length FORD SIERRA 1987 2.G SOHC Engines Workshop Manual
[x] Cancel search | Manufacturer: FORD, Model Year: 1987, Model line: SIERRA, Model: FORD SIERRA 1987 2.GPages: 24, PDF Size: 1.03 MB
Page 2 of 24
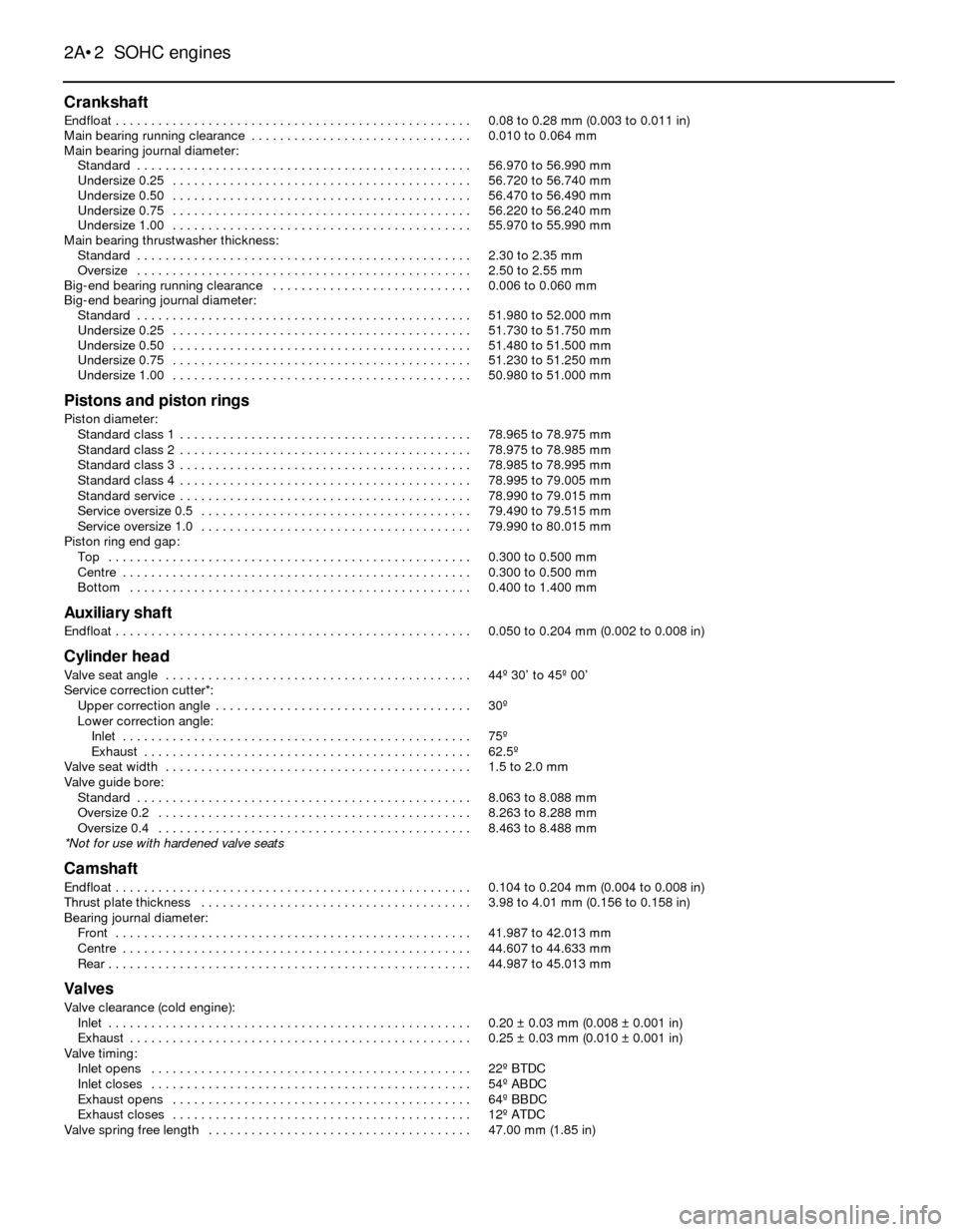
Crankshaft
Endfloat . . . . . . . . . . . . . . . . . . . . . . . . . . . . . . . . . . . . . . . . . . . . . . . . . .0.08 to 0.28 mm (0.003 to 0.011 in)
Main bearing running clearance . . . . . . . . . . . . . . . . . . . . . . . . . . . . . . .0.010 to 0.064 mm
Main bearing journal diameter:
Standard . . . . . . . . . . . . . . . . . . . . . . . . . . . . . . . . . . . . . . . . . . . . . . .56.970 to 56.990 mm
Undersize 0.25 . . . . . . . . . . . . . . . . . . . . . . . . . . . . . . . . . . . . . . . . . .56.720 to 56.740 mm
Undersize 0.50 . . . . . . . . . . . . . . . . . . . . . . . . . . . . . . . . . . . . . . . . . .56.470 to 56.490 mm
Undersize 0.75 . . . . . . . . . . . . . . . . . . . . . . . . . . . . . . . . . . . . . . . . . .56.220 to 56.240 mm
Undersize 1.00 . . . . . . . . . . . . . . . . . . . . . . . . . . . . . . . . . . . . . . . . . .55.970 to 55.990 mm
Main bearing thrustwasher thickness:
Standard . . . . . . . . . . . . . . . . . . . . . . . . . . . . . . . . . . . . . . . . . . . . . . .2.30 to 2.35 mm
Oversize . . . . . . . . . . . . . . . . . . . . . . . . . . . . . . . . . . . . . . . . . . . . . . .2.50 to 2.55 mm
Big-end bearing running clearance . . . . . . . . . . . . . . . . . . . . . . . . . . . .0.006 to 0.060 mm
Big-end bearing journal diameter:
Standard . . . . . . . . . . . . . . . . . . . . . . . . . . . . . . . . . . . . . . . . . . . . . . .51.980 to 52.000 mm
