sensor CHRYSLER CARAVAN 2003 Service Manual
[x] Cancel search | Manufacturer: CHRYSLER, Model Year: 2003, Model line: CARAVAN, Model: CHRYSLER CARAVAN 2003Pages: 2177, PDF Size: 59.81 MB
Page 2118 of 2177
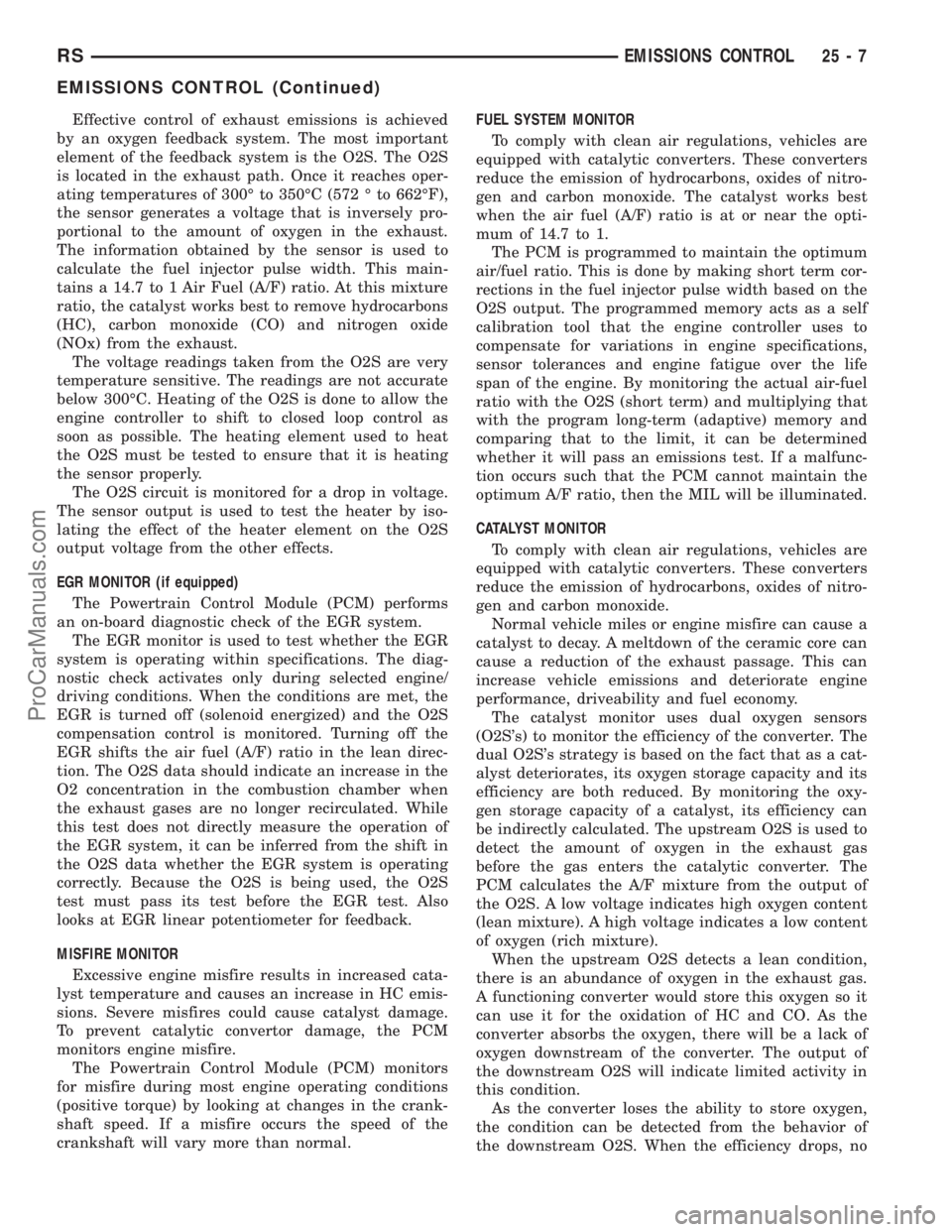
Effective control of exhaust emissions is achieved
by an oxygen feedback system. The most important
element of the feedback system is the O2S. The O2S
is located in the exhaust path. Once it reaches oper-
ating temperatures of 300É to 350ÉC (572 É to 662ÉF),
the sensor generates a voltage that is inversely pro-
portional to the amount of oxygen in the exhaust.
The information obtained by the sensor is used to
calculate the fuel injector pulse width. This main-
tains a 14.7 to 1 Air Fuel (A/F) ratio. At this mixture
ratio, the catalyst works best to remove hydrocarbons
(HC), carbon monoxide (CO) and nitrogen oxide
(NOx) from the exhaust.
The voltage readings taken from the O2S are very
temperature sensitive. The readings are not accurate
below 300ÉC. Heating of the O2S is done to allow the
engine controller to shift to closed loop control as
soon as possible. The heating element used to heat
the O2S must be tested to ensure that it is heating
the sensor properly.
The O2S circuit is monitored for a drop in voltage.
The sensor output is used to test the heater by iso-
lating the effect of the heater element on the O2S
output voltage from the other effects.
EGR MONITOR (if equipped)
The Powertrain Control Module (PCM) performs
an on-board diagnostic check of the EGR system.
The EGR monitor is used to test whether the EGR
system is operating within specifications. The diag-
nostic check activates only during selected engine/
driving conditions. When the conditions are met, the
EGR is turned off (solenoid energized) and the O2S
compensation control is monitored. Turning off the
EGR shifts the air fuel (A/F) ratio in the lean direc-
tion. The O2S data should indicate an increase in the
O2 concentration in the combustion chamber when
the exhaust gases are no longer recirculated. While
this test does not directly measure the operation of
the EGR system, it can be inferred from the shift in
the O2S data whether the EGR system is operating
correctly. Because the O2S is being used, the O2S
test must pass its test before the EGR test. Also
looks at EGR linear potentiometer for feedback.
MISFIRE MONITOR
Excessive engine misfire results in increased cata-
lyst temperature and causes an increase in HC emis-
sions. Severe misfires could cause catalyst damage.
To prevent catalytic convertor damage, the PCM
monitors engine misfire.
The Powertrain Control Module (PCM) monitors
for misfire during most engine operating conditions
(positive torque) by looking at changes in the crank-
shaft speed. If a misfire occurs the speed of the
crankshaft will vary more than normal.FUEL SYSTEM MONITOR
To comply with clean air regulations, vehicles are
equipped with catalytic converters. These converters
reduce the emission of hydrocarbons, oxides of nitro-
gen and carbon monoxide. The catalyst works best
when the air fuel (A/F) ratio is at or near the opti-
mum of 14.7 to 1.
The PCM is programmed to maintain the optimum
air/fuel ratio. This is done by making short term cor-
rections in the fuel injector pulse width based on the
O2S output. The programmed memory acts as a self
calibration tool that the engine controller uses to
compensate for variations in engine specifications,
sensor tolerances and engine fatigue over the life
span of the engine. By monitoring the actual air-fuel
ratio with the O2S (short term) and multiplying that
with the program long-term (adaptive) memory and
comparing that to the limit, it can be determined
whether it will pass an emissions test. If a malfunc-
tion occurs such that the PCM cannot maintain the
optimum A/F ratio, then the MIL will be illuminated.
CATALYST MONITOR
To comply with clean air regulations, vehicles are
equipped with catalytic converters. These converters
reduce the emission of hydrocarbons, oxides of nitro-
gen and carbon monoxide.
Normal vehicle miles or engine misfire can cause a
catalyst to decay. A meltdown of the ceramic core can
cause a reduction of the exhaust passage. This can
increase vehicle emissions and deteriorate engine
performance, driveability and fuel economy.
The catalyst monitor uses dual oxygen sensors
(O2S's) to monitor the efficiency of the converter. The
dual O2S's strategy is based on the fact that as a cat-
alyst deteriorates, its oxygen storage capacity and its
efficiency are both reduced. By monitoring the oxy-
gen storage capacity of a catalyst, its efficiency can
be indirectly calculated. The upstream O2S is used to
detect the amount of oxygen in the exhaust gas
before the gas enters the catalytic converter. The
PCM calculates the A/F mixture from the output of
the O2S. A low voltage indicates high oxygen content
(lean mixture). A high voltage indicates a low content
of oxygen (rich mixture).
When the upstream O2S detects a lean condition,
there is an abundance of oxygen in the exhaust gas.
A functioning converter would store this oxygen so it
can use it for the oxidation of HC and CO. As the
converter absorbs the oxygen, there will be a lack of
oxygen downstream of the converter. The output of
the downstream O2S will indicate limited activity in
this condition.
As the converter loses the ability to store oxygen,
the condition can be detected from the behavior of
the downstream O2S. When the efficiency drops, no
RSEMISSIONS CONTROL25-7
EMISSIONS CONTROL (Continued)
ProCarManuals.com
Page 2119 of 2177
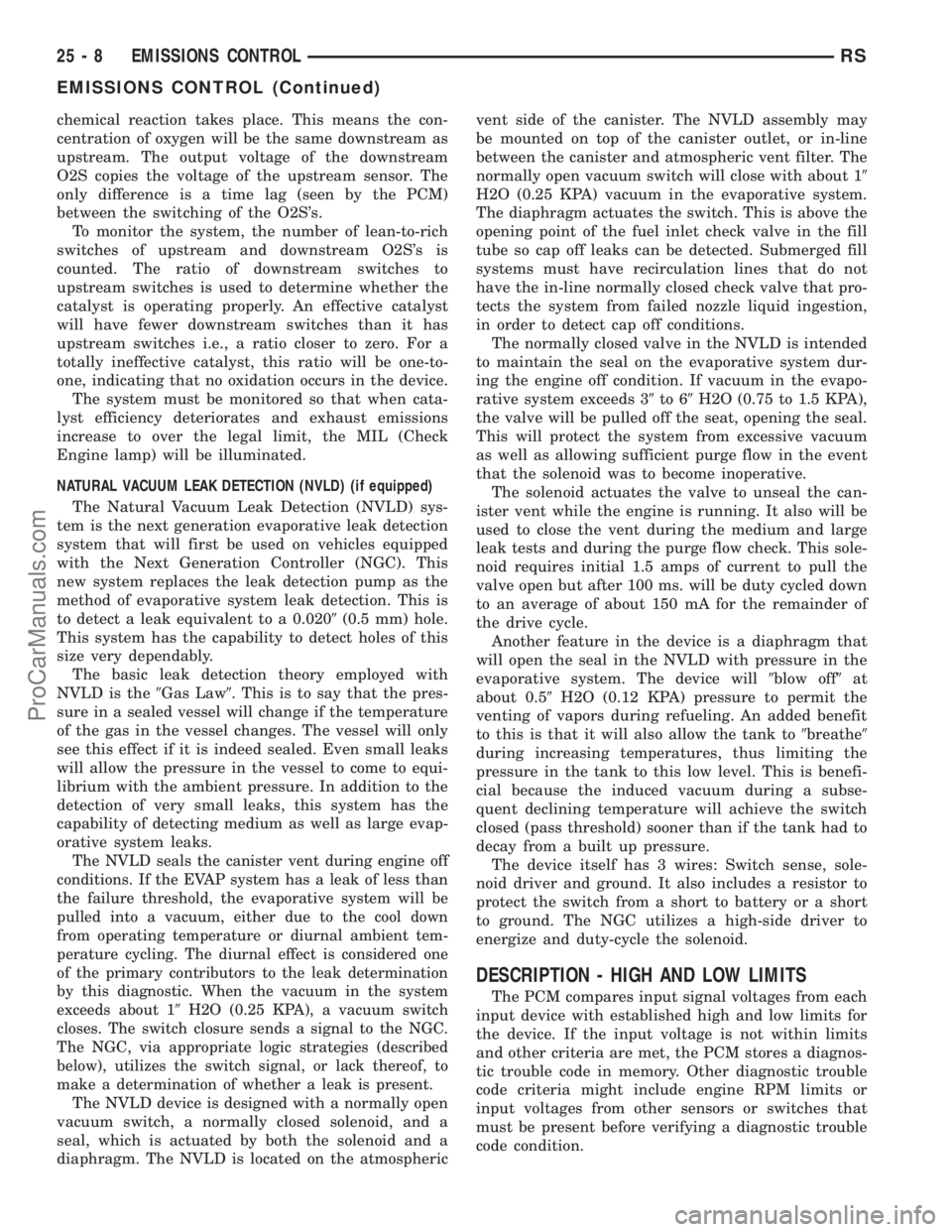
chemical reaction takes place. This means the con-
centration of oxygen will be the same downstream as
upstream. The output voltage of the downstream
O2S copies the voltage of the upstream sensor. The
only difference is a time lag (seen by the PCM)
between the switching of the O2S's.
To monitor the system, the number of lean-to-rich
switches of upstream and downstream O2S's is
counted. The ratio of downstream switches to
upstream switches is used to determine whether the
catalyst is operating properly. An effective catalyst
will have fewer downstream switches than it has
upstream switches i.e., a ratio closer to zero. For a
totally ineffective catalyst, this ratio will be one-to-
one, indicating that no oxidation occurs in the device.
The system must be monitored so that when cata-
lyst efficiency deteriorates and exhaust emissions
increase to over the legal limit, the MIL (Check
Engine lamp) will be illuminated.
NATURAL VACUUM LEAK DETECTION (NVLD) (if equipped)
The Natural Vacuum Leak Detection (NVLD) sys-
tem is the next generation evaporative leak detection
system that will first be used on vehicles equipped
with the Next Generation Controller (NGC). This
new system replaces the leak detection pump as the
method of evaporative system leak detection. This is
to detect a leak equivalent to a 0.0209(0.5 mm) hole.
This system has the capability to detect holes of this
size very dependably.
The basic leak detection theory employed with
NVLD is the9Gas Law9. This is to say that the pres-
sure in a sealed vessel will change if the temperature
of the gas in the vessel changes. The vessel will only
see this effect if it is indeed sealed. Even small leaks
will allow the pressure in the vessel to come to equi-
librium with the ambient pressure. In addition to the
detection of very small leaks, this system has the
capability of detecting medium as well as large evap-
orative system leaks.
The NVLD seals the canister vent during engine off
conditions. If the EVAP system has a leak of less than
the failure threshold, the evaporative system will be
pulled into a vacuum, either due to the cool down
from operating temperature or diurnal ambient tem-
perature cycling. The diurnal effect is considered one
of the primary contributors to the leak determination
by this diagnostic. When the vacuum in the system
exceeds about 19H2O (0.25 KPA), a vacuum switch
closes. The switch closure sends a signal to the NGC.
The NGC, via appropriate logic strategies (described
below), utilizes the switch signal, or lack thereof, to
make a determination of whether a leak is present.
The NVLD device is designed with a normally open
vacuum switch, a normally closed solenoid, and a
seal, which is actuated by both the solenoid and a
diaphragm. The NVLD is located on the atmosphericvent side of the canister. The NVLD assembly may
be mounted on top of the canister outlet, or in-line
between the canister and atmospheric vent filter. The
normally open vacuum switch will close with about 19
H2O (0.25 KPA) vacuum in the evaporative system.
The diaphragm actuates the switch. This is above the
opening point of the fuel inlet check valve in the fill
tube so cap off leaks can be detected. Submerged fill
systems must have recirculation lines that do not
have the in-line normally closed check valve that pro-
tects the system from failed nozzle liquid ingestion,
in order to detect cap off conditions.
