Timing BMW M3 1998 E36 Repair Manual
[x] Cancel search | Manufacturer: BMW, Model Year: 1998, Model line: M3, Model: BMW M3 1998 E36Pages: 759
Page 131 of 759
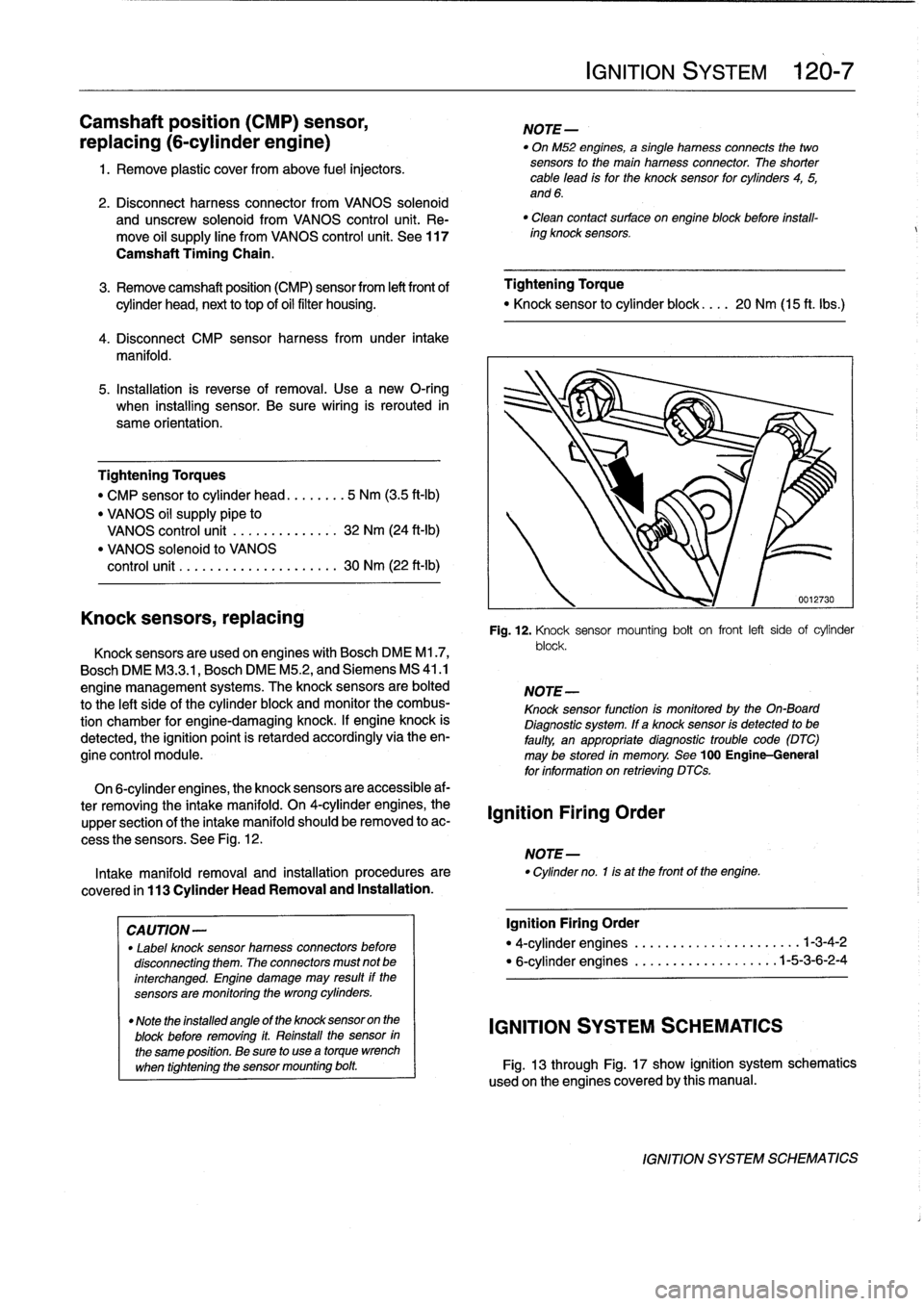
Camshaft
position
(CMP)
sensor,
replacing
(6-cylinder
engine)
1
.
Remove
plastic
cover
from
above
fuel
injectors
.
2
.
Disconnect
harness
connector
from
VANOS
solenoid
and
unscrew
solenoid
from
VANOS
control
unit
.
Re-
"
Clean
contactsurface
on
engine
block
before
fnstall
move
oil
supply
line
from
VANOS
control
unit
.
See
117
ing
knock
sensors
.
Camshaft
Timing
Chain
.
3
.
Remove
camshaft
position
(CMP)
sensor
from
left
frontof
cylinder
head,
next
to
top
of
oil
filter
housing
.
"
Knock
sensor
to
cylinder
block
....
20
Nm
(15
ft
.
lbs
.)
4
.
Disconnect
CMP
sensor
harnessfrom
under
intake
manifold
.
5
.
Installation
is
reverse
of
removal
.
Use
a
new
O-ring
when
installing
sensor
.
Be
sure
wiring
is
rerouted
in
same
orientation
.
Tightening
Torques
"
CMP
sensor
to
cylinder
head
....
.
.
..
5
Nm
(3
.5
ft-Ib)
"
VANOS
oil
supply
pipe
to
VANOS
control
unit
...........
.
..
32
Nm
(24
ft-Ib)
"
VANOS
solenoid
to
VANOS
control
unit
...
.
.................
30
Nm
(22
ft-Ib)
Knock
sensors,
replacing
Knock
sensors
are
usedon
engines
with
Bosch
DME
M1
.7,
Bosch
DME
M3
.3
.1,
Bosch
DME
M5
.2,
and
Siemens
MS
41
.1
engine
management
systems
.
The
knocksensors
are
bolted
to
the
left
sideof
the
cylinder
block
and
monitor
the
combus-
tion
chamber
for
engine-damaging
knock
.
If
engine
knock
is
detected,
the
ignition
point
is
retarded
accordingly
via
the
en-
gine
control
module
.
CA
UTION-
"
Label
knock
sensorharness
connectors
before
disconnecting
them
.
The
connectors
must
not
be
interchanged
.
Engine
damage
may
result
if
the
sensors
are
monitoring
the
wrong
cytinders
.
"
Note
the
installed
angle
of
the
knock
sensoron
the
block
before
removing
it
.
Reinstall
the
sensor
in
the
same
position
.
Be
sure
to
usea
torque
wrench
when
tightening
the
sensormounting
bola
NOTE
-
"
On
M52
engines,
a
single
harness
connects
the
twosensors
to
the
main
harness
connector
.
The
shorter
cable
lead
fs
for
the
knock
sensor
for
cytinders
4,
5,
and
6
.
Tightening
Torque
IGNITION
SYSTEM
120-
7
0012730
Fig
.
12
.
Knock
sensor
mounting
bolt
on
front
left
side
of
cylinder
block
.
NOTE-
Knock
sensor
function
Is
monitoredby
the
On-Board
Diagnostic
system
.
If
a
knock
sensor
is
detected
to
be
faulty,
an
appropriatediagnostic
trouble
code
(DTC)
may
be
stored
in
memory
.
See
100
Engine-General
for
information
on
retrieving
DTCs
.
On
6-cylinder
engines,
the
knock
sensors
are
accessible
af-
ter
removing
the
intake
manifold
.
On
4-cylinder
engines,
the
upper
section
of
the
intake
manifold
should
be
removed
to
ac-
cess
the
sensors
.
See
Fig
.
12
.
NOTE-
Intakemanifold
removal
and
installation
procedures
are
"
Cylinder
no
.
1is
at
the
front
of
the
engine
.
covered
in
113
Cylinder
HeadRemoval
and
Installation
.
Ignition
Firing
Order
Ignition
Firing
Order
"
4-cylinder
engines
.....
..
...
.
..........
.1-3-4-2
"
6-cylinder
engines
...........
..
.
.
..
..
1-5-3-6-2-4
IGNITION
SYSTEM
SCHEMATICS
Fig
.
13
through
Fig
.
17
show
ignition
system
schematics
usedon
the
enginescoveredby
this
manual
.
