boot FORD SIERRA 1983 1.G Braking System Workshop Manual
[x] Cancel search | Manufacturer: FORD, Model Year: 1983, Model line: SIERRA, Model: FORD SIERRA 1983 1.GPages: 22, PDF Size: 1.11 MB
Page 7 of 22
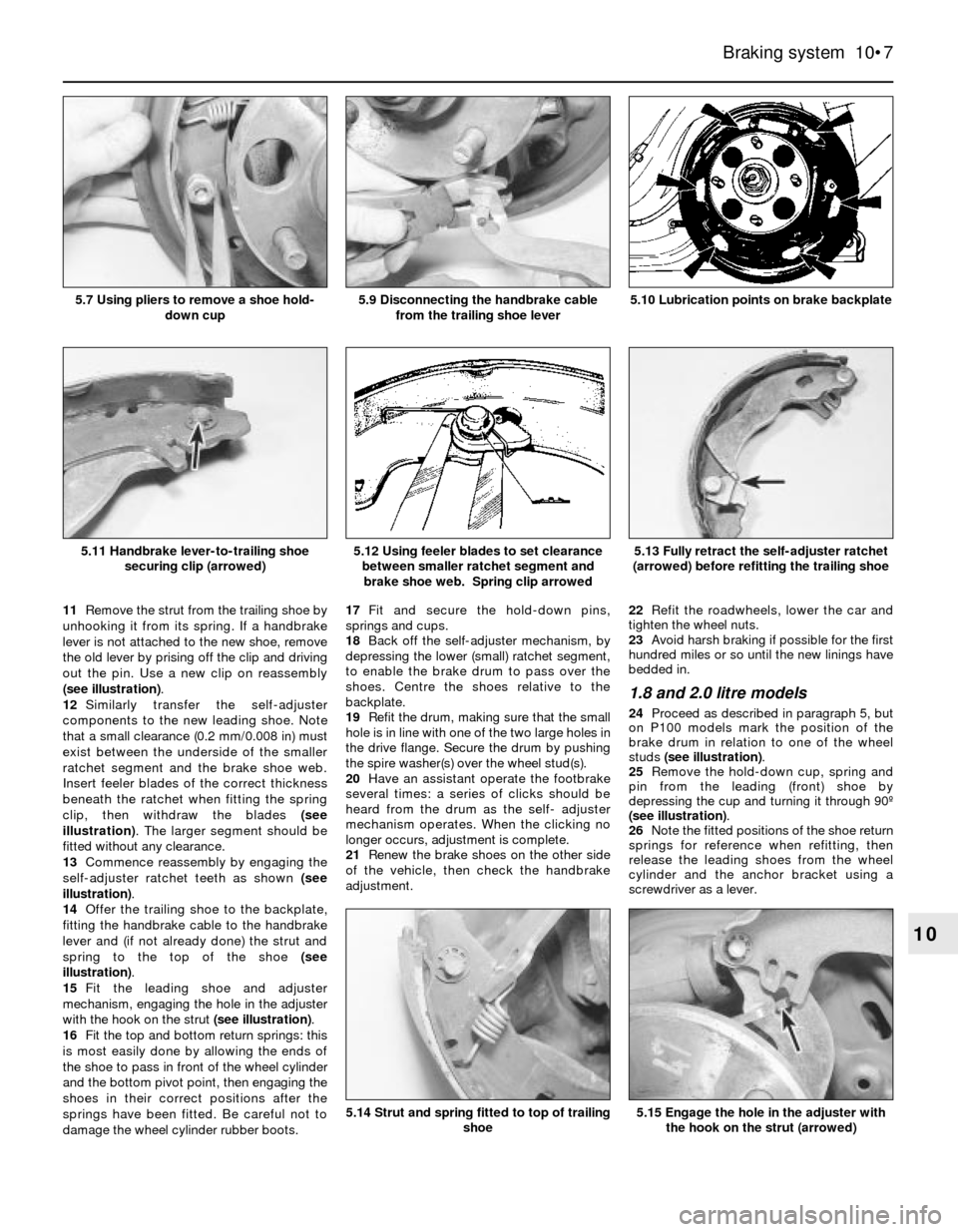
11Remove the strut from the trailing shoe by
unhooking it from its spring. If a handbrake
lever is not attached to the new shoe, remove
the old lever by prising off the clip and driving
out the pin. Use a new clip on reassembly
(see illustration).
