CHEVROLET PLYMOUTH ACCLAIM 1993 Service Manual
Manufacturer: CHEVROLET, Model Year: 1993, Model line: PLYMOUTH ACCLAIM, Model: CHEVROLET PLYMOUTH ACCLAIM 1993Pages: 2438, PDF Size: 74.98 MB
Page 731 of 2438
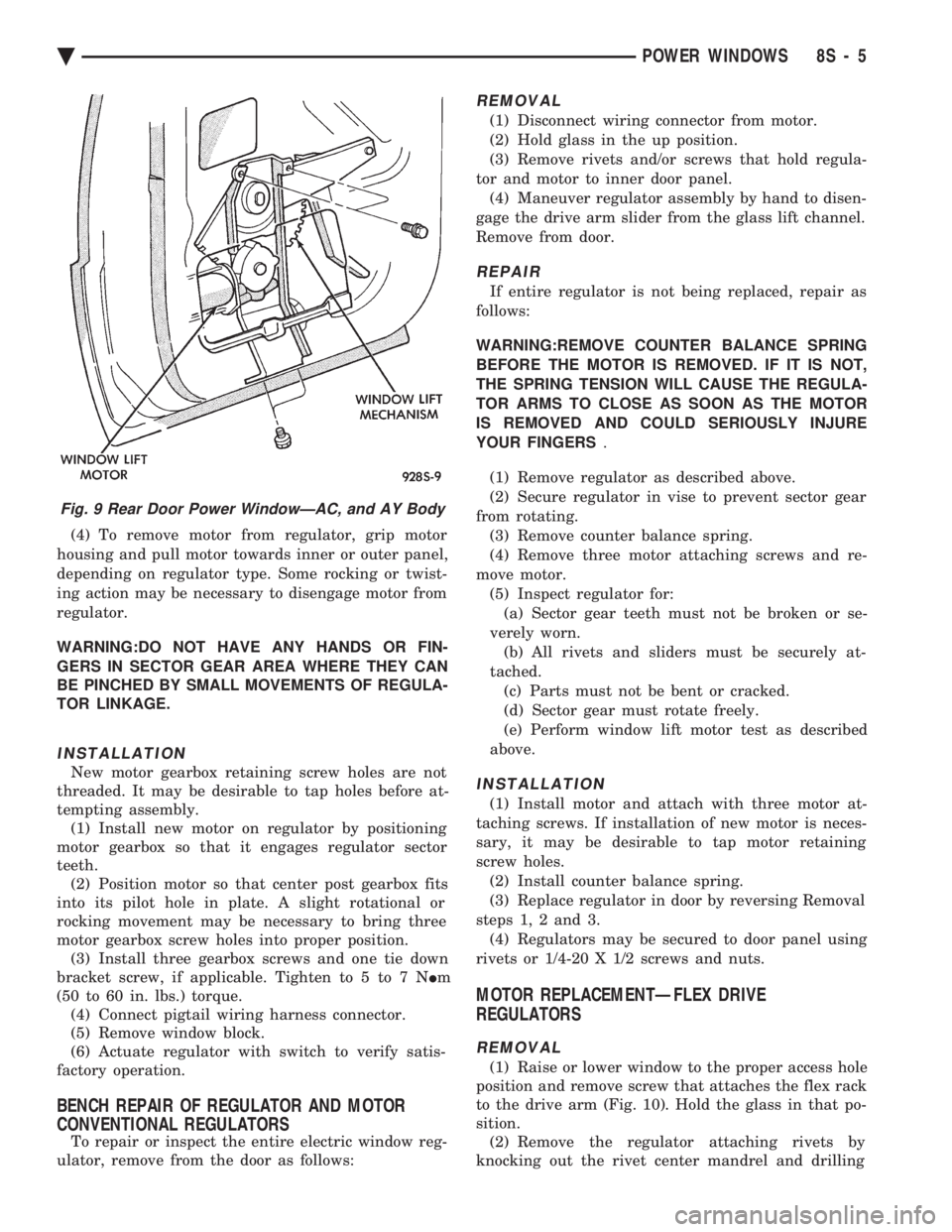
(4) To remove motor from regulator, grip motor
housing and pull motor towards inner or outer panel,
depending on regulator type. Some rocking or twist-
ing action may be necessary to disengage motor from
regulator.
WARNING:DO NOT HAVE ANY HANDS OR FIN-
GERS IN SECTOR GEAR AREA WHERE THEY CAN
BE PINCHED BY SMALL MOVEMENTS OF REGULA-
TOR LINKAGE.
INSTALLATION
New motor gearbox retaining screw holes are not
threaded. It may be desirable to tap holes before at-
tempting assembly. (1) Install new motor on regulator by positioning
motor gearbox so that it engages regulator sector
teeth. (2) Position motor so that center post gearbox fits
into its pilot hole in plate. A slight rotational or
rocking movement may be necessary to bring three
motor gearbox screw holes into proper position. (3) Install three gearbox screws and one tie down
bracket screw, if applicable. Tighten to 5 to 7 N Im
(50 to 60 in. lbs.) torque. (4) Connect pigtail wiring harness connector.
(5) Remove window block.
(6) Actuate regulator with switch to verify satis-
factory operation.
BENCH REPAIR OF REGULATOR AND MOTOR
CONVENTIONAL REGULATORS
To repair or inspect the entire electric window reg-
ulator, remove from the door as follows:
REMOVAL
(1) Disconnect wiring connector from motor.
(2) Hold glass in the up position.
(3) Remove rivets and/or screws that hold regula-
tor and motor to inner door panel. (4) Maneuver regulator assembly by hand to disen-
gage the drive arm slider from the glass lift channel.
Remove from door.
REPAIR
If entire regulator is not being replaced, repair as
follows:
WARNING:REMOVE COUNTER BALANCE SPRING
BEFORE THE MOTOR IS REMOVED. IF IT IS NOT,
THE SPRING TENSION WILL CAUSE THE REGULA-
TOR ARMS TO CLOSE AS SOON AS THE MOTOR
IS REMOVED AND COULD SERIOUSLY INJURE
YOUR FINGERS .
(1) Remove regulator as described above.
(2) Secure regulator in vise to prevent sector gear
from rotating. (3) Remove counter balance spring.
(4) Remove three motor attaching screws and re-
move motor. (5) Inspect regulator for:(a) Sector gear teeth must not be broken or se-
verely worn. (b) All rivets and sliders must be securely at-
tached. (c) Parts must not be bent or cracked.
(d) Sector gear must rotate freely.
(e) Perform window lift motor test as described
above.
INSTALLATION
(1) Install motor and attach with three motor at-
taching screws. If installation of new motor is neces-
sary, it may be desirable to tap motor retaining
screw holes. (2) Install counter balance spring.
(3) Replace regulator in door by reversing Removal
steps 1, 2 and 3. (4) Regulators may be secured to door panel using
rivets or 1/4-20 X 1/2 screws and nuts.
