sensor CHERY TIGGO 2009 Service Repair Manual
[x] Cancel search | Manufacturer: CHERY, Model Year: 2009, Model line: TIGGO, Model: CHERY TIGGO 2009Pages: 1903, PDF Size: 33.38 MB
Page 1468 of 1903
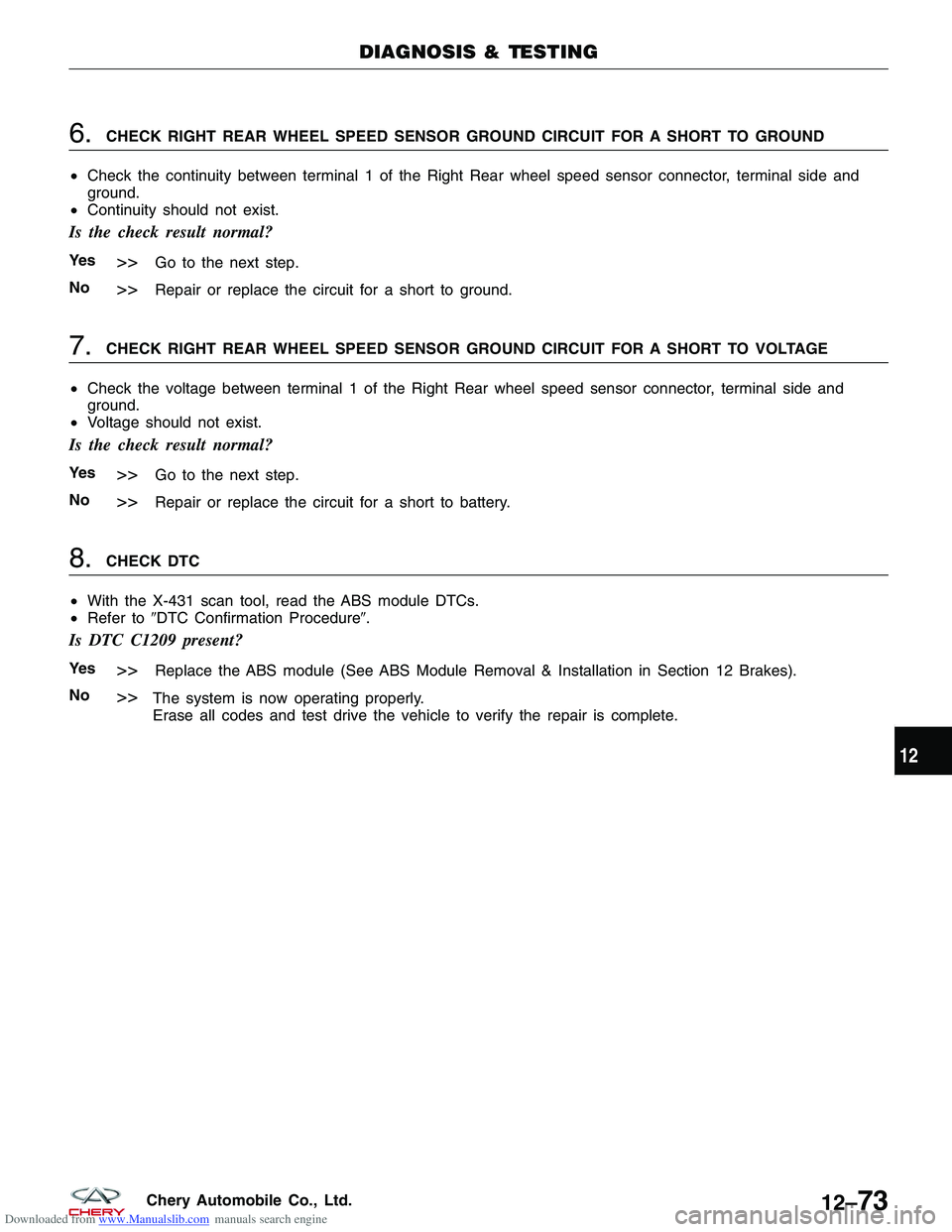
Downloaded from www.Manualslib.com manuals search engine 6.CHECK RIGHT REAR WHEEL SPEED SENSOR GROUND CIRCUIT FOR A SHORT TO GROUND
• Check the continuity between terminal 1 of the Right Rear wheel speed sensor connector, terminal side and
ground.
• Continuity should not exist.
Is the check result normal?
Ye s>>Go to the next step.
No
>>Repair or replace the circuit for a short to ground.
7.CHECK RIGHT REAR WHEEL SPEED SENSOR GROUND CIRCUIT FOR A SHORT TO VOLTAGE
• Check the voltage between terminal 1 of the Right Rear wheel speed sensor connector, terminal side and
ground.
• Voltage should not exist.
Is the check result normal?
Ye s>>Go to the next step.
No
>>Repair or replace the circuit for a short to battery.
8.CHECK DTC
• With the X-431 scan tool, read the ABS module DTCs.
• Refer to DTC Confirmation Procedure.
Is DTC C1209 present?
Ye s>>Replace the ABS module (See ABS Module Removal & Installation in Section 12 Brakes).
No
>>The system is now operating properly.
Erase all codes and test drive the vehicle to verify the repair is complete.
DIAGNOSIS & TESTING
12
12–73Chery Automobile Co., Ltd.
