FORD SIERRA 1983 1.G DOHC Engine User Guide
Manufacturer: FORD, Model Year: 1983, Model line: SIERRA, Model: FORD SIERRA 1983 1.GPages: 18, PDF Size: 0.9 MB
Page 11 of 18
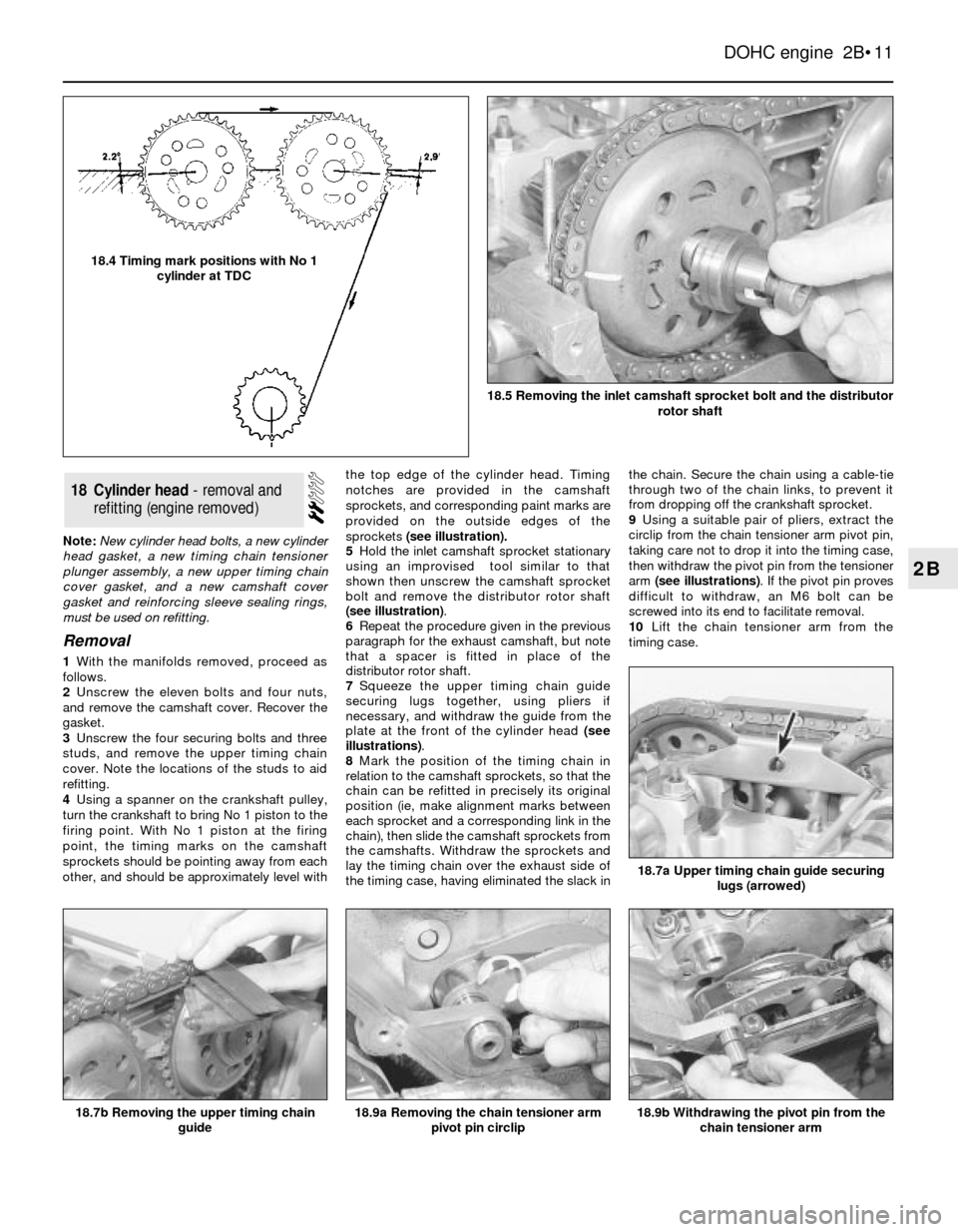
Note: New cylinder head bolts, a new cylinder
head gasket, a new timing chain tensioner
plunger assembly, a new upper timing chain
cover gasket, and a new camshaft cover
gasket and reinforcing sleeve sealing rings,
must be used on refitting.
Removal
1With the manifolds removed, proceed as
follows.
2Unscrew the eleven bolts and four nuts,
and remove the camshaft cover. Recover the
gasket.
3Unscrew the four securing bolts and three
studs, and remove the upper timing chain
cover. Note the locations of the studs to aid
refitting.
4Using a spanner on the crankshaft pulley,
turn the crankshaft to bring No 1 piston to the
firing point. With No 1 piston at the firing
point, the timing marks on the camshaft
sprockets should be pointing away from each
other, and should be approximately level withthe top edge of the cylinder head. Timing
notches are provided in the camshaft
sprockets, and corresponding paint marks are
provided on the outside edges of the
sprockets (see illustration).
5Hold the inlet camshaft sprocket stationary
using an improvised tool similar to that
shownthen unscrew the camshaft sprocket
bolt and remove the distributor rotor shaft
(see illustration).
6Repeat the procedure given in the previous
paragraph for the exhaust camshaft, but note
that a spacer is fitted in place of the
distributor rotor shaft.
7Squeeze the upper timing chain guide
securing lugs together, using pliers if
necessary, and withdraw the guide from the
plate at the front of the cylinder head (see
illustrations).
8Mark the position of the timing chain in
relation to the camshaft sprockets, so that the
chain can be refitted in precisely its original
position (ie, make alignment marks between
each sprocket and a corresponding link in the
chain), then slide the camshaft sprockets from
the camshafts. Withdraw the sprockets and
lay the timing chain over the exhaust side of
the timing case, having eliminated the slack inthe chain. Secure the chain using a cable-tie
through two of the chain links, to prevent it
from dropping off the crankshaft sprocket.
9Using a suitable pair of pliers, extract the
circlip from the chain tensioner arm pivot pin,
taking care not to drop it into the timing case,
then withdraw the pivot pin from the tensioner
arm (see illustrations). If the pivot pin proves
difficult to withdraw, an M6 bolt can be
screwed into its end to facilitate removal.
10Lift the chain tensioner arm from the
timing case.