MOTOR REPLACEMENTÐFLEX DRIVE
REGULATORS
REMOVAL
(1) Raise or lower window to the proper access hole
position and remove screw that attaches the flex rack
to the drive arm (Fig. 10). Hold the glass in that po-
sition. (2) Remove the regulator attaching rivets by
knocking out the rivet center mandrel and drilling
Fig. 9 Rear Door Power WindowÐAC, and AY Body
Ä POWER WINDOWS 8S - 5
Page 732 of 2438
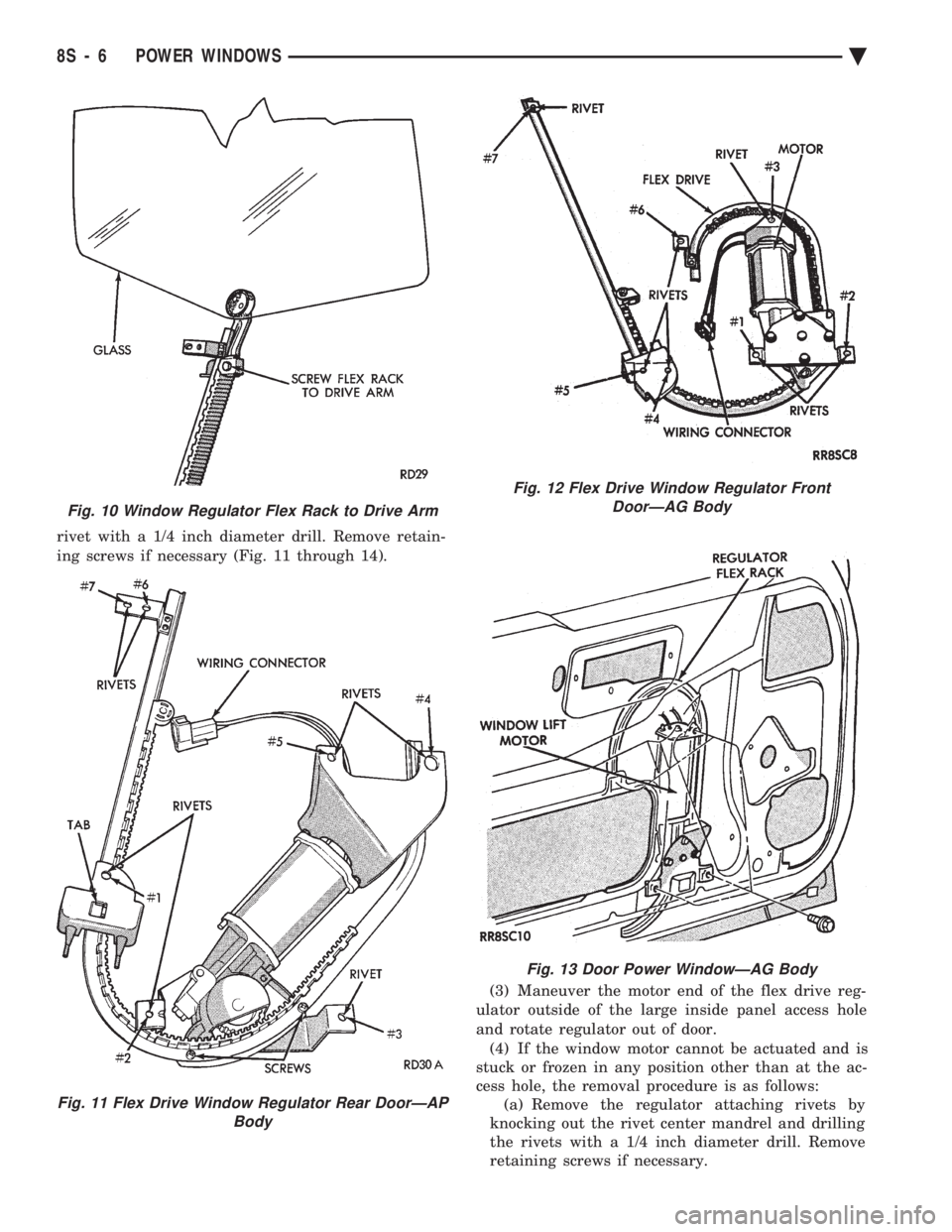
rivet with a 1/4 inch diameter drill. Remove retain-
ing screws if necessary (Fig. 11 through 14). (3) Maneuver the motor end of the flex drive reg-
ulator outside of the large inside panel access hole
and rotate regulator out of door. (4) If the window motor cannot be actuated and is
stuck or frozen in any position other than at the ac-
cess hole, the removal procedure is as follows: (a) Remove the regulator attaching rivets by
knocking out the rivet center mandrel and drilling
the rivets with a 1/4 inch diameter drill. Remove
retaining screws if necessary.
Fig. 10 Window Regulator Flex Rack to Drive Arm
Fig. 11 Flex Drive Window Regulator Rear DoorÐAP Body
Fig. 12 Flex Drive Window Regulator FrontDoorÐAG Body
Fig. 13 Door Power WindowÐAG Body
8S - 6 POWER WINDOWS Ä
Page 733 of 2438
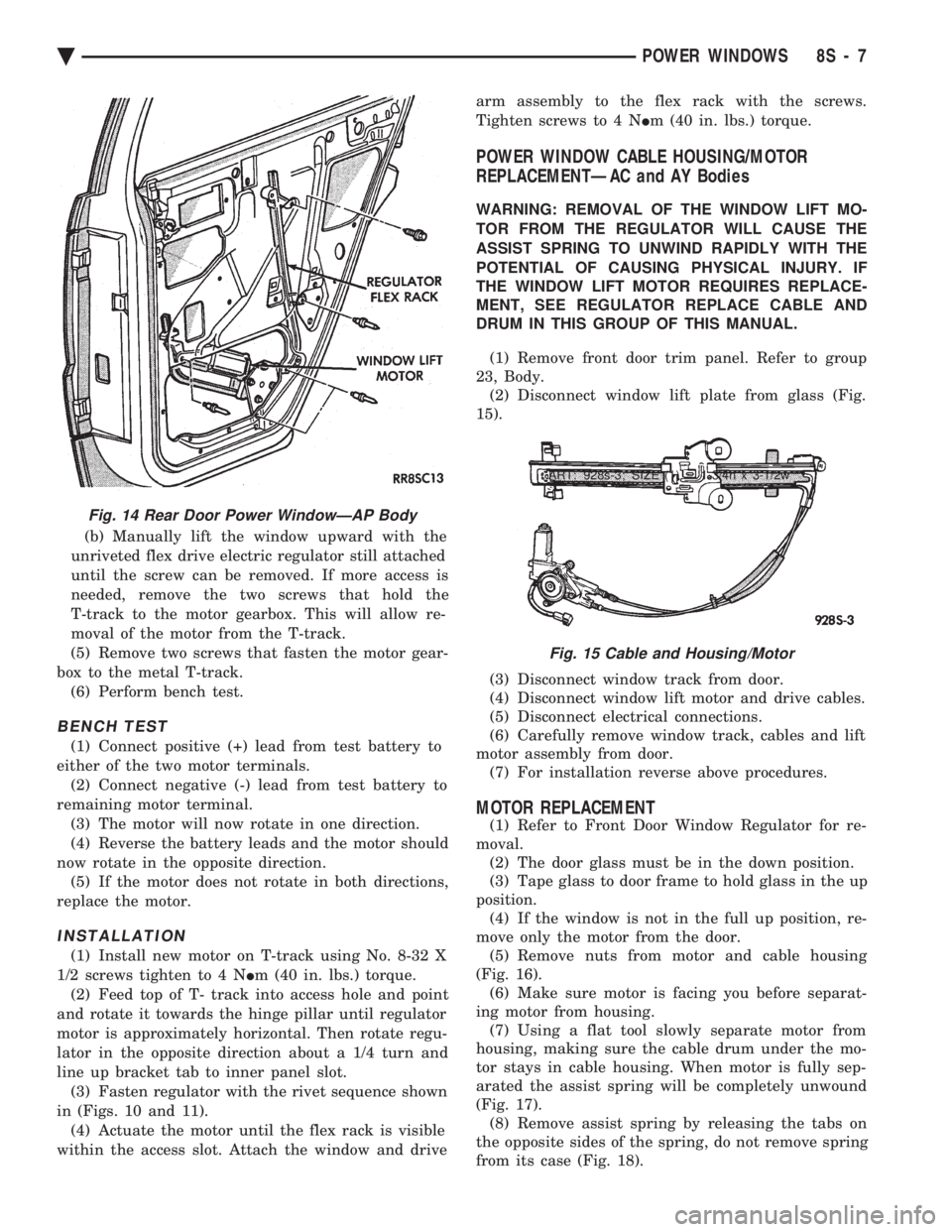
(b) Manually lift the window upward with the
unriveted flex drive electric regulator still attached
until the screw can be removed. If more access is
needed, remove the two screws that hold the
T-track to the motor gearbox. This will allow re-
moval of the motor from the T-track.
(5) Remove two screws that fasten the motor gear-
box to the metal T-track. (6) Perform bench test.
BENCH TEST
(1) Connect positive (+) lead from test battery to
either of the two motor terminals. (2) Connect negative (-) lead from test battery to
remaining motor terminal. (3) The motor will now rotate in one direction.
(4) Reverse the battery leads and the motor should
now rotate in the opposite direction. (5) If the motor does not rotate in both directions,
replace the motor.
INSTALLATION
