fuel filter DATSUN PICK-UP 1977 Service Manual
[x] Cancel search | Manufacturer: DATSUN, Model Year: 1977, Model line: PICK-UP, Model: DATSUN PICK-UP 1977Pages: 537, PDF Size: 35.48 MB
Page 21 of 537
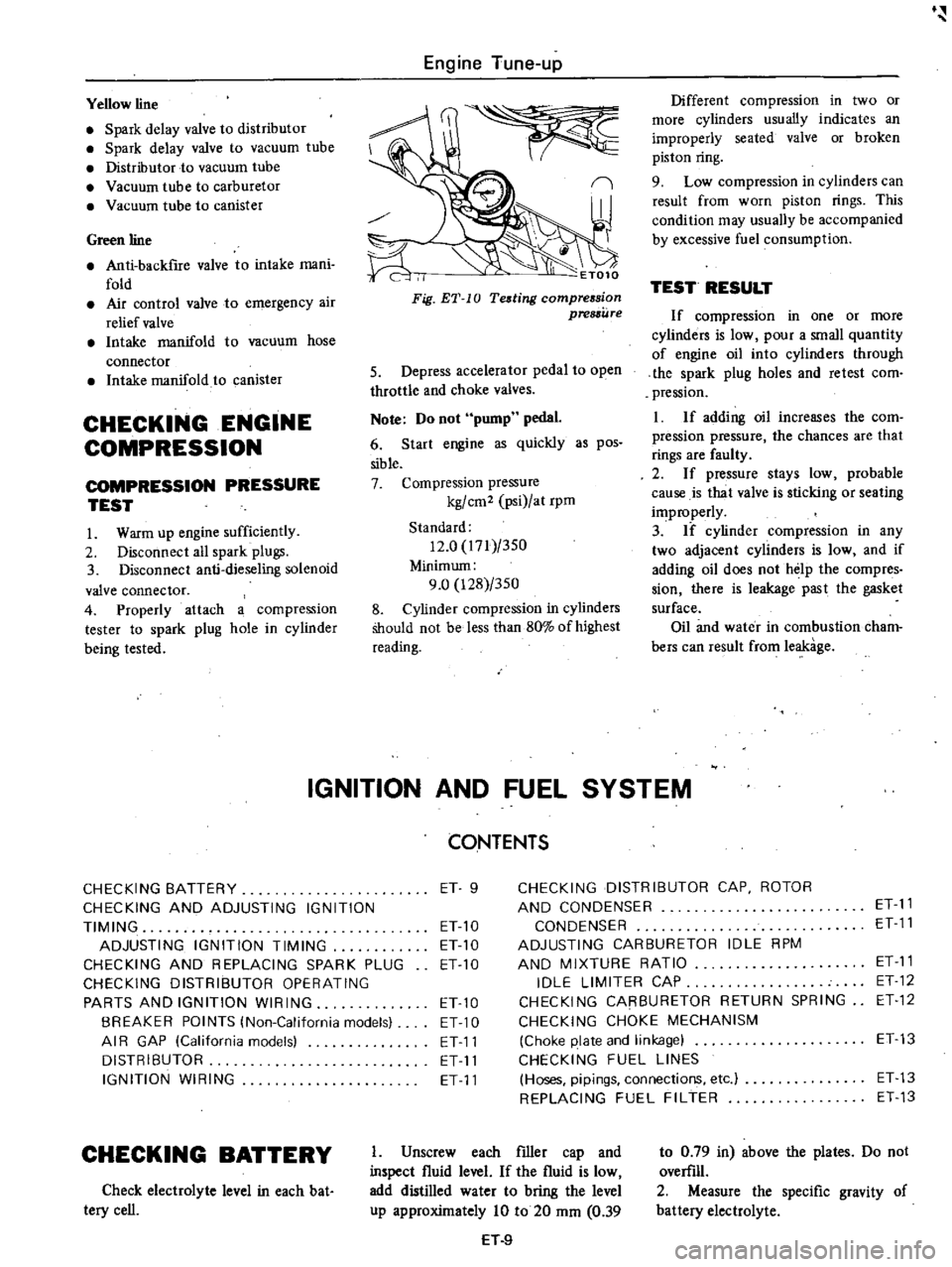
Yellow
line
Spark
delay
valve
to
distributor
Spark
delay
valve
to
vacuum
tube
Distributor
to
vacuum
tube
Vacuum
tube
to
carburetor
Vacuum
tube
to
canister
Green
line
Anti
backfire
valve
to
intake
mani
fold
Air
control
valve
to
emergency
air
relief
valve
Intake
manifold
to
vacuum
hose
connector
Intake
manifold
to
canister
CHECKING
ENGINE
COMPRESSION
COMPRESSION
PRESSURE
TEST
I
Warm
up
engine
sufficiently
2
Disconnect
all
spark
plugs
3
Disconnect
anti
dieseling
solenoid
valve
connector
4
Properly
attach
a
compression
tester
to
spark
plug
hole
in
cylinder
being
tested
Engine
Tune
up
I
ET010
Different
compression
in
two
or
more
cylinders
usually
indicates
an
improperly
seated
valve
or
broken
piston
ring
9
Low
compression
in
cylinders
can
result
from
worn
piston
rings
This
condition
may
usually
be
accompanied
by
excessive
fuel
consumption
TEST
RESULT
If
compression
in
one
or
more
cylinders
is
low
pour
a
small
quantity
of
engine
oil
into
cylinders
through
the
spark
plug
holes
and
retest
com
pression
I
If
adding
oil
increases
the
com
pression
pressure
the
chances
are
that
rings
are
faulty
2
If
pressure
stays
low
probable
cause
is
that
valve
is
sticking
or
seating
improperly
3
If
cylinder
compression
in
any
two
adjacent
cylinders
is
low
and
if
adding
oil
does
not
help
the
compres
sian
there
is
leakage
past
the
gasket
surface
Oil
and
water
in
combustion
cham
bers
can
result
from
leakage
IGNITION
AND
FUEL
SYSTEM
Fig
ET
10
Teding
compression
pressure
5
Depress
accelerator
pedal
to
open
throttle
and
choke
valves
Note
Do
not
pump
pedal
6
Start
engine
as
quickly
as
pos
sible
7
Compression
pressure
kg
cm2
psi
at
rpm
Standard
12
0
171
350
Minimum
9
0
128
350
8
Cylinder
compression
in
cylinders
Should
not
be
less
than
80
of
highest
reading
CONTENTS
CHECKING
BATTERY
ET
9
CHECKING
DISTRIBUTOR
CAP
ROTOR
CHECKING
AND
ADJUSTING
IGNITION
AND
CONDENSER
ET
11
TIMING
ET
10
CONDENSER
ET
11
ADJUSTING
IGNITION
TIMING
ET10
ADJUSTING
CARBURETOR
IDLE
RPM
CHECKING
AND
REPLACING
SPARK
PLUG
ETlO
AND
MIXTURE
RATIO
ET
11
CHECKING
DISTRIBUTOR
OPERATING
IDLE
LIMITER
CAP
ET
12
PARTS
AND
IGNITION
WIRING
ETlO
CHECKING
CARBURETOR
RETURN
SPRING
ET
12
BREAKER
POINTS
lNon
California
models
ET
10
CHECKING
CHOKE
MECHANISM
AI
R
GAP
lCalifornia
models
ET11
Choke
plate
and
linkage
ET13
DISTRIBUTOR
ET
11
CHECKING
FUEL
LINES
IGNITION
WIRING
ET
11
Hoses
pipings
connections
etc
ET
13
REPLACING
FUEL
FILTER
ET
13
CHECKING
BATTERY
Check
electrolyte
level
in
each
bat
tery
cell
I
Unscrew
each
filler
cap
and
inspect
fluid
level
If
the
fluid
is
low
add
distilled
water
to
bring
the
level
up
approximately
10
to
20
mm
0
39
H
9
to
0
79
in
above
the
plates
Do
not
overfill
2
Measure
the
specific
gravity
of
battery
electrolyte
Page 25 of 537
