heater DATSUN 610 1969 Workshop Manual
[x] Cancel search | Manufacturer: DATSUN, Model Year: 1969, Model line: 610, Model: DATSUN 610 1969Pages: 171, PDF Size: 10.63 MB
Page 6 of 171
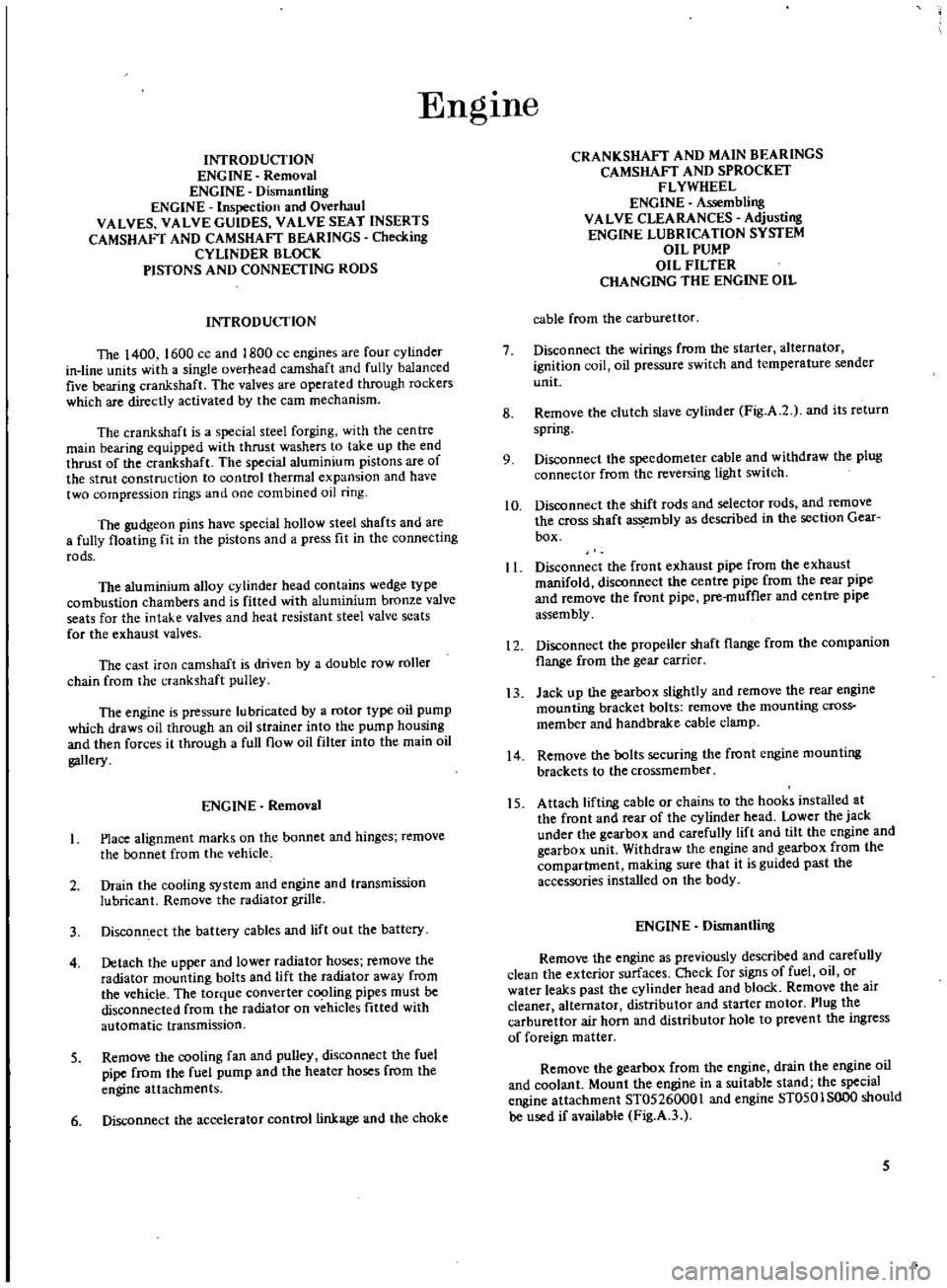
EngIne
INTRODUCTION
ENGINE
Removal
ENGINE
DismantUng
ENGINE
Inspection
and
Overhaul
VALVES
VALVE
GUIDES
VALVE
SEAT
INSERTS
CAMSHAFT
AND
CAMSHAFT
BEARINGS
Checking
CYliNDER
BLOCK
PtSTONS
AND
CONNECTING
RODS
INTRODUCTION
The
1400
1600
cc
and
1800
cc
engines
are
four
cylinder
in
line
units
with
a
single
overhead
camshaft
and
fully
balanced
five
bearing
crankshaft
The
valves
are
operated
through
rockers
which
are
directly
activated
by
the
earn
mechanism
The
crankshaft
is
a
special
steel
forging
with
the
centre
main
bearing
equipped
with
thrust
washers
to
take
up
the
end
thrust
of
the
crankshaft
The
special
aluminium
pistons
are
of
the
strut
construction
to
control
thermal
expansion
and
have
two
compression
rings
and
one
combined
oil
ring
The
gudgeon
pins
have
special
hollow
steel
shafts
and
are
a
fully
floating
fit
in
the
pistons
and
a
press
fit
in
the
connecting
rods
The
aluminium
alloy
cylinder
head
contains
wedge
type
combustion
chambers
and
is
fitted
with
aluminium
bronze
valve
seats
for
the
intake
valves
and
heat
resistant
steel
valve
seats
for
the
exhaust
valves
The
cast
iron
camshaft
is
driven
by
a
double
row
roller
chain
from
the
crankshaft
pulley
The
engine
is
pressure
lubricated
by
a
rotor
type
oil
pump
which
draws
oil
through
an
oil
strainer
into
the
pump
housing
and
then
forces
it
through
a
full
flow
oil
filter
into
the
main
oil
gallery
ENGINE
Removal
Place
alignment
marks
on
the
bonnet
and
hinges
remove
the
bonnet
from
the
vehicle
2
Drain
the
cooling
system
and
engine
and
transmission
lubricant
Remove
the
radiator
grille
3
Discon
ect
the
battery
cables
and
lift
out
the
battery
4
Detach
the
upper
and
lower
radiator
hoses
remove
the
radiator
mounting
bolts
and
