TIMING CHAIN DATSUN PICK-UP 1977 Service Manual
[x] Cancel search | Manufacturer: DATSUN, Model Year: 1977, Model line: PICK-UP, Model: DATSUN PICK-UP 1977Pages: 537, PDF Size: 35.48 MB
Page 43 of 537
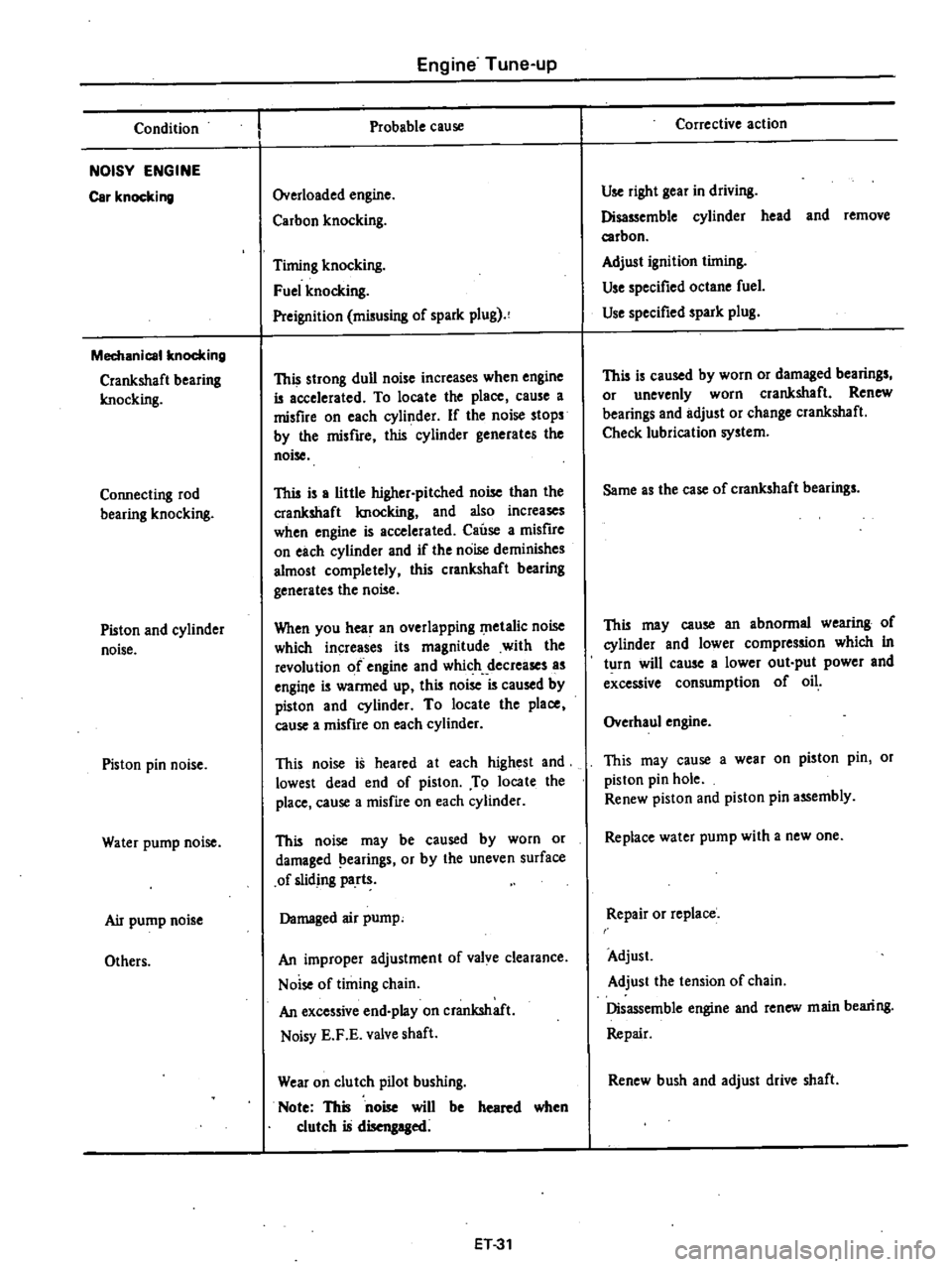
Condition
NOISY
ENGINE
Car
knocking
Mechanical
knocking
Crankshaft
bearing
Imocking
Connecting
rod
bearing
knocking
Piston
and
cylinder
noise
Piston
pin
noise
Water
pump
noise
Air
pump
noise
Others
Engine
Tune
up
Probable
cause
Overloaded
engine
Carbon
knocking
Timing
knocking
Fuel
knocking
Preignition
misusing
of
spark
plug
This
strong
dull
noise
increases
when
engine
is
accelerated
To
locate
the
place
cause
a
misfire
on
each
cylinder
If
the
noise
stops
by
the
misfire
this
cylinder
generates
the
noise
This
is
a
little
higher
pitched
noise
than
the
crankshaft
Imocking
and
also
increases
when
engine
is
accelerated
Cause
a
misfire
on
each
cylinder
and
if
the
noise
deminishes
almost
completely
this
crankshaft
bearing
generates
the
noise
When
you
hear
an
overlapping
metalic
noise
which
increases
its
magnitude
with
the
revolution
of
engine
and
which
decreases
as
engine
is
warmed
up
this
noise
is
caused
by
piston
and
cylinder
To
locate
the
place
cause
a
misfire
on
each
cylinder
This
noise
is
heared
at
each
highest
and
lowest
dead
end
of
piston
To
locate
the
place
cause
a
misfire
on
each
cylinder
This
noise
may
be
caused
by
worn
or
damaged
earings
or
by
the
uneven
surface
of
sliding
parts
Damaged
air
pump
An
improper
adjustment
of
valve
clearance
Noise
of
timing
chain
An
excessive
end
play
on
crankshaft
Noisy
E
F
E
valve
shaft
Wear
on
clutch
pilot
bushing
Note
This
noise
will
be
heared
when
clutch
is
disengaged
ET31
Corrective
action
Use
right
gear
in
driving
Disassemble
cylinder
head
and
remove
carbon
Adjust
ignition
timing
Use
specified
octane
fuel
Use
specified
spark
plug
This
is
caused
by
worn
or
damaged
bearings
or
unevenly
worn
crankshaft
Renew
bearings
and
adjust
or
change
crankshaft
Check
lubrication
system
Same
as
the
case
of
crankshaft
bearings
This
may
cause
an
abnormal
wearing
of
cylinder
and
lower
compression
which
in
turn
will
cause
a
lower
out
put
power
and
excessive
consumption
of
oil
Overhaul
engine
This
may
cause
a
wear
on
piston
pin
or
piston
pin
hole
Renew
piston
and
piston
pin
assembly
Replace
water
pump
with
a
new
one
Repair
or
replace
Adjust
Adjust
the
tension
of
chain
Disassemble
engine
and
renew
main
bearing
Repair
Renew
bush
and
adjust
drive
shaft
Page 44 of 537
