DAEWOO NUBIRA 2004 Service Repair Manual
Manufacturer: DAEWOO, Model Year: 2004, Model line: NUBIRA, Model: DAEWOO NUBIRA 2004Pages: 2643, PDF Size: 80.54 MB
Page 871 of 2643
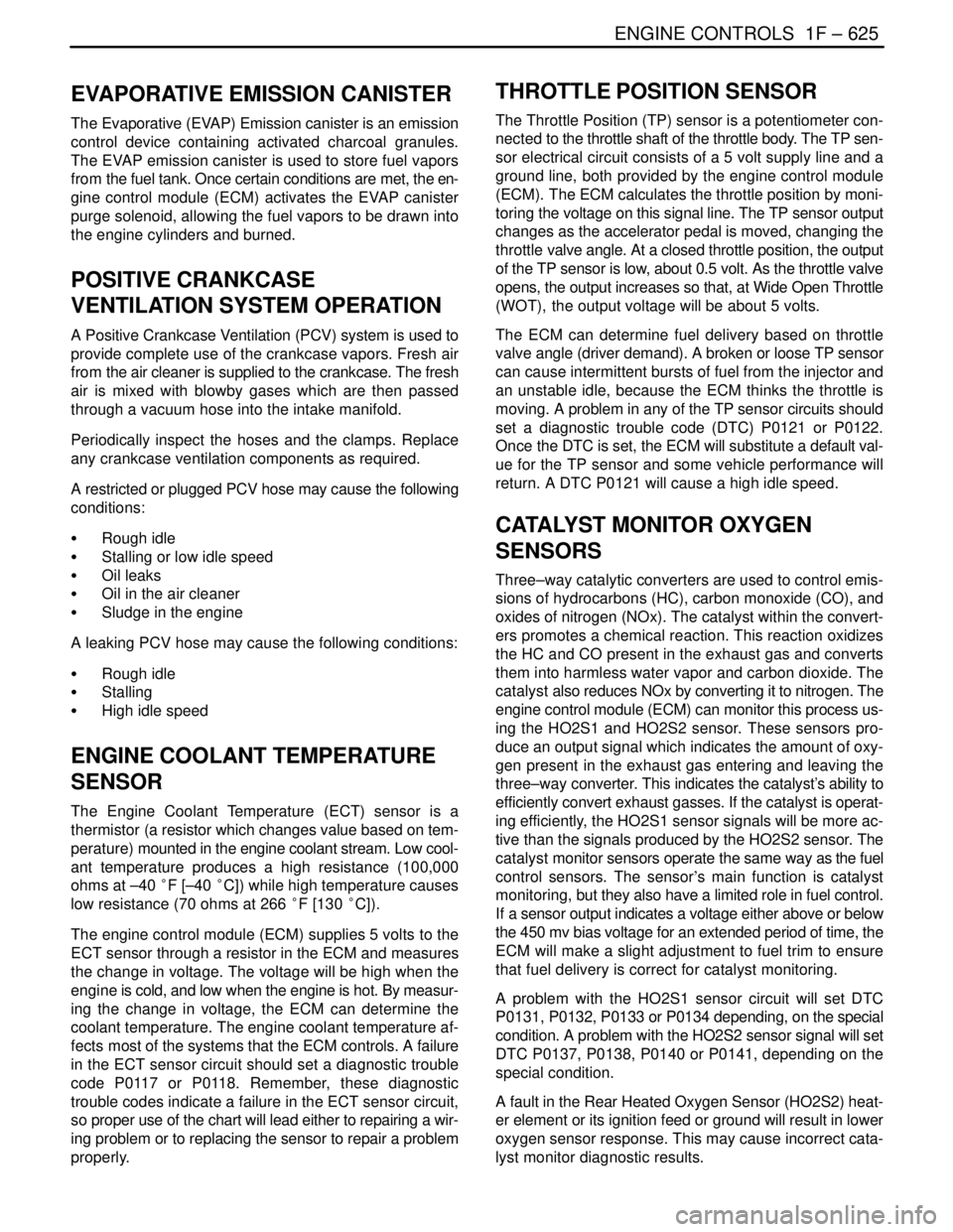
ENGINE CONTROLS 1F – 625
DAEWOO V–121 BL4
EVAPORATIVE EMISSION CANISTER
The Evaporative (EVAP) Emission canister is an emission
control device containing activated charcoal granules.
The EVAP emission canister is used to store fuel vapors
from the fuel tank. Once certain conditions are met, the en-
gine control module (ECM) activates the EVAP canister
purge solenoid, allowing the fuel vapors to be drawn into
the engine cylinders and burned.
POSITIVE CRANKCASE
VENTILATION SYSTEM OPERATION
A Positive Crankcase Ventilation (PCV) system is used to
provide complete use of the crankcase vapors. Fresh air
from the air cleaner is supplied to the crankcase. The fresh
air is mixed with blowby gases which are then passed
through a vacuum hose into the intake manifold.
Periodically inspect the hoses and the clamps. Replace
any crankcase ventilation components as required.
A restricted or plugged PCV hose may cause the following
conditions:
S Rough idle
S Stalling or low idle speed
S Oil leaks
S Oil in the air cleaner
S Sludge in the engine
A leaking PCV hose may cause the following conditions:
S Rough idle
S Stalling
S High idle speed
ENGINE COOLANT TEMPERATURE
SENSOR
The Engine Coolant Temperature (ECT) sensor is a
thermistor (a resistor which changes value based on tem-
perature) mounted in the engine coolant stream. Low cool-
ant temperature produces a high resistance (100,000
ohms at –40 °F [–40 °C]) while high temperature causes
low resistance (70 ohms at 266 °F [130 °C]).
The engine control module (ECM) supplies 5 volts to the
ECT sensor through a resistor in the ECM and measures
the change in voltage. The voltage will be high when the
engine is cold, and low when the engine is hot. By measur-
ing the change in voltage, the ECM can determine the
coolant temperature. The engine coolant temperature af-
fects most of the systems that the ECM controls. A failure
in the ECT sensor circuit should set a diagnostic trouble
code P0117 or P0118. Remember, these diagnostic
trouble codes indicate a failure in the ECT sensor circuit,
so proper use of the chart will lead either to repairing a wir-
ing problem or to replacing the sensor to repair a problem
properly.
THROTTLE POSITION SENSOR
The Throttle Position (TP) sensor is a potentiometer con-
nected to the throttle shaft of the throttle body. The TP sen-
sor electrical circuit consists of a 5 volt supply line and a
ground line, both provided by the engine control module
(ECM). The ECM calculates the throttle position by moni-
toring the voltage on this signal line. The TP sensor output
changes as the accelerator pedal is moved, changing the
throttle valve angle. At a closed throttle position, the output
of the TP sensor is low, about 0.5 volt. As the throttle valve
opens, the output increases so that, at Wide Open Throttle
(WOT), the output voltage will be about 5 volts.
The ECM can determine fuel delivery based on throttle
valve angle (driver demand). A broken or loose TP sensor
can cause intermittent bursts of fuel from the injector and
an unstable idle, because the ECM thinks the throttle is
moving. A problem in any of the TP sensor circuits should
set a diagnostic trouble code (DTC) P0121 or P0122.
Once the DTC is set, the ECM will substitute a default val-
ue for the TP sensor and some vehicle performance will
return. A DTC P0121 will cause a high idle speed.
CATALYST MONITOR OXYGEN
SENSORS
Three–way catalytic converters are used to control emis-
sions of hydrocarbons (HC), carbon monoxide (CO), and
oxides of nitrogen (NOx). The catalyst within the convert-
ers promotes a chemical reaction. This reaction oxidizes
the HC and CO present in the exhaust gas and converts
them into harmless water vapor and carbon dioxide. The
catalyst also reduces NOx by converting it to nitrogen. The
engine control module (ECM) can monitor this process us-
ing the HO2S1 and HO2S2 sensor. These sensors pro-
duce an output signal which indicates the amount of oxy-
gen present in the exhaust gas entering and leaving the
three–way converter. This indicates the catalyst’s ability to
efficiently convert exhaust gasses. If the catalyst is operat-
ing efficiently, the HO2S1 sensor signals will be more ac-
tive than the signals produced by the HO2S2 sensor. The
catalyst monitor sensors operate the same way as the fuel
control sensors. The sensor’s main function is catalyst
monitoring, but they also have a limited role in fuel control.
If a sensor output indicates a voltage either above or below
the 450 mv bias voltage for an extended period of time, the
ECM will make a slight adjustment to fuel trim to ensure
that fuel delivery is correct for catalyst monitoring.
A problem with the HO2S1 sensor circuit will set DTC
P0131, P0132, P0133 or P0134 depending, on the special
condition. A problem with the HO2S2 sensor signal will set
DTC P0137, P0138, P0140 or P0141, depending on the
special condition.
A fault in the Rear Heated Oxygen Sensor (HO2S2) heat-
er element or its ignition feed or ground will result in lower
oxygen sensor response. This may cause incorrect cata-
lyst monitor diagnostic results.
