Timing BMW M3 1998 E36 Service Manual
[x] Cancel search | Manufacturer: BMW, Model Year: 1998, Model line: M3, Model: BMW M3 1998 E36Pages: 759
Page 110 of 759
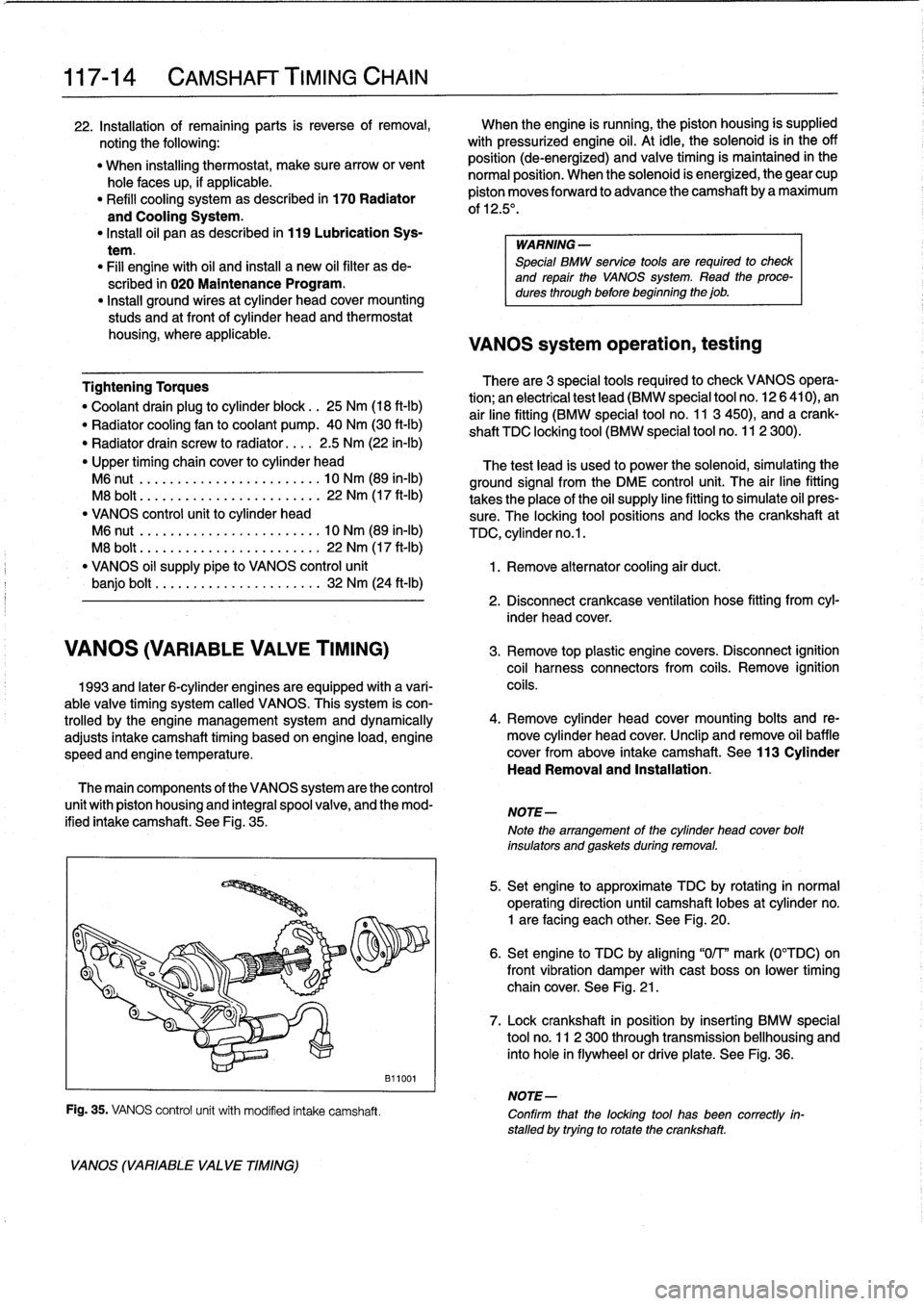
117-
1
4
CAMSHAFT
TIMING
CHAIN
22
.
Installation
of
remaining
parts
is
reverse
of
removal,
When
theengine
is
running,
the
piston
housing
is
supplied
noting
the
following
:
with
pressurized
engine
oil
.
At
idie,
the
solenoid
isin
the
off
"
When
installing
thermostat,
make
sure
arrow
or
vent
position
(de-energized)
and
valve
timing
is
maintained
in
the
hole
faces
up,
if
applicable
.
normal
position
:
When
the
solenoid
is
energized,
the
gear
cup
"
Refill
cooling
systemas
described
in
170
Radiator
piston
moves
forward
to
advance
the
camshaftby
a
maximum
and
Coming
System
.
of
12
.5
.
"
Install
oil
pan
as
described
in
119
Lubrication
Sys-
tem
.
"
Fill
engine
with
oil
and
install
a
new
oil
filter
as
de-
scribed
in
020
Maintenance
Program
.
"
Insta¡¡
ground
wires
at
cylinder
head
cover
mounting
studs
and
at
front
of
cylinder
head
and
thermostat
housing,
where
applicable
.
VANOS
system
operation,
testing
Tightening
Torques
There
are3
special
tools
required
to
check
VANOS
opera-
"
Coolant
drain
plugto
cylinder
block
.
.
25
Nm
(18
ft-Ib)
tion
;
an
electricaltest
lead
(BMW
special
tool
no
.
12
6
410),
an
"
Radiator
cooling
fan
to
coolant
pump
.
40
Nm
(30
ft-Ib)
air
line
fitting
(BMW
special
tool
no
.
11
3
450),
and
a
crank-
"
Radiator
drain
screw
to
radiator
...
.
2
.5
Nm
(22
in-Ib)
shaft
TDC
locking
tool
(BMW
special
tool
no
.
112
300)
.
"
Upper
timing
chaincover
to
cylinder
head
The
test
leal
is
used
to
power
the
solenoid,
simulating
the
M6
nut
...
.....
.............
..
.
10
Nm
(89
in-lb)
ground
signal
from
the
DME
control
unit
.
The
air
line
fitting
M8
bolt
.....
....
.
.
.............
22
Nm
(17
ft-Ib)
takes
the
place
of
the
oil
supply
line
fitting
to
simulate
oil
Ares-
"
VANOS
control
unit
to
cylinder
head
sure
.
The
locking
tool
positions
and
locks
the
crankshaft
at
M6
nut
.........
..
..
.
..........
10
Nm
(89
in-lb)
TDC,
cylinder
no
.
l.
M8
bolt
........
...
.............
22
Nm
(17
ft-Ib)
"
VANOS
oil
supply
pipe
to
VANOS
control
unit
1
.
Remove
alternator
cooling
air
duct
.
banjo
bolt
.......
..
..
.
..........
32
Nm
(24
ft-Ib)
VANOS
(VARIABLE
VALVE
TIMING)
3
.
Remove
top
plastic
enginecovers
.
Disconnect
ignition
coil
harness
connectors
fromcofs
.
Remove
ignition
1993
and
later
6-cylinder
engines
are
equipped
with
a
vari-
coils
.
able
valve
timing
system
called
VANOS
.
This
system
is
con-
trolled
by
the
engine
management
system
and
dynamically
4
.
Remove
cylinder
head
cover
mounting
bolts
and
re-
adjusts
intake
camshaft
timing
based
on
engine
load,
engine
move
cylinder
head
cover
.
Unclip
andremove
oil
baffle
speed
and
engine
temperature
.
cover
from
above
intake
camshaft
.
See
113
Cylinder
Head
Removal
and
installation
.
The
main
components
of
the
VANOS
system
are
the
control
unit
with
piston
housing
and
integral
spool
valve,
and
the
mod-
ified
intake
camshaft
.
See
Fig
.
35
.
VANOS
(VARIABLE
VA
LVE
TIMING)
Fig
.
35
.
VANOS
control
unit
with
modified
intake
camshaft
.
B11001
WARNING
-
Special
BMW
service
tools
are
required
to
check
and
repair
the
VANOS
System
.
Read
theproce-
dures
through
before
beginning
the
job
.
2
.
Disconnect
crankcase
ventilation
hose
fitting
from
cyl-
inder
head
cover
.
NOTE-
Note
the
arrangement
of
the
cylinder
head
cover
bolt
insulators
and
gaskets
during
removal
.
5
.
Set
engine
to
approximate
TDC
by
rotating
in
normal
operating
direction
until
camshaft
lobes
at
cylinder
no
.
1
are
facing
each
other
.
See
Fig
.
20
.
6
.
Set
engine
to
TDC
by
aligning
"0/T"
mark
(0°TDC)on
front
vibration
damper
withcast
boss
on
lower
timing
chain
cover
.
See
Fig
.
21
.
7
.
Lock
crankshaft
in
position
by
inserting
BMW
special
tool
no
.
11
2
300
through
transmission
bellhousing
and
into
hole
in
flywheelor
driveplate
.
See
Fig
.
36
.
NOTE-
Confirm
that
the
locking
tool
has
been
correctly
in-
stalled
by
trying
to
rotatethe
crankshaft
.
