Engine control 2 DODGE RAM 1500 1998 2.G Repair Manual
[x] Cancel search | Manufacturer: DODGE, Model Year: 1998, Model line: RAM 1500, Model: DODGE RAM 1500 1998 2.GPages: 2627
Page 471 of 2627
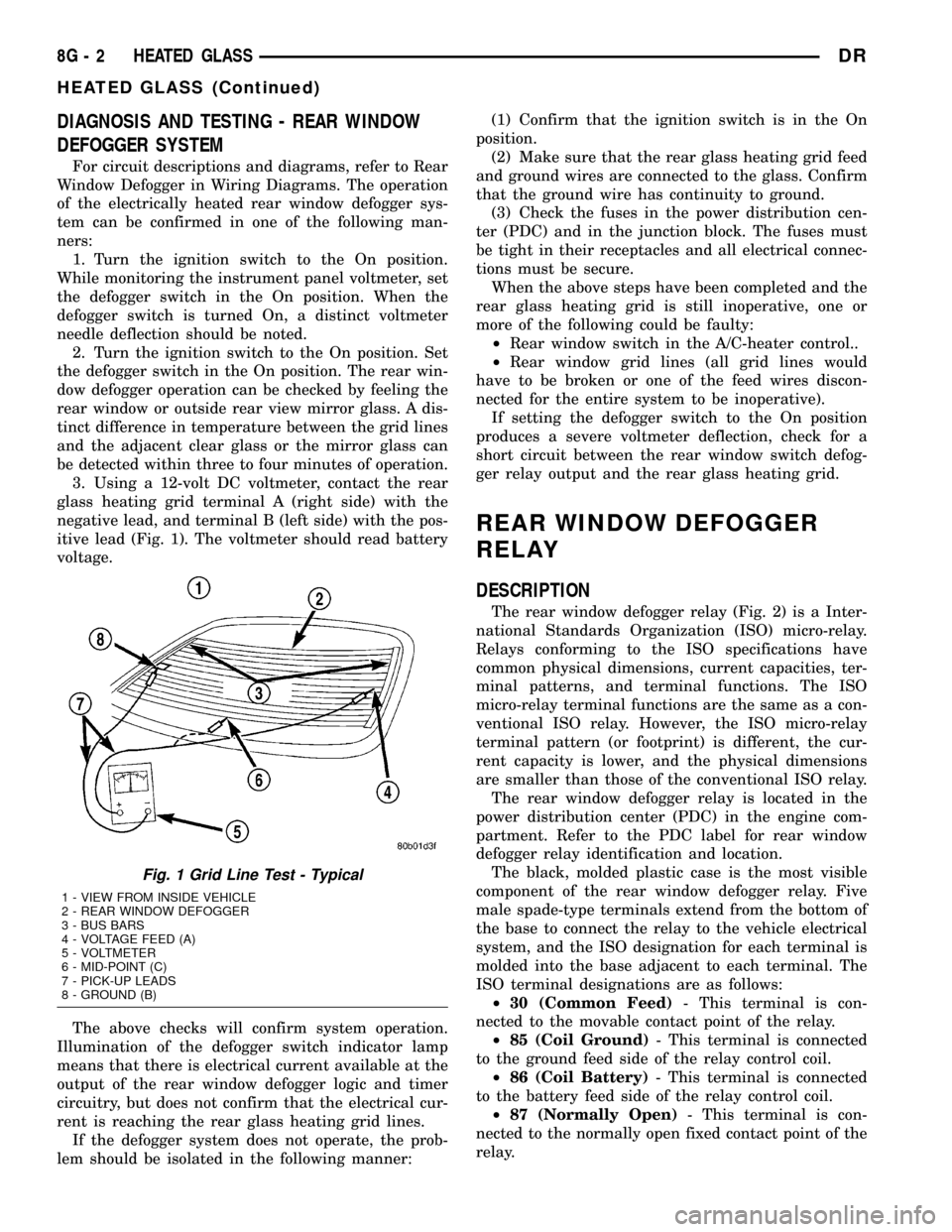
DIAGNOSIS AND TESTING - REAR WINDOW
DEFOGGER SYSTEM
For circuit descriptions and diagrams, refer to Rear
Window Defogger in Wiring Diagrams. The operation
of the electrically heated rear window defogger sys-
tem can be confirmed in one of the following man-
ners:
1. Turn the ignition switch to the On position.
While monitoring the instrument panel voltmeter, set
the defogger switch in the On position. When the
defogger switch is turned On, a distinct voltmeter
needle deflection should be noted.
2. Turn the ignition switch to the On position. Set
the defogger switch in the On position. The rear win-
dow defogger operation can be checked by feeling the
rear window or outside rear view mirror glass. A dis-
tinct difference in temperature between the grid lines
and the adjacent clear glass or the mirror glass can
be detected within three to four minutes of operation.
3. Using a 12-volt DC voltmeter, contact the rear
glass heating grid terminal A (right side) with the
negative lead, and terminal B (left side) with the pos-
itive lead (Fig. 1). The voltmeter should read battery
voltage.
The above checks will confirm system operation.
Illumination of the defogger switch indicator lamp
means that there is electrical current available at the
output of the rear window defogger logic and timer
circuitry, but does not confirm that the electrical cur-
rent is reaching the rear glass heating grid lines.
If the defogger system does not operate, the prob-
lem should be isolated in the following manner:(1) Confirm that the ignition switch is in the On
position.
(2) Make sure that the rear glass heating grid feed
and ground wires are connected to the glass. Confirm
that the ground wire has continuity to ground.
(3) Check the fuses in the power distribution cen-
ter (PDC) and in the junction block. The fuses must
be tight in their receptacles and all electrical connec-
tions must be secure.
When the above steps have been completed and the
rear glass heating grid is still inoperative, one or
more of the following could be faulty:
²Rear window switch in the A/C-heater control..
²Rear window grid lines (all grid lines would
have to be broken or one of the feed wires discon-
nected for the entire system to be inoperative).
If setting the defogger switch to the On position
produces a severe voltmeter deflection, check for a
short circuit between the rear window switch defog-
ger relay output and the rear glass heating grid.
REAR WINDOW DEFOGGER
RELAY
DESCRIPTION
The rear window defogger relay (Fig. 2) is a Inter-
national Standards Organization (ISO) micro-relay.
Relays conforming to the ISO specifications have
common physical dimensions, current capacities, ter-
minal patterns, and terminal functions. The ISO
micro-relay terminal functions are the same as a con-
ventional ISO relay. However, the ISO micro-relay
terminal pattern (or footprint) is different, the cur-
rent capacity is lower, and the physical dimensions
are smaller than those of the conventional ISO relay.
The rear window defogger relay is located in the
power distribution center (PDC) in the engine com-
partment. Refer to the PDC label for rear window
defogger relay identification and location.
The black, molded plastic case is the most visible
component of the rear window defogger relay. Five
male spade-type terminals extend from the bottom of
the base to connect the relay to the vehicle electrical
system, and the ISO designation for each terminal is
molded into the base adjacent to each terminal. The
ISO terminal designations are as follows:
²30 (Common Feed)- This terminal is con-
nected to the movable contact point of the relay.
²85 (Coil Ground)- This terminal is connected
to the ground feed side of the relay control coil.
²86 (Coil Battery)- This terminal is connected
to the battery feed side of the relay control coil.
²87 (Normally Open)- This terminal is con-
nected to the normally open fixed contact point of the
relay.