Undersize 0.25 . . . . . . . . . . . . . . . . . . . . . . . . . . . . . . . . . . . . . . . . . .51.730 to 51.750 mm
Undersize 0.50 . . . . . . . . . . . . . . . . . . . . . . . . . . . . . . . . . . . . . . . . . .51.480 to 51.500 mm
Undersize 0.75 . . . . . . . . . . . . . . . . . . . . . . . . . . . . . . . . . . . . . . . . . .51.230 to 51.250 mm
Undersize 1.00 . . . . . . . . . . . . . . . . . . . . . . . . . . . . . . . . . . . . . . . . . .50.980 to 51.000 mm
Pistons and piston rings
Piston diameter:
Standard class 1 . . . . . . . . . . . . . . . . . . . . . . . . . . . . . . . . . . . . . . . . .78.965 to 78.975 mm
Standard class 2 . . . . . . . . . . . . . . . . . . . . . . . . . . . . . . . . . . . . . . . . .78.975 to 78.985 mm
Standard class 3 . . . . . . . . . . . . . . . . . . . . . . . . . . . . . . . . . . . . . . . . .78.985 to 78.995 mm
Standard class 4 . . . . . . . . . . . . . . . . . . . . . . . . . . . . . . . . . . . . . . . . .78.995 to 79.005 mm
Standard service . . . . . . . . . . . . . . . . . . . . . . . . . . . . . . . . . . . . . . . . .78.990 to 79.015 mm
Service oversize 0.5 . . . . . . . . . . . . . . . . . . . . . . . . . . . . . . . . . . . . . .79.490 to 79.515 mm
Service oversize 1.0 . . . . . . . . . . . . . . . . . . . . . . . . . . . . . . . . . . . . . .79.990 to 80.015 mm
Piston ring end gap:
Top . . . . . . . . . . . . . . . . . . . . . . . . . . . . . . . . . . . . . . . . . . . . . . . . . . .0.300 to 0.500 mm
Centre . . . . . . . . . . . . . . . . . . . . . . . . . . . . . . . . . . . . . . . . . . . . . . . . .0.300 to 0.500 mm
