check engine BMW M3 1998 E36 Workshop Manual
[x] Cancel search | Manufacturer: BMW, Model Year: 1998, Model line: M3, Model: BMW M3 1998 E36Pages: 759
Page 217 of 759
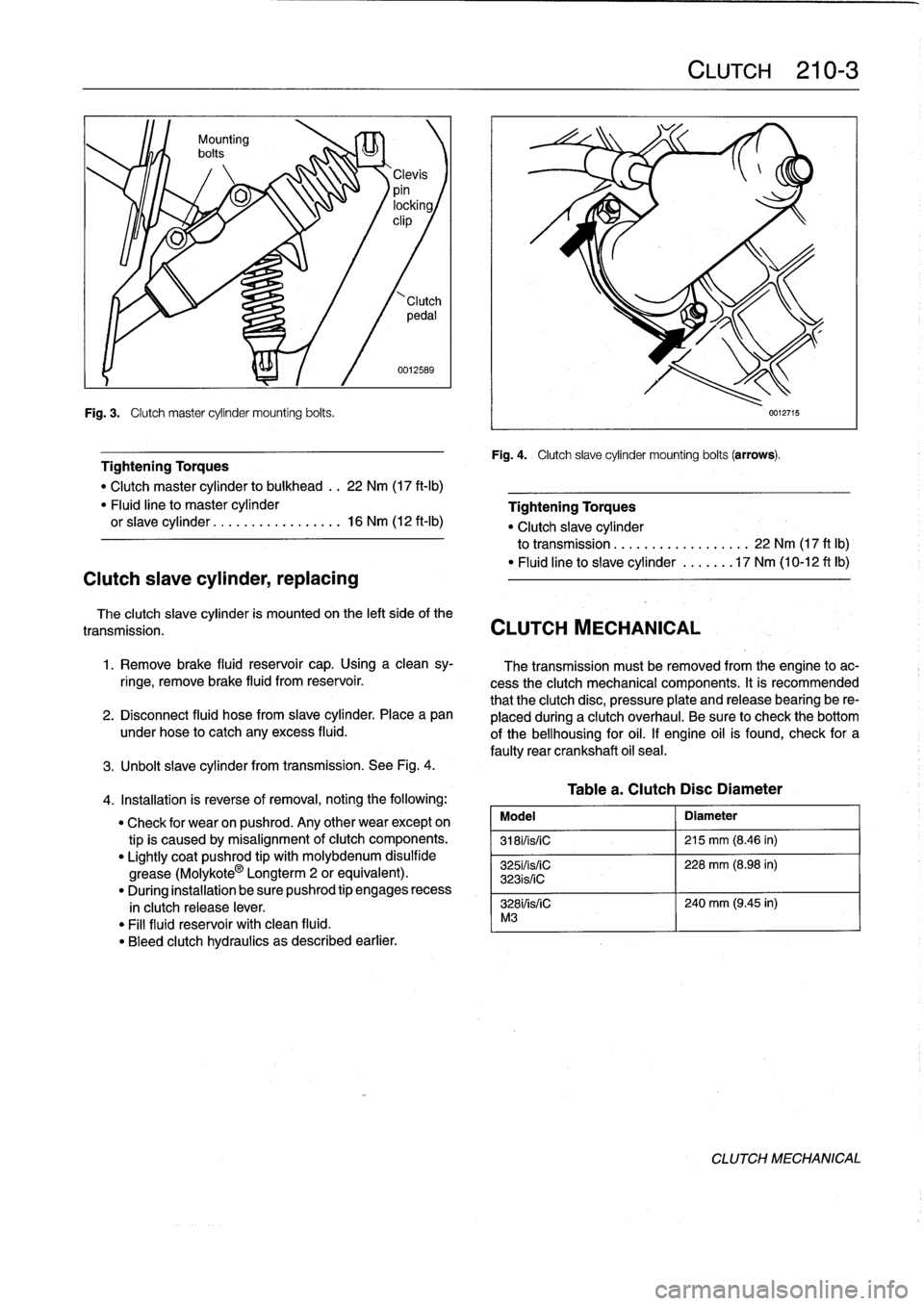
Fig
.
3
.
Clutch
master
cylinder
mounting
bolts
.
Clutch
slave
cylinder,
replacing
0012589
Tightening
Torques
"
Clutch
master
cylinder
to
bulkhead
..
22
Nm
(17
ft-Ib)
"
Fluid
line
to
master
cylinder
orslave
cylinder
.................
16
Nm
(12
ft-1b)
The
clutch
slave
cylinder
is
mounted
on
the
left
side
of
the
transmission
.
CLUTCH
MECHANICAL
1
.
Remove
brake
fluid
reservoir
cap
.
Using
a
clean
sy-
ringe,
remove
brake
fluid
from
reservoir
.
2
.
Disconnect
fluid
hose
from
slave
cylinder
.
Place
a
pan
under
hose
to
catch
any
excess
fluid
.
3
.
Unbolt
slave
cylinder
from
transmission
.
See
Fig
.
4
.
4
.
Installation
is
reverse
of
removal,
noting
the
following
:
"
Check
for
wear
on
pushrod
.
Any
other
wear
except
on
tipis
caused
by
misalignment
of
clutch
components
.
"
Lightly
coat
pushrod
tip
with
molybdenum
disulfide
grease
(Molykote
0
Longterm
2
or
equivalent)
.
"
During
installation
be
sure
pushrod
tip
engages
recess
in
clutch
release
lever
.
"
Fill
fluid
reservoir
with
clean
fluid
.
"
Bleed
clutch
hydraulics
as
described
earlier
.
CLUTCH
210-
3
Fig
.
4
.
Clutch
slave
cylinder
mounting
bolts
(arrows)
.
Tablea
.
ClutchDisc
Diameter
Model
Diameter
3181/is/iC
215
mm
(8
.46
in)
325i/is/iC
228
mm
(8
.98
in)
323is/iC
328i/is/iC
240
mm
(9
.45
in)
M3
0012715
Tightening
Torques
"
Clutch
slave
cylinder
to
transmission
.
.
................
22
Nm
(17
ft
lb)
"
Fluid
line
to
slave
cylinder
......
.17
Nm
(10-12
ft
lb)
The
transmission
must
be
removed
from
the
engine
to
ac-
cess
the
clutch
mechanical
components
.
It
is
recommended
that
the
clutch
disc,
pressure
plate
and
release
bearing
be
re-
placed
duringa
clutch
overhaul
.
Be
sure
to
check
the
bottom
of
the
bellhousing
for
oil
.
If
engine
oil
is
found,
check
for
a
faulty
rear
crankshaft
oil
seal
.
