fuel type FORD SIERRA 1992 2.G Engine Electrical Systems Workshop Manual
[x] Cancel search | Manufacturer: FORD, Model Year: 1992, Model line: SIERRA, Model: FORD SIERRA 1992 2.GPages: 24, PDF Size: 0.93 MB
Page 1 of 24
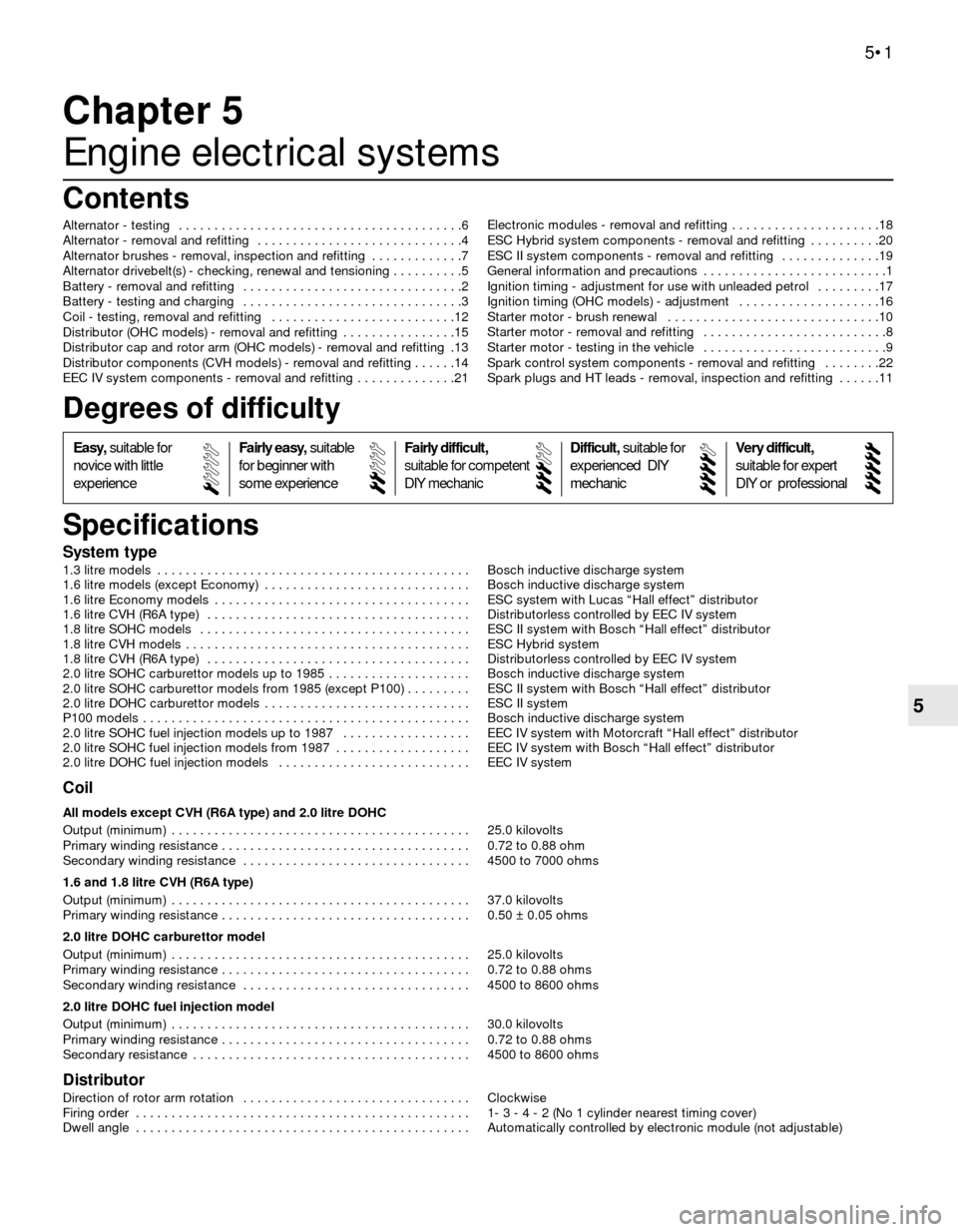
System type
1.3 litre models . . . . . . . . . . . . . . . . . . . . . . . . . . . . . . . . . . . . . . . . . . . . Bosch inductive discharge system
1.6 litre models (except Economy) . . . . . . . . . . . . . . . . . . . . . . . . . . . . . Bosch inductive discharge system
1.6 litre Economy models . . . . . . . . . . . . . . . . . . . . . . . . . . . . . . . . . . . . ESC system with Lucas “Hall effect” distributor
1.6 litre CVH (R6A type) . . . . . . . . . . . . . . . . . . . . . . . . . . . . . . . . . . . . . Distributorless controlled by EEC IV system
1.8 litre SOHC models . . . . . . . . . . . . . . . . . . . . . . . . . . . . . . . . . . . . . . ESC II system with Bosch “Hall effect” distributor
1.8 litre CVH models . . . . . . . . . . . . . . . . . . . . . . . . . . . . . . . . . . . . . . . . ESC Hybrid system
1.8 litre CVH (R6A type) . . . . . . . . . . . . . . . . . . . . . . . . . . . . . . . . . . . . . Distributorless controlled by EEC IV system
2.0 litre SOHC carburettor models up to 1985 . . . . . . . . . . . . . . . . . . . . Bosch inductive discharge system
2.0 litre SOHC carburettor models from 1985 (except P100) . . . . . . . . . ESC II system with Bosch “Hall effect” distributor
2.0 litre DOHC carburettor models . . . . . . . . . . . . . . . . . . . . . . . . . . . . . ESC II system
P100 models . . . . . . . . . . . . . . . . . . . . . . . . . . . . . . . . . . . . . . . . . . . . . . Bosch inductive discharge system
2.0 litre SOHC fuel injection models up to 1987 . . . . . . . . . . . . . . . . . . EEC IV system with Motorcraft “Hall effect” distributor
2.0 litre SOHC fuel injection models from 1987 . . . . . . . . . . . . . . . . . . . EEC IV system with Bosch “Hall effect” distributor
2.0 litre DOHC fuel injection models . . . . . . . . . . . . . . . . . . . . . . . . . . . EEC IV system
Coil
All models except CVH (R6A type) and 2.0 litre DOHC
Output (minimum) . . . . . . . . . . . . . . . . . . . . . . . . . . . . . . . . . . . . . . . . . . 25.0 kilovolts
Primary winding resistance . . . . . . . . . . . . . . . . . . . . . . . . . . . . . . . . . . . 0.72 to 0.88 ohm
Secondary winding resistance . . . . . . . . . . . . . . . . . . . . . . . . . . . . . . . . 4500 to 7000 ohms
1.6 and 1.8 litre CVH (R6A type)
Output (minimum) . . . . . . . . . . . . . . . . . . . . . . . . . . . . . . . . . . . . . . . . . . 37.0 kilovolts
Primary winding resistance . . . . . . . . . . . . . . . . . . . . . . . . . . . . . . . . . . . 0.50 ± 0.05 ohms
2.0 litre DOHC carburettor model
Output (minimum) . . . . . . . . . . . . . . . . . . . . . . . . . . . . . . . . . . . . . . . . . . 25.0 kilovolts
Primary winding resistance . . . . . . . . . . . . . . . . . . . . . . . . . . . . . . . . . . . 0.72 to 0.88 ohms
Secondary winding resistance . . . . . . . . . . . . . . . . . . . . . . . . . . . . . . . . 4500 to 8600 ohms
2.0 litre DOHC fuel injection model
Output (minimum) . . . . . . . . . . . . . . . . . . . . . . . . . . . . . . . . . . . . . . . . . . 30.0 kilovolts
Primary winding resistance . . . . . . . . . . . . . . . . . . . . . . . . . . . . . . . . . . . 0.72 to 0.88 ohms
Secondary resistance . . . . . . . . . . . . . . . . . . . . . . . . . . . . . . . . . . . . . . . 4500 to 8600 ohms
Distributor
Direction of rotor arm rotation . . . . . . . . . . . . . . . . . . . . . . . . . . . . . . . . Clockwise
Firing order . . . . . . . . . . . . . . . . . . . . . . . . . . . . . . . . . . . . . . . . . . . . . . . 1- 3 - 4 - 2 (No 1 cylinder nearest timing cover)
Dwell angle . . . . . . . . . . . . . . . . . . . . . . . . . . . . . . . . . . . . . . . . . . . . . . . Automatically controlled by electronic module (not adjustable)
Chapter 5
Engine electrical systems
Alternator - testing . . . . . . . . . . . . . . . . . . . . . . . . . . . . . . . . . . . . . . . .6
Alternator - removal and refitting . . . . . . . . . . . . . . . . . . . . . . . . . . . . .4
Alternator brushes - removal, inspection and refitting . . . . . . . . . . . . .7
Alternator drivebelt(s) - checking, renewal and tensioning . . . . . . . . . .5
Battery - removal and refitting . . . . . . . . . . . . . . . . . . . . . . . . . . . . . . .2
Battery - testing and charging . . . . . . . . . . . . . . . . . . . . . . . . . . . . . . .3
Coil - testing, removal and refitting . . . . . . . . . . . . . . . . . . . . . . . . . .12
Distributor (OHC models) - removal and refitting . . . . . . . . . . . . . . . .15
Distributor cap and rotor arm (OHC models) - removal and refitting .13
Distributor components (CVH models) - removal and refitting . . . . . .14
EEC IV system components - removal and refitting . . . . . . . . . . . . . .21Electronic modules - removal and refitting . . . . . . . . . . . . . . . . . . . . .18
ESC Hybrid system components - removal and refitting . . . . . . . . . .20
ESC II system components - removal and refitting . . . . . . . . . . . . . .19
General information and precautions . . . . . . . . . . . . . . . . . . . . . . . . . .1
Ignition timing - adjustment for use with unleaded petrol . . . . . . . . .17
Ignition timing (OHC models) - adjustment . . . . . . . . . . . . . . . . . . . .16
Starter motor - brush renewal . . . . . . . . . . . . . . . . . . . . . . . . . . . . . .10
Starter motor - removal and refitting . . . . . . . . . . . . . . . . . . . . . . . . . .8
Starter motor - testing in the vehicle . . . . . . . . . . . . . . . . . . . . . . . . . .9
Spark control system components - removal and refitting . . . . . . . .22
Spark plugs and HT leads - removal, inspection and refitting . . . . . .11
5•1
Specifications Contents
5
Easy,suitable for
novice with little
experienceFairly easy,suitable
for beginner with
some experienceFairly difficult,
suitable for competent
DIY mechanic
Difficult,suitable for
experienced DIY
mechanicVery difficult,
suitable for expert
DIY or professional
Degrees of difficulty
Page 2 of 24
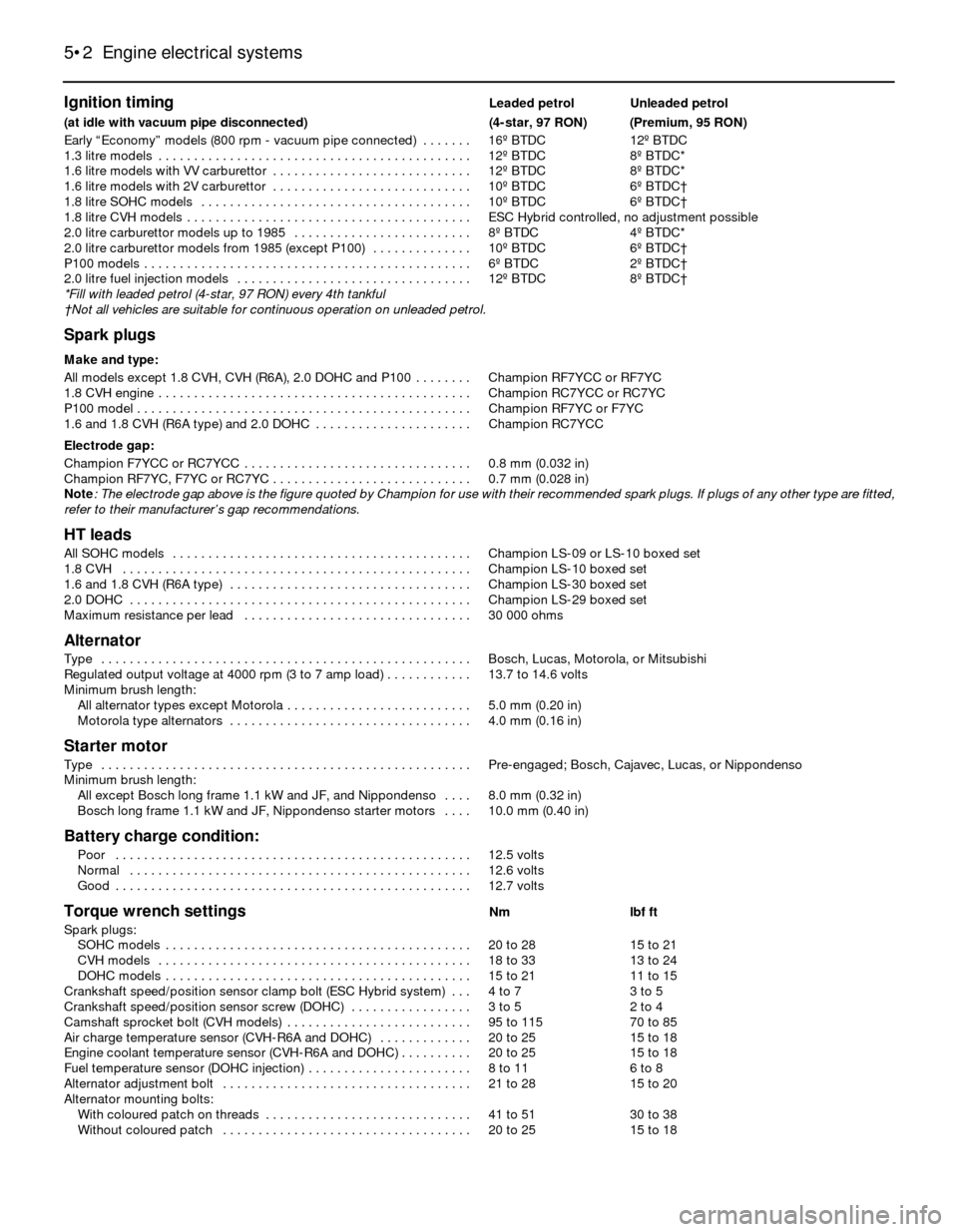
Ignition timingLeaded petrolUnleaded petrol
(at idle with vacuum pipe disconnected)(4-star, 97 RON)(Premium, 95 RON)
Early “Economy” models (800 rpm - vacuum pipe connected) . . . . . . .16º BTDC12º BTDC
1.3 litre models . . . . . . . . . . . . . . . . . . . . . . . . . . . . . . . . . . . . . . . . . . . .12º BTDC8º BTDC*
1.6 litre models with VV carburettor . . . . . . . . . . . . . . . . . . . . . . . . . . . .12º BTDC8º BTDC*
1.6 litre models with 2V carburettor . . . . . . . . . . . . . . . . . . . . . . . . . . . .10º BTDC6º BTDC†
