key DODGE RAM 1500 1998 2.G Workshop Manual
[x] Cancel search | Manufacturer: DODGE, Model Year: 1998, Model line: RAM 1500, Model: DODGE RAM 1500 1998 2.GPages: 2627
Page 35 of 2627
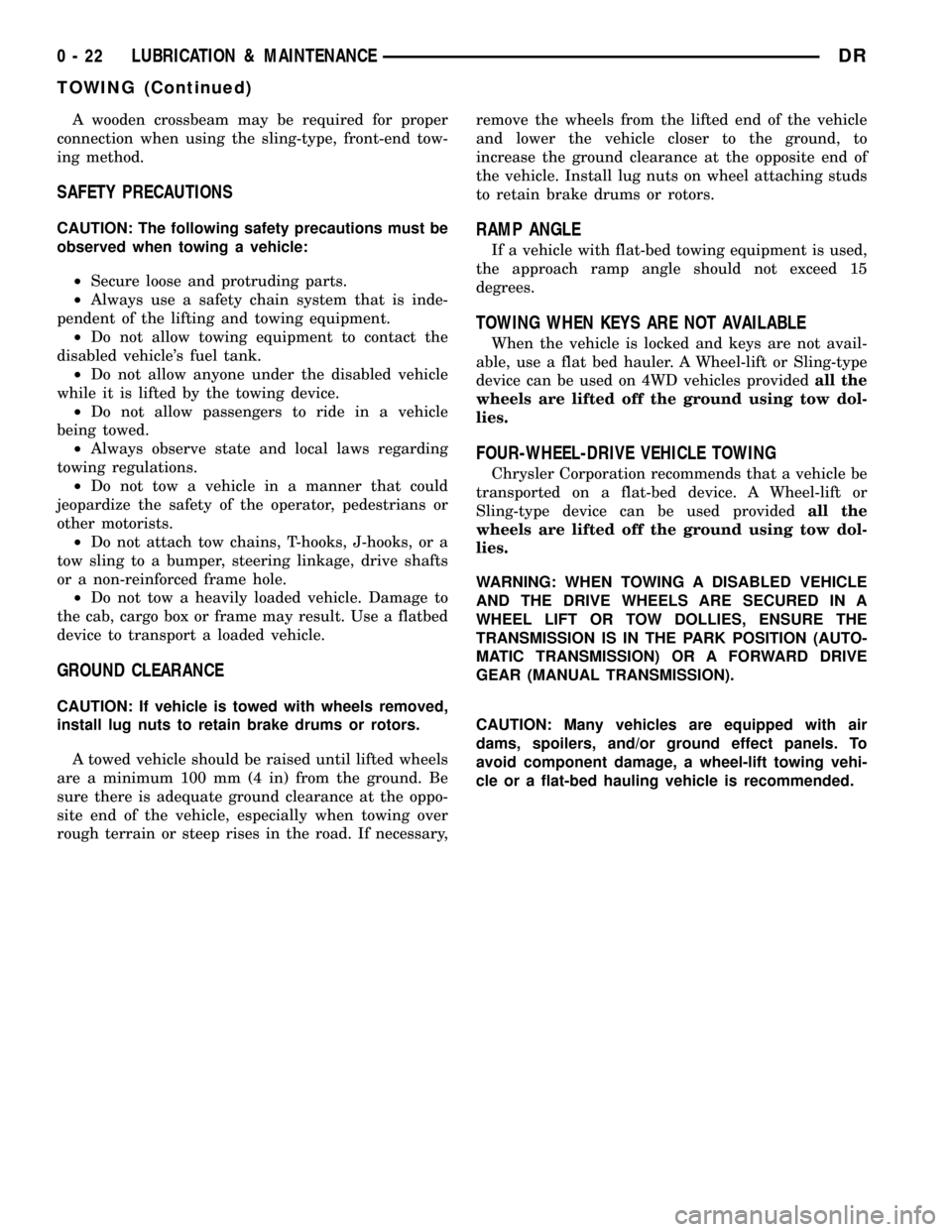
A wooden crossbeam may be required for proper
connection when using the sling-type, front-end tow-
ing method.
SAFETY PRECAUTIONS
CAUTION: The following safety precautions must be
observed when towing a vehicle:
²Secure loose and protruding parts.
²Always use a safety chain system that is inde-
pendent of the lifting and towing equipment.
²Do not allow towing equipment to contact the
disabled vehicle's fuel tank.
²Do not allow anyone under the disabled vehicle
while it is lifted by the towing device.
²Do not allow passengers to ride in a vehicle
being towed.
²Always observe state and local laws regarding
towing regulations.
²Do not tow a vehicle in a manner that could
jeopardize the safety of the operator, pedestrians or
other motorists.
²Do not attach tow chains, T-hooks, J-hooks, or a
tow sling to a bumper, steering linkage, drive shafts
or a non-reinforced frame hole.
²Do not tow a heavily loaded vehicle. Damage to
the cab, cargo box or frame may result. Use a flatbed
device to transport a loaded vehicle.
GROUND CLEARANCE
CAUTION: If vehicle is towed with wheels removed,
install lug nuts to retain brake drums or rotors.
A towed vehicle should be raised until lifted wheels
are a minimum 100 mm (4 in) from the ground. Be
sure there is adequate ground clearance at the oppo-
site end of the vehicle, especially when towing over
rough terrain or steep rises in the road. If necessary,remove the wheels from the lifted end of the vehicle
and lower the vehicle closer to the ground, to
increase the ground clearance at the opposite end of
the vehicle. Install lug nuts on wheel attaching studs
to retain brake drums or rotors.
RAMP ANGLE
If a vehicle with flat-bed towing equipment is used,
the approach ramp angle should not exceed 15
degrees.
TOWING WHEN KEYS ARE NOT AVAILABLE
When the vehicle is locked and keys are not avail-
able, use a flat bed hauler. A Wheel-lift or Sling-type
device can be used on 4WD vehicles providedall the
wheels are lifted off the ground using tow dol-
lies.
FOUR-WHEEL-DRIVE VEHICLE TOWING
Chrysler Corporation recommends that a vehicle be
transported on a flat-bed device. A Wheel-lift or
Sling-type device can be used providedall the
wheels are lifted off the ground using tow dol-
lies.
WARNING: WHEN TOWING A DISABLED VEHICLE
AND THE DRIVE WHEELS ARE SECURED IN A
WHEEL LIFT OR TOW DOLLIES, ENSURE THE
TRANSMISSION IS IN THE PARK POSITION (AUTO-
MATIC TRANSMISSION) OR A FORWARD DRIVE
GEAR (MANUAL TRANSMISSION).
CAUTION: Many vehicles are equipped with air
dams, spoilers, and/or ground effect panels. To
avoid component damage, a wheel-lift towing vehi-
cle or a flat-bed hauling vehicle is recommended.