12Similarly transfer the self-adjuster
components to the new leading shoe. Note
that a small clearance (0.2 mm/0.008 in) must
exist between the underside of the smaller
ratchet segment and the brake shoe web.
Insert feeler blades of the correct thickness
beneath the ratchet when fitting the spring
clip, then withdraw the blades (see
illustration). The larger segment should be
fitted without any clearance.
13Commence reassembly by engaging the
self-adjuster ratchet teeth as shown (see
illustration).
14Offer the trailing shoe to the backplate,
fitting the handbrake cable to the handbrake
lever and (if not already done) the strut and
spring to the top of the shoe (see
illustration).
15Fit the leading shoe and adjuster
mechanism, engaging the hole in the adjuster
with the hook on the strut (see illustration).
16Fit the top and bottom return springs: this
is most easily done by allowing the ends of
the shoe to pass in front of the wheel cylinder
and the bottom pivot point, then engaging the
shoes in their correct positions after the
springs have been fitted. Be careful not to
damage the wheel cylinder rubber boots.17Fit and secure the hold-down pins,
springs and cups.
18Back off the self-adjuster mechanism, by
depressing the lower (small) ratchet segment,
to enable the brake drum to pass over the
shoes. Centre the shoes relative to the
backplate.
19Refit the drum, making sure that the small
hole is in line with one of the two large holes in
the drive flange. Secure the drum by pushing
the spire washer(s) over the wheel stud(s).
20Have an assistant operate the footbrake
several times: a series of clicks should be
heard from the drum as the self-adjuster
mechanism operates. When the clicking no
longer occurs, adjustment is complete.
21Renew the brake shoes on the other side
of the vehicle, then check the handbrake
adjustment.22Refit the roadwheels, lower the car and
tighten the wheel nuts.
23Avoid harsh braking if possible for the first
hundred miles or so until the new linings have
bedded in.
1.8 and 2.0 litre models
24Proceed as described in paragraph 5, but
on P100 models mark the position of the
brake drum in relation to one of the wheel
studs (see illustration).
25Remove the hold-down cup, spring and
pin from the leading (front) shoe by
depressing the cup and turning it through 90º
(see illustration).
26Note the fitted positions of the shoe return
springs for reference when refitting, then
release the leading shoes from the wheel
cylinder and the anchor bracket using a
screwdriver as a lever.
