FORD F650 2005 11.G Owners Manual
Manufacturer: FORD, Model Year: 2005, Model line: F650, Model: FORD F650 2005 11.GPages: 272, PDF Size: 1.5 MB
Page 201 of 272
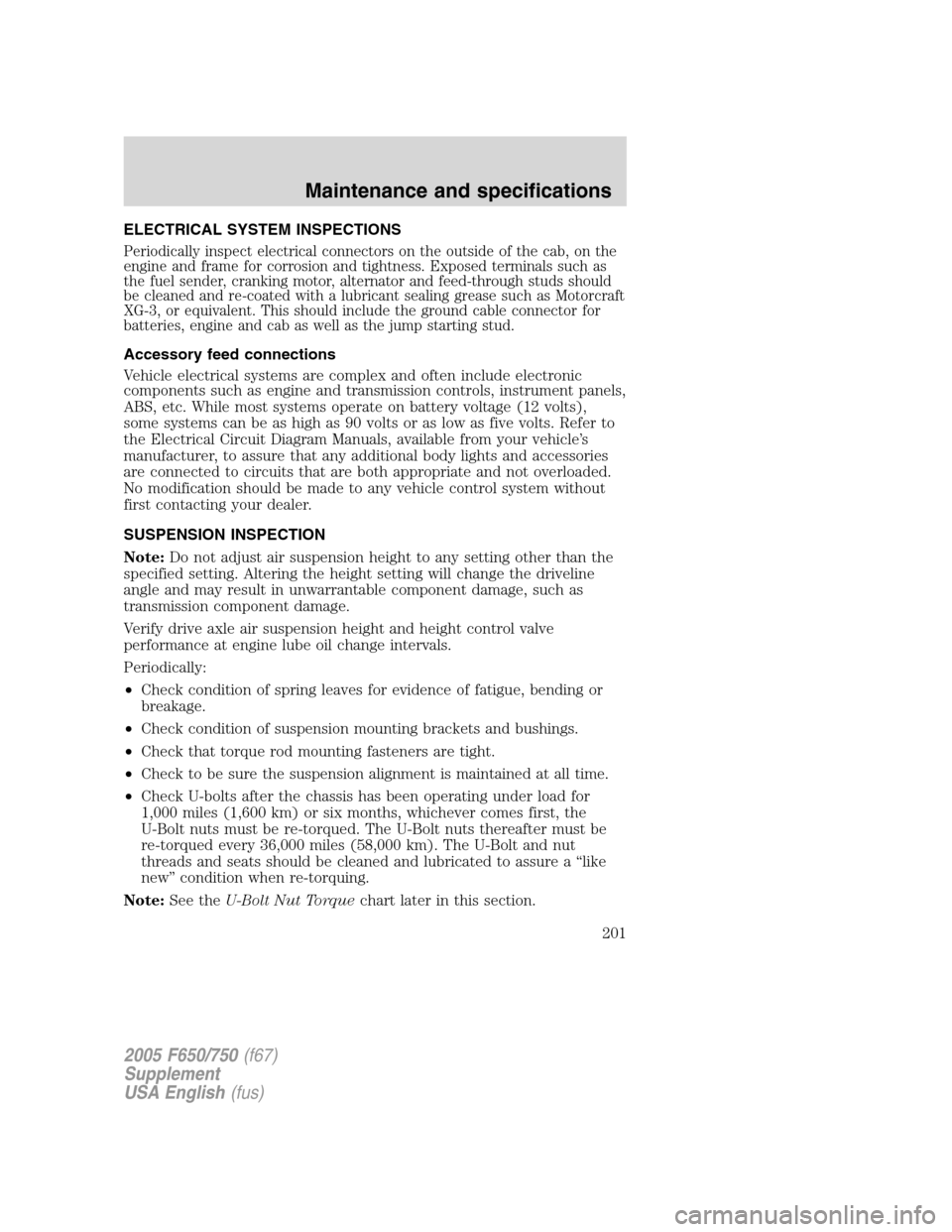
ELECTRICAL SYSTEM INSPECTIONS
Periodically inspect electrical connectors on the outside of the cab, on the
engine and frame for corrosion and tightness. Exposed terminals such as
the fuel sender, cranking motor, alternator and feed-through studs should
be cleaned and re-coated with a lubricant sealing grease such as Motorcraft
XG-3, or equivalent. This should include the ground cable connector for
batteries, engine and cab as well as the jump starting stud.
Accessory feed connections
Vehicle electrical systems are complex and often include electronic
components such as engine and transmission controls, instrument panels,
ABS, etc. While most systems operate on battery voltage (12 volts),
some systems can be as high as 90 volts or as low as five volts. Refer to
the Electrical Circuit Diagram Manuals, available from your vehicle’s
manufacturer, to assure that any additional body lights and accessories
are connected to circuits that are both appropriate and not overloaded.
No modification should be made to any vehicle control system without
first contacting your dealer.
SUSPENSION INSPECTION
Note:Do not adjust air suspension height to any setting other than the
specified setting. Altering the height setting will change the driveline
angle and may result in unwarrantable component damage, such as
transmission component damage.
Verify drive axle air suspension height and height control valve
performance at engine lube oil change intervals.
Periodically:
•Check condition of spring leaves for evidence of fatigue, bending or
breakage.
•Check condition of suspension mounting brackets and bushings.
•Check that torque rod mounting fasteners are tight.
•Check to be sure the suspension alignment is maintained at all time.
•Check U-bolts after the chassis has been operating under load for
1,000 miles (1,600 km) or six months, whichever comes first, the
U-Bolt nuts must be re-torqued. The U-Bolt nuts thereafter must be
re-torqued every 36,000 miles (58,000 km). The U-Bolt and nut
threads and seats should be cleaned and lubricated to assure a“like
new”condition when re-torquing.
Note:See theU-Bolt Nut Torquechart later in this section.