0 - 22 LUBRICATION & MAINTENANCEDR
TOWING (Continued)
Page 206 of 2627
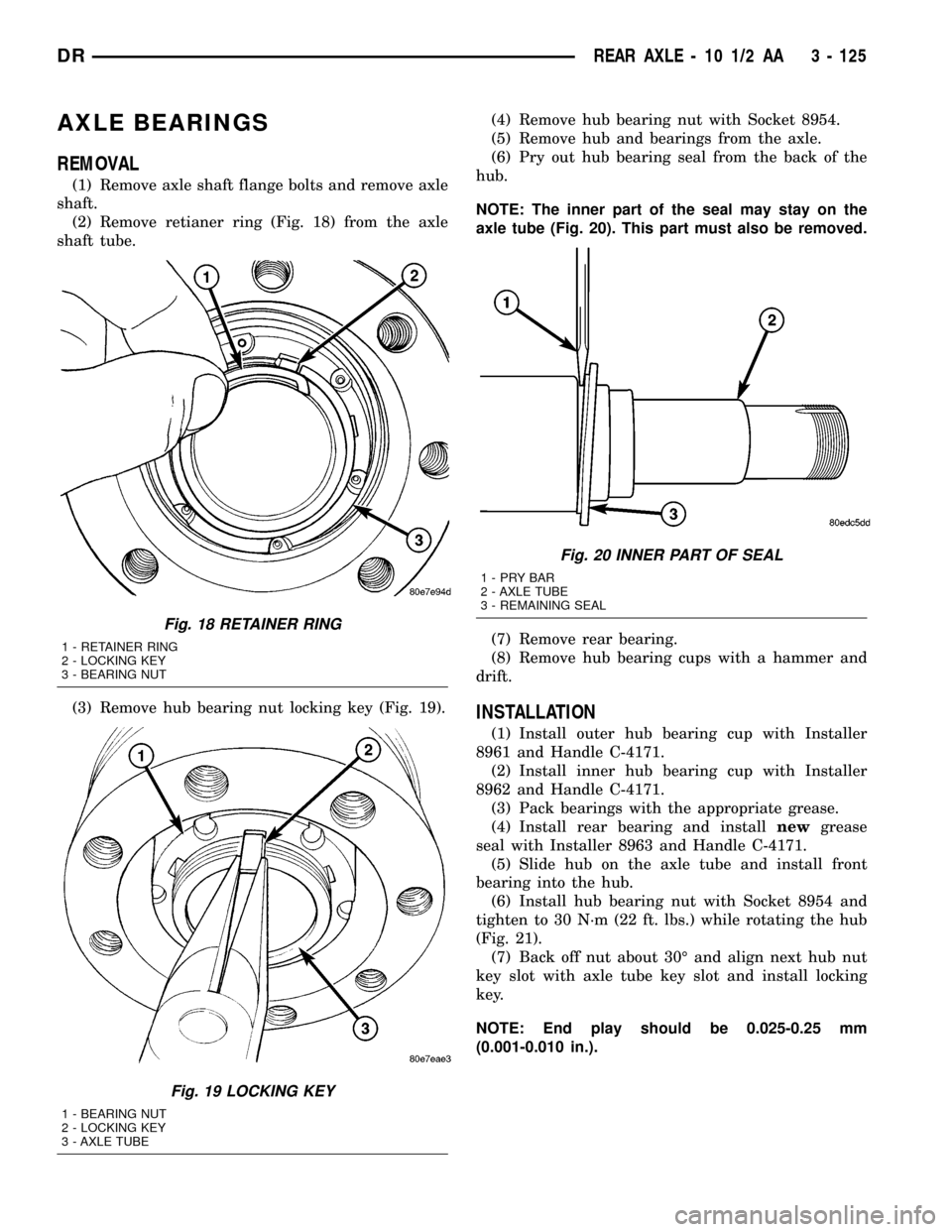
AXLE BEARINGS
REMOVAL
(1) Remove axle shaft flange bolts and remove axle
shaft.
(2) Remove retianer ring (Fig. 18) from the axle
shaft tube.
(3) Remove hub bearing nut locking key (Fig. 19).(4) Remove hub bearing nut with Socket 8954.
(5) Remove hub and bearings from the axle.
(6) Pry out hub bearing seal from the back of the
hub.
NOTE: The inner part of the seal may stay on the
axle tube (Fig. 20). This part must also be removed.
(7) Remove rear bearing.
(8) Remove hub bearing cups with a hammer and
drift.
INSTALLATION
(1) Install outer hub bearing cup with Installer
8961 and Handle C-4171.
(2) Install inner hub bearing cup with Installer
8962 and Handle C-4171.
(3) Pack bearings with the appropriate grease.
(4) Install rear bearing and installnewgrease
seal with Installer 8963 and Handle C-4171.
(5) Slide hub on the axle tube and install front
bearing into the hub.
(6) Install hub bearing nut with Socket 8954 and
tighten to 30 N´m (22 ft. lbs.) while rotating the hub
(Fig. 21).
(7) Back off nut about 30É and align next hub nut
key slot with axle tube key slot and install locking
key.
NOTE: End play should be 0.025-0.25 mm
(0.001-0.010 in.).
Fig. 18 RETAINER RING
1 - RETAINER RING
2 - LOCKING KEY
3 - BEARING NUT
Fig. 19 LOCKING KEY
1 - BEARING NUT
2 - LOCKING KEY
3 - AXLE TUBE
Fig. 20 INNER PART OF SEAL
1-PRYBAR
2 - AXLE TUBE
3 - REMAINING SEAL
DRREAR AXLE - 10 1/2 AA 3 - 125
Page 207 of 2627
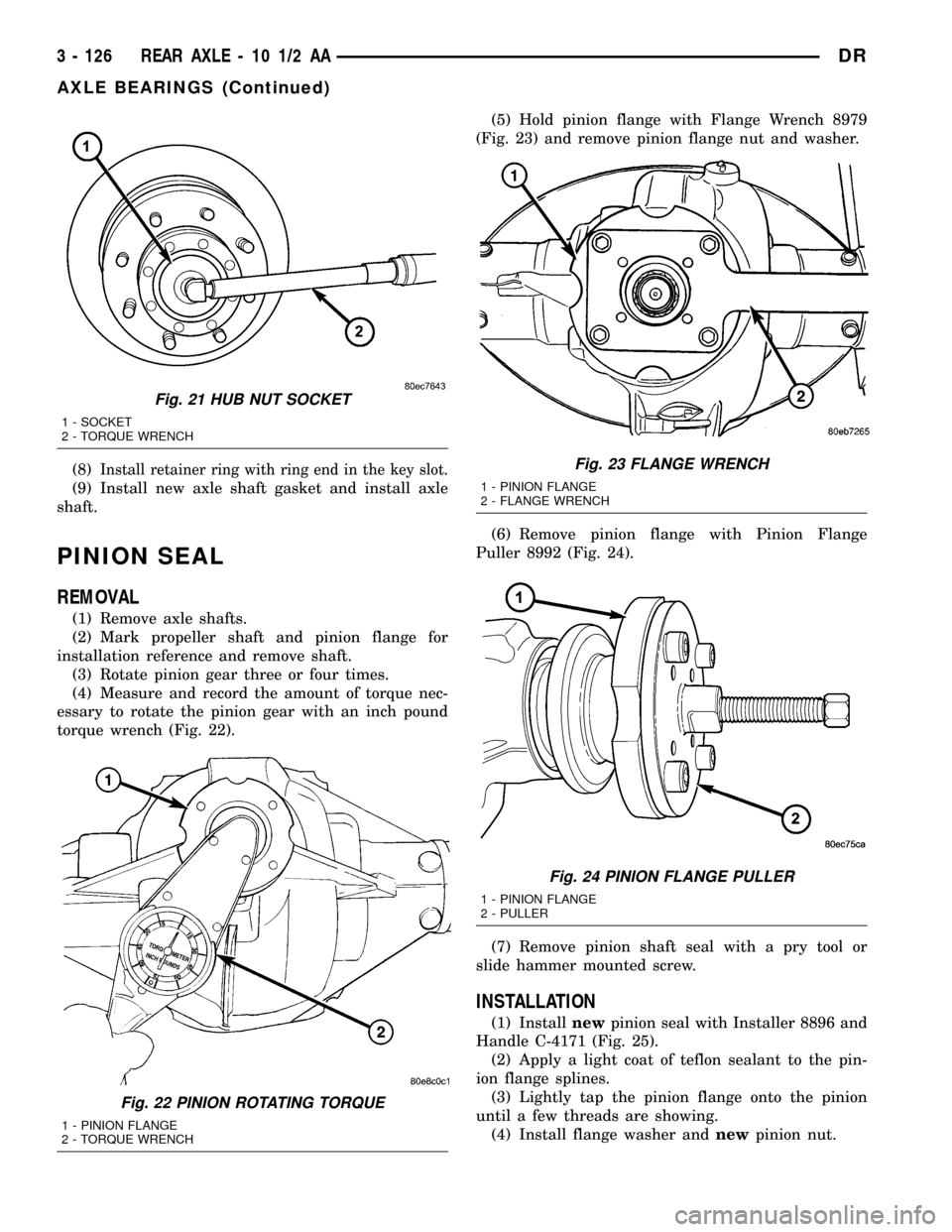
(8)Install retainer ring with ring end in the key slot.