CLUTCH
MECHANICAL
Page 221 of 759
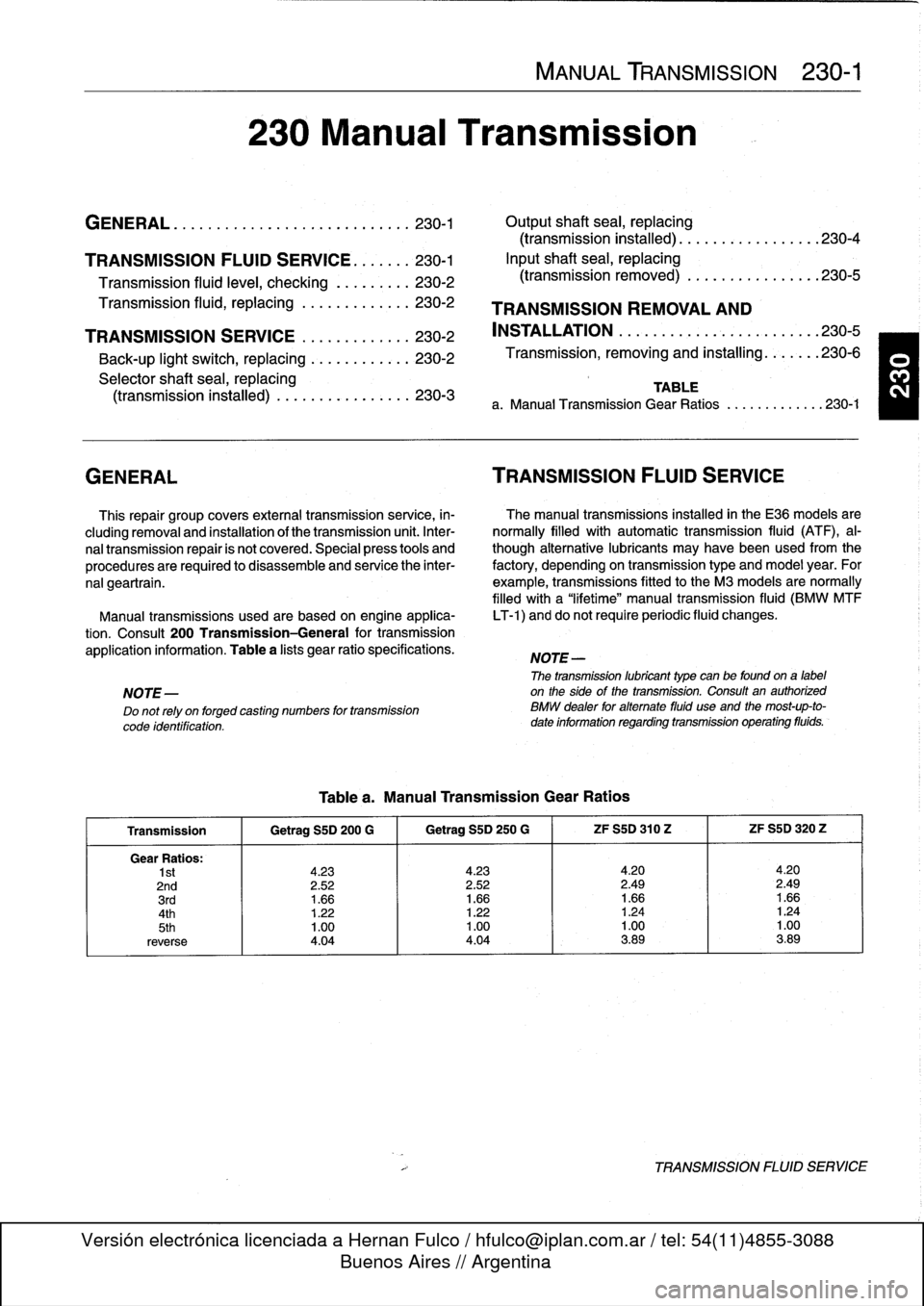
230
Manual
Transmission
MANUAL
TRANSMISSION
230-1
GENERAL
...
.
............
.
.......
.
.
.
.
230-1
Output
shaft
sea¡,
replacing
(transmission
installed)
....
.
.....
.
.....
.230-4
TRANSMISSION
FLUID
SERVICE
.
.
.
.
.
.
.230-1
Inputshaft
sea¡,
replacing
Transmission
fluid
leve¡,
checking
...
.
...
.
.
230-2
(transmission
removed)
.
.
.
.
...
.
.
.
.....
.
230-5
Transmission
fluid,
replacing
.........
.
.
.
.
230-2
TRANSMISSION
REMOVAL
AND
TRANSMISSION
SERVICE
.
.
.....
.
.
.
.
.
.
230-2
INSTALLATION
.
.
.
.
.
.
.....
.
.
.
.
.
.
.
.....
.
230-5
Back-up
light
switch,
replacing
.
.
.
...
.
.
.
.
.
.
230-2
Transmission,
removing
and
installing
...
.
.
.
.
230-6
_
Selector
shaft
sea¡,
replacing
(transmission
installed)
.
.
.
.
.
.
.
.
.
.
.
...
.
.
230-3
TAB
a
.
Manual
Transmission
Gear
Ratios
.
.
.
.........
.230-1
GENERAL
TRANSMISSION
FLUID
SERVICE
This
repair
group
covers
external
transmission
service,
in-
The
manual
transmissions
installed
in
the
E36
models
are
cluding
removal
and
installation
of
thetransmission
unit
.
Inter-
normally
filled
with
automatic
transmission
fluid
(ATF),
al-
nal
transmission
repair
is
not
covered
.
Special
press
tools
and
though
alternative
lubricants
may
have
beenused
from
the
procedures
are
required
to
disassemble
and
service
the
inter-
factory,
depending
on
transmission
type
and
model
year
.
For
nal
geartrain
.
example,
transmissions
fitted
to
the
M3
models
are
normally
filled
with
a
"lifetime"
manual
transmission
fluid
(BMW
MTF
Manual
transmissions
used
are
based
on
engine
applica-
LT-1)
and
do
not
require
periodic
fluid
changes
.
tion
.
Consult
200
Transmission-General
for
transmission
application
information
.
Table
a
lists
gear
ratio
specifications
.
NOTE-
The
transmission
lubricant
type
can
be
found
ona
label
NOTE-
on
the
sideof
the
transmission
.
Consult
an
authorized
Do
not
rely
on
forged
casting
numbers
for
transmission
BMW
dealer
for
altemate
fluid
use
and
the
most-up-to-
code
identification
.
date
information
regarding
transmission
operating
fluids
.
Tablea
.
Manual
Transmission
Gear
Ratios
Transmission
1
Getrag
S5D
200
G
1
Getrag
SSD
250
G
1
ZF
S5D
310
Z
1
ZF
S5D
320
Z
Gear
Ratios
:
1st
4
.23
4
.23
4
.20
4
.20
2nd
2
.52
2
.52
2
.49
2
.49
3rd
1
.66
1
.66
1
.66
1
.664th
1
.22
1
.22
1
.24
1
.24
5th
1
.00
1
.00
1
.00
1
.00
reverse
4
.04
4
.04
3
.89
3
.89
TRANSMISSION
FLUID
SERVICE
Page 223 of 759
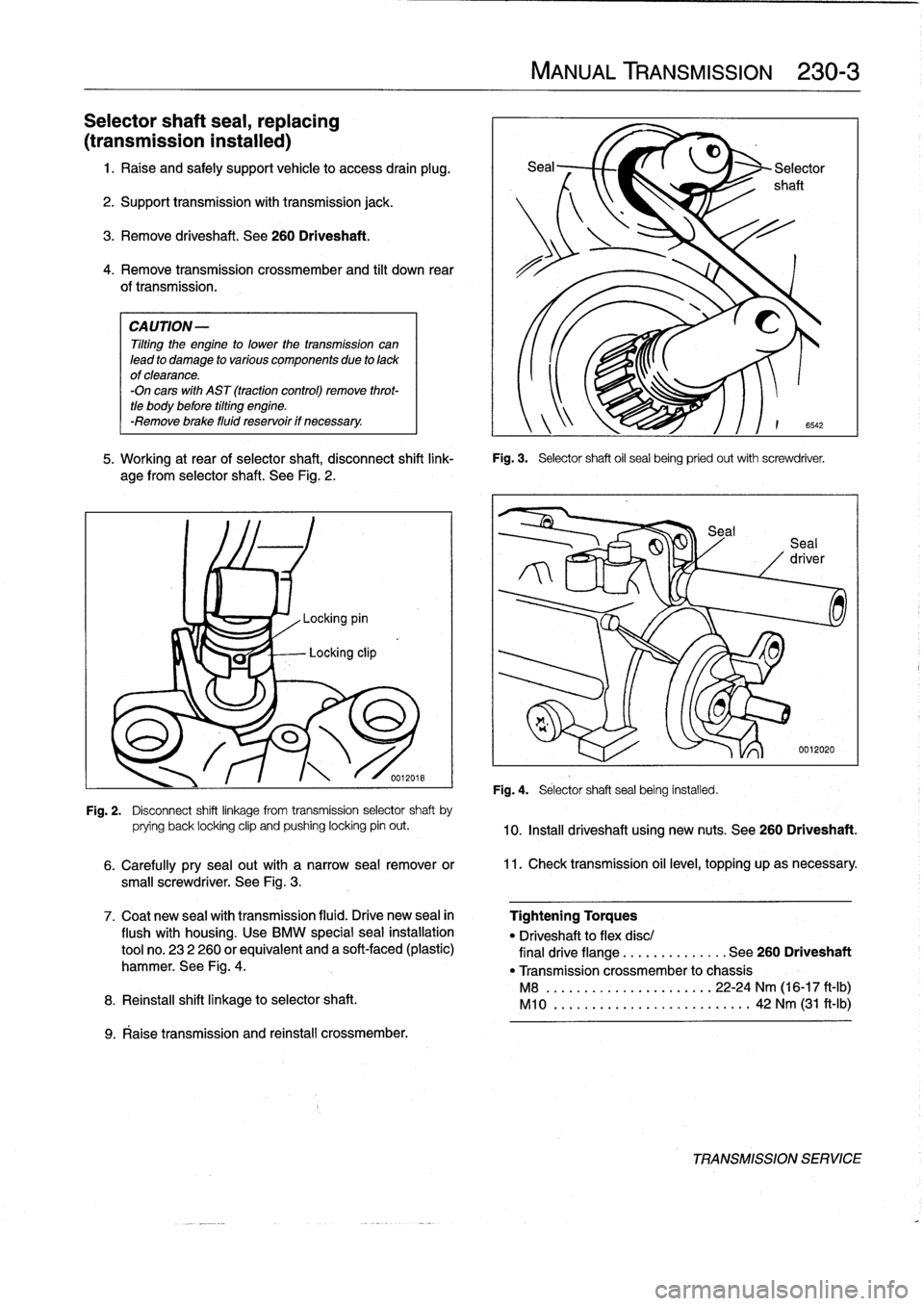
Selector
shaft
seal,
replacing
(transmission
instalied)
1
.