Fig. 1 Grid Line Test - Typical
1 - VIEW FROM INSIDE VEHICLE
2 - REAR WINDOW DEFOGGER
3 - BUS BARS
4 - VOLTAGE FEED (A)
5 - VOLTMETER
6 - MID-POINT (C)
7 - PICK-UP LEADS
8 - GROUND (B)
8G - 2 HEATED GLASSDR
HEATED GLASS (Continued)
Page 477 of 2627
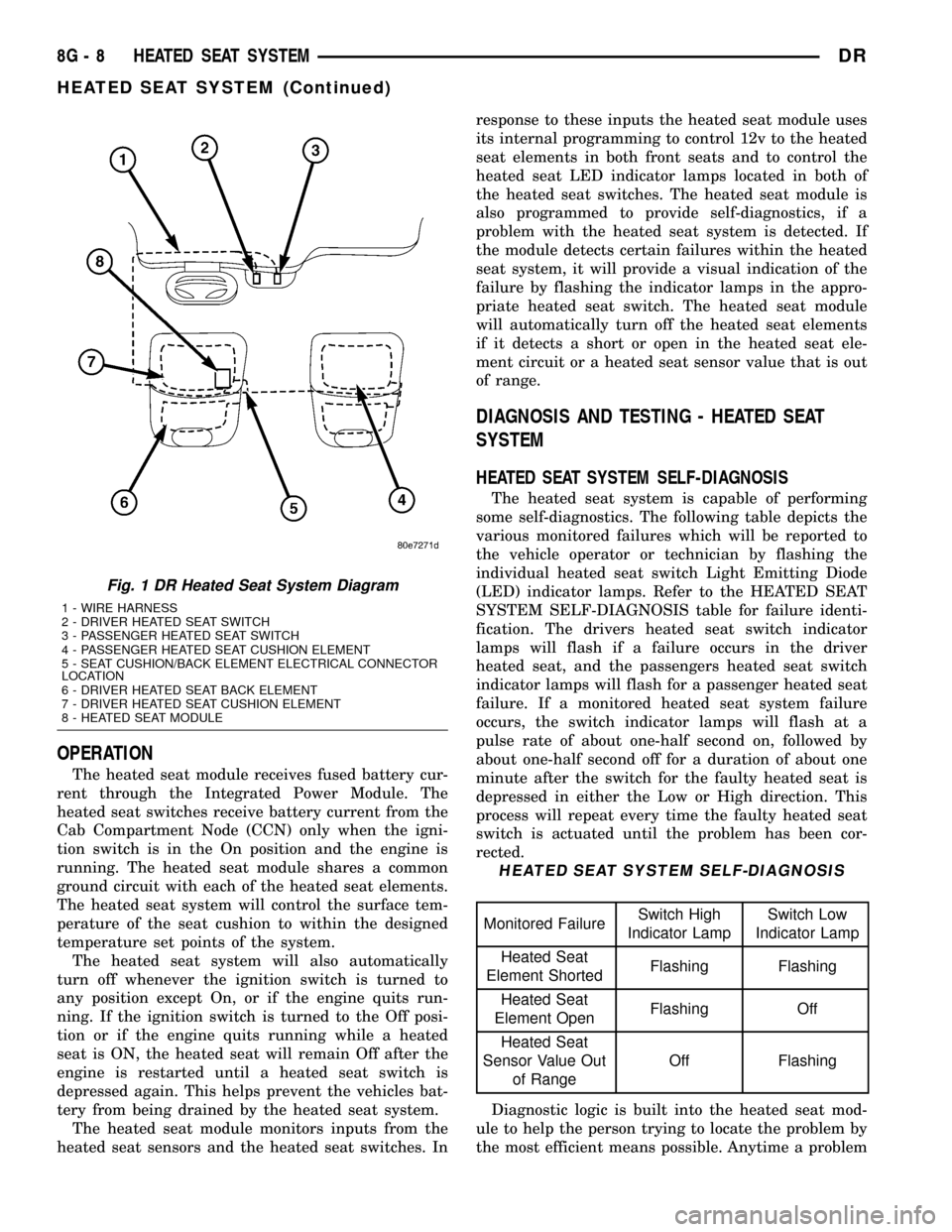
OPERATION
The heated seat module receives fused battery cur-
rent through the Integrated Power Module. The
heated seat switches receive battery current from the
Cab Compartment Node (CCN) only when the igni-
tion switch is in the On position and the engine is
running. The heated seat module shares a common
ground circuit with each of the heated seat elements.
The heated seat system will control the surface tem-
perature of the seat cushion to within the designed
temperature set points of the system.
The heated seat system will also automatically
turn off whenever the ignition switch is turned to
any position except On, or if the engine quits run-
ning. If the ignition switch is turned to the Off posi-
tion or if the engine quits running while a heated
seat is ON, the heated seat will remain Off after the
engine is restarted until a heated seat switch is
depressed again. This helps prevent the vehicles bat-
tery from being drained by the heated seat system.
The heated seat module monitors inputs from the
heated seat sensors and the heated seat switches. Inresponse to these inputs the heated seat module uses
its internal programming to control 12v to the heated
seat elements in both front seats and to control the
heated seat LED indicator lamps located in both of
the heated seat switches. The heated seat module is
also programmed to provide self-diagnostics, if a
problem with the heated seat system is detected. If
the module detects certain failures within the heated
seat system, it will provide a visual indication of the
failure by flashing the indicator lamps in the appro-
priate heated seat switch. The heated seat module
will automatically turn off the heated seat elements
if it detects a short or open in the heated seat ele-
ment circuit or a heated seat sensor value that is out
of range.
DIAGNOSIS AND TESTING - HEATED SEAT
SYSTEM
HEATED SEAT SYSTEM SELF-DIAGNOSIS
The heated seat system is capable of performing
some self-diagnostics. The following table depicts the
various monitored failures which will be reported to
the vehicle operator or technician by flashing the
individual heated seat switch Light Emitting Diode
(LED) indicator lamps. Refer to the HEATED SEAT
SYSTEM SELF-DIAGNOSIS table for failure identi-
fication. The drivers heated seat switch indicator
lamps will flash if a failure occurs in the driver
heated seat, and the passengers heated seat switch
indicator lamps will flash for a passenger heated seat
failure. If a monitored heated seat system failure
occurs, the switch indicator lamps will flash at a
pulse rate of about one-half second on, followed by
about one-half second off for a duration of about one
minute after the switch for the faulty heated seat is
depressed in either the Low or High direction. This
process will repeat every time the faulty heated seat
switch is actuated until the problem has been cor-
rected.