The normally closed valve in the NVLD is intended
to maintain the seal on the evaporative system dur-
ing the engine off condition. If vacuum in the evapo-
rative system exceeds 39to 69H2O (0.75 to 1.5 KPA),
the valve will be pulled off the seat, opening the seal.
This will protect the system from excessive vacuum
as well as allowing sufficient purge flow in the event
that the solenoid was to become inoperative.
The solenoid actuates the valve to unseal the can-
ister vent while the engine is running. It also will be
used to close the vent during the medium and large
leak tests and during the purge flow check. This sole-
noid requires initial 1.5 amps of current to pull the
valve open but after 100 ms. will be duty cycled down
to an average of about 150 mA for the remainder of
the drive cycle.
Another feature in the device is a diaphragm that
will open the seal in the NVLD with pressure in the
evaporative system. The device will9blow off9at
about 0.59H2O (0.12 KPA) pressure to permit the
venting of vapors during refueling. An added benefit
to this is that it will also allow the tank to9breathe9
during increasing temperatures, thus limiting the
pressure in the tank to this low level. This is benefi-
cial because the induced vacuum during a subse-
quent declining temperature will achieve the switch
closed (pass threshold) sooner than if the tank had to
decay from a built up pressure.
The device itself has 3 wires: Switch sense, sole-
noid driver and ground. It also includes a resistor to
protect the switch from a short to battery or a short
to ground. The NGC utilizes a high-side driver to
energize and duty-cycle the solenoid.
DESCRIPTION - HIGH AND LOW LIMITS
The PCM compares input signal voltages from each
input device with established high and low limits for
the device. If the input voltage is not within limits
and other criteria are met, the PCM stores a diagnos-
tic trouble code in memory. Other diagnostic trouble
code criteria might include engine RPM limits or
input voltages from other sensors or switches that
must be present before verifying a diagnostic trouble
code condition.
25 - 8 EMISSIONS CONTROLRS
EMISSIONS CONTROL (Continued)
ProCarManuals.com
Page 2120 of 2177
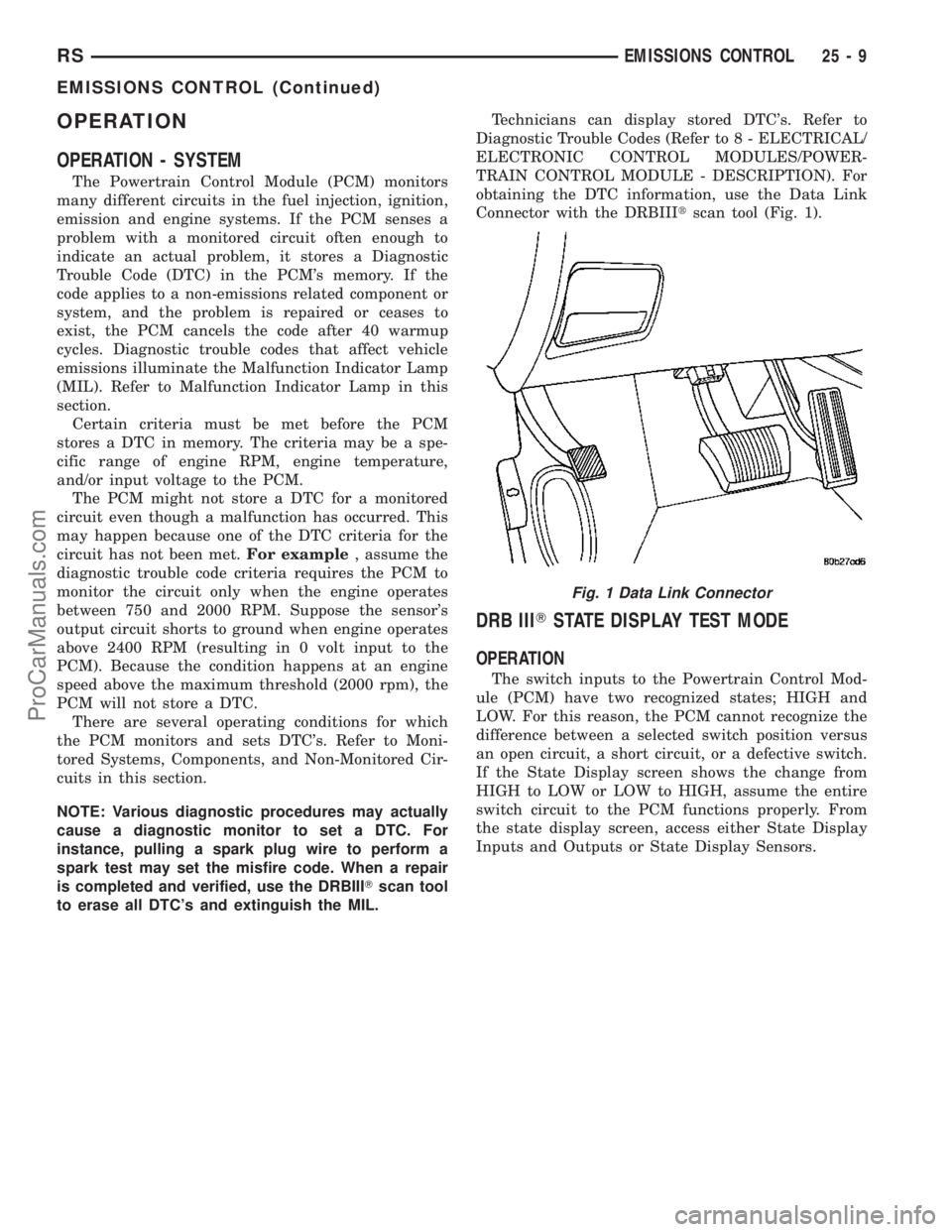
OPERATION
OPERATION - SYSTEM
The Powertrain Control Module (PCM) monitors
many different circuits in the fuel injection, ignition,
emission and engine systems. If the PCM senses a
problem with a monitored circuit often enough to
indicate an actual problem, it stores a Diagnostic
Trouble Code (DTC) in the PCM's memory. If the
code applies to a non-emissions related component or
system, and the problem is repaired or ceases to
exist, the PCM cancels the code after 40 warmup
cycles. Diagnostic trouble codes that affect vehicle
emissions illuminate the Malfunction Indicator Lamp
(MIL). Refer to Malfunction Indicator Lamp in this
section.
Certain criteria must be met before the PCM
stores a DTC in memory. The criteria may be a spe-
cific range of engine RPM, engine temperature,
and/or input voltage to the PCM.
The PCM might not store a DTC for a monitored
circuit even though a malfunction has occurred. This
may happen because one of the DTC criteria for the
circuit has not been met.For example, assume the
diagnostic trouble code criteria requires the PCM to
monitor the circuit only when the engine operates
between 750 and 2000 RPM. Suppose the sensor's
output circuit shorts to ground when engine operates
above 2400 RPM (resulting in 0 volt input to the
PCM). Because the condition happens at an engine
speed above the maximum threshold (2000 rpm), the
PCM will not store a DTC.
There are several operating conditions for which
the PCM monitors and sets DTC's. Refer to Moni-
tored Systems, Components, and Non-Monitored Cir-
cuits in this section.
NOTE: Various diagnostic procedures may actually
cause a diagnostic monitor to set a DTC. For
instance, pulling a spark plug wire to perform a
spark test may set the misfire code. When a repair
is completed and verified, use the DRBIIITscan tool
to erase all DTC's and extinguish the MIL.Technicians can display stored DTC's. Refer to
Diagnostic Trouble Codes (Refer to 8 - ELECTRICAL/
ELECTRONIC CONTROL MODULES/POWER-
TRAIN CONTROL MODULE - DESCRIPTION). For
obtaining the DTC information, use the Data Link
Connector with the DRBIIItscan tool (Fig. 1).
DRB IIITSTATE DISPLAY TEST MODE
OPERATION
The switch inputs to the Powertrain Control Mod-
ule (PCM) have two recognized states; HIGH and
LOW. For this reason, the PCM cannot recognize the
difference between a selected switch position versus
an open circuit, a short circuit, or a defective switch.
If the State Display screen shows the change from
HIGH to LOW or LOW to HIGH, assume the entire
switch circuit to the PCM functions properly. From
the state display screen, access either State Display
Inputs and Outputs or State Display Sensors.
Fig. 1 Data Link Connector
RSEMISSIONS CONTROL25-9
EMISSIONS CONTROL (Continued)
ProCarManuals.com
Page 2135 of 2177
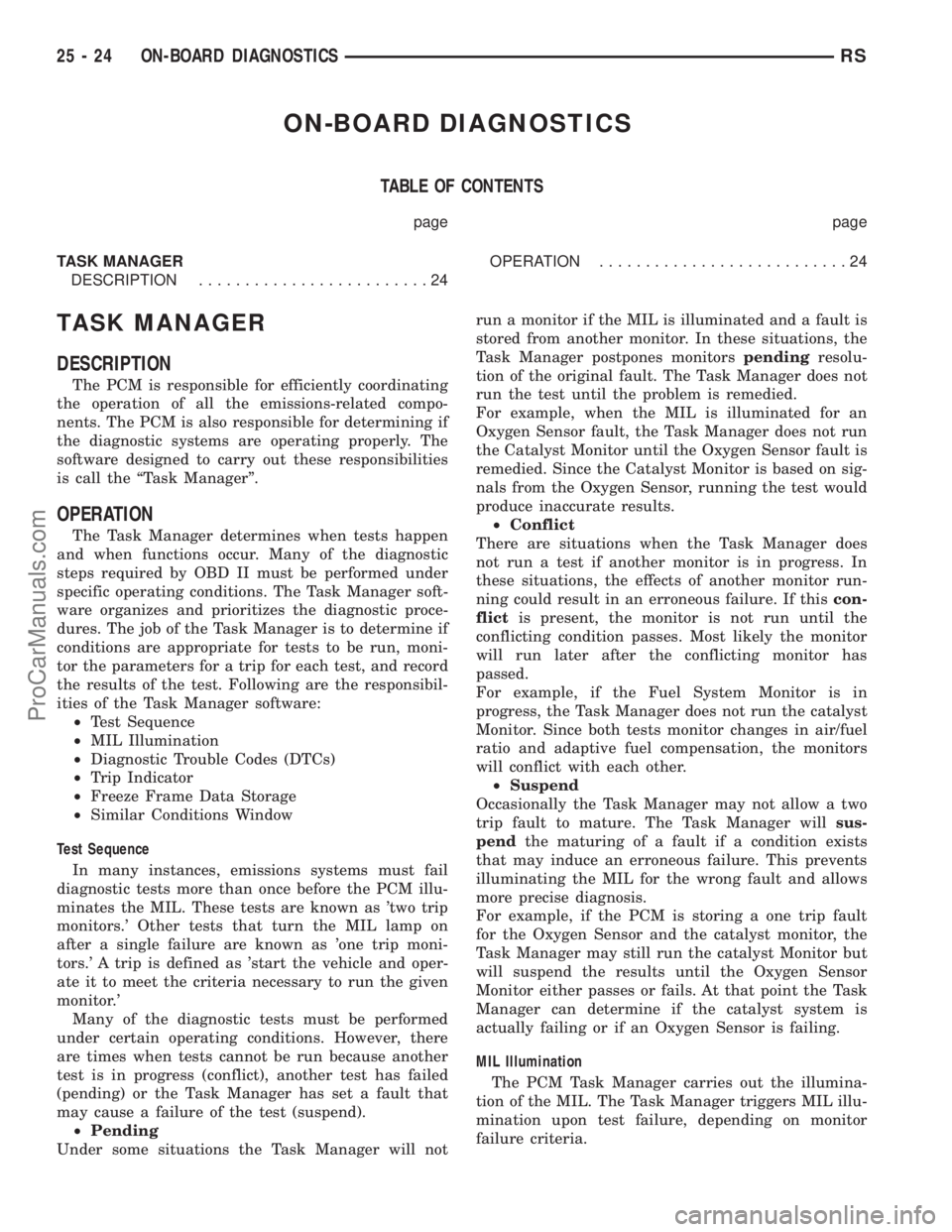
ON-BOARD DIAGNOSTICS
TABLE OF CONTENTS
page page
TASK MANAGER
DESCRIPTION.........................24OPERATION...........................24
TASK MANAGER
DESCRIPTION
The PCM is responsible for efficiently coordinating
the operation of all the emissions-related compo-
nents. The PCM is also responsible for determining if
the diagnostic systems are operating properly. The
software designed to carry out these responsibilities
is call the ªTask Managerº.
OPERATION
The Task Manager determines when tests happen
and when functions occur. Many of the diagnostic
steps required by OBD II must be performed under
specific operating conditions. The Task Manager soft-
ware organizes and prioritizes the diagnostic proce-
dures. The job of the Task Manager is to determine if
conditions are appropriate for tests to be run, moni-
tor the parameters for a trip for each test, and record
the results of the test. Following are the responsibil-
ities of the Task Manager software:
²Test Sequence
²MIL Illumination
²Diagnostic Trouble Codes (DTCs)
²Trip Indicator
²Freeze Frame Data Storage
²Similar Conditions Window
Test Sequence
In many instances, emissions systems must fail
diagnostic tests more than once before the PCM illu-
minates the MIL. These tests are known as 'two trip
monitors.' Other tests that turn the MIL lamp on
after a single failure are known as 'one trip moni-
tors.' A trip is defined as 'start the vehicle and oper-
ate it to meet the criteria necessary to run the given
monitor.'
Many of the diagnostic tests must be performed
under certain operating conditions. However, there
are times when tests cannot be run because another
test is in progress (conflict), another test has failed
(pending) or the Task Manager has set a fault that
may cause a failure of the test (suspend).
²Pending
Under some situations the Task Manager will notrun a monitor if the MIL is illuminated and a fault is
stored from another monitor. In these situations, the
Task Manager postpones monitorspendingresolu-
tion of the original fault. The Task Manager does not
run the test until the problem is remedied.
For example, when the MIL is illuminated for an
Oxygen Sensor fault, the Task Manager does not run
the Catalyst Monitor until the Oxygen Sensor fault is
remedied. Since the Catalyst Monitor is based on sig-
nals from the Oxygen Sensor, running the test would
produce inaccurate results.
²Conflict
There are situations when the Task Manager does
not run a test if another monitor is in progress. In
these situations, the effects of another monitor run-
ning could result in an erroneous failure. If thiscon-
flictis present, the monitor is not run until the
conflicting condition passes. Most likely the monitor
will run later after the conflicting monitor has
passed.
For example, if the Fuel System Monitor is in
progress, the Task Manager does not run the catalyst
Monitor. Since both tests monitor changes in air/fuel
ratio and adaptive fuel compensation, the monitors
will conflict with each other.
²Suspend
Occasionally the Task Manager may not allow a two
trip fault to mature. The Task Manager willsus-
pendthe maturing of a fault if a condition exists
that may induce an erroneous failure. This prevents
illuminating the MIL for the wrong fault and allows
more precise diagnosis.
For example, if the PCM is storing a one trip fault
for the Oxygen Sensor and the catalyst monitor, the
Task Manager may still run the catalyst Monitor but
will suspend the results until the Oxygen Sensor
Monitor either passes or fails. At that point the Task
Manager can determine if the catalyst system is
actually failing or if an Oxygen Sensor is failing.
MIL Illumination
The PCM Task Manager carries out the illumina-
tion of the MIL. The Task Manager triggers MIL illu-
mination upon test failure, depending on monitor
failure criteria.
