sensor BMW M3 1998 E36 User Guide
[x] Cancel search | Manufacturer: BMW, Model Year: 1998, Model line: M3, Model: BMW M3 1998 E36Pages: 759
Page 52 of 759
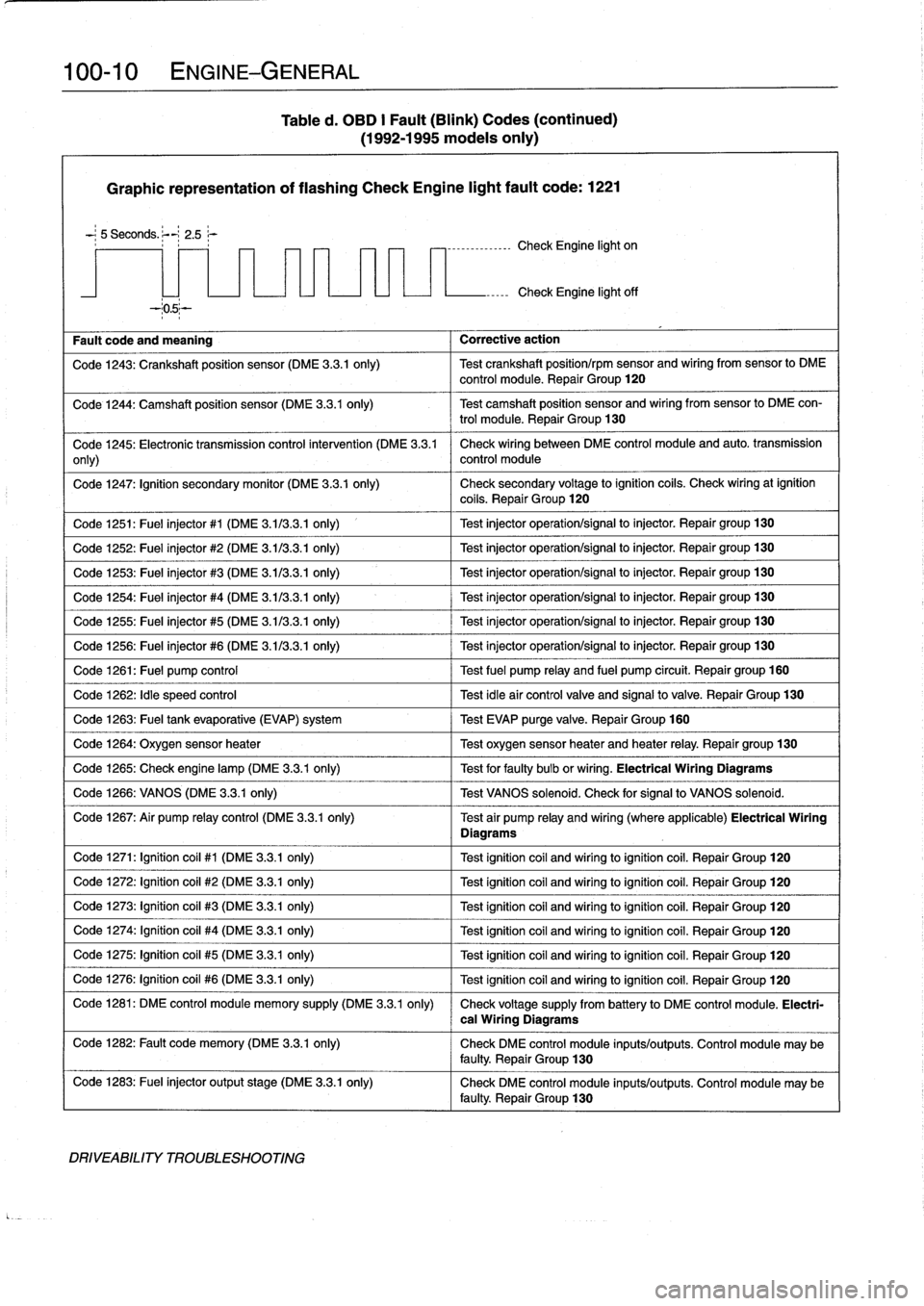
100-
1
0
ENGINE-GENERAL
Table
d
.
OBD
I
Fault
(Blink)
Codes
(continued)
(1992-1995
modeis
only)
Graphic
representation
of
flashing
Check
Engine
light
fault
code
:
1221
-
;
5
Seconds
.
;--~
2
.5
r
----------------
Check
Engine
light
on
Fault
code
and
meaning
Corrective
action
Check
Engine
light
off
Code
1243
:
Crankshaft
position
sensor
(DME
3
.3
.1
only)
Test
crankshaft
position/rpm
sensor
and
wiring
from
sensor
lo
DME
control
module
.
Repair
Group
120
Code
1244
:
Camshaft
position
sensor
(DME
3
.3
.1
only)
Test
camshaft
position
sensor
and
wiring
fromsensor
to
DME
con-
trol
module
.
Repair
Group
130
Code
1245
:
Electronic
transmission
control
intervention
(DME
3
.3
.1
Check
wiring
between
DME
control
module
and
auto
.
transmission
only)
control
module
Code
1247
:
Ignition
secondary
monitor
(DME
3
.3
.1
only)
Check
secondary
voltage
lo
ignition
coils
.
Check
wiringat
ignition
coils
.
Repair
Group
120
Code
1251
:
Fuel
injector
#1
(DME
3
.113
.3
.1
only)
1
Test
injector
operation/signal
lo
injector
.
Repair
group130
Code
1252
:
Fuel
injector
#2
(DME
3
.113
.3
.1
only)
Test
injector
operation/signal
lo
injector
.
Repair
group130
Code
1253
:
Fuel
injector
#3
(DME
3
.1/3
.3
.1
only)
Test
injector
operation/signal
to
injector
.
Repair
group130
Code
1254
:
Fuel
injector
#4
(DME
3
.1/3
.3
.1
only)
Test
injector
operation/signal
to
injector
.
Repair
group
130
Code
1255
:
Fuel
injector
#5
(DME
3
.1/3
.3
.1
only)
Test
injector
operation/signal
to
injector
.
Repair
group130
Code
1256
:
Fuel
injector
#6
(DME
3
.1/3
.3
.1
only)
Test
injector
operation/signal
lo
injector
.
Repair
group130
Code
1261
:
Fuel
pump
control
Test
fuel
pump
relay
and
fuel
pump
circuit
.
Repairgroup
160
Code
1262
:
Idle
speed
control
Test
idleair
controlvalve
and
signalto
valve
.
Repair
Group
130
Code
1263
:
Fuel
tank
evaporative
(EVAP)
system
Test
EVAP
purge
valve
.
Repair
Group
160
Code
1264
:
Oxygen
sensor
heater
1
Test
oxygen
sensorheater
and
heater
relay
.
Repair
group
130
Code
1265
:
Check
engine
lamp
(DME
3
.3.1
only)
1
Test
for
faulty
bulb
or
wiring
.
Electrical
Wiring
Diagrams
Code
1266
:
VANOS
(DME
3
.3
.1
only)
1
Test
VANOS
solenoid
.
Check
for
signal
to
VANOS
solenoid
.
Code
1267
:
Air
pump
relay
control
(DME
3
.3
.1
only)
Test
air
pump
relay
and
wiring
(where
applicable)
Electrical
Wiring
Diagrams
Code
1271
:
Ignition
coil
#1
(DME
3
.3.1
only)
Test
ignitioncoil
and
wiring
toignitioncoil
.
Repair
Group
120
Code
1272
:
Ignition
coil
#2
(DME
3
.3.1
only)
Test
ignitioncoil
and
wiring
loignitioncoil
.
Repair
Group
120
Code
1273
:
Ignition
coil
#3
(DME
3
.3.1
only)
Test
ignitioncoil
and
wiring
loignitioncoil
.
Repair
Group
120
Code
1274
:
Ignítion
coil
#4
(DME
3
.3.1
only)
Test
ignitioncoil
and
wiring
toignitioncoil
.
Repair
Group
120
Code
1275
:
Ignitioncoil
#5
(DME
3
.3.1
only)
Test
ignition
coil
and
wiring
loignitioncoil
.
Repair
Group
120
Code
1276
:
Ignition
coil
#6
(DME
3
.3.1
only)
Test
ignitioncoil
and
wiring
loignitioncoil
.
Repair
Group
120
Code
1281
:
DME
control
module
memory
supply
(DME
3
.3
.1
only)
Check
voltage
supply
from
battery
lo
DME
control
module
.
Electri-
Code
1282
:
Fault
code
memory
(DME
3
.3.1
only)
Check
DME
control
module
inputs/outputs
.
Control
module
may
be
faulty
.
Repair
Group
130
Code
1283
:
Fuel
injector
output
stage
(DME
3
.3
.1
only)
Check
DME
control
module
inputs/outputs
.
Control
module
may
be
faulty
.