1.8 litre SOHC models . . . . . . . . . . . . . . . . . . . . . . . . . . . . . . . . . . . . . .10º BTDC6º BTDC†
1.8 litre CVH models . . . . . . . . . . . . . . . . . . . . . . . . . . . . . . . . . . . . . . . .ESC Hybrid controlled, no adjustment possible
2.0 litre carburettor models up to 1985 . . . . . . . . . . . . . . . . . . . . . . . . .8º BTDC4º BTDC*
2.0 litre carburettor models from 1985 (except P100) . . . . . . . . . . . . . .10º BTDC6º BTDC†
P100 models . . . . . . . . . . . . . . . . . . . . . . . . . . . . . . . . . . . . . . . . . . . . . .6º BTDC2º BTDC†
2.0 litre fuel injection models . . . . . . . . . . . . . . . . . . . . . . . . . . . . . . . . .12º BTDC8º BTDC†
*Fill with leaded petrol (4-star, 97 RON) every 4th tankful
†Not all vehicles are suitable for continuous operation on unleaded petrol.
Spark plugs
Make and type:
All models except 1.8 CVH, CVH (R6A), 2.0 DOHC and P100 . . . . . . . .Champion RF7YCC or RF7YC
1.8 CVH engine . . . . . . . . . . . . . . . . . . . . . . . . . . . . . . . . . . . . . . . . . . . .Champion RC7YCC or RC7YC
P100 model . . . . . . . . . . . . . . . . . . . . . . . . . . . . . . . . . . . . . . . . . . . . . . .Champion RF7YC or F7YC
1.6 and 1.8 CVH (R6A type) and 2.0 DOHC . . . . . . . . . . . . . . . . . . . . . .Champion RC7YCC
Electrode gap:
Champion F7YCC or RC7YCC . . . . . . . . . . . . . . . . . . . . . . . . . . . . . . . .0.8 mm (0.032 in)
Champion RF7YC, F7YC or RC7YC . . . . . . . . . . . . . . . . . . . . . . . . . . . .0.7 mm (0.028 in)
Note: The electrode gap above is the figure quoted by Champion for use with their recommended spark plugs. If plugs of any other type are fitted,
refer to their manufacturer’s gap recommendations.
HT leads
All SOHC models . . . . . . . . . . . . . . . . . . . . . . . . . . . . . . . . . . . . . . . . . .Champion LS-09 or LS-10 boxed set
1.8 CVH . . . . . . . . . . . . . . . . . . . . . . . . . . . . . . . . . . . . . . . . . . . . . . . . .Champion LS-10 boxed set
1.6 and 1.8 CVH (R6A type) . . . . . . . . . . . . . . . . . . . . . . . . . . . . . . . . . .Champion LS-30 boxed set
2.0 DOHC . . . . . . . . . . . . . . . . . . . . . . . . . . . . . . . . . . . . . . . . . . . . . . . .Champion LS-29 boxed set
Maximum resistance per lead . . . . . . . . . . . . . . . . . . . . . . . . . . . . . . . .30 000 ohms
Alternator
Type . . . . . . . . . . . . . . . . . . . . . . . . . . . . . . . . . . . . . . . . . . . . . . . . . . . .Bosch, Lucas, Motorola, or Mitsubishi
Regulated output voltage at 4000 rpm (3 to 7 amp load) . . . . . . . . . . . .13.7 to 14.6 volts
Minimum brush length:
All alternator types except Motorola . . . . . . . . . . . . . . . . . . . . . . . . . .5.0 mm (0.20 in)
Motorola type alternators . . . . . . . . . . . . . . . . . . . . . . . . . . . . . . . . . .4.0 mm (0.16 in)
Starter motor
Type . . . . . . . . . . . . . . . . . . . . . . . . . . . . . . . . . . . . . . . . . . . . . . . . . . . .Pre-engaged; Bosch, Cajavec, Lucas, or Nippondenso
Minimum brush length:
All except Bosch long frame 1.1 kW and JF, and Nippondenso . . . .8.0 mm (0.32 in)
Bosch long frame 1.1 kW and JF, Nippondenso starter motors . . . .10.0 mm (0.40 in)
Battery charge condition:
Poor . . . . . . . . . . . . . . . . . . . . . . . . . . . . . . . . . . . . . . . . . . . . . . . . . .12.5 volts
Normal . . . . . . . . . . . . . . . . . . . . . . . . . . . . . . . . . . . . . . . . . . . . . . . .12.6 volts
Good . . . . . . . . . . . . . . . . . . . . . . . . . . . . . . . . . . . . . . . . . . . . . . . . . .12.7 volts
Torque wrench settingsNmlbf ft
Spark plugs:
SOHC models . . . . . . . . . . . . . . . . . . . . . . . . . . . . . . . . . . . . . . . . . . .20 to 2815 to 21
CVH models . . . . . . . . . . . . . . . . . . . . . . . . . . . . . . . . . . . . . . . . . . . .18 to 3313 to 24
DOHC models . . . . . . . . . . . . . . . . . . . . . . . . . . . . . . . . . . . . . . . . . . .15 to 2111 to 15
Crankshaft speed/position sensor clamp bolt (ESC Hybrid system) . . .4 to 73 to 5
Crankshaft speed/position sensor screw (DOHC) . . . . . . . . . . . . . . . . .3 to 52 to 4
Camshaft sprocket bolt (CVH models) . . . . . . . . . . . . . . . . . . . . . . . . . .95 to 11570 to 85
Air charge temperature sensor (CVH-R6A and DOHC) . . . . . . . . . . . . .20 to 2515 to 18
Engine coolant temperature sensor (CVH-R6A and DOHC) . . . . . . . . . .20 to 2515 to 18
Fuel temperature sensor (DOHC injection) . . . . . . . . . . . . . . . . . . . . . . .8 to 116 to 8
Alternator adjustment bolt . . . . . . . . . . . . . . . . . . . . . . . . . . . . . . . . . . .21 to 2815 to 20
Alternator mounting bolts:
With coloured patch on threads . . . . . . . . . . . . . . . . . . . . . . . . . . . . .41 to 5130 to 38
Without coloured patch . . . . . . . . . . . . . . . . . . . . . . . . . . . . . . . . . . .20 to 2515 to 18
5•2Engine electrical systems
Page 3 of 24
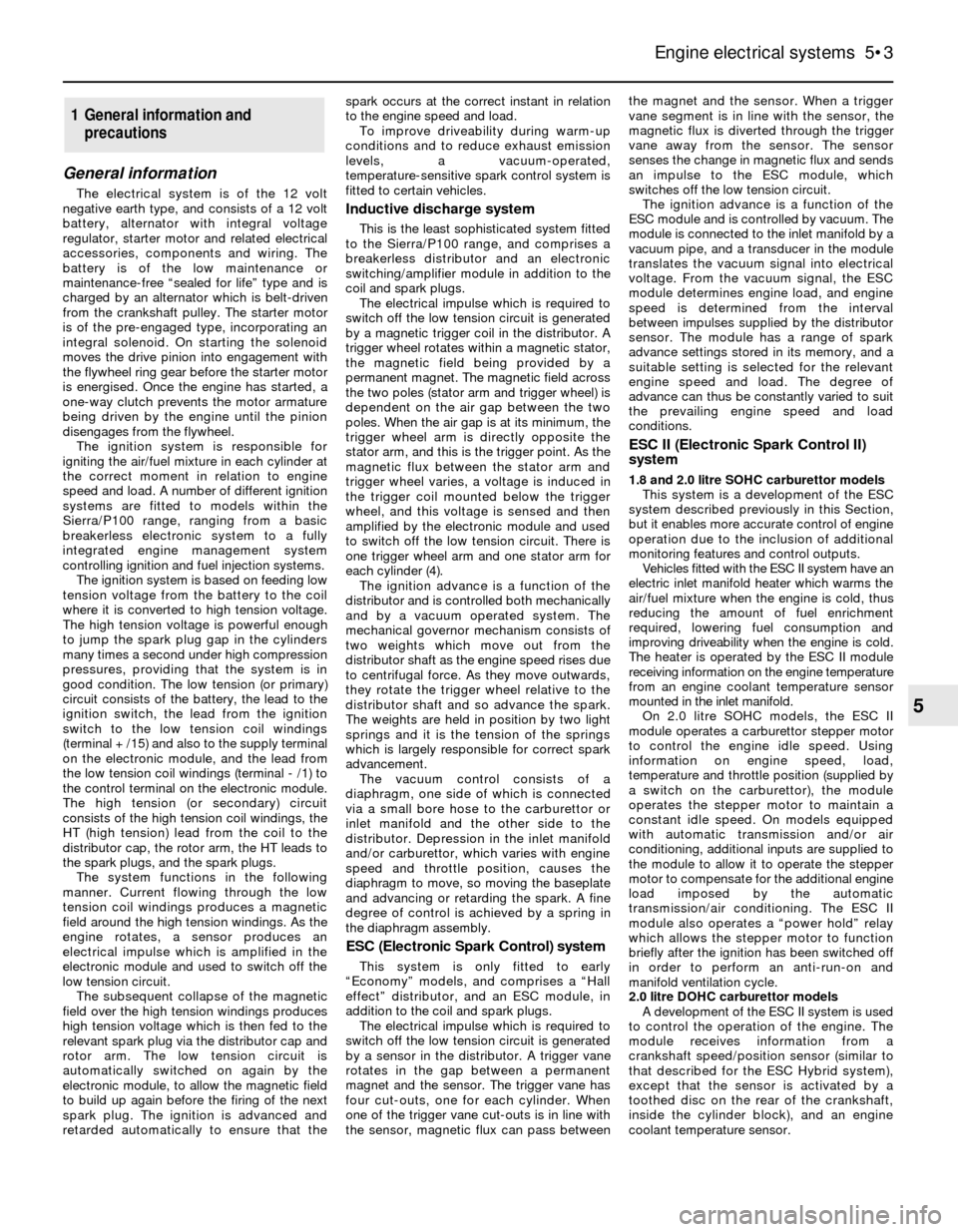
General information
The electrical system is of the 12 volt
negative earth type, and consists of a 12 volt
battery, alternator with integral voltage
regulator, starter motor and related electrical
accessories, components and wiring. The
battery is of the low maintenance or
maintenance-free “sealed for life” type and is
charged by an alternator which is belt-driven
from the crankshaft pulley. The starter motor
is of the pre-engaged type, incorporating an
integral solenoid. On starting the solenoid
moves the drive pinion into engagement with
the flywheel ring gear before the starter motor
is energised. Once the engine has started, a
one-way clutch prevents the motor armature
being driven by the engine until the pinion
disengages from the flywheel.
The ignition system is responsible for
igniting the air/fuel mixture in each cylinder at
the correct moment in relation to engine
speed and load. A number of different ignition
systems are fitted to models within the
Sierra/P100 range, ranging from a basic
breakerless electronic system to a fully
integrated engine management system
controlling ignition and fuel injection systems.
The ignition system is based on feeding low
tension voltage from the battery to the coil
where it is converted to high tension voltage.
The high tension voltage is powerful enough
to jump the spark plug gap in the cylinders
many times a second under high compression
pressures, providing that the system is in
good condition. The low tension (or primary)
circuit consists of the battery, the lead to the
ignition switch, the lead from the ignition
switch to the low tension coil windings
(terminal + /15) and also to the supply terminal
on the electronic module, and the lead from
the low tension coil windings (terminal -/1) to