25 - 24 ON-BOARD DIAGNOSTICSRS
ProCarManuals.com
Page 2137 of 2177
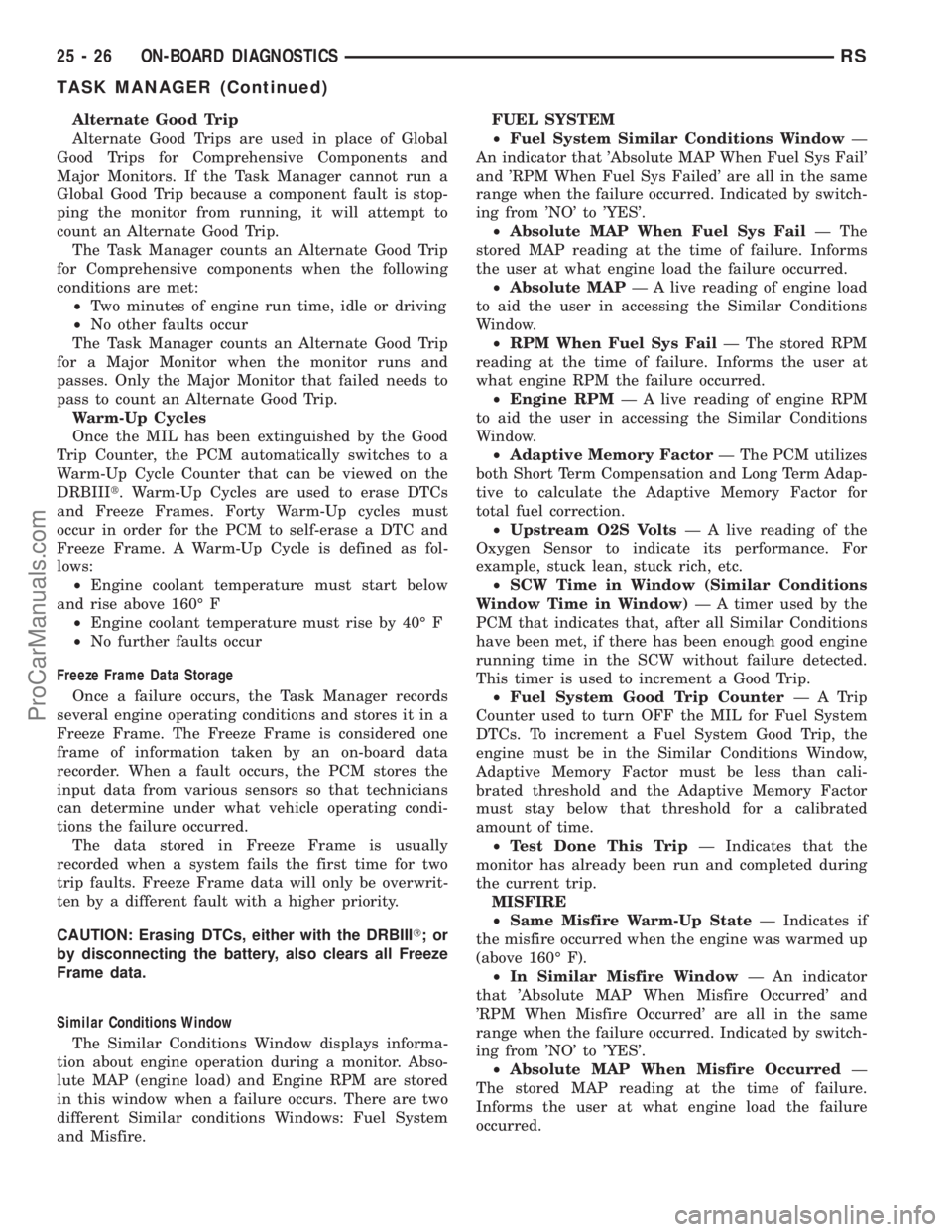
Alternate Good Trip
Alternate Good Trips are used in place of Global
Good Trips for Comprehensive Components and
Major Monitors. If the Task Manager cannot run a
Global Good Trip because a component fault is stop-
ping the monitor from running, it will attempt to
count an Alternate Good Trip.
The Task Manager counts an Alternate Good Trip
for Comprehensive components when the following
conditions are met:
²Two minutes of engine run time, idle or driving
²No other faults occur
The Task Manager counts an Alternate Good Trip
for a Major Monitor when the monitor runs and
passes. Only the Major Monitor that failed needs to
pass to count an Alternate Good Trip.
Warm-Up Cycles
Once the MIL has been extinguished by the Good
Trip Counter, the PCM automatically switches to a
Warm-Up Cycle Counter that can be viewed on the
DRBIIIt. Warm-Up Cycles are used to erase DTCs
and Freeze Frames. Forty Warm-Up cycles must
occur in order for the PCM to self-erase a DTC and
Freeze Frame. A Warm-Up Cycle is defined as fol-
lows:
²Engine coolant temperature must start below
and rise above 160É F
²Engine coolant temperature must rise by 40É F
²No further faults occur
Freeze Frame Data Storage
Once a failure occurs, the Task Manager records
several engine operating conditions and stores it in a
Freeze Frame. The Freeze Frame is considered one
frame of information taken by an on-board data
recorder. When a fault occurs, the PCM stores the
input data from various sensors so that technicians
can determine under what vehicle operating condi-
tions the failure occurred.
The data stored in Freeze Frame is usually
recorded when a system fails the first time for two
trip faults. Freeze Frame data will only be overwrit-
ten by a different fault with a higher priority.
CAUTION: Erasing DTCs, either with the DRBIIIT;or
by disconnecting the battery, also clears all Freeze
Frame data.
Similar Conditions Window
The Similar Conditions Window displays informa-
tion about engine operation during a monitor. Abso-
lute MAP (engine load) and Engine RPM are stored
in this window when a failure occurs. There are two
different Similar conditions Windows: Fuel System
and Misfire.FUEL SYSTEM
²Fuel System Similar Conditions WindowÐ
An indicator that 'Absolute MAP When Fuel Sys Fail'
and 'RPM When Fuel Sys Failed' are all in the same
range when the failure occurred. Indicated by switch-
ing from 'NO' to 'YES'.
²Absolute MAP When Fuel Sys FailÐ The
stored MAP reading at the time of failure. Informs
the user at what engine load the failure occurred.
²Absolute MAPÐ A live reading of engine load
to aid the user in accessing the Similar Conditions
Window.
²RPM When Fuel Sys FailÐ The stored RPM
reading at the time of failure. Informs the user at
what engine RPM the failure occurred.
²Engine RPMÐ A live reading of engine RPM
to aid the user in accessing the Similar Conditions
Window.
²Adaptive Memory FactorÐ The PCM utilizes
both Short Term Compensation and Long Term Adap-
tive to calculate the Adaptive Memory Factor for
total fuel correction.
²Upstream O2S VoltsÐ A live reading of the
Oxygen Sensor to indicate its performance. For
example, stuck lean, stuck rich, etc.
²SCW Time in Window (Similar Conditions
Window Time in Window)Ð A timer used by the
PCM that indicates that, after all Similar Conditions
have been met, if there has been enough good engine
running time in the SCW without failure detected.
This timer is used to increment a Good Trip.
²Fuel System Good Trip CounterÐATrip
Counter used to turn OFF the MIL for Fuel System
DTCs. To increment a Fuel System Good Trip, the
engine must be in the Similar Conditions Window,
Adaptive Memory Factor must be less than cali-
brated threshold and the Adaptive Memory Factor
must stay below that threshold for a calibrated
amount of time.
²Test Done This TripÐ Indicates that the
monitor has already been run and completed during
the current trip.
MISFIRE
²Same Misfire Warm-Up StateÐ Indicates if
the misfire occurred when the engine was warmed up
(above 160É F).
²In Similar Misfire WindowÐ An indicator
that 'Absolute MAP When Misfire Occurred' and
'RPM When Misfire Occurred' are all in the same
range when the failure occurred. Indicated by switch-
ing from 'NO' to 'YES'.
²Absolute MAP When Misfire OccurredÐ
The stored MAP reading at the time of failure.
Informs the user at what engine load the failure
occurred.
25 - 26 ON-BOARD DIAGNOSTICSRS
TASK MANAGER (Continued)
ProCarManuals.com
Page 2140 of 2177
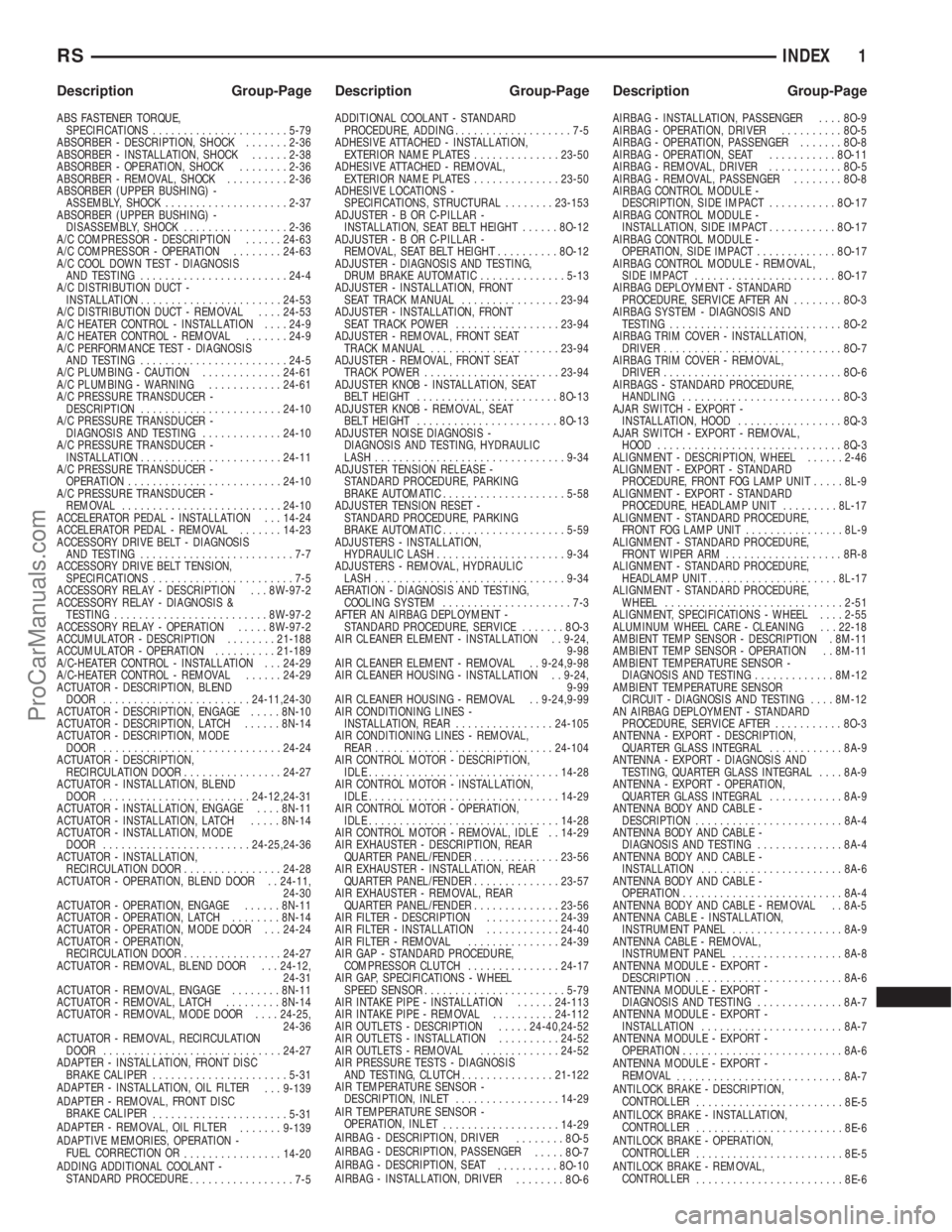
ABS FASTENER TORQUE,
SPECIFICATIONS......................5-79
ABSORBER - DESCRIPTION, SHOCK.......2-36
ABSORBER - INSTALLATION, SHOCK......2-38
ABSORBER - OPERATION, SHOCK........2-36
ABSORBER - REMOVAL, SHOCK..........2-36
ABSORBER (UPPER BUSHING) -
ASSEMBLY, SHOCK....................2-37
ABSORBER (UPPER BUSHING) -
DISASSEMBLY, SHOCK.................2-36
A/C COMPRESSOR - DESCRIPTION......24-63
A/C COMPRESSOR - OPERATION........24-63
A/C COOL DOWN TEST - DIAGNOSIS
AND TESTING........................24-4
A/C DISTRIBUTION DUCT -
INSTALLATION.......................24-53
A/C DISTRIBUTION DUCT - REMOVAL....24-53
A/C HEATER CONTROL - INSTALLATION....24-9
A/C HEATER CONTROL - REMOVAL.......24-9
A/C PERFORMANCE TEST - DIAGNOSIS
AND TESTING........................24-5
A/C PLUMBING - CAUTION.............24-61
A/C PLUMBING - WARNING............24-61
A/C PRESSURE TRANSDUCER -
DESCRIPTION.......................24-10
A/C PRESSURE TRANSDUCER -
DIAGNOSIS AND TESTING.............24-10
A/C PRESSURE TRANSDUCER -
INSTALLATION.......................24-11
A/C PRESSURE TRANSDUCER -
OPERATION.........................24-10
A/C PRESSURE TRANSDUCER -
REMOVAL..........................24-10
ACCELERATOR PEDAL - INSTALLATION . . . 14-24
ACCELERATOR PEDAL - REMOVAL.......14-23
ACCESSORY DRIVE BELT - DIAGNOSIS
AND TESTING.........................7-7
ACCESSORY DRIVE BELT TENSION,
SPECIFICATIONS.......................7-5
ACCESSORY RELAY - DESCRIPTION . . . 8W-97-2
ACCESSORY RELAY - DIAGNOSIS &
TESTING.........................8W-97-2
ACCESSORY RELAY - OPERATION.....8W-97-2
ACCUMULATOR - DESCRIPTION........21-188
ACCUMULATOR - OPERATION..........21-189
A/C-HEATER CONTROL - INSTALLATION . . . 24-29
A/C-HEATER CONTROL - REMOVAL......24-29
ACTUATOR - DESCRIPTION, BLEND
DOOR........................24-11,24-30
ACTUATOR - DESCRIPTION, ENGAGE.....8N-10
ACTUATOR - DESCRIPTION, LATCH......8N-14
ACTUATOR - DESCRIPTION, MODE
DOOR.............................24-24
ACTUATOR - DESCRIPTION,
RECIRCULATION DOOR................24-27
ACTUATOR - INSTALLATION, BLEND
DOOR........................24-12,24-31
ACTUATOR - INSTALLATION, ENGAGE....8N-11
ACTUATOR - INSTALLATION, LATCH.....8N-14
ACTUATOR - INSTALLATION, MODE
DOOR........................24-25,24-36
ACTUATOR - INSTALLATION,
RECIRCULATION DOOR................24-28
ACTUATOR - OPERATION, BLEND DOOR . . 24-11,
24-30
ACTUATOR - OPERATION, ENGAGE......8N-11
ACTUATOR - OPERATION, LATCH........8N-14
ACTUATOR - OPERATION, MODE DOOR . . . 24-24
ACTUATOR - OPERATION,
RECIRCULATION DOOR................24-27
ACTUATOR - REMOVAL, BLEND DOOR . . . 24-12,
24-31
ACTUATOR - REMOVAL, ENGAGE........8N-11
ACTUATOR - REMOVAL, LATCH.........8N-14
ACTUATOR - REMOVAL, MODE DOOR....24-25,
24-36
ACTUATOR - REMOVAL, RECIRCULATION
DOOR.............................24-27
ADAPTER - INSTALLATION, FRONT DISC
BRAKE CALIPER......................5-31
ADAPTER - INSTALLATION, OIL FILTER
. . . 9-139
ADAPTER - REMOVAL, FRONT DISC
BRAKE CALIPER
......................5-31
ADAPTER - REMOVAL, OIL FILTER
.......9-139
ADAPTIVE MEMORIES, OPERATION -
FUEL CORRECTION OR
................14-20
ADDING ADDITIONAL COOLANT -
STANDARD PROCEDURE
.................7-5ADDITIONAL COOLANT - STANDARD
PROCEDURE, ADDING...................7-5
ADHESIVE ATTACHED - INSTALLATION,
EXTERIOR NAME PLATES..............23-50
ADHESIVE ATTACHED - REMOVAL,
EXTERIOR NAME PLATES..............23-50
ADHESIVE LOCATIONS -
SPECIFICATIONS, STRUCTURAL........23-153
ADJUSTER-BORC-PILLAR -
INSTALLATION, SEAT BELT HEIGHT......8O-12
ADJUSTER-BORC-PILLAR -
REMOVAL, SEAT BELT HEIGHT..........8O-12
ADJUSTER - DIAGNOSIS AND TESTING,
DRUM BRAKE AUTOMATIC..............5-13
ADJUSTER - INSTALLATION, FRONT
SEAT TRACK MANUAL................23-94
ADJUSTER - INSTALLATION, FRONT
SEAT TRACK POWER.................23-94
ADJUSTER - REMOVAL, FRONT SEAT
TRACK MANUAL.....................23-94
ADJUSTER - REMOVAL, FRONT SEAT
TRACK POWER......................23-94
ADJUSTER KNOB - INSTALLATION, SEAT
BELT HEIGHT.......................8O-13
ADJUSTER KNOB - REMOVAL, SEAT
BELT HEIGHT.......................8O-13
ADJUSTER NOISE DIAGNOSIS -
DIAGNOSIS AND TESTING, HYDRAULIC
LASH...............................9-34
ADJUSTER TENSION RELEASE -
STANDARD PROCEDURE, PARKING
BRAKE AUTOMATIC....................5-58
