engine DODGE RAM 1500 1998 2.G Workshop Manual
[x] Cancel search | Manufacturer: DODGE, Model Year: 1998, Model line: RAM 1500, Model: DODGE RAM 1500 1998 2.GPages: 2627
Page 567 of 2627
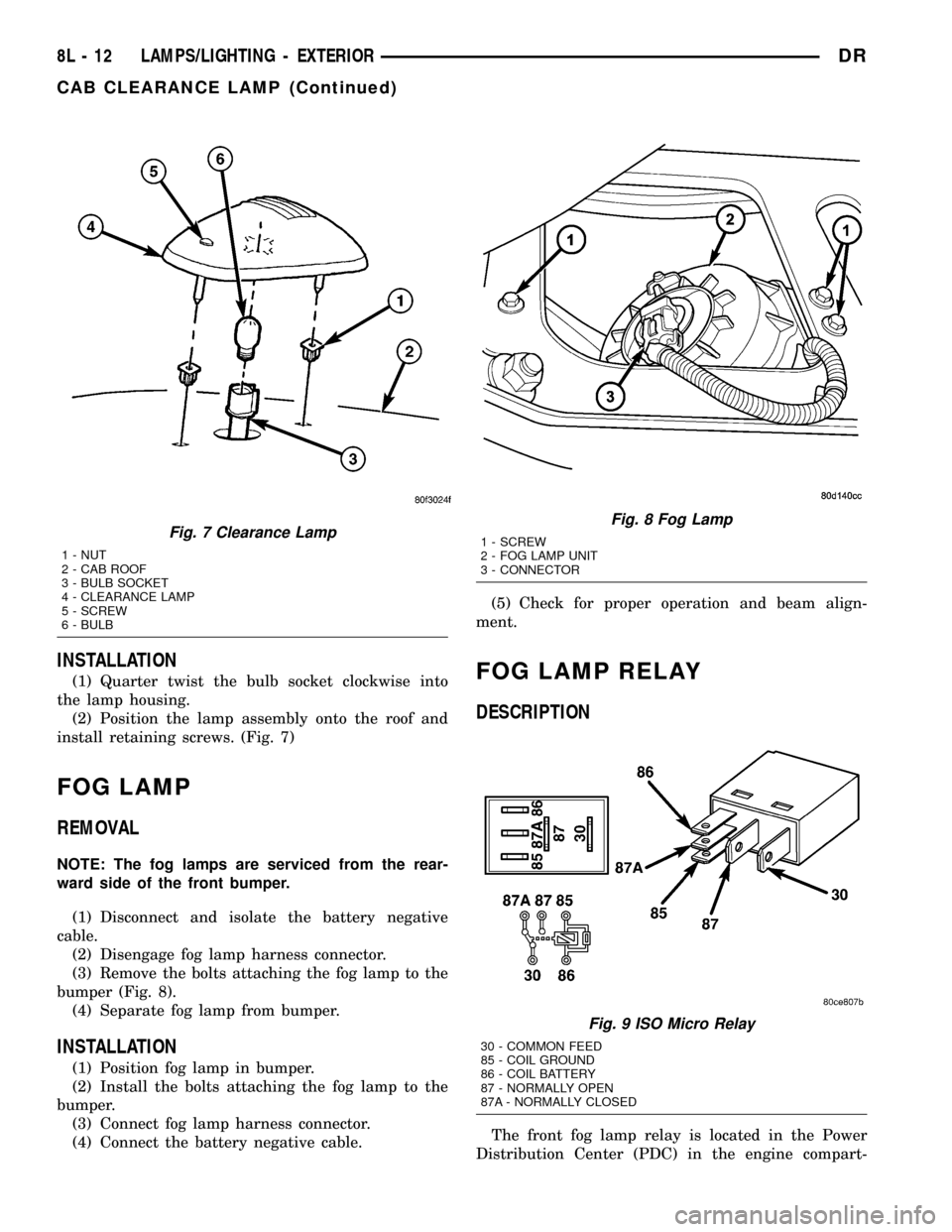
INSTALLATION
(1) Quarter twist the bulb socket clockwise into
the lamp housing.
(2) Position the lamp assembly onto the roof and
install retaining screws. (Fig. 7)
FOG LAMP
REMOVAL
NOTE: The fog lamps are serviced from the rear-
ward side of the front bumper.
(1) Disconnect and isolate the battery negative
cable.
(2) Disengage fog lamp harness connector.
(3) Remove the bolts attaching the fog lamp to the
bumper (Fig. 8).
(4) Separate fog lamp from bumper.
INSTALLATION
(1) Position fog lamp in bumper.
(2) Install the bolts attaching the fog lamp to the
bumper.
(3) Connect fog lamp harness connector.
(4) Connect the battery negative cable.(5) Check for proper operation and beam align-
ment.
FOG LAMP RELAY
DESCRIPTION
The front fog lamp relay is located in the Power
Distribution Center (PDC) in the engine compart-
Fig. 7 Clearance Lamp
1 - NUT
2 - CAB ROOF
3 - BULB SOCKET
4 - CLEARANCE LAMP
5 - SCREW
6 - BULB
Fig. 8 Fog Lamp
1 - SCREW
2 - FOG LAMP UNIT
3 - CONNECTOR
Fig. 9 ISO Micro Relay
30 - COMMON FEED
85 - COIL GROUND
86 - COIL BATTERY
87 - NORMALLY OPEN
87A - NORMALLY CLOSED
8L - 12 LAMPS/LIGHTING - EXTERIORDR
CAB CLEARANCE LAMP (Continued)
Page 595 of 2627
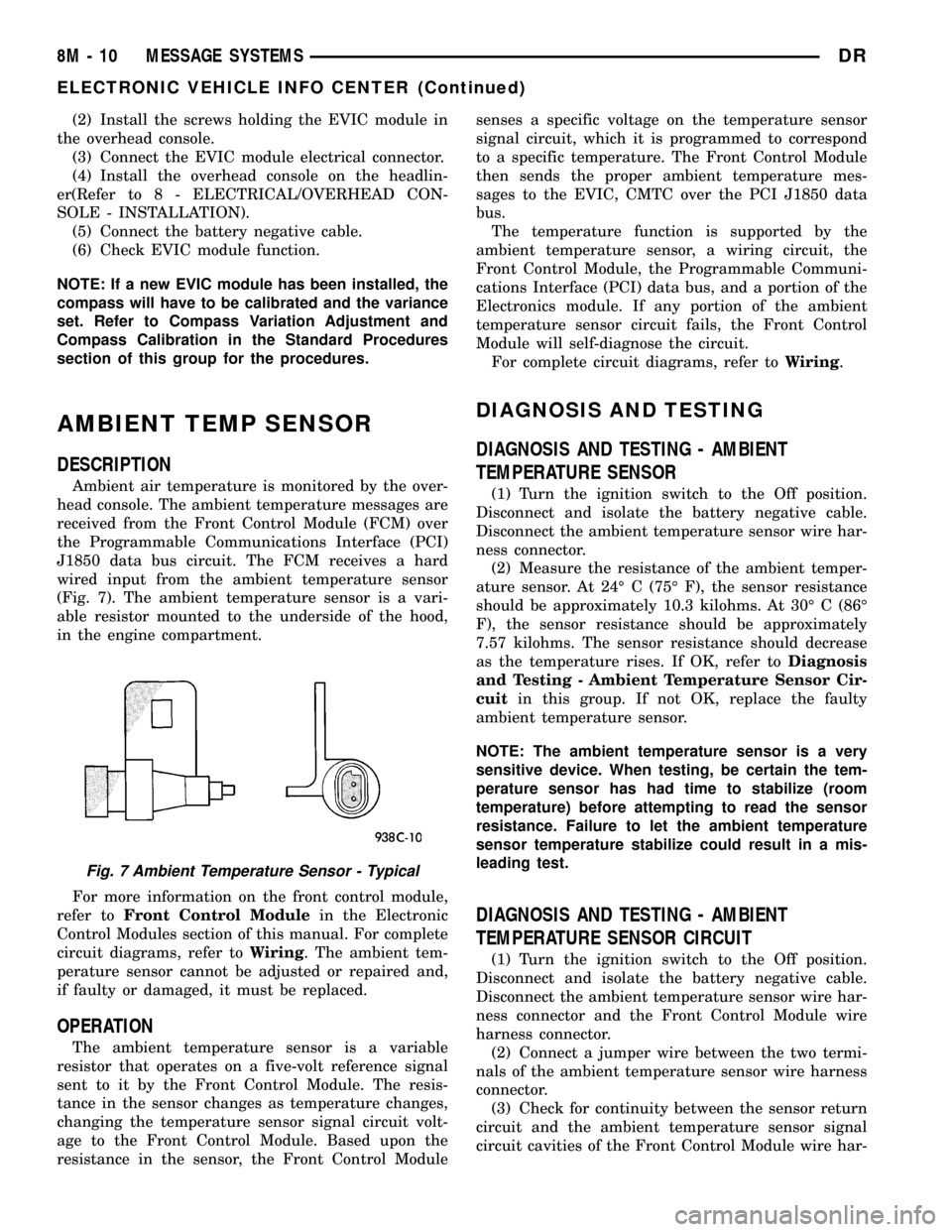
(2) Install the screws holding the EVIC module in
the overhead console.
