service indicator DODGE RAM 1500 1998 2.G Manual PDF
[x] Cancel search | Manufacturer: DODGE, Model Year: 1998, Model line: RAM 1500, Model: DODGE RAM 1500 1998 2.GPages: 2627
Page 1863 of 2627
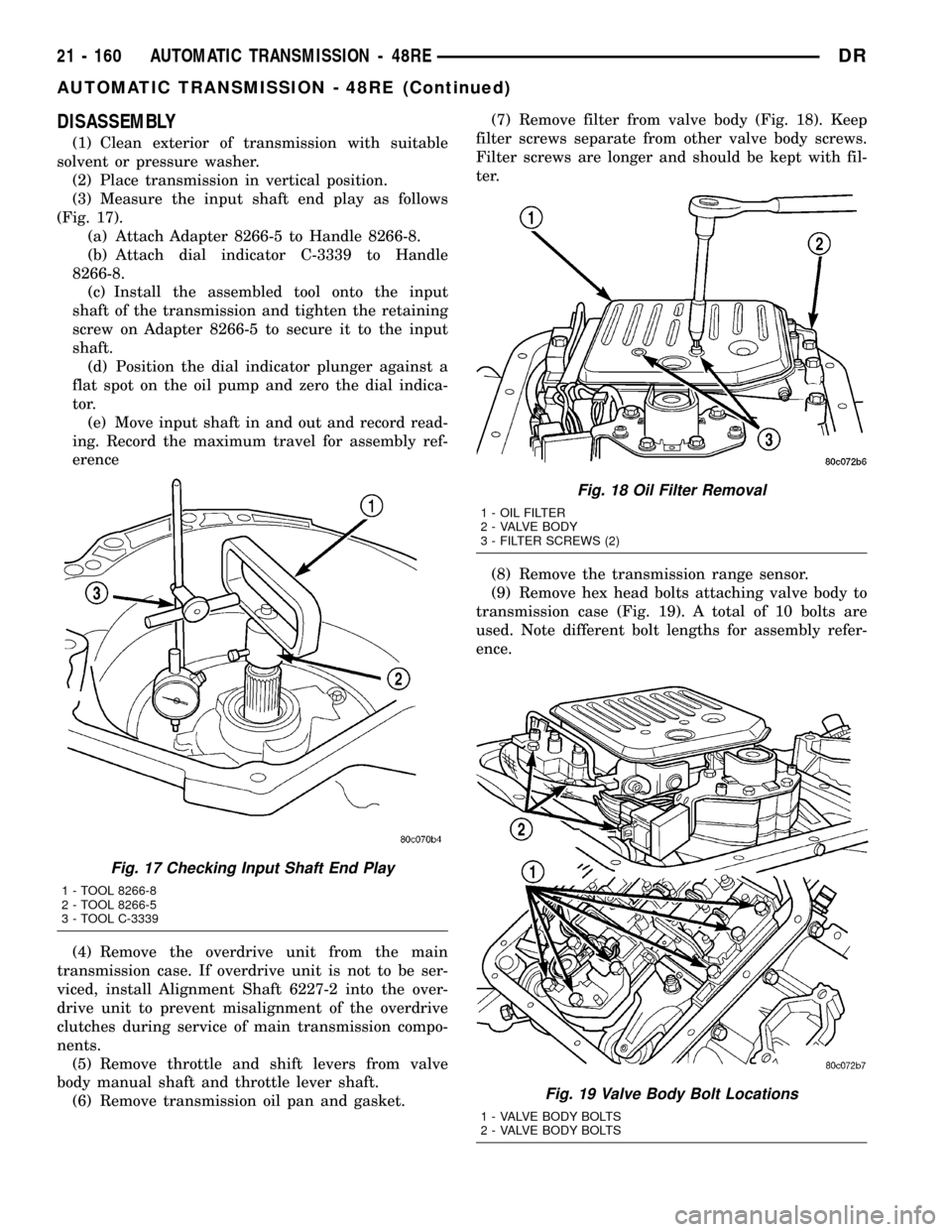
DISASSEMBLY
(1) Clean exterior of transmission with suitable
solvent or pressure washer.
(2) Place transmission in vertical position.
(3) Measure the input shaft end play as follows
(Fig. 17).
(a) Attach Adapter 8266-5 to Handle 8266-8.
(b) Attach dial indicator C-3339 to Handle
8266-8.
(c) Install the assembled tool onto the input
shaft of the transmission and tighten the retaining
screw on Adapter 8266-5 to secure it to the input
shaft.
(d) Position the dial indicator plunger against a
flat spot on the oil pump and zero the dial indica-
tor.
(e) Move input shaft in and out and record read-
ing. Record the maximum travel for assembly ref-
erence
(4) Remove the overdrive unit from the main
transmission case. If overdrive unit is not to be ser-
viced, install Alignment Shaft 6227-2 into the over-
drive unit to prevent misalignment of the overdrive
clutches during service of main transmission compo-
nents.
(5) Remove throttle and shift levers from valve
body manual shaft and throttle lever shaft.
(6) Remove transmission oil pan and gasket.(7) Remove filter from valve body (Fig. 18). Keep
filter screws separate from other valve body screws.
Filter screws are longer and should be kept with fil-
ter.
(8) Remove the transmission range sensor.
(9) Remove hex head bolts attaching valve body to
transmission case (Fig. 19). A total of 10 bolts are
used. Note different bolt lengths for assembly refer-
ence.
Fig. 19 Valve Body Bolt Locations
1 - VALVE BODY BOLTS
2 - VALVE BODY BOLTS
Fig. 17 Checking Input Shaft End Play
1 - TOOL 8266-8
2 - TOOL 8266-5
3 - TOOL C-3339
Fig. 18 Oil Filter Removal
1 - OIL FILTER
2 - VALVE BODY
3 - FILTER SCREWS (2)
21 - 160 AUTOMATIC TRANSMISSION - 48REDR
AUTOMATIC TRANSMISSION - 48RE (Continued)
Page 2069 of 2627
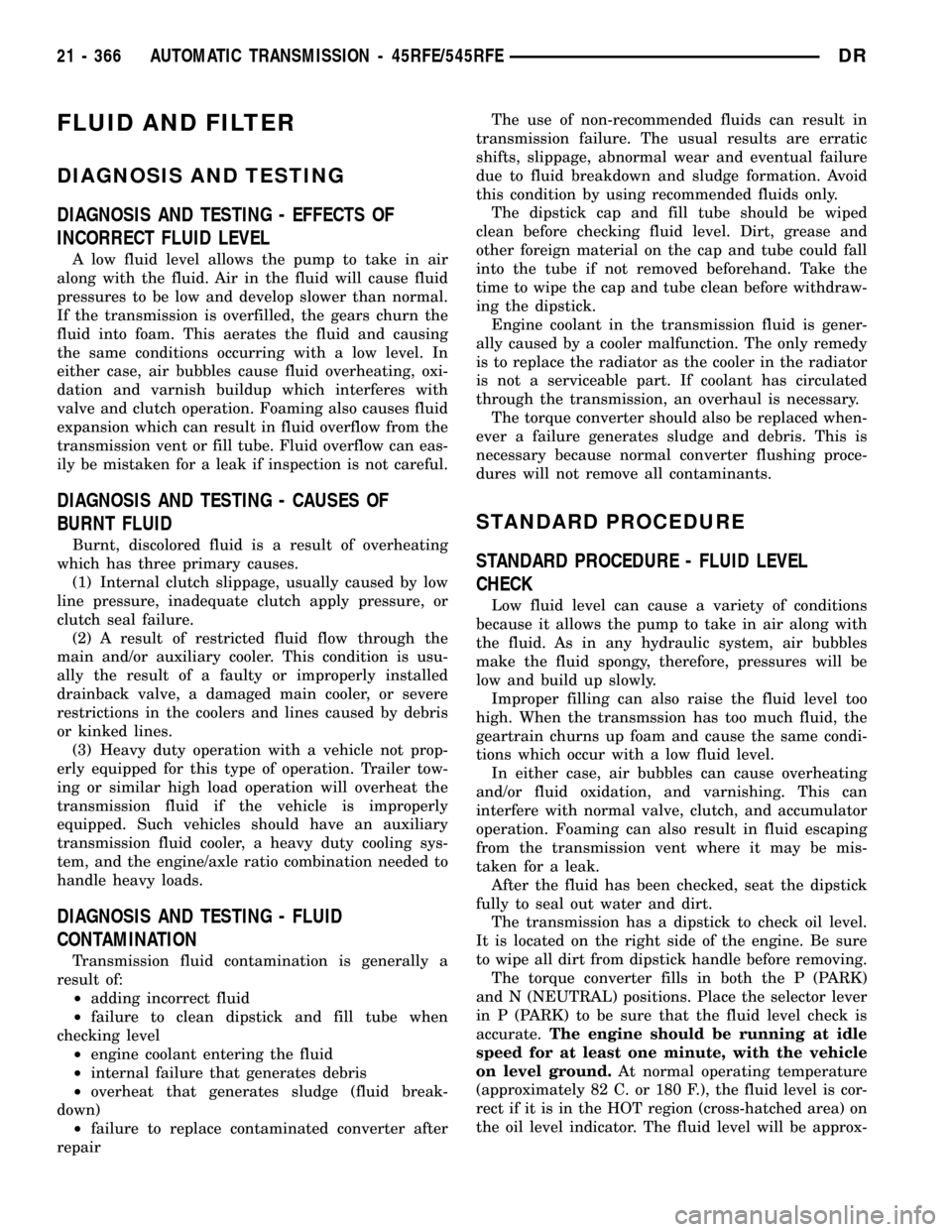
FLUID AND FILTER
DIAGNOSIS AND TESTING
DIAGNOSIS AND TESTING - EFFECTS OF
INCORRECT FLUID LEVEL
A low fluid level allows the pump to take in air
along with the fluid. Air in the fluid will cause fluid
pressures to be low and develop slower than normal.
If the transmission is overfilled, the gears churn the
fluid into foam. This aerates the fluid and causing
the same conditions occurring with a low level. In
either case, air bubbles cause fluid overheating, oxi-
dation and varnish buildup which interferes with
valve and clutch operation. Foaming also causes fluid
expansion which can result in fluid overflow from the
transmission vent or fill tube. Fluid overflow can eas-
ily be mistaken for a leak if inspection is not careful.
DIAGNOSIS AND TESTING - CAUSES OF
BURNT FLUID
Burnt, discolored fluid is a result of overheating
which has three primary causes.
(1) Internal clutch slippage, usually caused by low
line pressure, inadequate clutch apply pressure, or
clutch seal failure.
(2) A result of restricted fluid flow through the
main and/or auxiliary cooler. This condition is usu-
ally the result of a faulty or improperly installed
drainback valve, a damaged main cooler, or severe
restrictions in the coolers and lines caused by debris
or kinked lines.
(3) Heavy duty operation with a vehicle not prop-
erly equipped for this type of operation. Trailer tow-
ing or similar high load operation will overheat the
transmission fluid if the vehicle is improperly
equipped. Such vehicles should have an auxiliary
transmission fluid cooler, a heavy duty cooling sys-
tem, and the engine/axle ratio combination needed to
handle heavy loads.
DIAGNOSIS AND TESTING - FLUID
CONTAMINATION
Transmission fluid contamination is generally a
result of:
²adding incorrect fluid
²failure to clean dipstick and fill tube when
checking level
²engine coolant entering the fluid
²internal failure that generates debris
²overheat that generates sludge (fluid break-
down)
²failure to replace contaminated converter after
repairThe use of non-recommended fluids can result in
transmission failure. The usual results are erratic
shifts, slippage, abnormal wear and eventual failure
due to fluid breakdown and sludge formation. Avoid
this condition by using recommended fluids only.
The dipstick cap and fill tube should be wiped
clean before checking fluid level. Dirt, grease and
other foreign material on the cap and tube could fall
into the tube if not removed beforehand. Take the
time to wipe the cap and tube clean before withdraw-
ing the dipstick.
Engine coolant in the transmission fluid is gener-
ally caused by a cooler malfunction. The only remedy
is to replace the radiator as the cooler in the radiator
is not a serviceable part. If coolant has circulated
through the transmission, an overhaul is necessary.
The torque converter should also be replaced when-
ever a failure generates sludge and debris. This is
necessary because normal converter flushing proce-
dures will not remove all contaminants.
STANDARD PROCEDURE
STANDARD PROCEDURE - FLUID LEVEL
CHECK
Low fluid level can cause a variety of conditions
because it allows the pump to take in air along with
the fluid. As in any hydraulic system, air bubbles
make the fluid spongy, therefore, pressures will be
low and build up slowly.
Improper filling can also raise the fluid level too
high. When the transmssion has too much fluid, the
geartrain churns up foam and cause the same condi-
tions which occur with a low fluid level.
In either case, air bubbles can cause overheating
and/or fluid oxidation, and varnishing. This can
interfere with normal valve, clutch, and accumulator
operation. Foaming can also result in fluid escaping
from the transmission vent where it may be mis-
taken for a leak.
After the fluid has been checked, seat the dipstick
fully to seal out water and dirt.
