sensor BMW M3 1998 E36 Manual Online
[x] Cancel search | Manufacturer: BMW, Model Year: 1998, Model line: M3, Model: BMW M3 1998 E36Pages: 759
Page 232 of 759
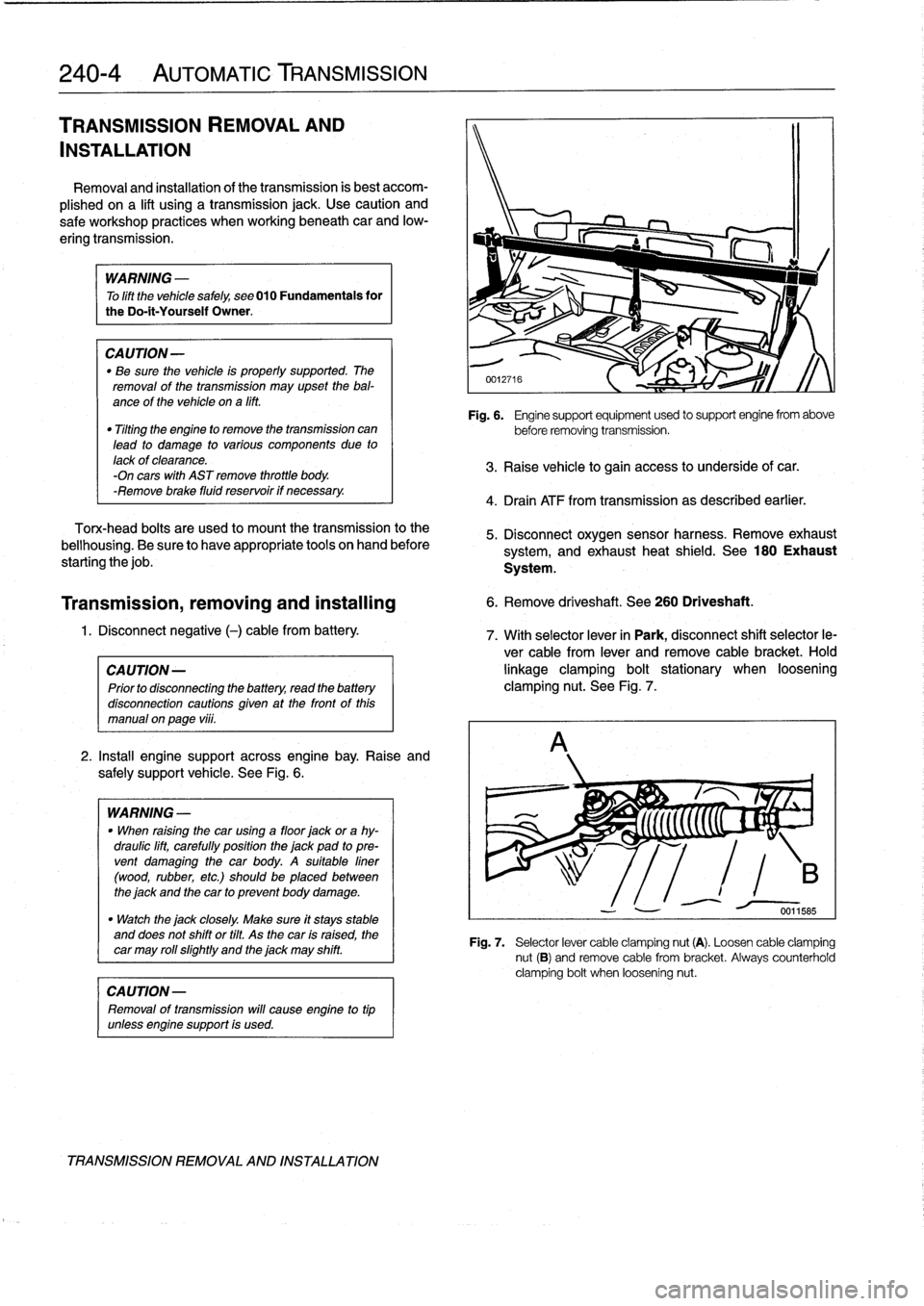
240-
4
AUTOMATIC
TRANSMISSION
TRANSMISSION
REMOVALAND
INSTALLATION
Removal
and
installation
of
thetransmission
is
best
accom-
plished
on
a
lift
using
a
transmission
jack
.
Use
caution
and
safe
workshop
practices
when
working
beneath
car
and
low-
ering
transmission
.
WARNING
-
To
lift
the
vehicle
safely,
see010
Fundamentals
for
the
Do-it-Yourself
Owner
.
CAUTION-
"
Be
sure
the
vehicle
is
properly
supported
.
The
removal
of
the
transmission
may
upset
the
bal-
ance
of
the
vehicle
on
a
lift
.
"
Tilting
the
engine
to
remove
the
transmission
can
lead
to
damage
to
various
components
due
to
lack
of
clearance
.
-On
carswith
AST
remove
throttle
body
.
-Remove
brake
fluid
reservoir
if
necessary
.
Torx-head
bolts
are
used
to
mount
thetransmission
to
the
bellhousing
.
Be
sure
to
have
appropriate
tools
on
hand
before
starting
thejob
.
2
.
Install
engine
support
across
engine
bay
.
Raise
and
safely
support
vehicle
.
See
Fig
.
6
.
WARNING
-
"
When
raising
thecar
using
a
floor
jack
or
a
hy-
draulic
lift,
carefully
position
the
jack
pad
to
pre-
vent
damaging
the
car
body
.
A
suitable
liner
(wood,
rubber,
etc
.)
should
be
placed
between
the
jack
and
the
car
to
prevent
body
damage
.
"
Watch
the
jack
closely
.
Make
sure
it
stays
stable
and
does
not
shift
or
tilt
.
As
the
car
is
raised,
the
car
may
roll
slightty
and
the
jack
may
shift
.
CAUTION-
Removal
of
transmission
will
cause
engine
to
tip
unlessengine
support
is
used
.
TRANSMISSION
REMOVAL
AND
INSTALLATION
Fig
.
6
.
Engine
support
equipment
used
to
support
engine
from
above
before
removing
transmission
.
3
.
Raise
vehicle
to
gain
access
to
underside
of
car
.
4
.
Drain
ATF
from
transmission
as
described
earlier
.
5
.
Disconnect
oxygen
sensor
harness
.
Remove
exhaust
system,
and
exhaust
heat
shield
.
See
180
Exhaust
System
.
Transmission,
removing
and
installing
6
.
Remove
driveshaft
.
See
260
Driveshaft
.
1
.
Disconnect
negative
(-)
cable
from
battery
.
7
.
With
selector
lever
in
Park,
disconnect
shift
selector
le-
ver
cable
from
lever
and
remove
cable
bracket
.
Hold
CA
UTION-
linkage
clamping
bolt
stationary
when
loosening
Prior
to
disconnectiog
the
battery,
read
the
battery
clamping
nut
.
See
Fig
.
7
.
disconnection
cautions
given
at
the
front
of
this
manual
on
page
vi¡¡
.
Fig
.
7
.
Selector
lever
cable
clamping
nut
(A)
.