Bottom . . . . . . . . . . . . . . . . . . . . . . . . . . . . . . . . . . . . . . . . . . . . . . . .0.400 to 1.400 mm
Auxiliary shaft
Endfloat . . . . . . . . . . . . . . . . . . . . . . . . . . . . . . . . . . . . . . . . . . . . . . . . . .0.050 to 0.204 mm (0.002 to 0.008 in)
Cylinder head
Valve seat angle . . . . . . . . . . . . . . . . . . . . . . . . . . . . . . . . . . . . . . . . . . .44¼ 30Õ to 45¼ 00Õ
Service correction cutter*:
Upper correction angle . . . . . . . . . . . . . . . . . . . . . . . . . . . . . . . . . . . .30¼
Lower correction angle:
Inlet . . . . . . . . . . . . . . . . . . . . . . . . . . . . . . . . . . . . . . . . . . . . . . . . .75¼
Exhaust . . . . . . . . . . . . . . . . . . . . . . . . . . . . . . . . . . . . . . . . . . . . . .62.5¼
Valve seat width . . . . . . . . . . . . . . . . . . . . . . . . . . . . . . . . . . . . . . . . . . .1.5 to 2.0 mm
Valve guide bore:
Standard . . . . . . . . . . . . . . . . . . . . . . . . . . . . . . . . . . . . . . . . . . . . . . .8.063 to 8.088 mm
Oversize 0.2 . . . . . . . . . . . . . . . . . . . . . . . . . . . . . . . . . . . . . . . . . . . .8.263 to 8.288 mm
Oversize 0.4 . . . . . . . . . . . . . . . . . . . . . . . . . . . . . . . . . . . . . . . . . . . .8.463 to 8.488 mm
*Not for use with hardened valve seats
Camshaft
Endfloat . . . . . . . . . . . . . . . . . . . . . . . . . . . . . . . . . . . . . . . . . . . . . . . . . .0.104 to 0.204 mm (0.004 to 0.008 in)
Thrust plate thickness . . . . . . . . . . . . . . . . . . . . . . . . . . . . . . . . . . . . . .3.98 to 4.01 mm (0.156 to 0.158 in)