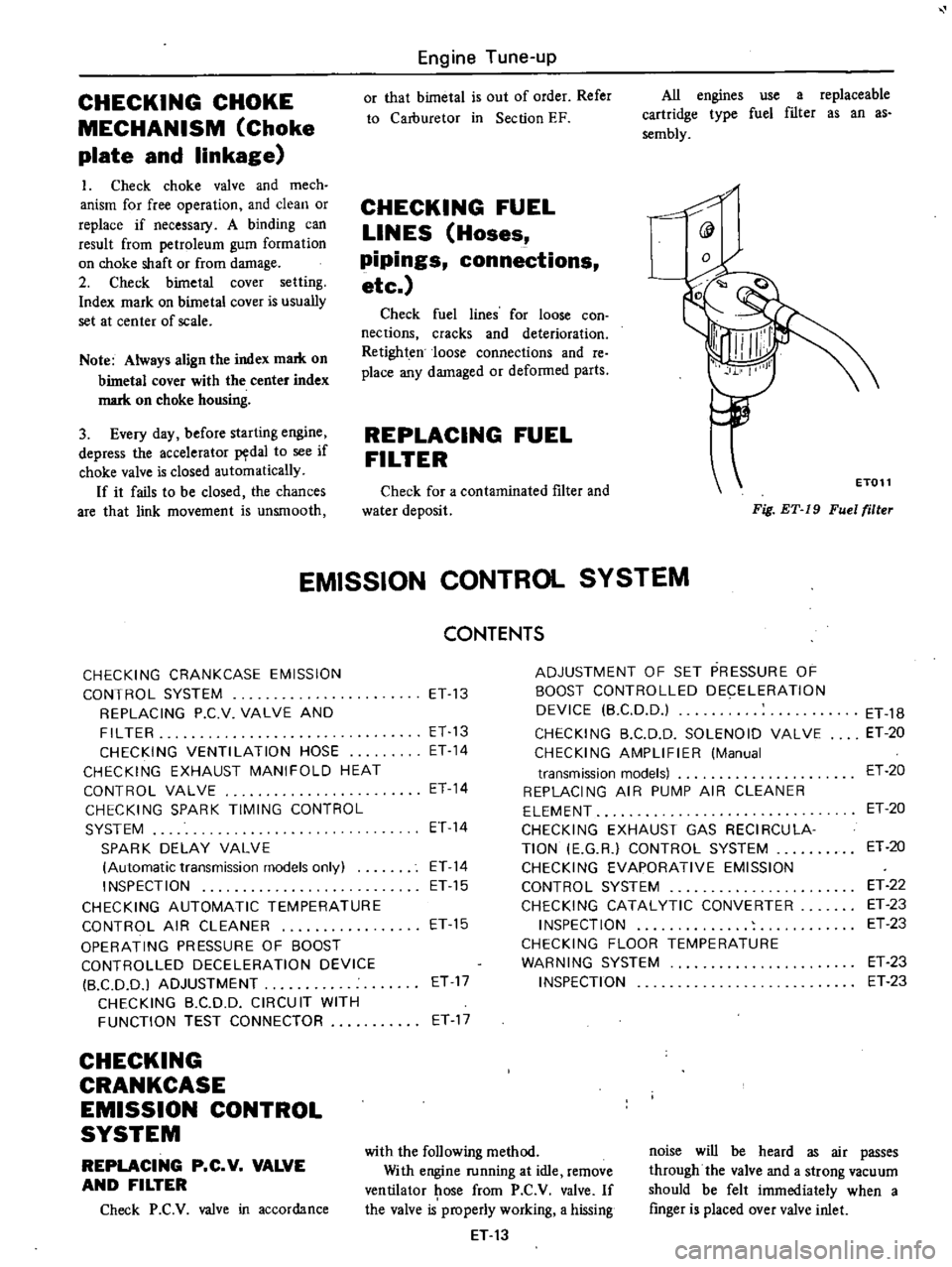
CHECKING
CHOKE
MECHANISM
Choke
plate
and
linkage
1
Check
choke
valve
and
mech
anism
for
free
operation
and
clean
or
replace
if
necessary
A
binding
can
result
from
petroleum
gum
formation
on
choke
shaft
or
from
damage
2
Check
bimetal
cover
setting
Index
mark
on
bimetal
cover
is
usually
set
at
center
of
scale
Note
Always
align
the
index
mark
on
bimetal
cover
with
the
center
index
mark
on
choke
housing
3
Every
day
before
starting
engine
depress
the
accelerator
P
dal
to
see
if
choke
valve
is
closed
automatically
If
it
fails
to
be
closed
the
chances
are
that
link
movement
is
unsmooth
Engine
Tune
up
or
that
bimetal
is
out
of
order
Refer
to
Carburetor
in
Section
EF
CHECKING
FUEL
LINES
Hoses
pipings
connections
etc
Check
fuel
lines
for
loose
con
nections
cracks
and
deterioration
Retighten
loose
connections
and
re
place
any
damaged
or
deformed
parts
REPLACING
FUEL
FILTER
Check
for
a
contaminated
filter
and
water
deposit
All
engines
use
a
replaceable
cartridge
type
fuel
filter
as
an
as
sembly
@
Fig
ET
19
Fuel
filler
ET011
EMISSION
CONTROL
SYSTEM
CHECKING
CRANKCASE
EMISSION
CONTROL
SYSTEM
REPLACING
P
C
V
VALVE
AND
FILTER
CHECKING
VENTILATION
HOSE
CHECKING
EXHAUST
MANIFOLD
HEAT
CONTROL
VALVE
CHECKING
SPARK
TIMING
CONTROL
SYSTEM
SPARK
DELAY
VALVE
Automatic
transmission
models
only
INSPECTION
CHECKING
AUTOMATIC
TEMPERATURE
CONTROL
AIR
CLEANER
OPERATING
PRESSURE
OF
BOOST
CONTROLLED
DECELERATION
DEVICE
B
CD
D
I
ADJUSTMENT
CHECKING
B
C
DD
CIRCUIT
WITH
FUNCTION
TEST
CONNECTOR
CHECKING
CRANKCASE
EMISSION
CONTROL
SYSTEM
REPLACING
P
C
V
VALVE
AND
FILTER
Check
P
C
V
valve
in
accordance
CONTENTS
ET
13
ET
13
ET
14
ET
14
ET
14
ET
14
ET
15
ET
15
ET
17
ET
17
ADJUSTMENT
OF
SET
PRESSURE
OF
BOOST
CONTROLLED
DECELERATION
DEVICE
B
CD
D
CHECKING
B
C
D
D
SOLENOID
VALVE
CHECKING
AMPLIFIER
Manual
transmission
models
REPLACING
AIR
PUMP
AIR
CLEANER
ELEMENT
CHECKING
EXHAUST
GAS
RECIRCULA
TION
E
G
R
CONTROL
SYSTEM
CHECKING
EVAPORATIVE
EMISSION
CONTROL
SYSTEM
CHECKING
CATALYTIC
CONVERTER
INSPECTION
CHECKING
FLOOR
TEMPERATURE
WARNING
SYSTEM
INSPECTION
with
the
following
method
With
engine
running
at
idle
remove
ventilator
ose
from
P
C
V
valve
If
the
valve
is
properly
working
a
hissing
ET
13
ET
18
ET
20
ET
20
ET
20
ET
20
ET
22
ET
23
ET
23
ET
23
ET
23
noise
will
be
heard
as
air
passes
through
the
valve
and
a
strong
vacuum
should
be
felt
immediately
when
a
finger
is
placed
over
valve
inlet
Page 35 of 537
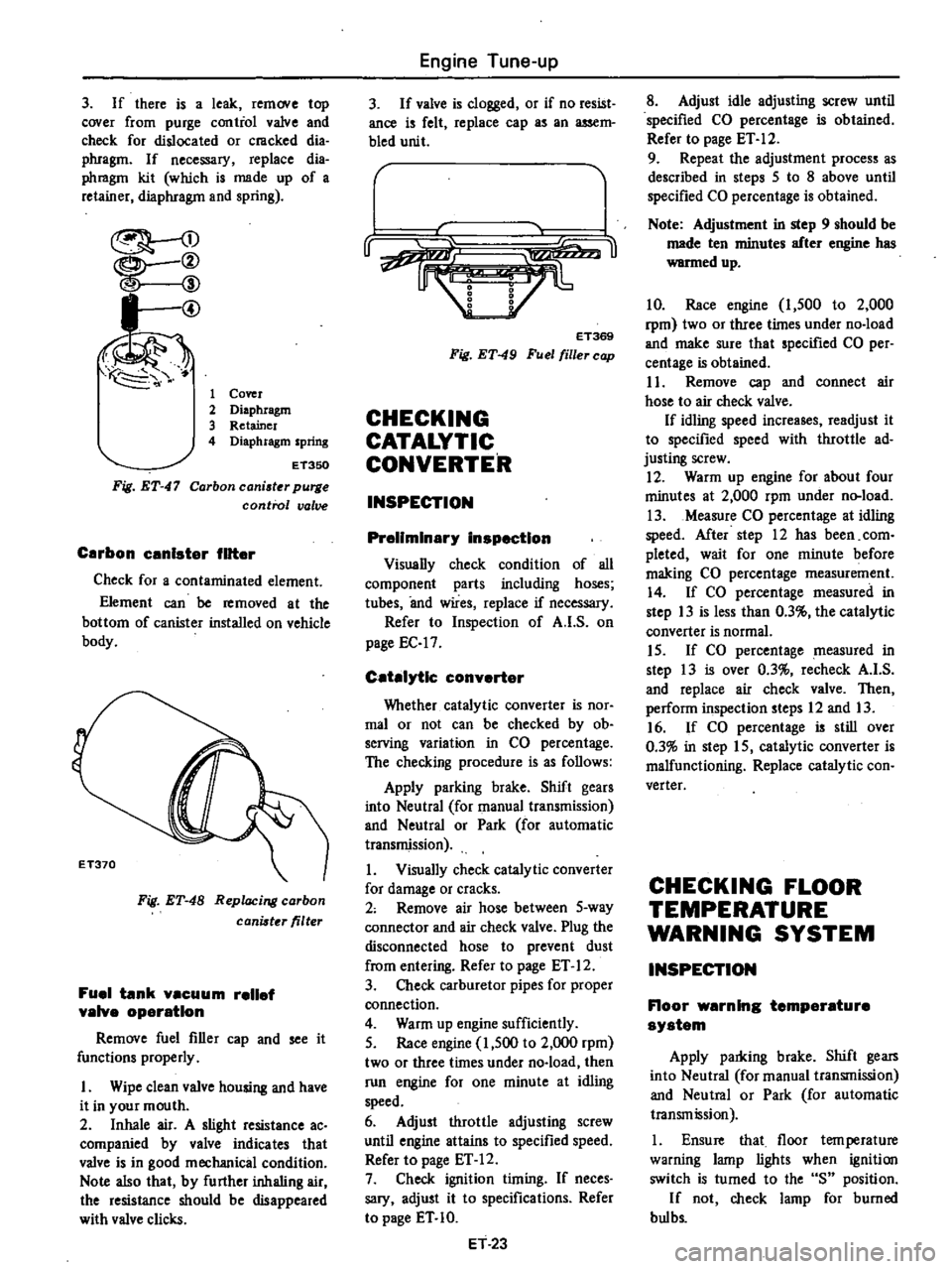
3
If
there
is
a
leak
remove
top
cover
from
purge
contiol
valve
and
check
for
dislocated
or
cmcked
dia
phragm
If
necessary
replace
dia
phmgm
kit
which
is
made
up
of
a
retainer
diaphragm
and
spring
I
@
1
Cover
2
Diaphragm
3
Retainer
4
Diaphragm
spring
Fig
ET
47
ET350
Carbon
caniater
purge
control
valve
Carbon
unlster
filter
Check
for
a
contaminated
element
Element
can
be
removed
at
the
bottom
of
canister
installed
on
vehicle
body
Fig
ET
48
Replacing
carbon
canister
filter
Fuel
tank
vacuum
relief
valve
operation
