engine DODGE RAM 1500 1998 2.G Workshop Manual
[x] Cancel search | Manufacturer: DODGE, Model Year: 1998, Model line: RAM 1500, Model: DODGE RAM 1500 1998 2.GPages: 2627
Page 689 of 2627
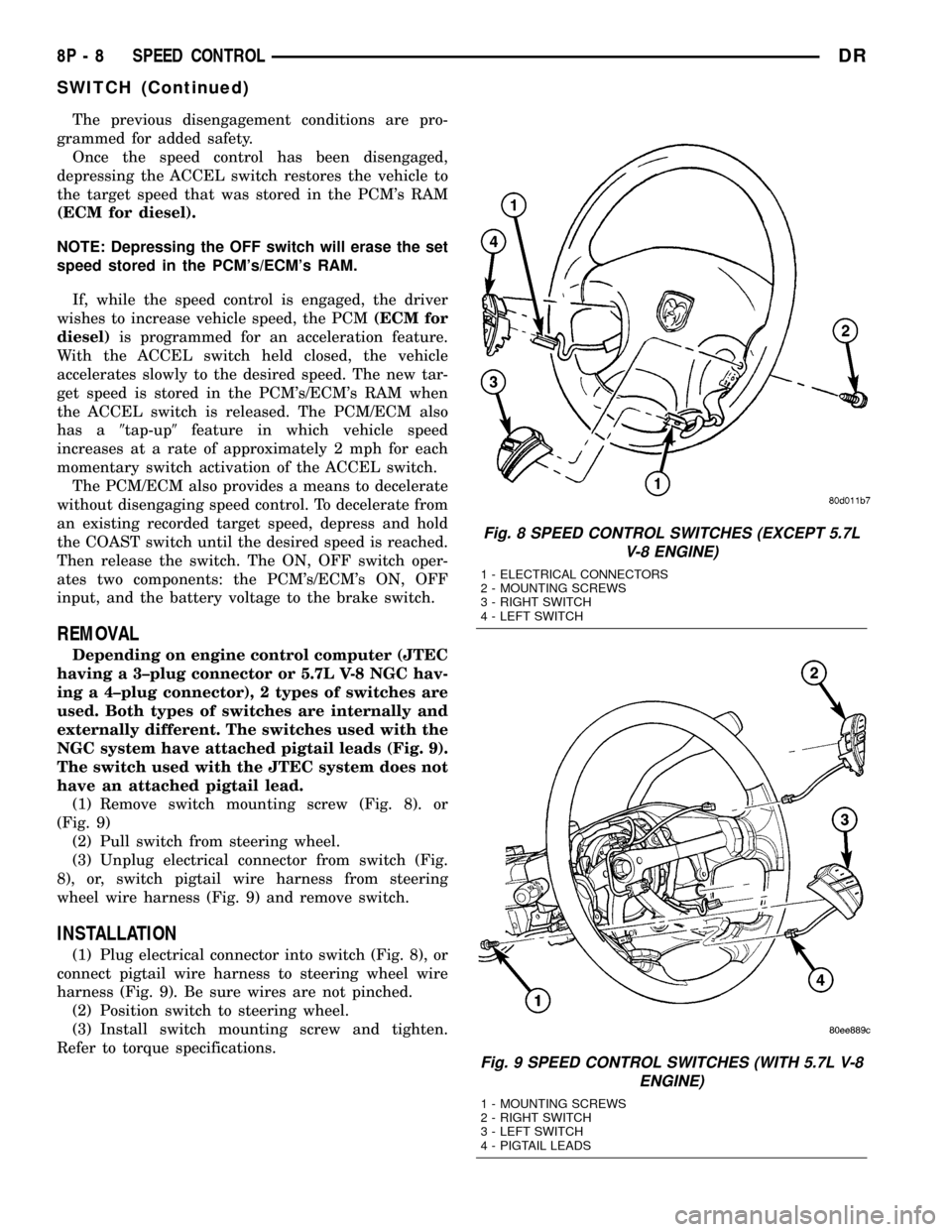
The previous disengagement conditions are pro-
grammed for added safety.
Once the speed control has been disengaged,
depressing the ACCEL switch restores the vehicle to
the target speed that was stored in the PCM's RAM
(ECM for diesel).
NOTE: Depressing the OFF switch will erase the set
speed stored in the PCM's/ECM's RAM.
If, while the speed control is engaged, the driver
wishes to increase vehicle speed, the PCM(ECM for
diesel)is programmed for an acceleration feature.
With the ACCEL switch held closed, the vehicle
accelerates slowly to the desired speed. The new tar-
get speed is stored in the PCM's/ECM's RAM when
the ACCEL switch is released. The PCM/ECM also
has a9tap-up9feature in which vehicle speed
increases at a rate of approximately 2 mph for each
momentary switch activation of the ACCEL switch.
The PCM/ECM also provides a means to decelerate
without disengaging speed control. To decelerate from
an existing recorded target speed, depress and hold
the COAST switch until the desired speed is reached.
Then release the switch. The ON, OFF switch oper-
ates two components: the PCM's/ECM's ON, OFF
input, and the battery voltage to the brake switch.
REMOVAL
Depending on engine control computer (JTEC
having a 3±plug connector or 5.7L V-8 NGC hav-
ing a 4±plug connector), 2 types of switches are
used. Both types of switches are internally and
externally different. The switches used with the
NGC system have attached pigtail leads (Fig. 9).
The switch used with the JTEC system does not
have an attached pigtail lead.
(1) Remove switch mounting screw (Fig. 8). or
(Fig. 9)
(2) Pull switch from steering wheel.
(3) Unplug electrical connector from switch (Fig.
8), or, switch pigtail wire harness from steering
wheel wire harness (Fig. 9) and remove switch.
INSTALLATION
(1) Plug electrical connector into switch (Fig. 8), or
connect pigtail wire harness to steering wheel wire
harness (Fig. 9). Be sure wires are not pinched.
(2) Position switch to steering wheel.
(3) Install switch mounting screw and tighten.
Refer to torque specifications.
Fig. 8 SPEED CONTROL SWITCHES (EXCEPT 5.7L
V-8 ENGINE)
1 - ELECTRICAL CONNECTORS
2 - MOUNTING SCREWS
3 - RIGHT SWITCH
4 - LEFT SWITCH
Fig. 9 SPEED CONTROL SWITCHES (WITH 5.7L V-8
ENGINE)
1 - MOUNTING SCREWS
2 - RIGHT SWITCH
3 - LEFT SWITCH
4 - PIGTAIL LEADS
8P - 8 SPEED CONTROLDR
SWITCH (Continued)
Page 690 of 2627
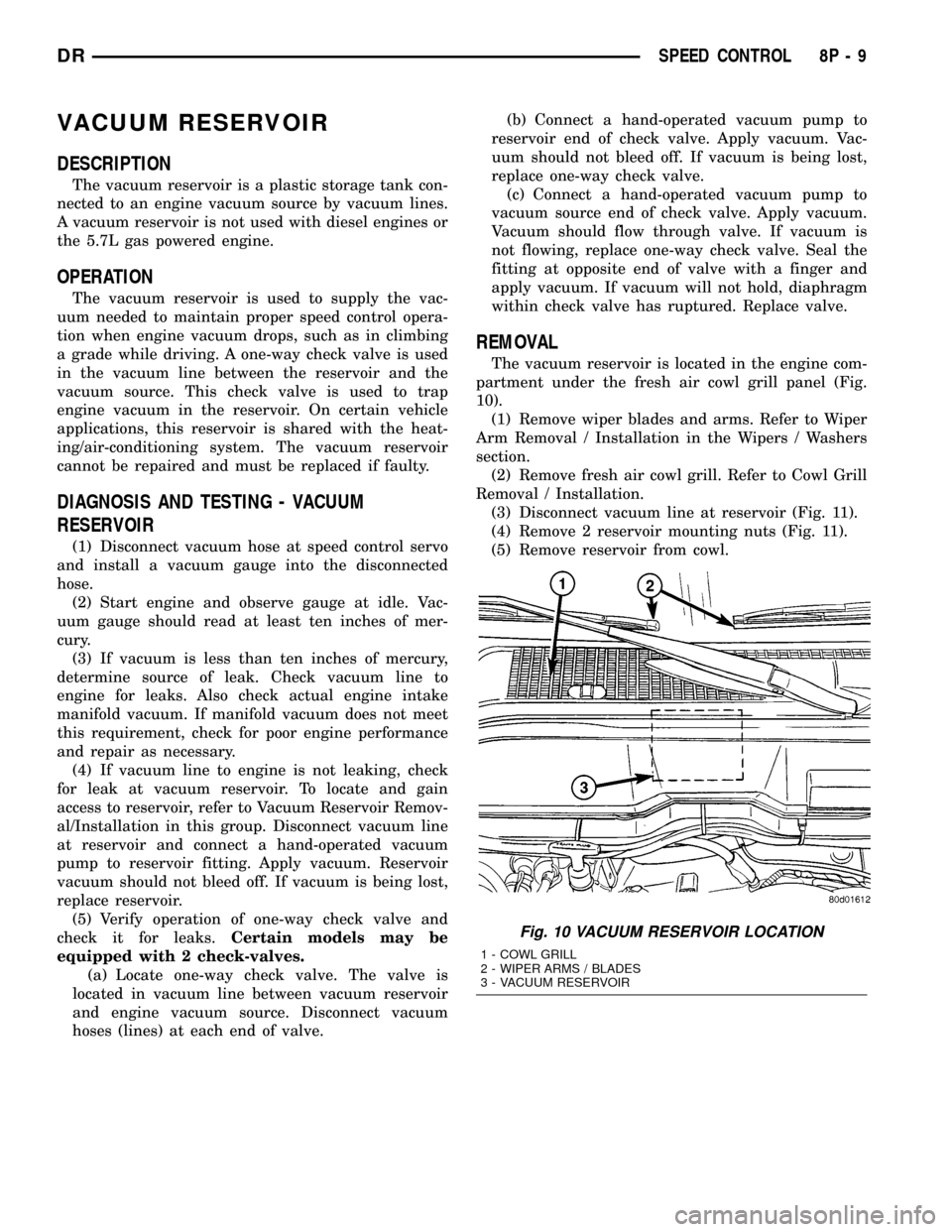
VACUUM RESERVOIR
DESCRIPTION
The vacuum reservoir is a plastic storage tank con-
nected to an engine vacuum source by vacuum lines.