(9) Install new axle shaft gasket and install axle
shaft.
PINION SEAL
REMOVAL
(1) Remove axle shafts.
(2) Mark propeller shaft and pinion flange for
installation reference and remove shaft.
(3) Rotate pinion gear three or four times.
(4) Measure and record the amount of torque nec-
essary to rotate the pinion gear with an inch pound
torque wrench (Fig. 22).(5) Hold pinion flange with Flange Wrench 8979
(Fig. 23) and remove pinion flange nut and washer.
(6) Remove pinion flange with Pinion Flange
Puller 8992 (Fig. 24).
(7) Remove pinion shaft seal with a pry tool or
slide hammer mounted screw.
INSTALLATION
(1) Installnewpinion seal with Installer 8896 and
Handle C-4171 (Fig. 25).
(2) Apply a light coat of teflon sealant to the pin-
ion flange splines.
(3) Lightly tap the pinion flange onto the pinion
until a few threads are showing.
(4) Install flange washer andnewpinion nut.
Fig. 21 HUB NUT SOCKET
1 - SOCKET
2 - TORQUE WRENCH
Fig. 22 PINION ROTATING TORQUE
1 - PINION FLANGE
2 - TORQUE WRENCH
Fig. 23 FLANGE WRENCH
1 - PINION FLANGE
2 - FLANGE WRENCH
Fig. 24 PINION FLANGE PULLER
1 - PINION FLANGE
2 - PULLER
3 - 126 REAR AXLE - 10 1/2 AADR
AXLE BEARINGS (Continued)
Page 233 of 2627
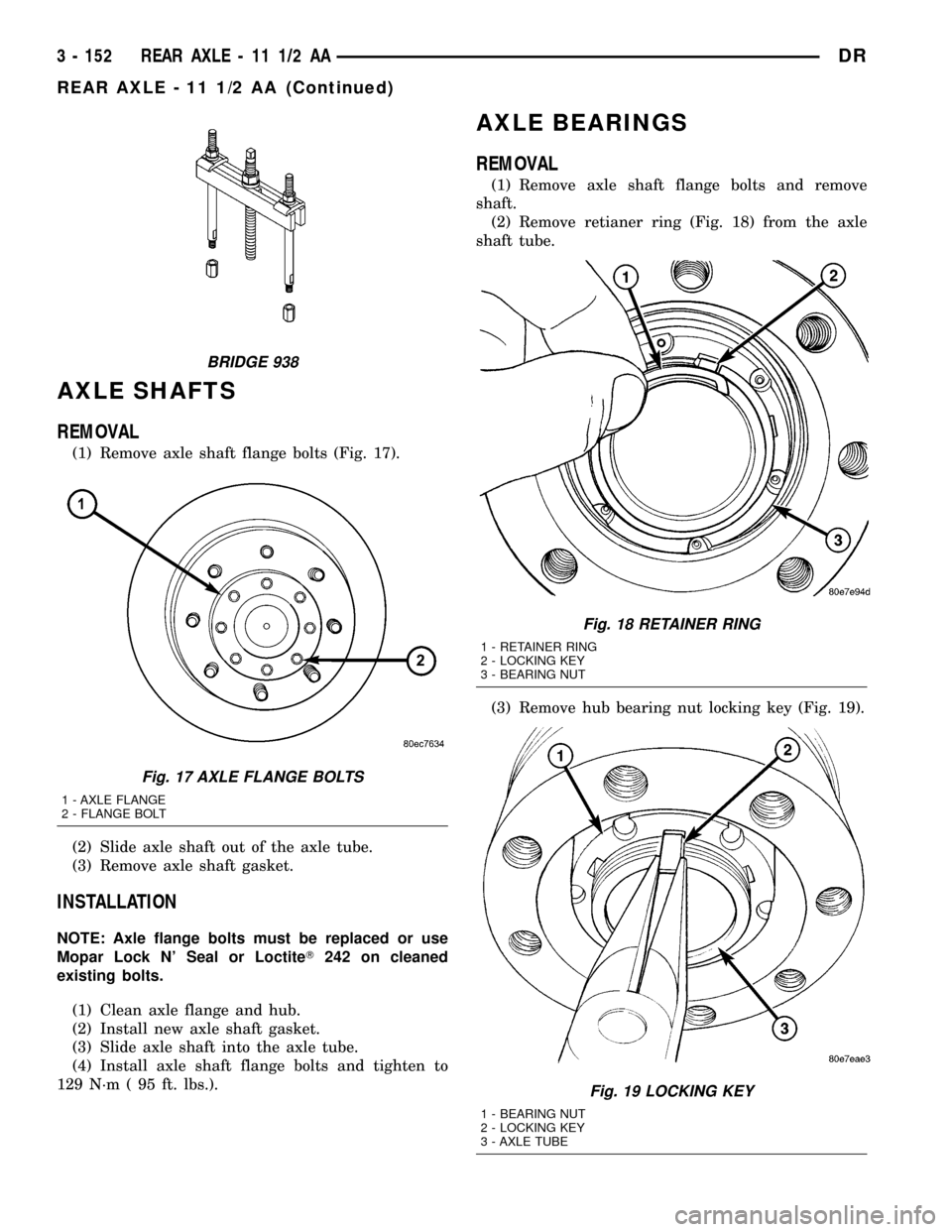
AXLE SHAFTS
REMOVAL
(1) Remove axle shaft flange bolts (Fig. 17).
(2) Slide axle shaft out of the axle tube.
(3) Remove axle shaft gasket.
INSTALLATION
NOTE: Axle flange bolts must be replaced or use
Mopar Lock N' Seal or LoctiteT242 on cleaned
existing bolts.
(1) Clean axle flange and hub.
(2) Install new axle shaft gasket.
(3) Slide axle shaft into the axle tube.
(4) Install axle shaft flange bolts and tighten to
129 N´m ( 95 ft. lbs.).
AXLE BEARINGS
REMOVAL
(1) Remove axle shaft flange bolts and remove
shaft.
(2) Remove retianer ring (Fig. 18) from the axle
shaft tube.
(3) Remove hub bearing nut locking key (Fig. 19).