Remove
fuel
filler
cap
and
see
it
functions
properly
I
Wipe
clean
valve
housing
and
have
it
in
your
mouth
2
Inhale
air
A
slight
resistance
ac
companied
by
valve
indicates
that
valve
is
in
good
mechanical
condition
Note
also
that
by
further
inhaling
air
the
resistance
should
be
disappeared
with
valve
clicks
Engine
Tune
up
3
If
valve
is
clogged
or
if
no
resist
ance
is
felt
replace
cap
as
an
assem
bled
unit
r
u
ET369
Fig
ET
49
Fuel
filler
cap
CHECKING
CATALYTIC
CONVERTER
INSPECTION
Preliminary
inspection
Visually
check
condition
of
all
component
parts
including
hoses
tubes
and
wires
replace
if
necessary
Refer
to
Inspection
of
A
I
S
on
page
EC
17
Catalytic
converter
Whether
catalytic
converter
is
nOf
mal
or
not
can
be
checked
by
ob
serving
variation
in
CO
percentage
The
checking
procedure
is
as
follows
Apply
parking
brake
Shift
gears
into
Neutral
for
manual
transmission
and
Neutral
or
Park
for
automatic
transmission
1
Visually
check
catalytic
converter
for
damage
or
cracks
2
Remove
air
hose
between
5
way
connector
and
air
check
valve
Plug
the
disconnected
hose
to
prevent
dust
from
entering
Refer
to
page
ET
12
3
Check
carburetor
pipes
for
proper
connection
4
Warm
up
engine
sufficiently
5
Race
engine
1
500
to
2
000
rpm
two
or
three
times
under
no
load
then
run
engine
for
one
minute
at
idling
speed
6
Adjust
throttle
adjusting
screw
until
engine
attains
to
specified
speed
Refer
to
page
ET
12
7
Check
ignition
timing
If
neces
sary
adjust
it
to
specifications
Refer
to
page
ET
10
ET
23
8
Adjust
idle
adjusting
screw
until
specified
CO
percentage
is
obtained
Refer
to
page
ET
12
9
Repeat
the
adjustment
process
as
described
in
steps
5
to
8
above
until
specified
CO
percentage
is
obtained
Note
Adjustment
in
step
9
should
be
made
ten
minutes
after
engine
has
warmed
up
10
Race
engine
1
500
to
2
000
rpm
two
or
three
times
under
no
load
and
make
sure
that
specified
CO
per
centage
is
obtained
I
1
Remove
cap
and
connect
air
hose
to
air
check
valve
If
idling
speed
increases
readjust
it
to
specified
speed
with
throttle
ad
justing
screw
12
Warm
up
engine
for
about
four
minutes
at
2
000
rpm
under
n
load
13
Measure
CO
percentage
at
idling
speed
After
step
12
has
been
com
pleted
wait
for
one
minute
before
making
CO
percentage
measurement
14
If
CO
percentage
measured
in
step
13
is
less
than
0
3
the
catalylic
converter
is
normal
15
If
CO
percentage
measured
in
step
13
is
over
0
3
recheck
A
I
S
and
replace
air
check
valve
Then
perform
inspection
steps
12
and
13
16
If
CO
percentage
is
still
over
0
3
in
step
15
catalytic
converter
is
malfunctioning
Replace
catalytic
con
verter
CHECKING
FLOOR
TEMPERATURE
WARNING
SYSTEM
INSPECTION
Floor
warning
temperature
system
Apply
parldng
brake
Shift
gears
into
Neutral
for
manual
transmission
and
Neutral
or
Park
for
automatic
transmission
1
Ensure
that
floor
tern
perature
warning
lamp
lights
when
ignition
switch
is
turned
to
the
S
position
If
not
check
lamp
for
burned
bul
bs
Page 41 of 537
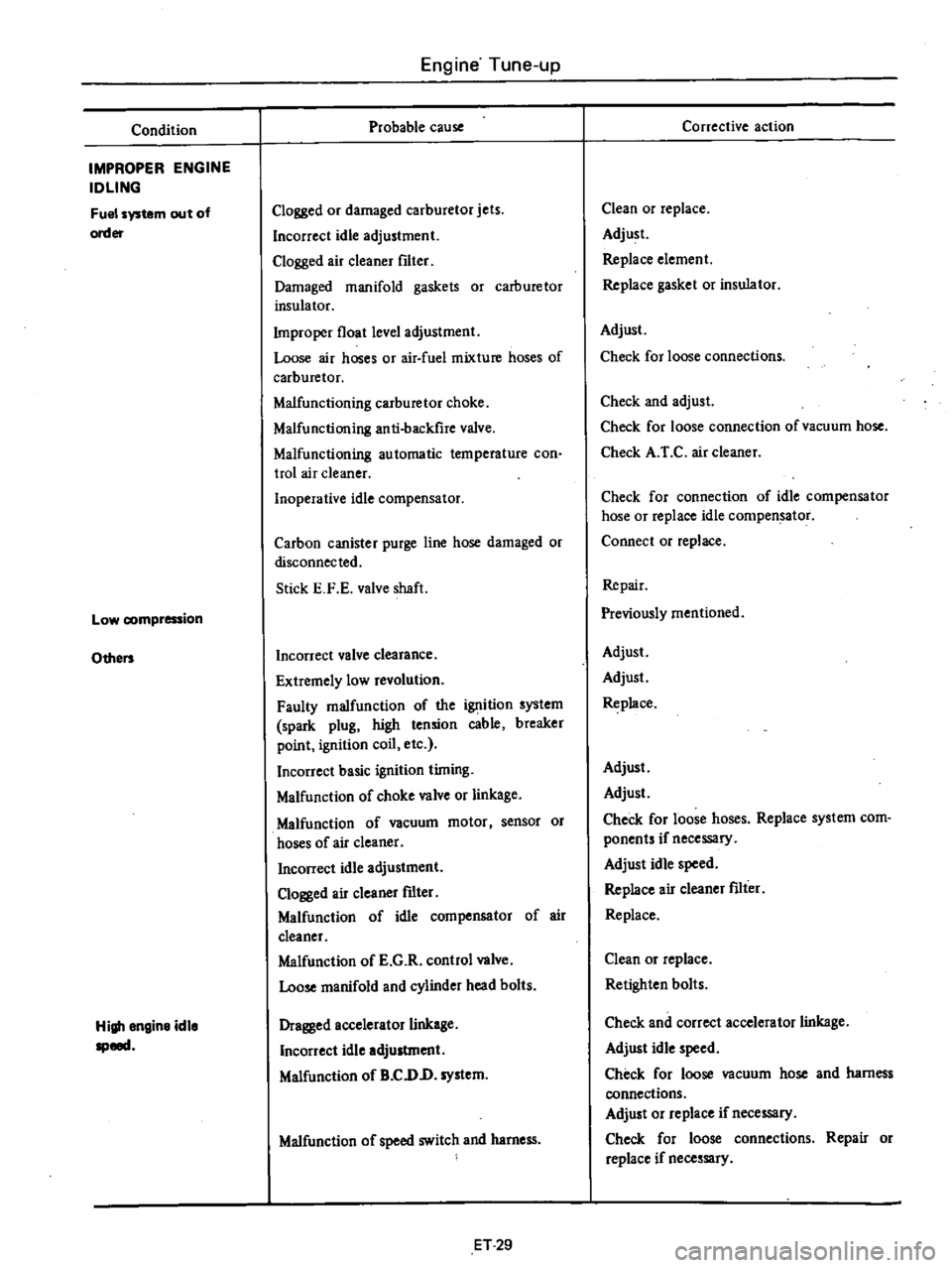