the control terminal on the electronic module.
The high tension (or secondary) circuit
consists of the high tension coil windings, the
HT (high tension) lead from the coil to the
distributor cap, the rotor arm, the HT leads to
the spark plugs, and the spark plugs.
The system functions in the following
manner. Current flowing through the low
tension coil windings produces a magnetic
field around the high tension windings. As the
engine rotates, a sensor produces an
electrical impulse which is amplified in the
electronic module and used to switch off the
low tension circuit.
The subsequent collapse of the magnetic
field over the high tension windings produces
high tension voltage which is then fed to the
relevant spark plug via the distributor cap and
rotor arm. The low tension circuit is
automatically switched on again by the
electronic module, to allow the magnetic field
to build up again before the firing of the next
spark plug. The ignition is advanced and
retarded automatically to ensure that thespark occurs at the correct instant in relation
to the engine speed and load.
To improve driveability during warm-up
conditions and to reduce exhaust emission
levels, a vacuum-operated,
temperature-sensitive spark control system is
fitted to certain vehicles.Inductive discharge system
This is the least sophisticated system fitted
to the Sierra/P100 range, and comprises a
breakerless distributor and an electronic
switching/amplifier module in addition to the
coil and spark plugs.
The electrical impulse which is required to
switch off the low tension circuit is generated
by a magnetic trigger coil in the distributor. A
trigger wheel rotates within a magnetic stator,
the magnetic field being provided by a
permanent magnet. The magnetic field across
the two poles (stator arm and trigger wheel) is
dependent on the air gap between the two
poles. When the air gap is at its minimum, the
trigger wheel arm is directly opposite the
stator arm, and this is the trigger point. As the
magnetic flux between the stator arm and
trigger wheel varies, a voltage is induced in
the trigger coil mounted below the trigger
wheel, and this voltage is sensed and then
amplified by the electronic module and used
to switch off the low tension circuit. There is
one trigger wheel arm and one stator arm for
each cylinder (4).
The ignition advance is a function of the
distributor and is controlled both mechanically
and by a vacuum operated system. The
mechanical governor mechanism consists of
two weights which move out from the
distributor shaft as the engine speed rises due
to centrifugal force. As they move outwards,
they rotate the trigger wheel relative to the
distributor shaft and so advance the spark.
The weights are held in position by two light
springs and it is the tension of the springs
which is largely responsible for correct spark
advancement.
The vacuum control consists of a
diaphragm, one side of which is connected
via a small bore hose to the carburettor or
inlet manifold and the other side to the
distributor. Depression in the inlet manifold
and/or carburettor, which varies with engine
speed and throttle position, causes the
diaphragm to move, so moving the baseplate
and advancing or retarding the spark. A fine
degree of control is achieved by a spring in
the diaphragm assembly.
ESC (Electronic Spark Control) system
This system is only fitted to early
“Economy” models, and comprises a “Hall
effect” distributor, and an ESC module, in
addition to the coil and spark plugs.
The electrical impulse which is required to
switch off the low tension circuit is generated
by a sensor in the distributor. A trigger vane
rotates in the gap between a permanent
magnet and the sensor. The trigger vane has
four cut-outs, one for each cylinder. When
one of the trigger vane cut-outs is in line with
the sensor, magnetic flux can pass betweenthe magnet and the sensor. When a trigger
vane segment is in line with the sensor, the
magnetic flux is diverted through the trigger
vane away from the sensor. The sensor
senses the change in magnetic flux and sends
an impulse to the ESC module, which
switches off the low tension circuit.
The ignition advance is a function of the
ESC module and is controlled by vacuum. The
module is connected to the inlet manifold by a
vacuum pipe, and a transducer in the module
translates the vacuum signal into electrical
voltage. From the vacuum signal, the ESC
module determines engine load, and engine
speed is determined from the interval
between impulses supplied by the distributor
sensor. The module has a range of spark
advance settings stored in its memory, and a
suitable setting is selected for the relevant
engine speed and load. The degree of
advance can thus be constantly varied to suit
the prevailing engine speed and load
conditions.
ESC II (Electronic Spark Control II)
system
1.8 and 2.0 litre SOHC carburettor models
This system is a development of the ESC
system described previously in this Section,
but it enables more accurate control of engine
operation due to the inclusion of additional
monitoring features and control outputs.
Vehicles fitted with the ESC II system have an
electric inlet manifold heater which warms the
air/fuel mixture when the engine is cold, thus
reducing the amount of fuel enrichment
required, lowering fuel consumption and
improving driveability when the engine is cold.
The heater is operated by the ESC II module
receiving information on the engine temperature
from an engine coolant temperature sensor
mounted in the inlet manifold.
On 2.0 litre SOHC models, the ESC II
module operates a carburettor stepper motor
to control the engine idle speed. Using
information on engine speed, load,
temperature and throttle position (supplied by
a switch on the carburettor), the module
operates the stepper motor to maintain a
constant idle speed. On models equipped
with automatic transmission and/or air
conditioning, additional inputs are supplied to
the module to allow it to operate the stepper
motor to compensate for the additional engine
load imposed by the automatic
transmission/air conditioning. The ESC II
module also operates a “power hold” relay
which allows the stepper motor to function
briefly after the ignition has been switched off
in order to perform an anti-run-on and
manifold ventilation cycle.
2.0 litre DOHC carburettor models
A development of the ESC II system is used
to control the operation of the engine. The
module receives information from a
crankshaft speed/position sensor (similar to
that described for the ESC Hybrid system),
except that the sensor is activated by a
toothed disc on the rear of the crankshaft,
inside the cylinder block), and an engine
coolant temperature sensor.