2005 F650/750(f67)
Supplement
USA English(fus)
Maintenance and specifications
201
Page 202 of 272
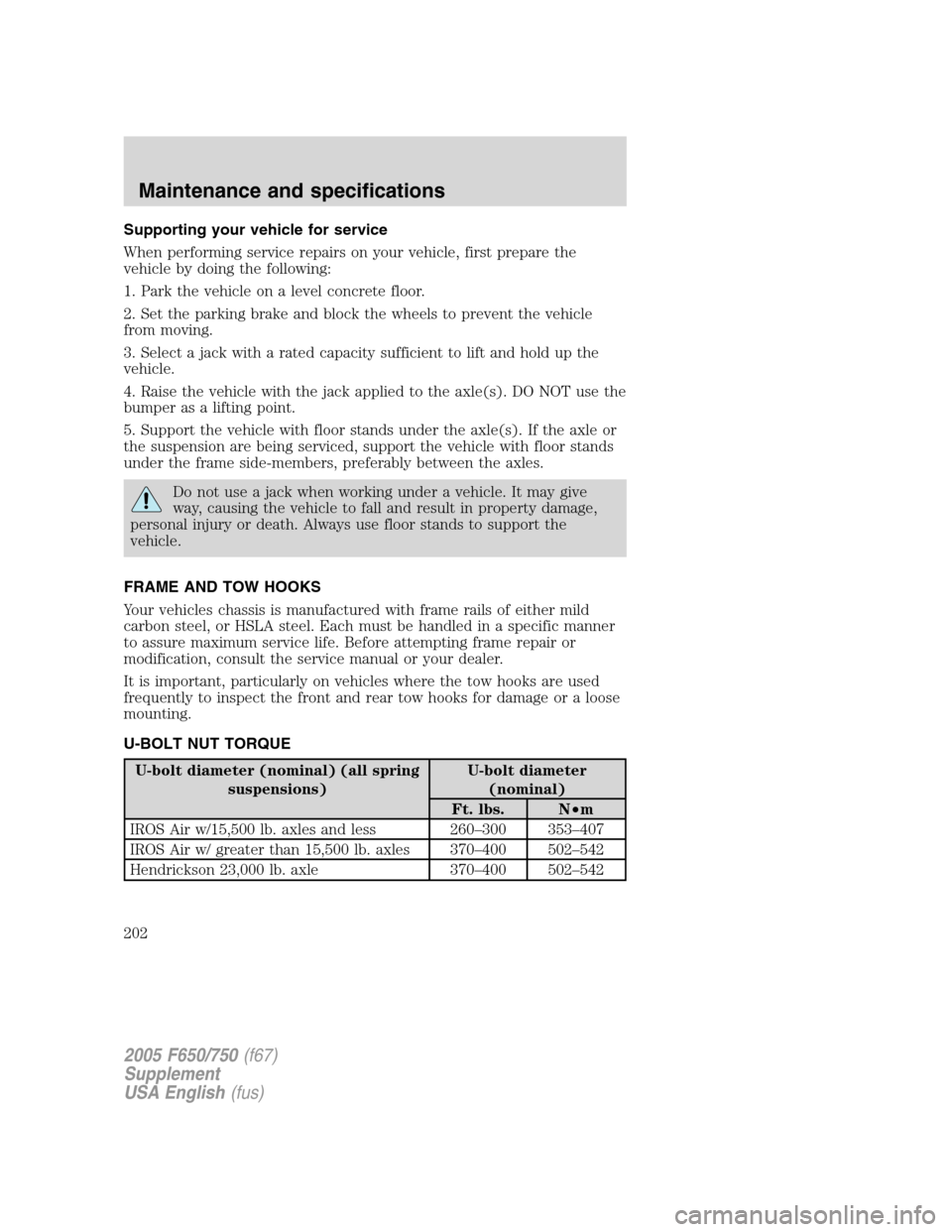
Supporting your vehicle for service
When performing service repairs on your vehicle, first prepare the
vehicle by doing the following:
1. Park the vehicle on a level concrete floor.
2. Set the parking brake and block the wheels to prevent the vehicle
from moving.
3. Select a jack with a rated capacity sufficient to lift and hold up the
vehicle.
4. Raise the vehicle with the jack applied to the axle(s). DO NOT use the
bumper as a lifting point.
5. Support the vehicle with floor stands under the axle(s). If the axle or
the suspension are being serviced, support the vehicle with floor stands
under the frame side-members, preferably between the axles.
Do not use a jack when working under a vehicle. It may give
way, causing the vehicle to fall and result in property damage,
personal injury or death. Always use floor stands to support the
vehicle.
FRAME AND TOW HOOKS
Your vehicles chassis is manufactured with frame rails of either mild
carbon steel, or HSLA steel. Each must be handled in a specific manner
to assure maximum service life. Before attempting frame repair or
modification, consult the service manual or your dealer.
It is important, particularly on vehicles where the tow hooks are used
frequently to inspect the front and rear tow hooks for damage or a loose
mounting.
U-BOLT NUT TORQUE
U-bolt diameter (nominal) (all spring
suspensions)U-bolt diameter
(nominal)
Ft. lbs. N•m
IROS Air w/15,500 lb. axles and less 260–300 353–407
IROS Air w/ greater than 15,500 lb. axles 370–400 502–542
Hendrickson 23,000 lb. axle 370–400 502–542
2005 F650/750(f67)
Supplement
USA English(fus)
Maintenance and specifications
202
Page 203 of 272
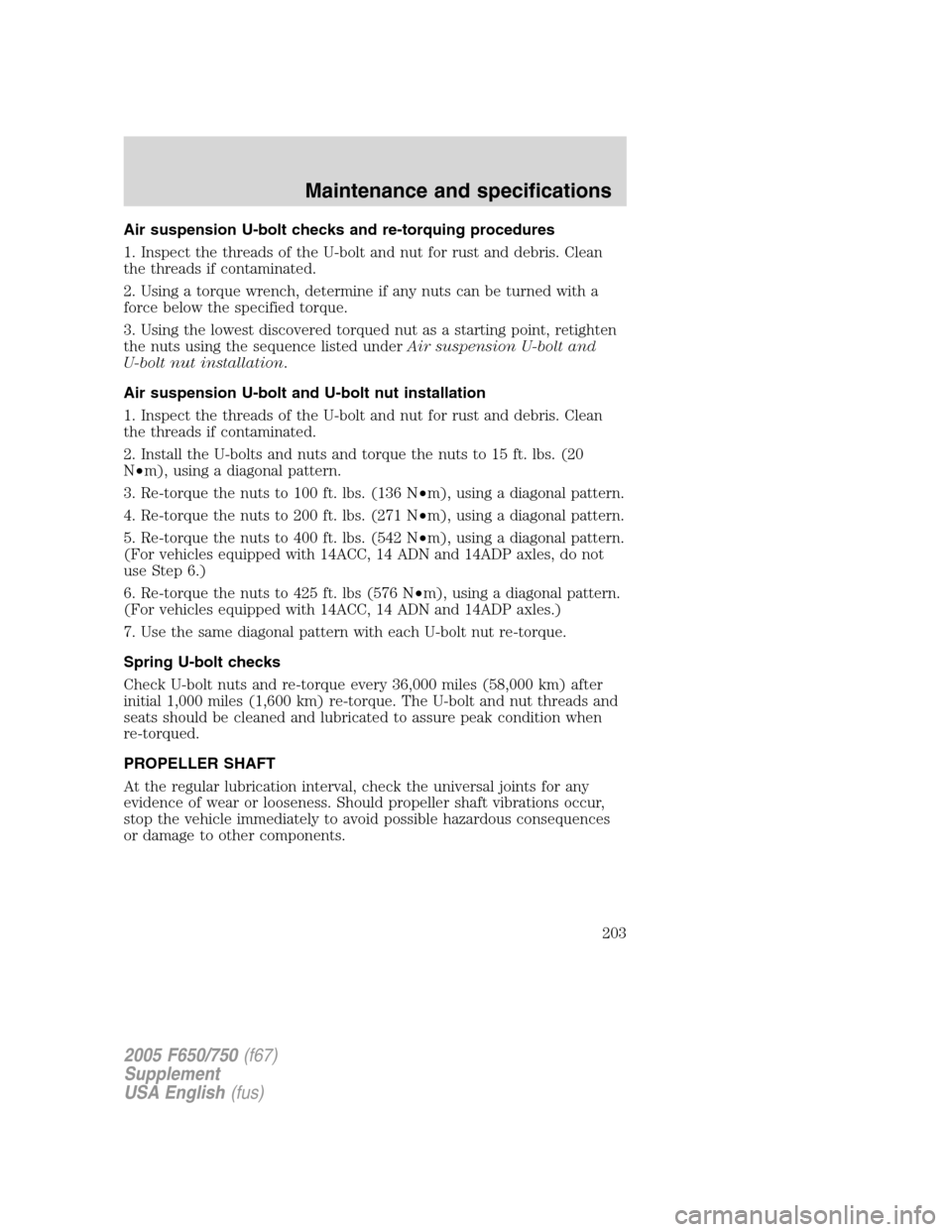
Air suspension U-bolt checks and re-torquing procedures
1. Inspect the threads of the U-bolt and nut for rust and debris. Clean
the threads if contaminated.