Braking system 10•7
10
5.10 Lubrication points on brake backplate
5.15 Engage the hole in the adjuster with
the hook on the strut (arrowed)5.14 Strut and spring fitted to top of trailing
shoe
5.13 Fully retract the self-adjuster ratchet
(arrowed) before refitting the trailing shoe5.12 Using feeler blades to set clearance
between smaller ratchet segment and
brake shoe web. Spring clip arrowed5.11 Handbrake lever-to-trailing shoe
securing clip (arrowed)
5.9 Disconnecting the handbrake cable
from the trailing shoe lever5.7 Using pliers to remove a shoe hold-
down cup
Page 8 of 22
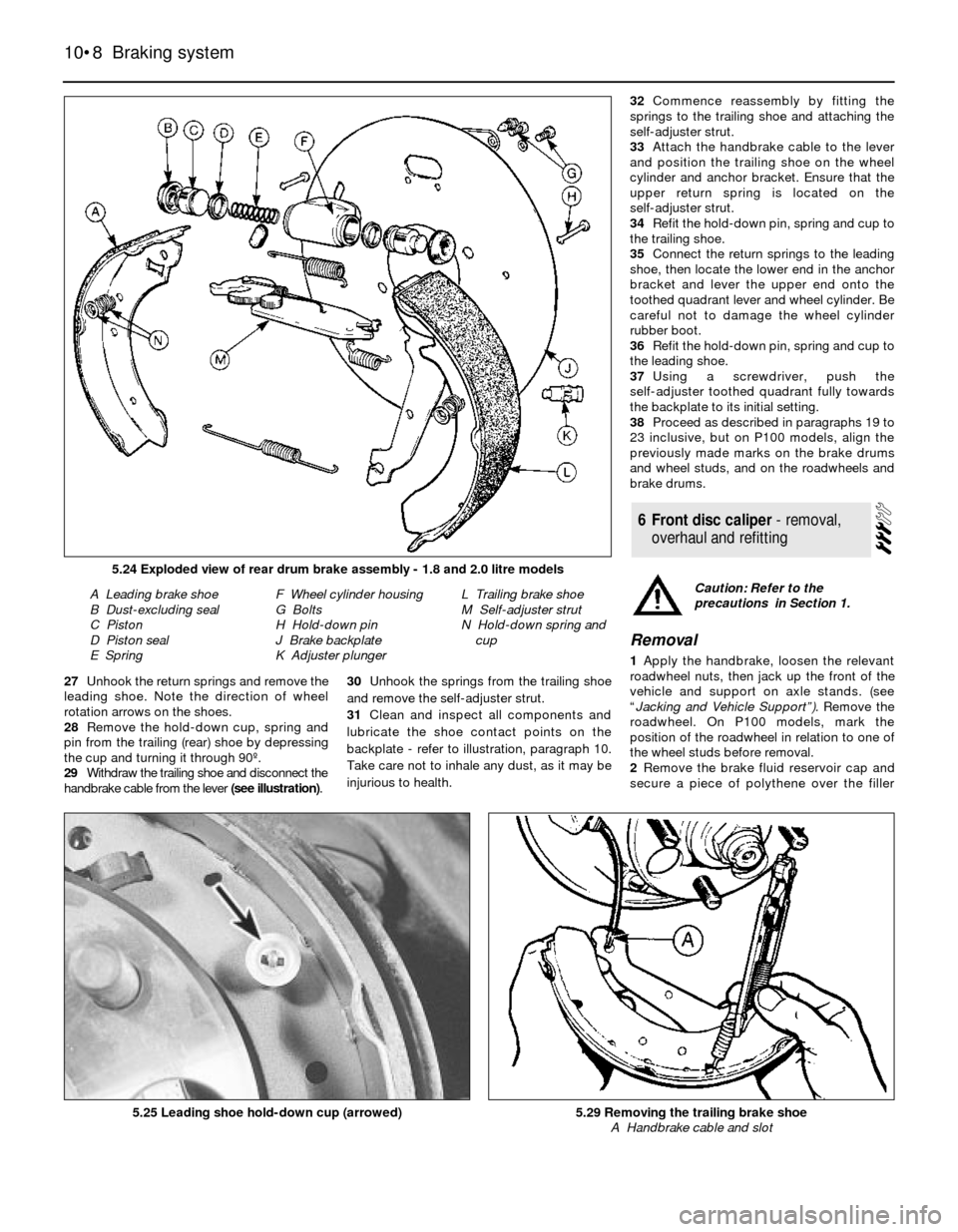
27Unhook the return springs and remove the
leading shoe. Note the direction of wheel
rotation arrows on the shoes.
28Remove the hold-down cup, spring and
pin from the trailing (rear) shoe by depressing
the cup and turning it through 90º.
29Withdraw the trailing shoe and disconnect the
handbrake cable from the lever (see illustration).30Unhook the springs from the trailing shoe
and remove the self-adjuster strut.