18Cylinder head - removal and
refitting (engine removed)
DOHC engine 2B•11
2B
18.7a Upper timing chain guide securing
lugs (arrowed)
18.9b Withdrawing the pivot pin from the
chain tensioner arm18.9a Removing the chain tensioner arm
pivot pin circlip18.7b Removing the upper timing chain
guide
18.5 Removing the inlet camshaft sprocket bolt and the distributor
rotor shaft
18.4 Timing mark positions with No 1
cylinder at TDC
Page 12 of 18
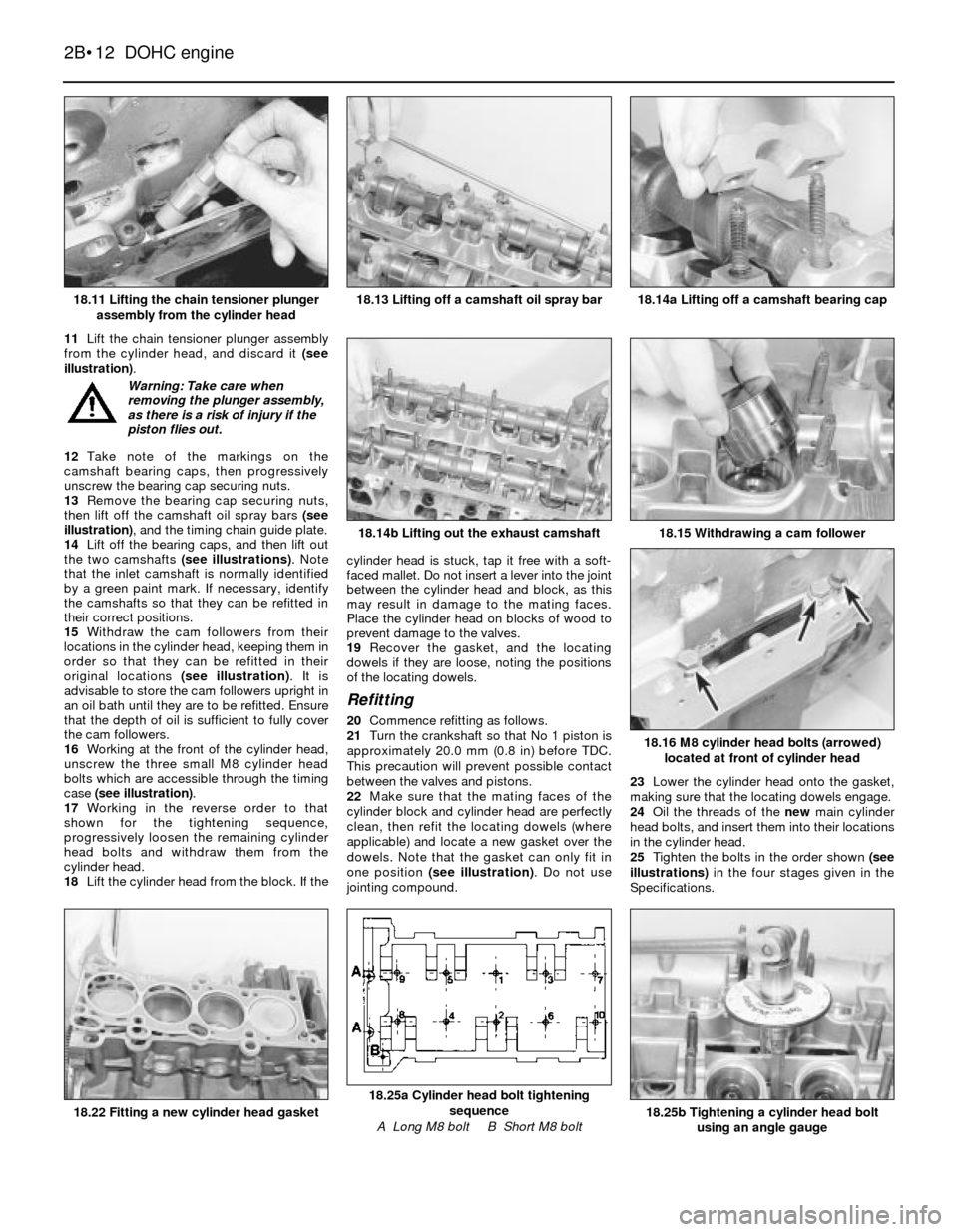
11Lift the chain tensioner plunger assembly
from the cylinder head, and discard it (see
illustration).
12Take note of the markings on the
camshaft bearing caps, then progressively
unscrew the bearing cap securing nuts.
13Remove the bearing cap securing nuts,
then lift off the camshaft oil spray bars (see
illustration), and the timing chain guide plate.
14Lift off the bearing caps, and then lift out
the two camshafts (see illustrations). Note
that the inlet camshaft is normally identified
by a green paint mark. If necessary, identify
the camshafts so that they can be refitted in
their correct positions.
15Withdraw the cam followers from their
locations in the cylinder head, keeping them in
order so that they can be refitted in their
original locations (see illustration). It is
advisable to store the cam followers upright in
an oil bath until they are to be refitted. Ensure
that the depth of oil is sufficient to fully cover
the cam followers.
16Working at the front of the cylinder head,
unscrew the three small M8 cylinder head
bolts which are accessible through the timing
case (see illustration).
17Working in the reverse order to that
shown for the tightening sequence,
progressively loosen the remaining cylinder
head bolts and withdraw them from the
cylinder head.
18Lift the cylinder head from the block. If thecylinder head is stuck, tap it free with a soft-
faced mallet. Do not insert a lever into the joint
between the cylinder head and block, as this
may result in damage to the mating faces.
Place the cylinder head on blocks of wood to
prevent damage to the valves.
19Recover the gasket, and the locating
dowels if they are loose, noting the positions
of the locating dowels.
Refitting
20Commence refitting as follows.
21Turn the crankshaft so that No 1 piston is
approximately 20.0 mm (0.8 in) before TDC.
This precaution will prevent possible contact
between the valves and pistons.
22Make sure that the mating faces of the
cylinder block and cylinder head are perfectly
clean, then refit the locating dowels (where
applicable) and locate a new gasket over the
dowels. Note that the gasket can only fit in
one position (see illustration). Do not use
jointing compound.23Lower the cylinder head onto the gasket,
making sure that the locating dowels engage.
24Oil the threads of the new main cylinder
head bolts, and insert them into their locations
in the cylinder head.
25Tighten the bolts in the order shown (see
illustrations)in the four stages given in the
Specifications.
2B•12DOHC engine
18.11 Lifting the chain tensioner plunger
assembly from the cylinder head18.14a Lifting off a camshaft bearing cap
18.25b Tightening a cylinder head bolt
using an angle gauge
18.25a Cylinder head bolt tightening
sequence
A Long M8 bolt B Short M8 bolt18.22 Fitting a new cylinder head gasket
18.16 M8 cylinder head bolts (arrowed)
located at front of cylinder head
18.15 Withdrawing a cam follower18.14b Lifting out the exhaust camshaft
18.13 Lifting off a camshaft oil spray bar
Warning: Take care when
removing the plunger assembly,
as there is a risk of injury if the
piston flies out.
Page 13 of 18
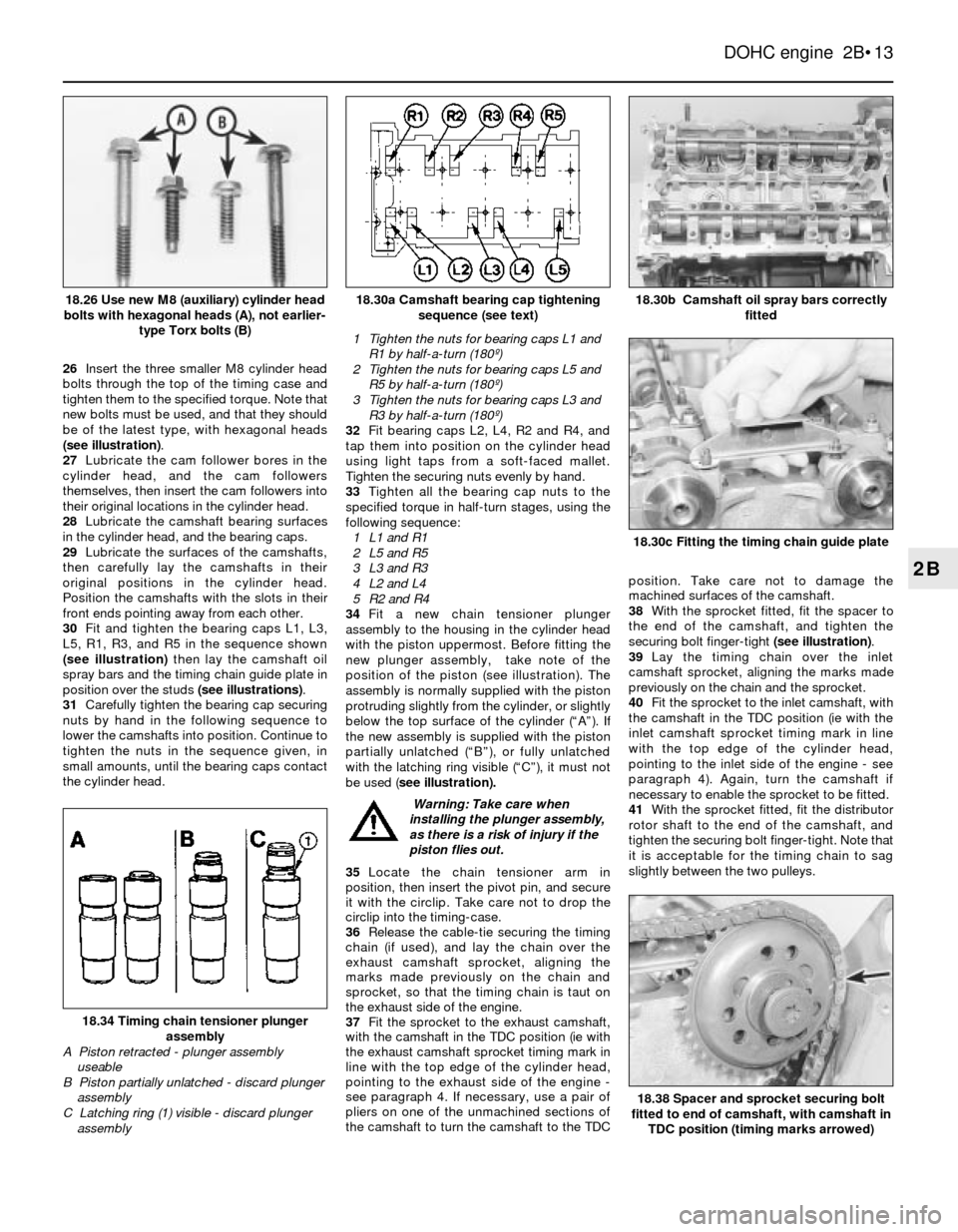
26Insert the three smaller M8 cylinder head
bolts through the top of the timing case and
tighten them to the specified torque. Note that
new bolts must be used, and that they should
be of the latest type, with hexagonal heads
(see illustration).