Page 872 of 2643
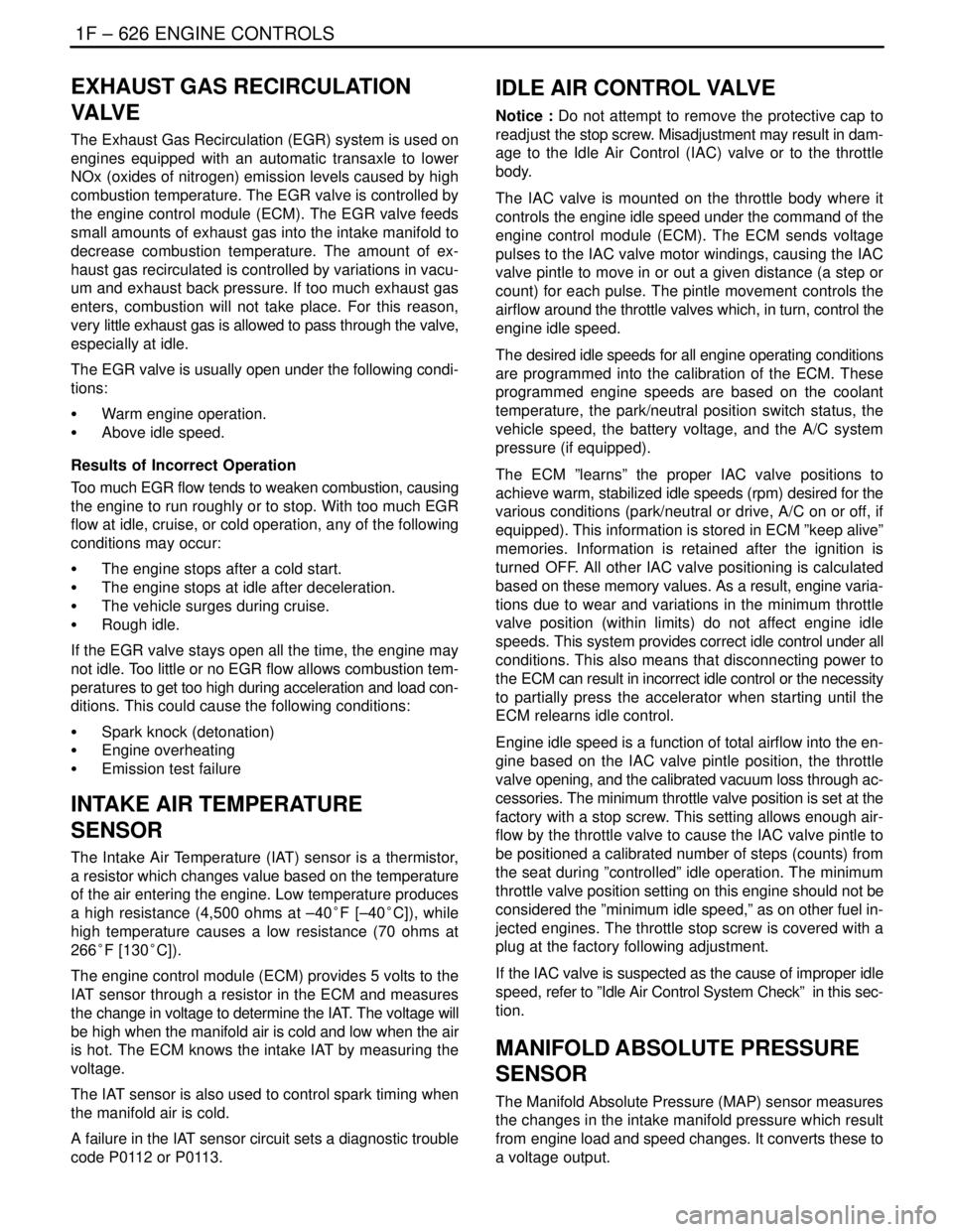
1F – 626IENGINE CONTROLS
DAEWOO V–121 BL4
EXHAUST GAS RECIRCULATION
VA LV E
The Exhaust Gas Recirculation (EGR) system is used on
engines equipped with an automatic transaxle to lower
NOx (oxides of nitrogen) emission levels caused by high
combustion temperature. The EGR valve is controlled by
the engine control module (ECM). The EGR valve feeds
small amounts of exhaust gas into the intake manifold to
decrease combustion temperature. The amount of ex-
haust gas recirculated is controlled by variations in vacu-
um and exhaust back pressure. If too much exhaust gas
enters, combustion will not take place. For this reason,
very little exhaust gas is allowed to pass through the valve,
especially at idle.
The EGR valve is usually open under the following condi-
tions:
S Warm engine operation.
S Above idle speed.
Results of Incorrect Operation
Too much EGR flow tends to weaken combustion, causing
the engine to run roughly or to stop. With too much EGR
flow at idle, cruise, or cold operation, any of the following
conditions may occur:
S The engine stops after a cold start.
S The engine stops at idle after deceleration.
S The vehicle surges during cruise.
S Rough idle.
If the EGR valve stays open all the time, the engine may
not idle. Too little or no EGR flow allows combustion tem-
peratures to get too high during acceleration and load con-
ditions. This could cause the following conditions:
S Spark knock (detonation)
S Engine overheating
S Emission test failure
INTAKE AIR TEMPERATURE
SENSOR
The Intake Air Temperature (IAT) sensor is a thermistor,
a resistor which changes value based on the temperature
of the air entering the engine. Low temperature produces
a high resistance (4,500 ohms at –40°F [–40°C]), while
high temperature causes a low resistance (70 ohms at
266°F [130°C]).
The engine control module (ECM) provides 5 volts to the
IAT sensor through a resistor in the ECM and measures
the change in voltage to determine the IAT. The voltage will
be high when the manifold air is cold and low when the air
is hot. The ECM knows the intake IAT by measuring the
voltage.
The IAT sensor is also used to control spark timing when
the manifold air is cold.
A failure in the IAT sensor circuit sets a diagnostic trouble
code P0112 or P0113.
IDLE AIR CONTROL VALVE
Notice : Do not attempt to remove the protective cap to
readjust the stop screw. Misadjustment may result in dam-
age to the Idle Air Control (IAC) valve or to the throttle
body.
The IAC valve is mounted on the throttle body where it
controls the engine idle speed under the command of the
engine control module (ECM). The ECM sends voltage
pulses to the IAC valve motor windings, causing the IAC
valve pintle to move in or out a given distance (a step or
count) for each pulse. The pintle movement controls the
airflow around the throttle valves which, in turn, control the
engine idle speed.
The desired idle speeds for all engine operating conditions
are programmed into the calibration of the ECM. These
programmed engine speeds are based on the coolant
temperature, the park/neutral position switch status, the
vehicle speed, the battery voltage, and the A/C system
pressure (if equipped).
The ECM ”learns” the proper IAC valve positions to
achieve warm, stabilized idle speeds (rpm) desired for the
various conditions (park/neutral or drive, A/C on or off, if
equipped). This information is stored in ECM ”keep alive”
memories. Information is retained after the ignition is
turned OFF. All other IAC valve positioning is calculated
based on these memory values. As a result, engine varia-
tions due to wear and variations in the minimum throttle
valve position (within limits) do not affect engine idle
speeds. This system provides correct idle control under all
conditions. This also means that disconnecting power to
the ECM can result in incorrect idle control or the necessity
to partially press the accelerator when starting until the
ECM relearns idle control.
Engine idle speed is a function of total airflow into the en-
gine based on the IAC valve pintle position, the throttle
valve opening, and the calibrated vacuum loss through ac-
cessories. The minimum throttle valve position is set at the
factory with a stop screw. This setting allows enough air-
flow by the throttle valve to cause the IAC valve pintle to
be positioned a calibrated number of steps (counts) from
the seat during ”controlled” idle operation. The minimum
throttle valve position setting on this engine should not be
considered the ”minimum idle speed,” as on other fuel in-
jected engines. The throttle stop screw is covered with a
plug at the factory following adjustment.
If the IAC valve is suspected as the cause of improper idle
speed, refer to ”Idle Air Control System Check” in this sec-
tion.
MANIFOLD ABSOLUTE PRESSURE
SENSOR
The Manifold Absolute Pressure (MAP) sensor measures
the changes in the intake manifold pressure which result
from engine load and speed changes. It converts these to
a voltage output.
Page 873 of 2643
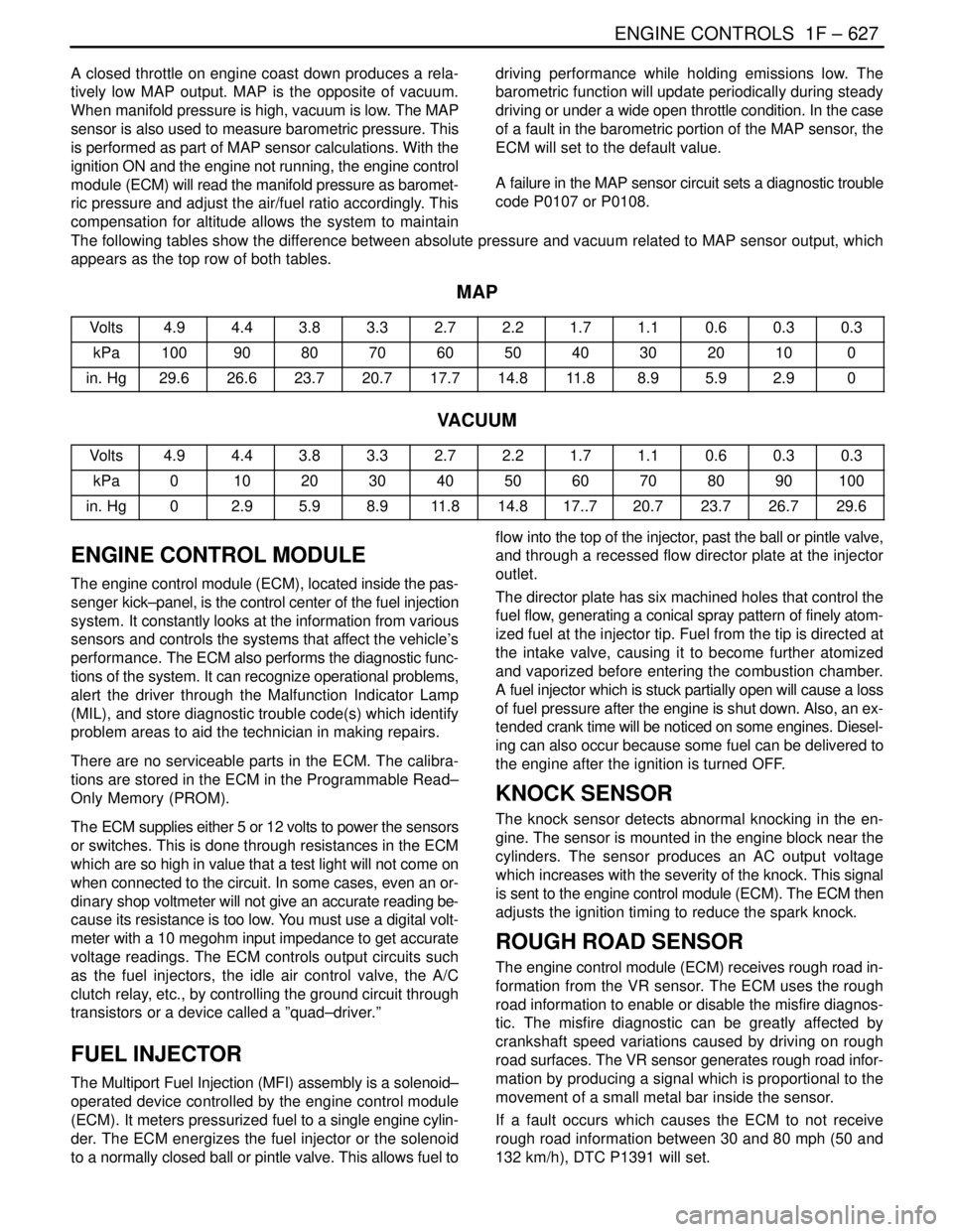
ENGINE CONTROLS 1F – 627
DAEWOO V–121 BL4
A closed throttle on engine coast down produces a rela-
tively low MAP output. MAP is the opposite of vacuum.