The transmission has a dipstick to check oil level.
It is located on the right side of the engine. Be sure
to wipe all dirt from dipstick handle before removing.
The torque converter fills in both the P (PARK)
and N (NEUTRAL) positions. Place the selector lever
in P (PARK) to be sure that the fluid level check is
accurate.The engine should be running at idle
speed for at least one minute, with the vehicle
on level ground.At normal operating temperature
(approximately 82 C. or 180 F.), the fluid level is cor-
rect if it is in the HOT region (cross-hatched area) on
the oil level indicator. The fluid level will be approx-
21 - 366 AUTOMATIC TRANSMISSION - 45RFE/545RFEDR
Page 2281 of 2627
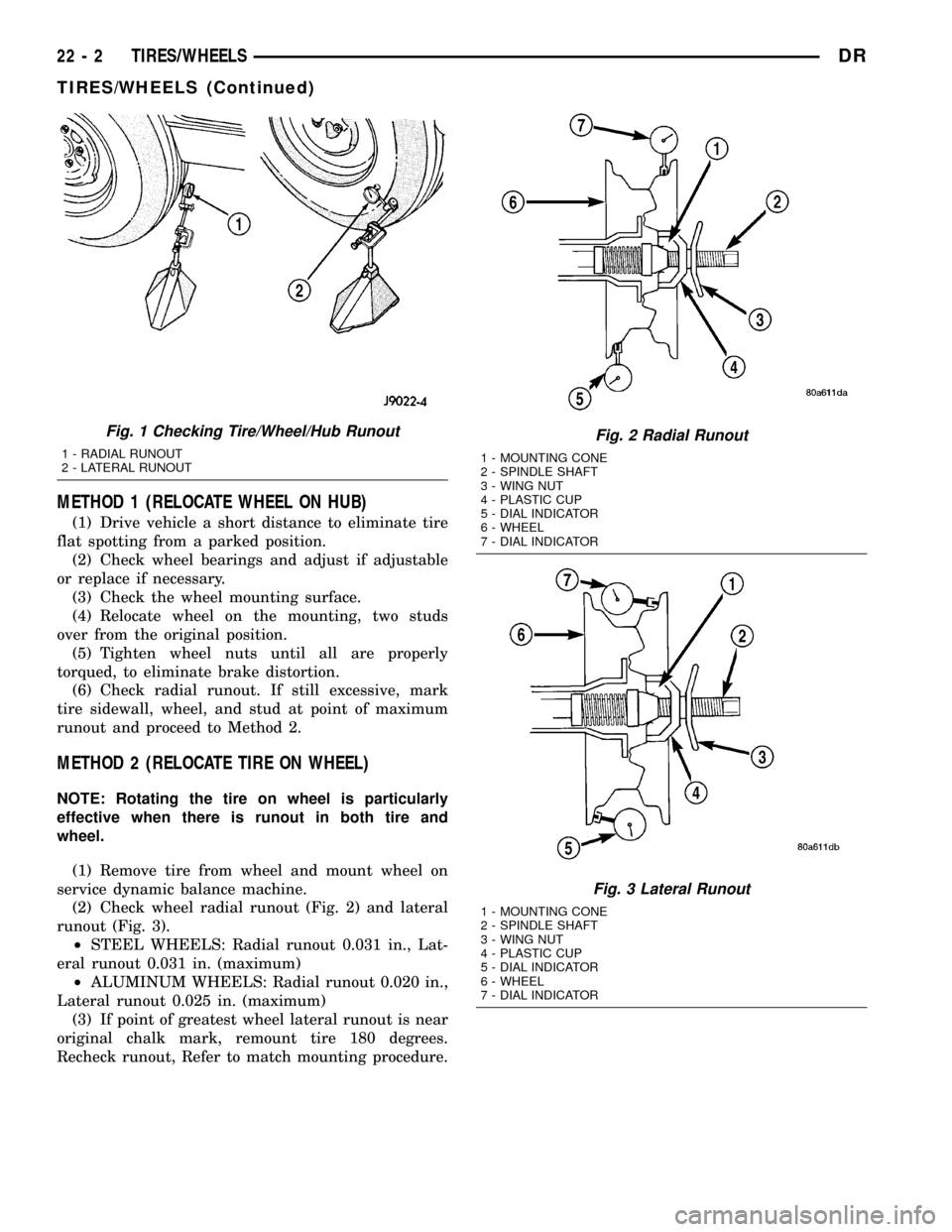
METHOD 1 (RELOCATE WHEEL ON HUB)
(1) Drive vehicle a short distance to eliminate tire
flat spotting from a parked position.
(2) Check wheel bearings and adjust if adjustable
or replace if necessary.
(3) Check the wheel mounting surface.
(4) Relocate wheel on the mounting, two studs
over from the original position.
(5) Tighten wheel nuts until all are properly
torqued, to eliminate brake distortion.
(6) Check radial runout. If still excessive, mark
tire sidewall, wheel, and stud at point of maximum
runout and proceed to Method 2.
METHOD 2 (RELOCATE TIRE ON WHEEL)
NOTE: Rotating the tire on wheel is particularly
effective when there is runout in both tire and
wheel.
(1) Remove tire from wheel and mount wheel on
service dynamic balance machine.
(2) Check wheel radial runout (Fig. 2) and lateral
runout (Fig. 3).
²STEEL WHEELS: Radial runout 0.031 in., Lat-
eral runout 0.031 in. (maximum)
²ALUMINUM WHEELS: Radial runout 0.020 in.,
Lateral runout 0.025 in. (maximum)
(3) If point of greatest wheel lateral runout is near
original chalk mark, remount tire 180 degrees.
Recheck runout, Refer to match mounting procedure.
Fig. 1 Checking Tire/Wheel/Hub Runout
1 - RADIAL RUNOUT
2 - LATERAL RUNOUT
Fig. 2 Radial Runout
1 - MOUNTING CONE
2 - SPINDLE SHAFT
3 - WING NUT
4 - PLASTIC CUP
5 - DIAL INDICATOR
6 - WHEEL
7 - DIAL INDICATOR
Fig. 3 Lateral Runout
1 - MOUNTING CONE
2 - SPINDLE SHAFT
3 - WING NUT
4 - PLASTIC CUP
5 - DIAL INDICATOR
6 - WHEEL
7 - DIAL INDICATOR
22 - 2 TIRES/WHEELSDR
TIRES/WHEELS (Continued)
Page 2282 of 2627

STANDARD PROCEDURE
STANDARD PROCEDURE - TIRE ROTATION
Tires on the front and rear axles operate at differ-
ent loads and perform different steering, driving, and
braking functions. For these reasons, the tires wear
at unequal rates. They may also develop irregular
wear patterns. These effects can be reduced by rotat-
ing the tires according to the maintenance schedule
in the Owners Manual. This will improve tread life,
traction and maintain a smooth quiet ride.
The recommended method of tire rotation is (Fig.
4) & (Fig. 5). Other methods can be used, but may
not provide the same tire longevity benefits.
CAUTION: 3500 Dual rear tires have a new tire rota-
tion pattern. This is to accommodate the asymmet-
rical design of the ON/OFF road tires and the use of
the outlined white letter (OWL) tires. When replac-
ing a flat, the spare tire may have to be remounted
on the rim or installed at a different location to
maintain the correct placement of the asymmetrical
design or the (OWL).
STANDARD PROCEDURE - MATCH MOUNTING
Wheels and tires are match mounted at the factory.
This means that the high spot of the tire is matched
to the low spot on the wheel rim. Each are marked
with a bright colored temporary label on the out-
board surface for alignment. The wheel is also
marked permanently on the inside of the rim in the
tire well. This permanent mark may be a paint dot
or line, a permanent label or a stamped impression
such as an X. An optional location mark is a small
spherical indentation on the vertical face of the out-
board flange on some non styled base steel wheels.
The tire must be removed to locate the permanent
mark on the inside of the wheel.
Before dismounting a tire from its wheel, a refer-
ence mark should be placed on the tire at the valve
stem location. This reference will ensure that it is
remounted in the original position on the wheel.
(1) Remove the tire and wheel assembly from the
vehicle and mount on a service dynamic balance
machine.
(2) Measure the total runout on the center of the
tire tread rib with a dial indicator. Record the indi-
cator reading. Mark the tire to indicate the high spot.
Place a mark on the tire at the valve stem location
(Fig. 6).
Fig. 4 TIRE ROTATION PATTERN - SINGLE REAR
WHEEL (SRW)
Fig. 5 TIRE ROTATION PATTERN - DUAL REAR
WHEELS (DRW)
Fig. 6 First Measurement On Tire
1 - REFERENCE MARK
2 - 1ST MEASUREMENT HIGH SPOT MARK TIRE AND RIM
3 - WHEEL
4 - VALVE STEM
DRTIRES/WHEELS 22 - 3
TIRES/WHEELS (Continued)
Page 2283 of 2627
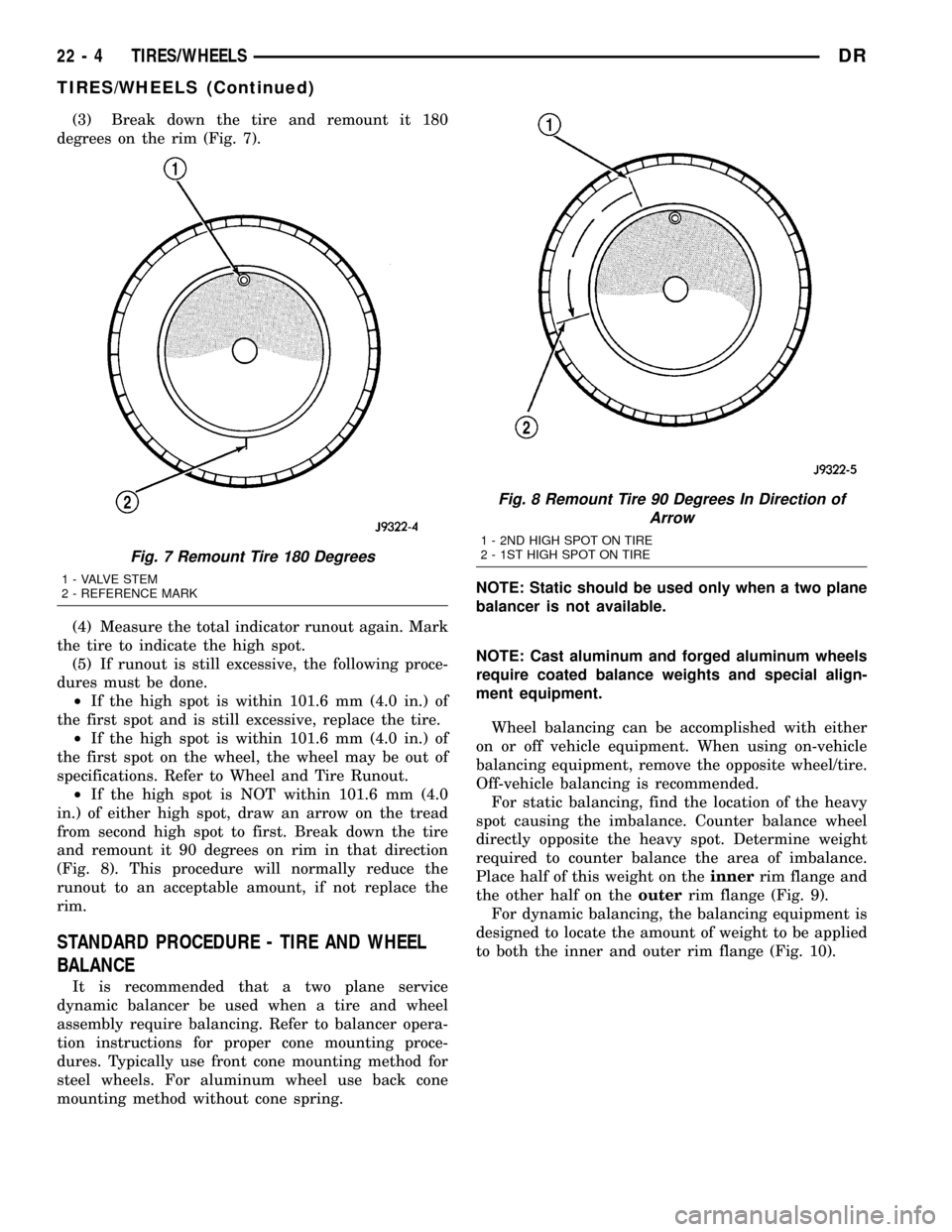
(3) Break down the tire and remount it 180
degrees on the rim (Fig. 7).
(4) Measure the total indicator runout again. Mark
the tire to indicate the high spot.
(5) If runout is still excessive, the following proce-
dures must be done.
²If the high spot is within 101.6 mm (4.0 in.) of
the first spot and is still excessive, replace the tire.
²If the high spot is within 101.6 mm (4.0 in.) of
the first spot on the wheel, the wheel may be out of
specifications. Refer to Wheel and Tire Runout.