A vacuum reservoir is not used with diesel engines or
the 5.7L gas powered engine.
OPERATION
The vacuum reservoir is used to supply the vac-
uum needed to maintain proper speed control opera-
tion when engine vacuum drops, such as in climbing
a grade while driving. A one-way check valve is used
in the vacuum line between the reservoir and the
vacuum source. This check valve is used to trap
engine vacuum in the reservoir. On certain vehicle
applications, this reservoir is shared with the heat-
ing/air-conditioning system. The vacuum reservoir
cannot be repaired and must be replaced if faulty.
DIAGNOSIS AND TESTING - VACUUM
RESERVOIR
(1) Disconnect vacuum hose at speed control servo
and install a vacuum gauge into the disconnected
hose.
(2) Start engine and observe gauge at idle. Vac-
uum gauge should read at least ten inches of mer-
cury.
(3) If vacuum is less than ten inches of mercury,
determine source of leak. Check vacuum line to
engine for leaks. Also check actual engine intake
manifold vacuum. If manifold vacuum does not meet
this requirement, check for poor engine performance
and repair as necessary.
(4) If vacuum line to engine is not leaking, check
for leak at vacuum reservoir. To locate and gain
access to reservoir, refer to Vacuum Reservoir Remov-
al/Installation in this group. Disconnect vacuum line
at reservoir and connect a hand-operated vacuum
pump to reservoir fitting. Apply vacuum. Reservoir
vacuum should not bleed off. If vacuum is being lost,
replace reservoir.
(5) Verify operation of one-way check valve and
check it for leaks.Certain models may be
equipped with 2 check-valves.
(a) Locate one-way check valve. The valve is
located in vacuum line between vacuum reservoir
and engine vacuum source. Disconnect vacuum
hoses (lines) at each end of valve.(b) Connect a hand-operated vacuum pump to
reservoir end of check valve. Apply vacuum. Vac-
uum should not bleed off. If vacuum is being lost,
replace one-way check valve.
(c) Connect a hand-operated vacuum pump to
vacuum source end of check valve. Apply vacuum.
Vacuum should flow through valve. If vacuum is
not flowing, replace one-way check valve. Seal the
fitting at opposite end of valve with a finger and
apply vacuum. If vacuum will not hold, diaphragm
within check valve has ruptured. Replace valve.
REMOVAL
The vacuum reservoir is located in the engine com-
partment under the fresh air cowl grill panel (Fig.
10).
(1) Remove wiper blades and arms. Refer to Wiper
Arm Removal / Installation in the Wipers / Washers
section.
(2) Remove fresh air cowl grill. Refer to Cowl Grill
Removal / Installation.
(3) Disconnect vacuum line at reservoir (Fig. 11).
(4) Remove 2 reservoir mounting nuts (Fig. 11).
(5) Remove reservoir from cowl.
Fig. 10 VACUUM RESERVOIR LOCATION
1 - COWL GRILL
2 - WIPER ARMS / BLADES
3 - VACUUM RESERVOIR
DRSPEED CONTROL 8P - 9
Page 692 of 2627
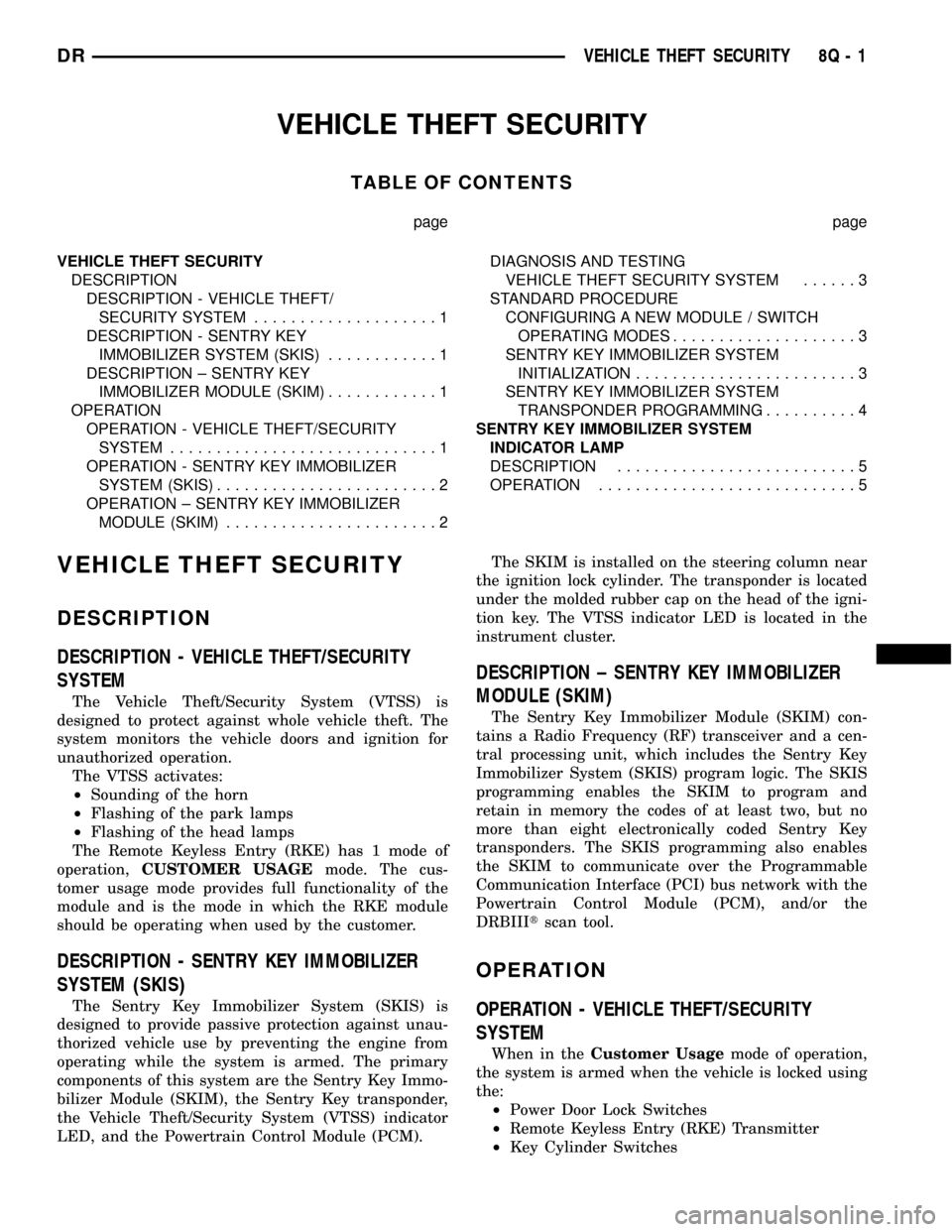
VEHICLE THEFT SECURITY
TABLE OF CONTENTS
page page
VEHICLE THEFT SECURITY
DESCRIPTION
DESCRIPTION - VEHICLE THEFT/
SECURITY SYSTEM....................1
DESCRIPTION - SENTRY KEY
IMMOBILIZER SYSTEM (SKIS)............1
DESCRIPTION ± SENTRY KEY
IMMOBILIZER MODULE (SKIM)............1
OPERATION
OPERATION - VEHICLE THEFT/SECURITY
SYSTEM.............................1
OPERATION - SENTRY KEY IMMOBILIZER
SYSTEM (SKIS)........................2
OPERATION ± SENTRY KEY IMMOBILIZER
MODULE (SKIM).......................2DIAGNOSIS AND TESTING
VEHICLE THEFT SECURITY SYSTEM......3
STANDARD PROCEDURE
CONFIGURING A NEW MODULE / SWITCH
OPERATING MODES....................3
SENTRY KEY IMMOBILIZER SYSTEM
INITIALIZATION........................3
SENTRY KEY IMMOBILIZER SYSTEM
TRANSPONDER PROGRAMMING..........4
SENTRY KEY IMMOBILIZER SYSTEM
INDICATOR LAMP
DESCRIPTION..........................5
OPERATION............................5
VEHICLE THEFT SECURITY
DESCRIPTION
DESCRIPTION - VEHICLE THEFT/SECURITY
SYSTEM
The Vehicle Theft/Security System (VTSS) is
designed to protect against whole vehicle theft. The
system monitors the vehicle doors and ignition for
unauthorized operation.