ADJUSTER TENSION RESET -
STANDARD PROCEDURE, PARKING
BRAKE AUTOMATIC.....................5-59
ADJUSTERS - INSTALLATION,
HYDRAULIC LASH.....................9-34
ADJUSTERS - REMOVAL, HYDRAULIC
LASH...............................9-34
AERATION - DIAGNOSIS AND TESTING,
COOLING SYSTEM.....................7-3
AFTER AN AIRBAG DEPLOYMENT -
STANDARD PROCEDURE, SERVICE.......8O-3
AIR CLEANER ELEMENT - INSTALLATION . . 9-24,
9-98
AIR CLEANER ELEMENT - REMOVAL . . 9-24,9-98
AIR CLEANER HOUSING - INSTALLATION . . 9-24,
9-99
AIR CLEANER HOUSING - REMOVAL . . 9-24,9-99
AIR CONDITIONING LINES -
INSTALLATION, REAR................24-105
AIR CONDITIONING LINES - REMOVAL,
REAR.............................24-104
AIR CONTROL MOTOR - DESCRIPTION,
IDLE...............................14-28
AIR CONTROL MOTOR - INSTALLATION,
IDLE...............................14-29
AIR CONTROL MOTOR - OPERATION,
IDLE...............................14-28
AIR CONTROL MOTOR - REMOVAL, IDLE . . 14-29
AIR EXHAUSTER - DESCRIPTION, REAR
QUARTER PANEL/FENDER..............23-56
AIR EXHAUSTER - INSTALLATION, REAR
QUARTER PANEL/FENDER..............23-57
AIR EXHAUSTER - REMOVAL, REAR
QUARTER PANEL/FENDER..............23-56
AIR FILTER - DESCRIPTION............24-39
AIR FILTER - INSTALLATION............24-40
AIR FILTER - REMOVAL...............24-39
AIR GAP - STANDARD PROCEDURE,
COMPRESSOR CLUTCH...............24-17
AIR GAP, SPECIFICATIONS - WHEEL
SPEED SENSOR.......................5-79
AIR INTAKE PIPE - INSTALLATION......24-113
AIR INTAKE PIPE - REMOVAL..........24-112
AIR OUTLETS - DESCRIPTION.....24-40,24-52
AIR OUTLETS - INSTALLATION..........24-52
AIR OUTLETS - REMOVAL.............24-52
AIR PRESSURE TESTS - DIAGNOSIS
AND TESTING, CLUTCH...............21-122
AIR TEMPERATURE SENSOR -
DESCRIPTION, INLET.................14-29
AIR TEMPERATURE SENSOR -
OPERATION, INLET
...................14-29
AIRBAG - DESCRIPTION, DRIVER
........8O-5
AIRBAG - DESCRIPTION, PASSENGER
.....8O-7
AIRBAG - DESCRIPTION, SEAT
..........8O-10
AIRBAG - INSTALLATION, DRIVER
........8O-6AIRBAG - INSTALLATION, PASSENGER....8O-9
AIRBAG - OPERATION, DRIVER..........8O-5
AIRBAG - OPERATION, PASSENGER.......8O-8
AIRBAG - OPERATION, SEAT...........8O-11
AIRBAG - REMOVAL, DRIVER............8O-5
AIRBAG - REMOVAL, PASSENGER........8O-8
AIRBAG CONTROL MODULE -
DESCRIPTION, SIDE IMPACT...........8O-17
AIRBAG CONTROL MODULE -
INSTALLATION, SIDE IMPACT...........8O-17
AIRBAG CONTROL MODULE -
OPERATION, SIDE IMPACT.............8O-17
AIRBAG CONTROL MODULE - REMOVAL,
SIDE IMPACT.......................8O-17
AIRBAG DEPLOYMENT - STANDARD
PROCEDURE, SERVICE AFTER AN........8O-3
AIRBAG SYSTEM - DIAGNOSIS AND
TESTING............................8O-2
AIRBAG TRIM COVER - INSTALLATION,
DRIVER.............................8O-7
AIRBAG TRIM COVER - REMOVAL,
DRIVER.............................8O-6
AIRBAGS - STANDARD PROCEDURE,
HANDLING..........................8O-3
AJAR SWITCH - EXPORT -
INSTALLATION, HOOD.................8Q-3
AJAR SWITCH - EXPORT - REMOVAL,
HOOD..............................8Q-3
ALIGNMENT - DESCRIPTION, WHEEL......2-46
ALIGNMENT - EXPORT - STANDARD
PROCEDURE, FRONT FOG LAMP UNIT.....8L-9
ALIGNMENT - EXPORT - STANDARD
PROCEDURE, HEADLAMP UNIT.........8L-17
ALIGNMENT - STANDARD PROCEDURE,
FRONT FOG LAMP UNIT................8L-9
ALIGNMENT - STANDARD PROCEDURE,
FRONT WIPER ARM...................8R-8
ALIGNMENT - STANDARD PROCEDURE,
HEADLAMP UNIT.....................8L-17
ALIGNMENT - STANDARD PROCEDURE,
WHEEL.............................2-51
ALIGNMENT, SPECIFICATIONS - WHEEL....2-55
ALUMINUM WHEEL CARE - CLEANING . . . 22-18
AMBIENT TEMP SENSOR - DESCRIPTION . 8M-11
AMBIENT TEMP SENSOR - OPERATION . . 8M-11
AMBIENT TEMPERATURE SENSOR -
DIAGNOSIS AND TESTING.............8M-12
AMBIENT TEMPERATURE SENSOR
CIRCUIT - DIAGNOSIS AND TESTING....8M-12
AN AIRBAG DEPLOYMENT - STANDARD
PROCEDURE, SERVICE AFTER...........8O-3
ANTENNA - EXPORT - DESCRIPTION,
QUARTER GLASS INTEGRAL............8A-9
ANTENNA - EXPORT - DIAGNOSIS AND
TESTING, QUARTER GLASS INTEGRAL....8A-9
ANTENNA - EXPORT - OPERATION,
QUARTER GLASS INTEGRAL............8A-9
ANTENNA BODY AND CABLE -
DESCRIPTION........................8A-4
ANTENNA BODY AND CABLE -
DIAGNOSIS AND TESTING..............8A-4
ANTENNA BODY AND CABLE -
INSTALLATION.......................8A-6
ANTENNA BODY AND CABLE -
OPERATION..........................8A-4
ANTENNA BODY AND CABLE - REMOVAL . . 8A-5
ANTENNA CABLE - INSTALLATION,
INSTRUMENT PANEL..................8A-9
ANTENNA CABLE - REMOVAL,
INSTRUMENT PANEL..................8A-8
ANTENNA MODULE - EXPORT -
DESCRIPTION........................8A-6
ANTENNA MODULE - EXPORT -
DIAGNOSIS AND TESTING..............8A-7
ANTENNA MODULE - EXPORT -
INSTALLATION.......................8A-7
ANTENNA MODULE - EXPORT -
OPERATION..........................8A-6
ANTENNA MODULE - EXPORT -
REMOVAL
...........................8A-7
ANTILOCK BRAKE - DESCRIPTION,
CONTROLLER
........................8E-5
ANTILOCK BRAKE - INSTALLATION,
CONTROLLER
........................8E-6
ANTILOCK BRAKE - OPERATION,
CONTROLLER
........................8E-5
ANTILOCK BRAKE - REMOVAL,
CONTROLLER
........................8E-6
RSINDEX1
Description Group-Page Description Group-Page Description Group-Page
ProCarManuals.com
Page 2141 of 2177
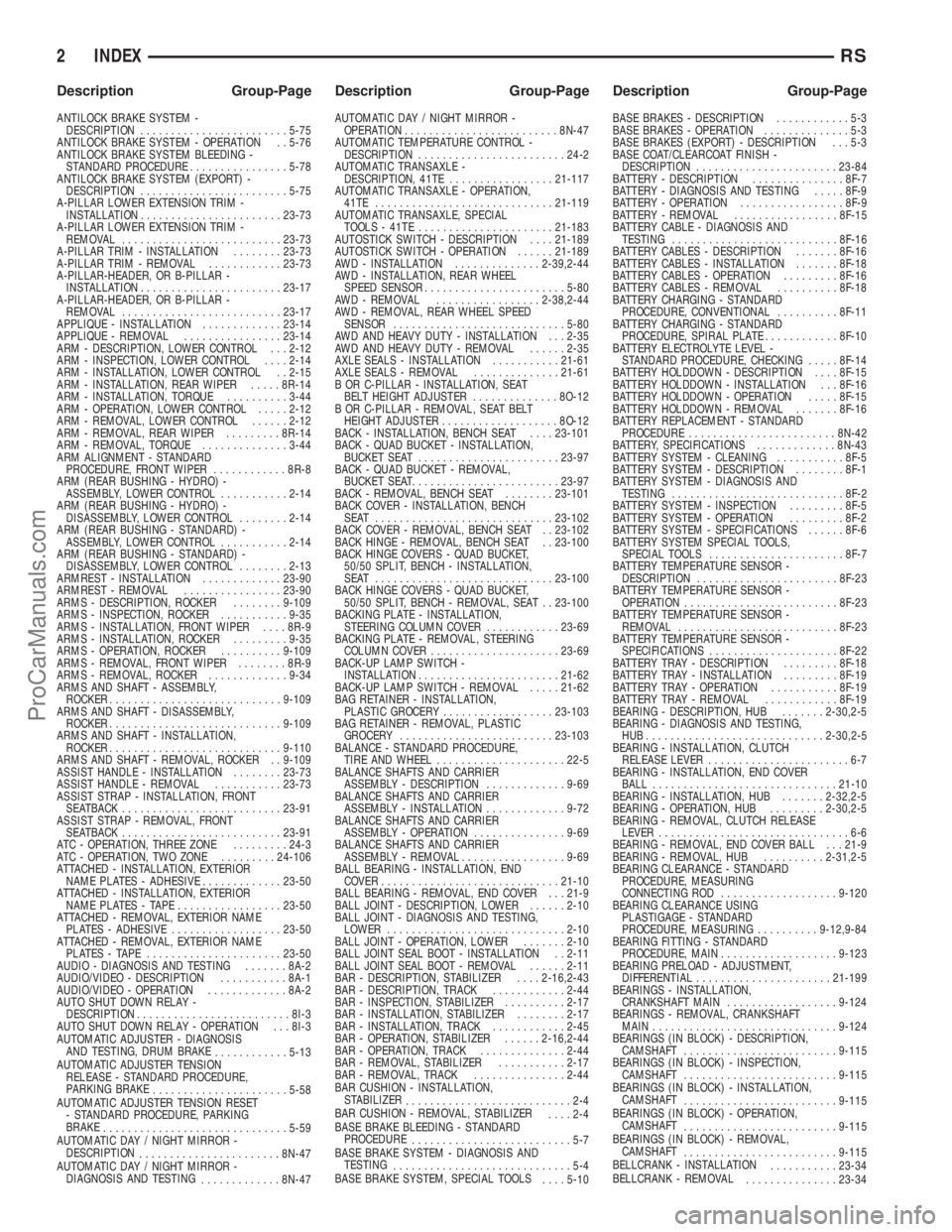
ANTILOCK BRAKE SYSTEM -
DESCRIPTION........................5-75
ANTILOCK BRAKE SYSTEM - OPERATION . . 5-76
ANTILOCK BRAKE SYSTEM BLEEDING -
STANDARD PROCEDURE................5-78
ANTILOCK BRAKE SYSTEM (EXPORT) -
DESCRIPTION........................5-75
A-PILLAR LOWER EXTENSION TRIM -
INSTALLATION.......................23-73
A-PILLAR LOWER EXTENSION TRIM -
REMOVAL..........................23-73
A-PILLAR TRIM - INSTALLATION........23-73
A-PILLAR TRIM - REMOVAL............23-73
A-PILLAR-HEADER, OR B-PILLAR -
INSTALLATION.......................23-17
A-PILLAR-HEADER, OR B-PILLAR -
REMOVAL..........................23-17
APPLIQUE - INSTALLATION.............23-14
APPLIQUE - REMOVAL................23-14
ARM - DESCRIPTION, LOWER CONTROL . . . 2-12
ARM - INSPECTION, LOWER CONTROL....2-14
ARM - INSTALLATION, LOWER CONTROL . . 2-15
ARM - INSTALLATION, REAR WIPER.....8R-14
ARM - INSTALLATION, TORQUE..........3-44
ARM - OPERATION, LOWER CONTROL.....2-12
ARM - REMOVAL, LOWER CONTROL......2-12
ARM - REMOVAL, REAR WIPER.........8R-14
ARM - REMOVAL, TORQUE..............3-44
ARM ALIGNMENT - STANDARD
PROCEDURE, FRONT WIPER............8R-8
ARM (REAR BUSHING - HYDRO) -
ASSEMBLY, LOWER CONTROL...........2-14
ARM (REAR BUSHING - HYDRO) -
DISASSEMBLY, LOWER CONTROL........2-14
ARM (REAR BUSHING - STANDARD) -
ASSEMBLY, LOWER CONTROL...........2-14
ARM (REAR BUSHING - STANDARD) -
DISASSEMBLY, LOWER CONTROL........2-13
ARMREST - INSTALLATION.............23-90
ARMREST - REMOVAL................23-90
ARMS - DESCRIPTION, ROCKER........9-109
ARMS - INSPECTION, ROCKER...........9-35
ARMS - INSTALLATION, FRONT WIPER....8R-9
ARMS - INSTALLATION, ROCKER.........9-35
ARMS - OPERATION, ROCKER..........9-109
ARMS - REMOVAL, FRONT WIPER........8R-9
ARMS - REMOVAL, ROCKER.............9-34
ARMS AND SHAFT - ASSEMBLY,
ROCKER............................9-109
ARMS AND SHAFT - DISASSEMBLY,
ROCKER............................9-109
ARMS AND SHAFT - INSTALLATION,
ROCKER............................9-110
ARMS AND SHAFT - REMOVAL, ROCKER . . 9-109
ASSIST HANDLE - INSTALLATION........23-73
ASSIST HANDLE - REMOVAL...........23-73
ASSIST STRAP - INSTALLATION, FRONT
SEATBACK..........................23-91
ASSIST STRAP - REMOVAL, FRONT
SEATBACK..........................23-91
ATC - OPERATION, THREE ZONE.........24-3
ATC - OPERATION, TWO ZONE.........24-106
ATTACHED - INSTALLATION, EXTERIOR
NAME PLATES - ADHESIVE.............23-50
ATTACHED - INSTALLATION, EXTERIOR
NAME PLATES - TAPE.................23-50
ATTACHED - REMOVAL, EXTERIOR NAME
PLATES - ADHESIVE..................23-50
ATTACHED - REMOVAL, EXTERIOR NAME
PLATES - TAPE ......................23-50
AUDIO - DIAGNOSIS AND TESTING.......8A-2
AUDIO/VIDEO - DESCRIPTION...........8A-1
AUDIO/VIDEO - OPERATION.............8A-2
AUTO SHUT DOWN RELAY -
DESCRIPTION.........................8I-3
AUTO SHUT DOWN RELAY - OPERATION . . . 8I-3
AUTOMATIC ADJUSTER - DIAGNOSIS
AND TESTING, DRUM BRAKE
............5-13
AUTOMATIC ADJUSTER TENSION
RELEASE - STANDARD PROCEDURE,
PARKING BRAKE
......................5-58
AUTOMATIC ADJUSTER TENSION RESET
- STANDARD PROCEDURE, PARKING
BRAKE
..............................5-59
AUTOMATIC DAY / NIGHT MIRROR -
DESCRIPTION
.......................8N-47
AUTOMATIC DAY / NIGHT MIRROR -
DIAGNOSIS AND TESTING
.............8N-47AUTOMATIC DAY / NIGHT MIRROR -
OPERATION.........................8N-47
AUTOMATIC TEMPERATURE CONTROL -
DESCRIPTION........................24-2
AUTOMATIC TRANSAXLE -
DESCRIPTION, 41TE.................21-117
AUTOMATIC TRANSAXLE - OPERATION,
41TE.............................21-119
AUTOMATIC TRANSAXLE, SPECIAL