Page 111 of 759
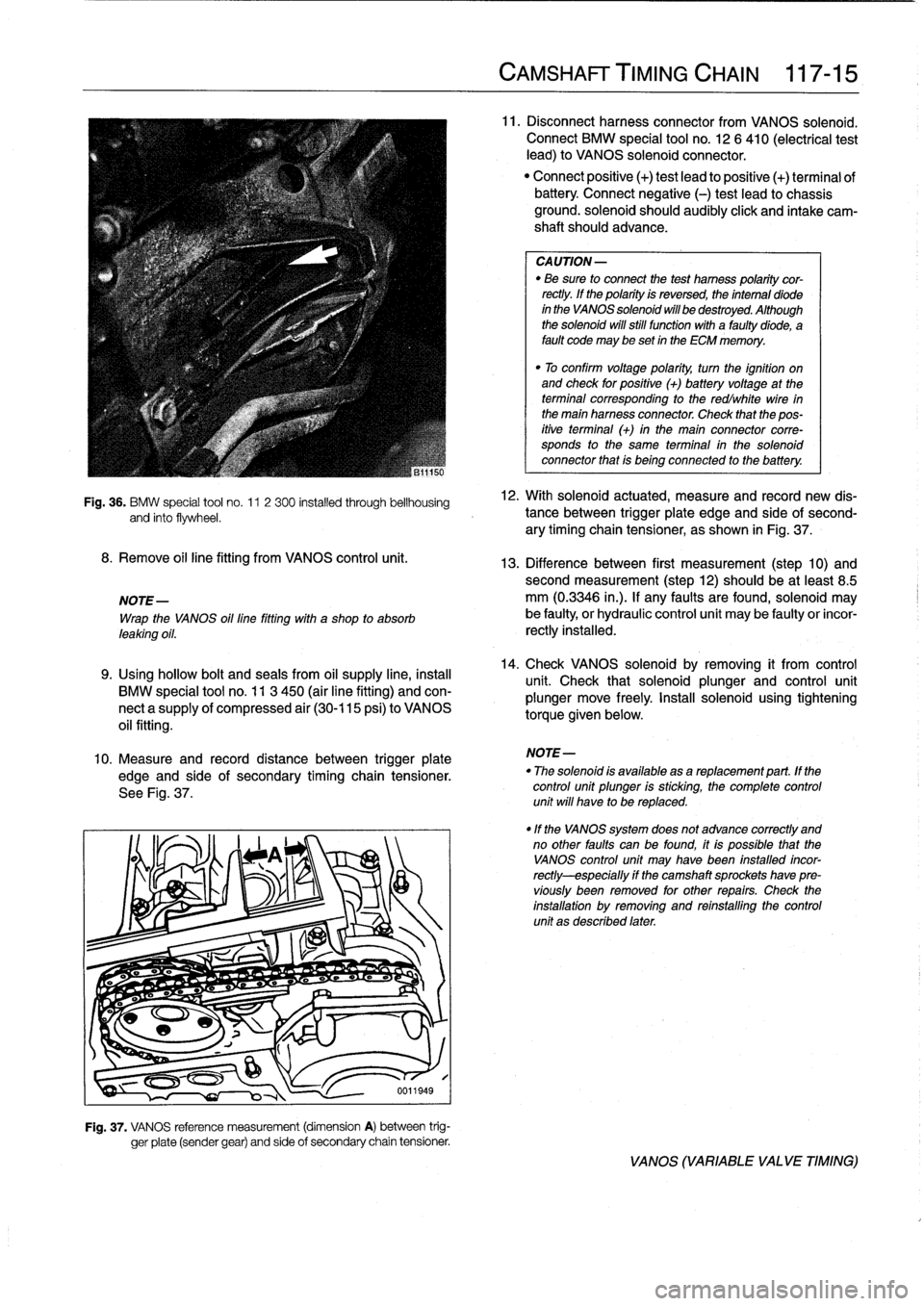
Fig
.
36
.
BMW
special
tool
no
.
11
2
300
installed
through
bellhousing
and
finto
flywheel
.
8
.
Remove
oil
line
fitting
from
VANOS
control
unit
.
NOTE-
Wrap
the
VANOS
oil
line
fitting
with
a
shop
to
absorb
leaking
oil
.
9
.
Using
hollow
bolt
and
seals
from
oil
supply
line,
instan
BMW
special
tool
no
.
11
3
450
(air
line
fitting)
and
con-
nect
a
supply
of
compressed
air
(30-115
psi)
to
VANOS
oil
fitting
.
10
.
Measure
and
record
distance
between
trigger
plate
edge
and
side
of
secondary
timing
chain
tensioner
.
See
Fig
.
37
.
Fig
.
37
.
VANOS
reference
measurement
(dimension
A)
between
trig-
ger
píate
(sender
gear)
and
side
of
secondary
chain
tensioner
.
CAMSHAFT
TIMING
CHAIN
117-
1
5
11
.
Disconnectharness
connector
from
VANOS
solenoid
.
Connect
BMW
special
tool
no
.
12
6
410
(electrical
test
lead)
to
VANOS
solenoid
connector
.
"
Connect
positive
(+)
test
lead
to
positive
(+)
terminal
ofbattery
Connect
negative
(-)
test
leadto
chassis
ground
.
solenoid
should
audibly
click
and
intake
cam-
shaft
should
advance
.
CA
UTION-
"
Be
sure
to
connect
the
test
hamess
polaritycor-
rectly
.
lf
the
polarity
is
reversed,
the
intemal
diode
in
the
VANOS
solenoid
will
be
destroyed
.
Although
the
solenoid
will
still
functionwith
a
faultydiode,
a
fault
code
may
be
set
in
the
ECM
memory
.
"
To
confirm
voltage
polarity,
turn
the
ignition
on
and
check
for
positive
(+)
batteryvoltage
at
the
terminal
corresponding
to
the
redlwhite
wire
in
the
main
harness
connector
.
Check
that
the
pos-
itive
terminal
(+)
in
the
main
connector
corre-
sponds
to
the
same
terminal
in
the
solenoid
connector
that
is
being
connected
to
the
battery
.
12
.
With
solenoid
actuated,
measure
and
record
new
dis-
tance
between
trigger
plate
edge
and
side'of
second-
ary
timing
chain
tensioner,
as
shown
in
Fig
.
37
.
13
.
Difference
between
first
measurement
(step
10)
andsecond
measurement
(step12)
should
be
at
least
8
.5
mm
(0
.3346
in
.)
.
lf
any
faults
arefound,
solenoid
may
be
faulty,
or
hydraulic
control
unit
may
be
faulty
or
incor-
rectly
installed
.
14
.
Check
VANOS
solenoid
byremoving
it
from
control
unit
.
Check
that
solenoid
plunger
and
control
unit
plunger
move
freely
.
Install
solenoid
using
tighteníng
torque
given
below
.
NOTE-
"
The
solenoid
is
available
asareplacement
part
.
lf
the
control
unit
plunger
is
sticking,
the
complete
control
unit
will
have
to
be
replaced
.
"lf
the
VANOS
system
does
not
advance
correctly
and
no
other
faults
can
be
found,
itis
possible
that
the
VANOS
control
unit
may
Nave
been
fnstalled
incor-
rectly-especially
if
the
camshaft
sprockets
have
pre-
víously
been
removed
for
other
repairs
.
Check
the
installation
by
removing
and
reinstalling
the
control
unit
as
described
later
.
VANOS
(VARIABLE
VALVE
TIMING)
Page 112 of 759
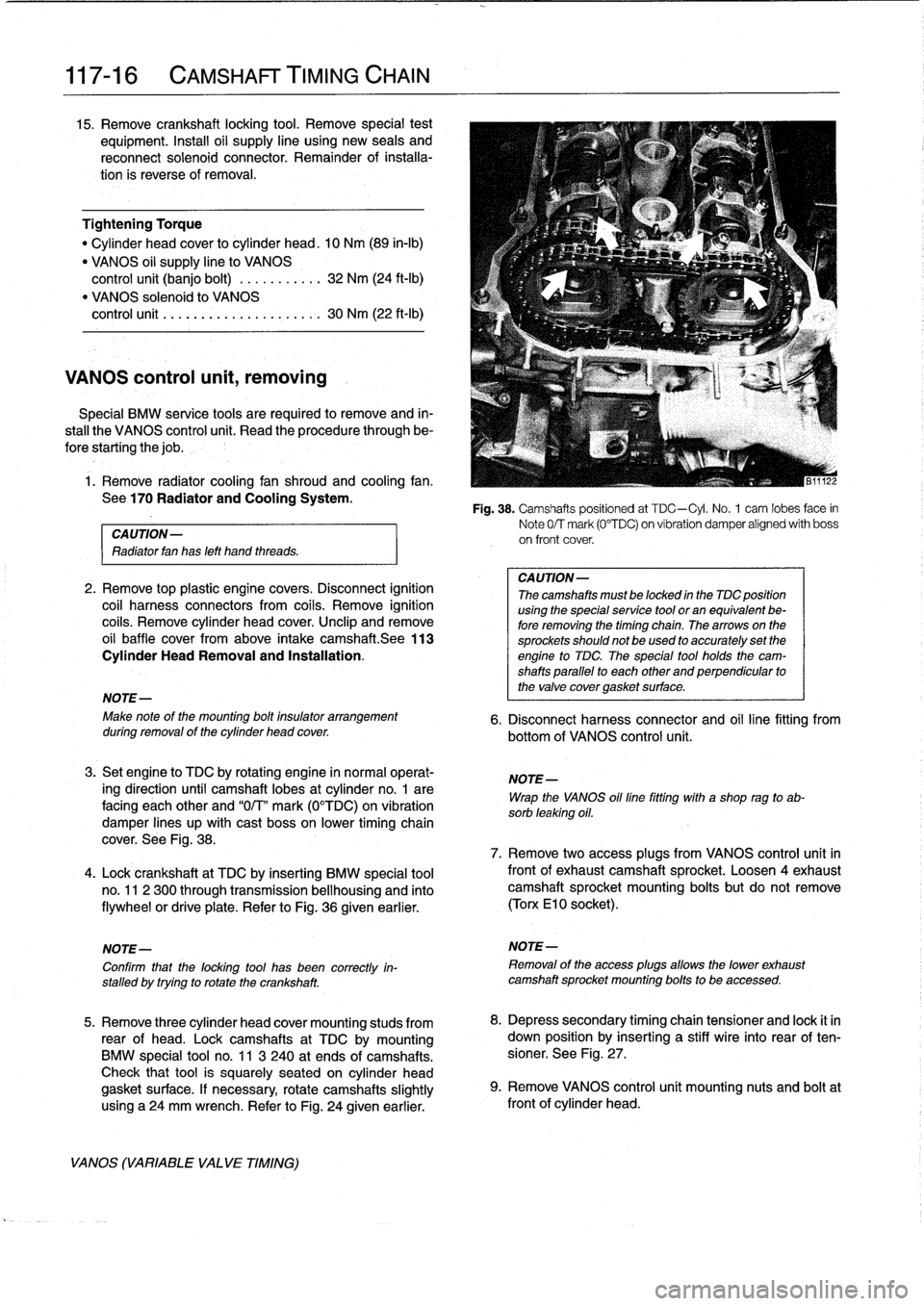
117-
1
6
CAMSHAFT
TIMING
CHAIN
15
.
