FORD MONDEO 1993 Service Repair Manual
Manufacturer: FORD, Model Year: 1993, Model line: MONDEO, Model: FORD MONDEO 1993Pages: 279, PDF Size: 12.71 MB
Page 101 of 279
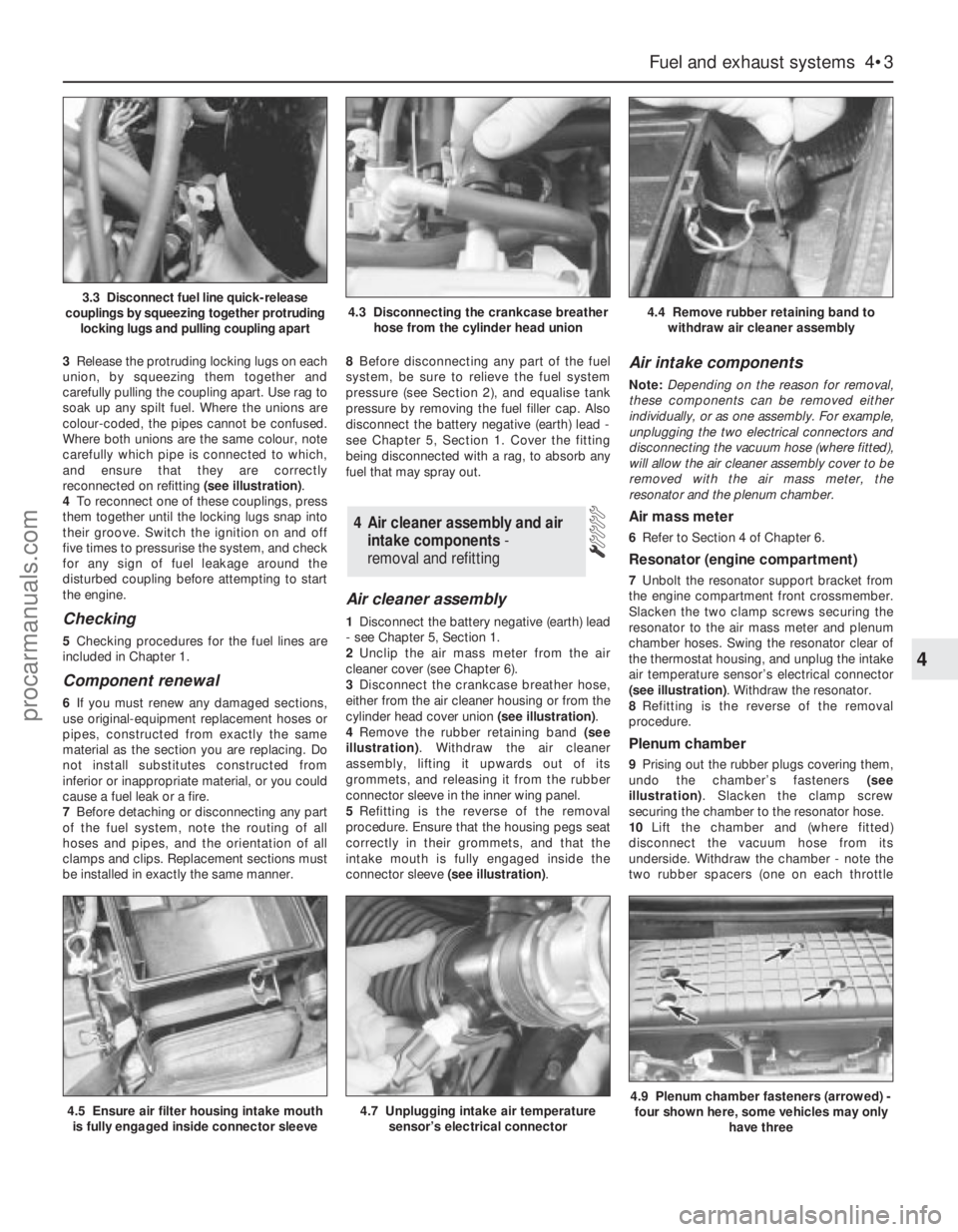
3Release the protruding locking lugs on each
union, by squeezing them together and
carefully pulling the coupling apart. Use rag to
soak up any spilt fuel. Where the unions are
colour-coded, the pipes cannot be confused.
Where both unions are the same colour, note
carefully which pipe is connected to which,
and ensure that they are correctly
reconnected on refitting (see illustration).
4To reconnect one of these couplings, press
them together until the locking lugs snap into
their groove. Switch the ignition on and off
five times to pressurise the system, and check
for any sign of fuel leakage around the
disturbed coupling before attempting to start
the engine.
Checking
5Checking procedures for the fuel lines are
included in Chapter 1.
Component renewal
6If you must renew any damaged sections,
use original-equipment replacement hoses or
pipes, constructed from exactly the same
material as the section you are replacing. Do
not install substitutes constructed from
inferior or inappropriate material, or you could
cause a fuel leak or a fire.
7Before detaching or disconnecting any part
of the fuel system, note the routing of all
hoses and pipes, and the orientation of all
clamps and clips. Replacement sections must
be installed in exactly the same manner.8Before disconnecting any part of the fuel
system, be sure to relieve the fuel system
pressure (see Section 2), and equalise tank
pressure by removing the fuel filler cap. Also
disconnect the battery negative (earth) lead -
see Chapter 5, Section 1. Cover the fitting
being disconnected with a rag, to absorb any
fuel that may spray out.
Air cleaner assembly
1Disconnect the battery negative (earth) lead
- see Chapter 5, Section 1.
2Unclip the air mass meter from the air
cleaner cover (see Chapter 6).
3Disconnect the crankcase breather hose,
either from the air cleaner housing or from the
cylinder head cover union (see illustration).
4Remove the rubber retaining band (see
illustration). Withdraw the air cleaner
assembly, lifting it upwards out of its
grommets, and releasing it from the rubber
connector sleeve in the inner wing panel.
5Refitting is the reverse of the removal
procedure. Ensure that the housing pegs seat
correctly in their grommets, and that the
intake mouth is fully engaged inside the
connector sleeve (see illustration).
Air intake components
Note:Depending on the reason for removal,
these components can be removed either
individually, or as one assembly. For example,
unplugging the two electrical connectors and
disconnecting the vacuum hose (where fitted),
will allow the air cleaner assembly cover to be
removed with the air mass meter, the
resonator and the plenum chamber.
Air mass meter
6Refer to Section 4 of Chapter 6.
Resonator (engine compartment)
7Unbolt the resonator support bracket from
the engine compartment front crossmember.
Slacken the two clamp screws securing the
resonator to the air mass meter and plenum
chamber hoses. Swing the resonator clear of
the thermostat housing, and unplug the intake
air temperature sensor’s electrical connector
(see illustration). Withdraw the resonator.
8Refitting is the reverse of the removal
procedure.
Plenum chamber
9Prising out the rubber plugs covering them,
undo the chamber’s fasteners (see
illustration). Slacken the clamp screw
securing the chamber to the resonator hose.
10Lift the chamber and (where fitted)
disconnect the vacuum hose from its
underside. Withdraw the chamber - note the
two rubber spacers (one on each throttle
4 Air cleaner assembly and air
intake components -
removal and refitting
Fuel and exhaust systems 4•3
4
4.5 Ensure air filter housing intake mouth
is fully engaged inside connector sleeve4.7 Unplugging intake air temperature
sensor’s electrical connector4.9 Plenum chamber fasteners (arrowed) -
four shown here, some vehicles may only
have three
3.3 Disconnect fuel line quick-release
couplings by squeezing together protruding
locking lugs and pulling coupling apart4.3 Disconnecting the crankcase breather
hose from the cylinder head union4.4 Remove rubber retaining band to
withdraw air cleaner assembly
procarmanuals.com
Page 102 of 279

housing stud) and the sealing O-ring in the
chamber’s mouth (see illustrations).
11Refitting is the reverse of the removal
procedure. Ensure that the O-ring and
spacers are correctly seated.
Underwing components
12Remove the left-hand wheel arch liner
(see Chapter 11).
13Unbolt and withdraw the air intake tube
and both resonators as required.
14Refitting is the reverse of the removal
procedure.
Removal
1Disconnect the battery negative (earth) lead
- see Chapter 5, Section 1.
2Remove the plenum chamber (see Sec-
tion 4).
3Remove the clip securing the cable to the
throttle housing bracket (see illustration).
Disconnect the cable end nipple from the
throttle linkage, and release the cable from
any securing clips or ties.
4Working in the passenger compartment,
reach up to the top of the accelerator pedal.
Pull the end fitting and collar out of the pedal,then release the cable inner wire through the
slot in the pedal (see illustration). Tie a length
of string to the end of the cable.
5Returning to the engine compartment, pull
the cable through the bulkhead until the string
can be untied and the cable removed.
Refitting
6Refitting is the reverse of the removal
procedure; use the string to draw the cable
through the bulkhead.
7Adjust the cable as described below.
Adjustment
8Remove the plenum chamber (see Sec-
tion 4).
9Find the cable adjuster - this is either at the
throttle housing bracket, or two-thirds along
the length of the cable, clipped to the front
suspension right-hand mounting (see
illustration). Remove the metal clip and
lubricate the adjuster’s grommet with soapy
water.
10Remove any slack by pulling the cable
outer as far as possible out of the adjuster.
Have an assistant depress the accelerator
pedal fully - the cable outer will move back
into the adjuster - and hold it there while the
clip is refitted.
11Check that the throttle valve moves
smoothly and easily from the fully-closed to
the fully-open position and back again, as the
assistant depresses and releases theaccelerator pedal. Re-adjust the cable if
required.
12When the setting is correct, refit the
plenum chamber (see Section 4).
Removal
Note:While the following procedure deals
with the complete cable, the pedal-to-
actuator and actuator-to-throttle housing
sections of the cable are available separately,
and can be removed and refitted individually.
If doing this, modify the procedure as
required.
1Disconnect the battery negative (earth) lead
- see Chapter 5, Section 1.
2Remove the plenum chamber (see Sec-
tion 4).