When manifold pressure is high, vacuum is low. The MAP
sensor is also used to measure barometric pressure. This
is performed as part of MAP sensor calculations. With the
ignition ON and the engine not running, the engine control
module (ECM) will read the manifold pressure as baromet-
ric pressure and adjust the air/fuel ratio accordingly. This
compensation for altitude allows the system to maintaindriving performance while holding emissions low. The
barometric function will update periodically during steady
driving or under a wide open throttle condition. In the case
of a fault in the barometric portion of the MAP sensor, the
ECM will set to the default value.
A failure in the MAP sensor circuit sets a diagnostic trouble
code P0107 or P0108.
The following tables show the difference between absolute pressure and vacuum related to MAP sensor output, which
appears as the top row of both tables.
MAP
Volts4.94.43.83.32.72.21.71.10.60.30.3
kPa1009080706050403020100
in. Hg29.626.623.720.717.714.811.88.95.92.90
VACUUM
Volts4.94.43.83.32.72.21.71.10.60.30.3
kPa0102030405060708090100
in. Hg02.95.98.911.814.817..720.723.726.729.6
ENGINE CONTROL MODULE
The engine control module (ECM), located inside the pas-
senger kick–panel, is the control center of the fuel injection
system. It constantly looks at the information from various
sensors and controls the systems that affect the vehicle’s
performance. The ECM also performs the diagnostic func-
tions of the system. It can recognize operational problems,
alert the driver through the Malfunction Indicator Lamp
(MIL), and store diagnostic trouble code(s) which identify
problem areas to aid the technician in making repairs.
There are no serviceable parts in the ECM. The calibra-
tions are stored in the ECM in the Programmable Read–
Only Memory (PROM).
The ECM supplies either 5 or 12 volts to power the sensors
or switches. This is done through resistances in the ECM
which are so high in value that a test light will not come on
when connected to the circuit. In some cases, even an or-
dinary shop voltmeter will not give an accurate reading be-
cause its resistance is too low. You must use a digital volt-
meter with a 10 megohm input impedance to get accurate
voltage readings. The ECM controls output circuits such
as the fuel injectors, the idle air control valve, the A/C
clutch relay, etc., by controlling the ground circuit through
transistors or a device called a ”quad–driver.”
FUEL INJECTOR
The Multiport Fuel Injection (MFI) assembly is a solenoid–
operated device controlled by the engine control module
(ECM). It meters pressurized fuel to a single engine cylin-
der. The ECM energizes the fuel injector or the solenoid
to a normally closed ball or pintle valve. This allows fuel toflow into the top of the injector, past the ball or pintle valve,
and through a recessed flow director plate at the injector
outlet.
The director plate has six machined holes that control the
fuel flow, generating a conical spray pattern of finely atom-
ized fuel at the injector tip. Fuel from the tip is directed at
the intake valve, causing it to become further atomized
and vaporized before entering the combustion chamber.
A fuel injector which is stuck partially open will cause a loss
of fuel pressure after the engine is shut down. Also, an ex-
tended crank time will be noticed on some engines. Diesel-
ing can also occur because some fuel can be delivered to
the engine after the ignition is turned OFF.
KNOCK SENSOR
The knock sensor detects abnormal knocking in the en-
gine. The sensor is mounted in the engine block near the
cylinders. The sensor produces an AC output voltage
which increases with the severity of the knock. This signal
is sent to the engine control module (ECM). The ECM then
adjusts the ignition timing to reduce the spark knock.
ROUGH ROAD SENSOR
The engine control module (ECM) receives rough road in-
formation from the VR sensor. The ECM uses the rough
road information to enable or disable the misfire diagnos-
tic. The misfire diagnostic can be greatly affected by
crankshaft speed variations caused by driving on rough
road surfaces. The VR sensor generates rough road infor-
mation by producing a signal which is proportional to the
movement of a small metal bar inside the sensor.
If a fault occurs which causes the ECM to not receive
rough road information between 30 and 80 mph (50 and
132 km/h), DTC P1391 will set.
Page 874 of 2643
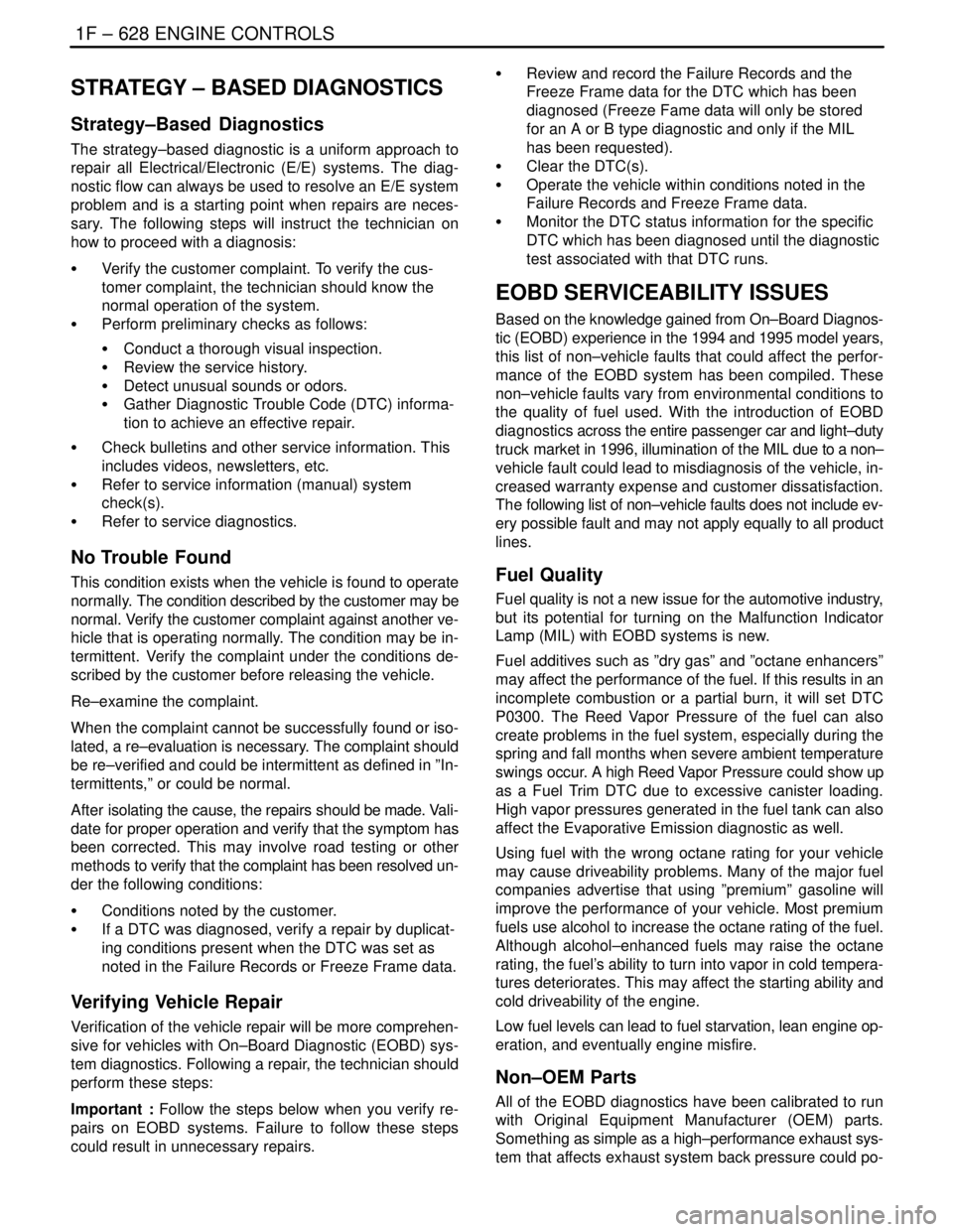
1F – 628IENGINE CONTROLS
DAEWOO V–121 BL4
STRATEGY – BASED DIAGNOSTICS
Strategy–Based Diagnostics
The strategy–based diagnostic is a uniform approach to
repair all Electrical/Electronic (E/E) systems. The diag-
nostic flow can always be used to resolve an E/E system
problem and is a starting point when repairs are neces-
sary. The following steps will instruct the technician on
how to proceed with a diagnosis:
S Verify the customer complaint. To verify the cus-
tomer complaint, the technician should know the
normal operation of the system.
S Perform preliminary checks as follows:
S Conduct a thorough visual inspection.
S Review the service history.
S Detect unusual sounds or odors.
S Gather Diagnostic Trouble Code (DTC) informa-
tion to achieve an effective repair.
S Check bulletins and other service information. This
includes videos, newsletters, etc.
S Refer to service information (manual) system
check(s).
S Refer to service diagnostics.
No Trouble Found
This condition exists when the vehicle is found to operate
normally. The condition described by the customer may be
normal. Verify the customer complaint against another ve-
hicle that is operating normally. The condition may be in-
termittent. Verify the complaint under the conditions de-
scribed by the customer before releasing the vehicle.
Re–examine the complaint.
When the complaint cannot be successfully found or iso-
lated, a re–evaluation is necessary. The complaint should
be re–verified and could be intermittent as defined in ”In-
termittents,” or could be normal.
After isolating the cause, the repairs should be made. Vali-
date for proper operation and verify that the symptom has
been corrected. This may involve road testing or other
methods to verify that the complaint has been resolved un-
der the following conditions:
S Conditions noted by the customer.