The VTSS activates:
²Sounding of the horn
²Flashing of the park lamps
²Flashing of the head lamps
The Remote Keyless Entry (RKE) has 1 mode of
operation,CUSTOMER USAGEmode. The cus-
tomer usage mode provides full functionality of the
module and is the mode in which the RKE module
should be operating when used by the customer.
DESCRIPTION - SENTRY KEY IMMOBILIZER
SYSTEM (SKIS)
The Sentry Key Immobilizer System (SKIS) is
designed to provide passive protection against unau-
thorized vehicle use by preventing the engine from
operating while the system is armed. The primary
components of this system are the Sentry Key Immo-
bilizer Module (SKIM), the Sentry Key transponder,
the Vehicle Theft/Security System (VTSS) indicator
LED, and the Powertrain Control Module (PCM).The SKIM is installed on the steering column near
the ignition lock cylinder. The transponder is located
under the molded rubber cap on the head of the igni-
tion key. The VTSS indicator LED is located in the
instrument cluster.
DESCRIPTION ± SENTRY KEY IMMOBILIZER
MODULE (SKIM)
The Sentry Key Immobilizer Module (SKIM) con-
tains a Radio Frequency (RF) transceiver and a cen-
tral processing unit, which includes the Sentry Key
Immobilizer System (SKIS) program logic. The SKIS
programming enables the SKIM to program and
retain in memory the codes of at least two, but no
more than eight electronically coded Sentry Key
transponders. The SKIS programming also enables
the SKIM to communicate over the Programmable
Communication Interface (PCI) bus network with the
Powertrain Control Module (PCM), and/or the
DRBIIItscan tool.
OPERATION
OPERATION - VEHICLE THEFT/SECURITY
SYSTEM
When in theCustomer Usagemode of operation,
the system is armed when the vehicle is locked using
the:
²Power Door Lock Switches
²Remote Keyless Entry (RKE) Transmitter
²Key Cylinder Switches
DRVEHICLE THEFT SECURITY 8Q - 1
Page 693 of 2627
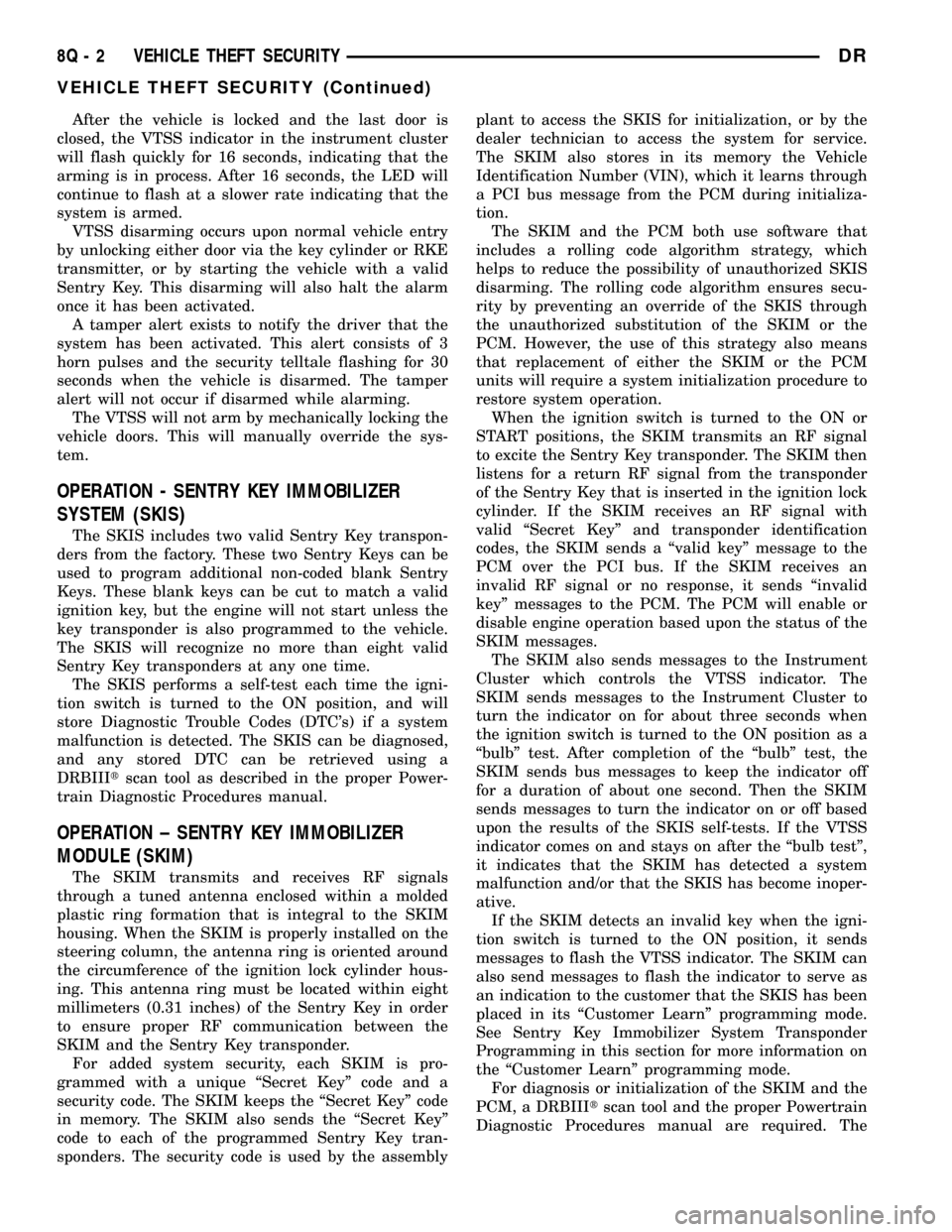
After the vehicle is locked and the last door is
closed, the VTSS indicator in the instrument cluster
will flash quickly for 16 seconds, indicating that the
arming is in process. After 16 seconds, the LED will
continue to flash at a slower rate indicating that the
system is armed.
VTSS disarming occurs upon normal vehicle entry
by unlocking either door via the key cylinder or RKE
transmitter, or by starting the vehicle with a valid
Sentry Key. This disarming will also halt the alarm
once it has been activated.
A tamper alert exists to notify the driver that the
system has been activated. This alert consists of 3
horn pulses and the security telltale flashing for 30
seconds when the vehicle is disarmed. The tamper
alert will not occur if disarmed while alarming.
The VTSS will not arm by mechanically locking the
vehicle doors. This will manually override the sys-
tem.
OPERATION - SENTRY KEY IMMOBILIZER
SYSTEM (SKIS)
The SKIS includes two valid Sentry Key transpon-
ders from the factory. These two Sentry Keys can be
used to program additional non-coded blank Sentry
Keys. These blank keys can be cut to match a valid
ignition key, but the engine will not start unless the
key transponder is also programmed to the vehicle.
The SKIS will recognize no more than eight valid
Sentry Key transponders at any one time.
The SKIS performs a self-test each time the igni-
tion switch is turned to the ON position, and will
store Diagnostic Trouble Codes (DTC's) if a system
malfunction is detected. The SKIS can be diagnosed,
and any stored DTC can be retrieved using a
DRBIIItscan tool as described in the proper Power-
train Diagnostic Procedures manual.
OPERATION ± SENTRY KEY IMMOBILIZER
MODULE (SKIM)
The SKIM transmits and receives RF signals
through a tuned antenna enclosed within a molded
plastic ring formation that is integral to the SKIM
housing. When the SKIM is properly installed on the
steering column, the antenna ring is oriented around
the circumference of the ignition lock cylinder hous-
ing. This antenna ring must be located within eight
millimeters (0.31 inches) of the Sentry Key in order
to ensure proper RF communication between the
SKIM and the Sentry Key transponder.
For added system security, each SKIM is pro-
grammed with a unique ªSecret Keyº code and a
security code. The SKIM keeps the ªSecret Keyº code
in memory. The SKIM also sends the ªSecret Keyº
code to each of the programmed Sentry Key tran-
sponders. The security code is used by the assemblyplant to access the SKIS for initialization, or by the
dealer technician to access the system for service.
The SKIM also stores in its memory the Vehicle
Identification Number (VIN), which it learns through
a PCI bus message from the PCM during initializa-
tion.