IGNITION
SYSTEM
SCHEMATICS
Page 148 of 759
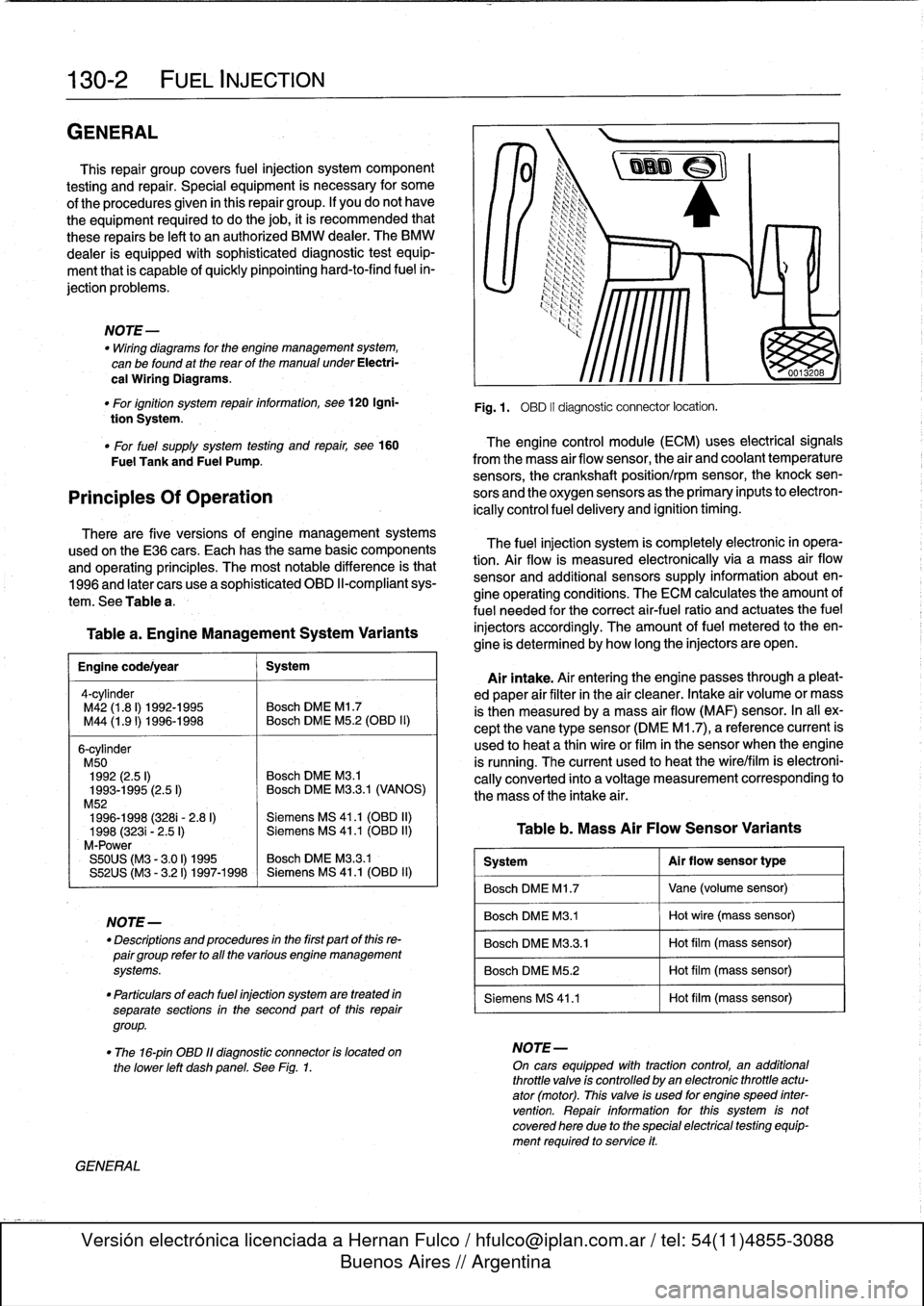
130-2
FUEL
INJECTION
GENERAL
This
repair
group
covers
fuel
injection
system
component
testing
and
repair
.
Special
equipment
is
necessary
for
some
of
the
procedures
given
in
this
repair
group
.
If
you
do
not
have
the
equipment
required
to
do
the
job,
it
is
recommended
that
these
repairs
be
left
to
an
authorized
BMW
dealer
.
The
BMW
dealer
is
equipped
with
sophisticated
diagnostic
test
equip-
ment
that
is
capable
of
quicklypinpointing
hard-to-find
fuel
in-
jection
problems
.
NOTE-
"
Wiring
diagrams
for
the
engine
management
system,
can
be
found
at
the
rear
of
the
manual
under
Electri-
cal
Wiring
Diagrams
.
"
For
ignition
system
repairinformation,
see120
Igni-
tion
System
.
"
For
fuel
supply
system
testing
and
repair,
see160
The
engine
control
module
(ECM)
uses
electrical
signals
Fuel
Tank
and
Fuel
Pump
.
from
the
mass
air
flow
sensor,
the
air
and
coolant
temperature
sensors,
the
crankshaft
position/rpm
sensor,
the
knock
sen
Principies
Of
Operation
sors
and
the
oxygen
sensorsas
the
primary
inputs
to
electron-
ically
control
fuel
delivery
and
ignition
timing
.
There
are
five
versions
of
engine
management
systems
usedon
the
E36
cars
.
Each
has
the
same
basic
components
and
operating
principles
.
The
most
notable
difference
is
that
1996
and
later
cars
use
a
sophisticated
OBD
II-compliant
sys-
tem
.
See
Table
a
.
Table
a
.
Engine
Management
System
Variants
Engine
code/year
1
System
4-cy1inder
M42
(1
.8
I)
1992-1995
Bosch
DME
Ml
.7
M44
(1
.91)
1996-1998
~
Bosch
DME
M5
.2
(OBD
II)
6-cylinder
M50
1992
(2.5
I)
Bosch
DME
M3
.1
1993-1995
(2.5
I)
Bosch
DME
M3
.3.1
(VANOS)
M52
1996-1998
(3281-
2
.8
I)
Siemens
MS
41
.1
(OBD
II)
1998
(3231
-
2
.5
I)
Siemens
MS
41
.1
(OBD
II)
M-Power
S50US
(M3
-
3
.01)
1995
Bosch
DME
M3
.3
.1
S52US
(M3
-
3
.21)
1997-1998
Siemens
MS
41
.1
(0131)
11)
NOTE-
-
Descriptions
and
procedures
in
the
first
partof
this
re-
pairgroup
refer
to
all
the
various
engine
management
systems
.
"
Particulars
of
each
fuel
injection
system
are
treated
in
separate
sections
in
the
second
part
of
this
repair
group
.
GENERAL
Fig
.1
.
OBD
II
diagnostic
connector
locatíon
.
The
fuel
injection
system
is
completely
electronic
in
opera-
tion
.
Air
flow
is
measured
electronically
via
a
mass
air
flow
sensor
and
additional
sensors
supply
information
about
en-
gine
operating
conditions
.
The
ECM
calculates
the
amount
of
fuel
needed
for
the
correct
air-fuel
ratio
and
actuates
the
fuel
injectors
accordingly
.
The
amount
offuel
metered
to
theen-
gine
is
determined
by
how
long
the
injectors
are
open
.
Airintake
.
Air
entering
the
engine
passes
through
a
pleat-
ed
paper
air
filter
in
the
air
cleaner
.
Intake
air
volume
or
mass
is
then
measured
bya
mass
air
flow
(MAF)
sensor
.
In
al¡
ex-
cept
the
vane
type
sensor
(DME
M1
.7),
a
reference
current
is
used
to
heat
a
thin
wireor
film
in
the
sensor
when
the
engine
is
running
.
The
current
used
to
heat
the
wire/film
is
electroni-
cally
converted
into
a
voltage
measurement
corresponding
to
the
mass
of
the
intake
air
.
Table
b
.
Mass
Air
Flow
Sensor
Variants
System
Al
r
flow
sensor
type
Bosch
DME
M1
.7
Vane
(volume
sensor)
Bosch
DME
M3
.1
Hot
wire
(mass
sensor)
Bosch
DME
M3
.3
.1
Hot
film
(mass
sensor)
Bosch
DME
M5
.2
Hot
film
(mass
sensor)
Siemens
MS
41
.1
Hot
film
(mass
sensor)
"
The
16-pin
OBD
11
diagnostic
connector
is
located
on
NOTE-
the
lower
left
dashpanel
.
See
Fig
.
1
.
On
cars
equipped
wíth
tractioncontrol,
an
additional
throttle
valve
is
controlled
by
an
electronic
throttle
actu-
ator
(motor)
.
This
valve
is
used
for
engine
speed
inter
vention
.
Repair
information
forthis
system
is
notcovered
here
due
to
the
special
electrical
testing
equip-
ment
required
to
service
it
.