Page 1472 of 1903
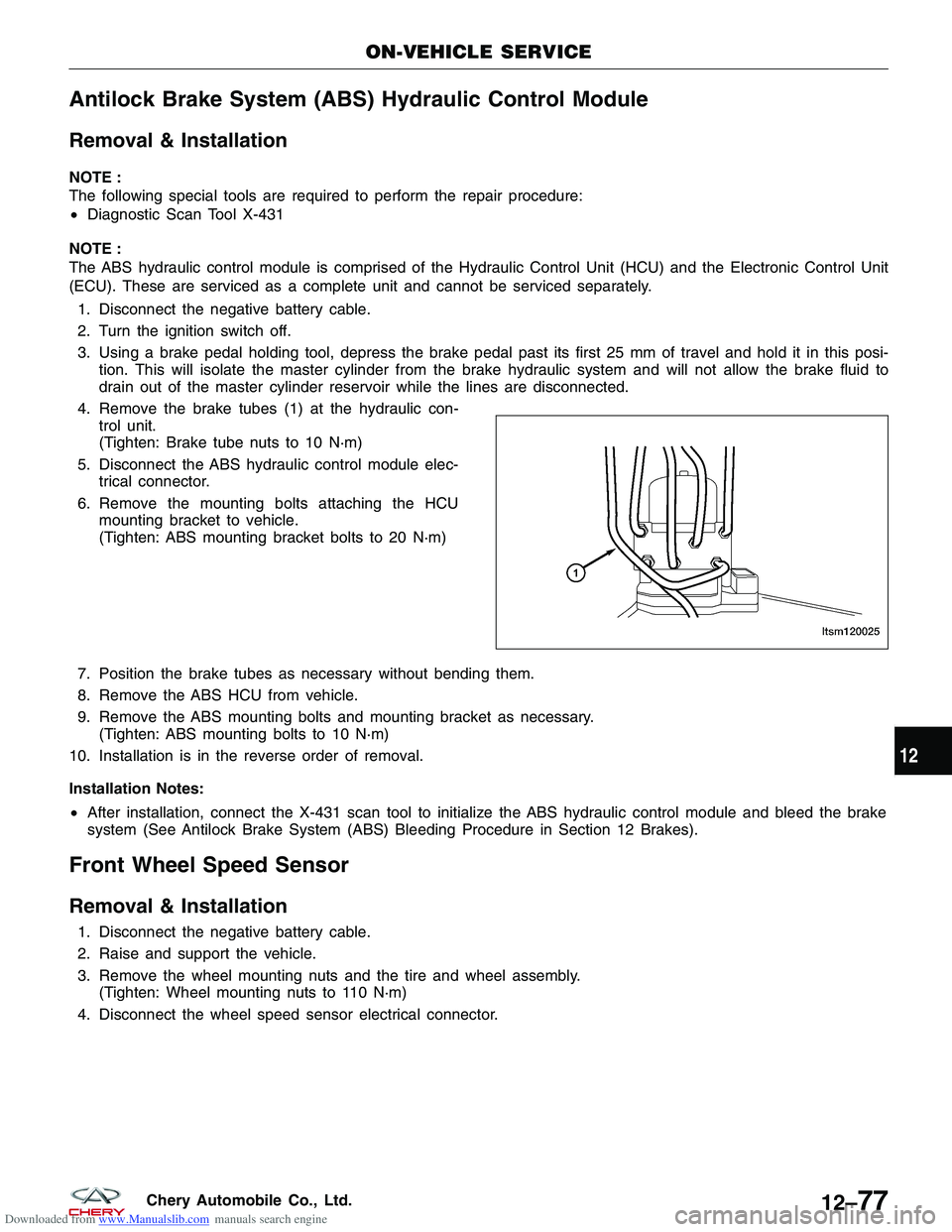
Downloaded from www.Manualslib.com manuals search engine Antilock Brake System (ABS) Hydraulic Control Module
Removal & Installation
NOTE :
The following special tools are required to perform the repair procedure:
•Diagnostic Scan Tool X-431
NOTE :
The ABS hydraulic control module is comprised of the Hydraulic Control Unit (HCU) and the Electronic Control Unit
(ECU). These are serviced as a complete unit and cannot be serviced separately. 1. Disconnect the negative battery cable.
2. Turn the ignition switch off.
3. Using a brake pedal holding tool, depress the brake pedal past its first 25 mm of travel and hold it in this posi- tion. This will isolate the master cylinder from the brake hydraulic system and will not allow the brake fluid to
drain out of the master cylinder reservoir while the lines are disconnected.
4. Remove the brake tubes (1) at the hydraulic con- trol unit.
(Tighten: Brake tube nuts to 10 N·m)
5. Disconnect the ABS hydraulic control module elec- trical connector.
6. Remove the mounting bolts attaching the HCU mounting bracket to vehicle.
(Tighten: ABS mounting bracket bolts to 20 N·m)
7. Position the brake tubes as necessary without bending them.
8. Remove the ABS HCU from vehicle.
9. Remove the ABS mounting bolts and mounting bracket as necessary. (Tighten: ABS mounting bolts to 10 N·m)
10. Installation is in the reverse order of removal.
Installation Notes:
• After installation, connect the X-431 scan tool to initialize the ABS hydraulic control module and bleed the brake
system (See Antilock Brake System (ABS) Bleeding Procedure in Section 12 Brakes).
Front Wheel Speed Sensor
Removal & Installation
1. Disconnect the negative battery cable.
2. Raise and support the vehicle.
3. Remove the wheel mounting nuts and the tire and wheel assembly.
(Tighten: Wheel mounting nuts to 110 N·m)
4. Disconnect the wheel speed sensor electrical connector.
ON-VEHICLE SERVICE
LTSM120025
12
12–77Chery Automobile Co., Ltd.
Page 1473 of 1903
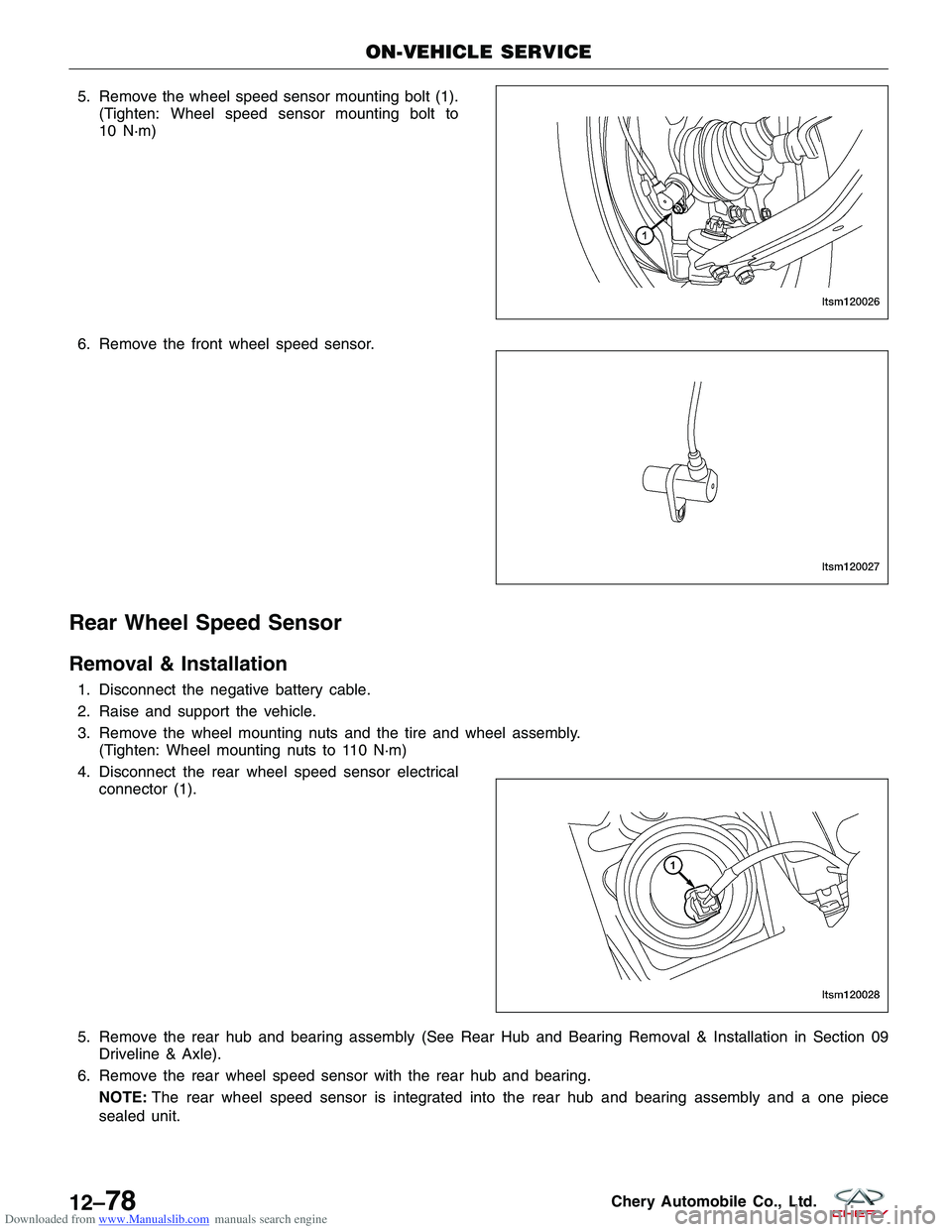
Downloaded from www.Manualslib.com manuals search engine 5. Remove the wheel speed sensor mounting bolt (1).(Tighten: Wheel speed sensor mounting bolt to