27Lubricate the cam follower bores in the
cylinder head, and the cam followers
themselves, then insert the cam followers into
their original locations in the cylinder head.
28Lubricate the camshaft bearing surfaces
in the cylinder head, and the bearing caps.
29Lubricate the surfaces of the camshafts,
then carefully lay the camshafts in their
original positions in the cylinder head.
Position the camshafts with the slots in their
front ends pointing away from each other.
30Fit and tighten the bearing caps L1, L3,
L5, R1, R3, and R5 in the sequence shown
(see illustration)then lay the camshaft oil
spray bars and the timing chain guide plate in
position over the studs (see illustrations).
31Carefully tighten the bearing cap securing
nuts by hand in the following sequence to
lower the camshafts into position. Continue to
tighten the nuts in the sequence given, in
small amounts, until the bearing caps contact
the cylinder head.1Tighten the nuts for bearing caps L1 and
R1 by half-a-turn (180º)
2Tighten the nuts for bearing caps L5 and
R5 by half-a-turn (180º)
3Tighten the nuts for bearing caps L3 and
R3 by half-a-turn (180º)
32Fit bearing caps L2, L4, R2 and R4, and
tap them into position on the cylinder head
using light taps from a soft-faced mallet.
Tighten the securing nuts evenly by hand.
33Tighten all the bearing cap nuts to the
specified torque in half-turn stages, using the
following sequence:
1L1 and R1
2L5 and R5
3L3 and R3
4L2 and L4
5R2 and R4
34Fit a newchain tensioner plunger
assembly to the housing in the cylinder head
with the piston uppermost. Before fitting the
new plunger assembly, take note of the
position of the piston(see illustration). The
assembly is normally supplied with the piston
protruding slightly from the cylinder, or slightly
below the top surface of the cylinder (“A”). If
the new assembly is supplied with the piston
partially unlatched (“B”), or fully unlatched
with the latching ring visible (“C”), it must not
be used (see illustration).
35Locate the chain tensioner arm in
position, then insert the pivot pin, and secure
it with the circlip. Take care not to drop the
circlip into the timing-case.
36Release the cable-tie securing the timing
chain (if used), and lay the chain over the
exhaust camshaft sprocket, aligning the
marks made previously on the chain and
sprocket, so that the timing chain is taut on
the exhaust side of the engine.
37Fit the sprocket to the exhaust camshaft,
with the camshaft in the TDC position (ie with
the exhaust camshaft sprocket timing mark in
line with the top edge of the cylinder head,
pointing to the exhaust side of the engine -
see paragraph 4. If necessary, use a pair of
pliers on one of the unmachined sections of
the camshaft to turn the camshaft to the TDCposition. Take care not to damage the
machined surfaces of the camshaft.
38With the sprocket fitted, fit the spacer to
the end of the camshaft, and tighten the
securing bolt finger-tight (see illustration).
39Lay the timing chain over the inlet
camshaft sprocket, aligning the marks made
previously on the chain and the sprocket.
40Fit the sprocket to the inlet camshaft, with
the camshaft in the TDC position (ie with the
inlet camshaft sprocket timing mark in line
with the top edge of the cylinder head,
pointing to the inlet side of the engine - see
paragraph 4). Again, turn the camshaft if
necessary to enable the sprocket to be fitted.
41With the sprocket fitted, fit the distributor
rotor shaft to the end of the camshaft, and
tighten the securing bolt finger-tight. Note that
it is acceptable for the timing chain to sag
slightly between the two pulleys.
DOHC engine 2B•13
2B
18.30b Camshaft oil spray bars correctly
fitted
18.38 Spacer and sprocket securing bolt
fitted to end of camshaft, with camshaft in
TDC position (timing marks arrowed)
18.34 Timing chain tensioner plunger
assembly
A Piston retracted - plunger assembly
useable
B Piston partially unlatched - discard plunger
assembly
C Latching ring (1) visible - discard plunger
assembly
18.30c Fitting the timing chain guide plate
18.30a Camshaft bearing cap tightening
sequence (see text)18.26 Use new M8 (auxiliary) cylinder head
bolts with hexagonal heads (A), not earlier-
type Torx bolts (B)
Warning: Take care when
installing the plunger assembly,
as there is a risk of injury if the
piston flies out.