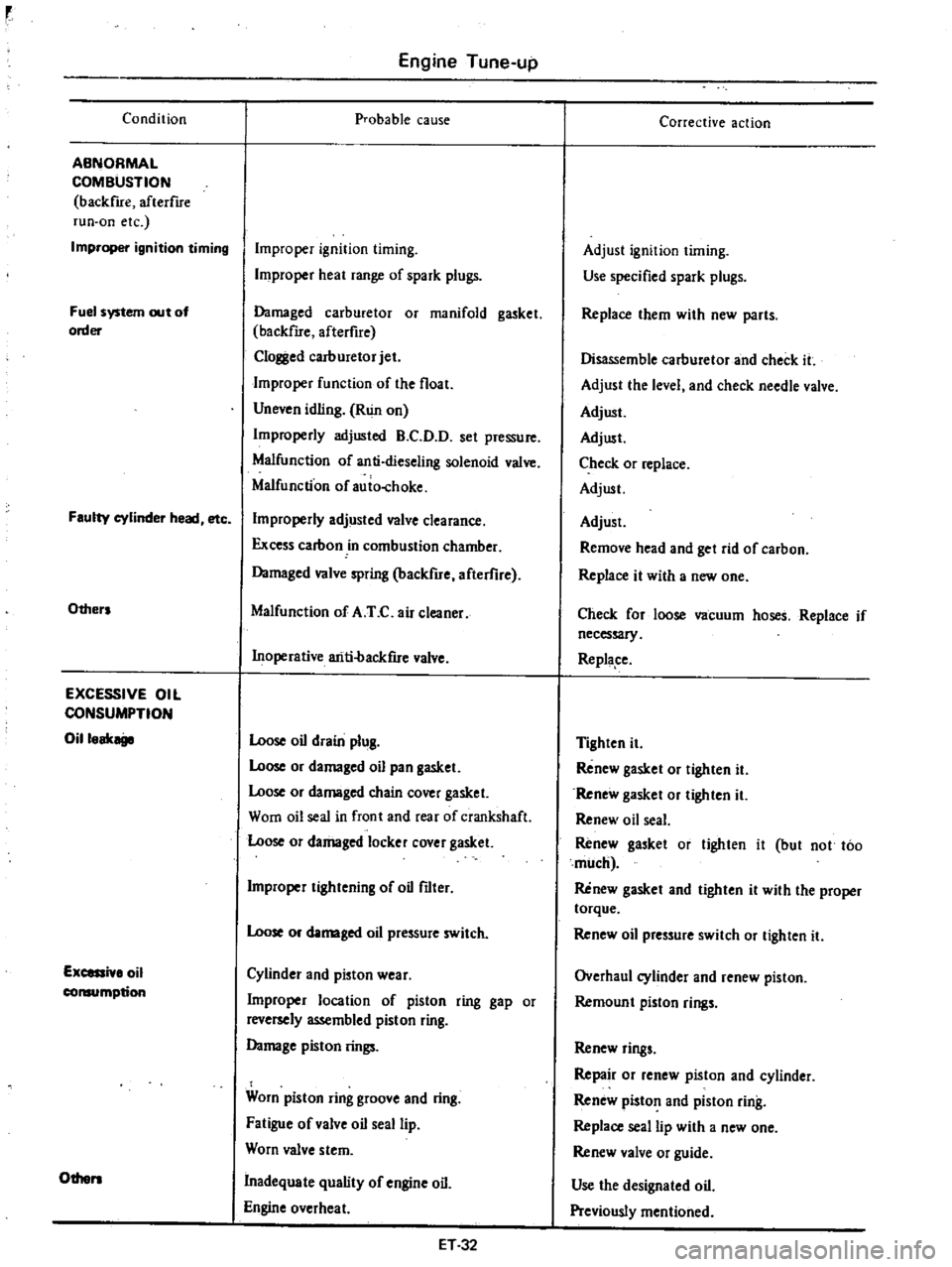
Condition
ABNORMAL
COMBUSTION
backfue
afterflre
run
on
etc
Improper
ignition
timing
Fuel
system
out
of
order
Faulty
cylinder
head
etc
Others
EXCESSIVE
OIL
CONSUMPTION
Oilloak
Excessi
lo
oil
consumption
Others
Engine
Tune
up
probable
cause
Improper
ignition
timing
Improper
heat
range
of
spark
plugs
Damaged
carburetor
or
manifold
gasket
backfue
afterfire
Clol
l
ed
carburetor
jet
Improper
function
of
the
float
Uneven
idling
Run
on
Improperly
adjusted
B
C
D
D
set
pressure
Malfunction
of
anti
dieseling
solenoid
valve
Malfunction
of
auio
choke
Improperly
adjusted
valve
clearance
Excess
carbon
in
combustion
chamber
Damaged
valve
spring
backfire
afterflre
Malfunction
of
A
T
C
air
cleaner
Inoperative
ariti
backfue
valve
Loose
oil
drain
plug
Loose
or
damaged
oil
pan
gasket
Loose
or
damaged
chain
cover
gasket
Worn
oil
seal
in
front
and
rear
of
crankshaft
Loose
or
damaged
locker
cover
gasket
Improper
tightening
of
oil
filter
Loose
or
damaged
oil
pressure
switch
Cylinder
and
pioton
wear
Improper
location
of
piston
ring
gap
or
reversely
assembled
piston
ring
Damage
piston
rings
Worn
piston
ring
groove
and
ring
Fatigue
of
valve
oil
seal
lip
Worn
valve
stem
Inadequate
quality
of
engine
oil
Engine
overheat
ET32
Corrective
action
Adjust
ignition
timing
Use
specified
spark
plugs
Replace
them
with
new
parts
Disassemble
carburetor
and
check
it
Adjust
the
level
and
check
needle
valve
Adjust
Adjust
Check
or
replace
Adjust
Adjust
Remove
head
and
get
rid
of
carbon
Replace
it
with
a
new
one
Check
for
loose
vacuum
hoses
Replace
if
necessary
Replape
Tighten
it
Renew
gasket
or
tighten
it
Renew
gasket
or
tighten
it
Renew
oil
seal
Renew
gasket
or
tighten
it
but
not
too
much
Renew
gasket
and
tighten
it
with
the
proper
torque
Renew
oil
pressure
switch
or
tighten
it
Overhaul
cylinder
and
renew
piston
Remoun
t
piston
rings
Renew
rings
Repair
or
renew
piston
and
cylinder
Renew
piston
and
piston
ring
Replace
seal
lip
with
a
new
one
Renew
valve
or
guide
Use
the
designated
oil
Previously
mentioned
Page 51 of 537
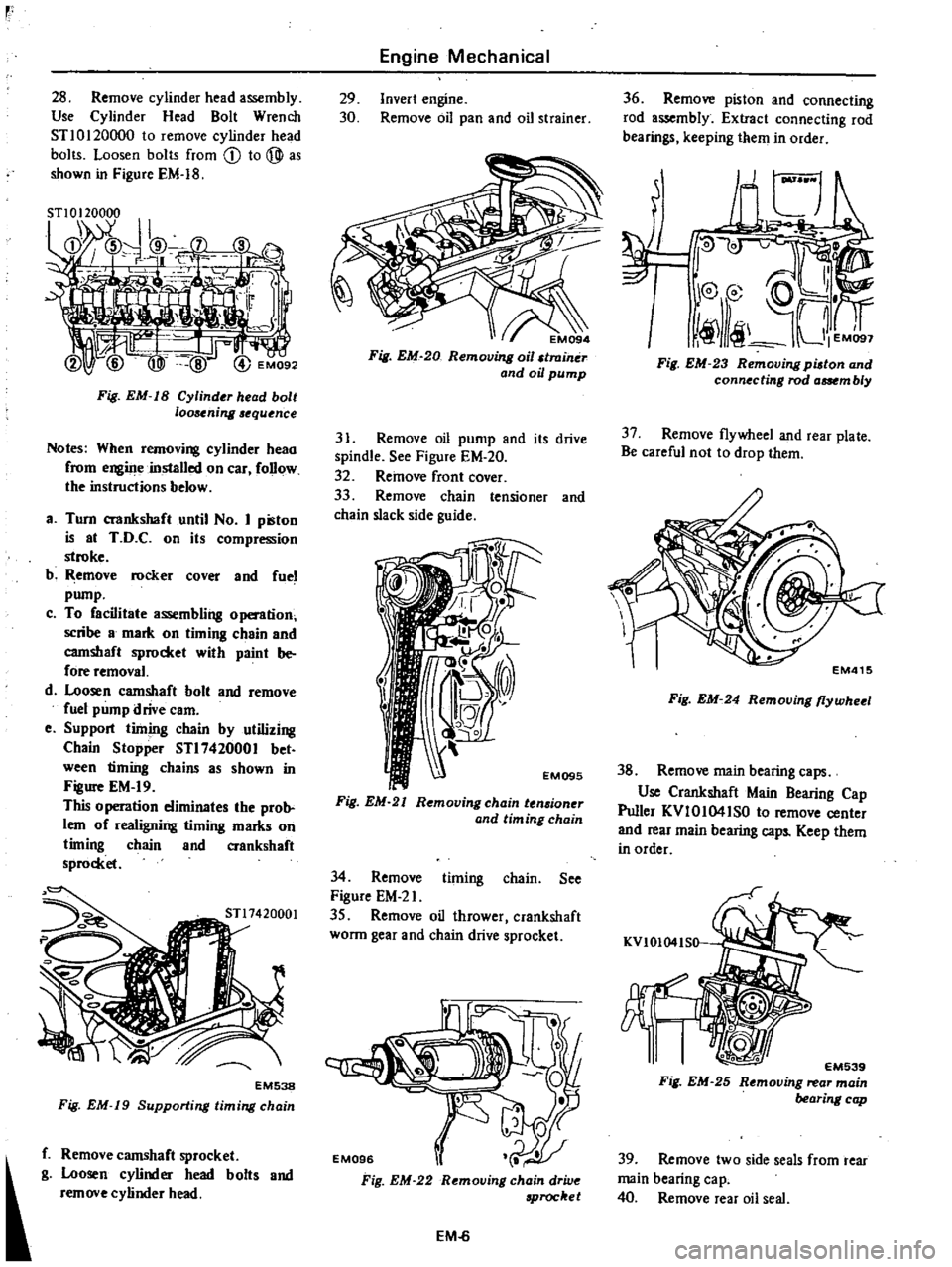
r
28
Remove
cylinder
head
assembly
Use
Cylinder
Head
Bolt
Wrench
STl0120000
to
remove
cylinder
head
bolts
Loosen
bolts
from
CD
to
@
as
shown
in
Figure
EM
18
Fig
EM
IS
Cylinder
head
bolt
loosening
equence
Notes
When
removing
cylinder
heao
from
engiJJe
installed
on
car
follow
the
instructions
below
a
Turn
crankshaft
until
No
I
pilton
is
at
T
D
C
on
its