Repair
Group
130
DRIVEABILITY
TROUBLESHOOTING
cal
Wiring
Diagrams
Page 53 of 759
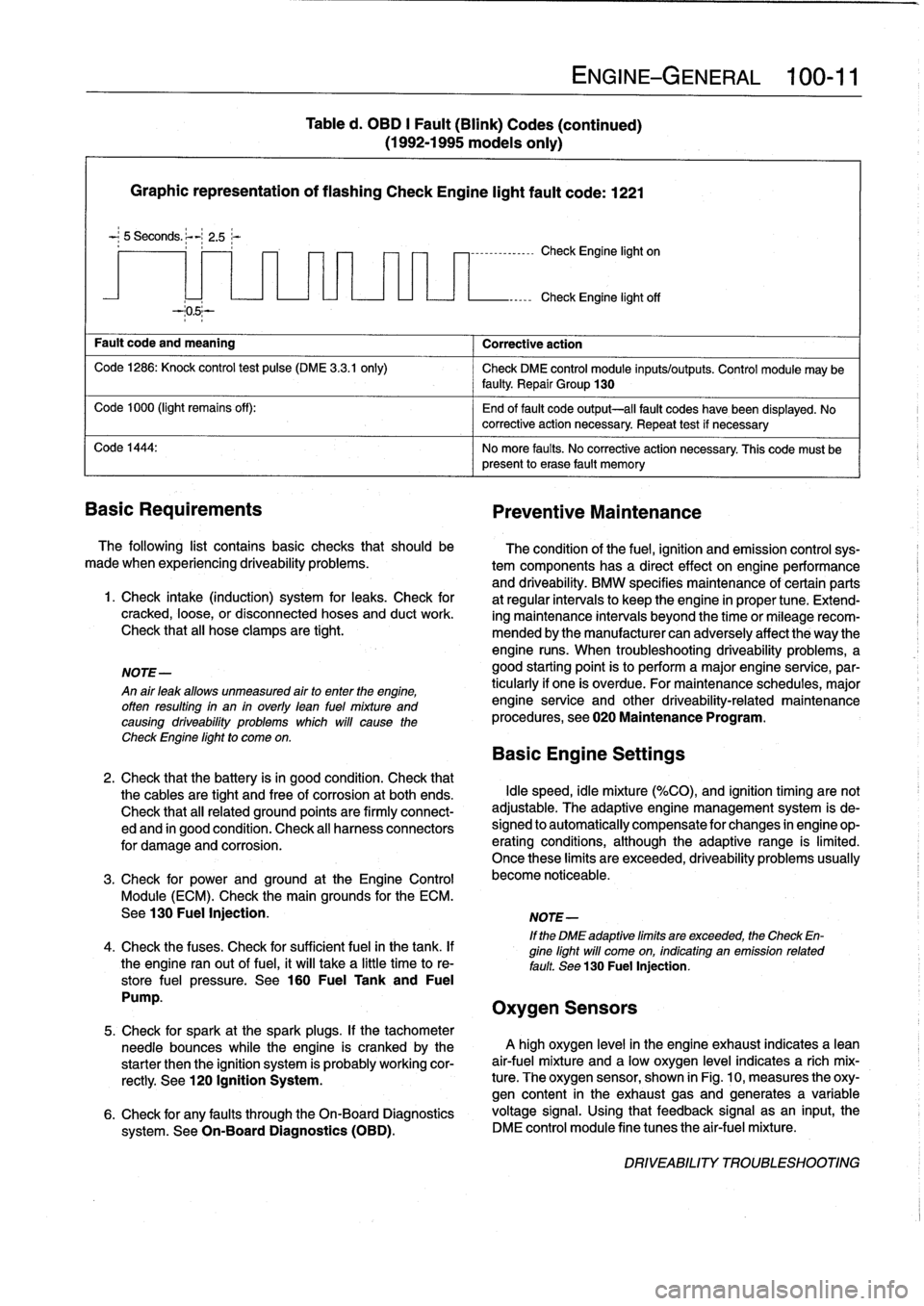
Graphic
representation
of
flashing
Check
Engine
light
fault
code
:
1221
-
;
5
Seconds
.
~-
2
.5;-
Fault
code
and
meaning
Corrective
action
Code
1286
:
Knock
control
test
pulse
(DME
3
.3
.1
only)
Check
DME
control
module
inputs/outputs
.
Control
module
may
be
faulty
Repair
Group
130
Code
1000
(light
remains
off)
:
End
of
fault
code
output-all
fault
codes
have
been
displayed
.
No
~
corrective
action
necessary
.
Repeat
test
if
necessary
Code
1444
:
No
more
faults
.
No
corrective
action
necessary
.
This
code
must
be
present
lo
erase
fault
memory
Basic
Requirements
Preventive
Maintenance
The
following
list
contains
basic
checks
that
should
be
made
when
experiencing
driveability
problems
.
1
.
Check
intake
(induction)
system
for
leaks
.
Check
for
cracked,
loose,
or
disconnected
hoses
and
duct
work
.
Check
that
all
hose
clamps
are
tight
.
NOTE-
An
air
leak
allows
unmeasured
airto
enter
the
engine,
offen
resulting
in
an
in
overly
lean
fuel
mixture
and
causing
driveability
problems
which
will
cause
the
Check
Engine
light
to
come
on
.
Table
d
.
OBD
I
Fault
(Blink)
Codes
(continued)
(1992-1995
models
only)
7
-
1
--------------
Check
Engine
light
on
ENGINE-GENERAL
100-
1
1
Check
Engine
light
off
The
condition
of
the
fuel,
ignition
and
emission
controlsys-
tem
components
has
a
directeffect
onengineperformance
and
driveability
.
BMW
specifies
maintenance
of
certain
parts
at
regular
intervals
lo
keep
the
engine
in
proper
tune
.
Extend-
ing
maintenance
intervals
beyond
the
time
or
mileagerecom-
mended
bythe
manufacturer
can
adversely
affect
the
way
the
engine
runs
.
When
troubleshooting
driveability
problems,
a
good
starting
point
is
to
perform
a
major
engine
service,par-
ticularly
if
one
is
overdue
.
For
maintenance
schedules,
major
engine
service
and
other
driveability-related
maintenance
procedures,
see020
Maintenance
Program
.
Basic
Engine
Settings
2
.
Check
that
the
battery
isin
good
condition
.
Check
that
the
cables
are
tight
and
free
of
corrosion
at
both
ends
.
Idle
speed,
idle
mixture
(%CO),
and
ignition
timing
are
not
Check
that
all
related
ground
points
are
firmly
connect-
adjustable
.
The
adaptive
engine
management
system
is
de-
ed
and
in
good
condition
.
Check
al¡
harness
connectors
signed
lo
automatically
compensate
for
changes
in
engine
op-
for
damage
and
corrosion
.
erating
conditions,
although
the
adaptive
range
is
limited
.
Once
these
limits
are
exceeded,
driveability
problems
usually
3
.
Check
for
prwer
and
ground
at
the
Engine
Control
become
noticeable
.
Module
(ECM)
.
Check
the
main
grounds
for
the
ECM
.
See130
Fuel
Injection
.
NOTE-
If
the
DME
adaptive
limits
are
exceeded,
the
Check
En-
4
.
Check
the
fuses
.
Check
for
sufficient
fuel
in
the
tank
.
If
gine
light
will
come
on,
indicating
an
emission
related
the
engine
ranout
of
fuel,
it
will
take
a
little
time
to
re-
fault
.
See
130
Fuel
Injection,
store
fuel
pressure
.
See
160
Fuel
Tank
and
Fuel
Pump
.
Oxygen
Sensors
5
.
Check
for
spark
at
the
spark
plugs
.
If
the
tachometer
needle
bounces
while
the
engine
is
crankedby
the
A
high
oxygen
level
in
the
engine
exhaust
indicates
a
lean
starter
then
the
ignition
system
is
probably
working
cor-
air-fuel
mixture
and
a
low
oxygen
level
indicates
a
rich
mix
rectly
.
See
120
Ignition
System
.
ture
.
The
oxygen
sensor,
shown
in
Fig
.
10,
measures
the
oxy-
gen
content
in
the
exhaust
gasand
generates
a
variable
6
.
Check
for
any
faults
through
the
On-Board
Diagnostics
voltage
signal
.
Using
that
feedback
signal
asan
input,
the
system
.
See
On-Board
Diagnostics
(OBD)
.
DME
control
module
fine
tunes
the
air-fuel
mixture
.