HEATED SEAT SYSTEM SELF-DIAGNOSIS
Monitored FailureSwitch High
Indicator LampSwitch Low
Indicator Lamp
Heated Seat
Element ShortedFlashing Flashing
Heated Seat
Element OpenFlashing Off
Heated Seat
Sensor Value Out
of RangeOff Flashing
Diagnostic logic is built into the heated seat mod-
ule to help the person trying to locate the problem by
the most efficient means possible. Anytime a problem
Fig. 1 DR Heated Seat System Diagram
1 - WIRE HARNESS
2 - DRIVER HEATED SEAT SWITCH
3 - PASSENGER HEATED SEAT SWITCH
4 - PASSENGER HEATED SEAT CUSHION ELEMENT
5 - SEAT CUSHION/BACK ELEMENT ELECTRICAL CONNECTOR
LOCATION
6 - DRIVER HEATED SEAT BACK ELEMENT
7 - DRIVER HEATED SEAT CUSHION ELEMENT
8 - HEATED SEAT MODULE
8G - 8 HEATED SEAT SYSTEMDR
HEATED SEAT SYSTEM (Continued)
Page 488 of 2627
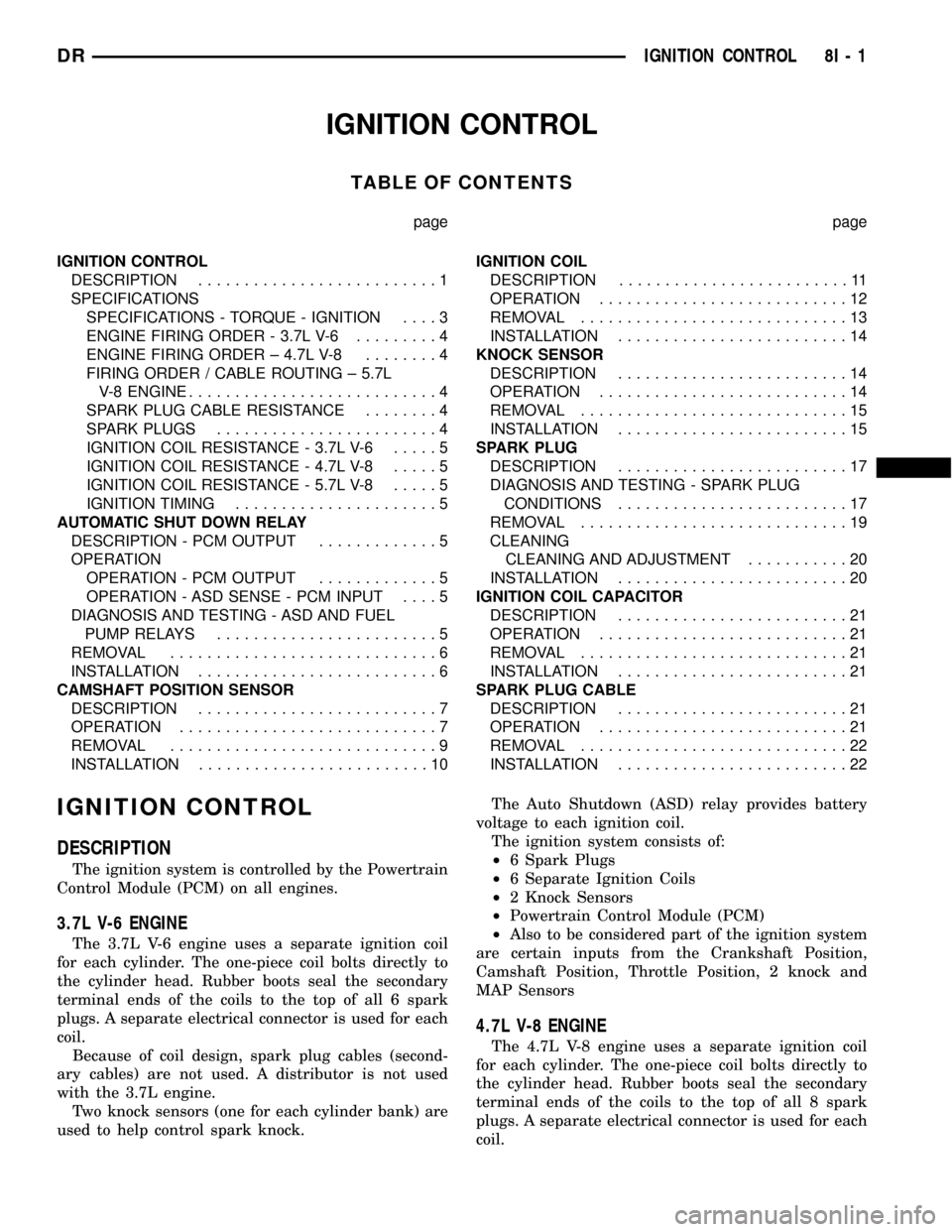
IGNITION CONTROL
TABLE OF CONTENTS
page page
IGNITION CONTROL
DESCRIPTION..........................1
SPECIFICATIONS
SPECIFICATIONS - TORQUE - IGNITION....3
ENGINE FIRING ORDER - 3.7L V-6.........4
ENGINE FIRING ORDER ± 4.7L V-8........4
FIRING ORDER / CABLE ROUTING ± 5.7L
V-8 ENGINE...........................4
SPARK PLUG CABLE RESISTANCE........4
SPARK PLUGS........................4
IGNITION COIL RESISTANCE - 3.7L V-6.....5
IGNITION COIL RESISTANCE - 4.7L V-8.....5
IGNITION COIL RESISTANCE - 5.7L V-8.....5
IGNITION TIMING......................5
AUTOMATIC SHUT DOWN RELAY
DESCRIPTION - PCM OUTPUT.............5
OPERATION
OPERATION - PCM OUTPUT.............5
OPERATION - ASD SENSE - PCM INPUT....5
DIAGNOSIS AND TESTING - ASD AND FUEL
PUMP RELAYS........................5
REMOVAL.............................6
INSTALLATION..........................6
CAMSHAFT POSITION SENSOR
DESCRIPTION..........................7
OPERATION............................7
REMOVAL.............................9
INSTALLATION.........................10IGNITION COIL
DESCRIPTION.........................11
OPERATION...........................12
REMOVAL.............................13
INSTALLATION.........................14
KNOCK SENSOR
DESCRIPTION.........................14
OPERATION...........................14
REMOVAL.............................15
INSTALLATION.........................15
SPARK PLUG
DESCRIPTION.........................17
DIAGNOSIS AND TESTING - SPARK PLUG
CONDITIONS.........................17
REMOVAL.............................19
CLEANING
CLEANING AND ADJUSTMENT...........20
INSTALLATION.........................20
IGNITION COIL CAPACITOR
DESCRIPTION.........................21
OPERATION...........................21
REMOVAL.............................21
INSTALLATION.........................21
SPARK PLUG CABLE
DESCRIPTION.........................21
OPERATION...........................21
REMOVAL.............................22
INSTALLATION.........................22
IGNITION CONTROL
DESCRIPTION
The ignition system is controlled by the Powertrain
Control Module (PCM) on all engines.
3.7L V-6 ENGINE
The 3.7L V-6 engine uses a separate ignition coil
for each cylinder. The one-piece coil bolts directly to
the cylinder head. Rubber boots seal the secondary
terminal ends of the coils to the top of all 6 spark
plugs. A separate electrical connector is used for each
coil.
Because of coil design, spark plug cables (second-
ary cables) are not used. A distributor is not used
with the 3.7L engine.
Two knock sensors (one for each cylinder bank) are
used to help control spark knock.The Auto Shutdown (ASD) relay provides battery
voltage to each ignition coil.
The ignition system consists of:
²6 Spark Plugs
²6 Separate Ignition Coils
²2 Knock Sensors
²Powertrain Control Module (PCM)
²Also to be considered part of the ignition system
are certain inputs from the Crankshaft Position,
Camshaft Position, Throttle Position, 2 knock and
MAP Sensors
4.7L V-8 ENGINE
The 4.7L V-8 engine uses a separate ignition coil
for each cylinder. The one-piece coil bolts directly to
the cylinder head. Rubber boots seal the secondary
terminal ends of the coils to the top of all 8 spark
plugs. A separate electrical connector is used for each
coil.
DRIGNITION CONTROL 8I - 1
Page 489 of 2627
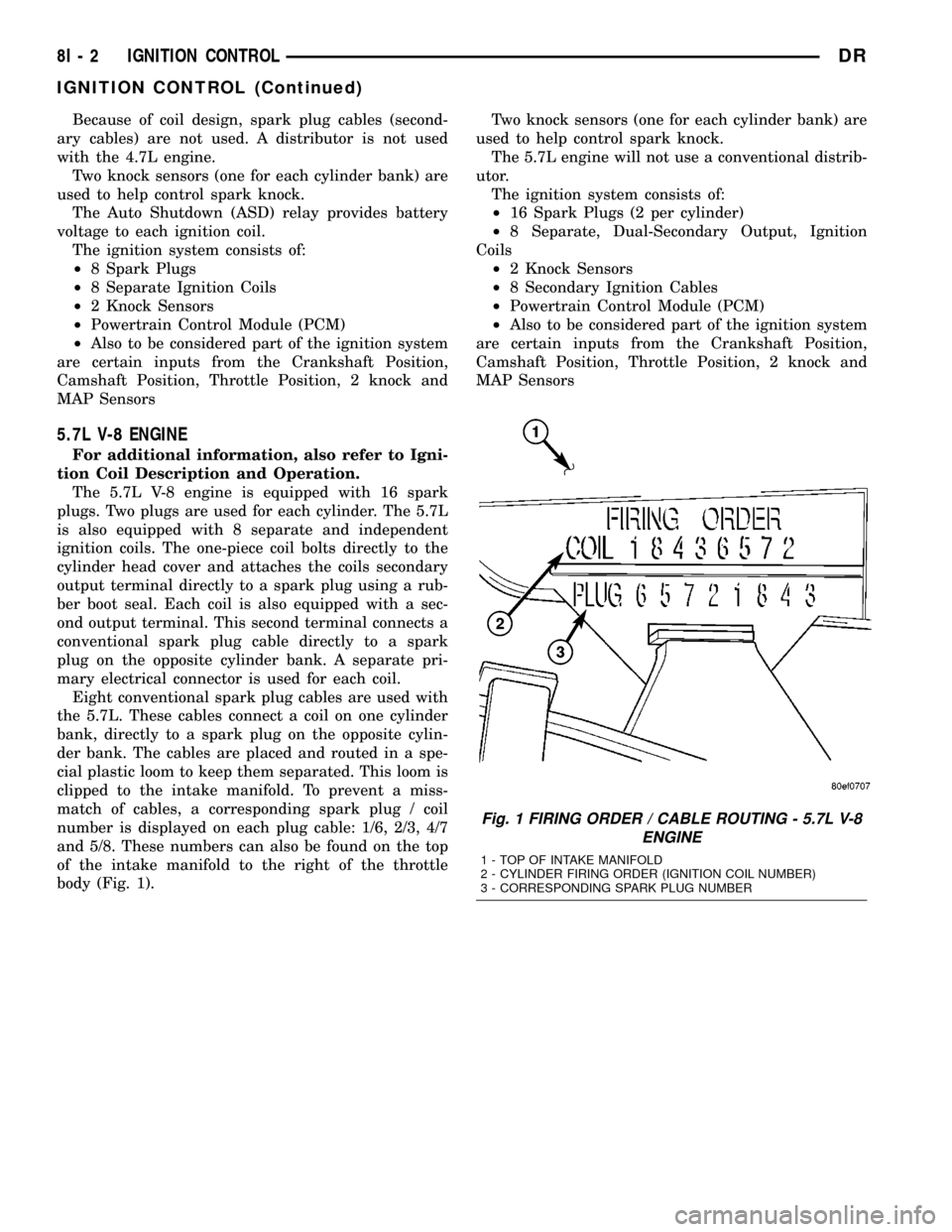
Because of coil design, spark plug cables (second-
ary cables) are not used. A distributor is not used
with the 4.7L engine.