BRIDGE 938
Fig. 17 AXLE FLANGE BOLTS
1 - AXLE FLANGE
2 - FLANGE BOLT
Fig. 18 RETAINER RING
1 - RETAINER RING
2 - LOCKING KEY
3 - BEARING NUT
Fig. 19 LOCKING KEY
1 - BEARING NUT
2 - LOCKING KEY
3 - AXLE TUBE
3 - 152 REAR AXLE - 11 1/2 AADR
REAR AXLE - 11 1/2 AA (Continued)
Page 234 of 2627
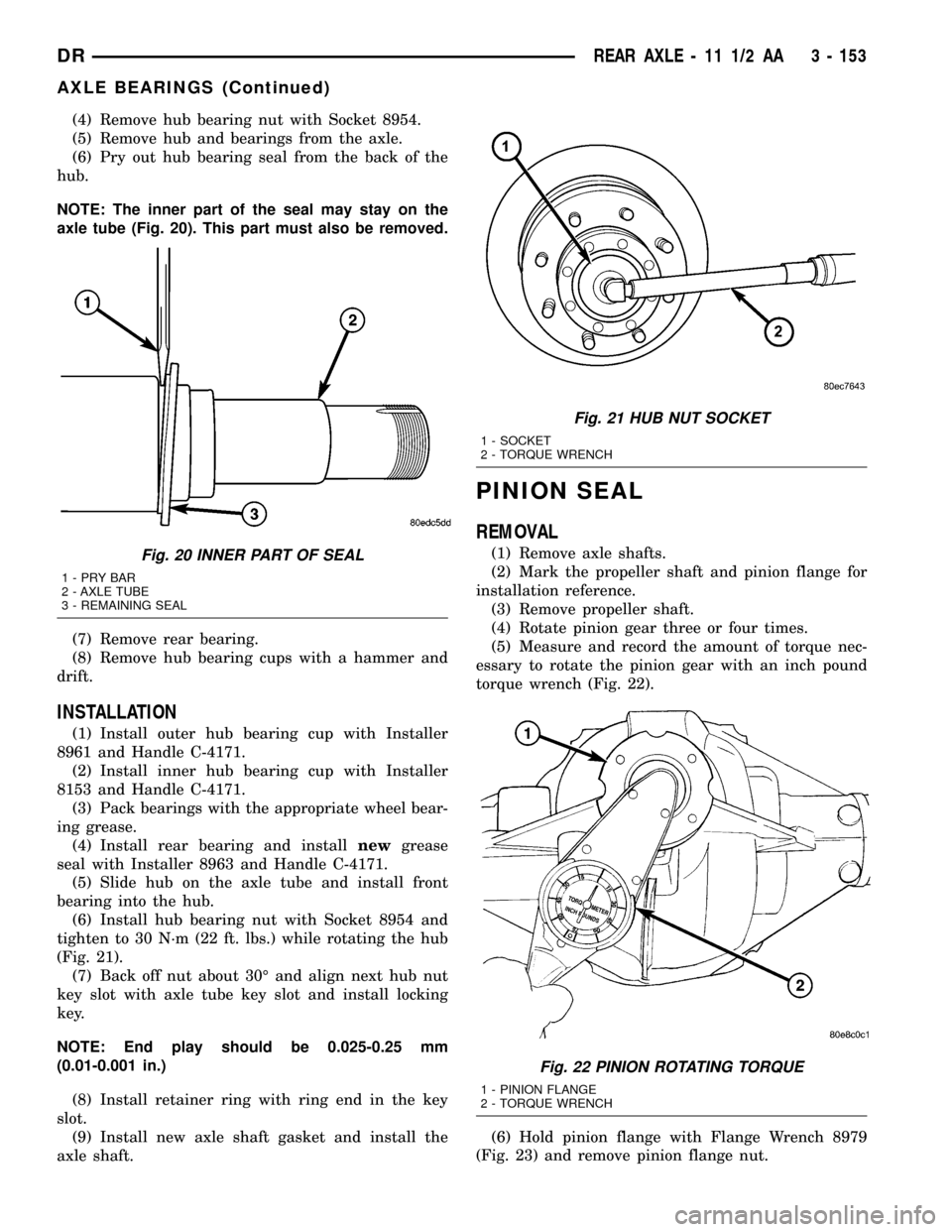
(4) Remove hub bearing nut with Socket 8954.
(5) Remove hub and bearings from the axle.
(6) Pry out hub bearing seal from the back of the
hub.
NOTE: The inner part of the seal may stay on the
axle tube (Fig. 20). This part must also be removed.
(7) Remove rear bearing.
(8) Remove hub bearing cups with a hammer and
drift.
INSTALLATION
(1) Install outer hub bearing cup with Installer
8961 and Handle C-4171.
(2) Install inner hub bearing cup with Installer
8153 and Handle C-4171.
(3) Pack bearings with the appropriate wheel bear-
ing grease.
(4) Install rear bearing and installnewgrease
seal with Installer 8963 and Handle C-4171.
(5) Slide hub on the axle tube and install front
bearing into the hub.
(6) Install hub bearing nut with Socket 8954 and
tighten to 30 N´m (22 ft. lbs.) while rotating the hub
(Fig. 21).
(7) Back off nut about 30É and align next hub nut
key slot with axle tube key slot and install locking
key.
NOTE: End play should be 0.025-0.25 mm
(0.01-0.001 in.)
(8) Install retainer ring with ring end in the key
slot.
(9) Install new axle shaft gasket and install the
axle shaft.
PINION SEAL
REMOVAL
(1) Remove axle shafts.
(2) Mark the propeller shaft and pinion flange for
installation reference.
(3) Remove propeller shaft.
(4) Rotate pinion gear three or four times.
(5) Measure and record the amount of torque nec-
essary to rotate the pinion gear with an inch pound
torque wrench (Fig. 22).
(6) Hold pinion flange with Flange Wrench 8979
(Fig. 23) and remove pinion flange nut.Fig. 20 INNER PART OF SEAL
1-PRYBAR
2 - AXLE TUBE
3 - REMAINING SEAL
Fig. 21 HUB NUT SOCKET
1 - SOCKET
2 - TORQUE WRENCH
Fig. 22 PINION ROTATING TORQUE
1 - PINION FLANGE
2 - TORQUE WRENCH
DRREAR AXLE - 11 1/2 AA 3 - 153
AXLE BEARINGS (Continued)
Page 353 of 2627
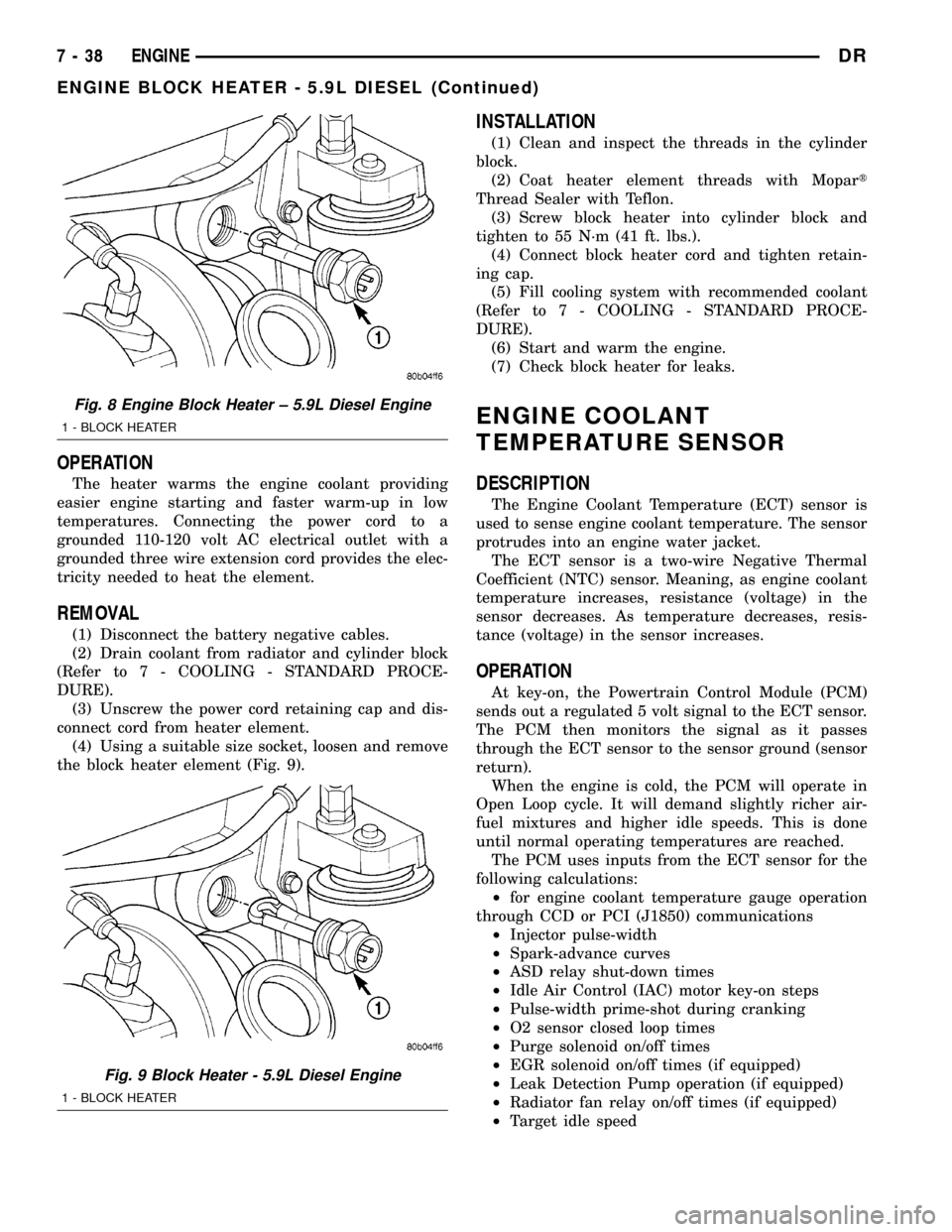
OPERATION
The heater warms the engine coolant providing
easier engine starting and faster warm-up in low
temperatures. Connecting the power cord to a
grounded 110-120 volt AC electrical outlet with a
grounded three wire extension cord provides the elec-
tricity needed to heat the element.