DRIVEABILITY
TROUBLESHOOTING
Page 54 of 759
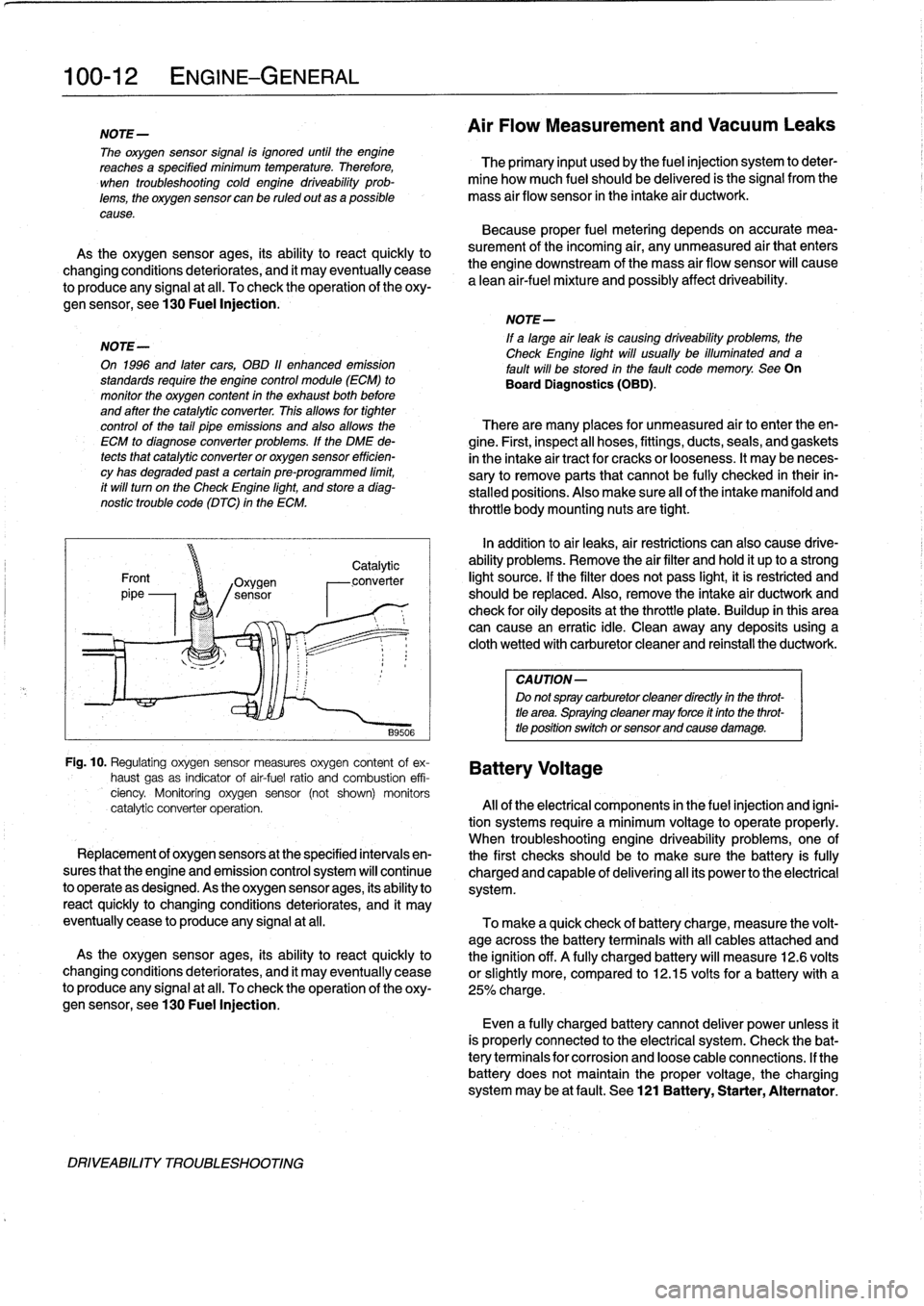
100-
1
2
ENGINE-GENERAL
NOTE-
The
oxygen
sensor
signal
is
ignored
until
the
engine
reachesa
specified
minimum
temperature
.
Therefore,
The
primary
input
usedby
the
fuel
injection
system
to
deter-
when
troubleshooting
cold
engine
driveability
prob-
mine
how
much
fuel
should
be
delivered
is
the
signal
from
the
lems,
the
oxygensensor
canbe
ruled
out
asa
possible
mass
air
flow
sensor
in
the
intake
air
ductwork
.
cause
.
As
the
oxygen
sensor
ages,
its
ability
to
react
quickly
to
changing
conditions
deteriorates,
and
it
may
eventually
cease
to
produce
any
signal
at
all
.
To
check
the
operation
of
the
oxy-
gen
sensor,
see
130
Fuel
Injection
:
NOTE-
On
1996
and
latercars,
OBD
11
enhanced
emission
standards
require
the
engine
control
module
(ECM)
to
monitor
the
oxygen
content
in
the
exhaust
both
before
and
after
the
catalytic
converter
.
Thisallows
for
tighter
control
of
the
tail
pipe
emissions
and
also
allowsthe
ECM
to
diagnose
converter
problems
.
If
the
DME
de-
tects
that
catalytic
converter
or
oxygensensor
efficien-
cyhas
degraded
pasta
certain
pre-programmed
limit,
it
will
turn
on
the
Check
Engine
light,
and
store
a
diag-
nostic
trouble
code
(DTC)
in
the
ECM
.
DRIVEABILITY
TROUBLESHOOTING
Catalytic
B9506
Air
Flow
Measurement
and
Vacuum
Leaks
Because
proper
fuel
metering
depends
on
accurate
mea-
surement
of
the
incoming
air,
any
unmeasured
air
that
enters
the
engine
downstream
of
the
mass
air
flow
sensor
will
cause
a
lean
air-fuel
mixture
and
possibly
affectdriveability
.
NOTE-
Fig
.
10
.
Regulating
oxygen
sensor
measures
oxygen
content
of
ex-
gattery
Voltage
hausY
gas
as
indicator
of
.¡_fi
.1
ratio
and
"-k,
.
E-
effi-
ciency
.
Monitoríng
oxygen
sensor
(not
shown)
monitors
If
a
large
air
leak
is
causing
driveability
problems,
the
Check
Engine
light
will
usually
be
illuminated
and
a
fault
will
be
stored
in
the
fault
code
memory
.
See
On
Board
Diagnostics
(OBD)
.
There
are
many
places
for
unmeasured
air
to
enter
theen-
gine
.
First,
inspect
all
hoses,
fittings,
ducts,
seals,
and
gaskets
in
the
intake
air
tract
for
cracks
or
looseness
.
It
may
be
neces-
sary
to
remove
parts
that
cannot
be
fully
checked
in
their
in-
stalled
positions
.
Also
make
sure
all
of
the
intake
manifold
and
throttle
body
mounting
nuts
are
tight
.
In
addition
to
air
leaks,
air
restrictions
can
also
cause
drive-
ability
problems
.
Remove
the
air
filter
and
hold
it
up
to
a
strong
light
source
.
If
the
filter
does
not
pass
light,
it
is
restricted
and
should
be
replaced
.
Also,
remove
the
intake
air
ductwork
and
check
for
oily
deposits
at
the
throttle
plate
.
Buildup
in
this
area
can
cause
an
erratic
idle
.
Clean
away
any
deposits
using
a
cloth
wetted
withcarburetor
cleaner
and
reinstall
the
ductwork
.
CAUTION-
Do
not
spray
carburetor
cleaner
directly
in
the
throt-
tle
anea
.
Spraying
cleaner
may
force
it
into
the
throt-
tle
position
switch
or
sensor
and
cause
damage
.
catalytic
converter
operation
.
All
of
the
electrical
components
in
the
fuelinjection
and
igni-
tion
systems
require
a
minimum
voltage
to
operate
properly
.
When
troubleshooting
engine
driveability
problems,
one
of
Replacement
of
oxygensensors
at
the
specified
intenrals
en-
the
first
checks
should
be
to
make
sure
the
battery
is
fully
sures
that
the
engine
and
emission
control
system
wili
continue
charged
and
capable
of
delivering
allits
power
to
the
electricalto
operate
as
designed
.
As
the
oxygen
sensor
ages,
its
ability
to
system
.
react
quickly
to
changing
conditions
deteriorates,
and
it
may
eventually
cease
to
produceany
signal
at
all
.
To
make
a
quick
check
of
battery
charge,
measure
the
volt-
age
across
the
battery
terminals
with
all
cables
attached
and
As
the
oxygen
sensor
ages,
its
ability
to
react
quickly
to
the
ignition
off
.
A
fully
charged
battery
will
measure
12
.6
volts
changing
conditions
deteriorates,
and
it
may
eventually
cease
or
slightly
more,
compared
to
12
.15
volts
for
a
battery
with
a
to
produce
any
signal
at
all
.
To
check
theoperation
of
the
oxy-
25%
charge
.
gen
sensor,
see130
Fuel
Injection
.
Even
a
fully
charged
battery
cannot
deliver
power
unless
it
is
properly
connected
to
the
electrical
system
.
Check
the
bat-
tery
terminals
for
corrosion
and
loosecableconnections
.
If
the
battery
does
not
maintain
the
proper
voltage,
the
charging
system
may
be
atfault
.
See
121
Battery,
Starter,
Alternator
.