²If the high spot is NOT within 101.6 mm (4.0
in.) of either high spot, draw an arrow on the tread
from second high spot to first. Break down the tire
and remount it 90 degrees on rim in that direction
(Fig. 8). This procedure will normally reduce the
runout to an acceptable amount, if not replace the
rim.
STANDARD PROCEDURE - TIRE AND WHEEL
BALANCE
It is recommended that a two plane service
dynamic balancer be used when a tire and wheel
assembly require balancing. Refer to balancer opera-
tion instructions for proper cone mounting proce-
dures. Typically use front cone mounting method for
steel wheels. For aluminum wheel use back cone
mounting method without cone spring.NOTE: Static should be used only when a two plane
balancer is not available.
NOTE: Cast aluminum and forged aluminum wheels
require coated balance weights and special align-
ment equipment.
Wheel balancing can be accomplished with either
on or off vehicle equipment. When using on-vehicle
balancing equipment, remove the opposite wheel/tire.
Off-vehicle balancing is recommended.
For static balancing, find the location of the heavy
spot causing the imbalance. Counter balance wheel
directly opposite the heavy spot. Determine weight
required to counter balance the area of imbalance.
Place half of this weight on theinnerrim flange and
the other half on theouterrim flange (Fig. 9).
For dynamic balancing, the balancing equipment is
designed to locate the amount of weight to be applied
to both the inner and outer rim flange (Fig. 10).
Fig. 7 Remount Tire 180 Degrees
1 - VALVE STEM
2 - REFERENCE MARK
Fig. 8 Remount Tire 90 Degrees In Direction of
Arrow
1 - 2ND HIGH SPOT ON TIRE
2 - 1ST HIGH SPOT ON TIRE
22 - 4 TIRES/WHEELSDR
TIRES/WHEELS (Continued)
Page 2554 of 2627
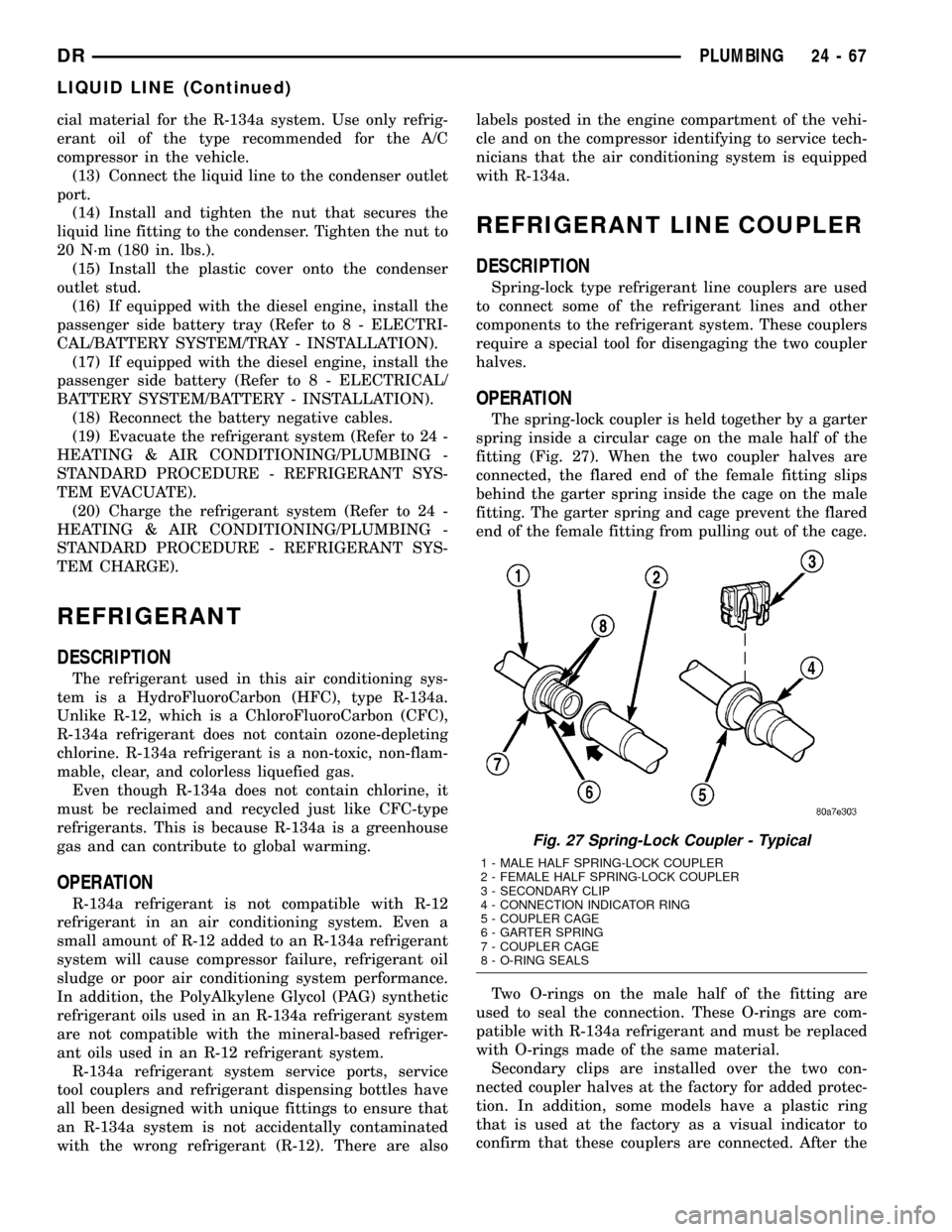
cial material for the R-134a system. Use only refrig-
erant oil of the type recommended for the A/C
compressor in the vehicle.
(13) Connect the liquid line to the condenser outlet
port.
(14) Install and tighten the nut that secures the
liquid line fitting to the condenser. Tighten the nut to
20 N´m (180 in. lbs.).
(15) Install the plastic cover onto the condenser
outlet stud.
(16) If equipped with the diesel engine, install the
passenger side battery tray (Refer to 8 - ELECTRI-
CAL/BATTERY SYSTEM/TRAY - INSTALLATION).
(17) If equipped with the diesel engine, install the
passenger side battery (Refer to 8 - ELECTRICAL/
BATTERY SYSTEM/BATTERY - INSTALLATION).
(18) Reconnect the battery negative cables.
(19) Evacuate the refrigerant system (Refer to 24 -
HEATING & AIR CONDITIONING/PLUMBING -
STANDARD PROCEDURE - REFRIGERANT SYS-
TEM EVACUATE).
(20) Charge the refrigerant system (Refer to 24 -
HEATING & AIR CONDITIONING/PLUMBING -
STANDARD PROCEDURE - REFRIGERANT SYS-
TEM CHARGE).
REFRIGERANT
DESCRIPTION
The refrigerant used in this air conditioning sys-
tem is a HydroFluoroCarbon (HFC), type R-134a.
Unlike R-12, which is a ChloroFluoroCarbon (CFC),
R-134a refrigerant does not contain ozone-depleting
chlorine. R-134a refrigerant is a non-toxic, non-flam-
mable, clear, and colorless liquefied gas.
Even though R-134a does not contain chlorine, it
must be reclaimed and recycled just like CFC-type
refrigerants. This is because R-134a is a greenhouse
gas and can contribute to global warming.
OPERATION
R-134a refrigerant is not compatible with R-12
refrigerant in an air conditioning system. Even a
small amount of R-12 added to an R-134a refrigerant
system will cause compressor failure, refrigerant oil
sludge or poor air conditioning system performance.
In addition, the PolyAlkylene Glycol (PAG) synthetic
refrigerant oils used in an R-134a refrigerant system
are not compatible with the mineral-based refriger-
ant oils used in an R-12 refrigerant system.
R-134a refrigerant system service ports, service
tool couplers and refrigerant dispensing bottles have
all been designed with unique fittings to ensure that
an R-134a system is not accidentally contaminated
with the wrong refrigerant (R-12). There are alsolabels posted in the engine compartment of the vehi-
cle and on the compressor identifying to service tech-
nicians that the air conditioning system is equipped
with R-134a.
REFRIGERANT LINE COUPLER
DESCRIPTION
Spring-lock type refrigerant line couplers are used
to connect some of the refrigerant lines and other
components to the refrigerant system. These couplers
require a special tool for disengaging the two coupler
halves.
OPERATION
The spring-lock coupler is held together by a garter
spring inside a circular cage on the male half of the
fitting (Fig. 27). When the two coupler halves are
connected, the flared end of the female fitting slips
behind the garter spring inside the cage on the male
fitting. The garter spring and cage prevent the flared
end of the female fitting from pulling out of the cage.
Two O-rings on the male half of the fitting are
used to seal the connection. These O-rings are com-
patible with R-134a refrigerant and must be replaced
with O-rings made of the same material.
Secondary clips are installed over the two con-
nected coupler halves at the factory for added protec-
tion. In addition, some models have a plastic ring
that is used at the factory as a visual indicator to
confirm that these couplers are connected. After the
Fig. 27 Spring-Lock Coupler - Typical
1 - MALE HALF SPRING-LOCK COUPLER
2 - FEMALE HALF SPRING-LOCK COUPLER
3 - SECONDARY CLIP
4 - CONNECTION INDICATOR RING
5 - COUPLER CAGE
6 - GARTER SPRING
7 - COUPLER CAGE
8 - O-RING SEALS
DRPLUMBING 24 - 67
LIQUID LINE (Continued)
Page 2588 of 2627
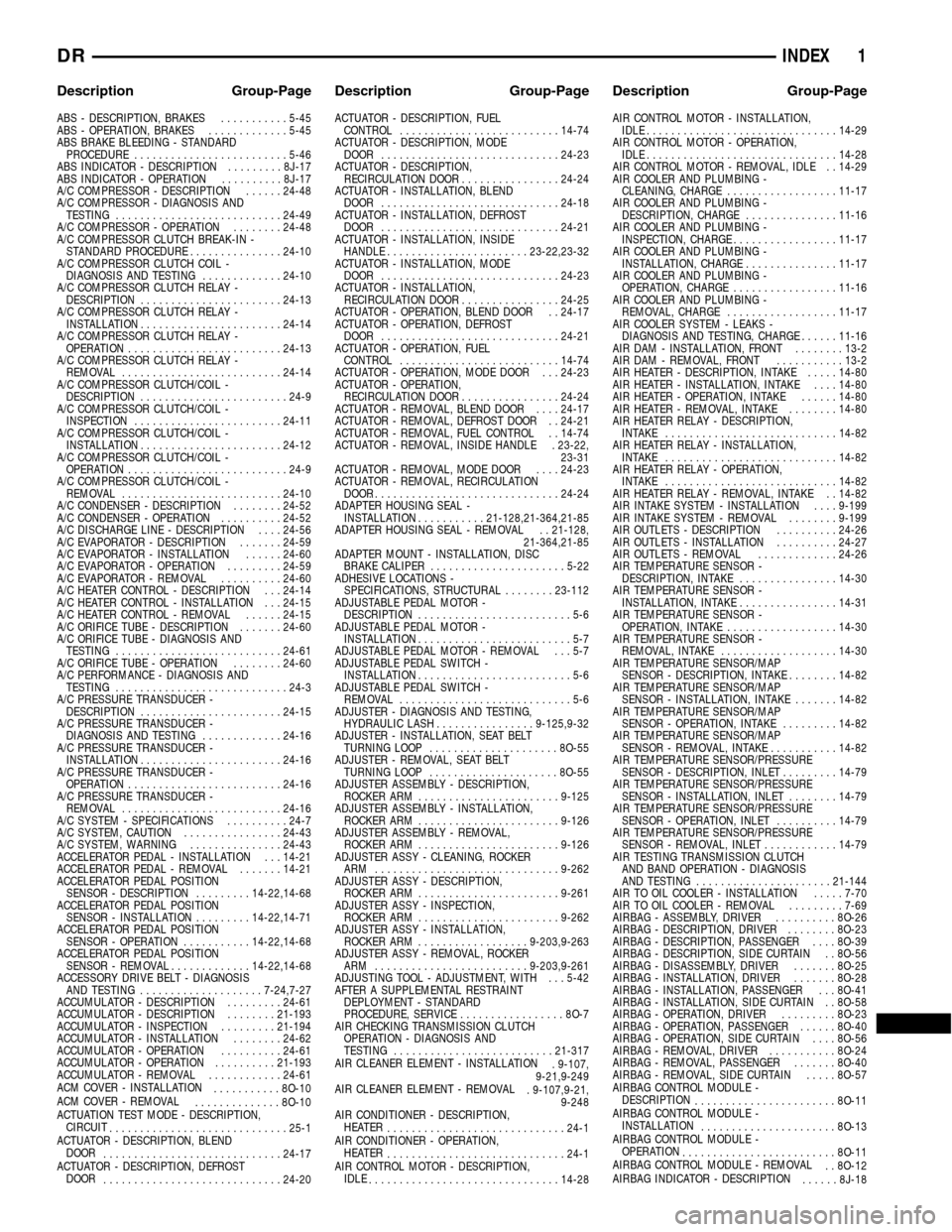
INDEX
ABS - DESCRIPTION, BRAKES...........5-45
ABS - OPERATION, BRAKES.............5-45
ABS BRAKE BLEEDING - STANDARD
PROCEDURE.........................5-46
ABS INDICATOR - DESCRIPTION.........8J-17
ABS INDICATOR - OPERATION..........8J-17
A/C COMPRESSOR - DESCRIPTION......24-48
A/C COMPRESSOR - DIAGNOSIS AND
TESTING...........................24-49
A/C COMPRESSOR - OPERATION........24-48
A/C COMPRESSOR CLUTCH BREAK-IN -
STANDARD PROCEDURE...............24-10
A/C COMPRESSOR CLUTCH COIL -
DIAGNOSIS AND TESTING.............24-10
A/C COMPRESSOR CLUTCH RELAY -
DESCRIPTION.......................24-13
A/C COMPRESSOR CLUTCH RELAY -
INSTALLATION.......................24-14
A/C COMPRESSOR CLUTCH RELAY -
OPERATION.........................24-13
A/C COMPRESSOR CLUTCH RELAY -
REMOVAL..........................24-14
A/C COMPRESSOR CLUTCH/COIL -
DESCRIPTION........................24-9
A/C COMPRESSOR CLUTCH/COIL -
INSPECTION........................24-11
A/C COMPRESSOR CLUTCH/COIL -
INSTALLATION.......................24-12
A/C COMPRESSOR CLUTCH/COIL -
OPERATION..........................24-9
A/C COMPRESSOR CLUTCH/COIL -
REMOVAL..........................24-10
A/C CONDENSER - DESCRIPTION........24-52
A/C CONDENSER - OPERATION..........24-52
A/C DISCHARGE LINE - DESCRIPTION....24-56
A/C EVAPORATOR - DESCRIPTION.......24-59
A/C EVAPORATOR - INSTALLATION......24-60
A/C EVAPORATOR - OPERATION.........24-59
A/C EVAPORATOR - REMOVAL..........24-60
A/C HEATER CONTROL - DESCRIPTION . . . 24-14
A/C HEATER CONTROL - INSTALLATION . . . 24-15
A/C HEATER CONTROL - REMOVAL......24-15
A/C ORIFICE TUBE - DESCRIPTION.......24-60
A/C ORIFICE TUBE - DIAGNOSIS AND
TESTING...........................24-61
A/C ORIFICE TUBE - OPERATION........24-60
A/C PERFORMANCE - DIAGNOSIS AND
TESTING............................24-3
