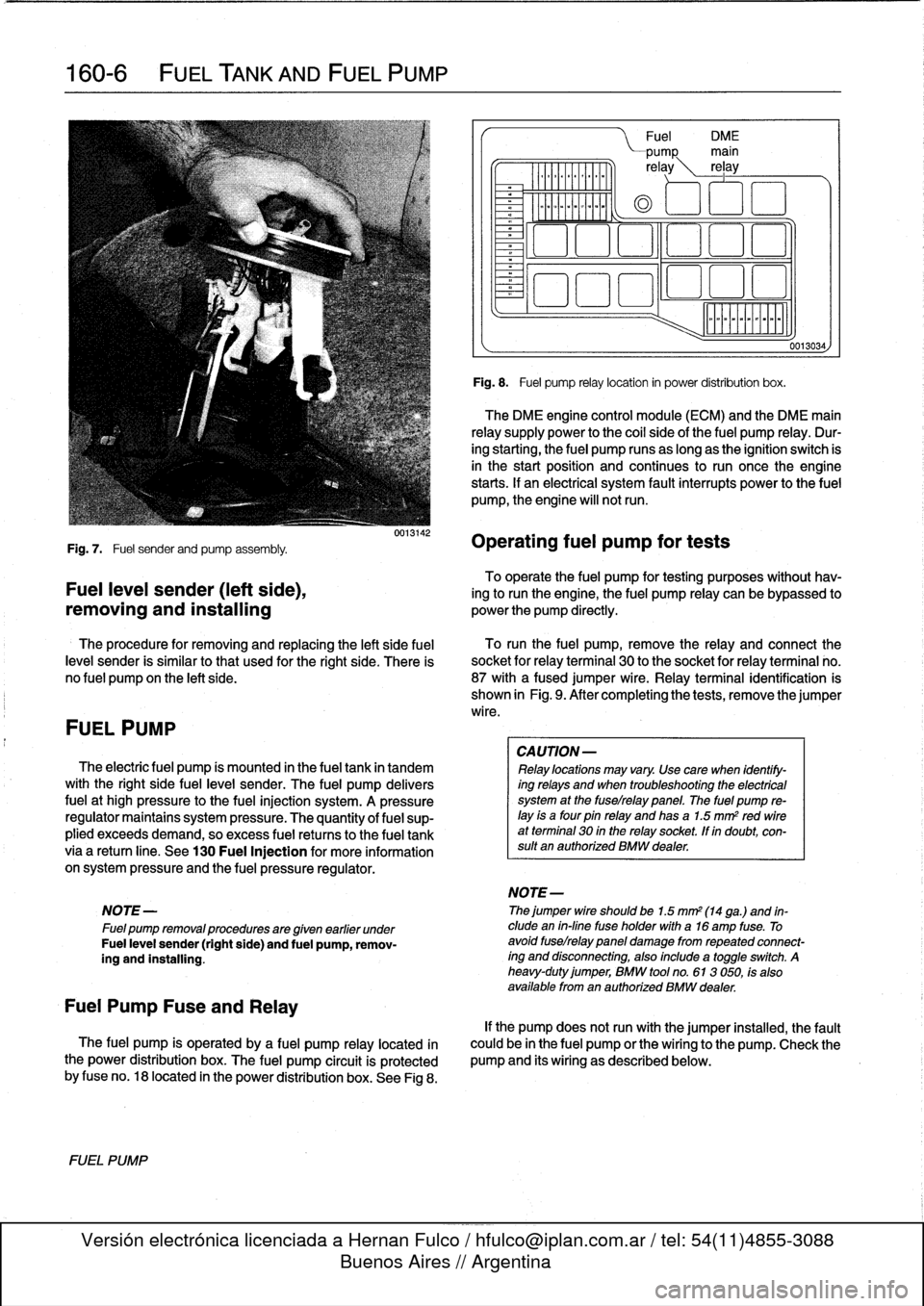
160-
6
FUEL
TANK
AND
FUEL
PUMP
Fig
.
7
.
Fuel
sender
and
pump
assembly
.
To
operate
the
fuel
pump
for
testing
purposes
without
hav-
Fuel
leve¡
sender
(left
side),
ing
to
runthe
engine,
the
fuel
pump
relay
can
be
bypassed
to
removing
and
installing
powerthe
pump
directly
.
The
procedure
for
removing
and
replacing
the
left
side
fuel
To
runthe
fuel
pump,
remove
the
relay
and
connect
the
leve¡
sender
is
similar
tothat
used
for
the
right
side
.