31Clean and inspect all components and
lubricate the shoe contact points on the
backplate - refer to illustration, paragraph 10.
Take care not to inhale any dust, as it may be
injurious to health.32Commence reassembly by fitting the
springs to the trailing shoe and attaching the
self-adjuster strut.
33Attach the handbrake cable to the lever
and position the trailing shoe on the wheel
cylinder and anchor bracket. Ensure that the
upper return spring is located on the
self-adjuster strut.
34Refit the hold-down pin, spring and cup to
the trailing shoe.
35Connect the return springs to the leading
shoe, then locate the lower end in the anchor
bracket and lever the upper end onto the
toothed quadrant lever and wheel cylinder. Be
careful not to damage the wheel cylinder
rubber boot.
36Refit the hold-down pin, spring and cup to
the leading shoe.
37Using a screwdriver, push the
self-adjuster toothed quadrant fully towards
the backplate to its initial setting.
38Proceed as described in paragraphs 19 to
23 inclusive, but on P100 models, align the
previously made marks on the brake drums
and wheel studs, and on the roadwheels and
brake drums.
Removal
1Apply the handbrake, loosen the relevant
roadwheel nuts, then jack up the front of the
vehicle and support on axle stands. (see
“Jacking and Vehicle Support”). Remove the
roadwheel. On P100 models, mark the
position of the roadwheel in relation to one of
the wheel studs before removal.
2Remove the brake fluid reservoir cap and
secure a piece of polythene over the filler
6Front disc caliper - removal,
overhaul and refitting
10•8Braking system
5.24 Exploded view of rear drum brake assembly - 1.8 and 2.0 litre models
A Leading brake shoe
B Dust-excluding seal
C Piston
D Piston seal
E SpringF Wheel cylinder housing
G Bolts
H Hold-down pin
J Brake backplate
K Adjuster plungerL Trailing brake shoe
M Self-adjuster strut
N Hold-down spring and
cup
5.25 Leading shoe hold-down cup (arrowed)5.29 Removing the trailing brake shoe
A Handbrake cable and slot