Two knock sensors (one for each cylinder bank) are
used to help control spark knock.
The Auto Shutdown (ASD) relay provides battery
voltage to each ignition coil.
The ignition system consists of:
²8 Spark Plugs
²8 Separate Ignition Coils
²2 Knock Sensors
²Powertrain Control Module (PCM)
²Also to be considered part of the ignition system
are certain inputs from the Crankshaft Position,
Camshaft Position, Throttle Position, 2 knock and
MAP Sensors
5.7L V-8 ENGINE
For additional information, also refer to Igni-
tion Coil Description and Operation.
The 5.7L V-8 engine is equipped with 16 spark
plugs. Two plugs are used for each cylinder. The 5.7L
is also equipped with 8 separate and independent
ignition coils. The one-piece coil bolts directly to the
cylinder head cover and attaches the coils secondary
output terminal directly to a spark plug using a rub-
ber boot seal. Each coil is also equipped with a sec-
ond output terminal. This second terminal connects a
conventional spark plug cable directly to a spark
plug on the opposite cylinder bank. A separate pri-
mary electrical connector is used for each coil.
Eight conventional spark plug cables are used with
the 5.7L. These cables connect a coil on one cylinder
bank, directly to a spark plug on the opposite cylin-
der bank. The cables are placed and routed in a spe-
cial plastic loom to keep them separated. This loom is
clipped to the intake manifold. To prevent a miss-
match of cables, a corresponding spark plug / coil
number is displayed on each plug cable: 1/6, 2/3, 4/7
and 5/8. These numbers can also be found on the top
of the intake manifold to the right of the throttle
body (Fig. 1).Two knock sensors (one for each cylinder bank) are
used to help control spark knock.
The 5.7L engine will not use a conventional distrib-
utor.
The ignition system consists of:
²16 Spark Plugs (2 per cylinder)
²8 Separate, Dual-Secondary Output, Ignition
Coils
²2 Knock Sensors
²8 Secondary Ignition Cables
²Powertrain Control Module (PCM)
²Also to be considered part of the ignition system
are certain inputs from the Crankshaft Position,
Camshaft Position, Throttle Position, 2 knock and
MAP Sensors
Fig. 1 FIRING ORDER / CABLE ROUTING - 5.7L V-8
ENGINE
1 - TOP OF INTAKE MANIFOLD
2 - CYLINDER FIRING ORDER (IGNITION COIL NUMBER)
3 - CORRESPONDING SPARK PLUG NUMBER
8I - 2 IGNITION CONTROLDR
IGNITION CONTROL (Continued)
Page 490 of 2627
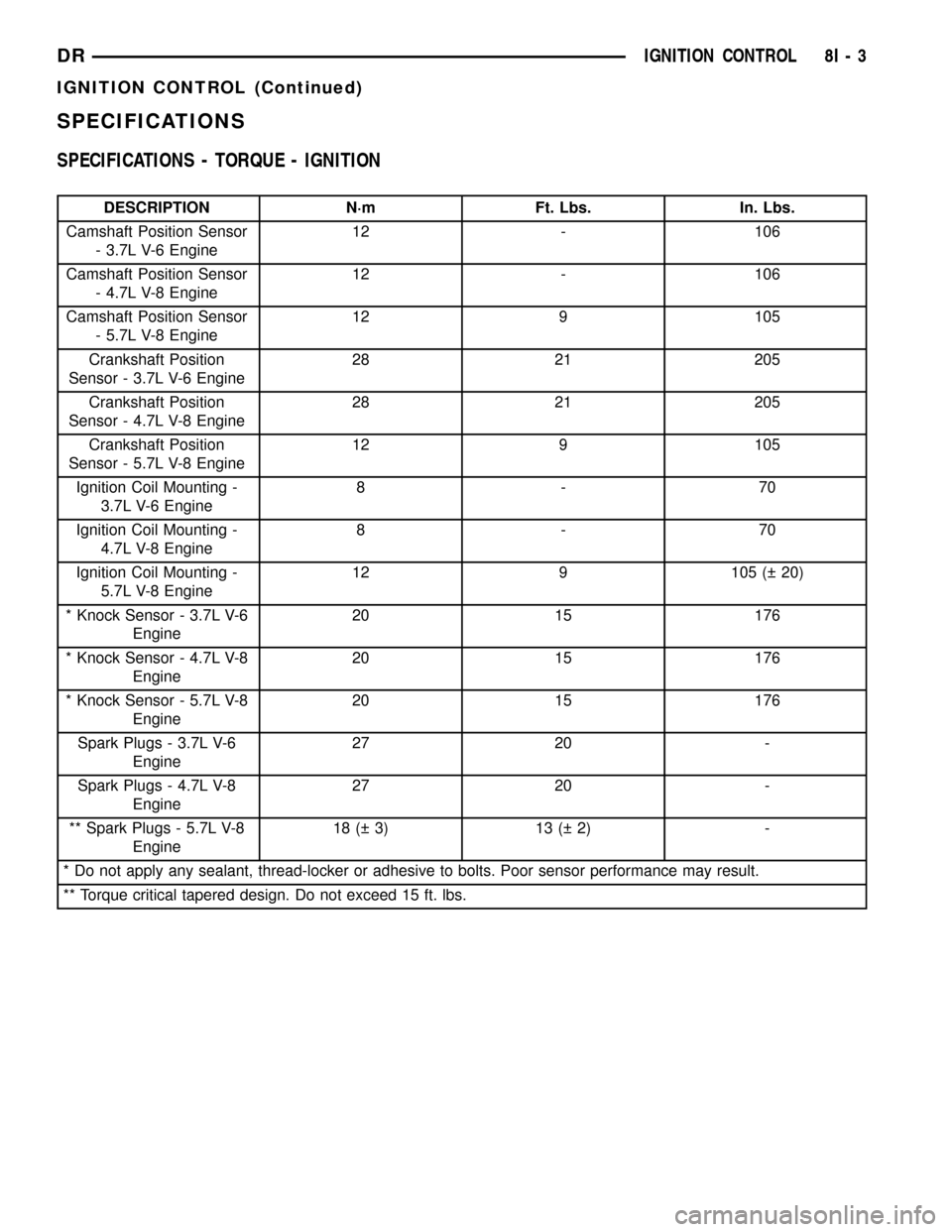
SPECIFICATIONS
SPECIFICATIONS - TORQUE - IGNITION
DESCRIPTION N´m Ft. Lbs. In. Lbs.