Bearing journal diameter:
Front . . . . . . . . . . . . . . . . . . . . . . . . . . . . . . . . . . . . . . . . . . . . . . . . . .41.987 to 42.013 mm
Centre . . . . . . . . . . . . . . . . . . . . . . . . . . . . . . . . . . . . . . . . . . . . . . . . .44.607 to 44.633 mm
Rear . . . . . . . . . . . . . . . . . . . . . . . . . . . . . . . . . . . . . . . . . . . . . . . . . . .44.987 to 45.013 mm
Valves
Valve clearance (cold engine):
Inlet . . . . . . . . . . . . . . . . . . . . . . . . . . . . . . . . . . . . . . . . . . . . . . . . . . .0.20 ±0.03 mm (0.008 ±0.001 in)
Exhaust . . . . . . . . . . . . . . . . . . . . . . . . . . . . . . . . . . . . . . . . . . . . . . . .0.25 ±0.03 mm (0.010 ±0.001 in)
Valve timing:
Inlet opens . . . . . . . . . . . . . . . . . . . . . . . . . . . . . . . . . . . . . . . . . . . . .22¼ BTDC
Inlet closes . . . . . . . . . . . . . . . . . . . . . . . . . . . . . . . . . . . . . . . . . . . . .54¼ ABDC
Exhaust opens . . . . . . . . . . . . . . . . . . . . . . . . . . . . . . . . . . . . . . . . . .64¼ BBDC
Exhaust closes . . . . . . . . . . . . . . . . . . . . . . . . . . . . . . . . . . . . . . . . . .12¼ ATDC
Valve spring free length . . . . . . . . . . . . . . . . . . . . . . . . . . . . . . . . . . . . .47.00 mm (1.85 in)
2A¥2SOHC engines
Page 9 of 24
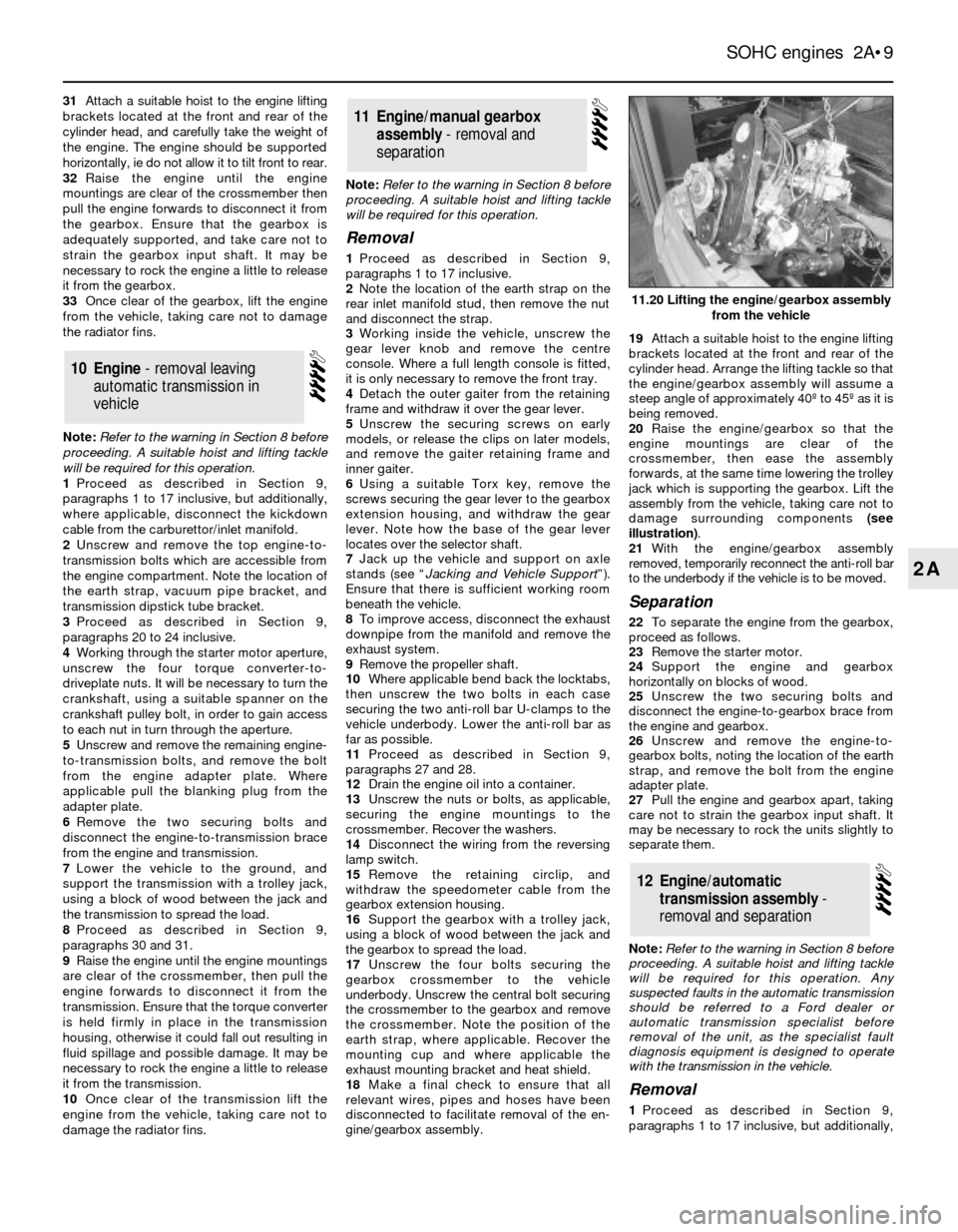
31Attach a suitable hoist to the engine lifting
brackets located at the front and rear of the
cylinder head, and carefully take the weight of
the engine. The engine should be supported
horizontally, ie do not allow it to tilt front to rear.