3Remove the clip securing the cable to the
throttle housing bracket, then pull the cable’s
grommet out of the bracket. Disconnect the
cable end nipple from the throttle linkage, and
release the cable from any securing clips or
ties.
4Unplug the TCS throttle actuator’s electrical
connector, and prise off its cover (see
illustration).
5Noting which cable section is connected to
6 Accelerator cable (models
with traction control)-
removal, refitting and adjustment
5 Accelerator cable (models
without traction control) -
removal, refitting and adjustment
4•4 Fuel and exhaust systems
4.10A Lift plenum chamber and (where
fitted) disconnect the vacuum hose - note
the two rubber spacers (arrowed) . . .4.10B . . . and the sealing O-ring (arrowed)
in the chamber’s mouth5.3 Removing clip securing accelerator
cable to throttle housing bracket
5.4 Pull the accelerator cable end fitting
(arrowed) out of the pedal5.9 Location of accelerator cable adjuster
- remove metal clip (arrowed) to enable
adjustment to be made6.4 Unplug TCS throttle actuator’s
electrical connector (A), and prise off its
cover at two points (B)
procarmanuals.com
Page 103 of 279
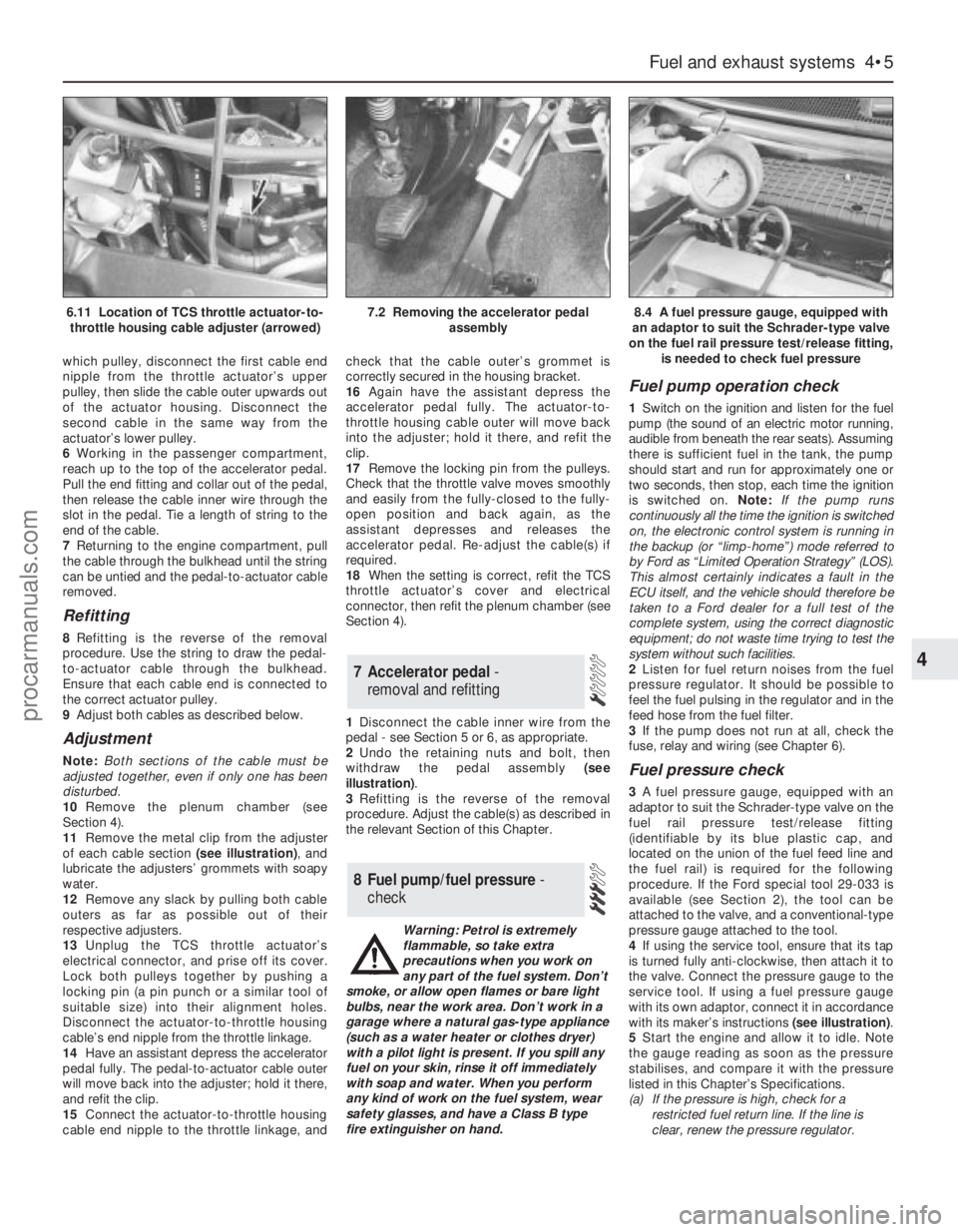
which pulley, disconnect the first cable end
nipple from the throttle actuator’s upper
pulley, then slide the cable outer upwards out
of the actuator housing. Disconnect the
second cable in the same way from the
actuator’s lower pulley.
6Working in the passenger compartment,
reach up to the top of the accelerator pedal.
Pull the end fitting and collar out of the pedal,
then release the cable inner wire through the
slot in the pedal. Tie a length of string to the
end of the cable.
7Returning to the engine compartment, pull
the cable through the bulkhead until the string
can be untied and the pedal-to-actuator cable
removed.
Refitting
8Refitting is the reverse of the removal
procedure. Use the string to draw the pedal-
to-actuator cable through the bulkhead.
Ensure that each cable end is connected to
the correct actuator pulley.
9Adjust both cables as described below.
Adjustment
Note:Both sections of the cable must be
adjusted together, even if only one has been
disturbed.
10Remove the plenum chamber (see
Section 4).
11Remove the metal clip from the adjuster
of each cable section (see illustration), and
lubricate the adjusters’ grommets with soapy
water.
12Remove any slack by pulling both cable
outers as far as possible out of their
respective adjusters.
13Unplug the TCS throttle actuator’s
electrical connector, and prise off its cover.
Lock both pulleys together by pushing a
locking pin (a pin punch or a similar tool of
suitable size) into their alignment holes.
Disconnect the actuator-to-throttle housing
cable’s end nipple from the throttle linkage.
14Have an assistant depress the accelerator
pedal fully. The pedal-to-actuator cable outer
will move back into the adjuster; hold it there,
and refit the clip.
15Connect the actuator-to-throttle housing
cable end nipple to the throttle linkage, andcheck that the cable outer’s grommet is
correctly secured in the housing bracket.
16Again have the assistant depress the
accelerator pedal fully. The actuator-to-
throttle housing cable outer will move back
into the adjuster; hold it there, and refit the
clip.
17Remove the locking pin from the pulleys.
Check that the throttle valve moves smoothly
and easily from the fully-closed to the fully-
open position and back again, as the
assistant depresses and releases the
accelerator pedal. Re-adjust the cable(s) if
required.
18When the setting is correct, refit the TCS
throttle actuator’s cover and electrical
connector, then refit the plenum chamber (see
Section 4).
1Disconnect the cable inner wire from the
pedal - see Section 5 or 6, as appropriate.
2Undo the retaining nuts and bolt, then
withdraw the pedal assembly (see
illustration).
3Refitting is the reverse of the removal
procedure. Adjust the cable(s) as described in
the relevant Section of this Chapter.
Warning: Petrol is extremely
flammable, so take extra
precautions when you work on
any part of the fuel system. Don’t
smoke, or allow open flames or bare light
bulbs, near the work area. Don’t work in a
garage where a natural gas-type appliance
(such as a water heater or clothes dryer)
with a pilot light is present. If you spill any
fuel on your skin, rinse it off immediately
with soap and water. When you perform
any kind of work on the fuel system, wear
safety glasses, and have a Class B type
fire extinguisher on hand.
Fuel pump operation check
1Switch on the ignition and listen for the fuel
pump (the sound of an electric motor running,
audible from beneath the rear seats). Assuming
there is sufficient fuel in the tank, the pump
should start and run for approximately one or
two seconds, then stop, each time the ignition
is switched on. Note:If the pump runs
continuously all the time the ignition is switched
on, the electronic control system is running in
the backup (or “limp-home”) mode referred to
by Ford as “Limited Operation Strategy” (LOS).
This almost certainly indicates a fault in the
ECU itself, and the vehicle should therefore be
taken to a Ford dealer for a full test of the
complete system, using the correct diagnostic
equipment; do not waste time trying to test the
system without such facilities.
2Listen for fuel return noises from the fuel
pressure regulator. It should be possible to
feel the fuel pulsing in the regulator and in the
feed hose from the fuel filter.
3If the pump does not run at all, check the
fuse, relay and wiring (see Chapter 6).
Fuel pressure check
3A fuel pressure gauge, equipped with an
adaptor to suit the Schrader-type valve on the
fuel rail pressure test/release fitting
(identifiable by its blue plastic cap, and
located on the union of the fuel feed line and
the fuel rail) is required for the following
procedure. If the Ford special tool 29-033 is
available (see Section 2), the tool can be
attached to the valve, and a conventional-type
pressure gauge attached to the tool.
4If using the service tool, ensure that its tap
is turned fully anti-clockwise, then attach it to
the valve. Connect the pressure gauge to the
service tool. If using a fuel pressure gauge
with its own adaptor, connect it in accordance
with its maker’s instructions (see illustration).
5Start the engine and allow it to idle. Note
the gauge reading as soon as the pressure
stabilises, and compare it with the pressure
listed in this Chapter’s Specifications.
(a) If the pressure is high, check for a
restricted fuel return line. If the line is
clear, renew the pressure regulator.