The SKIM and the PCM both use software that
includes a rolling code algorithm strategy, which
helps to reduce the possibility of unauthorized SKIS
disarming. The rolling code algorithm ensures secu-
rity by preventing an override of the SKIS through
the unauthorized substitution of the SKIM or the
PCM. However, the use of this strategy also means
that replacement of either the SKIM or the PCM
units will require a system initialization procedure to
restore system operation.
When the ignition switch is turned to the ON or
START positions, the SKIM transmits an RF signal
to excite the Sentry Key transponder. The SKIM then
listens for a return RF signal from the transponder
of the Sentry Key that is inserted in the ignition lock
cylinder. If the SKIM receives an RF signal with
valid ªSecret Keyº and transponder identification
codes, the SKIM sends a ªvalid keyº message to the
PCM over the PCI bus. If the SKIM receives an
invalid RF signal or no response, it sends ªinvalid
keyº messages to the PCM. The PCM will enable or
disable engine operation based upon the status of the
SKIM messages.
The SKIM also sends messages to the Instrument
Cluster which controls the VTSS indicator. The
SKIM sends messages to the Instrument Cluster to
turn the indicator on for about three seconds when
the ignition switch is turned to the ON position as a
ªbulbº test. After completion of the ªbulbº test, the
SKIM sends bus messages to keep the indicator off
for a duration of about one second. Then the SKIM
sends messages to turn the indicator on or off based
upon the results of the SKIS self-tests. If the VTSS
indicator comes on and stays on after the ªbulb testº,
it indicates that the SKIM has detected a system
malfunction and/or that the SKIS has become inoper-
ative.
If the SKIM detects an invalid key when the igni-
tion switch is turned to the ON position, it sends
messages to flash the VTSS indicator. The SKIM can
also send messages to flash the indicator to serve as
an indication to the customer that the SKIS has been
placed in its ªCustomer Learnº programming mode.
See Sentry Key Immobilizer System Transponder
Programming in this section for more information on
the ªCustomer Learnº programming mode.
For diagnosis or initialization of the SKIM and the
PCM, a DRBIIItscan tool and the proper Powertrain
Diagnostic Procedures manual are required. The
8Q - 2 VEHICLE THEFT SECURITYDR
VEHICLE THEFT SECURITY (Continued)
Page 695 of 2627
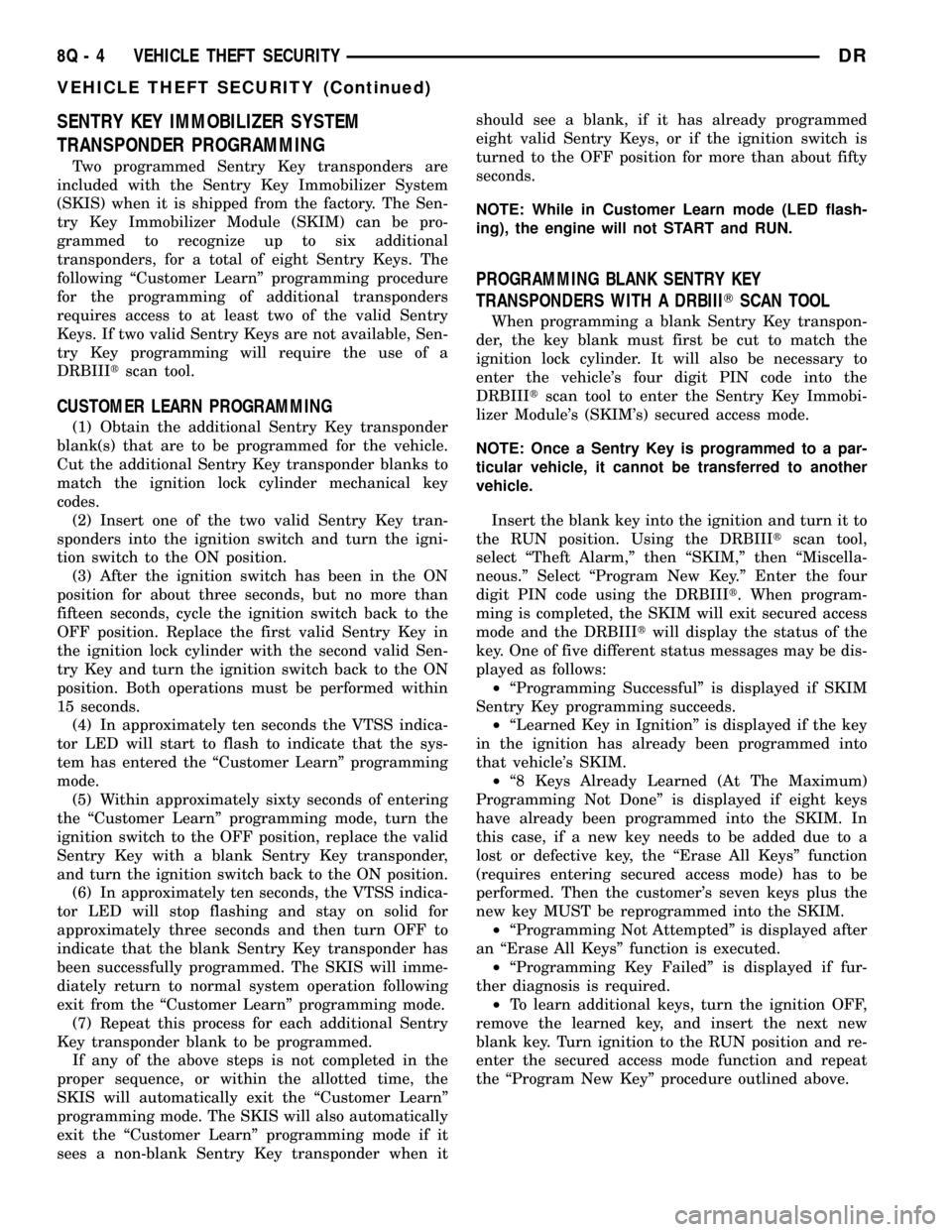
SENTRY KEY IMMOBILIZER SYSTEM
TRANSPONDER PROGRAMMING
Two programmed Sentry Key transponders are
included with the Sentry Key Immobilizer System
(SKIS) when it is shipped from the factory. The Sen-
try Key Immobilizer Module (SKIM) can be pro-
grammed to recognize up to six additional
transponders, for a total of eight Sentry Keys. The
following ªCustomer Learnº programming procedure
for the programming of additional transponders
requires access to at least two of the valid Sentry
Keys. If two valid Sentry Keys are not available, Sen-
try Key programming will require the use of a
DRBIIItscan tool.
CUSTOMER LEARN PROGRAMMING
(1) Obtain the additional Sentry Key transponder
blank(s) that are to be programmed for the vehicle.
Cut the additional Sentry Key transponder blanks to
match the ignition lock cylinder mechanical key
codes.
(2) Insert one of the two valid Sentry Key tran-
sponders into the ignition switch and turn the igni-
tion switch to the ON position.
(3) After the ignition switch has been in the ON
position for about three seconds, but no more than
fifteen seconds, cycle the ignition switch back to the
OFF position. Replace the first valid Sentry Key in
the ignition lock cylinder with the second valid Sen-
try Key and turn the ignition switch back to the ON
position. Both operations must be performed within
15 seconds.
(4) In approximately ten seconds the VTSS indica-
tor LED will start to flash to indicate that the sys-
tem has entered the ªCustomer Learnº programming
mode.
(5) Within approximately sixty seconds of entering
the ªCustomer Learnº programming mode, turn the
ignition switch to the OFF position, replace the valid
Sentry Key with a blank Sentry Key transponder,
and turn the ignition switch back to the ON position.
(6) In approximately ten seconds, the VTSS indica-
tor LED will stop flashing and stay on solid for
approximately three seconds and then turn OFF to
indicate that the blank Sentry Key transponder has
been successfully programmed. The SKIS will imme-
diately return to normal system operation following
exit from the ªCustomer Learnº programming mode.
(7) Repeat this process for each additional Sentry
Key transponder blank to be programmed.
If any of the above steps is not completed in the
proper sequence, or within the allotted time, the
SKIS will automatically exit the ªCustomer Learnº
programming mode. The SKIS will also automatically
exit the ªCustomer Learnº programming mode if it
sees a non-blank Sentry Key transponder when itshould see a blank, if it has already programmed
eight valid Sentry Keys, or if the ignition switch is
turned to the OFF position for more than about fifty
seconds.
NOTE: While in Customer Learn mode (LED flash-
ing), the engine will not START and RUN.
PROGRAMMING BLANK SENTRY KEY
TRANSPONDERS WITH A DRBIIITSCAN TOOL
When programming a blank Sentry Key transpon-
der, the key blank must first be cut to match the
ignition lock cylinder. It will also be necessary to
enter the vehicle's four digit PIN code into the
DRBIIItscan tool to enter the Sentry Key Immobi-
lizer Module's (SKIM's) secured access mode.
NOTE: Once a Sentry Key is programmed to a par-
ticular vehicle, it cannot be transferred to another
vehicle.