1General information and
precautions
Engine electrical systems 5•3
5
Page 4 of 24
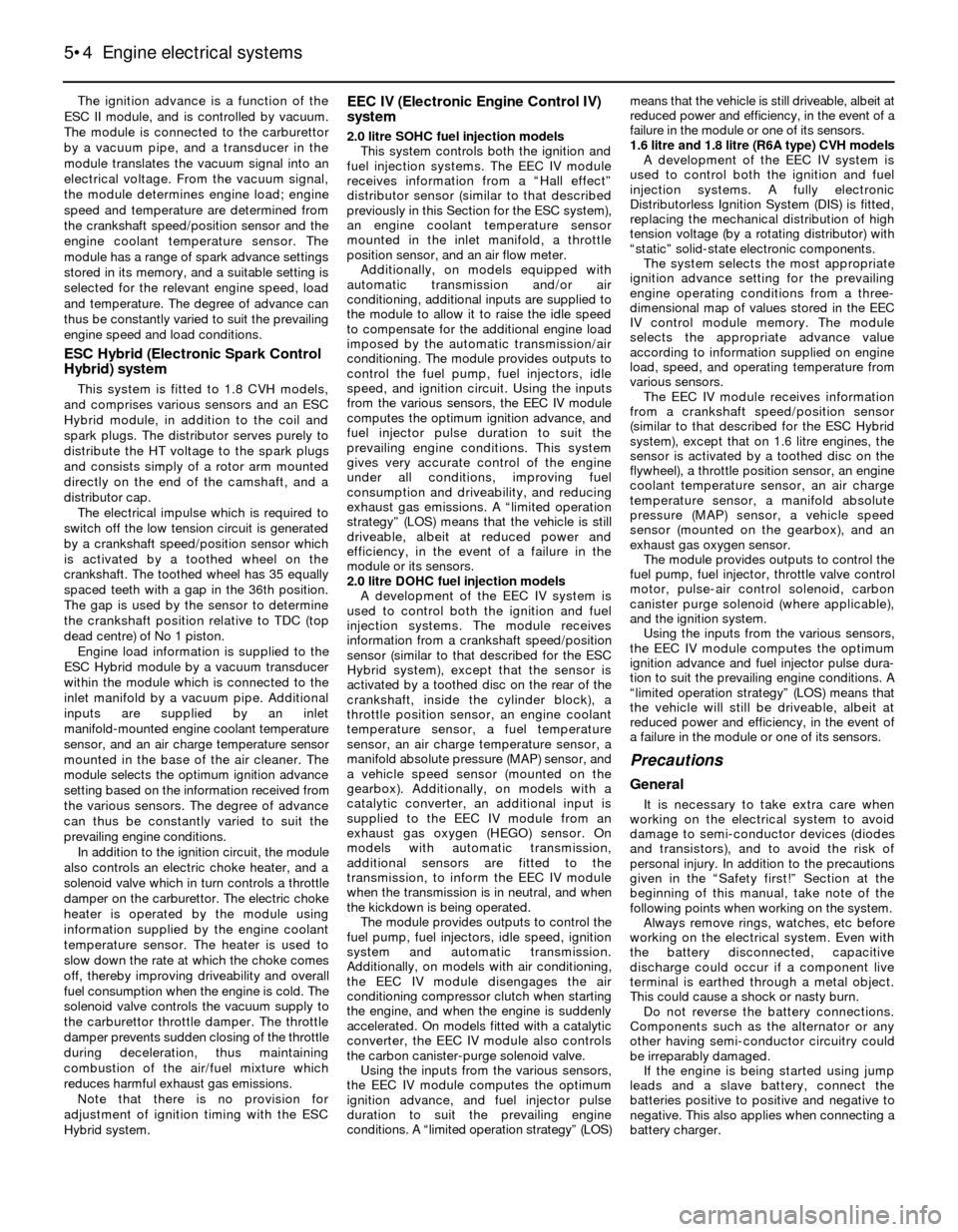
The ignition advance is a function of the
ESC II module, and is controlled by vacuum.
The module is connected to the carburettor
by a vacuum pipe, and a transducer in the
module translates the vacuum signal into an
electrical voltage. From the vacuum signal,
the module determines engine load; engine
speed and temperature are determined from
the crankshaft speed/position sensor and the
engine coolant temperature sensor. The
module has a range of spark advance settings
stored in its memory, and a suitable setting is
selected for the relevant engine speed, load
and temperature. The degree of advance can
thus be constantly varied to suit the prevailing
engine speed and load conditions.
ESC Hybrid (Electronic Spark Control
Hybrid) system
This system is fitted to 1.8 CVH models,
and comprises various sensors and an ESC
Hybrid module, in addition to the coil and
spark plugs. The distributor serves purely to
distribute the HT voltage to the spark plugs
and consists simply of a rotor arm mounted
directly on the end of the camshaft, and a
distributor cap.
The electrical impulse which is required to
switch off the low tension circuit is generated
by a crankshaft speed/position sensor which
is activated by a toothed wheel on the
crankshaft. The toothed wheel has 35 equally
spaced teeth with a gap in the 36th position.
The gap is used by the sensor to determine
the crankshaft position relative to TDC (top
dead centre) of No 1 piston.
Engine load information is supplied to the
ESC Hybrid module by a vacuum transducer
within the module which is connected to the
inlet manifold by a vacuum pipe. Additional
inputs are supplied by an inlet
manifold-mounted engine coolant temperature
sensor, and an air charge temperature sensor
mounted in the base of the air cleaner. The
module selects the optimum ignition advance
setting based on the information received from
the various sensors. The degree of advance
can thus be constantly varied to suit the
prevailing engine conditions.
In addition to the ignition circuit, the module
also controls an electric choke heater, and a
solenoid valve which in turn controls a throttle
damper on the carburettor. The electric choke
heater is operated by the module using
information supplied by the engine coolant
temperature sensor. The heater is used to
slow down the rate at which the choke comes
off, thereby improving driveability and overall
fuel consumption when the engine is cold. The
solenoid valve controls the vacuum supply to
the carburettor throttle damper. The throttle
damper prevents sudden closing of the throttle
during deceleration, thus maintaining
combustion of the air/fuel mixture which
reduces harmful exhaust gas emissions.
Note that there is no provision for
adjustment of ignition timing with the ESC
Hybrid system.
EEC IV (Electronic Engine Control IV)
system
2.0 litre SOHC fuel injection models
This system controls both the ignition and
fuel injection systems. The EEC IV module
receives information from a “Hall effect”
distributor sensor (similar to that described
previously in this Section for the ESC system),
an engine coolant temperature sensor
mounted in the inlet manifold, a throttle
position sensor, and an air flow meter.
Additionally, on models equipped with
automatic transmission and/or air
conditioning, additional inputs are supplied to
the module to allow it to raise the idle speed
to compensate for the additional engine load
imposed by the automatic transmission/air
conditioning. The module provides outputs to
control the fuel pump, fuel injectors, idle
speed, and ignition circuit. Using the inputs
from the various sensors, the EEC IV module
computes the optimum ignition advance, and
fuel injector pulse duration to suit the
prevailing engine conditions. This system
gives very accurate control of the engine
under all conditions, improving fuel
consumption and driveability, and reducing
exhaust gas emissions. A “limited operation
strategy” (LOS) means that the vehicle is still
driveable, albeit at reduced power and
efficiency, in the event of a failure in the
module or its sensors.
2.0 litre DOHC fuel injection models
A development of the EEC IV system is
used to control both the ignition and fuel
injection systems. The module receives
information from a crankshaft speed/position
sensor (similar to that described for the ESC
Hybrid system), except that the sensor is
activated by a toothed disc on the rear of the
crankshaft, inside the cylinder block), a
throttle position sensor, an engine coolant
temperature sensor, a fuel temperature
sensor, an air charge temperature sensor, a
manifold absolute pressure (MAP) sensor, and
a vehicle speed sensor (mounted on the
gearbox). Additionally, on models with a
catalytic converter, an additional input is
supplied to the EEC IV module from an
exhaust gas oxygen (HEGO) sensor. On
models with automatic transmission,
additional sensors are fitted to the
transmission, to inform the EEC IV module
when the transmission is in neutral, and when
the kickdown is being operated.
The module provides outputs to control the
fuel pump, fuel injectors, idle speed, ignition
system and automatic transmission.
Additionally, on models with air conditioning,
the EEC IV module disengages the air
conditioning compressor clutch when starting
the engine, and when the engine is suddenly
accelerated. On models fitted with a catalytic
converter, the EEC IV module also controls
the carbon canister-purge solenoid valve.
Using the inputs from the various sensors,
the EEC IV module computes the optimum
ignition advance, and fuel injector pulse
duration to suit the prevailing engine
conditions. A “limited operation strategy” (LOS)means that the vehicle is still driveable, albeit at
reduced power and efficiency, in the event of a
failure in the module or one of its sensors.
1.6 litre and 1.8 litre (R6A type) CVH models
A development of the EEC IV system is
used to control both the ignition and fuel
injection systems. A fully electronic
Distributorless Ignition System (DIS) is fitted,
replacing the mechanical distribution of high
tension voltage (by a rotating distributor) with
“static” solid-state electronic components.
The system selects the most appropriate
ignition advance setting for the prevailing
engine operating conditions from a three-
dimensional map of values stored in the EEC
IV control module memory. The module
selects the appropriate advance value
according to information supplied on engine
load, speed, and operating temperature from
various sensors.
The EEC IV module receives information
from a crankshaft speed/position sensor
(similar to that described for the ESC Hybrid
system), except that on 1.6 litre engines, the
sensor is activated by a toothed disc on the
flywheel), a throttle position sensor, an engine
coolant temperature sensor, an air charge
temperature sensor, a manifold absolute
pressure (MAP) sensor, a vehicle speed
sensor (mounted on the gearbox), and an
exhaust gas oxygen sensor.
The module provides outputs to control the
fuel pump, fuel injector, throttle valve control
motor, pulse-air control solenoid, carbon
canister purge solenoid (where applicable),
and the ignition system.
Using the inputs from the various sensors,
the EEC IV module computes the optimum
ignition advance and fuel injector pulse dura-
tion to suit the prevailing engine conditions. A
“limited operation strategy” (LOS) means that
the vehicle will still be driveable, albeit at
reduced power and efficiency, in the event of
a failure in the module or one of its sensors.
Precautions
General
It is necessary to take extra care when
working on the electrical system to avoid
damage to semi-conductor devices (diodes
and transistors), and to avoid the risk of
personal injury. In addition to the precautions
given in the “Safety first!” Section at the
beginning of this manual, take note of the
following points when working on the system.
Always remove rings, watches, etc before
working on the electrical system. Even with
the battery disconnected, capacitive
discharge could occur if a component live
terminal is earthed through a metal object.
This could cause a shock or nasty burn.
Do not reverse the battery connections.
Components such as the alternator or any
other having semi-conductor circuitry could
be irreparably damaged.
If the engine is being started using jump
leads and a slave battery, connect the
batteries positive to positive and negative to
negative. This also applies when connecting a
battery charger.