Page 149 of 759
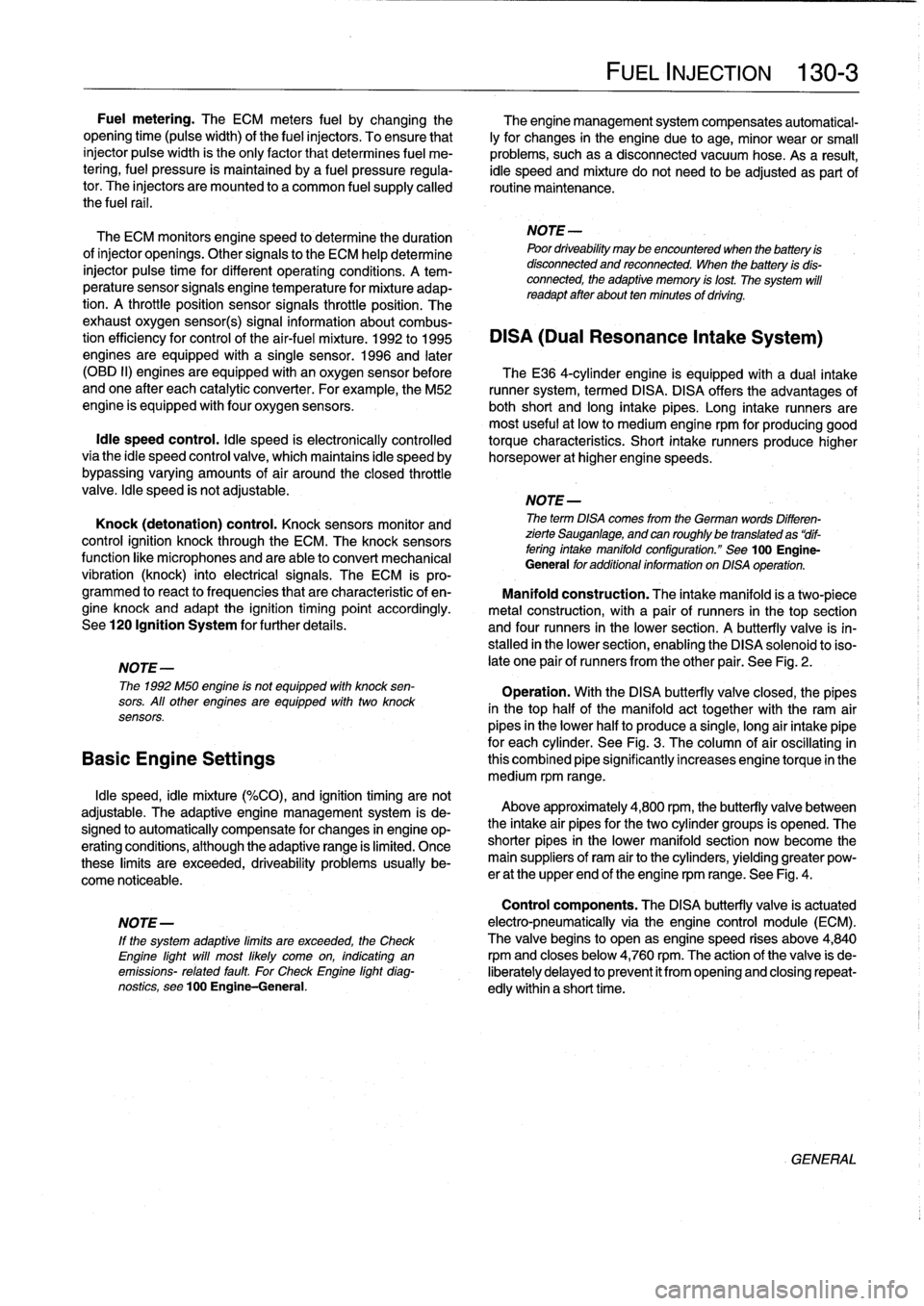
FUEL
INJECTION
130-
3
Fuel
metering
.
The
ECM
meters
fuel
bychanging
the
The
engine
management
system
compensates
automatical-
opening
time
(pulsewidth)
of
the
fuel
injectors
.
To
ensure
that
ly
for
changes
in
the
engine
due
to
age,
minor
wear
or
small
injector
pulsewídth
is
the
only
factor
that
determines
fuel
me-
problems,
such
as
a
disconnected
vacuum
hose
.
Asa
result,
tering,fuel
pressure
is
maintained
bya
fuel
pressure
regula-
idle
speed
and
mixture
do
not
need
lo
be
adjustedas
partof
tor
.
The
injectors
are
mounted
lo
a
common
fuel
supply
called
routine
maintenance
.
the
fuel
rail
.
The
ECM
monitors
engine
speed
to
determine
the
duration
NOTE-
ofinjector
openings
.
Other
signals
to
the
ECM
help
determine
Poordriveabilitymaybe
encountered
when
the
batteryis
injector
pulse
time
for
different
operating
conditions
.
A
tem-
disconnected
and
reconnected
.
when
the
battery
is
dis-
connected,
the
adaptive
memory
is
lost
The
system
will
perature
sensor
signals
engine
temperature
for
mixture
adap-
readaptafterabout
ten
minutes
of
drfving
.
tion
.
A
throttle
position
sensor
signals
throttle
position
.
The
exhaust
oxygen
sensor(s)
signal
information
about
combus-
tion
efficiency
for
control
of
the
air-fuel
mixture
.
1992
to
1995
DISA
(Dual
Resonance
Intake
System)
engines
are
equipped
with
a
single
sensor
.
1996
and
later
(OBD
II)
engines
are
equipped
with
an
oxygen
sensor
before
TheE36
4-cylinder
engine
is
equipped
with
a
dual
intake
andone
after
each
catalytic
converter
.
Forexample,the
M52
runner
system,
termed
DISA
.
DISA
offers
the
advantages
of
engine
is
equipped
withfour
oxygen
sensors
.
both
short
and
long
intake
pipes
.
Long
intake
runners
are
most
useful
at
low
to
medium
engine
rpm
for
producing
good
Idle
speed
control
.
ldle
speed
is
electronically
controlled
torque
characteristics
.
Short
intake
runners
produce
hígherviathe
idle
speed
control
valve,
which
maintains
idle
speed
by
horsepower
at
hígher
engine
speeds
.
bypassing
varying
amounts
of
air
around
theclosed
throttle
valve
.
Idle
speed
is
not
adjustable
.
NOTE-
Knock
(detonation)
control
.
Knock
sensors
monitor
and
The
term
DISA
comes
from
the
German
words
Differen-
control
ignition
knock
through
the
ECM
.
The
knock
sensors
zierte
Sauganlage,
and
can
roughlybe
translated
as
"dif-
fering
intake
manifold
configuration
."
See
100
Engine-
function
like
microphones
and
are
able
to
convert
mechanical
General
foradditional
information
on
DISA
operation
.
vibration
(knock)
into
electrical
signals
.
The
ECM
is
pro-
grammed
to
react
to
frequencies
that
are
characteristic
of
en-
Manifold
construction
:
The
intake
manifold
is
a
two-piece
gine
knock
and
adapt
the
ignition
timing
point
accordingly
.
metal
construction,
with
a
pair
of
runners
in
thetop
section
See120
Ignition
System
for
further
details
.
and
four
runners
in
the
lower
section
.
A
butterfly
valve
is
in-
stalled
in
the
lower
section,
enabling
the
DISA
solenoid
toiso-
NOTE-
late
one
pair
of
runners
from
the
other
pair
.
See
Fig
.
2
.
The
1992
M50
engine
is
not
equipped
with
knock
sen-
Operation
.
With
the
DISA
butterfly
valve
closed,
the
pipes
sors
.
All
other
engines
are
equipped
with
two
knock
in
thetop
half
of
the
manifold
act
together
with
the
ram
air
sensors
.
pipes
in
the
lower
halfto
producea
single,
long
air
intake
pipe
for
each
cylinder
.
See
Fig
.
3
.
The
column
of
aír
oscíllating
in
Basic
Engine
Settings
this
combined
pipe
significantly
increases
engine
torque
in
the
medium
rpm
range
.
Idle
speed,
idle
mixture
(%CO),
and
ignition
timing
arenot
adjustable
.
The
adaptive
engine
management
system
is
de-
signed
to
automatically
compensate
for
changes
in
engine
op-
eratingconditions,
although
the
adaptive
range
is
limited
.
Once
these
limits
are
exceeded,
driveability
problems
usually
be-
come
noticeable
.
Above
approximately
4,800
rpm,
the
butterfly
valve
between
the
intake
air
pipes
for
the
two
cylinder
groups
is
opened
.
The
shorter
pipes
in
the
lower
manifold
section
now
become
the
main
suppliers
of
ram
air
to
the
cylinders,yielding
greater
pow-
er
at
the
upper
end
of
the
engine
rpm
range
.
See
Fig
.
4
.
Control
components
.
The
DISA
butterfly
valve
is
actuated
NOTE-
electro-pneumatically
via
the
engine
control
module
(ECM)
.
lf
the
system
adaptive
limits
are
exceeded,
the
Check
The
valve
begins
to
open
as
engine
speed
rises
aboye
4,840
Engine
light
will
most
likely
come
on,
indicating
an
rpmand
closes
below
4,760
rpm
.
The
action
of
the
valve
is
de-
emissions-
related
fault
For
Check
Engine
light
diag-
liberately
delayed
to
prevent
it
from
opening
and
closing
repeat-
nostics,
see100
Engine-General
.
edly
within
a
short
time
.