Page 14 of 18
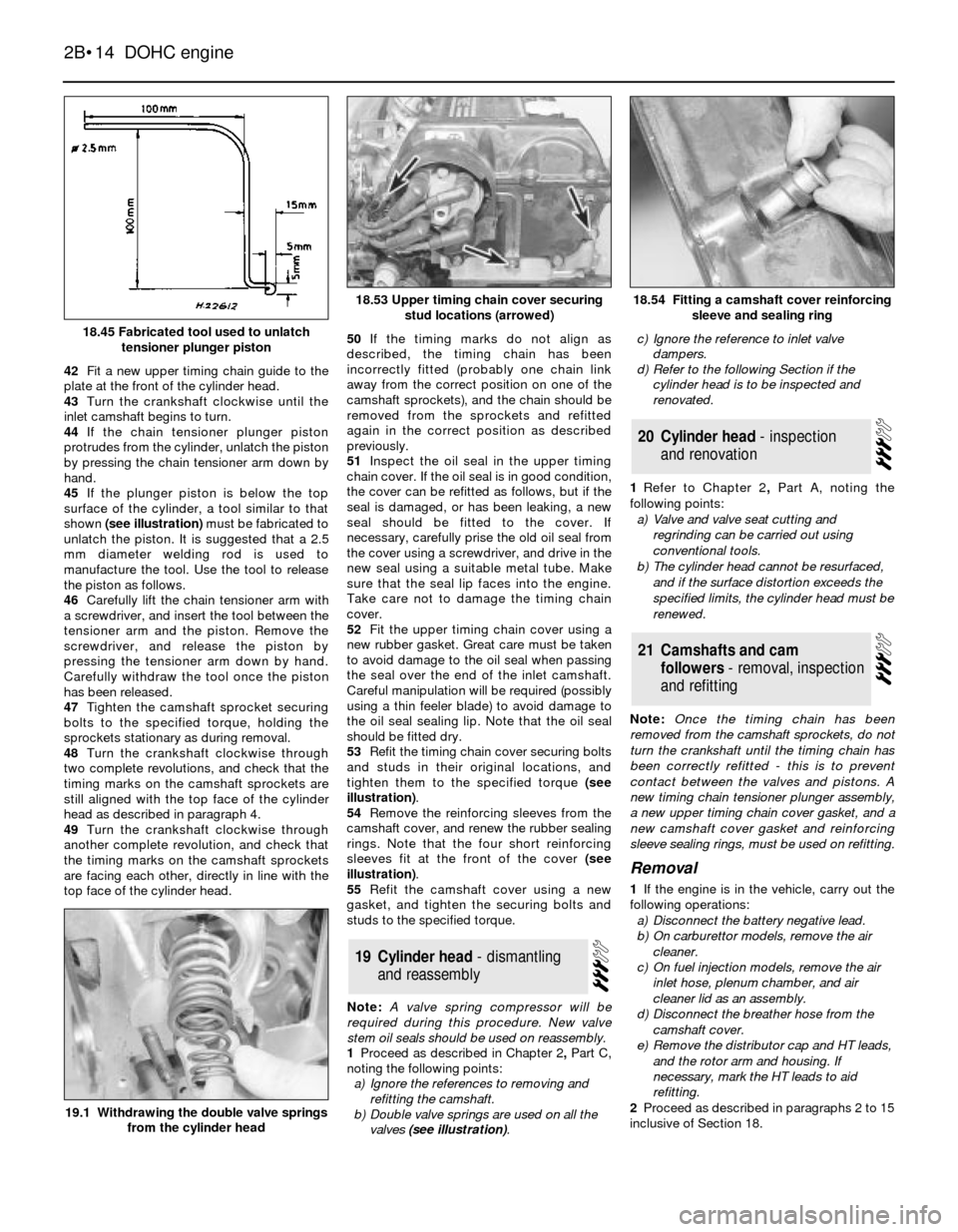
42Fit a new upper timing chain guide to the
plate at the front of the cylinder head.
43Turn the crankshaft clockwise until the
inlet camshaft begins to turn.
44If the chain tensioner plunger piston
protrudes from the cylinder, unlatch the piston
by pressing the chain tensioner arm down by
hand.
45If the plunger piston is below the top
surface of the cylinder, a tool similar to that
shown(see illustration)must be fabricated to
unlatch the piston. It is suggested that a 2.5
mm diameter welding rod is used to
manufacture the tool. Use the tool to release
the piston as follows.
46Carefully lift the chain tensioner arm with
a screwdriver, and insert the tool between the
tensioner arm and the piston. Remove the
screwdriver, and release the piston by
pressing the tensioner arm down by hand.
Carefully withdraw the tool once the piston
has been released.
47Tighten the camshaft sprocket securing
bolts to the specified torque, holding the
sprockets stationary as during removal.
48Turn the crankshaft clockwise through
two complete revolutions, and check that the
timing marks on the camshaft sprockets are
still aligned with the top face of the cylinder
head as described in paragraph 4.
49Turn the crankshaft clockwise through
another complete revolution, and check that
the timing marks on the camshaft sprockets
are facing each other, directly in line with the
top face of the cylinder head. 50If the timing marks do not align as
described, the timing chain has been
incorrectly fitted (probably one chain link
away from the correct position on one of the
camshaft sprockets), and the chain should be
removed from the sprockets and refitted
again in the correct position as described
previously.
51Inspect the oil seal in the upper timing
chain cover. If the oil seal is in good condition,
the cover can be refitted as follows, but if the
seal is damaged, or has been leaking, a new
seal should be fitted to the cover. If
necessary, carefully prise the old oil seal from
the cover using a screwdriver, and drive in the
new seal using a suitable metal tube. Make
sure that the seal lip faces into the engine.
Take care not to damage the timing chain
cover.
52Fit the upper timing chain cover using a
new rubber gasket. Great care must be taken
to avoid damage to the oil seal when passing
the seal over the end of the inlet camshaft.
Careful manipulation will be required (possibly
using a thin feeler blade) to avoid damage to
the oil seal sealing lip. Note that the oil seal
should be fitted dry.
53Refit the timing chain cover securing bolts
and studs in their original locations, and
tighten them to the specified torque (see
illustration).
54Remove the reinforcing sleeves from the
camshaft cover, and renew the rubber sealing
rings. Note that the four short reinforcing
sleeves fit at the front of the cover (see
illustration).
55Refit the camshaft cover using a new
gasket, and tighten the securing bolts and
studs to the specified torque.
Note: A valve spring compressor will be
required during this procedure. New valve
stem oil seals should be used on reassembly.
1Proceed as described in Chapter 2, PartC,
noting the following points:
a)Ignore the references to removing and
refitting the camshaft.
b)Double valve springs are used on all the
valves (see illustration).c)Ignore the reference to inlet valve
dampers.
d)Refer to the following Section if the
cylinder head is to be inspected and
renovated.
1Refer to Chapter 2, PartA, noting the
following points:
a)Valve and valve seat cutting and
regrinding can be carried out using
conventional tools.
b)The cylinder head cannot be resurfaced,
and if the surface distortion exceeds the
specified limits, the cylinder head must be
renewed.
Note: Once the timing chain has been
removed from the camshaft sprockets, do not
turn the crankshaft until the timing chain has
been correctly refitted - this is to prevent
contact between the valves and pistons. A
new timing chain tensioner plunger assembly,
a new upper timing chain cover gasket, and a
new camshaft cover gasket and reinforcing
sleeve sealing rings, must be used on refitting.
Removal
1If the engine is in the vehicle, carry out the
following operations:
a)Disconnect the battery negative lead.
b)On carburettor models, remove the air
cleaner.
c)On fuel injection models, remove the air
inlet hose, plenum chamber, and air
cleaner lid as an assembly.
d)Disconnect the breather hose from the
camshaft cover.
e)Remove the distributor cap and HT leads,
and the rotor arm and housing. If
necessary, mark the HT leads to aid
refitting.
2Proceed as described in paragraphs 2 to 15
inclusive of Section 18.