Loosen
cable
clamping
nut
(B)
and
remove
cable
from
bracket
.
Always
counterholdclamping
bolt
when
loosening
nut
.
Page 233 of 759
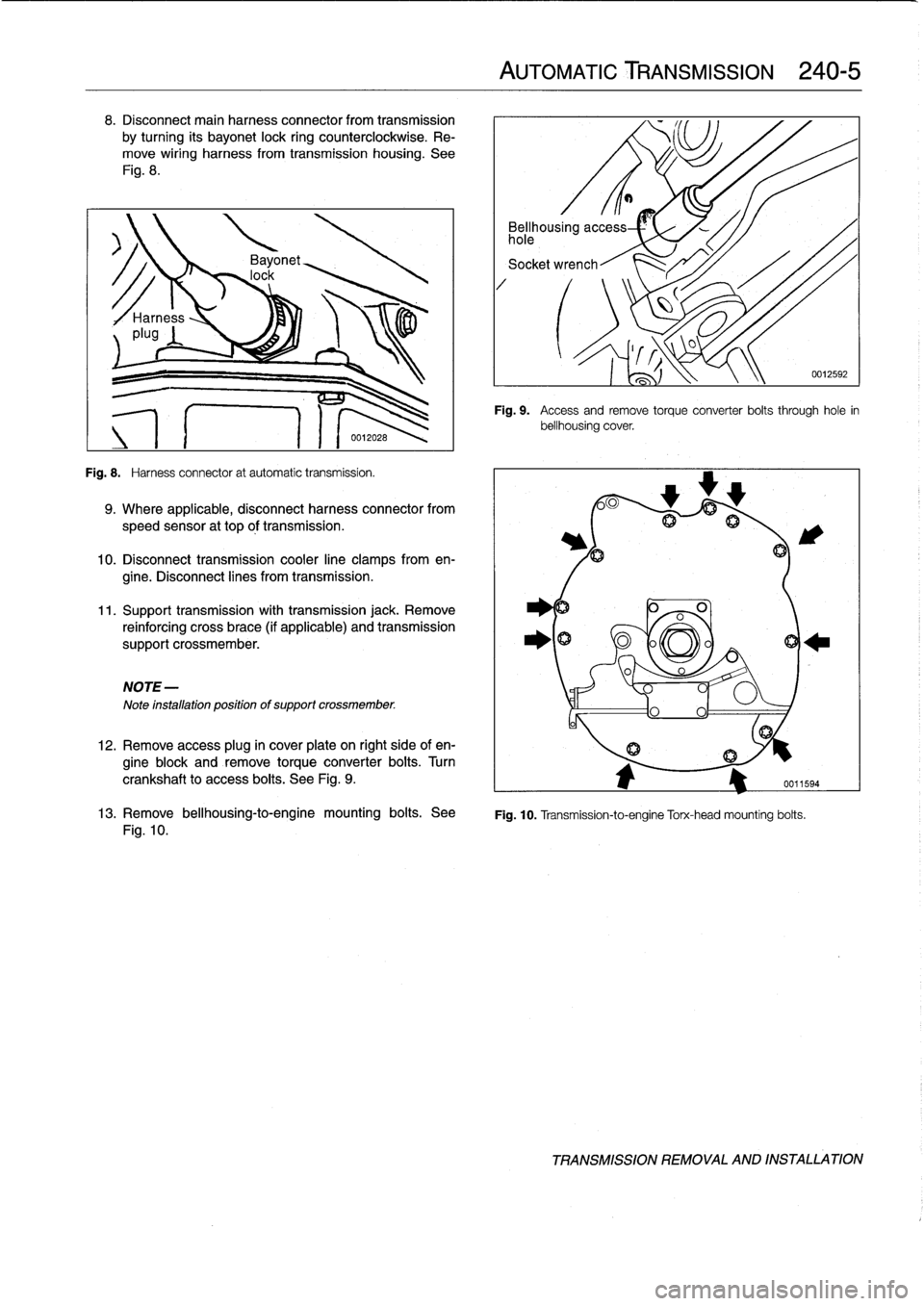
8
.
Disconnect
main
harness
connector
from
transmission
by
turning
its
bayonet
lock
ring
counterclockwise
.
Re-
move
wiring
harness
from
transmission
housing
.
See
Fig
.
8
.
Fig
.
8
.
Harness
connector
at
automatic
transmission
.
9
.
Where
applicable,
disconnect
harness
connector
from
speed
sensor
at
top
óf
transmission
.
10
.
Disconnect
transmission
cooler
line
clamps
from
en-
gine
.
Disconnect
lines
from
transmission
.
11
.
Support
transmission
with
transmission
jack
.
Remove
reinforcing
cross
brace
(if
applicable)
and
transmission
support
crossmember
.
NOTE-
Note
installation
positionof
support
crossmember
.
12
.
Remove
access
plug
in
cover
plate
on
right
side
of
en-
gine
block
and
remove
torqueconverter
bolts
.
Turn
crankshaft
to
access
boits
.
See
Fig
.
9
.
AUTOMATIC
TRANSMISSION
240-
5
Bellhousing
access
hole
Socket
wrench
Fig
.
9
.
Access
andremove
torque
converter
boits
through
hole
in
bellhousing
cover
.
0
A
fij
13
.
Remove
bellhousing-to-engine
mounting
bolts
.
See
Fig
.
10
.
Transmission-to-engine
Torx-head
mounting
bolts
.
Fig
.
10
.
0012592
TRANSMISSION
REMOVAL
AND
INSTALLATION
Page 235 of 759

GENERAL
.
.
.
.
.
.
.
.
.
................
.
.
.
250-1
AUTOMATIC
TRANSMISSION
GEARSHIFT
...
.
.........
.
.
.
.
.
.
.
.
.
.
.
.
.
.
250-3
MANUAL
TRANSMISSION
Gearshift
mechanism,
adjusting
GEARSHIFT
.
.
.
.
.
.
.
.....
.
..........
.
.
.
250-1
(automatictransmission)
..
.
.
.
.
.
.
.
.
.
...
.
.
250-3
Gearshift
lever,
removing
Gear
position/neutral
safety
switch,
replacing
(manual
transmission)
.
.
.
.
...
.
.
.
.......
250-1
(automatic
transmission)
..
.
.
.
.........
.
.
250-4
Gearshift
lever,
installing
Automatic
shiftlock,
checking
function
(manual
transmission)
.
.
.
.
.
.
.
.
.
.
.......
250-2
(automatic
transmission)
..
..
...
.
.
.
....
..
250-5
Shiftinterlock,
checking
function
(automatic
transmission)
.......
.
.
.
.....
.250-6
GENERAL
This
repair
group
covers
transmission
gearshift
and
linkage
service
.
Special
service
tools
are
required
for
some
of
the
proce-
dures
given
here
.
To
gain
access
to
the
complete
gearshift
mechanism
ít
is
necessary
to
remove
the
exhaust
system
and
the
driveshaft
as
described
in
180
Exhaust
System
and260
Driveshaft
.
MANUAL
TRANSMISSION
GEARSHIFT
Gearshift
lever,
removing
(manual
transmission)
The
manual
transmission
gearshift
linkage
is
shown
in
Fig
.1
.