10 N·m)
6. Remove the front wheel speed sensor.
Rear Wheel Speed Sensor
Removal & Installation
1. Disconnect the negative battery cable.
2. Raise and support the vehicle.
3. Remove the wheel mounting nuts and the tire and wheel assembly. (Tighten: Wheel mounting nuts to 110 N·m)
4. Disconnect the rear wheel speed sensor electrical connector (1).
5. Remove the rear hub and bearing assembly (See Rear Hub and Bearing Removal & Installation in Section 09 Driveline & Axle).
6. Remove the rear wheel speed sensor with the rear hub and bearing. NOTE: The rear wheel speed sensor is integrated into the rear hub and bearing assembly and a one piece
sealed unit.
ON-VEHICLE SERVICE
LTSM120026
LTSM120027
LTSM120028
12–78Chery Automobile Co., Ltd.
Page 1485 of 1903
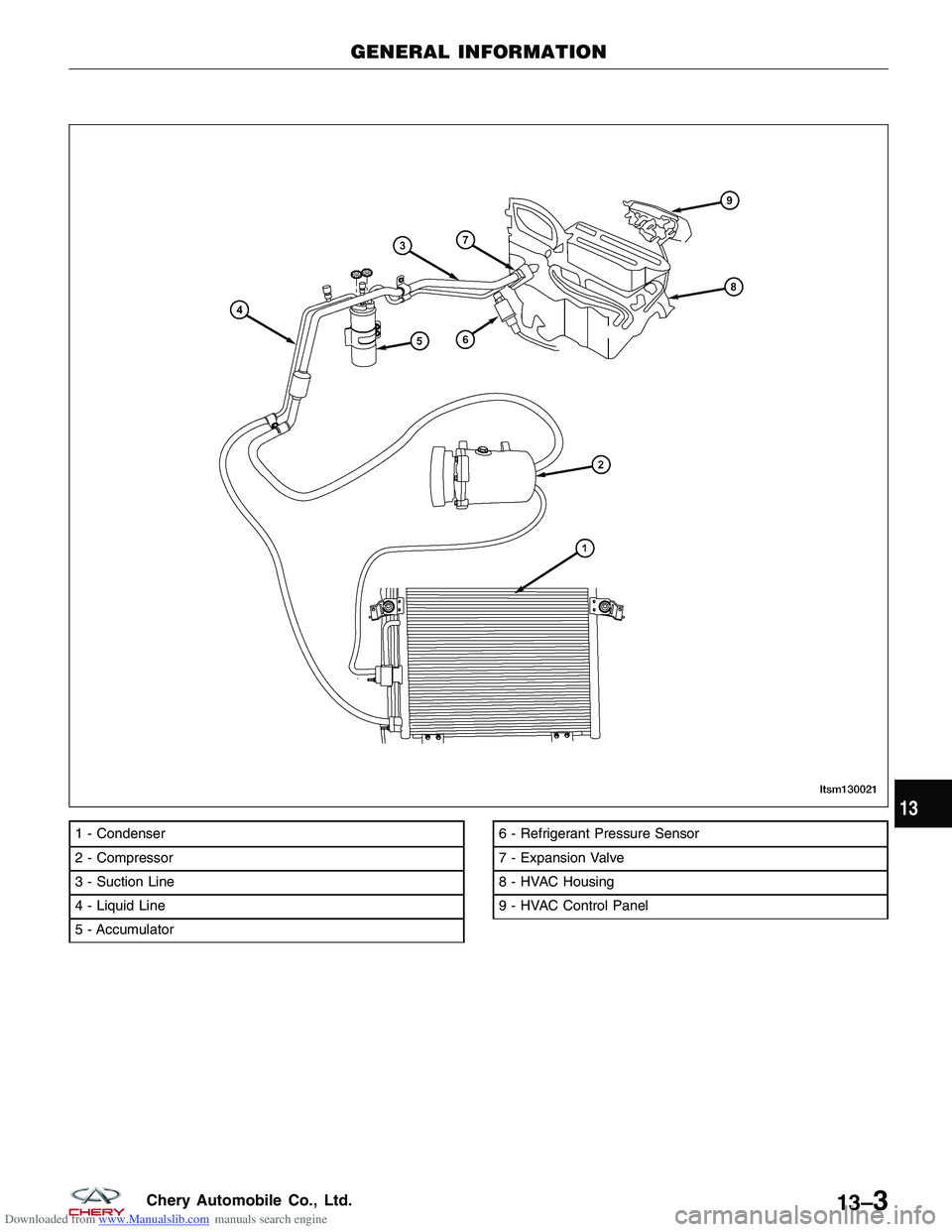
Downloaded from www.Manualslib.com manuals search engine 1 - Condenser
2 - Compressor
3 - Suction Line
4 - Liquid Line
5 - Accumulator6 - Refrigerant Pressure Sensor
7 - Expansion Valve
8 - HVAC Housing
9 - HVAC Control Panel
GENERAL INFORMATION
LTSM130021
13
13–3Chery Automobile Co., Ltd.