S If a DTC was diagnosed, verify a repair by duplicat-
ing conditions present when the DTC was set as
noted in the Failure Records or Freeze Frame data.
Verifying Vehicle Repair
Verification of the vehicle repair will be more comprehen-
sive for vehicles with On–Board Diagnostic (EOBD) sys-
tem diagnostics. Following a repair, the technician should
perform these steps:
Important : Follow the steps below when you verify re-
pairs on EOBD systems. Failure to follow these steps
could result in unnecessary repairs.S Review and record the Failure Records and the
Freeze Frame data for the DTC which has been
diagnosed (Freeze Fame data will only be stored
for an A or B type diagnostic and only if the MIL
has been requested).
S Clear the DTC(s).
S Operate the vehicle within conditions noted in the
Failure Records and Freeze Frame data.
S Monitor the DTC status information for the specific
DTC which has been diagnosed until the diagnostic
test associated with that DTC runs.
EOBD SERVICEABILITY ISSUES
Based on the knowledge gained from On–Board Diagnos-
tic (EOBD) experience in the 1994 and 1995 model years,
this list of non–vehicle faults that could affect the perfor-
mance of the EOBD system has been compiled. These
non–vehicle faults vary from environmental conditions to
the quality of fuel used. With the introduction of EOBD
diagnostics across the entire passenger car and light–duty
truck market in 1996, illumination of the MIL due to a non–
vehicle fault could lead to misdiagnosis of the vehicle, in-
creased warranty expense and customer dissatisfaction.
The following list of non–vehicle faults does not include ev-
ery possible fault and may not apply equally to all product
lines.
Fuel Quality
Fuel quality is not a new issue for the automotive industry,
but its potential for turning on the Malfunction Indicator
Lamp (MIL) with EOBD systems is new.
Fuel additives such as ”dry gas” and ”octane enhancers”
may affect the performance of the fuel. If this results in an
incomplete combustion or a partial burn, it will set DTC
P0300. The Reed Vapor Pressure of the fuel can also
create problems in the fuel system, especially during the
spring and fall months when severe ambient temperature
swings occur. A high Reed Vapor Pressure could show up
as a Fuel Trim DTC due to excessive canister loading.
High vapor pressures generated in the fuel tank can also
affect the Evaporative Emission diagnostic as well.
Using fuel with the wrong octane rating for your vehicle
may cause driveability problems. Many of the major fuel
companies advertise that using ”premium” gasoline will
improve the performance of your vehicle. Most premium
fuels use alcohol to increase the octane rating of the fuel.
Although alcohol–enhanced fuels may raise the octane
rating, the fuel’s ability to turn into vapor in cold tempera-
tures deteriorates. This may affect the starting ability and
cold driveability of the engine.
Low fuel levels can lead to fuel starvation, lean engine op-
eration, and eventually engine misfire.
Non–OEM Parts
All of the EOBD diagnostics have been calibrated to run
with Original Equipment Manufacturer (OEM) parts.
Something as simple as a high–performance exhaust sys-
tem that affects exhaust system back pressure could po-
Page 875 of 2643
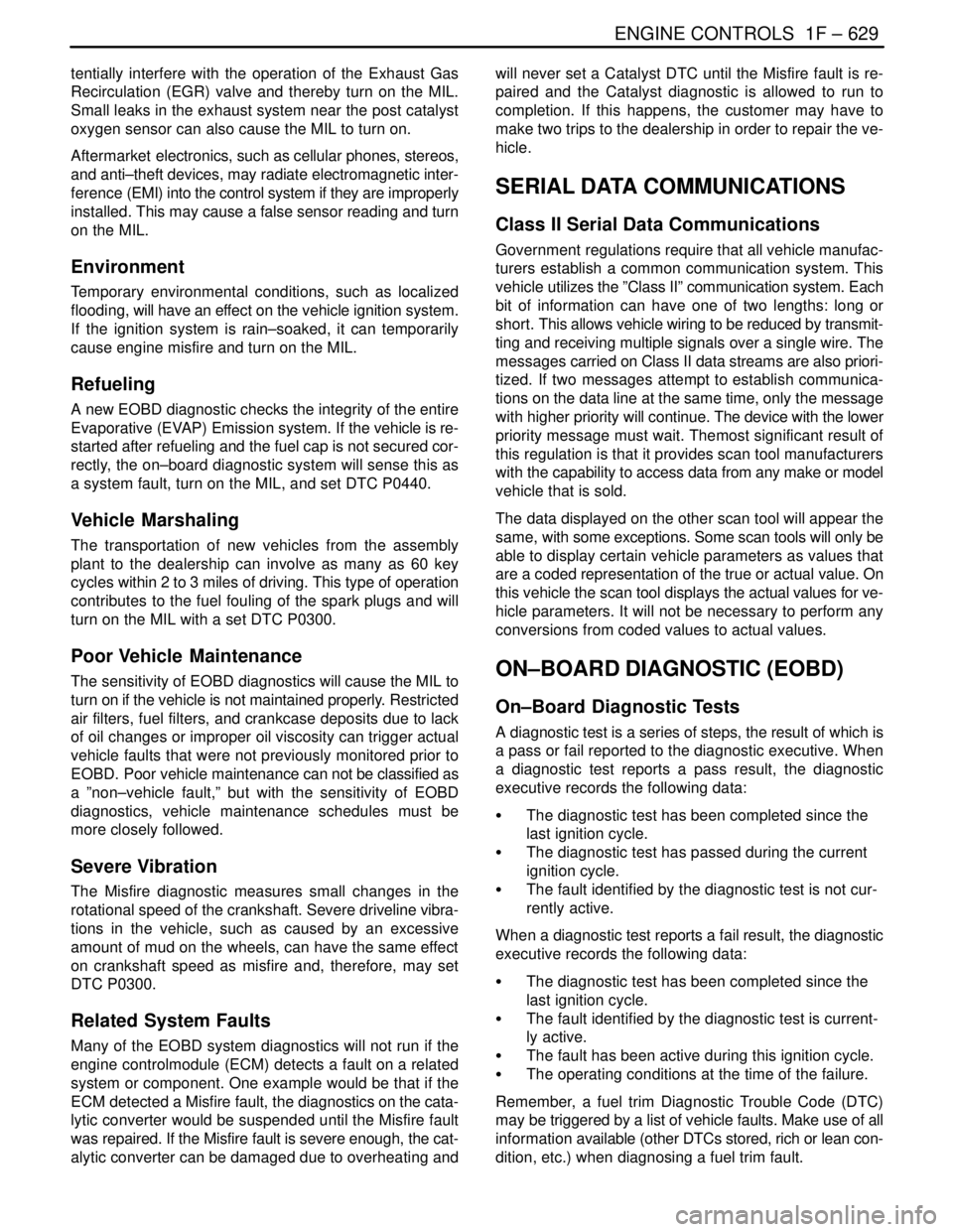
ENGINE CONTROLS 1F – 629
DAEWOO V–121 BL4
tentially interfere with the operation of the Exhaust Gas
Recirculation (EGR) valve and thereby turn on the MIL.
Small leaks in the exhaust system near the post catalyst
oxygen sensor can also cause the MIL to turn on.
Aftermarket electronics, such as cellular phones, stereos,
and anti–theft devices, may radiate electromagnetic inter-
ference (EMI) into the control system if they are improperly
installed. This may cause a false sensor reading and turn
on the MIL.
Environment
Temporary environmental conditions, such as localized
flooding, will have an effect on the vehicle ignition system.
If the ignition system is rain–soaked, it can temporarily
cause engine misfire and turn on the MIL.
Refueling
A new EOBD diagnostic checks the integrity of the entire
Evaporative (EVAP) Emission system. If the vehicle is re-
started after refueling and the fuel cap is not secured cor-
rectly, the on–board diagnostic system will sense this as
a system fault, turn on the MIL, and set DTC P0440.
Vehicle Marshaling
The transportation of new vehicles from the assembly
plant to the dealership can involve as many as 60 key
cycles within 2 to 3 miles of driving. This type of operation
contributes to the fuel fouling of the spark plugs and will
turn on the MIL with a set DTC P0300.
Poor Vehicle Maintenance
The sensitivity of EOBD diagnostics will cause the MIL to
turn on if the vehicle is not maintained properly. Restricted
air filters, fuel filters, and crankcase deposits due to lack
of oil changes or improper oil viscosity can trigger actual
vehicle faults that were not previously monitored prior to
EOBD. Poor vehicle maintenance can not be classified as
a ”non–vehicle fault,” but with the sensitivity of EOBD
diagnostics, vehicle maintenance schedules must be
more closely followed.
Severe Vibration
The Misfire diagnostic measures small changes in the
rotational speed of the crankshaft. Severe driveline vibra-
tions in the vehicle, such as caused by an excessive
amount of mud on the wheels, can have the same effect
on crankshaft speed as misfire and, therefore, may set
DTC P0300.
Related System Faults
Many of the EOBD system diagnostics will not run if the
engine controlmodule (ECM) detects a fault on a related
system or component. One example would be that if the
ECM detected a Misfire fault, the diagnostics on the cata-
lytic converter would be suspended until the Misfire fault
was repaired. If the Misfire fault is severe enough, the cat-
alytic converter can be damaged due to overheating andwill never set a Catalyst DTC until the Misfire fault is re-
paired and the Catalyst diagnostic is allowed to run to
completion. If this happens, the customer may have to
make two trips to the dealership in order to repair the ve-
hicle.
SERIAL DATA COMMUNICATIONS
Class II Serial Data Communications
Government regulations require that all vehicle manufac-
turers establish a common communication system. This
vehicle utilizes the ”Class II” communication system. Each
bit of information can have one of two lengths: long or
short. This allows vehicle wiring to be reduced by transmit-
ting and receiving multiple signals over a single wire. The
messages carried on Class II data streams are also priori-
tized. If two messages attempt to establish communica-
tions on the data line at the same time, only the message
with higher priority will continue. The device with the lower
priority message must wait. Themost significant result of
this regulation is that it provides scan tool manufacturers
with the capability to access data from any make or model
vehicle that is sold.
The data displayed on the other scan tool will appear the
same, with some exceptions. Some scan tools will only be
able to display certain vehicle parameters as values that
are a coded representation of the true or actual value. On
this vehicle the scan tool displays the actual values for ve-
hicle parameters. It will not be necessary to perform any
conversions from coded values to actual values.