21Camshafts and cam
followers - removal, inspection
and refitting
20Cylinder head - inspection
and renovation
19Cylinder head - dismantling
and reassembly
2B•14DOHC engine
18.45 Fabricated tool used to unlatch
tensioner plunger piston
18.54 Fitting a camshaft cover reinforcing
sleeve and sealing ring
19.1 Withdrawing the double valve springs
from the cylinder head
18.53 Upper timing chain cover securing
stud locations (arrowed)
Page 15 of 18
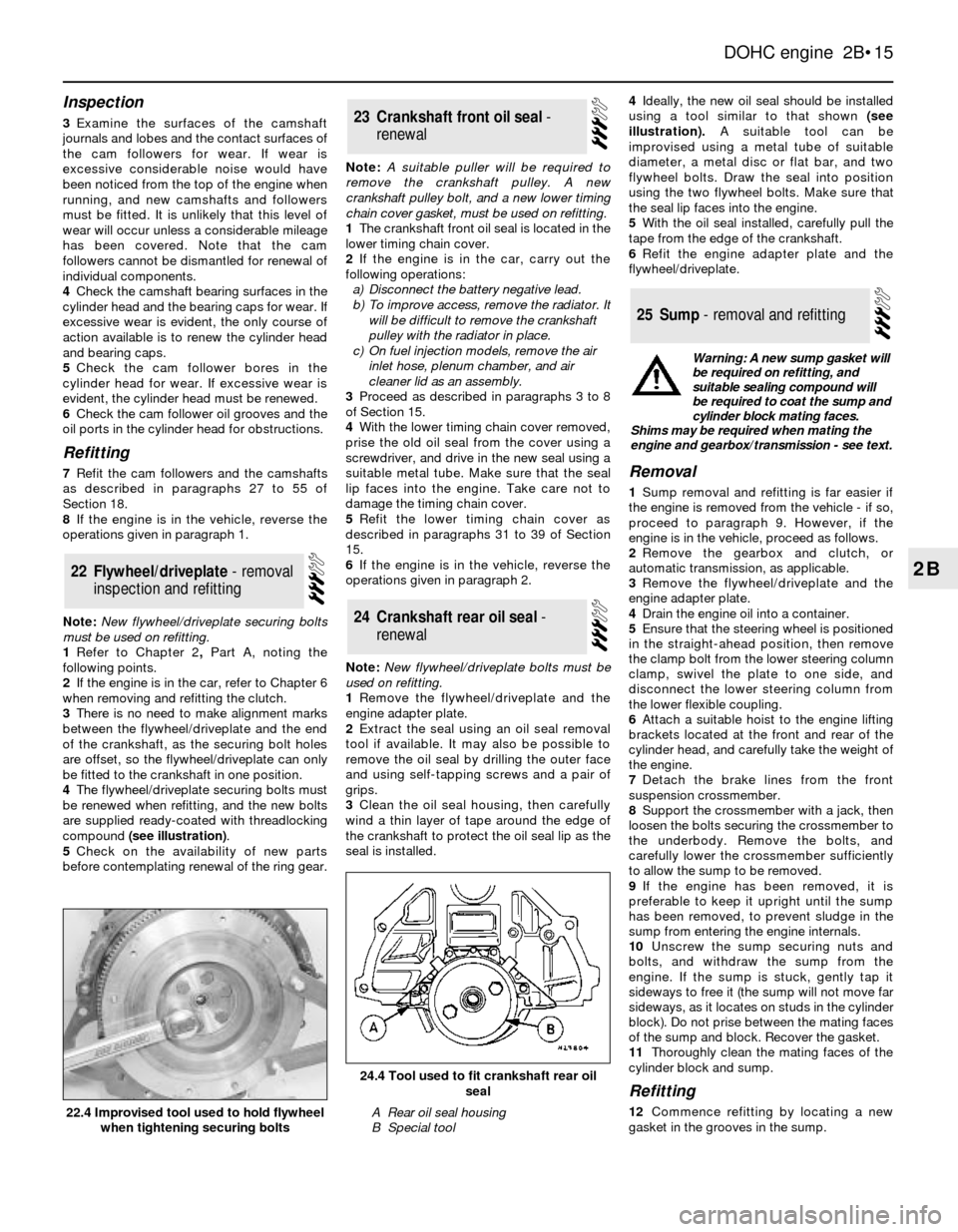
Inspection
3Examine the surfaces of the camshaft
journals and lobes and the contact surfaces of
the cam followers for wear. If wear is
excessive considerable noise would have
been noticed from the top of the engine when
running, and new camshafts and followers
must be fitted. It is unlikely that this level of
wear will occur unless a considerable mileage
has been covered. Note that the cam
followers cannot be dismantled for renewal of
individual components.
4Check the camshaft bearing surfaces in the
cylinder head and the bearing caps for wear. If
excessive wear is evident, the only course of
action available is to renew the cylinder head
and bearing caps.
5Check the cam follower bores in the
cylinder head for wear. If excessive wear is
evident, the cylinder head must be renewed.
6Check the cam follower oil grooves and the
oil ports in the cylinder head for obstructions.
Refitting
7Refit the cam followers and the camshafts
as described in paragraphs 27 to 55 of
Section 18.
8If the engine is in the vehicle, reverse the
operations given in paragraph 1.
Note: New flywheel/driveplate securing bolts
must be used on refitting.
1Refer to Chapter 2, PartA, noting the
following points.
2If the engine is in the car, refer to Chapter 6
when removing and refitting the clutch.
3There is no need to make alignment marks
between the flywheel/driveplate and the end
of the crankshaft, as the securing bolt holes
are offset, so the flywheel/driveplate can only
be fitted to the crankshaft in one position.
4The flywheel/driveplate securing bolts must
be renewed when refitting, and the new bolts
are supplied ready-coated with threadlocking
compound (see illustration).
5Check on the availability of new parts
before contemplating renewal of the ring gear.Note: A suitable puller will be required to
remove the crankshaft pulley. A new
crankshaft pulley bolt, and a new lower timing
chain cover gasket, must be used on refitting.
1The crankshaft front oil seal is located in the
lower timing chain cover.
2If the engine is in the car, carry out the
following operations:
a)Disconnect the battery negative lead.
b)To improve access, remove the radiator. It
will be difficult to remove the crankshaft
pulley with the radiator in place.
c)On fuel injection models, remove the air
inlet hose, plenum chamber, and air
cleaner lid as an assembly.
3Proceed as described in paragraphs 3 to 8
of Section 15.
4With the lower timing chain cover removed,
prise the old oil seal from the cover using a
screwdriver, and drive in the new seal using a
suitable metal tube. Make sure that the seal
lip faces into the engine. Take care not to
damage the timing chain cover.
5Refit the lower timing chain cover as
described in paragraphs 31 to 39 of Section
15.
6If the engine is in the vehicle, reverse the
operations given in paragraph 2.
Note: New flywheel/driveplate bolts must be
used on refitting.
1Remove the flywheel/driveplate and the
engine adapter plate.
2Extract the seal using an oil seal removal
tool if available. It may also be possible to
remove the oil seal by drilling the outer face
and using self-tapping screws and a pair of
grips.
3Clean the oil seal housing, then carefully
wind a thin layer of tape around the edge of
the crankshaft to protect the oil seal lip as the
seal is installed.4Ideally, the new oil seal should be installed
using a tool similar to that shown (see
illustration).A suitable tool can be
improvised using a metal tube of suitable
diameter, a metal disc or flat bar, and two
flywheel bolts. Draw the seal into position
using the two flywheel bolts. Make sure that
the seal lip faces into the engine.
5With the oil seal installed, carefully pull the
tape from the edge of the crankshaft.
6Refit the engine adapter plate and the
flywheel/driveplate.Removal
1Sump removal and refitting is far easier if
the engine is removed from the vehicle - if so,
proceed to paragraph 9. However, if the
engine is in the vehicle, proceed as follows.
2Remove the gearbox and clutch, or
automatic transmission, as applicable.
3Remove the flywheel/driveplate and the
engine adapter plate.
4Drain the engine oil into a container.
5Ensure that the steering wheel is positioned
in the straight-ahead position, then remove
the clamp bolt from the lower steering column
clamp, swivel the plate to one side, and
disconnect the lower steering column from
the lower flexible coupling.
6Attach a suitable hoist to the engine lifting
brackets located at the front and rear of the
cylinder head, and carefully take the weight of
the engine.
7Detach the brake lines from the front
suspension crossmember.
8Support the crossmember with a jack, then
loosen the bolts securing the crossmember to
the underbody. Remove the bolts, and
carefully lower the crossmember sufficiently
to allow the sump to be removed.
9If the engine has been removed, it is
preferable to keep it upright until the sump
has been removed, to prevent sludge in the
sump from entering the engine internals.
10Unscrew the sump securing nuts and
bolts, and withdraw the sump from the
engine. If the sump is stuck, gently tap it
sideways to free it (the sump will not move far
sideways, as it locates on studs in the cylinder
block). Do not prise between the mating faces
of the sump and block. Recover the gasket.
11Thoroughly clean the mating faces of the
cylinder block and sump.
Refitting
12Commence refitting by locating a new
gasket in the grooves in the sump.