TOOLS - 41TE......................21-183
AUTOSTICK SWITCH - DESCRIPTION....21-189
AUTOSTICK SWITCH - OPERATION......21-189
AWD - INSTALLATION..............2-39,2-44
AWD - INSTALLATION, REAR WHEEL
SPEED SENSOR.......................5-80
AWD - REMOVAL.................2-38,2-44
AWD - REMOVAL, REAR WHEEL SPEED
SENSOR............................5-80
AWD AND HEAVY DUTY - INSTALLATION . . . 2-35
AWD AND HEAVY DUTY - REMOVAL......2-35
AXLE SEALS - INSTALLATION...........21-61
AXLE SEALS - REMOVAL..............21-61
B OR C-PILLAR - INSTALLATION, SEAT
BELT HEIGHT ADJUSTER..............8O-12
B OR C-PILLAR - REMOVAL, SEAT BELT
HEIGHT ADJUSTER...................8O-12
BACK - INSTALLATION, BENCH SEAT....23-101
BACK - QUAD BUCKET - INSTALLATION,
BUCKET SEAT.......................23-97
BACK - QUAD BUCKET - REMOVAL,
BUCKET SEAT.........................23-97
BACK - REMOVAL, BENCH SEAT........23-101
BACK COVER - INSTALLATION, BENCH
SEAT .............................23-102
BACK COVER - REMOVAL, BENCH SEAT . . 23-102
BACK HINGE - REMOVAL, BENCH SEAT . . 23-100
BACK HINGE COVERS - QUAD BUCKET,
50/50 SPLIT, BENCH - INSTALLATION,
SEAT .............................23-100
BACK HINGE COVERS - QUAD BUCKET,
50/50 SPLIT, BENCH - REMOVAL, SEAT . . 23-100
BACKING PLATE - INSTALLATION,
STEERING COLUMN COVER............23-69
BACKING PLATE - REMOVAL, STEERING
COLUMN COVER.....................23-69
BACK-UP LAMP SWITCH -
INSTALLATION.......................21-62
BACK-UP LAMP SWITCH - REMOVAL.....21-62
BAG RETAINER - INSTALLATION,
PLASTIC GROCERY..................23-103
BAG RETAINER - REMOVAL, PLASTIC
GROCERY.........................23-103
BALANCE - STANDARD PROCEDURE,
TIRE AND WHEEL.....................22-5
BALANCE SHAFTS AND CARRIER
ASSEMBLY - DESCRIPTION.............9-69
BALANCE SHAFTS AND CARRIER
ASSEMBLY - INSTALLATION.............9-72
BALANCE SHAFTS AND CARRIER
ASSEMBLY - OPERATION...............9-69
BALANCE SHAFTS AND CARRIER
ASSEMBLY - REMOVAL.................9-69
BALL BEARING - INSTALLATION, END
COVER.............................21-10
BALL BEARING - REMOVAL, END COVER . . . 21-9
BALL JOINT - DESCRIPTION, LOWER......2-10
BALL JOINT - DIAGNOSIS AND TESTING,
LOWER.............................2-10
BALL JOINT - OPERATION, LOWER.......2-10
BALL JOINT SEAL BOOT - INSTALLATION . . 2-11
BALL JOINT SEAL BOOT - REMOVAL......2-11
BAR - DESCRIPTION, STABILIZER....2-16,2-43
BAR - DESCRIPTION, TRACK............2-44
BAR - INSPECTION, STABILIZER..........2-17
BAR - INSTALLATION, STABILIZER........2-17
BAR - INSTALLATION, TRACK............2-45
BAR - OPERATION, STABILIZER......2-16,2-44
BAR - OPERATION, TRACK..............2-44
BAR - REMOVAL, STABILIZER...........2-17
BAR - REMOVAL, TRACK...............2-44
BAR CUSHION - INSTALLATION,
STABILIZER
...........................2-4
BAR CUSHION - REMOVAL, STABILIZER
....2-4
BASE BRAKE BLEEDING - STANDARD
PROCEDURE
..........................5-7
BASE BRAKE SYSTEM - DIAGNOSIS AND
TESTING
.............................5-4
BASE BRAKE SYSTEM, SPECIAL TOOLS
....5-10BASE BRAKES - DESCRIPTION............5-3
BASE BRAKES - OPERATION..............5-3
BASE BRAKES (EXPORT) - DESCRIPTION . . . 5-3
BASE COAT/CLEARCOAT FINISH -
DESCRIPTION.......................23-84
BATTERY - DESCRIPTION...............8F-7
BATTERY - DIAGNOSIS AND TESTING.....8F-9
BATTERY - OPERATION.................8F-9
BATTERY - REMOVAL.................8F-15
BATTERY CABLE - DIAGNOSIS AND
TESTING...........................8F-16
BATTERY CABLES - DESCRIPTION.......8F-16
BATTERY CABLES - INSTALLATION.......8F-18
BATTERY CABLES - OPERATION.........8F-16
BATTERY CABLES - REMOVAL..........8F-18
BATTERY CHARGING - STANDARD
PROCEDURE, CONVENTIONAL..........8F-11
BATTERY CHARGING - STANDARD
PROCEDURE, SPIRAL PLATE............8F-10
BATTERY ELECTROLYTE LEVEL -
STANDARD PROCEDURE, CHECKING.....8F-14
BATTERY HOLDDOWN - DESCRIPTION....8F-15
BATTERY HOLDDOWN - INSTALLATION . . . 8F-16
BATTERY HOLDDOWN - OPERATION.....8F-15
BATTERY HOLDDOWN - REMOVAL.......8F-16
BATTERY REPLACEMENT - STANDARD
PROCEDURE........................8N-42
BATTERY, SPECIFICATIONS.............8N-43
BATTERY SYSTEM - CLEANING...........8F-5
BATTERY SYSTEM - DESCRIPTION........8F-1
BATTERY SYSTEM - DIAGNOSIS AND
TESTING............................8F-2
BATTERY SYSTEM - INSPECTION.........8F-5
BATTERY SYSTEM - OPERATION.........8F-2
BATTERY SYSTEM - SPECIFICATIONS......8F-6
BATTERY SYSTEM SPECIAL TOOLS,
SPECIAL TOOLS......................8F-7
BATTERY TEMPERATURE SENSOR -
DESCRIPTION.......................8F-23
BATTERY TEMPERATURE SENSOR -
OPERATION.........................8F-23
BATTERY TEMPERATURE SENSOR -
REMOVAL..........................8F-23
BATTERY TEMPERATURE SENSOR -
SPECIFICATIONS.....................8F-22
BATTERY TRAY - DESCRIPTION.........8F-18
BATTERY TRAY - INSTALLATION.........8F-19
BATTERY TRAY - OPERATION...........8F-19
BATTERY TRAY - REMOVAL............8F-19
BEARING - DESCRIPTION, HUB.......2-30,2-5
BEARING - DIAGNOSIS AND TESTING,
HUB.............................2-30,2-5
BEARING - INSTALLATION, CLUTCH
RELEASE LEVER.......................6-7
BEARING - INSTALLATION, END COVER
BALL..............................21-10
BEARING - INSTALLATION, HUB.......2-32,2-5
BEARING - OPERATION, HUB.........2-30,2-5
BEARING - REMOVAL, CLUTCH RELEASE
LEVER...............................6-6
BEARING - REMOVAL, END COVER BALL . . . 21-9
BEARING - REMOVAL, HUB..........2-31,2-5
BEARING CLEARANCE - STANDARD
PROCEDURE, MEASURING
CONNECTING ROD...................9-120
BEARING CLEARANCE USING
PLASTIGAGE - STANDARD
PROCEDURE, MEASURING..........9-12,9-84
BEARING FITTING - STANDARD
PROCEDURE, MAIN...................9-123
BEARING PRELOAD - ADJUSTMENT,
DIFFERENTIAL......................21-199
BEARINGS - INSTALLATION,
CRANKSHAFT MAIN..................9-124
BEARINGS - REMOVAL, CRANKSHAFT
MAIN..............................9-124
BEARINGS (IN BLOCK) - DESCRIPTION,
CAMSHAFT.........................9-115
BEARINGS (IN BLOCK) - INSPECTION,
CAMSHAFT.........................9-115
BEARINGS (IN BLOCK) - INSTALLATION,
CAMSHAFT
.........................9-115
BEARINGS (IN BLOCK) - OPERATION,
CAMSHAFT
.........................9-115
BEARINGS (IN BLOCK) - REMOVAL,
CAMSHAFT
.........................9-115
BELLCRANK - INSTALLATION
...........23-34
BELLCRANK - REMOVAL
...............23-34
2 INDEXRS
Description Group-Page Description Group-Page Description Group-Page
ProCarManuals.com
Page 2144 of 2177
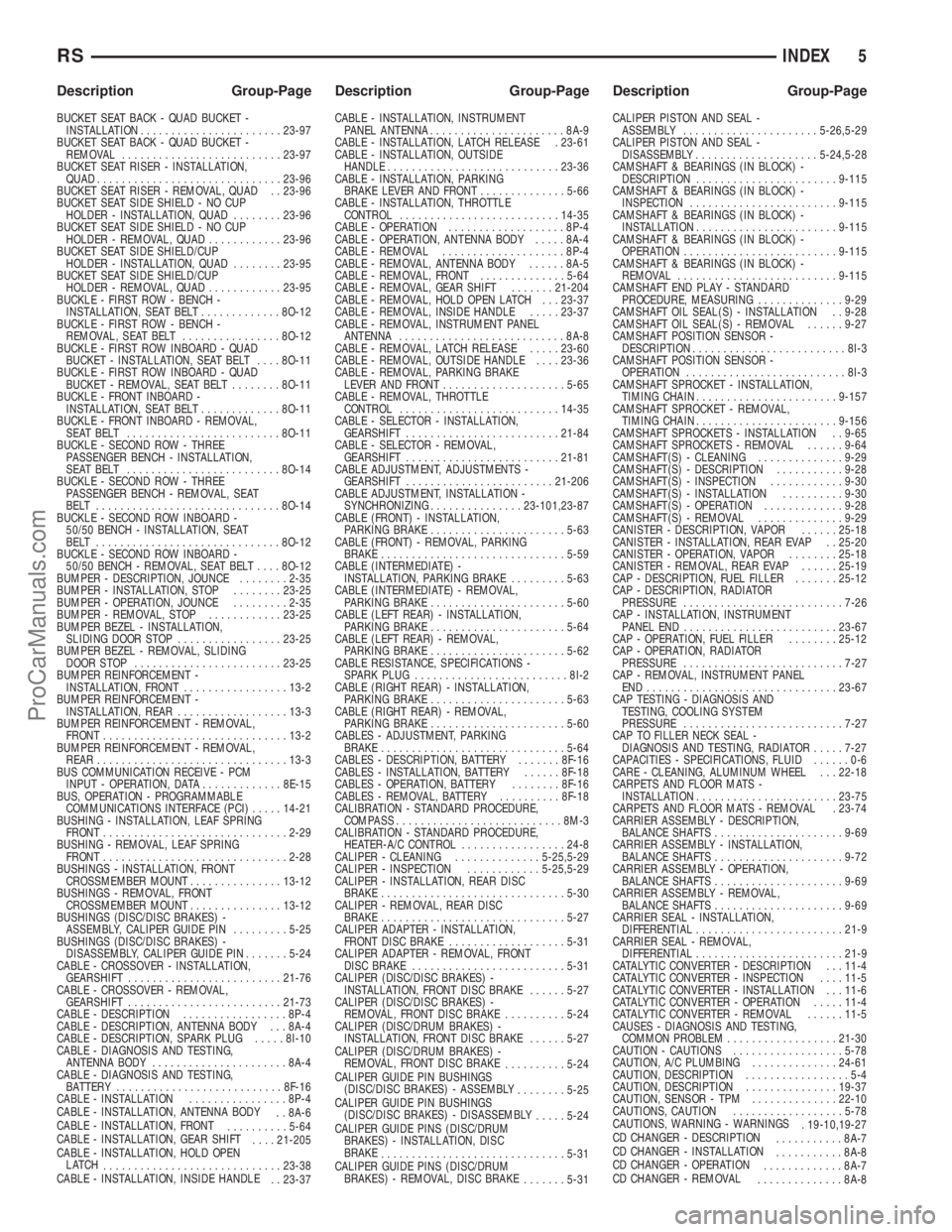
BUCKET SEAT BACK - QUAD BUCKET -
INSTALLATION.......................23-97
BUCKET SEAT BACK - QUAD BUCKET -
REMOVAL..........................23-97
BUCKET SEAT RISER - INSTALLATION,
QUAD..............................23-96
BUCKET SEAT RISER - REMOVAL, QUAD . . 23-96
BUCKET SEAT SIDE SHIELD - NO CUP
HOLDER - INSTALLATION, QUAD........23-96
BUCKET SEAT SIDE SHIELD - NO CUP
HOLDER - REMOVAL, QUAD............23-96
BUCKET SEAT SIDE SHIELD/CUP
HOLDER - INSTALLATION, QUAD........23-95
BUCKET SEAT SIDE SHIELD/CUP
HOLDER - REMOVAL, QUAD............23-95
BUCKLE - FIRST ROW - BENCH -
INSTALLATION, SEAT BELT.............8O-12
BUCKLE - FIRST ROW - BENCH -
REMOVAL, SEAT BELT................8O-12
BUCKLE - FIRST ROW INBOARD - QUAD
BUCKET - INSTALLATION, SEAT BELT....8O-11
BUCKLE - FIRST ROW INBOARD - QUAD
BUCKET - REMOVAL, SEAT BELT........8O-11
BUCKLE - FRONT INBOARD -
INSTALLATION, SEAT BELT.............8O-11
BUCKLE - FRONT INBOARD - REMOVAL,
SEAT BELT .........................8O-11
BUCKLE - SECOND ROW - THREE
PASSENGER BENCH - INSTALLATION,
SEAT BELT .........................8O-14
BUCKLE - SECOND ROW - THREE
PASSENGER BENCH - REMOVAL, SEAT
BELT ..............................8O-14
BUCKLE - SECOND ROW INBOARD -
50/50 BENCH - INSTALLATION, SEAT
BELT ..............................8O-12
BUCKLE - SECOND ROW INBOARD -
50/50 BENCH - REMOVAL, SEAT BELT....8O-12
BUMPER - DESCRIPTION, JOUNCE........2-35
BUMPER - INSTALLATION, STOP........23-25
BUMPER - OPERATION, JOUNCE.........2-35
BUMPER - REMOVAL, STOP............23-25
BUMPER BEZEL - INSTALLATION,
SLIDING DOOR STOP.................23-25
BUMPER BEZEL - REMOVAL, SLIDING
DOOR STOP........................23-25
BUMPER REINFORCEMENT -
INSTALLATION, FRONT.................13-2
BUMPER REINFORCEMENT -
INSTALLATION, REAR..................13-3
BUMPER REINFORCEMENT - REMOVAL,
FRONT..............................13-2
BUMPER REINFORCEMENT - REMOVAL,
REAR...............................13-3
BUS COMMUNICATION RECEIVE - PCM
INPUT - OPERATION, DATA.............8E-15
BUS, OPERATION - PROGRAMMABLE
COMMUNICATIONS INTERFACE (PCI).....14-21
BUSHING - INSTALLATION, LEAF SPRING
FRONT..............................2-29
BUSHING - REMOVAL, LEAF SPRING
FRONT..............................2-28
BUSHINGS - INSTALLATION, FRONT
CROSSMEMBER MOUNT...............13-12
BUSHINGS - REMOVAL, FRONT
CROSSMEMBER MOUNT...............13-12
BUSHINGS (DISC/DISC BRAKES) -
ASSEMBLY, CALIPER GUIDE PIN.........5-25
BUSHINGS (DISC/DISC BRAKES) -