There
is
socket
for
relayterminal
30
to
the
socket
for
relay
terminal
no
.
no
fuel
pump
on
the
left
side
.
87
with
afused
jumper
wire
.
Relay
terminal
identification
is
shown
in
Fig
.
9
.
After
completing
the
tests,
remove
the
jumper
wire
.
FUEL
PUMP
The
electric
fuel
pump
ís
mounted
in
the
fuel
tank
in
tandem
with
the
right
side
fuelleve¡
sender
.
The
fuel
pump
delivers
fuel
at
high
pressure
to
the
fuel
injection
system
.
A
pressure
regulator
maintains
system
pressure
.
The
quantity
of
fuel
sup-
plied
exceeds
demand,
so
excess
fuel
retums
to
the
fuel
tank
via
a
retum
líne
.
See
130
Fuel
Injection
for
more
information
on
system
pressure
and
the
fuel
pressure
regulator
.
NOTE
-
Fuel
pump
removalprocedures
are
given
earlier
under
Fuel
leve¡
sender
(right
side)
and
fuel
pump,
remov-
íng
and
installing
.
Fuel
Pump
Fuse
and
Relay
The
fuel
pump
is
operated
by
a
fuel
pump
relay
located
ín
the
power
distribution
box
.
The
fuel
pump
circuit
is
protected
by
fuse
no
.
18
located
in
the
power
distribution
box
.
See
Fig
8
.
FUEL
PUMP
0013142
Fuel
DM
E
PUMP
main
re
ay
rel
ay
0
aoo
o
~a
aao
ó
Fig
.
8
.
Fuel
pump
relay
location
in
power
distribution
box
.
The
DME
engine
control
module
(ECM)
and
the
DME
main
relay
supply
power
to
the
coi¡
sideof
the
fuel
pump
relay
.
Dur-
ing
starting,
the
fuel
pump
runs
as
long
as
the
ignition
switch
is
in
the
start
position
and
continues
to
run
oncethe
engine
starts
.
If
an
electrical
system
fault
interrupts
power
to
the
fuel
pump,
the
engine
will
notrun
.
Operating
fuel
pump
for
tests
CA
UTION-
Relay
locations
may
vary
.
Use
care
when
identify-
ing
relays
and
when
troubleshooting
the
electrical
system
at
the
fuselrelay
panel
.
The
fuel
pump
re-
¡ay
is
a
four
pin
relay
and
has
a
1.5
mm
2
red
wireat
terminal
30
in
the
relay
socket,
lf
in
doubt,
con-
sult
an
authorized
BMW
dealer
.
NOTE-
Thejumper
wire
shouldbe
1.5
mm2
(14
ga
.)
and
in-
clude
en
in-fine
fuse
holder
with
a16
amp
fuse
.
To
avoid
fuselrelay
panel
damage
fromrepeated
connect-
íng
and
disconnecting,
also
include
a
toggleswitch
.
A
heavy-duty
jumper,
BMW
tool
no
.
613
050,
fs
also
available
from
en
authorized
BMW
dealer
.
0013034,
If
the
pump
does
notrun
with
the
jumper
installed,
the
fault
could
be
in
the
fuel
pump
or
the
wiring
to
the
pump
.
Check
the
pump
and
its
wiring
as
described
below
.