ON–BOARD DIAGNOSTIC (EOBD)
On–Board Diagnostic Tests
A diagnostic test is a series of steps, the result of which is
a pass or fail reported to the diagnostic executive. When
a diagnostic test reports a pass result, the diagnostic
executive records the following data:
S The diagnostic test has been completed since the
last ignition cycle.
S The diagnostic test has passed during the current
ignition cycle.
S The fault identified by the diagnostic test is not cur-
rently active.
When a diagnostic test reports a fail result, the diagnostic
executive records the following data:
S The diagnostic test has been completed since the
last ignition cycle.
S The fault identified by the diagnostic test is current-
ly active.
S The fault has been active during this ignition cycle.
S The operating conditions at the time of the failure.
Remember, a fuel trim Diagnostic Trouble Code (DTC)
may be triggered by a list of vehicle faults. Make use of all
information available (other DTCs stored, rich or lean con-
dition, etc.) when diagnosing a fuel trim fault.
Page 876 of 2643
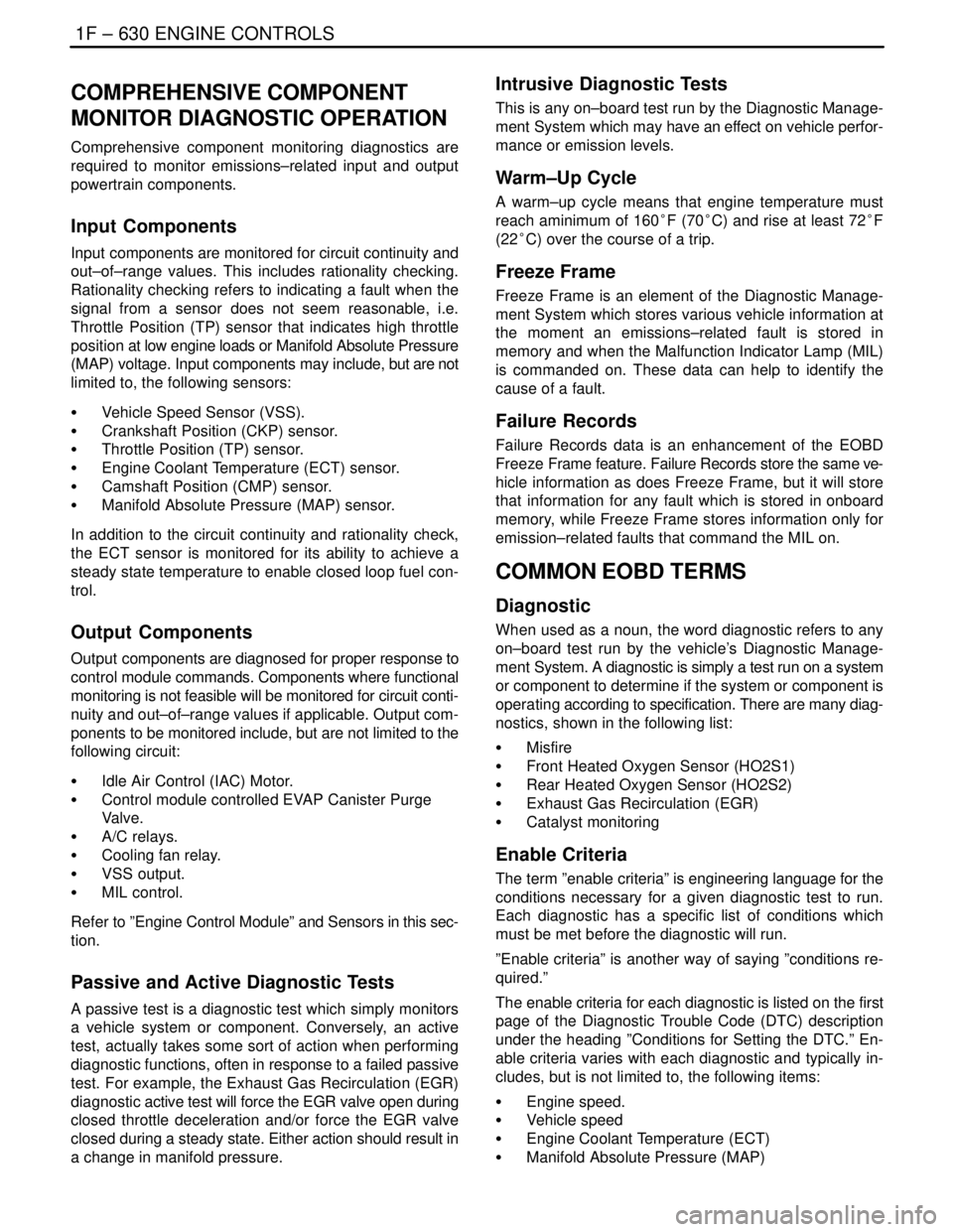
1F – 630IENGINE CONTROLS
DAEWOO V–121 BL4
COMPREHENSIVE COMPONENT
MONITOR DIAGNOSTIC OPERATION
Comprehensive component monitoring diagnostics are
required to monitor emissions–related input and output
powertrain components.
Input Components
Input components are monitored for circuit continuity and
out–of–range values. This includes rationality checking.
Rationality checking refers to indicating a fault when the
signal from a sensor does not seem reasonable, i.e.
Throttle Position (TP) sensor that indicates high throttle
position at low engine loads or Manifold Absolute Pressure
(MAP) voltage. Input components may include, but are not
limited to, the following sensors:
S Vehicle Speed Sensor (VSS).
S Crankshaft Position (CKP) sensor.
S Throttle Position (TP) sensor.
S Engine Coolant Temperature (ECT) sensor.
S Camshaft Position (CMP) sensor.
S Manifold Absolute Pressure (MAP) sensor.
In addition to the circuit continuity and rationality check,
the ECT sensor is monitored for its ability to achieve a
steady state temperature to enable closed loop fuel con-
trol.
Output Components
Output components are diagnosed for proper response to
control module commands. Components where functional
monitoring is not feasible will be monitored for circuit conti-
nuity and out–of–range values if applicable. Output com-
ponents to be monitored include, but are not limited to the
following circuit:
S Idle Air Control (IAC) Motor.
S Control module controlled EVAP Canister Purge
Valve.
S A/C relays.
S Cooling fan relay.
S VSS output.
S MIL control.
Refer to ”Engine Control Module” and Sensors in this sec-
tion.
Passive and Active Diagnostic Tests
A passive test is a diagnostic test which simply monitors
a vehicle system or component. Conversely, an active
test, actually takes some sort of action when performing
diagnostic functions, often in response to a failed passive
test. For example, the Exhaust Gas Recirculation (EGR)
diagnostic active test will force the EGR valve open during
closed throttle deceleration and/or force the EGR valve
closed during a steady state. Either action should result in
a change in manifold pressure.
Intrusive Diagnostic Tests
This is any on–board test run by the Diagnostic Manage-
ment System which may have an effect on vehicle perfor-
mance or emission levels.
Warm–Up Cycle
A warm–up cycle means that engine temperature must
reach aminimum of 160°F (70°C) and rise at least 72°F
(22°C) over the course of a trip.
Freeze Frame
Freeze Frame is an element of the Diagnostic Manage-
ment System which stores various vehicle information at
the moment an emissions–related fault is stored in
memory and when the Malfunction Indicator Lamp (MIL)
is commanded on. These data can help to identify the
cause of a fault.
Failure Records
Failure Records data is an enhancement of the EOBD
Freeze Frame feature. Failure Records store the same ve-
hicle information as does Freeze Frame, but it will store
that information for any fault which is stored in onboard
memory, while Freeze Frame stores information only for
emission–related faults that command the MIL on.
COMMON EOBD TERMS
Diagnostic
When used as a noun, the word diagnostic refers to any
on–board test run by the vehicle’s Diagnostic Manage-
ment System. A diagnostic is simply a test run on a system
or component to determine if the system or component is
operating according to specification. There are many diag-
nostics, shown in the following list:
S Misfire
S Front Heated Oxygen Sensor (HO2S1)
S Rear Heated Oxygen Sensor (HO2S2)
S Exhaust Gas Recirculation (EGR)
S Catalyst monitoring
Enable Criteria
The term ”enable criteria” is engineering language for the
conditions necessary for a given diagnostic test to run.
Each diagnostic has a specific list of conditions which
must be met before the diagnostic will run.
”Enable criteria” is another way of saying ”conditions re-
quired.”
The enable criteria for each diagnostic is listed on the first
page of the Diagnostic Trouble Code (DTC) description
under the heading ”Conditions for Setting the DTC.” En-
able criteria varies with each diagnostic and typically in-
cludes, but is not limited to, the following items:
S Engine speed.