Page 1494 of 1903
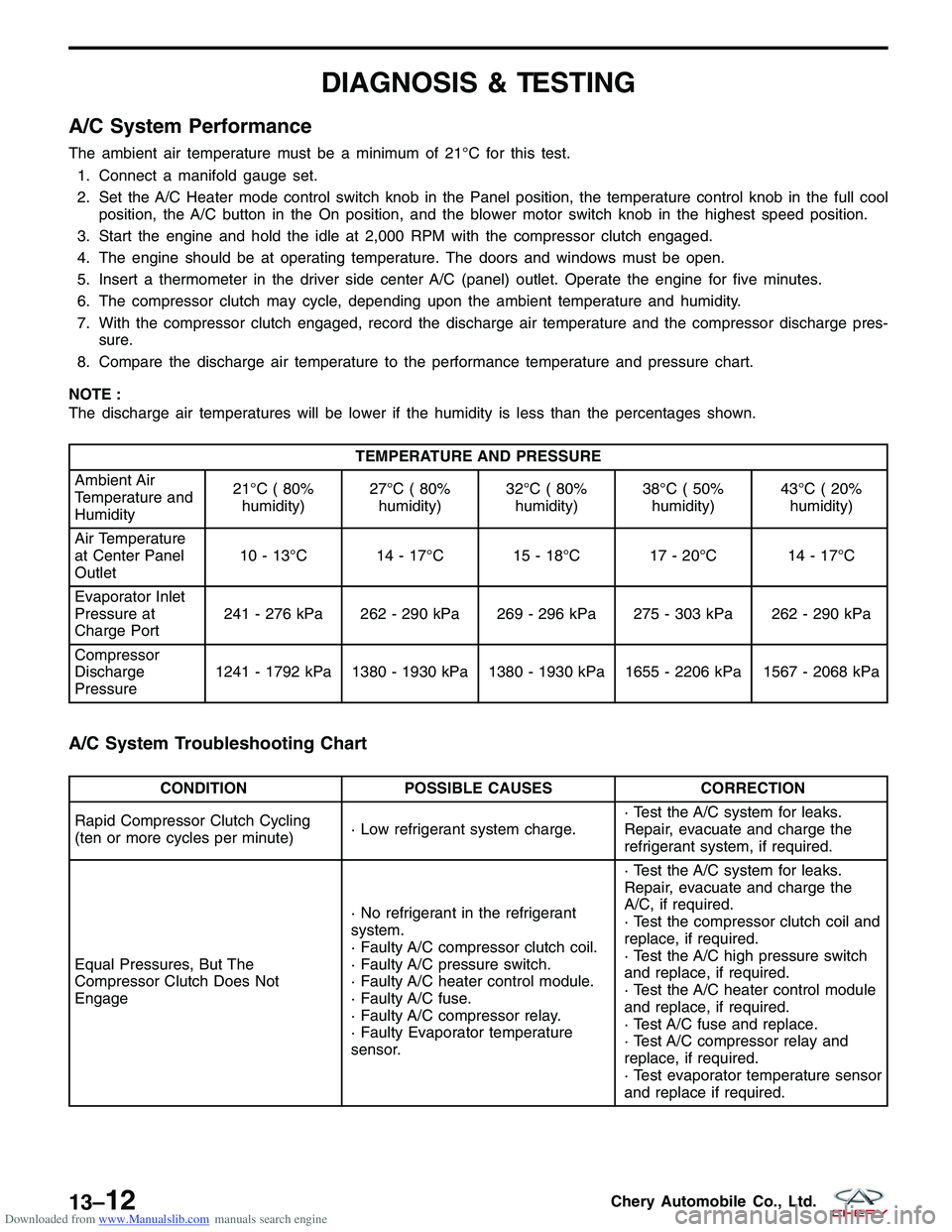
Downloaded from www.Manualslib.com manuals search engine DIAGNOSIS & TESTING
A/C System Performance
The ambient air temperature must be a minimum of 21°C for this test.1. Connect a manifold gauge set.
2. Set the A/C Heater mode control switch knob in the Panel position, the temperature control knob in the full cool position, the A/C button in the On position, and the blower motor switch knob in the highest speed position.
3. Start the engine and hold the idle at 2,000 RPM with the compressor clutch engaged.
4. The engine should be at operating temperature. The doors and windows must be open.
5. Insert a thermometer in the driver side center A/C (panel) outlet. Operate the engine for five minutes.
6. The compressor clutch may cycle, depending upon the ambient temperature and humidity.
7. With the compressor clutch engaged, record the discharge air temperature and the compressor discharge pres- sure.
8. Compare the discharge air temperature to the performance temperature and pressure chart.
NOTE :
The discharge air temperatures will be lower if the humidity is less than the percentages shown.
TEMPERATURE AND PRESSURE
Ambient Air
Temperature and
Humidity 21°C ( 80%
humidity) 27°C ( 80%
humidity) 32°C ( 80%
humidity) 38°C ( 50%
humidity) 43°C ( 20%
humidity)
Air Temperature
at Center Panel
Outlet 10 - 13°C 14 - 17°C 15 - 18°C 17 - 20°C 14 - 17°C
Evaporator Inlet
Pressure at
Charge Port 241 - 276 kPa 262 - 290 kPa 269 - 296 kPa 275 - 303 kPa 262 - 290 kPa
Compressor
Discharge
Pressure 1241 - 1792 kPa 1380 - 1930 kPa 1380 - 1930 kPa 1655 - 2206 kPa 1567 - 2068 kPa
A/C System Troubleshooting Chart
CONDITION
POSSIBLE CAUSES CORRECTION
Rapid Compressor Clutch Cycling
(ten or more cycles per minute) · Low refrigerant system charge.· Test the A/C system for leaks.
Repair, evacuate and charge the
refrigerant system, if required.
Equal Pressures, But The
Compressor Clutch Does Not
Engage · No refrigerant in the refrigerant
system.
· Faulty A/C compressor clutch coil.
· Faulty A/C pressure switch.
· Faulty A/C heater control module.
· Faulty A/C fuse.
· Faulty A/C compressor relay.
· Faulty Evaporator temperature
sensor.· Test the A/C system for leaks.
Repair, evacuate and charge the
A/C, if required.
· Test the compressor clutch coil and
replace, if required.
· Test the A/C high pressure switch
and replace, if required.
· Test the A/C heater control module
and replace, if required.
· Test A/C fuse and replace.
· Test A/C compressor relay and
replace, if required.
· Test evaporator temperature sensor
and replace if required.
13–12Chery Automobile Co., Ltd.