32Raise the engine until the engine
mountings are clear of the crossmember then
pull the engine forwards to disconnect it from
the gearbox. Ensure that the gearbox is
adequately supported, and take care not to
strain the gearbox input shaft. It may be
necessary to rock the engine a little to release
it from the gearbox.
33Once clear of the gearbox, lift the engine
from the vehicle, taking care not to damage
the radiator fins.
Note: Refer to the warning in Section 8 before
proceeding. A suitable hoist and lifting tackle
will be required for this operation.
1Proceed as described in Section 9,
paragraphs 1 to 17 inclusive, but additionally,
where applicable, disconnect the kickdown
cable from the carburettor/inlet manifold.
2Unscrew and remove the top engine-to-
transmission bolts which are accessible from
the engine compartment. Note the location of
the earth strap, vacuum pipe bracket, and
transmission dipstick tube bracket.
3Proceed as described in Section 9,
paragraphs 20 to 24 inclusive.
4Working through the starter motor aperture,
unscrew the four torque converter-to-
driveplate nuts. It will be necessary to turn the
crankshaft, using a suitable spanner on the
crankshaft pulley bolt, in order to gain access
to each nut in turn through the aperture.
5Unscrew and remove the remaining engine-
to-transmission bolts, and remove the bolt
from the engine adapter plate. Where
applicable pull the blanking plug from the
adapter plate.
6Remove the two securing bolts and
disconnect the engine-to-transmission brace
from the engine and transmission.
7Lower the vehicle to the ground, and
support the transmission with a trolley jack,
using a block of wood between the jack and
the transmission to spread the load.
8Proceed as described in Section 9,
paragraphs 30 and 31.
9Raise the engine until the engine mountings
are clear of the crossmember, then pull the
engine forwards to disconnect it from the
transmission. Ensure that the torque converter
is held firmly in place in the transmission
housing, otherwise it could fall out resulting in
fluid spillage and possible damage. It may be
necessary to rock the engine a little to release
it from the transmission.
10Once clear of the transmission lift the
engine from the vehicle, taking care not to
damage the radiator fins.Note: Refer to the warning in Section 8 before
proceeding. A suitable hoist and lifting tackle
will be required for this operation.
Removal
1Proceed as described in Section 9,
paragraphs 1 to 17 inclusive.
2Note the location of the earth strap on the
rear inlet manifold stud, then remove the nut
and disconnect the strap.
3Working inside the vehicle, unscrew the
gear lever knob and remove the centre
console. Where a full length console is fitted,
it is only necessary to remove the front tray.
4Detach the outer gaiter from the retaining
frame and withdraw it over the gear lever.
5Unscrew the securing screws on early
models, or release the clips on later models,
and remove the gaiter retaining frame and
inner gaiter.
6Using a suitable Torx key, remove the
screws securing the gear lever to the gearbox
extension housing, and withdraw the gear
lever. Note how the base of the gear lever
locates over the selector shaft.
7Jack up the vehicle and support on axle
stands (see ÒJacking and Vehicle SupportÓ).
Ensure that there is sufficient working room
beneath the vehicle.
8To improve access, disconnect the exhaust
downpipe from the manifold and remove the
exhaust system.
9Remove the propeller shaft.