Page 191 of 759
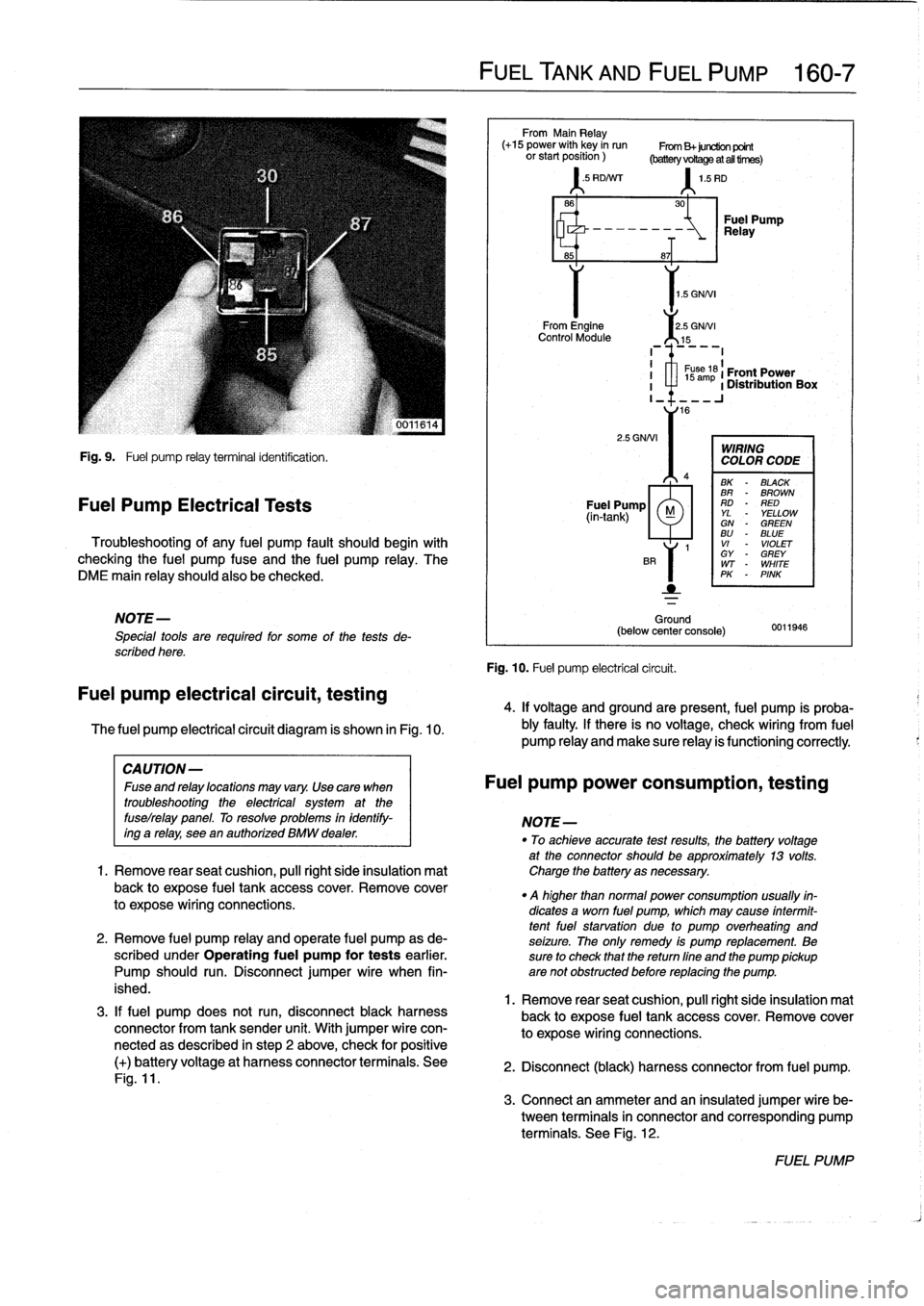
Fig
.
9
.
Fuel
pump
relay
terminal
identification
.
Fuel
Pump
Electrical
Tests
Troubleshooting
of
any
fuel
pump
fault
should
begin
with
checking
the
fuel
pump
fuse
and
the
fuel
pump
relay
.
The
DME
main
relay
should
also
be
checked
.
NOTE-
Special
tools
are
requíred
for
some
of
the
tests
de-
scribed
here
.
Fuel
pump
electrical
circuit,
testing
The
fuel
pump
electrical
circuit
diagram
is
shown
in
Fig
.
10
.
3
.
If
fuel
pump
does
not
run,
disconnect
black
harness
connector
from
tank
sender
unit
.
With
jumper
wire
con-
nectedas
described
in
step
2
above,
check
for
positive
(+)
batteryvoltage
at
harness
connector
terminals
.
See
Fig
.
11
.
FUEL
TANK
AND
FUEL
PUMP
160-
7
From
Main
Relay
(+15
power
with
key
in
run
From
B+juretion
point
orstartposition)
(batteryvoRageatalltirnes)
'
.5
RD/Nrr
1
.5
RD
1
.5
GNNI
From
Engine
2
.5
GNNI
Control
Module
15
2
.5
GNNI
Ground
(below
center
console)
Fig
.
10
.
Fuel
pump
electrical
circuit
.
30
-~
Relay
Fuel
Pump
8~T
I
1
s
ám
61
Front
Power
I
a
1
Distribution
Box
I_
16
WIRING
COLOR
CODE
BK
-
BLACK
BR
-
BROWN
Fuel
Pump
RD
-
RED
(in-tank)
M
YL
YELLOWGN
-
GREENBU
-
BLUE
1
VI
-
VIOLET
GY
-
GREY
WT
-
WHITE
PK
-
PINK
0011946
4
.
If
voltage
and
groundare
present,
fuel
pump
is
proba-
bly
faulty
.