Remove
crankshaft
locking
tool
.
Remove
special
test
equipment
.
Insta¡¡
oil
supply
line
using
new
seals
and
reconnect
solenoid
connector
.
Remainder
of
installa-
tion
is
reverse
of
removal
.
Tightening
Torque
"
Cylinder
head
cover
to
cylinder
head
.
10
Nm
(89
in-lb)
"
VANOS
oil
supply
line
to
VANOS
control
unit
(banjo
bolt)
..
.........
32
Nm
(24
ft-Ib)
"
VANOS
solenoidlo
VANOS
control
unit
........
.
.
.
..
........
30
Nm
(22
ft-Ib)
VANOS
control
unit,
removing
Special
BMW
service
tools
are
required
lo
remove
and
in-
stall
the
VANOS
control
unit
.
Read
the
procedure
through
be-
forestarting
the
job
.
1
.
Remove
radiator
cooling
fan
shroud
and
cooling
fan
.
See
170
Radiator
and
Cooling
System
.
CAUTION-
Radiator
fan
has
left
hand
threads
.
2
.
Remove
top
plastic
engine
covers
.
Disconnect
ignition
coil
harness
connectors
from
coils
.
Remove
ignition
coils
.
Remove
cylinder
head
cover
.
Unclip
andremove
oil
baffle
cover
from
above
intake
camshaft
.See
113
Cylinder
Head
Removal
and
Installation
.
NOTE-
Make
note
of
the
mounting
bolt
insulator
arrangement
during
removal
of
the
cylinder
head
cover
.
3
.
Set
engine
lo
TDC
by
rotating
engine
in
normal
operat-
ing
direction
until
camshaft
lobes
at
cylinder
no
.
1
are
facing
each
other
and
"0/T"
mark
(0°TDC)
on
vibration
damper
lines
up
with
cast
boss
on
lower
timing
chain
cover
.
See
Fig
.
38
.
4
.
Lock
crankshaft
at
TDC
by
inserting
BMW
special
tool
no
.
11
2
300
through
transmission
bellhousing
and
finto
flywheel
or
drive
plate
.
Refer
to
Fig
.
36
given
earlier
.
NOTE-
Confirm
that
the
locking
tool
has
been
correctly
in-
stalled
by
trying
to
rotatethe
crankshaft
.
5
.
Remove
three
cylinder
head
cover
mounting
studs
from
rear
of
head
.
Lockcamshafts
at
TDC
bymounting
BMW
special
tool
no
.
11
3
240
at
ends
of
camshafts
.
Check
that
tool
is
squarely
seated
on
cylinder
head
gasket
surface
.
If
necessary,
rotate
camshafts
slightly
using
a24
mm
wrench
.
Refer
to
Fig
.
24
given
earlier
.
VANOS
(VARIABLE
VALVE
TIMING)
Fig
.
38
.
Camshafts
positioned
at
TDC-Cyl
.
No
.
1
cam
lobes
face
in
Note
0/T
mark
(0°TDC)
on
vibration
damper
alígned
with
boss
on
front
cover
.
CA
UTION-
Thecamshafts
mustbe
locked
in
the
TDC
position
using
the
specialservice
tool
or
an
equivalent
be-
fore
removing
the
timing
chain
.
Thearrows
on
the
sprockets
should
not
be
used
to
accurately
set
the
engine
to
TDC
The
special
tool
holds
the
cam-
shafts
parallel
to
each
other
and
perpendicular
to
the
valve
cover
gasket
surface
.
6
.
Disconnect
harness
connector
and
oil
line
fitting
from
bottom
of
VANOS
control
unit
.
NOTE-
Wrap
the
VANOS
oilfine
fitting
with
a
shop
rag
to
ab-
sorb
leaking
oil
.
7
.
Remove
two
access
plugs
from
VANOS
control
unit
in
frontof
exhaustcamshaft
sprocket
.
Loosen
4exhaustcamshaft
sprocket
mounting
bolts
but
do
not
remove
(Torx
El
0
socket)
.
NOTE-
Removal
of
the
access
plugs
allows
the
lower
exhaust
camshaft
sprocket
mounting
bolts
to
be
accessed
.
8
.
Depress
secondary
timing
chain
tensioner
and
lock
it
in
down
position
by
inserting
a
stiff
wire
into
rear
of
ten-
sioner
.
See
Fig
.
27
.
9
.
Remove
VANOS
control
unít
mounting
nuts
and
boltat
front
of
cylinder
head
.
Page 113 of 759
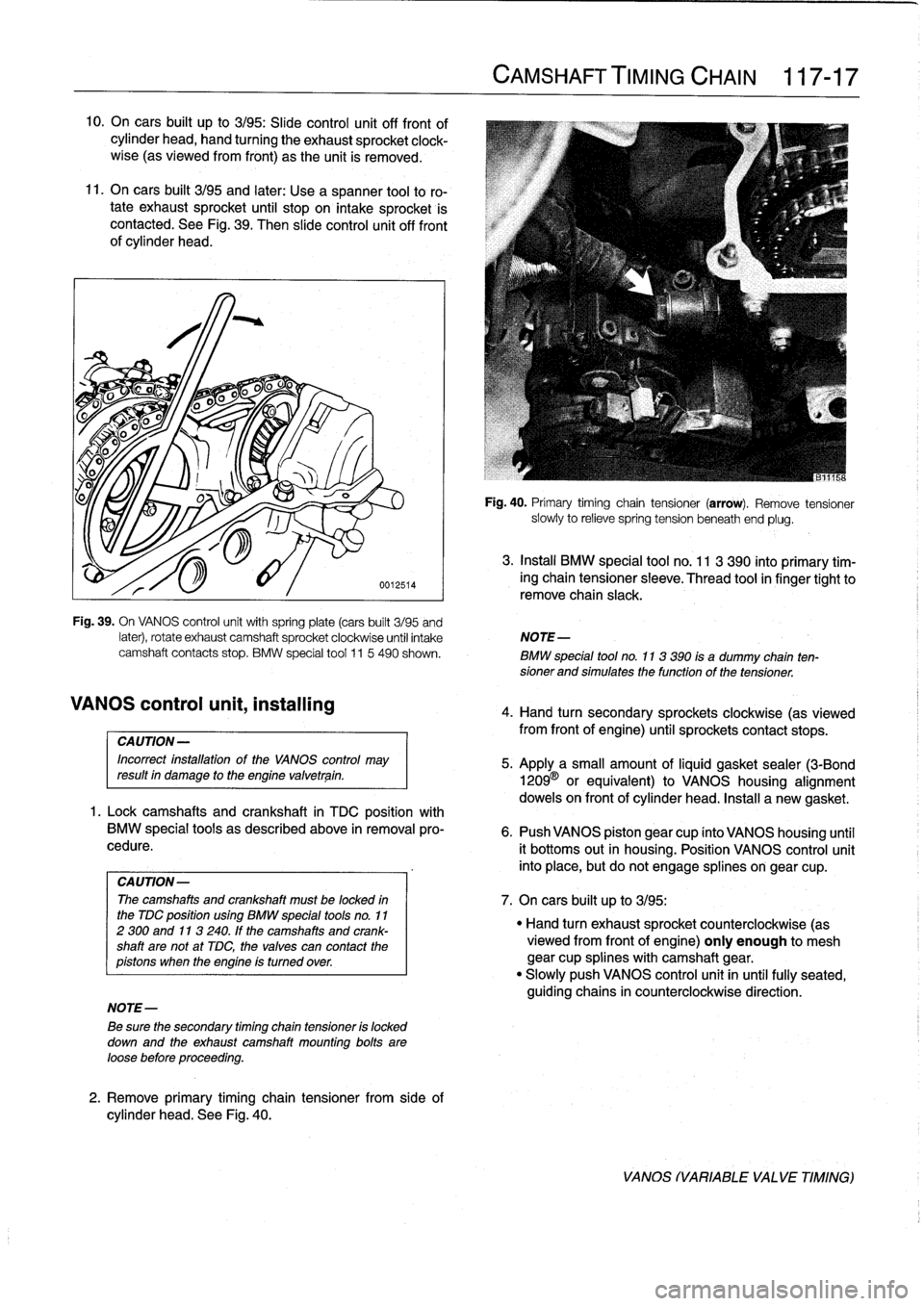
10
.
On
cars
built
up
to
3/95
:
Slide
control
unit
off
front
of
cylinder
head,
hand
turning
the
exhaust
sprocket
clock-
wise
(as
viewedfrom
front)
as
the
unit
is
removed
.
11
.
On
cars
built
3/95
and
latee
:
Use
a
spanner
toolto
ro-
tate
exhaust
sprocket
until
stop
on'
intake
sprocket
is
contacted
.
See
Fig
.
39
.
Then
slide
control
unit
off
front
of
cylinder
head
.
EMAÑ
0012514
Fig
.
39
.
On
VANOS
control
unit
withspringplate
(cars
built
3/95
and
later),
rotate
exhaust
camshaft
sprocket
clockwise
until
intake
NOTE-
camshaft
contacts
stop
.
BMW
special
tool11
5490shown
.
BMW
special
tool
no
.