Page 57 of 759
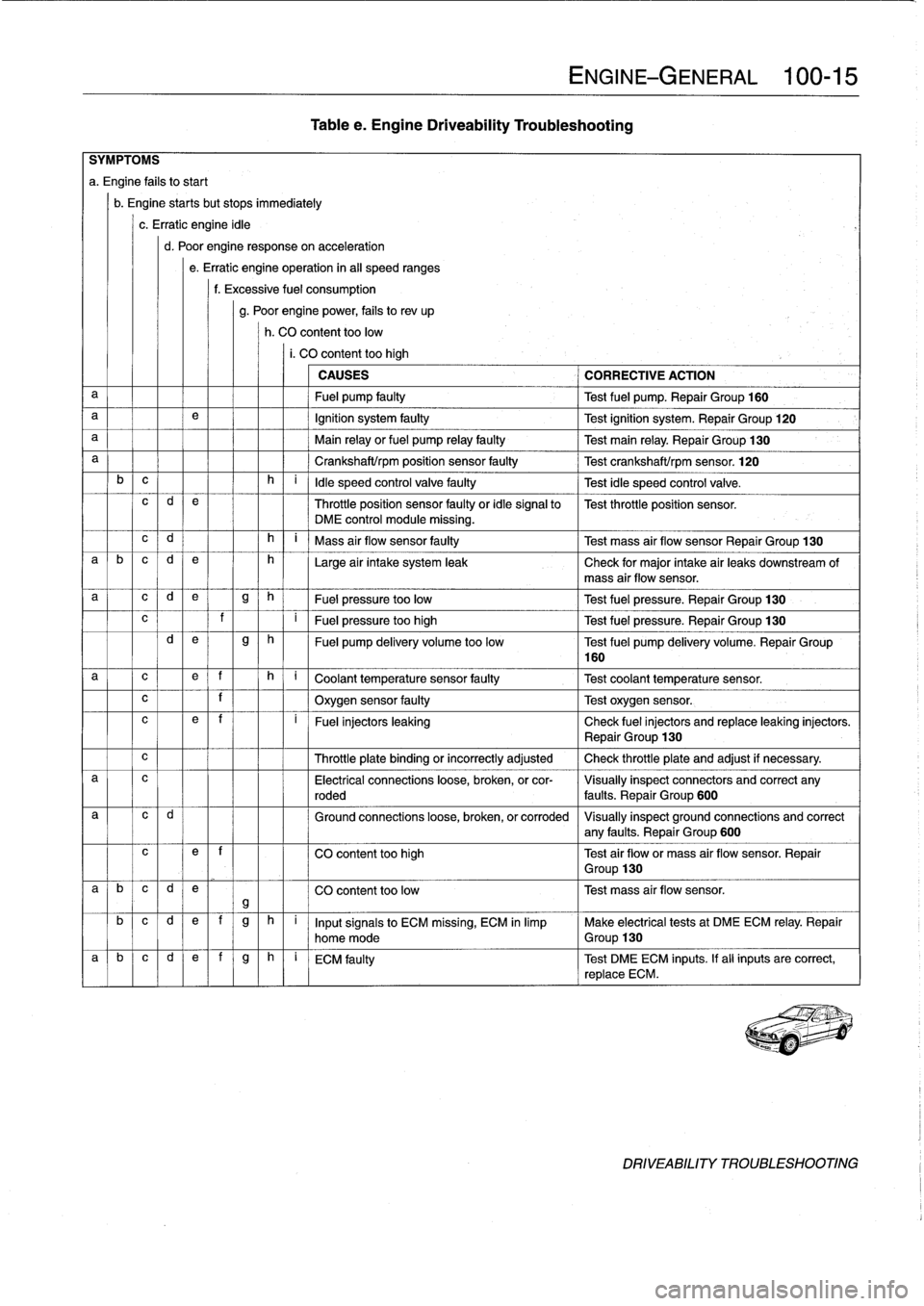
al
Icld
Table
e
.
Engine
Driveability
Troubleshooting
c
l
1
I
f
I
I
Oxygen
sensor
faulty
Test
oxygen
sensor
.
ENGINE-GENERAL
100-
1
5
SYMPTOMS
a
.
Engine
fafs
tostart
b
.
Engine
startsbut
stops
immediately
c
.
Erratic
engine
idle
d
.
Poor
engine
responseon
acceleration
e
.
Erratic
engine
operation
in
al¡
speed
ranges
f
.
Excessive
fuel
consumption
g
.
Poor
enginepower,
fails
to
rev
up
h
.
CO
content
toolow
i.
CO
content
too
high
CAUSES
CORRECTIVE
ACTION
a
Fuel
pump
faulty
Test
fuel
pump
.
Repair
Group
160
a
e
Ignition
system
faulty
Test
ignition
system
.
Repair
Group
120
a
Main
relay
or
fuel
pump
relay
faulty
Test
main
relay
.
Repair
Group
130
a
Crankshaft/rpm
position
sensor
faulty
Test
crankshaft/rpm
sensor
.
120
b
c
h
i
ldle
speed
control
valve
faulty
Test
idle
speed
control
valve
.
c
d
e
Throttle
position
sensor
faulty
or
idle
signal
to
Test
throttle
position
sensor
.
DME
control
module
missing
.
c
d
h
i
Mass
air
flow
sensor
faulty
Test
mass
air
flow
sensor
Repair
Group
130
a
b
c
d
e
h
Large
air
intake
system
leak
Check
for
major
intake
air
leaks
downstream
of
mass
air
flow
sensor
.
a
c
d
e
g
h
Fuel
pressure
too
low
Test
fuel
pressure
.
Repair
Group
130
?
I
F
ue
l
pr
essu
r
e
t
oo
high
T
est
f
u
el
pressure
.
Repair
Group
130
d
e
g
h
Fuel
pump
delivery
volume
too
low
Test
fuel
pump
delivery
volume
.
Repair
Group
160
a
c
e
f
h
q
C
oo
l
a
nt
t
e
mp
e
r
a
t
u
r
e
se
n
so
r
f
au
lty
--]
T
est
coo
l
a
n
t
temp
erature
sensor
.
c
e
~
f
i
~
Fuel
injectors
leaking
Check
fuel
injectors
and
replace
leaking
injectors
.
~
Repair
Group
130
Throttle
plate
binding
or
incorrectly
adjusted
Check
throttle
plate
and
adjust
if
necessary
.
a
c
Electrical
connections
loose,
broken,
or
cor-
Visually
inspect
connectors
and
correct
any
roded
faults
.
Repair
Group
600
Ground
connections
loose,
broken,
or
corroded
Visually
inspect
ground
connections
and
correct
any
faults
.
Repair
Group
600
c
e
~
f
CO
content
too
high
Test
air
flowor
mass
air
flow
sensor
.
Repair
~
Group
130
a
b
c
d
e
CO
content
too
low
Test
mass
air
flow
sensor
.
gb
c
d
e
f
g
h
i
Inputsignals
to
ECM
missing,
ECM
in
limp
Make
electrical
tests
at
DMEECM
relay
.
Repair
home
mode
Group
130
a
~
b
~
c
~
d
e]
f
g
h
i
ECM
faulty
Test
DMEECM
inputs
.
If
all
inputs
are
correct,
replace
ECM
.
DRIVEABILITY
TROUBLESHOOTING
Page 59 of 759
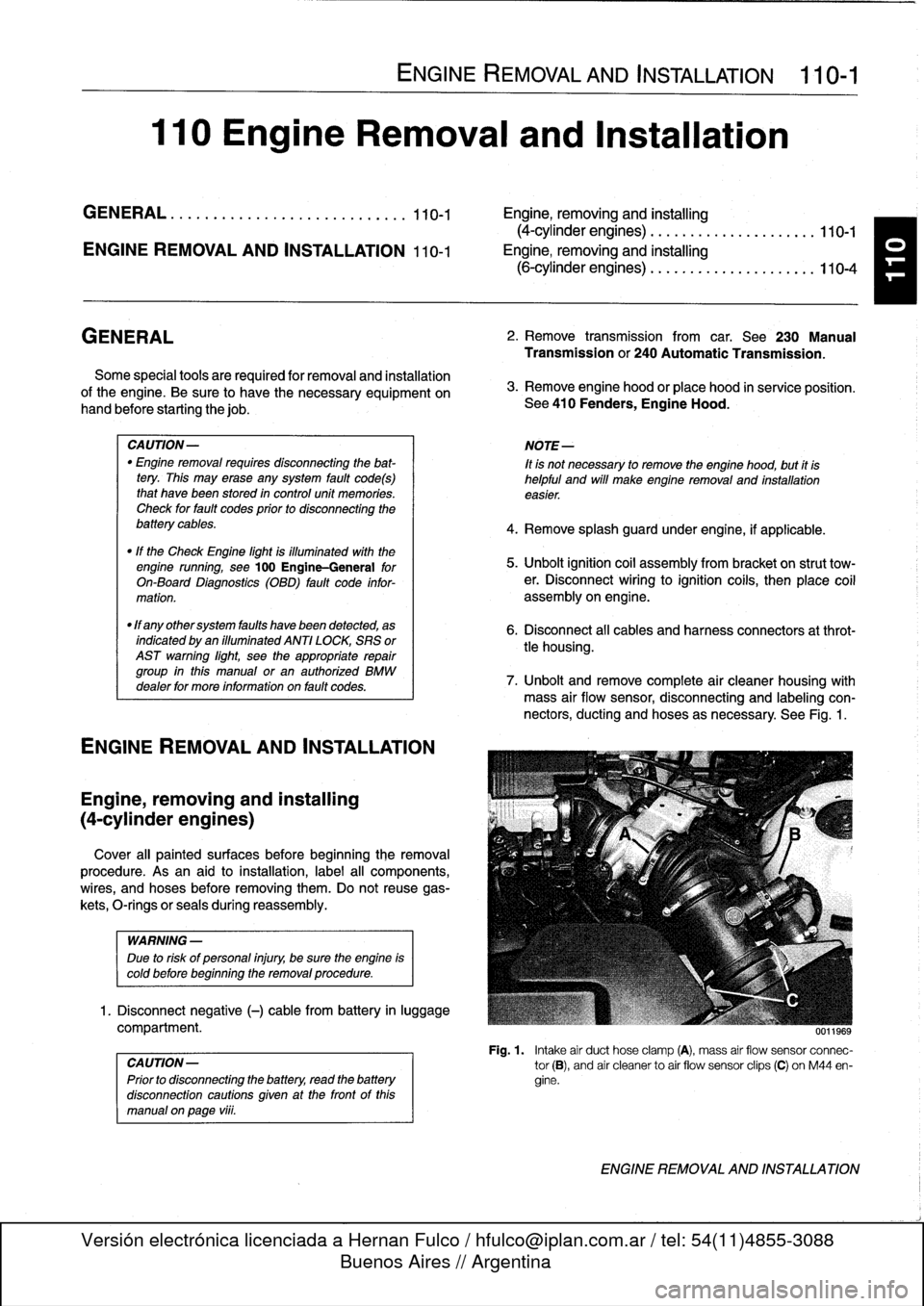
110
Engine
Removal
and
Installation
GENERAL
.