DISASSEMBLY, CALIPER GUIDE PIN.......5-24
CABLE - CROSSOVER - INSTALLATION,
GEARSHIFT.........................21-76
CABLE - CROSSOVER - REMOVAL,
GEARSHIFT.........................21-73
CABLE - DESCRIPTION.................8P-4
CABLE - DESCRIPTION, ANTENNA BODY . . . 8A-4
CABLE - DESCRIPTION, SPARK PLUG.....8I-10
CABLE - DIAGNOSIS AND TESTING,
ANTENNA BODY......................8A-4
CABLE - DIAGNOSIS AND TESTING,
BATTERY...........................8F-16
CABLE - INSTALLATION................8P-4
CABLE - INSTALLATION, ANTENNA BODY
. . 8A-6
CABLE - INSTALLATION, FRONT
..........5-64
CABLE - INSTALLATION, GEAR SHIFT
....21-205
CABLE - INSTALLATION, HOLD OPEN
LATCH
.............................23-38
CABLE - INSTALLATION, INSIDE HANDLE
. . 23-37CABLE - INSTALLATION, INSTRUMENT
PANEL ANTENNA......................8A-9
CABLE - INSTALLATION, LATCH RELEASE . 23-61
CABLE - INSTALLATION, OUTSIDE
HANDLE............................23-36
CABLE - INSTALLATION, PARKING
BRAKE LEVER AND FRONT..............5-66
CABLE - INSTALLATION, THROTTLE
CONTROL..........................14-35
CABLE - OPERATION...................8P-4
CABLE - OPERATION, ANTENNA BODY.....8A-4
CABLE - REMOVAL....................8P-4
CABLE - REMOVAL, ANTENNA BODY......8A-5
CABLE - REMOVAL, FRONT..............5-64
CABLE - REMOVAL, GEAR SHIFT.......21-204
CABLE - REMOVAL, HOLD OPEN LATCH . . . 23-37
CABLE - REMOVAL, INSIDE HANDLE.....23-37
CABLE - REMOVAL, INSTRUMENT PANEL
ANTENNA...........................8A-8
CABLE - REMOVAL, LATCH RELEASE.....23-60
CABLE - REMOVAL, OUTSIDE HANDLE....23-36
CABLE - REMOVAL, PARKING BRAKE
LEVER AND FRONT....................5-65
CABLE - REMOVAL, THROTTLE
CONTROL..........................14-35
CABLE - SELECTOR - INSTALLATION,
GEARSHIFT.........................21-84
CABLE - SELECTOR - REMOVAL,
GEARSHIFT.........................21-81
CABLE ADJUSTMENT, ADJUSTMENTS -
GEARSHIFT........................21-206
CABLE ADJUSTMENT, INSTALLATION -
SYNCHRONIZING...............23-101,23-87
CABLE (FRONT) - INSTALLATION,
PARKING BRAKE......................5-63
CABLE (FRONT) - REMOVAL, PARKING
BRAKE..............................5-59
CABLE (INTERMEDIATE) -
INSTALLATION, PARKING BRAKE.........5-63
CABLE (INTERMEDIATE) - REMOVAL,
PARKING BRAKE......................5-60
CABLE (LEFT REAR) - INSTALLATION,
PARKING BRAKE......................5-64
CABLE (LEFT REAR) - REMOVAL,
PARKING BRAKE......................5-62
CABLE RESISTANCE, SPECIFICATIONS -
SPARK PLUG.........................8I-2
CABLE (RIGHT REAR) - INSTALLATION,
PARKING BRAKE......................5-63
CABLE (RIGHT REAR) - REMOVAL,
PARKING BRAKE......................5-60
CABLES - ADJUSTMENT, PARKING
BRAKE..............................5-64
CABLES - DESCRIPTION, BATTERY.......8F-16
CABLES - INSTALLATION, BATTERY......8F-18
CABLES - OPERATION, BATTERY........8F-16
CABLES - REMOVAL, BATTERY..........8F-18
CALIBRATION - STANDARD PROCEDURE,
COMPASS...........................8M-3
CALIBRATION - STANDARD PROCEDURE,
HEATER-A/C CONTROL.................24-8
CALIPER - CLEANING..............5-25,5-29
CALIPER - INSPECTION............5-25,5-29
CALIPER - INSTALLATION, REAR DISC
BRAKE..............................5-30
CALIPER - REMOVAL, REAR DISC
BRAKE..............................5-27
CALIPER ADAPTER - INSTALLATION,
FRONT DISC BRAKE...................5-31
CALIPER ADAPTER - REMOVAL, FRONT
DISC BRAKE.........................5-31
CALIPER (DISC/DISC BRAKES) -
INSTALLATION, FRONT DISC BRAKE......5-27
CALIPER (DISC/DISC BRAKES) -
REMOVAL, FRONT DISC BRAKE..........5-24
CALIPER (DISC/DRUM BRAKES) -
INSTALLATION, FRONT DISC BRAKE......5-27
CALIPER (DISC/DRUM BRAKES) -
REMOVAL, FRONT DISC BRAKE
..........5-24
CALIPER GUIDE PIN BUSHINGS
(DISC/DISC BRAKES) - ASSEMBLY
........5-25
CALIPER GUIDE PIN BUSHINGS
(DISC/DISC BRAKES) - DISASSEMBLY
.....5-24
CALIPER GUIDE PINS (DISC/DRUM
BRAKES) - INSTALLATION, DISC
BRAKE
..............................5-31
CALIPER GUIDE PINS (DISC/DRUM
BRAKES) - REMOVAL, DISC BRAKE
.......5-31CALIPER PISTON AND SEAL -
ASSEMBLY......................5-26,5-29
CALIPER PISTON AND SEAL -
DISASSEMBLY....................5-24,5-28
CAMSHAFT & BEARINGS (IN BLOCK) -
DESCRIPTION.......................9-115
CAMSHAFT & BEARINGS (IN BLOCK) -
INSPECTION........................9-115
CAMSHAFT & BEARINGS (IN BLOCK) -
INSTALLATION.......................9-115
CAMSHAFT & BEARINGS (IN BLOCK) -
OPERATION.........................9-115
CAMSHAFT & BEARINGS (IN BLOCK) -
REMOVAL..........................9-115
CAMSHAFT END PLAY - STANDARD
PROCEDURE, MEASURING..............9-29
CAMSHAFT OIL SEAL(S) - INSTALLATION . . 9-28
CAMSHAFT OIL SEAL(S) - REMOVAL......9-27
CAMSHAFT POSITION SENSOR -
DESCRIPTION.........................8I-3
CAMSHAFT POSITION SENSOR -
OPERATION..........................8I-3
CAMSHAFT SPROCKET - INSTALLATION,
TIMING CHAIN.......................9-157
CAMSHAFT SPROCKET - REMOVAL,
TIMING CHAIN.......................9-156
CAMSHAFT SPROCKETS - INSTALLATION . . 9-65
CAMSHAFT SPROCKETS - REMOVAL......9-64
CAMSHAFT(S) - CLEANING..............9-29
CAMSHAFT(S) - DESCRIPTION...........9-28
CAMSHAFT(S) - INSPECTION............9-30
CAMSHAFT(S) - INSTALLATION..........9-30
CAMSHAFT(S) - OPERATION.............9-28
CAMSHAFT(S) - REMOVAL..............9-29
CANISTER - DESCRIPTION, VAPOR......25-18
CANISTER - INSTALLATION, REAR EVAP . . 25-20
CANISTER - OPERATION, VAPOR........25-18
CANISTER - REMOVAL, REAR EVAP......25-19
CAP - DESCRIPTION, FUEL FILLER.......25-12
CAP - DESCRIPTION, RADIATOR
PRESSURE..........................7-26
CAP - INSTALLATION, INSTRUMENT
PANEL END.........................23-67
CAP - OPERATION, FUEL FILLER........25-12
CAP - OPERATION, RADIATOR
PRESSURE..........................7-27
CAP - REMOVAL, INSTRUMENT PANEL
END ...............................23-67
CAP TESTING - DIAGNOSIS AND
TESTING, COOLING SYSTEM
PRESSURE..........................7-27
CAP TO FILLER NECK SEAL -
DIAGNOSIS AND TESTING, RADIATOR.....7-27
CAPACITIES - SPECIFICATIONS, FLUID......0-6
CARE - CLEANING, ALUMINUM WHEEL . . . 22-18
CARPETS AND FLOOR MATS -
INSTALLATION.......................23-75
CARPETS AND FLOOR MATS - REMOVAL . 23-74
CARRIER ASSEMBLY - DESCRIPTION,
BALANCE SHAFTS.....................9-69
CARRIER ASSEMBLY - INSTALLATION,
BALANCE SHAFTS.....................9-72
CARRIER ASSEMBLY - OPERATION,
BALANCE SHAFTS.....................9-69
CARRIER ASSEMBLY - REMOVAL,
BALANCE SHAFTS.....................9-69
CARRIER SEAL - INSTALLATION,
DIFFERENTIAL........................21-9
CARRIER SEAL - REMOVAL,
DIFFERENTIAL........................21-9
CATALYTIC CONVERTER - DESCRIPTION . . . 11-4
CATALYTIC CONVERTER - INSPECTION....11-5
CATALYTIC CONVERTER - INSTALLATION . . . 11-6
CATALYTIC CONVERTER - OPERATION.....11-4
CATALYTIC CONVERTER - REMOVAL......11-5
CAUSES - DIAGNOSIS AND TESTING,
COMMON PROBLEM..................21-30
CAUTION - CAUTIONS..................5-78
CAUTION, A/C PLUMBING..............24-61
CAUTION, DESCRIPTION.................5-4
CAUTION, DESCRIPTION...............19-37
CAUTION, SENSOR - TPM..............22-10
CAUTIONS, CAUTION..................5-78
CAUTIONS, WARNING - WARNINGS
. 19-10,19-27
CD CHANGER - DESCRIPTION
...........8A-7
CD CHANGER - INSTALLATION
...........8A-8
CD CHANGER - OPERATION
.............8A-7
CD CHANGER - REMOVAL
..............8A-8
RSINDEX5
Description Group-Page Description Group-Page Description Group-Page
ProCarManuals.com
Page 2145 of 2177
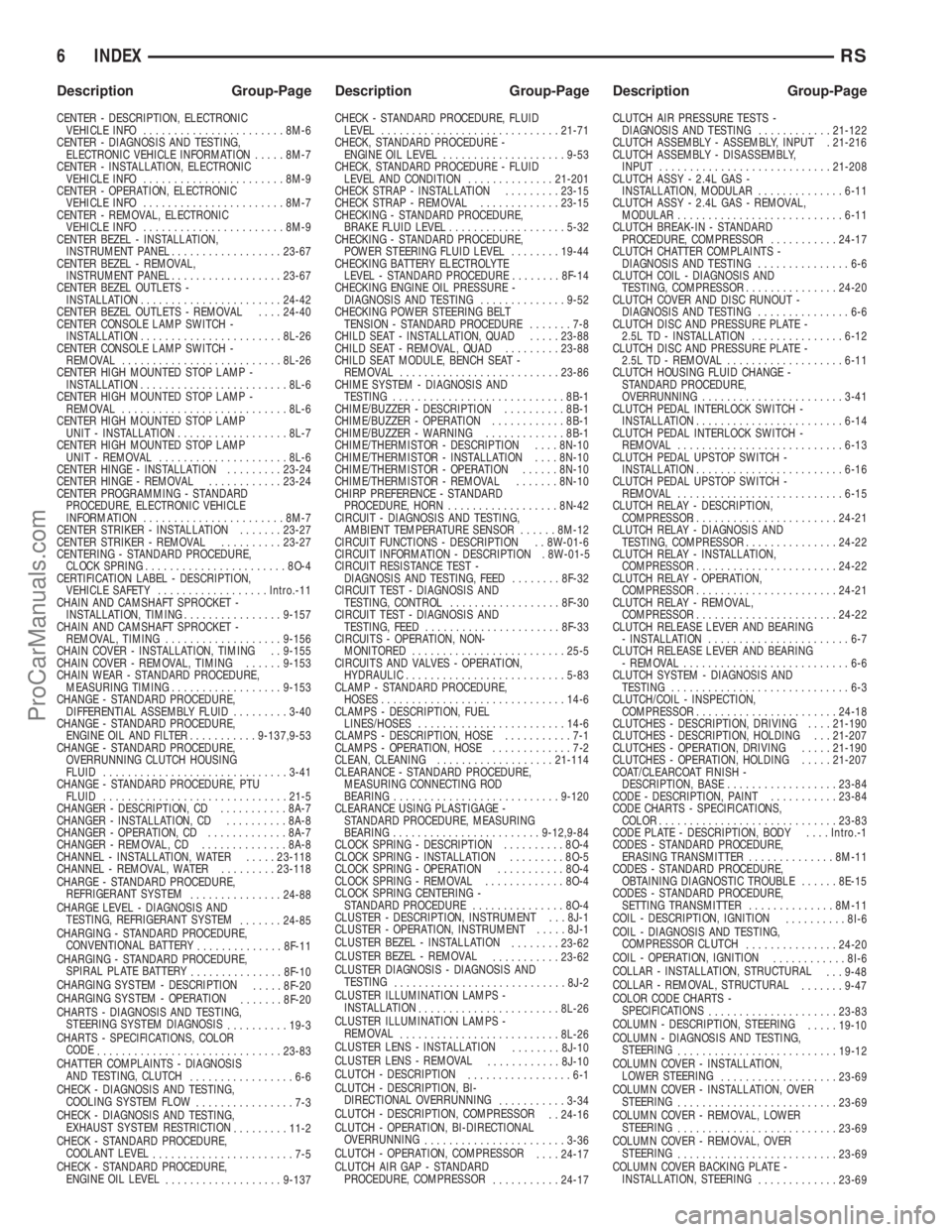
CENTER - DESCRIPTION, ELECTRONIC
VEHICLE INFO.......................8M-6
CENTER - DIAGNOSIS AND TESTING,
ELECTRONIC VEHICLE INFORMATION.....8M-7
CENTER - INSTALLATION, ELECTRONIC
VEHICLE INFO.......................8M-9
CENTER - OPERATION, ELECTRONIC
VEHICLE INFO.......................8M-7
CENTER - REMOVAL, ELECTRONIC
VEHICLE INFO.......................8M-9
CENTER BEZEL - INSTALLATION,
INSTRUMENT PANEL..................23-67
CENTER BEZEL - REMOVAL,
INSTRUMENT PANEL..................23-67
CENTER BEZEL OUTLETS -
INSTALLATION.......................24-42
CENTER BEZEL OUTLETS - REMOVAL....24-40
CENTER CONSOLE LAMP SWITCH -
INSTALLATION.......................8L-26
CENTER CONSOLE LAMP SWITCH -
REMOVAL..........................8L-26
CENTER HIGH MOUNTED STOP LAMP -
INSTALLATION........................8L-6
CENTER HIGH MOUNTED STOP LAMP -
REMOVAL...........................8L-6
CENTER HIGH MOUNTED STOP LAMP
UNIT - INSTALLATION..................8L-7
CENTER HIGH MOUNTED STOP LAMP
UNIT - REMOVAL.....................8L-6
CENTER HINGE - INSTALLATION.........23-24
CENTER HINGE - REMOVAL............23-24
CENTER PROGRAMMING - STANDARD
PROCEDURE, ELECTRONIC VEHICLE
INFORMATION.......................8M-7
CENTER STRIKER - INSTALLATION.......23-27
CENTER STRIKER - REMOVAL..........23-27
CENTERING - STANDARD PROCEDURE,
CLOCK SPRING.......................8O-4
CERTIFICATION LABEL - DESCRIPTION,
VEHICLE SAFETY..................Intro.-11
CHAIN AND CAMSHAFT SPROCKET -