lift
the
radiator
away
from
the
vehicle
The
torque
converter
c
jng
pipes
must
be
disconnected
from
the
radiator
on
vehicles
fitted
with
automatic
transmission
S
Remove
the
COOling
fan
and
pulley
disconnect
the
fuel
pipe
from
the
fuel
pump
and
the
heater
hoses
from
the
engine
attachments
6
Disconnect
the
accelerator
control
linkage
and
the
choke
CRANKSHAFT
AND
MAIN
BEARINGS
CAMSHAFT
AND
SPROCKET
FLYWHEEL
ENGINE
Assembling
VALVE
CLEARANCES
Adjusting
ENGINE
LUBRICATION
SYSTEM
OIL
PUMP
OIL
FILTER
CHANGING
THE
ENGINE
OIL
cable
from
the
carburettor
7
Disconnect
the
wirings
from
the
starter
alternator
ignition
coil
oil
pressure
switch
and
temperature
sender
unit
8
Remove
the
clutch
slave
cylinder
Fig
A
2
and
its
return
spring
9
Disconnect
the
speedometer
cable
and
withdraw
the
plug
connector
from
the
reversing
light
switch
10
Disconnect
the
shift
rods
and
seJector
rods
and
remove
the
cross
shaft
assembly
as
described
in
the
section
Gear
box
II
Disconnect
the
front
exhaust
pipe
from
the
exhaust
manifold
disconnect
the
centre
pipe
from
the
rear
pipe
and
remove
the
front
pipe
pre
muffler
and
centre
pipe
assembly
12
Disconnect
the
propeUer
shaft
flange
from
the
companion
flange
from
the
gear
carrier
13
Jack
up
the
gearbox
slightly
and
remove
the
rear
engine
mounting
bracket
bolts
remove
the
mounting
cross
member
and
handbrake
cable
c1amp
14
Remove
the
bolts
securing
the
front
engine
mounting
brackets
to
the
crossmember
15
Attach
lifting
cable
or
chains
to
the
hooks
installed
at
the
front
and
rear
of
the
cylinder
head
Lower
the
jack
under
the
gearbox
and
carefully
lift
and
tilt
the
engine
and
gearbox
unit
Withdraw
the
engine
and
gearbox
from
the
compartment
making
sure
that
it
is
guided
past
the
accessories
installed
on
the
body
ENGINE
Dismantling
Remove
the
engine
as
previously
described
and
carefully
clean
the
exterior
surfaces
Cbeck
for
signs
of
fuel
oil
or
water
leaks
past
the
cylinder
head
and
block