8 Fuel pump/fuel pressure -
check
7 Accelerator pedal -
removal and refitting
Fuel and exhaust systems 4•5
4
6.11 Location of TCS throttle actuator-to-
throttle housing cable adjuster (arrowed)7.2 Removing the accelerator pedal
assembly8.4 A fuel pressure gauge, equipped with
an adaptor to suit the Schrader-type valve
on the fuel rail pressure test/release fitting,
is needed to check fuel pressure
procarmanuals.com
Page 104 of 279
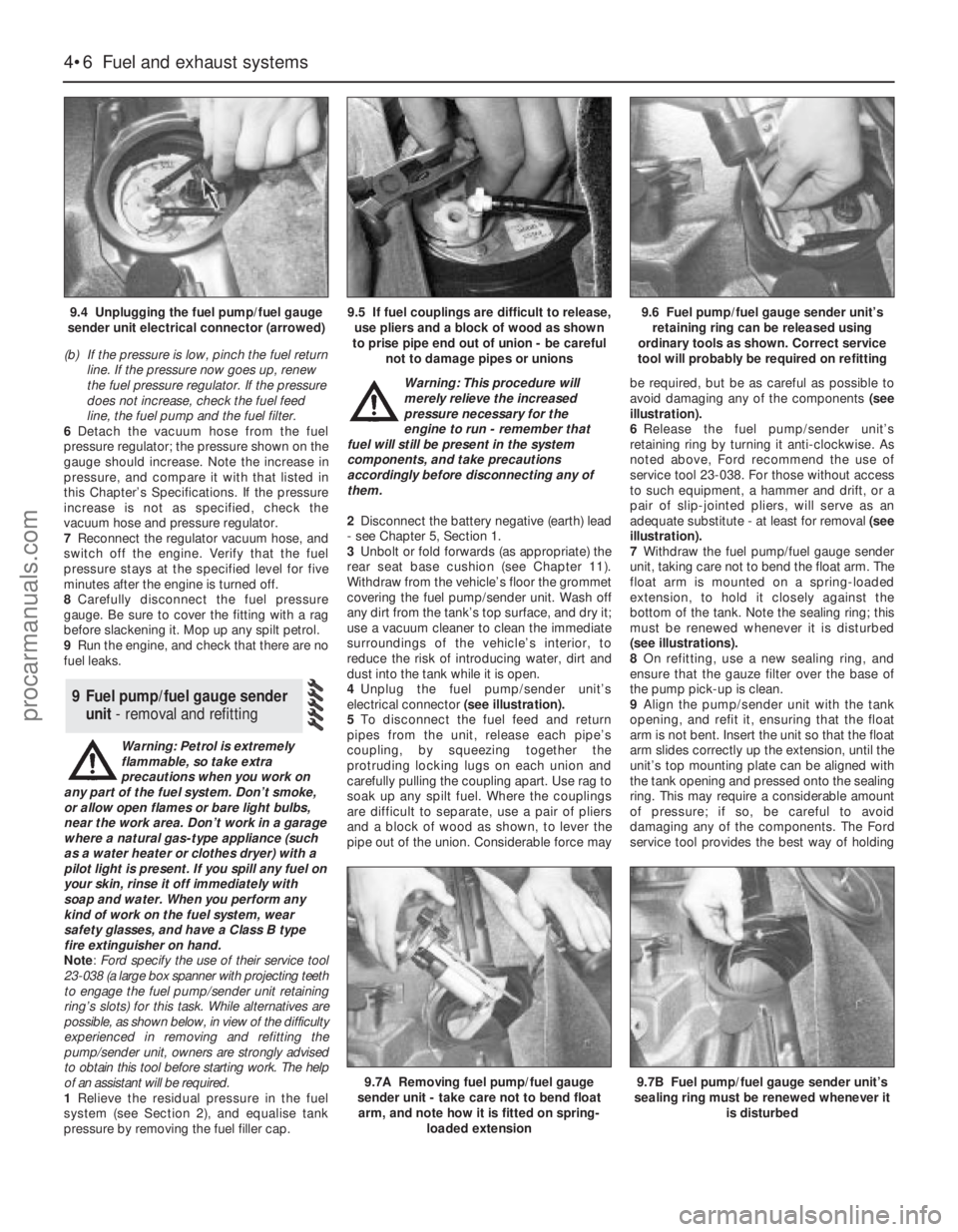
(b) If the pressure is low, pinch the fuel return
line. If the pressure now goes up, renew
the fuel pressure regulator. If the pressure
does not increase, check the fuel feed
line, the fuel pump and the fuel filter.
6Detach the vacuum hose from the fuel
pressure regulator; the pressure shown on the
gauge should increase. Note the increase in
pressure, and compare it with that listed in
this Chapter’s Specifications. If the pressure
increase is not as specified, check the
vacuum hose and pressure regulator.
7Reconnect the regulator vacuum hose, and
switch off the engine. Verify that the fuel
pressure stays at the specified level for five
minutes after the engine is turned off.
8Carefully disconnect the fuel pressure
gauge. Be sure to cover the fitting with a rag
before slackening it. Mop up any spilt petrol.
9Run the engine, and check that there are no
fuel leaks.
Warning: Petrol is extremely
flammable, so take extra
precautions when you work on
any part of the fuel system. Don’t smoke,
or allow open flames or bare light bulbs,
near the work area. Don’t work in a garage
where a natural gas-type appliance (such
as a water heater or clothes dryer) with a
pilot light is present. If you spill any fuel on
your skin, rinse it off immediately with
soap and water. When you perform any
kind of work on the fuel system, wear
safety glasses, and have a Class B type
fire extinguisher on hand.
Note: Ford specify the use of their service tool
23-038 (a large box spanner with projecting teeth
to engage the fuel pump/sender unit retaining
ring’s slots) for this task. While alternatives are
possible, as shown below, in view of the difficulty
experienced in removing and refitting the
pump/sender unit, owners are strongly advised
to obtain this tool before starting work. The help
of an assistant will be required.
1Relieve the residual pressure in the fuel
system (see Section 2), and equalise tank
pressure by removing the fuel filler cap. Warning: This procedure will
merely relieve the increased
pressure necessary for the
engine to run - remember that
fuel will still be present in the system
components, and take precautions
accordingly before disconnecting any of
them.
2Disconnect the battery negative (earth) lead
- see Chapter 5, Section 1.
3Unbolt or fold forwards (as appropriate) the
rear seat base cushion (see Chapter 11).
Withdraw from the vehicle’s floor the grommet
covering the fuel pump/sender unit. Wash off
any dirt from the tank’s top surface, and dry it;
use a vacuum cleaner to clean the immediate
surroundings of the vehicle’s interior, to
reduce the risk of introducing water, dirt and
dust into the tank while it is open.
4Unplug the fuel pump/sender unit’s
electrical connector (see illustration).
5To disconnect the fuel feed and return
pipes from the unit, release each pipe’s
coupling, by squeezing together the
protruding locking lugs on each union and
carefully pulling the coupling apart. Use rag to
soak up any spilt fuel. Where the couplings
are difficult to separate, use a pair of pliers
and a block of wood as shown, to lever the
pipe out of the union. Considerable force maybe required, but be as careful as possible to
avoid damaging any of the components (see
illustration).
6Release the fuel pump/sender unit’s
retaining ring by turning it anti-clockwise. As
noted above, Ford recommend the use of
service tool 23-038. For those without access
to such equipment, a hammer and drift, or a
pair of slip-jointed pliers, will serve as an
adequate substitute - at least for removal (see
illustration).
7Withdraw the fuel pump/fuel gauge sender
unit, taking care not to bend the float arm. The
float arm is mounted on a spring-loaded
extension, to hold it closely against the
bottom of the tank. Note the sealing ring; this
must be renewed whenever it is disturbed
(see illustrations).
8On refitting, use a new sealing ring, and
ensure that the gauze filter over the base of
the pump pick-up is clean.
9Align the pump/sender unit with the tank
opening, and refit it, ensuring that the float
arm is not bent. Insert the unit so that the float
arm slides correctly up the extension, until the
unit’s top mounting plate can be aligned with
the tank opening and pressed onto the sealing
ring. This may require a considerable amount
of pressure; if so, be careful to avoid
damaging any of the components. The Ford
service tool provides the best way of holding
9 Fuel pump/fuel gauge sender
unit- removal and refitting
4•6 Fuel and exhaust systems
9.4 Unplugging the fuel pump/fuel gauge
sender unit electrical connector (arrowed)9.5 If fuel couplings are difficult to release,
use pliers and a block of wood as shown
to prise pipe end out of union - be careful
not to damage pipes or unions9.6 Fuel pump/fuel gauge sender unit’s
retaining ring can be released using
ordinary tools as shown. Correct service
tool will probably be required on refitting
9.7A Removing fuel pump/fuel gauge
sender unit - take care not to bend float
arm, and note how it is fitted on spring-
loaded extension9.7B Fuel pump/fuel gauge sender unit’s
sealing ring must be renewed whenever it
is disturbed
procarmanuals.com
Page 105 of 279
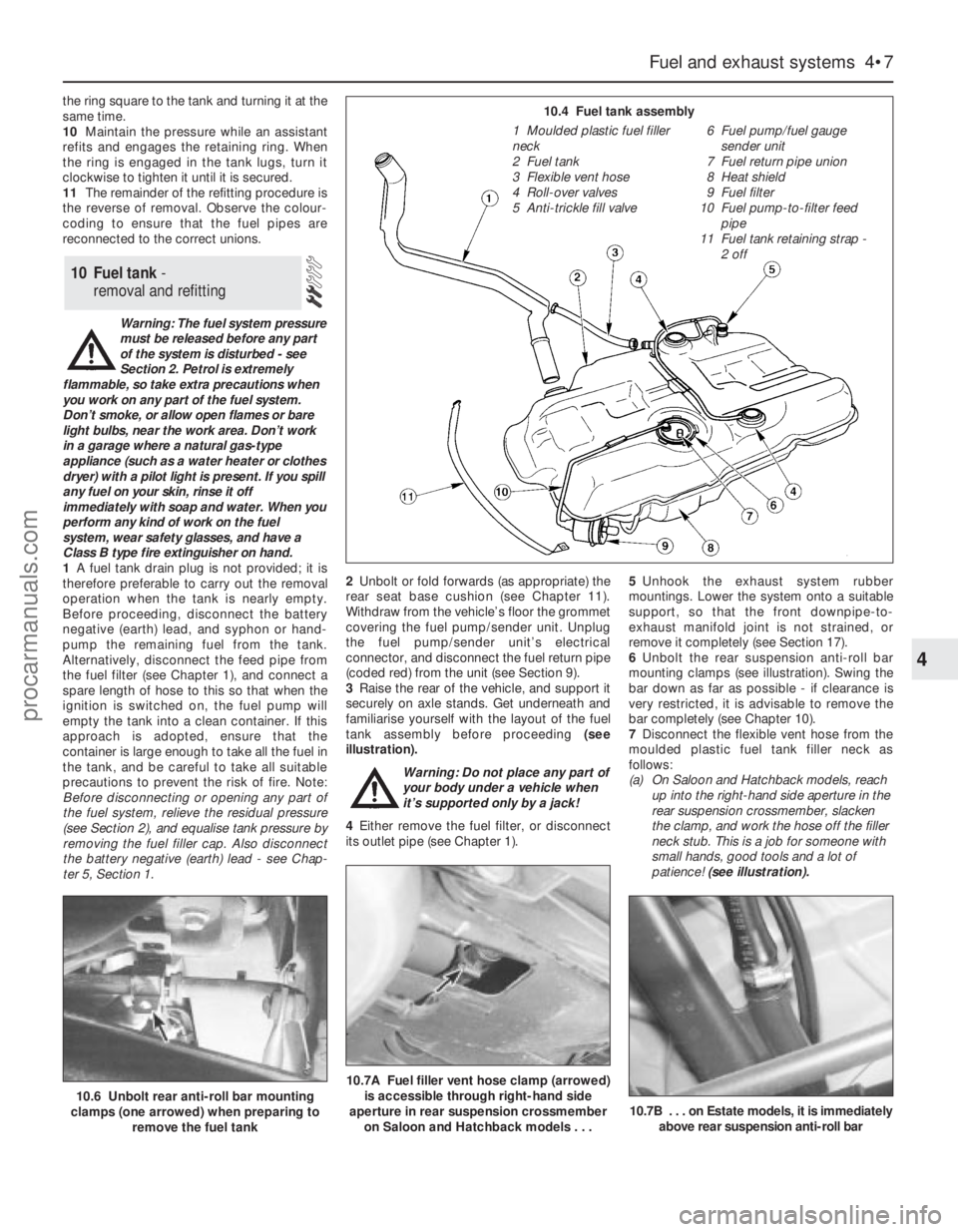
the ring square to the tank and turning it at the
same time.