compression
stroke
b
Remove
rocker
Cover
and
fuel
pump
c
To
facilitate
assembling
o
tion
scribe
8
mark
on
timing
c
8in
and
camshaft
sprocket
with
paint
be
fore
removal
d
Loosen
camshaft
bolt
and
remove
fuel
pump
drive
earn
e
Support
timing
chain
by
utilizing
Chain
Stopper
STl7420001
bet
ween
timiilg
chains
as
shown
in
Figure
EM
19
This
0
peration
eliminates
the
prob
lem
of
realigning
timing
marks
on
timing
chain
and
crankshaft
sprocket
EM538
Fig
EM
19
Supporting
timing
chain
f
Remove
camshaft
sprocket
g
Loosen
cylinder
head
bolts
and
remove
cylinder
head
Engine
Mechanical
29
Invert
engine
30
Remove
oil
pan
and
oil
strainer
EM094
Fig
EM
20
Removing
oil
traintir
and
oil
pump
31
Remove
oil
pump
and
its
drive
spindle
See
Figure
EM
20
32
Remove
front
cover
33
Remove
chain
tensioner
and
chain
slack
side
guide
EM095
Fig
EM
21
Removing
chain
ten
ioner
and
tim
ing
chain
34
Remove
timing
chain
See
Figure
EM
2l
35
Remove
oil
thrower
crankshaft
wonn
gear
and
chain
drive
sprocket
Fig
EM
22
Removing
chain
drive
Proc
et
EM
6
36
Remove
piston
and
connecting
rod
a
mbly
Extract
connecting
rod
bearings
keeping
them
in
order
I
Fig
EM
23
Removing
pilton
and
connecting
rod
aat
m
b
y
37
Remove
flywheel
and
rear
plate
Be
careful
not
to
drop
them
EM415
Fig
EM
24
Removing
flywheel
38
Remove
main
bearing
caps
Use
Crankshaft
Main
Bearing
Cap
Puller
KVIOI04ISO
to
remove
center
and
rear
main
bearing
caps
Keep
them
in
order
KVIOI04IS0
EM539
Fig
EM
25
Removing
rear
main
bearing
cap
39
Remove
two
side
seals
from
rear
main
bearing
ca
p
40
Remove
rear
oil
seal
Page 53 of 537
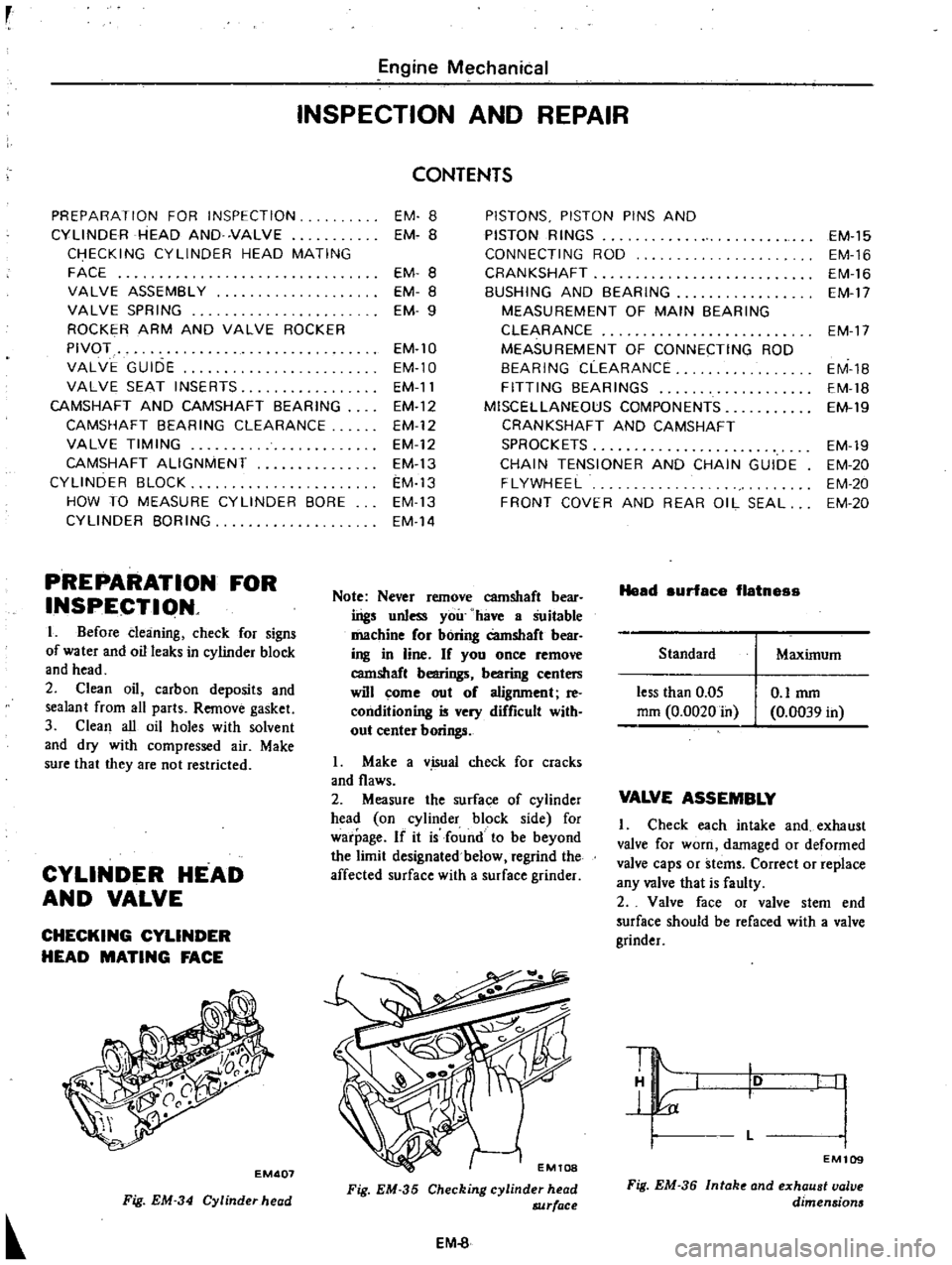
r
Engine
Mechanical
INSPECTION
AND
REPAIR
PREPARATION
FOR
INSPECTION
CYLINDER
HEAD
AND
VALVE
CHECKING
CYLINDER
HEAD
MATING
FACE
VALVE
ASSEMBLY
VALVE
SPRING
ROCKER
ARM
AND
VALVE
ROCKER
PIVOT
VALVE
GUIDE
VALVE
SEAT
INSERTS
CAMSHAFT
AND
CAMSHAFT
BEARING
CAMSHAFT
BEARING
CLEARANCE
VALVE
TIMING
CAMSHAFT
ALIGNMENT
CYLINDER
BLOCK
HOW
TO
MEASURE
CYLINDER
BORE
CYLINDER
BORING
PREPARATION
FOR
INSPECTI
N
I
Before
cleaning
check
for
signs
of
water
and
oil
leaks
in
cylinder
block
and
head
2
Clean
oil
carbon
deposits
and
sealant
from
an
parts
Remove
gasket
3
Clean
all
oil
holes
with
solvent
and
dry
with
compressed
air
Make
sure
that
they
are
not
restricted
CYLINDER
HEAD
AND
VALVE
CHECKING
CYLINDER
HEAD
MATING
FACE
EM407
Fig
EM
34
Cylinder
head
CONTENTS
EM
8
EM
B
EM
8
EM
8
EM
9
EM
lO
EM
l0
EM
11
EM
12
EM
12
EM
12
EM
13
EM
13
EM
13
EM
14
PISTONS
PISTON
PINS