113
'390
is
a
dummy
chain
ten-
sioner
and
simulates
the
function
of
thetensioner
.
VANOS
control
unit,
installing
CAUTION
-
Incorrect
installation
of
the
VANOS
control
may
result
in
damage
to
the
engine
valvetráin
.
1
.
Lock
camshafts
and
crankshaft
in
TDC
positionwith
BMW
special
tools
as
described
above
in
removal
pro-
cedure
.
CA
UTION-
The
camshafts
and
crankshaft
mustbe
locked
in
the
TDC
position
using
BMW
special
tools
no
.
11
2
300and
113
240
.
If
the
camshafts
and
crank-
shaft
are
not
at
TDC,
the
valves
can
contact
the
pistons
when
the
engine
is
turned
over
.
NOTE-
Be
sure
the
secondary
timing
chain
tensioner
is
locked
down
and
the
exhaustcamshaft
mounting
bolts
are
loosebefore
proceeding
.
2
.
Remove
primary
timing
chain
tensioner
from
side
of
cylinder
head
.
See
Fig
.
40
.
CAMSHAFT
TIMING
CHAIN
117-
1
7
Fig
.
40
.
Primary
timing
chain
tensioner
(arrow)
.
Remove
tensioner
slowlyto
relieve
spring
tension
beneath
end
plug
.
3
.
Install
BMW
special
tool
no
.
11
3
390
into
primary
tim-
ing
chain
tensionersleeve
.
Thread
tool
in
finger
tight
to
remove
chain
slack
.
4
.
Hand
turn
secondary
sprocketsclockwise
(as
viewed
from
front
of
engine)
until
sprockets
contact
stops
.
5
.
Apply
a
small
amount
of
¡¡quid
gasketsealer
(3-Bond
1209
®
or
equivalent)
to
VANOS
housing
alignment
doweis
on
front
of
cylinder
head
.
lnstall
a
new
gasket
.
6
.
Push
VANOS
piston
gear
cup
finto
VANOS
housing
until
it
bottoms
out
in
housing
.
Position
VANOS
control
unitinto
place,
but
do
not
engage
splines
on
gear
cup
.
7
.
On
cars
built
up
to
3/95
:
"
Hand
turn
exhaust
sprocketcounterclockwise
(as
viewedfrom
front
of
engine)
only
enough
to
mesh
gear
cup
splines
with
camshaft
gear
:
"
Slowly
push
VANOS
control
unit
in
untilfully
seated,
guiding
chains
in
counterclockwise
direction
.
VANOS
(VARIABLE
VALVE
TIMING)
Page 114 of 759
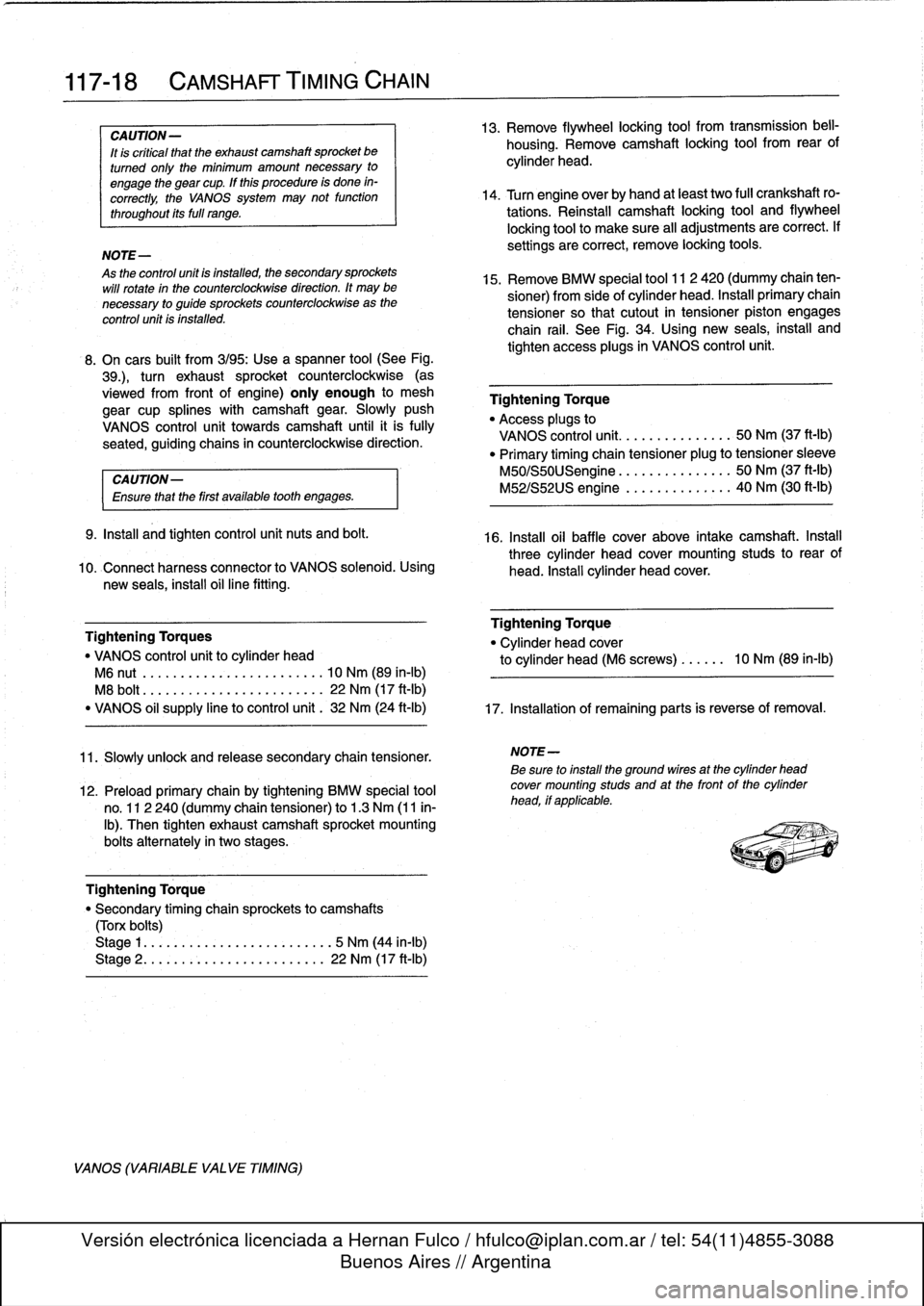
117-
1
8
CAMSHAFT
TIMING
CHAIN
CAUTION-
It
is
crítical
that
the
exhaustcamshaft
sprocket
be
turned
only
the
mínimum
amount
necessary
to
engage
the
gear
cup
.
If
this
procedure
is
done
ín-
correctly,
the
VANOS
system
may
not
function
throughout
íts
full
range
.
NOTE-
As
the
control
unit
isinstalled,
the
secondary
sprockets
will
rotate
in
the
counterclockwise
direction
.
It
may
be
necessary
to
guide
sprockets
counterclockwise
as
the
control
unit
is
installed
.
8
.
On
cars
built
from3/95
:
Use
a
spanner
tool
(See
Fig
.
39
.),
turn
exhaust
sprocket
counterclockwise
(as
víewed
from
front
of
engine)
only
enough
to
mesh
gear
cup
splines
with
camshaftgear
.
Slowly
push
VANOS
control
unit
towards
camshaft
until
it
is
fully
seated,guiding
chains
in
counterclockwise
direction
.
CA
UTION-
Ensure
that
the
first
available
tooth
engages
.
9
.
Install
and
tightencontrol
unit
nuts
and
bolt
.
10
.
Connect
harness
connector
to
VANOS
solenoid
.
Using
new
seals,
insta¡¡
oil
line
fitting
.
Tightening
Torques
"
VANOS
control
unitto
cylinder
head
M6
nut
.....
..
..
.
.
.............
10
Nm
(89
in-lb)
M8
bolt
.....
.
.
.
.
..
.............
22
Nm
(17
ft-Ib)
"
VANOS
oil
supply
line
to
control
unit
.
32
Nm
(24
ft-Ib)
11
.
Slowlyunlock
and
release
secondary
chain
tensioner
.
12
.
Preloadprimary
chain
by
tightening
BMW
special
tool
no
.
112
240
(dummy
chain
tensioner)
to
1
.3
Nm
(11
in-
lb)
.
Then
tighten
exhaust
camshaft
sprocket
mounting
bolts
alternately
in
two
stages
.
Tightening
Torque
"
Secondarytiming
chain
sprockets
to
camshafts
(Tora
boits)
Stage
1
..
...............
...
.
.
...
5
Nm
(44
in-lb)
Stage
2
..
...............
...
.
.
..
22
Nm
(17
ft-Ib)
VANOS
(VARIABLE
VALVE
TIMING)
13
.
Remove
flywheel
locking
tool
from
transmission
bell-
housing
.
Remove
camshaft
locking
tool
from
rear
of
cylinder
head
.
14
.
Turn
engine
over
by
hand
at
least
two
fui¡
crankshaft
ro-
tations
.
Reinstall
camshaft
locking
tool
and
flywheel
locking
toolto
make
sure
all
adjustments
are
correct
.
If
settings
are
correct,
remove
locking
tools
.
15
.
Remove
BMW
special
tool
112
420
(dummy
chain
ten-
sioner)
from
side
of
cylinder
head
.
Install
primary
chain
tensioner
so
that
cutout
in
tensioner
piston
engages
chain
rail
.
See
Fig
.
34
.
Using
new
seals,
install
and
tighten
access
plugs
in
VANOS
control
unit
.
Tightening
Torque
"
Access
plugs
to
VANOS
control
unit
.
..
.
.....
.
..
...
50
Nm
(37
ft-lb)
"
Primary
timing
chain
tensioner
plug
to
tensioner
sleeve
M50/S50USengine
.
.
..
.
.
...
.
...
..
50
Nm
(37
ft-Ib)
M52/S52US
engine
...
..
...
...
...