2. Using a torque wrench, determine if any nuts can be turned with a
force below the specified torque.
3. Using the lowest discovered torqued nut as a starting point, retighten
the nuts using the sequence listed underAir suspension U-bolt and
U-bolt nut installation.
Air suspension U-bolt and U-bolt nut installation
1. Inspect the threads of the U-bolt and nut for rust and debris. Clean
the threads if contaminated.
2. Install the U-bolts and nuts and torque the nuts to 15 ft. lbs. (20
N•m), using a diagonal pattern.
3. Re-torque the nuts to 100 ft. lbs. (136 N•m), using a diagonal pattern.
4. Re-torque the nuts to 200 ft. lbs. (271 N•m), using a diagonal pattern.
5. Re-torque the nuts to 400 ft. lbs. (542 N•m), using a diagonal pattern.
(For vehicles equipped with 14ACC, 14 ADN and 14ADP axles, do not
use Step 6.)
6. Re-torque the nuts to 425 ft. lbs (576 N•m), using a diagonal pattern.
(For vehicles equipped with 14ACC, 14 ADN and 14ADP axles.)
7. Use the same diagonal pattern with each U-bolt nut re-torque.
Spring U-bolt checks
Check U-bolt nuts and re-torque every 36,000 miles (58,000 km) after
initial 1,000 miles (1,600 km) re-torque. The U-bolt and nut threads and
seats should be cleaned and lubricated to assure peak condition when
re-torqued.
PROPELLER SHAFT
At the regular lubrication interval, check the universal joints for any
evidence of wear or looseness. Should propeller shaft vibrations occur,
stop the vehicle immediately to avoid possible hazardous consequences
or damage to other components.
2005 F650/750(f67)
Supplement
USA English(fus)
Maintenance and specifications
203
Page 204 of 272
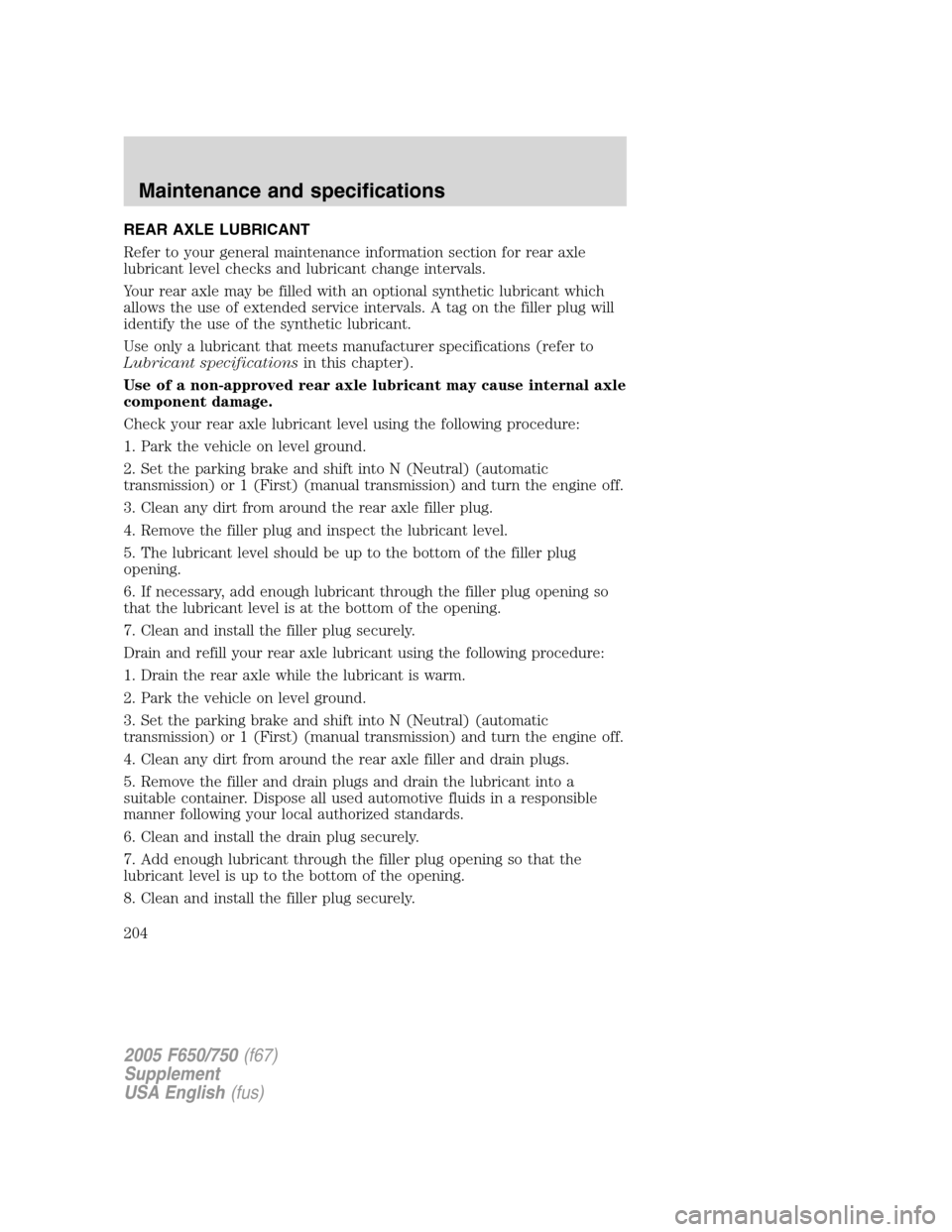
REAR AXLE LUBRICANT
Refer to your general maintenance information section for rear axle
lubricant level checks and lubricant change intervals.