Insert the blank key into the ignition and turn it to
the RUN position. Using the DRBIIItscan tool,
select ªTheft Alarm,º then ªSKIM,º then ªMiscella-
neous.º Select ªProgram New Key.º Enter the four
digit PIN code using the DRBIIIt. When program-
ming is completed, the SKIM will exit secured access
mode and the DRBIIItwill display the status of the
key. One of five different status messages may be dis-
played as follows:
²ªProgramming Successfulº is displayed if SKIM
Sentry Key programming succeeds.
²ªLearned Key in Ignitionº is displayed if the key
in the ignition has already been programmed into
that vehicle's SKIM.
²ª8 Keys Already Learned (At The Maximum)
Programming Not Doneº is displayed if eight keys
have already been programmed into the SKIM. In
this case, if a new key needs to be added due to a
lost or defective key, the ªErase All Keysº function
(requires entering secured access mode) has to be
performed. Then the customer's seven keys plus the
new key MUST be reprogrammed into the SKIM.
²ªProgramming Not Attemptedº is displayed after
an ªErase All Keysº function is executed.
²ªProgramming Key Failedº is displayed if fur-
ther diagnosis is required.
²To learn additional keys, turn the ignition OFF,
remove the learned key, and insert the next new
blank key. Turn ignition to the RUN position and re-
enter the secured access mode function and repeat
the ªProgram New Keyº procedure outlined above.
8Q - 4 VEHICLE THEFT SECURITYDR
VEHICLE THEFT SECURITY (Continued)
Page 698 of 2627
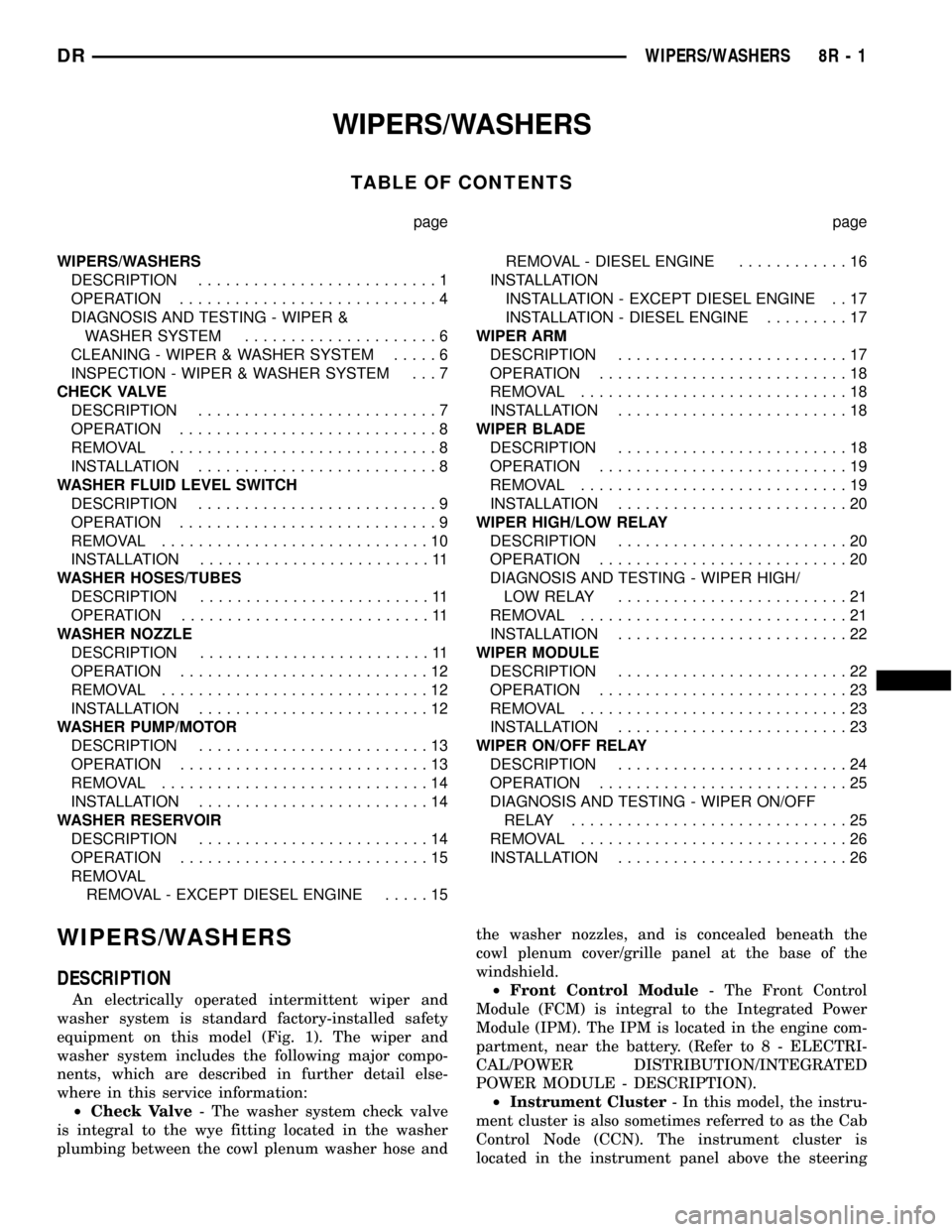
WIPERS/WASHERS
TABLE OF CONTENTS
page page
WIPERS/WASHERS
DESCRIPTION..........................1
OPERATION............................4
DIAGNOSIS AND TESTING - WIPER &
WASHER SYSTEM.....................6
CLEANING - WIPER & WASHER SYSTEM.....6
INSPECTION - WIPER & WASHER SYSTEM . . . 7
CHECK VALVE
DESCRIPTION..........................7
OPERATION............................8
REMOVAL.............................8
INSTALLATION..........................8
WASHER FLUID LEVEL SWITCH
DESCRIPTION..........................9
OPERATION............................9
REMOVAL.............................10
INSTALLATION.........................11
WASHER HOSES/TUBES
DESCRIPTION.........................11
OPERATION...........................11
WASHER NOZZLE
DESCRIPTION.........................11
OPERATION...........................12
REMOVAL.............................12
INSTALLATION.........................12
WASHER PUMP/MOTOR
DESCRIPTION.........................13
OPERATION...........................13
REMOVAL.............................14
INSTALLATION.........................14
WASHER RESERVOIR
DESCRIPTION.........................14
OPERATION...........................15
REMOVAL
REMOVAL - EXCEPT DIESEL ENGINE.....15REMOVAL - DIESEL ENGINE............16
INSTALLATION
INSTALLATION - EXCEPT DIESEL ENGINE . . 17
INSTALLATION - DIESEL ENGINE.........17
WIPER ARM
DESCRIPTION.........................17
OPERATION...........................18
REMOVAL.............................18
INSTALLATION.........................18
WIPER BLADE
DESCRIPTION.........................18
OPERATION...........................19
REMOVAL.............................19
INSTALLATION.........................20
WIPER HIGH/LOW RELAY
DESCRIPTION.........................20
OPERATION...........................20
DIAGNOSIS AND TESTING - WIPER HIGH/
LOW RELAY.........................21
REMOVAL.............................21
INSTALLATION.........................22
WIPER MODULE
DESCRIPTION.........................22
OPERATION...........................23
REMOVAL.............................23
INSTALLATION.........................23
WIPER ON/OFF RELAY
DESCRIPTION.........................24
OPERATION...........................25
DIAGNOSIS AND TESTING - WIPER ON/OFF
RELAY..............................25
REMOVAL.............................26
INSTALLATION.........................26
WIPERS/WASHERS
DESCRIPTION
An electrically operated intermittent wiper and
washer system is standard factory-installed safety
equipment on this model (Fig. 1). The wiper and
washer system includes the following major compo-
nents, which are described in further detail else-
where in this service information:
²Check Valve- The washer system check valve
is integral to the wye fitting located in the washer
plumbing between the cowl plenum washer hose andthe washer nozzles, and is concealed beneath the
cowl plenum cover/grille panel at the base of the
windshield.
²Front Control Module- The Front Control
Module (FCM) is integral to the Integrated Power
Module (IPM). The IPM is located in the engine com-
partment, near the battery. (Refer to 8 - ELECTRI-
CAL/POWER DISTRIBUTION/INTEGRATED
POWER MODULE - DESCRIPTION).