Caution: Refer to the
precautions in Section 1.
Page 9 of 22
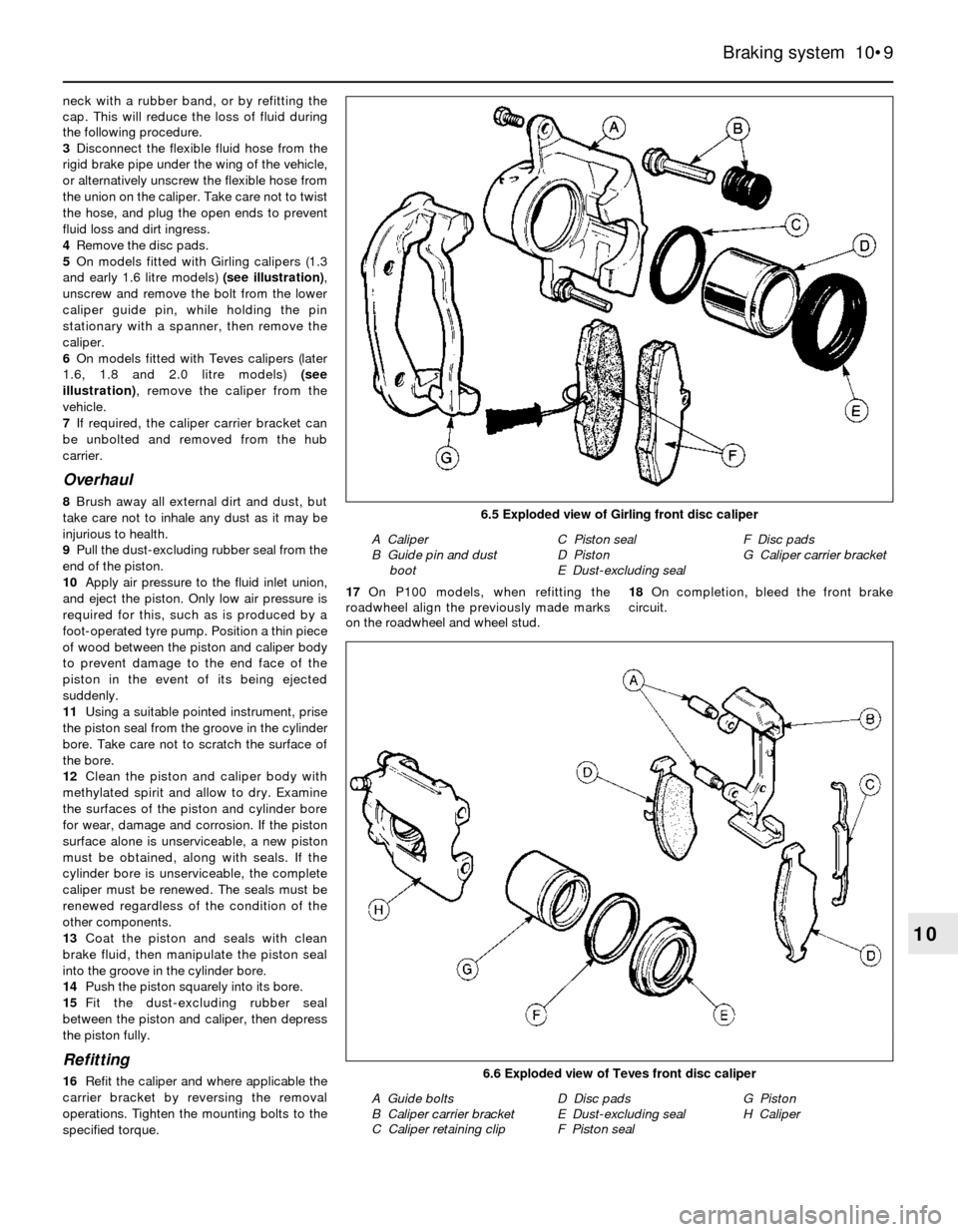
neck with a rubber band, or by refitting the
cap. This will reduce the loss of fluid during
the following procedure.
3Disconnect the flexible fluid hose from the
rigid brake pipe under the wing of the vehicle,
or alternatively unscrew the flexible hose from
the union on the caliper. Take care not to twist
the hose, and plug the open ends to prevent
fluid loss and dirt ingress.
4Remove the disc pads.
5On models fitted with Girling calipers (1.3
and early 1.6 litre models) (see illustration),
unscrew and remove the bolt from the lower
caliper guide pin, while holding the pin
stationary with a spanner, then remove the
caliper.
6On models fitted with Teves calipers (later
1.6, 1.8 and 2.0 litre models) (see
illustration), remove the caliper from the
vehicle.
7If required, the caliper carrier bracket can
be unbolted and removed from the hub
carrier.
Overhaul
8Brush away all external dirt and dust, but
take care not to inhale any dust as it may be
injurious to health.
9Pull the dust-excluding rubber seal from the
end of the piston.
10Apply air pressure to the fluid inlet union,
and eject the piston. Only low air pressure is
required for this, such as is produced by a
foot-operated tyre pump. Position a thin piece
of wood between the piston and caliper body
to prevent damage to the end face of the
piston in the event of its being ejected
suddenly.
11Using a suitable pointed instrument, prise
the piston seal from the groove in the cylinder
bore. Take care not to scratch the surface of
the bore.
12Clean the piston and caliper body with
methylated spirit and allow to dry. Examine
the surfaces of the piston and cylinder bore
for wear, damage and corrosion. If the piston
surface alone is unserviceable, a new piston
must be obtained, along with seals. If the
cylinder bore is unserviceable, the complete
caliper must be renewed. The seals must be
renewed regardless of the condition of the
other components.