Remove
the
air
cleaner
alternator
distributor
and
starter
motor
Plug
the
carburettor
air
horn
and
distributor
hole
to
prevent
the
ingress
of
foreign
matter
Remove
the
gearbox
from
the
engine
drain
the
engine
oil
and
coolant
Mount
the
engine
in
a
suitable
stand
the
special
engine
attachment
ST05260001
and
engine
ST0501SOO0
should
be
used
if
available
Fig
A
3
5
Page 26 of 171
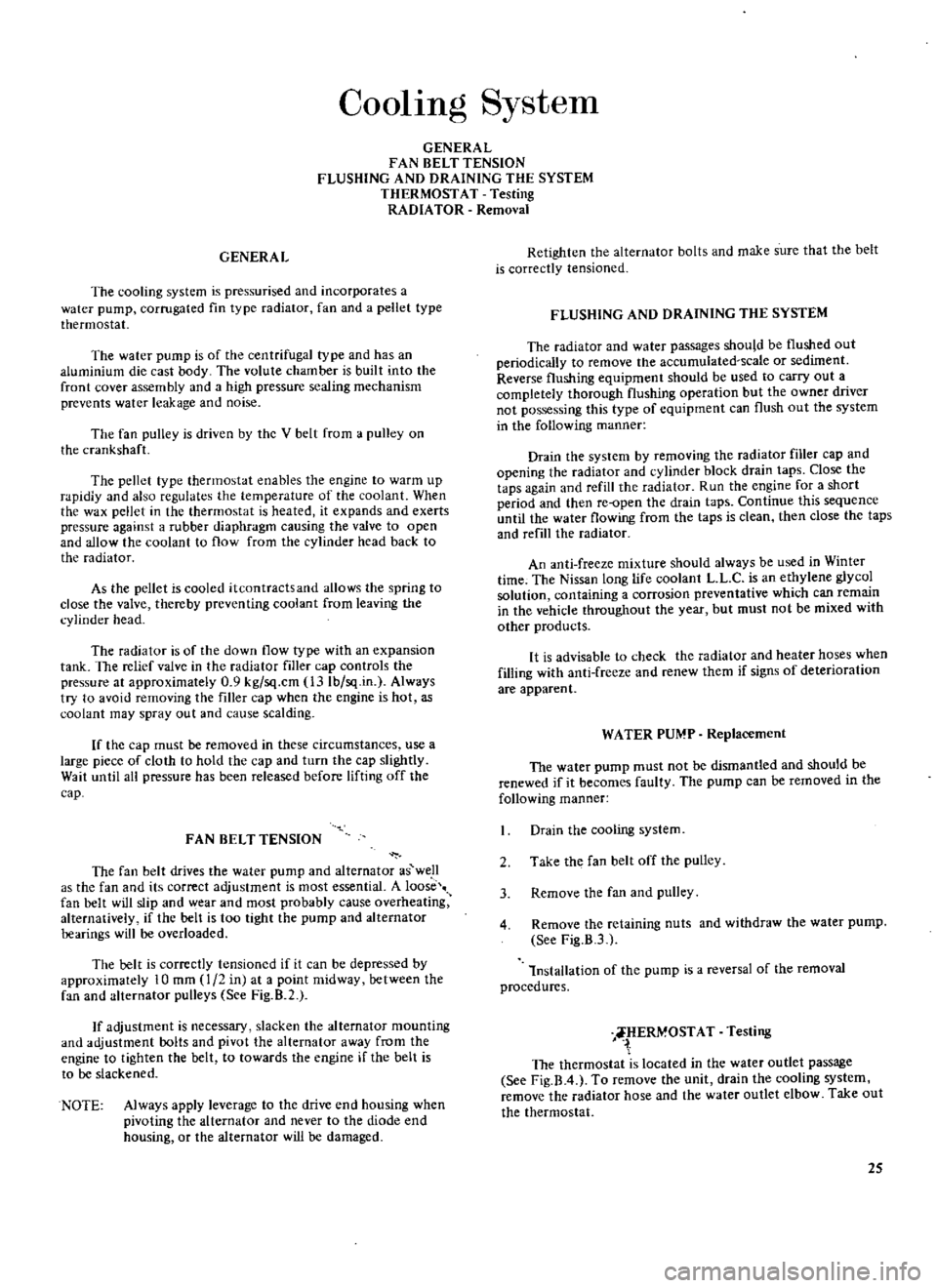
CoolIng
System
GENERAL
FAN
BELT
TENSION
FLUSHING
AND
DRAINING
THE
SYSTEM
THERMOSTAT
Testing
RADlA
TOR
Removal
GENERAL
The
cooling
system
is
pressurised
and
incorporates
a
water
pump
corrugated
fin
type
radiator
fan
and
a
pellet
type
thermostat
The
water
pump
is
of
the
centrifugal
type
and
has
an
aluminium
die
cast
body
The
volute
chamber
is
built
into
the
front
cover
assembly
and
a
high
pressure
sealing
mechanism
prevents
water
leakage
and
noise
The
fan
pulley
is
driven
by
the
V
belt
from
a
pulley
on
the
crankshaft
he
pellct
type
thermostat
enables
the
engine
to
warm
up
rapidlY
and
also
regulates
the
temperature
of
the
coolant
When
the
wax
pellet
in
the
thermostat
is
heated
it
expands
and
exerts
pressure
against
a
rubber
diaphragm
causing
the
valve
to
open
and
allow
the
coolant
to
flow
from
the
cylinder
head
back
to
the
radiator
As
the
pellet
is
cooled
itcontractsand
allows
the
spring
to
close
the
valve
thereby
preventing
coolant
from
leaving
the
cylinder
head
The
rad
ator
is
of
the
down
flow
type
with
an
expansion
tank
The
relIef
valve
in
the
radiator
filler
cap
controls
the
pressure
at
approximately
0
9
kg
sq
cm
l3Ib
sq
in
Always
try
to
avoid
removing
the
filler
cap
when
the
engine
is
hot
as
coolant
may
spray
out
and
cause
scalding
If
the
cap
must
be
removed
in
these
circumstances
use
a
lar
e
pic
c
of
cloth
to
hold
the
cap
and
turn
the
cap
sli
htlY
Walt
until
all
pressure
has
been
released
before
lifting
off
the
cap
F
AN
BELT
TENSION
The
fan
belt
drives
the
water
pump
and