Use
thisillustration
asaguide
when
removing
and
installing
the
linkage
.
1
.
Pull
straight
upon
shift
knob
lo
remove
it
from
shift
lever
.
NOTE
-
Removal
of
the
shift
knob
will
require
about
90
lbs
.
of
force
.
2
.
Pry
upon
rear
of
shift
boot
tounclip,
then
remove
boot
from
front
retainers
.
3
.
Raise
vehicle
togain
access
to
underside
of
vehicle
.
WARNING
-
Make
sure
thecar
is
stable
and
well
supported
at
afl
times
.
Use
a
professional
automotive
lift
orjackstands
designed
for
the
purpose
.
A
floor
jack
is
not
adequate
support
.
250
Gearshift
Linkage
GEARSHIFT
LINKAGE
250-1
Fig
.1
.
Manual
transmission
gearshift
linkage
.
4
.
Disconnect
oxygen
sensorharness
connectors
.
Re-
move
completeexhaust
system
.
See
180
Exhaust
System
.
MANUAL
TRANSMISSION
GEARSHIFT
Page 237 of 759

2
.
Install
rubber
grommet
with
arrow
pointing
forward
.
In-
AUTOMATic
TRANSMISSION
stall
shift
rod
and
shift
boot
.
GEARSHIFT
NOTE-
Install
rubbergrommet
correctly
so
that
is
seals
outwa-
ter
.
4
.
Install
driveshaft
and
heat
shield
.
See
260
Driveshaft
.
Manual
valveleven
(at
transmission)
Fig
.
6
.
Automatic
transmission
gearshift
assembfy
.
Shift
cable
GEARSHIFT
LINKAGE
250-
3
The
automatic
transmission
shift
mechanism
is
shown
in
Fig
.
6
.
Use
the
illustration
as
a
guide
when
servícing
the
gear-
shift
mechanism,
including
shift
cable
replacement
.
3
.
Connect
shift
rod
to
shift
lever
.
Install
transmission
crossmember
.
Lift
transmission
and
tighten
crossmem-
Gearshift
mechanism,
adjusting
ber
bolts
.
(automatictransmission)
NOTE-
1
.
Position
selector
lever
in
Park
.
Beforeconnecting
the
shift
rod
to
the
lever,
be
sure
the
2
.
Raise
vehicle
to
gain
access
to
shift
linkage
.
gearshift
leven
is
facing
the
correct
way
as
illustrated
in
Fig
.
1
.
WARNING
-
Make
sure
thecan
is
stable
and
well
supported
at
all
times
.
Use
a
professional
automotive
lift
or
jack
stands
designed
for
the
purpose
.
5
.
Reinstall
exhaust
system
.
See
180
Exhaust
System
.
Connect
oxygen
sensor
harness
connectors
.
3
.
Loosen
selector
cable
clamping
nut
.
See
Fig
.
7
.
6
.
Lower
vehicle
.
Insta¡¡
shift
boot
cover
.
Push
shift
knob
4
.
Push
shift
lever
forwardtoward
engine(Park
position)
onto
lever
.
while
applying
light
pressure
on
cable
end
.
Tighten
ca-
ble
clamping
nut
.
Tightening
Torques
NOTE-
"
Driveshaft
to
final
drive
Do
not
overtighten
the
nut
so
that
it
twists
the
cable
.
flange
(with
U-joint)
.
..
.
.....
.
.
See
250
Driveshaft
"
Flex-disc
to
driveshaft
or
transmission
flange
...
.
.......
See
250
Driveshaft
Tightening
Torque
"
Transmission
crossmember
"
Shift
cable
clamping
nut
.......
10-12
Nm
(75-9
ft-Ib)
to
body
(M8)
.
.
.
...
..............
21
Nm
(16
ft-Ib)
/S
r\
1
1
Gear
position/
neutral
safetyswitch
Automatic
shilo
solenoid
id
AUTOMATIC
TRANSMISSION
GEARSHIFT
Page 244 of 759
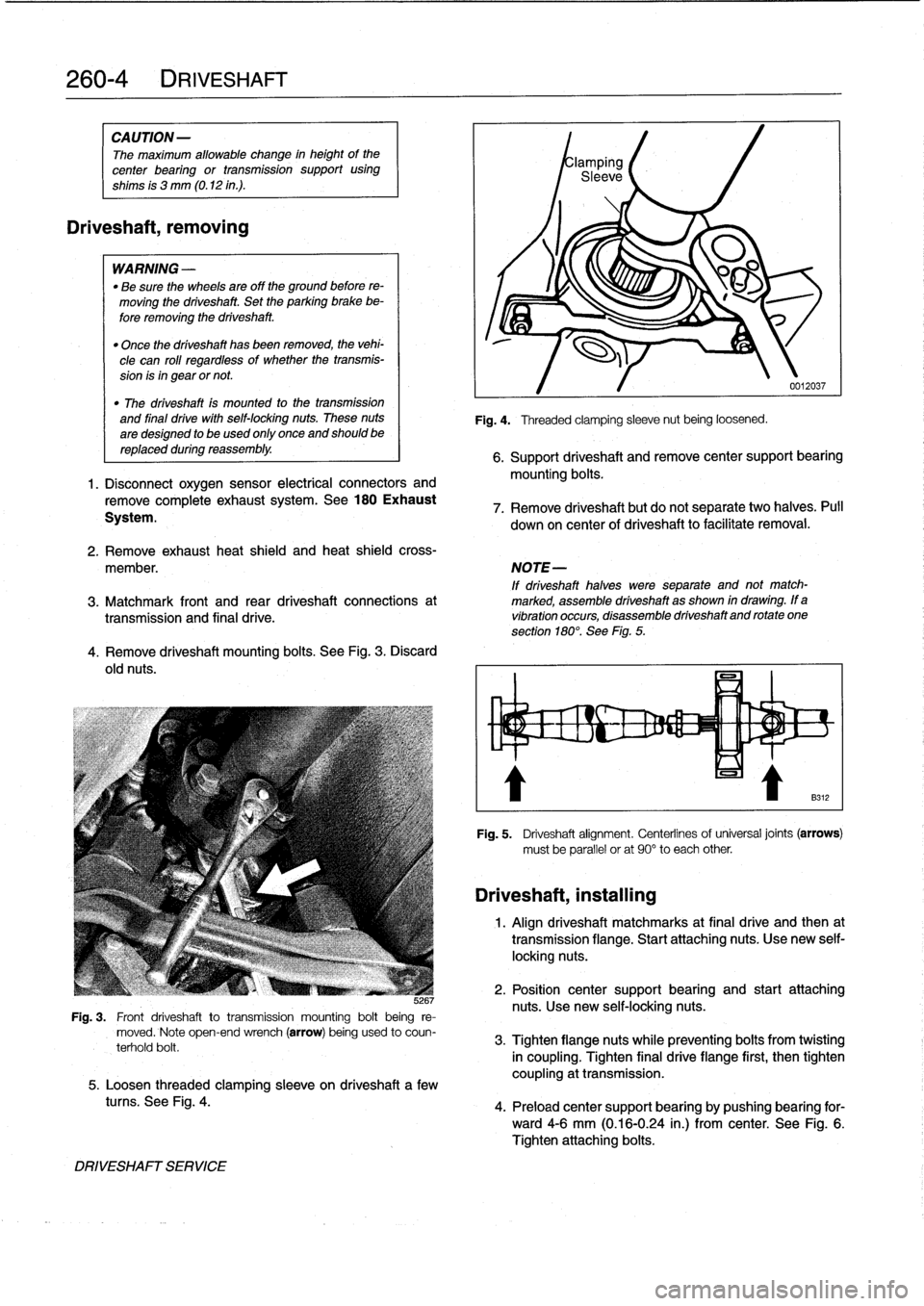
260-
4
DRIVESHAFT
CAUTION
-
The
maximum
allowable
change
in
height
of
the
center
bearing
or
transmission
support
using
shims
is
3
mm
(0
.12
in
.)