(1) Install new motor on T-track using No. 8-32 X
1/2 screws tighten to 4 N Im (40 in. lbs.) torque.
(2) Feed top of T- track into access hole and point
and rotate it towards the hinge pillar until regulator
motor is approximately horizontal. Then rotate regu-
lator in the opposite direction about a 1/4 turn and
line up bracket tab to inner panel slot. (3) Fasten regulator with the rivet sequence shown
in (Figs. 10 and 11). (4) Actuate the motor until the flex rack is visible
within the access slot. Attach the window and drive arm assembly to the flex rack with the screws.
Tighten screws to 4 N Im (40 in. lbs.) torque.
POWER WINDOW CABLE HOUSING/MOTOR
REPLACEMENTÐAC and AY Bodies
WARNING: REMOVAL OF THE WINDOW LIFT MO-
TOR FROM THE REGULATOR WILL CAUSE THE
ASSIST SPRING TO UNWIND RAPIDLY WITH THE
POTENTIAL OF CAUSING PHYSICAL INJURY. IF
THE WINDOW LIFT MOTOR REQUIRES REPLACE-
MENT, SEE REGULATOR REPLACE CABLE AND
DRUM IN THIS GROUP OF THIS MANUAL.
(1) Remove front door trim panel. Refer to group
23, Body. (2) Disconnect window lift plate from glass (Fig.
15).
(3) Disconnect window track from door.
(4) Disconnect window lift motor and drive cables.
(5) Disconnect electrical connections.
(6) Carefully remove window track, cables and lift
motor assembly from door. (7) For installation reverse above procedures.
MOTOR REPLACEMENT
(1) Refer to Front Door Window Regulator for re-
moval. (2) The door glass must be in the down position.
(3) Tape glass to door frame to hold glass in the up
position. (4) If the window is not in the full up position, re-
move only the motor from the door. (5) Remove nuts from motor and cable housing
(Fig. 16). (6) Make sure motor is facing you before separat-
ing motor from housing. (7) Using a flat tool slowly separate motor from
housing, making sure the cable drum under the mo-
tor stays in cable housing. When motor is fully sep-
arated the assist spring will be completely unwound
(Fig. 17). (8) Remove assist spring by releasing the tabs on
the opposite sides of the spring, do not remove spring
from its case (Fig. 18).