.
.
.
.......
.
.
.
..........
.
...
110-1
Engine,
removing
and
installing
(4-cylinder
engines)
.
..
.....
..
...........
110-1
ENGINE
REMOVAL
AND
INSTALLATION
110-1
Engine,
removing
and
installing
(6-cylinder
engines)
..
...
...
..
.....
..
....
110-4
GENERAL
Some
special
tools
are
required
for
removal
and
installation
of
the
engine
.
Be
sure
to
have
the
necessary
equipment
on
hand
before
starting
thejob
.
CAUTION-
"
Engine
removal
requires
disconnecting
the
bat-
tery
.
This
may
erase
any
system
fault
code(s)
that
havebeen
stored
in
control
unit
memories
.
Check
forfault
codes
prior
to
disconnecting
the
battery
cables
.
"
If
the
Check
Engine
lightis
illuminated
with
the
engine
running,
see
100
Engine-General
for
On-Board
Diagnostics
(08D)
fault
code
infor-
mation
.
"
If
any
other
system
faults
have
been
detected,
as
indicated
by
an
illuminated
ANTI
LOCK,
SRS
or
AST
warning
light,
see
the
appropriate
repair
group
inthis
manual
or
an
authorized
BMW
dealer
for
more
information
on
fault
codes
.
ENGINE
REMOVALAND
INSTALLATION
Engine,
removing
and
installing
(4-cylinder
engines)
Cover
al¡
painted
surfaces
before
beginning
theremoval
procedure
.
Asan
aid
to
installation,
label
al¡
components,
wires,
and
hoses
before
removing
them
.
Do
not
reuse
gas-
kets,
O-rings
or
seals
during
reassembly
.
WARNING
-
Due
to
risk
of
personal
injury,
be
sure
the
engine
is
cold
before
beginning
the
removalprocedure
.
1.
Disconnect
negative
(-)
cable
from
battery
in
luggage
compartment
.
0011969
CAUTION-
Prior
to
disconnecting
the
battery,
read
the
battery
disconnection
cautions
given
at
the
front
of
this
manual
on
page
viii
.
ENGINE
REMOVAL
AND
INSTALLATION
110-1
2
.
Remove
transmission
from
car
.
See230
Manual
Transmission
or
240
Automatic
Transmission
.
3
.
Remove
enginehood
or
place
hood
in
service
positíon
.
See
410
Fenders,
Engine
Hood
.
NOTE-
tt
is
notnecessary
to
remove
the
engine
hood,
but
it
is
helpful
and
will
make
engine
removal
and
installation
easier
.
4
.
Remove
splash
guard
under
engine,
if
applicable
.
5
.
Unbolt
ignition
coil
assembly
from
bracket
on
strut
tow-er
.
Disconnect
wiring
to
ignition
cofs,
then
place
coil
assembly
on
engine
.
6
.
Disconnect
al¡
cables
and
harness
connectors
at
throt-
tle
housing
.
7
.
Unbolt
andremove
complete
air
cleaner
housing
with
mass
air
flow
sensor,
disconnecting
and
labeling
con-
nectors,
ducting
and
hoses
asnecessary
.
See
Fig
.
1
.
Fig
.
1
.
Intake
air
duct
hose
clamp
(A),
mass
air
flow
sensor
connec-
tor
(B),
and
air
cleanerto
air
flow
sensor
clips
(C)
on
M44
en-
gine
.
ENGINE
REMOVAL
AND
INSTALLATION
Page 60 of 759
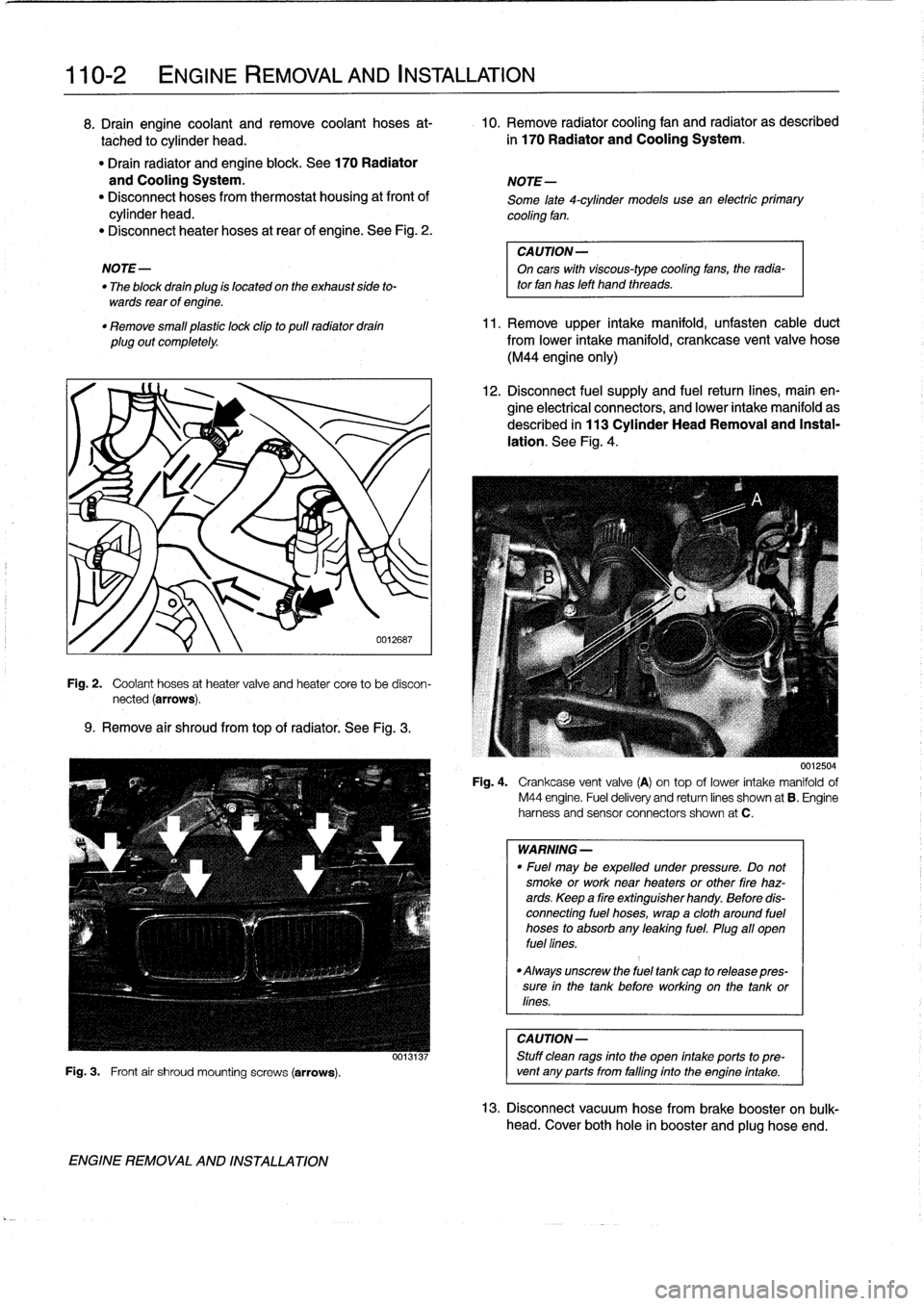
110-2
ENGINE
REMOVAL
AND
INSTALLATION
8
.
Drain
engine
coolant
andremove
coolant
hoses
at-
10
.
Remove
radiator
cooling
fan
and
radiator
as
described
tached
to
cylinder
head
.
in
170
Radiator
and
Cooling
System
.
"
Drain
radiator
and
engine
block
.
See
170
Radiator
and
Cooling
System
.
NOTE-
"
Disconnect
hoses
from
thermostat
housing
at
front
of
Some
late
4-cylinder
modelsuse
an
electric
prímary
cylinder
head
.
cooling
fan
.
"
Disconnect
heater
hoses
at
rear
of
engine
.
See
Fig
.
2
.
CAUTION-
NOTE-
On
cars
with
viscous-type
cooling
fans,
the
radia-
"
The
block
drain
plug
is
located
on
the
exhaust
side
to-
tor
fan
has
left
hand
threads
.
wards
rear
of
engine
.
"
Remove
small
plastic
lock
clíp
to
pull
radiator
drain
11
.
Remove
upper
intake
manifold,
unfasten
cable
duct
plug
out
completely
.
from
lower
intake
manifold,
crankcase
vent
valve
hose
(M44
engine
only)
0012687
Fig
.
2
.
Coolant
hoses
at
heater
valve
and
heatercore
to
be
discon-
nected
(arrows)
.
9
.
Remove
air
shroud
from
top
of
radiator
.
See
Fig
.