25Sump - removal and refitting
24Crankshaft rear oil seal -
renewal
23Crankshaft front oil seal -
renewal
22Flywheel/driveplate - removal
inspection and refitting
DOHC engine 2B•15
2B
24.4 Tool used to fit crankshaft rear oil
seal
A Rear oil seal housing
B Special tool22.4 Improvised tool used to hold flywheel
when tightening securing bolts
Warning: A new sump gasket will
be required on refitting, and
suitable sealing compound will
be required to coat the sump and
cylinder block mating faces.
Shims may be required when mating the
engine and gearbox/transmission - see text.
Page 16 of 18
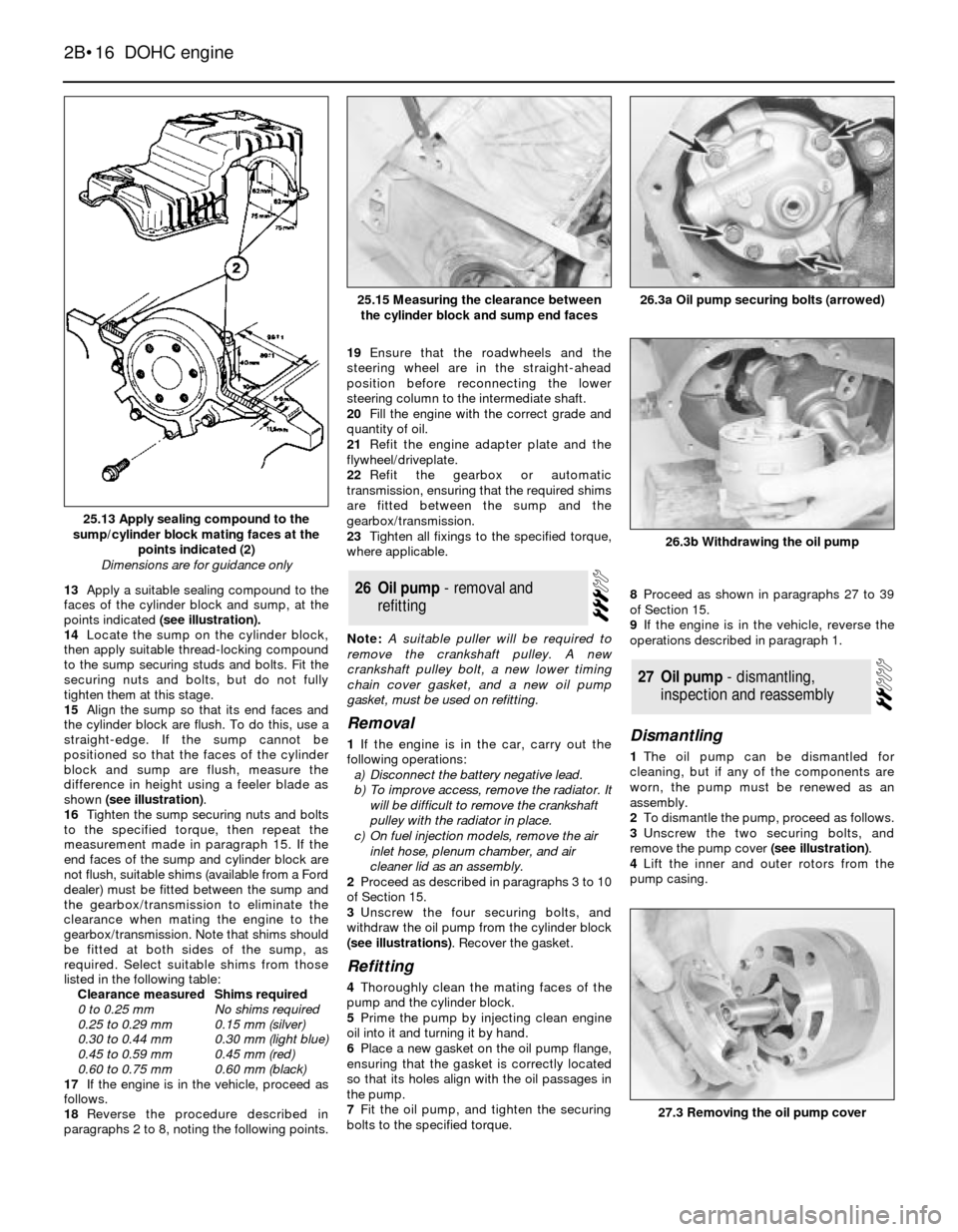
13Apply a suitable sealing compound to the
faces of the cylinder block and sump, at the
points indicated (see illustration).
14Locate the sump on the cylinder block,
then apply suitable thread-locking compound
to the sump securing studs and bolts. Fit the
securing nuts and bolts, but do not fully
tighten them at this stage.
15Align the sump so that its end faces and
the cylinder block are flush. To do this, use a
straight-edge. If the sump cannot be
positioned so that the faces of the cylinder
block and sump are flush, measure the
difference in height using a feeler blade as
shown (see illustration).
16Tighten the sump securing nuts and bolts
to the specified torque, then repeat the
measurement made in paragraph 15. If the
end faces of the sump and cylinder block are
not flush, suitable shims (available from a Ford
dealer) must be fitted between the sump and
the gearbox/transmission to eliminate the
clearance when mating the engine to the
gearbox/transmission. Note that shims should
be fitted at both sides of the sump, as
required. Select suitable shims from those
listed in the following table:
Clearance measuredShims required
0 to 0.25 mmNo shims required
0.25 to 0.29 mm0.15 mm (silver)
0.30 to 0.44 mm0.30 mm (light blue)
0.45 to 0.59 mm0.45 mm (red)
0.60 to 0.75 mm0.60 mm (black)
17If the engine is in the vehicle, proceed as
follows.
18Reverse the procedure described in
paragraphs 2 to 8, noting the following points.19Ensure that the roadwheels and the
steering wheel are in the straight-ahead
position before reconnecting the lower
steering column to the intermediate shaft.
20Fill the engine with the correct grade and
quantity of oil.
21Refit the engine adapter plate and the
flywheel/driveplate.
22Refit the gearbox or automatic
transmission, ensuring that the required shims
are fitted between the sump and the
gearbox/transmission.
23Tighten all fixings to the specified torque,
where applicable.
Note: A suitable puller will be required to
remove the crankshaft pulley. A new
crankshaft pulley bolt, a new lower timing
chain cover gasket, and a new oil pump
gasket, must be used on refitting.
Removal
1If the engine is in the car, carry out the
following operations:
a)Disconnect the battery negative lead.
b)To improve access, remove the radiator. It
will be difficult to remove the crankshaft
pulley with the radiator in place.
c)On fuel injection models, remove the air
inlet hose, plenum chamber, and air
cleaner lid as an assembly.
2Proceed as described in paragraphs 3 to 10
of Section 15.
3Unscrew the four securing bolts, and
withdraw the oil pump from the cylinder block
(see illustrations). Recover the gasket.
Refitting
4Thoroughly clean the mating faces of the
pump and the cylinder block.
5Prime the pump by injecting clean engine
oil into it and turning it by hand.
6Place a new gasket on the oil pump flange,
ensuring that the gasket is correctly located
so that its holes align with the oil passages in
the pump.
7Fit the oil pump, and tighten the securing
bolts to the specified torque.8Proceed as shown in paragraphs 27 to 39
of Section 15.
9If the engine is in the vehicle, reverse the
operations described in paragraph 1.
Dismantling
1The oil pump can be dismantled for
cleaning, but if any of the components are
worn, the pump must be renewed as an
assembly.
2To dismantle the pump, proceed as follows.
3Unscrew the two securing bolts, and
remove the pump cover (see illustration).
4Lift the inner and outer rotors from the
pump casing.