Page 1537 of 1903
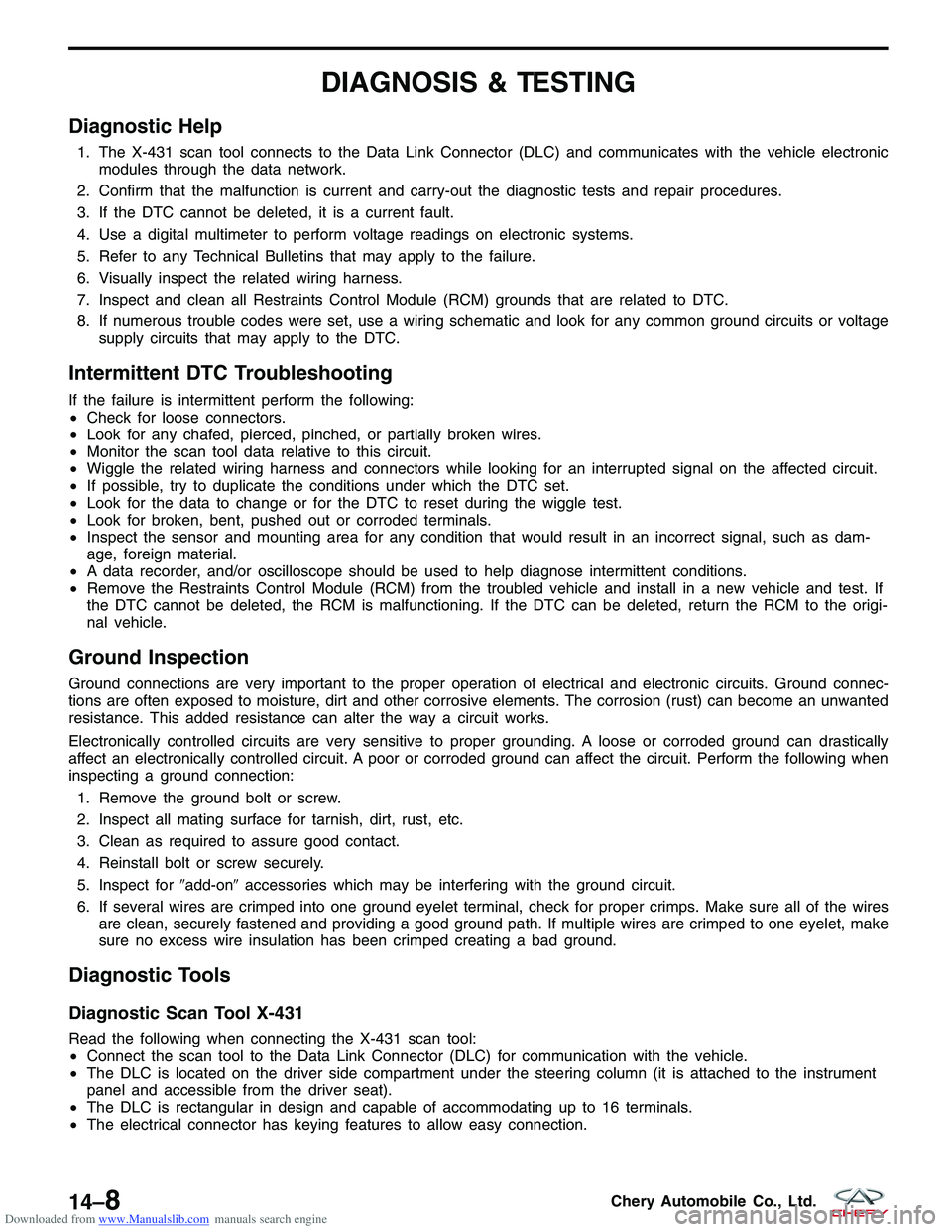
Downloaded from www.Manualslib.com manuals search engine DIAGNOSIS & TESTING
Diagnostic Help
1. The X-431 scan tool connects to the Data Link Connector (DLC) and communicates with the vehicle electronicmodules through the data network.
2. Confirm that the malfunction is current and carry-out the diagnostic tests and repair procedures.
3. If the DTC cannot be deleted, it is a current fault.
4. Use a digital multimeter to perform voltage readings on electronic systems.
5. Refer to any Technical Bulletins that may apply to the failure.
6. Visually inspect the related wiring harness.
7. Inspect and clean all Restraints Control Module (RCM) grounds that are related to DTC.
8. If numerous trouble codes were set, use a wiring schematic and look for any common ground circuits or voltage supply circuits that may apply to the DTC.
Intermittent DTC Troubleshooting
If the failure is intermittent perform the following:
•Check for loose connectors.
• Look for any chafed, pierced, pinched, or partially broken wires.
• Monitor the scan tool data relative to this circuit.
• Wiggle the related wiring harness and connectors while looking for an interrupted signal on the affected circuit.
• If possible, try to duplicate the conditions under which the DTC set.
• Look for the data to change or for the DTC to reset during the wiggle test.
• Look for broken, bent, pushed out or corroded terminals.
• Inspect the sensor and mounting area for any condition that would result in an incorrect signal, such as dam-
age, foreign material.
• A data recorder, and/or oscilloscope should be used to help diagnose intermittent conditions.
• Remove the Restraints Control Module (RCM) from the troubled vehicle and install in a new vehicle and test. If
the DTC cannot be deleted, the RCM is malfunctioning. If the DTC can be deleted, return the RCM to the origi-
nal vehicle.
Ground Inspection
Ground connections are very important to the proper operation of electrical and electronic circuits. Ground connec-
tions are often exposed to moisture, dirt and other corrosive elements. The corrosion (rust) can become an unwanted
resistance. This added resistance can alter the way a circuit works.
Electronically controlled circuits are very sensitive to proper grounding. A loose or corroded ground can drastically
affect an electronically controlled circuit. A poor or corroded ground can affect the circuit. Perform the following when
inspecting a ground connection:
1. Remove the ground bolt or screw.
2. Inspect all mating surface for tarnish, dirt, rust, etc.
3. Clean as required to assure good contact.
4. Reinstall bolt or screw securely.
5. Inspect for add-onaccessories which may be interfering with the ground circuit.
6. If several wires are crimped into one ground eyelet terminal, check for proper crimps. Make sure all of the wires are clean, securely fastened and providing a good ground path. If multiple wires are crimped to one eyelet, make
sure no excess wire insulation has been crimped creating a bad ground.
Diagnostic Tools
Diagnostic Scan Tool X-431
Read the following when connecting the X-431 scan tool:
•Connect the scan tool to the Data Link Connector (DLC) for communication with the vehicle.
• The DLC is located on the driver side compartment under the steering column (it is attached to the instrument
panel and accessible from the driver seat).
• The DLC is rectangular in design and capable of accommodating up to 16 terminals.
• The electrical connector has keying features to allow easy connection.
14–8Chery Automobile Co., Ltd.