A/C PRESSURE TRANSDUCER -
DESCRIPTION.......................24-15
A/C PRESSURE TRANSDUCER -
DIAGNOSIS AND TESTING.............24-16
A/C PRESSURE TRANSDUCER -
INSTALLATION.......................24-16
A/C PRESSURE TRANSDUCER -
OPERATION.........................24-16
A/C PRESSURE TRANSDUCER -
REMOVAL..........................24-16
A/C SYSTEM - SPECIFICATIONS..........24-7
A/C SYSTEM, CAUTION................24-43
A/C SYSTEM, WARNING...............24-43
ACCELERATOR PEDAL - INSTALLATION . . . 14-21
ACCELERATOR PEDAL - REMOVAL.......14-21
ACCELERATOR PEDAL POSITION
SENSOR - DESCRIPTION.........14-22,14-68
ACCELERATOR PEDAL POSITION
SENSOR - INSTALLATION.........14-22,14-71
ACCELERATOR PEDAL POSITION
SENSOR - OPERATION...........14-22,14-68
ACCELERATOR PEDAL POSITION
SENSOR - REMOVAL.............14-22,14-68
ACCESSORY DRIVE BELT - DIAGNOSIS
AND TESTING....................7-24,7-27
ACCUMULATOR - DESCRIPTION.........24-61
ACCUMULATOR - DESCRIPTION........21-193
ACCUMULATOR - INSPECTION.........21-194
ACCUMULATOR - INSTALLATION........24-62
ACCUMULATOR - OPERATION..........24-61
ACCUMULATOR - OPERATION..........21-193
ACCUMULATOR - REMOVAL............24-61
ACM COVER - INSTALLATION
...........8O-10
ACM COVER - REMOVAL
..............8O-10
ACTUATION TEST MODE - DESCRIPTION,
CIRCUIT
.............................25-1
ACTUATOR - DESCRIPTION, BLEND
DOOR
.............................24-17
ACTUATOR - DESCRIPTION, DEFROST
DOOR
.............................24-20ACTUATOR - DESCRIPTION, FUEL
CONTROL..........................14-74
ACTUATOR - DESCRIPTION, MODE
DOOR.............................24-23
ACTUATOR - DESCRIPTION,
RECIRCULATION DOOR................24-24
ACTUATOR - INSTALLATION, BLEND
DOOR.............................24-18
ACTUATOR - INSTALLATION, DEFROST
DOOR.............................24-21
ACTUATOR - INSTALLATION, INSIDE
HANDLE.......................23-22,23-32
ACTUATOR - INSTALLATION, MODE
DOOR.............................24-23
ACTUATOR - INSTALLATION,
RECIRCULATION DOOR................24-25
ACTUATOR - OPERATION, BLEND DOOR . . 24-17
ACTUATOR - OPERATION, DEFROST
DOOR.............................24-21
ACTUATOR - OPERATION, FUEL
CONTROL..........................14-74
ACTUATOR - OPERATION, MODE DOOR . . . 24-23
ACTUATOR - OPERATION,
RECIRCULATION DOOR................24-24
ACTUATOR - REMOVAL, BLEND DOOR....24-17
ACTUATOR - REMOVAL, DEFROST DOOR . . 24-21
ACTUATOR - REMOVAL, FUEL CONTROL . . 14-74
ACTUATOR - REMOVAL, INSIDE HANDLE . 23-22,
23-31
ACTUATOR - REMOVAL, MODE DOOR....24-23
ACTUATOR - REMOVAL, RECIRCULATION
DOOR...............................24-24
ADAPTER HOUSING SEAL -
INSTALLATION...........21-128,21-364,21-85
ADAPTER HOUSING SEAL - REMOVAL . . 21-128,
21-364,21-85
ADAPTER MOUNT - INSTALLATION, DISC
BRAKE CALIPER......................5-22
ADHESIVE LOCATIONS -
SPECIFICATIONS, STRUCTURAL........23-112
ADJUSTABLE PEDAL MOTOR -
DESCRIPTION.........................5-6
ADJUSTABLE PEDAL MOTOR -
INSTALLATION.........................5-7
ADJUSTABLE PEDAL MOTOR - REMOVAL . . . 5-7
ADJUSTABLE PEDAL SWITCH -
INSTALLATION.........................5-6
ADJUSTABLE PEDAL SWITCH -
REMOVAL............................5-6
ADJUSTER - DIAGNOSIS AND TESTING,
HYDRAULIC LASH................9-125,9-32
ADJUSTER - INSTALLATION, SEAT BELT
TURNING LOOP.....................8O-55
ADJUSTER - REMOVAL, SEAT BELT
TURNING LOOP.....................8O-55
ADJUSTER ASSEMBLY - DESCRIPTION,
ROCKER ARM.......................9-125
ADJUSTER ASSEMBLY - INSTALLATION,
ROCKER ARM.......................9-126
ADJUSTER ASSEMBLY - REMOVAL,
ROCKER ARM.......................9-126
ADJUSTER ASSY - CLEANING, ROCKER
ARM ..............................9-262
ADJUSTER ASSY - DESCRIPTION,
ROCKER ARM.......................9-261
ADJUSTER ASSY - INSPECTION,
ROCKER ARM.......................9-262
ADJUSTER ASSY - INSTALLATION,
ROCKER ARM..................9-203,9-263
ADJUSTER ASSY - REMOVAL, ROCKER
ARM .........................9-203,9-261
ADJUSTING TOOL - ADJUSTMENT, WITH . . . 5-42
AFTER A SUPPLEMENTAL RESTRAINT
DEPLOYMENT - STANDARD
PROCEDURE, SERVICE.................8O-7
AIR CHECKING TRANSMISSION CLUTCH
OPERATION - DIAGNOSIS AND
TESTING..........................21-317
AIR CLEANER ELEMENT - INSTALLATION
. 9-107,
9-21,9-249
AIR CLEANER ELEMENT - REMOVAL
. 9-107,9-21,
9-248
AIR CONDITIONER - DESCRIPTION,
HEATER
.............................24-1
AIR CONDITIONER - OPERATION,
HEATER
.............................24-1
AIR CONTROL MOTOR - DESCRIPTION,
IDLE
...............................14-28AIR CONTROL MOTOR - INSTALLATION,
IDLE...............................14-29
AIR CONTROL MOTOR - OPERATION,
IDLE...............................14-28
AIR CONTROL MOTOR - REMOVAL, IDLE . . 14-29
AIR COOLER AND PLUMBING -
CLEANING, CHARGE..................11-17
AIR COOLER AND PLUMBING -
DESCRIPTION, CHARGE...............11-16
AIR COOLER AND PLUMBING -
INSPECTION, CHARGE.................11-17
AIR COOLER AND PLUMBING -
INSTALLATION, CHARGE...............11-17
AIR COOLER AND PLUMBING -
OPERATION, CHARGE.................11-16
AIR COOLER AND PLUMBING -
REMOVAL, CHARGE..................11-17
AIR COOLER SYSTEM - LEAKS -
DIAGNOSIS AND TESTING, CHARGE......11-16
AIR DAM - INSTALLATION, FRONT........13-2
AIR DAM - REMOVAL, FRONT...........13-2
AIR HEATER - DESCRIPTION, INTAKE.....14-80
AIR HEATER - INSTALLATION, INTAKE....14-80
AIR HEATER - OPERATION, INTAKE......14-80
AIR HEATER - REMOVAL, INTAKE........14-80
AIR HEATER RELAY - DESCRIPTION,
INTAKE ............................14-82
AIR HEATER RELAY - INSTALLATION,
INTAKE ............................14-82
AIR HEATER RELAY - OPERATION,
INTAKE ............................14-82
AIR HEATER RELAY - REMOVAL, INTAKE . . 14-82
AIR INTAKE SYSTEM - INSTALLATION....9-199
AIR INTAKE SYSTEM - REMOVAL........9-199
AIR OUTLETS - DESCRIPTION..........24-26
AIR OUTLETS - INSTALLATION..........24-27
AIR OUTLETS - REMOVAL.............24-26
AIR TEMPERATURE SENSOR -
DESCRIPTION, INTAKE................14-30
AIR TEMPERATURE SENSOR -
INSTALLATION, INTAKE................14-31
AIR TEMPERATURE SENSOR -
OPERATION, INTAKE..................14-30
AIR TEMPERATURE SENSOR -
REMOVAL, INTAKE...................14-30
AIR TEMPERATURE SENSOR/MAP
SENSOR - DESCRIPTION, INTAKE........14-82
AIR TEMPERATURE SENSOR/MAP
SENSOR - INSTALLATION, INTAKE.......14-82
AIR TEMPERATURE SENSOR/MAP
SENSOR - OPERATION, INTAKE.........14-82
AIR TEMPERATURE SENSOR/MAP
SENSOR - REMOVAL, INTAKE...........14-82
AIR TEMPERATURE SENSOR/PRESSURE
SENSOR - DESCRIPTION, INLET.........14-79
AIR TEMPERATURE SENSOR/PRESSURE
SENSOR - INSTALLATION, INLET........14-79
AIR TEMPERATURE SENSOR/PRESSURE
SENSOR - OPERATION, INLET..........14-79
AIR TEMPERATURE SENSOR/PRESSURE
SENSOR - REMOVAL, INLET............14-79
AIR TESTING TRANSMISSION CLUTCH
AND BAND OPERATION - DIAGNOSIS
AND TESTING......................21-144
AIR TO OIL COOLER - INSTALLATION.....7-70
AIR TO OIL COOLER - REMOVAL.........7-69
AIRBAG - ASSEMBLY, DRIVER..........8O-26
AIRBAG - DESCRIPTION, DRIVER........8O-23
AIRBAG - DESCRIPTION, PASSENGER....8O-39
AIRBAG - DESCRIPTION, SIDE CURTAIN . . 8O-56
AIRBAG - DISASSEMBLY, DRIVER.......8O-25
AIRBAG - INSTALLATION, DRIVER.......8O-28
AIRBAG - INSTALLATION, PASSENGER . . . 8O-41
AIRBAG - INSTALLATION, SIDE CURTAIN . . 8O-58
AIRBAG - OPERATION, DRIVER.........8O-23
AIRBAG - OPERATION, PASSENGER......8O-40
AIRBAG - OPERATION, SIDE CURTAIN....8O-56
AIRBAG - REMOVAL, DRIVER...........8O-24
AIRBAG - REMOVAL, PASSENGER.......8O-40