Condition
IMPROPER
ENGINE
IDLING
Fuel
system
out
of
order
Low
compression
Others
High
engine
idle
speed
Engine
Tune
up
Probable
cause
Clogged
or
damaged
carburetor
jets
Incorrect
idle
adjustment
Clogged
air
cleaner
filter
Damaged
manifold
gaskets
or
carburetor
insulator
Improper
float
level
adjustment
Loose
air
hoses
or
air
fuel
mixture
hoses
of
carburetor
Malfunctioning
carburetor
choke
Malfunctioning
anti
backfire
valve
Malfunctioning
automatic
temperature
con
trol
air
cleaner
Inoperative
idle
compensator
Carbon
canister
purge
line
hose
damaged
or
disconnected
Stick
E
F
E
valve
shaft
Incorrect
valve
clearance
Extremely
low
revolution
Faulty
malfunction
of
the
ignition
system
spark
plug
high
tension
cable
breaker
point
ignition
coil
etc
Incorrect
basic
ignition
timing
Malfunction
of
choke
valve
or
linkage
Malfunction
of
vacuum
motor
sensor
or
hoses
of
air
cleaner
Incorrect
idle
adjustment
Clogged
air
cleaner
fdter
Malfunction
of
idle
compensator
of
air
cleaner
Malfunction
of
E
G
R
control
valve
Loose
manifold
and
cylinder
head
bolts
Dragged
accelerator
linkage
Incorrect
idle
adjustment
Malfunction
of
B
CDD
system
Malfunction
of
speed
switch
and
harness
ET
29
Corrective
action
Clean
or
replace
Adjust
Replace
element
Replace
gasket
or
insulator
Adjust
Check
for
loose
connections
Check
and
adjust
Check
for
loose
connection
of
vacuum
hose
Check
A
r
C
air
cleaner
Check
for
connection
of
idle
compensator
hose
or
replace
idle
compen
tor
Connect
or
replace
Repair
Previously
mentioned
Adjust
Adjust
Replace
Adjust
Adjust
Check
for
loose
hoses
Replace
system
com
ponents
if
necessary
Adjust
idle
speed
Replace
air
cleaner
fdter
Replace
Clean
or
replace
Retighten
bolts
Check
and
correct
accelerator
linkage
Adjust
idle
speed
Check
for
loose
vacuum
hose
and
harness
connections
Adjust
or
replace
if
necessary
Check
for
loose
connections
Repair
or
replace
if
necessary
Page 44 of 537
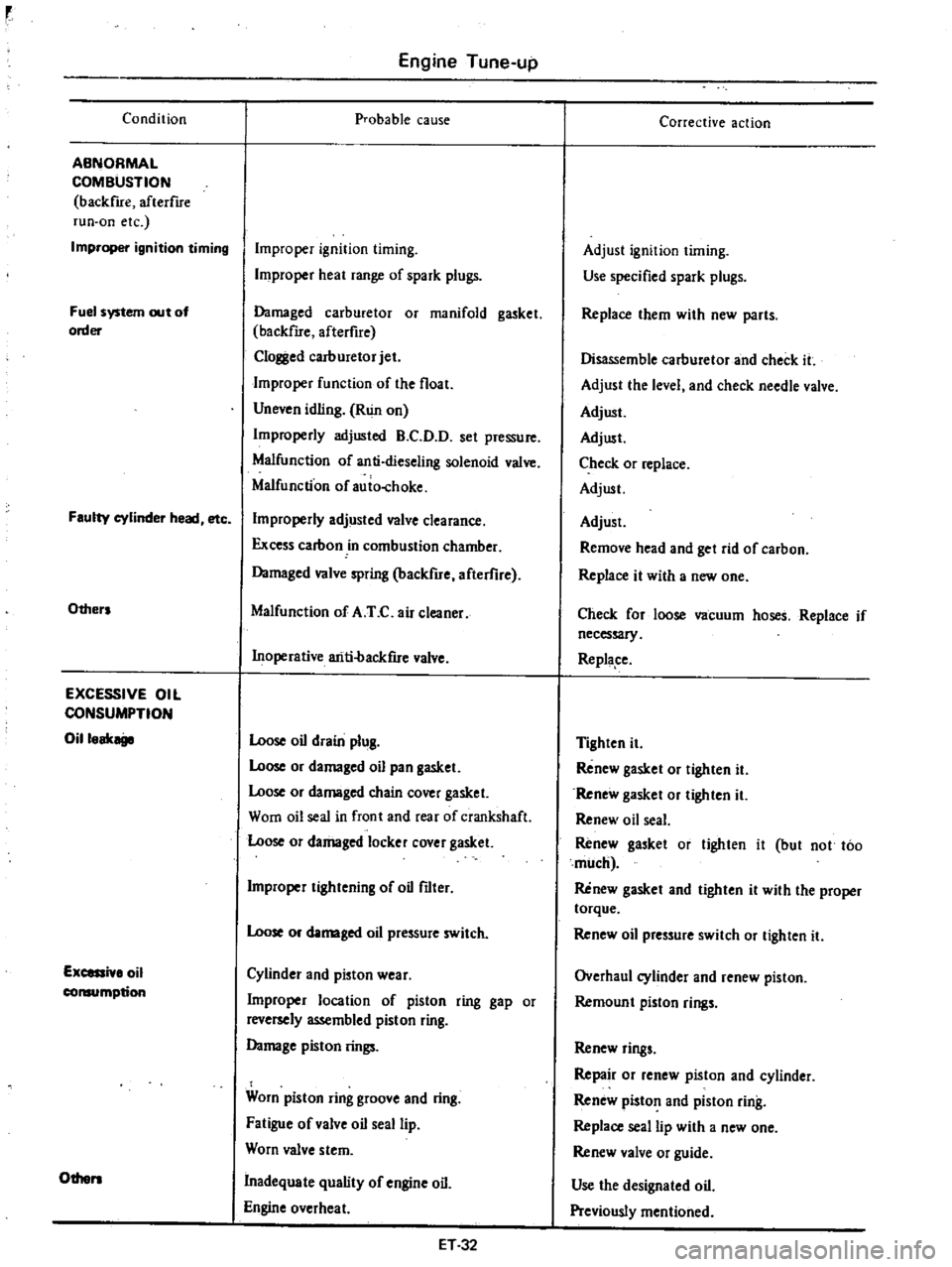
Condition
ABNORMAL
COMBUSTION
backfue
afterflre
run
on
etc
Improper
ignition
timing
Fuel
system
out
of
order
Faulty
cylinder
head
etc
Others
EXCESSIVE
OIL
CONSUMPTION
Oilloak
Excessi
lo
oil
consumption
Others
Engine
Tune
up
probable
cause
Improper
ignition
timing
Improper
heat
range
of
spark
plugs
Damaged
carburetor
or
manifold
gasket
backfue
afterfire
Clol
l
ed
carburetor
jet
Improper
function
of
the
float
Uneven
idling
Run
on
Improperly
adjusted
B
C
D
D
set
pressure
Malfunction
of
anti
dieseling
solenoid
valve
Malfunction
of
auio
choke
Improperly
adjusted
valve
clearance
Excess
carbon
in
combustion
chamber
Damaged
valve
spring
backfire
afterflre
Malfunction
of
A
T
C
air
cleaner
Inoperative
ariti
backfue
valve
Loose
oil
drain
plug
Loose
or
damaged
oil
pan
gasket
Loose
or
damaged
chain
cover
gasket
Worn
oil
seal
in
front
and
rear
of
crankshaft
Loose
or
damaged
locker
cover
gasket
Improper
tightening
of
oil
filter
Loose
or
damaged
oil
pressure
switch
Cylinder
and
pioton
wear
Improper
location
of
piston
ring
gap
or