If
there
is
no
voltage,
check
wiring
From
fuel
pump
Reay
and
make
sure
Reay
is
functioning
correctly
.
CAUTION-
Fuseandrelaylocationsmayvary
.
Usecara
when
Fuel
pump
power
consumption,
testing
troubleshooting
the
electrical
system
at
the
fuselrelay
panel
.
To
resolve
problems
in
identify-
NOTE-
ing
a
relay,
see
en
authorízed
BMW
dealer
.
"
To
achieveaccurate
testresults,
fhe
battery
voltage
at
the
connector
should
be
approximately
13
volts
.
1.
Remove
rearseat
cushion,
pull
right
side
insulation
mat
Charge
the
battery
asnecessary
.
back
to
expose
fuel
tank
accesscover
.
Remove
cover
.
q
higher
than
normal
power
consumption
usually
fin-
to
expose
wiring
connections
.
dicates
a
worn
fuel
pump,
which
may
cause
intermit-
tentfuel
starvation
due
lo
pump
overheating
and
2
.
Remove
fuel
pump
relay
and
opérate
fuel
pump
as
de-
seizure
.
The
only
remedy
is
pump
replacement
.
Be
scribed
under
Operating
fuel
pump
for
tests
earlier
.
sure
to
check
that
thereturn
fine
and
the
pump
pickup
Pump
should
run
.
Disconnect
jumper
wire
when
fin-
are
not
obstructed
before
replacing
the
pump
.
ished
.
1
.
Remove
rear
seat
cushion,
pull
right
side
insulation
mal
back
to
expose
fuel
tank
accesscover
.
Remove
cover
to
expose
wiring
connections
.
2
.
Disconnect
(black)
harness
connector
from
fuel
pump
.
3
.
Connect
an
ammeter
and
an
insulated
jumper
wire
be-
tween
terminals
in
connector
and
corresponding
pump
terminals
.
See
Fig
.
12
.
FUEL
PUMP
Page 192 of 759
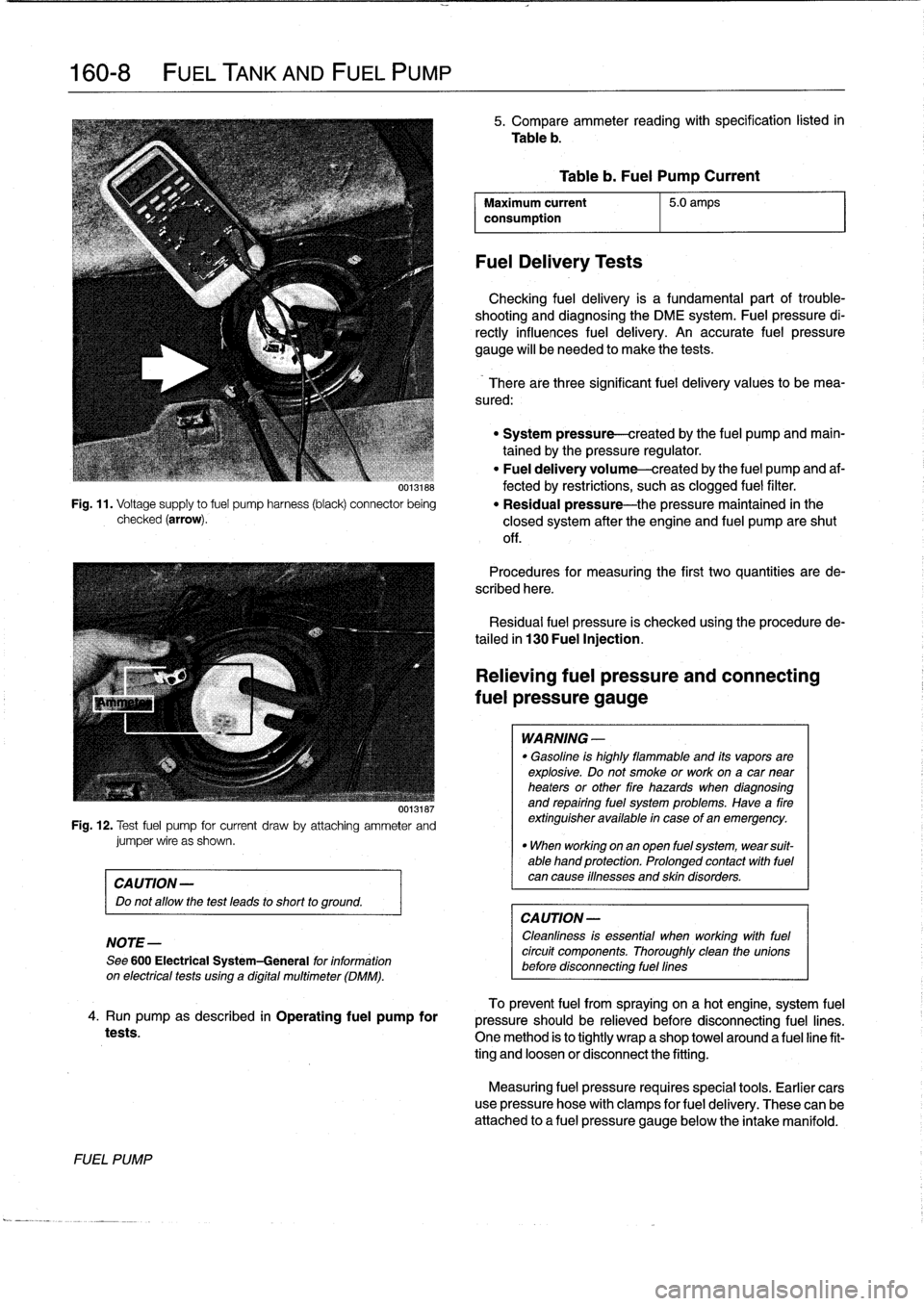
160-
8
FUEL
TANK
AND
FUEL
PUMP
UU131
tst5
Fig
.
11
.
Voltage
supply
to
fuel
pump
harness
(black)
connector
being
checked
(arrow)
.
00131ts7
Fig
.
12
.
Test
fuel
pump
for
current
draw
by
attadhing
ammeter
andjumper
wire
as
shown
.
CAUTION-
Do
not
allow
the
test
leads
to
short
to
ground
.
NOTE-
See
600
Electrical
System-General
for
information
on
electricaltests
using
a
digital
multimeter
(DMM)
.
4
.
Run
pump
as
described
in
Operating