alternator
as
well
as
the
fan
and
its
correct
adjustment
is
most
essential
A
loose
fan
belt
will
sl
ip
and
Y
e
r
and
most
probably
cause
overheating
alternatively
If
the
belt
IS
too
tight
the
pump
and
alternator
bearings
will
be
overloaded
The
belt
is
correctly
tensioned
if
it
can
be
depressed
by
approximately
10
mm
1
2
in
at
a
point
midway
between
the
fan
and
alternator
pulleys
See
Fig
R2
If
adjustment
is
neces
ary
slacken
the
alternator
mounting
and
adjustment
bolts
and
pivot
the
alternator
away
from
the
engine
to
tighten
the
belt
to
towards
the
engine
if
the
belt
is
to
be
slackened
NOTE
Always
apply
leverage
to
the
drive
end
housing
when
pivoting
the
alternator
and
never
to
the
diode
end
housing
or
the
alternator
will
be
damaged
Retighten
the
alternator
bolts
and
make
SUfe
that
the
belt
is
correctly
tensioned
FLUSHING
AND
DRAINING
THE
SYSTEM
The
radiator
and
water
passages
should
be
flushed
out
periodically
to
remove
the
accumulated
scale
or
sediment
Reverse
flushing
equipment
should
be
used
to
carry
out
a
completely
thorough
flushing
operation
but
the
owner
drivef
not
possessing
this
type
of
equipment
can
flush
out
the
system
in
the
following
manner
Drain
the
system
by
removing
the
radiator
filler
cap
and
opening
the
radiator
and
cylinder
block
drain
taps
Close
the
taps
again
and
refill
the
radiator
Run
the
engine
for
a
ShOft
period
and
then
rc
open
the
drain
taps
Continue
this
sequence
until
the
water
flowing
from
the
taps
is
clean
then
close
the
taps
and
refill
the
radiator
An
anti
freeze
mixture
should
always
be
used
in
Winter
time
The
Niss3n
long
life
coolant
L
L
c
is
an
ethylene
glycol
solution
containing
a
corrosion
preventative
which
can
remain
in
the
vehicle
throughout
the
year
but
must
not
be
mixed
with
other
products
It
is
advisable
to
check
the
radiator
and
heater
hoses
when
filling
with
anti
freeze
and
renew
them
if
signs
of
deterioration
are
apparent
WATER
PUMP
Replacement