Raise
and
safely
support
vehicle
to
access
drain
plug
.
2
.
Support
transmission
with
transmission
jack
.
3
.
Remove
driveshaft
.
See
260
Driveshaft
.
4
.
Remove
transmission
crossmember
and
tilt
down
rear
of
transmission
.
CA
UTION--
Tilting
the
engine
to
lower
the
transmission
can
lead
to
damage
to
various
cgmponents
due
to
lack
of
clearance
.
-On
cars
with
AST
(traction
control)
remove
throt-
tle
body
before
tiltlng
engine
.
-Remove
brake
fluid
reservoir
lf
necessary
.
Locking
pin
á
Locking
clip
8
.
Reinstall
shift
linkage
to
selectorshaft
.
7
.
Coat
new
seal
with
transmission
fluid
.
Drive
new
seal
in
flush
with
housing
.
Use
BMW
special
seal
installation
tool
no
.
23
2
260
orequivalent
and
a
soft-faced
(plastic)
hammer
.
See
Fig
.
4
.
9
.
Fiaise
transmission
and
reinstall
crossmember
.
MANUAL
TRANSMISSION
230-
3
Seal
Selector
_
shaft
5
.
Working
at
rear
of
selector
shaft,
disconnect
shift
link-
Fig
.
3
.
Selector
shaft
oil
sea¡
being
pried
out
with
screwdriver
.
age
from
selectorshaft
.
See
Fig
.
2
.
Fig
.
4
.
Selector
shaftseal
being
installed
.
6542
0012020
Fig
.
2
.
Disconnect
shift
linkage
from
transmission
selector
shaft
by
prying
back
locking
clip
and
pushing
locking
pin
out
.
10
.
Install
driveshaft
using
new
nuts
.
See260
Driveshaft
.
6
.
Carefully
pry
sea¡
out
with
a
narrow
seal
remover
or
11
.
Check
transmission
oil
level,
topping
upas
necessary
.
small
screwdriver
.
See
Fig
.
3
.
Tightening
Torques
"
Driveshaftto
flex
disc/
final
drive
flange
..............
See
260
Driveshaft
"
Transmission
crossmember
to
chassis
M8
........
..
.
...
........
22-24
Nm
(16-17
ft-1b)
M10
........
.
.
...
...
.
.........
42
Nm
(31
ft-Ib)
TRANSMISSIONSERVICE
Page 225 of 759
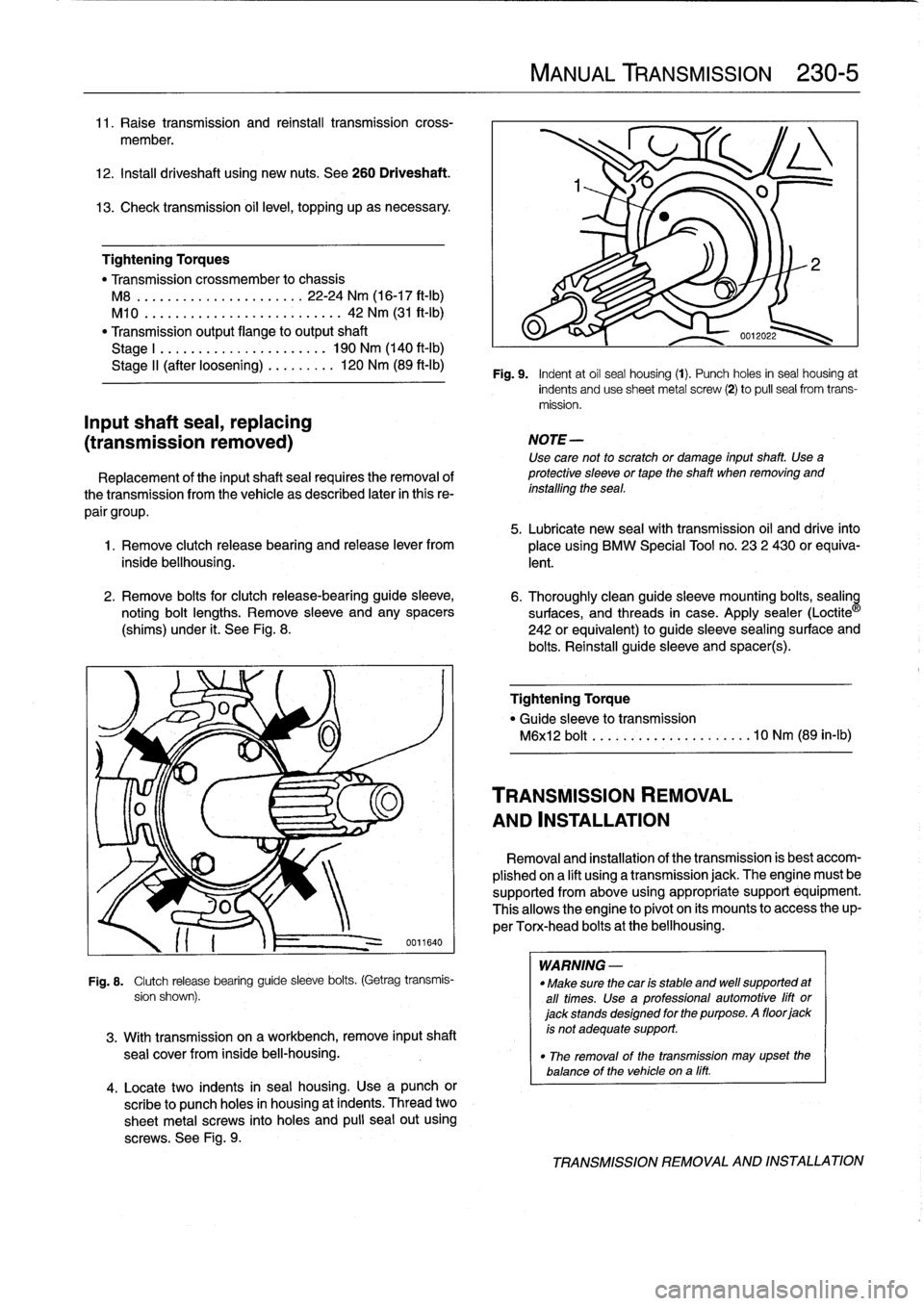
11
.
Raise
transmission
and
reinstall
transmission
cross-
member
.
12
.
Install
driveshaft
using
new
nuts
.
See
260
Driveshaft
.
13
.
Check
transmission
oil
leve¡,
topping
up
asnecessary
.
Tightening
Torques
"
Transmission
crossmember
to
chassis
M8
...............
.
...
.
..
22-24
Nm
(16-17
ft-Ib)
M10
..............
.
..
...
..
.
...
42
Nm
(31
ft-Ib)
"
Transmission
outputflange
to
output
shaft
O
001202
2
Z
:Z
ZZZ~
%
_
j
Stage
I.................
..
.
..
190
Nm
(140
ft-Ib)
Stage
II
(after
loosening)
....
.
.
.
..
120
Nm
(89
ft-Ib)
Fi
g
.
9
.
Indent
at
oil
seal
housing
(1)
.
Punch
holes
in
seal
housing
at
Inputshaft
sea¡,
replacing
(transmission
removed)
Replacement
of
the
inputshaft
sea¡
requires
the
removal
of
thetransmission
from
the
vehicle
as
described
later
in
this
re-
pair
group
.
5
.
Lubricate
new
sea¡with
transmission
oil
and
drive
into
1
.
Remove
clutch
release
bearing
and
release
lever
from
placeusing
BMW
Special
Tool
no
.
23
2
430
or
equiva-
inside
bellhousing
.
lent
.
2
.
Remove
bolts
for
clutch
release-bearing
guide
sleeve,
6
.
Thoroughly
cleanguide
sleeve
mounting
bolts,
sealin
noting
bolt
lengths
.