13Coat the piston and seals with clean
brake fluid, then manipulate the piston seal
into the groove in the cylinder bore.
14Push the piston squarely into its bore.
15Fit the dust-excluding rubber seal
between the piston and caliper, then depress
the piston fully.
Refitting
16Refit the caliper and where applicable the
carrier bracket by reversing the removal
operations. Tighten the mounting bolts to the
specified torque.17On P100 models, when refitting the
roadwheel align the previously made marks
on the roadwheel and wheel stud.18On completion, bleed the front brake
circuit.
Braking system 10•9
10
6.6 Exploded view of Teves front disc caliper
A Guide bolts
B Caliper carrier bracket
C Caliper retaining clipD Disc pads
E Dust-excluding seal
F Piston sealG Piston
H Caliper
6.5 Exploded view of Girling front disc caliper
A Caliper
B Guide pin and dust
bootC Piston seal
D Piston
E Dust-excluding sealF Disc pads
G Caliper carrier bracket
Page 15 of 22
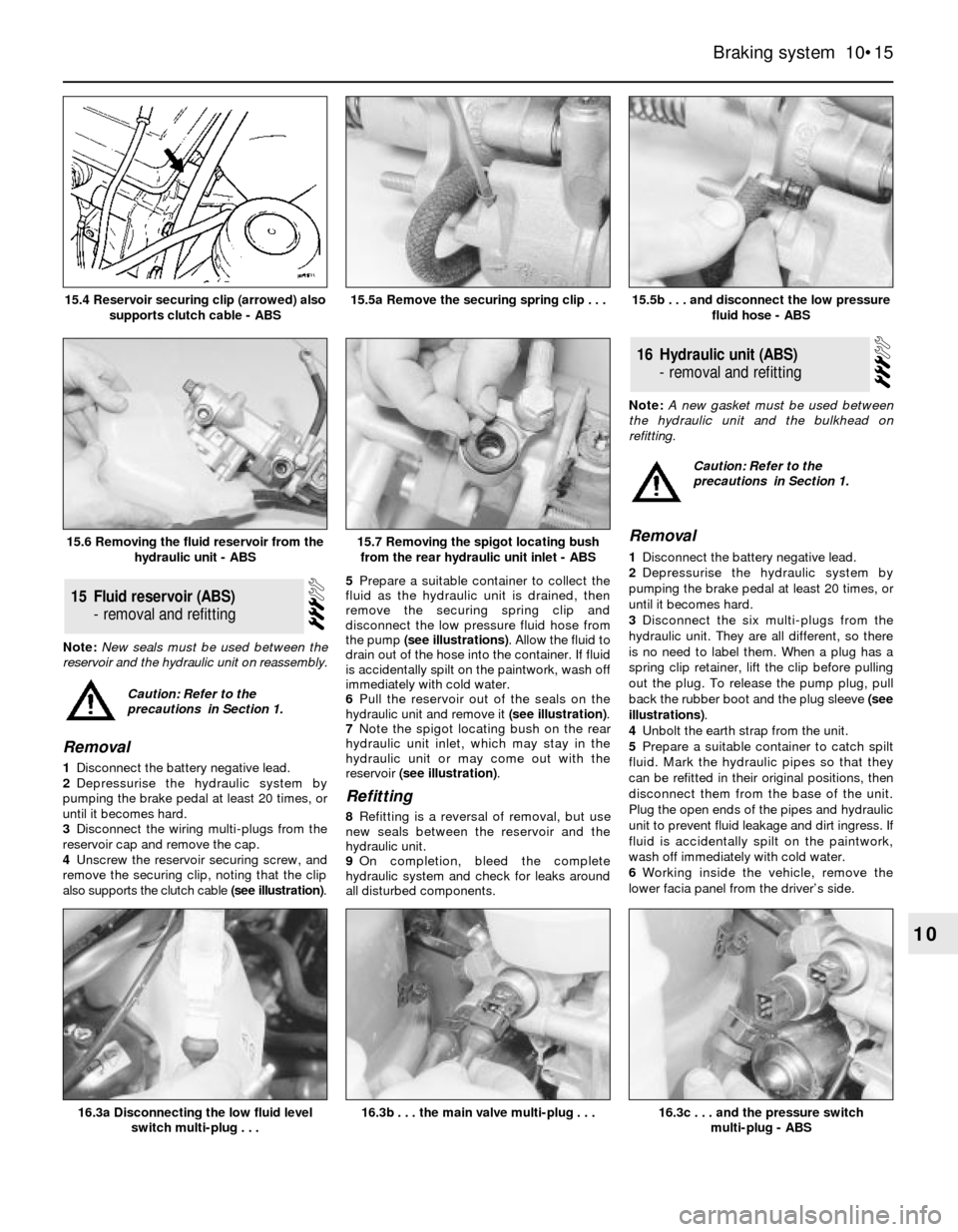
Note: New seals must be used between the
reservoir and the hydraulic unit on reassembly.