REMOVAL
(1) Disconnect the battery negative cables.
(2) Drain coolant from radiator and cylinder block
(Refer to 7 - COOLING - STANDARD PROCE-
DURE).
(3) Unscrew the power cord retaining cap and dis-
connect cord from heater element.
(4) Using a suitable size socket, loosen and remove
the block heater element (Fig. 9).
INSTALLATION
(1) Clean and inspect the threads in the cylinder
block.
(2) Coat heater element threads with Mopart
Thread Sealer with Teflon.
(3) Screw block heater into cylinder block and
tighten to 55 N´m (41 ft. lbs.).
(4) Connect block heater cord and tighten retain-
ing cap.
(5) Fill cooling system with recommended coolant
(Refer to 7 - COOLING - STANDARD PROCE-
DURE).
(6) Start and warm the engine.
(7) Check block heater for leaks.
ENGINE COOLANT
TEMPERATURE SENSOR
DESCRIPTION
The Engine Coolant Temperature (ECT) sensor is
used to sense engine coolant temperature. The sensor
protrudes into an engine water jacket.
The ECT sensor is a two-wire Negative Thermal
Coefficient (NTC) sensor. Meaning, as engine coolant
temperature increases, resistance (voltage) in the
sensor decreases. As temperature decreases, resis-
tance (voltage) in the sensor increases.
OPERATION
At key-on, the Powertrain Control Module (PCM)
sends out a regulated 5 volt signal to the ECT sensor.
The PCM then monitors the signal as it passes
through the ECT sensor to the sensor ground (sensor
return).
When the engine is cold, the PCM will operate in
Open Loop cycle. It will demand slightly richer air-
fuel mixtures and higher idle speeds. This is done
until normal operating temperatures are reached.
The PCM uses inputs from the ECT sensor for the
following calculations:
²for engine coolant temperature gauge operation
through CCD or PCI (J1850) communications
²Injector pulse-width
²Spark-advance curves
²ASD relay shut-down times
²Idle Air Control (IAC) motor key-on steps
²Pulse-width prime-shot during cranking
²O2 sensor closed loop times
²Purge solenoid on/off times
²EGR solenoid on/off times (if equipped)
²Leak Detection Pump operation (if equipped)
²Radiator fan relay on/off times (if equipped)
²Target idle speed
Fig. 8 Engine Block Heater ± 5.9L Diesel Engine
1 - BLOCK HEATER
Fig. 9 Block Heater - 5.9L Diesel Engine
1 - BLOCK HEATER
7 - 38 ENGINEDR
ENGINE BLOCK HEATER - 5.9L DIESEL (Continued)
Page 394 of 2627
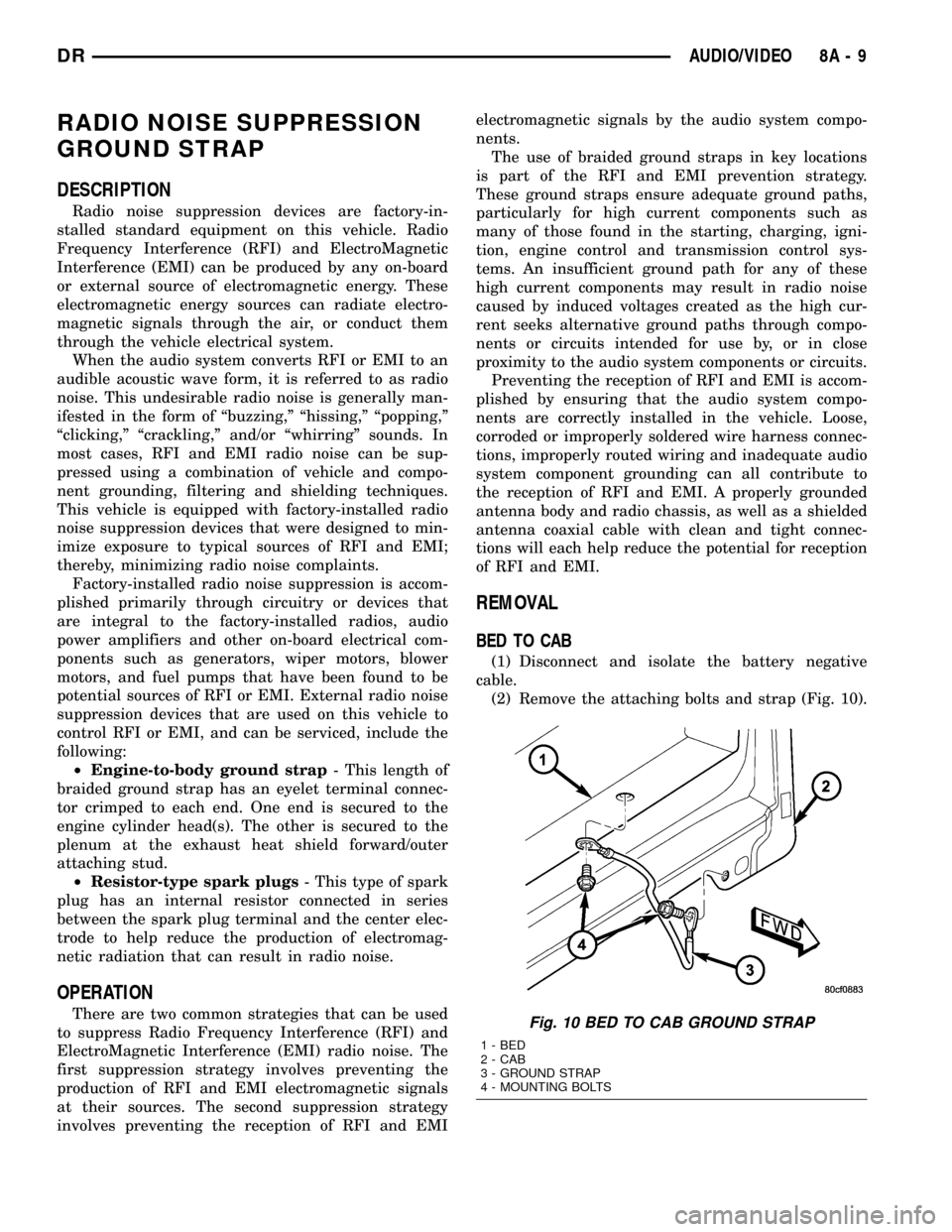
RADIO NOISE SUPPRESSION
GROUND STRAP
DESCRIPTION
Radio noise suppression devices are factory-in-
stalled standard equipment on this vehicle. Radio
Frequency Interference (RFI) and ElectroMagnetic
Interference (EMI) can be produced by any on-board
or external source of electromagnetic energy. These
electromagnetic energy sources can radiate electro-
magnetic signals through the air, or conduct them
through the vehicle electrical system.
When the audio system converts RFI or EMI to an
audible acoustic wave form, it is referred to as radio
noise. This undesirable radio noise is generally man-
ifested in the form of ªbuzzing,º ªhissing,º ªpopping,º
ªclicking,º ªcrackling,º and/or ªwhirringº sounds. In
most cases, RFI and EMI radio noise can be sup-
pressed using a combination of vehicle and compo-
nent grounding, filtering and shielding techniques.
This vehicle is equipped with factory-installed radio
noise suppression devices that were designed to min-
imize exposure to typical sources of RFI and EMI;
thereby, minimizing radio noise complaints.