Your rear axle may be filled with an optional synthetic lubricant which
allows the use of extended service intervals. A tag on the filler plug will
identify the use of the synthetic lubricant.
Use only a lubricant that meets manufacturer specifications (refer to
Lubricant specificationsin this chapter).
Use of a non-approved rear axle lubricant may cause internal axle
component damage.
Check your rear axle lubricant level using the following procedure:
1. Park the vehicle on level ground.
2. Set the parking brake and shift into N (Neutral) (automatic
transmission) or 1 (First) (manual transmission) and turn the engine off.
3. Clean any dirt from around the rear axle filler plug.
4. Remove the filler plug and inspect the lubricant level.
5. The lubricant level should be up to the bottom of the filler plug
opening.
6. If necessary, add enough lubricant through the filler plug opening so
that the lubricant level is at the bottom of the opening.
7. Clean and install the filler plug securely.
Drain and refill your rear axle lubricant using the following procedure:
1. Drain the rear axle while the lubricant is warm.
2. Park the vehicle on level ground.
3. Set the parking brake and shift into N (Neutral) (automatic
transmission) or 1 (First) (manual transmission) and turn the engine off.
4. Clean any dirt from around the rear axle filler and drain plugs.
5. Remove the filler and drain plugs and drain the lubricant into a
suitable container. Dispose all used automotive fluids in a responsible
manner following your local authorized standards.
6. Clean and install the drain plug securely.
7. Add enough lubricant through the filler plug opening so that the
lubricant level is up to the bottom of the opening.
8. Clean and install the filler plug securely.
2005 F650/750(f67)
Supplement
USA English(fus)
Maintenance and specifications
204
Page 205 of 272
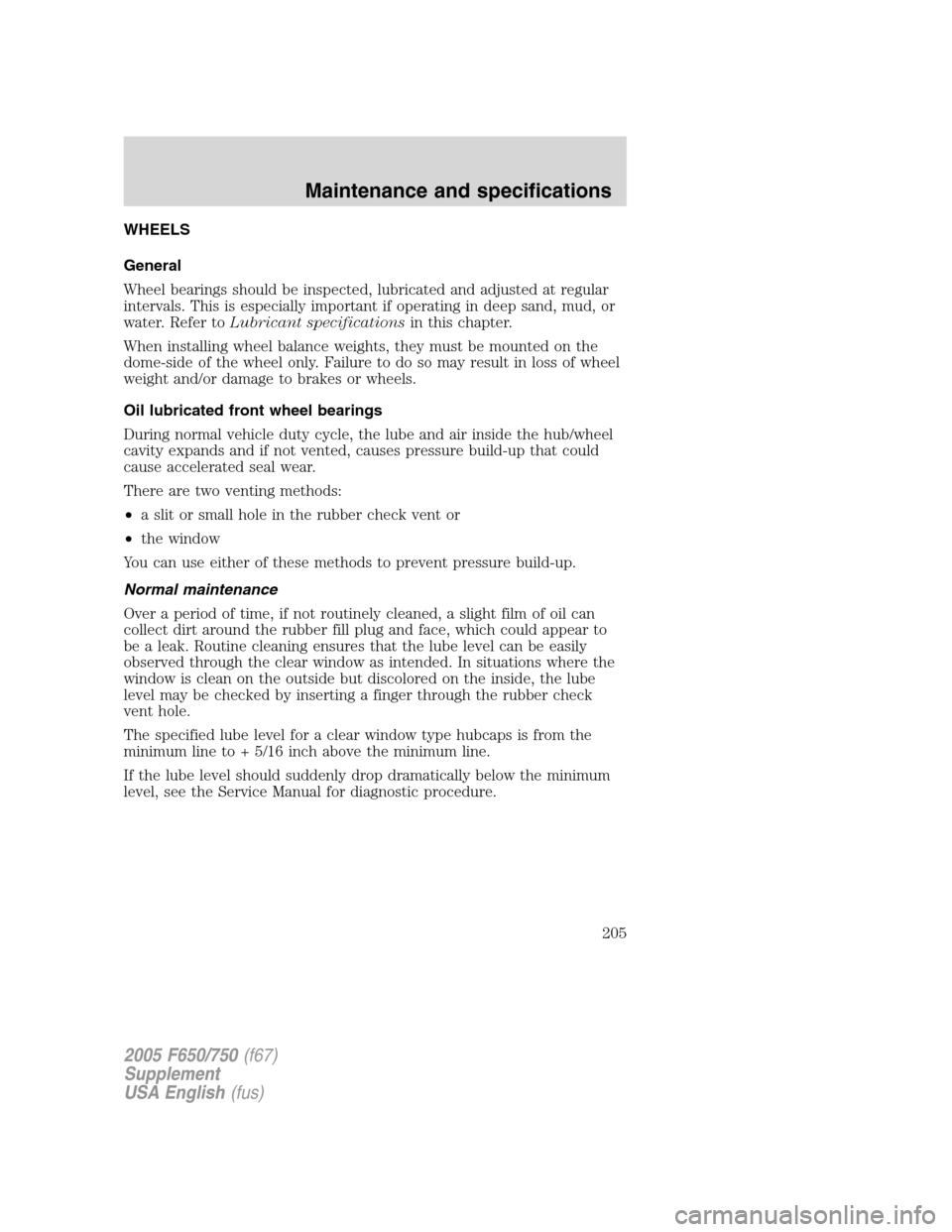
WHEELS
General
Wheel bearings should be inspected, lubricated and adjusted at regular
intervals. This is especially important if operating in deep sand, mud, or
water. Refer toLubricant specificationsin this chapter.