The
water
pump
must
not
be
dismantled
and
should
be
renewed
if
it
becomes
faulty
The
pump
can
be
removed
in
the
following
manner
Drain
the
cooling
system
2
Take
the
fan
belt
off
the
pulley
3
Remove
the
fan
and
pulley
4
Remove
the
retaining
nuts
and
withdraw
the
water
pump
See
Fig
B
3
lnstallation
of
the
pump
is
a
reversal
of
the
removal
procedures
rERMOST
ATTesting
The
thermostat
is
located
in
the
water
outlet
passage
See
Fig
B
4
To
remove
the
unit
drain
the
cooling
system
remove
the
radiator
hose
and
the
water
outlet
elbow
Take
out
the
thermostat
25
Page 28 of 171
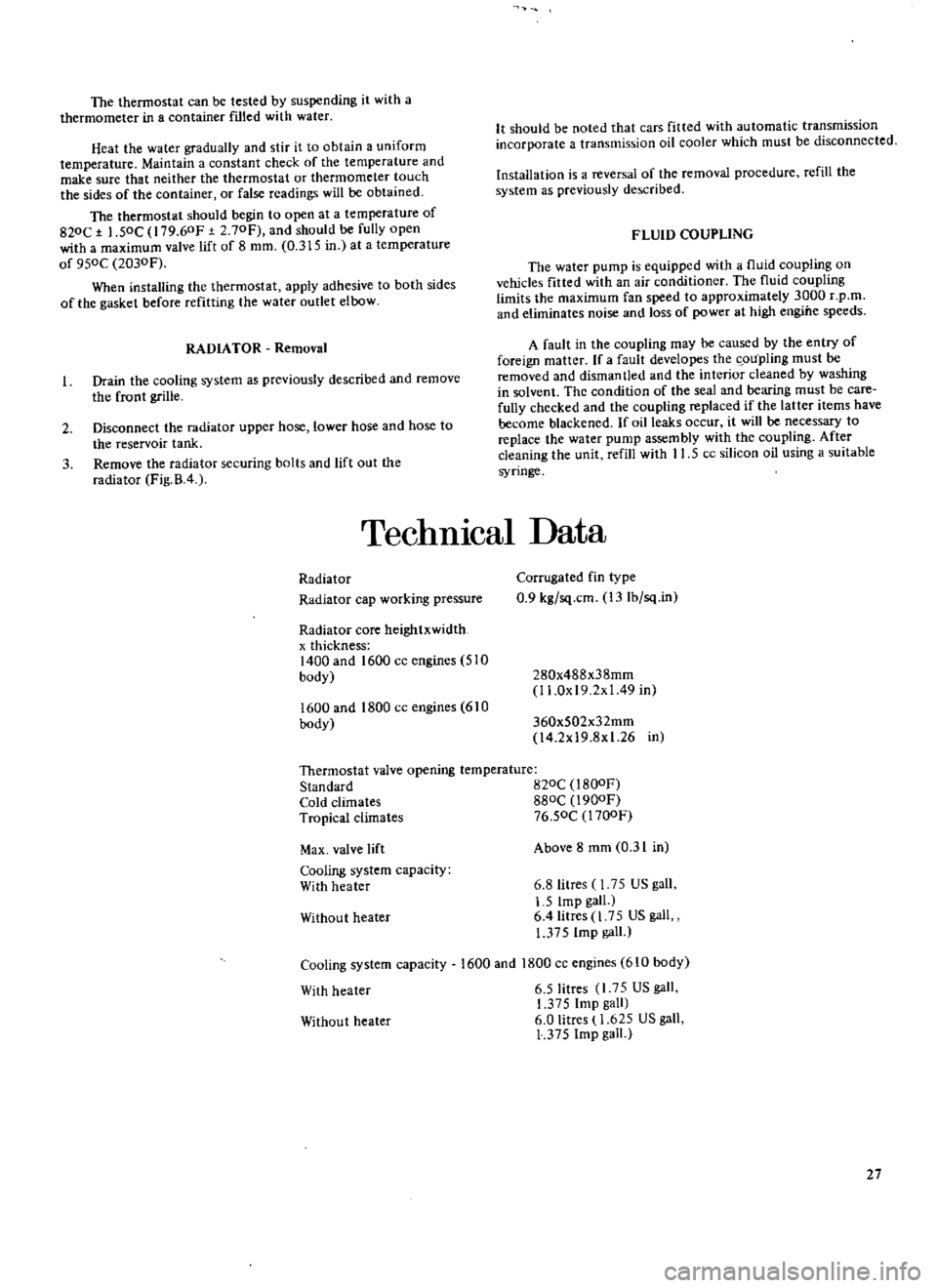
The
thermostat
can
be
tested
by
suspending
it
with
a
thermometer
in
a
container
ftlled
with
water
Heat
the
water
gradually
and
stir
it
to
obtain
a
uniform
temperature
Maintain
a
constant
check
of
the
temperature
and
make
sure
that
neither
the
thermostat
or
thermometer
touch
the
sides
of
the
container
or
false
readings
will
be
obtained
The
thermostat
should
begin
to
open
at
a
temperature
of
820C
1
50C
179
60F
2
70Fj
and
should
be
fully
open
with
a
maximum
valve
lift
of
8
mm
0
315
in
at
a
temperature
of
950C
2030F
When
installing
the
thermostat
apply
adhesive
to
both
sides
of
the
gasket
before
refitting
the
water
outlet
elbow
RADIATOR
Removal
Drain
the
cooling
system
as
previously
described
and
remove
the
front
grille
2
Disconnect
the
radiator
upper
hose
lower
hose
and
hose
to
the
reservoir
tank
3
Remove
the
radiator
securing
bolts
and
lift
out
the
radiator
Fig
B
4
It
should
be
noted
that
cars
fitted
with
automatic
transmission
incorporate
a
transmission
oil
cooler
which
must
be
disconnected
Installation
is
a
reversal
of
the
removal
procedure
refill
the
system
as
previously
described
FLUID
COUPLING
The
water
pump
is
equipped
with
a
fluid
coupling
on
vehicles
fitted
with
an
air
conditioner
The
fluid
coupling
Limits
the
maximum
fan
speed
to
approximately
3000
r
p
ro
and
eliminates
noise
and