AND
PISTON
RINGS
CONNECTING
ROD
CRANKSHAFT
BUSHING
AND
BEARING
MEASUREMENT
OF
MAIN
BEARING
CLEARANCE
MEASUREMENT
OF
CONNECTING
ROD
BEARING
CLEARANCE
FITTING
BEARINGS
MISCELLANEOUS
COMPONENTS
CRANKSHAFT
AND
CAMSHAFT
SPROCKETS
CHAIN
TENSIONER
AND
CHAIN
GUIDE
FLYWHEEL
FRONT
COVER
AND
REAR
OIL
SEAL
Note
Never
remove
camshaft
bear
ings
unless
you
have
a
Suitable
machine
or
boring
Camshaft
bear
ing
in
line
If
you
once
remove
camshaft
bearings
bearing
centers
will
come
out
o
alignment
reo
conditioning
is
very
difficult
with
out
center
borings
L
Make
a
v
isual
check
for
cracks
and
flaws
2
Measure
the
surface
of
cylinder
head
on
cylinder
block
side
for
warpage
If
it
is
found
to
be
beyond
the
limit
designated
below
regrind
the
affected
surface
with
a
surface
grinder
Fig
EM
35
Checking
cylinder
head
8JJrface
EM
8
Head
surface
flatnes
Standard
less
than
0
05
mm
0
0020
in
O
lmm
0
0039
in
EM
15
EM
16
EM
16
EM
17
EM
17
EM
1B
EM
18
EM
19
EM
19
EM
20
EM
20
EM
20
Maximum
VALVE
ASSEMBLY
Check
each
intake
and
exhaust
valve
for
worn
damaged
or
deformed
valve
caps
or
stems
Correct
or
replace
any
valve
that
is
faulty
2
Valve
face
or
valve
stem
end
surface
should
be
refaced
with
a
valve
grinder
10
L
I
I
I
EM109
Fig
EM
36
Intak
and
exhaust
valve
dimensions
Page 64 of 537
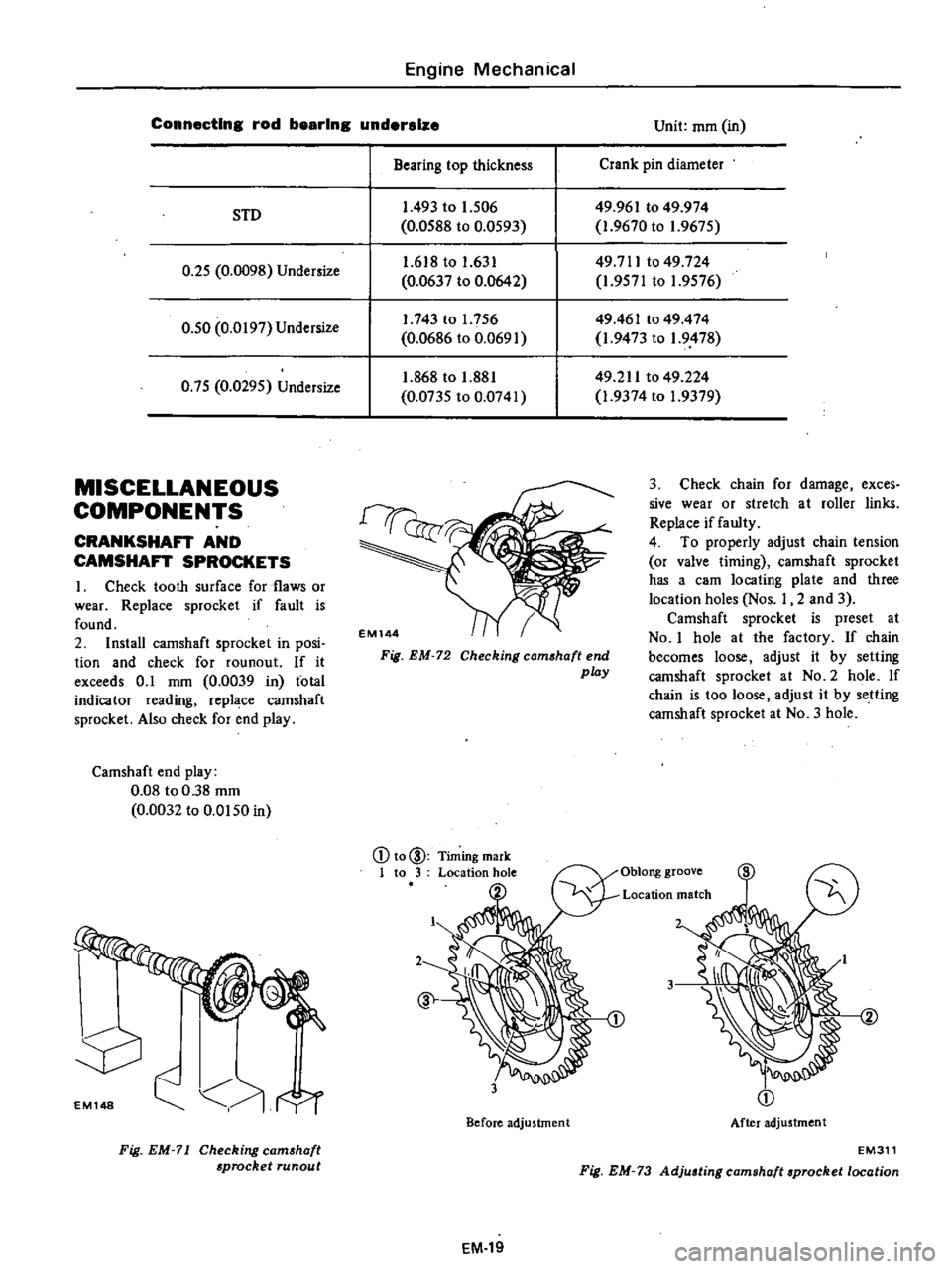
Engine
Mechanical
Connectlns
rod
be
rlns
undersize
SID
0
25
0
0098
Undersize
0
50
0
0197
Undersize
0
75
0
0295
Undersize
MISCELLANEOUS
COMPONENTS
CRANKSHA
AND
CAMSHA
SPROCKETS
I
Check
tooth
surface
for
flaws
or
wear
Replace
sprocket
if
fault
is
found
2
Install
camshaft
sprocket
in
posi
tion
and
check
for
rounout
If
it
exceeds
0
1
mm
0
0039
in
total
indicator
reading
repl
ce
camshaft
sprocket
Also
check
for
end
play
Camshaft
end
play
0
08
to
0
38
mm
0
0032
to
0
0150
in
EMl48
Fig
EM
71
Checking
eam
haft
sprocket
Tunaut
Unit
mm
in
Bearing
top
thickness
Crank
pin
diameter
1
493
to
1
506
0
0588
to
0
0593
49
961
to
49
974
1
9670
to
1
9675
49711
to
49
724
1
9571
to
1
9576
1
618
to
1
631
0
0637
to
0
0642
1
743
to
1
756
0
0686
to
0
0691
49461
to
49
474
1
9473
to
1
9478
1
868
to
1
881
0
0735
to
0
0741
49
211
to
49
224
1
9374
to
1
9379
Fig
EM
72
Checking
camshaft
end
play
3
Check
chain
for
damage
exces
sive
wear
or
stretch
at
roller
links
Replace
if
faulty
4
To
properly
adjust
chain
tension
or
valve
timing
camshaft
sprocket
has
a
earn
locating
plate
and
three
location
holes
Nos
I
2
and
3
Camshaft
sprocket
is
preset
at
No
I
hole
at
the
factory