3
.
ENGINE
REMOVAL
AND
INSTALLATION
12
.
Disconnect
fuel
supply
and
fuel
return
lines,
main
en-
gine
electrical
connectors,
and
lower
intake
manifold
as
described
in
113
Cylinder
HeadRemoval
and
Instal-
lation
.
See
Fig
.
4
.
0012504
Fig
.
4
.
Crankcase
ventvalve
(A)
on
top
of
lower
intake
manifoldof
M44
engine
.
Fueldelivery
and
retum
lines
shown
at
B
.
Engine
harness
and
sensor
connectors
shown
at
C
.
WARNING
-
"
Fuel
may
be
expelled
under
pressure
.
Do
not
smoke
orworknear
heaters
or
other
fire
haz-
ards
.
Keep
a
fire
extinguisher
handy
.
Before
dis-
connecting
fuel
hoses,
wrap
a
cloth
around
fuel
hoses
to
absorb
any
leaking
fuel
.
Plug
all
open
fuel
lines
.
"
Always
unscrew
the
fuel
tank
cap
to
release
pres-
sure
in
the
tank
before
working
on
the
tank
or
lines
.
CAUTION-
0013137
I
Stuff
clean
rags
into
the
open
intake
ports
topre-
Fig
.
3
.
Front
air
shroud
mounting
screws
(arrows)
.
vent
any
parts
from
falling
into
the
engine
intake
.
13
.
Disconnect
vacuum
hose
from
brake
booster
on
bulk-
head
.
Cover
bothhole
in
booster
and
plug
hose
end
.
Page 62 of 759
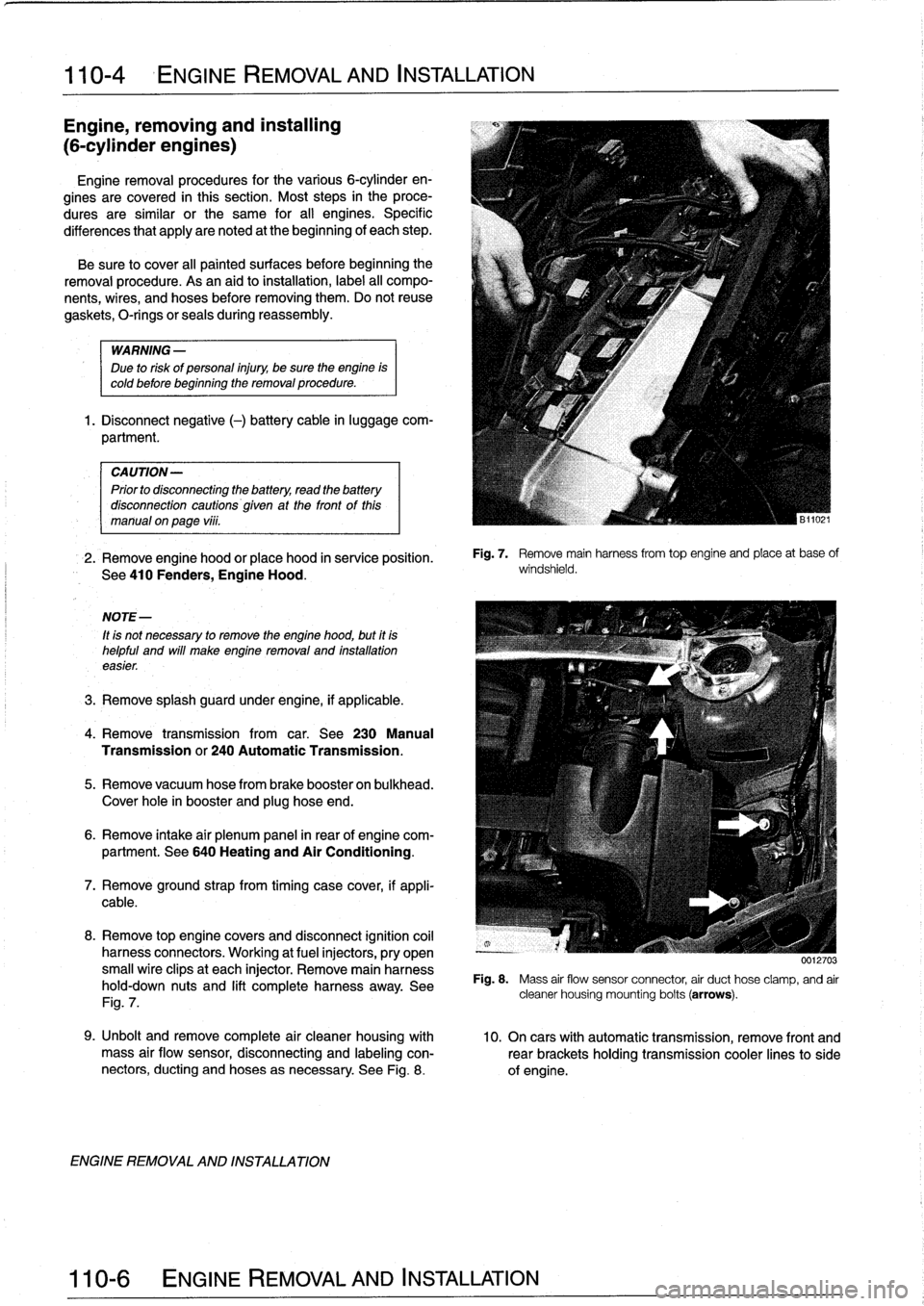
110-
4
ENGINE
REMOVAL
AND
INSTALLATION
Engine,
removing
and
installing
(6-cylinder
engines)
Engineremoval
procedures
for
the
various
6-cylinder
en-
gines
arecovered
in
this
section
.
Most
steps
in
theproce-
dures
are
similar
or
the
same
for
al¡
engines
.
Specific
differences
that
apply
are
noted
at
the
beginning
of
each
step
.
Be
sure
to
cover
all
painted
surfaces
before
beginning
the
removal
procedure
.
As
an
aid
to
installation,
label
all
compo-
nents,wires,
and
hoses
before
removing
them
.
Do
not
reuse
gaskets,
O-rings
or
seals
during
reassembly
.
WARNING
-
Due
to
risk
of
personal
injury,
be
sure
the
engine
is
cold
before
beginning
the
removalprocedure
.
1
.
Disconnect
negative
(-)
battery
cable
in
luggage
com-
partment
.
CAUTION-
Prior
to
disconnecting
the
battery,
read
the
battery
disconnection
cautions
given
at
the
front
of
this
manual
onpage
vi¡¡
.
2
.
Remove
engine
hood
or
place
hood
in
service
position
.
See410
Fenders,
Engine
Hood
.
NOTE-
1t
is
not
necessary
to
remove
the
engine
hood,
but
it
is
helpful
and
will
make
engine
removal
and
installation
easier
.
3
.
Remove
splash
guardunder
engine,
if
applicable
.
4
.
Remove
transmission
from
car
.
See
230
Manual
Transmission
or
240Automatic
Transmission
.
5
.
Remove
vacuum
hosefrom
brake
booster
on
bulkhead
.
Cover
hole
in
booster
and
plug
hose
end
.
6
.
Remove
intake
air
plenum
panel
in
rear
of
engine
com-
partment
.
See
640
Heating
and
AirConditioning
.
7
.
Remove
ground
strap
from
timing
case
cover,
if
appli-
cable
.
8
.
Remove
top
enginecovers
and
disconnect
ignition
coil
harness
connectors
.
Working
at
fuel
injectors,
pry
open
small
wire
clipsat
each
injector
.
Remove
main
harness
hold-down
nuts
and
lift
completeharness
away
.
See
Fig
.
7
.
ENGINE
REMOVAL
AND
INSTALLATION
Fig
.
7
.
Remove
mainharnessfrom
top
engine
and
place
at
base
of
windshield
.
0012703
Fig
.
8
.
Mass
air
flow
sensor
connector
air
duct
hose
clamp,
and
air
cleaner
housing
mounting
bolts
(arrows)
.
9
.
Unbolt
andremove
complete
air
cleaner
housing
with
10
.
On
cars
with
automatic
transmission,
remove
front
and
mass
air
flow
sensor,
disconnecting
and
labeling
con-
rearbrackets
holding
transmission
cooler
linesto
side
nectors,
ducting
and
hoses
asnecessary
.
See
Fig
.
8
.
of
engine
.