Remove
sleeve
and
any
spacers
surfaces,
and
threads
in
case
.
Apply
sealer
(Loctite
(shims)
under
¡t
.
See
Fig
.
8
.
242
or
equivalent)
to
guide
sleeve
sealingsurface
and
bolts
.
Reinstall
guide
sleeve
and
spacer(s)
.
0011640
Fig
.
8
.
Clutch
release
bearing
guide
sleeve
bolts
.
(Getrag
transmis-
sion
shown)
.
3
.
With
transmission
on
aworkbench,
remove
input
shaft
sea¡
cover
from
inside
bel¡-housing
.
4
.
Locate
two
indents
in
seal
housing
.
Use
a
punch
or
scribe
to
punch
holes
in
housing
at
indents
.
Thread
two
sheetmetal
screws
into
holes
and
pulí
seal
out
using
screws
.
See
Fig
.
9
.
MANUAL
TRANSMISSION
230-
5
indents
anduse
sheetmetal
screw
(2)
to
pul¡
sea¡
from
trans-
mission
.
NOTE-
Use
care
not
to
scratch
or
damage
input
shaft
.
Use
a
protective
sleeve
or
tape
the
shaft
when
removing
and
installing
the
sea¡
.
Tightening
Torque
"
Guide
sleeveto
transmission
M6xl2
bolt
.......
...
.
.
.........
10
Nm
(89
in-lb)
TRANSMISSION
REMOVAL
AND
INSTALLATION
Removal
and
installation
of
the
transmission
is
best
accom-
plished
ona
lift
using
a
transmission
jack
.
The
engine
must
be
supported
from
above
using
appropriate
support
equipment
.
Thisallows
the
engine
to
pivot
on
its
mounts
to
access
theup-
perTorx-head
bolts
at
the
bellhousing
.
WARNING
-
"
Make
sure
thecar
is
stable
and
well
supported
at
all
times
.
Use
a
professional
automotive
lift
or
jack
stands
designed
for
the
purpose
.
A
floor
jack
is
not
adequate
support
.
"
The
removal
of
the
transmission
may
upset
the
balance
of
the
vehicle
ona
líft
.
TRANSMISSION
REMOVAL
AND
INSTALLATION
Page 229 of 759
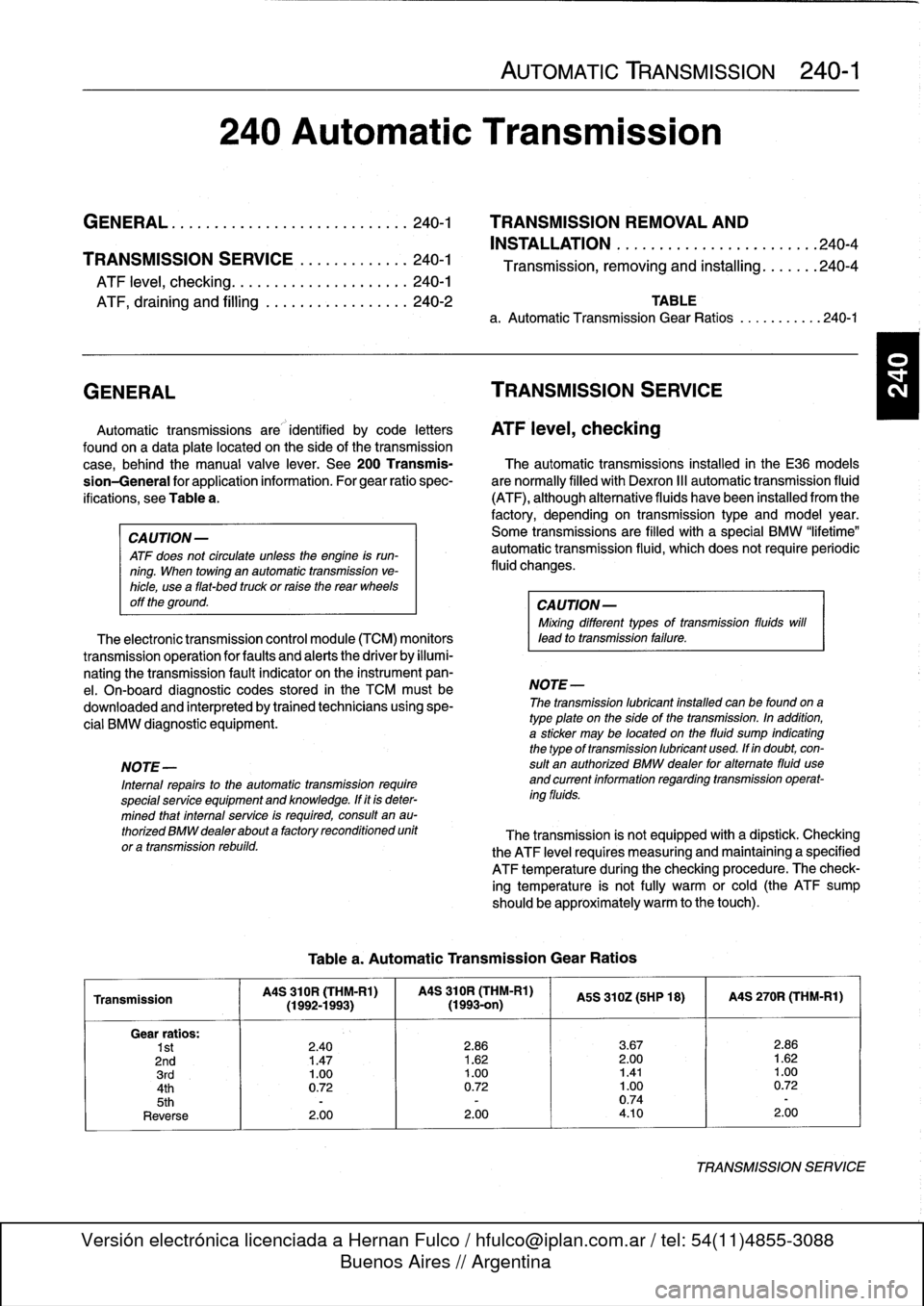
AUTOMATIC
TRANSMISSION
240-1
240
Automatic
Transmission
GENERAL
.....
.
.
.
.
.
.
.
.
.
.
.
.
.
.........
.
240-1
TRANSMISSION
REMOVAL
AND
INSTALLATION
..................
.
.
.
.
.240-4
TRANSMISSION
SERVICE
.
.
.
.
.
.......
.
240-1
Transmission,
removing
and
installing
....
.
.
.240-4
ATF
leve¡,
checking
..
.
.
.
.
.
.
.
.
.
..........
240-1
ATF,
draining
and
filling
.
.
.
.
.
.
.
..........
240-2
TABLE
a
.
Automatic
Transmission
Gear
Ratios
.......
..
.
.
240-1
GENERAL
TRANSMISSION
SERVICE
lo
Automatic
transmissions
are
identified
by
code
letters
ATF
leve¡,
checking
foundon
a
data
plate
located
on
the
sideof
thetransmission
case,
behind
the
manual
valve
lever
.
See
200Transmis-
The
automatic
transmissions
installed
in
the
E36
models
sion-General
for
application
information
.
Forgear
ratio
spec-
are
normally
filled
with
Dexron
III
automatic
transmission
fluid
ifications,
see
Table
a
.
(ATF),
although
alternative
fluids
have
been
installed
from
the
factory,
depending
on
transmission
type
and
model
year
.
CAUTION-
Some
transmíssions
are
filled
with
a
special
BMW
"lifetime"
ATF
does
not
circulate
unless
the
engine
is
run-
automatic
transmission
fluid,
which
does
not
require
periodic
ning
.
When
towing
an
automafic
transmission
ve-
fluid
changes
.
hicle,
usea
flat-bed
truck
or
ralse
the
rear
wheels
off
the
ground
.
CAUTION-
Mixing
different
types
of
transmission
fluids
will
The
electronic
transmission
control
module
(TCM)
monitors
lead
to
transmission
failure
.
transmissionoperation
for
faults
and
alerts
the
driver
by
illumi-
nating
the
transmission
fault
indicator
on
the
instrument
pan-
el
.
On-board
diagnostic
codes
stored
in
the
TCM
mustbe
NOTE-
downloaded
and
interpreted
by
trained
technicians
using
spe-
The
transmission
lubricant
instafed
can
be
foundona
cial
BMW
diagnostic
equipment
.
type
plate
on
the
side
of
the
transmission
.