Page 1586 of 1903
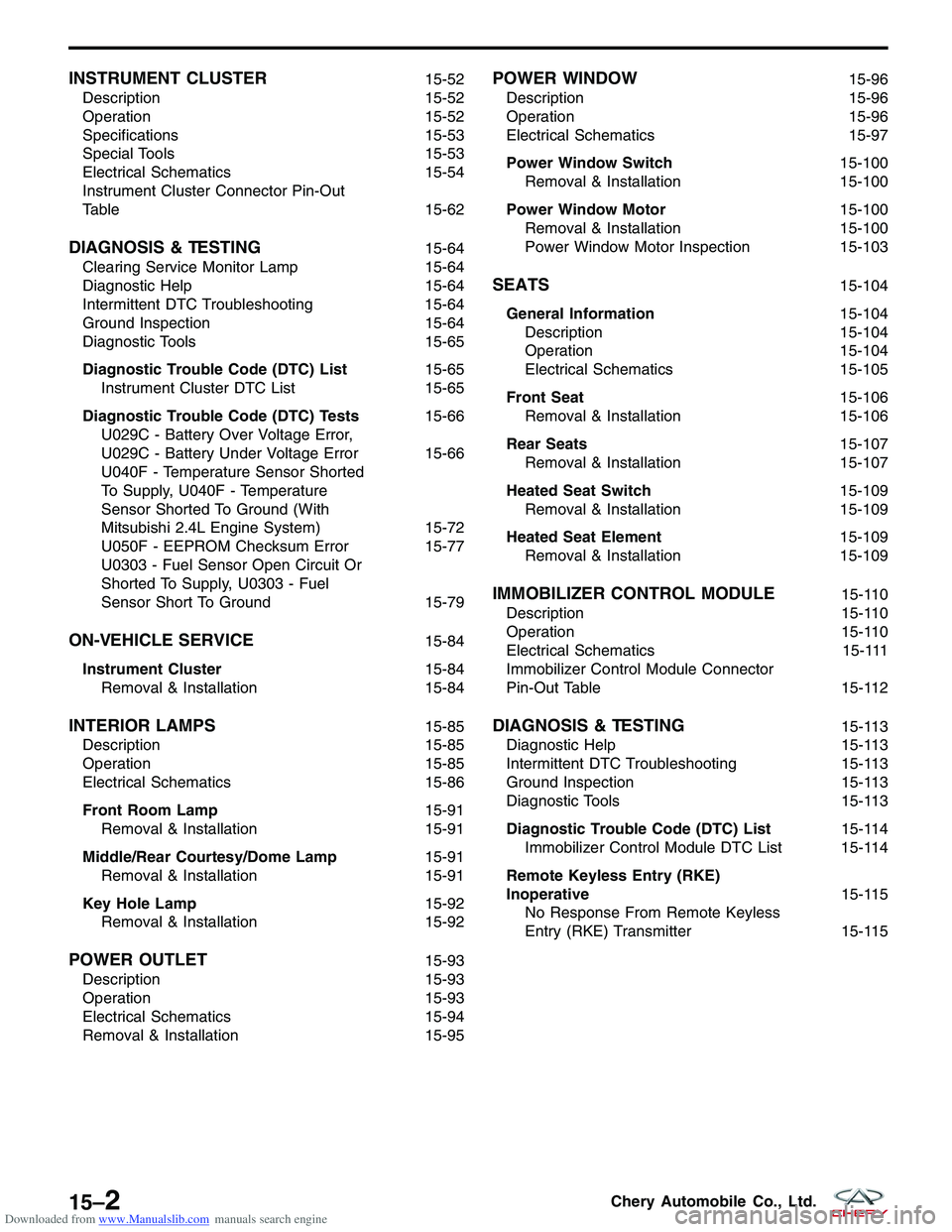
Downloaded from www.Manualslib.com manuals search engine INSTRUMENT CLUSTER15-52
Description 15-52
Operation 15-52
Specifications 15-53
Special Tools 15-53
Electrical Schematics 15-54
Instrument Cluster Connector Pin-Out
Table 15-62
DIAGNOSIS & TESTING15-64
Clearing Service Monitor Lamp 15-64
Diagnostic Help 15-64
Intermittent DTC Troubleshooting 15-64
Ground Inspection 15-64
Diagnostic Tools 15-65
Diagnostic Trouble Code (DTC) List 15-65
Instrument Cluster DTC List 15-65
Diagnostic Trouble Code (DTC) Tests 15-66
U029C - Battery Over Voltage Error,
U029C - Battery Under Voltage Error 15-66
U040F - Temperature Sensor Shorted
To Supply, U040F - Temperature
Sensor Shorted To Ground (With
Mitsubishi 2.4L Engine System) 15-72
U050F - EEPROM Checksum Error 15-77
U0303 - Fuel Sensor Open Circuit Or
Shorted To Supply, U0303 - Fuel
Sensor Short To Ground 15-79
ON-VEHICLE SERVICE15-84
Instrument Cluster 15-84
Removal & Installation 15-84
INTERIOR LAMPS15-85
Description 15-85
Operation 15-85
Electrical Schematics 15-86
Front Room Lamp 15-91
Removal & Installation 15-91
Middle/Rear Courtesy/Dome Lamp 15-91
Removal & Installation 15-91
Key Hole Lamp 15-92
Removal & Installation 15-92
POWER OUTLET15-93
Description 15-93
Operation 15-93
Electrical Schematics 15-94
Removal & Installation 15-95
POWER WINDOW15-96
Description 15-96
Operation 15-96
Electrical Schematics 15-97
Power Window Switch 15-100
Removal & Installation 15-100
Power Window Motor 15-100
Removal & Installation 15-100
Power Window Motor Inspection 15-103
SEATS15-104
General Information 15-104
Description 15-104
Operation 15-104
Electrical Schematics 15-105
Front Seat 15-106
Removal & Installation 15-106
Rear Seats 15-107
Removal & Installation 15-107
Heated Seat Switch 15-109
Removal & Installation 15-109
Heated Seat Element 15-109
Removal & Installation 15-109
IMMOBILIZER CONTROL MODULE15-110
Description 15-110
Operation 15-110
Electrical Schematics 15-111
Immobilizer Control Module Connector
Pin-Out Table 15-112
DIAGNOSIS & TESTING15-113
Diagnostic Help 15-113
Intermittent DTC Troubleshooting 15-113
Ground Inspection 15-113
Diagnostic Tools 15-113
Diagnostic Trouble Code (DTC) List 15-114
Immobilizer Control Module DTC List 15-114
Remote Keyless Entry (RKE)
Inoperative 15-115
No Response From Remote Keyless
Entry (RKE) Transmitter 15-115
15–2Chery Automobile Co., Ltd.