loss
of
power
at
high
engine
speeds
A
fault
in
the
coupling
may
be
caused
by
the
entry
of
foreign
matter
If
a
fault
developes
the
oupling
must
be
removed
and
dismantled
and
the
interior
cleaned
by
washing
in
solvent
The
condition
of
the
seal
and
bearing
must
be
care
fully
checked
and
the
coupling
replaced
if
the
latter
items
have
become
blackened
If
oil
leaks
occur
it
will
be
necessary
to
replace
the
water
pump
assembly
with
the
coupling
After
cleaning
the
unit
refill
with
11
5
cc
silicon
oil
using
a
suitable
syringe
TechnIcal
Data
Radiator
Radiator
cap
working
pressure
Radiator
core
heightxwidth
x
thickness
1400
and
1600
cc
engines
510
body
1600
and
1800
cc
engines
610
body
Corrugated
fin
type
0
9
kg
sq
cm
13Ib
sq
in
280x488x38mm
I
LOx
19
2x
1
49
in
360x502x32mm
l4
2x19
8x1
26
in
Thermostat
valve
opening
temperature
Standard
B20C
l
BOOF
Cold
climates
880C
1900F
Tropical
climates
76
50C
l700F
Max
valve
lift
Cooling
system
capacity
With
heater
Without
heater
Cooling
system
capacity
With
heater
Above
8
mm
0
31
in
6
8litres
1
75
US
gall
1
5
Imp
gall
6
4litres
1
75
US
gall
1
375
Imp
gall
1600
and
1800
cc
engines
610
body
6
5litres
l
7
US
gall
1
375
Imp
gall
6
0
Iitres
1
625
US
gall
1
375
Imp
gall
Without
heater
27
Page 134 of 171
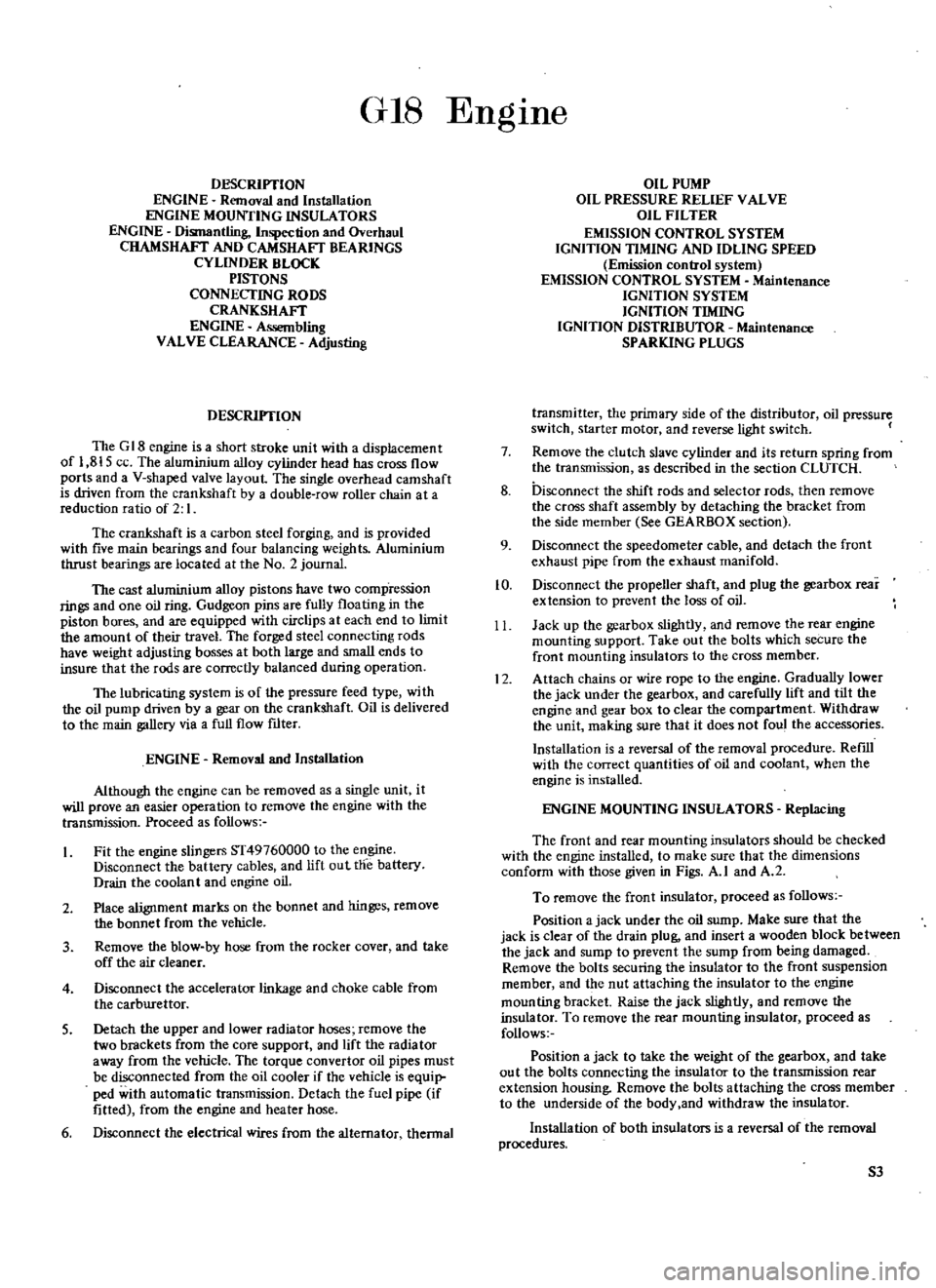
GIS
DESCRIYfION
ENGINE
Removal
and
Installation
ENGINE
MOUNTING
INSULATORS
ENGINE
Dismantling
Inspection
and
Overhaul
CHAMSHAFT
AND
CAMSHAFT
BEARINGS
CYLINDER
BLOCK
PISTONS
CONNECTING
RODS
CRANKSHAFT
ENGINE
Assembling
VALVE
CLEARANCE
Adjusting
DESCRIYfION
The
G
18
engine
is
a
short
stroke
unit
with
a
displacement
of
1
815
ce
The
aluminium
alloy
cylinder
head
has
cross
flow
ports
and
a
V
shaped
valve
layout
The
single
overhead
camshaft
is
driven
from
the
crankshaft
by
a
double
row
roller
chain
at
a
reduction
ratio
of
2
I
The
crankshaft
is
a
carbon
steel
forging
and
is
provided
with
five
main
bearings
and
four
balancing
weights