GENERAL
Page 165 of 759
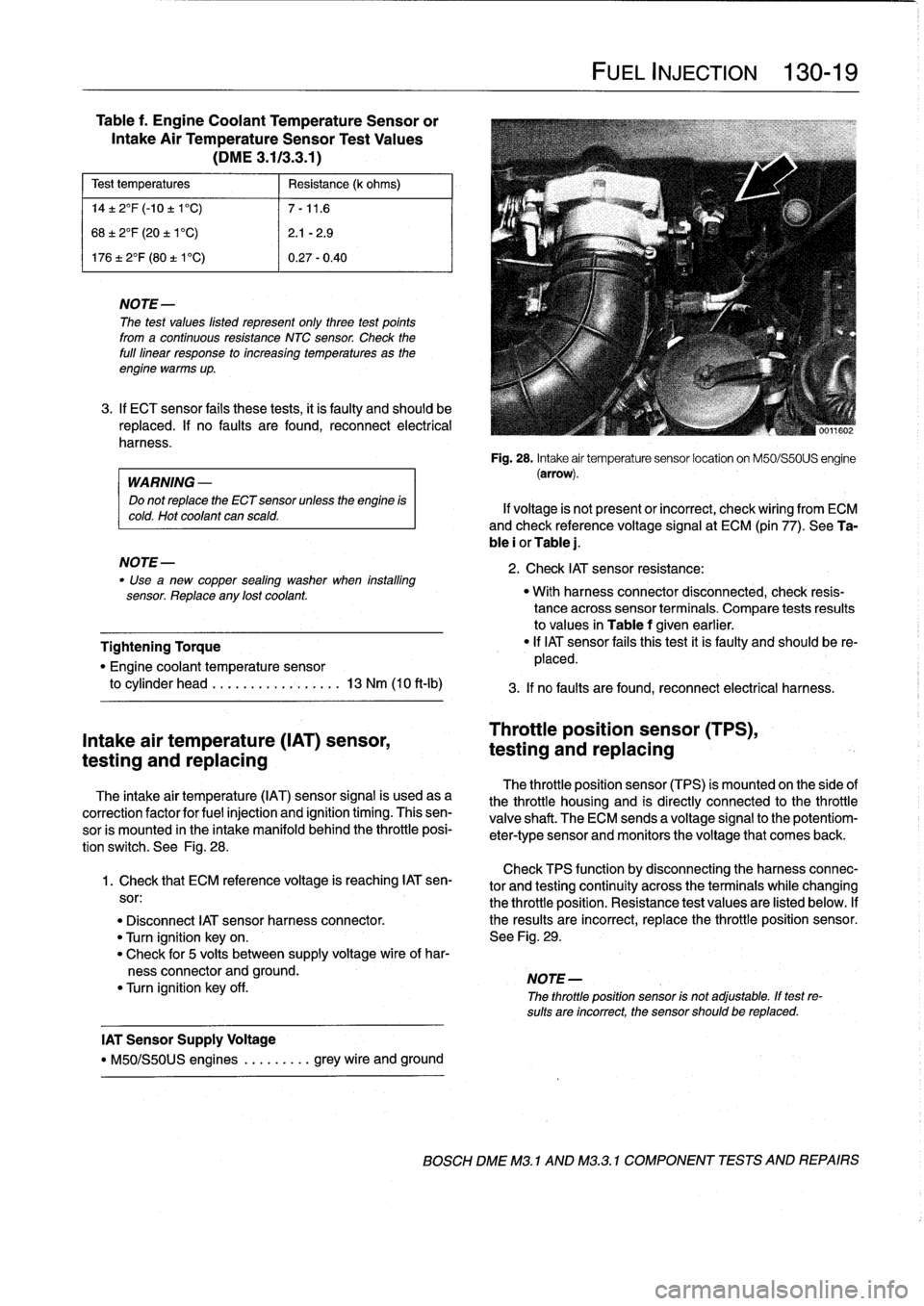
Table
f
.
Engine
Coolant
TemperatureSensor
or
Intake
Air
TemperatureSensor
Test
Values
(DME
3
.113
.3
.1)
Test
temperatures
Resistance
(k
ohms)
14±
2°F
(-10
±
1'C)
7-11
.6
68±
2°F
(20
±
1'C)
2
.1
-2
.9
17612°F
(80
t
V
C)
0
.27-0
.40
NOTE
The
test
values
listed
represent
only
three
test
points
from
a
continuous
resistance
NTC
sensor
.
Check
the
full
linear
response
to
increasing
temperatures
as
the
engine
warms
up
.
3
.
If
ECT
sensor
fails
these
tests,
it
is
faulty
and
should
be
replaced
.
If
no
faults
are
found,
reconnect
electrical
harness
.
WARNING
-
Do
not
replace
the
ECT
sensor
unless
the
engine
is
cold
.
Hot
coolant
can
scald
.
NOTE-
Use
"
a
new
copper
sealing
washer
when
installing
sensor
.
Replace
any
lost
coolant
.
Tightening
Torque
"
Engine
coolant
temperature
sensor
to
cylinder
head
.........
..
.
..
...
13
Nm
(10
ft-lb)
Intake
air
temperature
(IAT)
sensor,
testing
and
replacing
The
intake
air
temperature
(IAT)
sensor
signal
is
usedasa
correction
factor
for
fuel
injection
and
ignition
timing
.
Thissen-
sor
is
mounted
in
the
intake
manifold
behind
the
throttle
posi-
tion
switch
.
See
Fig
.
28
.
Check
TPS
function
by
disconnecting
theharnessconnec-
1
.
Check
that
ECM
reference
voltage
is
reaching
IAT
sen-
tor
and
testing
continuity
across
the
terminalswhile
changing
sor
:
the
throttle
position
.
Resistance
test
values
are
listed
below
.
If
"
Disconnect
IAT
sensor
harness
connector
.
the
resuits
are
incorrect,
replace
the
throttle
position
sensor
.
"
Turn
ignition
keyon
.
See
Fig
.
29
.
"
Check
for
5
volts
between
supply
voltage
wire
of
har-
ness
connector
and
ground
.
NOTE-
"
Turn
ignition
key
off
.
The
throttle
position
sensor
is
not
adjustable
.
If
test
re-
sults
are
incorrect,
the
sensor
should
be
replaced
.
IAT
Sensor
Supply
Voltage
"
M50/S50US
engines
.
........
grey
wire
and
ground
FUEL
INJECTION
130-19
Fig
.
28
.
Intake
air
temperature
sensor
location
on
M50/S50US
engine
(arrow)
.
If
voltage
is
not
present
or
incorrect,
check
wiring
from
ECM
and
check
reference
voltage
signal
at
ECM
(pin
77)
.
See
Ta-
ble
i
or
Table
j
.
2
.
Check
IAT
sensor
resistance
:
"
With
harness
connector
disconnected,
check
resis-
tance
acrosssensor
terminals
.
Compare
tests
resuits
to
values
in
Table
f
given
earlier
.
"
If
IAT
sensor
fafs
thistest
it
is
faulty
and
should
be
re-
placed
.
3
.
If
no
faults
are
found,
reconnect
electrical
harness
.
Throttle
position
sensor
(TPS),
testing
and
replacing
The
throttle
position
sensor
(TPS)
is
mounted
on
the
side
of
the
throttle
housing
and
is
directly
connected
to
the
throttle
valve
shaft
.
The
ECM
sends
a
voltage
signal
to
the
potentiom-
eter-type
sensor
and
monitors
the
voltage
that
comes
back
.
BOSCH
DME
M3
.