Camshaft Position Sensor
- 3.7L V-6 Engine12 - 106
Camshaft Position Sensor
- 4.7L V-8 Engine12 - 106
Camshaft Position Sensor
- 5.7L V-8 Engine12 9 105
Crankshaft Position
Sensor - 3.7L V-6 Engine28 21 205
Crankshaft Position
Sensor - 4.7L V-8 Engine28 21 205
Crankshaft Position
Sensor - 5.7L V-8 Engine12 9 105
Ignition Coil Mounting -
3.7L V-6 Engine8-70
Ignition Coil Mounting -
4.7L V-8 Engine8-70
Ignition Coil Mounting -
5.7L V-8 Engine12 9 105 ( 20)
* Knock Sensor - 3.7L V-6
Engine20 15 176
* Knock Sensor - 4.7L V-8
Engine20 15 176
* Knock Sensor - 5.7L V-8
Engine20 15 176
Spark Plugs - 3.7L V-6
Engine27 20 -
Spark Plugs - 4.7L V-8
Engine27 20 -
** Spark Plugs - 5.7L V-8
Engine18 ( 3) 13 ( 2) -
* Do not apply any sealant, thread-locker or adhesive to bolts. Poor sensor performance may result.
** Torque critical tapered design. Do not exceed 15 ft. lbs.
DRIGNITION CONTROL 8I - 3
IGNITION CONTROL (Continued)
Page 491 of 2627
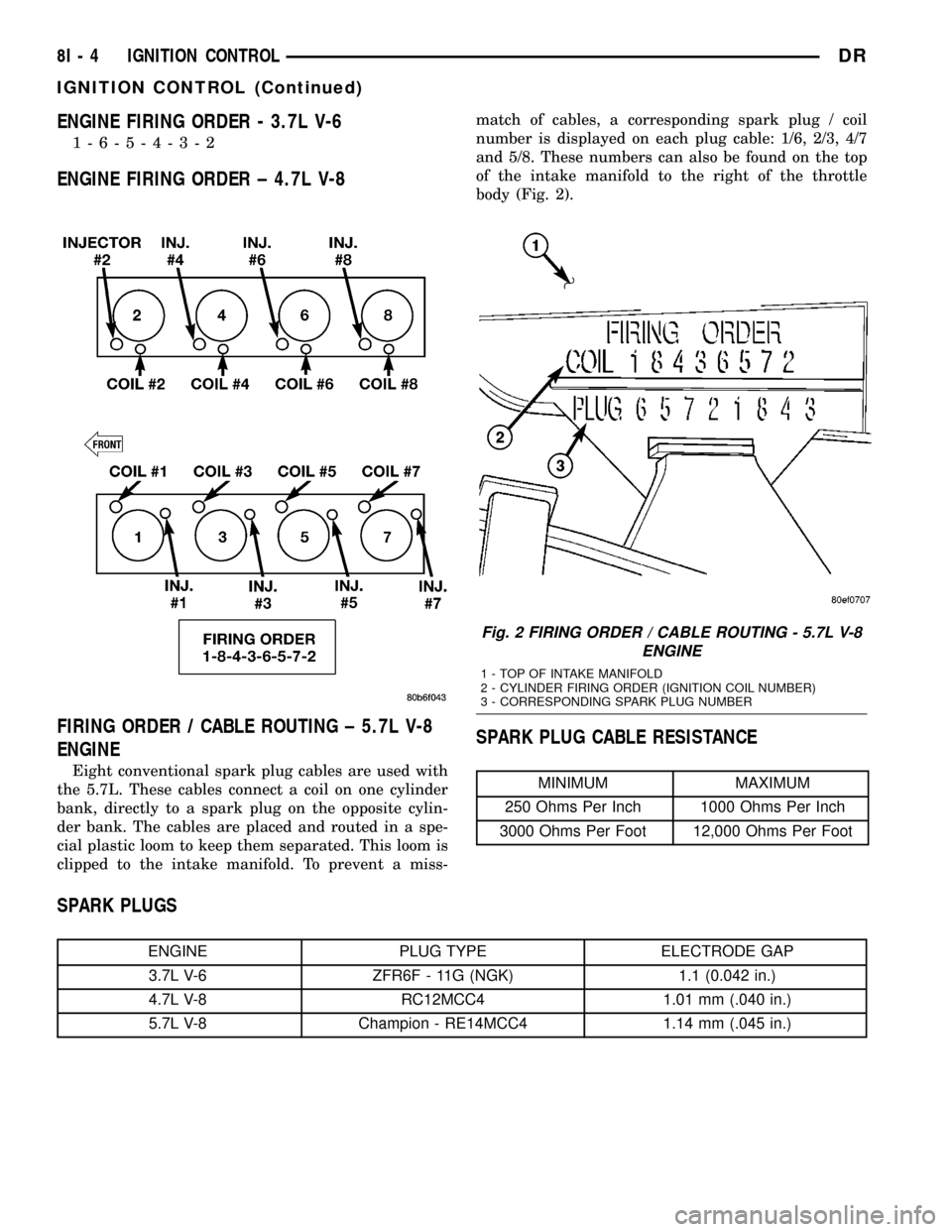
ENGINE FIRING ORDER - 3.7L V-6
1-6-5-4-3-2
ENGINE FIRING ORDER ± 4.7L V-8
FIRING ORDER / CABLE ROUTING ± 5.7L V-8
ENGINE
Eight conventional spark plug cables are used with
the 5.7L. These cables connect a coil on one cylinder
bank, directly to a spark plug on the opposite cylin-
der bank. The cables are placed and routed in a spe-
cial plastic loom to keep them separated. This loom is
clipped to the intake manifold. To prevent a miss-match of cables, a corresponding spark plug / coil
number is displayed on each plug cable: 1/6, 2/3, 4/7
and 5/8. These numbers can also be found on the top
of the intake manifold to the right of the throttle
body (Fig. 2).
SPARK PLUG CABLE RESISTANCE
MINIMUM MAXIMUM
250 Ohms Per Inch 1000 Ohms Per Inch
3000 Ohms Per Foot 12,000 Ohms Per Foot
SPARK PLUGS
ENGINE PLUG TYPE ELECTRODE GAP
3.7L V-6 ZFR6F - 11G (NGK) 1.1 (0.042 in.)
4.7L V-8 RC12MCC4 1.01 mm (.040 in.)
5.7L V-8 Champion - RE14MCC4 1.14 mm (.045 in.)