(3) Connect the EVIC module electrical connector.
(4) Install the overhead console on the headlin-
er(Refer to 8 - ELECTRICAL/OVERHEAD CON-
SOLE - INSTALLATION).
(5) Connect the battery negative cable.
(6) Check EVIC module function.
NOTE: If a new EVIC module has been installed, the
compass will have to be calibrated and the variance
set. Refer to Compass Variation Adjustment and
Compass Calibration in the Standard Procedures
section of this group for the procedures.
AMBIENT TEMP SENSOR
DESCRIPTION
Ambient air temperature is monitored by the over-
head console. The ambient temperature messages are
received from the Front Control Module (FCM) over
the Programmable Communications Interface (PCI)
J1850 data bus circuit. The FCM receives a hard
wired input from the ambient temperature sensor
(Fig. 7). The ambient temperature sensor is a vari-
able resistor mounted to the underside of the hood,
in the engine compartment.
For more information on the front control module,
refer toFront Control Modulein the Electronic
Control Modules section of this manual. For complete
circuit diagrams, refer toWiring. The ambient tem-
perature sensor cannot be adjusted or repaired and,
if faulty or damaged, it must be replaced.
OPERATION
The ambient temperature sensor is a variable
resistor that operates on a five-volt reference signal
sent to it by the Front Control Module. The resis-
tance in the sensor changes as temperature changes,
changing the temperature sensor signal circuit volt-
age to the Front Control Module. Based upon the
resistance in the sensor, the Front Control Modulesenses a specific voltage on the temperature sensor
signal circuit, which it is programmed to correspond
to a specific temperature. The Front Control Module
then sends the proper ambient temperature mes-
sages to the EVIC, CMTC over the PCI J1850 data
bus.
The temperature function is supported by the
ambient temperature sensor, a wiring circuit, the
Front Control Module, the Programmable Communi-
cations Interface (PCI) data bus, and a portion of the
Electronics module. If any portion of the ambient
temperature sensor circuit fails, the Front Control
Module will self-diagnose the circuit.
For complete circuit diagrams, refer toWiring.
DIAGNOSIS AND TESTING
DIAGNOSIS AND TESTING - AMBIENT
TEMPERATURE SENSOR
(1) Turn the ignition switch to the Off position.
Disconnect and isolate the battery negative cable.
Disconnect the ambient temperature sensor wire har-
ness connector.
(2) Measure the resistance of the ambient temper-
ature sensor. At 24É C (75É F), the sensor resistance
should be approximately 10.3 kilohms. At 30É C (86É
F), the sensor resistance should be approximately
7.57 kilohms. The sensor resistance should decrease
as the temperature rises. If OK, refer toDiagnosis
and Testing - Ambient Temperature Sensor Cir-
cuitin this group. If not OK, replace the faulty
ambient temperature sensor.
NOTE: The ambient temperature sensor is a very
sensitive device. When testing, be certain the tem-
perature sensor has had time to stabilize (room
temperature) before attempting to read the sensor
resistance. Failure to let the ambient temperature
sensor temperature stabilize could result in a mis-
leading test.
DIAGNOSIS AND TESTING - AMBIENT
TEMPERATURE SENSOR CIRCUIT
(1) Turn the ignition switch to the Off position.
Disconnect and isolate the battery negative cable.
Disconnect the ambient temperature sensor wire har-
ness connector and the Front Control Module wire
harness connector.
(2) Connect a jumper wire between the two termi-
nals of the ambient temperature sensor wire harness
connector.
(3) Check for continuity between the sensor return
circuit and the ambient temperature sensor signal
circuit cavities of the Front Control Module wire har-
Fig. 7 Ambient Temperature Sensor - Typical
8M - 10 MESSAGE SYSTEMSDR
ELECTRONIC VEHICLE INFO CENTER (Continued)
Page 597 of 2627
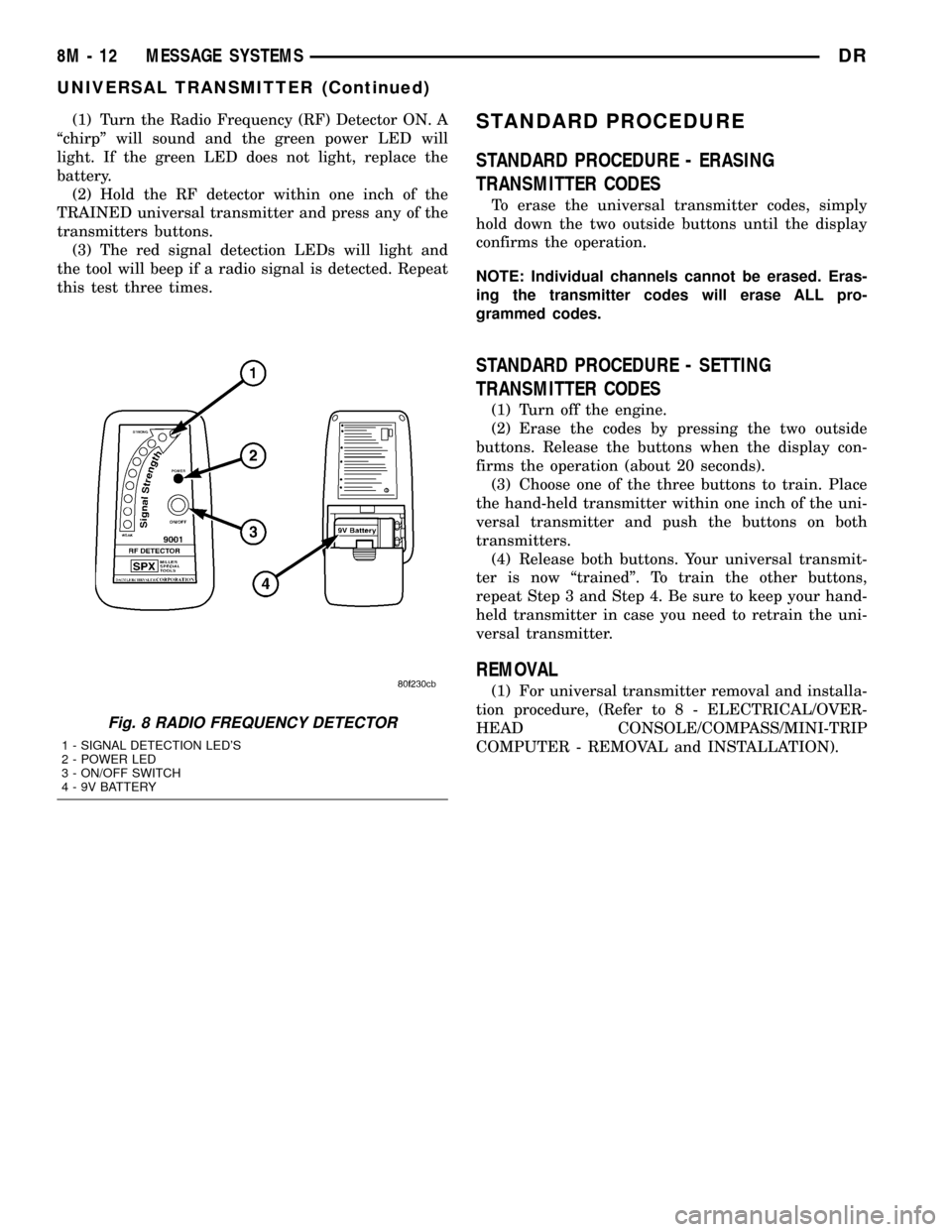
(1) Turn the Radio Frequency (RF) Detector ON. A
ªchirpº will sound and the green power LED will
light. If the green LED does not light, replace the
battery.