5•4Engine electrical systems
Page 7 of 24
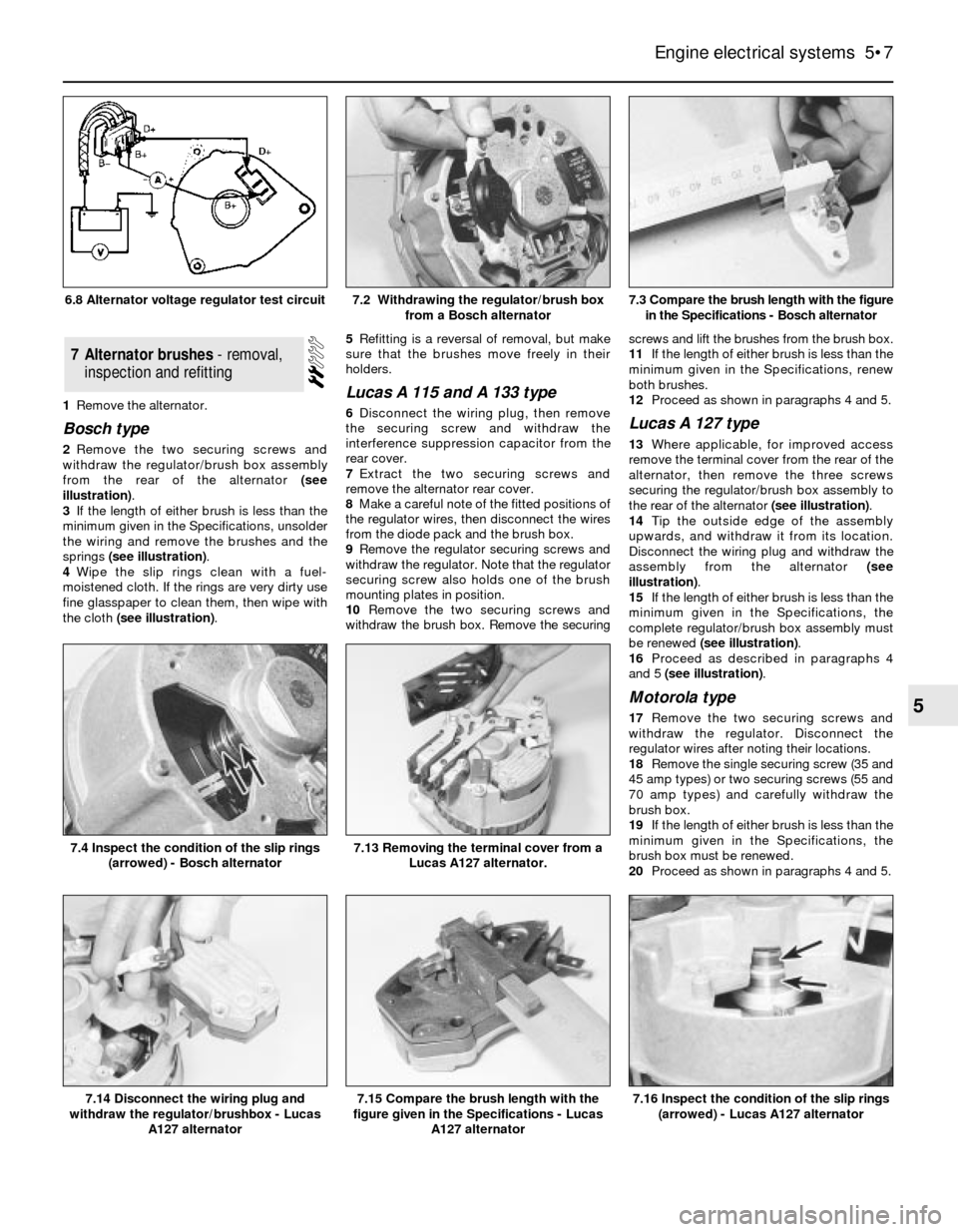
1Remove the alternator.
Bosch type
2Remove the two securing screws and
withdraw the regulator/brush box assembly
from the rear of the alternator (see
illustration).
3If the length of either brush is less than the
minimum given in the Specifications, unsolder
the wiring and remove the brushes and the
springs (see illustration).
4Wipe the slip rings clean with a fuel-
moistened cloth. If the rings are very dirty use
fine glasspaper to clean them, then wipe with
the cloth (see illustration).5Refitting is a reversal of removal, but make
sure that the brushes move freely in their
holders.
Lucas A 115 and A 133 type
6Disconnect the wiring plug, then remove
the securing screw and withdraw the
interference suppression capacitor from the
rear cover.
7Extract the two securing screws and
remove the alternator rear cover.
8Make a careful note of the fitted positions of
the regulator wires, then disconnect the wires
from the diode pack and the brush box.
9Remove the regulator securing screws and
withdraw the regulator. Note that the regulator
securing screw also holds one of the brush
mounting plates in position.
10Remove the two securing screws and
withdraw the brush box. Remove the securingscrews and lift the brushes from the brush box.
11If the length of either brush is less than the
minimum given in the Specifications, renew
both brushes.
12Proceed as shown in paragraphs 4 and 5.Lucas A 127 type
13Where applicable, for improved access
remove the terminal cover from the rear of the
alternator, then remove the three screws
securing the regulator/brush box assembly to
the rear of the alternator (see illustration).
14Tip the outside edge of the assembly
upwards, and withdraw it from its location.
Disconnect the wiring plug and withdraw the
assembly from the alternator (see
illustration).
15If the length of either brush is less than the
minimum given in the Specifications, the
complete regulator/brush box assembly must
be renewed (see illustration).
16Proceed as described in paragraphs 4
and 5 (see illustration).
Motorola type
17Remove the two securing screws and
withdraw the regulator. Disconnect the
regulator wires after noting their locations.
18Remove the single securing screw (35 and
45 amp types) or two securing screws (55 and
70 amp types) and carefully withdraw the
brush box.
19If the length of either brush is less than the
minimum given in the Specifications, the
brush box must be renewed.
20Proceed as shown in paragraphs 4 and 5.
7Alternator brushes - removal,
inspection and refitting
Engine electrical systems 5•7
5
7.3 Compare the brush length with the figure
in the Specifications - Bosch alternator
7.16 Inspect the condition of the slip rings
(arrowed) - Lucas A127 alternator7.15 Compare the brush length with the
figure given in the Specifications - Lucas
A127 alternator7.14 Disconnect the wiring plug and
withdraw the regulator/brushbox - Lucas
A127 alternator
7.13 Removing the terminal cover from a
Lucas A127 alternator.7.4 Inspect the condition of the slip rings
(arrowed) - Bosch alternator
7.2 Withdrawing the regulator/brush box
from a Bosch alternator6.8 Alternator voltage regulator test circuit
Page 8 of 24
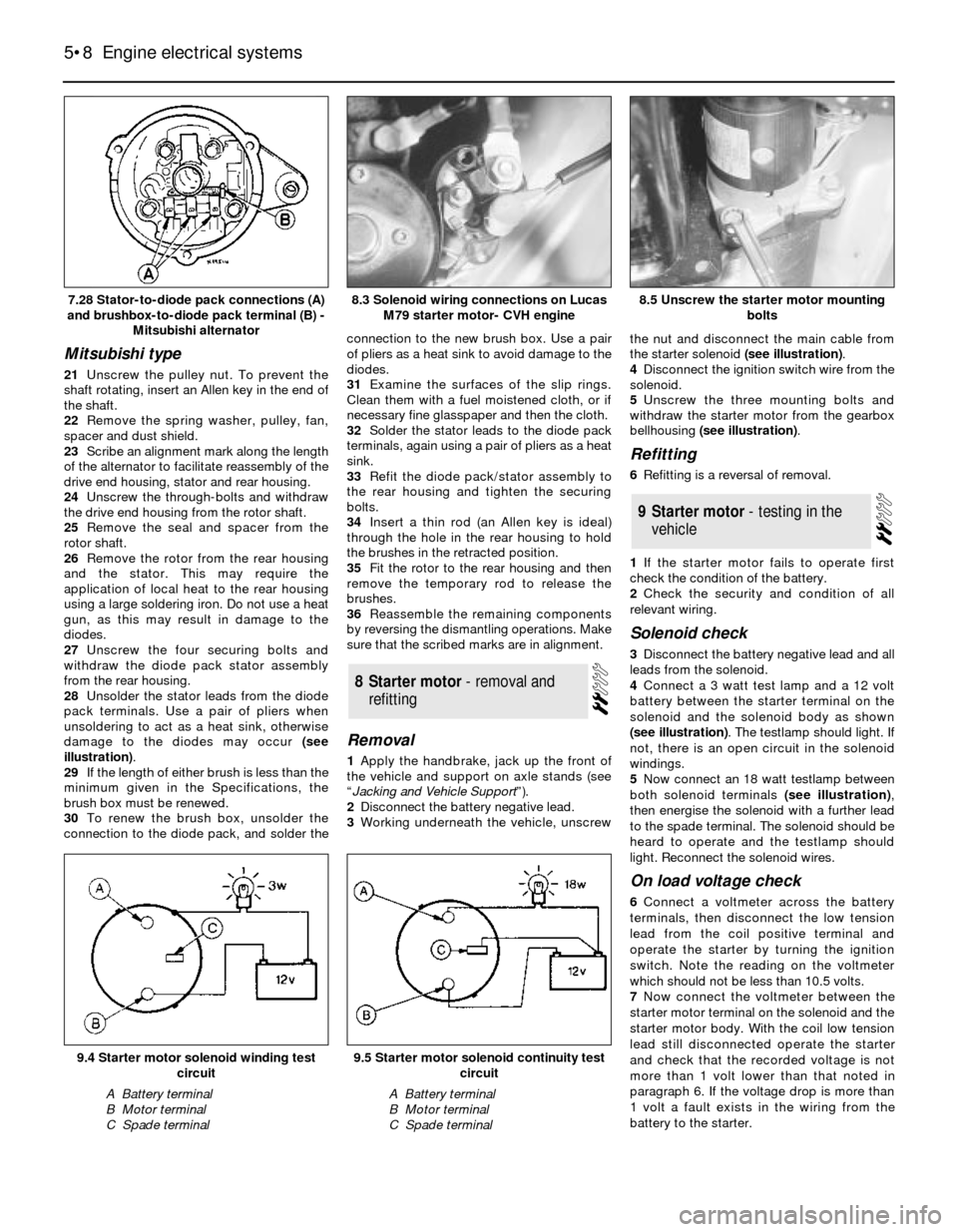
Mitsubishi type
21Unscrew the pulley nut. To prevent the
shaft rotating, insert an Allen key in the end of
the shaft.
22Remove the spring washer, pulley, fan,
spacer and dust shield.
23Scribe an alignment mark along the length
of the alternator to facilitate reassembly of the
drive end housing, stator and rear housing.
24Unscrew the through-bolts and withdraw
the drive end housing from the rotor shaft.
25Remove the seal and spacer from the
rotor shaft.
26Remove the rotor from the rear housing
and the stator. This may require the
application of local heat to the rear housing
using a large soldering iron. Do not use a heat
gun, as this may result in damage to the
diodes.