40
Nm
(30
ft-Ib)
16
.
Install
oil
baffle
cover
above
intake
camshaft
.
Install
three
cylinder
head
covermounting
studs
to
rear
of
head
.
Instali
cylinder
head
cover
.
Tightening
Torque
"
Cylinder
head
cover
to
cylinder
head
(M6
screws)
......
10
Nm
(89
in-Ib)
17
.
Installationof
remaining
parts
is
reverse
of
removal
.
NOTE-
Be
sure
to
install
the
ground
wíres
at
the
cylinder
head
cover
mounting
studs
and
at
the
front
of
the
cylinder
head,
if
applicable
.
Page 118 of 759
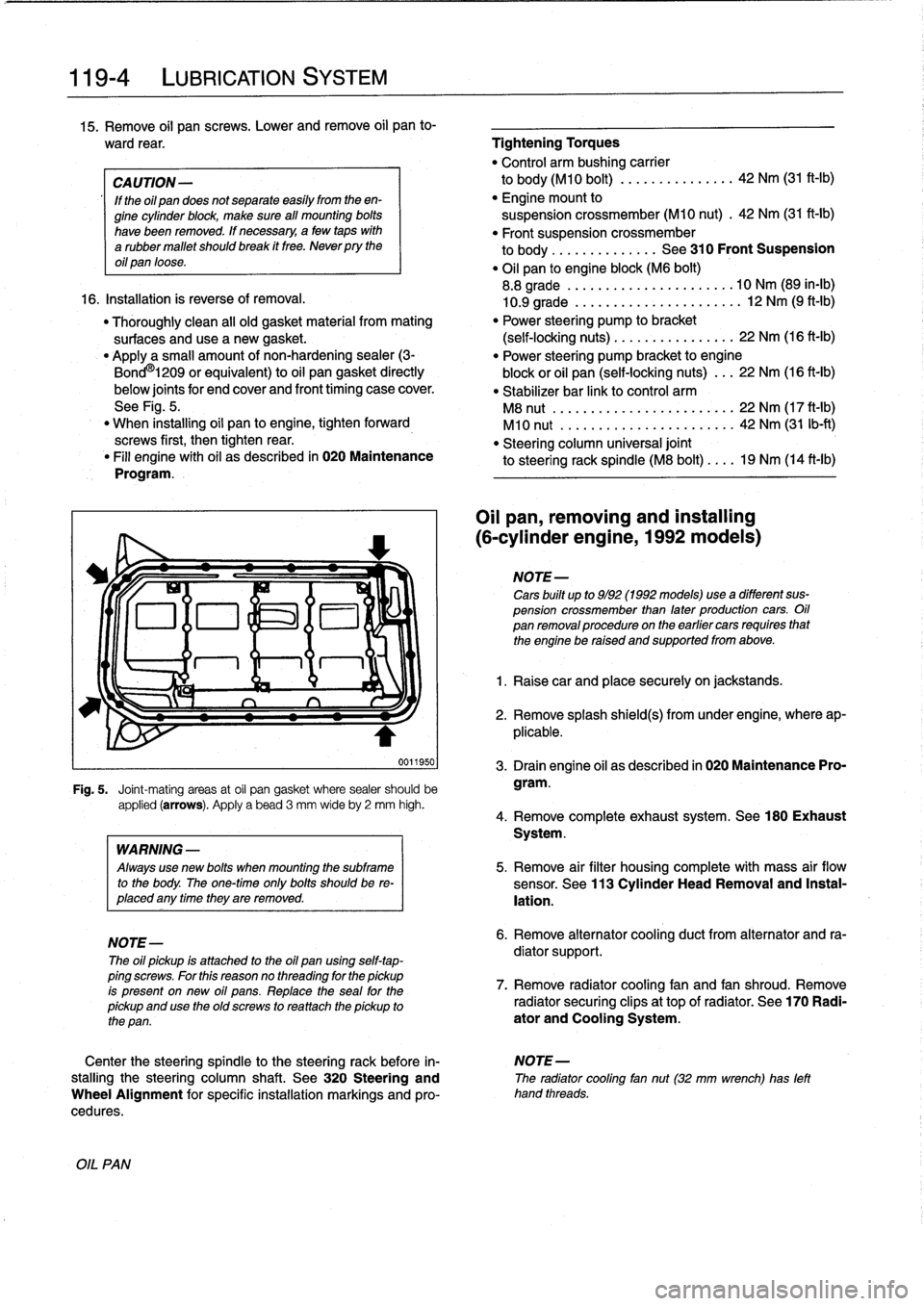
119-
4
LUBRICATION
SYSTEM
15
.
Remove
oil
pan
screws
.
Lower
andremove
oil
pan
to-
ward
rear
.
Tightening
Torques
"
Control
arm
bushing
carrier
CAUTION-
to
body(M10
bolt)
...............
42
Nm
(31
ft-Ib)
'
lf
the
oil
pan
does
not
separate
easily
from
the
en-
"
Engine
mount
to
gine
cylinder
block,
make
sure
all
mounting
bolis
suspension
crossmember
(M10
nut)
.
42
Nm
(31
ft-Ib)
have
been
removed
.
If
necessary,
a
few
tapswith
"
Front
suspension
crossmember
a
rubber
mallet
shouldbreak
it
free
.
Never
pry
the
to
body
.
.
..
...
..
.
....
See
310
Front
SusPension
oil
pan
loose
.
"
Oil
pan
to
engine
block
(M6
bolt)
8
.8
grade
..
....
.
...
...
.
........
10
Nm
(89
in-lb)
16
.
Installation
is
reverse
of
removal
.
10
.9
grade
...
..
.
....
..
.
.
.
.......
12
Nm
(9
ft-Ib)
"
Thoroughly
clean
all
old
gasket
material
from
mating
"
Power
steering
pump
to
bracket
surfaces
anduse
a
new
gasket
.
(self-locking
nuts)
....
..
.
....
..
.
..
22
Nm
(16
ft-Ib)
"
Applya
small
amount
of
non-hardening
sealer
(3-
"
Power
steering
pump
bracket
to
engine
Bond
O
l209
or
equivalent)
to
oil
pan
gasket
directly
block
or
oil
pan
(self-locking
nuts)
..
.
22
Nm
(16
ft-Ib)
below
joints
for
end
cover
and
front
timing
case
cover
.
"
Stabilizer
bar
link
to
control
arm
See
Fig
.
5
.
M8
nut
.................
...
.
...
22
Nm
(17
ft-Ib)
"
When
installing
oil
pan
to
engine,
tighten
forward
M10
nut
.....................
..
42
Nm
(31
Ib-ft)
screws
first,
then
tightenrear
.
"
Steering
column
universal
joint
"
Fill
engine
with
oil
as
described
in
020
Maintenance
to
steering
rack
spindle
(M8
bolt)
....
19
Nm
(14
ft-ib)
Program
.
0011950
Fig
.
5
.
Joint-mating
areas
at
oil
pan
gasket
where
sealer
should
be
applied
(arrows)
.
Apply
a
bead
3
mm
wideby
2
mm
high
.
OIL
PAN
WARNING
-
Always
use
new
bolis
when
mounting
the
subframe
to
the
body
.
The
one-timeonly
bolis
shouldbe
re-
placed
any
timethey
are
removed
.
NOTE-
The
oil
pickup
is
attached
to
the
oil
pan
using
self-tap-
ping
screws
.
For
this
reasonno
threading
for
the
pickup
is
present
on
new
oil
pans
.
Replace
the
seal
for
the
pickup
and
use
the
oíd
screws
to
rea
ttach
the
pickup
to
the
pan
.
Oil
pan,
removing
and
installing
(6-cylinder
engine,
1992models)
NOTE-
Cars
built
up
to
9/92
(1992models)usea
different
sus-
pension
crossmember
than
later
production
cars
.
Oil
pan
removalprocedureon
the
earlier
cars
requires
that
the
engine
be
raised
and
supportedfrom
above
.
1
.
Raise
car
and
place
securely
on
jackstands
.
2
.
Remove
splash
shield(s)
from
under
engine,
where
ap-
plicable
.
3
.
Drain
engine
oil
as
described
in
020
Maintenance
Pro-
gram
.
4
.
Remove
complete
exhaust
system
.
See180
Exhaust
System
.
5
.
Remove
air
filter
housing
complete
with
mass
air
flow
sensor
.
See
113
Cylinder
Head
Removal
and
Instal-
lation
.
6
.
Remove
alternator
cooling
duct
from
alternator
and
ra-
diator
support
.
7
.
Remove
radiator
cooling
fan
and
fan
shroud
.
Remove
radiator
securing
clips
at
top
of
radiator
.
See
170
Radi-
ator
and
Cooling
System
.
Center
the
steering
spindle
to
the
steering
rack
before
in-
NOTE-
stalling
the
steering
column
shaft
.
See
320
Steering
and
The
radiator
cooling
fan
nut(32
mm
wrench)
has
left
Wheel
Alignment
for
specific
installation
markings
and
pro-
hand
threads
.
cedures
.