10Maintain the pressure while an assistant
refits and engages the retaining ring. When
the ring is engaged in the tank lugs, turn it
clockwise to tighten it until it is secured.
11The remainder of the refitting procedure is
the reverse of removal. Observe the colour-
coding to ensure that the fuel pipes are
reconnected to the correct unions.
Warning: The fuel system pressure
must be released before any part
of the system is disturbed - see
Section 2. Petrol is extremely
flammable, so take extra precautions when
you work on any part of the fuel system.
Don’t smoke, or allow open flames or bare
light bulbs, near the work area. Don’t work
in a garage where a natural gas-type
appliance (such as a water heater or clothes
dryer) with a pilot light is present. If you spill
any fuel on your skin, rinse it off
immediately with soap and water. When you
perform any kind of work on the fuel
system, wear safety glasses, and have a
Class B type fire extinguisher on hand.
1A fuel tank drain plug is not provided; it is
therefore preferable to carry out the removal
operation when the tank is nearly empty.
Before proceeding, disconnect the battery
negative (earth) lead, and syphon or hand-
pump the remaining fuel from the tank.
Alternatively, disconnect the feed pipe from
the fuel filter (see Chapter 1), and connect a
spare length of hose to this so that when the
ignition is switched on, the fuel pump will
empty the tank into a clean container. If this
approach is adopted, ensure that the
container is large enough to take all the fuel in
the tank, and be careful to take all suitable
precautions to prevent the risk of fire. Note:
Before disconnecting or opening any part of
the fuel system, relieve the residual pressure
(see Section 2), and equalise tank pressure by
removing the fuel filler cap. Also disconnect
the battery negative (earth) lead - see Chap-
ter 5, Section 1.2Unbolt or fold forwards (as appropriate) the
rear seat base cushion (see Chapter 11).
Withdraw from the vehicle’s floor the grommet
covering the fuel pump/sender unit. Unplug
the fuel pump/sender unit’s electrical
connector, and disconnect the fuel return pipe
(coded red) from the unit (see Section 9).
3Raise the rear of the vehicle, and support it
securely on axle stands. Get underneath and
familiarise yourself with the layout of the fuel
tank assembly before proceeding (see
illustration).
Warning: Do not place any part of
your body under a vehicle when
it’s supported only by a jack!
4Either remove the fuel filter, or disconnect
its outlet pipe (see Chapter 1).5Unhook the exhaust system rubber
mountings. Lower the system onto a suitable
support, so that the front downpipe-to-
exhaust manifold joint is not strained, or
remove it completely (see Section 17).
6Unbolt the rear suspension anti-roll bar
mounting clamps (see illustration). Swing the
bar down as far as possible - if clearance is
very restricted, it is advisable to remove the
bar completely (see Chapter 10).
7Disconnect the flexible vent hose from the
moulded plastic fuel tank filler neck as
follows:
(a) On Saloon and Hatchback models, reach
up into the right-hand side aperture in the
rear suspension crossmember, slacken
the clamp, and work the hose off the filler
neck stub. This is a job for someone with
small hands, good tools and a lot of
patience! (see illustration).
10 Fuel tank -
removal and refitting
Fuel and exhaust systems 4•7
4
10.6 Unbolt rear anti-roll bar mounting
clamps (one arrowed) when preparing to
remove the fuel tank10.7A Fuel filler vent hose clamp (arrowed)
is accessible through right-hand side
aperture in rear suspension crossmember
on Saloon and Hatchback models . . .
10.7B . . . on Estate models, it is immediately
above rear suspension anti-roll bar
10.4 Fuel tank assembly
1 Moulded plastic fuel filler
neck
2 Fuel tank
3 Flexible vent hose
4 Roll-over valves
5 Anti-trickle fill valve6 Fuel pump/fuel gauge
sender unit
7 Fuel return pipe union
8 Heat shield
9 Fuel filter
10 Fuel pump-to-filter feed
pipe
11 Fuel tank retaining strap -
2 off
procarmanuals.com
Page 106 of 279
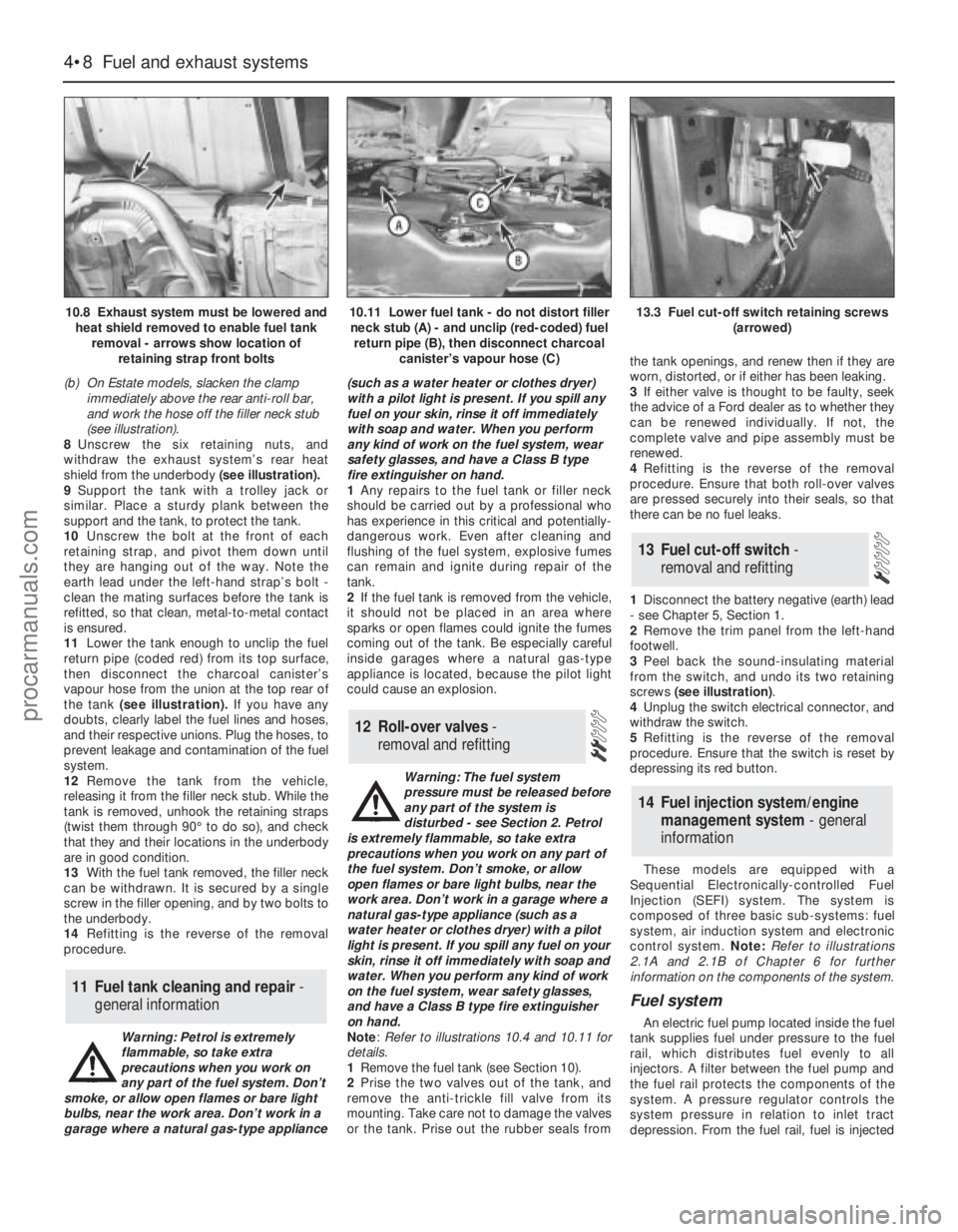
(b) On Estate models, slacken the clamp
immediately above the rear anti-roll bar,
and work the hose off the filler neck stub
(see illustration).
8Unscrew the six retaining nuts, and
withdraw the exhaust system’s rear heat
shield from the underbody (see illustration).