Fig. 14 Rear Door Power WindowÐAP Body
ART: 928s-3; SIZE (1) = 1-3/4h x 3-1/2w
Fig. 15 Cable and Housing/Motor
Ä POWER WINDOWS 8S - 7
Page 734 of 2438
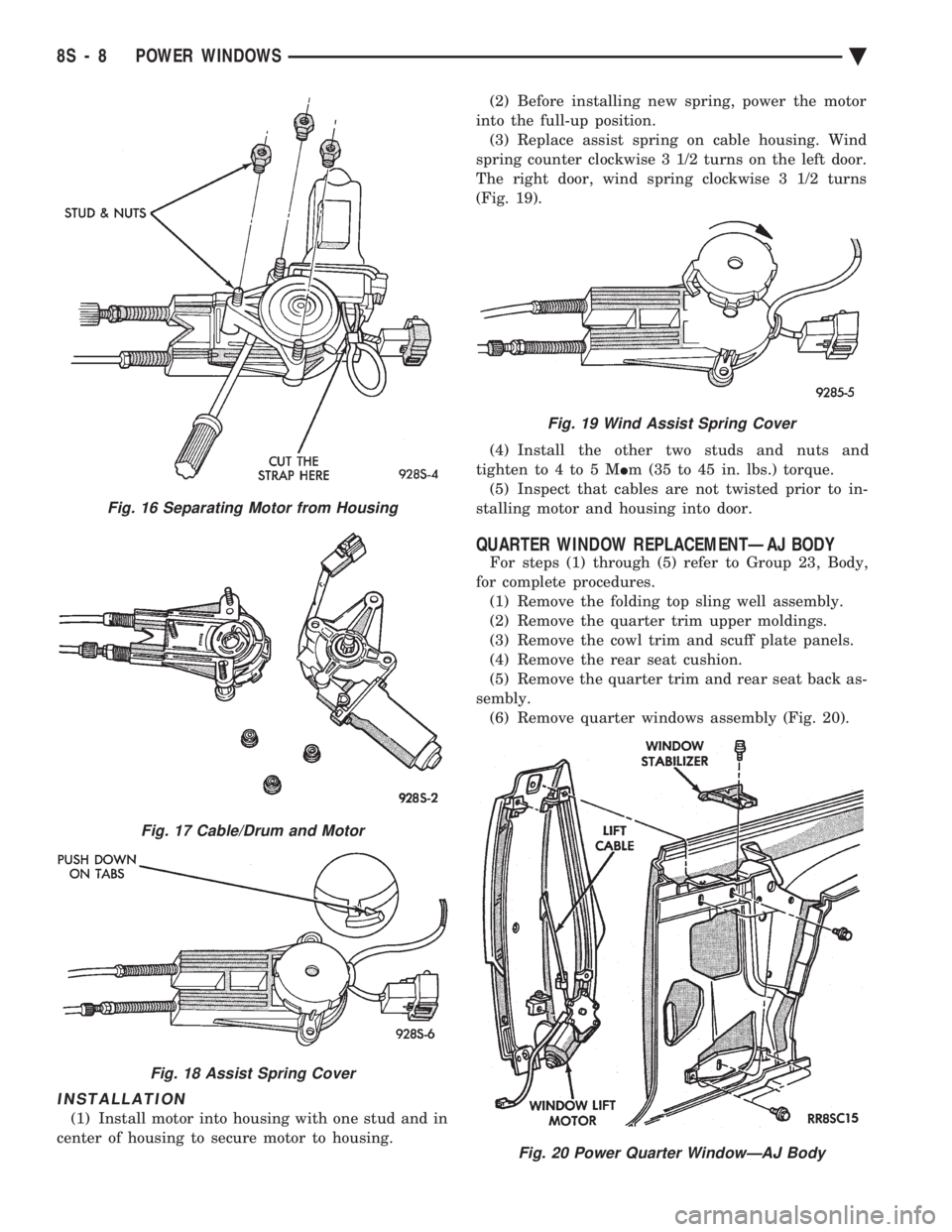
INSTALLATION
(1) Install motor into housing with one stud and in
center of housing to secure motor to housing. (2) Before installing new spring, power the motor
into the full-up position. (3) Replace assist spring on cable housing. Wind
spring counter clockwise 3 1/2 turns on the left door.
The right door, wind spring clockwise 3 1/2 turns
(Fig. 19).
(4) Install the other two studs and nuts and
tighten to 4 to 5 M Im (35 to 45 in. lbs.) torque.
(5) Inspect that cables are not twisted prior to in-
stalling motor and housing into door.
QUARTER WINDOW REPLACEMENTÐAJ BODY
For steps (1) through (5) refer to Group 23, Body,
for complete procedures. (1) Remove the folding top sling well assembly.
(2) Remove the quarter trim upper moldings.
(3) Remove the cowl trim and scuff plate panels.
(4) Remove the rear seat cushion.
(5) Remove the quarter trim and rear seat back as-
sembly. (6) Remove quarter windows assembly (Fig. 20).
Fig. 16 Separating Motor from Housing
Fig. 17 Cable/Drum and Motor
Fig. 18 Assist Spring Cover
Fig. 19 Wind Assist Spring Cover
Fig. 20 Power Quarter WindowÐAJ Body
8S - 8 POWER WINDOWS Ä
Page 735 of 2438
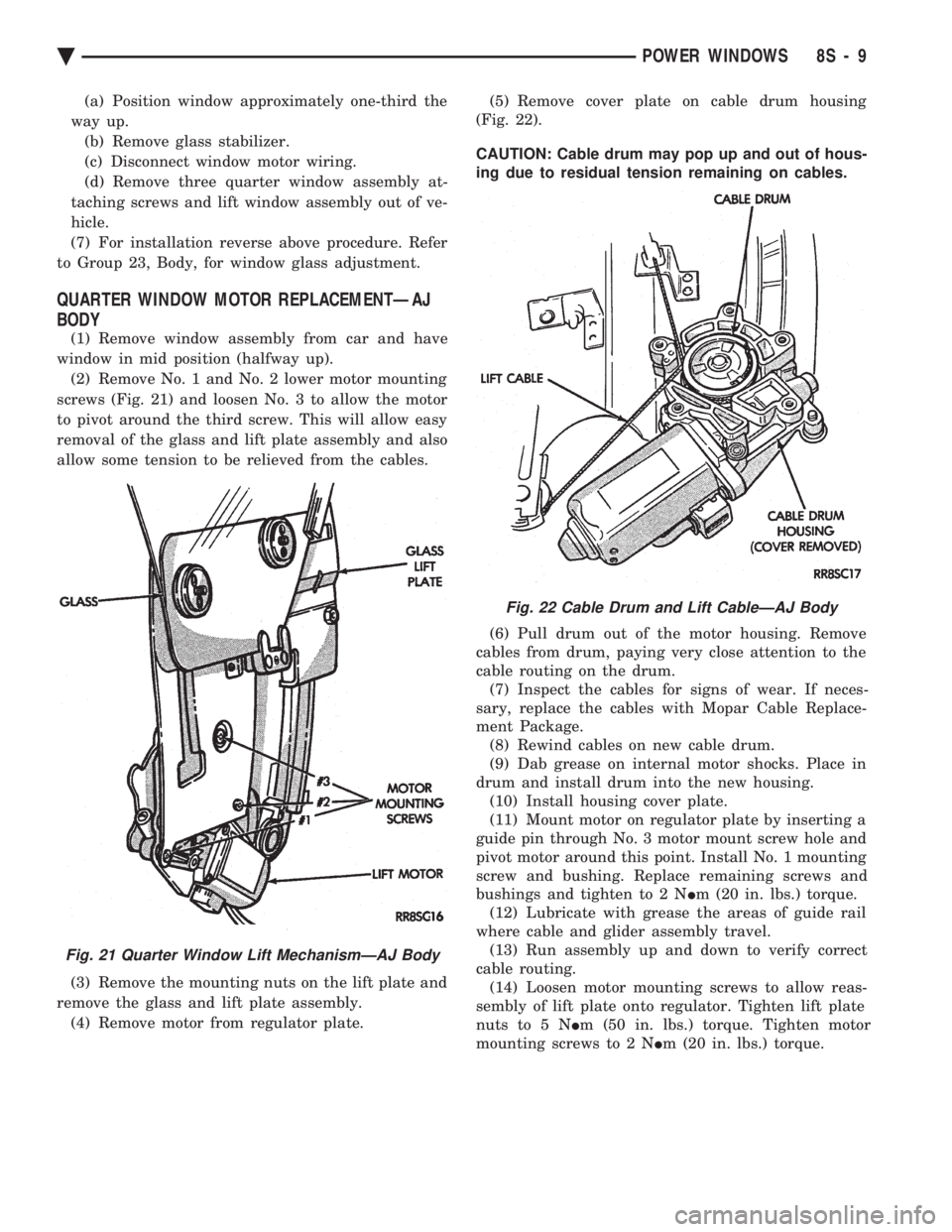
(a) Position window approximately one-third the
way up. (b) Remove glass stabilizer.