Page 68 of 759
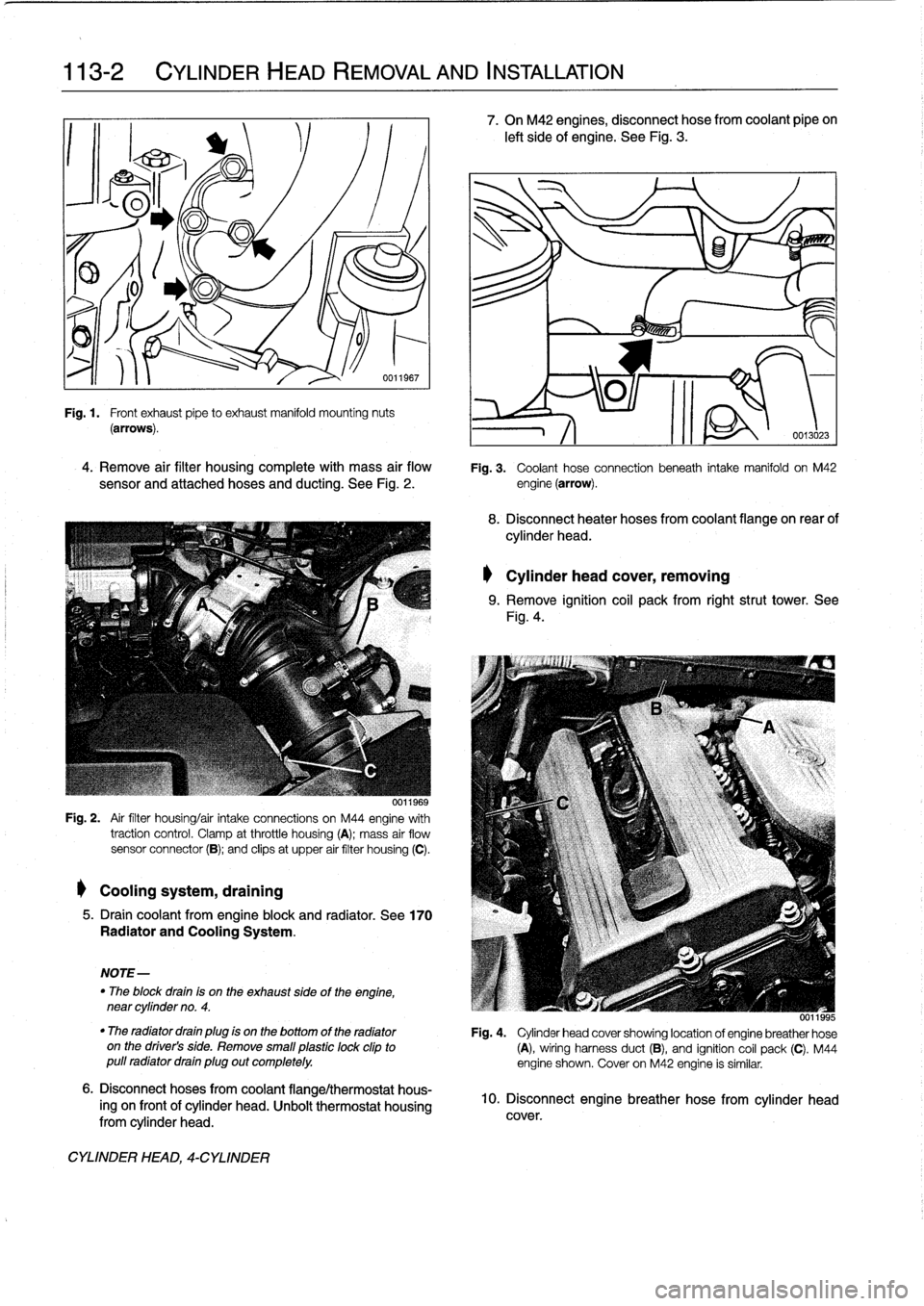
113-2
CYLINDER
HEAD
REMOVAL
AND
INSTALLATION
0011s6i
-
0Fig
.
1
.
Front
exhaust
pipe
to
exhaust
manifold
mountíng
nuts
(arrows)
.
-1
~~
0013023
4
.
Remove
air
filter
housing
complete
with
mass
air
flow
Fig
.
3
.
Coolant
hose
connection
beneath
intake
manifold
on
M42
sensor
and
attached
hoses
and
ducting
.
See
Fig
.
2
.
engine
(arrow)
.
0011969
Fig
.
2
.
Air
filter
housing/air
intake
connections
on
M44
engine
with
traction
control
.
Clamp
atthrottle
housing
(A)
;
mass
air
flow
sensor
connector
(B)
;
and
clips
at
upper
air
filter
housing
(C)
.
Coolingsystem,
draining
5
.
Draincoolant
from
engine
block
and
radiator
.
See
170
Radiator
and
Cooling
System
.
NOTE-
"
The
block
drain
is
on
the
exhaust
sideof
the
engine,
near
cylinder
no
.
4
.
6
.
Disconnect
hoses
from
coolant
flange/thermostat
hous-
ing
on
frontof
cylinder
head
.
Unbolt
thermostat
housing
from
cylinder
head
.
CYLINDER
HEAD,
4-CYLINDER
7
.
On
M42
engines,
disconnect
hose
from
coolant
pipe
on
left
side
of
engine
.
See
Fig
.
3
.
8
.
Disconnect
heater
hoses
from
coolant
flange
on
rear
of
cylinder
head
.
Cylinder
head
cover,
removing
9
.
Remove
ignition
coil
pack
from
rightstrut
tower
.
See
Fig
.
4
.
0011995
"
The
radiator
drain
plug
is
on
the
bottomof
the
radiator
Fig
.
4
.
Cylinder
head
cover
showing
location
of
engine
breather
hose
on
the
driver's
side
.
Remove
small
plastic
lock
clipto
(A),
wiring
harness
duct
(B),
and
ignition
coil
pack
(C)
.
M44
pull
radiator
drain
plug
out
completely
.
engine
shown
.
Cover
on
M42
engine
is
similar
.
10
.
Disconnect
engine
breather
hose
from
cylinder
head
cover
.
Page 70 of 759
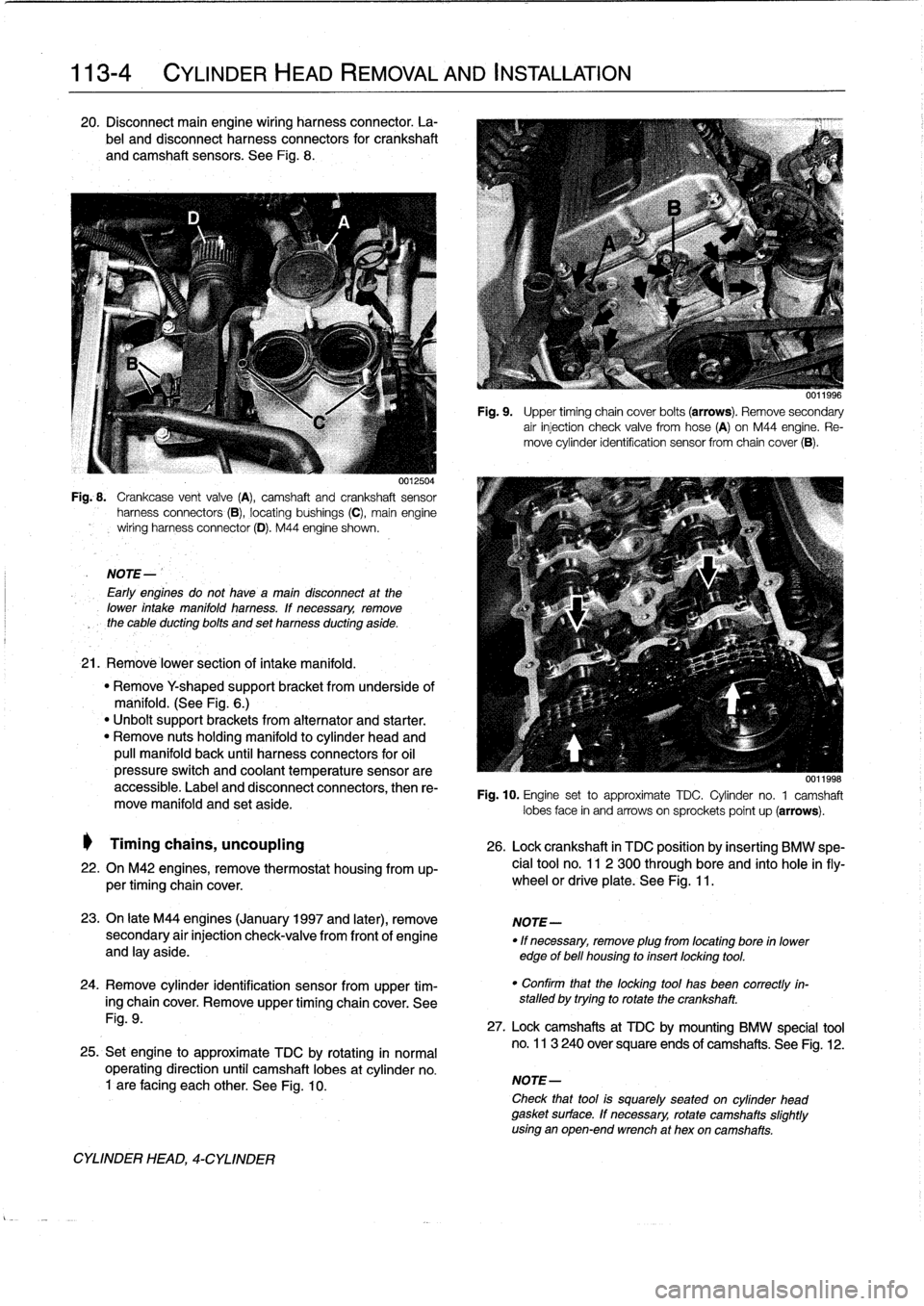
113-4
CYLINDER
HEAD
REMOVAL
AND
INSTALLATION
20
.
Disconnect
main
engine
wiring
harness
connector
.
La-
bel
and
disconnect
harness
connectors
for
crankshaft
and
camshaft
sensors
.
See
Fig
.
8
.
0012504
Fig
..