.
Driveshaft,
removing
WARNING
-
"
Be
sure
the
wheels
are
off
the
ground
before
re-
moving
the
driveshaft
.
Set
the
parking
brake
be-
fore
removing
the
driveshaft
.
"
Once
the
driveshaft
has
been
removed,
the
vehi-
cle
can
roll
regardless
of
whether
the
transmis-
sion
isin
gear
or
not
.
"
The
driveshaft
fs
mounted
to
thetransmission
and
final
drive
with
self-locking
nuts
.
These
nuts
are
designed
to
be
used
only
once
and
should
be
replaced
during
reassembly
.
1.
Disconnect
oxygen
sensor
electrical
connectors
and
remove
complete
exhaustsystem
.
See
180
Exhaust
System
.
4
.
Remove
driveshaft
mounting
bolts
.
See
Fig
.
3
.
Discard
old
nuts
.
JG
Fig
.
3
.
Front
driveshaft
totransmission
mounting
bolt
being
re-
moved
.
Note
open-end
wrench
(arrow)
being
used
to
coun-
terhold
bolt
.
5
.
Loosen
threaded
clamping
sleeve
on
driveshaft
a
few
tucos
.
See
Fig
.
4
.
DRIVESHAFT
SERVICE
Fig
.
4
.
Threaded
clamping
sleeve
nut
being
loosened
.
0012037
6
.
Support
driveshaft
andremove
center
support
bearing
mounting
bolts
.
7
.
Remove
driveshaft
but
do
not
separate
two
halves
.
Pull
down
on
center
of
driveshaft
to
facilitate
removal
.
2
.
Remove
exhaust
heat
shield
and
heat
shieldcross-
member
.
NOTE-
If
driveshaft
halves
were
separate
and
not
match-
3
.
Matchmark
front
and
rear
driveshaft
connections
at
marked,
assemble
driveshaft
as
shown
in
drawing
.
If
a
transmissíon
and
final
drive
.
vibration
occurs,
disassemble
driveshaftand
rotate
one
section
180°
.
See
Fig
.
5
.
Driveshaft,
installing
Fig
.
5
.
Driveshaft
alignment
.
Centerlinesof
universal
joints
(arrows)
must
be
parallel
or
at
90°
to
each
other
1
.
Align
driveshaft
matchmarks
at
final
drive
and
then
at
transmission
flange
.
Start
attaching
nuts
.
Use
new
self-
locking
nuts
.
2
.
Position
center
support
bearing
and
start
attaching
nuts
.
Use
new
self-locking
nuts
.
3
.
Tighten
flangenuts
while
preventing
bolts
from
twisting
in
coupling
.
Tighten
final
drive
flange
first,
then
tighten
coupling
at
transmission
.
4
.
Preload
center
support
bearing
by
pushing
bearing
for-
ward4-6
mm
(0
.16-0
.24
in
.)
from
center
.
See
Fig
.
6
.
Tighten
attaching
bolts
.
Page 245 of 759
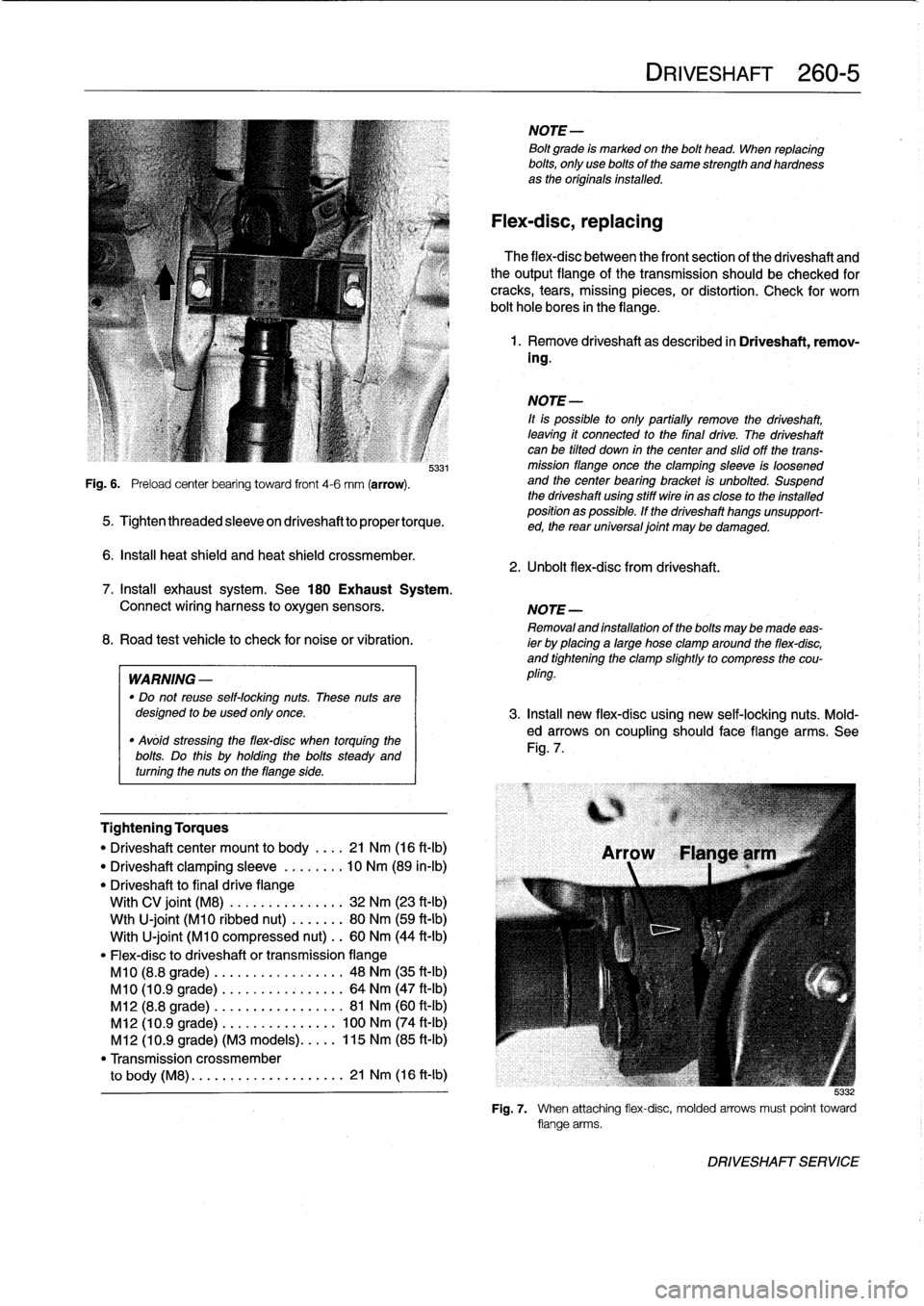
Fig
.