1
AND
M32
.1
COMPONENT
TESTS
AND
REPAIRS
Page 175 of 759
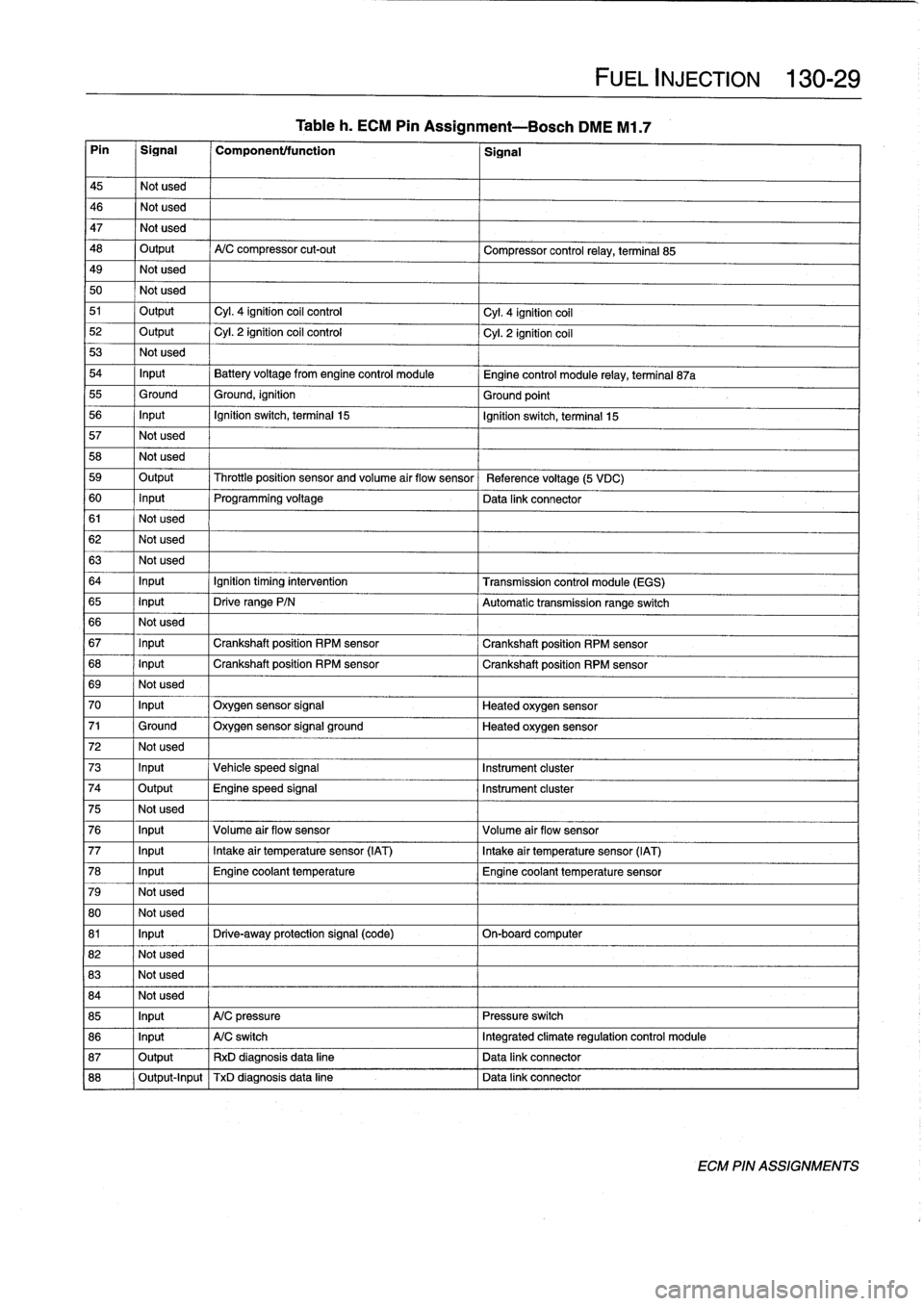
Tableh
.
ECM
Pin
Assignment--Bosch
DME
M1
.7
Pin
1
Signal
1
Component/function
1
Signal
45
Notused
46
Notused
47
Notused
48
Output
A/C
compressor
cut-out
Compressor
control
relay,
terminal
85
49
Notused
50
Notused
51
Output
Cyl
.
4
ignition
coil
control
Cyl
.
4
ignition
coil
52
Output
Cyl
.
2
ignition
coil
control
Cyl
.
2
ignition
coil
53
Not
used
54
Input
Battery
voltage
from
engine
control
module
Engine
control
module
relay,
terminal
87a
55
Ground
Ground,
ignition
Ground
point
56
Input
Ignition
switch,
terminal
15
Ignition
switch,
terminal
15
57
Notused
58
Not
used
59
Output
Throttleposition
sensor
and
volume
air
flow
sensor
Reference
voltage
(5
VDC)
60
Input
Programming
voltage
Data
link
connector
61
Notused
62
Notused
63
Notused
64
Input
Ignition
timing
intervention
Transmission
control
module
(EGS)
65
Input
Drive
range
P/N
Automatic
transmission
range
switch
66
Notused
67
Input
Crankshaft
position
RPM
sensor
Crankshaft
position
RPM
sensor
68
Input
Crankshaft
position
RPM
sensor
Crankshaft
position
RPM
sensor
69
Notused
70
Input
Oxygen
sensor
signal
Heated
oxygen
sensor
71
Ground
Oxygen
sensor
signal
ground
Heated
oxygen
sensor
72
Notused
73
Input
Vehicle
speed
signal
Instrument
cluster
74
Output
Engine
speed
signal
Instrument
cluster
75
Not
used
76
Input
Volume
air
flow
sensor
Volume
air
flow
sensor
77
Input
Intake
air
temperature
sensor
(IAT)
Intake
air
temperature
sensor
(IAT)
78
Input
Engine
coolant
temperature
Engine
coolant
temperature
sensor
79
Notused
80
Not
used
81
Input
Drive-away
protection
signal
(code)
On-boardcomputer
82
Not
used
83
Notused
84
Not
used
85
Input
A/C
pressure
Pressure
switch
86
Input
A/C
switch
Integrated
climate
regulation
control
module
87
Output
RxD
diagnosisdata
line
Data
link
connector
88
Output-Input
TxD
diagnosisdata
line
l
Data
link
connector
FUEL
INJECTION
130-
2
9
ECM
PIN
ASSIGNMENTS
Page 177 of 759
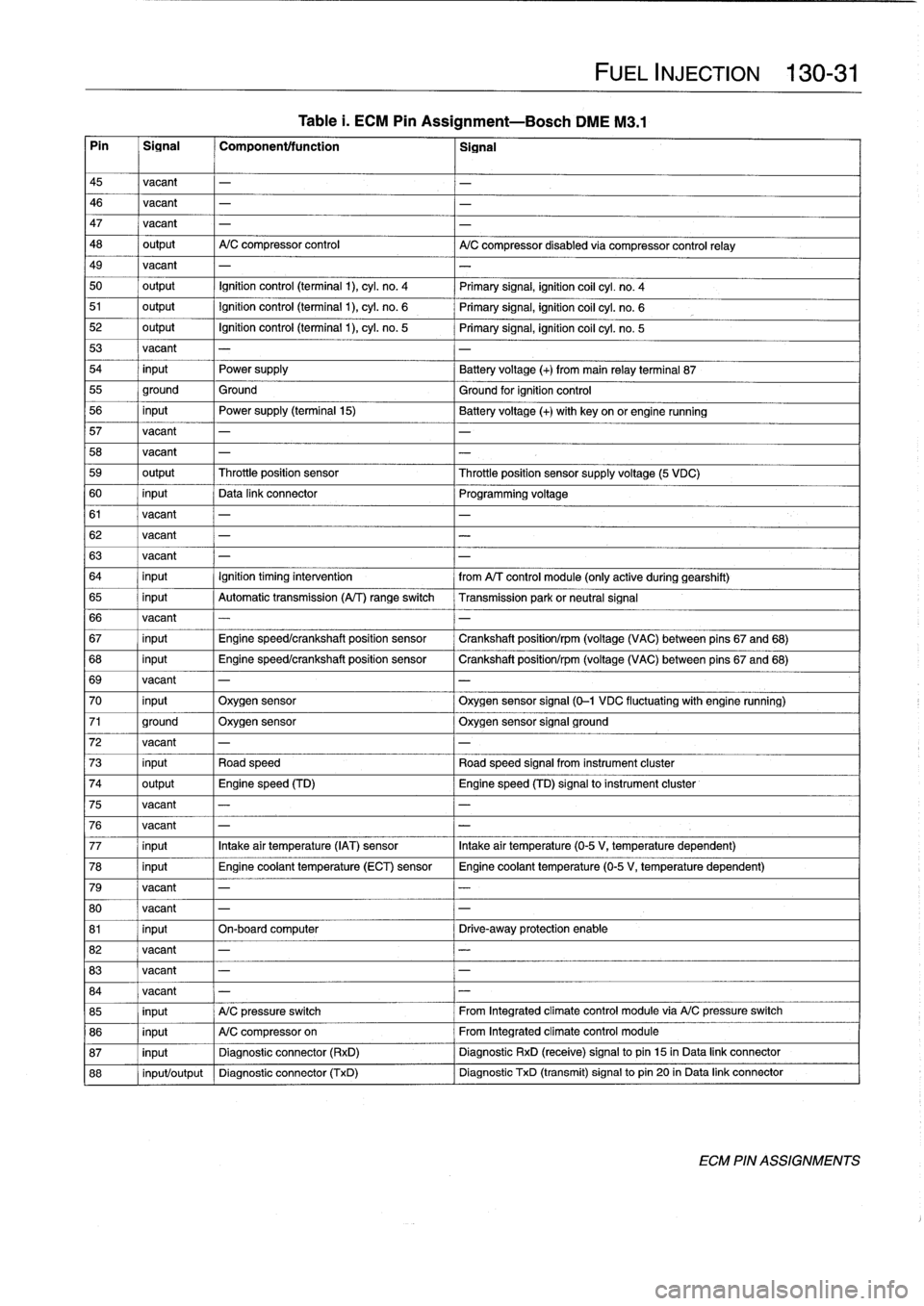
Table
i
.