Fig. 2 FIRING ORDER / CABLE ROUTING - 5.7L V-8
ENGINE
1 - TOP OF INTAKE MANIFOLD
2 - CYLINDER FIRING ORDER (IGNITION COIL NUMBER)
3 - CORRESPONDING SPARK PLUG NUMBER
8I - 4 IGNITION CONTROLDR
IGNITION CONTROL (Continued)
Page 492 of 2627
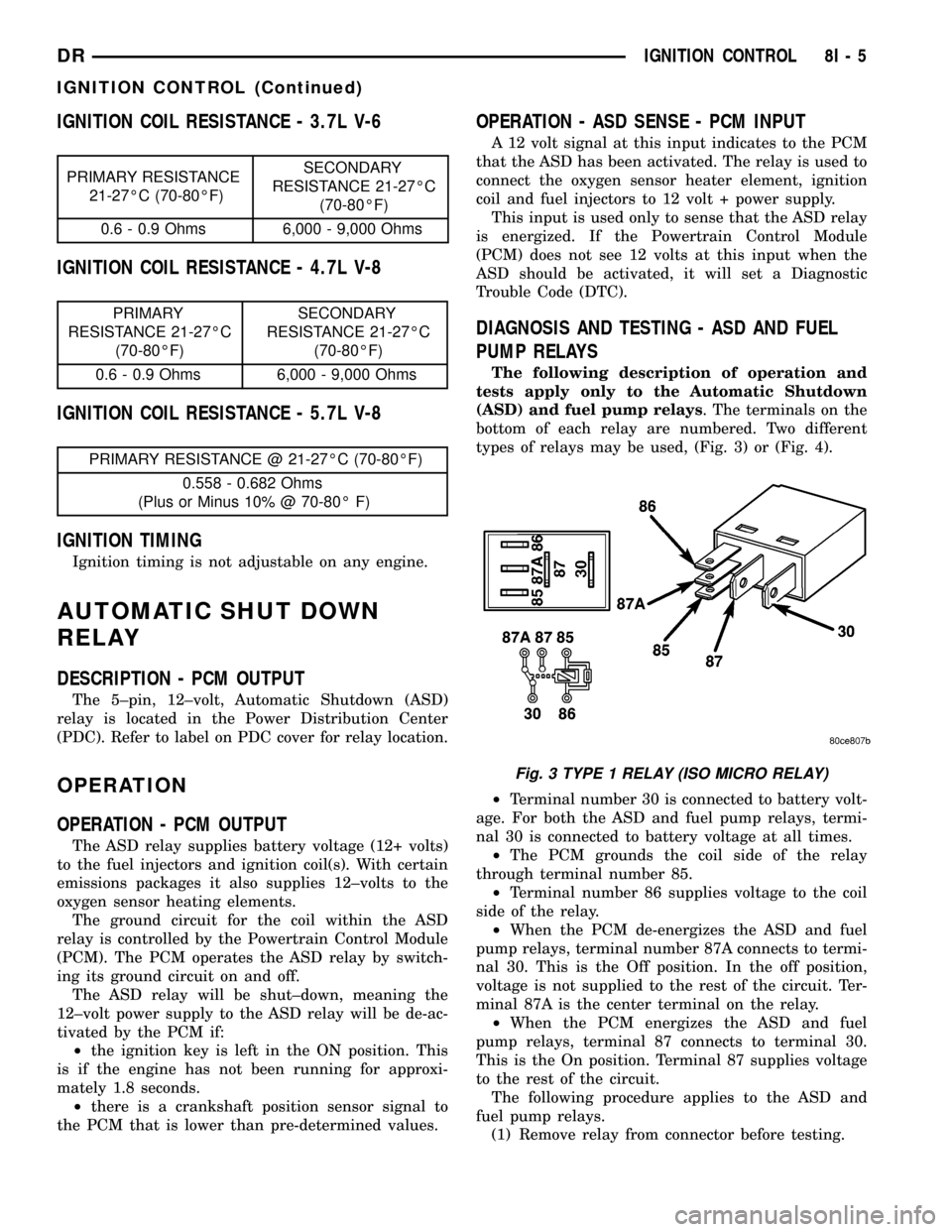
IGNITION COIL RESISTANCE - 3.7L V-6
PRIMARY RESISTANCE
21-27ÉC (70-80ÉF)SECONDARY
RESISTANCE 21-27ÉC
(70-80ÉF)
0.6 - 0.9 Ohms 6,000 - 9,000 Ohms
IGNITION COIL RESISTANCE - 4.7L V-8
PRIMARY
RESISTANCE 21-27ÉC
(70-80ÉF)SECONDARY
RESISTANCE 21-27ÉC
(70-80ÉF)
0.6 - 0.9 Ohms 6,000 - 9,000 Ohms
IGNITION COIL RESISTANCE - 5.7L V-8
PRIMARY RESISTANCE @ 21-27ÉC (70-80ÉF)
0.558 - 0.682 Ohms
(Plus or Minus 10% @ 70-80É F)
IGNITION TIMING
Ignition timing is not adjustable on any engine.
AUTOMATIC SHUT DOWN
RELAY
DESCRIPTION - PCM OUTPUT
The 5±pin, 12±volt, Automatic Shutdown (ASD)
relay is located in the Power Distribution Center
(PDC). Refer to label on PDC cover for relay location.
OPERATION
OPERATION - PCM OUTPUT
The ASD relay supplies battery voltage (12+ volts)
to the fuel injectors and ignition coil(s). With certain
emissions packages it also supplies 12±volts to the
oxygen sensor heating elements.
The ground circuit for the coil within the ASD
relay is controlled by the Powertrain Control Module
(PCM). The PCM operates the ASD relay by switch-
ing its ground circuit on and off.
The ASD relay will be shut±down, meaning the
12±volt power supply to the ASD relay will be de-ac-
tivated by the PCM if:
²the ignition key is left in the ON position. This
is if the engine has not been running for approxi-
mately 1.8 seconds.
²there is a crankshaft position sensor signal to
the PCM that is lower than pre-determined values.
OPERATION - ASD SENSE - PCM INPUT
A 12 volt signal at this input indicates to the PCM
that the ASD has been activated. The relay is used to
connect the oxygen sensor heater element, ignition
coil and fuel injectors to 12 volt + power supply.
This input is used only to sense that the ASD relay
is energized. If the Powertrain Control Module
(PCM) does not see 12 volts at this input when the
ASD should be activated, it will set a Diagnostic
Trouble Code (DTC).
DIAGNOSIS AND TESTING - ASD AND FUEL
PUMP RELAYS
The following description of operation and
tests apply only to the Automatic Shutdown
(ASD) and fuel pump relays. The terminals on the
bottom of each relay are numbered. Two different
types of relays may be used, (Fig. 3) or (Fig. 4).
²Terminal number 30 is connected to battery volt-
age. For both the ASD and fuel pump relays, termi-
nal 30 is connected to battery voltage at all times.
²The PCM grounds the coil side of the relay
through terminal number 85.
²Terminal number 86 supplies voltage to the coil
side of the relay.
²When the PCM de-energizes the ASD and fuel
pump relays, terminal number 87A connects to termi-
nal 30. This is the Off position. In the off position,
voltage is not supplied to the rest of the circuit. Ter-
minal 87A is the center terminal on the relay.
²When the PCM energizes the ASD and fuel
pump relays, terminal 87 connects to terminal 30.
This is the On position. Terminal 87 supplies voltage
to the rest of the circuit.
The following procedure applies to the ASD and
fuel pump relays.
(1) Remove relay from connector before testing.
Fig. 3 TYPE 1 RELAY (ISO MICRO RELAY)
DRIGNITION CONTROL 8I - 5
IGNITION CONTROL (Continued)
Page 494 of 2627
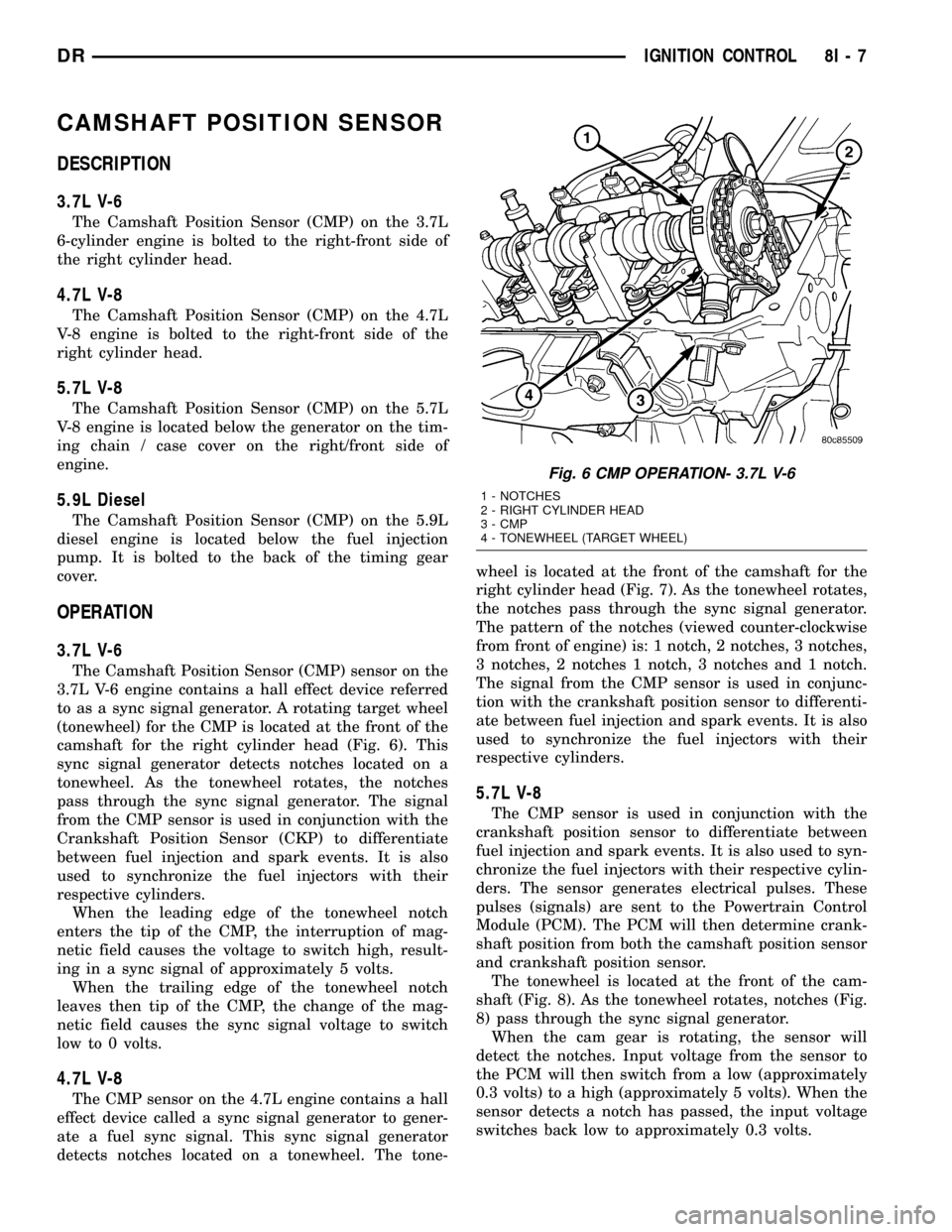
CAMSHAFT POSITION SENSOR
DESCRIPTION
3.7L V-6
The Camshaft Position Sensor (CMP) on the 3.7L
6-cylinder engine is bolted to the right-front side of
the right cylinder head.