(c) Disconnect window motor wiring.
(d) Remove three quarter window assembly at-
taching screws and lift window assembly out of ve-
hicle.
(7) For installation reverse above procedure. Refer
to Group 23, Body, for window glass adjustment.
QUARTER WINDOW MOTOR REPLACEMENTÐAJ
BODY
(1) Remove window assembly from car and have
window in mid position (halfway up). (2) Remove No. 1 and No. 2 lower motor mounting
screws (Fig. 21) and loosen No. 3 to allow the motor
to pivot around the third screw. This will allow easy
removal of the glass and lift plate assembly and also
allow some tension to be relieved from the cables.
(3) Remove the mounting nuts on the lift plate and
remove the glass and lift plate assembly. (4) Remove motor from regulator plate. (5) Remove cover plate on cable drum housing
(Fig. 22).
CAUTION: Cable drum may pop up and out of hous-
ing due to residual tension remaining on cables.
(6) Pull drum out of the motor housing. Remove
cables from drum, paying very close attention to the
cable routing on the drum. (7) Inspect the cables for signs of wear. If neces-
sary, replace the cables with Mopar Cable Replace-
ment Package. (8) Rewind cables on new cable drum.
(9) Dab grease on internal motor shocks. Place in
drum and install drum into the new housing. (10) Install housing cover plate.
(11) Mount motor on regulator plate by inserting a
guide pin through No. 3 motor mount screw hole and
pivot motor around this point. Install No. 1 mounting
screw and bushing. Replace remaining screws and
bushings and tighten to 2 N Im (20 in. lbs.) torque.
(12) Lubricate with grease the areas of guide rail
where cable and glider assembly travel. (13) Run assembly up and down to verify correct
cable routing. (14) Loosen motor mounting screws to allow reas-
sembly of lift plate onto regulator. Tighten lift plate
nuts to 5 N Im (50 in. lbs.) torque. Tighten motor
mounting screws to 2 N Im (20 in. lbs.) torque.
Fig. 21 Quarter Window Lift MechanismÐAJ Body
Fig. 22 Cable Drum and Lift CableÐAJ Body
Ä POWER WINDOWS 8S - 9
Page 736 of 2438
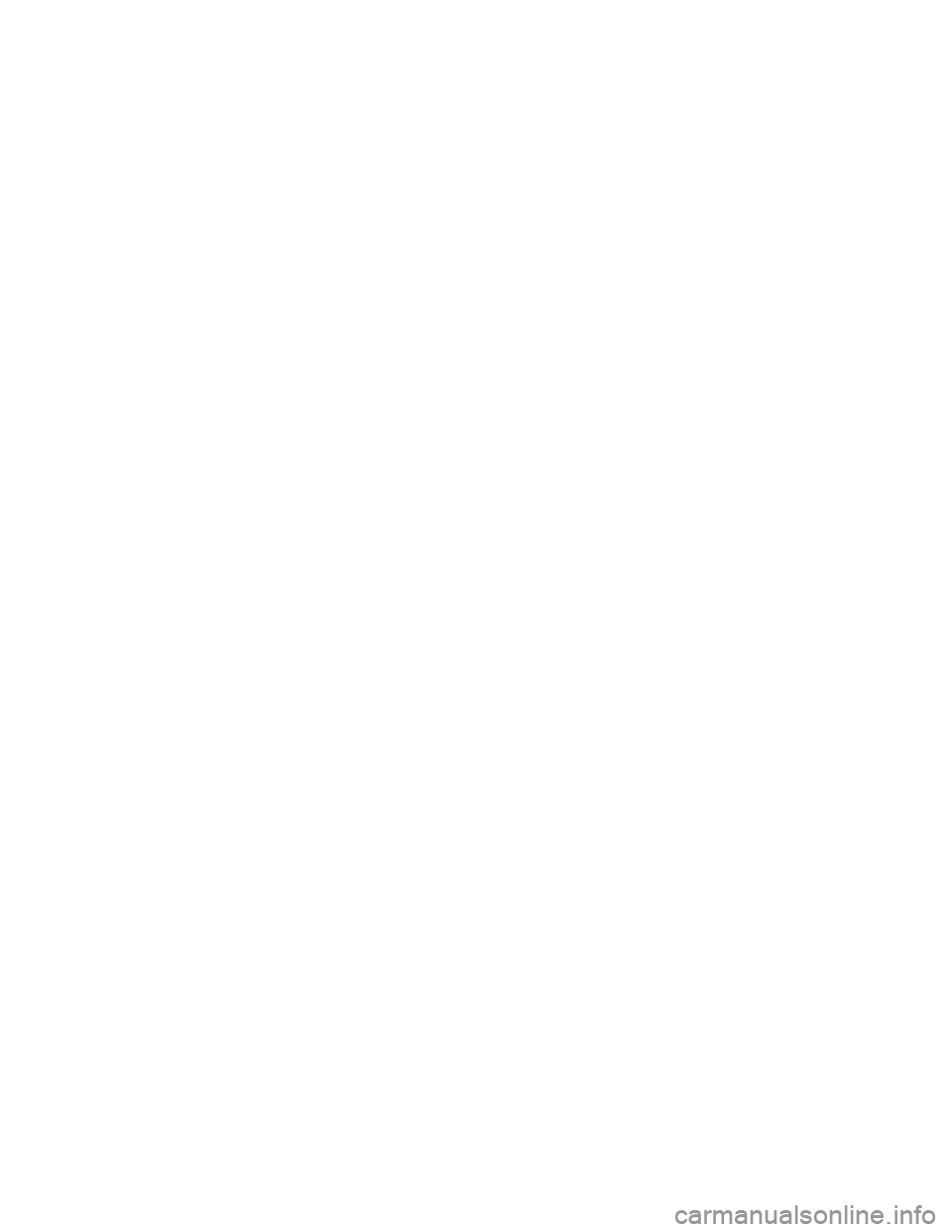
Page 737 of 2438
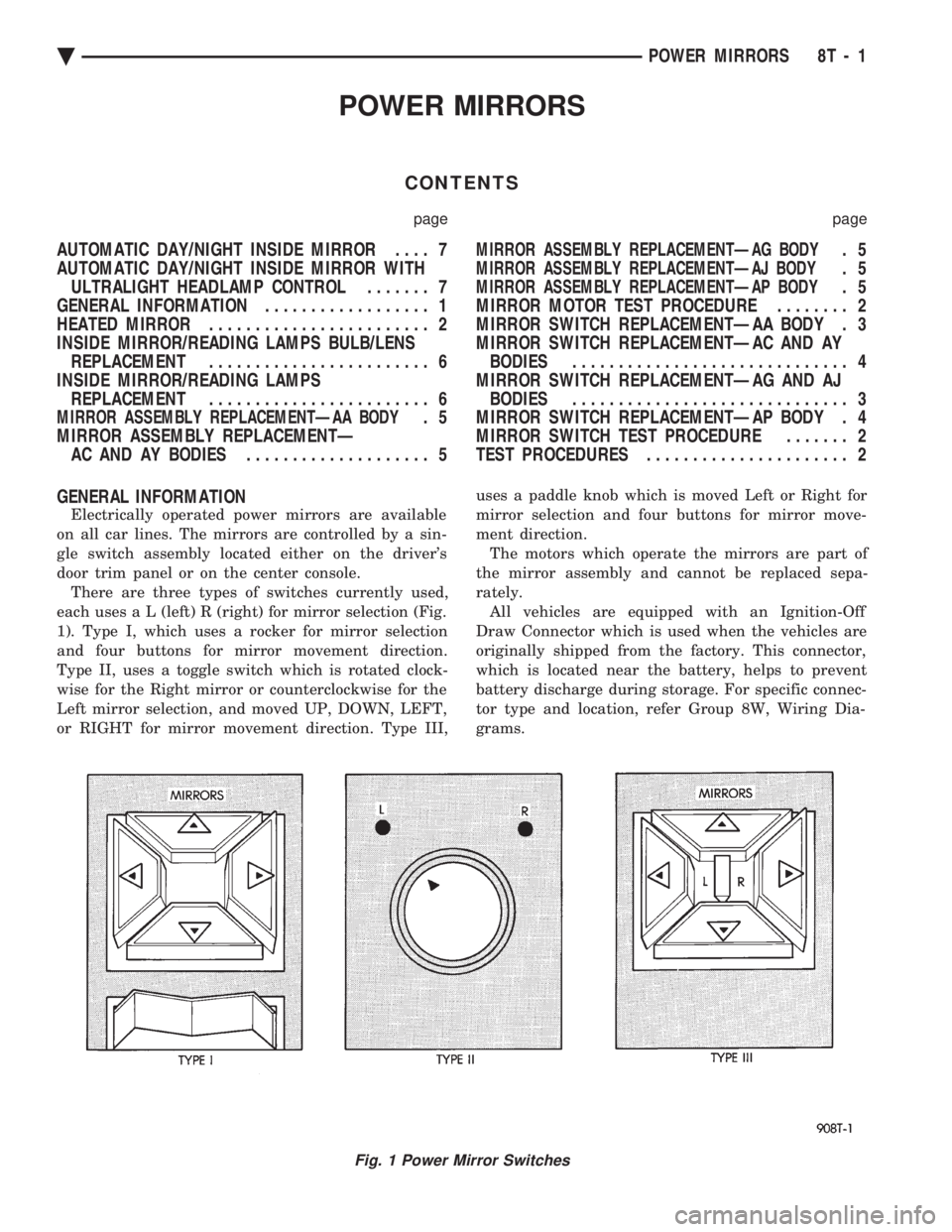