27Unscrew the four securing bolts and
withdraw the diode pack stator assembly
from the rear housing.
28Unsolder the stator leads from the diode
pack terminals. Use a pair of pliers when
unsoldering to act as a heat sink, otherwise
damage to the diodes may occur (see
illustration).
29If the length of either brush is less than the
minimum given in the Specifications, the
brush box must be renewed.
30To renew the brush box, unsolder the
connection to the diode pack, and solder theconnection to the new brush box. Use a pair
of pliers as a heat sink to avoid damage to the
diodes.
31Examine the surfaces of the slip rings.
Clean them with a fuel moistened cloth, or if
necessary fine glasspaper and then the cloth.
32Solder the stator leads to the diode pack
terminals, again using a pair of pliers as a heat
sink.
33Refit the diode pack/stator assembly to
the rear housing and tighten the securing
bolts.
34Insert a thin rod (an Allen key is ideal)
through the hole in the rear housing to hold
the brushes in the retracted position.
35Fit the rotor to the rear housing and then
remove the temporary rod to release the
brushes.
36Reassemble the remaining components
by reversing the dismantling operations. Make
sure that the scribed marks are in alignment.
Removal
1Apply the handbrake, jack up the front of
the vehicle and support on axle stands (see
“Jacking and Vehicle Support”).
2Disconnect the battery negative lead.
3Working underneath the vehicle, unscrewthe nut and disconnect the main cable from
the starter solenoid (see illustration).
4Disconnect the ignition switch wire from the
solenoid.
5Unscrew the three mounting bolts and
withdraw the starter motor from the gearbox
bellhousing (see illustration).
Refitting
6Refitting is a reversal of removal.
1If the starter motor fails to operate first
check the condition of the battery.
2Check the security and condition of all
relevant wiring.
Solenoid check
3Disconnect the battery negative lead and all
leads from the solenoid.
4Connect a 3 watt test lamp and a 12 volt
battery between the starter terminal on the
solenoid and the solenoid body as shown
(see illustration). The testlamp should light. If
not, there is an open circuit in the solenoid
windings.
5Now connect an 18 watt testlamp between
both solenoid terminals (see illustration),
then energise the solenoid with a further lead
to the spade terminal. The solenoid should be
heard to operate and the testlamp should
light. Reconnect the solenoid wires.
On load voltage check
6Connect a voltmeter across the battery
terminals, then disconnect the low tension
lead from the coil positive terminal and
operate the starter by turning the ignition
switch. Note the reading on the voltmeter
which should not be less than 10.5 volts.
7Now connect the voltmeter between the
starter motor terminal on the solenoid and the
starter motor body. With the coil low tension
lead still disconnected operate the starter
and check that the recorded voltage is not
more than 1 volt lower than that noted in
paragraph 6. If the voltage drop is more than
1 volt a fault exists in the wiring from the
battery to the starter.
9Starter motor - testing in the
vehicle
8Starter motor - removal and
refitting
5•8Engine electrical systems
7.28 Stator-to-diode pack connections (A)
and brushbox-to-diode pack terminal (B) -
Mitsubishi alternator8.5 Unscrew the starter motor mounting
bolts
9.5 Starter motor solenoid continuity test
circuit
A Battery terminal
B Motor terminal
C Spade terminal
9.4 Starter motor solenoid winding test
circuit
A Battery terminal
B Motor terminal
C Spade terminal
8.3 Solenoid wiring connections on Lucas
M79 starter motor- CVH engine
Page 9 of 24
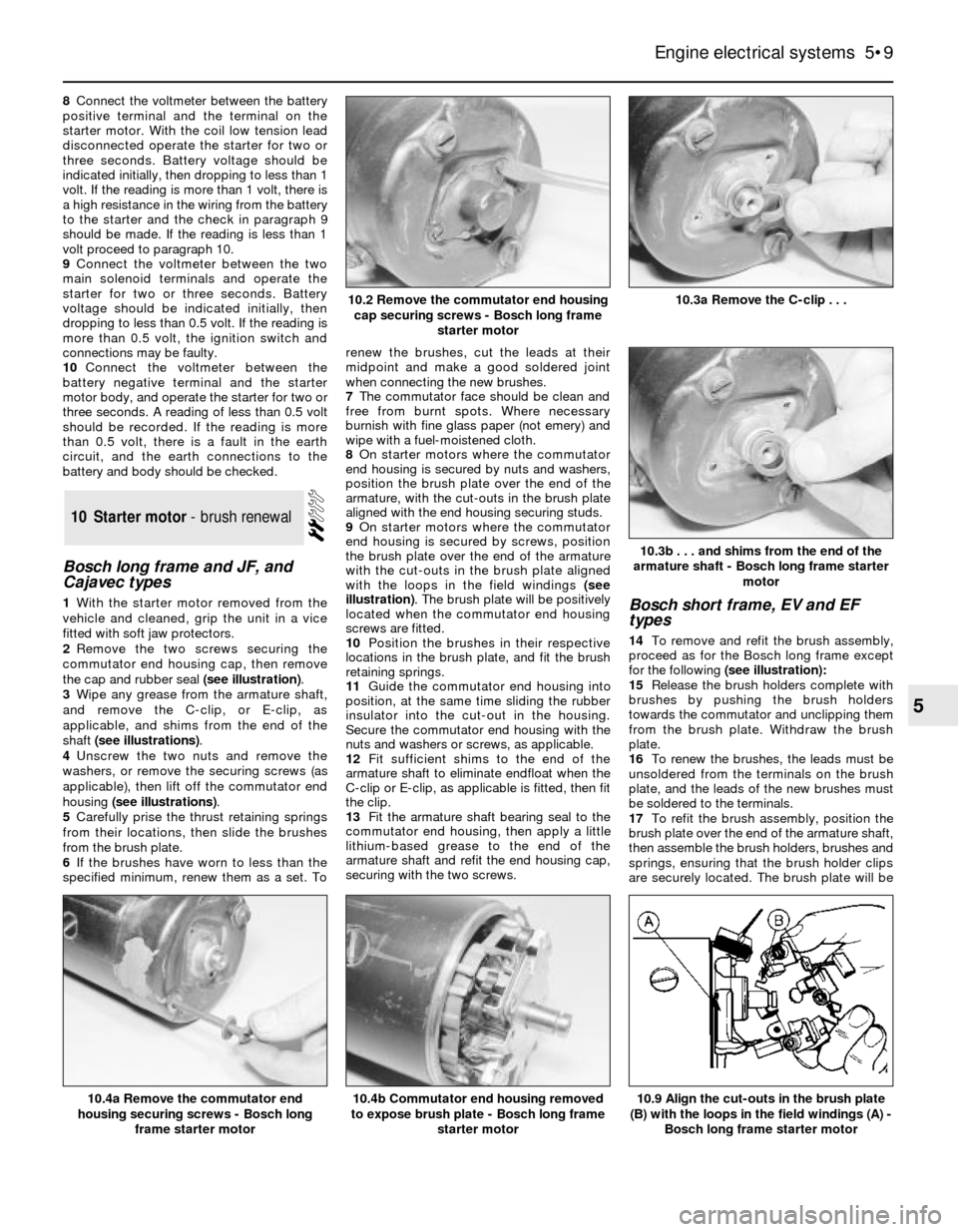
8Connect the voltmeter between the battery
positive terminal and the terminal on the
starter motor. With the coil low tension lead
disconnected operate the starter for two or
three seconds. Battery voltage should be
indicated initially, then dropping to less than 1
volt. If the reading is more than 1 volt, there is
a high resistance in the wiring from the battery
to the starter and the check in paragraph 9
should be made. If the reading is less than 1
volt proceed to paragraph 10.
9Connect the voltmeter between the two
main solenoid terminals and operate the
starter for two or three seconds. Battery
voltage should be indicated initially, then
dropping to less than 0.5 volt. If the reading is
more than 0.5 volt, the ignition switch and
connections may be faulty.
10Connect the voltmeter between the
battery negative terminal and the starter
motor body, and operate the starter for two or
three seconds. A reading of less than 0.5 volt
should be recorded. If the reading is more
than 0.5 volt, there is a fault in the earth
circuit, and the earth connections to the
battery and body should be checked.
Bosch long frame and JF, and
Cajavec types
1With the starter motor removed from the
vehicle and cleaned, grip the unit in a vice
fitted with soft jaw protectors.
2Remove the two screws securing the
commutator end housing cap, then remove
the cap and rubber seal (see illustration).
3Wipe any grease from the armature shaft,
and remove the C-clip, or E-clip, as
applicable, and shims from the end of the
shaft (see illustrations).
4Unscrew the two nuts and remove the
washers, or remove the securing screws (as
applicable), then lift off the commutator end
housing (see illustrations).
5Carefully prise the thrust retaining springs
from their locations, then slide the brushes
from the brush plate.
6If the brushes have worn to less than the
specified minimum, renew them as a set. Torenew the brushes, cut the leads at their
midpoint and make a good soldered joint
when connecting the new brushes.
7The commutator face should be clean and
free from burnt spots. Where necessary
burnish with fine glass paper (not emery) and
wipe with a fuel-moistened cloth.
8On starter motors where the commutator
end housing is secured by nuts and washers,
position the brush plate over the end of the
armature, with the cut-outs in the brush plate
aligned with the end housing securing studs.
9On starter motors where the commutator
end housing is secured by screws, position
the brush plate over the end of the armature
with the cut-outs in the brush plate aligned
with the loops in the field windings (see
illustration). The brush plate will be positively
located when the commutator end housing
screws are fitted.
10Position the brushes in their respective
locations in the brush plate, and fit the brush
retaining springs.
11Guide the commutator end housing into
position, at the same time sliding the rubber
insulator into the cut-out in the housing.
Secure the commutator end housing with the
nuts and washers or screws, as applicable.
12Fit sufficient shims to the end of the
armature shaft to eliminate endfloat when the
C-clip or E-clip, as applicable is fitted, then fit
the clip.
13Fit the armature shaft bearing seal to the
commutator end housing, then apply a little
lithium-based grease to the end of the
armature shaft and refit the end housing cap,
securing with the two screws.Bosch short frame, EV and EF
types
14To remove and refit the brush assembly,
proceed as for the Bosch long frame except
for the following(see illustration):
15Release the brush holders complete with
brushes by pushing the brush holders
towards the commutator and unclipping them
from the brush plate. Withdraw the brush
plate.
16To renew the brushes, the leads must be
unsoldered from the terminals on the brush
plate, and the leads of the new brushes must
be soldered to the terminals.