If
chain
becomes
loose
adjust
it
by
setting
camshaft
sprocket
at
NO
2
hole
If
chain
is
too
loose
adjust
it
by
setting
camshaft
sprocket
at
No
3
hole
2
3
Before
adjustment
Location
match
3
After
adju5tmen
t
EM311
Fig
EM
73
Adjuating
camshaft
aprocket
location
EM
19
Page 65 of 537
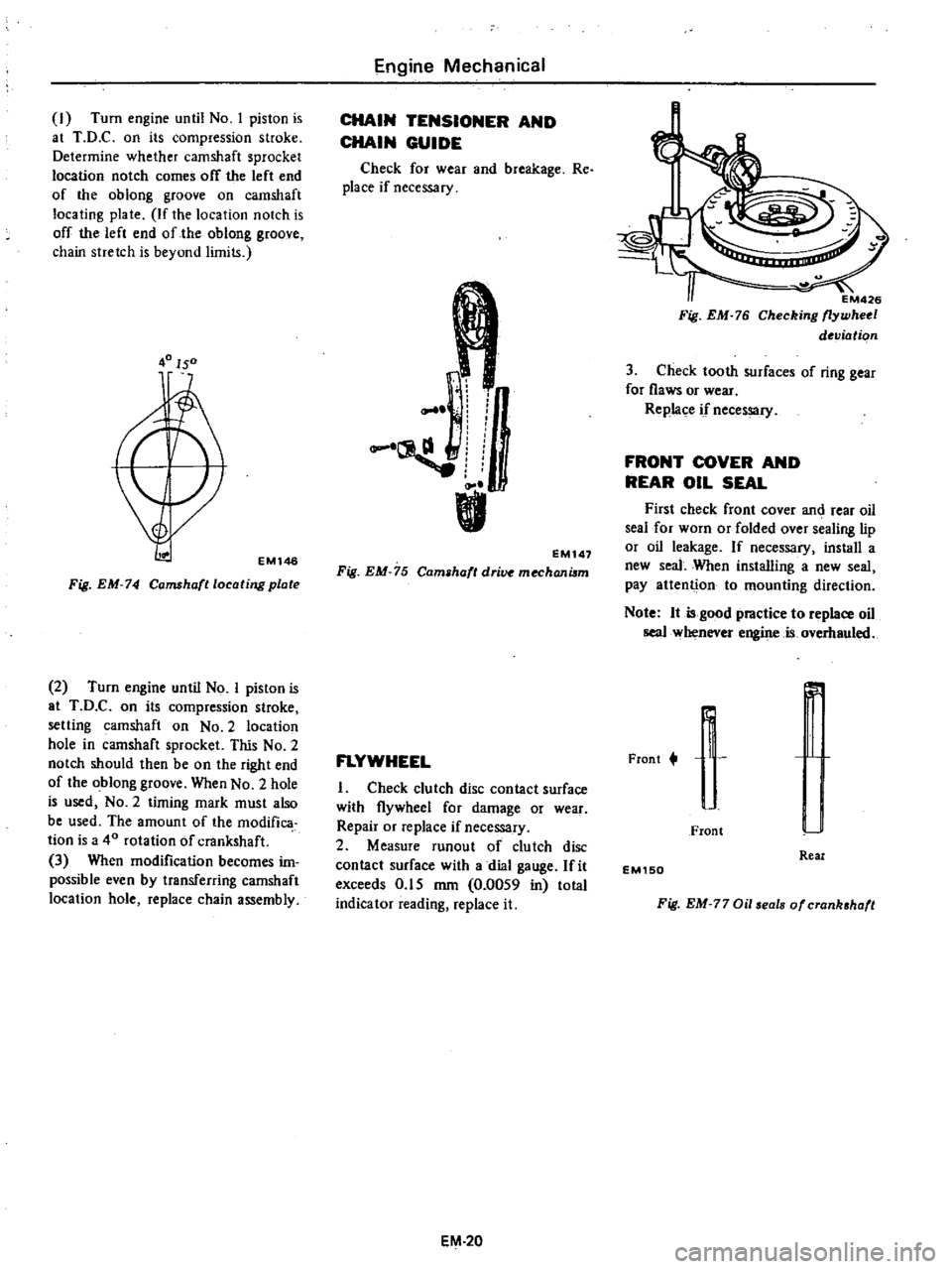
I
Turn
engine
until
No
I
piston
is
at
T
D
C
on
its
compression
stroke
Determine
whether
camshaft
sprocket
location
notch
comes
off
the
left
end
of
the
oblong
groove
on
camshaft
locating
plate
If
the
location
notch
is
off
the
left
end
of
the
oblong
groove
chain
stretch
is
beyond
limits
40150
EMl46
Fig
EM
74
Camshafllocating
plate
2
Turn
engine
until
No
I
piston
is
at
T
D
C
on
its
compression
stroke
setting
camshaft
on
No
2
location
hole
in
camshaft
sprocket
This
No
2
notch
should
then
be
on
the
right
end
of
the
oblong
groove
When
No
2
hole
is
used
NO
2
timing
mark
must
also
be
used
The
amount
of
the
modifica
tion
is
a
40
rotation
of
crankshaft
3
When
modification
becomes
im
possible
even
by
transferring
camshaft
location
hole
replace
chain
assembly
Engine
Mechanical
CHAIN
TENSIONER
AND
CHAIN
GUIDE
Check
for
wear
and
breakage
Re
place
if
necessary
r
I
L
EM147
Fig
EM
75
Cam
haft
dri
mechanilm
FLYWHEEL
I
Check
clutch
disc
contact
surface
with
flywheel
for
damage
or
wear
Repair
or
replace
if
necessary
2
Measure
runout
of
clutch
disc
contact
surface
with
a
dial
gauge
fit
exceeds
0
15
mm
0
0059
in
total
indicator
reading
replace
it
EM
20
EM426
Fig
EM
76
Checking
flywheel
deviation
3
Check
tooth
surfaces
of
ring
gear
for
flaws
or
wear
Replace
if
necessary
FRONT
COVER
AND
REAR
OIL
SEAL
First
check
front
cover
an
rear
oil
seal
for
worn
or
folded
over
sealing
lip
or
oil
leakage
If
necessary
install
a
new
seal
When
installing
a
new
seal
pay
attenti
on
to
mounting
direction
Note
It
is
good
practice
to
replace
oil
seal
whenever
engine
is
overhauled
Frant
t
r
r
J
I
Front
Real
EM150
Fig
EM
77
Oil
eals
of
crank
haft
Page 69 of 537
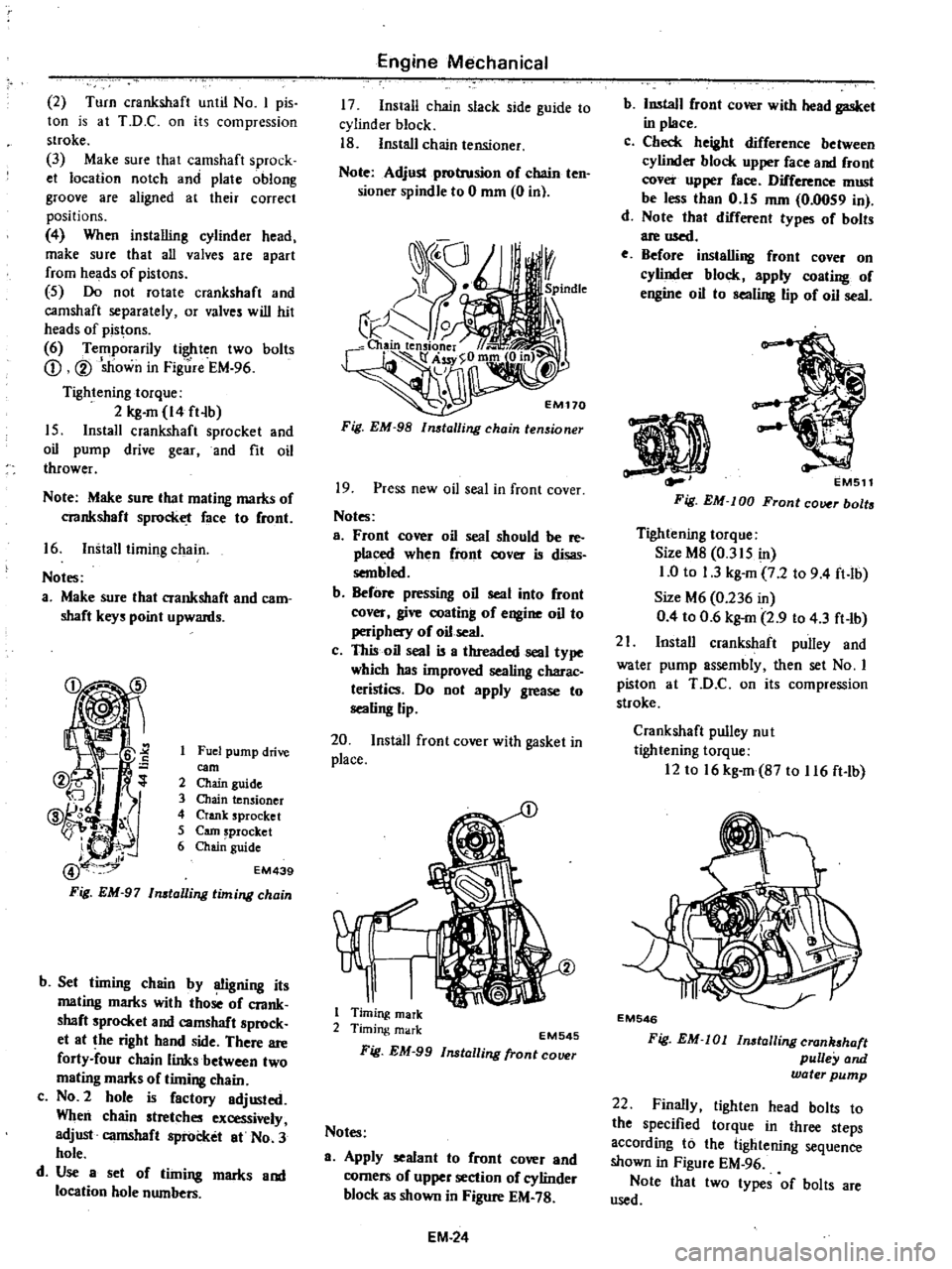
2
Turn
crankshaft
until
No
I
pis
ton
is
at
T
D
C
on
its
compression
stroke
3
Make
sure
thai
camshaft
sprock
et
location
notch
and
plate
oblong
groove
are
aligned
at
their
correct
positions
4
When
installing
cylinder
head
make
sure
that
all
valves
are
apart
from
heads
of
pistons
5
Do
not
rotate
crankshaft
and
camshaft
separately
or
valves
will
hit
heads
of
pistons
6
Temporarily
tighten
two
bolts
CD
V
sJiown
in
Fig
re
EM
96
Tightening
torque
2
kg