6
.
Preload
center
bearing
toward
front
4-6
mm
(arrow)
.
5331
5
.
Tightenthreadedsleeveondriveshafttopropertorque
.
6
.
Insta¡¡
heat
shield
and
heat
shield
crossmember
.
Tightening
Torques
"
Driveshaftcenter
mount
to
body
.
.
..
21
Nm
(16
ft-Ib)
"
Driveshaft
clamping
sleeve
.....
.
.
.
10
Nm
(89
in-lb)
"
Driveshaft
to
final
drive
flange
With
CV
joint
(M8)
............
...
32
Nm
(23
ft-Ib)
Wth
U-joint
(M10
ribbed
nut)
....
...
80
Nm
(59
ft-Ib)
With
U-joint
(M10
compressed
nut)
..
60
Nm
(44
ft-Ib)
"
Flex-disc
to
driveshaft
or
transmissionflange
M10
(8.8
grade)
.........
.
....
..
.
48
Nm
(35
ft-Ib)
M10
(10
.9
grade)
........
.
....
...
64
Nm
(47
ft-Ib)
M12
(8.8
grade)
........
.....
..
.
.
81
Nm
(60
ft-Ib)
M12
(10
.9
grade)
.
.
....
......
...
100
Nm
(74
ft-Ib)
M12
(10
.9
grade)
(M3
models)
..
.
.
.
115
Nm
(85
ft-Ib)
"
Transmission
crossmember
to
body
(M8)
.
....
...........
....
21
Nm
(16
ft-Ib)
NOTE-
Bolt
grade
is
markedon
the
bolt
head
.
When
replacing
bolts,
only
use
bolts
of
the
same
strength
and
hardnessas
the
originalsinstalled
.
Flex-disc,
replacing
The
flex-disc
between
the
front
section
of
the
driveshaft
and
theoutputflange
of
the
transmission
should
be
checked
for
cracks,
tears,
missing
pieces,
or
distortion
.
Check
for
worn
bolt
hole
bores
in
theflange
.
1
.
Remove
driveshaft
as
described
in
Driveshaft,
remov-
ing
.
NOTE-
¡t
is
possible
to
only
partially
remove
the
driveshaft,
leaving
it
connected
to
the
final
drive
.
The
driveshaft
canbe
tilted
down
in
thecenter
and
slidoff
the
trans-
mission
flange
once
the
clamping
sleeve
is
loosened
and
the
center
bearing
bracket
is
unbolted
.
Suspend
the
driveshaft
using
stiff
wire
in
as
close
to
the
installed
position
as
possible
.
If
the
driveshaft
hangs
unsupport-
ed,
the
rear
universal
joint
may
be
damaged
.
2
.
Unbolt
flex-dísc
from
driveshaft
.
DRIVESHAFT
260-
5
7
.
Install
exhaust
system
.
See
180
Exhaust
System
.
Connect
wiring
harness
to
oxygen
sensors
.
NOTE-
Removaland
installation
of
the
boltsmaybe
made
eas-
8
.
Road
test
vehicle
to
check
for
noiseor
vibration
.
ier
by
placing
a
large
hose
clamp
around
the
flex-disc,
and
tightening
the
clamp
slightlyto
compress
the
cou
WARNING
-
pling
.
"
Do
not
reuse
self-locking
nuts
.
These
nuts
aredesigned
to
beused
only
once
.
3
.
Insta¡¡
new
flex-disc
using
new
self-locking
nuts
.
Mold-
"
Avóid
stressing
the
flex-disc
when
torquing
the
ed
arrows
on
coupling
should
face
flange
arms
.
See
bolts
Do
this
holding
the
bolts
Fig
.
7
.
steady
and
.
uy
turning
the
nuts
on
theflange
side
.
5
:132
Fig
.
7
.
When
attaching
flex-disc,
molded
arrows
must
point
toward
flange
arms
.
DRIVESHAFT
SERVICE
Page 250 of 759
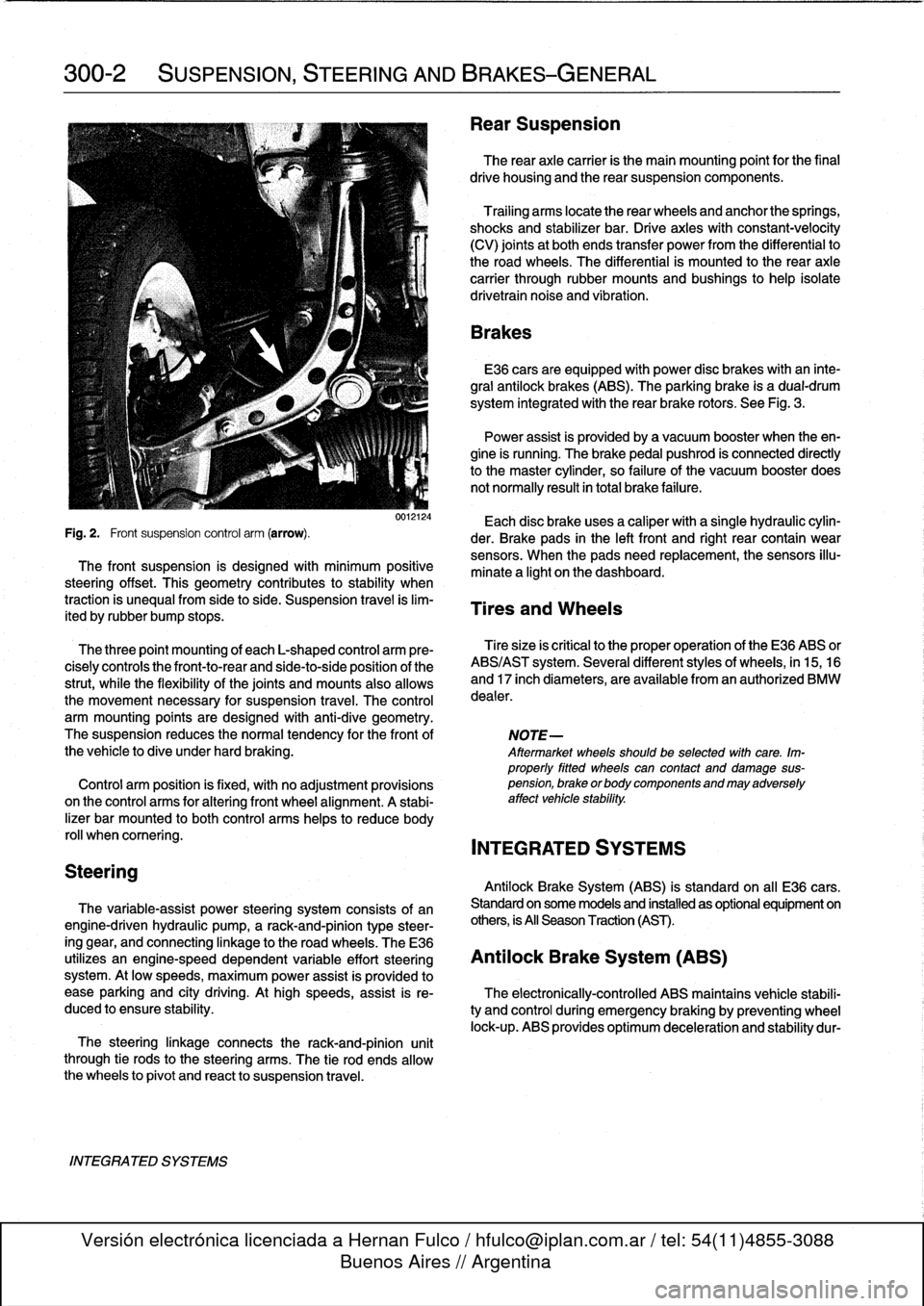
300-2
SUSPENSION,
STEERING
AND
BRAKES-GENERAL
Steering
INTEGRATED
SYSTEMS
The
steering
linkage
connects
the
rack-and-pinion
unit
through
tie
rodsto
the
steering
arms
.