10Where applicable bend back the locktabs,
then unscrew the two bolts in each case
securing the two anti-roll bar U-clamps to the
vehicle underbody. Lower the anti-roll bar as
far as possible.
11Proceed as described in Section 9,
paragraphs 27 and 28.
12Drain the engine oil into a container.
13Unscrew the nuts or bolts, as applicable,
securing the engine mountings to the
crossmember. Recover the washers.
14Disconnect the wiring from the reversing
lamp switch.
15Remove the retaining circlip, and
withdraw the speedometer cable from the
gearbox extension housing.
16Support the gearbox with a trolley jack,
using a block of wood between the jack and
the gearbox to spread the load.
17Unscrew the four bolts securing the
gearbox crossmember to the vehicle
underbody. Unscrew the central bolt securing
the crossmember to the gearbox and remove
the crossmember. Note the position of the
earth strap, where applicable. Recover the
mounting cup and where applicable the
exhaust mounting bracket and heat shield.
18Make a final check to ensure that all
relevant wires, pipes and hoses have been
disconnected to facilitate removal of the en-
gine/gearbox assembly.19Attach a suitable hoist to the engine lifting
brackets located at the front and rear of the
cylinder head. Arrange the lifting tackle so that
the engine/gearbox assembly will assume a
steep angle of approximately 40¼ to 45¼ as it is
being removed.
20Raise the engine/gearbox so that the
engine mountings are clear of the
crossmember, then ease the assembly
forwards, at the same time lowering the trolley
jack which is supporting the gearbox. Lift the
assembly from the vehicle, taking care not to
damage surrounding components (see
illustration).
21With the engine/gearbox assembly
removed, temporarily reconnect the anti-roll bar
to the underbody if the vehicle is to be moved.
Separation
22To separate the engine from the gearbox,
proceed as follows.
23Remove the starter motor.
24Support the engine and gearbox
horizontally on blocks of wood.
25Unscrew the two securing bolts and
disconnect the engine-to-gearbox brace from
the engine and gearbox.