4.7L V-8
The Camshaft Position Sensor (CMP) on the 4.7L
V-8 engine is bolted to the right-front side of the
right cylinder head.
5.7L V-8
The Camshaft Position Sensor (CMP) on the 5.7L
V-8 engine is located below the generator on the tim-
ing chain / case cover on the right/front side of
engine.
5.9L Diesel
The Camshaft Position Sensor (CMP) on the 5.9L
diesel engine is located below the fuel injection
pump. It is bolted to the back of the timing gear
cover.
OPERATION
3.7L V-6
The Camshaft Position Sensor (CMP) sensor on the
3.7L V-6 engine contains a hall effect device referred
to as a sync signal generator. A rotating target wheel
(tonewheel) for the CMP is located at the front of the
camshaft for the right cylinder head (Fig. 6). This
sync signal generator detects notches located on a
tonewheel. As the tonewheel rotates, the notches
pass through the sync signal generator. The signal
from the CMP sensor is used in conjunction with the
Crankshaft Position Sensor (CKP) to differentiate
between fuel injection and spark events. It is also
used to synchronize the fuel injectors with their
respective cylinders.
When the leading edge of the tonewheel notch
enters the tip of the CMP, the interruption of mag-
netic field causes the voltage to switch high, result-
ing in a sync signal of approximately 5 volts.
When the trailing edge of the tonewheel notch
leaves then tip of the CMP, the change of the mag-
netic field causes the sync signal voltage to switch
low to 0 volts.
4.7L V-8
The CMP sensor on the 4.7L engine contains a hall
effect device called a sync signal generator to gener-
ate a fuel sync signal. This sync signal generator
detects notches located on a tonewheel. The tone-wheel is located at the front of the camshaft for the
right cylinder head (Fig. 7). As the tonewheel rotates,
the notches pass through the sync signal generator.
The pattern of the notches (viewed counter-clockwise
from front of engine) is: 1 notch, 2 notches, 3 notches,
3 notches, 2 notches 1 notch, 3 notches and 1 notch.
The signal from the CMP sensor is used in conjunc-
tion with the crankshaft position sensor to differenti-
ate between fuel injection and spark events. It is also
used to synchronize the fuel injectors with their
respective cylinders.
5.7L V-8
The CMP sensor is used in conjunction with the
crankshaft position sensor to differentiate between
fuel injection and spark events. It is also used to syn-
chronize the fuel injectors with their respective cylin-
ders. The sensor generates electrical pulses. These
pulses (signals) are sent to the Powertrain Control
Module (PCM). The PCM will then determine crank-
shaft position from both the camshaft position sensor
and crankshaft position sensor.
The tonewheel is located at the front of the cam-
shaft (Fig. 8). As the tonewheel rotates, notches (Fig.
8) pass through the sync signal generator.
When the cam gear is rotating, the sensor will
detect the notches. Input voltage from the sensor to
the PCM will then switch from a low (approximately
0.3 volts) to a high (approximately 5 volts). When the
sensor detects a notch has passed, the input voltage
switches back low to approximately 0.3 volts.
Fig. 6 CMP OPERATION- 3.7L V-6
1 - NOTCHES
2 - RIGHT CYLINDER HEAD
3 - CMP
4 - TONEWHEEL (TARGET WHEEL)
DRIGNITION CONTROL 8I - 7
Page 495 of 2627
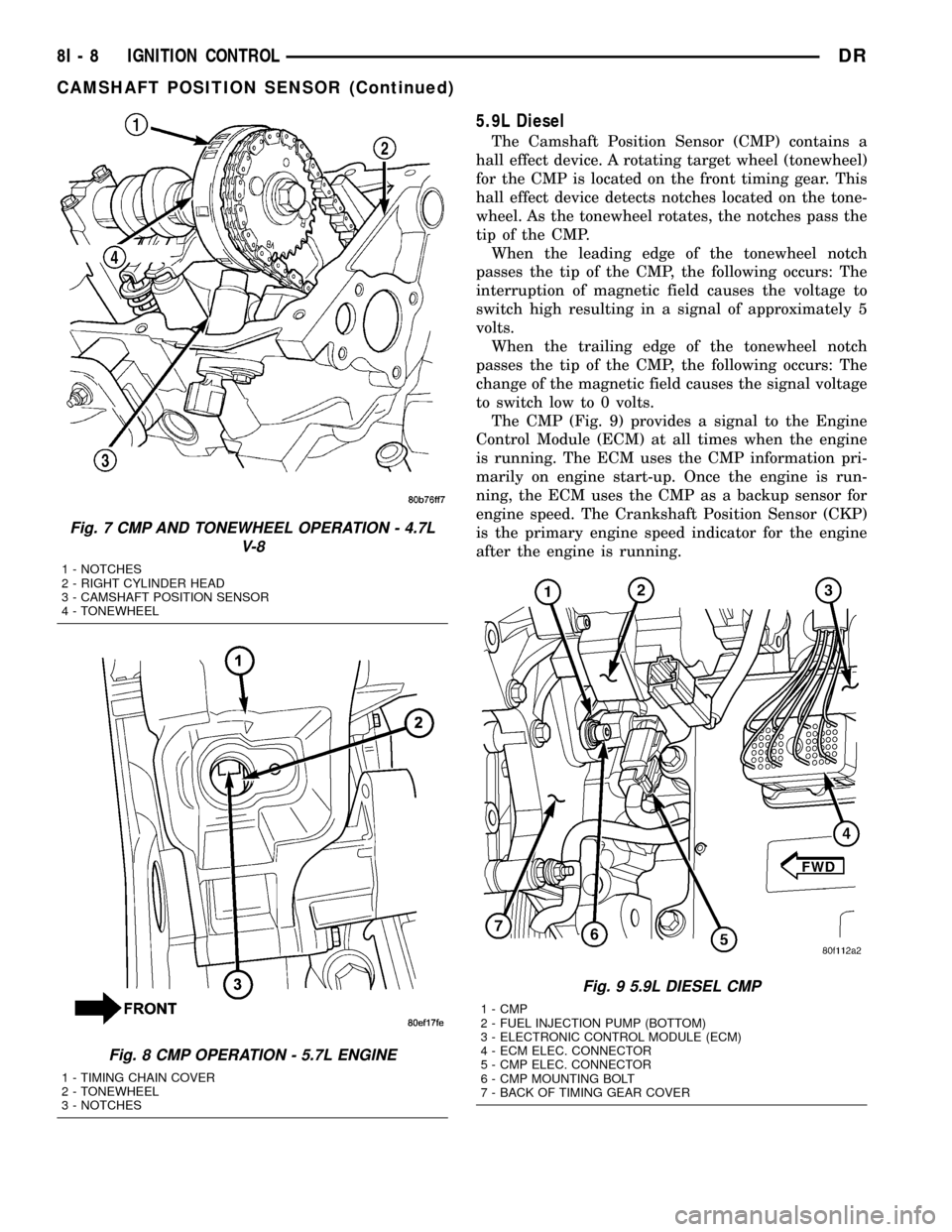
5.9L Diesel
The Camshaft Position Sensor (CMP) contains a
hall effect device. A rotating target wheel (tonewheel)
for the CMP is located on the front timing gear. This
hall effect device detects notches located on the tone-
wheel. As the tonewheel rotates, the notches pass the
tip of the CMP.