POWER MIRRORS
CONTENTS
page page
AUTOMATIC DAY/NIGHT INSIDE MIRROR .... 7
AUTOMATIC DAY/NIGHT INSIDE MIRROR WITH ULTRALIGHT HEADLAMP CONTROL ....... 7
GENERAL INFORMATION .................. 1
HEATED MIRROR ........................ 2
INSIDE MIRROR/READING LAMPS BULB/LENS REPLACEMENT ........................ 6
INSIDE MIRROR/READING LAMPS REPLACEMENT ........................ 6
MIRROR ASSEMBLY REPLACEMENTÐAA BODY.5
MIRROR ASSEMBLY REPLACEMENTÐ AC AND AY BODIES .................... 5
MIRROR ASSEMBLY REPLACEMENTÐAG BODY.5
MIRROR ASSEMBLY REPLACEMENTÐAJ BODY.5
MIRROR ASSEMBLY REPLACEMENTÐAP BODY.5
MIRROR MOTOR TEST PROCEDURE ........ 2
MIRROR SWITCH REPLACEMENTÐAA BODY . 3
MIRROR SWITCH REPLACEMENTÐAC AND AY BODIES .............................. 4
MIRROR SWITCH REPLACEMENTÐAG AND AJ BODIES .............................. 3
MIRROR SWITCH REPLACEMENTÐAP BODY . 4
MIRROR SWITCH TEST PROCEDURE ....... 2
TEST PROCEDURES ...................... 2
GENERAL INFORMATION
Electrically operated power mirrors are available
on all car lines. The mirrors are controlled by a sin-
gle switch assembly located either on the driver's
door trim panel or on the center console. There are three types of switches currently used,
each use s a L (left) R (right) for mirror selection (Fig.
1). Type I, which uses a rocker for mirror selection
and four buttons for mirror movement direction.
Type II, uses a toggle switch which is rotated clock-
wise for the Right mirror or counterclockwise for the
Left mirror selection, and moved UP, DOWN, LEFT,
or RIGHT for mirror movement direction. Type III, uses a paddle knob which is moved Left or Right for
mirror selection and four buttons for mirror move-
ment direction.
The motors which operate the mirrors are part of
the mirror assembly and cannot be replaced sepa-
rately. All vehicles are equipped with an Ignition-Off
Draw Connector which is used when the vehicles are
originally shipped from the factory. This connector,
which is located near the battery, helps to prevent
battery discharge during storage. For specific connec-
tor type and location, refer Group 8W, Wiring Dia-
grams.