26Unscrew and remove the engine-to-
gearbox bolts, noting the location of the earth
strap, and remove the bolt from the engine
adapter plate.
27Pull the engine and gearbox apart, taking
care not to strain the gearbox input shaft. It
may be necessary to rock the units slightly to
separate them.
Note: Refer to the warning in Section 8 before
proceeding. A suitable hoist and lifting tackle
will be required for this operation. Any
suspected faults in the automatic transmission
should be referred to a Ford dealer or
automatic transmission specialist before
removal of the unit, as the specialist fault
diagnosis equipment is designed to operate
with the transmission in the vehicle.
Removal
1Proceed as described in Section 9,
paragraphs 1 to 17 inclusive, but additionally,
12Engine/automatic
transmission assembly -
removal and separation
11Engine/manual gearbox
assembly - removal and
separation
10Engine - removal leaving
automatic transmission in
vehicle
SOHC engines 2A¥9
2A
11.20 Lifting the engine/gearbox assembly
from the vehicle
Page 16 of 24
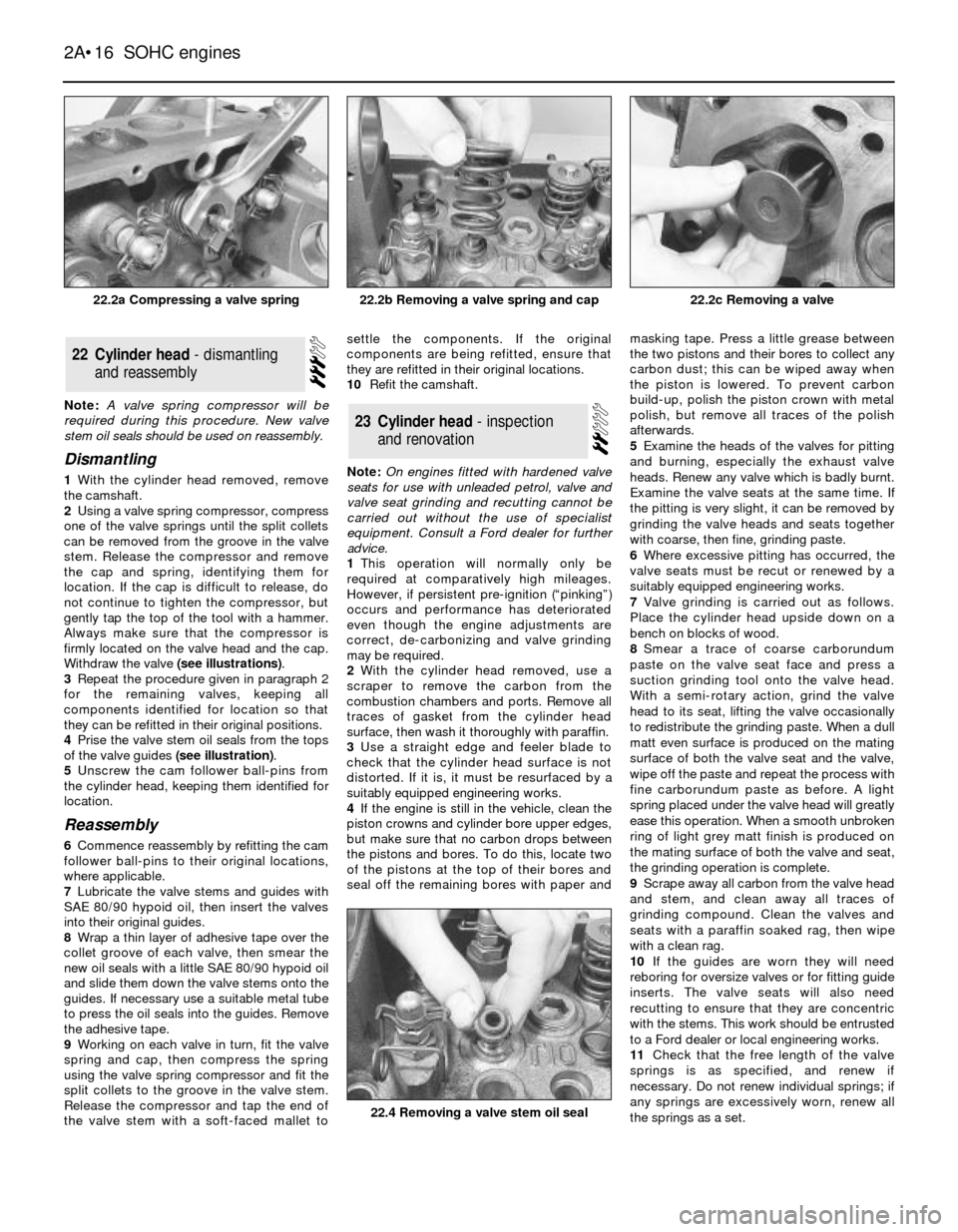
Note: A valve spring compressor will be
required during this procedure. New valve
stem oil seals should be used on reassembly.
Dismantling
1With the cylinder head removed, remove
the camshaft.
2Using a valve spring compressor, compress
one of the valve springs until the split collets
can be removed from the groove in the valve
stem. Release the compressor and remove
the cap and spring, identifying them for
location. If the cap is difficult to release, do
not continue to tighten the compressor, but
gently tap the top of the tool with a hammer.
Always make sure that the compressor is
firmly located on the valve head and the cap.
Withdraw the valve (see illustrations).
3Repeat the procedure given in paragraph 2
for the remaining valves, keeping all
components identified for location so that
they can be refitted in their original positions.
4Prise the valve stem oil seals from the tops
of the valve guides (see illustration).
5Unscrew the cam follower ball-pins from
the cylinder head, keeping them identified for
location.