Removal
1Disconnect the battery negative lead.
2Depressurise the hydraulic system by
pumping the brake pedal at least 20 times, or
until it becomes hard.
3Disconnect the wiring multi-plugs from the
reservoir cap and remove the cap.
4Unscrew the reservoir securing screw, and
remove the securing clip, noting that the clip
also supports the clutch cable (see illustration).5Prepare a suitable container to collect the
fluid as the hydraulic unit is drained, then
remove the securing spring clip and
disconnect the low pressure fluid hose from
the pump (see illustrations). Allow the fluid to
drain out of the hose into the container. If fluid
is accidentally spilt on the paintwork, wash off
immediately with cold water.
6Pull the reservoir out of the seals on the
hydraulic unit and remove it (see illustration).
7Note the spigot locating bush on the rear
hydraulic unit inlet, which may stay in the
hydraulic unit or may come out with the
reservoir (see illustration).
Refitting
8Refitting is a reversal of removal, but use
new seals between the reservoir and the
hydraulic unit.
9On completion, bleed the complete
hydraulic system and check for leaks around
all disturbed components.Note: A new gasket must be used between
the hydraulic unit and the bulkhead on
refitting.
Removal
1Disconnect the battery negative lead.
2Depressurise the hydraulic system by
pumping the brake pedal at least 20 times, or
until it becomes hard.
3Disconnect the six multi-plugs from the
hydraulic unit. They are all different, so there
is no need to label them. When a plug has a
spring clip retainer, lift the clip before pulling
out the plug. To release the pump plug, pull
back the rubber boot and the plug sleeve (see
illustrations).
4Unbolt the earth strap from the unit.
5Prepare a suitable container to catch spilt
fluid. Mark the hydraulic pipes so that they
can be refitted in their original positions, then
disconnect them from the base of the unit.
Plug the open ends of the pipes and hydraulic
unit to prevent fluid leakage and dirt ingress. If
fluid is accidentally spilt on the paintwork,
wash off immediately with cold water.
6Working inside the vehicle, remove the
lower facia panel from the driver’s side.
16Hydraulic unit (ABS)
- removal and refitting
15Fluid reservoir (ABS)
- removal and refitting
Braking system 10•15
10
15.5b . . . and disconnect the low pressure
fluid hose - ABS
16.3c . . . and the pressure switch
multi-plug - ABS16.3b . . . the main valve multi-plug . . .16.3a Disconnecting the low fluid level
switch multi-plug . . .
15.7 Removing the spigot locating bush
from the rear hydraulic unit inlet - ABS15.6 Removing the fluid reservoir from the
hydraulic unit - ABS
15.5a Remove the securing spring clip . . .15.4 Reservoir securing clip (arrowed) also
supports clutch cable - ABS
Caution: Refer to the
precautions in Section 1.
Caution: Refer to the
precautions in Section 1.