(2) Hold the RF detector within one inch of the
TRAINED universal transmitter and press any of the
transmitters buttons.
(3) The red signal detection LEDs will light and
the tool will beep if a radio signal is detected. Repeat
this test three times.STANDARD PROCEDURE
STANDARD PROCEDURE - ERASING
TRANSMITTER CODES
To erase the universal transmitter codes, simply
hold down the two outside buttons until the display
confirms the operation.
NOTE: Individual channels cannot be erased. Eras-
ing the transmitter codes will erase ALL pro-
grammed codes.
STANDARD PROCEDURE - SETTING
TRANSMITTER CODES
(1) Turn off the engine.
(2) Erase the codes by pressing the two outside
buttons. Release the buttons when the display con-
firms the operation (about 20 seconds).
(3) Choose one of the three buttons to train. Place
the hand-held transmitter within one inch of the uni-
versal transmitter and push the buttons on both
transmitters.
(4) Release both buttons. Your universal transmit-
ter is now ªtrainedº. To train the other buttons,
repeat Step 3 and Step 4. Be sure to keep your hand-
held transmitter in case you need to retrain the uni-
versal transmitter.
REMOVAL
(1) For universal transmitter removal and installa-
tion procedure, (Refer to 8 - ELECTRICAL/OVER-
HEAD CONSOLE/COMPASS/MINI-TRIP
COMPUTER - REMOVAL and INSTALLATION).
Fig. 8 RADIO FREQUENCY DETECTOR
1 - SIGNAL DETECTION LED'S
2 - POWER LED
3 - ON/OFF SWITCH
4 - 9V BATTERY
8M - 12 MESSAGE SYSTEMSDR
UNIVERSAL TRANSMITTER (Continued)
Page 682 of 2627
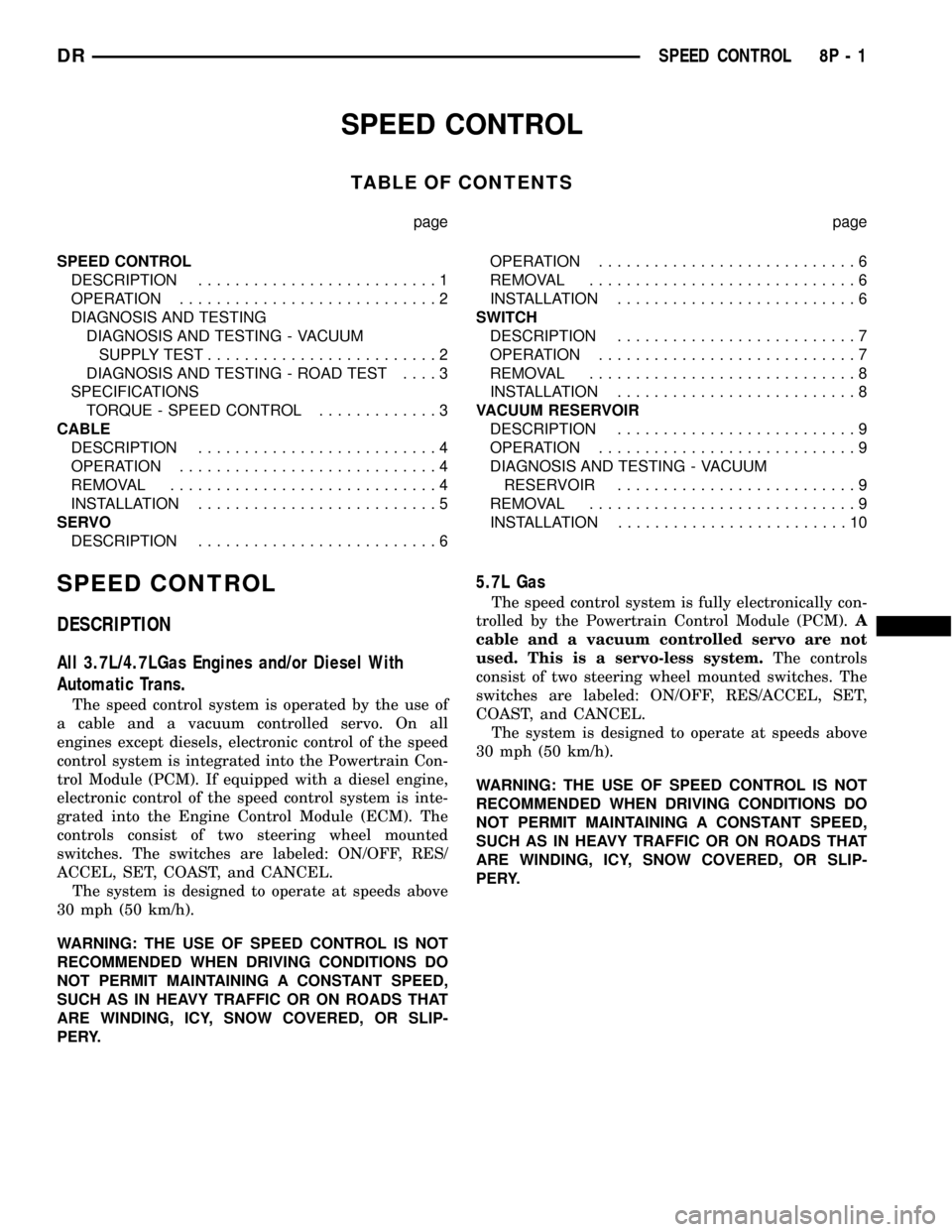
SPEED CONTROL
TABLE OF CONTENTS
page page
SPEED CONTROL
DESCRIPTION..........................1
OPERATION............................2
DIAGNOSIS AND TESTING
DIAGNOSIS AND TESTING - VACUUM
SUPPLY TEST.........................2
DIAGNOSIS AND TESTING - ROAD TEST....3
SPECIFICATIONS
TORQUE - SPEED CONTROL.............3
CABLE
DESCRIPTION..........................4
OPERATION............................4
REMOVAL.............................4
INSTALLATION..........................5
SERVO
DESCRIPTION..........................6OPERATION............................6
REMOVAL.............................6
INSTALLATION..........................6
SWITCH
DESCRIPTION..........................7
OPERATION............................7
REMOVAL.............................8
INSTALLATION..........................8
VACUUM RESERVOIR
DESCRIPTION..........................9
OPERATION............................9
DIAGNOSIS AND TESTING - VACUUM
RESERVOIR..........................9
REMOVAL.............................9
INSTALLATION.........................10
SPEED CONTROL
DESCRIPTION
All 3.7L/4.7LGas Engines and/or Diesel With
Automatic Trans.
The speed control system is operated by the use of
a cable and a vacuum controlled servo. On all
engines except diesels, electronic control of the speed
control system is integrated into the Powertrain Con-
trol Module (PCM). If equipped with a diesel engine,
electronic control of the speed control system is inte-
grated into the Engine Control Module (ECM). The
controls consist of two steering wheel mounted
switches. The switches are labeled: ON/OFF, RES/
ACCEL, SET, COAST, and CANCEL.
The system is designed to operate at speeds above
30 mph (50 km/h).
WARNING: THE USE OF SPEED CONTROL IS NOT
RECOMMENDED WHEN DRIVING CONDITIONS DO
NOT PERMIT MAINTAINING A CONSTANT SPEED,
SUCH AS IN HEAVY TRAFFIC OR ON ROADS THAT
ARE WINDING, ICY, SNOW COVERED, OR SLIP-
PERY.
5.7L Gas
The speed control system is fully electronically con-
trolled by the Powertrain Control Module (PCM).A
cable and a vacuum controlled servo are not
used. This is a servo-less system.The controls
consist of two steering wheel mounted switches. The
switches are labeled: ON/OFF, RES/ACCEL, SET,
COAST, and CANCEL.
The system is designed to operate at speeds above
30 mph (50 km/h).
WARNING: THE USE OF SPEED CONTROL IS NOT
RECOMMENDED WHEN DRIVING CONDITIONS DO
NOT PERMIT MAINTAINING A CONSTANT SPEED,
SUCH AS IN HEAVY TRAFFIC OR ON ROADS THAT
ARE WINDING, ICY, SNOW COVERED, OR SLIP-
PERY.