Aluminium
thrust
bearings
are
located
at
the
No
2
journal
The
cast
aluminium
alloy
pistons
have
two
comp
ression
rings
and
one
oil
ring
Gudgeon
pins
are
fully
floating
in
the
piston
bores
and
are
equipped
with
circlips
at
each
end
to
limit
the
amount
of
their
travel
The
forged
steel
connecting
rods
have
weight
adjusting
bosses
at
both
large
and
small
ends
to
insure
that
the
rods
are
correctly
balanced
during
operation
The
lubricating
system
is
of
the
pressure
feed
type
with
the
oil
pump
driven
by
a
gear
on
the
crankshaft
Oil
is
delivered
to
the
main
gallery
via
a
full
flow
ftlter
ENGINE
Removal
and
Installation
Although
the
engine
can
be
removed
as
a
single
unit
it
will
prove
an
easier
operation
to
remove
the
engine
with
the
transmission
Proceed
as
follows
Fit
the
engine
slingers
ST49760000
to
the
engine
Disconnect
the
battery
cables
and
lift
out
the
battery
Drain
the
coolant
and
engine
oil
2
Place
alignment
marks
on
the
bonnet
and
hinges
remove
the
bonnet
from
the
vehicle
3
Remove
the
blow
by
hose
from
the
rocker
cover
and
take
off
the
air
cleaner
4
Disconnect
the
accelerator
linkage
and
choke
cable
from
the
carburettor
S
Detach
the
upper
and
lower
radiator
hoses
remove
the
two
brackets
from
the
core
support
and
lift
the
radia
tor
away
from
the
vehicle
The
torque
convertor
oil
pipes
must
be
disconnected
from
the
oil
cooler
if
the
vehicle
is
equip
ped
with
automatic
transmission
Detach
the
fuel
pipe
if
fitted
from
the
engine
and
heater
hose
6
Disconnect
the
electrical
wires
from
the
alternator
thennal
EngIne
OIL
PUMP
OIL
PRESSURE
RELIEF
VALVE
OIL
FILTER
EMISSION
CONTROL
SYSTEM
IGNITION
TIMING
AND
IDLING
SPEED
Emission
control
system
EMISSION
CONTROL
SYSTEM
Maintenance
IGNITION
SYSTEM
IGNITION
TIMING
IGNITION
DISTRIBUTOR
Maintenance
SPARKING
PLUGS
transmitter
the
primary
side
of
the
distributor
oil
pressure
switch
starter
motor
and
reverse
light
switch
7
Remove
the
clutch
slave
cylinder
and
its