fuel
pump
for
tests
.
FUEL
PUMP
5
.
Compare
ammeter
reading
with
specification
listed
in
Table
b
.
Maximum
current
5
.0
amps
consumption
FuelDelivery
Tests
Table
b
.
Fuel
Pump
Current
Checking
fuel
delivery
is
a
fundamental
part
of
trouble-
shooting
and
diagnosing
the
DME
system
.
Fuelpressure
di-
rectly
influences
fuel
delivery
.
An
accurate
fuel
pressure
gauge
will
be
needed
to
make
the
tests
.
There
arethree
significant
fuel
delivery
values
to
bemea-
sured
:
"
System
pressure-created
by
the
fuel
pump
and
main-
tained
by
the
pressure
regulator
.
"
Fuel
delivery
volume-created
by
the
fuel
pump
and
af-
fected
by
restrictions,
suchas
clogged
fuel
filter
.
"
Residual
pressure-the
pressure
maintained
in
the
closed
system
after
the
engine
and
fuel
pump
areshut
off
.
Procedures
for
measuring
the
first
two
quantities
arede-
scribed
here
.
Residual
fuel
pressure
is
checked
using
the
procedurede-
tailed
in
130
Fuel
Injection
.
Relieving
fuel
pressure
and
connecting
fuel
pressure
gauge
WARNING
-
"
Gasoline
is
highly
flammable
and
its
vaporsare
explosive
.
Do
not
smoke
or
work
ona
car
near
heaters
or
other
fire
hazards
when
diagnosing
and
repairing
fuel
system
problems
.
Have
a
fire
extinguisher
available
in
case
of
an
emergency
.
"
When
working
onan
open
fuel
system,
wear
suit-
able
hand
protection
.
Prolonged
contact
with
fuel
can
cause
iflnesses
and
skin
disorders
.
CA
UTION-
Cleanliness
is
essential
when
working
withfuel
circuit
components
.
Thoroughly
clean
the
unionsbefore
disconnecting
fuel
fines
To
prevent
fuel
from
spraying
on
a
hotengine,
system
fuel
pressure
should
be
relieved
before
disconnecting
fuel
lines
.
One
method
is
to
tightly
wrap
a
shop
towel
around
a
fuel
line
fit-
ting
and
loosen
or
disconnect
the
fitting
.
Measuring
fuel
pressure
requires
special
tools
.
Earlier
cars
use
pressure
hose
with
clamps
for
fuel
delivery
.
These
can
be
attached
to
a
fuel
pressure
gauge
below
the
intake
manifold
.