DRSPEED CONTROL 8P - 1
Page 683 of 2627
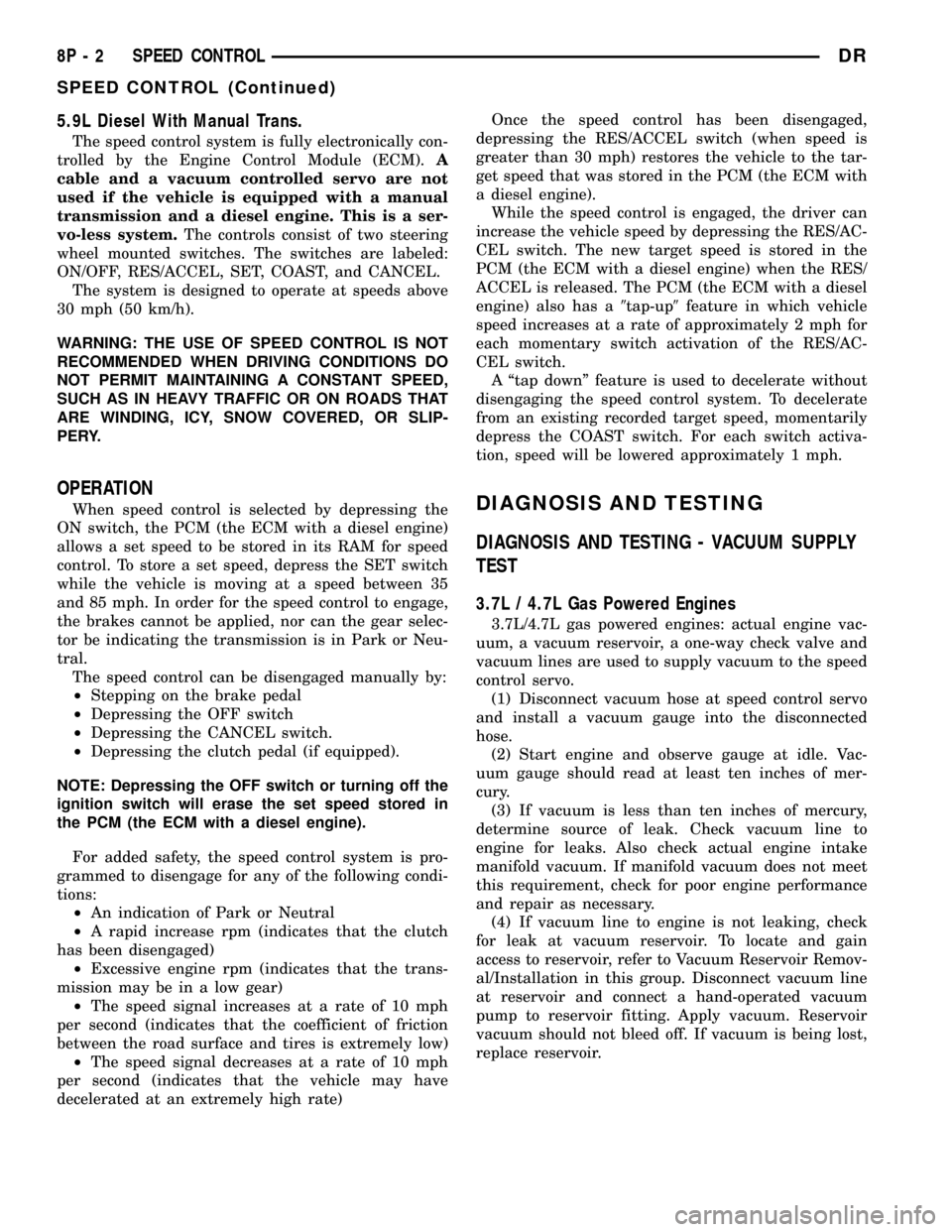
5.9L Diesel With Manual Trans.
The speed control system is fully electronically con-
trolled by the Engine Control Module (ECM).A
cable and a vacuum controlled servo are not
used if the vehicle is equipped with a manual
transmission and a diesel engine. This is a ser-
vo-less system.The controls consist of two steering
wheel mounted switches. The switches are labeled:
ON/OFF, RES/ACCEL, SET, COAST, and CANCEL.
The system is designed to operate at speeds above
30 mph (50 km/h).
WARNING: THE USE OF SPEED CONTROL IS NOT
RECOMMENDED WHEN DRIVING CONDITIONS DO
NOT PERMIT MAINTAINING A CONSTANT SPEED,
SUCH AS IN HEAVY TRAFFIC OR ON ROADS THAT
ARE WINDING, ICY, SNOW COVERED, OR SLIP-
PERY.
OPERATION
When speed control is selected by depressing the
ON switch, the PCM (the ECM with a diesel engine)
allows a set speed to be stored in its RAM for speed
control. To store a set speed, depress the SET switch
while the vehicle is moving at a speed between 35
and 85 mph. In order for the speed control to engage,
the brakes cannot be applied, nor can the gear selec-
tor be indicating the transmission is in Park or Neu-
tral.
The speed control can be disengaged manually by:
²Stepping on the brake pedal
²Depressing the OFF switch
²Depressing the CANCEL switch.
²Depressing the clutch pedal (if equipped).
NOTE: Depressing the OFF switch or turning off the
ignition switch will erase the set speed stored in
the PCM (the ECM with a diesel engine).
For added safety, the speed control system is pro-
grammed to disengage for any of the following condi-
tions:
²An indication of Park or Neutral
²A rapid increase rpm (indicates that the clutch
has been disengaged)
²Excessive engine rpm (indicates that the trans-
mission may be in a low gear)
²The speed signal increases at a rate of 10 mph
per second (indicates that the coefficient of friction
between the road surface and tires is extremely low)
²The speed signal decreases at a rate of 10 mph
per second (indicates that the vehicle may have
decelerated at an extremely high rate)Once the speed control has been disengaged,
depressing the RES/ACCEL switch (when speed is
greater than 30 mph) restores the vehicle to the tar-
get speed that was stored in the PCM (the ECM with
a diesel engine).
While the speed control is engaged, the driver can
increase the vehicle speed by depressing the RES/AC-
CEL switch. The new target speed is stored in the
PCM (the ECM with a diesel engine) when the RES/
ACCEL is released. The PCM (the ECM with a diesel
engine) also has a9tap-up9feature in which vehicle
speed increases at a rate of approximately 2 mph for
each momentary switch activation of the RES/AC-
CEL switch.
A ªtap downº feature is used to decelerate without
disengaging the speed control system. To decelerate
from an existing recorded target speed, momentarily
depress the COAST switch. For each switch activa-
tion, speed will be lowered approximately 1 mph.DIAGNOSIS AND TESTING
DIAGNOSIS AND TESTING - VACUUM SUPPLY
TEST
3.7L / 4.7L Gas Powered Engines
3.7L/4.7L gas powered engines: actual engine vac-
uum, a vacuum reservoir, a one-way check valve and
vacuum lines are used to supply vacuum to the speed
control servo.
(1) Disconnect vacuum hose at speed control servo
and install a vacuum gauge into the disconnected
hose.
(2) Start engine and observe gauge at idle. Vac-
uum gauge should read at least ten inches of mer-
cury.
(3) If vacuum is less than ten inches of mercury,
determine source of leak. Check vacuum line to
engine for leaks. Also check actual engine intake
manifold vacuum. If manifold vacuum does not meet
this requirement, check for poor engine performance
and repair as necessary.
(4) If vacuum line to engine is not leaking, check
for leak at vacuum reservoir. To locate and gain
access to reservoir, refer to Vacuum Reservoir Remov-
al/Installation in this group. Disconnect vacuum line
at reservoir and connect a hand-operated vacuum
pump to reservoir fitting. Apply vacuum. Reservoir
vacuum should not bleed off. If vacuum is being lost,
replace reservoir.