reversely
assembled
piston
ring
Damage
piston
rings
Worn
piston
ring
groove
and
ring
Fatigue
of
valve
oil
seal
lip
Worn
valve
stem
Inadequate
quality
of
engine
oil
Engine
overheat
ET32
Corrective
action
Adjust
ignition
timing
Use
specified
spark
plugs
Replace
them
with
new
parts
Disassemble
carburetor
and
check
it
Adjust
the
level
and
check
needle
valve
Adjust
Adjust
Check
or
replace
Adjust
Adjust
Remove
head
and
get
rid
of
carbon
Replace
it
with
a
new
one
Check
for
loose
vacuum
hoses
Replace
if
necessary
Replape
Tighten
it
Renew
gasket
or
tighten
it
Renew
gasket
or
tighten
it
Renew
oil
seal
Renew
gasket
or
tighten
it
but
not
too
much
Renew
gasket
and
tighten
it
with
the
proper
torque
Renew
oil
pressure
switch
or
tighten
it
Overhaul
cylinder
and
renew
piston
Remoun
t
piston
rings
Renew
rings
Repair
or
renew
piston
and
cylinder
Renew
piston
and
piston
ring
Replace
seal
lip
with
a
new
one
Renew
valve
or
guide
Use
the
designated
oil
Previously
mentioned
Page 49 of 537
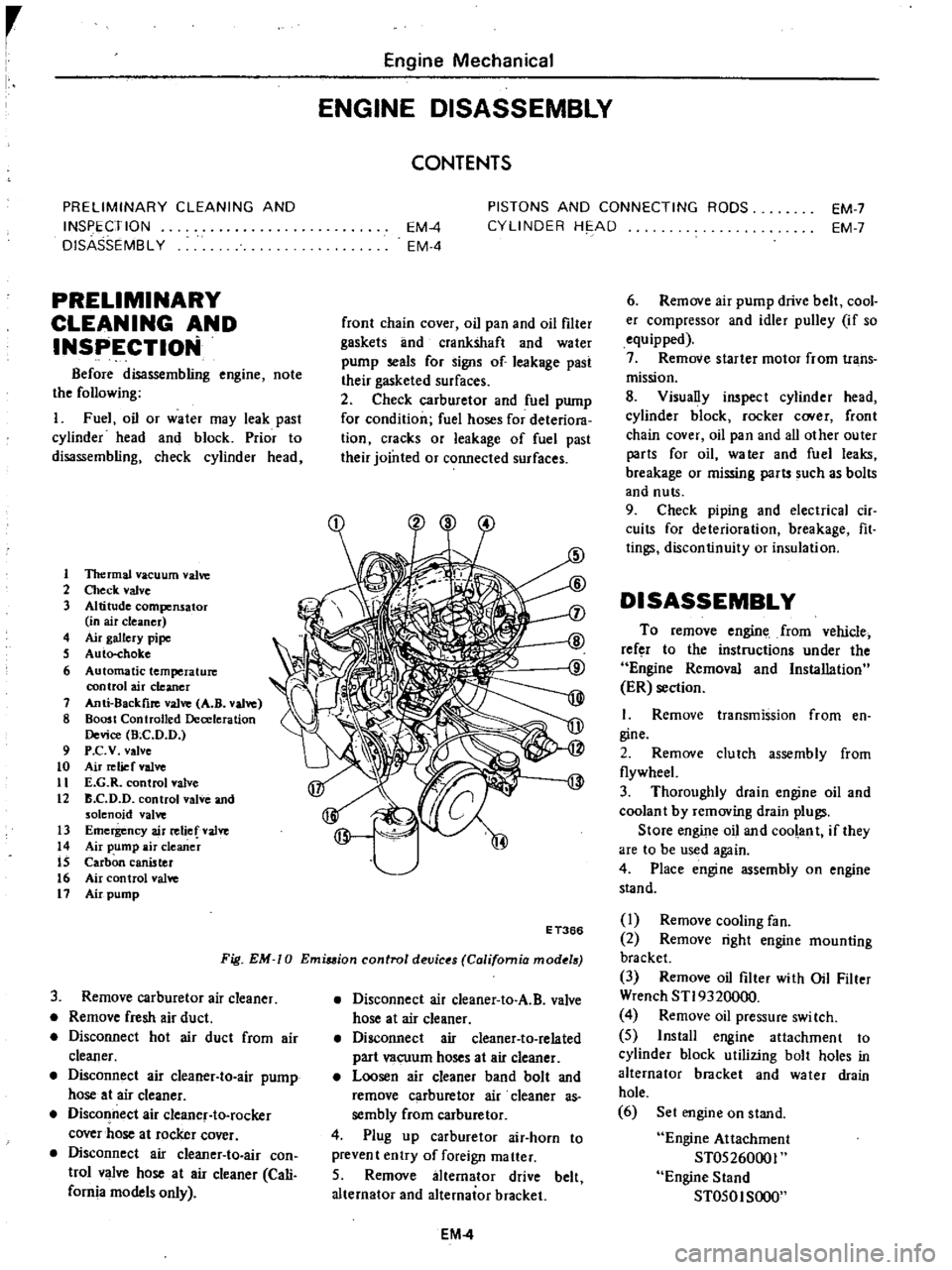
r
I
I
PRELIMINARY
CLEANING
AND
INSPECTION
DISASSEMBL
Y
PRELIMINARY
CLEANING
AND
INSt
ECTION
Before
disassembling
engine
note
the
following
I
Fuel
oil
or
water
may
leak
past
cylinder
head
and
block
Prior
to
disassembling
check
cylinder
head
1
1ltermal
vacuum
valve
2
Check
valve
3
Altitude
compensator
in
air
cleaner
4
Air
gallery
pipe
S
Auto
choke
6
Automatic
temperature
control
air
cleaner
7
Anti
8ackfire
valve
A
B
valve
8
Boost
Controlled
Deceleration
Device
Bee
D
D
9
P
c
v
valve
to
Air
relief
valve
11
E
G
R
control
valve
12
B
C
D
D
control
valve
and
solenoid
valve
13
Emergency
air
relief
valve
14
Air
pump
air
cleaner
IS
Carbon
canister
16
Air
control
valve
11
Air
pump
Engine
Mechanical
ENGINE
DISASSEMBLY
CONTENTS
EM
4
EM
4
PISTONS
AND
CONNECTING
RODS
CYLINDER
HE
AD
EM
7
EM
7
front
chain
cover
oil
pan
and
oil
filter
gaskets
lInd
crankshaft
and
water
pump
seals
for
signs
of
leakage
past
their
gasketed
surfaces
2
Check
carburetor
and
fuel
pump
for
condition
fuel
hoses
for
deteriora
tion
cracks
or
leakage
of
fuel
past
their
jointed
or
connected
surfaces
Fig
EM
0
Emiuion
control
devic
s
California
mod
18
E
T366
3
Remove
carburetor
air
cleaner
Remove
fresh
air
duct
Disconnect
hot
air
duct
from
air
cleaner
Disconnect
air
cleaner
to
air
pump
hose
at
air
cleaner
Disconnect
air
cleanef
to
rocker
cover
hose
at
rocker
cover
Disconnect
air
cIeaner
to
air
con
trol
valve
hose
at
air
cleaner
Cali
fornia
models
only
Disconnect
air
cleaner
to
A
B
valve
hose
at
air
cleaner
Disconnect
air
cleaner
to
related
part
vacuum
hoses
at
air
cleaner
Loosen
air
cleaner
band
bolt
and
remove
carburetor
air
cleaner
as
sembly
from
carburetor
4
Plug
up
carburetor
air
horn
to
prevent
entry
of
foreign
matter
5
Remove
alternator
drive
belt
alternator
and
alternator
bracket
EM
4
6
Remove
air
pump
drive
belt
cool
er
compressor
and
idler
pulley
if
so
equipped
7
Remove
starter
motor
from
trans
mission
8
Visually
inspect
cylinder
head
cylinder
block
rocker
C
Ner
front