Factory-installed radio noise suppression is accom-
plished primarily through circuitry or devices that
are integral to the factory-installed radios, audio
power amplifiers and other on-board electrical com-
ponents such as generators, wiper motors, blower
motors, and fuel pumps that have been found to be
potential sources of RFI or EMI. External radio noise
suppression devices that are used on this vehicle to
control RFI or EMI, and can be serviced, include the
following:
²Engine-to-body ground strap- This length of
braided ground strap has an eyelet terminal connec-
tor crimped to each end. One end is secured to the
engine cylinder head(s). The other is secured to the
plenum at the exhaust heat shield forward/outer
attaching stud.
²Resistor-type spark plugs- This type of spark
plug has an internal resistor connected in series
between the spark plug terminal and the center elec-
trode to help reduce the production of electromag-
netic radiation that can result in radio noise.
OPERATION
There are two common strategies that can be used
to suppress Radio Frequency Interference (RFI) and
ElectroMagnetic Interference (EMI) radio noise. The
first suppression strategy involves preventing the
production of RFI and EMI electromagnetic signals
at their sources. The second suppression strategy
involves preventing the reception of RFI and EMIelectromagnetic signals by the audio system compo-
nents.
The use of braided ground straps in key locations
is part of the RFI and EMI prevention strategy.
These ground straps ensure adequate ground paths,
particularly for high current components such as
many of those found in the starting, charging, igni-
tion, engine control and transmission control sys-
tems. An insufficient ground path for any of these
high current components may result in radio noise
caused by induced voltages created as the high cur-
rent seeks alternative ground paths through compo-
nents or circuits intended for use by, or in close
proximity to the audio system components or circuits.
Preventing the reception of RFI and EMI is accom-
plished by ensuring that the audio system compo-
nents are correctly installed in the vehicle. Loose,
corroded or improperly soldered wire harness connec-
tions, improperly routed wiring and inadequate audio
system component grounding can all contribute to
the reception of RFI and EMI. A properly grounded
antenna body and radio chassis, as well as a shielded
antenna coaxial cable with clean and tight connec-
tions will each help reduce the potential for reception
of RFI and EMI.
REMOVAL
BED TO CAB
(1) Disconnect and isolate the battery negative
cable.
(2) Remove the attaching bolts and strap (Fig. 10).
Fig. 10 BED TO CAB GROUND STRAP
1 - BED
2 - CAB
3 - GROUND STRAP
4 - MOUNTING BOLTS
DRAUDIO/VIDEO 8A - 9
Page 402 of 2627
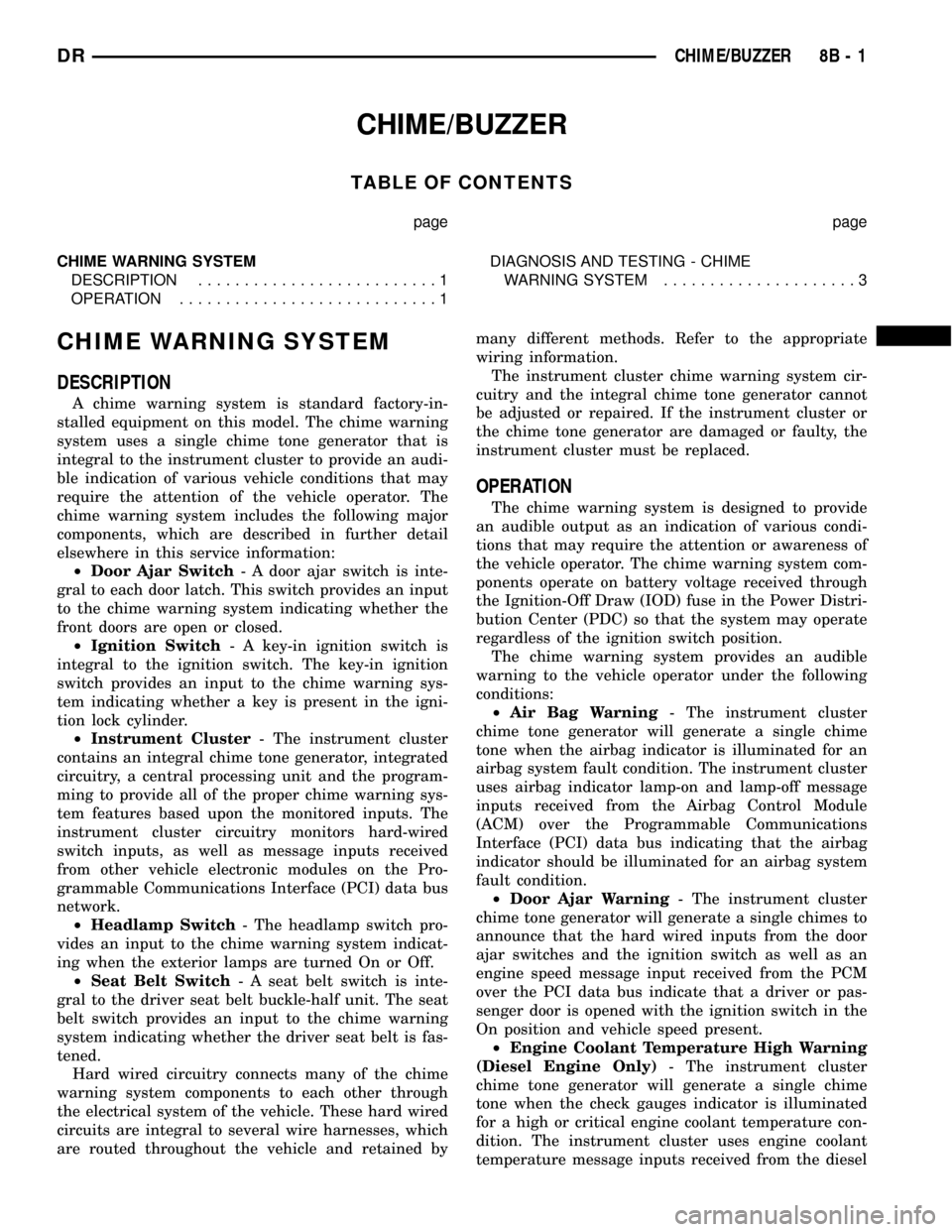
CHIME/BUZZER
TABLE OF CONTENTS
page page
CHIME WARNING SYSTEM
DESCRIPTION..........................1
OPERATION............................1DIAGNOSIS AND TESTING - CHIME
WARNING SYSTEM.....................3
CHIME WARNING SYSTEM
DESCRIPTION
A chime warning system is standard factory-in-
stalled equipment on this model. The chime warning
system uses a single chime tone generator that is
integral to the instrument cluster to provide an audi-
ble indication of various vehicle conditions that may
require the attention of the vehicle operator. The
chime warning system includes the following major
components, which are described in further detail
elsewhere in this service information:
²Door Ajar Switch- A door ajar switch is inte-
gral to each door latch. This switch provides an input
to the chime warning system indicating whether the
front doors are open or closed.
²Ignition Switch- A key-in ignition switch is
integral to the ignition switch. The key-in ignition
switch provides an input to the chime warning sys-
tem indicating whether a key is present in the igni-
tion lock cylinder.
²Instrument Cluster- The instrument cluster
contains an integral chime tone generator, integrated
circuitry, a central processing unit and the program-
ming to provide all of the proper chime warning sys-
tem features based upon the monitored inputs. The
instrument cluster circuitry monitors hard-wired
switch inputs, as well as message inputs received
from other vehicle electronic modules on the Pro-
grammable Communications Interface (PCI) data bus
network.
²Headlamp Switch- The headlamp switch pro-
vides an input to the chime warning system indicat-
ing when the exterior lamps are turned On or Off.
²Seat Belt Switch- A seat belt switch is inte-
gral to the driver seat belt buckle-half unit. The seat
belt switch provides an input to the chime warning
system indicating whether the driver seat belt is fas-
tened.
Hard wired circuitry connects many of the chime
warning system components to each other through
the electrical system of the vehicle. These hard wired
circuits are integral to several wire harnesses, which
are routed throughout the vehicle and retained bymany different methods. Refer to the appropriate
wiring information.
The instrument cluster chime warning system cir-
cuitry and the integral chime tone generator cannot
be adjusted or repaired. If the instrument cluster or
the chime tone generator are damaged or faulty, the
instrument cluster must be replaced.