Page 1603 of 1903
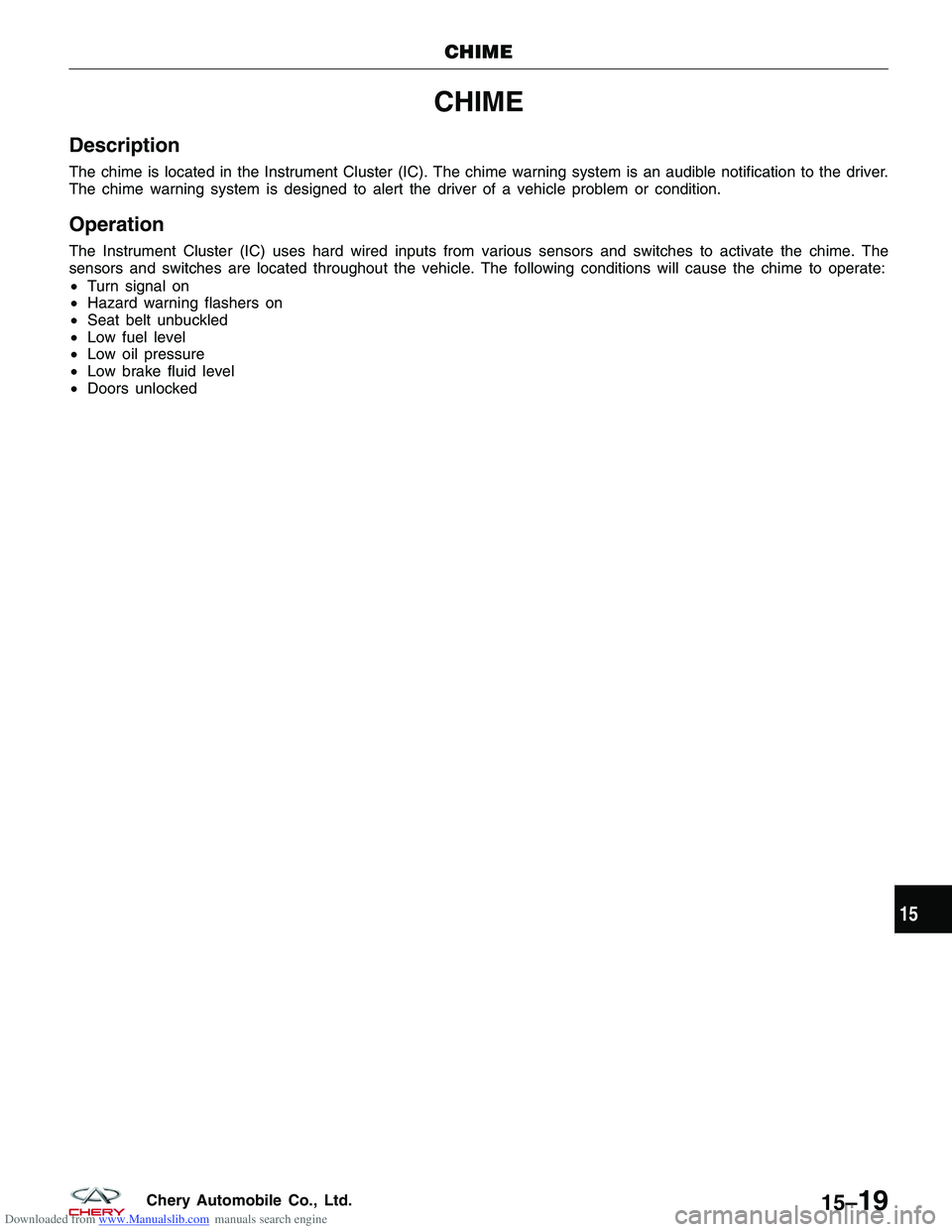
Downloaded from www.Manualslib.com manuals search engine CHIME
Description
The chime is located in the Instrument Cluster (IC). The chime warning system is an audible notification to the driver.
The chime warning system is designed to alert the driver of a vehicle problem or condition.
Operation
The Instrument Cluster (IC) uses hard wired inputs from various sensors and switches to activate the chime. The
sensors and switches are located throughout the vehicle. The following conditions will cause the chime to operate:
•Turn signal on
• Hazard warning flashers on
• Seat belt unbuckled
• Low fuel level
• Low oil pressure
• Low brake fluid level
• Doors unlocked
CHIME
15
15–19Chery Automobile Co., Ltd.
Page 1622 of 1903
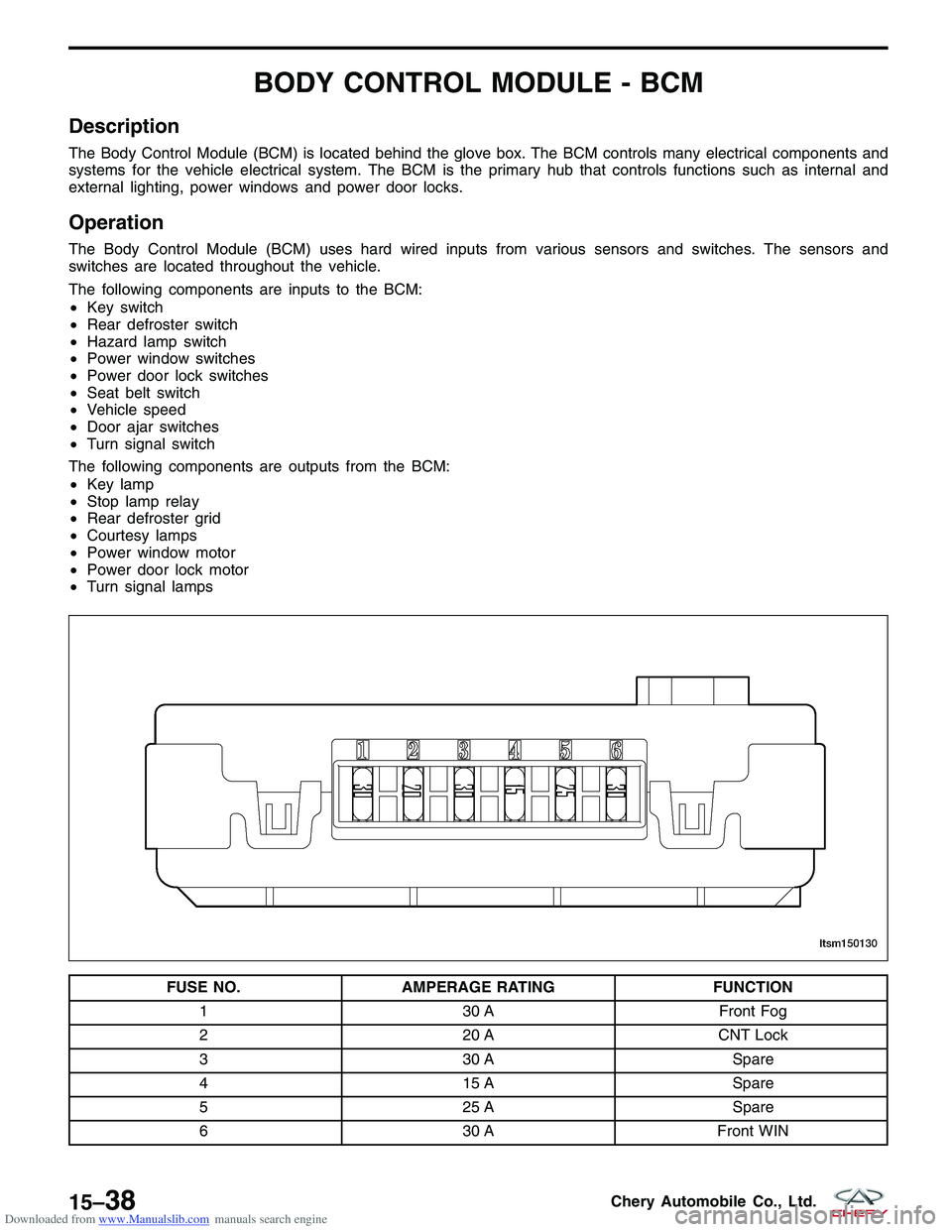
Downloaded from www.Manualslib.com manuals search engine BODY CONTROL MODULE - BCM
Description
The Body Control Module (BCM) is located behind the glove box. The BCM controls many electrical components and
systems for the vehicle electrical system. The BCM is the primary hub that controls functions such as internal and
external lighting, power windows and power door locks.