²Instrument Cluster- In this model, the instru-
ment cluster is also sometimes referred to as the Cab
Control Node (CCN). The instrument cluster is
located in the instrument panel above the steering
DRWIPERS/WASHERS 8R - 1
Page 699 of 2627
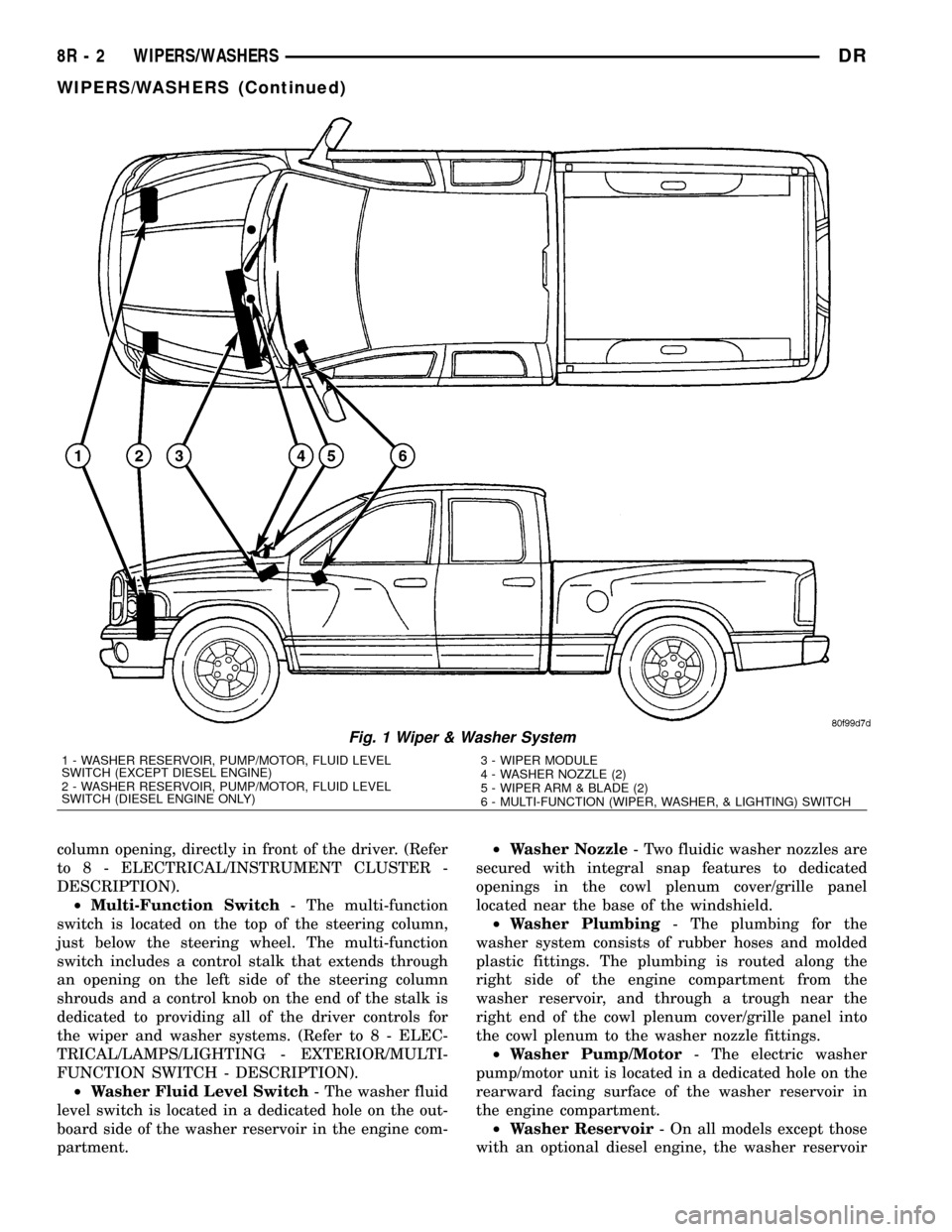
column opening, directly in front of the driver. (Refer
to 8 - ELECTRICAL/INSTRUMENT CLUSTER -
DESCRIPTION).
²Multi-Function Switch- The multi-function
switch is located on the top of the steering column,
just below the steering wheel. The multi-function
switch includes a control stalk that extends through
an opening on the left side of the steering column
shrouds and a control knob on the end of the stalk is
dedicated to providing all of the driver controls for
the wiper and washer systems. (Refer to 8 - ELEC-
TRICAL/LAMPS/LIGHTING - EXTERIOR/MULTI-
FUNCTION SWITCH - DESCRIPTION).
²Washer Fluid Level Switch- The washer fluid
level switch is located in a dedicated hole on the out-
board side of the washer reservoir in the engine com-
partment.²Washer Nozzle- Two fluidic washer nozzles are
secured with integral snap features to dedicated
openings in the cowl plenum cover/grille panel
located near the base of the windshield.
²Washer Plumbing- The plumbing for the
washer system consists of rubber hoses and molded
plastic fittings. The plumbing is routed along the
right side of the engine compartment from the
washer reservoir, and through a trough near the
right end of the cowl plenum cover/grille panel into
the cowl plenum to the washer nozzle fittings.
²Washer Pump/Motor- The electric washer
pump/motor unit is located in a dedicated hole on the
rearward facing surface of the washer reservoir in
the engine compartment.
²Washer Reservoir- On all models except those
with an optional diesel engine, the washer reservoir
Fig. 1 Wiper & Washer System
1 - WASHER RESERVOIR, PUMP/MOTOR, FLUID LEVEL
SWITCH (EXCEPT DIESEL ENGINE)
2 - WASHER RESERVOIR, PUMP/MOTOR, FLUID LEVEL
SWITCH (DIESEL ENGINE ONLY)3 - WIPER MODULE
4 - WASHER NOZZLE (2)
5 - WIPER ARM & BLADE (2)
6 - MULTI-FUNCTION (WIPER, WASHER, & LIGHTING) SWITCH
8R - 2 WIPERS/WASHERSDR
WIPERS/WASHERS (Continued)
Page 700 of 2627
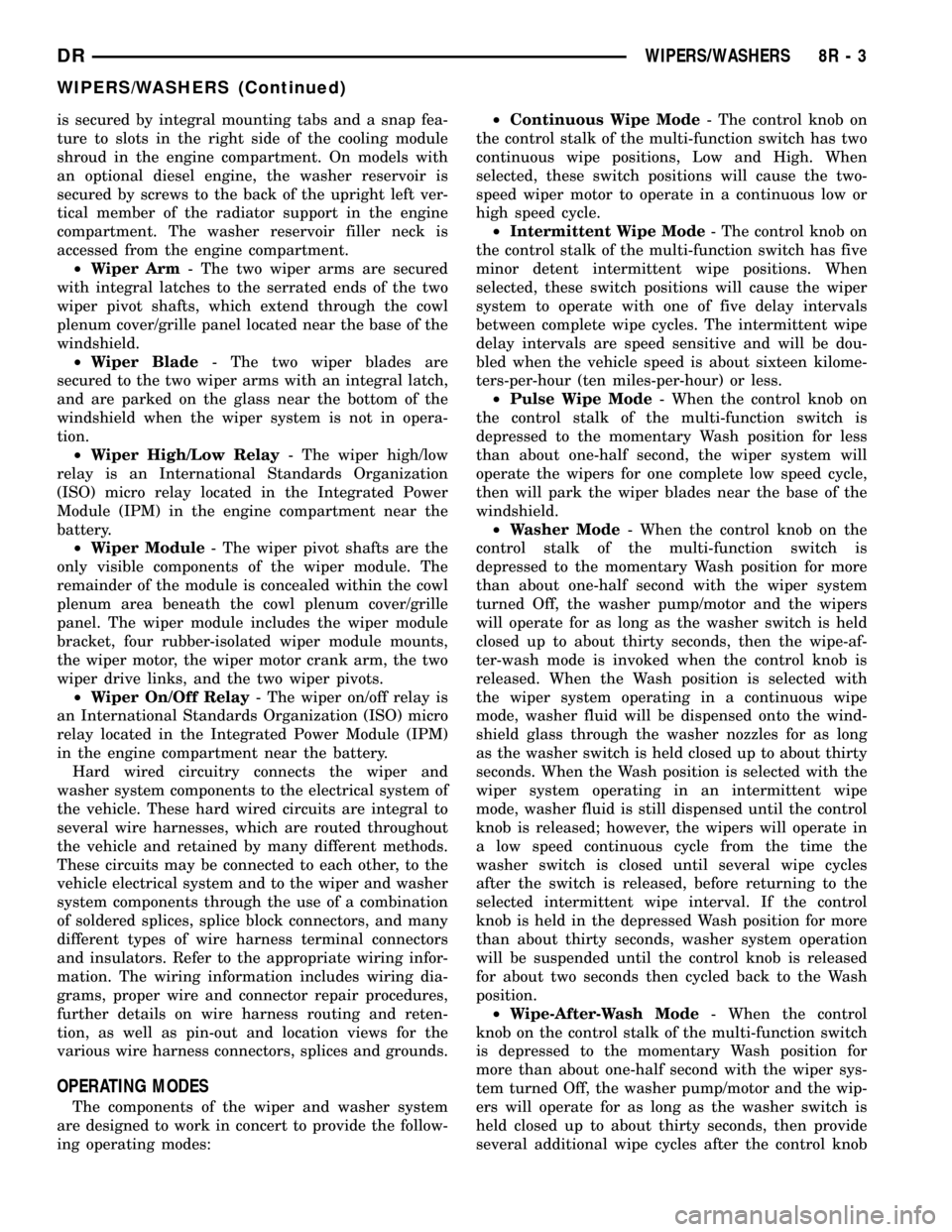
is secured by integral mounting tabs and a snap fea-
ture to slots in the right side of the cooling module
shroud in the engine compartment. On models with
an optional diesel engine, the washer reservoir is
secured by screws to the back of the upright left ver-
tical member of the radiator support in the engine
compartment. The washer reservoir filler neck is
accessed from the engine compartment.