S Vehicle speed
S Engine Coolant Temperature (ECT)
S Manifold Absolute Pressure (MAP)
Page 877 of 2643
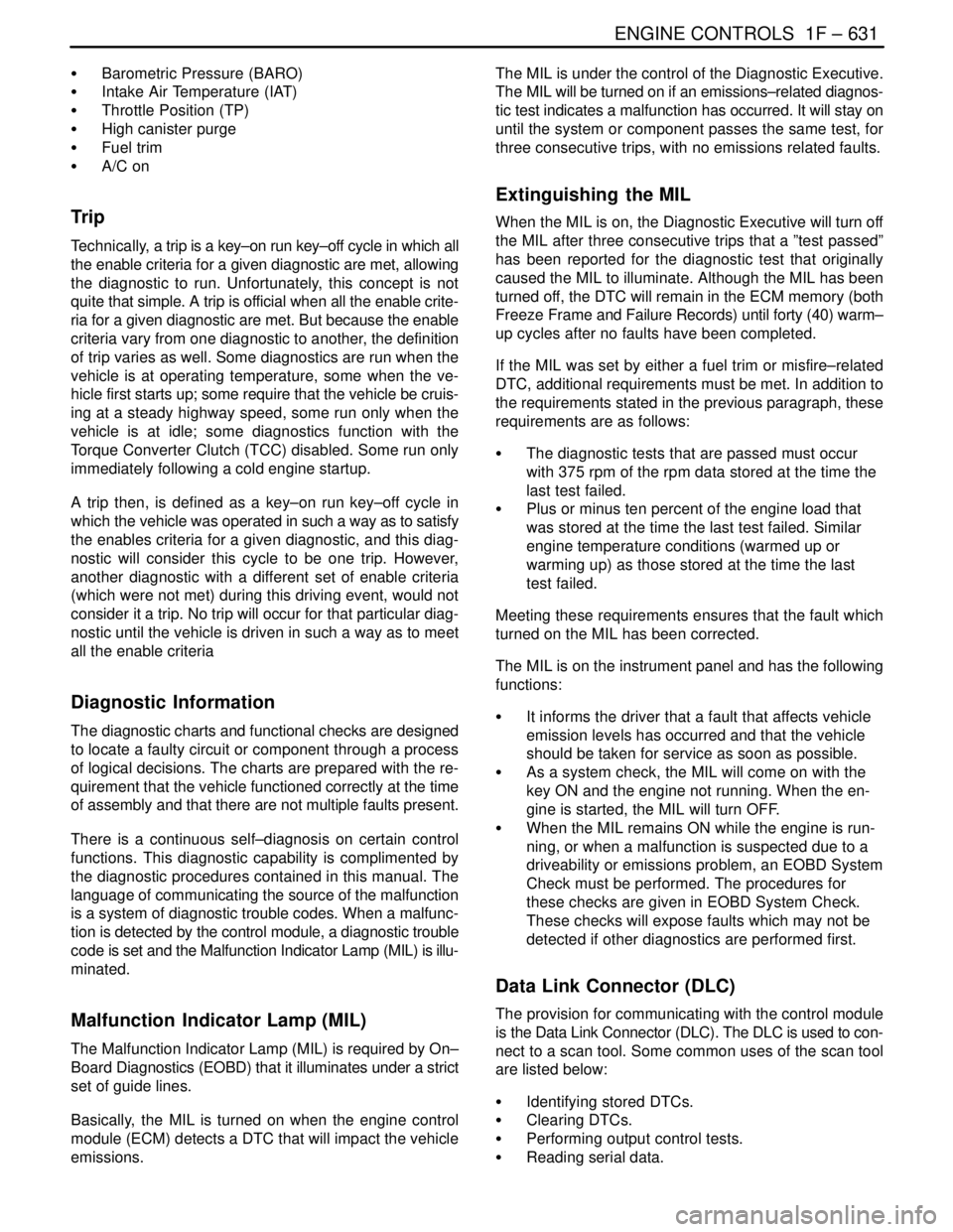
ENGINE CONTROLS 1F – 631
DAEWOO V–121 BL4
S Barometric Pressure (BARO)
S Intake Air Temperature (IAT)
S Throttle Position (TP)
S High canister purge
S Fuel trim
S A/C on
Trip
Technically, a trip is a key–on run key–off cycle in which all
the enable criteria for a given diagnostic are met, allowing
the diagnostic to run. Unfortunately, this concept is not
quite that simple. A trip is official when all the enable crite-
ria for a given diagnostic are met. But because the enable
criteria vary from one diagnostic to another, the definition
of trip varies as well. Some diagnostics are run when the
vehicle is at operating temperature, some when the ve-
hicle first starts up; some require that the vehicle be cruis-
ing at a steady highway speed, some run only when the
vehicle is at idle; some diagnostics function with the
Torque Converter Clutch (TCC) disabled. Some run only
immediately following a cold engine startup.
A trip then, is defined as a key–on run key–off cycle in
which the vehicle was operated in such a way as to satisfy
the enables criteria for a given diagnostic, and this diag-
nostic will consider this cycle to be one trip. However,
another diagnostic with a different set of enable criteria
(which were not met) during this driving event, would not
consider it a trip. No trip will occur for that particular diag-
nostic until the vehicle is driven in such a way as to meet
all the enable criteria
Diagnostic Information
The diagnostic charts and functional checks are designed
to locate a faulty circuit or component through a process
of logical decisions. The charts are prepared with the re-
quirement that the vehicle functioned correctly at the time
of assembly and that there are not multiple faults present.
There is a continuous self–diagnosis on certain control
functions. This diagnostic capability is complimented by
the diagnostic procedures contained in this manual. The
language of communicating the source of the malfunction
is a system of diagnostic trouble codes. When a malfunc-
tion is detected by the control module, a diagnostic trouble
code is set and the Malfunction Indicator Lamp (MIL) is illu-
minated.
Malfunction Indicator Lamp (MIL)
The Malfunction Indicator Lamp (MIL) is required by On–
Board Diagnostics (EOBD) that it illuminates under a strict
set of guide lines.
Basically, the MIL is turned on when the engine control
module (ECM) detects a DTC that will impact the vehicle
emissions.The MIL is under the control of the Diagnostic Executive.
The MIL will be turned on if an emissions–related diagnos-
tic test indicates a malfunction has occurred. It will stay on
until the system or component passes the same test, for
three consecutive trips, with no emissions related faults.
Extinguishing the MIL
When the MIL is on, the Diagnostic Executive will turn off
the MIL after three consecutive trips that a ”test passed”
has been reported for the diagnostic test that originally
caused the MIL to illuminate. Although the MIL has been
turned off, the DTC will remain in the ECM memory (both
Freeze Frame and Failure Records) until forty (40) warm–
up cycles after no faults have been completed.
If the MIL was set by either a fuel trim or misfire–related
DTC, additional requirements must be met. In addition to
the requirements stated in the previous paragraph, these
requirements are as follows:
S The diagnostic tests that are passed must occur
with 375 rpm of the rpm data stored at the time the
last test failed.
S Plus or minus ten percent of the engine load that
was stored at the time the last test failed. Similar
engine temperature conditions (warmed up or
warming up) as those stored at the time the last
test failed.
Meeting these requirements ensures that the fault which
turned on the MIL has been corrected.
The MIL is on the instrument panel and has the following
functions:
S It informs the driver that a fault that affects vehicle
emission levels has occurred and that the vehicle
should be taken for service as soon as possible.
S As a system check, the MIL will come on with the
key ON and the engine not running. When the en-
gine is started, the MIL will turn OFF.
S When the MIL remains ON while the engine is run-
ning, or when a malfunction is suspected due to a
driveability or emissions problem, an EOBD System
Check must be performed. The procedures for
these checks are given in EOBD System Check.
These checks will expose faults which may not be
detected if other diagnostics are performed first.
Data Link Connector (DLC)
The provision for communicating with the control module
is the Data Link Connector (DLC). The DLC is used to con-
nect to a scan tool. Some common uses of the scan tool
are listed below:
S Identifying stored DTCs.
S Clearing DTCs.
S Performing output control tests.
S Reading serial data.
Page 878 of 2643
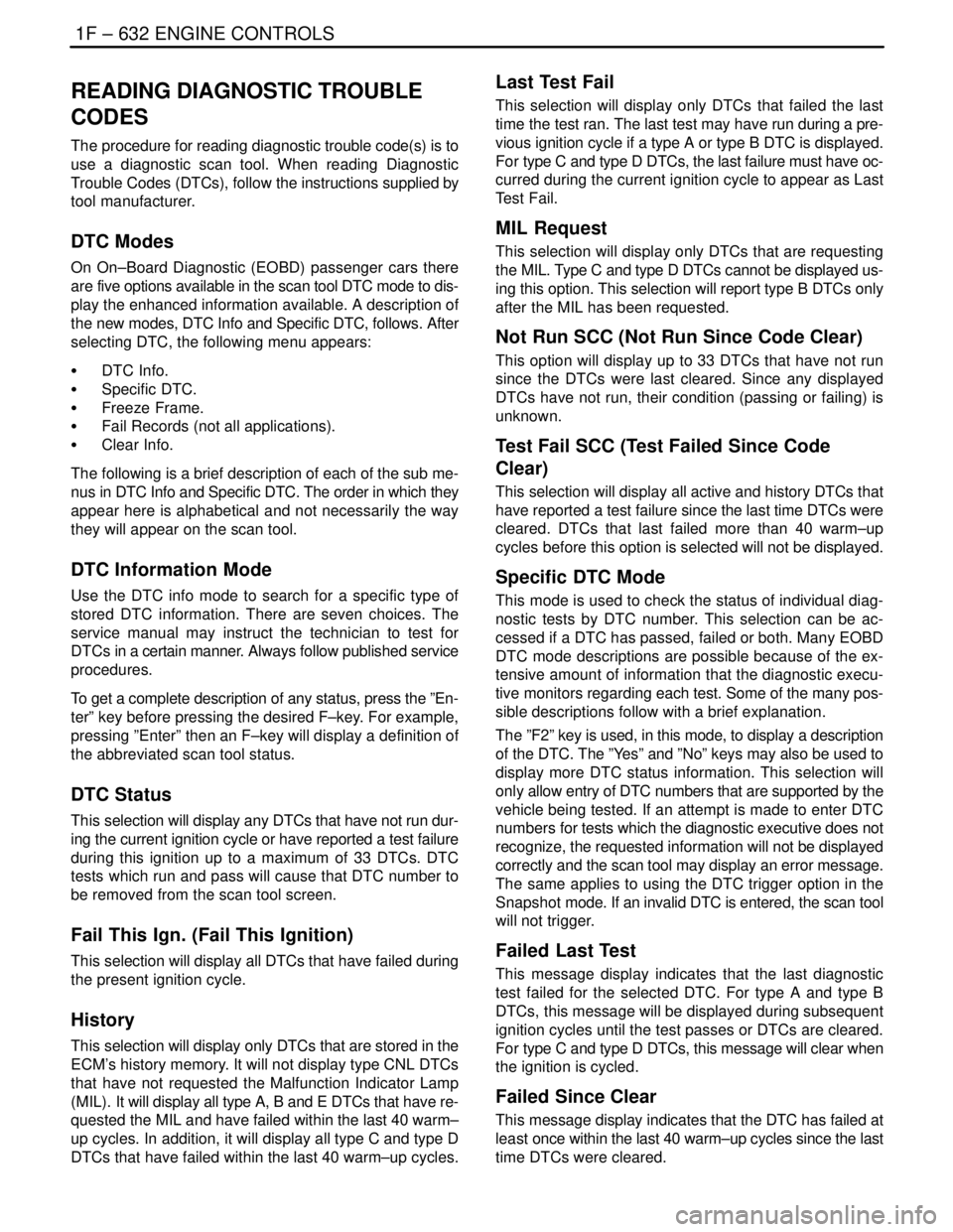
1F – 632IENGINE CONTROLS
DAEWOO V–121 BL4
READING DIAGNOSTIC TROUBLE
CODES
The procedure for reading diagnostic trouble code(s) is to
use a diagnostic scan tool. When reading Diagnostic
Trouble Codes (DTCs), follow the instructions supplied by
tool manufacturer.