9Support the tank with a trolley jack or
similar. Place a sturdy plank between the
support and the tank, to protect the tank.
10Unscrew the bolt at the front of each
retaining strap, and pivot them down until
they are hanging out of the way. Note the
earth lead under the left-hand strap’s bolt -
clean the mating surfaces before the tank is
refitted, so that clean, metal-to-metal contact
is ensured.
11Lower the tank enough to unclip the fuel
return pipe (coded red) from its top surface,
then disconnect the charcoal canister’s
vapour hose from the union at the top rear of
the tank (see illustration). If you have any
doubts, clearly label the fuel lines and hoses,
and their respective unions. Plug the hoses, to
prevent leakage and contamination of the fuel
system.
12Remove the tank from the vehicle,
releasing it from the filler neck stub. While the
tank is removed, unhook the retaining straps
(twist them through 90° to do so), and check
that they and their locations in the underbody
are in good condition.
13With the fuel tank removed, the filler neck
can be withdrawn. It is secured by a single
screw in the filler opening, and by two bolts to
the underbody.
14Refitting is the reverse of the removal
procedure.
Warning: Petrol is extremely
flammable, so take extra
precautions when you work on
any part of the fuel system. Don’t
smoke, or allow open flames or bare light
bulbs, near the work area. Don’t work in a
garage where a natural gas-type appliance(such as a water heater or clothes dryer)
with a pilot light is present. If you spill any
fuel on your skin, rinse it off immediately
with soap and water. When you perform
any kind of work on the fuel system, wear
safety glasses, and have a Class B type
fire extinguisher on hand.
1Any repairs to the fuel tank or filler neck
should be carried out by a professional who
has experience in this critical and potentially-
dangerous work. Even after cleaning and
flushing of the fuel system, explosive fumes
can remain and ignite during repair of the
tank.
2If the fuel tank is removed from the vehicle,
it should not be placed in an area where
sparks or open flames could ignite the fumes
coming out of the tank. Be especially careful
inside garages where a natural gas-type
appliance is located, because the pilot light
could cause an explosion.
Warning: The fuel system
pressure must be released before
any part of the system is
disturbed - see Section 2. Petrol
is extremely flammable, so take extra
precautions when you work on any part of
the fuel system. Don’t smoke, or allow
open flames or bare light bulbs, near the
work area. Don’t work in a garage where a
natural gas-type appliance (such as a
water heater or clothes dryer) with a pilot
light is present. If you spill any fuel on your
skin, rinse it off immediately with soap and
water. When you perform any kind of work
on the fuel system, wear safety glasses,
and have a Class B type fire extinguisher
on hand.
Note: Refer to illustrations 10.4 and 10.11 for
details.
1Remove the fuel tank (see Section 10).
2Prise the two valves out of the tank, and
remove the anti-trickle fill valve from its
mounting. Take care not to damage the valves
or the tank. Prise out the rubber seals fromthe tank openings, and renew then if they are
worn, distorted, or if either has been leaking.
3If either valve is thought to be faulty, seek
the advice of a Ford dealer as to whether they
can be renewed individually. If not, the
complete valve and pipe assembly must be
renewed.
4Refitting is the reverse of the removal
procedure. Ensure that both roll-over valves
are pressed securely into their seals, so that
there can be no fuel leaks.
1Disconnect the battery negative (earth) lead
- see Chapter 5, Section 1.
2Remove the trim panel from the left-hand
footwell.
3Peel back the sound-insulating material
from the switch, and undo its two retaining
screws (see illustration).
4Unplug the switch electrical connector, and
withdraw the switch.
5Refitting is the reverse of the removal
procedure. Ensure that the switch is reset by
depressing its red button.
These models are equipped with a
Sequential Electronically-controlled Fuel
Injection (SEFI) system. The system is
composed of three basic sub-systems: fuel
system, air induction system and electronic
control system. Note:Refer to illustrations
2.1A and 2.1B of Chapter 6 for further
information on the components of the system.
Fuel system
An electric fuel pump located inside the fuel
tank supplies fuel under pressure to the fuel
rail, which distributes fuel evenly to all
injectors. A filter between the fuel pump and
the fuel rail protects the components of the
system. A pressure regulator controls the
system pressure in relation to inlet tract
depression. From the fuel rail, fuel is injected
14 Fuel injection system/engine
management system - general
information
13 Fuel cut-off switch -
removal and refitting
12 Roll-over valves -
removal and refitting
11 Fuel tank cleaning and repair -
general information
4•8 Fuel and exhaust systems
10.8 Exhaust system must be lowered and
heat shield removed to enable fuel tank
removal - arrows show location of
retaining strap front bolts10.11 Lower fuel tank - do not distort filler
neck stub (A) - and unclip (red-coded) fuel
return pipe (B), then disconnect charcoal
canister’s vapour hose (C)13.3 Fuel cut-off switch retaining screws
(arrowed)
procarmanuals.com
Page 107 of 279
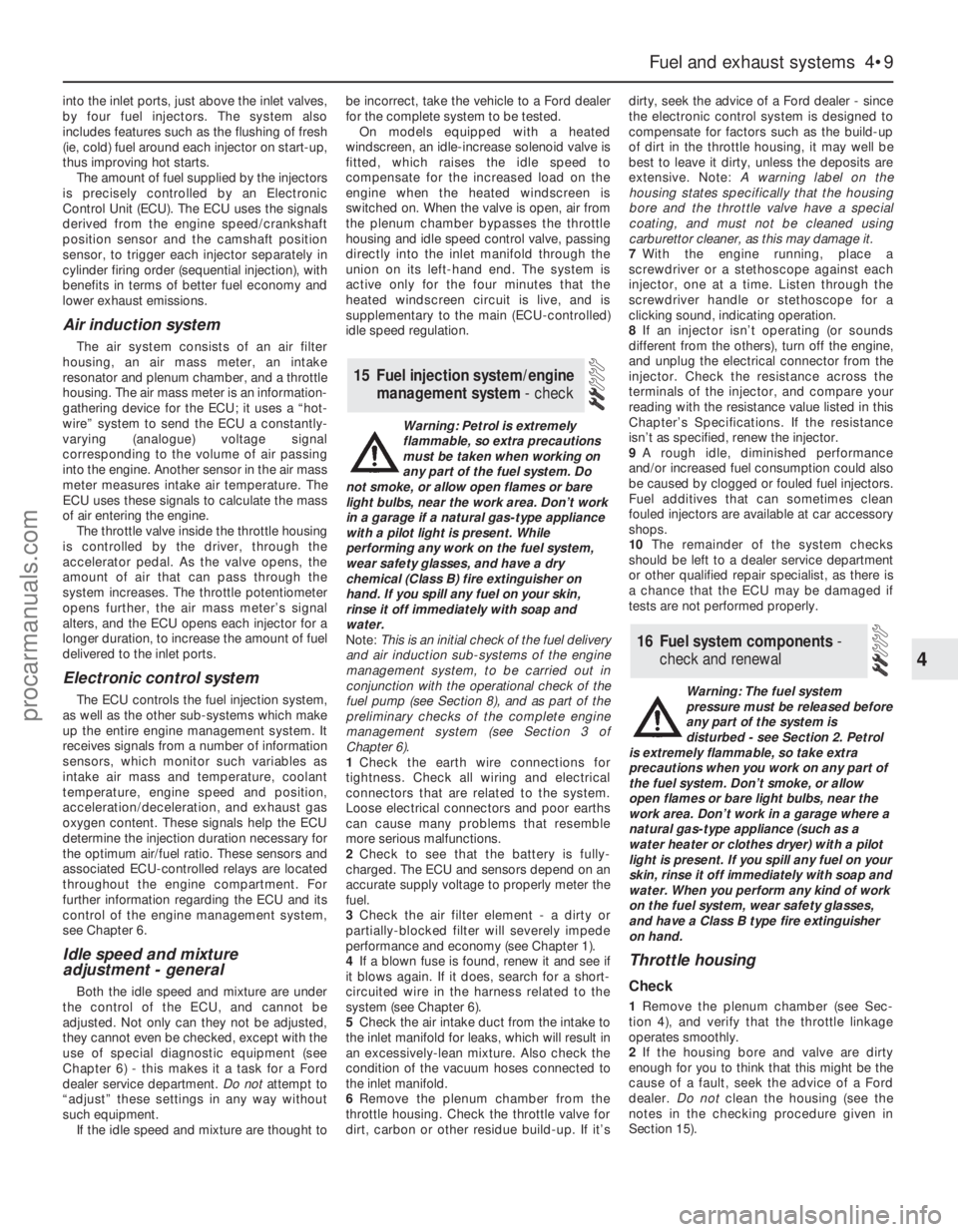
into the inlet ports, just above the inlet valves,
by four fuel injectors. The system also
includes features such as the flushing of fresh
(ie, cold) fuel around each injector on start-up,
thus improving hot starts.
The amount of fuel supplied by the injectors
is precisely controlled by an Electronic
Control Unit (ECU). The ECU uses the signals
derived from the engine speed/crankshaft
position sensor and the camshaft position
sensor, to trigger each injector separately in
cylinder firing order (sequential injection), with
benefits in terms of better fuel economy and
lower exhaust emissions.
Air induction system
The air system consists of an air filter
housing, an air mass meter, an intake
resonator and plenum chamber, and a throttle
housing. The air mass meter is an information-
gathering device for the ECU; it uses a “hot-
wire” system to send the ECU a constantly-
varying (analogue) voltage signal
corresponding to the volume of air passing
into the engine. Another sensor in the air mass
meter measures intake air temperature. The
ECU uses these signals to calculate the mass
of air entering the engine.
The throttle valve inside the throttle housing
is controlled by the driver, through the
accelerator pedal. As the valve opens, the
amount of air that can pass through the
system increases. The throttle potentiometer
opens further, the air mass meter’s signal
alters, and the ECU opens each injector for a
longer duration, to increase the amount of fuel
delivered to the inlet ports.