²Wiper Arm- The two wiper arms are secured
with integral latches to the serrated ends of the two
wiper pivot shafts, which extend through the cowl
plenum cover/grille panel located near the base of the
windshield.
²Wiper Blade- The two wiper blades are
secured to the two wiper arms with an integral latch,
and are parked on the glass near the bottom of the
windshield when the wiper system is not in opera-
tion.
²Wiper High/Low Relay- The wiper high/low
relay is an International Standards Organization
(ISO) micro relay located in the Integrated Power
Module (IPM) in the engine compartment near the
battery.
²Wiper Module- The wiper pivot shafts are the
only visible components of the wiper module. The
remainder of the module is concealed within the cowl
plenum area beneath the cowl plenum cover/grille
panel. The wiper module includes the wiper module
bracket, four rubber-isolated wiper module mounts,
the wiper motor, the wiper motor crank arm, the two
wiper drive links, and the two wiper pivots.
²Wiper On/Off Relay- The wiper on/off relay is
an International Standards Organization (ISO) micro
relay located in the Integrated Power Module (IPM)
in the engine compartment near the battery.
Hard wired circuitry connects the wiper and
washer system components to the electrical system of
the vehicle. These hard wired circuits are integral to
several wire harnesses, which are routed throughout
the vehicle and retained by many different methods.
These circuits may be connected to each other, to the
vehicle electrical system and to the wiper and washer
system components through the use of a combination
of soldered splices, splice block connectors, and many
different types of wire harness terminal connectors
and insulators. Refer to the appropriate wiring infor-
mation. The wiring information includes wiring dia-
grams, proper wire and connector repair procedures,
further details on wire harness routing and reten-
tion, as well as pin-out and location views for the
various wire harness connectors, splices and grounds.
OPERATING MODES
The components of the wiper and washer system
are designed to work in concert to provide the follow-
ing operating modes:²Continuous Wipe Mode- The control knob on
the control stalk of the multi-function switch has two
continuous wipe positions, Low and High. When
selected, these switch positions will cause the two-
speed wiper motor to operate in a continuous low or
high speed cycle.
²Intermittent Wipe Mode- The control knob on
the control stalk of the multi-function switch has five
minor detent intermittent wipe positions. When
selected, these switch positions will cause the wiper
system to operate with one of five delay intervals
between complete wipe cycles. The intermittent wipe
delay intervals are speed sensitive and will be dou-
bled when the vehicle speed is about sixteen kilome-
ters-per-hour (ten miles-per-hour) or less.
²Pulse Wipe Mode- When the control knob on
the control stalk of the multi-function switch is
depressed to the momentary Wash position for less
than about one-half second, the wiper system will
operate the wipers for one complete low speed cycle,
then will park the wiper blades near the base of the
windshield.
²Washer Mode- When the control knob on the
control stalk of the multi-function switch is
depressed to the momentary Wash position for more
than about one-half second with the wiper system
turned Off, the washer pump/motor and the wipers
will operate for as long as the washer switch is held
closed up to about thirty seconds, then the wipe-af-
ter-wash mode is invoked when the control knob is
released. When the Wash position is selected with
the wiper system operating in a continuous wipe
mode, washer fluid will be dispensed onto the wind-
shield glass through the washer nozzles for as long
as the washer switch is held closed up to about thirty
seconds. When the Wash position is selected with the
wiper system operating in an intermittent wipe
mode, washer fluid is still dispensed until the control
knob is released; however, the wipers will operate in
a low speed continuous cycle from the time the
washer switch is closed until several wipe cycles
after the switch is released, before returning to the
selected intermittent wipe interval. If the control
knob is held in the depressed Wash position for more
than about thirty seconds, washer system operation
will be suspended until the control knob is released
for about two seconds then cycled back to the Wash
position.
²Wipe-After-Wash Mode- When the control
knob on the control stalk of the multi-function switch
is depressed to the momentary Wash position for
more than about one-half second with the wiper sys-
tem turned Off, the washer pump/motor and the wip-
ers will operate for as long as the washer switch is
held closed up to about thirty seconds, then provide
several additional wipe cycles after the control knob
DRWIPERS/WASHERS 8R - 3
WIPERS/WASHERS (Continued)
Page 705 of 2627
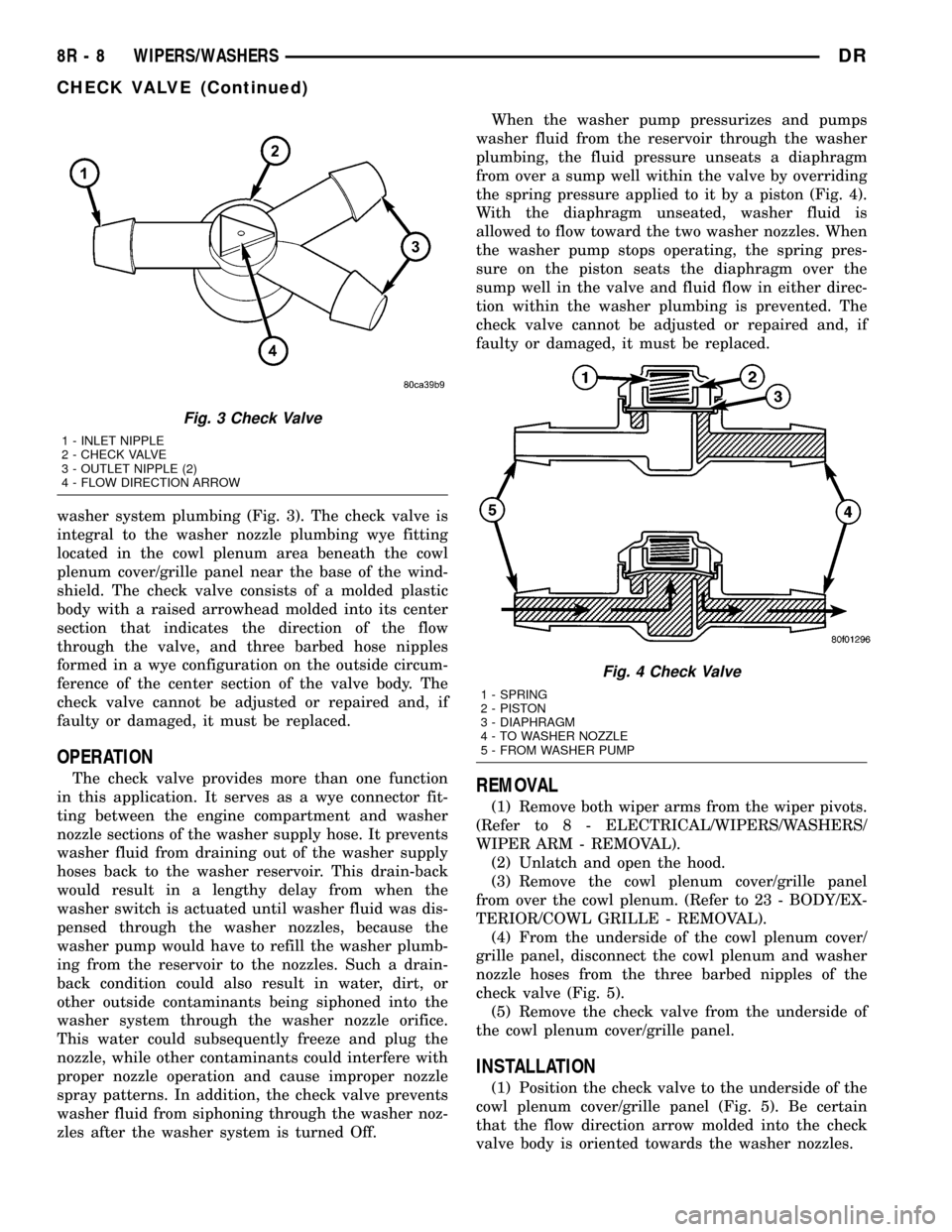
washer system plumbing (Fig. 3). The check valve is
integral to the washer nozzle plumbing wye fitting
located in the cowl plenum area beneath the cowl
plenum cover/grille panel near the base of the wind-
shield. The check valve consists of a molded plastic
body with a raised arrowhead molded into its center
section that indicates the direction of the flow
through the valve, and three barbed hose nipples
formed in a wye configuration on the outside circum-
ference of the center section of the valve body. The
check valve cannot be adjusted or repaired and, if
faulty or damaged, it must be replaced.
OPERATION
The check valve provides more than one function
in this application. It serves as a wye connector fit-
ting between the engine compartment and washer
nozzle sections of the washer supply hose. It prevents
washer fluid from draining out of the washer supply
hoses back to the washer reservoir. This drain-back
would result in a lengthy delay from when the
washer switch is actuated until washer fluid was dis-
pensed through the washer nozzles, because the
washer pump would have to refill the washer plumb-
ing from the reservoir to the nozzles. Such a drain-
back condition could also result in water, dirt, or
other outside contaminants being siphoned into the
washer system through the washer nozzle orifice.