Fig. 1 Power Mirror Switches
Ä POWER MIRRORS 8T - 1
Page 738 of 2438
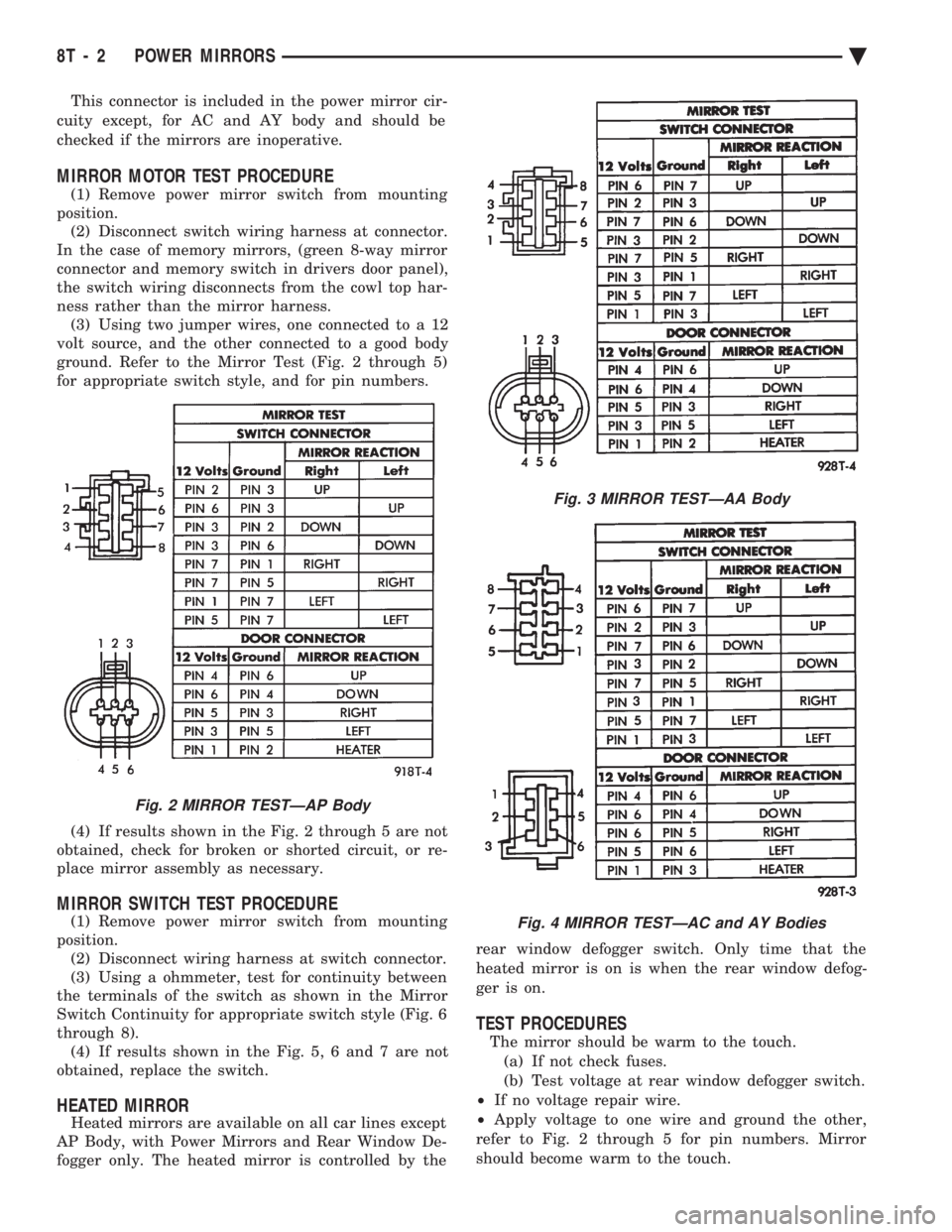
This connector is included in the power mirror cir-
cuity except, for AC and AY body and should be
checked if the mirrors are inoperative.
MIRROR MOTOR TEST PROCEDURE
(1) Remove power mirror switch from mounting
position. (2) Disconnect switch wiring harness at connector.
In the case of memory mirrors, (green 8-way mirror
connector and memory switch in drivers door panel),
the switch wiring disconnects from the cowl top har-
ness rather than the mirror harness. (3) Using two jumper wires, one connected to a 12
volt source, and the other connected to a good body
ground. Refer to the Mirror Test (Fig. 2 through 5)
for appropriate switch style, and for pin numbers.
(4) If results shown in the Fig. 2 through 5 are not
obtained, check for broken or shorted circuit, or re-
place mirror assembly as necessary.
MIRROR SWITCH TEST PROCEDURE
(1) Remove power mirror switch from mounting
position. (2) Disconnect wiring harness at switch connector.
(3) Using a ohmmeter, test for continuity between
the terminals of the switch as shown in the Mirror
Switch Continuity for appropriate switch style (Fig. 6
through 8). (4) If results shown in the Fig. 5, 6 and 7 are not
obtained, replace the switch.
HEATED MIRROR
Heated mirrors are available on all car lines except
AP Body, with Power Mirrors and Rear Window De-
fogger only. The heated mirror is controlled by the rear window defogger switch. Only time that the
heated mirror is on is when the rear window defog-
ger is on.
TEST PROCEDURES
The mirror should be warm to the touch. (a) If not check fuses.
(b) Test voltage at rear window defogger switch.
² If no voltage repair wire.
² Apply voltage to one wire and ground the other,
refer to Fig. 2 through 5 for pin numbers. Mirror
should become warm to the touch.
Fig. 2 MIRROR TESTÐAP Body
Fig. 3 MIRROR TESTÐAA Body
Fig. 4 MIRROR TESTÐAC and AY Bodies
8T - 2 POWER MIRRORS Ä
Page 739 of 2438
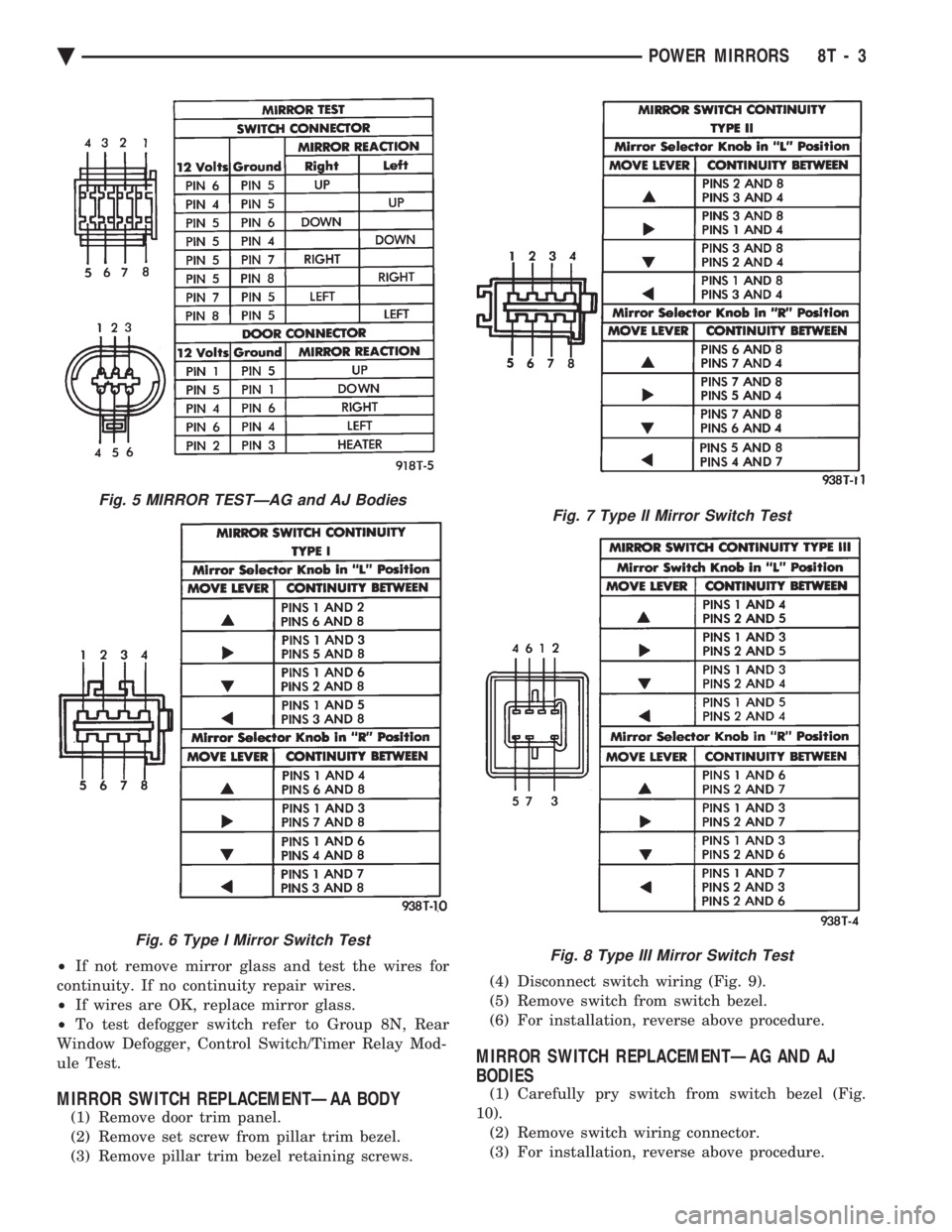
² If not remove mirror glass and test the wires for
continuity. If no continuity repair wires.