AIRBAG - REMOVAL, SIDE CURTAIN.....8O-57
AIRBAG CONTROL MODULE -
DESCRIPTION
.......................8O-11
AIRBAG CONTROL MODULE -
INSTALLATION
......................8O-13
AIRBAG CONTROL MODULE -
OPERATION
.........................8O-11
AIRBAG CONTROL MODULE - REMOVAL
. . 8O-12
AIRBAG INDICATOR - DESCRIPTION
......8J-18
DRINDEX 1
Description Group-Page Description Group-Page Description Group-Page
Page 2597 of 2627
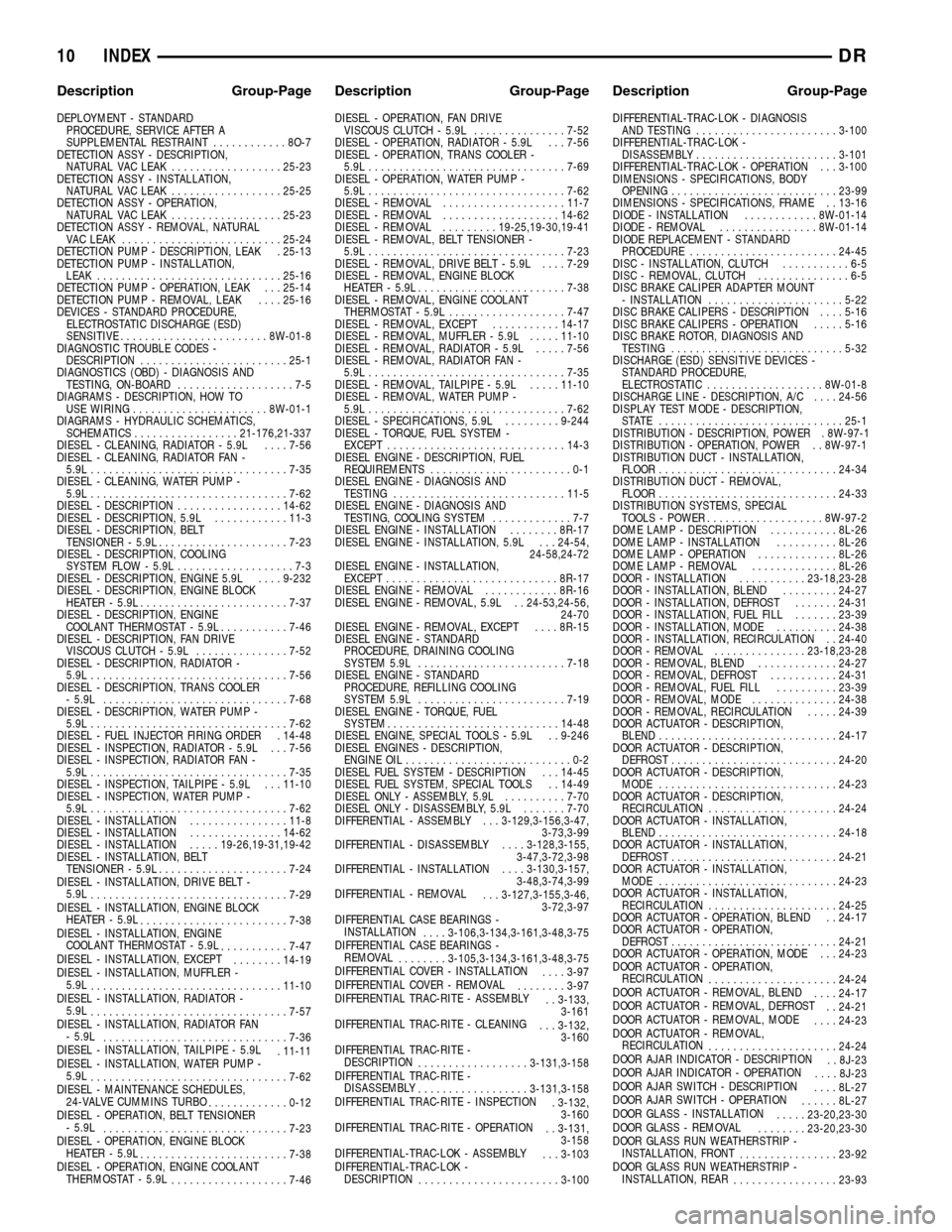
DEPLOYMENT - STANDARD
PROCEDURE, SERVICE AFTER A
SUPPLEMENTAL RESTRAINT............8O-7
DETECTION ASSY - DESCRIPTION,
NATURAL VAC LEAK..................25-23
DETECTION ASSY - INSTALLATION,
NATURAL VAC LEAK..................25-25
DETECTION ASSY - OPERATION,
NATURAL VAC LEAK..................25-23
DETECTION ASSY - REMOVAL, NATURAL
VAC LEAK..........................25-24
DETECTION PUMP - DESCRIPTION, LEAK . 25-13
DETECTION PUMP - INSTALLATION,
LEAK..............................25-16
DETECTION PUMP - OPERATION, LEAK . . . 25-14
DETECTION PUMP - REMOVAL, LEAK....25-16
DEVICES - STANDARD PROCEDURE,
ELECTROSTATIC DISCHARGE (ESD)
SENSITIVE........................8W-01-8
DIAGNOSTIC TROUBLE CODES -
DESCRIPTION........................25-1
DIAGNOSTICS (OBD) - DIAGNOSIS AND
TESTING, ON-BOARD...................7-5
DIAGRAMS - DESCRIPTION, HOW TO
USE WIRING......................8W-01-1
DIAGRAMS - HYDRAULIC SCHEMATICS,
SCHEMATICS.................21-176,21-337
DIESEL - CLEANING, RADIATOR - 5.9L....7-56
DIESEL - CLEANING, RADIATOR FAN -
5.9L................................7-35
DIESEL - CLEANING, WATER PUMP -
5.9L................................7-62
DIESEL - DESCRIPTION.................14-62
DIESEL - DESCRIPTION, 5.9L............11-3
DIESEL - DESCRIPTION, BELT
TENSIONER - 5.9L.....................7-23
DIESEL - DESCRIPTION, COOLING
SYSTEM FLOW - 5.9L...................7-3
DIESEL - DESCRIPTION, ENGINE 5.9L....9-232
DIESEL - DESCRIPTION, ENGINE BLOCK
HEATER - 5.9L........................7-37
DIESEL - DESCRIPTION, ENGINE
COOLANT THERMOSTAT - 5.9L...........7-46
DIESEL - DESCRIPTION, FAN DRIVE
VISCOUS CLUTCH - 5.9L...............7-52
DIESEL - DESCRIPTION, RADIATOR -
5.9L................................7-56
DIESEL - DESCRIPTION, TRANS COOLER
- 5.9L..............................7-68
DIESEL - DESCRIPTION, WATER PUMP -
5.9L................................7-62
DIESEL - FUEL INJECTOR FIRING ORDER . 14-48
DIESEL - INSPECTION, RADIATOR - 5.9L . . . 7-56
DIESEL - INSPECTION, RADIATOR FAN -
5.9L................................7-35
DIESEL - INSPECTION, TAILPIPE - 5.9L . . . 11-10
DIESEL - INSPECTION, WATER PUMP -
5.9L................................7-62
DIESEL - INSTALLATION................11-8
DIESEL - INSTALLATION...............14-62
DIESEL - INSTALLATION.....19-26,19-31,19-42
DIESEL - INSTALLATION, BELT
TENSIONER - 5.9L.....................7-24
DIESEL - INSTALLATION, DRIVE BELT -
5.9L
................................7-29
DIESEL - INSTALLATION, ENGINE BLOCK
HEATER - 5.9L
........................7-38
DIESEL - INSTALLATION, ENGINE
COOLANT THERMOSTAT - 5.9L
...........7-47
DIESEL - INSTALLATION, EXCEPT
........14-19
DIESEL - INSTALLATION, MUFFLER -
5.9L
...............................11-10
DIESEL - INSTALLATION, RADIATOR -
5.9L
................................7-57
DIESEL - INSTALLATION, RADIATOR FAN
- 5.9L
..............................7-36
DIESEL - INSTALLATION, TAILPIPE - 5.9L
. 11-11
DIESEL - INSTALLATION, WATER PUMP -
5.9L
................................7-62
DIESEL - MAINTENANCE SCHEDULES,
24-VALVE CUMMINS TURBO
.............0-12
DIESEL - OPERATION, BELT TENSIONER
- 5.9L
..............................7-23
DIESEL - OPERATION, ENGINE BLOCK
HEATER - 5.9L
........................7-38
DIESEL - OPERATION, ENGINE COOLANT
THERMOSTAT - 5.9L
...................7-46DIESEL - OPERATION, FAN DRIVE
VISCOUS CLUTCH - 5.9L...............7-52
DIESEL - OPERATION, RADIATOR - 5.9L . . . 7-56
DIESEL - OPERATION, TRANS COOLER -
5.9L................................7-69
DIESEL - OPERATION, WATER PUMP -
5.9L................................7-62
DIESEL - REMOVAL....................11-7
DIESEL - REMOVAL...................14-62
DIESEL - REMOVAL.........19-25,19-30,19-41
DIESEL - REMOVAL, BELT TENSIONER -
5.9L................................7-23
DIESEL - REMOVAL, DRIVE BELT - 5.9L....7-29
DIESEL - REMOVAL, ENGINE BLOCK
HEATER - 5.9L........................7-38
DIESEL - REMOVAL, ENGINE COOLANT
THERMOSTAT - 5.9L...................7-47
DIESEL - REMOVAL, EXCEPT...........14-17
DIESEL - REMOVAL, MUFFLER - 5.9L.....11-10
DIESEL - REMOVAL, RADIATOR - 5.9L.....7-56
DIESEL - REMOVAL, RADIATOR FAN -
5.9L................................7-35
DIESEL - REMOVAL, TAILPIPE - 5.9L.....11-10
DIESEL - REMOVAL, WATER PUMP -
5.9L................................7-62
DIESEL - SPECIFICATIONS, 5.9L.........9-244
DIESEL - TORQUE, FUEL SYSTEM -
EXCEPT.............................14-3
DIESEL ENGINE - DESCRIPTION, FUEL
REQUIREMENTS.......................0-1
DIESEL ENGINE - DIAGNOSIS AND
TESTING............................11-5
DIESEL ENGINE - DIAGNOSIS AND
TESTING, COOLING SYSTEM.............7-7
DIESEL ENGINE - INSTALLATION........8R-17
DIESEL ENGINE - INSTALLATION, 5.9L . . . 24-54,
24-58,24-72
DIESEL ENGINE - INSTALLATION,
EXCEPT............................8R-17
DIESEL ENGINE - REMOVAL............8R-16
DIESEL ENGINE - REMOVAL, 5.9L . . 24-53,24-56,
24-70
DIESEL ENGINE - REMOVAL, EXCEPT....8R-15
DIESEL ENGINE - STANDARD
PROCEDURE, DRAINING COOLING
SYSTEM 5.9L........................7-18
DIESEL ENGINE - STANDARD
PROCEDURE, REFILLING COOLING
SYSTEM 5.9L........................7-19
DIESEL ENGINE - TORQUE, FUEL
SYSTEM............................14-48
DIESEL ENGINE, SPECIAL TOOLS - 5.9L . . 9-246
DIESEL ENGINES - DESCRIPTION,
ENGINE OIL...........................0-2
DIESEL FUEL SYSTEM - DESCRIPTION . . . 14-45
DIESEL FUEL SYSTEM, SPECIAL TOOLS . . 14-49
DIESEL ONLY - ASSEMBLY, 5.9L..........7-70
DIESEL ONLY - DISASSEMBLY, 5.9L.......7-70
DIFFERENTIAL - ASSEMBLY . . . 3-129,3-156,3-47,
3-73,3-99
DIFFERENTIAL - DISASSEMBLY....3-128,3-155,
3-47,3-72,3-98
DIFFERENTIAL - INSTALLATION....3-130,3-157,
3-48,3-74,3-99
DIFFERENTIAL - REMOVAL
. . . 3-127,3-155,3-46,
3-72,3-97
DIFFERENTIAL CASE BEARINGS -
INSTALLATION
....3-106,3-134,3-161,3-48,3-75
DIFFERENTIAL CASE BEARINGS -
REMOVAL
........3-105,3-134,3-161,3-48,3-75
DIFFERENTIAL COVER - INSTALLATION
....3-97
DIFFERENTIAL COVER - REMOVAL
........3-97
DIFFERENTIAL TRAC-RITE - ASSEMBLY
. . 3-133,
3-161
DIFFERENTIAL TRAC-RITE - CLEANING
. . . 3-132,
3-160
DIFFERENTIAL TRAC-RITE -
DESCRIPTION
..................3-131,3-158
DIFFERENTIAL TRAC-RITE -
DISASSEMBLY
..................3-131,3-158
DIFFERENTIAL TRAC-RITE - INSPECTION
. 3-132,
3-160
DIFFERENTIAL TRAC-RITE - OPERATION
. . 3-131,
3-158
DIFFERENTIAL-TRAC-LOK - ASSEMBLY
. . . 3-103
DIFFERENTIAL-TRAC-LOK -
DESCRIPTION
.......................3-100DIFFERENTIAL-TRAC-LOK - DIAGNOSIS
AND TESTING.......................3-100
DIFFERENTIAL-TRAC-LOK -
DISASSEMBLY.......................3-101
DIFFERENTIAL-TRAC-LOK - OPERATION . . . 3-100
DIMENSIONS - SPECIFICATIONS, BODY
OPENING...........................23-99
DIMENSIONS - SPECIFICATIONS, FRAME . . 13-16
DIODE - INSTALLATION............8W-01-14
DIODE - REMOVAL................8W-01-14
DIODE REPLACEMENT - STANDARD
PROCEDURE........................24-45
DISC - INSTALLATION, CLUTCH...........6-5
DISC - REMOVAL, CLUTCH...............6-5
DISC BRAKE CALIPER ADAPTER MOUNT
- INSTALLATION......................5-22
DISC BRAKE CALIPERS - DESCRIPTION....5-16