chain
cover
oil
pan
and
all
other
outer
parts
for
oil
water
and
fuel
leaks
breakage
or
missing
parts
such
as
bolts
and
nuts
9
Check
piping
and
electrical
cir
cuits
for
deterioration
breakage
fit
tings
discontinuity
or
insulation
DISASSEMBLY
To
remove
engine
from
vehicle
refer
to
the
instructions
under
the
Engine
Removal
and
Installation
ER
section
I
Remove
transmission
from
en
gine
2
Remove
clutch
assembly
from
flywheeL
3
Thoroughly
drain
engine
oil
and
coolan
t
by
removing
drain
plugs
Store
engine
oil
and
coolant
if
they
are
to
be
used
again
4
Place
engine
assembly
on
engine
stand
I
Remove
cooling
fan
2
Remove
right
engine
mounting
bracket
3
Remove
oil
filter
with
Oil
Filter
Wrench
STI9320000
4
Remove
oil
pressure
swi
tch
5
Install
engine
attachment
to
cylinder
block
utilizing
bolt
holes
in
alternator
bracket
and
water
drain
hole
6
Set
engine
on
stand
Engine
Attachment
ST05260001
Engine
Stand
ST050I
SOOO
Page 71 of 537
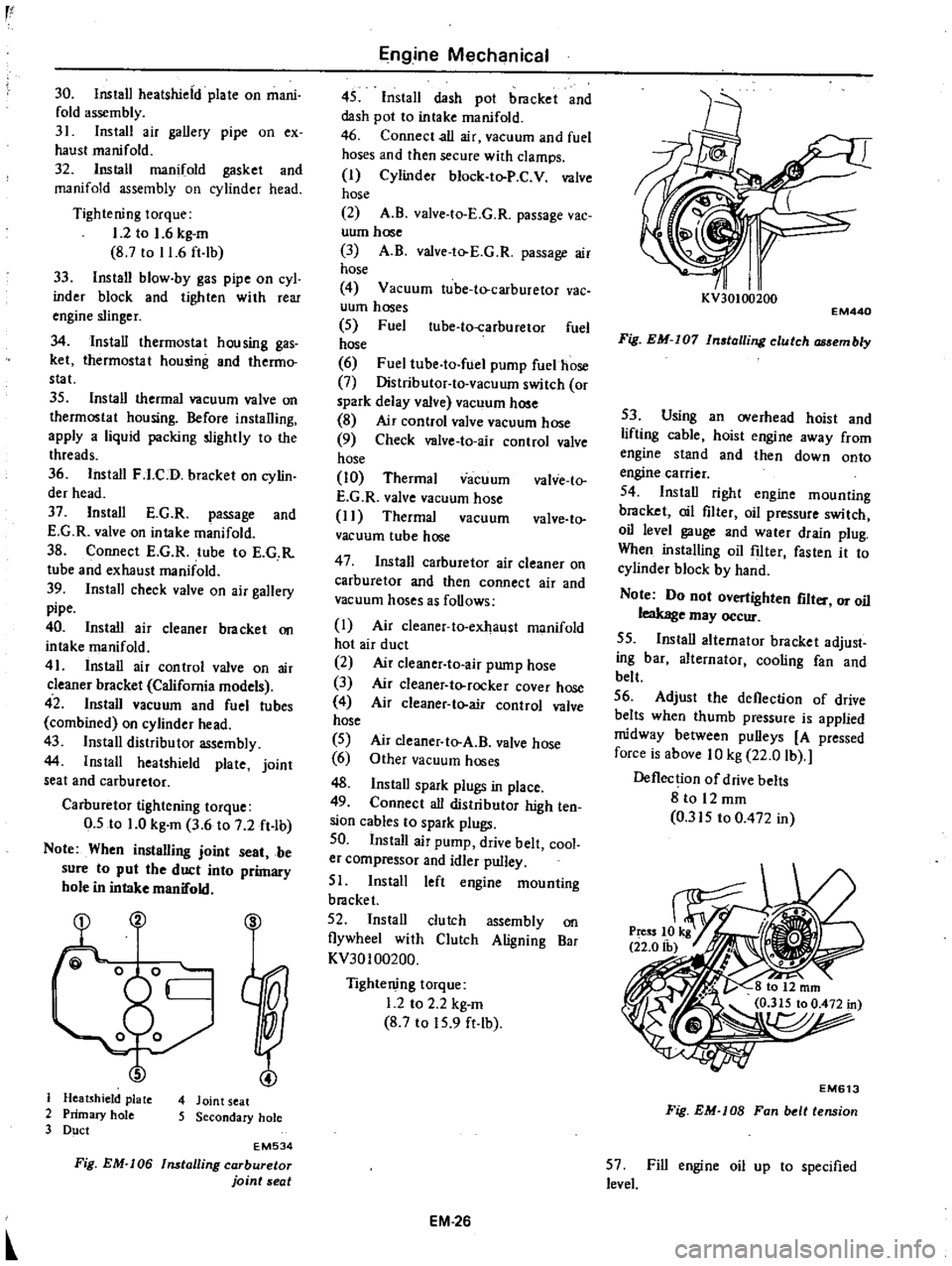
30
Install
heatshieid
plate
on
mani
fold
assembly
31
Install
air
gallery
pipe
on
ex
haust
manifold
32
Install
manifold
gasket
and
manifold
assembly
on
cylinder
head
Tightening
torque
1
2to
1
6kg
m
8
7
to
11
6
ft
lb
33
Install
blow
by
gas
pipe
on
cyl
inder
block
and
tighten
with
rear
engine
slinger
34
Install
thermostat
housing
gas
ket
thermostat
housing
and
thermo
stat
35
Install
thermal
vacuum
valve
on
thermostat
housing
Before
installing
apply
a
liquid
packing
slightly
to
the
threads
36
Install
FJ
C
D
bracket
on
cylin
der
head
37
Install
E
G
R
passage
and
E
G
R
valve
on
intake
manifold
38
Connect
E
G
R
tube
to
E
G
R
tube
and
exhaust
manifold
39
Install
check
valve
on
air
gallery
pipe
40
Install
air
cleaner
bracket
on
intake
manifold
41
Install
air
control
valve
on
air
cleaner
bracket
California
models
42
Install
vacuum
and
fuel
tubes
combined
on
cylinder
head
43
Install
distributor
assembly
44
Install
heatshield
plate
joint
seat
and
carburetor
Carbure10r
tightening
torque
0
5
to
1
0
kg
m
3
6
to
7
2
ft
lb
Note
When
instalUng
joint
seat
be
sure
to
put
the
duct
into
primary
hole
in
intake
manifold
S
J
Heatshield
plate
4
Joint
seat
2
Primary
hole
5
Secondary
hole
3
Duct
EM534
Fig
EM
I06
Installing
carburetor
joint
seat
Engine
Mechanical
45
Install
dash
pot
bracket
and
dash
pot
to
intake
manifold
46
Connect
all
air
vacuum
and
fuel
hoses
and
then
secure
with
clamps
I
Cylinder
block
to
P
C
V
valve
hose
2
A
B
valve
to
E
G
R
passage
vac
uum
hose
3
A
B
valve
to
E
G
R
passage
air
hose
4
Vacuum
tube
to
carburetor
vac
uum
hoses
5
Fuel
ube
to
carburetor
fuel
hose
6
Fuel
tube
to
fuel
pump
fuelhose
7
Distributor
to
vacuum
switch
or
spark
delay
valve
vacuum
hose
8
Air
control
valve
vacuum
hose
9
Check
valve
to
air
control
valve
hose
10
Thermal
vacuum
valve
to
E
G
R
valve
vacuum
hose
I
I
Thermal
vacuum
valve
to
vacuum
tube
hose
47
Install
carburetor
air
cleaner
on
carburetor
and
then
connect
air
and
vacuum
hoses
as
follows
I
Air
cleaner
to
exhaust
manifold
hot
air
duct
2
Air
c1eaner
to