8P - 2 SPEED CONTROLDR
SPEED CONTROL (Continued)
Page 684 of 2627
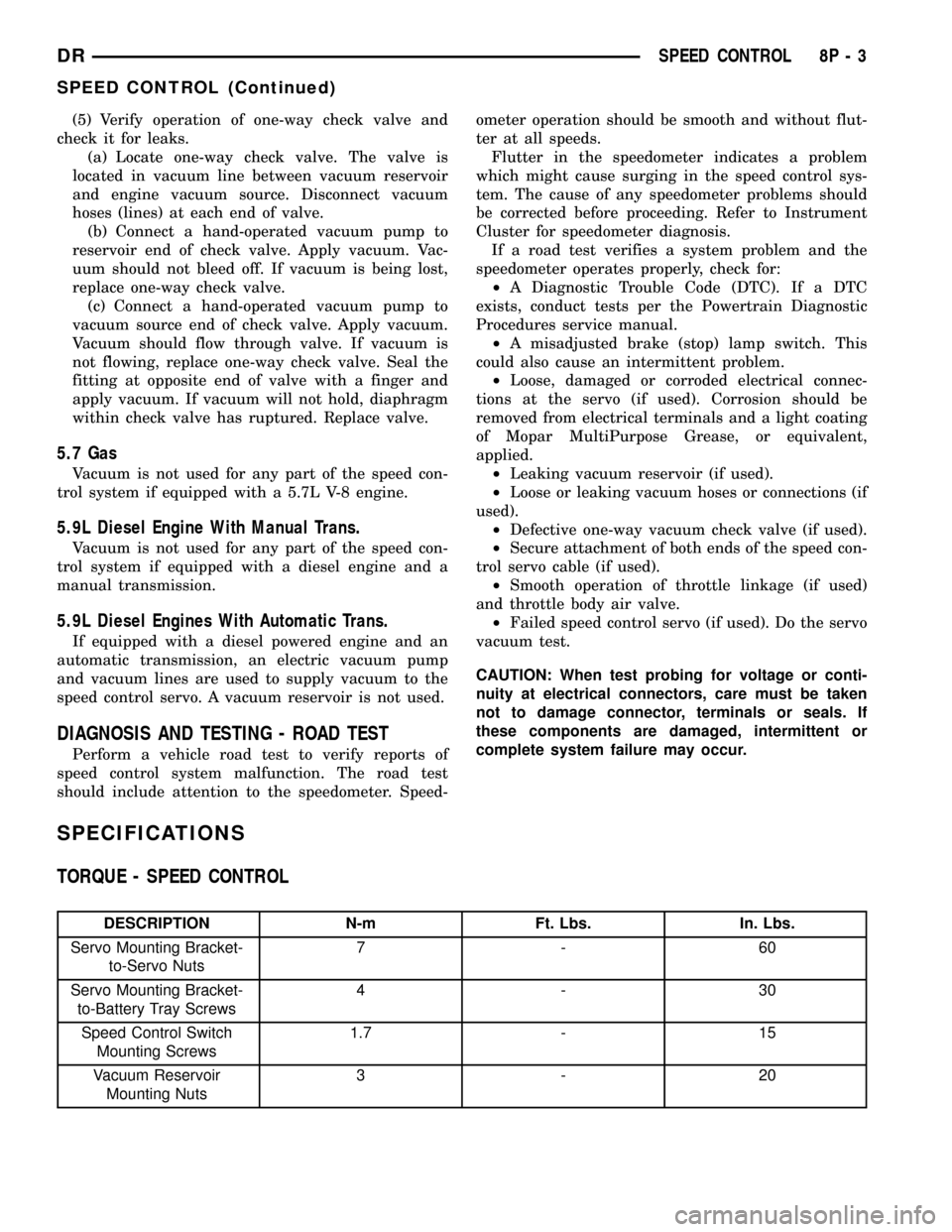
(5) Verify operation of one-way check valve and
check it for leaks.
(a) Locate one-way check valve. The valve is
located in vacuum line between vacuum reservoir
and engine vacuum source. Disconnect vacuum
hoses (lines) at each end of valve.
(b) Connect a hand-operated vacuum pump to
reservoir end of check valve. Apply vacuum. Vac-
uum should not bleed off. If vacuum is being lost,
replace one-way check valve.
(c) Connect a hand-operated vacuum pump to
vacuum source end of check valve. Apply vacuum.
Vacuum should flow through valve. If vacuum is
not flowing, replace one-way check valve. Seal the
fitting at opposite end of valve with a finger and
apply vacuum. If vacuum will not hold, diaphragm
within check valve has ruptured. Replace valve.
5.7 Gas
Vacuum is not used for any part of the speed con-
trol system if equipped with a 5.7L V-8 engine.
5.9L Diesel Engine With Manual Trans.
Vacuum is not used for any part of the speed con-
trol system if equipped with a diesel engine and a
manual transmission.
5.9L Diesel Engines With Automatic Trans.
If equipped with a diesel powered engine and an
automatic transmission, an electric vacuum pump
and vacuum lines are used to supply vacuum to the
speed control servo. A vacuum reservoir is not used.
DIAGNOSIS AND TESTING - ROAD TEST
Perform a vehicle road test to verify reports of
speed control system malfunction. The road test
should include attention to the speedometer. Speed-ometer operation should be smooth and without flut-
ter at all speeds.
Flutter in the speedometer indicates a problem
which might cause surging in the speed control sys-
tem. The cause of any speedometer problems should
be corrected before proceeding. Refer to Instrument
Cluster for speedometer diagnosis.
If a road test verifies a system problem and the
speedometer operates properly, check for:
²A Diagnostic Trouble Code (DTC). If a DTC
exists, conduct tests per the Powertrain Diagnostic
Procedures service manual.
²A misadjusted brake (stop) lamp switch. This
could also cause an intermittent problem.
²Loose, damaged or corroded electrical connec-
tions at the servo (if used). Corrosion should be
removed from electrical terminals and a light coating
of Mopar MultiPurpose Grease, or equivalent,
applied.
²Leaking vacuum reservoir (if used).
²Loose or leaking vacuum hoses or connections (if
used).
²Defective one-way vacuum check valve (if used).
²Secure attachment of both ends of the speed con-
trol servo cable (if used).
²Smooth operation of throttle linkage (if used)
and throttle body air valve.
²Failed speed control servo (if used). Do the servo
vacuum test.
CAUTION: When test probing for voltage or conti-
nuity at electrical connectors, care must be taken
not to damage connector, terminals or seals. If
these components are damaged, intermittent or
complete system failure may occur.
SPECIFICATIONS
TORQUE - SPEED CONTROL
DESCRIPTION N-m Ft. Lbs. In. Lbs.