The
tie
rod
ends
allow
the
wheels
to
pivot
and
react
to
suspension
travel
.
Rear
Suspension
The
rear
axle
carrier
is
the
main
mounting
point
for
the
final
drive
housing
and
the
rear
suspension
components
.
Trailing
arms
locatethe
rear
wheels
and
anchorthe
springs,
shocks
and
stabilizer
bar
.
Driveaxies
with
constant-velocity
(CV)
joints
at
both
ends
transfer
power
from
the
differential
to
the
road
wheels
.
The
differential
is
mounted
to
the
rearaxle
carrier
through
rubber
mountsand
bushings
to
hele
isolate
drivetrain
noise
and
vibration
.
Brakes
E36
cars
areequipped
with
power
disc
brakes
with
an
inte-
gral
antilock
brakes
(ABS)
.
The
parking
brake
is
a
dual-drum
system
integrated
with
the
rear
brake
rotors
.
See
Fig
.
3
.
Power
assist
is
provided
by
a
vacuum
booster
when
the
en-
gine
is
running
.
The
brakepedal
pushrod
is
connected
directly
to
the
master
cylinder,
so
failure
of
the
vacuum
booster
does
not
normally
result
in
total
brake
failure
.
0012124
Each
disc
brakeuses
a
caliper
with
a
single
hydraulic
cylin-
Fig
.
2
.
Front
suspension
control
arm
(arrow)
.
der
.
Brake
pads
in
the
left
front
and
right
rear
contain
wear
sensors
.
When
the
padsneed
replacement,the
sensors
illu-
The
front
suspension
is
designed
with
minimum
positive
minate
a
light
on
the
dashboard
.
steering
offset
.
This
geometry
contributes
to
stability
when
traction
is
unequalfrom
side
to
side
.
Suspension
travel
is
lim-
Tires
and
Wheels
ited
by
rubber
bump
stops
.
The
three
point
mounting
of
each
L-shaped
control
arm
ere-
Tiresize
is
critica¡
to
the
proper
operatíon
of
the
E36
ABS
or
cisely
controls
the
front-to-rear
and
side-to-side
position
of
the
ABS/AST
system
.
Severa¡
different
styles
of
wheels,
in
15,16
strut,
while
the
flexibility
of
the
joints
and
mounts
alsoallows
and
17
inch
diameters,
are
available
from
an
authorized
BMW
the
movement
necessary
for
suspension
travel
.
The
control
dealer
.
arm
mounting
points
are
designed
with
anti-dive
geometry
.
The
suspension
reduces
the
normaltendency
for
the
front
of
NOTE-
the
vehicle
to
dive
under
hard
braking
.
Aftermarket
wheelsshould
be
selected
wlth
care
.
Im-
properly
fitted
wheels
can
contact
anddamage
sus
Control
arm
position
is
fixed,
with
no
adjustment
provisions
pension,
brakeorbodycomponentsandmayadversely
on
the
control
arms
for
alter¡ng
front
wheel
al
ignment
.
A
stabi-
affect
vehicle
stability
.
lizer
bar
mounted
to
both
control
arms
heles
to
reduce
body
rol¡
whencomering
.
INTEGRATED
SYSTEMS
Antilock
Brake
System
(ABS)
is
standard
on
all
E36
cars
.
The
variable-assist
power
steering
system
consists
of
an
Standard
on
some
models
and
installed
as
optional
equipment
on
engine-driven
hydraulic
pump,
a
rack-and-pinion
type
steer-
others,
is
All
Season
Traction
(AST)
.
ing
gear,
and
connecting
linkage
to
the
road
wheels
.
TheE36
utilizes
an
engine-speed
dependent
variable
effort
steering
Antilock
Brake
System
(ABS)
system
.
At
low
speeds,
maximum
power
assist
is
provided
to
ease
parking
and
city
driving
.
Athigh
speeds,
assist
is
re-
The
electronically-controlled
ABS
maintains
vehícle
stabili
duced
to
ensure
stability
.
ty
and
control
during
emergency
braking
by
preventing
wheel
lock-up
.