DISC BRAKE CALIPERS - OPERATION.....5-16
DISC BRAKE ROTOR, DIAGNOSIS AND
TESTING............................5-32
DISCHARGE (ESD) SENSITIVE DEVICES -
STANDARD PROCEDURE,
ELECTROSTATIC...................8W-01-8
DISCHARGE LINE - DESCRIPTION, A/C....24-56
DISPLAY TEST MODE - DESCRIPTION,
STATE ..............................25-1
DISTRIBUTION - DESCRIPTION, POWER . 8W-97-1
DISTRIBUTION - OPERATION, POWER . . 8W-97-1
DISTRIBUTION DUCT - INSTALLATION,
FLOOR.............................24-34
DISTRIBUTION DUCT - REMOVAL,
FLOOR.............................24-33
DISTRIBUTION SYSTEMS, SPECIAL
TOOLS - POWER...................8W-97-2
DOME LAMP - DESCRIPTION...........8L-26
DOME LAMP - INSTALLATION..........8L-26
DOME LAMP - OPERATION.............8L-26
DOME LAMP - REMOVAL..............8L-26
DOOR - INSTALLATION...........23-18,23-28
DOOR - INSTALLATION, BLEND.........24-27
DOOR - INSTALLATION, DEFROST.......24-31
DOOR - INSTALLATION, FUEL FILL.......23-39
DOOR - INSTALLATION, MODE..........24-38
DOOR - INSTALLATION, RECIRCULATION . . 24-40
DOOR - REMOVAL...............23-18,23-28
DOOR - REMOVAL, BLEND.............24-27
DOOR - REMOVAL, DEFROST...........24-31
DOOR - REMOVAL, FUEL FILL..........23-39
DOOR - REMOVAL, MODE..............24-38
DOOR - REMOVAL, RECIRCULATION.....24-39
DOOR ACTUATOR - DESCRIPTION,
BLEND.............................24-17
DOOR ACTUATOR - DESCRIPTION,
DEFROST...........................24-20
DOOR ACTUATOR - DESCRIPTION,
MODE.............................24-23
DOOR ACTUATOR - DESCRIPTION,
RECIRCULATION.....................24-24
DOOR ACTUATOR - INSTALLATION,
BLEND.............................24-18
DOOR ACTUATOR - INSTALLATION,
DEFROST...........................24-21
DOOR ACTUATOR - INSTALLATION,
MODE.............................24-23
DOOR ACTUATOR - INSTALLATION,
RECIRCULATION.....................24-25
DOOR ACTUATOR - OPERATION, BLEND . . 24-17
DOOR ACTUATOR - OPERATION,
DEFROST...........................24-21
DOOR ACTUATOR - OPERATION, MODE . . . 24-23
DOOR ACTUATOR - OPERATION,
RECIRCULATION
.....................24-24
DOOR ACTUATOR - REMOVAL, BLEND
....24-17
DOOR ACTUATOR - REMOVAL, DEFROST
. . 24-21
DOOR ACTUATOR - REMOVAL, MODE
....24-23
DOOR ACTUATOR - REMOVAL,
RECIRCULATION
.....................24-24
DOOR AJAR INDICATOR - DESCRIPTION
. . 8J-23
DOOR AJAR INDICATOR - OPERATION
....8J-23
DOOR AJAR SWITCH - DESCRIPTION
....8L-27
DOOR AJAR SWITCH - OPERATION
......8L-27
DOOR GLASS - INSTALLATION
.....23-20,23-30
DOOR GLASS - REMOVAL
........23-20,23-30
DOOR GLASS RUN WEATHERSTRIP -
INSTALLATION, FRONT
................23-92
DOOR GLASS RUN WEATHERSTRIP -
INSTALLATION, REAR
.................23-93
10 INDEXDR
Description Group-Page Description Group-Page Description Group-Page
Page 2599 of 2627
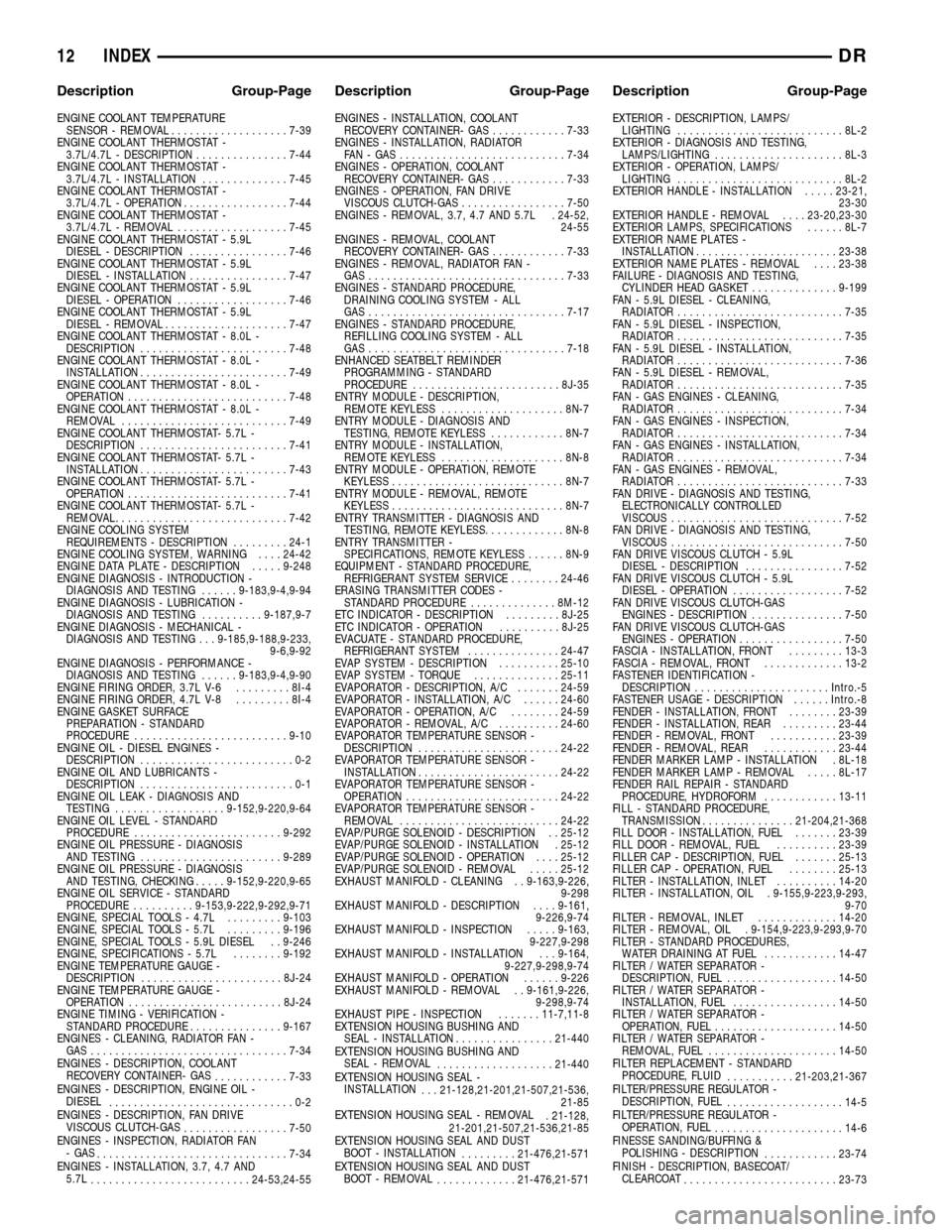
ENGINE COOLANT TEMPERATURE
SENSOR - REMOVAL...................7-39
ENGINE COOLANT THERMOSTAT -
3.7L/4.7L - DESCRIPTION...............7-44
ENGINE COOLANT THERMOSTAT -
3.7L/4.7L - INSTALLATION..............7-45
ENGINE COOLANT THERMOSTAT -
3.7L/4.7L - OPERATION.................7-44
ENGINE COOLANT THERMOSTAT -
3.7L/4.7L - REMOVAL..................7-45
ENGINE COOLANT THERMOSTAT - 5.9L
DIESEL - DESCRIPTION................7-46
ENGINE COOLANT THERMOSTAT - 5.9L
DIESEL - INSTALLATION................7-47
ENGINE COOLANT THERMOSTAT - 5.9L
DIESEL - OPERATION..................7-46
ENGINE COOLANT THERMOSTAT - 5.9L
DIESEL - REMOVAL....................7-47
ENGINE COOLANT THERMOSTAT - 8.0L -
DESCRIPTION........................7-48
ENGINE COOLANT THERMOSTAT - 8.0L -
INSTALLATION........................7-49
ENGINE COOLANT THERMOSTAT - 8.0L -
OPERATION..........................7-48
ENGINE COOLANT THERMOSTAT - 8.0L -
REMOVAL...........................7-49
ENGINE COOLANT THERMOSTAT-5.7L -
DESCRIPTION........................7-41
ENGINE COOLANT THERMOSTAT-5.7L -
INSTALLATION........................7-43
ENGINE COOLANT THERMOSTAT-5.7L -
OPERATION..........................7-41
ENGINE COOLANT THERMOSTAT-5.7L -
REMOVAL.............................7-42
ENGINE COOLING SYSTEM
REQUIREMENTS - DESCRIPTION.........24-1
ENGINE COOLING SYSTEM, WARNING....24-42
ENGINE DATA PLATE - DESCRIPTION.....9-248
ENGINE DIAGNOSIS - INTRODUCTION -
DIAGNOSIS AND TESTING......9-183,9-4,9-94
ENGINE DIAGNOSIS - LUBRICATION -
DIAGNOSIS AND TESTING..........9-187,9-7
ENGINE DIAGNOSIS - MECHANICAL -
DIAGNOSIS AND TESTING . . . 9-185,9-188,9-233,
9-6,9-92
ENGINE DIAGNOSIS - PERFORMANCE -
DIAGNOSIS AND TESTING......9-183,9-4,9-90
ENGINE FIRING ORDER, 3.7L V-6.........8I-4
ENGINE FIRING ORDER, 4.7L V-8.........8I-4
ENGINE GASKET SURFACE
PREPARATION - STANDARD
PROCEDURE.........................9-10
ENGINE OIL - DIESEL ENGINES -
DESCRIPTION.........................0-2
ENGINE OIL AND LUBRICANTS -
DESCRIPTION.........................0-1
ENGINE OIL LEAK - DIAGNOSIS AND
TESTING..................9-152,9-220,9-64
ENGINE OIL LEVEL - STANDARD
PROCEDURE........................9-292
ENGINE OIL PRESSURE - DIAGNOSIS
AND TESTING.......................9-289
ENGINE OIL PRESSURE - DIAGNOSIS
AND TESTING, CHECKING.....9-152,9-220,9-65
ENGINE OIL SERVICE - STANDARD
PROCEDURE..........9-153,9-222,9-292,9-71
ENGINE, SPECIAL TOOLS - 4.7L.........9-103
ENGINE, SPECIAL TOOLS - 5.7L.........9-196
ENGINE, SPECIAL TOOLS - 5.9L DIESEL . . 9-246
ENGINE, SPECIFICATIONS - 5.7L........9-192
ENGINE TEMPERATURE GAUGE -
DESCRIPTION.......................8J-24
ENGINE TEMPERATURE GAUGE -
OPERATION.........................8J-24
ENGINE TIMING - VERIFICATION -
STANDARD PROCEDURE...............9-167
ENGINES - CLEANING, RADIATOR FAN -
GAS................................7-34
ENGINES - DESCRIPTION, COOLANT
RECOVERY CONTAINER- GAS
............7-33
ENGINES - DESCRIPTION, ENGINE OIL -
DIESEL
..............................0-2
ENGINES - DESCRIPTION, FAN DRIVE
VISCOUS CLUTCH-GAS
.................7-50
ENGINES - INSPECTION, RADIATOR FAN
- GAS
...............................7-34
ENGINES - INSTALLATION, 3.7, 4.7 AND
5.7L
..........................24-53,24-55ENGINES - INSTALLATION, COOLANT
RECOVERY CONTAINER- GAS............7-33
ENGINES - INSTALLATION, RADIATOR
FAN - GAS...........................7-34
ENGINES - OPERATION, COOLANT
RECOVERY CONTAINER- GAS............7-33
ENGINES - OPERATION, FAN DRIVE
VISCOUS CLUTCH-GAS.................7-50
ENGINES - REMOVAL, 3.7, 4.7 AND 5.7L . 24-52,
24-55
ENGINES - REMOVAL, COOLANT
RECOVERY CONTAINER- GAS............7-33
ENGINES - REMOVAL, RADIATOR FAN -
GAS................................7-33
ENGINES - STANDARD PROCEDURE,
DRAINING COOLING SYSTEM - ALL
GAS................................7-17
ENGINES - STANDARD PROCEDURE,
REFILLING COOLING SYSTEM - ALL
GAS................................7-18
ENHANCED SEATBELT REMINDER
PROGRAMMING - STANDARD
PROCEDURE........................8J-35
ENTRY MODULE - DESCRIPTION,
REMOTE KEYLESS....................8N-7
ENTRY MODULE - DIAGNOSIS AND
TESTING, REMOTE KEYLESS............8N-7
ENTRY MODULE - INSTALLATION,
REMOTE KEYLESS....................8N-8
ENTRY MODULE - OPERATION, REMOTE
KEYLESS............................8N-7
ENTRY MODULE - REMOVAL, REMOTE
KEYLESS............................8N-7
ENTRY TRANSMITTER - DIAGNOSIS AND
TESTING, REMOTE KEYLESS..............8N-8
ENTRY TRANSMITTER -
SPECIFICATIONS, REMOTE KEYLESS......8N-9
EQUIPMENT - STANDARD PROCEDURE,
REFRIGERANT SYSTEM SERVICE........24-46
ERASING TRANSMITTER CODES -
STANDARD PROCEDURE..............8M-12
ETC INDICATOR - DESCRIPTION.........8J-25