OPERATION
The chime warning system is designed to provide
an audible output as an indication of various condi-
tions that may require the attention or awareness of
the vehicle operator. The chime warning system com-
ponents operate on battery voltage received through
the Ignition-Off Draw (IOD) fuse in the Power Distri-
bution Center (PDC) so that the system may operate
regardless of the ignition switch position.
The chime warning system provides an audible
warning to the vehicle operator under the following
conditions:
²Air Bag Warning- The instrument cluster
chime tone generator will generate a single chime
tone when the airbag indicator is illuminated for an
airbag system fault condition. The instrument cluster
uses airbag indicator lamp-on and lamp-off message
inputs received from the Airbag Control Module
(ACM) over the Programmable Communications
Interface (PCI) data bus indicating that the airbag
indicator should be illuminated for an airbag system
fault condition.
²Door Ajar Warning- The instrument cluster
chime tone generator will generate a single chimes to
announce that the hard wired inputs from the door
ajar switches and the ignition switch as well as an
engine speed message input received from the PCM
over the PCI data bus indicate that a driver or pas-
senger door is opened with the ignition switch in the
On position and vehicle speed present.
²Engine Coolant Temperature High Warning
(Diesel Engine Only)- The instrument cluster
chime tone generator will generate a single chime
tone when the check gauges indicator is illuminated
for a high or critical engine coolant temperature con-
dition. The instrument cluster uses engine coolant
temperature message inputs received from the diesel
DRCHIME/BUZZER 8B - 1
Page 403 of 2627
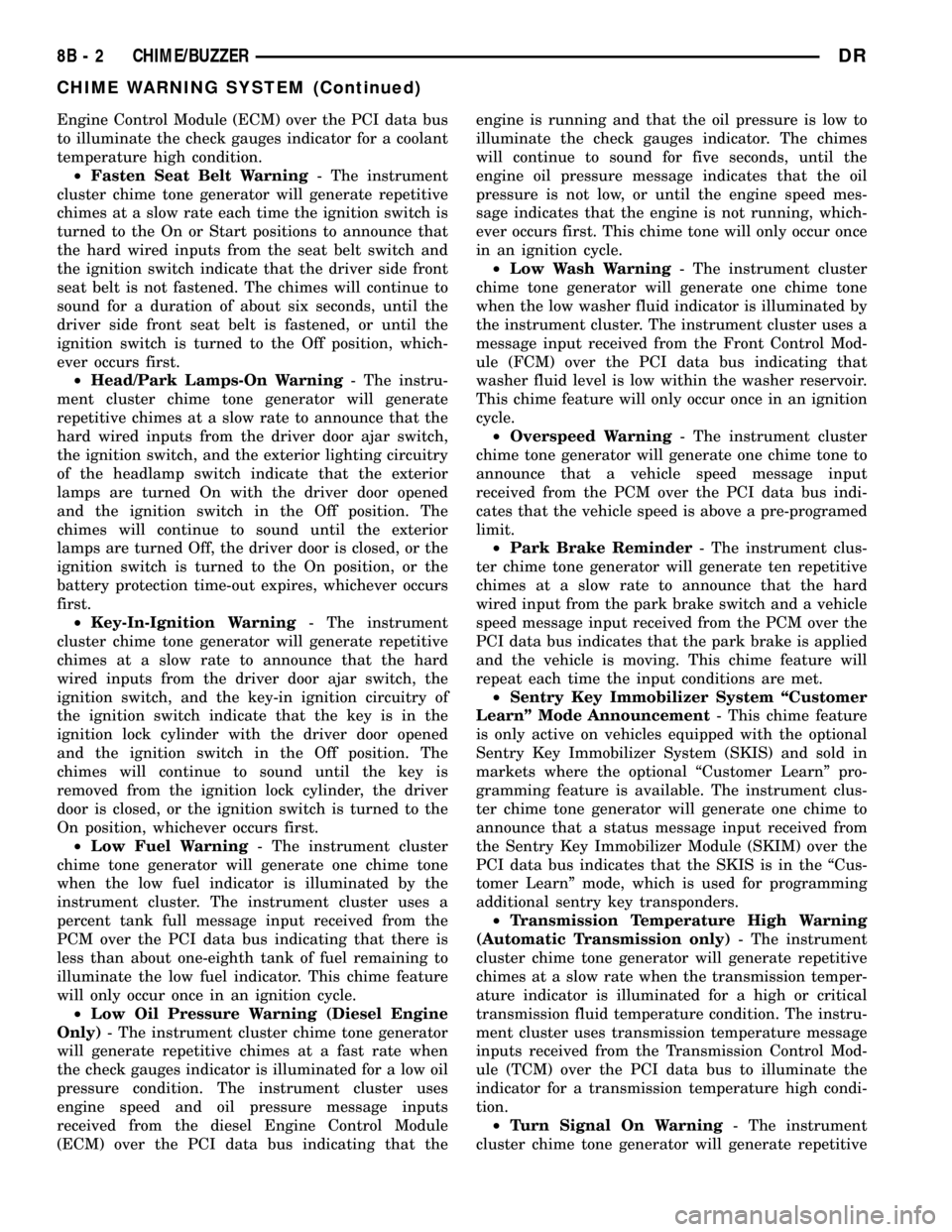
Engine Control Module (ECM) over the PCI data bus
to illuminate the check gauges indicator for a coolant
temperature high condition.
²Fasten Seat Belt Warning- The instrument
cluster chime tone generator will generate repetitive
chimes at a slow rate each time the ignition switch is
turned to the On or Start positions to announce that
the hard wired inputs from the seat belt switch and
the ignition switch indicate that the driver side front
seat belt is not fastened. The chimes will continue to
sound for a duration of about six seconds, until the
driver side front seat belt is fastened, or until the
ignition switch is turned to the Off position, which-
ever occurs first.
²Head/Park Lamps-On Warning- The instru-
ment cluster chime tone generator will generate
repetitive chimes at a slow rate to announce that the
hard wired inputs from the driver door ajar switch,
the ignition switch, and the exterior lighting circuitry
of the headlamp switch indicate that the exterior
lamps are turned On with the driver door opened
and the ignition switch in the Off position. The
chimes will continue to sound until the exterior
lamps are turned Off, the driver door is closed, or the
ignition switch is turned to the On position, or the
battery protection time-out expires, whichever occurs
first.
²Key-In-Ignition Warning- The instrument
cluster chime tone generator will generate repetitive
chimes at a slow rate to announce that the hard
wired inputs from the driver door ajar switch, the
ignition switch, and the key-in ignition circuitry of
the ignition switch indicate that the key is in the
ignition lock cylinder with the driver door opened
and the ignition switch in the Off position. The
chimes will continue to sound until the key is
removed from the ignition lock cylinder, the driver
door is closed, or the ignition switch is turned to the
On position, whichever occurs first.
²Low Fuel Warning- The instrument cluster
chime tone generator will generate one chime tone
when the low fuel indicator is illuminated by the
instrument cluster. The instrument cluster uses a
percent tank full message input received from the
PCM over the PCI data bus indicating that there is
less than about one-eighth tank of fuel remaining to
illuminate the low fuel indicator. This chime feature
will only occur once in an ignition cycle.
²Low Oil Pressure Warning (Diesel Engine
Only)- The instrument cluster chime tone generator
will generate repetitive chimes at a fast rate when
the check gauges indicator is illuminated for a low oil
pressure condition. The instrument cluster uses
engine speed and oil pressure message inputs
received from the diesel Engine Control Module
(ECM) over the PCI data bus indicating that theengine is running and that the oil pressure is low to
illuminate the check gauges indicator. The chimes
will continue to sound for five seconds, until the
engine oil pressure message indicates that the oil
pressure is not low, or until the engine speed mes-
sage indicates that the engine is not running, which-
ever occurs first. This chime tone will only occur once
in an ignition cycle.