ABS
provides
optimum
deceleration
and
stability
dur-
Page 251 of 759
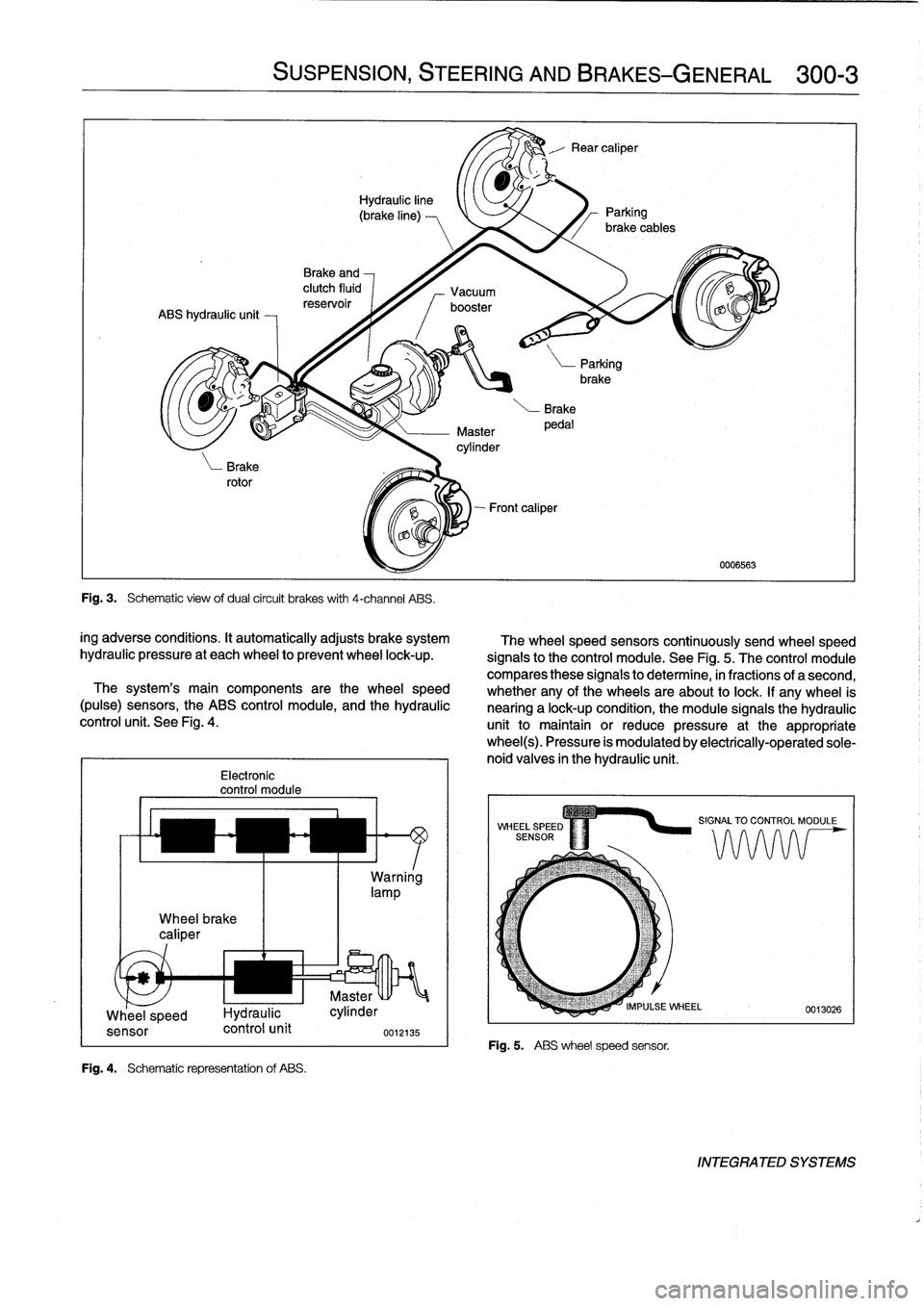
Wheel
brake
caliper
Electronic
control
module
Fig
.
4
.
Schematic
representation
of
ABS
.
SUSPENSION,
STEERING
ANDBRAKES-GENERAL
300-3
Fig
.
3
.
Schematic
view
ofdual
circuit
brakes
with
4-channel
ABS
.
ing
adverse
conditions
.
It
automatically
adjusts
brake
system
hydraulic
pressure
at
each
wheel
to
prevent
wheel
lock-up
.
The
system's
main
components
arethe
wheel
speed
(pulse)
sensors,
the
ABS
control
module,
and
the
hydraulic
control
unit
.
See
Fig
.
4
.
Warning
lamp
u
Master
Whee
_
l
speed
I-lydraulic
cylinder
sensor
control
unit
0012135
UNI
The
wheel
speed
sensors
continuously
send
wheel
speed
signals
to
the
control
module
.
See
Fig
.
5
.
The
control
module
compares
these
signals
to
determine,
in
fractions
of
a
second,
whether
any
of
the
wheels
areabout
to
lock
.
If
any
wheel
is
nearing
a
lock-up
condition,
the
module
signals
the
hydraulic
unit
to
maintain
or
reduce
pressure
at
the
appropriatewheel(s)
.
Pressure
is
modulated
by
electrically-operated
sole-
noid
valves
in
the
hydraulic
unit
.
Fig
.
5
.
ABS
wheelspeed
sensor
.
0006563
INTEGRATED
SYSTEMS
Page 252 of 759
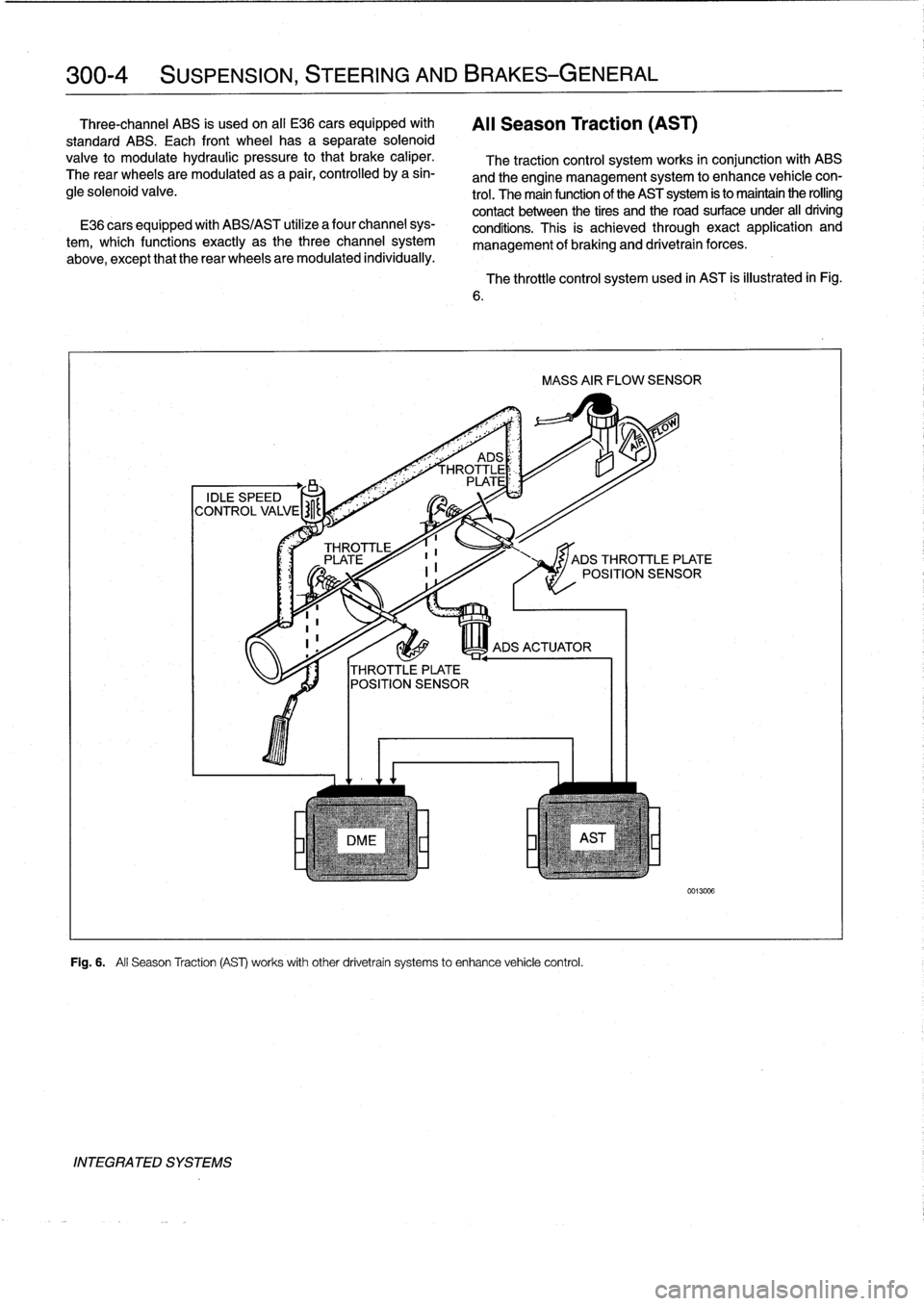
300-4
SUSPENSION,
STEERING
AND
BRAKES-GENERAL
Three-channel
ABS
ís
used
on
al[
E36
cars
equipped
with
Al¡
Season
Traction
(AST)
standard
ABS
.