ECM
Pin
Assignment-Bosch
DME
M3
.1
Pin
Signal
Component/function
2
ignal
FUEL
INJECTION
130-
3
1
45
vacant
-
46
vacant
-
-
47
vacant
-
-
48
output
A/C
compressor
control
A/C
compressor
disabled
via
compressor
control
relay
49
vacant
-
-
50
output
Ignition
control
(terminal
1),cyl
.
n
o
.
4
Primary
signal,
ignition
coil
cyl
.
n
o
.
4
51
output
Ignition
control
(terminal
1),cyl
.
n
o
.
6
Primary
signal,
ignition
coil
cyl
.
no
.
6
52
output
Ignition
control
(terminal
1),cyl
.
n
o
.
5
Primary
signal,
ignitioncoil
cyl
.
no
.
5
53
vacant
-
54
input
Power
supply
Battery
voltage
(+)
from
main
relay
terminal
87
55
ground
Ground
Ground
for
ignition
control
56
input
Power
supply
(terminal
15)
Batteryvoltage
(+)
with
key
on
or
engine
running
57
vacant
-
-
58
vacant
-
-
59
output
Throttleposition
sensor
Throttleposition
sensorsupply
voltage
(5
VDC)
60
input
Data
link
connector
Programming
voltage
61
vacant
-
-
62
vacant
-
-
63
vacant
-
-
64
input
Ignition
timing
intervention
from
A/T
control
module
(only
active
during
gearshift)
65
input
Automatic
transmission
(A/T)
range
switch
Transmission
park
or
neutral
signal
66
vacant
-
-
67
input
Engine
speed/crankshaft
position
sensor
Crankshaft
position/rpm
(voltage
(VAC)
between
pins
67
and
68)
68
input
Engine
speed/crankshaft
position
sensor
Crankshaft
position/rpm
(voltage
(VAC)
between
pins
67
and
68)
69
vacant
-
-
70
input
Oxygen
sensor
Oxygen
sensor
signal
(0-1
VDC
fluctuating
with
engine
running)
71
ground
Oxygen
sensor
Oxygen
sensor
signal
ground
72
vacant
-
-
73
input
Road
speed
Road
speed
signal
from
instrument
cluster
74
output
Engine
speed
(TD)
Engine
speed
(TD)
signalto
instrument
cluster
75
vacant
-
-
76
vacant
-
-
77
input
Intakeair
temperature
(IAT)
sensor
Intake
air
temperature
(0-5
V,
temperaturedependent)
78
input
Engine
coolant
temperature
(ECT)
sensor
Engine
coolant
temperature
(0-5V,
temperature
dependent)
79
vacant
-
-
80
vacant
-
-
81
input
On-boardcomputer
Drive-away
protection
enable
82
vacant
-
-
83
vacant
-
-
84
vacant
-
-
85
input
A/C
pressure
switch
From
Integrated
climate
control
module
via
A/C
pressure
switch
86
input
A/C
compressor
on
From
Integrated
climate
control
module
87
input
Diagnostic
connector
(RxD)
Diagnostic
RxD
(receive)signal
to
pin
15
in
Data
link
connector
88
input/output
Diagnostic
connector
(TxD)
Diagnostic
TxD
(transmit)
signal
to
pin
20
in
Data
link
connector
ECM
PIN
ASSIGNMENTS
Page 179 of 759
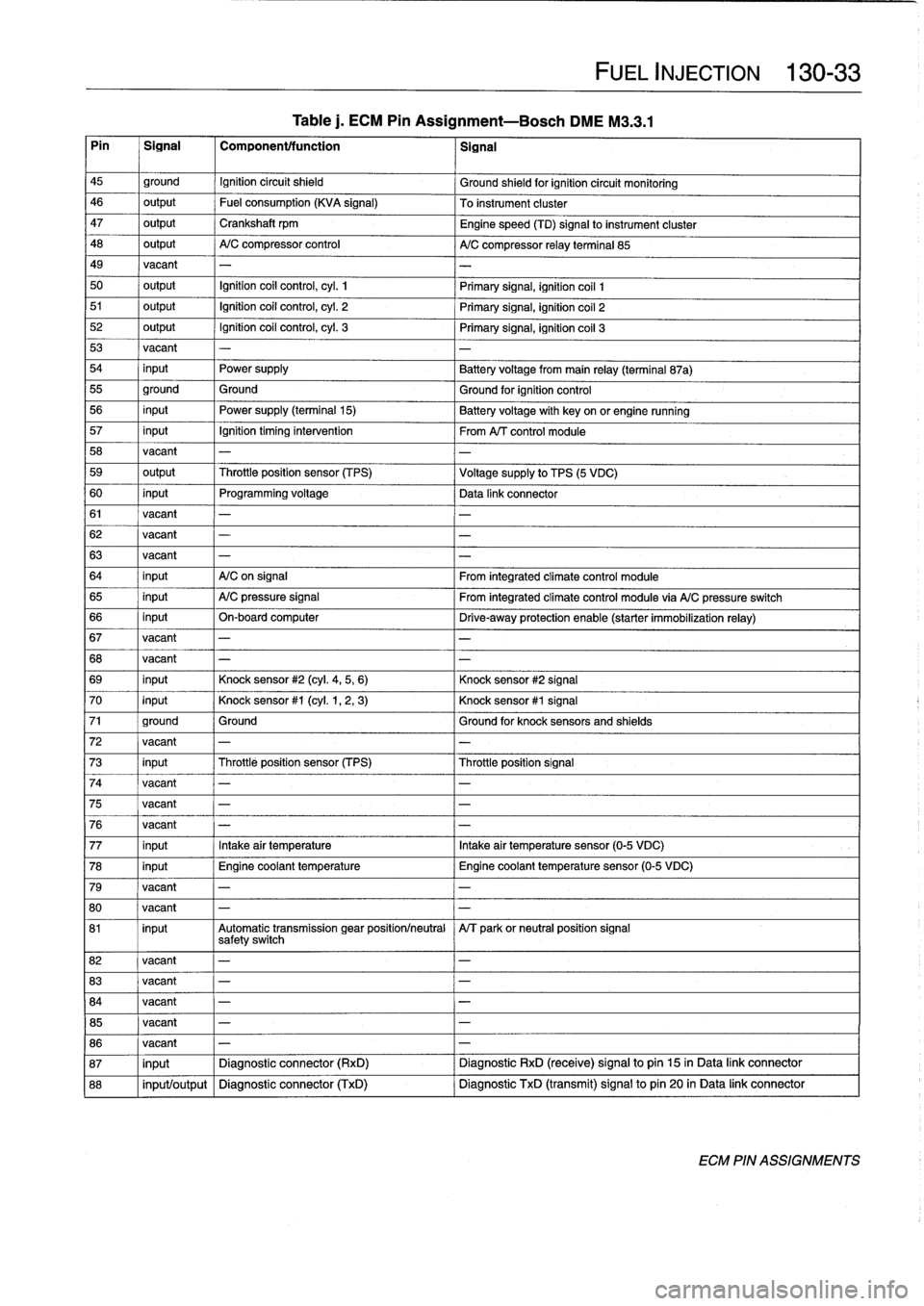
Table
j.
ECM
Pin
Assignment-Bosch
DME
M3
.3
.1
Pin
~
Signal
1
Componentffunction
1
signal
FUEL
INJECTION
130-
33
45
ground
Ignition
circuit
shield
Ground
shieldfor
ignition
circuit
monitoring
46
output
Fuel
consumption
(KVA
signal)
To
instrument
cluster
47
output
Crankshaft
rpm
Engine
speed
(TD)
signal
to
instrument
cluster
48
output
A/C
compressor
control
A/C
compressor
relay
terminal
85
49
vacant
-
-
50
output
Ignition
coil
control,
cyl
.
1
Primary
signal,
ignition
coil
1
51
output
Ignition
coil
control,
cyl
.
2
Primary
signal,
ignition
coil
2
52
output
Ignition
coil
control,
cyl
.
3
Primary
signal,
ignition
coil
3
53
vacant
-
-
54
input
Power
supply
Battery
voltagefrom
main
relay
(terminal
87a)
55
ground
Ground
Ground
for
ignition
control
56
input
Power
supply
(terminal15)
Batteryvoltage
with
key
on
or
engine
running
57
input
Ignition
timing
intervention
From
A/T
control
module
58
vacant
-
-
59
output
Throttleposition
sensor
(TPS)
Voltage
supply
to
TPS
(5
VDC)
60
input
Programming
voltage
Data
link
connector
61
vacant
-
-
62
vacant
-
-
63
vacant
-
-
64
input
A/C
on
signal
From
integrated
climate
control
module
65
input
A/C
pressure
signal
From
integrated
climate
control
module
via
A/C
pressure
switch
66
input
On-board
computer
Drive-away
protection
enable
(starter
immobilization
relay)
67
vacant
-
-
68
vacant
-
-
69
input
Knock
sensor
#2
(cyl
.