Operation
The Body Control Module (BCM) uses hard wired inputs from various sensors and switches. The sensors and
switches are located throughout the vehicle.
The following components are inputs to the BCM:
•Key switch
• Rear defroster switch
• Hazard lamp switch
• Power window switches
• Power door lock switches
• Seat belt switch
• Vehicle speed
• Door ajar switches
• Turn signal switch
The following components are outputs from the BCM:
• Key lamp
• Stop lamp relay
• Rear defroster grid
• Courtesy lamps
• Power window motor
• Power door lock motor
• Turn signal lamps
FUSE NO. AMPERAGE RATING FUNCTION
1 30 AFront Fog
2 20 ACNT Lock
3 30 A Spare
4 15 A Spare
5 25 A Spare
6 30 AFront WIN
LTSM150130
15–38Chery Automobile Co., Ltd.
Page 1636 of 1903
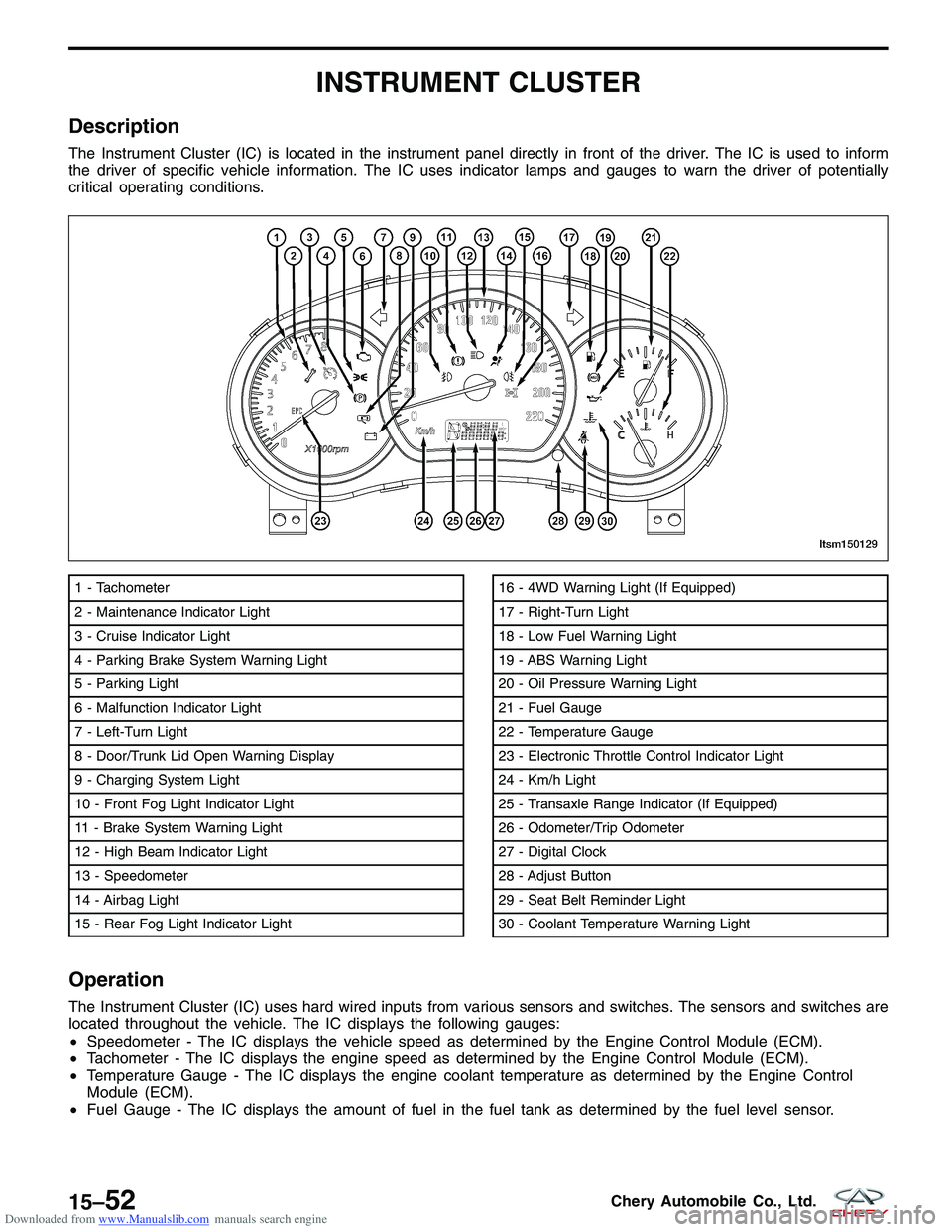
Downloaded from www.Manualslib.com manuals search engine INSTRUMENT CLUSTER
Description
The Instrument Cluster (IC) is located in the instrument panel directly in front of the driver. The IC is used to inform
the driver of specific vehicle information. The IC uses indicator lamps and gauges to warn the driver of potentially
critical operating conditions.
Operation
The Instrument Cluster (IC) uses hard wired inputs from various sensors and switches. The sensors and switches are
located throughout the vehicle. The IC displays the following gauges:
•Speedometer - The IC displays the vehicle speed as determined by the Engine Control Module (ECM).
• Tachometer - The IC displays the engine speed as determined by the Engine Control Module (ECM).
• Temperature Gauge - The IC displays the engine coolant temperature as determined by the Engine Control
Module (ECM).
• Fuel Gauge - The IC displays the amount of fuel in the fuel tank as determined by the fuel level sensor.
1 - Tachometer
2 - Maintenance Indicator Light
3 - Cruise Indicator Light
4 - Parking Brake System Warning Light
5 - Parking Light
6 - Malfunction Indicator Light
7 - Left-Turn Light
8 - Door/Trunk Lid Open Warning Display
9 - Charging System Light
10 - Front Fog Light Indicator Light
11 - Brake System Warning Light
12 - High Beam Indicator Light
13 - Speedometer
14 - Airbag Light
15 - Rear Fog Light Indicator Light16 - 4WD Warning Light (If Equipped)
17 - Right-Turn Light
18 - Low Fuel Warning Light
19 - ABS Warning Light
20 - Oil Pressure Warning Light
21 - Fuel Gauge
22 - Temperature Gauge
23 - Electronic Throttle Control Indicator Light
24 - Km/h Light
25 - Transaxle Range Indicator (If Equipped)
26 - Odometer/Trip Odometer
27 - Digital Clock
28 - Adjust Button
29 - Seat Belt Reminder Light
30 - Coolant Temperature Warning Light
LTSM150129
15–52Chery Automobile Co., Ltd.