In
addition,
a
sticker
may
be
located
on
the
fluid
sump
indicatingthe
typeof
transmission
lubricant
used
.
Ifin
doubt,
con
NOTE-
sult
an
authorized
BMW
dealer
for
altemate
fluid
use
Internal
repairs
to
the
automatic
transmission
require
and
current
information
regardingtransmission
operat-
special
service
equipment
and
knowledge
.
If
it
is
deter-
ing
fluids
.
mined
thatinterna¡
service
is
required,
consult
en
au-
thorízedBMWdealerabouta
factoryreconditioned
unit
The
transmission
is
not
equipped
with
a
dipstick
.
Checking
or
a
transmission
rebuild
.
the
ATF
leve¡
requires
measuring
and
maintaining
a
specified
ATF
temperature
during
the
checking
procedure
.
The
check-
ing
temperature
is
not
fully
warm
orcold
(the
ATF
sump
should
be
approximately
warm
to
the
touch)
.
Table
a
.
Automatic
Transmission
Gear
Ratios
Transmission
MS
310R
(THM-R1)
MS
310R
(THM-Rl)
MS
310Z(5HP
18)
I
MS
270R
(THM-R1)
(1992-1993)(1993-on)
Gear
ratios
:
1st
2
.40
2
.86
3
.67
2
.86
2nd
1
.47
1
.62
2
.00
1
.62
3rd
1
.00
1
.00
1.41
1
.00
4th
0
.72
0
.72
1
.00
0
.72
5th
-
-
0
.74
-
Reverse
2
.00
2
.00
4
.10
2
.00
TRANSMISSIONSERVICE
Page 230 of 759
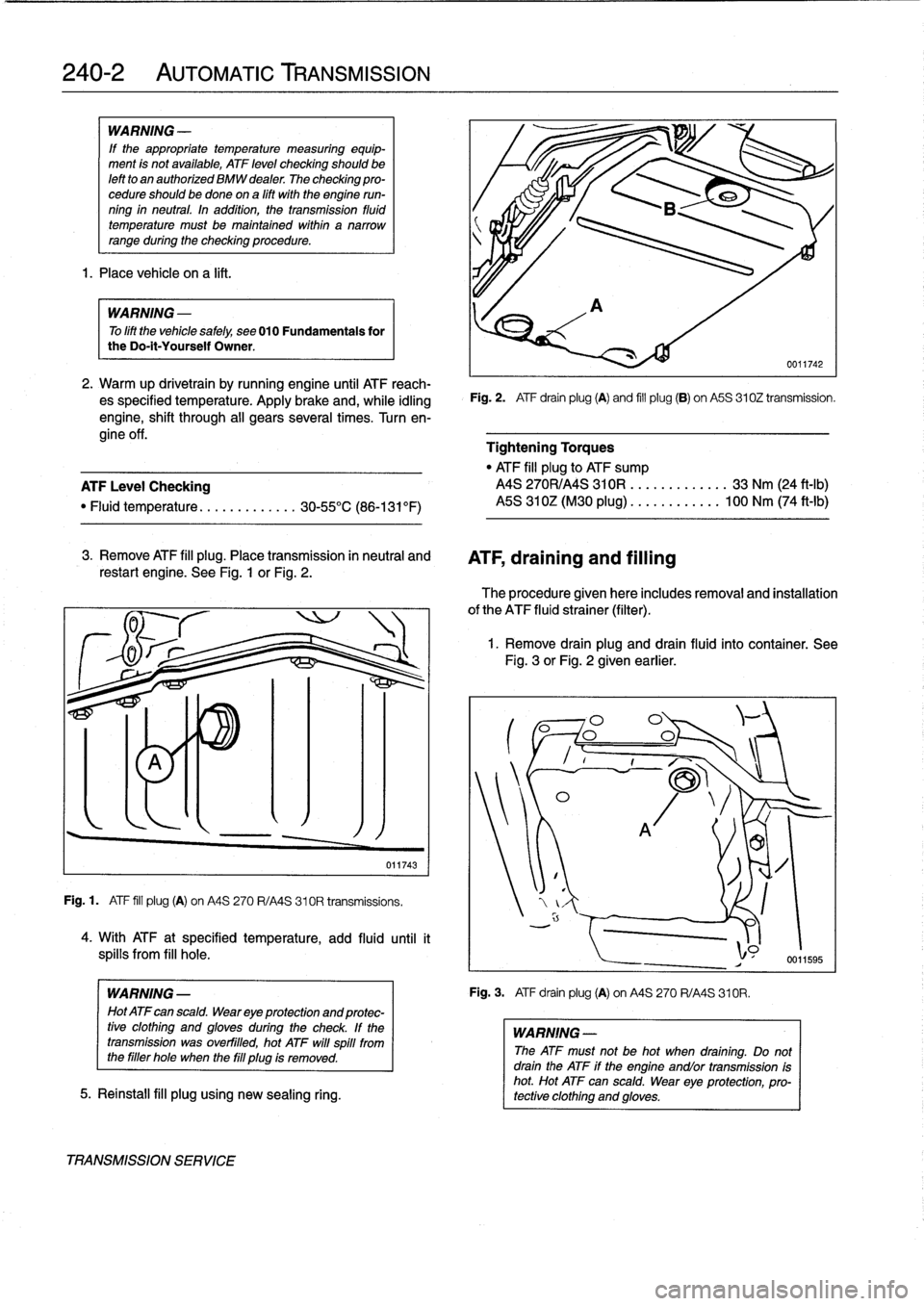
240-2
AUTOMATIC
TRANSMISSION
WARNING
-
If
the
appropriate
temperature
measuring
equip-
ment
is
not
available,
ATF
leve¡
checking
shouldbe
left
to
an
authorized
BMW
dealer
The
checking
pro-
cedure
should
be
done
on
a
lift
with
the
engine
run-
ning
in
neutral
.
In
addition,
the
transmission
fluid
temperature
must
be
maintained
within
a
narrow
range
duringthe
checking
procedure
.
1
.
Place
vehicle
on
a
lift
.
WARNING
-
To
lift
the
vehicle
safely,
see
010
Fundamentals
for
the
Do-it-Yourself
Owner
.
2
.
Warm
up
drivetrain
by
running
engine
until
ATF
reach-
es
specified
temperature
.
Apply
brake
and,
while
idling
engine,
shift
through
all
gears
severa¡
times
.
Turn
en-
gine
off
.
ATF
Level
Checking
"
Fluid
temperature
..
...........
30-55°C
(86-131°F)
3
.
Remove
ATF
fill
plug
.
Place
transmission
in
neutral
and
ATF,draining
and
filling
restart
engine
.
See
Fig
.
1
or
Fig
.
2
.
Fig
.
1
.
ATF
fill
plug
(A)
on
MS
270R/A4S310R
transmissions
.
4
.
With
ATF
at
specified
temperature,
add
(luid
until
it
spilis
from
fill
hole
.
WARNING
-
HotATFcan
scald
.
Weareye
protection
and
protec-
tive
clothing
and
gloves
duringthe
check
.
If
thetransmission
was
overfilled,
hot
ATF
will
spill
from
the
filler
hole
when
the
fill
plug
is
removed
.
5
.
Reinstall
fill
plug
using
new
sealing
ring
.
TRANSMISSION
SERVICE
011743
0011742
Fig
.
2
.
ATF
drain
plug
(A)
and
fill
plug
(B)
on
A5S
310Z
transmission
.
Tightening
Torques
"
ATF
fill
plug
to
ATF
sump
MS
270R/A4S
31
OR
.............
33
Nm
(24
ft-Ib)
MS
310Z
(M30
plug)
............
100
Nm
(74
ft-Ib)
The
procedure
given
here
includes
removal
and
installation
of
the
ATF
(luid
strainer
(filter)
.
1
.
Remove
drain
plug
and
drain
fluidinto
container
.
See
Fig
.
3
or
Fig
.
2
given
earlier
.
0~
0
/\1--Z
.IZ
~
~
A
~
"o
15/
Fig
.
3
.
ATF
drain
plug
(A)
on
A4S
270R/A4S
310R
.
WARNING
-
The
ATF
must
not
be
hot
when
draining
.
Do
not
drain
the
ATF
if
the
engineandlor
transmission
Is
hot
.
Hot
ATF
can
scald
.
Wear
eye
protection,
pro-
tective
clothing
and
gloves
.
0011595
Page 234 of 759

240-
6
AUTOMATIC
TRANSMISSION
14
.
Remove
transmission
by
pulling
back
and
down
.
Lower
jack
to
allow
transmission
to
clear
vehicle
.