4,5,
6)
Knock
sensor
#2
signal
70
input
Knock
sensor
#1
(cyl
.
1,2,
3)
Knock
sensor
#1
signal
71
ground
Ground
Ground
for
knock
sensors
and
shields
72
vacant
-
-
73
input
Throttleposition
sensor
(TPS)
Throttleposition
signal
74
vacant
-
75
vacant
-
-
76
vacant
-
77
input
Intakeair
temperatura
Intakeair
temperatura
sensor
(0-5
VDC)
78
input
Engine
coolant
temperature
Engine
coolant
temperature
sensor
(0-5
VDC)
79
vacant
-
80
vacant
-
-
81
input
Automatic
transmission
gear
positionlneutral
A/T
parkor
neutral
position
signal
safetyswitch
82
vacant
-
-
83
vacant
-
-
84
vacant
-
-
85
vacant
-
-
86
vacant
-
-
87
input
Diagnostic
connector
(RxD)
Diagnostic
RxD
(receive)
signal
to
pin
15
in
Data
link
connector
88
input/output
Diagnostic
connector
(TxD)
Diagnostic
TxD
(transmit)
signal
to
pin
20
in
Data
link
connector
ECM
PIN
ASSIGNMENTS
Page 204 of 759
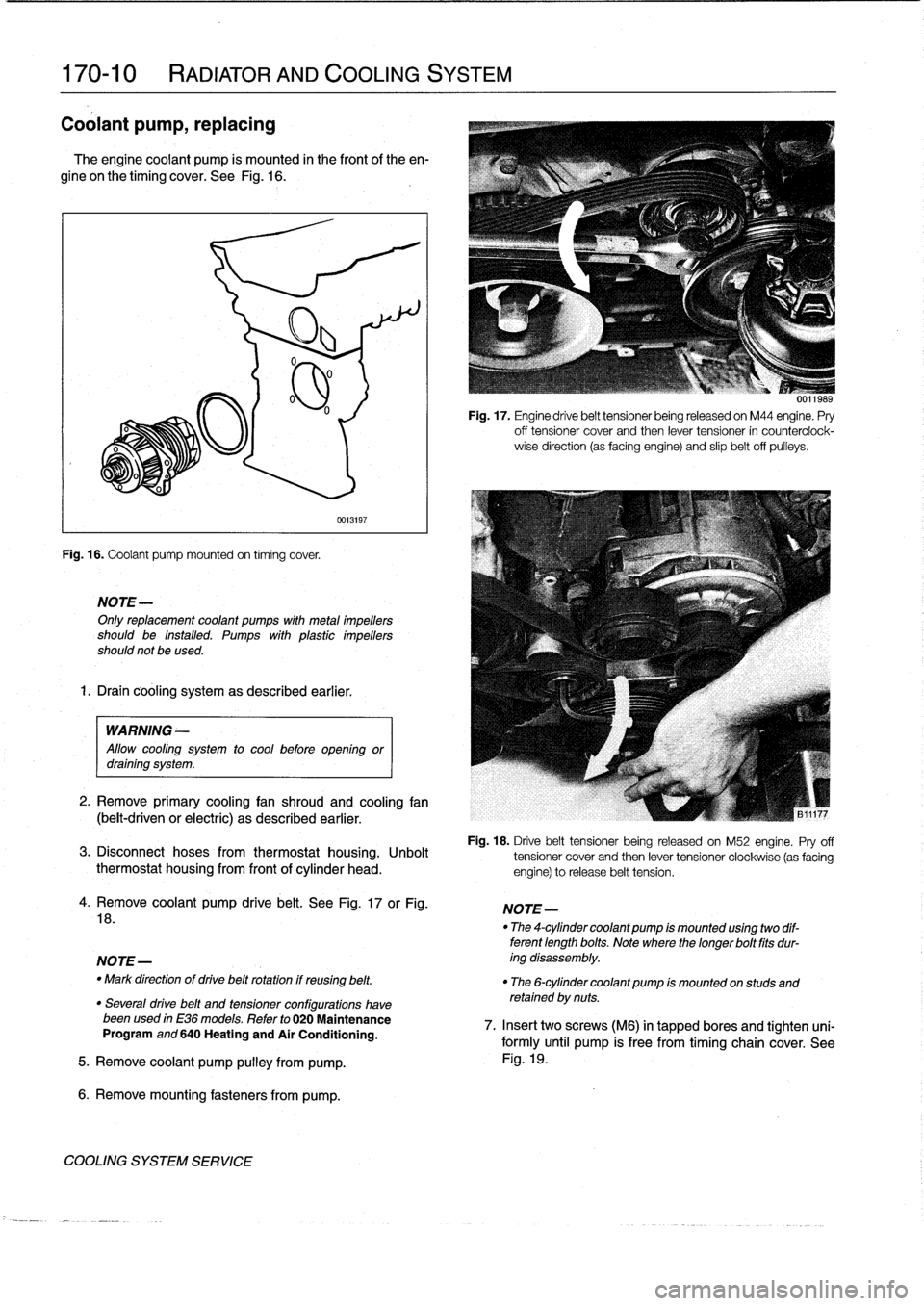
170-10
RADIATOR
AND
COOLING
SYSTEM
Coolant
pump,
replacing
The
engine
coolant
pump
is
mounted
in
the
frontof
the
en-
gine
on
the
timing
cover
.
See
Fig
.
16
.
Fig
.
16
.
Coolant
pump
mounted
on
timing
cover
.
NOTE-
Onlyreplacement
coolant
pumps
with
metal
¡mpellers
should
be
installed
.
Pumps
with
plastic
impellers
should
not
be
used
.
1.
Drain
cooling
system
as
described
earlier
.
0013197
WARNING
-
Allow
cool¡ng
system
to
cool
before
open¡ngor
drain¡ng
system
.
2
.
Remove
primary
cooling
fan
shroud
and
cooling
fan
(belt-driven
or
electric)
as
described
earlier
.
Fig
.
17
.
Engine
drive
belt
tensioner
being
released
on
M44
engine
.
Pry
off
tensioner
cover
and
then
lever
tensioner
in
counterciock-
wise
direction
(as
facing
engine)
and
slip
belt
off
pulleys
.
Fig
.
18
.
Drive
belt
tensioner
being
released
on
M52
engine
.
Pry
off
3
.
Disconnect
hoses
from
thermostat
housing
.
Unbolt
tensioner
cover
and
then
lever
tensioner
clockwise
(as
facing
thermostat
housing
from
front
of
cylinder
head
.
engine)torelease
belt
tension
.
4
.
Remove
coolant
pump
drive
belt
.
See
Fig
.
17
or
Fig
.
18
.
NOTE-
-
Mark
direction
of
drive
belt
rotation
if
reusing
belt
.
"
The
6-cylinder
coolant
pump
¡s
mounted
on
studs
and
retained
by
nuts
.
"
Severa¡
drive
belt
and
tensioner
configurations
havebeenused
in
E36
models
.
Refer
to
020
Maintenance
Program
and
640
Heating
and
Air
Conditioning
.
5
.
Remove
coolant
pump
pulley
from
pump
.
6
.
Remove
mounting
fasteners
from
pump
.
COOLING
SYSTEM
SERVICE
NOTE-
"
The
4-cylinder
coolant
pump
¡s
mounted
us¡ng
two
dif-
terent
length
bolts
.
Note
where
thelonger
bolt
fits
dur-
ing
disassembly
.
0011989
7
.
Insert
twoscrews
(M6)
in
tapped
bores
and
tighten
uni-
formly
until
pump
is
free
from
timing
chain
cover
.
See
Fig
.
19
.