Electronic control system
The ECU controls the fuel injection system,
as well as the other sub-systems which make
up the entire engine management system. It
receives signals from a number of information
sensors, which monitor such variables as
intake air mass and temperature, coolant
temperature, engine speed and position,
acceleration/deceleration, and exhaust gas
oxygen content. These signals help the ECU
determine the injection duration necessary for
the optimum air/fuel ratio. These sensors and
associated ECU-controlled relays are located
throughout the engine compartment. For
further information regarding the ECU and its
control of the engine management system,
see Chapter 6.
Idle speed and mixture
adjustment - general
Both the idle speed and mixture are under
the control of the ECU, and cannot be
adjusted. Not only can they not be adjusted,
they cannot even be checked, except with the
use of special diagnostic equipment (see
Chapter 6) - this makes it a task for a Ford
dealer service department. Do notattempt to
“adjust” these settings in any way without
such equipment.
If the idle speed and mixture are thought tobe incorrect, take the vehicle to a Ford dealer
for the complete system to be tested.
On models equipped with a heated
windscreen, an idle-increase solenoid valve is
fitted, which raises the idle speed to
compensate for the increased load on the
engine when the heated windscreen is
switched on. When the valve is open, air from
the plenum chamber bypasses the throttle
housing and idle speed control valve, passing
directly into the inlet manifold through the
union on its left-hand end. The system is
active only for the four minutes that the
heated windscreen circuit is live, and is
supplementary to the main (ECU-controlled)
idle speed regulation.
Warning: Petrol is extremely
flammable, so extra precautions
must be taken when working on
any part of the fuel system. Do
not smoke, or allow open flames or bare
light bulbs, near the work area. Don’t work
in a garage if a natural gas-type appliance
with a pilot light is present. While
performing any work on the fuel system,
wear safety glasses, and have a dry
chemical (Class B) fire extinguisher on
hand. If you spill any fuel on your skin,
rinse it off immediately with soap and
water.
Note: This is an initial check of the fuel delivery
and air induction sub-systems of the engine
management system, to be carried out in
conjunction with the operational check of the
fuel pump (see Section 8), and as part of the
preliminary checks of the complete engine
management system (see Section 3 of
Chapter 6).
1Check the earth wire connections for
tightness. Check all wiring and electrical
connectors that are related to the system.
Loose electrical connectors and poor earths
can cause many problems that resemble
more serious malfunctions.
2Check to see that the battery is fully-
charged. The ECU and sensors depend on an
accurate supply voltage to properly meter the
fuel.
3Check the air filter element - a dirty or
partially-blocked filter will severely impede
performance and economy (see Chapter 1).
4If a blown fuse is found, renew it and see if
it blows again. If it does, search for a short-
circuited wire in the harness related to the
system (see Chapter 6).
5Check the air intake duct from the intake to
the inlet manifold for leaks, which will result in
an excessively-lean mixture. Also check the
condition of the vacuum hoses connected to
the inlet manifold.
6Remove the plenum chamber from the
throttle housing. Check the throttle valve for
dirt, carbon or other residue build-up. If it’sdirty, seek the advice of a Ford dealer - since
the electronic control system is designed to
compensate for factors such as the build-up
of dirt in the throttle housing, it may well be
best to leave it dirty, unless the deposits are
extensive. Note: A warning label on the
housing states specifically that the housing
bore and the throttle valve have a special
coating, and must not be cleaned using
carburettor cleaner, as this may damage it.
7With the engine running, place a
screwdriver or a stethoscope against each
injector, one at a time. Listen through the
screwdriver handle or stethoscope for a
clicking sound, indicating operation.
8If an injector isn’t operating (or sounds
different from the others), turn off the engine,
and unplug the electrical connector from the
injector. Check the resistance across the
terminals of the injector, and compare your
reading with the resistance value listed in this
Chapter’s Specifications. If the resistance
isn’t as specified, renew the injector.
9A rough idle, diminished performance
and/or increased fuel consumption could also
be caused by clogged or fouled fuel injectors.
Fuel additives that can sometimes clean
fouled injectors are available at car accessory
shops.
10The remainder of the system checks
should be left to a dealer service department
or other qualified repair specialist, as there is
a chance that the ECU may be damaged if
tests are not performed properly.
Warning: The fuel system
pressure must be released before
any part of the system is
disturbed - see Section 2. Petrol
is extremely flammable, so take extra
precautions when you work on any part of
the fuel system. Don’t smoke, or allow
open flames or bare light bulbs, near the
work area. Don’t work in a garage where a
natural gas-type appliance (such as a
water heater or clothes dryer) with a pilot
light is present. If you spill any fuel on your
skin, rinse it off immediately with soap and
water. When you perform any kind of work
on the fuel system, wear safety glasses,
and have a Class B type fire extinguisher
on hand.
Throttle housing
Check
1Remove the plenum chamber (see Sec-
tion 4), and verify that the throttle linkage
operates smoothly.
2If the housing bore and valve are dirty
enough for you to think that this might be the
cause of a fault, seek the advice of a Ford
dealer. Do notclean the housing (see the
notes in the checking procedure given in
Section 15).
16 Fuel system components-
check and renewal
15 Fuel injection system/engine
management system - check
Fuel and exhaust systems 4•9
4
procarmanuals.com
Page 108 of 279
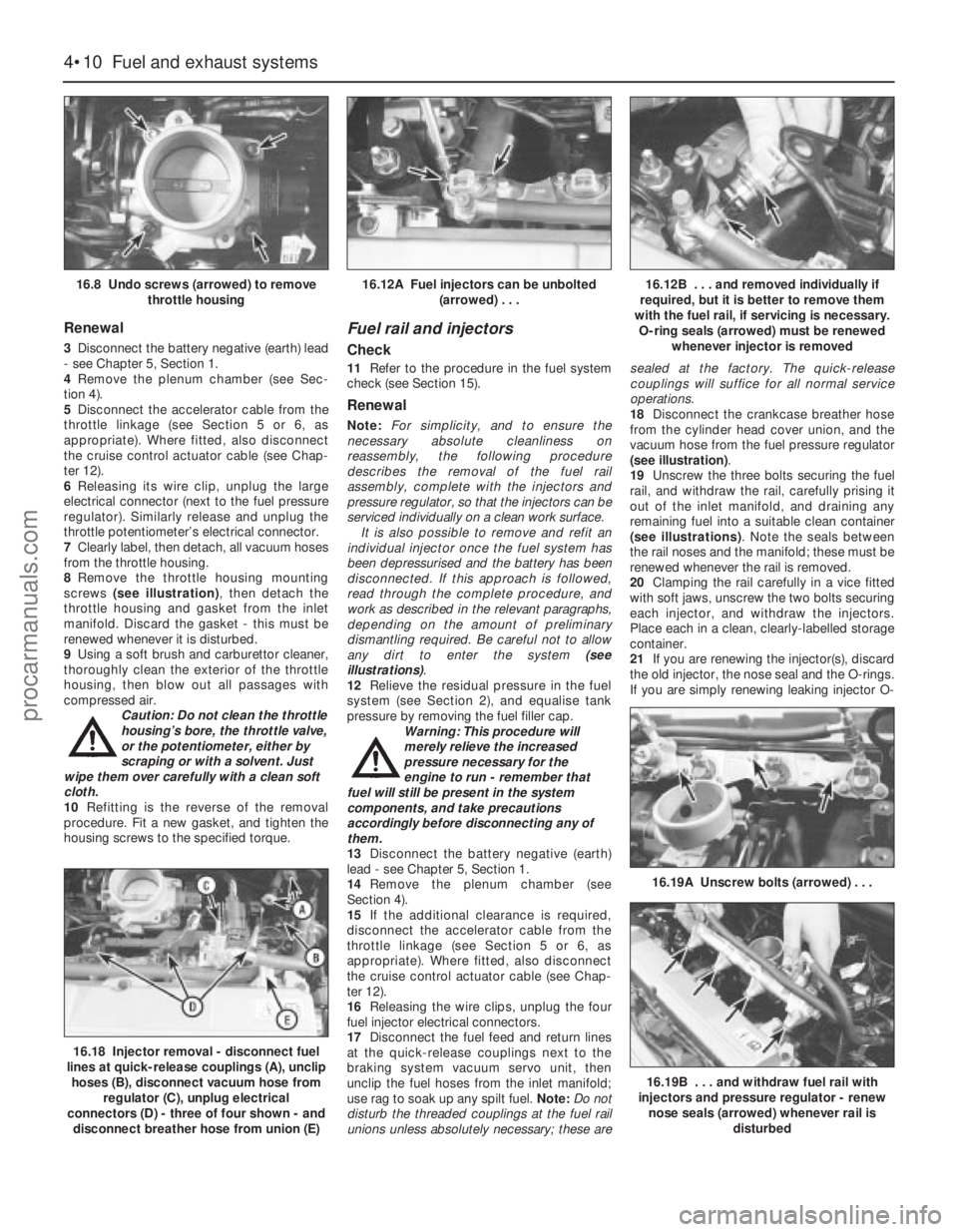
Renewal
3Disconnect the battery negative (earth) lead
- see Chapter 5, Section 1.
4Remove the plenum chamber (see Sec-
tion 4).
5Disconnect the accelerator cable from the
throttle linkage (see Section 5 or 6, as
appropriate). Where fitted, also disconnect
the cruise control actuator cable (see Chap-
ter 12).
6Releasing its wire clip, unplug the large
electrical connector (next to the fuel pressure
regulator). Similarly release and unplug the
throttle potentiometer’s electrical connector.
7Clearly label, then detach, all vacuum hoses
from the throttle housing.
8Remove the throttle housing mounting
screws (see illustration), then detach the
throttle housing and gasket from the inlet
manifold. Discard the gasket - this must be
renewed whenever it is disturbed.
9Using a soft brush and carburettor cleaner,
thoroughly clean the exterior of the throttle
housing, then blow out all passages with
compressed air.
Caution: Do not clean the throttle
housing’s bore, the throttle valve,
or the potentiometer, either by
scraping or with a solvent. Just
wipe them over carefully with a clean soft
cloth.
10Refitting is the reverse of the removal
procedure. Fit a new gasket, and tighten the
housing screws to the specified torque.
Fuel rail and injectors
Check
11Refer to the procedure in the fuel system
check (see Section 15).