²Low Wash Warning- The instrument cluster
chime tone generator will generate one chime tone
when the low washer fluid indicator is illuminated by
the instrument cluster. The instrument cluster uses a
message input received from the Front Control Mod-
ule (FCM) over the PCI data bus indicating that
washer fluid level is low within the washer reservoir.
This chime feature will only occur once in an ignition
cycle.
²Overspeed Warning- The instrument cluster
chime tone generator will generate one chime tone to
announce that a vehicle speed message input
received from the PCM over the PCI data bus indi-
cates that the vehicle speed is above a pre-programed
limit.
²Park Brake Reminder- The instrument clus-
ter chime tone generator will generate ten repetitive
chimes at a slow rate to announce that the hard
wired input from the park brake switch and a vehicle
speed message input received from the PCM over the
PCI data bus indicates that the park brake is applied
and the vehicle is moving. This chime feature will
repeat each time the input conditions are met.
²Sentry Key Immobilizer System ªCustomer
Learnº Mode Announcement- This chime feature
is only active on vehicles equipped with the optional
Sentry Key Immobilizer System (SKIS) and sold in
markets where the optional ªCustomer Learnº pro-
gramming feature is available. The instrument clus-
ter chime tone generator will generate one chime to
announce that a status message input received from
the Sentry Key Immobilizer Module (SKIM) over the
PCI data bus indicates that the SKIS is in the ªCus-
tomer Learnº mode, which is used for programming
additional sentry key transponders.
²Transmission Temperature High Warning
(Automatic Transmission only)- The instrument
cluster chime tone generator will generate repetitive
chimes at a slow rate when the transmission temper-
ature indicator is illuminated for a high or critical
transmission fluid temperature condition. The instru-
ment cluster uses transmission temperature message
inputs received from the Transmission Control Mod-
ule (TCM) over the PCI data bus to illuminate the
indicator for a transmission temperature high condi-
tion.
²Turn Signal On Warning- The instrument
cluster chime tone generator will generate repetitive
8B - 2 CHIME/BUZZERDR
CHIME WARNING SYSTEM (Continued)
Page 405 of 2627
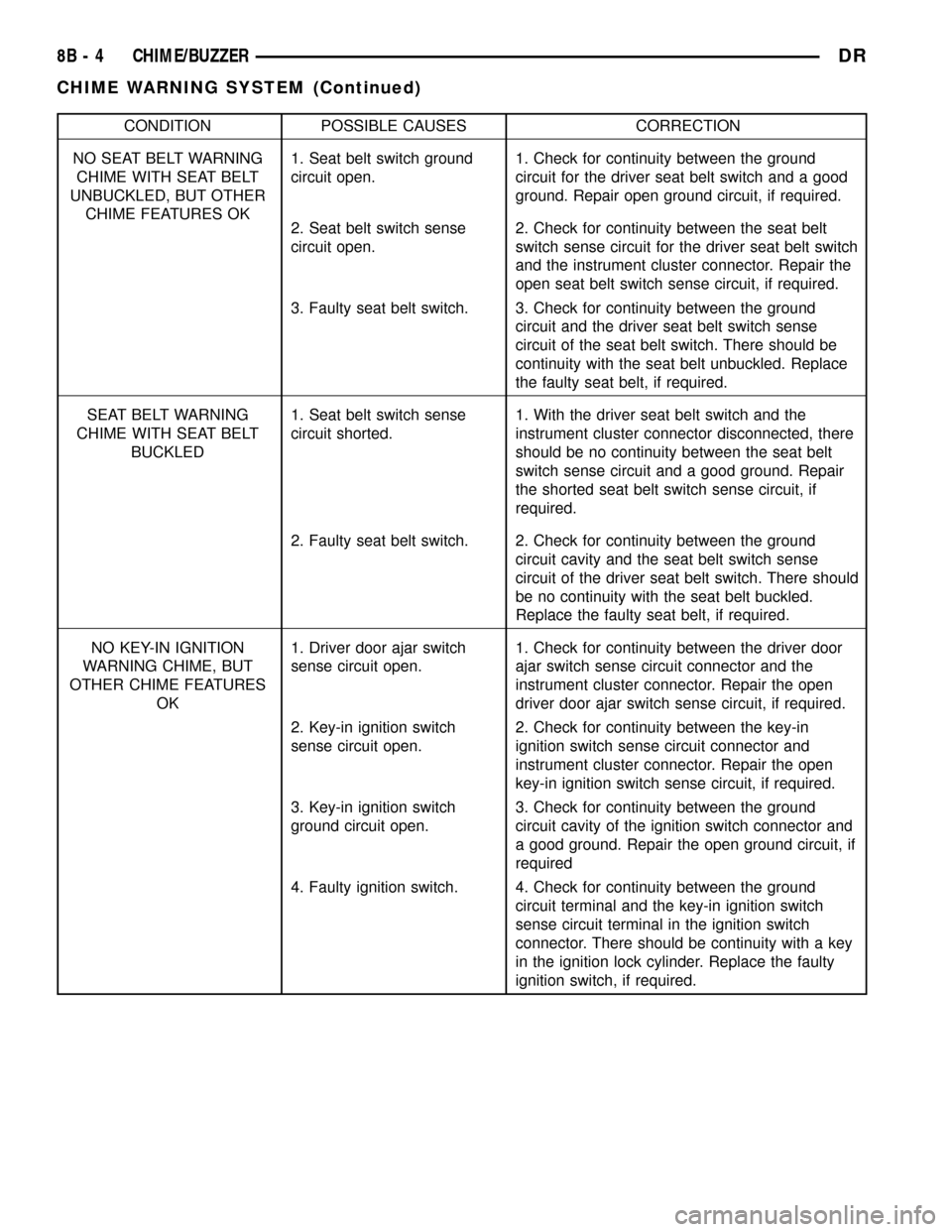
CONDITION POSSIBLE CAUSES CORRECTION
NO SEAT BELT WARNING
CHIME WITH SEAT BELT
UNBUCKLED, BUT OTHER
CHIME FEATURES OK1. Seat belt switch ground
circuit open.1. Check for continuity between the ground
circuit for the driver seat belt switch and a good
ground. Repair open ground circuit, if required.
2. Seat belt switch sense
circuit open.2. Check for continuity between the seat belt
switch sense circuit for the driver seat belt switch
and the instrument cluster connector. Repair the
open seat belt switch sense circuit, if required.
3. Faulty seat belt switch. 3. Check for continuity between the ground
circuit and the driver seat belt switch sense
circuit of the seat belt switch. There should be
continuity with the seat belt unbuckled. Replace
the faulty seat belt, if required.
SEAT BELT WARNING
CHIME WITH SEAT BELT
BUCKLED1. Seat belt switch sense
circuit shorted.1. With the driver seat belt switch and the
instrument cluster connector disconnected, there
should be no continuity between the seat belt
switch sense circuit and a good ground. Repair
the shorted seat belt switch sense circuit, if
required.
2. Faulty seat belt switch. 2. Check for continuity between the ground
circuit cavity and the seat belt switch sense
circuit of the driver seat belt switch. There should
be no continuity with the seat belt buckled.
Replace the faulty seat belt, if required.
NO KEY-IN IGNITION
WARNING CHIME, BUT
OTHER CHIME FEATURES
OK1. Driver door ajar switch
sense circuit open.1. Check for continuity between the driver door
ajar switch sense circuit connector and the
instrument cluster connector. Repair the open
driver door ajar switch sense circuit, if required.
2. Key-in ignition switch
sense circuit open.2. Check for continuity between the key-in
ignition switch sense circuit connector and
instrument cluster connector. Repair the open
key-in ignition switch sense circuit, if required.
3. Key-in ignition switch
ground circuit open.3. Check for continuity between the ground
circuit cavity of the ignition switch connector and
a good ground. Repair the open ground circuit, if
required
4. Faulty ignition switch. 4. Check for continuity between the ground
circuit terminal and the key-in ignition switch
sense circuit terminal in the ignition switch
connector. There should be continuity with a key
in the ignition lock cylinder. Replace the faulty
ignition switch, if required.
8B - 4 CHIME/BUZZERDR
CHIME WARNING SYSTEM (Continued)