INSTALLATION, TIMING................9-157
CHAIN AND CAMSHAFT SPROCKET -
REMOVAL, TIMING...................9-156
CHAIN COVER - INSTALLATION, TIMING . . 9-155
CHAIN COVER - REMOVAL, TIMING......9-153
CHAIN WEAR - STANDARD PROCEDURE,
MEASURING TIMING..................9-153
CHANGE - STANDARD PROCEDURE,
DIFFERENTIAL ASSEMBLY FLUID.........3-40
CHANGE - STANDARD PROCEDURE,
ENGINE OIL AND FILTER...........9-137,9-53
CHANGE - STANDARD PROCEDURE,
OVERRUNNING CLUTCH HOUSING
FLUID..............................3-41
CHANGE - STANDARD PROCEDURE, PTU
FLUID..............................21-5
CHANGER - DESCRIPTION, CD...........8A-7
CHANGER - INSTALLATION, CD..........8A-8
CHANGER - OPERATION, CD.............8A-7
CHANGER - REMOVAL, CD..............8A-8
CHANNEL - INSTALLATION, WATER.....23-118
CHANNEL - REMOVAL, WATER.........23-118
CHARGE - STANDARD PROCEDURE,
REFRIGERANT SYSTEM
...............24-88
CHARGE LEVEL - DIAGNOSIS AND
TESTING, REFRIGERANT SYSTEM
.......24-85
CHARGING - STANDARD PROCEDURE,
CONVENTIONAL BATTERY
..............8F-11
CHARGING - STANDARD PROCEDURE,
SPIRAL PLATE BATTERY
...............8F-10
CHARGING SYSTEM - DESCRIPTION
.....8F-20
CHARGING SYSTEM - OPERATION
.......8F-20
CHARTS - DIAGNOSIS AND TESTING,
STEERING SYSTEM DIAGNOSIS
..........19-3
CHARTS - SPECIFICATIONS, COLOR
CODE
..............................23-83
CHATTER COMPLAINTS - DIAGNOSIS
AND TESTING, CLUTCH
.................6-6
CHECK - DIAGNOSIS AND TESTING,
COOLING SYSTEM FLOW
................7-3
CHECK - DIAGNOSIS AND TESTING,
EXHAUST SYSTEM RESTRICTION
.........11-2
CHECK - STANDARD PROCEDURE,
COOLANT LEVEL
.......................7-5
CHECK - STANDARD PROCEDURE,
ENGINE OIL LEVEL
...................9-137CHECK - STANDARD PROCEDURE, FLUID
LEVEL.............................21-71
CHECK, STANDARD PROCEDURE -
ENGINE OIL LEVEL....................9-53
CHECK, STANDARD PROCEDURE - FLUID
LEVEL AND CONDITION..............21-201
CHECK STRAP - INSTALLATION.........23-15
CHECK STRAP - REMOVAL.............23-15
CHECKING - STANDARD PROCEDURE,
BRAKE FLUID LEVEL...................5-32
CHECKING - STANDARD PROCEDURE,
POWER STEERING FLUID LEVEL........19-44
CHECKING BATTERY ELECTROLYTE
LEVEL - STANDARD PROCEDURE........8F-14
CHECKING ENGINE OIL PRESSURE -
DIAGNOSIS AND TESTING..............9-52
CHECKING POWER STEERING BELT
TENSION - STANDARD PROCEDURE.......7-8
CHILD SEAT - INSTALLATION, QUAD.....23-88
CHILD SEAT - REMOVAL, QUAD.........23-88
CHILD SEAT MODULE, BENCH SEAT -
REMOVAL..........................23-86
CHIME SYSTEM - DIAGNOSIS AND
TESTING............................8B-1
CHIME/BUZZER - DESCRIPTION..........8B-1
CHIME/BUZZER - OPERATION............8B-1
CHIME/BUZZER - WARNING.............8B-1
CHIME/THERMISTOR - DESCRIPTION....8N-10
CHIME/THERMISTOR - INSTALLATION....8N-10
CHIME/THERMISTOR - OPERATION......8N-10
CHIME/THERMISTOR - REMOVAL.......8N-10
CHIRP PREFERENCE - STANDARD
PROCEDURE, HORN..................8N-42
CIRCUIT - DIAGNOSIS AND TESTING,
AMBIENT TEMPERATURE SENSOR......8M-12
CIRCUIT FUNCTIONS - DESCRIPTION . . 8W-01-6
CIRCUIT INFORMATION - DESCRIPTION . 8W-01-5
CIRCUIT RESISTANCE TEST -
DIAGNOSIS AND TESTING, FEED........8F-32
CIRCUIT TEST - DIAGNOSIS AND
TESTING, CONTROL..................8F-30
CIRCUIT TEST - DIAGNOSIS AND
TESTING, FEED......................8F-33
CIRCUITS - OPERATION, NON-
MONITORED.........................25-5
CIRCUITS AND VALVES - OPERATION,
HYDRAULIC..........................5-83
CLAMP - STANDARD PROCEDURE,
HOSES..............................14-6
CLAMPS - DESCRIPTION, FUEL
LINES/HOSES........................14-6
CLAMPS - DESCRIPTION, HOSE...........7-1
CLAMPS - OPERATION, HOSE.............7-2
CLEAN, CLEANING...................21-114
CLEARANCE - STANDARD PROCEDURE,
MEASURING CONNECTING ROD
BEARING...........................9-120
CLEARANCE USING PLASTIGAGE -
STANDARD PROCEDURE, MEASURING
BEARING........................9-12,9-84
CLOCK SPRING - DESCRIPTION..........8O-4
CLOCK SPRING - INSTALLATION.........8O-5
CLOCK SPRING - OPERATION...........8O-4
CLOCK SPRING - REMOVAL.............8O-4
CLOCK SPRING CENTERING -
STANDARD PROCEDURE...............8O-4
CLUSTER - DESCRIPTION, INSTRUMENT . . . 8J-1
CLUSTER - OPERATION, INSTRUMENT.....8J-1
CLUSTER BEZEL - INSTALLATION
........23-62
CLUSTER BEZEL - REMOVAL
...........23-62
CLUSTER DIAGNOSIS - DIAGNOSIS AND
TESTING
............................8J-2
CLUSTER ILLUMINATION LAMPS -
INSTALLATION
.......................8L-26
CLUSTER ILLUMINATION LAMPS -
REMOVAL
..........................8L-26
CLUSTER LENS - INSTALLATION
........8J-10
CLUSTER LENS - REMOVAL
............8J-10
CLUTCH - DESCRIPTION
.................6-1
CLUTCH - DESCRIPTION, BI-
DIRECTIONAL OVERRUNNING
...........3-34
CLUTCH - DESCRIPTION, COMPRESSOR
. . 24-16
CLUTCH - OPERATION, BI-DIRECTIONAL
OVERRUNNING
.......................3-36
CLUTCH - OPERATION, COMPRESSOR
....24-17
CLUTCH AIR GAP - STANDARD
PROCEDURE, COMPRESSOR
...........24-17CLUTCH AIR PRESSURE TESTS -
DIAGNOSIS AND TESTING............21-122
CLUTCH ASSEMBLY - ASSEMBLY, INPUT . 21-216
CLUTCH ASSEMBLY - DISASSEMBLY,
INPUT............................21-208
CLUTCH ASSY - 2.4L GAS -
INSTALLATION, MODULAR..............6-11
CLUTCH ASSY - 2.4L GAS - REMOVAL,
MODULAR...........................6-11
CLUTCH BREAK-IN - STANDARD
PROCEDURE, COMPRESSOR...........24-17
CLUTCH CHATTER COMPLAINTS -
DIAGNOSIS AND TESTING...............6-6
CLUTCH COIL - DIAGNOSIS AND
TESTING, COMPRESSOR...............24-20
CLUTCH COVER AND DISC RUNOUT -
DIAGNOSIS AND TESTING...............6-6
CLUTCH DISC AND PRESSURE PLATE -
2.5L TD - INSTALLATION...............6-12
CLUTCH DISC AND PRESSURE PLATE -
2.5L TD - REMOVAL...................6-11
CLUTCH HOUSING FLUID CHANGE -
STANDARD PROCEDURE,
OVERRUNNING.......................3-41
CLUTCH PEDAL INTERLOCK SWITCH -
INSTALLATION........................6-14
CLUTCH PEDAL INTERLOCK SWITCH -
REMOVAL...........................6-13
CLUTCH PEDAL UPSTOP SWITCH -
INSTALLATION........................6-16
CLUTCH PEDAL UPSTOP SWITCH -
REMOVAL...........................6-15
CLUTCH RELAY - DESCRIPTION,
COMPRESSOR........................24-21
CLUTCH RELAY - DIAGNOSIS AND
TESTING, COMPRESSOR...............24-22
CLUTCH RELAY - INSTALLATION,
COMPRESSOR.......................24-22
CLUTCH RELAY - OPERATION,
COMPRESSOR.......................24-21
CLUTCH RELAY - REMOVAL,
COMPRESSOR.......................24-22
CLUTCH RELEASE LEVER AND BEARING
- INSTALLATION.......................6-7
CLUTCH RELEASE LEVER AND BEARING
- REMOVAL...........................6-6
CLUTCH SYSTEM - DIAGNOSIS AND
TESTING.............................6-3
CLUTCH/COIL - INSPECTION,
COMPRESSOR.......................24-18
CLUTCHES - DESCRIPTION, DRIVING....21-190
CLUTCHES - DESCRIPTION, HOLDING . . . 21-207
CLUTCHES - OPERATION, DRIVING.....21-190
CLUTCHES - OPERATION, HOLDING.....21-207
COAT/CLEARCOAT FINISH -
DESCRIPTION, BASE..................23-84
CODE - DESCRIPTION, PAINT...........23-84
CODE CHARTS - SPECIFICATIONS,
COLOR.............................23-83
CODE PLATE - DESCRIPTION, BODY....Intro.-1
CODES - STANDARD PROCEDURE,
ERASING TRANSMITTER..............8M-11
CODES - STANDARD PROCEDURE,
OBTAINING DIAGNOSTIC TROUBLE......8E-15
CODES - STANDARD PROCEDURE,
SETTING TRANSMITTER..............8M-11
COIL - DESCRIPTION, IGNITION
..........8I-6
COIL - DIAGNOSIS AND TESTING,
COMPRESSOR CLUTCH
...............24-20
COIL - OPERATION, IGNITION
............8I-6
COLLAR - INSTALLATION, STRUCTURAL
. . . 9-48
COLLAR - REMOVAL, STRUCTURAL
.......9-47
COLOR CODE CHARTS -
SPECIFICATIONS
.....................23-83
COLUMN - DESCRIPTION, STEERING
.....19-10
COLUMN - DIAGNOSIS AND TESTING,
STEERING
..........................19-12
COLUMN COVER - INSTALLATION,
LOWER STEERING
...................23-69
COLUMN COVER - INSTALLATION, OVER
STEERING
..........................23-69
COLUMN COVER - REMOVAL, LOWER
STEERING
..........................23-69
COLUMN COVER - REMOVAL, OVER
STEERING
..........................23-69
COLUMN COVER BACKING PLATE -
INSTALLATION, STEERING
.............23-69
6 INDEXRS
Description Group-Page Description Group-Page Description Group-Page
ProCarManuals.com
Page 2147 of 2177
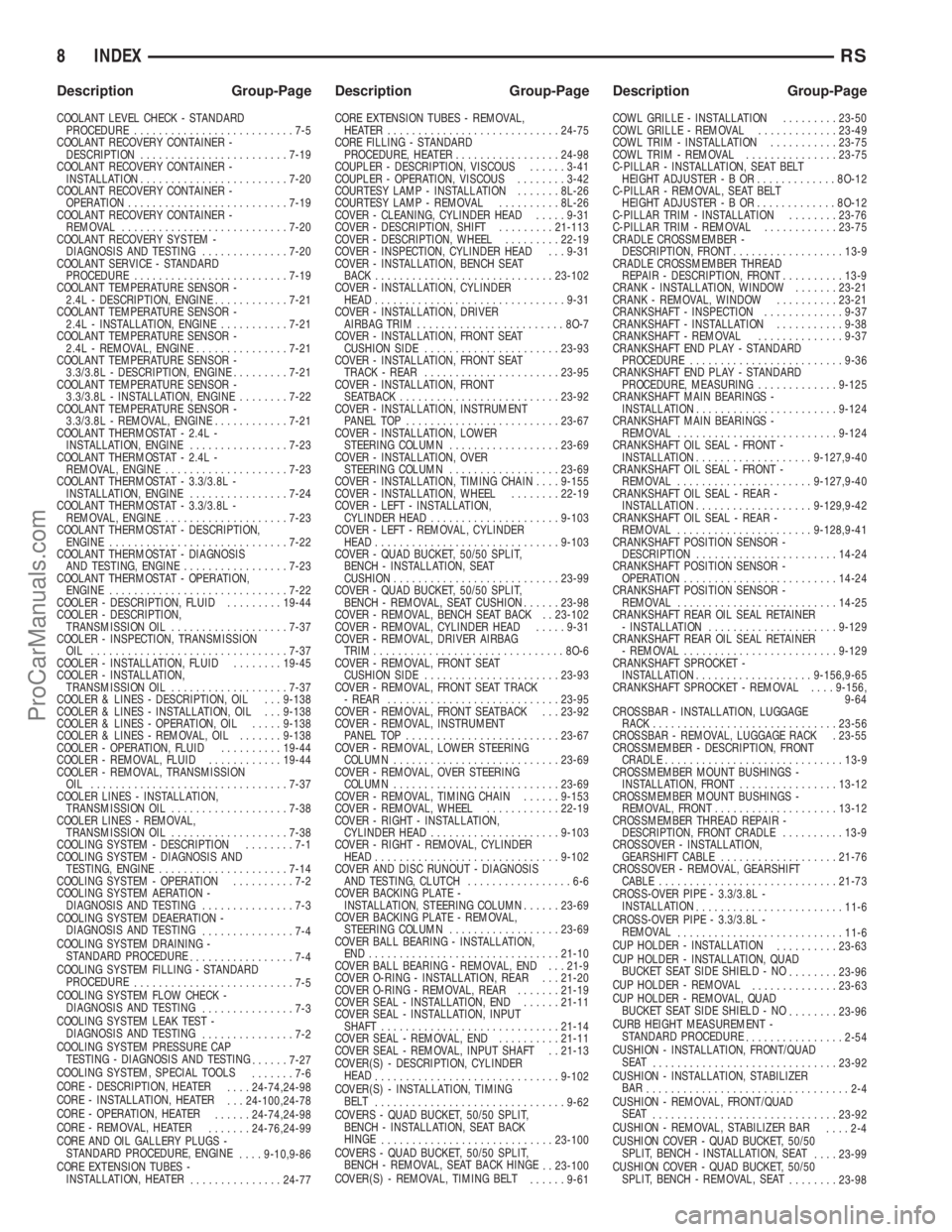
COOLANT LEVEL CHECK - STANDARD
PROCEDURE..........................7-5
COOLANT RECOVERY CONTAINER -
DESCRIPTION........................7-19
COOLANT RECOVERY CONTAINER -
INSTALLATION........................7-20
COOLANT RECOVERY CONTAINER -
OPERATION..........................7-19
COOLANT RECOVERY CONTAINER -
REMOVAL...........................7-20
COOLANT RECOVERY SYSTEM -
DIAGNOSIS AND TESTING..............7-20
COOLANT SERVICE - STANDARD
PROCEDURE.........................7-19
COOLANT TEMPERATURE SENSOR -
2.4L - DESCRIPTION, ENGINE............7-21
COOLANT TEMPERATURE SENSOR -
2.4L - INSTALLATION, ENGINE...........7-21
COOLANT TEMPERATURE SENSOR -
2.4L - REMOVAL, ENGINE...............7-21
COOLANT TEMPERATURE SENSOR -
3.3/3.8L - DESCRIPTION, ENGINE.........7-21