Reassembly
6Commence reassembly by refitting the cam
follower ball-pins to their original locations,
where applicable.
7Lubricate the valve stems and guides with
SAE 80/90 hypoid oil, then insert the valves
into their original guides.
8Wrap a thin layer of adhesive tape over the
collet groove of each valve, then smear the
new oil seals with a little SAE 80/90 hypoid oil
and slide them down the valve stems onto the
guides. If necessary use a suitable metal tube
to press the oil seals into the guides. Remove
the adhesive tape.
9Working on each valve in turn, fit the valve
spring and cap, then compress the spring
using the valve spring compressor and fit the
split collets to the groove in the valve stem.
Release the compressor and tap the end of
the valve stem with a soft-faced mallet tosettle the components. If the original
components are being refitted, ensure that
they are refitted in their original locations.
10Refit the camshaft.
Note: On engines fitted with hardened valve
seats for use with unleaded petrol, valve and
valve seat grinding and recutting cannot be
carried out without the use of specialist
equipment. Consult a Ford dealer for further
advice.
1This operation will normally only be
required at comparatively high mileages.
However, if persistent pre-ignition (ÒpinkingÓ)
occurs and performance has deteriorated
even though the engine adjustments are
correct, de-carbonizing and valve grinding
may be required.
2With the cylinder head removed, use a
scraper to remove the carbon from the
combustion chambers and ports. Remove all
traces of gasket from the cylinder head
surface, then wash it thoroughly with paraffin.
3Use a straight edge and feeler blade to
check that the cylinder head surface is not
distorted. If it is, it must be resurfaced by a
suitably equipped engineering works.
4If the engine is still in the vehicle, clean the
piston crowns and cylinder bore upper edges,
but make sure that no carbon drops between
the pistons and bores. To do this, locate two
of the pistons at the top of their bores and
seal off the remaining bores with paper andmasking tape. Press a little grease between
the two pistons and their bores to collect any
carbon dust; this can be wiped away when
the piston is lowered. To prevent carbon
build-up, polish the piston crown with metal
polish, but remove all traces of the polish
afterwards.
5Examine the heads of the valves for pitting
and burning, especially the exhaust valve
heads. Renew any valve which is badly burnt.
Examine the valve seats at the same time. If
the pitting is very slight, it can be removed by
grinding the valve heads and seats together
with coarse, then fine, grinding paste.
6Where excessive pitting has occurred, the
valve seats must be recut or renewed by a
suitably equipped engineering works.
7Valve grinding is carried out as follows.
Place the cylinder head upside down on a
bench on blocks of wood.
8Smear a trace of coarse carborundum
paste on the valve seat face and press a
suction grinding tool onto the valve head.
With a semi-rotary action, grind the valve
head to its seat, lifting the valve occasionally
to redistribute the grinding paste. When a dull
matt even surface is produced on the mating
surface of both the valve seat and the valve,
wipe off the paste and repeat the process with
fine carborundum paste as before. A light
spring placed under the valve head will greatly
ease this operation. When a smooth unbroken
ring of light grey matt finish is produced on
the mating surface of both the valve and seat,
the grinding operation is complete.
9Scrape away all carbon from the valve head
and stem, and clean away all traces of
grinding compound. Clean the valves and
seats with a paraffin soaked rag, then wipe
with a clean rag.
10If the guides are worn they will need
reboring for oversize valves or for fitting guide
inserts. The valve seats will also need
recutting to ensure that they are concentric
with the stems. This work should be entrusted
to a Ford dealer or local engineering works.
11Check that the free length of the valve
springs is as specified, and renew if
necessary. Do not renew individual springs; if
any springs are excessively worn, renew all
the springs as a set.
23Cylinder head - inspection
and renovation
22Cylinder head - dismantling
and reassembly
2A¥16SOHC engines
22.2a Compressing a valve spring22.2c Removing a valve
22.4 Removing a valve stem oil seal
22.2b Removing a valve spring and cap