Servo Mounting Bracket-
to-Servo Nuts7-60
Servo Mounting Bracket-
to-Battery Tray Screws4-30
Speed Control Switch
Mounting Screws1.7 - 15
Vacuum Reservoir
Mounting Nuts3-20
DRSPEED CONTROL 8P - 3
SPEED CONTROL (Continued)
Page 685 of 2627
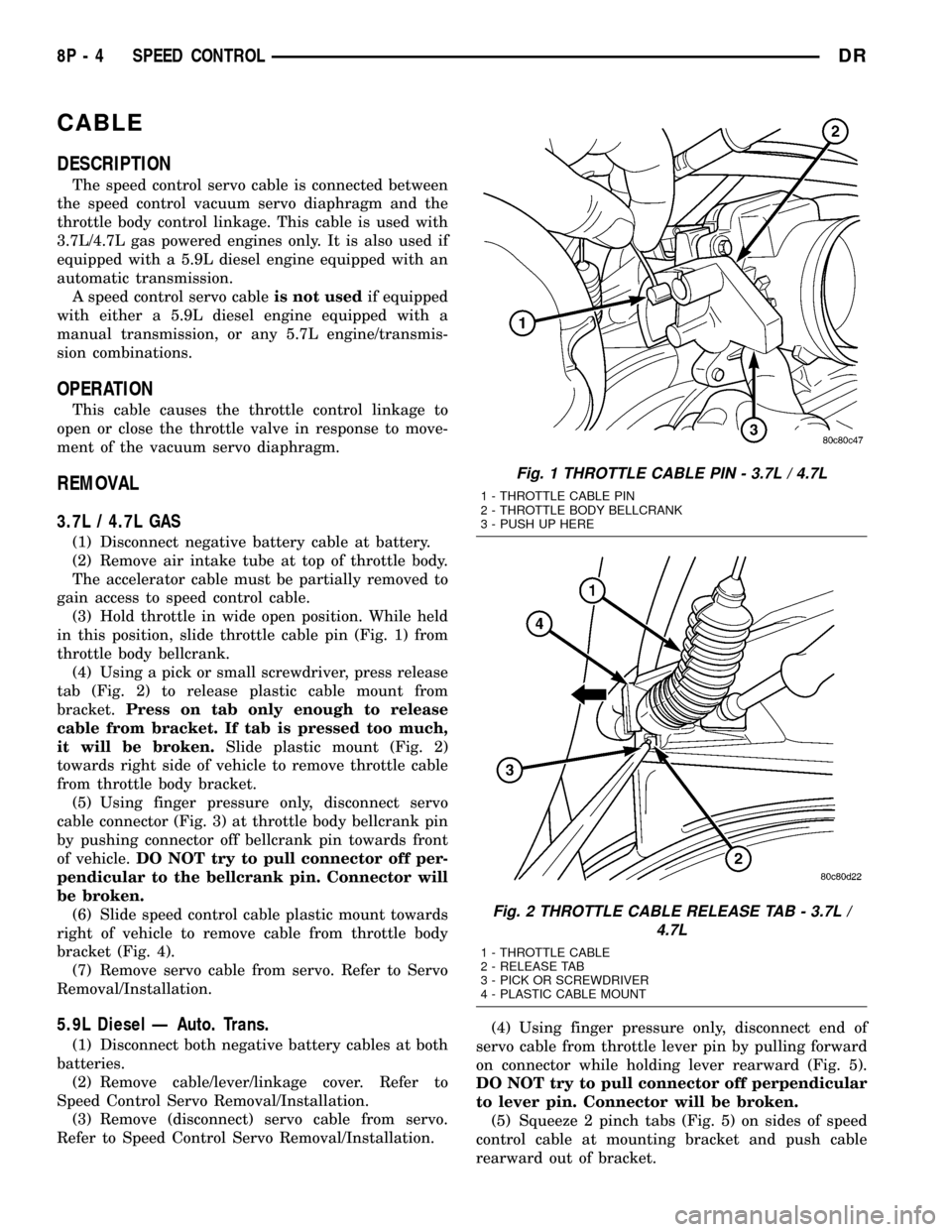
CABLE
DESCRIPTION
The speed control servo cable is connected between
the speed control vacuum servo diaphragm and the
throttle body control linkage. This cable is used with
3.7L/4.7L gas powered engines only. It is also used if
equipped with a 5.9L diesel engine equipped with an
automatic transmission.
A speed control servo cableis not usedif equipped
with either a 5.9L diesel engine equipped with a
manual transmission, or any 5.7L engine/transmis-
sion combinations.
OPERATION
This cable causes the throttle control linkage to
open or close the throttle valve in response to move-
ment of the vacuum servo diaphragm.
REMOVAL
3.7L / 4.7L GAS
(1) Disconnect negative battery cable at battery.
(2) Remove air intake tube at top of throttle body.
The accelerator cable must be partially removed to
gain access to speed control cable.
(3) Hold throttle in wide open position. While held
in this position, slide throttle cable pin (Fig. 1) from
throttle body bellcrank.
(4) Using a pick or small screwdriver, press release
tab (Fig. 2) to release plastic cable mount from
bracket.Press on tab only enough to release
cable from bracket. If tab is pressed too much,
it will be broken.Slide plastic mount (Fig. 2)
towards right side of vehicle to remove throttle cable
from throttle body bracket.
(5) Using finger pressure only, disconnect servo
cable connector (Fig. 3) at throttle body bellcrank pin
by pushing connector off bellcrank pin towards front
of vehicle.DO NOT try to pull connector off per-
pendicular to the bellcrank pin. Connector will
be broken.
(6) Slide speed control cable plastic mount towards
right of vehicle to remove cable from throttle body
bracket (Fig. 4).
(7) Remove servo cable from servo. Refer to Servo
Removal/Installation.
5.9L Diesel Ð Auto. Trans.
(1) Disconnect both negative battery cables at both
batteries.
(2) Remove cable/lever/linkage cover. Refer to
Speed Control Servo Removal/Installation.
(3) Remove (disconnect) servo cable from servo.
Refer to Speed Control Servo Removal/Installation.(4) Using finger pressure only, disconnect end of
servo cable from throttle lever pin by pulling forward
on connector while holding lever rearward (Fig. 5).
DO NOT try to pull connector off perpendicular
to lever pin. Connector will be broken.
(5) Squeeze 2 pinch tabs (Fig. 5) on sides of speed
control cable at mounting bracket and push cable
rearward out of bracket.
Fig. 1 THROTTLE CABLE PIN - 3.7L / 4.7L
1 - THROTTLE CABLE PIN
2 - THROTTLE BODY BELLCRANK
3 - PUSH UP HERE
Fig. 2 THROTTLE CABLE RELEASE TAB - 3.7L /
4.7L
1 - THROTTLE CABLE
2 - RELEASE TAB
3 - PICK OR SCREWDRIVER
4 - PLASTIC CABLE MOUNT
8P - 4 SPEED CONTROLDR
Page 686 of 2627
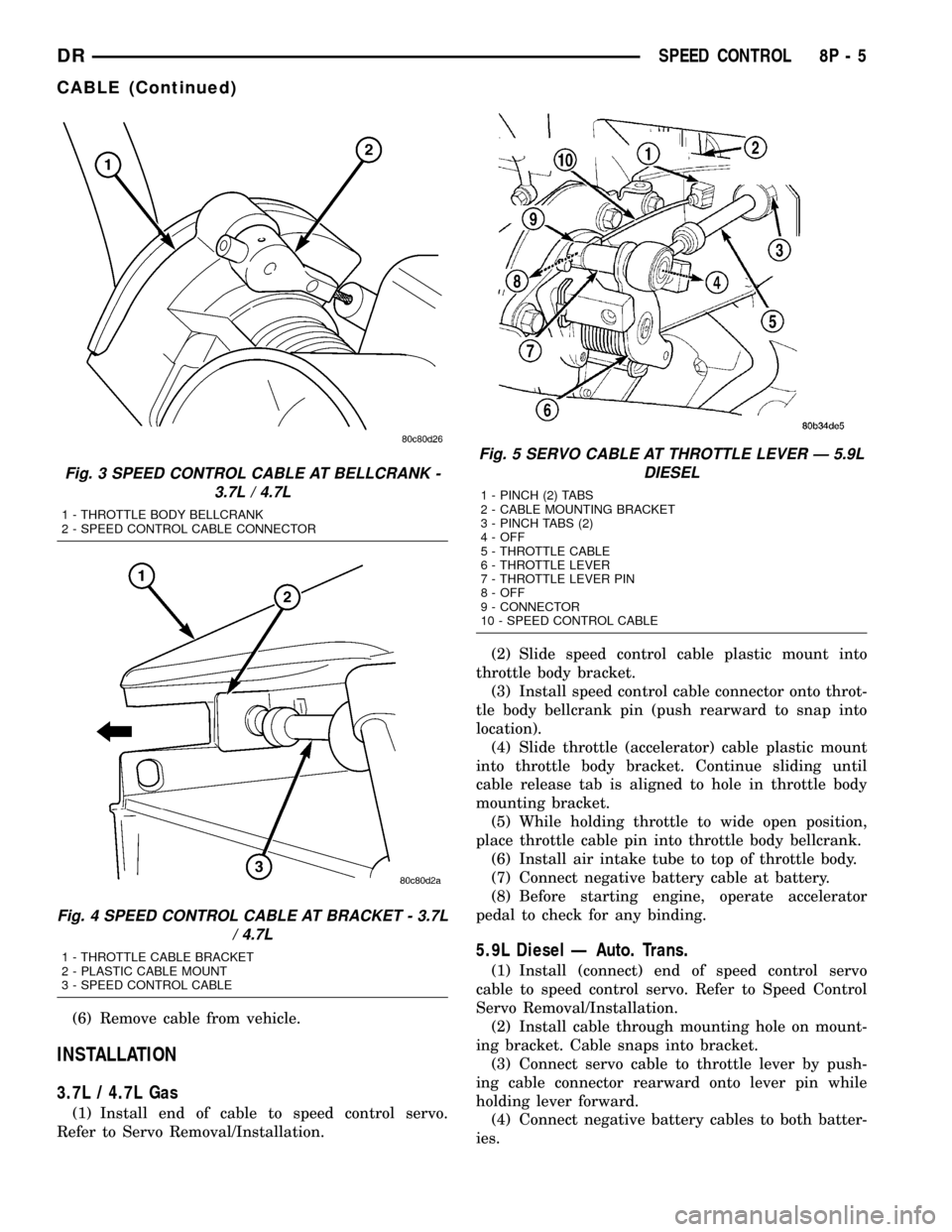
(6) Remove cable from vehicle.