DTC Modes
On On–Board Diagnostic (EOBD) passenger cars there
are five options available in the scan tool DTC mode to dis-
play the enhanced information available. A description of
the new modes, DTC Info and Specific DTC, follows. After
selecting DTC, the following menu appears:
S DTC Info.
S Specific DTC.
S Freeze Frame.
S Fail Records (not all applications).
S Clear Info.
The following is a brief description of each of the sub me-
nus in DTC Info and Specific DTC. The order in which they
appear here is alphabetical and not necessarily the way
they will appear on the scan tool.
DTC Information Mode
Use the DTC info mode to search for a specific type of
stored DTC information. There are seven choices. The
service manual may instruct the technician to test for
DTCs in a certain manner. Always follow published service
procedures.
To get a complete description of any status, press the ”En-
ter” key before pressing the desired F–key. For example,
pressing ”Enter” then an F–key will display a definition of
the abbreviated scan tool status.
DTC Status
This selection will display any DTCs that have not run dur-
ing the current ignition cycle or have reported a test failure
during this ignition up to a maximum of 33 DTCs. DTC
tests which run and pass will cause that DTC number to
be removed from the scan tool screen.
Fail This Ign. (Fail This Ignition)
This selection will display all DTCs that have failed during
the present ignition cycle.
History
This selection will display only DTCs that are stored in the
ECM’s history memory. It will not display type CNL DTCs
that have not requested the Malfunction Indicator Lamp
(MIL). It will display all type A, B and E DTCs that have re-
quested the MIL and have failed within the last 40 warm–
up cycles. In addition, it will display all type C and type D
DTCs that have failed within the last 40 warm–up cycles.
Last Test Fail
This selection will display only DTCs that failed the last
time the test ran. The last test may have run during a pre-
vious ignition cycle if a type A or type B DTC is displayed.
For type C and type D DTCs, the last failure must have oc-
curred during the current ignition cycle to appear as Last
Test Fail.
MIL Request
This selection will display only DTCs that are requesting
the MIL. Type C and type D DTCs cannot be displayed us-
ing this option. This selection will report type B DTCs only
after the MIL has been requested.
Not Run SCC (Not Run Since Code Clear)
This option will display up to 33 DTCs that have not run
since the DTCs were last cleared. Since any displayed
DTCs have not run, their condition (passing or failing) is
unknown.
Test Fail SCC (Test Failed Since Code
Clear)
This selection will display all active and history DTCs that
have reported a test failure since the last time DTCs were
cleared. DTCs that last failed more than 40 warm–up
cycles before this option is selected will not be displayed.
Specific DTC Mode
This mode is used to check the status of individual diag-
nostic tests by DTC number. This selection can be ac-
cessed if a DTC has passed, failed or both. Many EOBD
DTC mode descriptions are possible because of the ex-
tensive amount of information that the diagnostic execu-
tive monitors regarding each test. Some of the many pos-
sible descriptions follow with a brief explanation.
The ”F2” key is used, in this mode, to display a description
of the DTC. The ”Yes” and ”No” keys may also be used to
display more DTC status information. This selection will
only allow entry of DTC numbers that are supported by the
vehicle being tested. If an attempt is made to enter DTC
numbers for tests which the diagnostic executive does not
recognize, the requested information will not be displayed
correctly and the scan tool may display an error message.
The same applies to using the DTC trigger option in the
Snapshot mode. If an invalid DTC is entered, the scan tool
will not trigger.
Failed Last Test
This message display indicates that the last diagnostic
test failed for the selected DTC. For type A and type B
DTCs, this message will be displayed during subsequent
ignition cycles until the test passes or DTCs are cleared.
For type C and type D DTCs, this message will clear when
the ignition is cycled.
Failed Since Clear
This message display indicates that the DTC has failed at
least once within the last 40 warm–up cycles since the last
time DTCs were cleared.
Page 879 of 2643
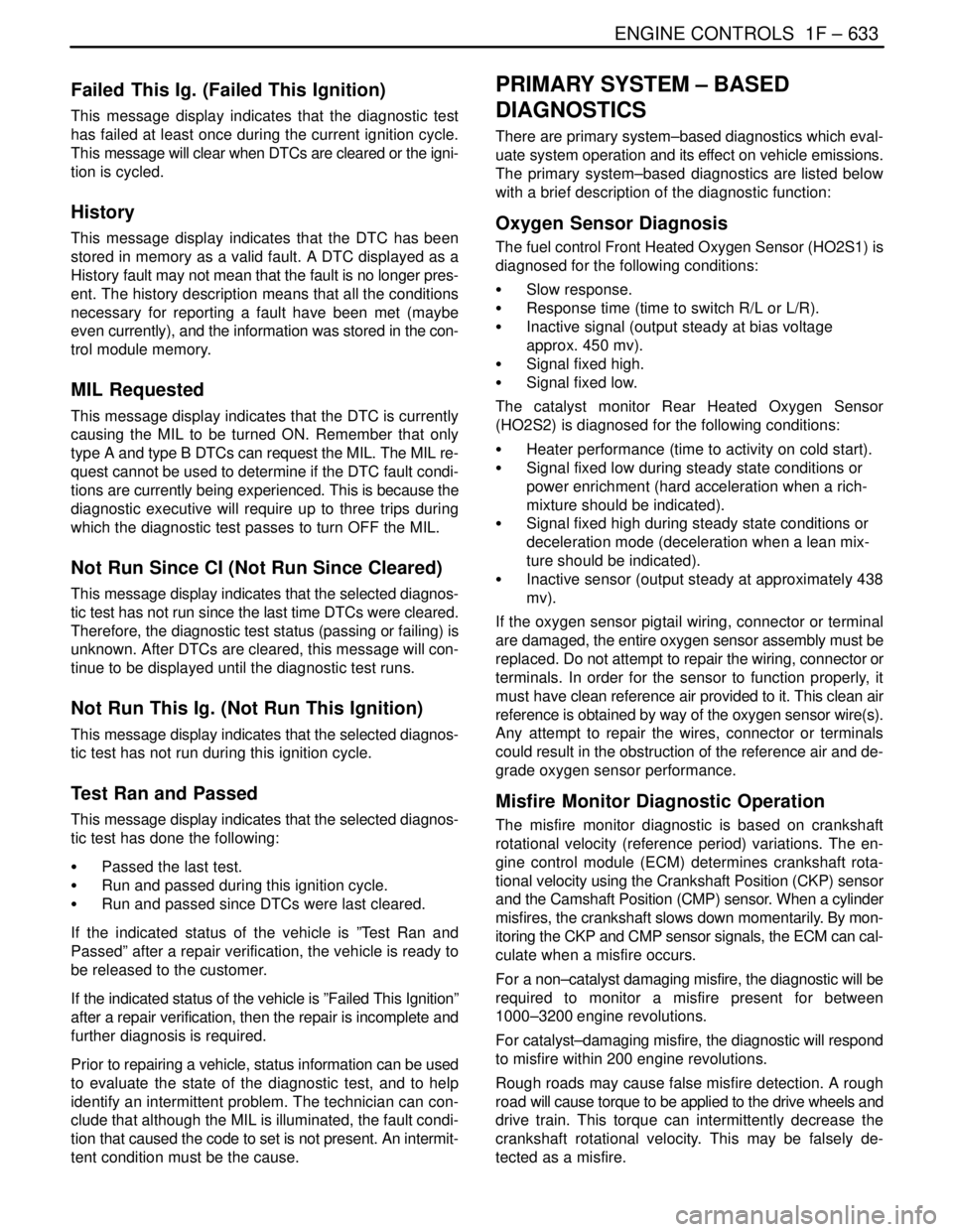
ENGINE CONTROLS 1F – 633
DAEWOO V–121 BL4
Failed This Ig. (Failed This Ignition)
This message display indicates that the diagnostic test
has failed at least once during the current ignition cycle.
This message will clear when DTCs are cleared or the igni-
tion is cycled.
History
This message display indicates that the DTC has been
stored in memory as a valid fault. A DTC displayed as a
History fault may not mean that the fault is no longer pres-
ent. The history description means that all the conditions
necessary for reporting a fault have been met (maybe
even currently), and the information was stored in the con-
trol module memory.
MIL Requested
This message display indicates that the DTC is currently
causing the MIL to be turned ON. Remember that only
type A and type B DTCs can request the MIL. The MIL re-
quest cannot be used to determine if the DTC fault condi-
tions are currently being experienced. This is because the
diagnostic executive will require up to three trips during
which the diagnostic test passes to turn OFF the MIL.
Not Run Since CI (Not Run Since Cleared)
This message display indicates that the selected diagnos-
tic test has not run since the last time DTCs were cleared.
Therefore, the diagnostic test status (passing or failing) is
unknown. After DTCs are cleared, this message will con-
tinue to be displayed until the diagnostic test runs.
Not Run This Ig. (Not Run This Ignition)
This message display indicates that the selected diagnos-
tic test has not run during this ignition cycle.
Test Ran and Passed
This message display indicates that the selected diagnos-
tic test has done the following:
S Passed the last test.
S Run and passed during this ignition cycle.
S Run and passed since DTCs were last cleared.
If the indicated status of the vehicle is ”Test Ran and
Passed” after a repair verification, the vehicle is ready to
be released to the customer.
If the indicated status of the vehicle is ”Failed This Ignition”
after a repair verification, then the repair is incomplete and
further diagnosis is required.
Prior to repairing a vehicle, status information can be used
to evaluate the state of the diagnostic test, and to help
identify an intermittent problem. The technician can con-
clude that although the MIL is illuminated, the fault condi-
tion that caused the code to set is not present. An intermit-
tent condition must be the cause.