17To refit the brush assembly, position the
brush plate over the end of the armature shaft,
then assemble the brush holders, brushes and
springs, ensuring that the brush holder clips
are securely located. The brush plate will be
10Starter motor - brush renewal
Engine electrical systems 5•9
5
10.3b . . . and shims from the end of the
armature shaft - Bosch long frame starter
motor
10.9 Align the cut-outs in the brush plate
(B) with the loops in the field windings (A) -
Bosch long frame starter motor10.4b Commutator end housing removed
to expose brush plate - Bosch long frame
starter motor10.4a Remove the commutator end
housing securing screws - Bosch long
frame starter motor
10.3a Remove the C-clip . . .10.2 Remove the commutator end housing
cap securing screws - Bosch long frame
starter motor
Page 10 of 24
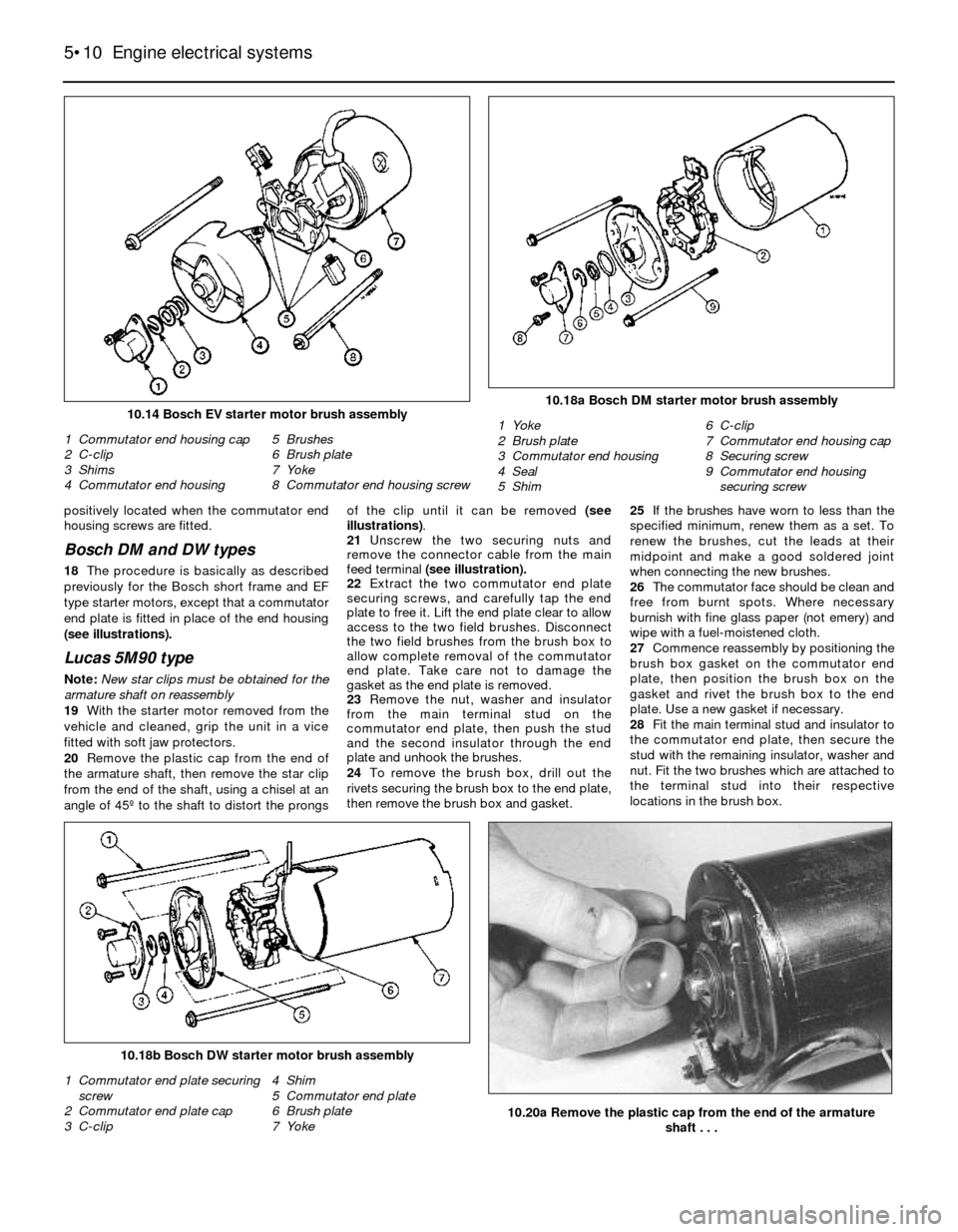
positively located when the commutator end
housing screws are fitted.
Bosch DM and DW types
18The procedure is basically as described
previously for the Bosch short frame and EF
type starter motors, except that a commutator
end plate is fitted in place of the end housing
(see illustrations).
Lucas 5M90 type
Note: New star clips must be obtained for the
armature shaft on reassembly
19With the starter motor removed from the
vehicle and cleaned, grip the unit in a vice
fitted with soft jaw protectors.
20Remove the plastic cap from the end of
the armature shaft, then remove the star clip
from the end of the shaft, using a chisel at an
angle of 45º to the shaft to distort the prongsof the clip until it can be removed (see
illustrations).
21Unscrew the two securing nuts and
remove the connector cable from the main
feed terminal (see illustration).
22Extract the two commutator end plate
securing screws, and carefully tap the end
plate to free it. Lift the end plate clear to allow
access to the two field brushes. Disconnect
the two field brushes from the brush box to
allow complete removal of the commutator
end plate. Take care not to damage the
gasket as the end plate is removed.
23Remove the nut, washer and insulator
from the main terminal stud on the
commutator end plate, then push the stud
and the second insulator through the end
plate and unhook the brushes.
24To remove the brush box, drill out the
rivets securing the brush box to the end plate,
then remove the brush box and gasket.25If the brushes have worn to less than the
specified minimum, renew them as a set. To
renew the brushes, cut the leads at their
midpoint and make a good soldered joint
when connecting the new brushes.
26The commutator face should be clean and
free from burnt spots. Where necessary
burnish with fine glass paper (not emery) and
wipe with a fuel-moistened cloth.
27Commence reassembly by positioning the
brush box gasket on the commutator end
plate, then position the brush box on the
gasket and rivet the brush box to the end
plate. Use a new gasket if necessary.
28Fit the main terminal stud and insulator to
the commutator end plate, then secure the
stud with the remaining insulator, washer and
nut. Fit the two brushes which are attached to
the terminal stud into their respective
locations in the brush box.
5•10Engine electrical systems
10.18a Bosch DM starter motor brush assembly
1 Yoke
2 Brush plate
3 Commutator end housing
4 Seal
5 Shim6 C-clip
7 Commutator end housing cap
8 Securing screw
9 Commutator end housing
securing screw
10.20a Remove the plastic cap from the end of the armature
shaft . . .
10.18b Bosch DW starter motor brush assembly
1 Commutator end plate securing
screw
2 Commutator end plate cap
3 C-clip4 Shim
5 Commutator end plate
6 Brush plate
7 Yoke
10.14 Bosch EV starter motor brush assembly
1 Commutator end housing cap
2 C-clip
3 Shims
4 Commutator end housing5 Brushes
6 Brush plate
7 Yoke
8 Commutator end housing screw
Page 11 of 24
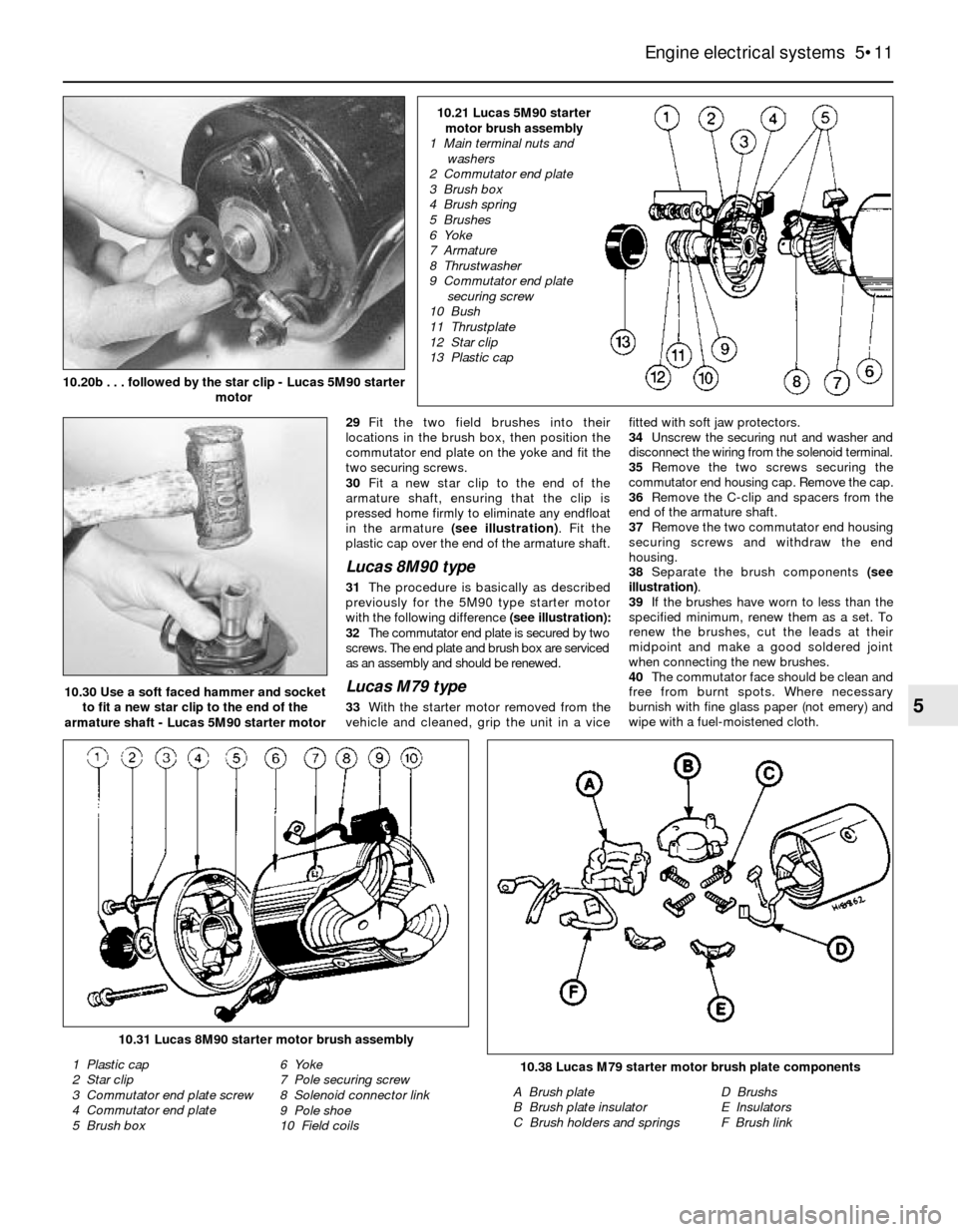
29Fit the two field brushes into their
locations in the brush box, then position the
commutator end plate on the yoke and fit the
two securing screws.
30Fit a new star clip to the end of the
armature shaft, ensuring that the clip is
pressed home firmly to eliminate any endfloat
in the armature (see illustration). Fit the
plastic cap over the end of the armature shaft.