return
spring
from
the
transmission
as
described
in
the
section
CLUTCH
8
Disconnect
the
shift
rods
and
selector
rods
then
remove
the
cross
shaft
assembly
by
detaching
the
bracket
from
the
side
member
See
GEARBOX
section
9
Disconnect
the
speedometer
cable
and
detach
the
front
exhaust
pipe
from
the
exhaust
manifold
10
Disconnect
the
propeller
shaft
and
plug
the
gearbox
rear
extension
to
prevent
the
loss
of
oil
11
Jack
up
the
gearbox
slightly
and
remove
the
rear
engine
mounting
support
Take
out
the
bolts
which
secure
the
front
mounting
insulators
to
the
cross
member
12
Attach
chains
or
wire
rope
to
the
engine
Gradually
lower
the
jack
under
the
gearbox
and
carefully
lift
and
tilt
the
engine
and
gear
box
to
clear
the
compartment
Withdraw
the
unit
making
sure
that
it
does
not
foul
the
accessories
Installation
is
a
reversal
of
the
removal
procedure
RefIll
with
the
correct
quantities
of
oil
and
coolant
when
the
engine
is
installed
ENGINE
MOUNTING
INSULATORS
Replacing
The
front
and
rear
mounting
insulators
should
be
checked
with
the
engine
installed
to
make
sure
that
the
dimensions
conform
with
those
given
in
Figs
A
I
and
A
2
To
remove
the
front
insulator
proceed
as
follows
Position
a
jack
under
the
oil
sump
Make
sure
that
the
jack
is
clear
of
the
drain
plug
and
insert
a
wooden
block
between
the
jack
and
sump
to
prevent
the
sump
from
being
damaged
Remove
the
bolts
securing
the
insulator
to
the
front
suspension
member
and
the
nut
attaching
the
insulator
to
the
engine
mounting
bracket
Raise
the
jack
slightly
and
remove
the
insulator
To
remove
the
rear
mounting
insulator
proceed
as
follows
Position
a
jack
to
take
the
weight
of
the
gearbox
and
take
out
the
bolts
connecting
the
insulator
to
the
transmission
rear
extension
housing
Remove
the
bolts
attaching
the
cross
member
to
the
underside
of
the
body
and
withdraw
the
insulator
Installation
of
both
insulators
is
a
reversal
of
the
removal
procedures
S3