Page 122 of 759
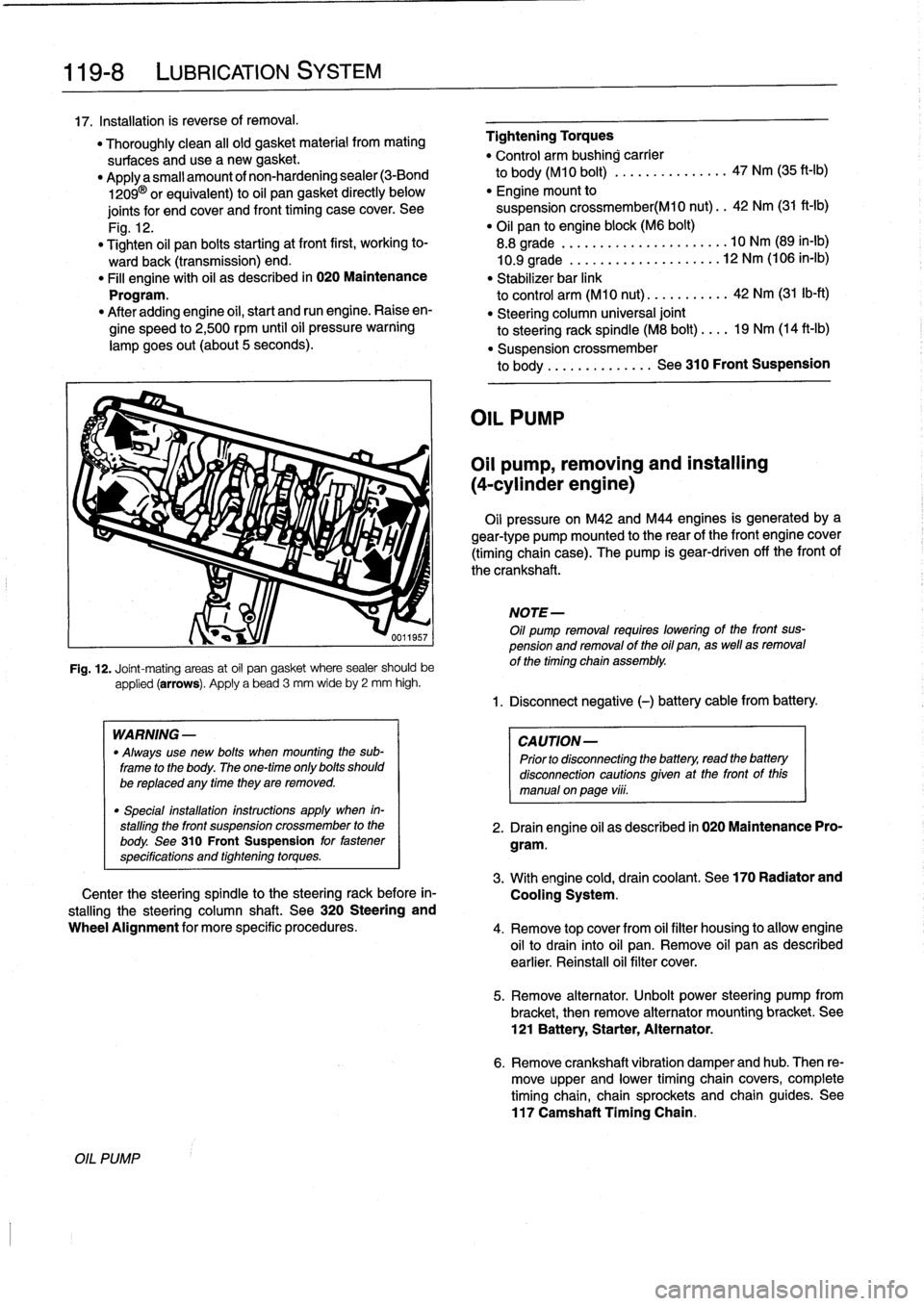
119-
8
LUBRICATION
SYSTEM
17
.
Installation
is
reverse
of
removal
.
"
Thoroughly
clean
all
old
gasket
material
from
mating
surtaces
anduse
a
new
gasket
.
"
Applya
small
amount
of
non-hardening
sealer
(3-Bond
1209
0
or
equivalent)
to
oil
pan
gasket
directly
below
joints
for
and
cover
and
front
timing
case
cover
.
See
Fig
.
12
.
"
Tighten
oil
pan
bolts
starting
at
front
first,
working
to-
wardback
(transmission)
end
.
"
Fill
engine
with
oil
as
described
in
020
Maintenance
Program
.
"
After
addingengine
oil,
start
and
run
engine
.
Raiseen-
gine
speed
to
2,500
rpm
until
oíl
pressure
warning
lampgoes
out
(about
5seconds)
.
OIL
PUMP
applied
(arrows)
.
Apply
a
bead
3
mm
wideby
2
mm
high
.
WARNING
-
"
Always
use
new
bolts
when
mounting
the
sub-
frame
to
the
body
.
The
one-time
only
bolts
should
be
replaced
any
timethey
are
removed
.
"
Special
installation
instructions
apply
when
in-
stalling
the
front
suspension
crossmember
to
the
body
.
See
310
Front
Suspension
for
fastener
specifications
and
tightening
torques
.
Fig
.
12
.
Joint-mating
areas
at
oil
pan
gasket
where
sealer
should
be
Center
the
steering
spindle
to
the
steering
rack
before
in-
stalling
the
steering
column
shaft
.
See
320
Steering
and
Wheel
Alignment
for
more
specific
procedures
.
Tightening
Torques
"
Control
arm
bushing
carrier
to
body
(M10
bolt)
...............
47
Nm
(35
ft-Ib)
"
Engine
mount
to
suspension
crossmember(M10
nut)
..
42
Nm
(31
ft-Ib)
"
Oil
pan
to
engine
block
(M6
bolt)
8
.8
grade
...........
.......
....
10
Nm
(89
in-lb)
10
.9
grade
...........
..
...
...
.
12
Nm
(106
in-lb)
"
Stabilizer
bar
link
to
control
arm
(M10
nut)
.......
....
42
Nm
(31
Ib-ft)
"
Steering
column
universal
joint
to
steering
rack
spindle
(M8
bolt)
....
19
Nm
(14
ft-Ib)
"
Suspensíon
crossmember
to
body
...
...
.
...
..
.
.
See
310
Front
Suspension
OIL
PUMP
Oil
pump,
removing
and
installing
(4-cylinder
engine)
Oil
pressure
on
M42
and
M44
engines
is
generatedbya
gear-type
pump
mounted
to
the
rear
of
the
front
engine
cover
(timing
chaincase)
.
The
pump
is
gear-driven
off
the
front
of
the
crankshaft
.
NOTE-
Oil
pump
removal
requires
lowering
of
the
front
sus-
pension
and
removal
of
the
oil
pan,
as
well
asremoval
of
the
timing
chain
assembly
.
1
.
Disconnect
negative
(-)
battery
cable
from
battery
.
CAUTION-
Prior
to
disconnectiog
the
battery,
read
the
battery
disconnection
cautions
given
at
the
front
of
this
manual
on
paga
vÍii
.
2
.
Drain
engine
oil
as
described
in
020
Maintenance
Pro-
gram
.
3
.
Withengine
cold,
drain
coolant
.
See
170
Radiator
and
Cooling
System
.
4
.
Remove
top
cover
from
oil
filter
housing
to
allow
engine
oil
to
drain
into
oil
pan
.
Remove
oil
pan
as
described
earlier
.
Reinstall
oil
filter
cover
.
5
.
Remove
alternator
.
Unbolt
power
steering
pump
from
bracket,
then
remove
alternator
mountíng
bracket
.
See
121
Battery,
Starter,
Alternator
.
6
.
Remove
crankshaft
vibration
damper
andhub
.
Then
re-
move
upper
and
lower
timing
chain
covers,
complete
timingchain,
chain
sprockets
and
chain
guides
.
See
117
Camshaft
Tíming
Chain
.
Page 123 of 759
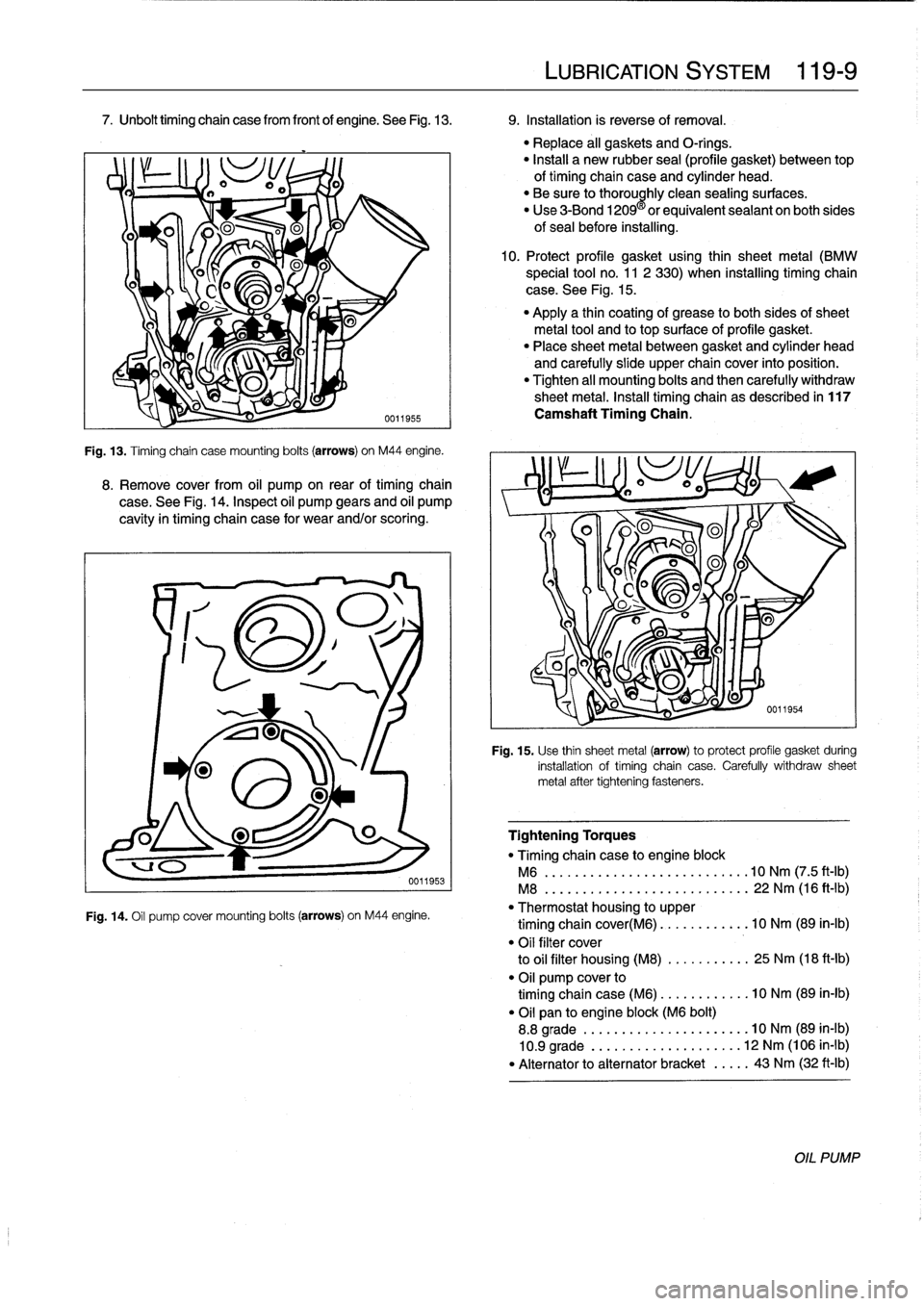
7
.