Page 205 of 759
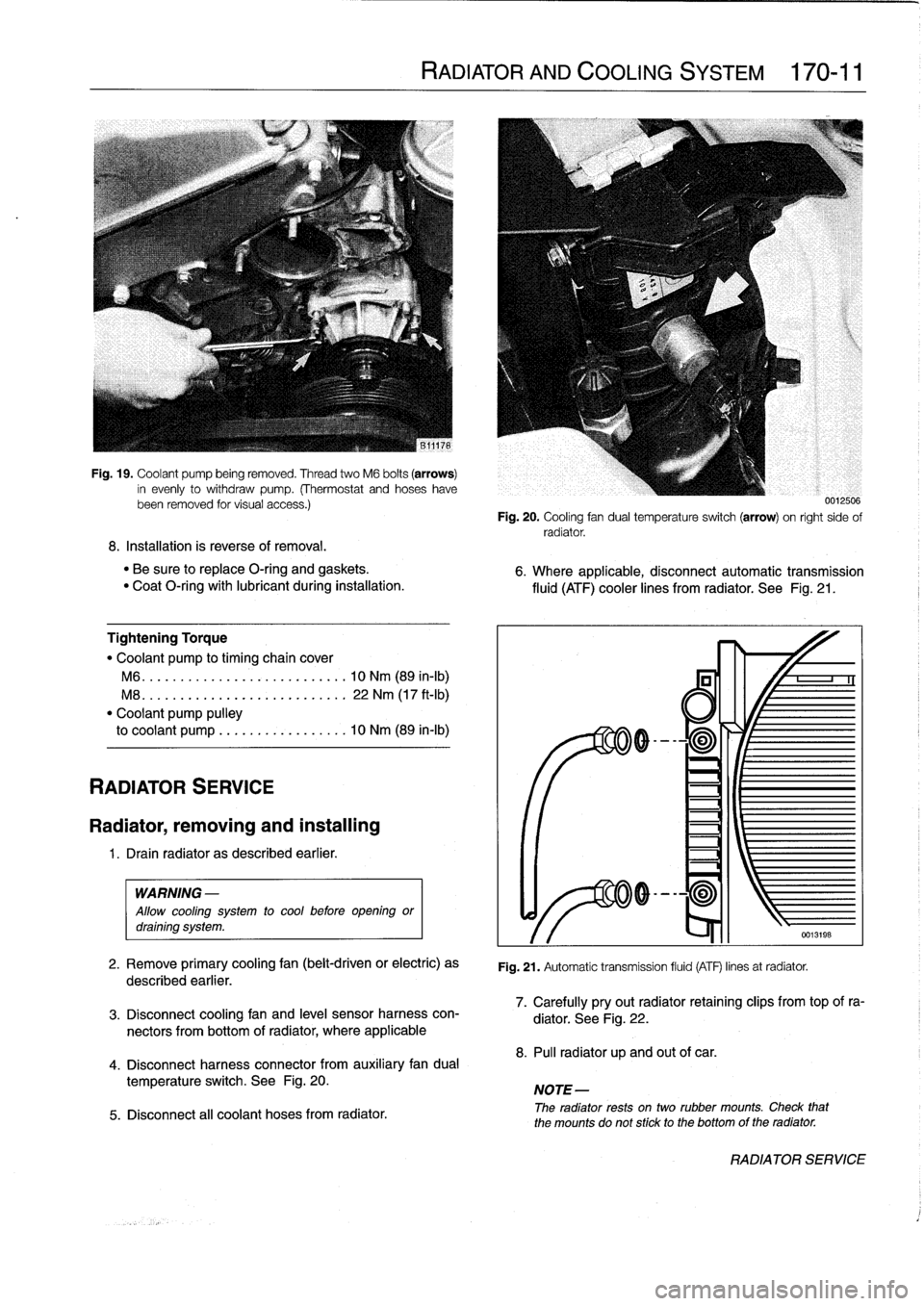
Fig
.
19
.
Coolant
pump
being
removed
.
Thread
two
M6
bolts
(arrows)
in
evenly
to
withdraw
pump
.
(Thermostat
and
hoseshavebeen
removed
tor
visual
access
.)
8
.
Installation
is
reverse
of
removal
.
"
Be
sure
to
replace
O-ring
and
gaskets
.
"
Coat
O-ring
with
lubricant
during
installation
.
Tightening
Torque
"
Coolant
pump
to
timing
chaincover
M6
...
.
...................
..
.
.
10
Nm
(89
in-lb)
M8
.
..
.
....................
.
.
.
22
Nm
(17
ft-Ib)
"
Coolant
pump
pulley
to
coolant
pump
.................
10
Nm
(89
in-lb)
RADIATOR
SERVICE
Radiator,
removing
and
installing
1
.
Drain
radiator
as
described
earlier
.
WARNING
-
Allow
cooling
system
to
cool
before
opening
ordraining
system
.
2
.
Remove
primary
cooling
fan
(belt-driven
or
electric)
as
described
earlier
.
3
.
Disconnect
coolingfan
and
leve¡
sensor
harness
con-
nectors
from
bottom
of
radiator,
where
applicable
4
.
Disconnect
harness
connector
from
auxiliary
fandual
temperature
switch
.
See
Fig
.
20
.
5
.
Disconnect
all
coolant
hoses
from
radiator
.
RADIATOR
AND
COOLING
SYSTEM
170-11
0012500
Fig
.
20
.
Cooling
fan
dual
temperatura
switch
(arrow)
on
right
sido
of
radiator
.
6
.
Where
applicable,
disconnectautomatic
transmission
fluid
(ATF)
cooler
lines
from
radiator
.
See
Fig
.
21
.
Fig
.
21
.
Automatic
transmission
fluid
(ATF)
linos
at
radiator
.
7
.
Carefully
pryout
radiator
retaining
clips
from
top
of
ra-
diator
.
See
Fig
.
22
.
8
.
Pul¡
radiator
up
and
out
of
car
.
NOTE-
The
radiator
rests
ontwo
rubber
mounts
.
Check
that
the
mounts
do
not
stick
to
the
bottomof
the
radiator
.
RADIATOR
SERVICE
Page 253 of 759

NOTE-
The
traction
control
system
referred
to
as
AST
(all
sea-
son
traction)
may
also
be
referred
to
as
ASC
(Automat-
ic
Stability
Control)
and
ASC+T
(Automatic
Stability
Control+Traction)
.
The
AST
system
improves
traction
by
electronically
apply-
ing
the
rear
brakes
when
therear
drive
wheels
are
spinning
at
a
faster
rate
than
the
front
wheels
.
The
combined
ABS/AST
control
module,
operating
through
the
ABS
hydraulic
control
unit,
modulates
braking
force
at
therear
wheels
.
In
addition,
AST
uses
retarded
ignition
timing
and
an
auxil-iary
engine
throttle
plate
to
reduceengine
torque
and
maintain
vehicle
stability
.
The
auxiliary
throttle
plate
is
held
open
by
spring
pressure
.
The
AST
system
actívates
the
auxiliary
throttie
position
motor
(ADS)
to
cose
the
AST
throttle
as
needed
.
This
reduces
the
volume
of
engine
intake
air
.
Due
to
the
throttle
closing
very
rapidly
during
AST
operationthe
driver
cannot
increase
theengine
power
output
regardless
of
how
far
theaccelerator
pedal
is
pushed
to
the
floor
.
The
auxiliary
throttle
plate
is
placed
ahead
of
the
conven-
tional
throttle
plate
in
the
throttle
body
.
Traction
control
also
comes
into
operationduringdecelera-
tion
.
Decelerating
on
snowy
or
icy
road
surfaces
can
lead
to
rear
wheel
slip
.
If
a
rear
wheel
startsto
drag
or
lock
up
when
the
throttle
is
closed
rapidly
orduringdownshifting,the
AST
system
can
limit
the
problem
by
advancing
the
ignition
timing
.
A
switch
on
the
center
console
is
used
to
togglethe
AST
on
or
off
.
The
AST
system
is
designed
to
be
maintenance
free
.
There
are
no
adjustments
that
can
be
made
.
Repair
and
trouble-
shooting
of
the
AST
system
requires
special
test
equipment
andknowledgeand
should
be
performed
only
by
an
autho-
rized
BMW
dealer
.
Table
a
lists
theconditions
indicated
by
the
AST
indicator
light
in
the
instrument
cluster
SUSPENSION,
STEERING
AND
BRAKES-GENERAL
300-5
Tablea
.
AST
Indicator
Lamp
Function
Indicator
lamp
1
Condition
1
Comment
Light
on
Normal
AST
start-
Automatic
AST
up
self-test
Light
off
AST
monitoring
Automatic
AST
op-
mode
eration
Press
AST
button,
AST
off
(disabled)
Rocking
the
car
tolight
comes
on
getout
of
snow
or
other
loose
surface
Driving
with
snow
chains
Press
AST
button
:
AST
monitoring
Automatic
AST
op-
light
goes
out
I
mode
eration
Light
flashes
AST
active
mode
I
Normal
AST
oper-
ation
as
it
controls
wheel
speed
Light
stays
on
af-
Defect
in
AST
Consult
BMW
ter
start
up
or
dealer
for
diagno-
comes
on
while
sis/repair
driving
(Vehicle
operation
remains
normal)
WARNING
-
Even
a
car
with
AST
is
subject
to
the
normal
physi-
cal
laws
.
Avoid
excessive
speeds
for
the
road
con-
ditions
encountered
.
CAUTION-
"
If
the
tires
on
the
carare
of
different
makes,
the
AST
system
may
over-react
.
Only
fit
tires
of
the
same
make
and
tread
pattem,
"In
adverse
conditions,
such
as
trying
to
rock
the
car
outof
deep
snow
or
another
soft
surface,
or
when
snow
chainsare
fitted,
it
is
advisable
to
switch
off
AST
and
allow
the
cars
driveline
to
op-
erate
conventionally
.
INTEGRATED
SYSTEMS