Tightening
Torques
"
ATF
drain
plug
to
ATF
sump
CA
UTION-
MS
270R/A4S
310R
....
..
....
.
..
25
Nm
(18
ft-Ib)
Do
not
allow
the
torque
converter
to
fati
off
the
ASS
310Z(M10
plug)
..
..
..
.
.
..
.
..
16
Nm
(12
ft-Ib)
transmission
inputshaft
.
"
ATF
fill
plug
to
ATF
sump
MS
270R/A4S
310R
..
..
....
..
..
.
33
Nm
(24
ft-Ib)
15
.
Installation
is
reverse
of
removal,
noting
the
following
:
MS
310Z(M30
plug)
......
.
.
..
.
.
100
Nm
(74
ft-Ib)
"Blowoutofcoolerlineswithlow-pressurecompressed
"
ATF
cooler
lines
(A4S
270R/A4S
310R)
air
and
flush
coolerwith
clean
ATF
twice
before
reat-
Coupling
nuts
............
.
.
..
..
.
20
Nm
(15
ft-Ib)
taching
lines
to
transmission
.
Hollow
bolts
.........
.
.....
..
..
.
37
Nm
(28
ft-Ib)
"
Reinforcing
cross
brace
CAUTION-
to
chassis
(M10)
.............
.
..
.
42
Nm
(31
ft-Ib)
"
Wear
safety
glasses
when
working
with
com-
"
Torque
converter
pressedair
.
to
driveplate
(M10)
.........
..
.
..
45
Nm
(33
ft-Ib)
"
Transmissionsupport
crossmember
to
chassis
"
Do
not
reuse
ATF
after
flushing
.
M8
......................
22-24
Nm
(16-17
ft-1b)
M10
................
.
....
..
.
..
42
Nm
(31
ft-Ib)
"
Install
new
sealing
washers
on
hollow
bolts
.
"
Transmissíon
to
engine
(Torx-head
with
washer)
"
Insta¡¡
new
O-rings
on
transmission
cooler
lines,
where
M8
......................
..
.
..
21
Nm
(15
ft-Ib)
applicable
.
M10
.....................
..
..
.
42
Nm
(31
ft-Ib)
"
Inspect
driveplate
for
cracks
or
elongatedholes
.
Re-
M12
................
.
....
..
.
..
72
Nm
(53ft-Ib)
place
if
necessary
.
"
Check
to
be
sure
torque
converter
is
seated
correctly
in
transmission
during
final
installation
.
"
When
mounting
transmission
to
engine,
the
three
mounting
tabs
on
torque
converter
must
be
aligned
with
indentations
on
driveplate
.
Use
an
alignment
dowel
to
line
up
bolt
holes,
if
necessary
.
"
Fill
transmission
with
clean
ATF
until
oil
leve¡
is
even
with
fill
hole
.
Then
check
fluid
leve¡
as
described
ear-
lier
.
"
Adjust
gearshift
mechanism
.
See
250
Gearshift
link-
age
.
NOTE-
Torx-head
mounting
bolts
shouldalwaysbe
used
with
washers
to
prevent
difficult
removal
.
TRANSMISSION
REMOVAL
AND
INSTALLATION
Page 239 of 759
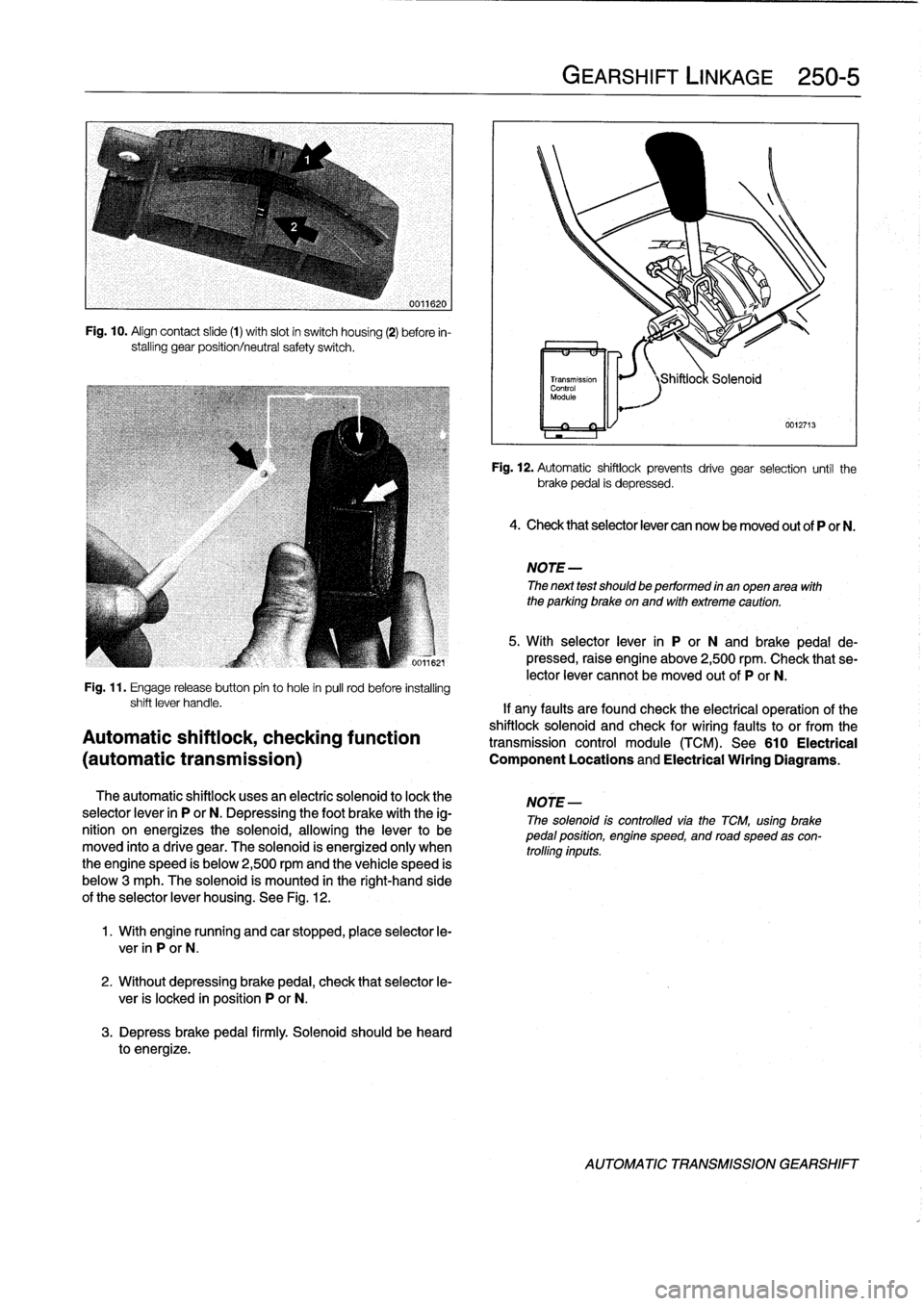
Fig
.
10
.
Align
contact
slide
(1)
with
slot
in
switch
housing
(2)
before
in-
stalling
gear
position/neutral
safety
switch
.
Fig
.
11
.
Engage
release
button
pin
to
hole
in
pull
rod
before
installing
The
automatic
shiftlock
uses
an
electríc
solenoid
to
lock
the
selector
lever
in
P
or
N
.
Depressing
the
foot
brake
withthe
ig-
nition
on
energizes
the
solenoid,
allowingthe
lever
to
be
moved
into
a
drive
gear
.
The
solenoid
is
energized
only
when
the
engine
speed
is
below
2,500
rpmand
thevehicle
speed
is
below
3
mph
.
The
solenoid
ís
mounted
in
the
right-hand
side
of
theselector
lever
housing
.
See
Fig
.
12
.
1
.
With
engine
running
and
car
stopped,
place
selector
le-
ver
in
P
or
N
.
2
.
Without
depressing
brake
pedal,
check
that
selector
le-
ver
is
locked
in
position
P
or
N
.
3
.
Depress
brakepedal
firmly
.
Solenoid
should
be
heard
to
energize
.
GEARSHIFT
LINKAGE
250-
5
Fig
.
12
.
Automatic
shiftlock
prevents
drive
gear
selection
until
the
brakepedal
is
depressed
.
4
.
Check
thatselector
lever
can
now
be
moved
out
of
P
or
N
.
NOTE
-
The
next
test
should
be
performed
in
anopen
area
with
the
parking
brake
on
and
with
extreme
caution
.