² If wires are OK, replace mirror glass.
² To test defogger switch refer to Group 8N, Rear
Window Defogger, Control Switch/Timer Relay Mod-
ule Test.
MIRROR SWITCH REPLACEMENTÐAA BODY
(1) Remove door trim panel.
(2) Remove set screw from pillar trim bezel.
(3) Remove pillar trim bezel retaining screws. (4) Disconnect switch wiring (Fig. 9).
(5) Remove switch from switch bezel.
(6) For installation, reverse above procedure.
MIRROR SWITCH REPLACEMENTÐAG AND AJ
BODIES
(1) Carefully pry switch from switch bezel (Fig.
10). (2) Remove switch wiring connector.
(3) For installation, reverse above procedure.
Fig. 5 MIRROR TESTÐAG and AJ Bodies
Fig. 6 Type I Mirror Switch Test
Fig. 7 Type II Mirror Switch Test
Fig. 8 Type III Mirror Switch Test
Ä POWER MIRRORS 8T - 3
Page 740 of 2438
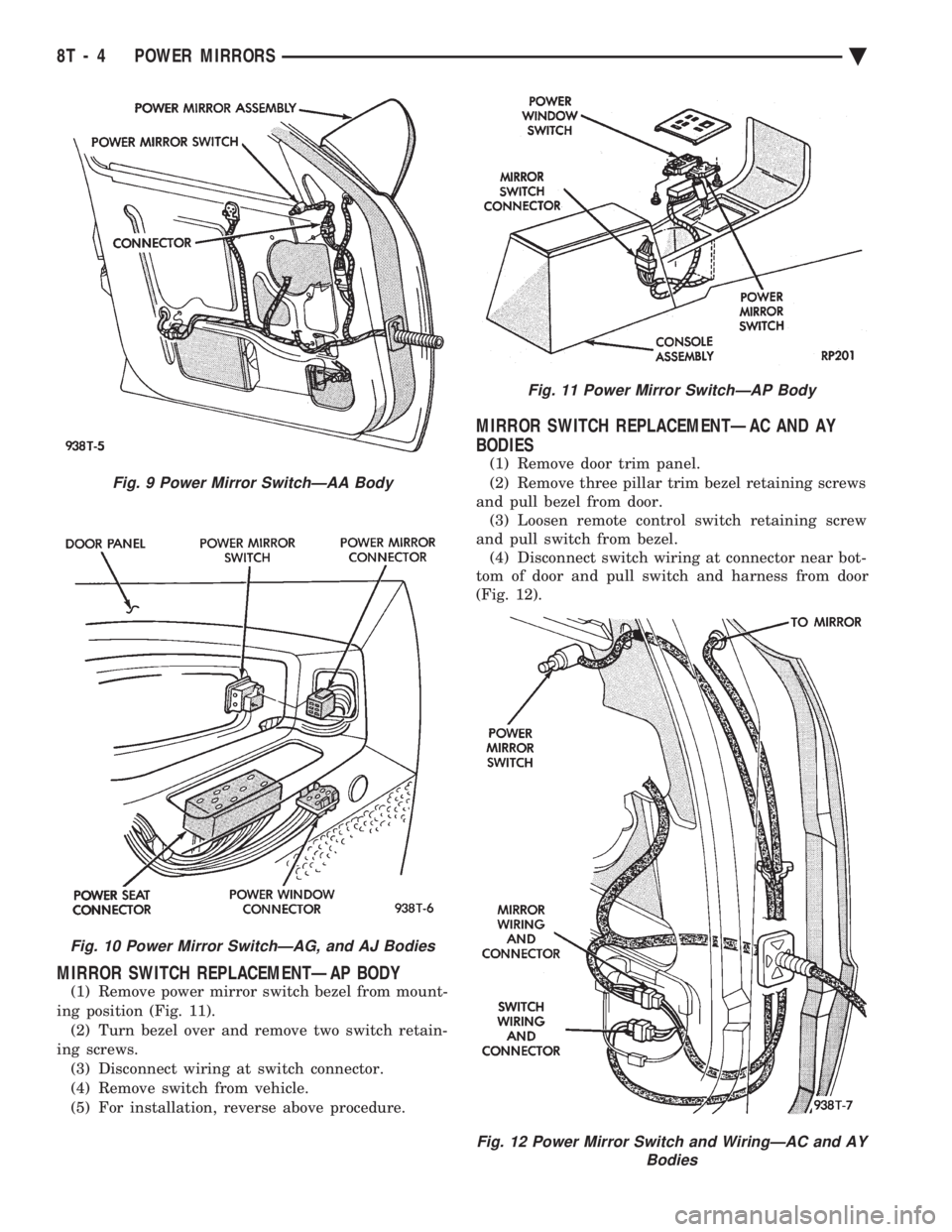
MIRROR SWITCH REPLACEMENTÐAP BODY
(1) Remove power mirror switch bezel from mount-
ing position (Fig. 11). (2) Turn bezel over and remove two switch retain-
ing screws. (3) Disconnect wiring at switch connector.
(4) Remove switch from vehicle.
(5) For installation, reverse above procedure.
MIRROR SWITCH REPLACEMENTÐAC AND AY
BODIES
(1) Remove door trim panel.
(2) Remove three pillar trim bezel retaining screws
and pull bezel from door. (3) Loosen remote control switch retaining screw
and pull switch from bezel. (4) Disconnect switch wiring at connector near bot-
tom of door and pull switch and harness from door
(Fig. 12).
Fig. 9 Power Mirror SwitchÐAA Body
Fig. 10 Power Mirror SwitchÐAG, and AJ Bodies
Fig. 11 Power Mirror SwitchÐAP Body
Fig. 12 Power Mirror Switch and WiringÐAC and AY Bodies
8T - 4 POWER MIRRORS Ä