Crankcase
vent
valve
(A),
camshaft
and
crankshaft
sensor
harness
connectors
(B),
locating
bushings
(C),
main
engine
wiring
harnessconnector
(D)
.
M44
engine
shown
.
NOTE-
Early
engines
do
not
havea
maín
disconnect
at
the
lower
intake
manifold
harness
.
lf
necessary,
remove
the
cable
ducting
bolts
and
set
harness
ducting
aside
.
21
.
Remové
lower
section
of
intake
manifold
.
"
Remove
Y
shaped
supportbracket
from
underside
of
manifold
.
(See
Fig
.
6
.)
"
Unbolt
support
brackets
from
alternator
and
starter
.
"
Remove
nuts
holding
manifold
to
cylinder
head
and
pull
manifold
back
until
harness
connectors
for
oil
pressure
switch
and
coolant
temperature
sensorare
accessible
.
Label
and
disconnect
connectors,
then
re-
move
manifold
and
set
aside
.
Timing
chains,
uncoupling
26
.
Lock
crankshaft
in
TDC
position
by
insertíng
BMW
spe-
22
.
On
M42
engines,
remove
thermostat
housing
from
up-
cial
tool
no
.
11
2
300
through
bore
and
into
hole
infly-
per
timing
chaincover
.
wheel
or
driveplate
.
See
Fig
.
11
.
23
.
On
late
M44
engines
(January
1997
and
later),
remove
NOTE-
secondary
air
injection
check-valve
from
front
of
engine
"
If
necessary,
remove
plug
from
locating
bore
in
lower
and
lay
aside
.
edge
of
bell
housing
to
insert
locking
tool
.
24
.
Remove
cylinder
identification
sensor
from
upper
tim-
ing
chaincover
.
Remove
upper
timing
chaincover
.
See
Fig
.
9
.
25
.
Set
engine
to
approximate
TDC
by
rotating
in
normal
operating
direction
until
camshaft
lobes
at
cylinder
no
.
1
are
facing
each
other
.
See
Fig
.
10
.
CYLINDER
HEAD,
4-CYLINDER
Fig
.
9
.
Upper
timing
chain
cover
bolts
(arrows)
.
Remove
secondary
air
injection
check
valve
fromhose
(A)
on
M44
engine
.
Re-
move
cylinder
identification
sensor
from
chaincover
(B)
.
0011998
Fig
.
10
.
Engine
set
to
approximate
TDC
.
Cylinder
no
.
1
camshaft
lobes
face
in
and
arrows
on
sprockets
poínt
up
(arrows)
.
"
Confirm
that
the
locking
tool
has
been
correctly
in-
stalled
by
trying
to
rotate
the
crankshaft
.
27
.
Lock
camshafts
at
TDC
by
mounting
BMW
specíal
tool
no
.
113
240
over
square
ends
of
camshafts
.
See
Fig
.
12
.
NOTE-
Check
that
tool
is
squarely
seated
on
cylinder
head
gasket
surface
.
If
necessary,
rotate
camshafts
slightly
using
an
open-end
wrench
at
hex
oncamshafts
.
Page 71 of 759
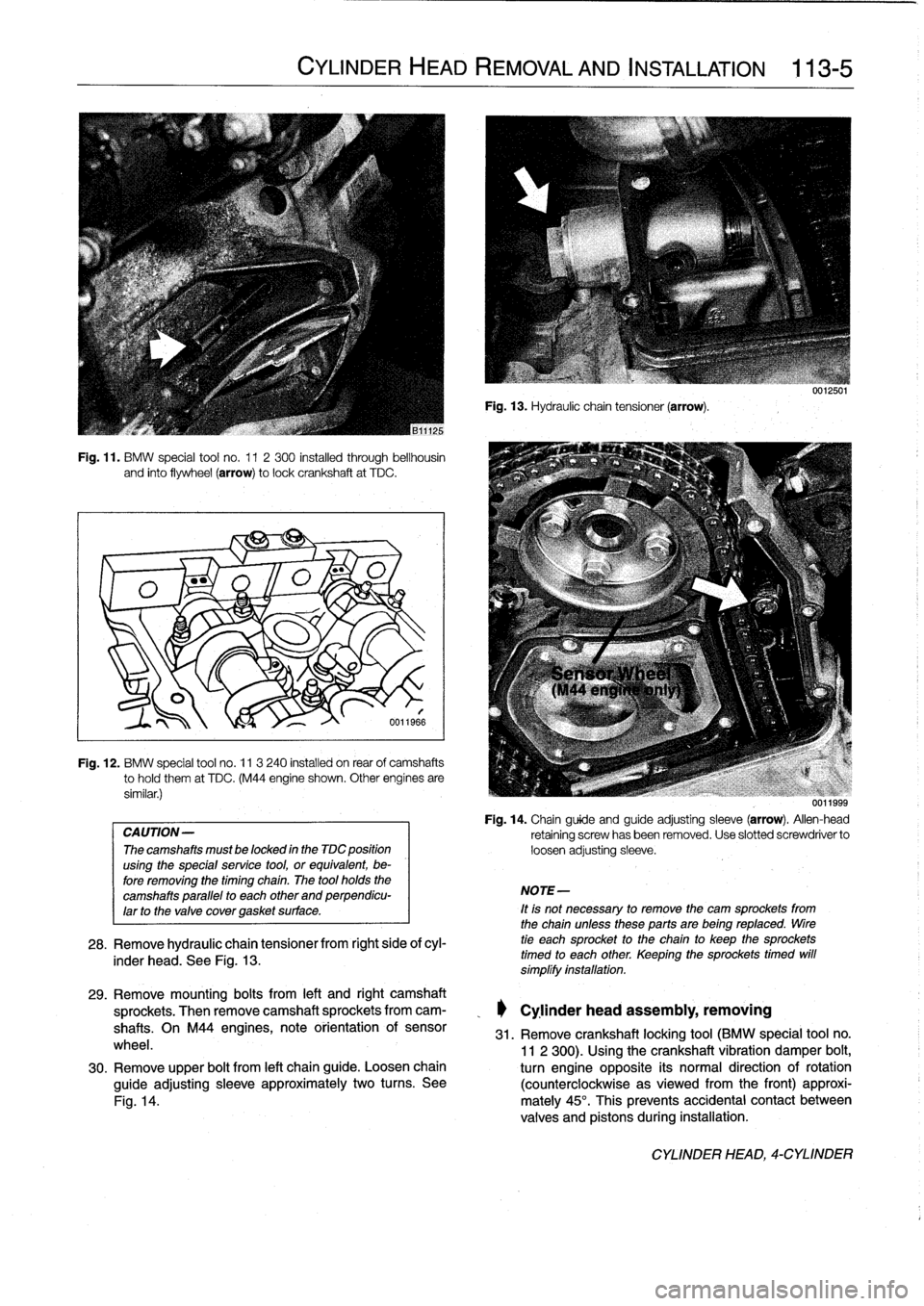
Fig
.
11
.
BMW
special
tool
no
.
11
2300
installed
through
bellhousin
and
finto
flywheel
(arrow)
tolockcrankshaft
at
TDC
.
Fig
.
12
.
BMW
special
tool
no
.
11
3
240
installed
on
rear
of
camshafts
tohold
them
at
TDC
.
(M44
engine
shown
.
Other
engínes
are
similar
.)
CAUTION-
The
camshafts
must
be
locked
in
the
TDC
position
using
the
special
service
tool,
or
equivalent,
be-
fore
removing
the
timing
chaín
.
The
tool
holds
the
camshafts
parallel
to
each
other
and
perpendicu-
larto
the
valve
covergasket
surface
.
CYLINDER
HEAD
REMOVAL
AND
INSTALLATION
113-5
6011966
28
.
Remove
hydraulic
chain
tensiones
from
right
side
ofcyl-
inder
head
.
See
Fig
.
13
.
Fig
.
13
.
Hydraulic
chain
tensioner
(arrow)
.
NOTE-
It
is
not
necessary
to
remove
the
cam
sprockets
from
the
chainuntessthese
parts
are
being
reptaced
.
tire
tie
each
sprocket
to
the
chain
to
keep
the
sprockets
timed
to
each
other
.
Keeping
the
sprockets
timed
will
símplífy
instaftation
.
uu
11999
Fig
.
14
.
Chainguide
and
guide
adjusting
sleeve
(arrow)
.
Allen-head
retaining
screwhasbeen
removed
.
Use
slotted
screwdriver
to
loosen
adjusting
sleeve
.
29
.
Remove
mounting
bolts
from
left
and
right
camshaft
sprockets
.
Then
remove
camshaft
sprockets
from
cam-
_
Cylinder
head
assembly,
removing
shafts
.
On
M44
engines,
note
orientation
of
sensor
31
.
Remove
crankshaft
locking
tool
(BMW
special
tool
no
.
wheel
.
11
2
300)
.
Usingthe
crankshaft
vibration
damper
bolt,
30
.
Remove
upper
bolt
from
left
chainguide
.
Loosen
chain
turn
engine
opposite
its
normal
direction
of
rotation
guide
adjusting
sleeve
approximately
two
turns
.
See
(counterclockwise
asviewed
from
the
front)
approxi
Fig
.
14
.
mately
45°
.
This
prevents
accidental
contact
between
valves
and
pistons
during
installation
.
CYLINDER
HEAD,
4-CYLINDER