ETC INDICATOR - OPERATION..........8J-25
EVACUATE - STANDARD PROCEDURE,
REFRIGERANT SYSTEM...............24-47
EVAP SYSTEM - DESCRIPTION..........25-10
EVAP SYSTEM - TORQUE..............25-11
EVAPORATOR - DESCRIPTION, A/C.......24-59
EVAPORATOR - INSTALLATION, A/C......24-60
EVAPORATOR - OPERATION, A/C........24-59
EVAPORATOR - REMOVAL, A/C..........24-60
EVAPORATOR TEMPERATURE SENSOR -
DESCRIPTION.......................24-22
EVAPORATOR TEMPERATURE SENSOR -
INSTALLATION.......................24-22
EVAPORATOR TEMPERATURE SENSOR -
OPERATION.........................24-22
EVAPORATOR TEMPERATURE SENSOR -
REMOVAL..........................24-22
EVAP/PURGE SOLENOID - DESCRIPTION . . 25-12
EVAP/PURGE SOLENOID - INSTALLATION . 25-12
EVAP/PURGE SOLENOID - OPERATION....25-12
EVAP/PURGE SOLENOID - REMOVAL.....25-12
EXHAUST MANIFOLD - CLEANING . . 9-163,9-226,
9-298
EXHAUST MANIFOLD - DESCRIPTION....9-161,
9-226,9-74
EXHAUST MANIFOLD - INSPECTION.....9-163,
9-227,9-298
EXHAUST MANIFOLD - INSTALLATION . . . 9-164,
9-227,9-298,9-74
EXHAUST MANIFOLD - OPERATION......9-226
EXHAUST MANIFOLD - REMOVAL . . 9-161,9-226,
9-298,9-74
EXHAUST PIPE - INSPECTION.......11-7,11-8
EXTENSION HOUSING BUSHING AND
SEAL - INSTALLATION................21-440
EXTENSION HOUSING BUSHING AND
SEAL - REMOVAL
...................21-440
EXTENSION HOUSING SEAL -
INSTALLATION
. . . 21-128,21-201,21-507,21-536,
21-85
EXTENSION HOUSING SEAL - REMOVAL
. 21-128,
21-201,21-507,21-536,21-85
EXTENSION HOUSING SEAL AND DUST
BOOT - INSTALLATION
.........21-476,21-571
EXTENSION HOUSING SEAL AND DUST
BOOT - REMOVAL
.............21-476,21-571EXTERIOR - DESCRIPTION, LAMPS/
LIGHTING...........................8L-2
EXTERIOR - DIAGNOSIS AND TESTING,
LAMPS/LIGHTING.....................8L-3
EXTERIOR - OPERATION, LAMPS/
LIGHTING...........................8L-2
EXTERIOR HANDLE - INSTALLATION.....23-21,
23-30
EXTERIOR HANDLE - REMOVAL....23-20,23-30
EXTERIOR LAMPS, SPECIFICATIONS......8L-7
EXTERIOR NAME PLATES -
INSTALLATION.......................23-38
EXTERIOR NAME PLATES - REMOVAL....23-38
FAILURE - DIAGNOSIS AND TESTING,
CYLINDER HEAD GASKET..............9-199
FAN - 5.9L DIESEL - CLEANING,
RADIATOR...........................7-35
FAN - 5.9L DIESEL - INSPECTION,
RADIATOR...........................7-35
FAN - 5.9L DIESEL - INSTALLATION,
RADIATOR...........................7-36
FAN - 5.9L DIESEL - REMOVAL,
RADIATOR...........................7-35
FAN - GAS ENGINES - CLEANING,
RADIATOR...........................7-34
FAN - GAS ENGINES - INSPECTION,
RADIATOR...........................7-34
FAN - GAS ENGINES - INSTALLATION,
RADIATOR...........................7-34
FAN - GAS ENGINES - REMOVAL,
RADIATOR...........................7-33
FAN DRIVE - DIAGNOSIS AND TESTING,
ELECTRONICALLY CONTROLLED
VISCOUS............................7-52
FAN DRIVE - DIAGNOSIS AND TESTING,
VISCOUS............................7-50
FAN DRIVE VISCOUS CLUTCH - 5.9L
DIESEL - DESCRIPTION................7-52
FAN DRIVE VISCOUS CLUTCH - 5.9L
DIESEL - OPERATION..................7-52
FAN DRIVE VISCOUS CLUTCH-GAS
ENGINES - DESCRIPTION...............7-50
FAN DRIVE VISCOUS CLUTCH-GAS
ENGINES - OPERATION.................7-50
FASCIA - INSTALLATION, FRONT.........13-3
FASCIA - REMOVAL, FRONT.............13-2
FASTENER IDENTIFICATION -
DESCRIPTION......................Intro.-5
FASTENER USAGE - DESCRIPTION......Intro.-8
FENDER - INSTALLATION, FRONT........23-39
FENDER - INSTALLATION, REAR.........23-44
FENDER - REMOVAL, FRONT...........23-39
FENDER - REMOVAL, REAR............23-44
FENDER MARKER LAMP - INSTALLATION . 8L-18
FENDER MARKER LAMP - REMOVAL.....8L-17
FENDER RAIL REPAIR - STANDARD
PROCEDURE, HYDROFORM............13-11
FILL - STANDARD PROCEDURE,
TRANSMISSION...............21-204,21-368
FILL DOOR - INSTALLATION, FUEL.......23-39
FILL DOOR - REMOVAL, FUEL..........23-39
FILLER CAP - DESCRIPTION, FUEL.......25-13
FILLER CAP - OPERATION, FUEL........25-13
FILTER - INSTALLATION, INLET..........14-20
FILTER - INSTALLATION, OIL . 9-155,9-223,9-293,
9-70
FILTER - REMOVAL, INLET.............14-20
FILTER - REMOVAL, OIL . 9-154,9-223,9-293,9-70
FILTER - STANDARD PROCEDURES,
WATER DRAINING AT FUEL............14-47
FILTER / WATER SEPARATOR -
DESCRIPTION, FUEL..................14-50
FILTER / WATER SEPARATOR -
INSTALLATION, FUEL.................14-50
FILTER / WATER SEPARATOR -
OPERATION, FUEL....................14-50
FILTER / WATER SEPARATOR -
REMOVAL, FUEL.....................14-50
FILTER REPLACEMENT - STANDARD
PROCEDURE, FLUID
...........21-203,21-367
FILTER/PRESSURE REGULATOR -
DESCRIPTION, FUEL
...................14-5
FILTER/PRESSURE REGULATOR -
OPERATION, FUEL
.....................14-6
FINESSE SANDING/BUFFING &
POLISHING - DESCRIPTION
............23-74
FINISH - DESCRIPTION, BASECOAT/
CLEARCOAT
.........................23-73
12 INDEXDR
Description Group-Page Description Group-Page Description Group-Page
Page 2604 of 2627
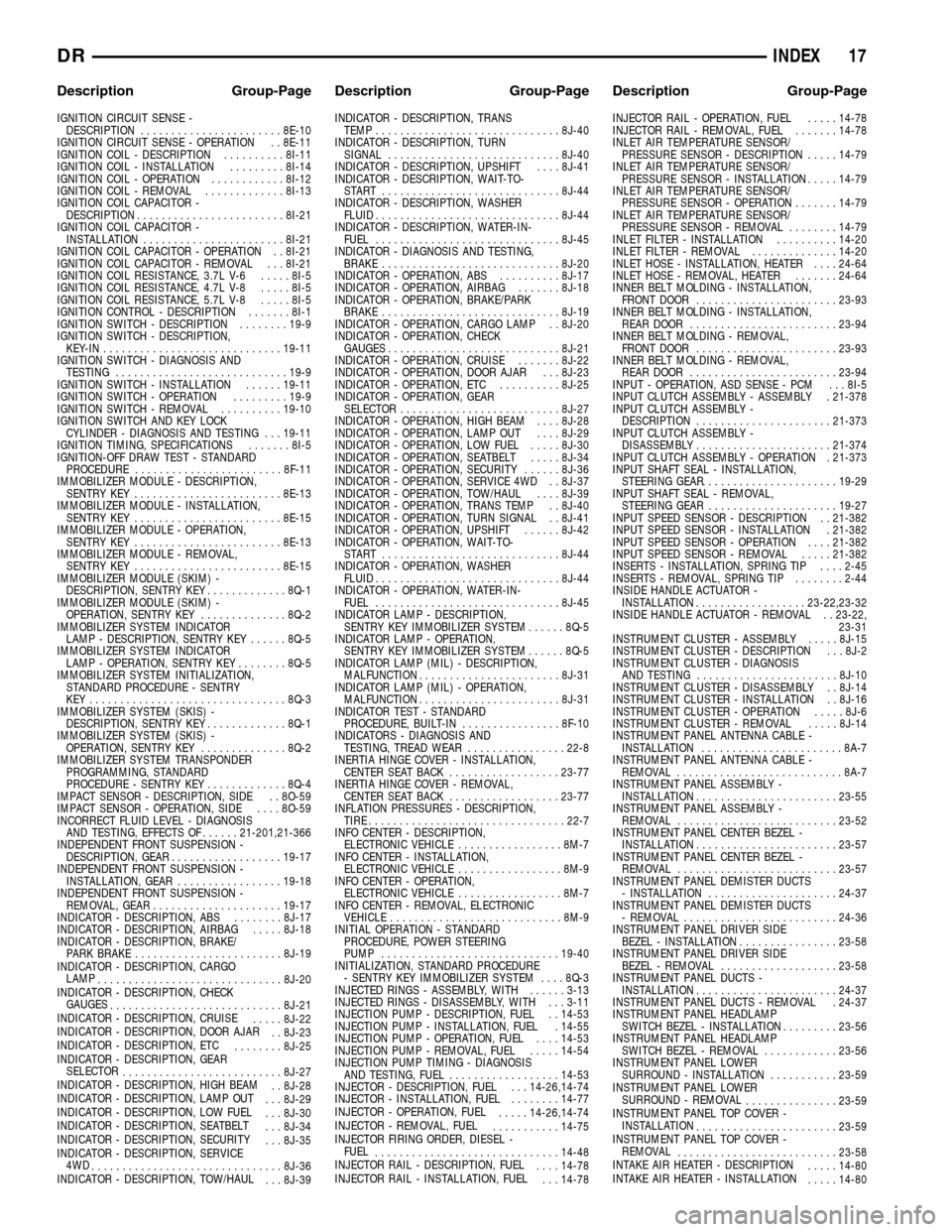
IGNITION CIRCUIT SENSE -
DESCRIPTION.......................8E-10
IGNITION CIRCUIT SENSE - OPERATION . . 8E-11
IGNITION COIL - DESCRIPTION..........8I-11
IGNITION COIL - INSTALLATION.........8I-14
IGNITION COIL - OPERATION............8I-12
IGNITION COIL - REMOVAL.............8I-13
IGNITION COIL CAPACITOR -
DESCRIPTION........................8I-21
IGNITION COIL CAPACITOR -
INSTALLATION.......................8I-21
IGNITION COIL CAPACITOR - OPERATION . . 8I-21
IGNITION COIL CAPACITOR - REMOVAL . . . 8I-21
IGNITION COIL RESISTANCE, 3.7L V-6.....8I-5
IGNITION COIL RESISTANCE, 4.7L V-8.....8I-5
IGNITION COIL RESISTANCE, 5.7L V-8.....8I-5
IGNITION CONTROL - DESCRIPTION.......8I-1
IGNITION SWITCH - DESCRIPTION........19-9
IGNITION SWITCH - DESCRIPTION,
KEY-IN.............................19-11
IGNITION SWITCH - DIAGNOSIS AND
TESTING............................19-9
IGNITION SWITCH - INSTALLATION......19-11
IGNITION SWITCH - OPERATION.........19-9
IGNITION SWITCH - REMOVAL..........19-10
IGNITION SWITCH AND KEY LOCK
CYLINDER - DIAGNOSIS AND TESTING . . . 19-11
IGNITION TIMING, SPECIFICATIONS.......8I-5
IGNITION-OFF DRAW TEST - STANDARD
PROCEDURE........................8F-11
IMMOBILIZER MODULE - DESCRIPTION,
SENTRY KEY........................8E-13
IMMOBILIZER MODULE - INSTALLATION,
SENTRY KEY........................8E-15
IMMOBILIZER MODULE - OPERATION,
SENTRY KEY........................8E-13
IMMOBILIZER MODULE - REMOVAL,
SENTRY KEY........................8E-15
IMMOBILIZER MODULE (SKIM) -
DESCRIPTION, SENTRY KEY.............8Q-1
IMMOBILIZER MODULE (SKIM) -
OPERATION, SENTRY KEY..............8Q-2
IMMOBILIZER SYSTEM INDICATOR
LAMP - DESCRIPTION, SENTRY KEY......8Q-5
IMMOBILIZER SYSTEM INDICATOR
LAMP - OPERATION, SENTRY KEY........8Q-5
IMMOBILIZER SYSTEM INITIALIZATION,
STANDARD PROCEDURE - SENTRY
KEY................................8Q-3
IMMOBILIZER SYSTEM (SKIS) -
DESCRIPTION, SENTRY KEY.............8Q-1
IMMOBILIZER SYSTEM (SKIS) -
OPERATION, SENTRY KEY..............8Q-2
IMMOBILIZER SYSTEM TRANSPONDER
PROGRAMMING, STANDARD
PROCEDURE - SENTRY KEY.............8Q-4
IMPACT SENSOR - DESCRIPTION, SIDE . . 8O-59
IMPACT SENSOR - OPERATION, SIDE....8O-59
INCORRECT FLUID LEVEL - DIAGNOSIS
AND TESTING, EFFECTS OF......21-201,21-366
INDEPENDENT FRONT SUSPENSION -
DESCRIPTION, GEAR..................19-17
INDEPENDENT FRONT SUSPENSION -
INSTALLATION, GEAR.................19-18
INDEPENDENT FRONT SUSPENSION -
REMOVAL, GEAR.....................19-17
INDICATOR - DESCRIPTION, ABS........8J-17