Unbolt
timing
chain
casefrom
frontof
engine
.
See
Fig
.
13
.
9
.
Installation
is
reverse
of
removal
.
Fig
.
13
.
Timing
chain
case
mounting
bolts
(arrows)
on
M44
engine
.
8
.
Remove
cover
from
oil
pump
on
rear
of
timing
chain
case
.
See
Fig
.
14
.
Inspect
oil
pump
gears
and
oil
pump
cavity
in
timing
chain
case
for
wear
andlor
scoring
.
Fig
.
14
.
Oil
pump
cover
mounting
bolts
(arrows)
on
M44
engine
.
LUBRICATION
SYSTEM
119-
9
"
Replace
al¡
gaskets
and
O-rings
.
"
Install
a
new
rubber
sea¡
(profile
gasket)
between
top
of
timing
chain
case
and
cylinder
head
.
"
Be
sure
to
thoroughly
clean
sealing
surfaces
.
-Use
3-Bond
1209
orequivalent
sealant
on
both
sides
of
sea¡
before
installing
.
10
.
Protect
profile
gasket
using
thin
sheet
metal
(BMW
special
tool
no
.
11
2
330)
when
installing
timing
chain
case
.
See
Fig
.
15
.
"
Applya
thin
coating
of
grease
to
both
sides
of
sheet
metal
tool
and
to
top
surface
of
profile
gasket
.
"
Placesheet
metal
between
gasket
and
cylinder
head
and
carefully
slíde
upper
chain
cover
into
position
.
"
Tighten
al¡
mounting
bolts
and
then
carefully
withdraw
sheet
metal
.
Install
timing
chain
as
described
in
117
Camshaft
Timing
Chain
.
Fig
.
15
.
Use
thin
sheetmetal
(arrow)
toprotect
profile
gasket
during
installation
of
timing
chain
case
.
Carefully
withdraw
sheetmetal
after
tightening
fasteners
.
Tightening
Torques
"
Timing
chain
case
to
engine
block
M6
..
.
...
...
.
..
.............
.
.10
Nm
(7
.5
ft-Ib)
M8
........
.
..
..
..............
22
Nm
(16
ft-Ib)
"
Thermostathousing
to
upper
timing
chain
cover(M6)
............
10
Nm
(89
in-lb)
"
OH
filter
cover
to
oil
filter
housing
(M8)
.
.
.........
25
Nm
(18
ft-lb)
"
Oil
pump
cover
to
timing
chain
case
(M6)
...
..
.......
10
Nm
(89
in-lb)
"
Oil
pan
to
engine
block
(M6
bolt)
8
.8
grade
.........
.
.
..
.........
10
Nm
(89
in-lb)
10
.9
grade
............
.
.......
12
Nm
(106
in-lb)
"
Alternator
to
alternator
bracket
.....
43
Nm
(32
ft-Ib)
OIL
PUMP
Page 125 of 759
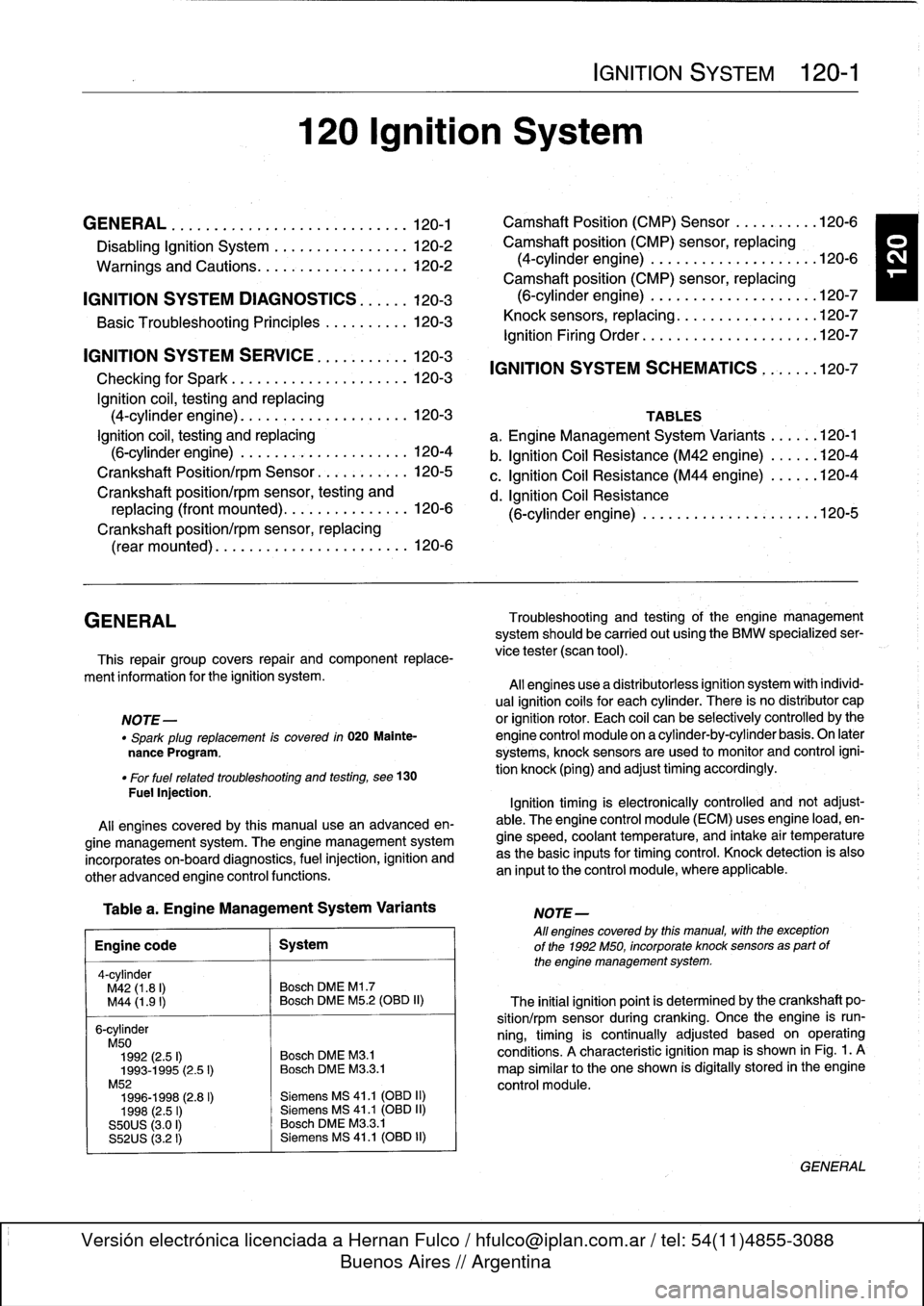
GENERAL
.
........
.
...........
.
.
.
.
.
.
.
120-1
Camshaft
Position
(CMP)
Sensor
....
.
.
.
...
120-6
Disabling
Ignition
System
.
.
.
.
.....
.
.
.
.
.
.
.
120-2
Camshaft
position
(CMP)
sensor,
replacing
Warnings
and
Cautions
.
.
.
.
.
.
.....
.
.
.
.
.
.
.
120-2
(4-cylinder
engine)
..
.
.
.
.
.
.
.
.
.
.
.
.
.
.
.
...
120-6
Camshaft
position
(CMP)
sensor,
replacing
IGNITION
SYSTEM
DIAGNOSTICS
.
.
.
.
.
.
120-3
(6-cylinder
engine)
..
.
.
.
.
.
.
.
.
.
.
.
.
.
.
.
.
.
.
120-7
Basic
Troubleshooting
Principles
...
.
.
.
.
.
.
.
120-3
Knock
sensors,
replacing
.
.
...
.
.
.
.
.
.
.
.
.
.
.
.
120-7
Ignition
Firing
Order
.....
.
...
.
.
.
.....
.
.
.
.120-7
IGNITION
SYSTEM
SERVICE
.
.........
.
120-3
Checking
for
Spark
..
.
.
.
.
.
.
.
.
.
.......
.
.
.
120-3
Ignition
coil,
testing
and
replacing
(4-cylinder
engine)
.
.
.
.
.
.
.
.
.
.
.........
.
120-3
Ignition
coil,
testing
and
replacing
(6-cylinder
engine)
.........
.
..........
120-4
Crankshaft
Positionlrpm
Sensor
.......
.
...
120-5
Crankshaft
position/rpm
sensor,
testing
and
replacing
(front
mounted)
.........
.
.
.
.
.
.
120-6
Crankshaft
position/rpm
sensor,replacing
(rear
mounted)
.....
.
.....
.
.....
.
.
.
.
.
.
120-6
GENERAL
Troubleshooting
and
testing
of
the
engine
management
system
should
be
carried
out
using
the
BMW
specialized
ser
This
repair
group
covers
repair
andcomponent
replace-
vice
tester
(scan
tool)
.
ment
information
for
the
ignition
system
.