Renewal
Note:For simplicity, and to ensure the
necessary absolute cleanliness on
reassembly, the following procedure
describes the removal of the fuel rail
assembly, complete with the injectors and
pressure regulator, so that the injectors can be
serviced individually on a clean work surface.
It is also possible to remove and refit an
individual injector once the fuel system has
been depressurised and the battery has been
disconnected. If this approach is followed,
read through the complete procedure, and
work as described in the relevant paragraphs,
depending on the amount of preliminary
dismantling required. Be careful not to allow
any dirt to enter the system (see
illustrations).
12Relieve the residual pressure in the fuel
system (see Section 2), and equalise tank
pressure by removing the fuel filler cap.
Warning: This procedure will
merely relieve the increased
pressure necessary for the
engine to run - remember that
fuel will still be present in the system
components, and take precautions
accordingly before disconnecting any of
them.
13Disconnect the battery negative (earth)
lead - see Chapter 5, Section 1.
14Remove the plenum chamber (see
Section 4).
15If the additional clearance is required,
disconnect the accelerator cable from the
throttle linkage (see Section 5 or 6, as
appropriate). Where fitted, also disconnect
the cruise control actuator cable (see Chap-
ter 12).
16Releasing the wire clips, unplug the four
fuel injector electrical connectors.
17Disconnect the fuel feed and return lines
at the quick-release couplings next to the
braking system vacuum servo unit, then
unclip the fuel hoses from the inlet manifold;
use rag to soak up any spilt fuel. Note:Do not
disturb the threaded couplings at the fuel rail
unions unless absolutely necessary; these aresealed at the factory. The quick-release
couplings will suffice for all normal service
operations.
18Disconnect the crankcase breather hose
from the cylinder head cover union, and the
vacuum hose from the fuel pressure regulator
(see illustration).
19Unscrew the three bolts securing the fuel
rail, and withdraw the rail, carefully prising it
out of the inlet manifold, and draining any
remaining fuel into a suitable clean container
(see illustrations). Note the seals between
the rail noses and the manifold; these must be
renewed whenever the rail is removed.
20Clamping the rail carefully in a vice fitted
with soft jaws, unscrew the two bolts securing
each injector, and withdraw the injectors.
Place each in a clean, clearly-labelled storage
container.
21If you are renewing the injector(s), discard
the old injector, the nose seal and the O-rings.
If you are simply renewing leaking injector O-
4•10 Fuel and exhaust systems
16.8 Undo screws (arrowed) to remove
throttle housing16.12A Fuel injectors can be unbolted
(arrowed) . . .16.12B . . . and removed individually if
required, but it is better to remove them
with the fuel rail, if servicing is necessary.
O-ring seals (arrowed) must be renewed
whenever injector is removed
16.18 Injector removal - disconnect fuel
lines at quick-release couplings (A), unclip
hoses (B), disconnect vacuum hose from
regulator (C), unplug electrical
connectors (D) - three of four shown - and
disconnect breather hose from union (E)
16.19A Unscrew bolts (arrowed) . . .
16.19B . . . and withdraw fuel rail with
injectors and pressure regulator - renew
nose seals (arrowed) whenever rail is
disturbed
procarmanuals.com
Page 109 of 279
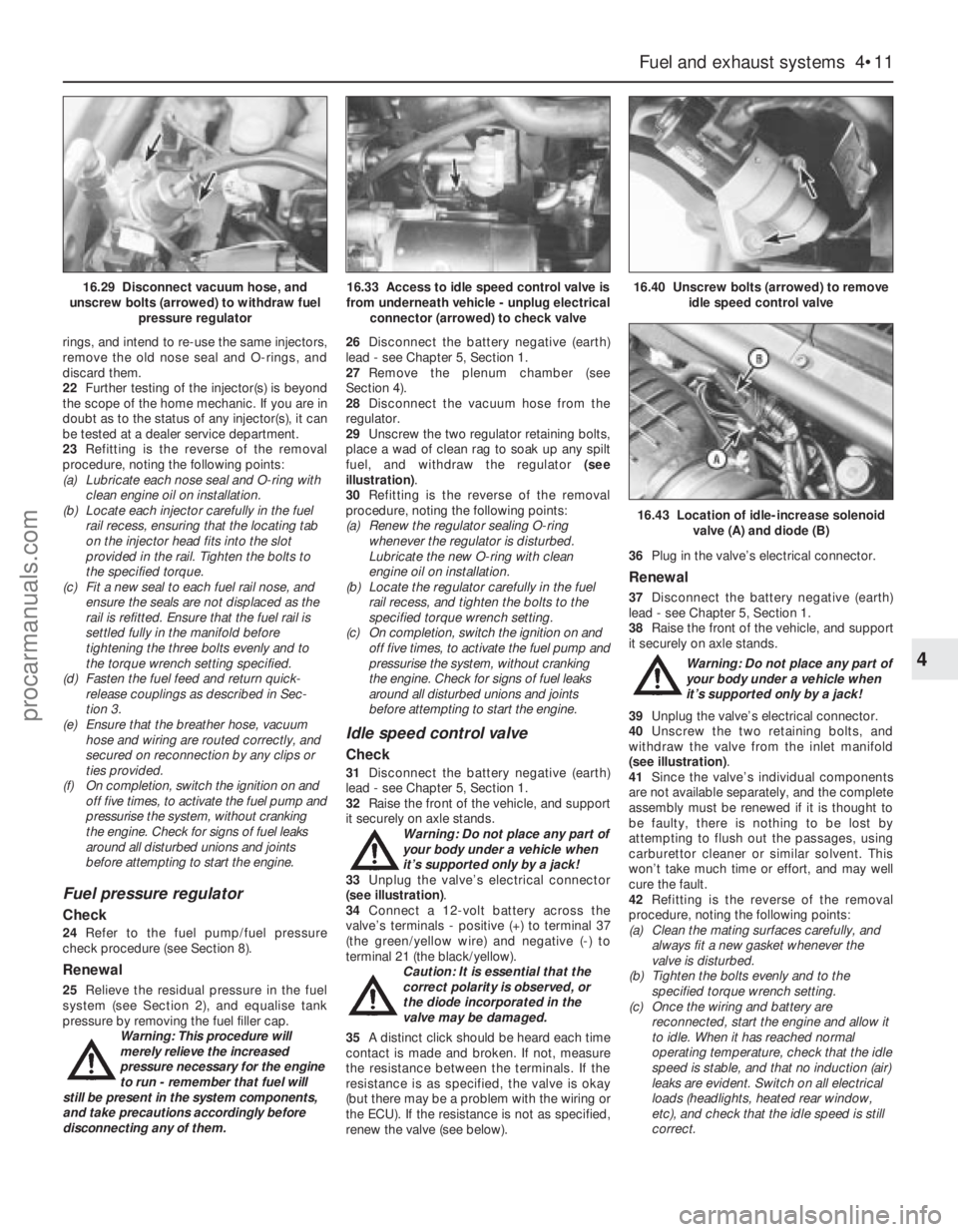
rings, and intend to re-use the same injectors,
remove the old nose seal and O-rings, and
discard them.
22Further testing of the injector(s) is beyond
the scope of the home mechanic. If you are in
doubt as to the status of any injector(s), it can
be tested at a dealer service department.
23Refitting is the reverse of the removal
procedure, noting the following points:
(a) Lubricate each nose seal and O-ring with
clean engine oil on installation.
(b) Locate each injector carefully in the fuel
rail recess, ensuring that the locating tab
on the injector head fits into the slot
provided in the rail. Tighten the bolts to
the specified torque.
(c) Fit a new seal to each fuel rail nose, and
ensure the seals are not displaced as the
rail is refitted. Ensure that the fuel rail is
settled fully in the manifold before
tightening the three bolts evenly and to
the torque wrench setting specified.
(d) Fasten the fuel feed and return quick-
release couplings as described in Sec-
tion 3.
(e) Ensure that the breather hose, vacuum
hose and wiring are routed correctly, and
secured on reconnection by any clips or
ties provided.
(f) On completion, switch the ignition on and
off five times, to activate the fuel pump and
pressurise the system, without cranking
the engine. Check for signs of fuel leaks
around all disturbed unions and joints
before attempting to start the engine.
Fuel pressure regulator
Check
24Refer to the fuel pump/fuel pressure
check procedure (see Section 8).
Renewal
25Relieve the residual pressure in the fuel
system (see Section 2), and equalise tank
pressure by removing the fuel filler cap.
Warning: This procedure will
merely relieve the increased
pressure necessary for the engine
to run - remember that fuel will
still be present in the system components,
and take precautions accordingly before
disconnecting any of them.26Disconnect the battery negative (earth)
lead - see Chapter 5, Section 1.
27Remove the plenum chamber (see
Section 4).
28Disconnect the vacuum hose from the
regulator.
29Unscrew the two regulator retaining bolts,
place a wad of clean rag to soak up any spilt
fuel, and withdraw the regulator (see
illustration).
30Refitting is the reverse of the removal
procedure, noting the following points:
(a) Renew the regulator sealing O-ring
whenever the regulator is disturbed.
Lubricate the new O-ring with clean
engine oil on installation.
(b) Locate the regulator carefully in the fuel
rail recess, and tighten the bolts to the
specified torque wrench setting.
(c) On completion, switch the ignition on and
off five times, to activate the fuel pump and
pressurise the system, without cranking
the engine. Check for signs of fuel leaks
around all disturbed unions and joints
before attempting to start the engine.
Idle speed control valve
Check
31Disconnect the battery negative (earth)
lead - see Chapter 5, Section 1.
32Raise the front of the vehicle, and support
it securely on axle stands.
Warning: Do not place any part of
your body under a vehicle when
it’s supported only by a jack!
33Unplug the valve’s electrical connector
(see illustration).
34Connect a 12-volt battery across the
valve’s terminals - positive (+) to terminal 37
(the green/yellow wire) and negative (-) to
terminal 21 (the black/yellow).
Caution: It is essential that the
correct polarity is observed, or
the diode incorporated in the
valve may be damaged.
35A distinct click should be heard each time
contact is made and broken. If not, measure
the resistance between the terminals. If the
resistance is as specified, the valve is okay
(but there may be a problem with the wiring or
the ECU). If the resistance is not as specified,
renew the valve (see below).36Plug in the valve’s electrical connector.