When installing wheel balance weights, they must be mounted on the
dome-side of the wheel only. Failure to do so may result in loss of wheel
weight and/or damage to brakes or wheels.
Oil lubricated front wheel bearings
During normal vehicle duty cycle, the lube and air inside the hub/wheel
cavity expands and if not vented, causes pressure build-up that could
cause accelerated seal wear.
There are two venting methods:
•a slit or small hole in the rubber check vent or
•the window
You can use either of these methods to prevent pressure build-up.
Normal maintenance
Over a period of time, if not routinely cleaned, a slight film of oil can
collect dirt around the rubber fill plug and face, which could appear to
be a leak. Routine cleaning ensures that the lube level can be easily
observed through the clear window as intended. In situations where the
window is clean on the outside but discolored on the inside, the lube
level may be checked by inserting a finger through the rubber check
vent hole.
The specified lube level for a clear window type hubcaps is from the
minimum line to + 5/16 inch above the minimum line.
If the lube level should suddenly drop dramatically below the minimum
level, see the Service Manual for diagnostic procedure.
2005 F650/750(f67)
Supplement
USA English(fus)
Maintenance and specifications
205
Page 206 of 272
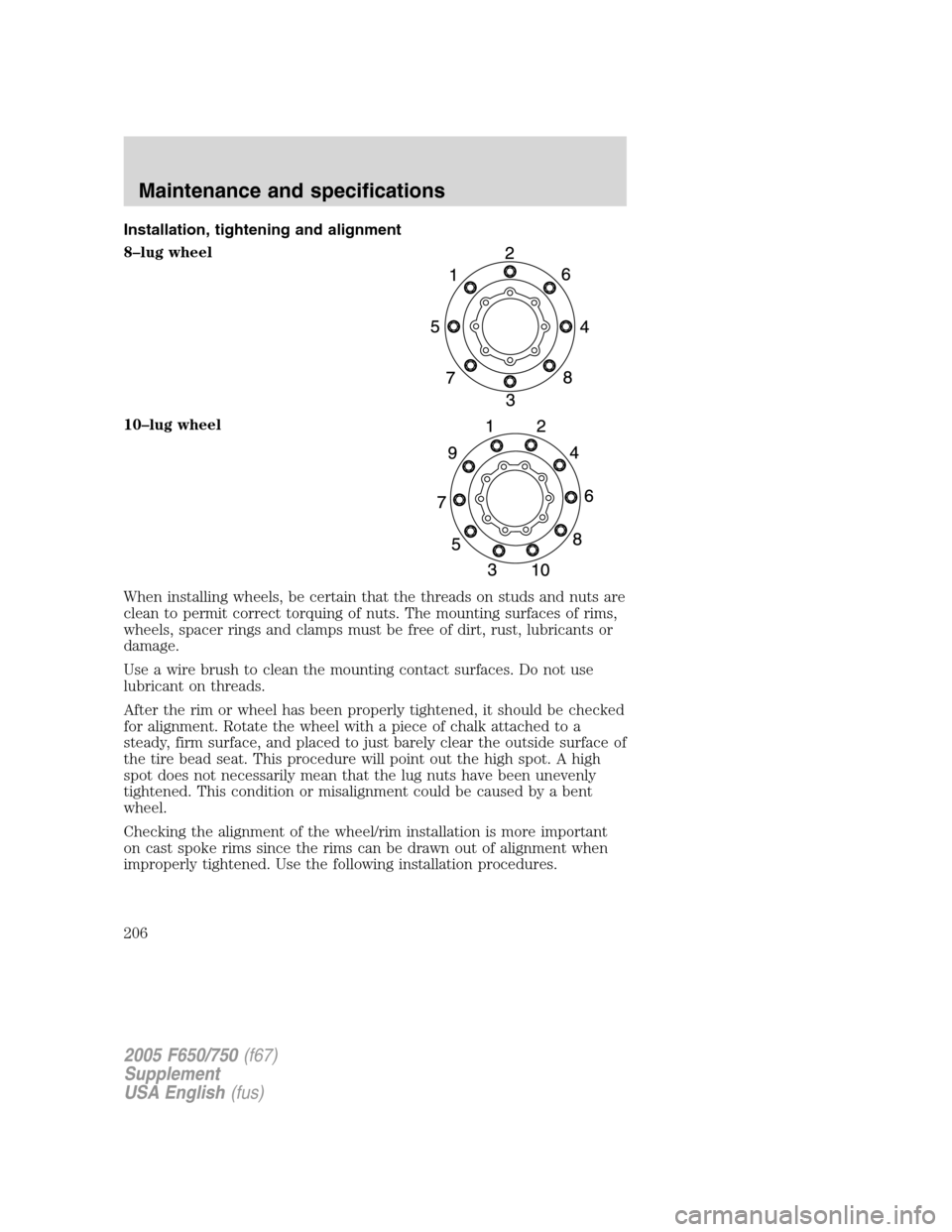
Installation, tightening and alignment
8–lug wheel
10–lug wheel
When installing wheels, be certain that the threads on studs and nuts are
clean to permit correct torquing of nuts. The mounting surfaces of rims,
wheels, spacer rings and clamps must be free of dirt, rust, lubricants or
damage.
Use a wire brush to clean the mounting contact surfaces. Do not use
lubricant on threads.
After the rim or wheel has been properly tightened, it should be checked
for alignment. Rotate the wheel with a piece of chalk attached to a
steady, firm surface, and placed to just barely clear the outside surface of
the tire bead seat. This procedure will point out the high spot. A high
spot does not necessarily mean that the lug nuts have been unevenly
tightened. This condition or misalignment could be caused by a bent
wheel.
Checking the alignment of the wheel/rim installation is more important
on cast spoke rims since the rims can be drawn out of alignment when
improperly tightened. Use the following installation procedures.