INSTALLATION
3.7L / 4.7L Gas
(1) Install end of cable to speed control servo.
Refer to Servo Removal/Installation.(2) Slide speed control cable plastic mount into
throttle body bracket.
(3) Install speed control cable connector onto throt-
tle body bellcrank pin (push rearward to snap into
location).
(4) Slide throttle (accelerator) cable plastic mount
into throttle body bracket. Continue sliding until
cable release tab is aligned to hole in throttle body
mounting bracket.
(5) While holding throttle to wide open position,
place throttle cable pin into throttle body bellcrank.
(6) Install air intake tube to top of throttle body.
(7) Connect negative battery cable at battery.
(8) Before starting engine, operate accelerator
pedal to check for any binding.
5.9L Diesel Ð Auto. Trans.
(1) Install (connect) end of speed control servo
cable to speed control servo. Refer to Speed Control
Servo Removal/Installation.
(2) Install cable through mounting hole on mount-
ing bracket. Cable snaps into bracket.
(3) Connect servo cable to throttle lever by push-
ing cable connector rearward onto lever pin while
holding lever forward.
(4) Connect negative battery cables to both batter-
ies.
Fig. 3 SPEED CONTROL CABLE AT BELLCRANK -
3.7L / 4.7L
1 - THROTTLE BODY BELLCRANK
2 - SPEED CONTROL CABLE CONNECTOR
Fig. 4 SPEED CONTROL CABLE AT BRACKET - 3.7L
/ 4.7L
1 - THROTTLE CABLE BRACKET
2 - PLASTIC CABLE MOUNT
3 - SPEED CONTROL CABLE
Fig. 5 SERVO CABLE AT THROTTLE LEVER Ð 5.9L
DIESEL
1 - PINCH (2) TABS
2 - CABLE MOUNTING BRACKET
3 - PINCH TABS (2)
4 - OFF
5 - THROTTLE CABLE
6 - THROTTLE LEVER
7 - THROTTLE LEVER PIN
8 - OFF
9 - CONNECTOR
10 - SPEED CONTROL CABLE
DRSPEED CONTROL 8P - 5
CABLE (Continued)
Page 687 of 2627
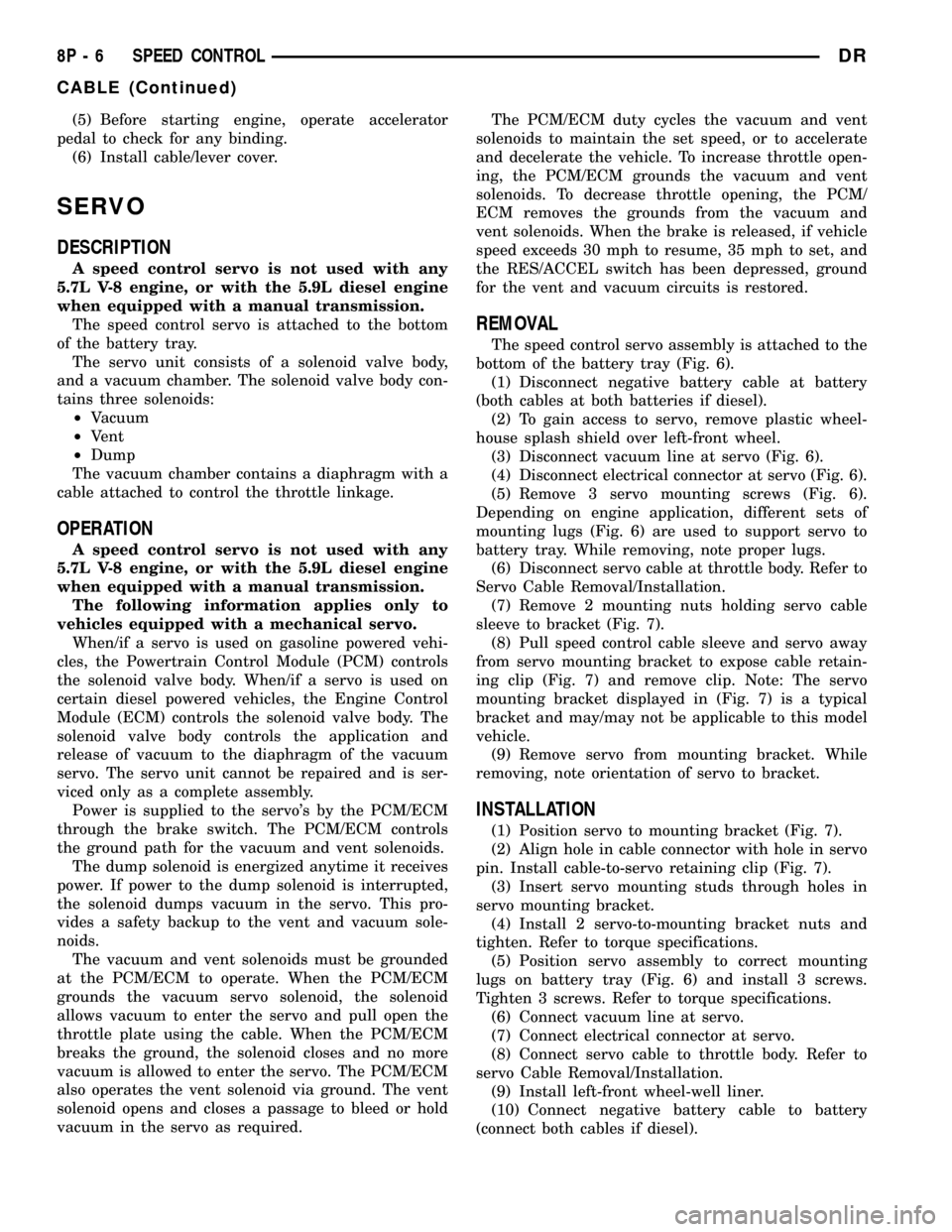
(5) Before starting engine, operate accelerator
pedal to check for any binding.
(6) Install cable/lever cover.
SERVO
DESCRIPTION
A speed control servo is not used with any
5.7L V-8 engine, or with the 5.9L diesel engine
when equipped with a manual transmission.
The speed control servo is attached to the bottom
of the battery tray.
The servo unit consists of a solenoid valve body,
and a vacuum chamber. The solenoid valve body con-
tains three solenoids:
²Vacuum
²Vent
²Dump
The vacuum chamber contains a diaphragm with a
cable attached to control the throttle linkage.
OPERATION
A speed control servo is not used with any
5.7L V-8 engine, or with the 5.9L diesel engine
when equipped with a manual transmission.
The following information applies only to
vehicles equipped with a mechanical servo.
When/if a servo is used on gasoline powered vehi-
cles, the Powertrain Control Module (PCM) controls
the solenoid valve body. When/if a servo is used on
certain diesel powered vehicles, the Engine Control
Module (ECM) controls the solenoid valve body. The
solenoid valve body controls the application and
release of vacuum to the diaphragm of the vacuum
servo. The servo unit cannot be repaired and is ser-
viced only as a complete assembly.
Power is supplied to the servo's by the PCM/ECM
through the brake switch. The PCM/ECM controls
the ground path for the vacuum and vent solenoids.
The dump solenoid is energized anytime it receives
power. If power to the dump solenoid is interrupted,
the solenoid dumps vacuum in the servo. This pro-
vides a safety backup to the vent and vacuum sole-
noids.
The vacuum and vent solenoids must be grounded
at the PCM/ECM to operate. When the PCM/ECM
grounds the vacuum servo solenoid, the solenoid
allows vacuum to enter the servo and pull open the
throttle plate using the cable. When the PCM/ECM
breaks the ground, the solenoid closes and no more
vacuum is allowed to enter the servo. The PCM/ECM
also operates the vent solenoid via ground. The vent
solenoid opens and closes a passage to bleed or hold
vacuum in the servo as required.The PCM/ECM duty cycles the vacuum and vent
solenoids to maintain the set speed, or to accelerate
and decelerate the vehicle. To increase throttle open-
ing, the PCM/ECM grounds the vacuum and vent
solenoids. To decrease throttle opening, the PCM/
ECM removes the grounds from the vacuum and
vent solenoids. When the brake is released, if vehicle
speed exceeds 30 mph to resume, 35 mph to set, and
the RES/ACCEL switch has been depressed, ground
for the vent and vacuum circuits is restored.