PRIMARY SYSTEM – BASED
DIAGNOSTICS
There are primary system–based diagnostics which eval-
uate system operation and its effect on vehicle emissions.
The primary system–based diagnostics are listed below
with a brief description of the diagnostic function:
Oxygen Sensor Diagnosis
The fuel control Front Heated Oxygen Sensor (HO2S1) is
diagnosed for the following conditions:
S Slow response.
S Response time (time to switch R/L or L/R).
S Inactive signal (output steady at bias voltage
approx. 450 mv).
S Signal fixed high.
S Signal fixed low.
The catalyst monitor Rear Heated Oxygen Sensor
(HO2S2) is diagnosed for the following conditions:
S Heater performance (time to activity on cold start).
S Signal fixed low during steady state conditions or
power enrichment (hard acceleration when a rich-
mixture should be indicated).
S Signal fixed high during steady state conditions or
deceleration mode (deceleration when a lean mix-
ture should be indicated).
S Inactive sensor (output steady at approximately 438
mv).
If the oxygen sensor pigtail wiring, connector or terminal
are damaged, the entire oxygen sensor assembly must be
replaced. Do not attempt to repair the wiring, connector or
terminals. In order for the sensor to function properly, it
must have clean reference air provided to it. This clean air
reference is obtained by way of the oxygen sensor wire(s).
Any attempt to repair the wires, connector or terminals
could result in the obstruction of the reference air and de-
grade oxygen sensor performance.
Misfire Monitor Diagnostic Operation
The misfire monitor diagnostic is based on crankshaft
rotational velocity (reference period) variations. The en-
gine control module (ECM) determines crankshaft rota-
tional velocity using the Crankshaft Position (CKP) sensor
and the Camshaft Position (CMP) sensor. When a cylinder
misfires, the crankshaft slows down momentarily. By mon-
itoring the CKP and CMP sensor signals, the ECM can cal-
culate when a misfire occurs.
For a non–catalyst damaging misfire, the diagnostic will be
required to monitor a misfire present for between
1000–3200 engine revolutions.
For catalyst–damaging misfire, the diagnostic will respond
to misfire within 200 engine revolutions.
Rough roads may cause false misfire detection. A rough
road will cause torque to be applied to the drive wheels and
drive train. This torque can intermittently decrease the
crankshaft rotational velocity. This may be falsely de-
tected as a misfire.
Page 880 of 2643
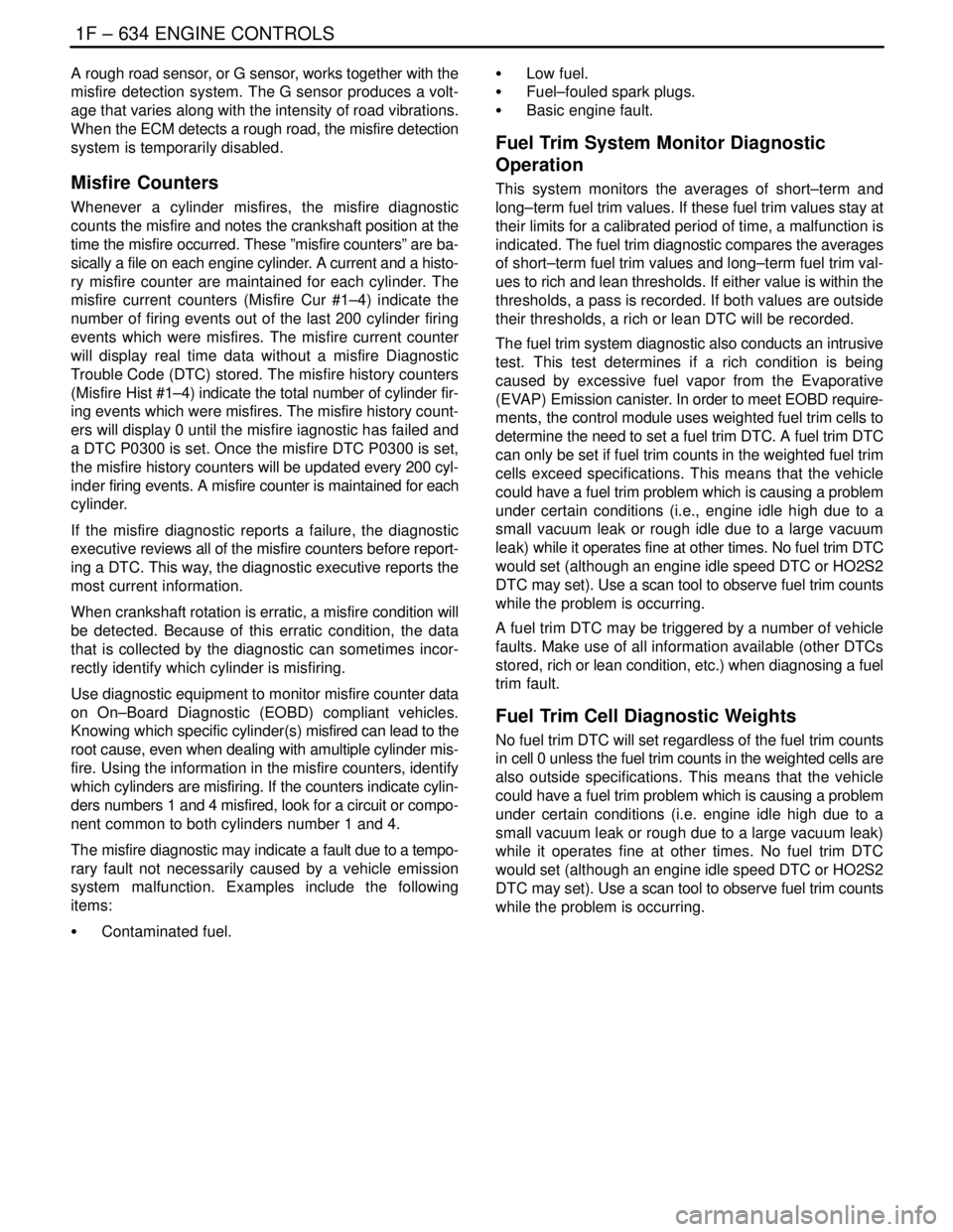
1F – 634IENGINE CONTROLS
DAEWOO V–121 BL4
A rough road sensor, or G sensor, works together with the
misfire detection system. The G sensor produces a volt-
age that varies along with the intensity of road vibrations.
When the ECM detects a rough road, the misfire detection
system is temporarily disabled.
Misfire Counters
Whenever a cylinder misfires, the misfire diagnostic
counts the misfire and notes the crankshaft position at the
time the misfire occurred. These ”misfire counters” are ba-
sically a file on each engine cylinder. A current and a histo-
ry misfire counter are maintained for each cylinder. The
misfire current counters (Misfire Cur #1–4) indicate the
number of firing events out of the last 200 cylinder firing
events which were misfires. The misfire current counter
will display real time data without a misfire Diagnostic
Trouble Code (DTC) stored. The misfire history counters
(Misfire Hist #1–4) indicate the total number of cylinder fir-
ing events which were misfires. The misfire history count-
ers will display 0 until the misfire iagnostic has failed and
a DTC P0300 is set. Once the misfire DTC P0300 is set,
the misfire history counters will be updated every 200 cyl-
inder firing events. A misfire counter is maintained for each
cylinder.
If the misfire diagnostic reports a failure, the diagnostic
executive reviews all of the misfire counters before report-
ing a DTC. This way, the diagnostic executive reports the
most current information.
When crankshaft rotation is erratic, a misfire condition will
be detected. Because of this erratic condition, the data
that is collected by the diagnostic can sometimes incor-
rectly identify which cylinder is misfiring.
Use diagnostic equipment to monitor misfire counter data
on On–Board Diagnostic (EOBD) compliant vehicles.
Knowing which specific cylinder(s) misfired can lead to the
root cause, even when dealing with amultiple cylinder mis-
fire. Using the information in the misfire counters, identify
which cylinders are misfiring. If the counters indicate cylin-
ders numbers 1 and 4 misfired, look for a circuit or compo-
nent common to both cylinders number 1 and 4.
The misfire diagnostic may indicate a fault due to a tempo-
rary fault not necessarily caused by a vehicle emission
system malfunction. Examples include the following
items:
S Contaminated fuel.S Low fuel.
S Fuel–fouled spark plugs.
S Basic engine fault.
Fuel Trim System Monitor Diagnostic
Operation
This system monitors the averages of short–term and
long–term fuel trim values. If these fuel trim values stay at
their limits for a calibrated period of time, a malfunction is
indicated. The fuel trim diagnostic compares the averages
of short–term fuel trim values and long–term fuel trim val-
ues to rich and lean thresholds. If either value is within the
thresholds, a pass is recorded. If both values are outside
their thresholds, a rich or lean DTC will be recorded.
The fuel trim system diagnostic also conducts an intrusive
test. This test determines if a rich condition is being
caused by excessive fuel vapor from the Evaporative
(EVAP) Emission canister. In order to meet EOBD require-
ments, the control module uses weighted fuel trim cells to
determine the need to set a fuel trim DTC. A fuel trim DTC
can only be set if fuel trim counts in the weighted fuel trim
cells exceed specifications. This means that the vehicle
could have a fuel trim problem which is causing a problem
under certain conditions (i.e., engine idle high due to a
small vacuum leak or rough idle due to a large vacuum
leak) while it operates fine at other times. No fuel trim DTC
would set (although an engine idle speed DTC or HO2S2
DTC may set). Use a scan tool to observe fuel trim counts
while the problem is occurring.
A fuel trim DTC may be triggered by a number of vehicle
faults. Make use of all information available (other DTCs
stored, rich or lean condition, etc.) when diagnosing a fuel
trim fault.
Fuel Trim Cell Diagnostic Weights
No fuel trim DTC will set regardless of the fuel trim counts
in cell 0 unless the fuel trim counts in the weighted cells are
also outside specifications. This means that the vehicle
could have a fuel trim problem which is causing a problem
under certain conditions (i.e. engine idle high due to a
small vacuum leak or rough due to a large vacuum leak)
while it operates fine at other times. No fuel trim DTC
would set (although an engine idle speed DTC or HO2S2
DTC may set). Use a scan tool to observe fuel trim counts
while the problem is occurring.