2005 F650/750(f67)
Supplement
USA English(fus)
Maintenance and specifications
206
Page 207 of 272
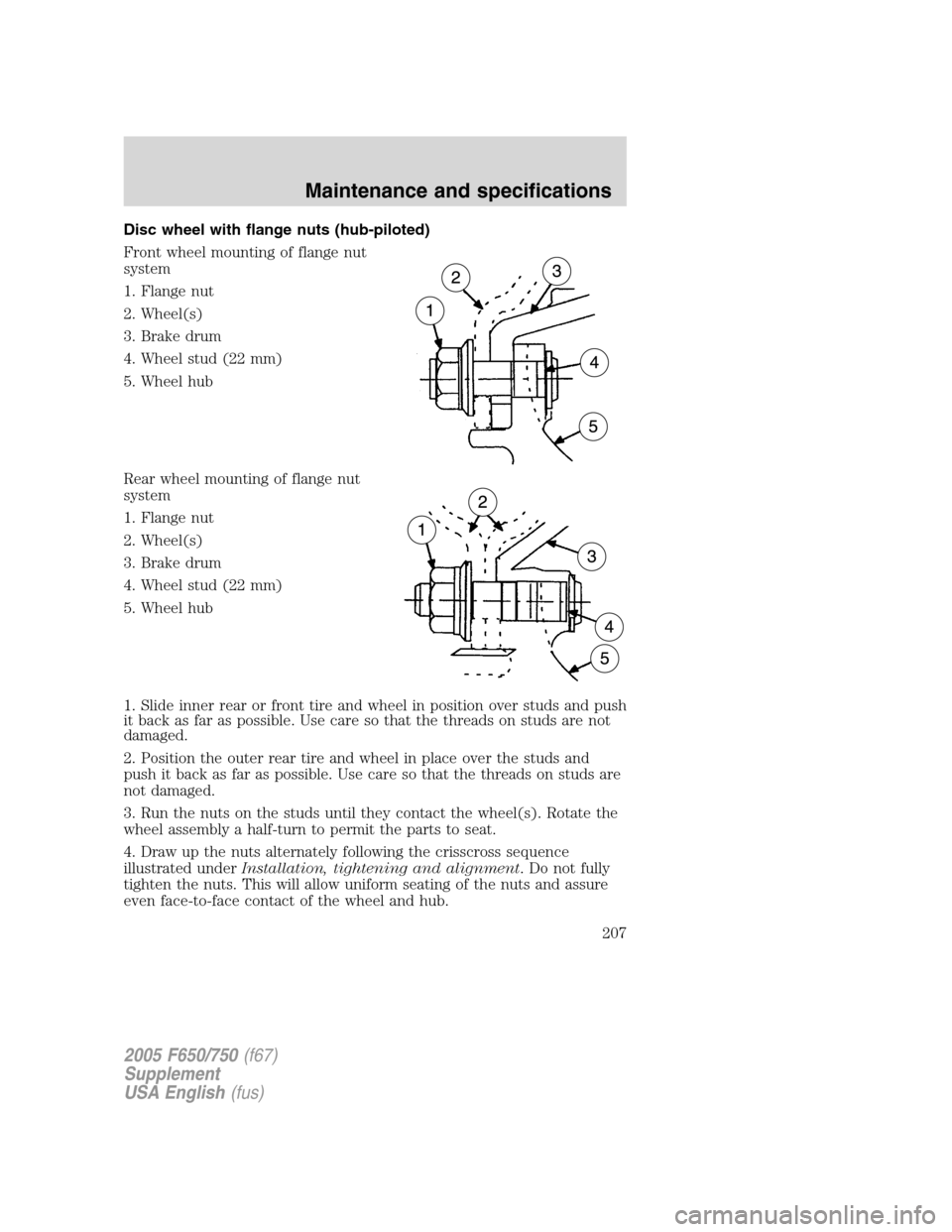
Disc wheel with flange nuts (hub-piloted)
Front wheel mounting of flange nut
system
1. Flange nut
2. Wheel(s)
3. Brake drum
4. Wheel stud (22 mm)
5. Wheel hub
Rear wheel mounting of flange nut
system
1. Flange nut
2. Wheel(s)
3. Brake drum
4. Wheel stud (22 mm)
5. Wheel hub
1. Slide inner rear or front tire and wheel in position over studs and push
it back as far as possible. Use care so that the threads on studs are not
damaged.
2. Position the outer rear tire and wheel in place over the studs and
push it back as far as possible. Use care so that the threads on studs are
not damaged.
3. Run the nuts on the studs until they contact the wheel(s). Rotate the
wheel assembly a half-turn to permit the parts to seat.
4. Draw up the nuts alternately following the crisscross sequence
illustrated underInstallation, tightening and alignment. Do not fully
tighten the nuts. This will allow uniform seating of the nuts and assure
even face-to-face contact of the wheel and hub.
2005 F650/750(f67)
Supplement
USA English(fus)
Maintenance and specifications
207
Page 208 of 272
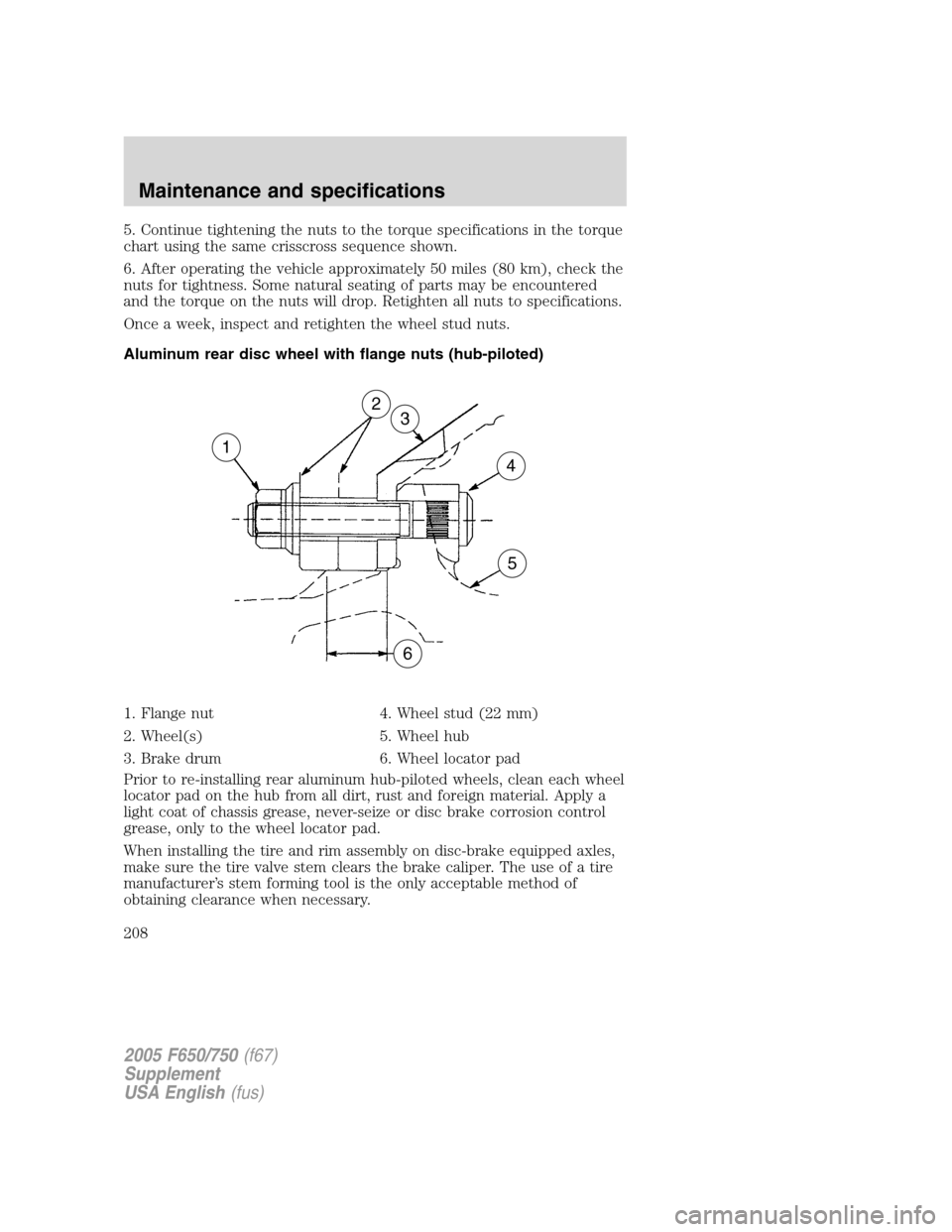
5. Continue tightening the nuts to the torque specifications in the torque
chart using the same crisscross sequence shown.