This water could subsequently freeze and plug the
nozzle, while other contaminants could interfere with
proper nozzle operation and cause improper nozzle
spray patterns. In addition, the check valve prevents
washer fluid from siphoning through the washer noz-
zles after the washer system is turned Off.When the washer pump pressurizes and pumps
washer fluid from the reservoir through the washer
plumbing, the fluid pressure unseats a diaphragm
from over a sump well within the valve by overriding
the spring pressure applied to it by a piston (Fig. 4).
With the diaphragm unseated, washer fluid is
allowed to flow toward the two washer nozzles. When
the washer pump stops operating, the spring pres-
sure on the piston seats the diaphragm over the
sump well in the valve and fluid flow in either direc-
tion within the washer plumbing is prevented. The
check valve cannot be adjusted or repaired and, if
faulty or damaged, it must be replaced.REMOVAL
(1) Remove both wiper arms from the wiper pivots.
(Refer to 8 - ELECTRICAL/WIPERS/WASHERS/
WIPER ARM - REMOVAL).
(2) Unlatch and open the hood.
(3) Remove the cowl plenum cover/grille panel
from over the cowl plenum. (Refer to 23 - BODY/EX-
TERIOR/COWL GRILLE - REMOVAL).
(4) From the underside of the cowl plenum cover/
grille panel, disconnect the cowl plenum and washer
nozzle hoses from the three barbed nipples of the
check valve (Fig. 5).
(5) Remove the check valve from the underside of
the cowl plenum cover/grille panel.
INSTALLATION
(1) Position the check valve to the underside of the
cowl plenum cover/grille panel (Fig. 5). Be certain
that the flow direction arrow molded into the check
valve body is oriented towards the washer nozzles.
Fig. 3 Check Valve
1 - INLET NIPPLE
2 - CHECK VALVE
3 - OUTLET NIPPLE (2)
4 - FLOW DIRECTION ARROW
Fig. 4 Check Valve
1 - SPRING
2 - PISTON
3 - DIAPHRAGM
4 - TO WASHER NOZZLE
5 - FROM WASHER PUMP
8R - 8 WIPERS/WASHERSDR
CHECK VALVE (Continued)
Page 706 of 2627
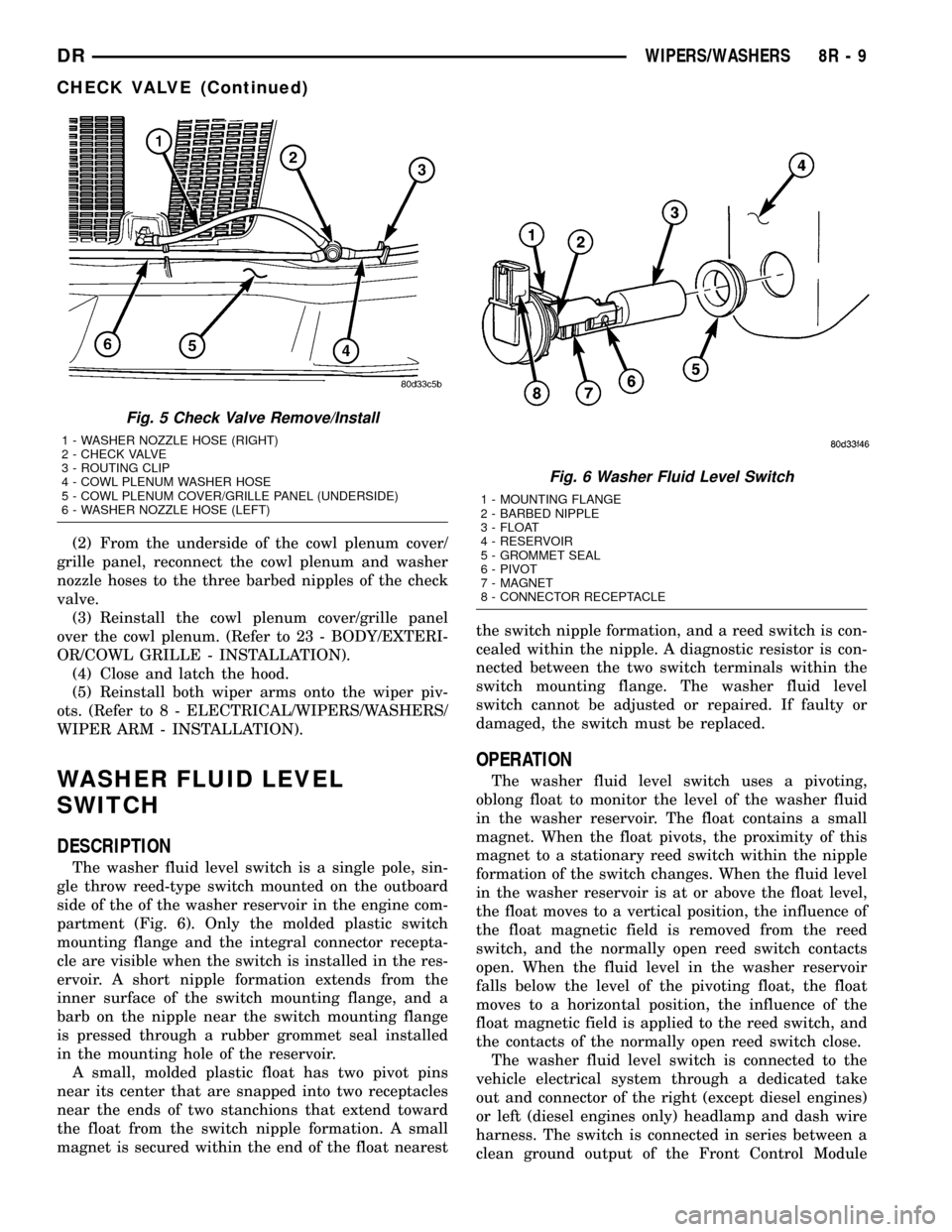
(2) From the underside of the cowl plenum cover/
grille panel, reconnect the cowl plenum and washer
nozzle hoses to the three barbed nipples of the check
valve.
(3) Reinstall the cowl plenum cover/grille panel
over the cowl plenum. (Refer to 23 - BODY/EXTERI-
OR/COWL GRILLE - INSTALLATION).
(4) Close and latch the hood.
(5) Reinstall both wiper arms onto the wiper piv-
ots. (Refer to 8 - ELECTRICAL/WIPERS/WASHERS/
WIPER ARM - INSTALLATION).
WASHER FLUID LEVEL
SWITCH
DESCRIPTION
The washer fluid level switch is a single pole, sin-
gle throw reed-type switch mounted on the outboard
side of the of the washer reservoir in the engine com-
partment (Fig. 6). Only the molded plastic switch
mounting flange and the integral connector recepta-
cle are visible when the switch is installed in the res-
ervoir. A short nipple formation extends from the
inner surface of the switch mounting flange, and a
barb on the nipple near the switch mounting flange
is pressed through a rubber grommet seal installed
in the mounting hole of the reservoir.
A small, molded plastic float has two pivot pins
near its center that are snapped into two receptacles
near the ends of two stanchions that extend toward
the float from the switch nipple formation. A small
magnet is secured within the end of the float nearestthe switch nipple formation, and a reed switch is con-
cealed within the nipple. A diagnostic resistor is con-
nected between the two switch terminals within the
switch mounting flange. The washer fluid level
switch cannot be adjusted or repaired. If faulty or
damaged, the switch must be replaced.
OPERATION
The washer fluid level switch uses a pivoting,
oblong float to monitor the level of the washer fluid
in the washer reservoir. The float contains a small
magnet. When the float pivots, the proximity of this
magnet to a stationary reed switch within the nipple
formation of the switch changes. When the fluid level
in the washer reservoir is at or above the float level,
the float moves to a vertical position, the influence of
the float magnetic field is removed from the reed
switch, and the normally open reed switch contacts
open. When the fluid level in the washer reservoir
falls below the level of the pivoting float, the float
moves to a horizontal position, the influence of the
float magnetic field is applied to the reed switch, and
the contacts of the normally open reed switch close.
The washer fluid level switch is connected to the
vehicle electrical system through a dedicated take
out and connector of the right (except diesel engines)
or left (diesel engines only) headlamp and dash wire
harness. The switch is connected in series between a
clean ground output of the Front Control Module
Fig. 5 Check Valve Remove/Install
1 - WASHER NOZZLE HOSE (RIGHT)
2 - CHECK VALVE
3 - ROUTING CLIP
4 - COWL PLENUM WASHER HOSE
5 - COWL PLENUM COVER/GRILLE PANEL (UNDERSIDE)
6 - WASHER NOZZLE HOSE (LEFT)
Fig. 6 Washer Fluid Level Switch
1 - MOUNTING FLANGE
2 - BARBED NIPPLE
3 - FLOAT
4 - RESERVOIR
5 - GROMMET SEAL
6 - PIVOT
7 - MAGNET
8 - CONNECTOR RECEPTACLE
DRWIPERS/WASHERS 8R - 9
CHECK VALVE (Continued)