Lucas 8M90 type
31The procedure is basically as described
previously for the 5M90 type starter motor
with the following difference(see illustration):
32The commutator end plate is secured by two
screws. The end plate and brush box are serviced
as an assembly and should be renewed.
Lucas M79 type
33With the starter motor removed from the
vehicle and cleaned, grip the unit in a vicefitted with soft jaw protectors.
34Unscrew the securing nut and washer and
disconnect the wiring from the solenoid terminal.
35Remove the two screws securing the
commutator end housing cap. Remove the cap.
36Remove the C-clip and spacers from the
end of the armature shaft.
37Remove the two commutator end housing
securing screws and withdraw the end
housing.
38Separate the brush components (see
illustration).
39If the brushes have worn to less than the
specified minimum, renew them as a set. To
renew the brushes, cut the leads at their
midpoint and make a good soldered joint
when connecting the new brushes.
40The commutator face should be clean and
free from burnt spots. Where necessary
burnish with fine glass paper (not emery) and
wipe with a fuel-moistened cloth.
Engine electrical systems 5•11
5
10.38 Lucas M79 starter motor brush plate components
A Brush plate
B Brush plate insulator
C Brush holders and springsD Brushs
E Insulators
F Brush link
10.31 Lucas 8M90 starter motor brush assembly
1 Plastic cap
2 Star clip
3 Commutator end plate screw
4 Commutator end plate
5 Brush box6 Yoke
7 Pole securing screw
8 Solenoid connector link
9 Pole shoe
10 Field coils
10.30 Use a soft faced hammer and socket
to fit a new star clip to the end of the
armature shaft - Lucas 5M90 starter motor
10.20b . . . followed by the star clip - Lucas 5M90 starter
motor
10.21 Lucas 5M90 starter
motor brush assembly
1 Main terminal nuts and
washers
2 Commutator end plate
3 Brush box
4 Brush spring
5 Brushes
6 Yoke
7 Armature
8 Thrustwasher
9 Commutator end plate
securing screw
10 Bush
11 Thrustplate
12 Star clip
13 Plastic cap
Page 12 of 24
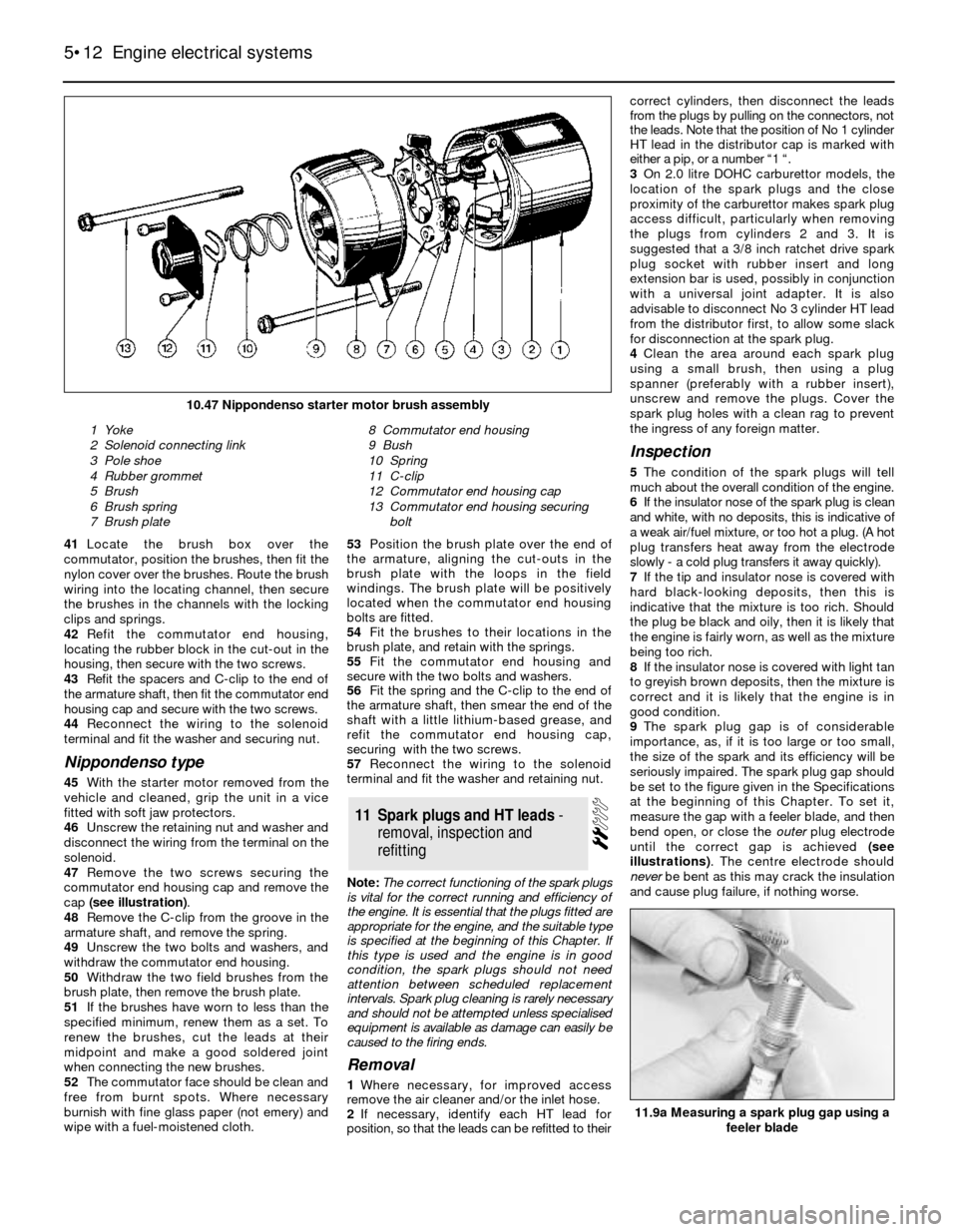
41Locate the brush box over the
commutator, position the brushes, then fit the
nylon cover over the brushes. Route the brush
wiring into the locating channel, then secure
the brushes in the channels with the locking
clips and springs.
42Refit the commutator end housing,
locating the rubber block in the cut-out in the
housing, then secure with the two screws.
43Refit the spacers and C-clip to the end of
the armature shaft, then fit the commutator end
housing cap and secure with the two screws.
44Reconnect the wiring to the solenoid
terminal and fit the washer and securing nut.
Nippondenso type
45With the starter motor removed from the
vehicle and cleaned, grip the unit in a vice
fitted with soft jaw protectors.
46Unscrew the retaining nut and washer and
disconnect the wiring from the terminal on the
solenoid.
47Remove the two screws securing the
commutator end housing cap and remove the
cap (see illustration).
48Remove the C-clip from the groove in the
armature shaft, and remove the spring.
49Unscrew the two bolts and washers, and
withdraw the commutator end housing.
50Withdraw the two field brushes from the
brush plate, then remove the brush plate.
51If the brushes have worn to less than the
specified minimum, renew them as a set. To
renew the brushes, cut the leads at their
midpoint and make a good soldered joint
when connecting the new brushes.
52The commutator face should be clean and
free from burnt spots. Where necessary
burnish with fine glass paper (not emery) and
wipe with a fuel-moistened cloth. 53Position the brush plate over the end of
the armature, aligning the cut-outs in the
brush plate with the loops in the field
windings. The brush plate will be positively
located when the commutator end housing
bolts are fitted.
54Fit the brushes to their locations in the
brush plate, and retain with the springs.
55Fit the commutator end housing and
secure with the two bolts and washers.
56Fit the spring and the C-clip to the end of
the armature shaft, then smear the end of the
shaft with a little lithium-based grease, and
refit the commutator end housing cap,
securing with the two screws.
57Reconnect the wiring to the solenoid
terminal and fit the washer and retaining nut.
Note: The correct functioning of the spark plugs
is vital for the correct running and efficiency of
the engine. It is essential that the plugs fitted are
appropriate for the engine, and the suitable type
is specified at the beginning of this Chapter. If
this type is used and the engine is in good
condition, the spark plugs should not need
attention between scheduled replacement
intervals. Spark plug cleaning is rarely necessary
and should not be attempted unless specialised
equipment is available as damage can easily be
caused to the firing ends.
Removal
1Where necessary, for improved access
remove the air cleaner and/or the inlet hose.
2If necessary, identify each HT lead for
position, so that the leads can be refitted to theircorrect cylinders, then disconnect the leads
from the plugs by pulling on the connectors, not
the leads. Note that the position of No 1 cylinder
HT lead in the distributor cap is marked with
either a pip, or a number “1 “.
3On 2.0 litre DOHC carburettor models, the
location of the spark plugs and the close
proximity of the carburettor makes spark plug
access difficult, particularly when removing
the plugs from cylinders 2 and 3. It is
suggested that a 3/8 inch ratchet drive spark
plug socket with rubber insert and long
extension bar is used, possibly in conjunction
with a universal joint adapter. It is also
advisable to disconnect No 3 cylinder HT lead
from the distributor first, to allow some slack
for disconnection at the spark plug.
4Clean the area around each spark plug
using a small brush, then using a plug
spanner (preferably with a rubber insert),
unscrew and remove the plugs. Cover the
spark plug holes with a clean rag to prevent
the ingress of any foreign matter.
Inspection
5The condition of the spark plugs will tell
much about the overall condition of the engine.
6If the insulator nose of the spark plug is clean
and white, with no deposits, this is indicative of
a weak air/fuel mixture, or too hot a plug. (A hot
plug transfers heat away from the electrode
slowly - a cold plug transfers it away quickly).
7If the tip and insulator nose is covered with
hard black-looking deposits, then this is
indicative that the mixture is too rich. Should
the plug be black and oily, then it is likely that
the engine is fairly worn, as well as the mixture
being too rich.
8If the insulator nose is covered with light tan
to greyish brown deposits, then the mixture is
correct and it is likely that the engine is in
good condition.
9The spark plug gap is of considerable
importance, as, if it is too large or too small,
the size of the spark and its efficiency will be
seriously impaired. The spark plug gap should
be set to the figure given in the Specifications
at the beginning of this Chapter. To set it,
measure the gap with a feeler blade, and then
bend open, or close the outer plug electrode
until the correct gap is achieved (see
illustrations). The centre electrode should
never be bent as this may crack the insulation
and cause plug failure, if nothing worse.
11Spark plugs and HT leads -
removal, inspection and
refitting
5•12Engine electrical systems
10.47 Nippondenso starter motor brush assembly
1 Yoke
2 Solenoid connecting link
3 Pole shoe
4 Rubber grommet
5 Brush
6 Brush spring
7 Brush plate8 Commutator end housing
9 Bush
10 Spring
11 C-clip
12 Commutator end housing cap
13 Commutator end housing securing
bolt
11.9a Measuring a spark plug gap using a
feeler blade