m
14
ft
b
15
Install
crankshaft
sprocket
and
oil
pump
drive
gear
and
fit
oil
thrower
Note
Make
sure
lhat
maling
marks
of
crankshaft
sprocket
face
10
Cront
16
Install
timing
chain
Noles
a
Make
sure
that
crankshaft
and
cam
shaft
keys
point
upwards
Fuel
pump
drive
earn
2
Chain
guide
3
Chain
tensioner
4
Crank
sprocket
5
earn
sprocket
6
Chai
guide
EM439
b
Set
timing
chain
by
OOgning
its
mating
marks
with
those
oC
crank
shaft
sprocket
and
camshaft
sprock
et
at
the
right
hand
side
There
are
forty
four
chain
links
between
two
mating
marks
of
timing
chain
c
NO
2
hole
is
Cactory
adjusted
When
chain
stretches
excessively
adjust
camshaft
sprocket
at
No
3
hole
d
Use
a
set
of
timing
marks
and
location
hole
numbers
Engine
Mechanical
17
Install
chain
slack
side
guide
to
cylinder
block
18
Install
chain
tensioner
Note
Adjust
protrusion
oC
chain
ten
sioner
spindle
to
0
mm
0
in
Fig
EM
98
lmtalling
chain
tensioner
19
Press
new
oil
seal
in
front
cover
Notes
a
Front
cover
oil
seal
should
be
reo
placed
when
Cront
cover
is
disas
sembled
b
BeCore
pressing
oil
seal
into
Cront
cover
give
coating
of
engine
oil
to
periphery
of
oil
seal
c
This
oil
seal
is
a
threaded
seal
type
which
has
improved
sealing
charac
teristics
Do
not
apply
grease
to
sealing
lip
20
Install
front
cover
with
gasket
in
place
1
Timing
mark
2
Timing
mark
EM545
Fig
EM
99
Installing
fronl
COlHlr
Notes
a
Apply
sealant
to
Cront
cover
and
corners
oC
upper
section
of
cylinder
block
as
shown
in
Figure
EM
78
EM
24
b
Install
Cront
cover
with
head
gasket
in
place
c
Check
height
diCCerence
between
cylinder
block
upper
Cace
and
Cront
cover
upper
Cace
DifCerence
must
be
less
than
0
15
mm
0
0059
in
d
Note
that
difCerent
types
oC
bolts
are
used
e
Before
installing
front
cover
on
cylinder
block
apply
coating
oC
engine
oil
10
sealing
lip
of
oil
seal
EMS11
Fig
EM
lOD
Front
cover
bolts
Tightening
torque
Size
M8
0
315
in
1
0
to
1
3
kg
m
7
2
to
9
4
ft
lb
Size
M6
0
236
in
0
4
to
0
6
kg
m
2
9
to
4
3
ft
lb
21
Install
crankshaft
pulley
and
water
pump
assembly
then
set
No
I
piston
at
ToO
C
on
its
compression
stloke
Crankshaft
pulley
nu
I
tightening
torque
12
to
16
kg
m
B7
to
116
ft
lb
EM546
Fig
EM
Ol
lnstallingcran
haft
pulley
and
water
pump
22
Finally
tighten
head
bolts
to
the
specified
torque
in
three
steps
according
to
the
lightening
sequence
shown
in
Figure
EM
96
Note
thai
Iwo
types
of
bolts
are
used
Page 73 of 537
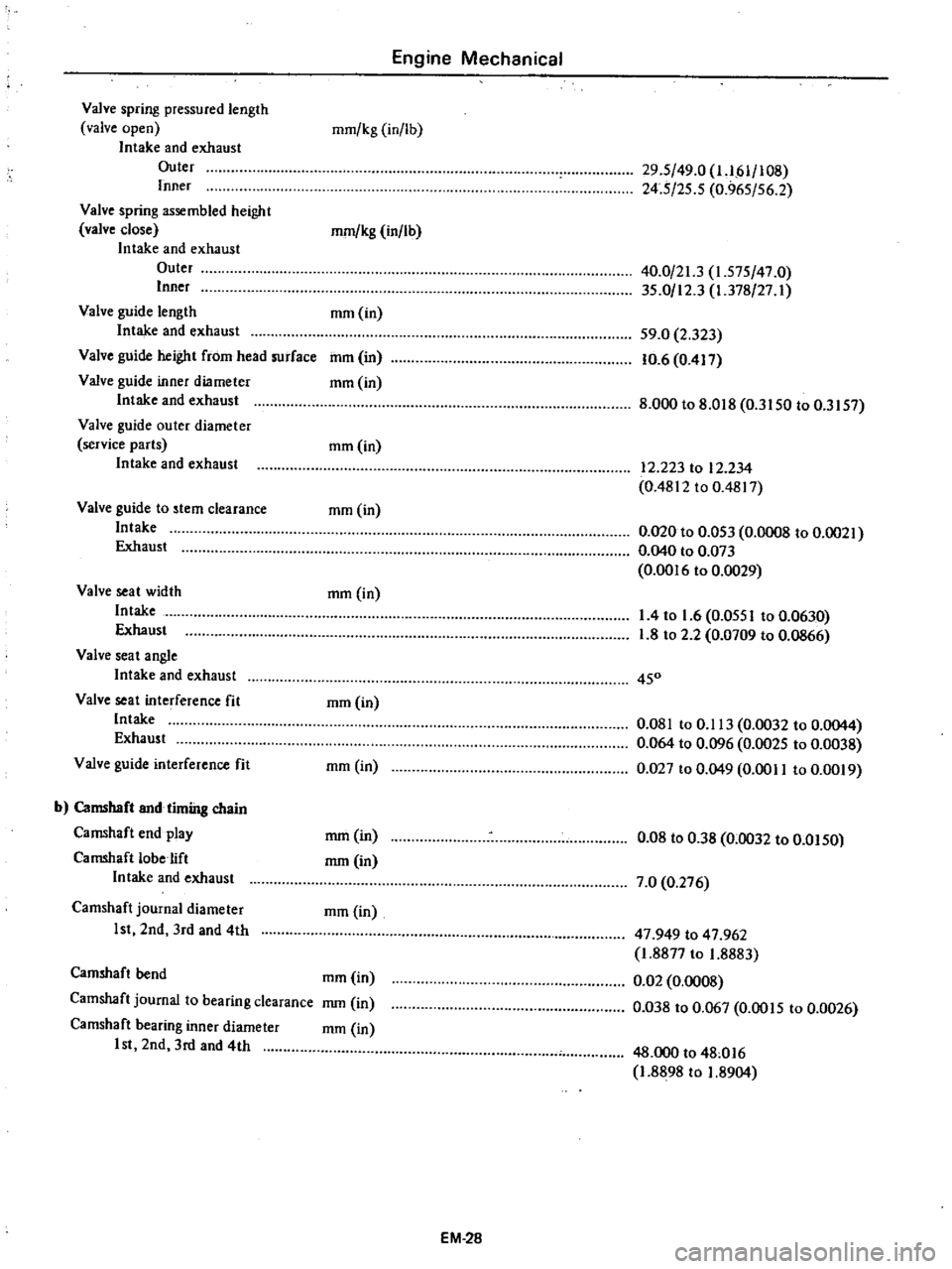
Valve
spring
pressured
length
valve
open