air
pump
hose
3
Air
cleaner
to
rocker
cover
hose
4
Air
cleaner
to
air
control
valve
hose
5
6
48
Install
spark
plugs
in
place
49
Connect
all
distributor
high
ten
sion
cables
to
spark
plugs
50
Install
air
pump
drive
belt
cool
er
compressor
and
idler
pulley
51
Install
left
engine
mounting
bracket
52
Install
clutch
assembly
on
flywheel
with
Clutch
Aligning
Bar
KV30100200
Air
cleaner
to
A
B
valve
hose
Other
vacuum
hoses
Tightening
torque
1
2
to
2
2
kg
m
8
7
to
15
9
ft
lb
EM
26
I
I
KV30100200
EM440
Fig
EM
I07
In
talling
clutch
embly
53
Using
an
overhead
hoist
and
lifting
cable
hoist
engine
away
from
engine
stand
and
then
down
onto
engine
carrier
54
Install
right
engine
mounting
bracket
oil
filter
oil
pressure
switch
oil
level
gauge
and
water
drain
plug
When
installing
oil
filter
fasten
it
to
cylinder
block
by
hand
Note
Do
not
overtighten
flit
or
oil
leakage
may
occur
55
Install
alternator
bracket
adjust
ing
bar
alternator
cooling
fan
and
belt
56
Adjust
the
deflection
of
drive
belts
when
thumb
pressure
is
applied
midway
between
pulleys
A
pressed
force
is
above
10
kg
22
0
lb
Deflection
of
drive
belts
8
to
12
mm
0
315
to
0
472
in
EM613
Fig
EM
lOB
Fan
belt
tension
57
Fill
engine
oil
up
to
specified
level
Page 97 of 537
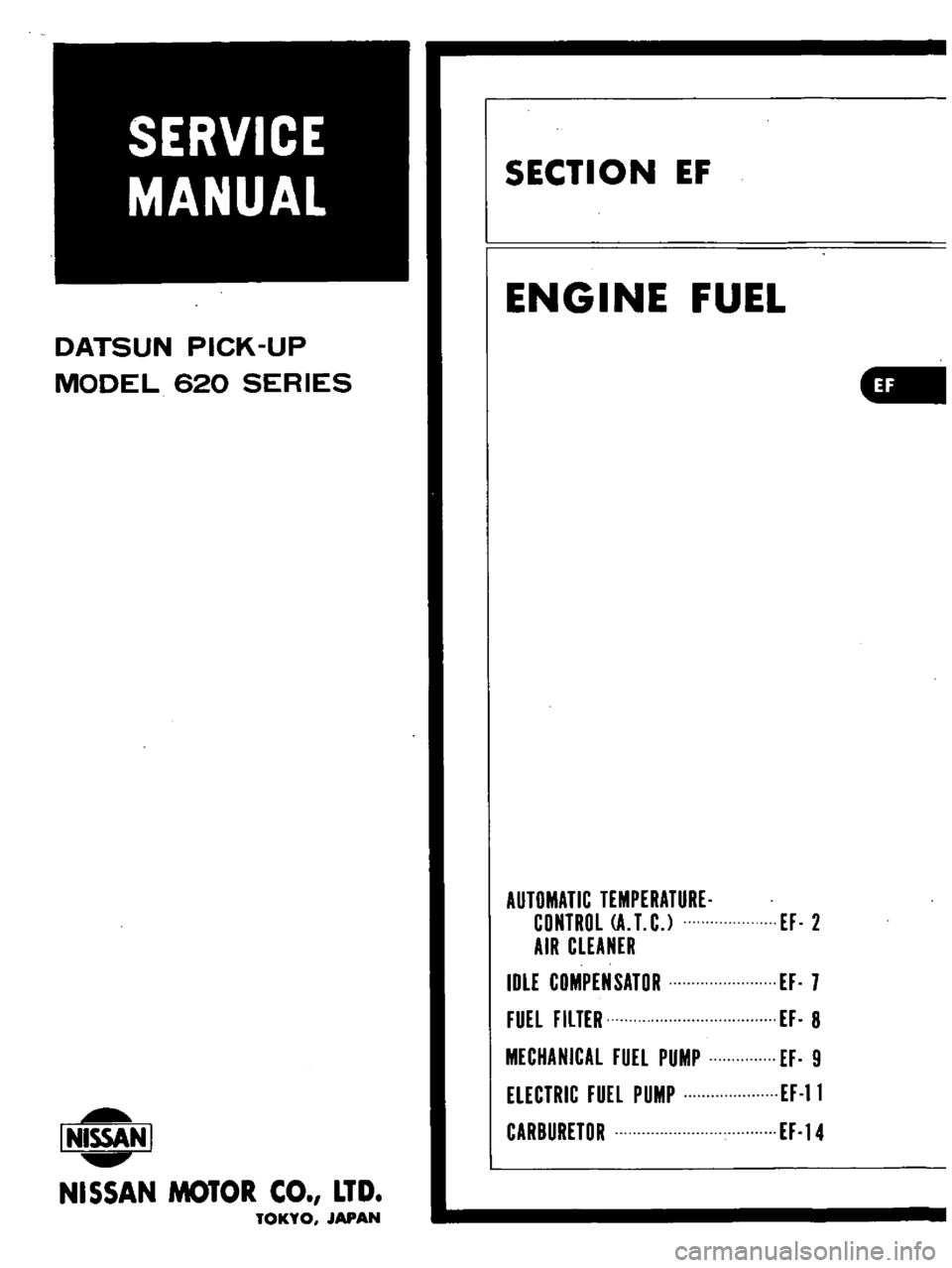
DATSUN
PICK
UP
MODEL
620
SERIES
l
NISSAN
I
NISSAN
MOTOR
CO
LTD
TOKYO
JAPAN
SECTION
EF
ENGINE
FUEL
AUTOMATIC
TEMPERATURE
CONTROL
A
T
C
l
AIR
CLEANER
IDLE
COMPENSATOR
FUEL
FILTER
MECHANICAL
FUEL
PUMP
ELECTRIC
FUEL
PUMP
CARBURETOR
H
2
H
7
H
8
H
9
H
ll
H
14
Page 98 of 537
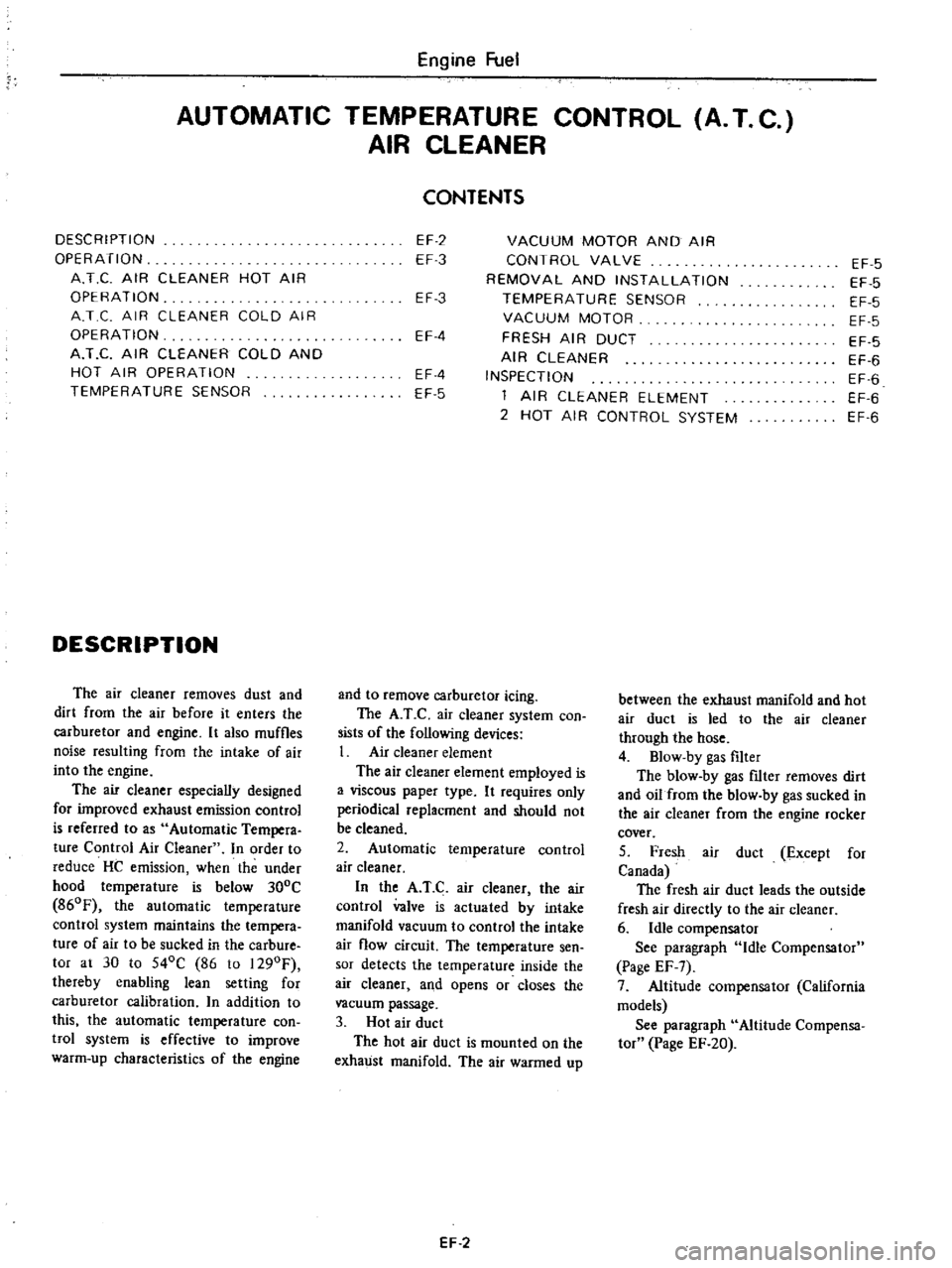
Engine
Fuel
AUTOMATIC
TEMPERATURE
CONTROL
A
T
C
AIR
CLEANER
DESCRIPTION
OPERATION
A
T
C
AIR
CLEANER
HOT
AIR
OPERATION
A
T
C
AIR
CLEANER
COLD
AIR
OPERATION
A
T
C
AIR
CLEANER
COLD
AND
HOT
AIR
OPERATION
TEMPERATURE
SENSOR
DESCRIPTION
The
air
cleaner
removes
dust
and
dirt
from
the
air
before
it
enters
the
carburetor
and
engine
It
also
muffles
noise
resulting
from
the
intake
of
air
into
the
engine
The
air
cleaner
especially
designed
for
improved
exhaust
emission
control
is
referred
to
as
Automatic
Tempera
ture
Control
Air
Cleaner
In
order
to
reduce
HC
emission
when
the
under
hood
temperature
is
below
300C
860F
the
automatic
temperature
control
system
maintains
the
tempera
ture
of
air
to
be
sucked
in
the
carbure
tor
at
30
to
540C
86
to
1290F
thereby
enabling
lean
setting
for
carburetor
calibration
n
addition
to
this
the
automatic
temperature
con
twl
system
is
effective
to
improve
warm
up
characteristics
of
the
engine
CONTENTS
EF
2
EF
3
VACUUM
MOTOR
AND
AIR
CONTROL
VALVE
REMOVAL
AND
INSTALLATION
TEMPERATURE
SENSOR
VACUUM
MOTOR
FRESH
AIR
DUCT
AIR
CLEANER
INSPECTION
1
AIR
CLEANER
ELEMENT
2
HOT
AIR
CONTROL
SYSTEM
EF
3
EF
4
EF
4
EF
5
and
to
remove
carburetor
icing
The
A
T
C
air
cleaner
system
con
sists
of
the
following
devices
1
Air
cleaner
element
The
air
cleaner
element
employed
is
a
viscous
paper
type
It
requires
only
periodical
replacment
and
should
not
be
cleaned
2
Automatic
temperature