6. After operating the vehicle approximately 50 miles (80 km), check the
nuts for tightness. Some natural seating of parts may be encountered
and the torque on the nuts will drop. Retighten all nuts to specifications.
Once a week, inspect and retighten the wheel stud nuts.
Aluminum rear disc wheel with flange nuts (hub-piloted)
1. Flange nut
2. Wheel(s)
3. Brake drum4. Wheel stud (22 mm)
5. Wheel hub
6. Wheel locator pad
Prior to re-installing rear aluminum hub-piloted wheels, clean each wheel
locator pad on the hub from all dirt, rust and foreign material. Apply a
light coat of chassis grease, never-seize or disc brake corrosion control
grease, only to the wheel locator pad.
When installing the tire and rim assembly on disc-brake equipped axles,
make sure the tire valve stem clears the brake caliper. The use of a tire
manufacturer’s stem forming tool is the only acceptable method of
obtaining clearance when necessary.
1
6
5
4
32
2005 F650/750(f67)
Supplement
USA English(fus)
Maintenance and specifications
208
Page 209 of 272
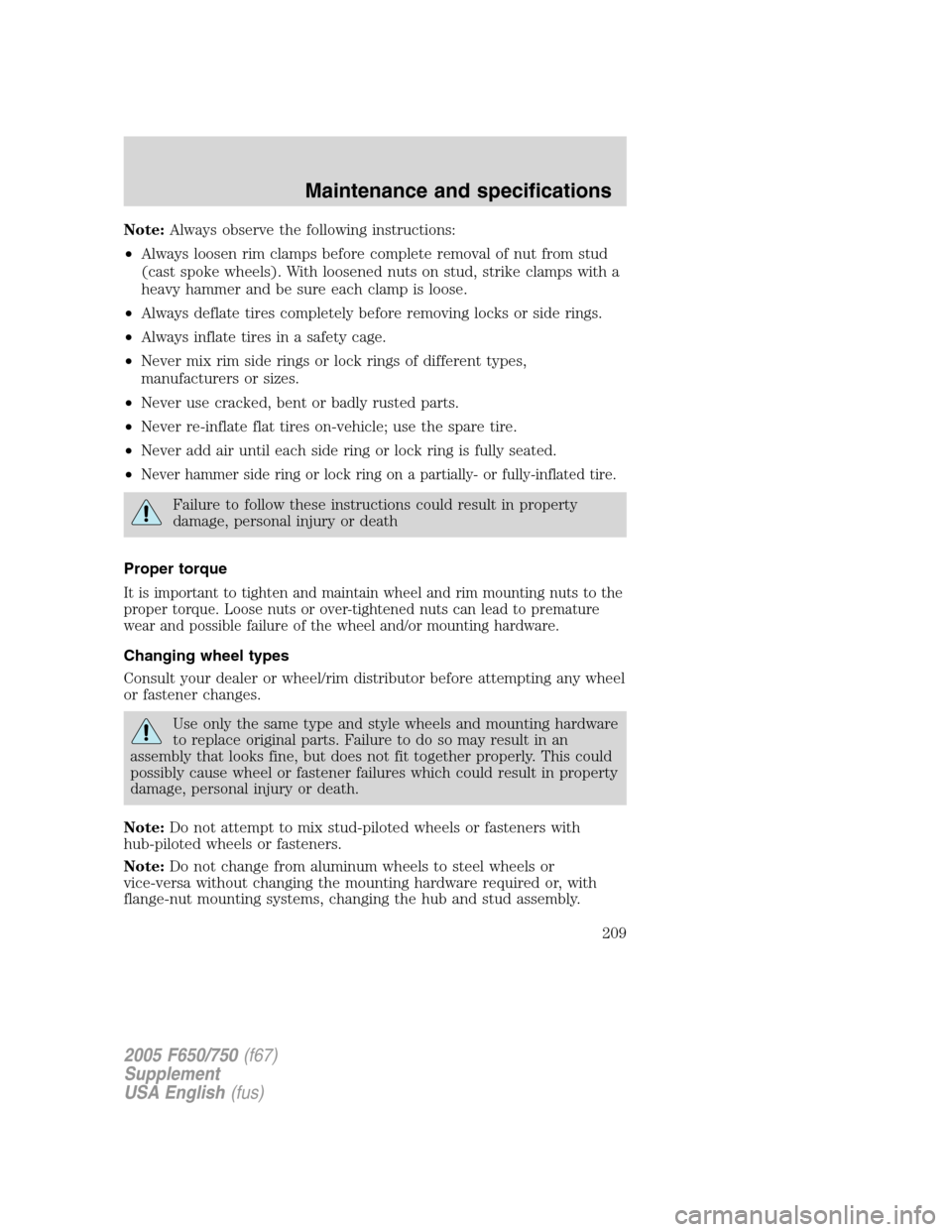
Note:Always observe the following instructions:
•Always loosen rim clamps before complete removal of nut from stud
(cast spoke wheels). With loosened nuts on stud, strike clamps with a
heavy hammer and be sure each clamp is loose.
•Always deflate tires completely before removing locks or side rings.
•Always inflate tires in a safety cage.
•Never mix rim side rings or lock rings of different types,
manufacturers or sizes.
•Never use cracked, bent or badly rusted parts.
•Never re-inflate flat tires on-vehicle; use the spare tire.
•Never add air until each side ring or lock ring is fully seated.