Each
front
wheelhas
a
separate
solenoid
valve
to
modulate
hydraulic
pressure
to
that
brake
caliper
.
The
traction
control
system
works
in
conjunction
with
ABS
The
rear
wheels
are
modulated
asa
pair,
controlled
by
a
sin-
and
the
engine
management
system
to
enhance
vehicle
con
gle
solenoid
valve
.
trol
.
The
main
function
of
the
AST
system
is
to
maintain
the
rolling
contact
between
the
tires
and
the
road
surface
under
al¡
driving
E36
cars
equipped
with
ABS/AST
utilize
a
four
channel
sys-
conditions
.
This
is
achieved
through
exact
application
and
tem,
which
functionsexactly
as
the
three
channelsystem
management
of
braking
and
drivetrain
forces
.
above,except
that
the
rear
wheels
are
modulated
individually
.
IDLE
SPEED
CONTROL
VALVE
HROTTLE
PLATE
6
.
Í
III
i
ADS
ACTU
AT
OR
THROTTLE
PLATE
POSITION
SENSOR
DME
Fig
.
6
.
All
Season
Traction
(AS)
works
withother
drivetrain
systems
to
enhance
vehicle
control
.
INTEGRATED
SYSTEMS
The
throttle
control
system
used
in
AST
is
illustrated
in
Fig
.
MASS
AIR
FLOW
SENSOR
JADS
THROTTLE
PLATE
POSITION
SENSOR
0013006
Page 254 of 759
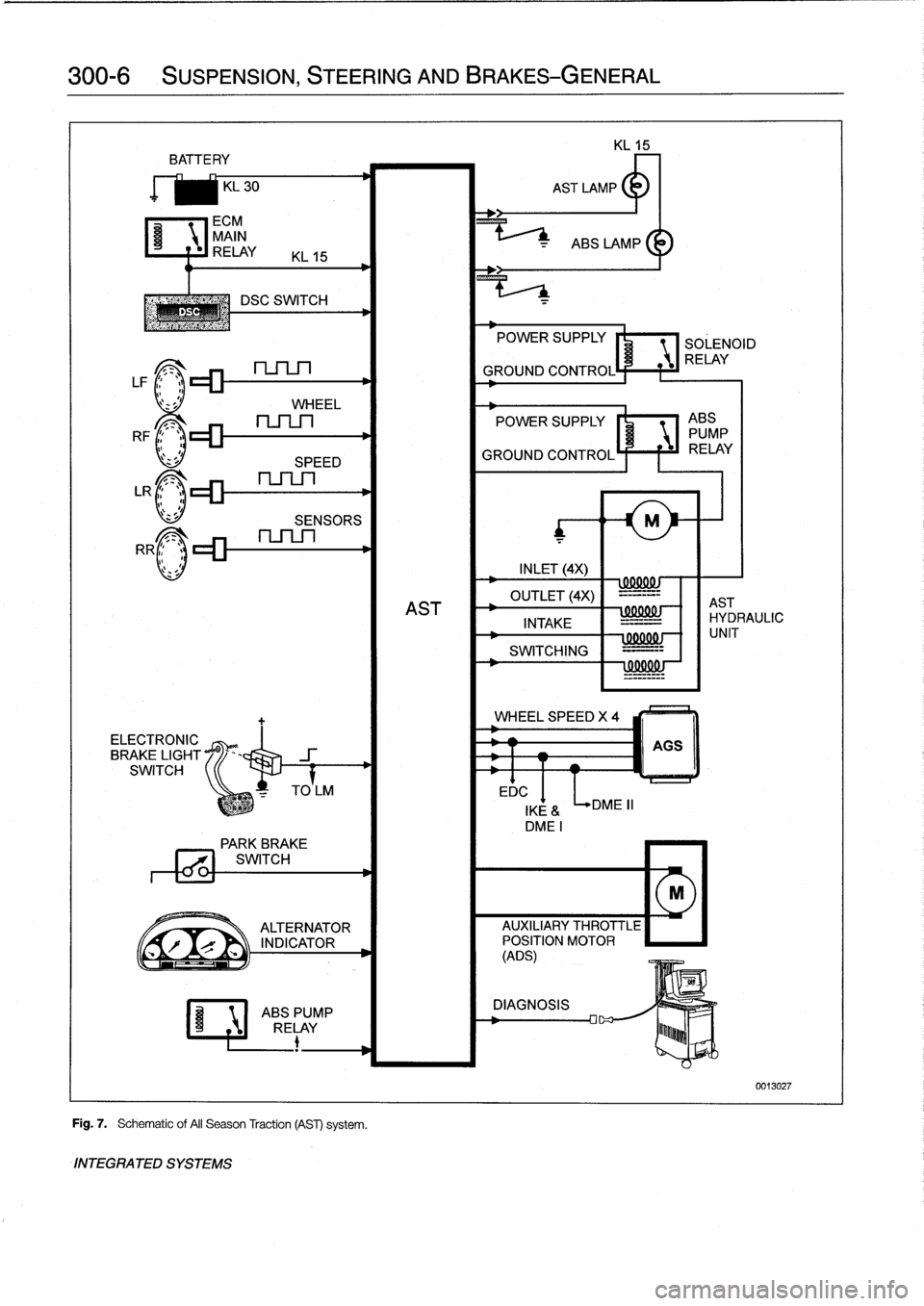
300-6
SUSPENSION,
STEERING
AND
BRAKES-GENERAL
BATTE
RY
KL
30
ECM
MAIN
C~
RELAY
KL
15
DSC
SWITCH
LF1
;1~lZZ~
nSLn
l'
z
sJ
WHEEL
RF
c_
.
LR
r_
.
>
RR
ELECTRONIC
BRAKE
LIGHT
SWITCH
SPEED
SENSORS
Fig
.
7
.
Schematic
of
AII
Season
Traction
(AST)
system
.
INTEGRATED
SYSTEMS
EDC
POWER
SUPPLY
SOLENOID
RELAY
GROUND
CONTROL
POWER
SUPPLY
I'
1
ABS
PUMP
GROUND
CONTROLÍ
F
f
iJ
RELAY
INLET
(4X)
wxxuw
OUTLET
(4X)
-=-=--
AST
AST
INTAKE
IHYDRAULIC
-
=-
SWITCHING
=---
!
99001
!J
WHEEL
SPEED
X
4
DME
II
000001
-
f
1
UNIT
AGS
IKE
&
DMEI
PARK
BREVE
771
SWITCH
M
ALTERNATOR
AUXILIARY
THROTTLE
r
`
INDICATOR
POSITION
MOTOR
(ADS)
ABSPUMP
DIAGNOSIS
RELAY
lu~~~b
0013027