5
.
With
selector
lever
in
P
or
N
and
brake
pedal
de-
pressed,
raise
engine
above
2,500
rpm
.
Check
that
se-
lector
lever
cannotbe
moved
outof
P
or
N
.
shift
lever
handle
.
If
any
faults
are
found
check
the
electrical
operation
of
the
shiftlock
solenoid
and
check
for
wiring
faultsto
or
from
the
Automatic
shiftiock,
checking
function
transmission
control
module(TCM)
.
See610
Electrical
(automatic
transmission)
Component
Locations
and
Electrical
Wiring
Diagrams
.
NOTE
-
The
solenoid
is
controlled
viathe
TCM,
using
brakepedal
position,
engine
speed,
and
road
speed
as
con-
trolling
inputs
.
AUTOMATIC
TRANSMISSION
GEARSHIFT
Page 241 of 759
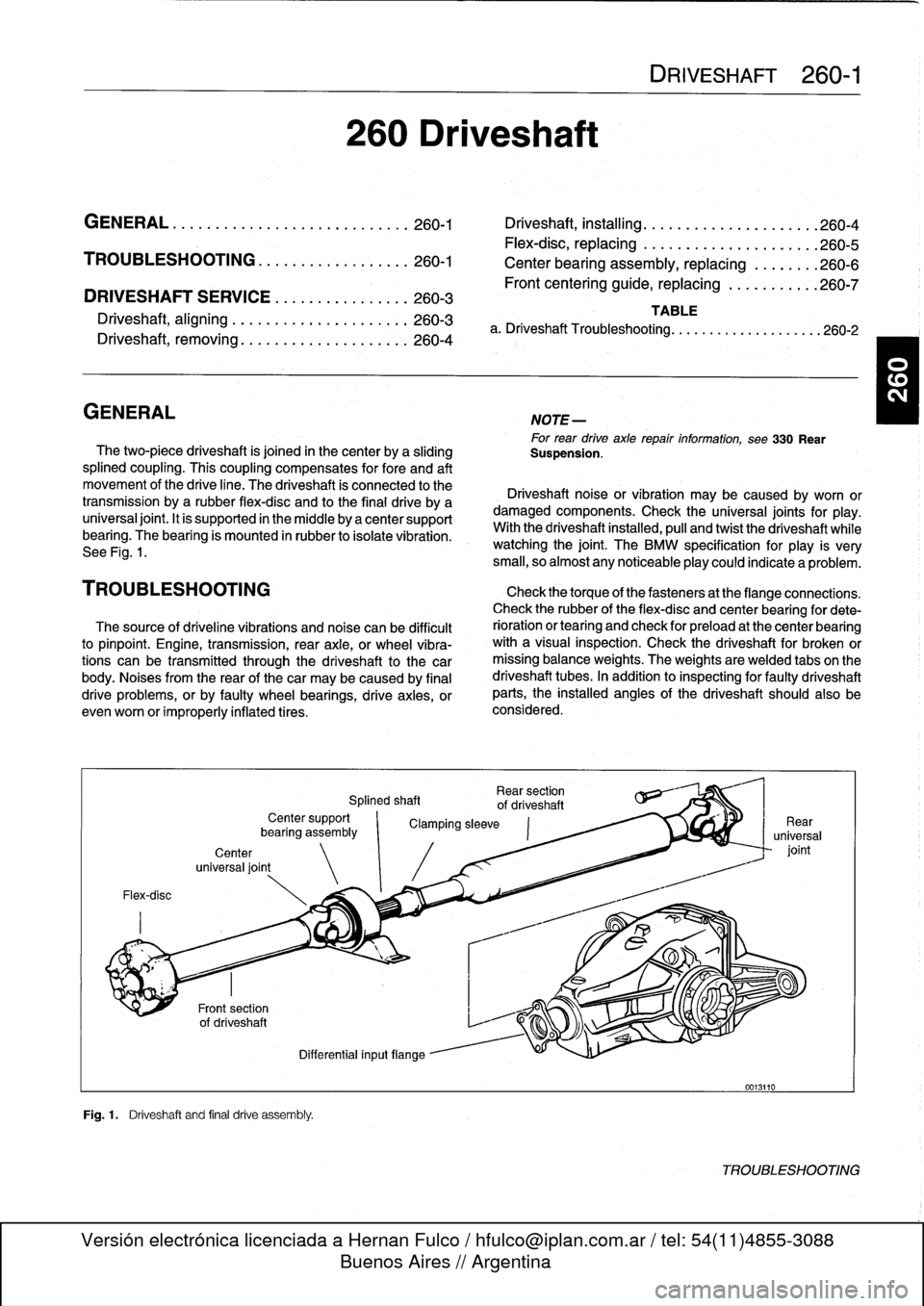
DRIVESHAFT
SERVICE
.
...
.
.
.
...
.
..
.
.
.260-3
Driveshaft,
aligning
...............
.
...
.
.
260-3
Driveshaft,
removing
..............
.
.
.
.
.
.
260-4
260
Driveshaft
DRIVESHAFT
260-1
GENERAL
.
.
.
.
.
.
.
.....
.
.
.
........
.
...
.
260-1
Driveshaft,
installing
.
....
.
..
.
............
260-4
Flex-disc,
replacing
.....
.
.
.
.............
260-5
TROUBLESHOOTING
..
.
.
.
...
.
.........
260-1
Center
bearing
assembly,
replacing
.
......
.260-6
Frontcentering
guide,
replacing
..
.
.......
.
260-7
TABLE
a
.
Driveshaft
Troubleshooting
.
.
...
......
.
....
..
.
.
260-2
GENERAL
NOTE-
For
rear
drive
axlerepair
information,
see330
Rear
The
two-piece
driveshaft
is
joined
in
thecenter
by
a
sliding
Suspension
.
splined
coupling
.
This
coupling
compensates
for
fore
and
aft
movement
of
the
drive
line
.
The
driveshaft
ís
connected
to
the
Driveshaft
noise
or
vibration
may
be
caused
by
worn
or
transmission
bya
rubber
flex-disc
and
to
the
final
drive
by
a
damaged
components
.
Check
the
universal
joints
for
play
.
universal
joint
.
It
is
supported
in
the
micidle
by
a
center
support
With
the
driveshaft
installed,
pull
and
twist
the
driveshaft
while
bearing
.
The
bearing
is
mounted
in
rubber
to
isolate
vibration
.
watching
the
joint
.
The
BMW
specificationfor
play
is
very
See
Fig
.
1
.
small,
so
almost
any
noticeableplay
could
indicate
a
problem
.
TROU
BLESHOOTING
Check
thetorque
of
thefasteners
at
the
flange
connections
.
Check
therubber
of
the
flex-disc
and
center
bearing
for
dete
The
source
of
driveline
vibrations
and
noise
can
be
difficult
rioration
or
tearíng
and
check
for
preload
at
the
center
bearing
to
pinpoint
.
Engine,
transmission,
rear
axle,
or
wheel
vibra-
with
a
visual
inspection
.
Check
the
driveshaft
for
broken
or
tions
can
be
transmitted
through
the
driveshaft
to
the
car
missing
balance
weights
.
The
weights
are
welded
tabs
on
the
body
.
Noises
from
the
rear
of
thecar
may
be
caused
by
final
driveshaft
tubes
.
In
addition
to
inspecting
for
faulty
driveshaft
drive
problems,
orby
faulty
wheel
bearings,
drive
axies,
or
parts,
the
installed
angles
of
the
driveshaft
should
also
be
evenworn
or
improperly
inflatedtires
.
considered
.
Flex-disc
Center
universal
joint
Fig
.1
.
Driveshaft
and
final
drive
assembly
.