Renewal
37Disconnect the battery negative (earth)
lead - see Chapter 5, Section 1.
38Raise the front of the vehicle, and support
it securely on axle stands.
Warning: Do not place any part of
your body under a vehicle when
it’s supported only by a jack!
39Unplug the valve’s electrical connector.
40Unscrew the two retaining bolts, and
withdraw the valve from the inlet manifold
(see illustration).
41Since the valve’s individual components
are not available separately, and the complete
assembly must be renewed if it is thought to
be faulty, there is nothing to be lost by
attempting to flush out the passages, using
carburettor cleaner or similar solvent. This
won’t take much time or effort, and may well
cure the fault.
42Refitting is the reverse of the removal
procedure, noting the following points:
(a) Clean the mating surfaces carefully, and
always fit a new gasket whenever the
valve is disturbed.
(b) Tighten the bolts evenly and to the
specified torque wrench setting.
(c) Once the wiring and battery are
reconnected, start the engine and allow it
to idle. When it has reached normal
operating temperature, check that the idle
speed is stable, and that no induction (air)
leaks are evident. Switch on all electrical
loads (headlights, heated rear window,
etc), and check that the idle speed is still
correct.
Fuel and exhaust systems 4•11
4
16.43 Location of idle-increase solenoid
valve (A) and diode (B)
16.29 Disconnect vacuum hose, and
unscrew bolts (arrowed) to withdraw fuel
pressure regulator16.33 Access to idle speed control valve is
from underneath vehicle - unplug electrical
connector (arrowed) to check valve16.40 Unscrew bolts (arrowed) to remove
idle speed control valve
procarmanuals.com
Page 110 of 279
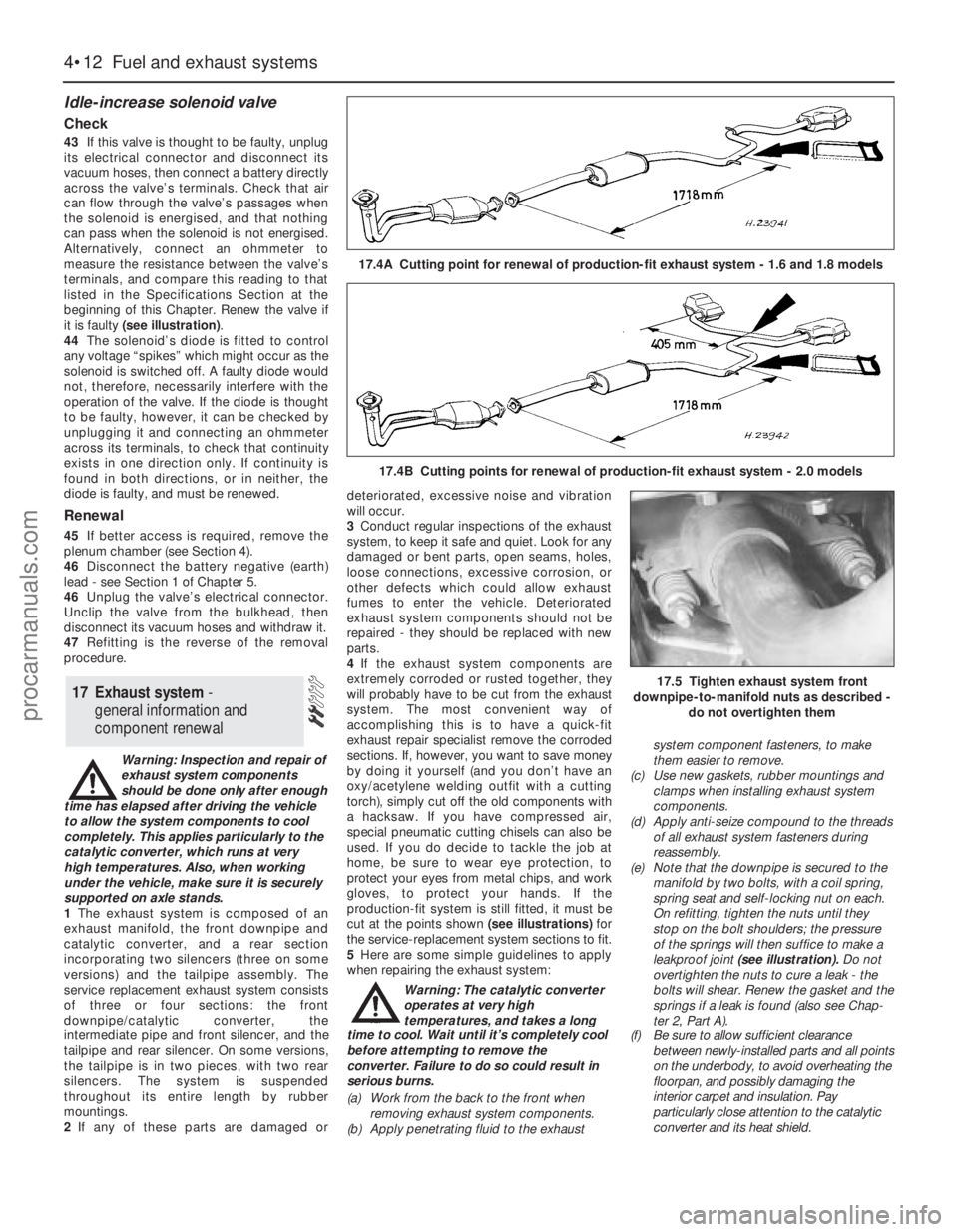
Idle-increase solenoid valve
Check
43If this valve is thought to be faulty, unplug
its electrical connector and disconnect its
vacuum hoses, then connect a battery directly
across the valve’s terminals. Check that air
can flow through the valve’s passages when
the solenoid is energised, and that nothing
can pass when the solenoid is not energised.
Alternatively, connect an ohmmeter to
measure the resistance between the valve’s
terminals, and compare this reading to that
listed in the Specifications Section at the
beginning of this Chapter. Renew the valve if
it is faulty (see illustration).
44The solenoid’s diode is fitted to control
any voltage “spikes” which might occur as the
solenoid is switched off. A faulty diode would
not, therefore, necessarily interfere with the
operation of the valve. If the diode is thought
to be faulty, however, it can be checked by
unplugging it and connecting an ohmmeter
across its terminals, to check that continuity
exists in one direction only. If continuity is
found in both directions, or in neither, the
diode is faulty, and must be renewed.
Renewal
45If better access is required, remove the
plenum chamber (see Section 4).
46Disconnect the battery negative (earth)
lead - see Section 1 of Chapter 5.
46Unplug the valve’s electrical connector.
Unclip the valve from the bulkhead, then
disconnect its vacuum hoses and withdraw it.
47Refitting is the reverse of the removal
procedure.
Warning: Inspection and repair of
exhaust system components
should be done only after enough
time has elapsed after driving the vehicle
to allow the system components to cool
completely. This applies particularly to the
catalytic converter, which runs at very
high temperatures. Also, when working
under the vehicle, make sure it is securely
supported on axle stands.
1The exhaust system is composed of an
exhaust manifold, the front downpipe and
catalytic converter, and a rear section
incorporating two silencers (three on some
versions) and the tailpipe assembly. The
service replacement exhaust system consists
of three or four sections: the front
downpipe/catalytic converter, the
intermediate pipe and front silencer, and the
tailpipe and rear silencer. On some versions,
the tailpipe is in two pieces, with two rear
silencers. The system is suspended
throughout its entire length by rubber
mountings.
2If any of these parts are damaged ordeteriorated, excessive noise and vibration
will occur.
3Conduct regular inspections of the exhaust
system, to keep it safe and quiet. Look for any
damaged or bent parts, open seams, holes,
loose connections, excessive corrosion, or
other defects which could allow exhaust
fumes to enter the vehicle. Deteriorated
exhaust system components should not be
repaired - they should be replaced with new
parts.
4If the exhaust system components are
extremely corroded or rusted together, they
will probably have to be cut from the exhaust
system. The most convenient way of
accomplishing this is to have a quick-fit
exhaust repair specialist remove the corroded
sections. If, however, you want to save money
by doing it yourself (and you don’t have an
oxy/acetylene welding outfit with a cutting
torch), simply cut off the old components with
a hacksaw. If you have compressed air,
special pneumatic cutting chisels can also be
used. If you do decide to tackle the job at
home, be sure to wear eye protection, to
protect your eyes from metal chips, and work
gloves, to protect your hands. If the
production-fit system is still fitted, it must be
cut at the points shown (see illustrations) for
the service-replacement system sections to fit.
5Here are some simple guidelines to apply
when repairing the exhaust system:
Warning: The catalytic converter
operates at very high
temperatures, and takes a long
time to cool. Wait until it’s completely cool
before attempting to remove the
converter. Failure to do so could result in
serious burns.
(a) Work from the back to the front when
removing exhaust system components.
(b) Apply penetrating fluid to the exhaustsystem component fasteners, to make
them easier to remove.
(c) Use new gaskets, rubber mountings and
clamps when installing exhaust system
components.
(d) Apply anti-seize compound to the threads
of all exhaust system fasteners during
reassembly.
(e) Note that the downpipe is secured to the
manifold by two bolts, with a coil spring,
spring seat and self-locking nut on each.
On refitting, tighten the nuts until they
stop on the bolt shoulders; the pressure
of the springs will then suffice to make a
leakproof joint (see illustration). Do not
overtighten the nuts to cure a leak - the
bolts will shear. Renew the gasket and the
springs if a leak is found (also see Chap-
ter 2, Part A).
(f) Be sure to allow sufficient clearance
between newly-installed parts and all points
on the underbody, to avoid overheating the
floorpan, and possibly damaging the
interior carpet and insulation. Pay
particularly close attention to the catalytic
converter and its heat shield.
17 Exhaust system -
general information and
component renewal
4•12 Fuel and exhaust systems
17.4A Cutting point for renewal of production-fit exhaust system - 1.6 and 1.8 models
17.4B Cutting points for renewal of production-fit exhaust system - 2.0 models
17.5 Tighten exhaust system front
downpipe-to-manifold nuts as described -
do not overtighten them
procarmanuals.com