All
engines
use
a
distributorless
ignition
system
with
indívid-
ual
ignitioncoils
for
each
cylinder
.
There
is
no
distributor
cap
NOTE-
or
ignition
rotor
.
Each
coil
can
be
selectively
controlled
by
the
"
Spark
plug
replacement
is
covered
in
020
Mainte-
engine
control
module
on
a
cylinder-by-cylinder
basis
.
On
later
nance
Program
.
systems,
knock
sensors
are
used
to
monitor
and
control
igni-
"
For
fuel
related
troubleshooting
and
testing,
see
130
tion
knock
(ping)
and
adjusttiming
accordingly
.
Fuel
lnjection
.
Ignition
timing
is
electronically
controlled
and
not
adjust-
All
engines
covered
by
this
manual
use
an
advanced
en-
able
.
The
engine
control
module
(ECM)
usesengine
load,
en-
gine
management
system
.
The
engine
management
system
gine
speed,
coolant
temperature,
and
intake
air
temperature
incorporates
on-board
diagnostics,
fuel
injection,
ignition
and
as
the
basic
inputs
for
timing
control
.
Knock
detection
is
also
other
advanced
engine
control
functions
.
an
input
to
the
control
module,
where
applicable
.
Table
a
.
Engine
Management
System
Variants
Engine
code
1
System
4-cylinder
M42
(1.8
I)
Bosch
DME
Ml
.7
M44
(1
.9
I)
Bosch
DME
M5
.2
(OBD
II)
6-cylinder
M50
1992
(2.5
I)
Bosch
DME
M8
.1
1993-1995
(2
.5
I)
Bosch
DME
M33
.1
M52
1996-1998
(2.8
I)
Siemens
MS
41
.1
(OBD
II)
1998
(2
.5
I)
Siemens
MS
41
.1
(013D
11)
S50US
(3.0
I)
Bosch
DME
M3
.3.1
S52US
(3.2
I)
Siemens
MS
41
.1
(OBD
II)
120
Ignition
System
IGNITION
SYSTEM
120-1
IGNITION
SYSTEM
SCHEMATICS
...
.
.
.
.120-7
TABLES
a
.
Engine
Management
System
Variants
......
120-1
b
.
Ignition
Coil
Resistance
(M42
engine)
......
120-4
c
.
Ignition
Coil
Resistance
(M44
engine)
......
120-4
d
.
Ignition
Coil
Resistance
(6-cylinder
engine)
..
.
.
.
.
.
.
.
.
.
.
.
.....
.
..
120-5
NOTE-
All
engines
coveredby
this
manual,
with
theexception
of
the
1992
M50,
incorporate
knocksensors
as
part
of
the
engine
management
system
.
The
initial
ignition
point
is
determined
by
the
crankshaft
po-
sition/rpm
sensor
during
cranking
.
Once
the
engine
is
run-
ning,
timing
is
continually
adjusted
based
on
operating
conditions
.
A
characteristic
ignition
map
is
shown
in
Fig
.
1
.
A
map
similar
to
the
one
shown
is
digitally
stored
in
the
engine
control
module
.
GENERAL
Page 130 of 759
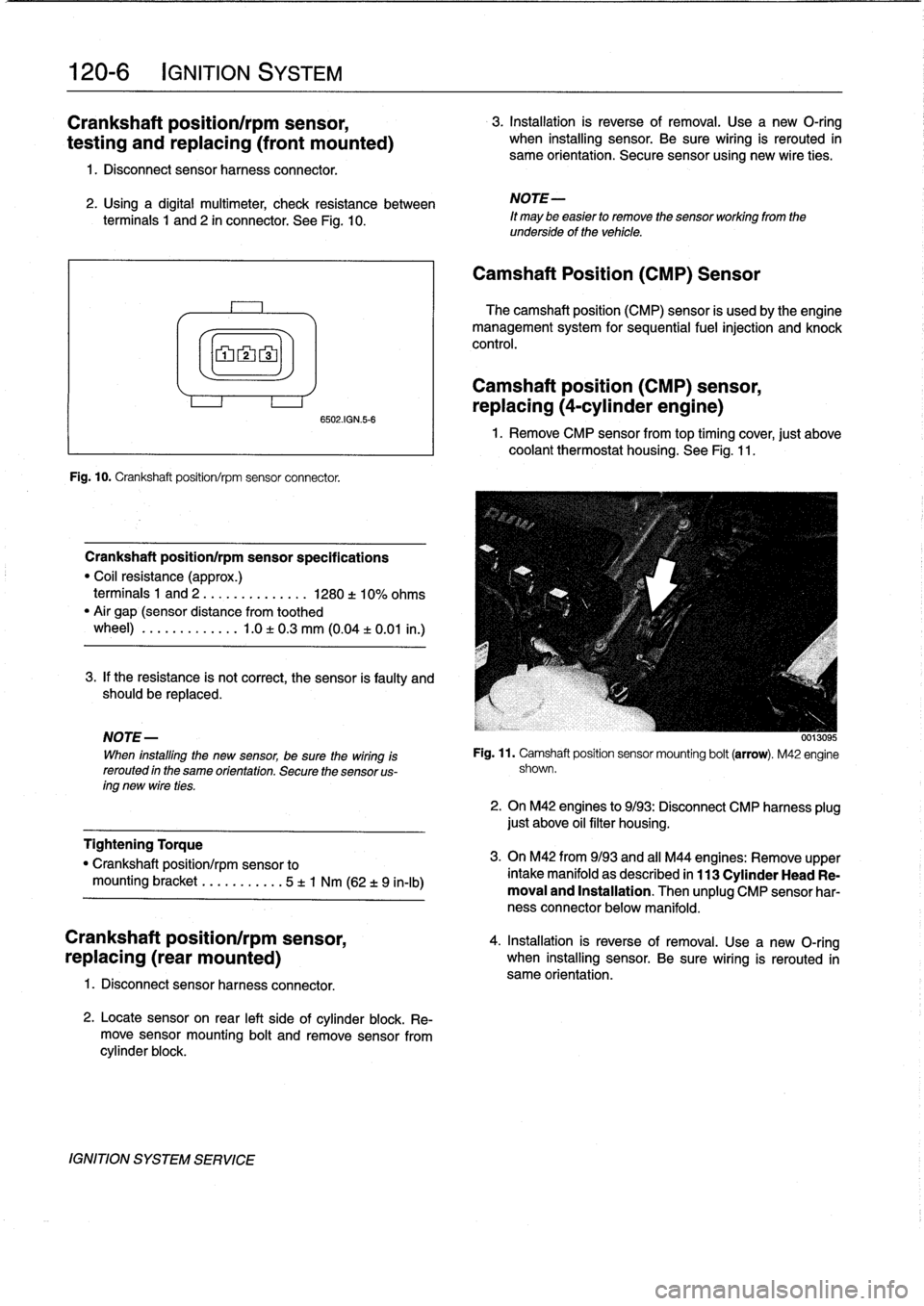
120-
6
IGNITION
SYSTEM
Crankshaft
position/rpm
sensor,
testing
and
replacing
(front
mounted)
1
.
Disconnect
sensor
harness
connector
.
2
.
Using
a
digital
multimeter,
check
resistance
between
terminals
1
and
2
in
connector
.
See
Fig
.
10
.
n1
n2n3
Fig
.
10
.
Crankshaft
position/rpm
sensorconnector
.
Crankshaft
positionlrpm
sensor
specifications
"
Coil
resistance
(approx
.)
terminais
1
and
2
....
.
..
...
....
1280
±
10%
ohms
"
Air
gap
(sensor
distance
from
toothed
wheel)
..
.
.
........
.1
.0
±
0
.3
mm
(0
.04
±
0
.01
in
.)
3
.
If
the
resistance
is
not
correct,
the
sensor
is
faulty
and
should
be
replaced
.
NOTE
-
When
installing
the
new
sensor,
be
sure
thewiring
Is
rerouted
in
the
same
orientation
.
Secure
the
sensor
us-
ing
new
wire
ties
.
Tightening
Torque
"
Crankshaft
position/rpm
sensor
to
mounting
bracket
.........
.
.
5
t
1
Nm
(62
t
9
in-lb)
Crankshaft
position/rpm
sensor,
4
.
Installation
is
reverse
of
removal
.
Use
a
new
O-ring
replacing
(rear
mounted)
when
installing
sensor
.
Be
sure
wiring
is
rerouted
in
same
orientation
.
1
.
Disconnect
sensor
harness
connector
.
6502AGN56
2
.
Locatesensor
on
rear
left
sideof
cylinder
block
.
Re-
move
sensormounting
bolt
and
remove
sensorfrom
cylinder
block
.
IGNITION
SYSTEM
SERVICE
3
.
Installation
is
reverse
of
removal
.
Use
a
new
O-ring
when
installing
sensor
.
Be
sure
wiring
is
rerouted
in
same
orientation
.
Secure
sensor
using
new
wire
ties
.
NOTE-
It
may
be
easier
to
remove
the
sensor
working
from
the
underside
of
the
vehicle
.
Camshaft
Position
(CMP)
Sensor
The
camshaft
position
(CMP)
sensor
is
usedby
the
engine
management
system
for
sequential
fuel
injection
and
knock
control
.
Camshaft
position
(CMP)
sensor,
replacing
(4-cylinder
engine)
1
.
Remove
CMP
sensorfromtop
timing
cover,
just
above
coolantthermostat
housing
.
See
Fig
.
11
.
Fig
.
11
.
Camshaft
position
sensor
mounting
bolt
(arrow)
.
M42
engine
shown
.
2
.
On
M42
engines
to
9/93
:
Disconnect
CMP
harness
plug
just
above
oil
filter
housing
.
3
.
On
M42
from9/93
and
all
M44
engines
:
Remove
upper
intake
manifold
as
described
in
113
Cylinder
Head
Re-
moval
and
Installation
.
Then
unplug
CMP
sensor
har-
ness
connector
below
manifold
.