When the leading edge of the tonewheel notch
passes the tip of the CMP, the following occurs: The
interruption of magnetic field causes the voltage to
switch high resulting in a signal of approximately 5
volts.
When the trailing edge of the tonewheel notch
passes the tip of the CMP, the following occurs: The
change of the magnetic field causes the signal voltage
to switch low to 0 volts.
The CMP (Fig. 9) provides a signal to the Engine
Control Module (ECM) at all times when the engine
is running. The ECM uses the CMP information pri-
marily on engine start-up. Once the engine is run-
ning, the ECM uses the CMP as a backup sensor for
engine speed. The Crankshaft Position Sensor (CKP)
is the primary engine speed indicator for the engine
after the engine is running.
Fig. 7 CMP AND TONEWHEEL OPERATION - 4.7L
V-8
1 - NOTCHES
2 - RIGHT CYLINDER HEAD
3 - CAMSHAFT POSITION SENSOR
4 - TONEWHEEL
Fig. 8 CMP OPERATION - 5.7L ENGINE
1 - TIMING CHAIN COVER
2 - TONEWHEEL
3 - NOTCHES
Fig. 9 5.9L DIESEL CMP
1 - CMP
2 - FUEL INJECTION PUMP (BOTTOM)
3 - ELECTRONIC CONTROL MODULE (ECM)
4 - ECM ELEC. CONNECTOR
5 - CMP ELEC. CONNECTOR
6 - CMP MOUNTING BOLT
7 - BACK OF TIMING GEAR COVER
8I - 8 IGNITION CONTROLDR
CAMSHAFT POSITION SENSOR (Continued)
Page 496 of 2627
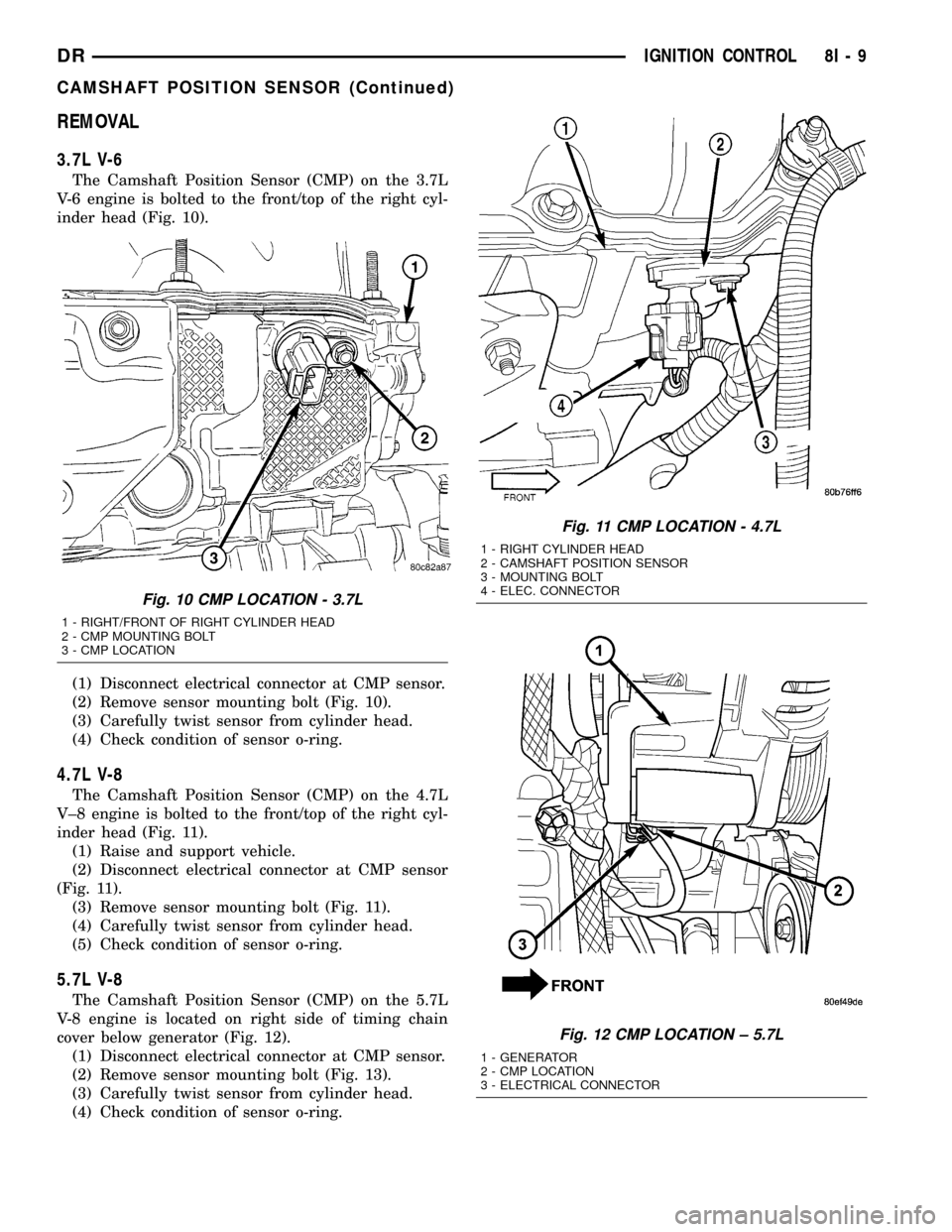
REMOVAL
3.7L V-6
The Camshaft Position Sensor (CMP) on the 3.7L
V-6 engine is bolted to the front/top of the right cyl-
inder head (Fig. 10).
(1) Disconnect electrical connector at CMP sensor.
(2) Remove sensor mounting bolt (Fig. 10).
(3) Carefully twist sensor from cylinder head.
(4) Check condition of sensor o-ring.
4.7L V-8
The Camshaft Position Sensor (CMP) on the 4.7L
V±8 engine is bolted to the front/top of the right cyl-
inder head (Fig. 11).
(1) Raise and support vehicle.
(2) Disconnect electrical connector at CMP sensor
(Fig. 11).
(3) Remove sensor mounting bolt (Fig. 11).
(4) Carefully twist sensor from cylinder head.
(5) Check condition of sensor o-ring.
5.7L V-8
The Camshaft Position Sensor (CMP) on the 5.7L
V-8 engine is located on right side of timing chain
cover below generator (Fig. 12).
(1) Disconnect electrical connector at CMP sensor.
(2) Remove sensor mounting bolt (Fig. 13).
(3) Carefully twist sensor from cylinder head.
(4) Check condition of sensor o-ring.
Fig. 10 CMP LOCATION - 3.7L
1 - RIGHT/FRONT OF RIGHT CYLINDER HEAD
2 - CMP MOUNTING BOLT
3 - CMP LOCATION
Fig. 11 CMP LOCATION - 4.7L
1 - RIGHT CYLINDER HEAD
2 - CAMSHAFT POSITION SENSOR
3 - MOUNTING BOLT
4 - ELEC. CONNECTOR
Fig. 12 CMP LOCATION ± 5.7L
1 - GENERATOR
2 - CMP LOCATION
3 - ELECTRICAL CONNECTOR
DRIGNITION CONTROL 8I - 9
CAMSHAFT POSITION SENSOR (Continued)