INDICATOR - DESCRIPTION, AIRBAG.....8J-18
INDICATOR - DESCRIPTION, BRAKE/
PARK BRAKE........................8J-19
INDICATOR - DESCRIPTION, CARGO
LAMP
..............................8J-20
INDICATOR - DESCRIPTION, CHECK
GAUGES
............................8J-21
INDICATOR - DESCRIPTION, CRUISE
.....8J-22
INDICATOR - DESCRIPTION, DOOR AJAR
. . 8J-23
INDICATOR - DESCRIPTION, ETC
........8J-25
INDICATOR - DESCRIPTION, GEAR
SELECTOR
..........................8J-27
INDICATOR - DESCRIPTION, HIGH BEAM
. . 8J-28
INDICATOR - DESCRIPTION, LAMP OUT
. . . 8J-29
INDICATOR - DESCRIPTION, LOW FUEL
. . . 8J-30
INDICATOR - DESCRIPTION, SEATBELT
. . . 8J-34
INDICATOR - DESCRIPTION, SECURITY
. . . 8J-35
INDICATOR - DESCRIPTION, SERVICE
4WD
...............................8J-36
INDICATOR - DESCRIPTION, TOW/HAUL
. . . 8J-39INDICATOR - DESCRIPTION, TRANS
TEMP..............................8J-40
INDICATOR - DESCRIPTION, TURN
SIGNAL............................8J-40
INDICATOR - DESCRIPTION, UPSHIFT....8J-41
INDICATOR - DESCRIPTION, WAIT-TO-
START .............................8J-44
INDICATOR - DESCRIPTION, WASHER
FLUID..............................8J-44
INDICATOR - DESCRIPTION, WATER-IN-
FUEL..............................8J-45
INDICATOR - DIAGNOSIS AND TESTING,
BRAKE.............................8J-20
INDICATOR - OPERATION, ABS..........8J-17
INDICATOR - OPERATION, AIRBAG.......8J-18
INDICATOR - OPERATION, BRAKE/PARK
BRAKE.............................8J-19
INDICATOR - OPERATION, CARGO LAMP . . 8J-20
INDICATOR - OPERATION, CHECK
GAUGES............................8J-21
INDICATOR - OPERATION, CRUISE.......8J-22
INDICATOR - OPERATION, DOOR AJAR . . . 8J-23
INDICATOR - OPERATION, ETC..........8J-25
INDICATOR - OPERATION, GEAR
SELECTOR..........................8J-27
INDICATOR - OPERATION, HIGH BEAM....8J-28
INDICATOR - OPERATION, LAMP OUT....8J-29
INDICATOR - OPERATION, LOW FUEL.....8J-30
INDICATOR - OPERATION, SEATBELT.....8J-34
INDICATOR - OPERATION, SECURITY......8J-36
INDICATOR - OPERATION, SERVICE 4WD . . 8J-37
INDICATOR - OPERATION, TOW/HAUL....8J-39
INDICATOR - OPERATION, TRANS TEMP . . 8J-40
INDICATOR - OPERATION, TURN SIGNAL . . 8J-41
INDICATOR - OPERATION, UPSHIFT......8J-42
INDICATOR - OPERATION, WAIT-TO-
START .............................8J-44
INDICATOR - OPERATION, WASHER
FLUID..............................8J-44
INDICATOR - OPERATION, WATER-IN-
FUEL..............................8J-45
INDICATOR LAMP - DESCRIPTION,
SENTRY KEY IMMOBILIZER SYSTEM......8Q-5
INDICATOR LAMP - OPERATION,
SENTRY KEY IMMOBILIZER SYSTEM......8Q-5
INDICATOR LAMP (MIL) - DESCRIPTION,
MALFUNCTION.......................8J-31
INDICATOR LAMP (MIL) - OPERATION,
MALFUNCTION.......................8J-31
INDICATOR TEST - STANDARD
PROCEDURE, BUILT-IN................8F-10
INDICATORS - DIAGNOSIS AND
TESTING, TREAD WEAR................22-8
INERTIA HINGE COVER - INSTALLATION,
CENTER SEAT BACK..................23-77
INERTIA HINGE COVER - REMOVAL,
CENTER SEAT BACK..................23-77
INFLATION PRESSURES - DESCRIPTION,
TIRE................................22-7
INFO CENTER - DESCRIPTION,
ELECTRONIC VEHICLE.................8M-7
INFO CENTER - INSTALLATION,
ELECTRONIC VEHICLE.................8M-9
INFO CENTER - OPERATION,
ELECTRONIC VEHICLE.................8M-7
INFO CENTER - REMOVAL, ELECTRONIC
VEHICLE............................8M-9
INITIAL OPERATION - STANDARD
PROCEDURE, POWER STEERING
PUMP.............................19-40
INITIALIZATION, STANDARD PROCEDURE
- SENTRY KEY IMMOBILIZER SYSTEM....8Q-3
INJECTED RINGS - ASSEMBLY, WITH......3-13
INJECTED RINGS - DISASSEMBLY, WITH . . . 3-11
INJECTION PUMP - DESCRIPTION, FUEL . . 14-53
INJECTION PUMP - INSTALLATION, FUEL . 14-55
INJECTION PUMP - OPERATION, FUEL....14-53
INJECTION PUMP - REMOVAL, FUEL.....14-54
INJECTION PUMP TIMING - DIAGNOSIS
AND TESTING, FUEL..................14-53
INJECTOR - DESCRIPTION, FUEL . . . 14-26,14-74
INJECTOR - INSTALLATION, FUEL........14-77
INJECTOR - OPERATION, FUEL
.....14-26,14-74
INJECTOR - REMOVAL, FUEL
...........14-75
INJECTOR FIRING ORDER, DIESEL -
FUEL
..............................14-48
INJECTOR RAIL - DESCRIPTION, FUEL
....14-78
INJECTOR RAIL - INSTALLATION, FUEL
. . . 14-78INJECTOR RAIL - OPERATION, FUEL.....14-78
INJECTOR RAIL - REMOVAL, FUEL.......14-78
INLET AIR TEMPERATURE SENSOR/
PRESSURE SENSOR - DESCRIPTION.....14-79
INLET AIR TEMPERATURE SENSOR/
PRESSURE SENSOR - INSTALLATION.....14-79
INLET AIR TEMPERATURE SENSOR/
PRESSURE SENSOR - OPERATION.......14-79
INLET AIR TEMPERATURE SENSOR/
PRESSURE SENSOR - REMOVAL........14-79
INLET FILTER - INSTALLATION..........14-20
INLET FILTER - REMOVAL..............14-20
INLET HOSE - INSTALLATION, HEATER....24-64
INLET HOSE - REMOVAL, HEATER.......24-64
INNER BELT MOLDING - INSTALLATION,
FRONT DOOR.......................23-93
INNER BELT MOLDING - INSTALLATION,
REAR DOOR........................23-94
INNER BELT MOLDING - REMOVAL,
FRONT DOOR.......................23-93
INNER BELT MOLDING - REMOVAL,
REAR DOOR........................23-94
INPUT - OPERATION, ASD SENSE - PCM . . . 8I-5
INPUT CLUTCH ASSEMBLY - ASSEMBLY . 21-378
INPUT CLUTCH ASSEMBLY -
DESCRIPTION......................21-373
INPUT CLUTCH ASSEMBLY -
DISASSEMBLY......................21-374
INPUT CLUTCH ASSEMBLY - OPERATION . 21-373
INPUT SHAFT SEAL - INSTALLATION,
STEERING GEAR.......................19-29
INPUT SHAFT SEAL - REMOVAL,
STEERING GEAR.....................19-27
INPUT SPEED SENSOR - DESCRIPTION . . 21-382
INPUT SPEED SENSOR - INSTALLATION . 21-382
INPUT SPEED SENSOR - OPERATION....21-382
INPUT SPEED SENSOR - REMOVAL.....21-382
INSERTS - INSTALLATION, SPRING TIP....2-45
INSERTS - REMOVAL, SPRING TIP........2-44
INSIDE HANDLE ACTUATOR -
INSTALLATION..................23-22,23-32
INSIDE HANDLE ACTUATOR - REMOVAL . . 23-22,
23-31
INSTRUMENT CLUSTER - ASSEMBLY.....8J-15
INSTRUMENT CLUSTER - DESCRIPTION . . . 8J-2
INSTRUMENT CLUSTER - DIAGNOSIS
AND TESTING.......................8J-10
INSTRUMENT CLUSTER - DISASSEMBLY . . 8J-14
INSTRUMENT CLUSTER - INSTALLATION . . 8J-16
INSTRUMENT CLUSTER - OPERATION.....8J-6
INSTRUMENT CLUSTER - REMOVAL.....8J-14
INSTRUMENT PANEL ANTENNA CABLE -
INSTALLATION.......................8A-7
INSTRUMENT PANEL ANTENNA CABLE -
REMOVAL...........................8A-7
INSTRUMENT PANEL ASSEMBLY -
INSTALLATION.......................23-55
INSTRUMENT PANEL ASSEMBLY -
REMOVAL..........................23-52
INSTRUMENT PANEL CENTER BEZEL -
INSTALLATION.......................23-57
INSTRUMENT PANEL CENTER BEZEL -
REMOVAL..........................23-57
INSTRUMENT PANEL DEMISTER DUCTS
- INSTALLATION.....................24-37
INSTRUMENT PANEL DEMISTER DUCTS
- REMOVAL.........................24-36
INSTRUMENT PANEL DRIVER SIDE
BEZEL - INSTALLATION................23-58
INSTRUMENT PANEL DRIVER SIDE
BEZEL - REMOVAL...................23-58
INSTRUMENT PANEL DUCTS -
INSTALLATION.......................24-37
INSTRUMENT PANEL DUCTS - REMOVAL . 24-37
INSTRUMENT PANEL HEADLAMP
SWITCH BEZEL - INSTALLATION.........23-56
INSTRUMENT PANEL HEADLAMP
SWITCH BEZEL - REMOVAL............23-56
INSTRUMENT PANEL LOWER
SURROUND - INSTALLATION...........23-59
INSTRUMENT PANEL LOWER
SURROUND - REMOVAL
...............23-59
INSTRUMENT PANEL TOP COVER -
INSTALLATION
.......................23-59
INSTRUMENT PANEL TOP COVER -
REMOVAL
..........................23-58
INTAKE AIR HEATER - DESCRIPTION
.....14-80
INTAKE AIR HEATER - INSTALLATION
.....14-80
DRINDEX 17
Description Group-Page Description Group-Page Description Group-Page