Intake
and
exhaust
Outer
Inner
Valve
spring
assembled
height
valve
close
Intake
and
exhaust
Outer
Inner
Valve
guide
length
Intake
and
exhaust
Valve
guide
height
from
head
surface
Valve
guide
inner
diameter
Intake
and
exhaust
Valve
guide
outer
diameter
service
parts
Intake
and
exhaust
Valve
guide
to
stem
clearance
Intake
Exhaust
Valve
seat
width
Intake
Exhaust
Valve
seat
angle
Intake
and
exhaust
Valve
seat
interference
fit
Intake
Exhaust
Valve
guide
interference
fit
b
Camshaft
and
timing
chain
Camshaft
end
play
Camshaft
lobe
ift
Intake
and
exhaust
Camshaft
joumal
diameter
1st
2nd
3rd
and
4th
Engine
Mechanical
mm
kg
in
lb
mm
kg
in
lb
mm
in
mIll
in
mm
in
mm
in
mm
in
mm
in
mm
in
mm
in
rnm
in
rnm
in
mm
in
Camshaft
bend
mm
in
Camshaft
journal
to
bearing
clearance
mm
in
Camshaft
bearing
inner
diameter
rnm
in
1st
2nd
3rd
and
4th
29
5
49
0
1
IM
108
24
5
25
5
0
965
56
2
40
0
21
3
1
575
47
0
35
0
12
3
1
378
27
I
59
0
2
323
10
6
0
417
8
000
to
8
018
0
3150
to
0
3157
12
223
to
12
234
0
4812
to
0
4817
0
020
to
0
053
0
0008
to
0
0021
0
040
to
0
073
0
0016
to
0
0029
1
4
to
1
6
0
0551
to
0
0630
1
8
to
2
2
0
0709
to
0
0866
450
0
081
to
0
113
0
0032
to
0
0044
0
064
to
0
096
0
0025
to
0
0038
0
027
to
0
049
0
0011
to
0
0019
0
08
to
038
0
0032
to
0
0150
7
0
0
276
47
949
to
47
962
1
8877
to
1
8883
0
02
0
0008
0
Q38
to
0
067
0
00
I
5
to
0
0026
48
000
to
48
016
1
8898
to
1
8904
EM
28
Page 76 of 537
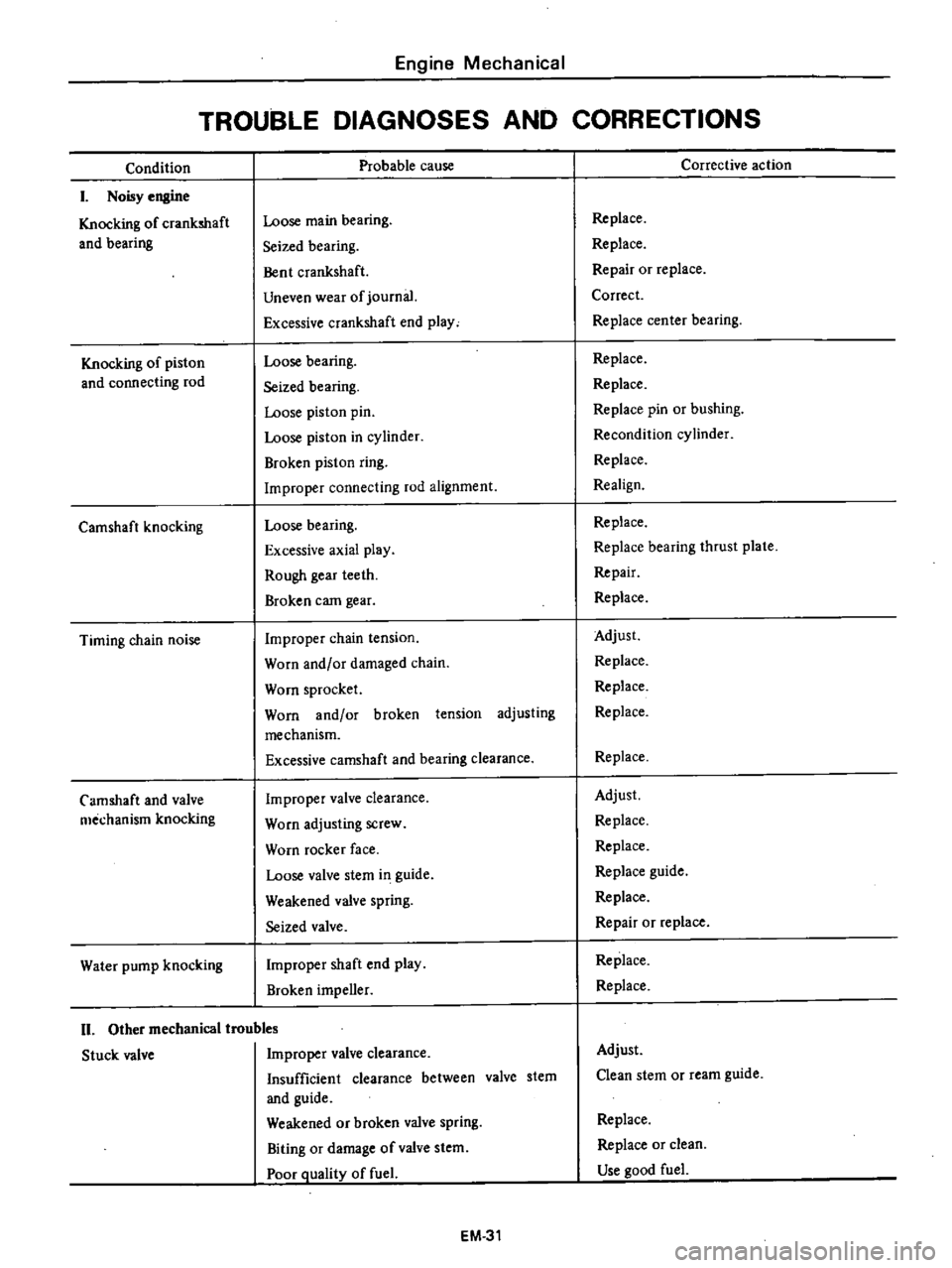
Engine
Mechanical
TROUBLE
DIAGNOSES
AND
CORRECTIONS
Condition
I
Noisy
engine
Knocking
of
crankshaft
and
bearing
Knocking
of
piston
and
connecting
rod
Camshaft
knocking
Timing
chain
noise
Camshaft
and
valve
mechanism
knocking
Water
pump
knocking
Probable
cause
Loose
main
bearing
Seized
bearing
Bent
crankshaft
Uneven
wear
of
journal
Excessive
crankshaft
end
play
Loose
bearing
Seized
bearing
Loose
piston
pin
Loose
piston
in
cylinder
Broken
piston
ring
Improper
connecting
rod
alignment
Loose
bearing
Excessive
axial
play
Rough
gear
teeth
Broken
eam
gear
Improper
chain
tension
Worn
and
or
damaged
chain
Worn
sprocket
Worn
and
or
broken
tension
adjusting
mechanism
Excessive
camshaft
and
bearing
clearance
Improper
valve
clearance
Worn
adjusting
screw
Worn
rocker
face
Loose
valve
stem
i1
1
guide
Weakened
valve
spring
Seized
valve
Improper
shaft
end
play
Broken
impeller
II
Other
mechanical
troubles
Stuck
valve
Improper
valve
clearance
Insufficient
clearance
between
valve
stem
and
guide
Weakened
or
broken
valve