control
air
cleaner
In
the
A
T
C
air
cleaner
the
air
control
valve
is
actuated
by
intake
manifold
vacuum
to
control
the
intake
air
flow
circuit
The
temperature
sen
sor
detects
the
temperature
inside
the
air
cleaner
and
opens
or
closes
the
vacuum
passage
3
Hot
air
duct
The
hot
air
duct
is
mounted
on
the
exhaust
manifold
The
air
warmed
up
EF
2
EF
5
EF
5
EF
5
EF
5
EF
5
EF
6
EF
6
EF
6
EF
6
between
the
exhaust
manifold
and
hot
air
duct
is
led
to
the
air
cleaner
through
the
hose
4
Blow
by
gas
filter
The
blow
by
gas
nIter
removes
dirt
and
oil
from
the
blow
by
gas
sucked
in
the
air
cleaner
from
the
engine
rocker
cover
5
Fresh
air
duct
Except
for
Canada
The
fresh
air
duct
leads
the
outside
fresh
air
directly
to
the
air
cleaner
6
Idle
compensator
See
paragraph
Idle
Compensator
Page
EF
7
7
Altitude
compensator
California
models
See
paragraph
Altitude
Compensa
tor
Page
EF
20
Page 104 of 537
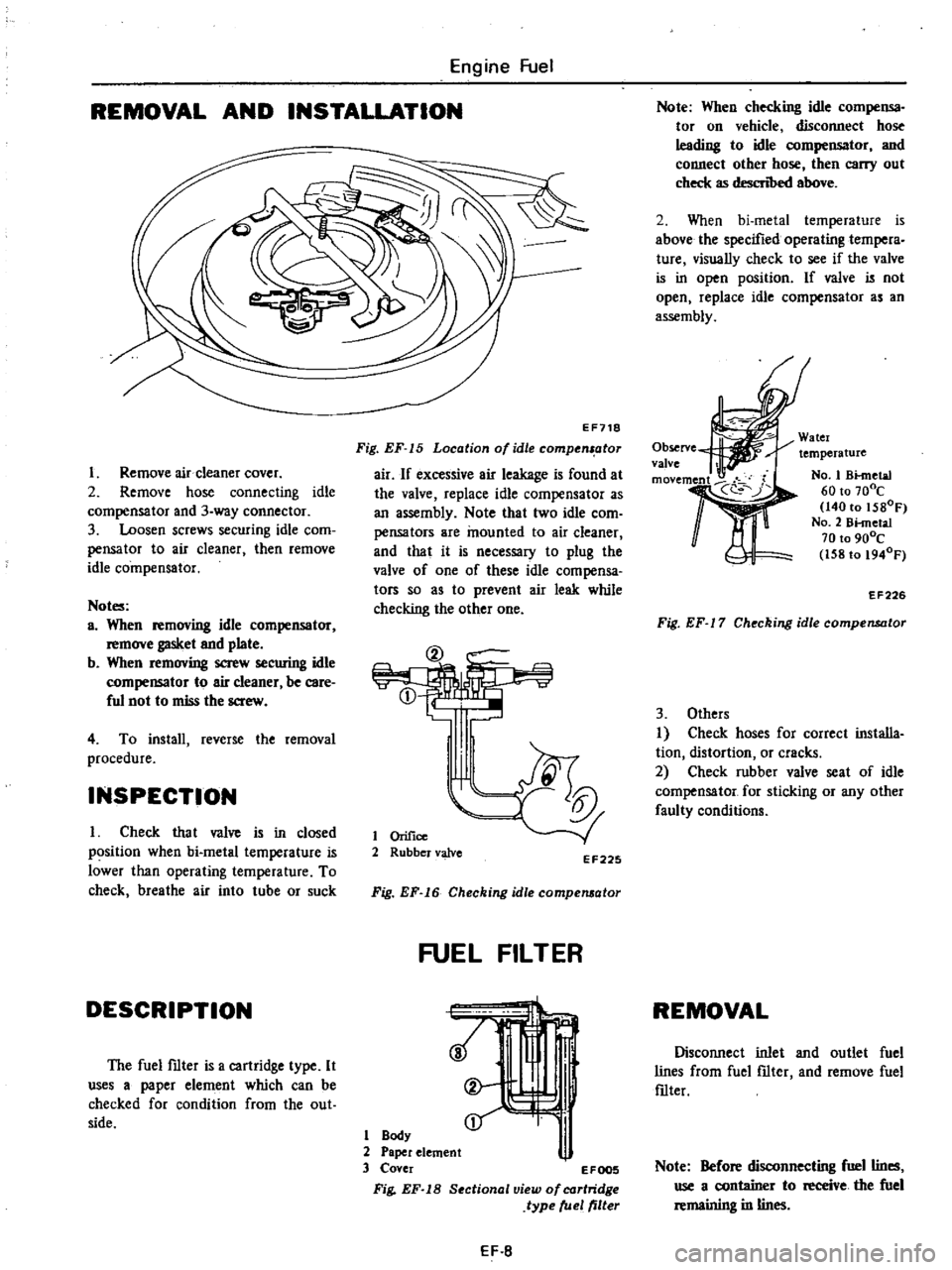
Engine
Fuel
REMOVAL
AND
INSTALLATION
Remove
air
cleaner
cover
2
Remove
hose
connecting
idle
compensator
and
3
way
connector
3
Loosen
screws
securing
idle
com
pensator
to
air
cleaner
then
remove
idle
compensator
Notes
a
When
removing
idle
compensator
remove
gasket
and
plate
b
When
removing
screw
securing
idle
compensator
to
air
cleaner
be
care
ful
not
to
miss
the
saew
4
To
install
reverse
the
removal
procedure
INSPECTION
I
Check
tha
t
valve
IS
m
closed
position
when
bi
metal
temperature
is
lower
than
operating
temperature
To
check
breathe
air
into
tube
or
suck
DESCRIPTION
The
fuel
fJlter
is
a
cartridge
type
It
uses
a
paper
element
which
can
be
checked
for
condition
from
the
out
side
EF718
Fig
EF
15
Location
of
idle
compenl
otor
air
If
excessive
air
leakage
is
found
at
the
valve
replace
idle
compensator
as
an
assembly
Note
that
two
idle
com
pensators
are
mounted
to
air
cleaner
and
that
it
is
necessary
to
plug
the
valve
of
one
of
these
idle
compensa
tors
so
as
to
prevent
air
leak
while
checking
the
other
one
@
CD
I
tl
1
Orifice
2
Rubber
valve
EF225
Fig
EF
16
Checking
idle
compelll
lor
FUEL
FILTER
1
Body
2
Paper
element
3
Cover
1
EFOO5
Fig
EF
18
Sectional
view
of
cartridge
type
fuel
filter
EF
8
Note
When
checking
idle
compensa
tor
on
vehicle
disconnect
hose
leading
to
idle
compensator
and
connect
other
hose
then
carry
out
check
as
descn
bed
above
2
When
bi
metal
temperature
is
above
the
specified
operating
tempera
ture
visually
check
to
see
if
the
valve
is
in
open
position
If
valve
is
not
open
replace
idle
compensator
as
an
assembly
Watcr
temperature
Observe
valve
11t
No
1
Bknctal
60
to
70De
140
to
1580F
NO
2
Bi
metal
70
to
900C
158to
1940F
EF226
Fig
EF
17
Checking
idle
compensator
3
Others
I
Check
hoses
for
correct
installa
tion
distortion
or
cracks
2
Check
rubber
valve
seat
of
idle
compensator
for
sticking
or
any
other
faulty
conditions
REMOVAL
Disconnect
inlet
and
outlet
fuel
lines
from
fuel
fJlter
and
remove
fuel
fJlter
Note
Before
disconnecting
fuel
lines
use
a
container
to
receive
the
fuel
remaining
in
lines