COOLANT TEMPERATURE SENSOR -
3.3/3.8L - INSTALLATION, ENGINE........7-22
COOLANT TEMPERATURE SENSOR -
3.3/3.8L - REMOVAL, ENGINE............7-21
COOLANT THERMOSTAT - 2.4L -
INSTALLATION, ENGINE................7-23
COOLANT THERMOSTAT - 2.4L -
REMOVAL, ENGINE....................7-23
COOLANT THERMOSTAT - 3.3/3.8L -
INSTALLATION, ENGINE................7-24
COOLANT THERMOSTAT - 3.3/3.8L -
REMOVAL, ENGINE......................7-23
COOLANT THERMOSTAT - DESCRIPTION,
ENGINE.............................7-22
COOLANT THERMOSTAT - DIAGNOSIS
AND TESTING, ENGINE.................7-23
COOLANT THERMOSTAT - OPERATION,
ENGINE.............................7-22
COOLER - DESCRIPTION, FLUID.........19-44
COOLER - DESCRIPTION,
TRANSMISSION OIL...................7-37
COOLER - INSPECTION, TRANSMISSION
OIL ................................7-37
COOLER - INSTALLATION, FLUID........19-45
COOLER - INSTALLATION,
TRANSMISSION OIL...................7-37
COOLER & LINES - DESCRIPTION, OIL . . . 9-138
COOLER & LINES - INSTALLATION, OIL . . . 9-138
COOLER & LINES - OPERATION, OIL.....9-138
COOLER & LINES - REMOVAL, OIL.......9-138
COOLER - OPERATION, FLUID..........19-44
COOLER - REMOVAL, FLUID............19-44
COOLER - REMOVAL, TRANSMISSION
OIL ................................7-37
COOLER LINES - INSTALLATION,
TRANSMISSION OIL...................7-38
COOLER LINES - REMOVAL,
TRANSMISSION OIL...................7-38
COOLING SYSTEM - DESCRIPTION........7-1
COOLING SYSTEM - DIAGNOSIS AND
TESTING, ENGINE.....................7-14
COOLING SYSTEM - OPERATION..........7-2
COOLING SYSTEM AERATION -
DIAGNOSIS AND TESTING...............7-3
COOLING SYSTEM DEAERATION -
DIAGNOSIS AND TESTING
...............7-4
COOLING SYSTEM DRAINING -
STANDARD PROCEDURE
.................7-4
COOLING SYSTEM FILLING - STANDARD
PROCEDURE
..........................7-5
COOLING SYSTEM FLOW CHECK -
DIAGNOSIS AND TESTING
...............7-3
COOLING SYSTEM LEAK TEST -
DIAGNOSIS AND TESTING
...............7-2
COOLING SYSTEM PRESSURE CAP
TESTING - DIAGNOSIS AND TESTING
......7-27
COOLING SYSTEM, SPECIAL TOOLS
.......7-6
CORE - DESCRIPTION, HEATER
....24-74,24-98
CORE - INSTALLATION, HEATER
. . . 24-100,24-78
CORE - OPERATION, HEATER
......24-74,24-98
CORE - REMOVAL, HEATER
.......24-76,24-99
CORE AND OIL GALLERY PLUGS -
STANDARD PROCEDURE, ENGINE
....9-10,9-86
CORE EXTENSION TUBES -
INSTALLATION, HEATER
...............24-77CORE EXTENSION TUBES - REMOVAL,
HEATER ............................24-75
CORE FILLING - STANDARD
PROCEDURE, HEATER.................24-98
COUPLER - DESCRIPTION, VISCOUS......3-41
COUPLER - OPERATION, VISCOUS........3-42
COURTESY LAMP - INSTALLATION.......8L-26
COURTESY LAMP - REMOVAL..........8L-26
COVER - CLEANING, CYLINDER HEAD.....9-31
COVER - DESCRIPTION, SHIFT.........21-113
COVER - DESCRIPTION, WHEEL.........22-19
COVER - INSPECTION, CYLINDER HEAD . . . 9-31
COVER - INSTALLATION, BENCH SEAT
BACK.............................23-102
COVER - INSTALLATION, CYLINDER
HEAD...............................9-31
COVER - INSTALLATION, DRIVER
AIRBAG TRIM........................8O-7
COVER - INSTALLATION, FRONT SEAT
CUSHION SIDE......................23-93
COVER - INSTALLATION, FRONT SEAT
TRACK - REAR......................23-95
COVER - INSTALLATION, FRONT
SEATBACK..........................23-92
COVER - INSTALLATION, INSTRUMENT
PANEL TOP.........................23-67
COVER - INSTALLATION, LOWER
STEERING COLUMN..................23-69
COVER - INSTALLATION, OVER
STEERING COLUMN..................23-69
COVER - INSTALLATION, TIMING CHAIN....9-155
COVER - INSTALLATION, WHEEL........22-19
COVER - LEFT - INSTALLATION,
CYLINDER HEAD.....................9-103
COVER - LEFT - REMOVAL, CYLINDER
HEAD..............................9-103
COVER - QUAD BUCKET, 50/50 SPLIT,
BENCH - INSTALLATION, SEAT
CUSHION...........................23-99
COVER - QUAD BUCKET, 50/50 SPLIT,
BENCH - REMOVAL, SEAT CUSHION......23-98
COVER - REMOVAL, BENCH SEAT BACK . . 23-102
COVER - REMOVAL, CYLINDER HEAD.....9-31
COVER - REMOVAL, DRIVER AIRBAG
TRIM...............................8O-6
COVER - REMOVAL, FRONT SEAT
CUSHION SIDE......................23-93
COVER - REMOVAL, FRONT SEAT TRACK
- REAR............................23-95
COVER - REMOVAL, FRONT SEATBACK . . . 23-92
COVER - REMOVAL, INSTRUMENT
PANEL TOP.........................23-67
COVER - REMOVAL, LOWER STEERING
COLUMN...........................23-69
COVER - REMOVAL, OVER STEERING
COLUMN...........................23-69
COVER - REMOVAL, TIMING CHAIN......9-153
COVER - REMOVAL, WHEEL............22-19
COVER - RIGHT - INSTALLATION,
CYLINDER HEAD.....................9-103
COVER - RIGHT - REMOVAL, CYLINDER
HEAD..............................9-102
COVER AND DISC RUNOUT - DIAGNOSIS
AND TESTING, CLUTCH.................6-6
COVER BACKING PLATE -
INSTALLATION, STEERING COLUMN......23-69
COVER BACKING PLATE - REMOVAL,
STEERING COLUMN..................23-69
COVER BALL BEARING - INSTALLATION,
END ...............................21-10
COVER BALL BEARING - REMOVAL, END . . . 21-9
COVER O-RING - INSTALLATION, REAR . . . 21-20
COVER O-RING - REMOVAL, REAR.......21-19
COVER SEAL - INSTALLATION, END......21-11
COVER SEAL - INSTALLATION, INPUT
SHAFT.............................21-14
COVER SEAL - REMOVAL, END..........21-11
COVER SEAL - REMOVAL, INPUT SHAFT . . 21-13
COVER(S) - DESCRIPTION, CYLINDER
HEAD
..............................9-102
COVER(S) - INSTALLATION, TIMING
BELT
...............................9-62
COVERS - QUAD BUCKET, 50/50 SPLIT,
BENCH - INSTALLATION, SEAT BACK
HINGE
............................23-100
COVERS - QUAD BUCKET, 50/50 SPLIT,
BENCH - REMOVAL, SEAT BACK HINGE
. . 23-100
COVER(S) - REMOVAL, TIMING BELT
......9-61COWL GRILLE - INSTALLATION.........23-50
COWL GRILLE - REMOVAL.............23-49
COWL TRIM - INSTALLATION...........23-75
COWL TRIM - REMOVAL...............23-75
C-PILLAR - INSTALLATION, SEAT BELT
HEIGHT ADJUSTER-BOR.............8O-12
C-PILLAR - REMOVAL, SEAT BELT
HEIGHT ADJUSTER-BOR.............8O-12
C-PILLAR TRIM - INSTALLATION........23-76
C-PILLAR TRIM - REMOVAL............23-75
CRADLE CROSSMEMBER -
DESCRIPTION, FRONT..................13-9
CRADLE CROSSMEMBER THREAD
REPAIR - DESCRIPTION, FRONT..........13-9
CRANK - INSTALLATION, WINDOW.......23-21
CRANK - REMOVAL, WINDOW..........23-21
CRANKSHAFT - INSPECTION.............9-37
CRANKSHAFT - INSTALLATION...........9-38
CRANKSHAFT - REMOVAL..............9-37
CRANKSHAFT END PLAY - STANDARD
PROCEDURE.........................9-36
CRANKSHAFT END PLAY - STANDARD
PROCEDURE, MEASURING.............9-125
CRANKSHAFT MAIN BEARINGS -
INSTALLATION.......................9-124
CRANKSHAFT MAIN BEARINGS -
REMOVAL..........................9-124
CRANKSHAFT OIL SEAL - FRONT -
INSTALLATION...................9-127,9-40
CRANKSHAFT OIL SEAL - FRONT -
REMOVAL......................9-127,9-40
CRANKSHAFT OIL SEAL - REAR -
INSTALLATION...................9-129,9-42
CRANKSHAFT OIL SEAL - REAR -
REMOVAL......................9-128,9-41
CRANKSHAFT POSITION SENSOR -
DESCRIPTION.......................14-24
CRANKSHAFT POSITION SENSOR -
OPERATION.........................14-24
CRANKSHAFT POSITION SENSOR -
REMOVAL..........................14-25
CRANKSHAFT REAR OIL SEAL RETAINER
- INSTALLATION.....................9-129
CRANKSHAFT REAR OIL SEAL RETAINER
- REMOVAL.........................9-129
CRANKSHAFT SPROCKET -
INSTALLATION...................9-156,9-65
CRANKSHAFT SPROCKET - REMOVAL....9-156,
9-64
CROSSBAR - INSTALLATION, LUGGAGE
RACK..............................23-56
CROSSBAR - REMOVAL, LUGGAGE RACK . 23-55
CROSSMEMBER - DESCRIPTION, FRONT
CRADLE.............................13-9
CROSSMEMBER MOUNT BUSHINGS -
INSTALLATION, FRONT................13-12
CROSSMEMBER MOUNT BUSHINGS -
REMOVAL, FRONT....................13-12
CROSSMEMBER THREAD REPAIR -
DESCRIPTION, FRONT CRADLE..........13-9
CROSSOVER - INSTALLATION,
GEARSHIFT CABLE...................21-76
CROSSOVER - REMOVAL, GEARSHIFT
CABLE.............................21-73
CROSS-OVER PIPE - 3.3/3.8L -
INSTALLATION
........................11-6
CROSS-OVER PIPE - 3.3/3.8L -
REMOVAL
...........................11-6
CUP HOLDER - INSTALLATION
..........23-63
CUP HOLDER - INSTALLATION, QUAD
BUCKET SEAT SIDE SHIELD - NO
........23-96
CUP HOLDER - REMOVAL
..............23-63
CUP HOLDER - REMOVAL, QUAD
BUCKET SEAT SIDE SHIELD - NO
........23-96
CURB HEIGHT MEASUREMENT -
STANDARD PROCEDURE
................2-54
CUSHION - INSTALLATION, FRONT/QUAD
SEAT
..............................23-92
CUSHION - INSTALLATION, STABILIZER
BAR
.................................2-4
CUSHION - REMOVAL, FRONT/QUAD
SEAT
..............................23-92
CUSHION - REMOVAL, STABILIZER BAR
....2-4
CUSHION COVER - QUAD BUCKET, 50/50
SPLIT, BENCH - INSTALLATION, SEAT
....23-99
CUSHION COVER - QUAD BUCKET, 50/50
SPLIT, BENCH - REMOVAL, SEAT
........23-98
8 INDEXRS
Description Group-Page Description Group-Page Description Group-Page
ProCarManuals.com