REMOVAL
The speed control servo assembly is attached to the
bottom of the battery tray (Fig. 6).
(1) Disconnect negative battery cable at battery
(both cables at both batteries if diesel).
(2) To gain access to servo, remove plastic wheel-
house splash shield over left-front wheel.
(3) Disconnect vacuum line at servo (Fig. 6).
(4) Disconnect electrical connector at servo (Fig. 6).
(5) Remove 3 servo mounting screws (Fig. 6).
Depending on engine application, different sets of
mounting lugs (Fig. 6) are used to support servo to
battery tray. While removing, note proper lugs.
(6) Disconnect servo cable at throttle body. Refer to
Servo Cable Removal/Installation.
(7) Remove 2 mounting nuts holding servo cable
sleeve to bracket (Fig. 7).
(8) Pull speed control cable sleeve and servo away
from servo mounting bracket to expose cable retain-
ing clip (Fig. 7) and remove clip. Note: The servo
mounting bracket displayed in (Fig. 7) is a typical
bracket and may/may not be applicable to this model
vehicle.
(9) Remove servo from mounting bracket. While
removing, note orientation of servo to bracket.
INSTALLATION
(1) Position servo to mounting bracket (Fig. 7).
(2) Align hole in cable connector with hole in servo
pin. Install cable-to-servo retaining clip (Fig. 7).
(3) Insert servo mounting studs through holes in
servo mounting bracket.
(4) Install 2 servo-to-mounting bracket nuts and
tighten. Refer to torque specifications.
(5) Position servo assembly to correct mounting
lugs on battery tray (Fig. 6) and install 3 screws.
Tighten 3 screws. Refer to torque specifications.
(6) Connect vacuum line at servo.
(7) Connect electrical connector at servo.
(8) Connect servo cable to throttle body. Refer to
servo Cable Removal/Installation.
(9) Install left-front wheel-well liner.
(10) Connect negative battery cable to battery
(connect both cables if diesel).
8P - 6 SPEED CONTROLDR
CABLE (Continued)
Page 688 of 2627
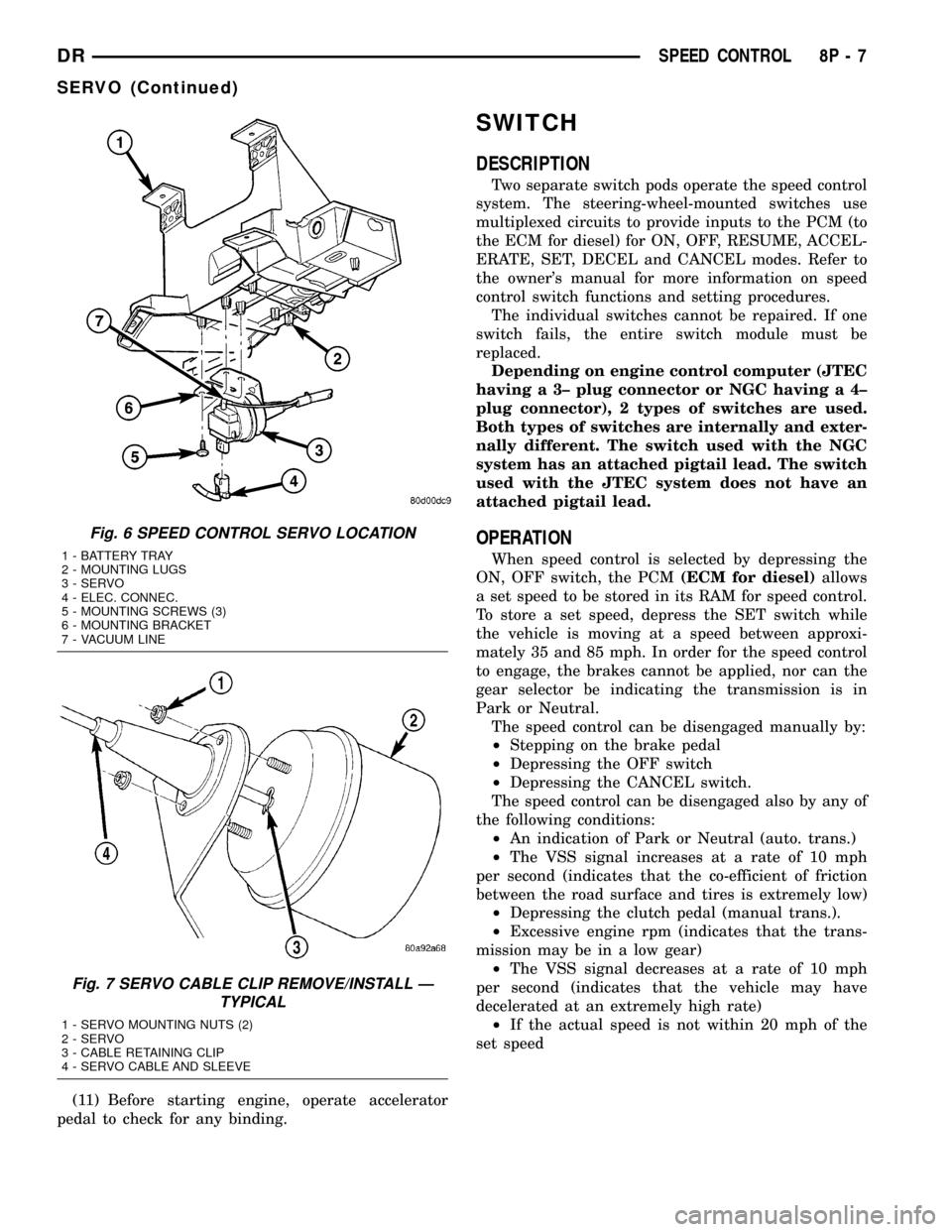
(11) Before starting engine, operate accelerator
pedal to check for any binding.
SWITCH
DESCRIPTION
Two separate switch pods operate the speed control
system. The steering-wheel-mounted switches use
multiplexed circuits to provide inputs to the PCM (to
the ECM for diesel) for ON, OFF, RESUME, ACCEL-
ERATE, SET, DECEL and CANCEL modes. Refer to
the owner's manual for more information on speed
control switch functions and setting procedures.
The individual switches cannot be repaired. If one
switch fails, the entire switch module must be
replaced.
Depending on engine control computer (JTEC
having a 3± plug connector or NGC having a 4±
plug connector), 2 types of switches are used.
Both types of switches are internally and exter-
nally different. The switch used with the NGC
system has an attached pigtail lead. The switch
used with the JTEC system does not have an
attached pigtail lead.
OPERATION
When speed control is selected by depressing the
ON, OFF switch, the PCM(ECM for diesel)allows
a set speed to be stored in its RAM for speed control.
To store a set speed, depress the SET switch while
the vehicle is moving at a speed between approxi-
mately 35 and 85 mph. In order for the speed control
to engage, the brakes cannot be applied, nor can the
gear selector be indicating the transmission is in
Park or Neutral.
The speed control can be disengaged manually by:
²Stepping on the brake pedal
²Depressing the OFF switch
²Depressing the CANCEL switch.
The speed control can be disengaged also by any of
the following conditions:
²An indication of Park or Neutral (auto. trans.)
²The VSS signal increases at a rate of 10 mph
per second (indicates that the co-efficient of friction
between the road surface and tires is extremely low)
²Depressing the clutch pedal (manual trans.).
²Excessive engine rpm (indicates that the trans-
mission may be in a low gear)
²The VSS signal decreases at a rate of 10 mph
per second (indicates that the vehicle may have
decelerated at an extremely high rate)
²If the actual speed is not within 20 mph of the
set speed
Fig. 6 SPEED CONTROL SERVO LOCATION
1 - BATTERY TRAY
2 - MOUNTING LUGS
3 - SERVO
4 - ELEC. CONNEC.
5 - MOUNTING SCREWS (3)
6 - MOUNTING BRACKET
7 - VACUUM LINE
Fig. 7 SERVO CABLE CLIP REMOVE/INSTALL Ð
TYPICAL
1 - SERVO MOUNTING NUTS (2)
2 - SERVO
3 - CABLE RETAINING CLIP
4 - SERVO CABLE AND SLEEVE
DRSPEED CONTROL 8P - 7
SERVO (Continued)