27Oil pump - dismantling,
inspection and reassembly
26Oil pump - removal and
refitting
2B•16DOHC engine
25.13 Apply sealing compound to the
sump/cylinder block mating faces at the
points indicated (2)
Dimensions are for guidance only
26.3b Withdrawing the oil pump
26.3a Oil pump securing bolts (arrowed)25.15 Measuring the clearance between
the cylinder block and sump end faces
27.3 Removing the oil pump cover
Page 17 of 18
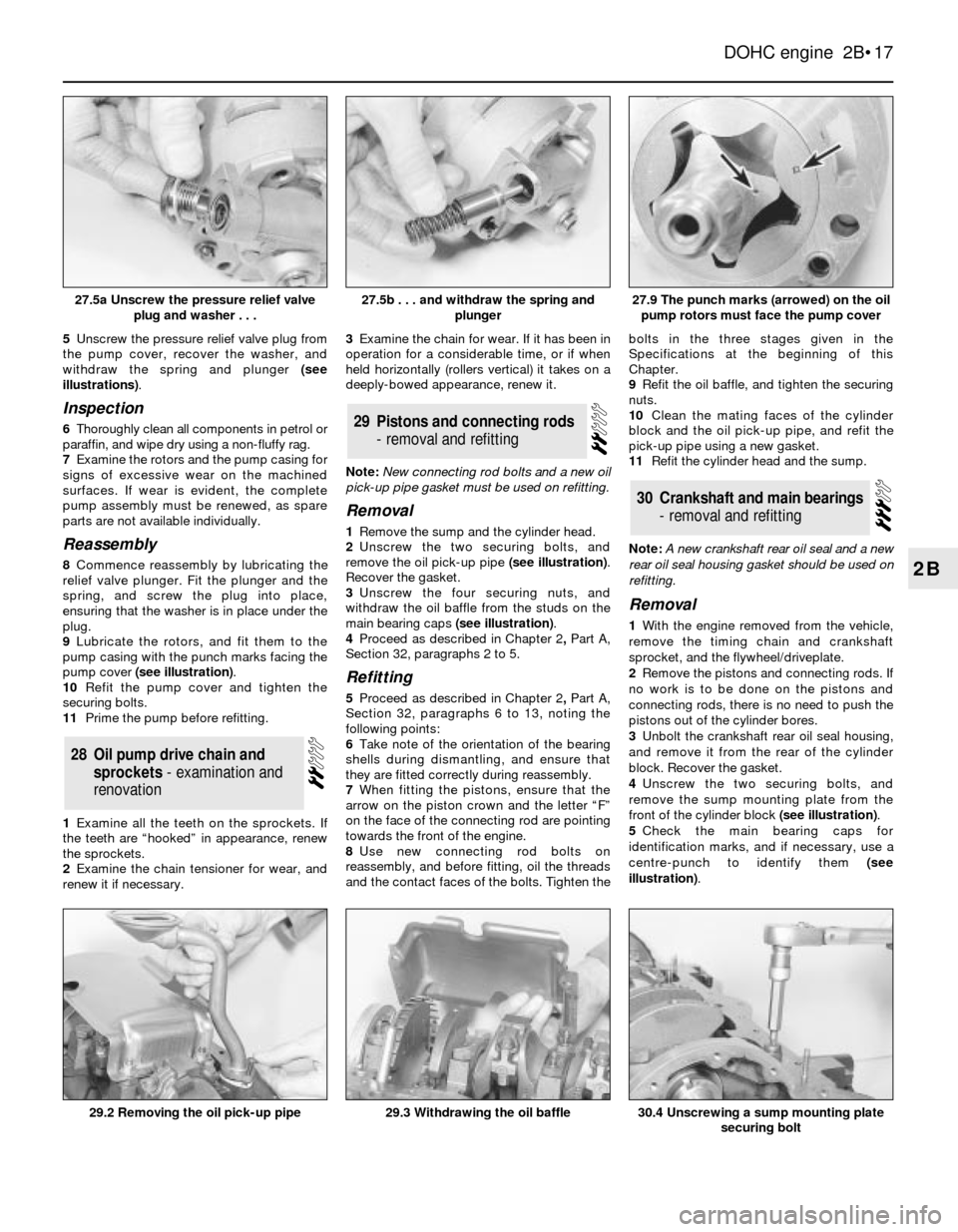
5Unscrew the pressure relief valve plug from
the pump cover, recover the washer, and
withdraw the spring and plunger (see
illustrations).
Inspection
6Thoroughly clean all components in petrol or
paraffin, and wipe dry using a non-fluffy rag.
7Examine the rotors and the pump casing for
signs of excessive wear on the machined
surfaces. If wear is evident, the complete
pump assembly must be renewed, as spare
parts are not available individually.
Reassembly
8Commence reassembly by lubricating the
relief valve plunger. Fit the plunger and the
spring, and screw the plug into place,
ensuring that the washer is in place under the
plug.
9Lubricate the rotors, and fit them to the
pump casing with the punch marks facing the
pump cover (see illustration).
10Refit the pump cover and tighten the
securing bolts.
11Prime the pump before refitting.
1Examine all the teeth on the sprockets. If
the teeth are “hooked” in appearance, renew
the sprockets.
2Examine the chain tensioner for wear, and
renew it if necessary.3Examine the chain for wear. If it has been in
operation for a considerable time, or if when
held horizontally (rollers vertical) it takes on a
deeply-bowed appearance, renew it.
Note: New connecting rod bolts and a new oil
pick-up pipe gasket must be used on refitting.
Removal
1Remove the sump and the cylinder head.
2Unscrew the two securing bolts, and
remove the oil pick-up pipe (see illustration).
Recover the gasket.
3Unscrew the four securing nuts, and
withdraw the oil baffle from the studs on the
main bearing caps (see illustration).
4Proceed as described in Chapter 2, PartA,
Section 32, paragraphs 2 to 5.
Refitting
5Proceed as described in Chapter 2, PartA,
Section 32, paragraphs 6 to 13, noting the
following points:
6Take note of the orientation of the bearing
shells during dismantling, and ensure that
they are fitted correctly during reassembly.
7When fitting the pistons, ensure that the
arrow on the piston crown and the letter “F”
on the face of the connecting rod are pointing
towards the front of the engine.
8Use new connecting rod bolts on
reassembly, and before fitting, oil the threads
and the contact faces of the bolts. Tighten thebolts in the three stages given in the
Specifications at the beginning of this
Chapter.
9Refit the oil baffle, and tighten the securing
nuts.
10Clean the mating faces of the cylinder
block and the oil pick-up pipe, and refit the
pick-up pipe using a new gasket.
11Refit the cylinder head and the sump.
Note: A new crankshaft rear oil seal and a new
rear oil seal housing gasket should be used on
refitting.
Removal
1With the engine removed from the vehicle,
remove the timing chain and crankshaft
sprocket, and the flywheel/driveplate.
2Remove the pistons and connecting rods. If
no work is to be done on the pistons and
connecting rods, there is no need to push the
pistons out of the cylinder bores.
3Unbolt the crankshaft rear oil seal housing,
and remove it from the rear of the cylinder
block. Recover the gasket.
4Unscrew the two securing bolts, and
remove the sump mounting plate from the
front of the cylinder block (see illustration).
5Check the main bearing caps for
identification marks, and if necessary, use a
centre-punch to identify them (see
illustration).
30Crankshaft and main bearings
- removal and refitting
29Pistons and connecting rods
- removal and refitting
28Oil pump drive chain and
sprockets - examination and
renovation
DOHC engine 2B•17
2B
27.5b . . . and withdraw the spring and
plunger
30.4 Unscrewing a sump mounting plate
securing bolt29.3 Withdrawing the oil baffle29.2 Removing the oil pick-up pipe
27.9 The punch marks (arrowed) on the oil
pump rotors must face the pump cover27.5a Unscrew the pressure relief valve
plug and washer . . .