•
Never hammer side ring or lock ring on a partially- or fully-inflated tire.
Failure to follow these instructions could result in property
damage, personal injury or death
Proper torque
It is important to tighten and maintain wheel and rim mounting nuts to the
proper torque. Loose nuts or over-tightened nuts can lead to premature
wear and possible failure of the wheel and/or mounting hardware.
Changing wheel types
Consult your dealer or wheel/rim distributor before attempting any wheel
or fastener changes.
Use only the same type and style wheels and mounting hardware
to replace original parts. Failure to do so may result in an
assembly that looks fine, but does not fit together properly. This could
possibly cause wheel or fastener failures which could result in property
damage, personal injury or death.
Note:Do not attempt to mix stud-piloted wheels or fasteners with
hub-piloted wheels or fasteners.
Note:Do not change from aluminum wheels to steel wheels or
vice-versa without changing the mounting hardware required or, with
flange-nut mounting systems, changing the hub and stud assembly.
2005 F650/750(f67)
Supplement
USA English(fus)
Maintenance and specifications
209
Page 210 of 272
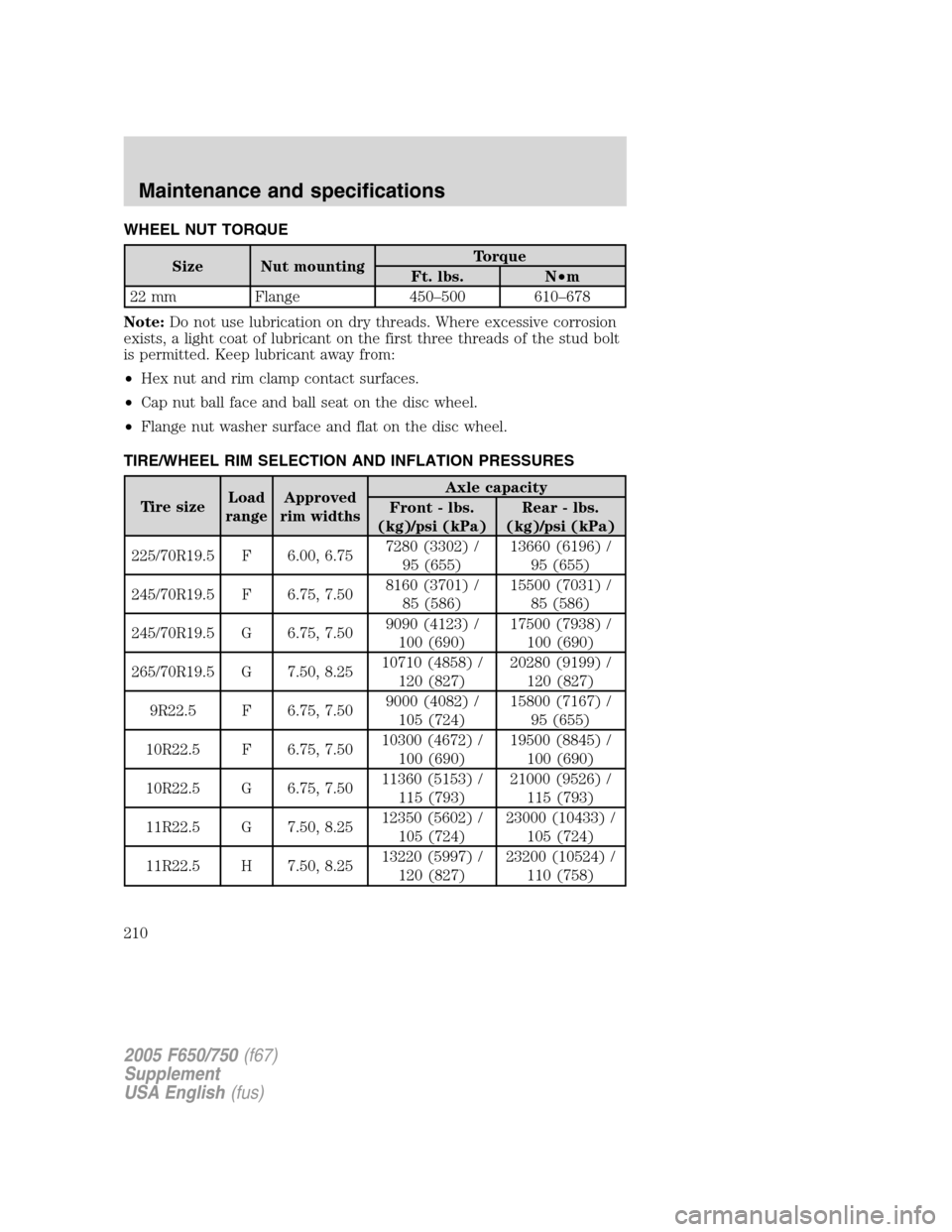
WHEEL NUT TORQUE
Size Nut mountingTorque
Ft. lbs. N•m
22 mm Flange 450–500 610–678
Note:Do not use lubrication on dry threads. Where excessive corrosion
exists, a light coat of lubricant on the first three threads of the stud bolt
is permitted. Keep lubricant away from:
•Hex nut and rim clamp contact surfaces.
•Cap nut ball face and ball seat on the disc wheel.
•Flange nut washer surface and flat on the disc wheel.
TIRE/WHEEL RIM SELECTION AND INFLATION PRESSURES
Tire sizeLoad
rangeApproved
rim widthsAxle capacity
Front - lbs.
(kg)/psi (kPa)Rear - lbs.
(kg)/psi (kPa)
225/70R19.5 F 6.00, 6.757280 (3302) /
95 (655)13660 (6196) /
95 (655)
245/70R19.5 F 6.75, 7.508160 (3701) /
85 (586)15500 (7031) /
85 (586)
245/70R19.5 G 6.75, 7.509090 (4123) /
100 (690)17500 (7938) /
100 (690)
265/70R19.5 G 7.50, 8.2510710 (4858) /
120 (827)20280 (9199) /
120 (827)
9R22.5 F 6.75, 7.509000 (4082) /
105 (724)15800 (7167) /
95 (655)
10R22.5 F 6.75, 7.5010300 (4672) /
100 (690)19500 (8845) /
100 (690)
10R22.5 G 6.75, 7.5011360 (5153) /
115 (793)21000 (9526) /
115 (793)
11R22.5 G 7.50, 8.2512350 (5602) /
105 (724)23000 (10433) /
105 (724)
11R22.5 H 7.50, 8.2513220 (5997) /
120 (827)23200 (10524) /
110 (758)
2005 F650/750(f67)
Supplement
USA English(fus)
Maintenance and specifications
210