Rear
section
Splined
shaft
of
driveshaft
Center
support
`
Clamping
sleeve
bearíng
assembly
Differential
inputflange
0013110
TROUBLESHOOTING
Page 242 of 759
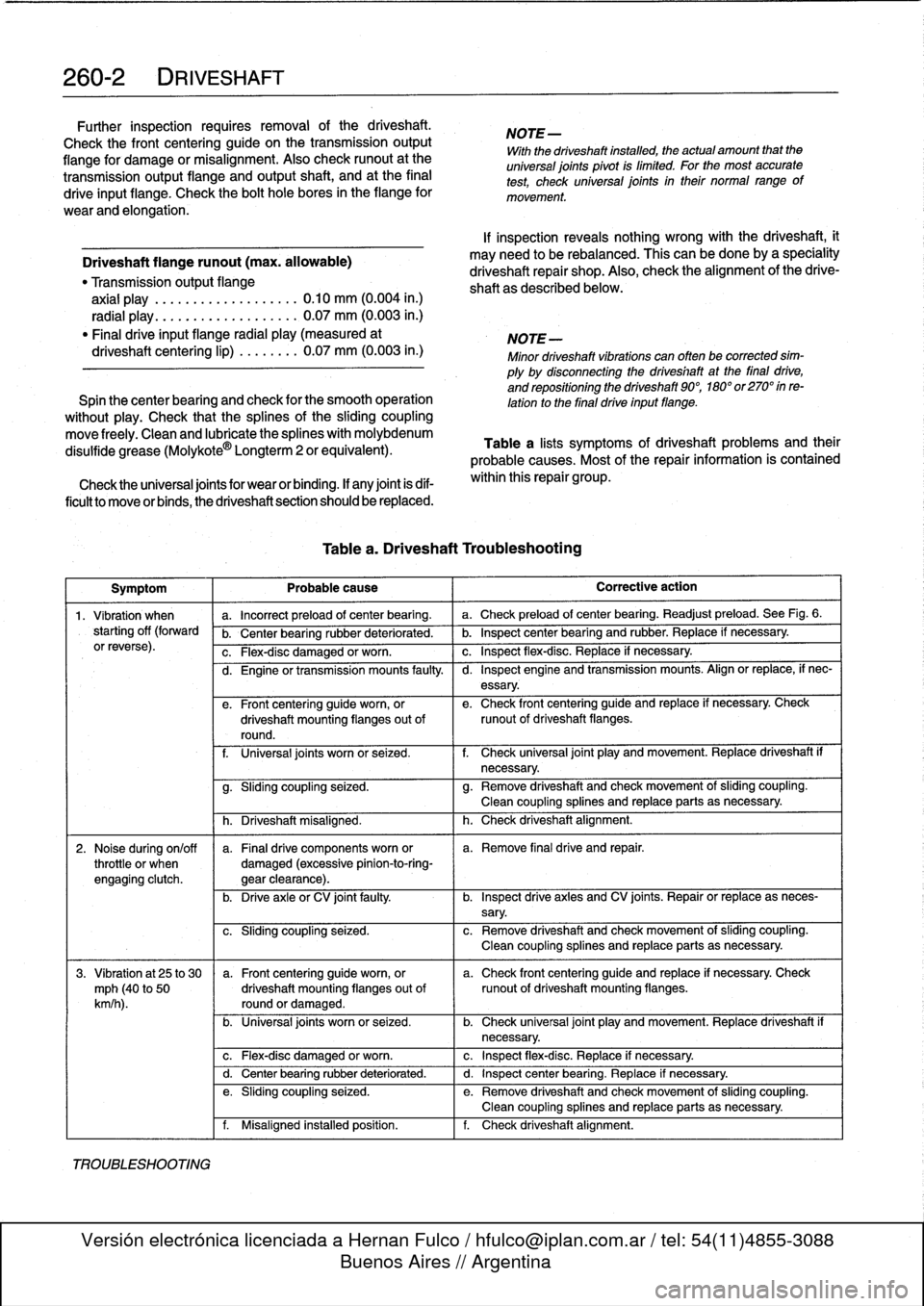
260-2
DRIVESHAFT
Further
inspection
requires
removal
of
the
driveshaft
.
Check
the
front
centering
guide
on
the
transmission
output
flange
for
damage
or
misalignment
.
Also
check
runoutatthe
transmission
outputflange
and
output
shaft,
and
at
the
final
drive
input
flange
.
Check
the
bolt
hole
bores
in
theflange
for
wear
and
elongation
.
Driveshaftflange
runout
(max
.
allowable)
"
Transmission
outputflange
axial
play
...
.
..
...
..
.
.......
0
.10
mm
(0
.004
in
.)
radial
play
.......
...
.
.
.......
0
.07
mm
(0
.003
in
.)
"
Final
driveinput
flange
radial
play
(measured
at
driveshaft
centering
lip)
..
......
0
.07
mm
(0
.003
in
.)
Spinthe
center
bearing
and
check
for
the
smooth
operation
without
play
.
Check
that
thesplines
of
the
sliding
coupling
move
freely
.
Clean
and
lubricate
the
splines
with
molybdenum
disulfide
grease
(Molykote
®
Longterm
2
or
equivalent)
.
Check
the
universal
joints
for
wear
or
binding
.
If
any
joint
isdif-
ficult
to
move
or
binds,
the
driveshaft
section
should
be
replaced
.
Table
a
.
Driveshaft
Troubleshooting
NOTE-
With
the
driveshaft
installed,
theactual
amount
that
the
universal
joints
pivot
is
limited
.
For
the
most
accurate
test,
check
universal
joints
in
their
normal
range
of
movement
.
If
inspection
revealsnothing
wrong
with
the
driveshaft,
it
may
need
to
be
rebalanced
.
This
can
be
done
by
a
speciality
driveshaft
repair
shop
.
Also,
check
the
alignment
ofthe
drive-
shaft
as
described
below
.
NOTE-
Minor
driveshaftvibrations
can
often
be
correctedsim-
ply
by
disconnecting
the
driveshaftat
the
finaldrive,
and
repositíoning
the
driveshaft
90°,
180°
or270°
inre-
lationto
the
final
drive
input
flange
.
Table
a
lists
symptoms
of
driveshaft
problems
and
their
probable
causes
.
Most
of
the
repair
information
is
contained
within
this
repair
group
.
Symptom
Probable
cause
Corrective
action
1
.
Vibration
when
a
.
Incorrect
preload
of
center
bearing
.
a
.
Check
preload
of
center
bearing
.
Readjust
preload
.
See
Fig
.
6
.
starting
off
(forward
b
.
Center
bearing
rubber
deteriorated
.
b
.
Inspect
center
bearing
and
rubber
.
Replace
if
necessary
.
orreverse)
.
c
.
Flex-disc
damaged
or
worn
.
c
.
Inspect
flex-disc
.
Replace
if
necessary
.
TROUBLESHOOTING
d
.
Engine
or
transmission
mounts
faulty
.
I
d
.
Inspect
engine
and
transmission
mounts
.
Align
or
replace,
if
nec-
essary
.
e
.
Front
centering
guide
worn,
or
e
.
Check
front
centering
guide
and
replace
if
necessary
.
Check
driveshaft
mounting
flanges
out
of
runout
of
driveshaft
flanges
.
round
.
f
.
Universal
joints
worn
or
seized
.
f
.
Check
universal
joint
play
and
movement
.
Replace
driveshaft
if
necessary
.
g
.
Sliding
coupling
seized
.
g
.
Remove
driveshaft
and
check
movement
of
sliding
coupling
.
Clean
coupling
splines
and
replace
parts
asnecessary
.
h
.
Driveshaft
misaligned
.
h
.
Check
driveshaft
alignment
.
2
.
Noise
during
on/off
a
.
Finaldrive
components
worn
or
a
.
Remove
final
drive
and
repair
.
throttle
or
when
damaged
(excessive
pinion-to-ring-
engagíng
clutch
.
gear
clearance)
.
b
.
Drive
axleor
CV
joint
faulty
.
b
.
Inspect
drive
axles
and
CV
joints
.
Repair
or
replace
as
neces-
sary
.
c
.
Sliding
coupling
seized
.
c
.
Remove
driveshaft
and
check
movement
of
sliding
coupling
.
Clean
coupling
splines
and
replace
parts
as
necessary
.
3
.
Vibration
at
25
to
30
a
.
Front
centering
guideworn,
or
a
.
Check
front
centering
guide
and
replace
if
necessary
.
Check
mph
(40
to
50
driveshaft
mounting
flanges
out
of
runout
of
driveshaft
mounting
flanges
.
km/h
).
round
or
damaged
.
b
.
Universal
joints
worn
or
seized
.
b
.
Check
universal
joint
play
and
movement
.
Replace
driveshaft
if
necessary
.
c
.
Flex-disc
damaged
or
worn
.
c
.
Inspect
flex-disc
.
Replace
if
necessary
.
d
.
Center
bearing
rubber
deteriorated
.
d
.
Inspect
center
bearing
.
Replace
if
necessary
.
e
.
Sliding
coupling
seized
.
e
.
Remove
driveshaft
and
check
movement
of
sliding
coupling
.
Clean
coupling
splines
and
replace
parts
asnecessary
.
f
.
Misaligned
installed
position
.
f
.
Check
driveshaft
alignment
.