Page 18 of 18
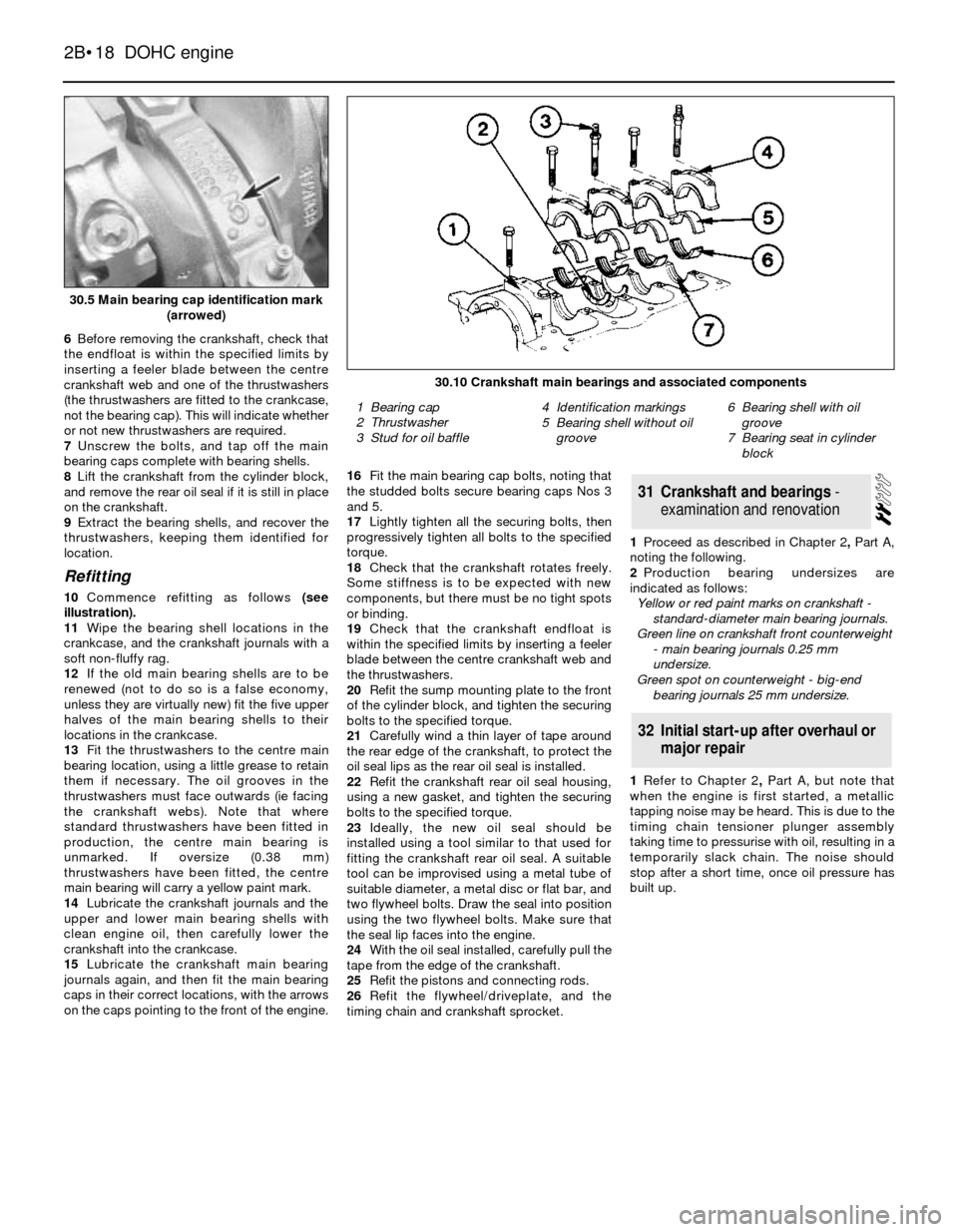
6Before removing the crankshaft, check that
the endfloat is within the specified limits by
inserting a feeler blade between the centre
crankshaft web and one of the thrustwashers
(the thrustwashers are fitted to the crankcase,
not the bearing cap). This will indicate whether
or not new thrustwashers are required.
7Unscrew the bolts, and tap off the main
bearing caps complete with bearing shells.
8Lift the crankshaft from the cylinder block,
and remove the rear oil seal if it is still in place
on the crankshaft.
9Extract the bearing shells, and recover the
thrustwashers, keeping them identified for
location.
Refitting
10Commence refitting as follows(see
illustration).
11Wipe the bearing shell locations in the
crankcase, and the crankshaft journals with a
soft non-fluffy rag.
12If the old main bearing shells are to be
renewed (not to do so is a false economy,
unless they are virtually new) fit the five upper
halves of the main bearing shells to their
locations in the crankcase.
13Fit the thrustwashers to the centre main
bearing location, using a little grease to retain
them if necessary. The oil grooves in the
thrustwashers must face outwards (ie facing
the crankshaft webs). Note that where
standard thrustwashers have been fitted in
production, the centre main bearing is
unmarked. If oversize (0.38 mm)
thrustwashers have been fitted, the centre
main bearing will carry a yellow paint mark.
14Lubricate the crankshaft journals and the
upper and lower main bearing shells with
clean engine oil, then carefully lower the
crankshaft into the crankcase.
15Lubricate the crankshaft main bearing
journals again, and then fit the main bearing
caps in their correct locations, with the arrows
on the caps pointing to the front of the engine.16Fit the main bearing cap bolts, noting that
the studded bolts secure bearing caps Nos 3
and 5.
17Lightly tighten all the securing bolts, then
progressively tighten all bolts to the specified
torque.
18Check that the crankshaft rotates freely.
Some stiffness is to be expected with new
components, but there must be no tight spots
or binding.
19Check that the crankshaft endfloat is
within the specified limits by inserting a feeler
blade between the centre crankshaft web and
the thrustwashers.
20Refit the sump mounting plate to the front
of the cylinder block, and tighten the securing
bolts to the specified torque.
21Carefully wind a thin layer of tape around
the rear edge of the crankshaft, to protect the
oil seal lips as the rear oil seal is installed.
22Refit the crankshaft rear oil seal housing,
using a new gasket, and tighten the securing
bolts to the specified torque.
23Ideally, the new oil seal should be
installed using a tool similar to that used for
fitting the crankshaft rear oil seal. A suitable
tool can be improvised using a metal tube of
suitable diameter, a metal disc or flat bar, and
two flywheel bolts. Draw the seal into position
using the two flywheel bolts. Make sure that
the seal lip faces into the engine.
24With the oil seal installed, carefully pull the
tape from the edge of the crankshaft.
25Refit the pistons and connecting rods.
26Refit the flywheel/driveplate, and the
timing chain and crankshaft sprocket.1Proceed as described in Chapter 2, PartA,
noting the following.
2Production bearing undersizes are
indicated as follows:
Yellow or red paint marks on crankshaft -
standard-diameter main bearing journals.
Green line on crankshaft front counterweight
- main bearing journals 0.25 mm
undersize.
Green spot on counterweight - big-end
bearing journals 25 mm undersize.
1Refer to Chapter 2, PartA, but note that
when the engine is first started, a metallic
tapping noise may be heard. This is due to the
timing chain tensioner plunger assembly
taking time to pressurise with oil, resulting in a
temporarily slack chain. The noise should
stop after a short time, once oil pressure has
built up.
32Initial start-up after overhaul or
major repair
31Crankshaft and bearings -
examination and renovation
2B•18DOHC engine
30.5 Main bearing cap identification mark
(arrowed)
30.10 Crankshaft main bearings and associated components
1 Bearing cap
2 Thrustwasher
3 Stud for oil baffle4 Identification markings
5 Bearing shell without oil
groove6 Bearing shell with oil
groove
7 Bearing seat in cylinder
block