spring
Biting
or
damage
of
valve
stem
Poor
Quality
of
fuel
EM
31
Corrective
action
Replace
Replace
Repair
or
replace
Correct
Replace
cen
ter
bearing
Replace
Replace
Replace
pin
or
bushing
Recondition
cylinder
Replace
Realign
Replace
Replace
bearing
thrust
plate
Repair
Replace
Adjust
Replace
Replace
Replace
Replace
Adjust
Replace
Replace
Replace
guide
Replace
Repair
or
replace
Replace
Replace
Adjust
Clean
stem
or
ream
guide
Replace
Replace
or
clean
Use
ood
fuel
Page 85 of 537
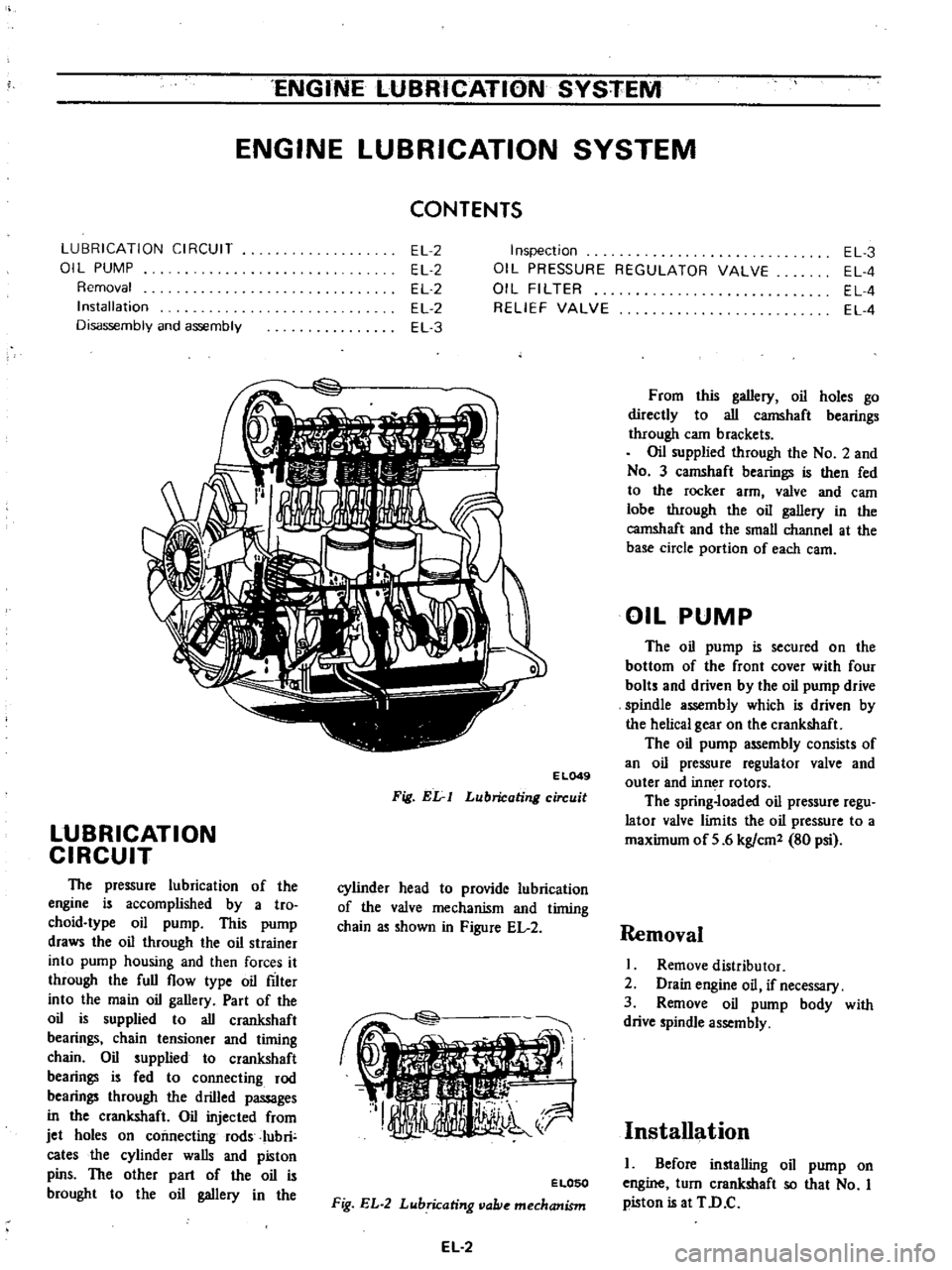
ENGINE
LUBRICATION
SYSTEM
ENGINE
LUBRICATION
SYSTEM
CONTENTS
LUBRICATION
CIRCUIT
01
L
PUMP
Removal
Installation
Disassembly
and
assembly
EL
2
EL
2
EL
2
EL
2
EL
3
Inspection
OIL
PRESSURE
REGULATOR
VALVE
OIL
FILTER
RELIEF
VALVE
EL
3
EL
4
EL
4
EL
4
E
L049
Fig
Elr
I
Lubricating
circuit
LUBRICATION
CIRCUIT
The
pressure
lubrication
of
the
engine
is
accomplished
by
a
tro
choid
type
oil
pump
This
pump
draws
the
oil
through
the
oil
strainer
into
pump
housing
and
then
forces
it
through
the
full
flow
type
oil
filter
into
the
main
oil
gallery
Part
of
the
oil
is
supplied
to
all
crankshaft
bearings
chain
tensioner
and
timing
chain
Oil
supplied
to
crankshaft
bearings
is
fed
to
connecting
rod
bearings
through
the
drilled
passages
in
the
crankshaft
Oil
injected
from
jet
holes
on
connecting
rods
Iubri
cates
the
cylinder
walls
and
piston
pins
The
other
part
of
the
oil
is
brought
to
the
oil
gallery
in
the
cylinder
head
to
provide
lubrication
of
the
valve
mechanism
and
timing
chain
as
shown
in
Figure
EL
2
ELOSO
Fig
EL
2
Lubricating
vallie
mechanism
EL
2
From
this
gallery
oil
holes
go
directly
to
all
camshaft
bearings
through
cam
brackets
Oil
supplied
through
the
No
2
and
No
3
camshaft
bearings
is
then
fed
to
the
rocker
arm
valve
and
eam
lobe
through
the
oil
gallery
in
the
camshaft
and
the
small
channel
at
the
base
circle
portion
of
each
earn
OIL
PUMP
The
oil
pump
is
secured
on
the
bottom
of
the
front
cover
with
four
bolts
and
driven
by
the
oil
pump
drive
spindle
assembly
which
is
driven
by
the
helical
gear
on
the
crankshaft
The
oil
pump
assembly
consists
of
an
oil
pressure
regulator
valve
and
outer
and
inn
r
rotors
The
spring
loaded
oil
pressure
regu
lator
valve
limits
the
oil
pressure
to
a
maximum
of
5
6
kg
em
80
psi
Removal
I
Remove
distributor
2
Drain
engine
oil
if
necessary
3
Remove
oil
pump
body
with
drive
spindle
assembly
Installation
I
Before
installing
oil
pump
on
engine
turn
crankshaft
so
that
No
I
piston
is
at
TD
C